DOI:
10.1039/C6RA28448E
(Paper)
RSC Adv., 2017,
7, 12805-12811
Trifluoromethanesulfonic acid-based DESs as extractants and catalysts for removal of DBT from model oil
Received
20th December 2016
, Accepted 10th February 2017
First published on 23rd February 2017
Abstract
A series of deep eutectic solvents (DESs) of ChCl/XCF3SO3H (X from 1.0 to 2.0) were synthesized by stirring a mixture of choline chloride (ChCl) and trifluoromethanesulfonic acid (CF3SO3H) at room temperature. The DESs were characterized by Fourier transform infrared (FT-IR) and 1H nuclear magnetic resonance (1H NMR). The oxidative desulfurization of model oil was investigated using ChCl/1.5CF3SO3H as a catalyst and extraction agent, and H2O2 as the oxidant. Some reaction parameters such as type of DES, molar ratio of CF3SO3H and ChCl in DESs, H2O2 dose, reaction temperature, DES dose and type of sulfur compound were investigated. Under the optimum conditions, the removal rate of dibenzothiophene (DBT) and 4,6-dimethyldibenzothiophene (4,6-DMDBT) can reach up to 98.65% and 96.8%, respectively. After five recycling runs, the removal rate of DBT can still reach 97.16%.
1 Introduction
SOx emission, which is mainly produced by vehicles, not only pollutes the environment, such as acid rain,1 but also harms the health of humans, such as cancer. In order to decrease the pollution caused by SOx, many countries have laid down a series of rules for restricting the sulfur content of fuel oil. It is an aim to achieve little sulfur in oil (sulfur content < 10 μg g−1).2 The traditional hydrodesulfurization (HDS) process, removing aliphatic and acyclic sulfur compounds, has been considered as a mature technology. However, HDS finds it difficult to remove aromatic sulfur compounds3,4 such as thiophene (TH), benzothiophene (BT) dibenzothiophene (DBT) and their derivatives because of their large steric hindrance. Therefore, some non-hydrodesulfurization processes, such as oxidative desulfurization (ODS),5 biodesulfurization (BDS),6 extractive desulfurization (EDS)7 and adsorption desulfurization (ADS),8 etc., have attracted wide attention.
Among these non-hydrodesulfurization processes, oxidative desulfurization (ODS) was considered as one of the most promising technologies due to its advantages,9 such as the high desulfurization rate and the mild reaction conditions. Various oxidants such as H2O2, NO2, O2, O3, K2FeO4, and organic peroxides have been investigated in the oxidative desulfurization system. Among these oxidants, H2O2 is widely employed due to its high activity and low price.10
In recent years, a Brønsted acid based ionic liquid was used in the oxidative desulfurization process. Fang et al.11 reported the synthesis of 1-butyl-3-methyl-imidazolium trifluoroacetic acid ([C4mim]TFA) ionic liquids and their application in oxidative desulfurization and found that the anion of the ionic liquid has an important influence on the desulfurization rate. Lu et al.12 synthesized 1-methylimidazolium tetrafluoroborate ([HMIm]BF4) ionic liquids and the sulfur removal of DBT in model oil can reach 93% under optimum conditions. Gao et al.13 synthesized an acidic ionic liquid N-butyl-N-methylimidazolium hydrogen sulfate ([BMIm]HSO4), its oxidative desulfurization rate can reach 100% for DBT in model oil. The [BMIm]HSO4 ionic liquid can be recycled 5 times with only a slight reduction in activity. Zhao et al.14 synthesized the Brønsted acid ionic liquid N-methyl-pyrrolidonium tetrafluoroborate ([Hnmp]BF4) and used as the extractant and catalyst for desulfurization (ODS) of model oil. The experimental results indicated that 99.4% sulfur compounds in diesel fuel can be removed. Although these ionic liquids have better desulfurization activity in the oxidative desulfurization system, the raw materials of ionic liquids are expensive and the preparation process is complex.
