DOI:
10.1039/C7RA00349H
(Paper)
RSC Adv., 2017,
7, 12938-12944
Fabrication of single-walled carbon nanotubes from vulcanized scrap rubber via thermal chemical vapor deposition
Received
9th January 2017
, Accepted 20th February 2017
First published on 24th February 2017
Abstract
Our previous investigations found that when acrylonitrile butadiene rubber (NBR) was compatibilized with styrene butadiene rubber (SBR) using montmorillonite, the resulting blend exhibited enhanced mechanical strength and heat resistance. However, the enhancement complicates the recycling possibility of the blend at the end of its service period. Pyrolysis of the blend disposal, as a facile recycling route for beneficiation of this material, was elaborated optimally at 450 °C, as specified from thermal gravimetric analysis (TGA), in a horizontal chemical vapor deposition (CVD) pyrolyzer under nitrogen flow to yield hydrocarbon fractions. The CVD process of the resulting hydrocarbons on different catalytic systems was undertaken at 850 °C for 30 min. The investigations carried out using high resolution transmission electron microscopy (HRTEM), thermal gravimetric analysis (TGA) and Raman spectroscopy proved prominent formation of single-walled carbon nanotubes (SWCNTs) in a very efficient yield. It was found that the structure and diameter of produced CNTs were controlled by the crystallinity of the Fe–Ni catalyst supported on different zeolites. Conclusively, the prepared catalyst support played a crucial role in determining both the morphology and yield of the resulting CNTs.
1. Introduction
Rubber is produced from natural or synthetic sources. Natural rubber is obtained from a milky white fluid called latex, found in many plants, while synthetic rubbers are produced from unsaturated hydrocarbons. The vulcanization process, which involves intensive chemical crosslinking, was a breakthrough because it gives increased strength, elasticity, and resistance to changes in temperature. It also renders the rubber impermeable to gases and resistant to heat, electricity, chemical action and abrasion. The acquired interesting properties are desirable for many industries, which broadened the applications of rubber products. Nevertheless, a major shortcoming of vulcanization is that it makes further recycling of rubber a hard process. As such, vulcanized rubber products consist of about 60–70% hydrocarbons and can be considered as a store of energy.
The ever increasing number of automobiles and the consequential increase in consumption of tyres generated a pressing environmental issue, because they are not biodegradable.1,2 The rubber scraps are class of rubber materials which composed mainly of hydrocarbons, and therefore present carbon rich sources. As far as these waste materials are vulcanized (thermoset polymers), they cannot be reprocessed easily like thermoplastic polymers. Therefore, recycling of these materials requires special techniques that demands high investment and sophisticated technologies.3–5
One form of thermal recovery is pyrolysis that involves heating the rubber waste under nitrogen atmosphere. This causes decomposition into gases and constituent parts. It has been reported that combustion or pyrolysis of tyres yielded char, pyro-oil, light hydrocarbons (CH4, C2H4, C3H6, and C4H8), H2, CO, and CO2.3 The char product can be used to prepare activated carbon, whereas the pyro-oil and light hydrocarbons could be used as a fuel source.3 On the other hand, the use of gas phase hydrocarbons as carbon source for synthesis of carbon nanotubes is very important for industrial and environmental concerns.
Styrene–butadiene rubber and butadiene rubber are commonly used for tyre manufacture. The manufacture process requires various additives to give desired characteristics to the finished products. The rubber formulations presented in the current work comprise acrylonitrile butadiene rubber (NBR) compatiblized with styrene butadiene rubber (SBR), with the aid of Na-montmorillonite.6 These formulations were considered as a model scrap for production of carbon nanotubes in our previous study.7
The production of carbon nanotubes (MWCNTs) from rubber scrap is very rare.8 Its potential use as carbon precursor depends upon different parameters including type and particle size of both catalyst and support, carrier gas and its flow rate, time and temperature of CNTs growth via catalytic chemical vapor deposition (CVD). These parameters need further investigations to study their influences on the yield and flawlessness of produced CNTs from scrap rubber. Therefore, the area of producing CNTs from plastic or rubber waste is still very open for further research and seems as a promising route for both waste reduction and synthesis of added-value products such as carbon nanotubes.
