DOI:
10.1039/C7RA00014F
(Paper)
RSC Adv., 2017,
7, 9567-9572
Cupric oxide nanowires on three-dimensional copper foam for application in click reaction†
Received
1st January 2017
, Accepted 27th January 2017
First published on 1st February 2017
Abstract
Readily prepared CuO nanowires (CuO NWs) have been found to be effective heterogeneous catalysts for the 1,3-dipolar cycloaddition (CuAAC) reaction without using any additional support and bases. Examination of CuO nanowire catalysts synthesized at various temperatures showed that the use of CuO-600 catalyst was the best choice for the success of the present click reaction. Not only aromatic and heteroaromatic alkynes but also alkylalkynes were catalyzed regioselectively, affording triazoles in excellent yields. Furthermore, we have identified that the reaction proceeded in a heterogeneous manner. It is noteworthy that the CuO-600 catalyst can be easily recovered and reused nine times.
Introduction
1,2,3-Triazoles are one of the most vital class of N-containing heterocyclic compounds that have received a much attention, not only as biological active drugs but also as functional materials.1–9 In addition, these compounds are attracting much attention mainly due to the fact that they are used in numerous fields, such as organic semiconductors, dyes, dehydroannulenes, and electroluminescent materials.10–21 Due to their intrinsic importance, many methodologies have been developed for the preparation of 1,2,3-triazoles. Among them, Huisgen's 1,3-dipolar cycloaddition reaction of terminal alkynes and organic azides, catalysed by homogeneous CuI salts (CuAAC), was reported independently by Sharpless22 and Meldal23 (the so-called click reaction), which is known as one of the most efficient synthetic application tools in organic synthesis due to its 100% atom economy, mild reaction conditions, wide substrate scope and exclusive regioselectivity in the formation of the 1,4-disubstituted 1,2,3-triazoles. The click reaction can be catalysed also by heterogeneous copper, which strategy is immobilization of copper nanoparticles onto various heterogeneous organic and inorganic supports.24–28 However, copper metal alone catalysed this click reaction is relatively slow and requires high catalyst loading with bases. Recently, Jin and co-workers developed an interesting monolithic nanoporous Cu catalysts, which nanoporosity structure of Cu surface led to a significant enhancement of catalytic activity in click chemistry without using any additional supports and bases.29,30 Therefore, design of nanostructure on the surface of monolithic copper is not only feasible for development of high catalytic activity catalysts application in click chemistry but also simplified for recovery of catalyst project.
Cupric oxide (CuO) are promising materials for gas sensors, heterogeneous catalysts, photovoltaics, infrared detectors, field emission emitters and lithium ion electrodes applications due to their unique properties such as direct band gap (1.2–1.7 eV), non-toxicity, chemical stability, abundant availability and low production cost.31–38 To date, most of the ways used to generate CuO nanowires (CuO NWs) are physical and chemical routes, for instance, precursor methods, hydrothermal reaction, anodization, electrospinning, and seed-mediated growth solution.39–43 Compared with these methods, the formation of CuO NWs by direct thermal oxidation of Cu has been recently given considerable attention due to its simplicity and large-scale growth.44 Herein, we report an efficient approach for the synthesis of CuO NW and its remarkable catalytic properties in click chemistry without using any additional supports and bases. To the best of our knowledge, this is the first report on a monolithic CuO NWs catalysed organic molecular transformation.
Experimental
General information
All the chemicals are used as received without further purification: foam Cu, porosity ≥ 98%, purity ≥ 99, PPI = 110, thickness = 1.5 mm, bulk density = 0.4–0.6 g cm−3, average pore size = 200–300 μm (Kunshan desco electronics Co., Ltd); benzyl azide (Aladdin Industrial Corporation); the terminal alkyne, benzyl bromide (J&K Chemical); sodium azide (Micxy Reagent); t-BuOH, toluene, hexane, THF, HCl (Beijing Chemical Works). Deionized water was used in this study.
Synthesis of CuO NWs
In a typical procedure, a 3D CuO NWs network can be facile prepared by one step thermal oxidation of Cu foam in air. The Cu foam substrate was cleaned in an aqueous 1.0 M HCl solution for about 20 s, followed by repeated rinsing with distilled water. After it had been dried under a nitrogen gas flow, the Cu foam was placed in an alumina boat and immediately heated to the set-point temperature at ambient pressure in an oven and annealed in air for 4 hours. The growth process was accompanied with a change of colour from reddish to black, indicating the forming of CuO NWs. We have tested a number of temperatures: 400, 500, 600 and 700 °C, and the respective materials called CuO-n, (n = 400, 500, 600, 700).