As a new type of solvent, deep eutectic solvents have attracted great attention because of its excellent physical and chemical properties, which is friendly for environment. DESs are composed of two or more components that interact via intermolecular hydrogen bonds.15 Compared with the traditional ionic liquids, DESs have many advantages such as cheap and easily accessible raw material, a simple preparation process, and wide range of applications.16 In developmental history of DESs, ChCl-based DESs are first reported by Abbott and his co-workers, its physical properties have been researched.17 Thereafter, DESs are used in various fields such as electrochemistry, organic synthesis and separation processes.18–21 DESs also are used in the desulfurization process of fuels. For example, Zhu et al.22 reported the synthesis of ChCl·2CH3COOH and it was used as the extractant of oxidation desulfurization process. The study found that the removal rate of DBT in model oil can up to 98.6% under UV light irradiation. Gano Z. S. et al.23 reported that the FeCl3-based deep eutectic solvents for the extractive desulfurization of liquid fuels. Experimental results show the desulfurization efficiencies of 64% and 44% can be achieved for DBT and thiophene, respectively. Yin et al.24 reported that the synthesis of ChCl/p-TsOH and the desulfurization efficiencies of ChCl/p-TsOH can reach up to 97.25%, which are much higher than those obtained with traditional and functional ionic liquids. Our research group has synthesized phenylpropanoic acid-based DESs and was applied to the oxidation desulfurization process.25 In the synthesis, the acid-based DESs was synthesized by heating method. As is known to all, simpler preparation process and higher acidity of DESs are favorable for the desulfurization.26 Therefore, it is necessary to develop a new DES using a simple preparation method and apply it to the oxidative desulfurization process.
Trifluoromethanesulfonic acid (CF3SO3H) is one of the strongest organic acids, it is widely used in the synthesis reaction. In this work, the novel CF3SO3H-based DESs were synthesized by stirring a mixture of ChCl and CF3SO3H at the room temperature. The removal rate of DBT from model oil was investigated using CF3SO3H-based DESs as an extraction agent and catalyst, H2O2 as the oxidant. The influence of different type DESs, the molar ratio of ChCl to CF3SO3H, the oxygen to sulfur (O/S) molar ratio, the reaction temperature and the amount of DESs on the desulfurization rate was investigated. Under the optimum conditions, the removal rate of dibenzothiophene (DBT) and 4,6-dimethyldibenzothiophene (4,6-DMDBT) can reach up to 98.65% and 96.8%, respectively. After five recycling runs, the removal rate of DBT can still reach 97.16%.
2 Experimental
2.1 Chemical regent and instrument
Dibenzothiophene (DBT, 98%), benzothiophene (BT, 97%), thiophene (TH, 99.8%) and 4,6-dimethyldibenzothiophene (4,6-DMDBT, 97%) were purchased from Aladdin Chemistry Co. Ltd. The choline chloride (ChCl, AR), tetrabutylammonium chloride (TBAC, AR), tetraethylammonium chloride (TEAC, AR), n-octane, carbon tetrachloride (CCl4, 99.5%), trifluoromethanesulfonic acid (CF3SO3H, 98%), and hydrogen peroxide (H2O2, 30 wt%) were purchased from Sinopharm Chemical Reagent Co. Ltd. Gas chromatography was carried out on an Agilent 7890A GC with an FID detector using a 30 m packed HP5 column. Infrared spectra of DBT, oxidation of DBT, DESs and raw materials were determined on Fourier-transform infrared spectrometer (WQF-520; Beijing Beifen Ruili Instrument Company, China). 1H NMR of DESs were determined by using the Mercury Plus 400 MHz spectrometer (Varian Co., Ltd. American).
2.2 Synthesis of ChCl/XCF3SO3H
ChCl/XCF3SO3H was synthesized by stirring a mixing of ChCl and CF3SO3H at room temperature. The specific process is as follows: ChCl was added to a 100 mL round-bottomed flask. Then, the CF3SO3H was carefully added according to a certain molar ratio under stirring conditions. The two raw materials were stirred vigorously for 1 h in order to fully release the reaction heat. After the reaction, the ChCl/XCF3SO3H (X from 1.0 to 2.0) DESs homogeneous liquid was obtained. The reaction was shown in Fig. 1. TBAC/CF3SO3H and TEAC/CF3SO3H were synthesized according to the same method.
 |
| Fig. 1 Synthetic mechanism of DESs. | |
1H NMR spectra of CF3SO3H, ChCl and ChCl/CF3SO3H were obtained on hydrogen spectrum detector. Coupling constants (J1) in Hz and chemical shifts (d) are given in ppm. The multiplicities of signals in 1H NMR are given with chemical shifts (s = singlet, d = doublet, t = triplet, q = quartet, m = multiplet), and the data are listed as follows:
CF3SO3H for 1H NMR (500 MHz, D2O) δ 4.86 (s, 1H).
