DOI:
10.1039/C6NH00077K
(Review Article)
Nanoscale Horiz., 2017,
2, 6-30
Synthesis of aerogels: from molecular routes to 3-dimensional nanoparticle assembly
Received
29th April 2016
, Accepted 26th September 2016
First published on 20th October 2016
Abstract
Colloidal nanocrystals are extensively used as building blocks in nanoscience, and amazing results have been achieved in assembling them into ordered, close-packed structures. But in spite of great efforts, the size of these structures is typically restricted to a few micrometers, and it is very hard to extend them into the macroscopic world. In comparison, aerogels are macroscopic materials, highly porous, disordered, ultralight and with immense surface areas. With these distinctive characteristics, they are entirely contrary to common nanoparticle assemblies such as superlattices or nanocrystal solids, and therefore cover a different range of applications. While aerogels are traditionally synthesized by molecular routes based on aqueous sol–gel chemistry, in the last few years the gelation of nanoparticle dispersions became a viable alternative to improve the crystallinity and to widen the structural, morphological and compositional complexity of aerogels. In this Review, the different approaches to inorganic non-siliceous and non-carbon aerogels are addressed. We start our discussion with wet chemical routes involving molecular precursors, followed by processing methods using nanoparticles as building blocks. A unique feature of many of these routes is the fact that a macroscopic, often monolithic body is produced by pure self-assembly of nanosized colloids without the need for any templates.
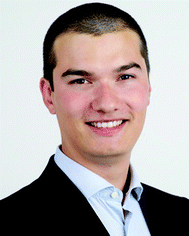
Felix Rechberger
| Felix Rechberger is currently a PhD candidate in the Laboratory for Multifunctional Materials of Prof. Niederberger at ETH Zurich. In 2010 he received his BSc degree in Materials Science, which was followed by an MSc degree with distinction in Materials Science in 2013. His research interests focus on the synthesis and characterization of nanoparticles by nonaqueous sol–gel methods and ultimately their exploitation as building blocks for the 3D-assembly into macroscopic xero- and aerogels as multifunctional materials. |
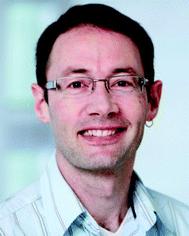
Markus Niederberger
| Markus Niederberger is Chair of the Laboratory for Multifunctional Materials in the Department of Materials at ETH Zurich. He studied chemistry at ETH Zurich, where he also received his PhD. After a postdoctoral stay at the University of California at Santa Barbara, he became a group leader at the Max Planck Institute of Colloids and Interfaces in Potsdam. In 2007 he was appointed as an Assistant Professor at ETH Zurich and in 2012 he was promoted to an Associate Professor. His research interests are focused on the development of liquid-phase synthesis routes to inorganic nanoparticles with defined sizes, shapes and surface chemistry, the study of their formation mechanisms, and their assembly and processing into macroscopic materials with tailored properties and functionalities for specific applications in energy storage and conversion, optics, gas sensing and (photo)catalysis. |
1. Introduction
The ability to create materials on different as well as over many length scales is the basis of today's technological progress.1–11 Over thousands of years materials processing routes were developed with the goal to fabricate bulk materials such as ceramics, polymers, metals or composites. The major part of these processes involves engineering, i.e., the desired functionality of a material is obtained by casting, shaping, joining, blending or annealing without necessarily tailoring the composition of the individual components. Chemistry, on the other hand, exactly focuses on this aspect: the synthesis of new molecules, compounds and materials, starting basically from the atoms. Somewhat oversimplified one could say that the chemist makes the material, while the engineer brings it into a specific shape that is suitable for the targeted technological application. With the advent of nanoscience however, the traditional working areas and their corresponding size regimes got blurred and chemists, physicists, engineers and materials scientists now address all length scales from the nano- to the macroscale.7,8 At the same time, the subtleness how materials can be processed has tremendously increased. In comparison to traditional processing routes, the focus now lies on the use of well-defined building blocks (molecules, molecular assemblies or particles) and their sequential and modular arrangement into, ideally, hierarchical and complex structures.1,2 The main challenge is to keep full control over the assembly of the building blocks including their spatial arrangement, orientation and their interaction from the nano- to the macroscale, thus bridging several orders of length scales.12 In the best case, the final material exhibits a combination of the intrinsic properties of the building blocks as well as new properties resulting from collective or synergistic effects.13–16 Clearly, such a materials design strategy demands the highest level of synthesis control for the building blocks including composition, crystallinity/crystal structure, size, size distribution, shape, defect chemistry and surface functionalization.4,17–23 Nevertheless, after several years of intense research on nanoparticle synthesis, an immense library of well-defined building blocks is available, and the next step towards their arrangement into 1-,24,25 2-25 and 3-dimensional structures26,27 has already been taken.4,28,29 As an illustrative example, Fig. 1 summarizes the assembly behavior of anisotropic Mn3O4 nanocuboids.30 Either 1D, 2D or 3D microarrays are formed by oriented self-assembly through evaporation of nanoparticle dispersions with different concentrations, and the orientation of the tetragonal crystals was controlled to be parallel and perpendicular to the substrate by changing the polarity of the solvent (Fig. 1a). Scanning electron microscopy (SEM) images show linear chains of cuboids aligned in the 〈100〉 direction (Fig. 1c), monolayers with domain sizes of about 1 μm (Fig. 1b) or 3-dimensional superlattices several microns in size (Fig. 1d).30
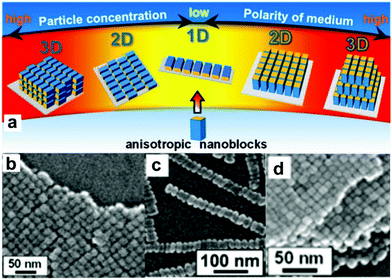 |
| Fig. 1 (a) Schematic of the assembly behavior of anisotropic Mn3O4 nanoblocks in dependence of the dispersion media and the particle concentration. SEM images of (b) a monolayer (2D), (c) linear chains (1D), and (d) a superlattice (3D) of Mn3O4 cuboids. Adapted with permission from ref. 30, Copyright 2013, American Chemical Society. | |
This is just one example that underlines the impressive progress in the field of particle assembly, but at the same time it also reveals the major limitation. While it is possible to produce complex/hierarchical structures,31 quasicrystals,32 mesocrystals,33 supracrystals,34 polymer-like crystals,35 helices36 and many others, their size is typically limited to a few micrometers, and it is very hard to translate such structures into the macroscopic world. It is interesting to note that in most of these examples great efforts were made to arrange the particles into dense and highly ordered structures, and often the degree of order is the limiting factor for their performance in a specific application (e.g., photonic crystals). However, if opposing properties like low density, extended porosity and high surface areas are desired, then colloidal gels represent the materials of choice. For their synthesis, the key challenge is not only to produce the network structure over several orders of length scales, but also to be able to control the degree of order and porosity. In the case of ordered mesoporous materials, amphiphilic molecules like surfactants and block-copolymers are used to control the size and the arrangement of the pores during synthesis.37–40 In aerogels, which are typically produced without the help of any templates or structure-directing agents, the pores are disordered and the pore size distribution is broad. Nevertheless, they offer a series of advantages when it comes to functional applications.41,42 Because the pores are interconnected with sizes reaching from the nano- up to the macroporous regime, molecular diffusion is facilitated by multiple entrance and exit points. Therefore, if the pathways are locally blocked by reactants or through collapse of the pore structure, the molecular transport is not interrupted, which is impossible in systems with regular and non-percolating pores.43
As a matter of fact, if the building blocks are nanosized, it is essential that the 3-dimensional assembly occurs in a way that the large surface area of the nanocrystals and their size- and shape-dependent properties are preserved in the final material. This is only possible, if the whole gelation process is controlled from the primary particle level up to the macroscopic body.
In this Review, we address the self-assembly of nanoparticles into macroscopic, 3-dimensional, disordered and porous structures. Starting from a historical perspective on colloidal particles and gels, we move on to the preparation of aerogels by molecular routes and in the last section we discuss nanoparticle-based aerogels. In the last few years, this research field made immense progress and a large number of different nanoparticle-based aerogels are available nowadays, covering almost all classes of materials. A unique feature of these routes is the macroscopic size of the final, often monolithic aerogels, which is reached by pure self-assembly without the use of any templates.
2. Historical overview
According to IUPAC, a gel is a “Non-fluid colloidal network or polymer network that is expanded throughout its whole volume by a fluid.”44 As the definition already suggests, these structures are based on colloids as point of origin. These particles cover a wide range of multiphase substances of small particles (1 μm > colloids > 10 nm) dispersed in a continuous phase. Colloids occur naturally and are all but a new phenomenon. Observations by Robert Brown in 1827 were performed on the colloidal motion in pollen and spores,45 thereby laying the foundations for the research of Einstein on atoms46 and Perrin on Avogadro's number47 in the beginning of the 20th century. However, these studies were not the first discoveries or even uses of colloids. In the following, we move back in time to the late Pleistocene age to start our short historical overview on the human usage and understanding of colloids.48–51
Dating back 17
000 years, cave paintings in Lascaux in France showed the earliest known use of human-made colloidal suspensions. By using natural oils as surface stabilizing agents, fine ground powders of iron oxide, carbon and clays were dispersed in water and used as paint. Efforts of the Chinese and Egyptians using lamp blacks in natural polymers in the form of colloidal dispersions with protective agents like gelatin or gum led to non-coagulating and therefore not-gelling inks.
The next major milestone was reached some 8000 years ago in the Atlantic age period by early examples of colloids in plaster and bricks produced through burning. At around 4000 BCE faience was produced in Egypt by firing an aqueous paste of crushed sand, binder and sodium flux, connecting silica particles together with the molten flux. In China and Mesopotamia surfaces were sealed in porous clay vessels by fusing powdered glass through glazing methods, dating back as far as 2000 BCE. First developments of concrete were based on the idea of using chemically linked particles as a matrix to form a composite with other colloidal materials in Iran 700 BCE. The Romans improved this process between 200 BCE and 400 CE, and the British, French and Germans continued the work until the 18th century. Later, Alchemists made gold and silver in colloidal form in stained glass for church windows. A significant development was the discovery of “water glass” by van Helmont in 1644.52 Silicates were dissolved in alkali and formed a precipitate upon acidification of the liquid. In 1779 Bergman described the gelation of silicates upon addition of a dilute acid.53 Following this discovery, many materials were prepared from hydroxide gels, such as zirconium or uranium oxide gels.49 Shortly before Faraday reported his studies on the optical properties of colloidal gold solutions in his famous Bakerian lecture in 1857,54 Ebelmen prepared the first silicon alkoxide in 1846 through the reaction of silicon tetrachloride in alcohol.55 Upon exposure to atmosphere with normal humidity, the product gelled, laying the basis for future discoveries in the field of colloidal gels. Hydrolysed derivatives of silicon alkoxides and silicic acid were discovered between 187656 and 1884.57 Important work towards processibility of gels was performed by Graham, showing that the porous water in silica gels could be exchanged to organic solvents.58 This observation led Kistler in 1931 to the conclusion that a gel (once it is formed) is independent of the pore fluid59 and this fluid could very well be a gas rather than a liquid.60 At that time, gels were dried by simply evaporating the liquid in ambient conditions, which was accompanied by large shrinkage. Liquid–vapour interfaces within the network of the gel resulted in strong surface tensions, which destroyed the network and caused the structure to collapse. In order to preserve the macroscopic body of the wet gel after drying, Kistler worked out the following idea: “Obviously if one wishes to produce an aerogel, he must replace the liquid with air by some means in which the surface of the liquid is never permitted to recede within the gel. If a liquid is held under pressure always greater than the vapour pressure, and the temperature is raised, it will be transformed at the critical temperature into a gas without two phases having been present at any time. […] Accordingly, it becomes possible to take a gel filled with a liquid, transform the liquid gradually into a gas, allow the gas to expand above the critical temperature, and end with the gel filled with gas of low density without at any time having subjected the gel to compressive forces. This, in general, is the procedure […]”59 of supercritical drying.61–64 Supercritical drying is obviously able to avoid capillary forces present during ambient drying, thus making it possible to produce aerogels as a representative of ultralight materials.59,61
Further insight in the structure of silica gels was gained in the late 1930s, when Hurd showed the percolating polymeric skeleton of silicic acid containing a continuous liquid phase.65 In the 1970s, significant research efforts were conducted on gels and colloidal particles mainly by nuclear industry for fuel cells in nuclear reactors49 and by the mining industry for Bingham fluids in waste clay disposal.66 Further interest was generated by food and cosmetic industry on reversible aggregation of colloids, leading to features like yield stress and thixotropy observed e.g. in Ketchup or shampoo.67 From the 1980s on, there was a big push in gel research, mainly generated by the progress in the synthesis routes and the discovery of fractal structures within gelled colloids. Meakin and Weitz became the pioneers in understanding fractal aggregates (Fig. 2) and their ramifications in gels.68–70 The development of a wide range of characterization techniques based on light,71 X-ray72 and neutron73,74 scattering and confocal microscopy techniques75,76 has allowed a deep insight into the structure and mechanics of gels and how they are influenced by the aggregation kinetics. Application of simulation techniques in gel research allowed a detailed view on the interaction models within the colloidal network.77–79
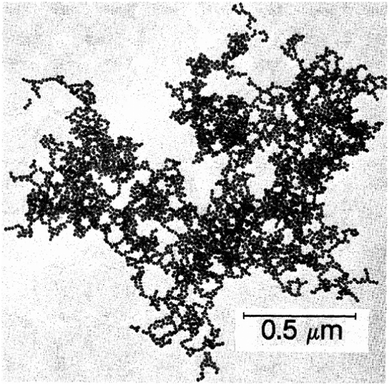 |
| Fig. 2 Transmission electron microscope (TEM) image of a fractal gold colloid aggregate. Reproduced with permission from ref. 69, Copyright 1984, American Physical Society. | |
The concept of gels is related to that of glass. Therefore, the differences and similarities in the rheological signatures of these materials were elaborated.80–87 Recently, the focus has shifted towards depletion gels, which were actually discovered many years ago.88 These systems allow the systematic study of “sticky” colloids by varying the strength of the depletion potential.75,76,85,86,89
Without any doubts, research in the field of sol–gel processes has undergone immense progress until today with significant impact on the development of synthesis routes to nanoparticles, gels and ceramics. Many of today's known sol–gel techniques have their historical origin in decorative and constructional materials, sometimes discovered by serendipity, sometimes rationally developed. Applied in art in ancient times, then implemented in technology, colloids and gels also became science. Although research on wet gels remains a “hot topic”, we change our focus now towards the preparation of their self-supporting, supercritically dried counterparts: aerogels.