In particular, various methods have been developed for the synthesis of CNTs such as arc discharge,9 pyrolysis,10 laser ablation,11 plasma assisted deposition12 and thermal chemical vapor deposition.13 Among them, chemical vapor deposition (CVD) is currently the most widely used, because it requires relatively low cost equipment and therefore tends to be the choice both for academic and industrial purposes for producing comparatively large amounts of CNTs in a short time. It is well-known that catalytic decomposition of hydrocarbons was found to be a promising means to produce CNTs at a large scale.14 Synthesis of CNTs through thermal decomposition of plastic derivatives, such as polyethylene (PE), polypropylene (PP) using catalysts, has also been reported.15–19 Kong and Zhang17 and Zhang et al.19 used PE and MA-PP as precursors for synthesis of CNTs through mixing PE and PP with ferrocene/Ni as catalyst in a stainless steel autoclave heated at 700 °C for 100 min. Jiang et al.18 used combustion method for synthesis of CNTs using Ni compound/organic-modified montmorillonite (OMMT) and polypropylene as a source. Multi-walled carbon nanotubes (MWCNTs) were efficiently synthesized by catalytic combustion of PP using nickel compounds as catalysts in the presence of OMMT at 630–830 °C as reported by Tang et al.20 In an earlier effort by Zhou et al.,21 two step processes comprising combustion and pyrolysis were used for synthesis of carbon nanomaterials using catalyst.
It is well-known that catalyst-support interaction is vital factor affecting the final properties of CNTs produced through CVD process and indicating the type of growth mechanism. Various catalyst-support materials containing common catalysts such as Fe, Ni, Co, supported on porous inorganic supports like graphite, quartz, silicon, silicon carbide, silica, alumina, zeolite, CaCO3, MgO, etc., were prepared in mono-, bi- or tertiary metal oxides and/or metals to be used in CVD for growing CNTs. Indeed, catalyst-support interaction would possess a significant effect on the shape, quality and yield of the resulting CNTs. For instance, in a previous study carried out by Yang et al.8 the CVD of NBR/SBR degradation products in presence of Fe2O3/Al2O3 as catalyst produced low yield of CNTs bundles with wide range of diameters. Such result has been explained on the strong interaction between iron oxide and alumina, which forms aggregation of metal species and undesired large clusters, hence produces graphite particles or defective MWCNTs.22
Among literature, it was reported that zeolite supports impregnated with mono- or mixed-metals of Co, Fe, Ni (e.g. Fe–Co or Fe–Ni–Mn) have produced significantly high yields of SWCNTs and/or MWCNTs from CVD of camphor as carbon gas source.23,24 Accordingly, the chemical state, surface morphology and pore size distributions of the catalyst-support composites are important factors for this process. Further, the temperature of CNT growth during chemical vapor deposition of hydrocarbons was found to affect the yield and type of produced CNTs considerably.25
The homogeneous nano-scale structure of SWCNTs leads to extraordinary mechanical, thermal, electrical and optical applications. In particular, the diameter and degree of twist have impressive effect on their electronic properties. This causes the tubes to behave as metallic conductors for many electronic applications.26,27
Therefore, this study will explore the potential use of Ni–Fe oxides supported on three different morphologies of zeolites by impregnation–evaporation method to produce SWCNTs from blend of scrap rubber (NBR/SBR) through chemical vapor deposition (CVD) which we hope to represent an efficient and economic recipe.
2. Experimental
2.1. Materials
Montmorillonite (Na-MMT), with a maximum particle size of 60 μm, was ordered from Alfa Aesar GmbH & Co, Karlsruhe, Germany. Iron nitrate was purchased from Aldrich in purity of 99.9%. Commercial grade tetramethyl thiuram disulfide (TMTD), N-cyclohexyl-2-benzothiazolesulfenamide (CBS) and zinc oxide were used. Styrene–butadiene rubber (SBR 1502) was a gift from Transportation and Engineering Company, Alexandria – Egypt. Acrylonitrile–butadiene rubber (under trade name perbunan) was supplied from Bayer AG – Germany and will be denoted as NBR through the current work.