ChCl for 1H NMR (500 MHz, D2O) δ 4.71 (d, 26H), 4.08 (m, 59H), 3.56–3.46 (m, 39H), 3.25 (s, J = 68.7 Hz, 30H), 3.18 (d, 176H), 3.03 (s, 2H).
ChCl/CF3SO3H for 1H NMR (500 MHz, D2O) δ 4.77 (s, 2H), 3.90 (ddd, J = 7.7, 5.3, 2.8 Hz, 1H), 3.35 (dd, J = 5.8, 4.2 Hz, 1H), 3.04 (s, 5H).
2.3 Desulfurization experiment
The 500 μg g−1 model oil was prepared by dissolving 1.437 g DBT in 500 mL n-octane. The model oil, DESs, and 30 wt% H2O2 were added into a three-necked flask. The mixture was stirred in a water bath at a certain temperature. A small amount of the upper oil phase was removed every 20 min and determined by gas chromatography. The desulfurization rate was calculated using the following formula:
where Stot (500 μg g−1) is the initial concentration of the sulfur compound in the model oil and Sres is the residual concentration of the sulfur compound after the ODS process.
3 Results and discussion
3.1 Characterization
3.1.1 Infrared spectra analysis. The infrared spectra of ChCl, CF3SO3H and ChCl/1.5CF3SO3H were shown in Fig. 2. Compared with the peaks of ChCl and CF3SO3H, the stretching vibration peak of O–H at 3272 cm−1, stretching vibration peak of C–H at 3018 cm−1 and stretching vibration peak of S
O at 1406 cm−1 in ChCl, and stretching vibration peak of F–C at 947 cm−1 and bending vibration peak of F–C at 621 cm−1 in CF3SO3H shift to 3466, 3048, 1416, 960 and 644 cm−1 in ChCl/1.5CF3SO3H were clearly seen (Fig. 2). The peaks happening to shift are attribute to the formation of hydrogen bond in the DES.27
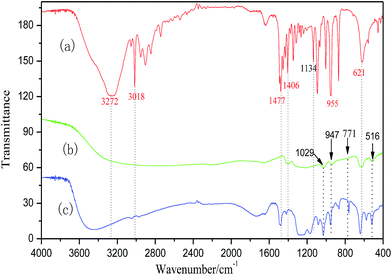 |
| Fig. 2 IR-FT (a) ChCl; (b) CF3SO3H; (c) ChCl/1.5CF3SO3H. | |
3.1.2 1H NMR characterization. In order to further confirm the interactions between ChCl and CF3SO3H, 1H NMR spectra of CF3SO3H, ChCl and DESs were obtained in Fig. 3. The 1H NMR spectra of ChCl/1.5CF3SO3H in Fig. 3(c), the peak of hydrogen bond obviously became stronger and slightly shift to right compare with ChCl in Fig. 3(b). 1H NMR spectra of CF3SO3H demonstrate there is a peak of hydrogen bond in Fig. 3(a). The peak of ChCl labeled “4” and the peak of hydrogen bond in CF3SO3H disappeared and there is a new peak of hydrogen bond appeared in ChCl/1.5CF3SO3H. These results demonstrate that there are formation of hydrogen bond between ChCl and CF3SO3H.22
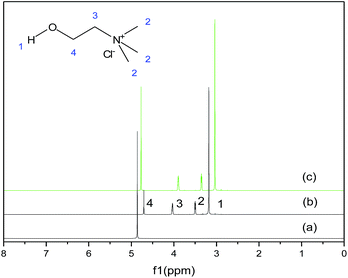 |
| Fig. 3 1H NMR spectra of (a) CF3SO3H; (b) ChCl; (c) ChCl/1.5CF3SO3H. | |
3.2 Oxidative desulfurization reaction conditions
3.2.1 Desulfurization rate of different desulfurization system. In this study, the removal rate of DBT in desulfurization system of ChCl/CF3SO3H, TBAC/CF3SO3H and TEAC/CF3SO3H was investigated. The results are shown in Fig. 4(a). It can be seen from Fig. 4(a), the desulfurization rate of DBT reached 90.58% for ChCl/CF3SO3H, 41.54% for TBAC/CF3SO3H and 85.38% for TEAC/CF3SO3H after the 180 min, respectively. The difference of desulfurization rate may be due to the difference in steric hindrance of DESs. It is well known that the steric hindrance of DESs follow the order TBAC/CF3SO3H > TEAC/CF3SO3H > ChCl/CF3SO3H. The order of desulfurization rate with these DESs is ChCl/CF3SO3H > TEAC/CF3SO3H > TBAC/CF3SO3H. The research shows that the bigger steric hindrance of long cation chain is not conducive to the oxidative desulfurization.28 Four cation chains of TBAC/CF3SO3H are the longest, therefore its steric hindrance is the biggest result in lowest desulfurization rate. Four cation chains of ChCl/CF3SO3H was the shortest, so the its steric hindrance is the smallest result in the highest desulfurization rate. Therefore, ChCl/CF3SO3H was chosen as the catalyst and extractant for the system of oxidation desulfurization.