Characterization
X-ray diffraction (XRD, Bruker D8 Advance Germany) was applied to characterize the crystal structure of the hybrid materials, and the data were collected on a Shimadzu XD-3A diffractometer using Cu Kα radiation. The X-ray photoelectron spectroscopy (XPS, Thermo Fisher K-Alpha American with an Al K α X-ray source) was used to measure the elemental composition of samples. Transmission electron microscopy (TEM, Tecnai G2, F20) combined with an energy dispersive X-ray spectroscopy (EDS) at an acceleration voltage of 200 kV were used to measure the size, morphology, size distribution and element content of nanoparticles.
Representative procedure for the Cu NWs catalysed click reaction
To a H2O/t-BuOH (0.66 ml/0.33 ml) solution of 2 mg CuO NW (5 mol%, calculated the amount of catalyst basis of CuO) was added phenylacetylene 1a (0.5 mmol, 51 mg) and benzyl azide 2a (0.5 mmol, 67 mg) in a V-shaped reactor vial. The reaction mixture was stirred at room temperature for 12 h by using a bulky round-shaped magnetic stirring bar. After consumption of 1a and 2a which were monitored by TLC, the CuO NWs was picked out of the reaction mixture by tweezers. The recovered CuO NWs catalyst was washed with acetone and dried under vacuum to use for the next run. After concentrated of the filtrate, the white solid was purified via short silica gel chromatography by using a 3
:
1 mixture of hexane and ethyl acetate as an eluent, to afford 1-benzyl-4-phenyl-1H-1,2,3-triazole 3a as a white solid, yield: 116 mg (99%).
Results and discussion
High-density CuO NWs were first grown by heating copper foam substrate in air for 4 h at a suitable range of temperature (400 °C, 500 °C, 600 °C, 700 °C), and the respective materials called CuO-n, (n = 400, 500, 600, 700). The morphology and structure of all CuO-n catalysts have been examined by scanning electron microscopy (SEM) (Fig. 1). For the Cu foam, the crack on the surface of the skeleton with 3D structure was distinctly observed as seen in Fig. 1a and b. When the Cu foam heated at 400 °C for 4 h in air, only the sparse nanowires related to CuO were formed on the surface of Cu foam (Fig. 1c and d). It was quite obvious that CuO NWs of CuO-500 were formed denser than that of CuO-400 (Fig. 1e and f). While the growth temperature enhanced to 600 °C, the density and length of CuO NWs were perfectly formed compared with CuO-400 and CuO-500 samples (Fig. 1g and h). When the temperature was higher than 700 °C, no CuO NWs were found and the growth of CuO NWs will be terminated, which is due to the free energy of CuO changes from negative to positive state,38 as seen in Fig. 1i and j.
 |
| Fig. 1 SEM images of (a and b) Cu foam, (c and d) CuO-400, (e and f) CuO-500, (g and h) CuO-600, (i and j) CuO-700. | |
XRD is a useful method to characterize the crystal structure of these catalysts, and the crystal information of CuO-400, CuO-500, CuO-600 and CuO-700 are shown in Fig. 2. The characterized peaks locate at 2θ value of 43.5° and 50.6° were corresponding to the metal Cu (JCPDS PDF#85-1326). The characterized peaks locate at 2θ value of 36.6°, 42.5°, 61.6° and 74.2° were attributed to the Cu2O (JCPDS PDF#73-2076). The peaks locate at 2θ value of 32.7°, 35.7°, 38.9°, 48.9°, 53.7°, 58.4°, 66.5° and 68.2° correspond to the CuO (JCPDS PDF#80-1917). It was obvious to observe that the CuO-n were a mixture of Cu2O, CuO and metal Cu skeleton. Moreover, the Cu characterized peaks were disappeared and the Cu2O characterized peaks were reduced along with the temperature increasing, which were in accordance with the two steps growth mechanism of CuO NWs: the first one is forming of a Cu2O layer on the surface of copper, and then CuO NWs were subsequently grown on the Cu2O layer.44–46
 |
| Fig. 2 The XRD patterns of CuO-400, CuO-500, CuO-600 and CuO-700. | |
The chemical composition and electronic structure of the CuO NWs were investigated by XPS. Fig. 3 depicts a high sensitivity scan with the presence of Cu and O elements. No other obvious impurities were found in the spectrum expect low-intensity peak of carbon, which might result from the surface contamination. The Cu 2p peak of CuO nanostructures was illustrated in detail in Fig. 2b. The Cu 2p3/2 lies at 933.9 eV with a shake-up satellite at about 944 eV and Cu 2p1/2 lies at 953.5 eV with a satellite at about 962.4 eV, which was in good agreement with previously reported.45,47 The bonding energy gap between Cu 2p1/2 and Cu 2p3/2 was about 20 eV, which was in agreement with the standard spectrum of CuO. The O 1s peak for CuO and Cu2O was at 530 eV and Cu2O was at 531.8 eV (Fig. S1†), respectively.