2.2. Blending of NBR and SBR
Compounding of NBR and SBR was undertaken at a weight ratio of 1
:
1. Thus, both were mixed on a two-roll mill with 470 mm outer diameter and a roll was running at a slow speed 24 rpm and a gear ratio of 1
:
1.4. A fixed loading of montmorillonite (20 phr) was included at ambient temperature in addition to other components necessary for processing and vulcanization. In brief, zinc oxide (5 phr), stearic acid (2 phr), CBS (1.5 phr), TMTD (0.3 phr) and sulphur (2 phr). The mixing process was undertaken in about 25 min. An oscillating disc rheometer model 100 Monsanto-USA, was used for measuring the curing characteristics of the blends at 152 °C.6 The produced blend was subjected to curing (vulcanization) after one day from its preparation using electrically heated platens at 152 °C and 4 MPa to produce vulcanized rubber sheet with 2 mm thickness.
2.3. Preparation of zeolite substrate with different compositions
To prepare zeolite X (ZX), refined kaolin, supplied by Middle East Mining Company (Memco), was used as the starting material, its chemical composition in wt% contained 51.25 SiO2, 40.94 Al2O3, 0.31 Fe2O3, 0.62 TiO2 and some other minor constituents of MgO, CaO and K2O. Sodium hydroxide, in the form pellets, of analyzed ACS reagent with the composition of 98.6% NaOH + 0.4% chloride (Sigma-Aldrich), was applied. Ludox 40 was the source of additional SiO2 for adjusting the kaolin composition to meet the targeted zeolite formula. The batch composition of the starting rock and the corresponding gel modification to the targeted zeolites are given in Table 1.
Table 1 Batch composition of the starting gel
Materials (ratio) |
ZeoliteX composition |
Faujasite-Na (ZX) |
SiO2/Al2O3 |
2–7 |
NaOH molarity |
3–4 |
H2O/SiO2 |
120–150 |
A calculated amount of NaOH is dissolved in distilled water, to which a weighed amount of metakaolinite is added under stirring for 1 h. A measured quantity of ludox 40 (as silica source) is then added dropwise to the previous mixture and finally the resulting slurry is stirred overnight. Subsequently, an amount of 20–25 mL of the previously prepared slurry was batched in the 100 mL capacity Xpress vessels of microwave digestive system (Mars 5, Model XP-1500, CEM Corp., Matthews, NC). Two exposure times were applied to the resulting slurry, mainly, 60 min and 30 min. The system was operated at a frequency of 2.45 GHz and 1–100% of 1600 W power. After heat treatment, the prepared powders were collected, washed several times with distilled water and then dried at 100 °C overnight in an electric oven. The prepared samples were denoted as ZX-M and ZX-N according to working time of 60 and 30 min, respectively. On the other hand, preparation of titanosilicate zeolite (ETS4) was carried out by a hydrothermal technique as mentioned previously28 and denoted as Z-T25.
2.4. Preparation of Ni–Fe/zeolites by wet impregnation–evaporation method
An incipient wetness impregnation–evaporation method was employed for the preparation of Ni–Fe supported on three different zeolites (ZX-M, ZX-N and Z-T25) as a catalyst for the growth of carbon nanotubes. Briefly, definite amounts from nitrate salts of both nickel and iron, which are equivalent to 5 wt% of their oxides after pyrolysis, were dissolved in 10 mL of distilled water. Then, zeolite was added slowly to a solution of mixed nitrates under mechanical stirring at ambient temperature for 30 min. After that, the mixture was vaporized by heating at 80 °C in an air-oven for 1 h then left overnight for drying. The dried mixture was ground to very fine powder and denoted as Ni–Fe/ZX-M, Ni–Fe/ZX-N and Ni–Fe/Z-T25.
2.5. Thermal chemical vapor deposition using rubber composites as carbon source
Pyrolysis was undertaken in a home-made horizontal flow CVD furnace consisting of two sections. The mass ratio of rubber to catalyst was fixed at 1
:
0.15 through the process. Rubber samples were shredded and put in an alumina boat and kept inside the first furnace where pyrolysis process of rubber sample takes place under flowing nitrogen. The nitrogen pushes the cracked hydrocarbons and other gaseous products into alumina boat containing the catalyst (ZX-M, ZX-N or Z-T25) in the second section. This section was heated gradually first to 850 °C then the first one is heated slowly to 450 °C for inducing cracking of the rubber. After reaching 450 °C, a growth time of 30 min was elapsed for the maturation of CNTs. At the end, the two sections were switched off and a deposit of black carbon was formed on the catalyst. The resulting CNTs on the catalyst were subjected to purification treatment using 5 M of HNO3 and H2SO4 mixed solutions.