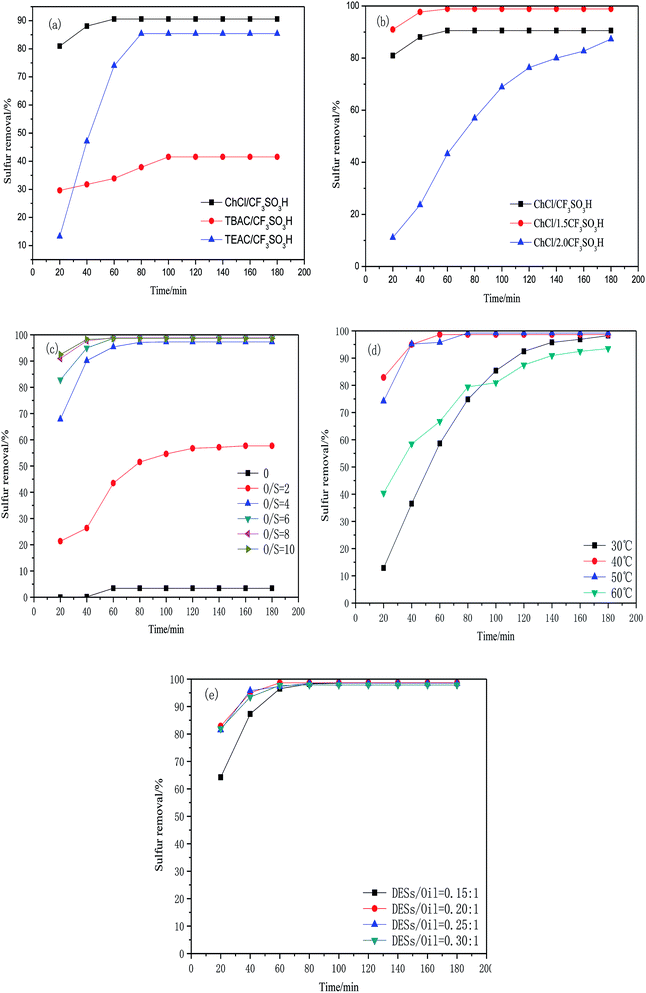 |
| Fig. 4 (a) Influence of different type DESs on desulfurization rate (5 mL model oil, O/S molar ratio of 8, 1 mL DESs, 40 °C); (b) influence of different acidity DESs on desulfurization rate (5 mL model oil, O/S molar ratio of 8, 1 mL DESs, 40 °C); (c) influence of amount of H2O2 on desulfurization rate (5 mL model oil, 1 mL DESs, 40 °C); (d) influence of reaction temperature on desulfurization rate (5 mL model oil, O/S molar ratio of 6, 1 mL DESs); (e) influence of amount of DESs on desulfurization rate (5 mL model oil, O/S molar ratio of 6, 40 °C). | |
3.2.2 Influence of acidity of DESs on desulfurization rate. ChCl/XCF3SO3H were synthesized using CF3SO3H and ChCl as raw materials. A series of ChCl/XCF3SO3H (X from 1.0 to 2.0) with different acidity were investigated by changing the molar ratio of ChCl to CF3SO3H. As shown in Fig. 4(b), the desulfurization rate obviously increased from 90.58% to 98.85% when the molar ratio of CF3SO3H to ChCl were increased from 1 to 1.5. However, the desulfurization rate dropped from 98.85% to 87.3% when the molar ratio of CF3SO3H to ChCl was increased to 2. It is because that acidity of DESs is too strong when the molar ratio of CF3SO3H to ChCl was increased to 2. It could be attributed to the higher acidity rapidly decomposed H2O2 into oxygen, thereby decrease the oxidative ability of the system.29 The highest desulfurization rate of 98.85% can be attached when the molar ratio of ChCl to CF3SO3H is 1.5. Moreover, the viscosity of DESs have important influence on desulfurization, the high viscosity of DESs decrease extractive ability of DESs.30 The high conductivity show there are a lot of ions in DESs.12 Therefore, high conductivity is benefit for desulfurization. As shown in Table 1, the conductivity and viscosity of DESs decrease with increasing molar ratio of CF3SO3H to ChCl. The consideration for influence of acidity, the conductivity and the viscosity of DESs on desulfurization, ChCl/1.5CF3SO3H can be selected as extractant and catalyst in the desulfurization system.