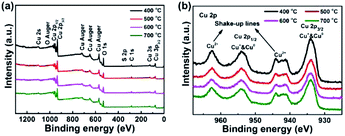 |
| Fig. 3 XPS survey of CuO-n samples (a). Cu 2p scans of CuO-n (b). | |
The catalytic activities of various fabricated CuO-n samples were examined in the click reaction of phenylacetylene (1a) and benzyl azide (2a) in H2O at room temperature without using any additional supports and bases (Table 1). The reactions using CuO-n catalysts with calcination temperature at 400 °C and 500 °C (CuO-400 and CuO-500) gave moderate yields of the corresponding triazole 3a (entries 1 and 2). Surprisingly, the use of CuO-600 afforded 3a in almost quantitative yield (entry 3). The reaction using CuO-700 as catalyst, resulted in a dramatically decreased yield of 3a (entry 4). However, Cu foam was inactive as a catalyst in current click reaction system (entry 5). These results indicated that the annealing temperature has a strong influence on catalytic activity in the click reaction. The remarkable difference catalytic activities are possibly ascribed to the different morphology, density and surface component of CuO NWs. Although, it can be found that the CuO component is increased along with the temperature increasing in our XRD results. It is hard to say which kind of Cu species (Cu2O and CuO) mainly affect the catalytic activity in current stage, due to the fact that both the morphology and density of the CuO NWs are also influential factors. Can be ascribed to the formation morphology of the CuO NWs on the Cu foam. In order to determine the solvent system most suitable for the catalyst, several experiments were conducted. Quantitative yield was obtained with a solvent mixture of t-BuOH and H2O (2
:
1) (entry 6). The reactions were carried out in different solvents including toluene, hexane and THF, no better results were obtained compared with the mixture solvent of t-BuOH and H2O. These results indicated that solubility and hygroscopic properties are all important factors for CuO-600 catalysis of click reactions.48
Table 1 Click reaction under different conditionsa
The scope extension of the protocol to other alkynes and benzyl azide was also investigated under the previously optimized reaction conditions (Table 2). Phenyl acetylenes with electron-donating and electron-withdrawing groups such as 1-ethynyl-4-methylbenzene, 1-ethynyl-4-methoxybenzene and 1-chloro-4-ethynylbenzene reacted readily with benzyl azide. The corresponding triazoles 3b–3d were obtained in high yields (entries 1–3). Heteroaromatic alkynes also gave the expected adducts 3e and 3f as single regioisomers in high yields (entries 4 and 5). Hydroxy-substituted alkynes such as propargyl alcohol and pent-4-yn-1-ol also gave the expected adducts (1-benzyltriazol-4-yl) methanol 1g and 3-(1-benzyl-1H-1,2,3-triazol-4-yl)propan-1-ol 1h as single regioisomers in good to high yields (entries 6 and 7). While acetylenes conjugated with an ester group such as phenyl propargyl ether and aliphatic alkynes such as hex-1-yne and ethynylcyclohexane react with benzyl azide produced the corresponding product with excellent yields (entries 8–10). The reaction with alkynes containing electron-withdrawing substituents and trimethyl silanes gave high yields (entries 11 and 12). These results illustrated that not only aromatic and heteroaromatic alkynes but also alkylalkynes were catalyzed regioselectively, affording triazoles in excellent yields.