2.6. Characterizations
The thermal stability of the samples was examined under nitrogen atmosphere a heating rate of 10 °C min−1 using Shimadzu-60 thermal analyzer, Japan. High resolution transmission electron microscopy (HRTEM) images for the resulting catalysts and carbon nanotubes (CNTs) were taken using high resolution transmission electron microscope (JEM-1230, Japan) operated at 120 kV. The Raman investigation was carried out at room temperature with Sentera laser Raman spectrometer (Bruker, Germany).
3. Results and discussion
3.1. Thermal decomposition of scrap rubber
The thermal decomposition of the scrap rubber was studied under nitrogen atmosphere in the range from 25–550 °C to help in deciding the optimal temperature at which the pyrolysis process will be acted upon. It is obvious from Fig. 1 that the main degradation region lies between 350 and 47 °C which results in liberation of gaseous degradation products. The liberated gases will act as the carbon source for production of CNTs via CVD. A residual weight of 20% at the end of the thermal run matches well with the originally inserted loading of the inorganic montmorillonite, which corroborates complete conversion of the organic rubber into gaseous hydrocarbon products and hydrogen.6 At 450 °C, the decomposition process was approximately complete. As such, 450 °C was selected as the temperature at which the pyrolysis process will be undertaken. It was reached through heating from room temperature at a low heating rate to ensure maximal release of lighter hydrocarbons entrapped in the scrap rubber. It is well known that high heating rates will leave significant portion of heavier hydrocarbon fractions behind, which lowers the efficiency of the CVD process and yield of produced CNTs as well.
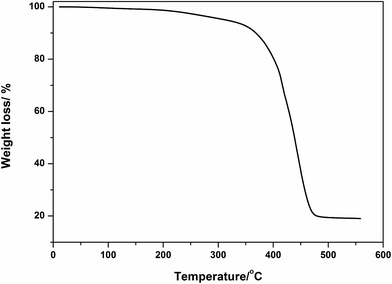 |
| Fig. 1 TGA profile of NBR/SBR-Mont (20 phr). | |
3.2. Morphology characterization of catalyst supported zeolites
TEM images of Ni–Fe/zeolite catalysts before chemical vapor deposition process are exhibited in Fig. 2a–c. Based on the chemical and surface compositions of prepared zeolites in the current work, three different morphologies of interconnected zeolite particles impregnated with catalysts can be observed in nanometer scale. The images reveal uniform distribution of the catalyst particles in high concentration over the surface of the zeolite support, confirming the preparation of nanosized catalysts supported on zeolites. It can be noticed that the Fe–Ni catalyst supported on ZX-N exhibited better distribution than Fe–Ni catalyst supported on ZX-M. As a result of crystallization time employed during preparation of ZX by microwave, the produced catalyst supported on ZX-M was more crystalline than that supported on ZX-N. On the other hand, the produced ZX-M consists of larger particle size than ZX-N when prepared through microwave under different crystallization time. Accordingly, the structure, type and diameter of the produced CNTs were found to be controlled by the morphological properties of the prepared catalysts as shown in the next section.
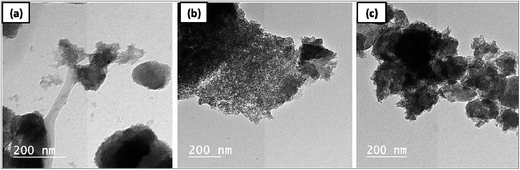 |
| Fig. 2 HR-TEM images of prepared zeolite based catalyst systems, Fe–Ni/ZX-M (a) Fe–Ni/ZX-N (b) and Fe–Ni/Z-T25 (c). | |
3.3. Morphology characterization of prepared CNTs
Fig. 3a–c shows TEM images of the CNTs accumulated on the catalysts surfaces after chemical vapor deposition at 850 °C for 30 min for the cracked gases resulting from the pyrolysis of NBR/SBR scrap rubber at 450 °C. By using Fe–Ni/ZX-M as catalyst, it can be seen obviously that a large amount of CNTs is obtained with coiled, twisted structure and a smooth outer surface (Fig. 3a). The formed CNTs/ZX-M exhibited quite regular outer diameters of approximately 13 nm. Moreover, a very tiny amount of amorphous carbon can also be detected.