Table 1 Conductivity and viscosity of DESs at 25 °C
DESs |
Conductivity (δ)/(μs cm−1) |
Viscosity (η)/(mPa s) |
ChCl/1.0CF3SO3H |
5200 |
100 |
ChCl/1.5CF3SO3H |
4200 |
85 |
ChCl/2.0CF3SO3H |
4000 |
70 |
3.2.3 Influence of O/S molar ratio on desulfurization rate. Amount of H2O2 has an important influence on the desulfurization rate. The removal of DBT from the model oil in the ChCl/1.5CF3SO3H–H2O2 system with various O/S molar ratio was investigated. As shown in Fig. 4(c), removal rate of DBT is only 3.42% in the absence of H2O2. When the hydrogen peroxide was added into the oxidative desulfurization system, the desulfurization rate obviously increases. The desulfurization rate increased from 57.69% to 98.65% when O/S was increased from 2 to 6. According to stoichiometry, 2 molar H2O2 can transform 1 molar DBT to DBTO2. However, the removal rate of DBT is only 66.1% with O/S molar ratio of 2. The reasons are the decomposition of H2O2.31 When the O/S molar ratio is 4, the desulfurization rate can attach to 96.4% and continue to increase the O/S ratio, desulfurization rate increase slightly. So, the O/S molar ratio of 6 was the optimal choice.
3.2.4 Influence of reaction temperature on desulfurization rate. The reaction temperature is also an important factor influencing oxidative desulfurization. As shown in Fig. 4(d), the reaction rate of desulfurization was obviously increased and removal rate of DBT increase from 98.27% to 98.65% when the reaction temperature increased from 30 °C to 40 °C. However, the desulfurization rate no longer increased when the reaction temperature was beyond 40 °C. It could be attributed to high temperature accelerate the decomposition of H2O2,32 which decrease oxidative ability in the oxidative desulfurization process. So, the optimal temperature in the oxidative desulfurization system is 40 °C.
3.2.5 Influence of volume ratio of DESs/oil on desulfurization rate. Fig. 4(e) illustrates the DESs dosage has an important influence on removal of DBT. The removal rate for DBT was increased from 98.46% to 98.65 when the volume ratio of DESs/oil increased from 0.15 to 0.2. Continue to increase the DESs/oil ratio, removal rate of DBT no longer increase. So, it can be concluded that the optimal volume ratio of DESs/oil is 0.2 in the desulfurization system.
3.2.6 Influence of different sulfur compounds on desulfurization rate. In this study, DBT in model oil could be effectively removed using ChCl/1.5CF3SO3H as the catalyst and extractant, with H2O2 as the oxidant. In order to determine the desulfurization efficiency of the ChCl/1.5CF3SO3H for other organic sulfides in fuels, such as 4,6-DMDBT, BT and TH were researched in oxidation desulfurization under identical conditions. The results are shown in Fig. 5. The removal rate of BT, DBT, 4,6-DMDBT and TH were 39.53%, 98.65%, 96.8% and 24.35% after 180 min, respectively. The removal rate of four sulfur compound in the desulfurization system followed the order DBT > 4,6-DMBT > BT > TH. The desulfurization rate is related to the electron density of the sulfur atoms in organic sulfide. The electron cloud densities of these compounds are 5.758 for DBT, 5.760 for 4,6-DMDBT, 5.739 for BT, and 5.696 for TH,33,34 respectively. The electron cloud densities of 4,6-DMDBT and DBT are very approximation. However, removal rate for DBT was higher than 4,6-DMDBT due to the steric hindrance of the methyl substituent in 4,6-DMDBT.35 Therefore, the removal rate of 4,6-DMDBT is a little lower than DBT.