Table 2 Click reaction of benzyl azide with terminal alkynes in the presence of CuO-600a
Under neat conditions, the catalytic loading can be decreased to 1 mol% without any significant influence on the reaction efficiency on the reaction temperature at 65 °C. As known to all, the CuO NWs are formed on the surface of the Cu surface and the role of Cu foam is to support the CuO NWs catalytic species rather than the click reaction catalyst eqn (1). Hence, we picked off the CuO NWs by ultrasonic in ethanol solution, finding that no more than 20 wt% of the CuO NWs were existed in CuO-600 catalyst. The TON value for the CuO-600 can be reached as high as 495 in current click reaction system. In comparison with other Cu catalysts reported recently (Table S1†), it is obvious that the CuO-600 catalyst demonstrates superior or comparable catalytic activity. It is worthy to mention that, the recyclability, separation and fabrication of CuO-600 are much more advantageous than these Cu catalysts for practical applications. Moreover, the CuO-600 catalyst demonstrated to be very efficient in the multi-component 1,3-dipolar cycloaddition of phenyl acetylene and benzyl azide yielded in situ from sodium azide and benzyl bromide, affording 1,2,3-triazoles 3a in excellent yield eqn (2).
|
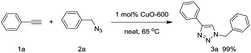 | (1) |
|
 | (2) |
The reusability is the most important feature of a heterogeneous catalyst, which is superior to a homogenous one. First, to confirm the reaction indeed catalysed by CuO-600 rather than by homogenous CuO species, we have carried out the following leaching experiments as shown in eqn (3). After the catalytic click reaction of 1a and 2a was carried out for 4 h under the standard conditions, the CuO-600 catalyst was removed from the vessel by tweezers with 3a produced in 55% yield at this time. No further reaction were took place after removing the catalyst, the CuO-600 catalyst was then put back into the mixture. As a result, the click reaction was restarted, and production 3a was obtained in 99% yield in 8 h. To assess recyclability of CuO-600 catalyst, multiple phenyl acetylene 1a and benzyl azide 1b click reactions were carried out, the recovery of the heterogeneous catalyst was carried out by tweezers for the separation of the catalyst from the reaction mixture. It was found that the catalytic activity was slightly reduced after the catalyst repetition four times at room temperature. The yield of 3a can be improved by increasing the reaction temperature to 45 °C. When the reaction temperature enhanced to 65 °C, the catalyst can be further recycled four times with producing 3a excellent yield every time (Fig. 4a). After reaction, the catalyst was again examined by SEM, and the image indicated that the CuO NWs were covered by some organic compounds and some of NWs were broke (Fig. 4b). However, the CuO NWs crystal structure were not changed dramatically as shown in Fig. S3,† which revealed that the CuO NWs was not transformed after the recycle test.
|
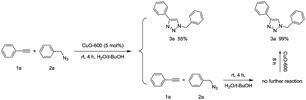 | (3) |
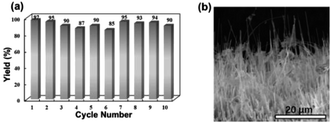 |
| Fig. 4 The yields for 10 cycles of CuO-600 catalysed click reaction (a), and SEM image of Pd-3 catalyst after 10 cycles (b). | |
Conclusions
In summary, CuO NWs can be synthesized by thermal oxidation of 3D Cu foam in air at different temperatures. Among all of the as-prepared catalysts, CuO-600 exhibits superior catalytic activity for 1,3-dipolar cycloaddition of phenyl acetylene and benzyl azide without using any additional supports and bases compared with CuO-400, CuO-500 and CuO-700 catalysts. A wide range of functional groups on terminal alkyne were tolerated, affording the corresponding substituted 1,2,3-triazole in good to high yields with a sole selectivity. Moreover, leaching experiment revealed that the click reaction occurred by heterogeneous way, and the CuO-600 catalyst can be effective reused nine times. Further work is in progress to extend such kind of catalyst for other applications.
Acknowledgements
We gratefully thank for the National Natural Science Foundation of China (No. 21576289), the Science Foundation of China University of Petroleum, Beijing (No. 2462015YQ0306, 2462016YJRC027, 2462014QZDX01 and C201603), Thousand Talents Program and National High-tech R&D Program of China (863 Program, No. 2015AA034603).