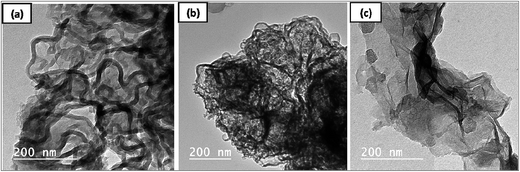 |
| Fig. 3 HR-TEM images for CNTs growth on Fe–Ni/ZX-M (a) Fe–Ni/ZX-N (b) and Fe–Ni/Z-T25 (c) at 850 °C within 30 min. | |
Moreover, the TEM image of CNTs derived from CVD of released hydrocarbon gases of NBR/SBR scrap rubber over Fe–Ni/ZX-N at 850 °C for 30 min is shown in Fig. 3b. Straight, dense rope-like CNTs are grown on the surface of the dark catalyst clusters and characterized by uniform diameters of 12–15 nm, which is almost in the same range as that for the CNTs obtained onto Fe–Ni/ZX-M. The difference in shape of CNTs might be attributed to the higher crystallinity of ZX-M, which enhances the catalytic activity of the catalyst Fe–Ni on its surface to produce higher amount of CNTs with well-defined structure as compared to CNTs/ZX-N.
In case of Z-T25, the corresponding TEM image shown in Fig. 3c depicts the formation of low amount of CNTs bundles based on oval-shaped sheets of graphene. This result may be attributed to the catalytic graphitization role of titanium dioxide nanoparticles in presence of nanobimetallic oxides of Fe and Ni that can enhance the graphitization degree during the CVD process. Thereby, it can be concluded that the prepared catalyst (containing Ti, Fe and Ni) can be used as a template for the synthesis of 3D network comprising CNTs–graphene hybrid nanomaterials.29 Nevertheless, it could not be possible to decide whether the produced CNTs are single- or double-walled from the TEM images.
Comparing with the system of Yang et al.,8 our system provides more advantages as it gives rise to much higher yield of CNTs from lower amount of the scrap rubber, even so of the complications in the structure of the blend used in the current work.
3.4. Raman spectra of the prepared CNTs
Micro-Raman spectroscopy is frequently used to estimate the type and quality of CNTs. This technique gives details about the configuration of CNTs: number of walls, the presence of crystalline and amorphous carbon in addition to the possibility to determine the diameter of the produced CNTs.
Fig. 4 refers to the Raman spectra of the accumulated CNTs on the prepared catalysts to investigate their identity. Two main bands can be recognized in all cases, namely, G-bands at 1563, 1594, and 1585 cm−1, respectively. These peaks belong to tangential C–C stretching mode in a graphite layer.18 Additional D-bands were detected at 1364, 1332, and 1325 cm−1, respectively, and correspond to vibration of carbon atoms with dangling bonds in plane terminations of disordered graphite or amorphous carbon.18 The higher intensity of the G-band as compared to the D-band in all cases translates into limited extent of defects in the structure of the resulting CNTs thus it is suggested that the formed CNTs are rather single-walled, which is in accordance with the flexibility exhibited by the tubes as shown in the TEM images (Fig. 3). Further specific indication for formation SWCNTs, the Raman spectrum of CNTs/ZX-M involves peaks of radial breathing mode (RBM) from 100 to 500 cm−1 (e.g. 106 cm−1, 153 cm−1, 189 cm−1, 313 cm−1, 413 cm−1 and 459 cm−1), while in case of CNTs/ZX-N, only one RBM peak appeared at 141 cm−1. According to these peaks, the diameter distribution of SWCNTs can be estimated from the following equation: d (nm) = 284 (cm−1 nm)/ω (cm−1).30 The corresponding diameters were found to be 2.68 nm, 1.86 nm, 1.50 nm, 0.91 nm, 0.69 nm and 0.62 nm for CNTs/ZX-M, and 2.01 nm for CNTs/ZX-N. This diameters range illustrates the usefulness of the produced metallic elements of SWCNTs for applications such as electrical conductivity and photovoltaics. However, the RBM peaks could not be detected in the Raman spectrum of CNTs/Z-T25 which composed mostly of graphene sheets as stated before (Fig. 3).