3. Terms and definitions
Before we discuss the preparation of aerogels, we begin with the definition of a few terms used throughout the Review. Gelation has been defined in different ways, but the most common definition is often associated with percolation.90 The colloids are linked together, forming branched fractal chains, thereby filling the entire volume homogenously with a coherent network of particles. Once there is a sample-spanning arrangement of particles in the reaction container, the percolation threshold, also called the gelling point, is reached. Percolation is clearly related to “connectedness” and therefore can also be applied to other physical properties such as electrical conductivity. However, percolation alone is not sufficient for defining a gel state, but simply a necessary prerequisite, as often the associated bonds are not permanent (yet) and can still break and reform (“hopping”).91 Further aging of the gel beyond the percolation point increases the stiffness and leads to a rigid structure with a permanent stress bearing capacity.92 Unfortunately, a clear definition of when the “gelled state” is reached is still missing and part of ongoing discussions.92
Flocculation also involves the linking of colloidal particles to a three-dimensional network. However, the formed flocks do not span the entire sample volume. Depending on gravitational settling, flocculation leads to sedimentation. Highly concentrated dispersions undergoing a phase separation either by gelation or flocculation cannot be distinguished from each other, because the single flocks can form bridges, leading to percolation and gel formation.50,93
Kistler's work on supercritical drying made use of a reactor able to sustain pressures of 300 bars and temperatures of over 250 °C to reach and hold the supercritical state of organic solvents without crossing the liquid–gas phase boundary, before the pressure is reduced at constant temperature to ambient pressure to remove the sample.59 Apart from the obvious safety risks, these harsh conditions might damage the cell structure of the gel through surface modifications or accelerated aging and ripening.63 The development of milder supercritical drying with CO2 solved this problem, but introduced another time consuming step. Solvent exchange to an intermediate liquid miscible with liquid CO2, e.g. ethanol or acetone, is required, because water is immiscible. In addition, a considerable amount of time for diffusion and substitution of this intermediate liquid with CO2 within the gel is needed in the pressure reactor. After increasing the temperature to reach the supercritical state, it is kept for a certain period of time to ensure a homogeneous distribution of the supercritical state within all pores of the gel. As the critical conditions of CO2 (31 °C and 74 bar) are relatively moderate compared with other organic solvents, structural changes in the gel are marginal. Recently, suggestions for alternatives such as aerosol gelation94 or freeze dried aerogels from aqueous95 or organic solvent dispersions96 have been published. Freeze drying is however often accompanied by shrinkage or destruction of the fine gel structure due to slow freezing rates.
In this Review we will focus on supercritically dried gels. Contrary to their ambient dried counterparts (xerogels),97 where pores collapse due to capillary forces present during evaporation, aerogels show a preserved percolating microstructure which is often fractal and with open porosity. Fractals are self-similar structures with objects looking similar even when viewed at different length scales, i.e. at different magnifications. Thus, the structure on the length scales of a few particles resembles the microstructure of the aerogel. Interestingly, the word ‘aerogel’ itself is not clearly defined throughout the literature. Hüsing et al. used a definition closest associated to the necessary supercritical drying step: “materials in which the typical structure of the pores and the network is largely maintained […] while the pore liquid of a gel is replaced by air are called aerogel.”63 The authors of this Review believe that aerogels are increasingly recognized as materials with special structures and characteristics, while the specific drying technique or preparation procedure is less important. Therefore, we prefer a structural definition similar to Fricke et al.:98 aerogels are open-celled porous solid materials composed of a network of interconnected nanostructures with the majority of pore sizes below 100 nm and a porosity of over 80%.
4. Molecular routes to aerogels
The vast majority of publications are dedicated to aerogels based on silica and carbon. Silica was the first material produced as aerogel and it became the most extensively studied system in the community. For the synthesis of silica aerogels, mostly alkoxides are used as molecular precursors in sol–gel reactions, because the chemistry and the reaction kinetics are well known and controllable for these systems, and silica offers extensive potential for surface functionalization.99,100 For carbon aerogels, which have gained a lot of attention in the past years, the typical synthesis involves polymerization of resorcinol and formaldehyde (RF), followed by pyrolysis.100,101 Compared to silica, carbon aerogels are not necessarily prepared by sol–gel processes, but can even be produced from other carbon sources like nanotubes.102 There is extensive literature on carbon and silica aerogels, and therefore a detailed discussion of these materials and their composites goes far beyond the scope of this Review. The interested reader is referred to other publications and reviews covering the recent advances in carbon and silica aerogel research.100,103–106
In this section, we focus on different wet-chemical molecular routes to non-siliceous and non-carbon aerogel materials,107 which mainly include metal oxides and chalcogenides.108 Metal oxides and metal chalcogenides offer a great variety of diverse and distinctive properties in many fields of materials science. Their synthesis in form of aerogels results in highly multifunctional materials with properties well beyond those of a simple support or scaffold material as it is often the case for silica and carbon.
Metal alkoxides are the most widely used precursors in aqueous sol–gel chemistry for the synthesis of metal oxides. Their chemical transformation basically involves two reactions: hydrolysis and condensation (Scheme 1). These two types of reactions are fundamental for all metal alkoxides, although of course coordination numbers, oxidation states, reaction rates and finally the materials properties are different for each metal ion. Further information on the specific reactions leading to metal oxides can be found somewhere else.109,110 During hydrolysis, the alkoxide groups (–OR) are (partly or completely) substituted by hydroxyl groups (–OH) through a nucleophilic attack of water. In the second step, condensation reactions occur between two M–OH species under the release of water (oxolation) or between M–OH and M–OR under release of an alcohol (alkoxolation), resulting in the formation of bridged M–O–M bonds.97 Through nucleation and growth these hydrolysis and condensation reactions produce an often amorphous oxidic sol, a dispersion of colloids in a liquid (Scheme 2).109 Further condensation and crosslinking beyond the so-called sol-to-gel transition results in a percolating, open-porous network enclosing a continuous liquid phase throughout the sample.97 The main issue of sol–gel chemistry is that, even though the chemical reactions are well-known, the hydrolysis and condensation rates are fast and hard to control, making it difficult to adjust the gelling behaviour and to tailor the final porosity. However, there are a number of strategies to influence the reaction kinetics of the sol–gel process, such as using precursors with bulky non-reacting side chains (which do not participate in the condensation reactions), concentration of precursors, addition of surfactants, variation of solvents, regulation of pH and many more.48 Similar modifications and tricks are also adapted for particle synthesis to achieve control over morphology and size.97 However, as the system is constantly changing, controlling the kinetics especially related to gel formation remains a major challenge and slight deviations from the optimal conditions has a detrimental effect on the gelling behavior.40 Accordingly, after sol formation, gelation is the second and fundamental step en route to an aerogel, as Kistler postulated: “the ability to form an aerogel is a general property of gels.”59 It is important to note that upon formation of the gel network, the chemical reactions are not terminated. Structural changes within the gels due to condensation reactions of neighbouring –OH and –OR groups and thermodynamically driven rearrangements like Ostwald ripening of the still flexible network lead to a mechanically more stable scaffold. Therefore, gels are often aged and ripened after synthesis before supercritical drying.100
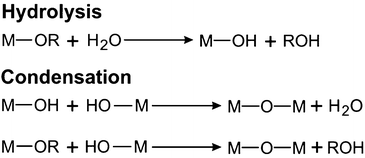 |
| Scheme 1 Main reactions of the sol–gel process using metal alkoxides (represented by M–OR) in aqueous solutions: hydrolysis and condensation involving both oxolation (elimination of water) and alkoxolation (elimination of an alcohol ROH). | |
 |
| Scheme 2 Overview of an aerogel synthesis by the sol–gel route from molecular precursors undergoing hydrolysis and condensation reactions. The wet gel, formed by the sol-to-gel transition, is supercritically dried to obtain the final aerogel. | |
Although research efforts on aerogel materials have been ongoing since nearly a century, their characterization is not yet fully established. The mechanical properties are quite poor and the structure covers several orders of magnitude. A detailed description of possible characterization techniques goes beyond our Review, but is readily available in dedicated literature.100,111–113
Sol–gel approaches
In this section, the most prominent examples of non-siliceous oxides and chalcogenide aerogels produced by sol–gel synthesis are presented. The aerogels are grouped into paragraphs according to their compositions, and additionally we briefly discuss selected applications.
In 1975, Yoldas found a method to fabricate Al2O3 ‘aerogels’ from alkoxides. Although their porosity does not completely fit to the definition of aerogels, they are one of the first examples of highly porous non-siliceous structures (Fig. 3).114–117 Different attempts were made to study the intermediate species during formation118 and to improve the mechanical119 and thermal120 stability. Al2O3 aerogels are interesting for applications as catalysts and catalyst supports,121–126 and they are also used for the removal of mustard gas127 or for silica alternatives in capturing cometary fragments.128
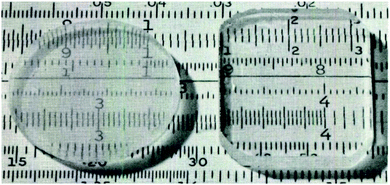 |
| Fig. 3 Transparent alumina ‘aerogels’ with 4.8 mm thickness heat treated at 1000 °C. Right specimen is impregnated with benzyl alcohol to improve transparency. Reprinted from ref. 116, Copyright 1975, with permission of The American Ceramic Society. | |
A lot of attention has been directed towards the synthesis of titania aerogels.63,100,129 These materials are usually synthesized from the corresponding ethoxide,130 isopropoxide131–136 or butoxide137,138 by classical sol–gel approaches in aqueous alcohol or ketone mixtures. After calcination, the TiO2 aerogels are mainly used for applications in catalysis,129,132,134 dye-sensitized solar cells136 and in monolithic form as columns for chromatography.133 In order to offer a rare possibility to modify the porosity, TiO2 aerogels are co-gelled with SiO2.139–143 Doping with Eu,144 Fe145 and Pt improved the photocatalytic activity.146 By using gold nanoparticles as “guests” during gelling of a TiO2 “host”, the electron scavenging properties of gold could be introduced in the TiO2 aerogel composite.147 Producing mixed oxides of CeO2,148 RuO2,149 MnOx/V2O5150 and ZrO2151 with TiO2 presents another approach to tune the photocatalytic activity.