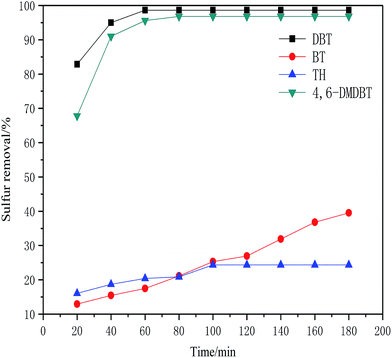 |
| Fig. 5 Influence of different sulfur compounds on desulfurization rate (5 mL model oil, O/S molar ratio of 6, 1 mL DESs, 40 °C). | |
According to the experimental results, ChCl/1.5CF3SO3H show excellent oxidative desulfurization activity. Table 2 shows a comparison of the desulfurization activity of ChCl/1.5CF3SO3H and other acidic ionic liquids. It can be seen that ChCl/1.5CF3SO3H has a high desulfurization rate under mild experimental conditions. Furthermore, ChCl/1.5CF3SO3H can be prepared by a simple method and the raw material are easily obtained.
Table 2 Comparison of the desulfurization activity of ChCl/1.5CF3SO3H and other acidic ionic liquids
Catalysts |
S content (μg g−1) |
Reaction conditions |
Removal of DBT |
Ref. |
[C4mim]TFA |
202 |
IL : oil = 1 : 35, H2O2 = 1 mL, 70 °C, 30 min |
100% |
20 |
[HMIm]BF4 |
1000 |
IL : oil = 5 : 3.2, O/S = 10, 90 °C, 360 min |
93% |
21 |
[BMIM][HSO4] |
1000 |
IL : oil = 1 : 2, O/S = 5, 25 °C, 90 min |
99.6% |
22 |
[Hnmp]BF4 |
1550 |
IL : oil = 1 : 1, O/S = 3, 60 °C, 60 min |
100% |
23 |
ChCl/1.5CF3SO3H |
500 |
IL : oil = 1 : 5, O/S = 6, 40 °C, 60 min |
98.65% |
This work |
3.2.7 Recovery and regeneration of DESs. After the oxidative desulfurization reaction, the upper oil phase was removed by using a separating funnel. The water in the DESs was removed by rotary evaporation. The DESs were extracted three times using CCl4 of equal volume. Fresh H2O2, recovered DESs were added into model oil under the optimal conditions. As shown in Fig. 6, the removal rate of DBT decreased from 98.65% to 97.16% after five recycles. Two reasons result in the decrease of desulfurization rate. On the one hand, it could be attributed to minimal loss in DESs during the recovery process; on the other hand, it might be attributed to a little of residual oxidation products of sulfide in the recovered DESs.
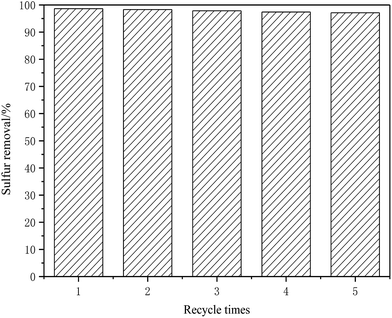 |
| Fig. 6 Recovery and regeneration of DESs (5 mL model oil, O/S molar ratio of 6, 1 mL DESs, 40 °C). | |
3.2.8 FT-IR characterization of oxidative production. As shown in Fig. 7(a), the mixture of oil phase and DESs phase is transparent liquid before the desulfurization reaction. However, there is white precipitate between oil and DESs after the desulfurization reaction in Fig. 7(a). In order to identify the white precipitate, a reverse extraction experiment was carried out using carbon tetrachloride (CCl4) as the extraction agent and the DESs as the extraction phase at room temperature. It can be found that the white substance is quickly dissolved into carbon tetrachloride. After the carbon tetrachloride were remove by distillation, the white powder was obtained. The infrared analysis of the white powder is shown in Fig. 7(b). Three infrared absorption peaks are observed at 1166, 1047, and 1288 cm−1 corresponding to the three characterization peaks of DBTO2.36,37 This shows that the DBT was oxidized to DBTO2 in the oxidative desulfurization system.