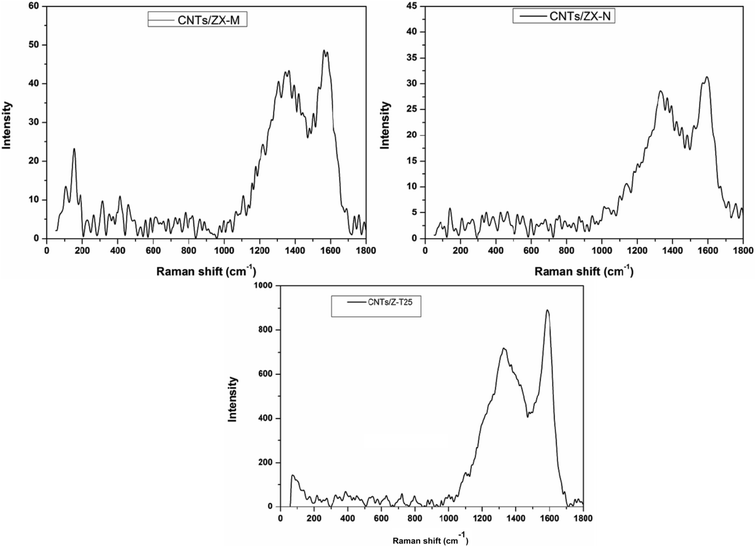 |
| Fig. 4 Raman spectra of CNTs grown on different catalyst systems of Fe–Ni/ZX-M, Fe–Ni/ZX-N and Z-T25. | |
3.5. Thermal properties of the prepared catalysts and CNTs
The percentage and quality of the deposited carbon on the catalyst was estimated from thermal gravimetric runs performed for the products under nitrogen atmosphere in the range room temperature to 800 °C as displayed in Fig. 5. The encountered weight loss in case of the supported catalysts is attributed to a residual solvent from the impregnation process during catalyst fixation on the support. On the other hand, it can be implied from the thermal traces of the CNTs that the moisture and amorphous carbon liberated off steadily at ambient temperature and continued onward up to 400 °C, where the weight loss at this stage reached 5% for Fe–Ni/ZX-N and 14% for Fe–Ni/ZX-M. The decomposition in the range 400–600 °C belongs to the produced CNTs. At this stage the weight loss reached about additional 20% for Fe–Ni/ZX-N and 35% for Fe–Ni/ZX-M. No degradation was experienced any longer beyond 600 °C which ensures the absence of any graphene based structures and that the yield of the produced CNTs is 72% with respect to the weight of Fe–Ni/ZX-M. The thermogram of the CNTs grown on Fe–Ni/ZX-N was similar but it can be noticed a collapse in the percentage of the amorphous carbon to very low level (less than 5%). However, the estimated yield of CNTs was 27% based on the weight of the catalyst Fe–Ni/ZX-N. Accordingly, Fe–Ni/ZX-M is considered more efficient as compared to Fe–Ni/ZX-N in the production of CNTs.
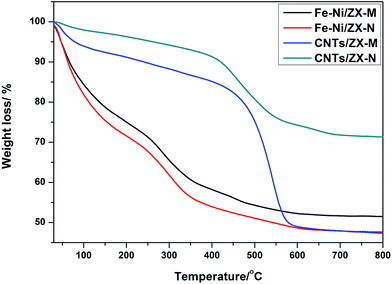 |
| Fig. 5 TGA profiles of zeolite based catalyst systems; Fe–Ni/ZX-M, Fe–Ni/ZX-N and the as-prepared carbon nanotubes. | |
4. Conclusions
Pyrolysis of compatibilized NBR-SBR blend under controlled and optimized conditions can overcome the enhanced heat resistance of the blend and lead to high content of light hydrocarbons being released. This can be considered as a good means for recycling of scrap rubbers at the end of their service period. The liberated hydrocarbon fractions can be exploited, via thermal chemical vapor deposition at 850 °C on suitable catalytic systems, such as bimetallic oxides of Fe and Ni supported on zeolites, for the production of carbon nanotubes bearing different morphologies in high yield. The catalyst supports play an important role in determining the morphology and yield of the produced CNTs.