Vanadium oxide is a promising cathode material in lithium ion batteries due to its capability to intercalate Li ions. For such an application, the porous structure of an aerogel should be highly beneficial. Several groups investigated the electrochemical properties of V2O5 aerogels for energy storage.152–165 Apart from Li+, these aerogels showed great potential to host other ions such as Na+, K+, Mg2+, Ba2+, Al3+ and Zn2+.166,167 The electrochemical performance was modified by doping V2O5 with copper or zinc,168 by fabricating nanocomposites with RuO2169 or with polypyrrole170 and by introducing Ba0.25V2O4 whiskers as 1D electron conducting additive.171 By nitridation of V2O5, various degrees of nitrogen enrichments were achieved with different vanadium valence states. These vanadium oxynitrides were tested in sensor devices.172 In combination with TiO2, V2O5 also showed excellent photocatalytic activity.150,173–181
Zirconia aerogels were prepared by different traditional sol–gel syntheses with alkoxides or salts as precursors and subsequent calcination.100,182–187 Baiker et al. investigated the effect of acids and solvents on the structural properties.188,189 The short range order and the fractal properties of zirconia aerogels were investigated by Zeng et al. with X-ray diffraction (XRD)190 and small angle X-ray scattering (SAXS) measurements.191 SAXS allowed analysis of the morphological changes by local surface diffusion, leading to fragmentation during thermal relaxation.192 Zirconia aerogels find applications in catalysis,193–195 phosphopeptide enrichment196 and thermal insulation.197 Doping enhanced the catalytic activity, especially through the impregnation with sulphur.198–205 Furthermore, ZrO2 aerogels stabilized with Y2O3,206,207 doped with Rh,206 Ni,202,204 Fe,208 Cu209 and Co,203 and mixed oxides with Al2O3,210 TiO2211 or WOx198 were reported.
Klabunde et al. synthesized and investigated the formation of magnesia aerogels.212–215 Another group slowed down the gelation by adding glycerol and acetic acid to produce large and crack-free samples.216 Recently, the influence of structure directing agents (Pluronic 123) was investigated by Hüsing et al.217 The potential applications for MgO are in catalysis or in the removal of toxic gases.218 The catalytic activity could be improved by loading gold particles onto the surface,219 by co-gelling with VOx220,221 or by producing Mg–Zr mixed oxides.222
The influence of organics on the properties of chromia aerogels was investigated by Skapin et al.223 Furthermore, the fluorination effects on Cr2O3 were studied,224 which was later also adapted to alumina aerogels.225–227 But the metal oxides were only partially fluorinated on the surface, while deep bulk fluorination led to the complete loss of the aerogel structure.228 More chromium based materials were synthesized by Landau229,230 and co-workers including α-Cr2O3, α-CrOOH and other compounds as catalysts supports.231 Younes et al. combined Cr2O3 with Al2O3 to catalyse the nitroxidation of toluene to benzonitrile.232
In addition to the metal oxide aerogels described above, which are among the most studied ones, there are also examples, for which the literature is much more limited, e.g. Fe–Cr–Al mixed oxides,233,234 gold–iron oxides,235 MoO3,236–238 WO3,239,240 Li2O·B2O2,241 GeO2,242 ZnO243 and V doped ZnO,244–247 SnO2,248–250 Sn–Al oxides,251 Nb2O5,252 Pd doped CeO2,253 MnO2,254,255 Ta2O5256 and more complex compositions like MgFe2O4,257 BaTiO3,258–260 SrTiO3,260 PbTiO3,261 Li4Ti5O12,262 VOHPO4·0.5H2O,263 La2Mo2O9264 and CuO–ZrxCe1−xOy.265
For some applications, chalcogenides are preferred over oxides. Analogous to classical aqueous sol–gel synthesis it is possible to produce amorphous or poorly crystalline sulfide gels through thiolysis, where H2O is replaced by H2S gas, resulting in sulfur-linked gels. Similar to metal oxide gels, the relative reaction kinetics of thiolysis and condensation play a major role for gel formation.100 Another reaction towards sulfide gels is metathesis, a partner-switching polymerization reaction.266 Here, soluble chalcogenide clusters are linked by metal ions leading to a three dimensional network.267
Pioneering work on chalcogels was performed by Stanić et al. starting in 1996 on sulfides such as ZnS,268 WSx269 and GeS2.270,271 Doping GeS2 with Er3+ increased the thiolysis rate and consequently led to a more grainy gel.272 The group of Kanatzidis later on developed the expertise to synthesize various sulfide chalcogels, many of which show interesting ion-exchange properties273–275 and high efficiencies towards adsorption of heavy metals.274–276 The same group investigated the improvement of the selective adsorption of gases on inorganic networks with high surface polarizability.277 Especially CoMoxSx278,279 based chalcogels showed excellent results.280 An example of a hierarchical architecture involved one dimensional chains of chalcogenide clusters, which were then used as building blocks for three dimensional chalcogenide gels.281,282 Recently, chalcogels with biomimetic functionalities produced by a controlled metathesis reaction between precursor clusters were reported, leading to a bottom-up assembly of redox-active species linked in between a network of tin sulfide clusters. These structures were then used as hybrid systems, combining both biomimetic and porous properties of heterogeneous catalysts. The chalcogels showed good photochemical conversions of nitrogen283 and production of solar fuels.284–288 Furthermore, these tin sulfide based chalcogels also showed promising properties for the remediation of radionuclides and could possibly solve problems in nuclear waste treatments.289–292
Recently, Rothenberger et al. reported polysulfides such as KFexMxSx (M = Sb, As, Co, Y, Eu)293,294 and CuSb2S4.295 Additionally, they prepared the first telluride based quaternary aerogel (KFeSbTe3).296 All these materials showed great potential in gas adsorption for the purification of gases.
For the sake of completeness, we conclude this section with selected aerogels beyond oxides and chalcogenides, and which were produced by special methods. Zettl et al. used a carbothermal reduction of boron oxide and simultaneous nitridation to obtain BN aerogels.297,298 These aerogels could then be loaded with platinum nanoparticles for gas sensing applications.299 Furthermore, the first carbide aerogels consisting of TiC and NbC were synthesized from a carbon aerogel network by using a low temperature pseudomorphic carbidization approach with volatile metal compounds.300 Recently, the direct preparation of fluorides from sol–gel processes has been shown for luminescent EuF3 compounds301 and for AlF3 synthesized in the presence of methanol.302
Epoxide addition methods
Despite the respectable collection of metal oxide and chalcogenide aerogels, the fast reaction kinetics of the sol–gel process remains an issue for many oxidic materials. Even under ideal conditions, hydrolysis and condensation of the precursors generally lead to dense hydroxide or oxide sediments. To obtain porous gels, the hydrolysis and condensation rates need to be significantly slowed down.100 An interesting study was published by Gash et al. in 2001 in the context of Fe2O3303 and Cr2O3304 aerogels. They used inorganic salts and epoxides (epoxide addition: EA method) to induce gelation. This method was introduced for the formation of lanthanide(–silicate) aerogels with erbium and praseodymium.305 The group of Gash investigated the influence of different types of epoxides (see Fig. 4) on the microstructural properties of iron oxides.306 In the following years, the EA method allowed the formation of many different materials, which were not accessible until then, significantly expanding the range of possible monolithic aerogel materials.
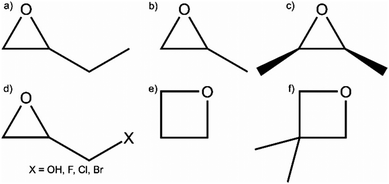 |
| Fig. 4 Examples of epoxides used in different EA methods for the formation of gels. (a) 1,2-Epoxybutane, (b) propylene oxide, (c) cis-2,3-epoxybutane, (d) glycidol (X = OH) and epihalohydrines (X = F, Cl, Br), (e) trimethylene oxide, and (f) 3,3-dimethyloxetane. | |
Propylene oxide (PO) is the most frequently used epoxide for gel formation by the EA method, and therefore we discuss its reaction mechanism in more details. In a first step, the oxygen in the epoxide is protonated by an acid HA, as depicted in Fig. 5a. In a second step, the acid anion A− undergoes a nucleophilic attack, leading to a ring opening reaction (Fig. 5b). Therefore, the epoxide acts as proton scavenger, thus slowly raising the pH. This pH change induces hydrolysis and condensation of the inorganic salts and more importantly slows down the condensation rate, which is highly beneficial to form an inorganic oxide framework.
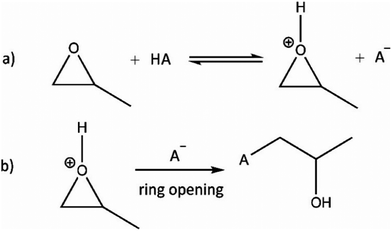 |
| Fig. 5 Reaction schematics for propylene oxide as proton scavenger. In a first step, (a) propylene oxide gets protonated by the acid HA and (b) in a second step the acid anion induces a ring opening reaction through a nucleophilic attack. | |
This type of reaction worked for transition and main group metal oxides as long as the formal oxidation state of the metal in the precursor is larger or equal to 3+.304 The work on Fe2O3303 by Gash et al. was then gradually extended to Fe3O4,307,308 β-FeOOH,306 Fe3C,309 Pd310 and K311 doped iron oxide and iron–chromium mixed oxides gels.312 Gash et al. were also the first to synthesize a metal oxide based aerogel with a divalent metal ion through the EA method.313 However, the formation of divalent metal containing aerogels remained difficult until the discovery of the dispersed inorganic method (DIS), which will be covered later in this Review. Hu et al. expanded the EA method to binary spinel nickel cobaltite aerogels, which were crystallized already at a calcination temperature of 200 °C and which were tested as capacitor materials.314 Also Al2O3 was synthesized,315,316 and by addition of poly(ethylene oxide), the pore size could be modified.317 Heterogeneous catalysts based on Al2O3 with CuO and ZnO for methanol synthesis were obtained by Epple et al.,318 while Hope-Weeks et al. later on showed the co-gelation of aluminium and nickel nitrate salts.319
Combined with non-alkoxide chemistry, the EA method allowed the synthesis of yttria stabilized zirconia.320 The formation mechanism, role of cyclic ether,321 solvents321 and PO322 on surface area and morphology were investigated thoroughly, and alternative synthesis routes were found with different salts and alkoxides.323 Recently, monolithic zirconia aerogels were obtained by a nitric acid assisted EA method.324
High surface area SnO2325 and ZnO326–328 aerogels were synthesized by different groups. Their combination as nanocomposite ZnO–SnO2 showed an efficient degradation of RhB.329
Doping of tin oxide is a widely used strategy towards conducting materials, which are often used as transparent electrodes in LCD,330 LED331 and solar cells.332 Through traditional sol–gel chemistry the synthesis of well-crystalline conducting aerogels is difficult, while the demand for porous conducting networks in battery materials333 and fuel cells334 continuously grows. With the synthesis of indium doped tin oxide aerogels through the EA method with glycidol, this gap could be closed.335 Agrios et al.336 produced transparent conducting aerogels through the EA route with antimony doped tin oxide as electron scavenger in dye sensitized solar cells.337
Until today, the family of accessible materials for aerogels through the EA method has grown a lot. It is possible to gel materials including TiO2,338 V2O5,339 Co3O4,340 UO3,341 Gd2O3,342 many different lanthanide oxides,343 mixed oxides from chloride precursors,344 Ta2O5,345 Mn3O4,346 Y2O3347 and Eu doped Y2O3,348 ThO2,349 and more complex materials such as nickel alumina composites,350 ZnFe2O4,351,352 VFe2Ox,353 La0.85Sr0.15MnO3,354 MnFe2O4,355 NiFe2O4356 and recently simonkolleite.357
Despite all the improvements that came along with the EA method, crack-free monolithic materials from bivalent metal ions (Cu2+, Ni2+, Zn2+, etc.…) were still not easily accessible. Further progress was achieved with the development of the DIS route, a modification of the EA procedure, by Du et al.,358 which involves the addition of polyacrylic acid (PAA) and PO to inorganic salt solutions. PAA acts as both dispersant through its steric hindrance and also as template for gel formation. The carboxyl group is an active nucleation site for the sol, which grows along the PAA backbone and links the colloids together to build a three dimensional network (Scheme 3).