References
- R. Manetsch, A. Krasiski, Z. Radi, J. Raushel, P. Taylor, K. B. Sharpless and H. C. Kolb, J. Am. Chem. Soc., 2004, 126, 12809–12818 CrossRef CAS PubMed.
- G. C. Tron, T. Pirali, R. A. Billington, P. L. Canonico, G. orba and A. A. Genazzani, Med. Res. Rev., 2008, 28, 278–308 CrossRef CAS PubMed.
- Y. M. A. Yamada, A. hno, T. Sato and Y. Uozumi, Chem.–Eur. J., 2015, 21, 17269–17273 CrossRef CAS PubMed.
- H. Nandivada, X. W. Jiang and J. Lahann, Adv. Mater., 2007, 19, 2197–2208 CrossRef CAS.
- P. Wu, A. K. Feldman, A. K. Nugent, C. J. Hawker, A. Scheel, B. Voit, J. Pyun, J. M. J. Fréchet, K. B. Sharpless and V. V. Fokin, Angew. Chem., Int. Ed., 2004, 43, 3928–3932 CrossRef CAS PubMed.
- V. Aucagne, K. D. Hanni, D. A. Leigh, P. J. Lusby and D. B. alker, J. Am. Chem. Soc., 2006, 128, 2186–2187 CrossRef CAS PubMed.
- D. Astruc, R. Ciganda, C. Deraedt, S. atard, L. Liang, N. Li, C. Ornelas, A. Rapakousiou, J. Ruiz, D. Wang, Y. Wang and P. Zhao, Synlett, 2015, 26, 1437–1449 CrossRef CAS.
- D. Huang, P. Zhao and D. Astruc, Coord. Chem. Rev., 2014, 272, 145–165 CrossRef CAS.
- F. Alonso, Y. Moglie and G. Radivoy, Acc. Chem. Res., 2015, 48, 2516–2528 CrossRef CAS PubMed.
- G. P. Ellis and T. M. Romney Alexandar, Chem. Rev., 1987, 87, 779–794 CrossRef CAS.
- K. Mori, K. Yamaguchi, T. Mizugaki, K. Ebitani and K. Kaneda, Chem. Commun., 2001, 461–462 RSC.
- K. Yamaguchi and N. Mizuno, Angew. Chem., Int. Ed., 2003, 42, 1480–1483 CrossRef CAS PubMed.
- M. Kotani, T. Koike, K. Yamaguchi and N. Mizuno, Green Chem., 2006, 8, 735–741 RSC.
- F. Li, J. Chen, Q. Zhang and Y. Wang, Green Chem., 2008, 10, 553–562 RSC.
- Y. Zhang, K. Xu, X. Chen, T. Hu, Y. Yu, J. Zhang and J. Hung, Catal. Commun., 2010, 11, 951–954 CrossRef CAS.
- M. L. Mihailovic, A. Stojiljikovic and V. Andrewjevic, Tetrahedron Lett., 1965, 6, 461–464 CrossRef.
- T. Kajimoto, H. Takahashi and J. Tsuji, J. Org. Chem., 1976, 41, 1389–1393 CrossRef CAS.
- P. Capdevielle, A. Lavigne, D. Sparfel, J. Baranne-Lafont, K. C. Ngyuen and M. Maumy, Tetrahedron Lett., 1990, 31, 3305–3308 CrossRef CAS.
- R. Tang, S. E. Diamond, N. Neary and F. Marks, J. Chem. Soc., Chem. Commun., 1978, 562 RSC.
- F. Porta, C. Crotti and S. Cennini, J. Mol. Catal., 1989, 50, 333–341 CrossRef CAS.
- Y. Maeda, T. Nishimura and S. Uemura, Bull. Chem. Soc. Jpn., 2003, 76, 2399–2403 CrossRef CAS.
- V. V. Rostovtsev, L. G. Green, V. V. Fokin and K. B. Sharpless, Angew. Chem., 2002, 114, 2708–2711 CrossRef.
- C. W. Tornøe, C. Christensen and M. Meldal, J. Org. Chem., 2002, 67, 3057–3062 CrossRef.
- M. Gholinejad and N. Jeddi, ACS Sustainable Chem. Eng., 2014, 2, 2658–2665 CrossRef CAS.
- S. Mohammed, A. K. Padala, B. A. Dar, B. Singh, B. Sreedhar, R. A. Vishwakarma and S. Bharate, Tetrahedron, 2012, 68, 8156–8162 CrossRef CAS.