References
- H. Huang and L. Tang, Pyrolysis treatment of waste tyre powder in a capacitively coupled RF plasma reactor, Energy Convers. Manage., 2009, 50, 611–617 CrossRef CAS.
- M. Massarotto, J. S. Crespo, A. J. Zattera and M. Zeni, Characterization of Ground SBR Scraps from Shoe Industry, Mater. Res., 2008, 11, 81–84 CrossRef CAS.
- C. Berrueco, E. Esperanza and F. J. Mastral, Pyrolysis of waste tyres in an atmospheric static-bed batch reactor: analysis of the gases obtained, J. Anal. Appl. Pyrolysis, 2005, 74, 245–253 CrossRef CAS.
- J. P. Tessonnier, D. Rosenthal, T. W. Hansen, C. Hess, M. E. Schuster and R. Blume, Analysis of the structure and chemical properties of some commercial carbon nanostructures, Carbon, 2009, 47, 1779–1798 CrossRef CAS.
- S. Murugan, M. C. Ramaswamy and G. Nagarajan, The use of tyre pyrolysis oil in diesel engines, Waste Manag., 2008, 28, 2743–2749 CrossRef CAS PubMed.
- H. A. Essawy, M. E. Tawfik and S. H. El-Sabbagh, Rubber nanocomposites based on compatibilized NBR/SBR blends using a series of amphiphilic montmorillonites, J. Elastomers Plast., 2014, 46, 113–131 CrossRef CAS.
- M. E. Tawfik, S. H. El-Sabbagh, H. A. Essawy, N. A. Fathy and A. A. Attia, NBR/SBR blends compatibilized with amphiphilic montmorillonites: pyrolytic degradation of their disposals as cheap carbon rich sources for fabrication of carbon nanotubes via chemical vapor deposition, KGK, Kautsch. Gummi Kunstst., 2016, 7–8, 30–35 Search PubMed.
- W. Yang, W. J. Sun, W. Chu, C. F. Jiang and J. Wen, Synthesis of carbon nanotubes using scrap rubber tyre as carbon source, Chin. Chem. Lett., 2012, 23, 363–366 CrossRef CAS.
- S. Cui, P. Scharff, C. Siegmund, D. Schneider, K. Risch and S. Klotzer, Investigation on preparation of multiwalled carbon nanotubes by DC arc discharge under N2 atmosphere, Carbon, 2004, 42, 931–939 CrossRef CAS.
- B. C. Liu, T. J. Lee, S. H. Lee, C. Y. Park and C. J. Lee, Large-scale synthesis of high-purity well-aligned carbon nanotubes using pyrolysis of iron(II) phthalocyanine and acetylene, Chem. Phys. Lett., 2003, 377, 55–59 CrossRef CAS.
- T. F. Kuo, C. C. Chi and I. N. Lin, Synthesis of carbon nanotubes by laser ablation of graphites at room temperature, Jpn. J. Appl. Phys., 2001, 40, 7147–7150 CrossRef CAS.
- M. Chhowalla, K. Teo, C. Ducati, N. L. Rupesinghe, G. Amaratunga and A. C. Ferrari, Growth process conditions of vertically aligned carbon nanotubes using plasma enhanced chemical vapor deposition, J. Appl. Phys., 2001, 90, 5308–5317 CrossRef CAS.
- N. K. Reddy, J. L. Meunier and S. Coulombe, Growth of carbon nanotubes directly on a nickel surface by thermal CVD, Mater. Lett., 2006, 60, 3761–3765 CrossRef CAS.