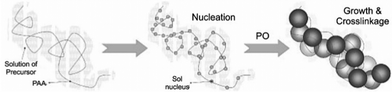 |
| Scheme 3 Nucleation and growth of the sol along the PAA chain via DIS method. Adapted from ref. 358, Copyright 2008, with permission from Elsevier B.V. | |
Compared to the EA approach, this method yields aerogels with less shrinkage and a stronger scaffold. Especially for bivalent metal ions the difficulties of three dimensional crosslinking could be solved.358,359 The DIS method allowed the synthesis of oxidic aerogels from inorganic salts (selected examples are visualized in Fig. 6).358–360 Later, Zhang et al. adapted the DIS method to amorphous nickel oxide based aerogels with enhanced firmness compared to the EA method.361
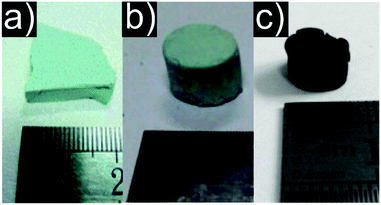 |
| Fig. 6 Representative photographs of aerogels produced by the DIS method: (a) chromia, (b) Cu containing (c) CuO. (a) Adapted with permission from ref. 359, Copyright 2011, The Royal Society of Chemistry and the Centre National de la Recherche Scientifique. (b and c) Adapted from ref. 358, Copyright 2008, with permission from Elsevier B.V. | |
So far, we only discussed materials with metal ions in oxidation states larger than 0. To our knowledge, there is no direct synthesis route available so far for pure metallic aerogels.362 However, there are several other routes to porous metal architectures available in literature.9,363 In a typical sol–gel process, the formation of the metal oxide is often favoured, and to obtain a metal, the oxide needs to be further reduced.364,365
Hope-Weeks et al. showed an elegant solution to this problem by first gelling copper oxide,366 CuO–NiO367 or ZnO–CuO.368 After calcination in an atmosphere containing 5% hydrogen and 95% nitrogen, the copper oxide was reduced to Cu2O and metallic Cu.369 Zhang et al.370–372 managed to obtain pure metallic copper aerogels after annealing under reducing atmosphere.373 Leventis et al. produced pig iron aerogels, an intermediate product of smelting pure iron from ore, by nanosmelting interpenetrated networks of carbon and iron oxide aerogels.374 Recently, the same group introduced a new route to pure metallic iron aerogels by simultaneously gelling iron precursors with a polybenzoxazine network as template. After carbonization and removal of the carbon network a porous metallic iron structure with 7% relative bulk density was achieved.375,376 The group of Zhou et al. recently showed the formation of metallic titanium aerogels by using TiO2 aerogels as template and subsequent magnesiothermic reduction and etching with HCl.377
To sum up, a large variety of aerogels have been produced by molecular approaches. Properties such as high surface area and extremely low density make aerogels promising candidates for applications as catalysts,378,379 supports for catalysts,380 sensors,63 filters,381 cosmic dust collectors,100,382 detectors in particle physics,103,383 thermal insulators,384 interlayer dielectrics,103 optical applications,63 and many others.98,385–388 As a conductive matrix, aerogels could be potentially applied in battery materials, capacitors and components in fuel- or solar cells.389 But despite their enormous application potential, the great morphological features of aerogels are still far from being fully exploited mainly due to their low crystallinity and the difficulties to access compositions with particularly broad functionalities. The reasons for these drawbacks can be found in the underlying sol–gel process, which is still the most popular route to such aerogels. On the one hand, some precursors are not commercially available or only at high costs, and on the other hand their chemistry is not understood and thus not controllable. Additionally, gels obtained through the sol–gel route are most often amorphous and calcination at high temperatures is necessary for crystallization. However, annealing is accompanied by loss of many properties typical for aerogels. Particle growth and coalescence lowers the surface area and the porosity, leading to the collapse of the structure and destruction of the monolithic body. Additionally, phase separation and loss of stoichiometry might occur at high temperatures. Many metal oxides, especially mixed oxides,390 are hard to synthesize in gel form as adjusting and controlling the hydrolysis and condensation rates of the molecular precursors remains a major challenge. With the development of the EA and DIS methods, the range of available materials could be expanded significantly, but the crystallinity has not yet been satisfactorily resolved. Furthermore, pure metallic aerogels cannot directly be synthesized through molecular routes without thermal treatment in reducing atmospheres.
An elegant and likewise powerful method to overcome these drawbacks is to use preformed nanoparticles as building blocks and assemble them into aerogels.391 The difficulty here is to control the assembly behavior of the nanoparticles into a three-dimensional percolating network stable enough to allow further processing without the use of any templates. This approach is covered in the next section of this Review.
5. Particle based aerogels
The availability of an immense library of nanoparticles with different sizes and shapes offers a great opportunity to control and combine the distinct and versatile properties and functionalities by using them as building blocks. Assembling nanoparticles in a bottom-up process, similar to connecting LEGO bricks,29 into aerogel monoliths opens up the possibility to conserve their properties in a truly nanostructured macroscopic bulk material. Such aerogels not only show high porosity, high surface area and low density, but due to the intrinsic properties of their building blocks also new functionalities such as super-paramagnetism,392 ferroelectricity,393 luminescence,394 (photo)catalytic activity99,395 or electrical conductivity389,396 can be introduced to the whole framework. Especially for batteries,397 fuel398 or solar cells337 such porous conducting networks are of high interest. The next part of this Review is dedicated to a general overview of the different steps of assembling preformed nanoparticles into aerogels (Scheme 4).
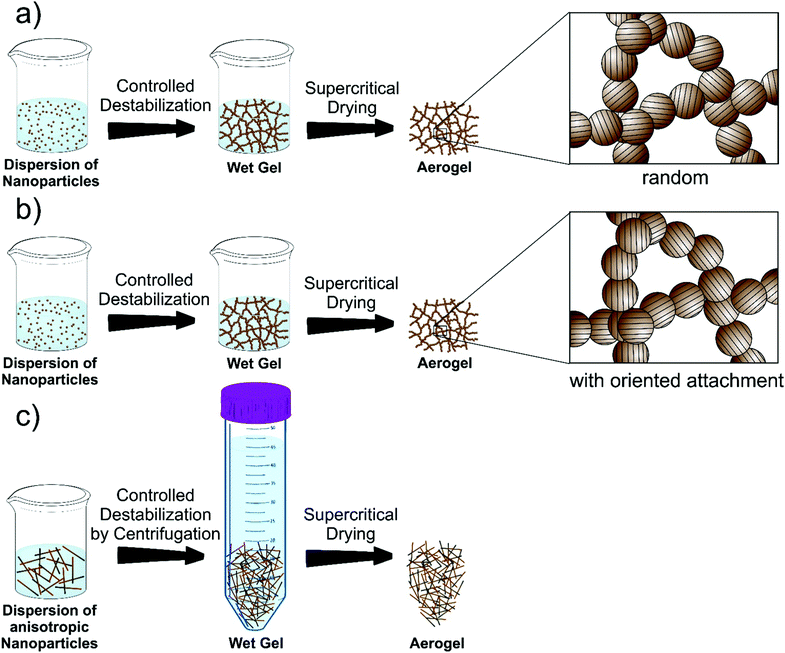 |
| Scheme 4 Overview of the gelation of preformed nanocrystal building blocks into three dimensional macroscopic aerogel monoliths. After dispersing the nanoparticles in high concentration, the controlled destabilization leads to gelation. (a) In most systems the assembly of the nanoparticles occurs at random crystallographic orientation (e.g. chalcogenides, metals,…). (b) Selected systems assemble through an oriented attachment mechanism (e.g. TiO2 and SnO2). (c) Dispersions of anisotropic building blocks can often be destabilized through mild centrifugation (e.g. WOx, Y2O3,…). | |
In a first step, the building blocks need to be synthesized. In most cases, wet chemical processes are applied, because they offer good control over particle size, size distribution and shape. Most importantly, solution approaches enable control over the surface chemistry, which is essential to prevent or minimize agglomeration for good redispersibility in the next step. Nowadays a broad variety of synthesis methods for defined nanoparticles is available, including aqueous109 and nonaqueous sol–gel processes,399,400 polyol route,401 hot-injection,402 heating-up method,403 hydro- and solvothermal processing404 and many others.
The next step is to immerse the building blocks in a highly concentrated dispersion. The concentration needs to be high enough to reach a percolation threshold during gelling. However, it is vital that the particles remain separated without aggregation. Dispersion forces such as van der Waals interactions are omnipresent sources of attraction and depend strongly on the nature of the particles within the medium and are seldom practical to modify.92 Therefore, in an unstable system, the colloids tend to form aggregates and sediment. In colloidal science the objective in this step is to turn the particles into so-called “hard spheres”. This model involves impenetrable spheres that experience an extremely strong repulsion at very close distances but otherwise do not interact which each other. They are subjected to the Brownian motion, but at close proximity van der Waals forces are not able to cause aggregation due to the strong repulsion.92 For a dispersion to remain stable, the nanoparticles typically need to be stabilized sterically by brushes, surfactants or electronic charges to avoid spontaneous aggregation. For any specific system, the balance of attractive and repulsive forces between particles governs the behaviour of the particles, i.e., whether they form a stable dispersion or undergo coagulation.405–407 Each system is a unique combination of stabilizing strategies and solvents used. A generally applicable recipe or unifying concept to prepare concentrated colloidal nanoparticle dispersions is still missing and part of intense research.
The third step towards aerogel formation is the controlled and efficient destabilization of the dispersions. Obviously, the dispersions should not be too stable, otherwise the gelation is not possible anymore. Usually, strategies for destabilization involve photochemical treatment,408 temperature change,396 sonication,393 adding chemicals394 or additional solvents396 for the removal of stabilizing ligands from the surface of the nanoparticles395 or neutralizing surface charges by changing the ionic strength409 or pH410 of the media. As the subtle balance between attractive and repulsive forces is sufficiently disturbed, the attractive interactions gain the upper hand and the dispersed colloids are no longer sterically or electrostatically well separated.92 As a result, the particles become more “sticky” and do not act like hard spheres anymore, but collide and fuse together.411 Due to the large number of colloids in a concentrated dispersion, rapid aggregation occurs. Although van der Waals forces are very weak and thus easily broken, irreversible strong interactions can still be formed upon contact through diffusion of atoms to reduce the surface free energy.412,413 In any case, it is crucial to control the rate of the destabilization process.414,415 If it is not efficient enough, the nanoparticles do not gel but flocculate and, depending on gravitational settling, simply sediment. Under optimal conditions, the colloidal aggregates form a percolating network throughout the entire volume of the sample and a gel is formed.92 In most systems, the nanoparticles fuse upon contact at random orientations and atom diffusion can occur (Scheme 4a). However, TiO2 and SnO2 are among the few systems undergoing oriented attachment upon controlled destabilization (Scheme 4b). This mechanism and the destabilization of anisotropic building blocks (Scheme 4c) will be discussed later in this Review. Finally, in the last step, the wet gel is supercritically dried to obtain the nanoparticle based aerogel.
The assembly of building blocks of just a few nanometres in size to centimetre sized macroscopic structures looks particularly impressive, if we consider that such a process bridges seven orders of magnitude in length scale.
Chalcogenides
The first and presumably best understood example of a particle based aerogel made use of chalcogenide quantum dot semiconductor nanocrystals as building blocks. Boilot et al. investigated the sol to gel transition through oxidative surface ligand removal in capped CdS416–418 colloids with 19F NMR measurements.419 The group of Brock et al. studied the bottom up assembly of chalcogenide nanocrystals into macroscopic aerogels extensively and with great success, laying the foundations for the particle based approach to aerogels. The first results on CdS (Fig. 7a),394,420 ZnS,394 PbS394 and CdSe394 (Fig. 7b) aerogels showed optical properties (i.e., blue-shift) characteristic for quantum confined nanocrystals even in the bulk aerogel.421 Later, also GeSx aerogels were produced.422 The optical properties were related to the pore structure and could be tuned by changing the network density423 through different concentrations of the primary particles,424 their morphology425,426 and subsequent heat treatments.427 However, these aerogels only showed weak emissions due to the large number of trap states leading to nonradiative recombination. This drawback was resolved by the development of CdSe/ZnS core/shell nanoparticle based aerogels (Fig. 8a), where the structural dependence of the optical properties could be bypassed.428 Furthermore, the aggregation kinetics of these core/shell nanoparticles was investigated by time resolved dynamic light scattering,429 and transparent conducting xerogel films were produced directly from the same dispersions.430 Progress and perspective of this emerging field was summarized in several reviews.266,267,431–433 Meanwhile, the family of available aerogels includes selenides (Ag2Se434 and PbSe435) and tellurides (PbTe,436 CdTe,437 Bi2Te3438 and Bi2−xSbxTe3).438 The gelation mechanism of the selenides (and tellurides analogously) involved oxidation of the surface attached thiolates (e.g. by H2O2), leading to the release of Cd2+ ions from the surface of the particles and to the formation of a selenide rich surface. Excess oxidizing agents then oxidized the surface selenide groups, resulting in crosslinked di- or polyselenide species. The mechanism of linking particles through selenide and telluride bonds, respectively, was confirmed by Raman and XPS measurements,437,439 and the pore structure of the aerogels was analysed by 129Xe NMR measurements.440 These chalcogenide aerogels are promising for applications in optoelectronic devices,441 optical sensing,442 remediation of polluted water443 and for quantum dot based photovoltaic devices.444 Recently, the same group managed to synthesize InP445 and Ni2P446 aerogels with similar gelling mechanisms (Fig. 7c).