- B. S. P. Anil Kumar, K. Harsha Vardhan Reddy, K. Karnakar, G. Satish and Y. V. D. Nageswar, Tetrahedron Lett., 2015, 56, 1968–1972 CrossRef CAS.
- B. B. Lai, Z. P. Huang, Z. F. Jia, R. X. Bai and Y. L. Gu, Catal. Sci. Technol., 2016, 6, 1810–1820 CAS.
- A. S. Nia, S. Ran, D. Döhler, X. Noirfalise, A. Belfiore and W. H. Binder, Chem. Commun., 2014, 50, 15374–15377 RSC.
- T. N. Jin, M. Yan, Menggenbateer, T. Minato, M. Bao and Y. Yamamoto, Adv. Synth. Catal., 2011, 353, 3095–3100 CrossRef CAS.
- T. N. Jin, M. Yan and Y. Yamamoto, ChemCatChem, 2012, 4, 1217–1229 CrossRef CAS.
- G. Avgouropoulos, T. Ioannides and H. Matralis, Appl. Catal., B, 2005, 56, 87–93 CrossRef CAS.
- K. T. Liao, P. Shimpi and P. X. Gao, J. Mater. Chem., 2011, 21, 9564–9569 RSC.
- G. Avgouropoulos and T. Ioannides, Chem. Eng. J., 2011, 176, 14–21 CrossRef.
- A. Aslani and V. Oroojpour, Phys. B, 2011, 406, 144–149 CrossRef CAS.
- P. Shao, S. Deng, J. Chen and N. Xu, Chin. Sci. Bull., 2011, 56, 906–911 CrossRef CAS.
- J. Huang, Y. Zhu, X. Yang, W. Chen, Y. Zhou and C. Li, Nanoscale, 2015, 7, 559–569 RSC.
- P. J. Ni, Y. J. Sun, Y. Shi, H. C. Dai, J. T. Hu, Y. L. Wang and Z. Li, RSC Adv., 2014, 4, 28842–28847 RSC.
- L. Q. Zhang, Z. F. Gao, C. Liu, L. Ren, Z. Q. Tu, R. Liu, F. Yang, Y. H. Zhang, Z. Z. Ye, Y. F Li and L. S. Cui, RSC Adv., 2014, 4, 47455–47460 RSC.
- C. K. Xu, Y. K. Liu, G. D. Xu and G. H. Wang, Mater. Res. Bull., 2002, 37, 2365–2372 CrossRef CAS.
- H. M. Xiao, S. Y. Fu, L. P. Zhu, Y. Q. Li and G. Yang, Eur. J. Inorg. Chem., 2007, 2007, 1966–1971 CrossRef.
- X. F. Wu, H. Bai, J. X. Zhang, F. E. Chen and G. Q. Shi, J. Phys. Chem. B, 2005, 109, 22836–22842 CrossRef CAS PubMed.
- H. Wu, D. D. Lin and W. Pan, Appl. Phys. Lett., 2006, 89, 133125 CrossRef.
- A. A. Umar and M. Oyama, Cryst. Growth Des., 2007, 7, 2404–2409 CAS.
- X. C. Jiang, T. Herricks and Y. N. Xia, Nano Lett., 2002, 2, 1333–1338 CrossRef CAS.
- M. A. Dar, S. H. Nam, Y. S. Kim and W. B. Kim, J. Solid State Electrochem., 2010, 14, 1719–1726 CrossRef CAS.
- J. T. Chen, F. Zhang, J. Wang, G. A. Zhang, B. B. Miao, X. Y. Fan, D. Yan and P. X. Yan, J. Alloys Compd., 2008, 454, 268–273 CrossRef CAS.
- D. Tahir and S. Tougaard, J. Phys.: Condens. Matter, 2012, 24, 175002 CrossRef PubMed.
- J. Y. Kim, J. C. Park, H. Kang, H. Song and K. H. Park, Chem. Commun., 2010, 46, 439–441 RSC.
Footnotes |
† Electronic supplementary information (ESI) available. See DOI: 10.1039/c7ra00014f |
‡ These authors contributed equally to this work. |
|
This journal is © The Royal Society of Chemistry 2017 |
Click here to see how this site uses Cookies. View our privacy policy here.