- J. F. Colomer, G. Bister, I. Willems, Z. Konya, A. Fonseca, G. Van Tendeloob and J. B. Nagy, Synthesis of single-wall carbon nanotubes by catalytic decomposition of hydrocarbons, Chem. Commun., 1999, 1, 1343–1344 RSC.
- H. Qi, C. Qian and J. Liu, Synthesis of high-purity few-walled carbon nanotubes from ethanol/methanol mixture, Chem. Mater., 2006, 18, 5691–5695 CrossRef CAS.
- X. Chen, H. Wang and J. He, Synthesis of carbon nanotubes and nanospheres with controlled morphology using different catalyst precursors, Nanotechnology, 2008, 19, 1–6 CAS.
- Q. Kong and J. Zhang, Synthesis of straight and helical carbon nanotubes from catalytic pyrolysis of polyethylene, Polym. Degrad. Stab., 2007, 92, 2005–2010 CrossRef CAS.
- Z. Jiang, R. Song, W. Bi, J. Lu and T. Tang, Polypropylene as a carbon source for the synthesis of multi-walled carbon nanotubes via catalytic combustion, Carbon, 2007, 45, 449–458 CrossRef CAS.
- J. Zhang, J. Li, J. Cao and Y. Qian, Synthesis and characterization of larger diameter carbon nanotubes from catalytic pyrolysis of polypropylene, Mater. Lett., 2008, 62, 1839–1842 CrossRef CAS.
- T. Tang, X. Chen, X. Meng, H. Chen and Y. Ding, Synthesis of multi-walled carbon nanotubes by catalytic combustion of polypropylene, Angew. Chem., Int. Ed., 2005, 44, 1517–1520 CrossRef CAS PubMed.
- C. Zhou, B. Hall, H. Richter and Y. Levendis, Synthesis of carbon nanotubes by sequential pyrolysis and combustion of polyethylene, Carbon, 2010, 48, 4024–4034 CrossRef.
- H. Ago, K. Nakamura, N. Uehara and M. Tsuji, Roles of metal-support interaction in growth of single- and double-walled carbon nanotubes studied with diameter-controlled iron particles supported on MgO, J. Phys. Chem. B, 2004, 108, 18908–18915 CrossRef CAS.
- M. Kumar and Y. Ando, Controlling the diameter distribution of carbon nanotubes grown from camphor on a zeolite support, Carbon, 2005, 43, 533–540 CrossRef CAS.
- A. A. Azira, N. F. A. Zainal, T. Soga, S. Abdullah and M. Rusop, Efficient synthesis of carbon nanotubes over zeolites by thermal chemical vapor deposition, AIP Conf. Proc., 2008, 1017, 164–168 CrossRef CAS.
- Z. Y. Juanga, I. P. Chienb, J. F. Laib, T. S. Laib and C. H. Tsaia, The effects of ammonia on the growth of large-scale patterned aligned carbon nanotubes using thermal chemical vapor deposition method, Diamond Relat. Mater., 2004, 13, 1203–1209 CrossRef.
- T. Yamamoto, K. Watanabe and E. R. Hernandez, Mechanical properties, thermal stability and heat transport in carbon nanotubes, Carbon nanotubes: advanced topics in the synthesis, structure, properties and applications, 2008, vol. 111, pp. 165–194 Search PubMed.
- P. Avouris and R. Martel, Progress in carbon nanotube electronics and photonics, MRS Bull., 2010, 35, 306–313 CrossRef CAS.
- N. Ismail, H. Abd El-Maksod and H. Ezzat, Synthesis and characterization of titanosilicates from white sand silica and its hydrogen uptake, Int. J. Hydrogen Energy, 2010, 35, 10359–10365 CrossRef CAS.
- S. Woo, Y.-R. Kim, T. D. Chung, Y. Piao and H. Kim, Synthesis of a graphene–carbon nanotube composite and its electrochemical sensing of hydrogen peroxide, Electrochim. Acta, 2012, 59, 509–514 CrossRef CAS.
- M. S. Dresselhaus, G. Dresselhaus, R. Saito and A. Jorio, Raman spectroscopy of carbon nanotubes, Phys. Rep., 2005, 409, 47–99 CrossRef.
|
This journal is © The Royal Society of Chemistry 2017 |
Click here to see how this site uses Cookies. View our privacy policy here.