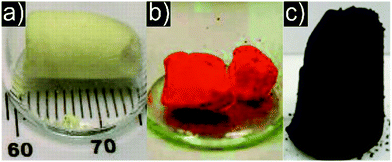 |
| Fig. 7 Representative photographs of aerogel monoliths consisting of (a) CdS, (b) CdSe, and (c) Ni2P nanoparticles. (a) From ref. 394, Copyright 2005, adapted with permission from AAAS. (b) Adapted with permission from ref. 425, Copyright 2008, American Chemical Society. (c) Adapted with permission from ref. 446, Copyright 2014, American Chemical Society. | |
 |
| Fig. 8 Representative photograph of luminescent gels under UV illumination: (a) wet CdSe/ZnS core/shell nanoparticle based gels, (b) CdTe nanoparticle based aerogel. (a) Adapted with permission from ref. 428, Copyright 2007, American Chemical Society. (b) Adapted with permission from ref. 408, Copyright 2008, Wiley-VCH Verlag GmbH & Co. | |
The success of the method developed by Brock et al. inspired other groups to investigate other systems suitable for gelation. Hope-Weeks et al. studied the influence of gold447 and silver448 coatings on CdS on the aerogel morphology and porosity. Yunfeng et al. used different carbohydrates as ligands for the formation of PbTe nanoparticle networks.449 Extremely high exciton lifetimes and large fluorescence quantum yields were achieved by Bigall et al. through the combination of CdSe and CdS nanorods.450 Recently, they synthesized aerogel monoliths from CdSe and CdSe/CdS core/crown nanoplatelets with solely (111) as the exposed facet, strong quantum confinement and high photoluminescence quantum yields.451 Capped CdTe nanocrystals were used by Eychmüller et al. and assembled through a photochemical treatment408 or metal salt addition (Fig. 8b).452,453 Later, this assembly method was extended to CdTe/Au mixed aerogel structures.454,455 Furthermore, the optical properties could be controlled by using different types (ZnSe, CdTe) and different sized semiconductor quantum dots in a single hybrid network. Due to different energy levels and nonradiative transfers from donor to acceptor levels of the different colloids, the emission of the aerogel could be finally tuned to achieve white photoluminescence.456 In another work, enzymes were encapsulated within the gels, resulting in multifunctional hybrids with a sensing and signalling unit in the same spatially confined structure.457 Recently the group showed the removal of the native long-chain organic ligands from a variety of synthesized nanocrystals, replacing them by different inorganic ionic or complexing ligands. Subsequently, the nanoparticle dispersions could be destabilized by the addition of acetate salts with the appropriate coordinating cations such as Cd2+, Pb2+ and Zn2+. The resulting gels showed a complete lack of organic residues with strong linking of the nanocrystals through bridging of the cations.458
Metals
Previously in this Review, the difficulties to synthesize metal aerogels directly from molecular precursors have been shown. However, the use of preformed nanoparticles as building blocks represents a viable alternative, especially because metal nanoparticles are readily available in a large variety.459
Although low-density metal foams are sometimes regarded as the first examples of metal aerogels,460 we want to highlight instead the pioneering work of Eychmüller et al., who in 2009 reported the synthesis of metallic aerogels based on colloidal assembly.461,462 Various noble metal nanoparticles were gelled into single (Ag, Au, Pt, see Fig. 9a) and bimetallic (Ag–Au and Ag–Pt) aerogels. For the formation mechanism they proposed the initial metal nanoparticles to coalesce upon contact by atom diffusion occurring between the connected particles.463 Later, they prepared pure Pd,464 bimetallic as well as alloyed PtxPdy aerogels (Fig. 9b) with excellent electrocatalytic and bioelectrocatalytic activities using enzyme electrodes.465–467
 |
| Fig. 9 TEM images of aerogels consisting of (a) pure metallic platinum and (b) bimetallic platinum–palladium nanoparticles. Scale bars: 50 nm. (a) Adapted with permission from ref. 461, Copyright 2009, Wiley-VCH Verlag GmbH & Co. (b) Adapted with permission from ref. 463, Copyright 2014, American Chemical Society. | |
The formation of the Pd gel involved the assembly of the nanoparticles into short nanowires, followed by the formation of a nanowire network and finally the Pd gel.468 For the enzyme composites a Ca2+ induced assembly of citrate coated Pd nanoparticles was applied.466,467 With the availability of Pd aerogels, another possibility for bi- or even trimetallic noble metal aerogels was opened.463,469 Among their latest results, the group of Eychmüller et al. showed the dopamine-induced assembly of metallic Au nanoparticles into aerogels with high surface area and promising applications in electrocatalysis.470 The group showed the bottom-up design of functional aerogels by assembling alloyed PdNi nanospheres to aerogels for electrocatalysis471 and Pd/ZnO aerogels, which were transferred into ZnPd/ZnO aerogels as catalytic material for methanol steam reforming.472
The group of Arachchige et al. reported the self-assembly of noble metal nanoshells through salt mediation409 and oxidative removal of surface thiolates.473 In a next step, they combined the metal (Ag) and semiconductor (CdSe) colloids to form hybrid aerogels through oxidative surface ligand removal.474 This method allowed the tuning of interfacial reactions leading to different optical properties.
Using amyloid fibers as templates, Mezzenga et al. recently obtained metallic gold aerogels.475
Metal oxides
In spite of significant efforts, for a long time the compositions of nanoparticle based aerogels remained mostly limited to metal chalcogenides,267 noble metals468 and combinations thereof.455 The gelation of colloidal manganese oxide into gels reported by Brock et al. in 2001 remained the only example for metal oxides for about ten years.476 One of the reasons lies in the difficulty to synthesize well-defined, crystalline and dispersible metal oxide nanoparticles. A generally applicable synthesis method was developed by the group of Niederberger. The so-called benzyl alcohol route gave access to a large library of metal oxide nanoparticles covering a broad range of properties including electronic conductivity, ferroelectricity or magnetism.97,477 As these nanomaterials are typically obtained in the form of powders, they lose a major part of their surface area. Assembled into an aerogel, however, the immense surface area of the nanoparticles can be retained. In comparison to aqueous routes, the use of benzyl alcohol as solvent results in nanoparticles with high crystallinity and small crystal sizes due to the stabilizing effect of benzyl alcohol. As a matter of fact, the solvent plays manifold roles as reaction medium, oxygen source, and surface modifying agent. As a result, the non-aqueous sol–gel method represents an ideal tool for the synthesis of nanocrystalline oxidic building blocks for aerogels.97,478
In 2011 the Niederberger group made use of the tendency of titania nanoparticles functionalized with 2-amino-2-(hydroxymethyl)-1,3-propanediol (Trizma, see Fig. 10a) to undergo oriented attachment for the formation of macroscopic aerogels (Scheme 4b and Fig. 11a), finally opening a sustainable approach to metal oxide particle based aerogels.395 The aqueous dispersion was destabilized by a simple heat treatment. Addition of ethanol improved the transparency of the aerogels.392
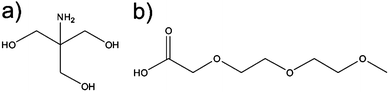 |
| Fig. 10 Chemical structure of (a) 2-amino-2-(hydroxymethyl)-1,3-propanediol (Trizma) and (b) 2-[2-(2-methoxyethoxy) ethoxy] acetic acid (MEEAA). | |
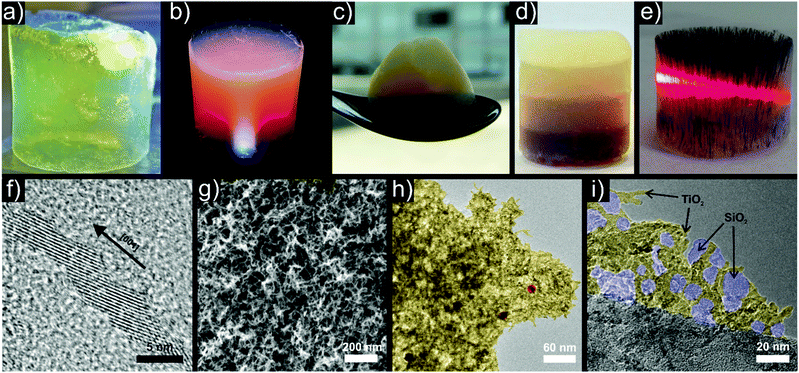 |
| Fig. 11 Representative examples of titania based aerogels with the incorporation of different functional nanocrystals. Photographs of aerogels based on (a) pure anatase, (b) anatase with Au nanoparticles, (c) anatase – WOx nanowires – Au, (d) layered anatase with four different concentrations of magnetite increasing from top to bottom and (e) magnetically textured anatase – magnetite with a laser beam passing through the aerogel. Selected electron microscopy images: (f) HRTEM of oriented attached anatase building blocks, (g) SEM of a pure anatase aerogel, (h) HRTEM of anatase (yellow) – Au (red) aerogel, (i) anatase (yellow) – silica (blue) composite aerogel. (a) Adapted with permission from ref. 487, Copyright 2005, Wiley-VCH Verlag GmbH & Co. KGaA. | |
Co-assembly of different types of nanoparticles in the same dispersion enabled the formation of multicomponent aerogels. The concept of introducing guests to a host, thereby combining the properties potentially even in a synergistical way, has already been shown for catalytically active sol–gel derived aerogels,147 but is also known for silica aerogels.479–482 In the latter case, however, the silica matrix always represents an amorphous (and typically not very functional) host, whereas in the nanoparticle approach introduction of additional functional materials within a crystalline matrix is possible.
The addition of gold nanoparticles (Fig. 11b, high resolution TEM (HRTEM) image in Fig. 11h) improved the photocatalytic dye degradation of rhodamine B by acting as electron sinks, reducing the recombination rate of the electron–hole pairs and thus resulting in longer lifetimes of the charge carriers.395 The photocatalytic properties can be tailored further through incorporation of WOx nanowires and gold nanoparticles into titania (Fig. 11c).483 The addition of gold led to a higher performance in OH radical generation, whereas the addition of WOx increased the degradation rate of methylene blue. Together the two types of building blocks gave rise to an overall increased activity of both OH radical production and MB degradation, thereby combining their beneficial effects.483
Addition of negatively charged silica particles, obtained by the Stöber method, to a dispersion of positively charged Trizma functionalized titania nanoparticles resulted after gelling in an interconnected titania–silica framework (Fig. 11i).484 Such a composite combines the photocatalytic activity of the anatase particles with the extensive possibilities of silica surface functionalization.
Furthermore, it turned out that the ternary composite aerogel consisting of a titania matrix, Pt nanoparticles and reduced graphene oxide is well suited for photocatalytic hydrogen production.485
The use of superparamagnetic Fe3O4 nanoparticles as building blocks offers several interesting possibilities. Incorporated in a non-magnetic host such as titania they enable contactless manipulation of the aerogel monolith by a magnet.392 Different dispersion concentrations and magnetic fields during gelation gave rise to anisotropic aerogels such as layered monoliths with gradients in Fe3O4 concentration (Fig. 11d) or with magnetic texture (Fig. 11e) along the magnetic field lines.
Common to all these systems is the destabilization of aqueous dispersions of the Trizma stabilized anatase nanoparticles, which builds up the matrix. The selective removal of Trizma from {001} facets by water induces oriented attachment in a preferential direction over several length scales (Fig. 11f).486,487 Due to imperfect assembly events, this process allows branching and by increasing the particle concentration in the initial dispersion, a 3-dimensional and percolating network forms, resulting in a gel (Fig. 11g). In this case, the tendency of titania to undergo oriented attachment greatly facilitates the formation of porous gels (Scheme 4b).