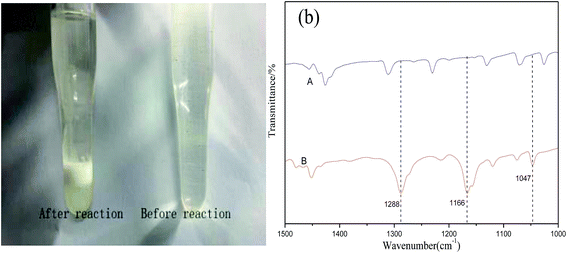 |
| Fig. 7 (a) Contrast diagram of before and after reaction; (b) FTIR characterization of oxidative production (A) DBT, (B) DBTO2. | |
3.2.9 Mechanism of catalytic oxidative desulfurization. As seen in Fig. 8, H2O2 is a strong oxidant in the acidic medium. DBT was extracted into the DESs phase and was oxidized to DBTO2 under the action of ChCl/1.5CF3SO3H and H2O2. During oxidative desulfurization process, DESs acted as not only extractant but also catalyst, so a continuous decrease of the content of DBT in n-octane was observed until H2O2 was completely decomposed.
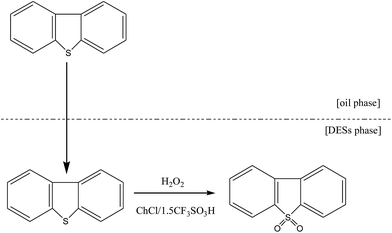 |
| Fig. 8 Mechanism of oxidative desulfurization. | |
3.3 Catalytic oxidative desulfurization of diesel oil
The S-removal activity of ChCl/1.5CF3SO3H for the real diesel oil with a total S-content of 375 mg L−1 was also investigated. Under the optimal condition, the desulfurization rate of 68.5% was obtained. Sulfur removal efficiency was found to be lower in diesel oil than that obtained in model oil (98.65%), which may be attributed to the more complex chemical composition of diesel.38
4 Conclusion
A series of ChCl/XCF3SO3H (X from 1.0 to 2.0) were synthesized by stirring a mixture of ChCl and CF3SO3H. The DESs were used as extractant and catalyst in the oxidative desulfurization process. Compared to other acidic ionic liquids, the synthesis method of ChCl/XCF3SO3H is simple. The ChCl/1.5CF3SO3H exhibits a high desulfurization activity for DBT in model oil and can be recycled 5 times without a significant decrease in activity. The results demonstrate the DESs exhibit the high catalytic activity and stability for the desulfurization system.
Acknowledgements
The authors also acknowledge the financial support of the Natural Science Foundation of China (Project no. 21003069); the authors also acknowledge the financial support of the Doctoral Fund of Liaoning Province (201501105).
References
- X. M. Yan, Z. Mei and P. Mei, et al., J. Porous Mater., 2014, 21(5), 729–737 CrossRef CAS.
- H. Li, W. Zhu and J. Lu, et al., React. Kinet., Mech. Catal., 2009, 96(1), 165–173 CrossRef CAS.
- J. Zhang, W. Zhu and H. Li, et al., Green Chem., 2009, 11(11), 1801–1807 RSC.
- X. Tang, Y. Zhang and J. Li, et al., Ind. Eng. Chem. Res., 2015, 54(16), 4625–4632 CrossRef CAS.
- R. Wang, G. Zhang and H. Zhao, Catal. Today, 2010, 149(1), 117–121 CrossRef CAS.
- J. M. Campos-Martin, M. C. Capel-Sanchez and P. Perez-Presas, et al., J. Chem. Technol. Biotechnol., 2010, 85(7), 879–890 CrossRef CAS.
- Z. S. Gano, F. S. Mjalli and T. Al-Wahaibi, et al., Chem. Eng. Process., 2015, 93, 10–20 CrossRef CAS.
- H. X. Zhang, H. L. Huang and C. X. Li, et al., Ind. Eng. Chem. Res., 2012, 51(38), 12449–12455 CAS.
- S. Ribeiro, C. M. Granadeiro and P. Silva, et al., Catal. Sci. Technol., 2013, 3(9), 2404–2414 CAS.