Another system, which undergoes oriented attachment is SnO2, when exposed to hydrothermal conditions.488–490 SnO2 is a wide-band-gap material, but it can be made conductive by doping. By traditional aqueous sol–gel synthesis it is challenging to produce aerogels of crystalline conducting oxides. However, they are readily available as nanoparticles with high crystallinity.331,491 Therefore, antimony doped tin oxide (ATO) nanoparticles were used as building blocks for conductive aerogels.396 Destabilization of concentrated dispersions by heat treatment led to the gelation of the building blocks with partial oriented attachment.396 After annealing, conductivity over the whole monolithic body (Fig. 12a) could be induced without destroying the integrity and microstructure of the aerogel (HRTEM image in Fig. 12e before and SEM image in Fig. 12f after annealing). Recently, different strategies were developed to improve the electrical conductivity of these conducting aerogels without losing the porous microstructure.492
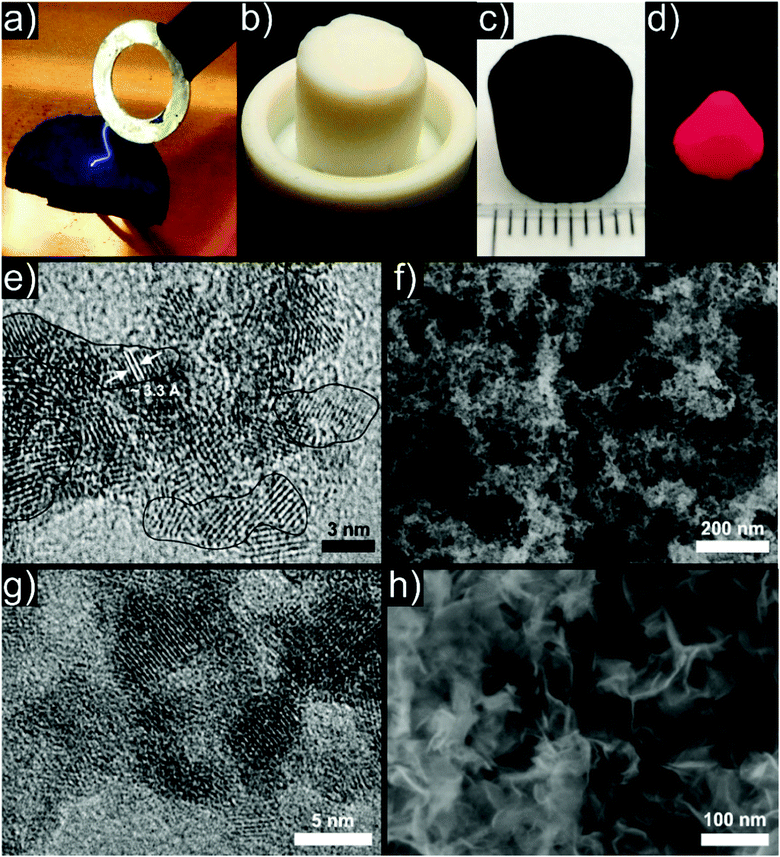 |
| Fig. 12 Representative photographs of particle based aerogel monoliths composed of (a) conducting ATO, (b) BaTiO3, (c) Cu3N and (d) Eu3+ doped Y2O3. Electron microscopy images of (e) ATO aerogel before and (f) after heat treatment. (g) HRTEM image of BaTiO3 nanoparticles and (h) SEM image of Y2O3 nanosheets in the corresponding aerogels. | |
With the observation that 2-[2-(2-methoxyethoxy)ethoxy] acetic acid (MEEAA, Fig. 10b) functionalized nanoparticles493 synthesized by the benzyl alcohol route can easily be dispersed in different organic solvents in high concentration,393 another very versatile route to aerogels was discovered. A first example with this method included the formation of ferroelectric barium titanate aerogels (Fig. 12b), introducing a new type of functionality. The addition of water and heat to a concentrated ethanolic dispersion of BaTiO3 nanocrystals of about 5 nm in size led to an effective destabilization process and eventually to a gel.393 HRTEM investigations indicated another gelation mechanism than oriented attachment, as the lattice fringes of adjacent nanocrystals are randomly distributed and no oriented attachment is observed (Scheme 4a and Fig. 12g). In both systems water plays a decisive role as destabilizing agent. In case of BaTiO3, it leads to a nonselective removal of MEEAA from the surface and subsequent fusion of colliding nanocrystals. Although BaTiO3 is just one example of such a rapidly induced destabilization process beyond oriented attachment, the method with MEEAA functionalization is straightforward. Considering that nanoparticles prepared by the benzyl alcohol route often have a comparable surface chemistry,477 this method could potentially be applied to other metal oxide nanoparticles, laying the foundation for a general synthesis strategy to crystalline oxide aerogels with broader compositional and functional variety.
Using a different method, many monolithic perovskite gels have been fabricated by another group.494
Recently, the family of aerogels was expanded to another class of materials. Starting from very small Cu3N nanoparticles,495 the Niederberger group presented a transition metal nitride aerogel (Fig. 12c). Here, no surface functionalization nor chemical crosslinkers were needed to gel the samples.496
Anisotropic building blocks
Up to here we mainly discussed aerogels made of spherical nanoparticles as building blocks. But nanocrystals are of course available in an immense variety of sizes and shapes. Especially anisotropic building blocks497–500 such as nanowires (1D) or nanosheets (2D) are attractive, and therefore the question arises, whether it is possible to form aerogels based on building blocks of reduced dimensionality. Jung et al. reported the assembly of nanowires (Ag, Si, CNT, MnO2) into 3D networks, if the critical concentration of the anisotropic colloidal dispersions was reached during solvent evaporation.501 Furthermore, copper nanowires were freeze-casted in water and after subsequent vacuum drying a monolithic copper aerogel could be produced.502 A simple approach to alumina based aerogels was carried out by Hayase et al. by aggregating boehmite nanofibers through a pH change from acidic to weakly basic.410 Recently, Niederberger et al. used ultrathin tungsten oxide nanowires with very high aspect ratio as building blocks to synthesize monolithic aerogels (Scheme 4c).503 Jung et al. also investigated the assembly of 2D nanosheets (MoS2, h-BN) into macroscopic aerogels.501 Recently, another approach for BN aerogels was found involving freeze drying of an aqueous dispersion of BN nanosheets obtained by an urea assisted ball milling process and subsequent exfoliation.504 Furthermore, MoO2 nanosheets were assembled by freeze drying. Contrary to most nanocrystal based systems, no organic stabilizers were needed and therefore no organic impurities could be found in the resulting aerogel.505 These aerogel architectures showed excellent performance in applications for lithium–air battery materials.506
The Niederberger group recently published a method to produce flexible hybrid aerogels based on spinel-type metal oxides and reduced graphene oxide sheets as anode materials for lithium ion batteries with greatly enhanced rate capability and long-term stability.397 Moreover, they introduced a centrifugation assisted gelation method to produce monolithic Y2O3 aerogels from nanosheets (Scheme 4c). By doping and co-doping with Eu3+ and Tb3+, luminescent aerogels with tunable color emissions from red to green under UV excitation were fabricated (Fig. 12d and h). Moreover, the as-prepared gels and aerogels exhibit excellent adsorption capacities for organic dyes.507 Recently, WS2 and MoS2 aerogels were produced by freeze-drying and thermal decomposition of the metal chalcogenide precursors resulting in aerogels with layered morphologies.508
These examples show that the synthesis of aerogels from preformed nanocrystals is not limited to isotropic particles, offering a completely new aspect in aerogel research not accessible by molecular sol–gel routes. However, the gelling mechanisms and the various forces involved in the assembly process of anisotropic particles differ significantly and remain to be explored.
6. Conclusions & outlook
Nanoparticles are the ideal building blocks for the creation of materials. They show physical properties, which vary systematically as a function of size, but also depending on their mutual arrangement enable collective or synergistic properties. Most of the efforts were dedicated to the assembly of nanoparticles into ordered and dense structures. But in spite of all the progress, it is not yet possible to produce such assemblies with macroscopic dimensions. Aerogels, on the other hand, are nanostructured bulk materials, however with completely contrary properties: they have a low density, high porosity, large surface area and are completely disordered. But these characteristics are advantageous in terms of molecular diffusion.41,42 One gram of TiO2 aerogel combines the surface area of more than a tennis field with a percolating pore system for molecular transport.483 All these properties make aerogels unique candidates for applications involving transport of matter and charges on the nanoscale.43
After a short historical perspective on colloidal particles and the pioneering work of Kistler on supercritical drying, we discussed the preparation of a broad range of aerogel materials (however excluding silica and carbon), starting from molecular sol–gel routes involving hydrolysis and condensation reactions, which allow for the formation of highly multifunctional materials with distinctive intrinsic properties. The major issue for these materials is their typically amorphous nature, which is also a characteristic of silica aerogels. With the discovery of new approaches like the EA and DIS methods, the range of accessible compositions was significantly expanded by facilitating control over the hydrolysis and condensation rates and by introducing steric guidance by the polyacrylic acid.
A major advancement on the way to further increase the compositional variety and architectural complexity and to overcome the amorphous nature can be achieved by switching from molecular precursors to the assembly of preformed, nanocrystalline colloids. Since the early example of quantum dots, many different nanoparticles have been processed into crystalline aerogels including metals, metal oxides and mixtures thereof. Most recently, also anisotropic nanostructures such as nanowires or nanosheets were assembled into monolithic aerogels of macroscopic sizes.
In spite of all the progress on nanoparticle based aerogels, it is clear that we are still just at the beginning. On an incredible pace new nanoparticles with different compositions, sizes, and shapes are synthesized and published, and only a minor fraction of them has been processed into aerogels. The possibilities to use and combine these nanoparticles as a large toolbox of building blocks are only limited by imagination, and many new complex aerogel architectures will be produced in the coming years.
But in spite of all the enthusiasm for these disordered and porous materials, there are several challenges to overcome not only on the synthesis side, but also on the application side. For example, a great deal of efforts has been dedicated to the preparation of monolithic aerogels. But because most of the studied applications were performed in liquid medium,464–466 the monolithic bodies irreversibly disintegrate into aggregates with micron size once in contact with a liquid.395,485 Although the fragments typically still showed enhanced photocatalytic activity compared to a mixture of the corresponding nanopowders, all the benefits of a monolithic body, especially hierarchical porosity, close interaction between the different nanoparticle building blocks of the aerogels, simple isolation of the photocatalyst after the reaction, large contact area between photocatalyst and reactant are fully, or at least partly lost. Although a careful thermal treatment increases the mechanical stability of aerogel monoliths, they typically remain rather fragile, and it is hardly possible to use them in liquid media without destroying their monolithic shape.
One promising application of monolithic aerogels is in gas phase reactions. As a matter of fact, for reactions such as the production of solar fuels it seems to be even more promising to focus on gas phase solar fuel (e.g. fuels from CO2 with the use of sunlight) reactions, or, as Geoffrey Ozin wrote in his recent perspective: “It is becoming increasingly apparent that the solar refinery of the future cannot be limited to the historical approach of aqueous-phase biomimetics, which is often characterized by low […] conversion efficiencies. A shift to gasphase heterogeneous catalysis is occurring and looks promising in terms of its ability to deliver high […] conversion efficiencies with the added advantage of being able to interface seamlessly with existing chemical and petrochemical industrial infrastructure.”509 The development of aerogels as all-active highly porous gas-phase catalysts without the need of an inactive catalyst support (e.g. silica-based aerogel catalysts)479 will allow for very efficient conversion rates. We expect that results in this direction will lead to a breakthrough in the field of aerogel research and will have a significant impact.
Acknowledgements
We gratefully acknowledge the financial support by the Swiss National Science Foundation (project no. 200021_165888) and by ETH Zurich. The authors thank Prof. Jan Vermant and Dr. Eric Furst of ETH Zurich and Prof. Norman Wagner of the University of Delaware for fruitful discussions concerning the historical view of gels.
References
- G. A. Ozin, Chem. Commun., 2000, 419–432 RSC
.
- C. Sanchez, G. Soler-Illia, F. Ribot, T. Lalot, C. R. Mayer and V. Cabuil, Chem. Mater., 2001, 13, 3061–3083 CrossRef CAS
.
- G. M. Whitesides and B. Grzybowski, Science, 2002, 295, 2418–2421 CrossRef CAS PubMed
.
- A. L. Rogach, D. V. Talapin, E. V. Shevchenko, A. Kornowski, M. Haase and H. Weller, Adv. Funct. Mater., 2002, 12, 653–664 CrossRef CAS
.
- S. Veprek and M. J. G. Veprek-Heijman, Surf. Coat. Technol., 2008, 202, 5063–5073 CrossRef CAS
.
- M. C. Orilall and U. Wiesner, Chem. Soc. Rev., 2011, 40, 520–535 RSC
.
- J.-W. Liu, H.-W. Liang and S.-H. Yu, Chem. Rev., 2012, 112, 4770–4799 CrossRef CAS PubMed
.
- D. Koziej, A. Lauria and M. Niederberger, Adv. Mater., 2014, 26, 235–257 CrossRef CAS PubMed
.
- N. Kranzlin and M. Niederberger, Mater. Horiz., 2015, 2, 359–377 RSC
.
- K. Muellen, Angew. Chem., Int. Ed., 2015, 54, 10040–10042 CrossRef CAS PubMed
.
- W. J. Stark, P. R. Stoessel, W. Wohlleben and A. Hafner, Chem. Soc. Rev., 2015, 44, 5793–5805 RSC
.
- L. Xu, W. Ma, L. Wang, C. Xu, H. Kuang and N. A. Kotov, Chem. Soc. Rev., 2013, 42, 3114–3126 RSC
.
- M. P. Pileni, Acc. Chem. Res., 2007, 40, 685–693 CrossRef CAS PubMed
.
- Y. K. Kho, A. Iwase, W. Y. Teoh, L. Maedler, A. Kudo and R. Amal, J. Phys. Chem. C, 2010, 114, 2821–2829 CAS
.
- Z. Nie, A. Petukhova and E. Kumacheva, Nat. Nanotechnol., 2010, 5, 15–25 CrossRef CAS PubMed
.
- Y. Liang, Y. Li, H. Wang, J. Zhou, J. Wang, T. Regier and H. Dai, Nat. Mater., 2011, 10, 780–786 CrossRef CAS PubMed
.
- J. Park, E. Lee, N. M. Hwang, M. S. Kang, S. C. Kim, Y. Hwang, J. G. Park, H. J. Noh, J. Y. Kini, J. H. Park and T. Hyeon, Angew. Chem., Int. Ed., 2005, 44, 2872–2877 CrossRef CAS PubMed
.
- X. Wang, J. Zhuang, Q. Peng and Y. D. Li, Nature, 2005, 437, 121–124 CrossRef CAS PubMed
.
- J. Park, J. Joo, S. G. Kwon, Y. Jang and T. Hyeon, Angew. Chem., Int. Ed., 2007, 46, 4630–4660 CrossRef CAS PubMed
.
- M. Niederberger, Acc. Chem. Res., 2007, 40, 793–800 CrossRef CAS PubMed
.
- D. V. Talapin, J.-S. Lee, M. V. Kovalenko and E. V. Shevchenko, Chem. Rev., 2010, 110, 389–458 CrossRef CAS PubMed
.
- H. Goesmann and C. Feldmann, Angew. Chem., Int. Ed., 2010, 49, 1362–1395 CrossRef CAS PubMed
.
- M. Yarema, R. Caputo and M. V. Kovalenko, Nanoscale, 2013, 5, 8398–8410 RSC
.
- Z. Y. Tang and N. A. Kotov, Adv. Mater., 2005, 17, 951–962 CrossRef CAS
.
- S. Srivastava and N. A. Kotov, Soft Matter, 2009, 5, 1146–1156 RSC
.
- S. J. Barrow, A. M. Funston, X. Wei and P. Mulvaney, Nano Today, 2013, 8, 138–167 CrossRef CAS
.
- M. Stefik, S. Guldin, S. Vignolini, U. Wiesner and U. Steiner, Chem. Soc. Rev., 2015, 44, 5076–5091 RSC
.
- A. P. Alivisatos, ACS Nano, 2008, 2, 1514–1516 CrossRef CAS PubMed
.
- D. V. Talapin, ACS Nano, 2008, 2, 1097–1100 CrossRef CAS PubMed
.
- Y. Nakagawa, H. Kageyama, Y. Oaki and H. Imai, J. Am. Chem. Soc., 2014, 136, 3716–3719 CrossRef CAS PubMed
.
- K. Miszta, J. de Graaf, G. Bertoni, D. Dorfs, R. Brescia, S. Marras, L. Ceseracciu, R. Cingolani, R. van Roij, M. Dijkstra and L. Manna, Nat. Mater., 2011, 10, 872–876 CrossRef CAS PubMed
.
- D. V. Talapin, E. V. Shevchenko, M. I. Bodnarchuk, X. Ye, J. Chen and C. B. Murray, Nature, 2009, 461, 964–967 CrossRef CAS PubMed
.
- S. Disch, E. Wetterskog, R. P. Hermann, G. Salazar-Alvarez, P. Busch, T. Brueckel, L. Bergstroem and S. Kamali, Nano Lett., 2011, 11, 1651–1656 CrossRef CAS PubMed
.
- M. P. Pileni, Acc. Chem. Res., 2008, 41, 1799–1809 CrossRef CAS PubMed
.
- S. Shaw and L. Cademartiri, Adv. Mater., 2013, 25, 4829–4844 CrossRef CAS PubMed
.
- M. Yang and N. A. Kotov, J. Mater. Chem., 2011, 21, 6775–6792 RSC
.
- P. Yang, D. Zhao, D. I. Margolese, B. F. Chmelka and G. D. Stucky, Chem. Mater., 1999, 11, 2813–2826 CrossRef CAS
.
- Y. Meng, D. Gu, F. Zhang, Y. Shi, H. Yang, Z. Li, C. Yu, B. Tu and D. Zhao, Angew. Chem., 2005, 117, 7215–7221 CrossRef
.
- Y. Deng, J. Wei, Z. Sun and D. Zhao, Chem. Soc. Rev., 2013, 42, 4054–4070 RSC
.
- A. Feinle, M. S. Elsaesser and N. Hüsing, Chem. Soc. Rev., 2016, 45, 3377–3399 RSC
.
- J. W. Long and D. R. Rolison, Acc. Chem. Res., 2007, 40, 854–862 CrossRef CAS PubMed
.
- D. R. Rolison, Science, 2003, 299, 1698–1701 CrossRef CAS PubMed
.
-
S. L. Brock, Nanoscale Materials in Chemistry, John Wiley & Sons, Inc., 2009, pp. 207–241 Search PubMed
.
- IUPAC, Compendium of Chemical Terminology, 2nd ed. (the “Gold Book”), Blackwell Scientific Publications, Oxford, 1997 Search PubMed
.
- R. Brown, Philos. Mag., 1828, 4, 161–173 Search PubMed
.
- A. Einstein, Ann. Phys., 1905, 17, 549–560 CrossRef CAS
.
- J. Perrin, Ann. Chim. Phys., 1909, 18, 5–114 CAS
.
-
C. J. Brinker and G. W. Scherer, Sol–Gel Science: The Physics and Chemistry of Sol–Gel Processing, Academic Press, San Diego, 1990 Search PubMed
.
-
J. D. Wright and N. A. J. M. Sommerdijk, Sol-Gel Materials: Chemistry and Applications, Taylor & Francis, 2000 Search PubMed
.
-
H. E. Bergna and W. O. Roberts, Colloidal Silica - Fundamentals and Applications, Taylor & Francis, 2006 Search PubMed
.
- F. J. Heiligtag and M. Niederberger, Mater. Today, 2013, 16, 262–271 CrossRef CAS
.
- J. B. V. Helmont, De lithiase, 1644, 28 Search PubMed
.
- T. Bergmann, De terra silicea, 1779, 4 Search PubMed
.
- M. Faraday, Philos. Trans. R. Soc. London, 1857, 147, 145–181 CrossRef
.
- M. Ebelmen, Ann. Chim., 1846, 57, 319–355 CrossRef
.
- L. Troost and P. Hautefeuille, Ann. Chim. Phys., 1876, 7, 452–479 Search PubMed
.
- E. Grimaux, Compt. Rend., 1884, 98, 105 Search PubMed
.
- T. Graham, J. Chem. Soc., 1864, 17, 318–327 RSC
.
- S. S. Kistler, J. Phys. Chem., 1931, 36, 52–64 CrossRef
.
-
J. Fricke, Aerogels, Springer London, Limited, 1986 Search PubMed
.
- S. S. Kistler, Nature, 1931, 127, 741 CrossRef CAS
.
- J. Fricke and A. Emmerling, J. Am. Chem. Soc., 1992, 75, 2027–2035 CAS
.
- N. Hüsing and U. Schubert, Angew. Chem., Int. Ed., 1998, 37, 22–45 CrossRef
.
-
R. C. Mehrotra and A. Singh, in Progress in Inorganic Chemistry, John Wiley & Sons, Inc., 2007, pp. 239–454 Search PubMed
.
- C. B. Hurd, Chem. Rev., 1938, 22, 403–422 CrossRef CAS
.
-
E. I. Robinsky, Thickened Tailings Disposal in the Mining Industry, E. I. Robinsky Associates, Limited, 1999 Search PubMed
.
- S. D. Holdsworth, J. Texture Stud., 1971, 2, 393–418 CrossRef
.
- P. Meakin, Phys. Rev. Lett., 1983, 51, 1119–1122 CrossRef
.
- D. A. Weitz and M. Oliveria, Phys. Rev. Lett., 1984, 52, 1433–1436 CrossRef CAS
.
- P. Meakin, Adv. Colloid Interface Sci., 1987, 28, 249–331 CrossRef
.
- D. J. Pine, D. A. Weitz, P. M. Chaikin and E. Herbolzheimer, Phys. Rev. Lett., 1988, 60, 1134–1137 CrossRef CAS PubMed
.
- D. W. Schaefer, T. Rieker, M. Agamalian, J. S. Lin, D. Fischer, S. Sukumaran, C. Chen, G. Beaucage, C. Herd and J. Ivie, J. Appl. Crystallogr., 2000, 33, 587–591 CrossRef CAS
.
- E. Mendes, R. Oeser, C. Hayes, F. Boué and J. Bastide, Macromolecules, 1996, 29, 5574–5584 CrossRef CAS
.
- M. Stieger, W. Richtering, J. S. Pedersen and P. Lindner, J. Chem. Phys., 2004, 120, 6197–6206 CrossRef CAS PubMed
.
- C. J. Dibble, M. Kogan and M. J. Solomon, Phys. Rev. E: Stat., Nonlinear, Soft Matter Phys., 2006, 74, 041403 CrossRef PubMed
.
- L. C. Hsiao, M. J. Solomon, K. A. Whitaker and E. M. Furst, J. Rheol., 2014, 58, 1485–1504 CrossRef CAS
.
- W. Kob, C. Donati, S. J. Plimpton, P. H. Poole and S. C. Glotzer, Phys. Rev. Lett., 1997, 79, 2827–2830 CrossRef CAS
.
- R. N. Zia, B. J. Landrum and W. B. Russel, J. Rheol., 2014, 58, 1121–1157 CrossRef CAS
.
- R. N. Zia, J. W. Swan and Y. Su, J. Chem. Phys., 2015, 143, 224901 CrossRef PubMed
.
- V. Trappe, V. Prasad, L. Cipelletti, P. N. Segre and D. A. Weitz, Nature, 2001, 411, 772–775 CrossRef CAS PubMed
.
- H. H. Winter, M. Siebenbürger, D. Hajnal, O. Henrich, M. Fuchs and M. Ballauff, Rheol. Acta, 2009, 48, 747–753 CrossRef CAS
.
- M. Siebenbürger, M. Fuchs, H. Winter and M. Ballauff, J. Rheol., 2009, 53, 707–726 CrossRef
.
- A. P. R. Eberle, N. J. Wagner and R. Castañeda-Priego, Phys. Rev. Lett., 2011, 106, 105704 CrossRef PubMed
.
- G. L. Hunter and E. R. Weeks, Rep. Prog. Phys., 2012, 75, 066501 CrossRef PubMed
.
- A. P. R. Eberle, R. Castañeda-Priego, J. M. Kim and N. J. Wagner, Langmuir, 2012, 28, 1866–1878 CrossRef CAS PubMed
.
- J. M. Kim, J. Fang, A. P. R. Eberle, R. Castañeda-Priego and N. J. Wagner, Phys. Rev. Lett., 2013, 110, 208302 CrossRef PubMed
.
-
C. P. Royall, S. R. Williams and H. Tanaka, 2014, arXiv:1409.5469 [cond-mat.soft].
- S. Asakura and F. Oosawa, J. Polym. Sci., 1958, 33, 183–192 CrossRef CAS
.
-
H. N. W. Lekkerkerker and R. Tuinier, Colloids and the Depletion Interaction, Springer, Netherlands, 2011 Search PubMed
.
-
D. Stauffer and A. Aharony, Introduction to percolation theory, Taylor & Francis, London, 2nd edn, 1992 Search PubMed
.
- Z. Emanuela, J. Phys.: Condens. Matter, 2007, 19, 323101 CrossRef
.
-
J. Mewis and N. J. Wagner, Colloidal Suspension Rheology, Cambridge University Press, 2011 Search PubMed
.
-
R. K. Iler, The Chemistry of Silica: Solubility, Polymerization, Colloid and Surface Properties and Biochemistry of Silica, John Wiley & Sons, New York, 1979 Search PubMed
.
- R. Dhaubhadel, C. S. Gerving, A. Chakrabarti and C. M. Sorensen, Aerosol Sci. Technol., 2007, 41, 804–810 CrossRef CAS
.
- A. Freytag, S. Sánchez-Paradinas, S. Naskar, N. Wendt, M. Colombo, G. Pugliese, J. Poppe, C. Demirci, I. Kretschmer, D. W. Bahnemann, P. Behrens and N. C. Bigall, Angew. Chem., Int. Ed., 2016, 55, 1200–1203 CrossRef CAS PubMed
.
- L. Ren, S. Cui, F. Cao and Q. Guo, Angew. Chem., Int. Ed., 2014, 53, 10147–10149 CrossRef CAS PubMed
.
-
M. Niederberger and N. Pinna, Metal Oxide Nanoparticles in Inorganic Solvents – Synthesis, Formation, Assembly and Application, Springer, 2009 Search PubMed
.
-
J. Fricke and A. Emmerling, in Chemistry, Spectroscopy and Applications of Sol–Gel Glasses, ed. R. Reisfeld and C. K. Jjørgensen, Springer, Berlin Heidelberg, 1992, ch. 2, vol. 77, pp. 37–87 Search PubMed
.
- A. C. Pierre and G. M. Pajonk, Chem. Rev., 2002, 102, 4243–4266 CrossRef CAS PubMed
.
-
M. A. Aegerter, N. Leventis and M. M. Koebel, Aerogels Handbook, Springer, Dordrecht, 2011 Search PubMed
.