- H. Yang, B. Jiang and Y. Sun, et al., Chem. Eng. J., 2016, 306, 131–138 CrossRef CAS.
- D. Fang, Q. Wang and Y. Liu, et al., Energy Fuels, 2014, 28(10), 6677–6682 CrossRef CAS.
- L. Lu, S. Cheng and J. Gao, et al., Energy Fuels, 2007, 21(1), 383–384 CrossRef CAS.
- H. Gao, C. Guo and J. Xing, et al., Green Chem., 2010, 12(7), 1220–1224 RSC.
- D. Zhao, J. Wang and E. Zhou, Green Chem., 2007, 9(11), 1219–1222 RSC.
- A. Paiva, R. Craveiro and I. Aroso, et al., ACS Sustainable Chem. Eng., 2014, 2(5), 1063–1071 CrossRef CAS.
- C. Li, D. Li and S. Zou, et al., Green Chem., 2013, 15(10), 2793–2799 RSC.
- A. P. Abbott, D. Boothby and G. Capper, et al., J. Am. Chem. Soc., 2004, 126(29), 9142–9147 CrossRef CAS PubMed.
- Q. Zhang, K. D. O. Vigier and S. Royer, et al., Chem. Soc. Rev., 2012, 41(21), 7108–7146 RSC.
- A. P. Abbott, G. Capper and K. J. McKenzie, et al., J. Electroanal. Chem., 2007, 599(2), 288–294 CrossRef CAS.
- B. P. Wu, Q. Wen and H. Xu, et al., J. Mol. Catal. B: Enzym., 2014, 101, 101–107 CrossRef CAS.
- K. Pang, Y. Hou and W. Wu, et al., Green Chem., 2012, 14(9), 2398–2401 RSC.
- W. Zhu, C. Wang and H. Li, et al., Green Chem., 2015, 17(4), 2464–2472 RSC.
- Z. S. Gano, F. S. Mjalli and T. Al-Wahaibi, et al., Chem. Eng. Prog., 2015, 93, 10–20 CrossRef CAS.
- J. Yin, J. Wang and Z. Li, et al., Green Chem., 2015, 17(9), 4552–4559 RSC.
- C. Mao, R. Zhao and X. Li, Fuel, 2017, 189, 400–407 CrossRef CAS.
- P. S. Kulkarni and C. A. M. Afonso, Green Chem., 2010, 12(7), 1139–1149 RSC.
- P. Liu, J. W. Hao and S. J. Liang, et al., Monatsh. Chem., 2016, 147(4), 801–808 CrossRef CAS.
- W. Jiang, W. Zhu and Y. Chang, et al., Chem. Eng. J., 2014, 250, 48–54 CrossRef CAS.
- Y. Dong, Y. Nie and Q. Zhou, Chem. Eng. Technol., 2013, 36(3), 435–442 CrossRef CAS.
- F. Li, B. Wu and R. Liu, et al., Chem. Eng. J., 2015, 274, 192–199 CrossRef CAS.
- X. Chen, H. Guo and A. A. Abdeltawab, et al., Energy Fuels, 2015, 29(5), 2998–3003 CrossRef CAS.
- W. Jiang, W. Zhu and H. Li, et al., RSC Adv., 2013, 3(7), 2355–2361 RSC.
- W. S. Zhu, H. Li and Q. Q. Gu, et al., J. Mol. Catal. A: Chem., 2011, 336(1), 16–22 CrossRef CAS.
- D. Wang, E. W. Qian and H. Amano, et al., Appl. Catal., A, 2003, 253(1), 91–99 CrossRef CAS.
- W. Zhu, H. Li and X. Jiang, et al., Green Chem., 2008, 10(6), 641–646 RSC.
- C. Mao, R. Zhao and X. Li, Fuel, 2017, 189, 400–407 CrossRef CAS.
- M. Zhang, W. Zhu and S. Xun, et al., Chem. Eng. J., 2013, 220, 328–336 CrossRef CAS.
- W. Zhu, G. Zhu and H. Li, et al., J. Mol. Catal. A: Chem., 2011, 347, 8–14 CrossRef CAS.
|
This journal is © The Royal Society of Chemistry 2017 |
Click here to see how this site uses Cookies. View our privacy policy here.