- H. Tamon, H. Ishizaka, M. Mikami and M. Okazaki, Carbon, 1997, 35, 791–796 CrossRef CAS
.
- A. E. Aliev, J. Oh, M. E. Kozlov, A. A. Kuznetsov, S. Fang, A. F. Fonseca, R. Ovalle, M. D. Lima, M. H. Haque, Y. N. Gartstein, M. Zhang, A. A. Zakhidov and R. H. Baughman, Science, 2009, 323, 1575–1578 CrossRef CAS PubMed
.
- J. L. Gurav, I. K. Jung, H. H. Park, E. S. Kang and D. Y. Nadargi, J. Nanomater., 2010, 2010, 409310 Search PubMed
.
- S. Nardecchia, D. Carriazo, M. L. Ferrer, M. C. Gutierrez and F. del Monte, Chem. Soc. Rev., 2013, 42, 794–830 RSC
.
- H. Maleki, L. Durães and A. Portugal, J. Non-Cryst. Solids, 2014, 385, 55–74 CrossRef CAS
.
- A. Allahbakhsh and A. R. Bahramian, Nanoscale, 2015, 7, 14139–14158 RSC
.
- A. Du, B. Zhou, Z. Zhang and J. Shen, Materials, 2013, 6, 941–968 CrossRef CAS
.
- S. J. Teichner, G. A. Nicolaon, M. A. Vicarini and G. E. E. Gardes, Adv. Colloid Interface Sci., 1976, 5, 245–273 CrossRef CAS
.
-
J. P. Jolivet, M. Henry and J. Livage, Metal Oxide Chemistry and Synthesis: From Solution to Solid State, Wiley, 2000 Search PubMed
.
- J. Livage, M. Henry and C. Sanchez, Prog. Solid State Chem., 1988, 18, 259–341 CrossRef CAS
.
- G. W. Scherer, Adv. Colloid Interface Sci., 1998, 76–77, 321–339 CrossRef
.
- G. Reichenauer, Part. Part. Syst. Charact., 2004, 21, 117–127 CrossRef
.
- R. M. Stroud, J. W. Long, J. J. Pietron and D. R. Rolison, J. Non-Cryst. Solids, 2004, 350, 277–284 CrossRef CAS
.
- B. E. Yoldas, J. Mater. Sci., 1975, 10, 1856–1860 CrossRef CAS
.
- B. E. Yoldas, Am. Ceram. Soc. Bull., 1975, 54, 289–290 CAS
.
- B. E. Yoldas, Am. Ceram. Soc. Bull., 1975, 54, 286–288 CAS
.
- B. E. Yoldas, J. Mater. Sci., 1976, 11, 465–470 CrossRef CAS
.
- U. Janosovits, G. Ziegler, U. Scharf and A. Wokaun, J. Non-Cryst. Solids, 1997, 210, 1–13 CrossRef CAS
.
- J. F. Poco, J. H. Satcher Jr and L. W. Hrubesh, J. Non-Cryst. Solids, 2001, 285, 57–63 CrossRef CAS
.
- E. Ponthieu, J. Grimblot, E. Elaloui and G. M. Pajonk, J. Mater. Chem., 1993, 3, 287–293 RSC
.
- J. S. Raschko, R. J. Willey and J. B. Peri, Chem. Eng. Commun., 1991, 104, 167–176 CrossRef CAS
.
- C. Hoang-Van, B. Pommier, R. Harivololona and P. Pichat, J. Non-Cryst. Solids, 1992, 145, 250–254 CrossRef CAS
.
-
C. Hoang-Van, R. Harivololona and B. Pommier, in Stud. Surf. Sci. Catal., ed. G. Poncelet, J. Martens, B. Delmon, P. A. Jacobs and P. Grange, Elsevier, 1995, vol. 91, pp. 435–443 Search PubMed
.
- T. Osaki, T. Horiuchi, T. Sugiyama, K. Suzuki and T. Mori, J. Non-Cryst. Solids, 1998, 225, 111–114 CrossRef CAS
.
- T. Horiuchi, L. Chen, T. Osaki and T. Mori, Catal. Lett., 2001, 72, 77–81 CrossRef CAS
.
- L. Courthéoux, F. Popa, E. Gautron, S. Rossignol and C. Kappenstein, J. Non-Cryst. Solids, 2004, 350, 113–119 CrossRef
.
- V. Stengl, S. Bakardjieva, M. Marikova, J. Subrt, F. Oplustil and M. Olsanska, Ceram.-Silik., 2003, 47, 175–180 CAS
.
- S. M. Jones, Meteorit. Planet. Sci., 2010, 45, 91–98 CAS
.
- M. Schneider and A. Baiker, Catal. Today, 1997, 35, 339–365 CrossRef CAS
.
- M. Schneider and A. Baiker, J. Mater. Chem., 1992, 2, 587–589 RSC
.
- O. Masson, V. Rieux, R. Guinebretière and A. Dauger, Nanostruct. Mater., 1996, 7, 725–731 CrossRef CAS
.
- B. Malinowska, J. Walendziewski, D. Robert, J. V. Weber and M. Stolarski, Int. J. Photoenergy, 2003, 5, 147–152 CrossRef CAS
.
- R. Sui, S. Liu, G. A. Lajoie and P. A. Charpentier, J. Sep. Sci., 2010, 33, 1604–1609 CrossRef CAS PubMed
.
- P. A. DeSario, J. J. Pietron, D. H. Taffa, R. Compton, S. Schünemann, R. Marschall, T. H. Brintlinger, R. M. Stroud, M. Wark, J. C. Owrutsky and D. R. Rolison, J. Phys. Chem. C, 2015, 119, 17529–17538 CAS
.
- R. Nistico and G. Magnacca, RSC Adv., 2015, 5, 14333–14340 RSC
.
- C.-Y. Kim and Y.-S. Park, J. Nanosci. Nanotechnol., 2015, 15, 5271–5274 CrossRef CAS PubMed
.
- Z. Zhao, X. Jiao and D. Chen, J. Mater. Chem., 2009, 19, 3078–3083 RSC
.
- H. Yang, W. Zhu, S. Sun and X. Guo, RSC Adv., 2014, 4, 32934–32940 RSC
.
- J. B. Miller, L. J. Mathers and E. I. Ko, J. Mater. Chem., 1995, 5, 1759–1760 RSC
.
- J. J. Pietron and D. R. Rolison, J. Non-Cryst. Solids, 2004, 350, 107–112 CrossRef CAS
.
- K. Brodzik, J. Walendziewski, M. Stolarski, L. Van Ginneken, K. Elst and V. Meynen, J. Porous Mater., 2008, 15, 541–549 CrossRef CAS
.
- N. Yao, S. Cao and K. L. Yeung, Microporous Mesoporous Mater., 2009, 117, 570–579 CrossRef CAS
.
- Y. N. Zhao, W. Z. Ren and H. T. Cui, J. Colloid Interface Sci., 2013, 398, 7–12 CrossRef CAS PubMed
.
- H. S. Kibombo, A. S. Weber, C.-M. Wu, K. R. Raghupathi and R. T. Koodali, J. Photochem. Photobiol., A, 2013, 269, 49–58 CrossRef CAS
.
- C.-T. Wang and S.-H. Ro, Mater. Chem. Phys., 2007, 101, 41–48 CrossRef CAS
.
- J. Puskelova, L. Baia, A. Vulpoi, M. Baia, M. Antoniadou, V. Dracopoulos, E. Stathatos, K. Gabor, Z. Pap, V. Danciu and P. Lianos, Chem. Eng. J., 2014, 242, 96–101 CrossRef CAS
.
- J. J. Pietron, R. M. Stroud and D. R. Rolison, Nano Lett., 2002, 2, 545–549 CrossRef CAS
.
- T. Hammedi, M. Triki, Z. Ksibi, A. Ghorbel and F. Medina, J. Porous Mater., 2015, 22, 939–948 CrossRef CAS
.
- K. E. Swider, C. I. Merzbacher, P. L. Hagans and D. R. Rolison, Chem. Mater., 1997, 9, 1248–1255 CrossRef CAS
.
- J. Choi and D. Suh, Korean J. Chem. Eng., 2014, 31, 1773–1779 CrossRef CAS
.
- Y. Wan, J. Ma, W. Zhou, Y. Zhu, X. Song and H. Li, Appl. Catal., A, 2004, 277, 55–59 CrossRef CAS
.
- F. Chaput, B. Dunn, P. Fuqua and K. Salloux, J. Non-Cryst. Solids, 1995, 188, 11–18 CrossRef CAS
.
- D. B. Le, S. Passerini, J. Guo, J. Ressler, B. B. Owens and W. H. Smyrl, J. Electrochem. Soc., 1996, 143, 2099–2104 CrossRef CAS
.
- S. Passerini, D. Ba Le, W. H. Smyrl, M. Berrettoni, R. Tossici, R. Marassi and M. Giorgetti, Solid State Ionics, 1997, 104, 195–204 CrossRef CAS
.
- J. H. Harreld, W. Dong and B. Dunn, Mater. Res. Bull., 1998, 33, 561–567 CrossRef CAS
.
- H. Li, P. He, Y. Wang, E. Hosono and H. Zhou, J. Mater. Chem., 2011, 21, 10999–11009 RSC
.
- A. N. Mansour, P. H. Smith, W. M. Baker, M. Balasubramanian and J. McBreen, Electrochim. Acta, 2002, 47, 3151–3161 CrossRef CAS
.
- D. Winny, S. S. Jeffrey and D. Bruce, Sci. Technol. Adv. Mater., 2003, 4, 3–11 CrossRef
.
- A. N. Mansour, P. H. Smith, W. M. Baker, M. Balasubramanian and J. McBreen, J. Electrochem. Soc., 2003, 150, A403–A413 CrossRef CAS
.
- G. Sudant, E. Baudrin, B. Dunn and J.-M. Tarascon, J. Electrochem. Soc., 2004, 151, A666–A671 CrossRef CAS
.
- K. Xiao, G. Wu, J. Shen, D. Xie and B. Zhou, Mater. Chem. Phys., 2006, 100, 26–30 CrossRef CAS
.
- V. Augustyn and B. Dunn, C. R. Chim., 2010, 13, 130–141 CrossRef CAS
.
- L. Zhang, G. Wu, G. Gao and H. Yang, Key Eng. Mater., 2013, 537, 165–168 CrossRef
.
- A. Moretti, F. Maroni, I. Osada, F. Nobili and S. Passerini, ChemElectroChem, 2015, 2, 529–537 CrossRef CAS
.
- S. V. Balakhonov, S. Z. Vatsadze and B. R. Churagulov, Russ. J. Inorg. Chem., 2015, 60, 9–15 CrossRef CAS
.
- D. B. Le, S. Passerini, F. Coustier, J. Guo, T. Soderstrom, B. B. Owens and W. H. Smyrl, Chem. Mater., 1998, 10, 682–684 CrossRef CAS
.
- P. E. Tang, J. S. Sakamoto, E. Baudrin and B. Dunn, J. Non-Cryst. Solids, 2004, 350, 67–72 CrossRef CAS
.
- E. Frabetti, G. A. Deluga, W. H. Smyrl, M. Giorgetti and M. Berrettoni, J. Phys. Chem. B, 2004, 108, 3765–3771 CrossRef CAS
.
- F. Zhang, S. Passerini, B. B. Owens and W. H. Smyrl, Electrochem. Solid-State Lett., 2001, 4, A221–A223 CrossRef CAS
.
- J. Harreld, H. P. Wong, B. C. Dave, B. Dunn and L. F. Nazar, J. Non-Cryst. Solids, 1998, 225, 319–324 CrossRef CAS
.
- S. V. Balakhonov, K. I. Astafyeva, M. V. Efremova, T. L. Kulova, A. M. Skundin, B. R. Churagulov and Y. D. Tretyakov, Mendeleev Commun., 2011, 21, 315–317 CrossRef CAS
.
- O. Merdrignac-Conanec, K. El Badraoui and P. L'Haridon, J. Solid State Chem., 2005, 178, 218–223 CrossRef CAS
.
- K. Sudoh and H. Hirashima, J. Non-Cryst. Solids, 1992, 147–148, 386–388 CrossRef CAS
.
- H. Schneider, S. Tschudin, M. Schneider, A. Wokaun and A. Baiker, J. Catal., 1994, 147, 5–14 CrossRef CAS
.
- U. Scharf, M. Schneider, A. Baiker and A. Wokaun, J. Catal., 1994, 149, 344–355 CrossRef CAS
.
- R. J. Willey, C.-T. Wang and J. B. Peri, J. Non-Cryst. Solids, 1995, 186, 408–414 CrossRef CAS
.
- O. Zegaoui, C. Hoang-Van and M. Karroua, Appl. Catal., B, 1996, 9, 211–227 CrossRef CAS
.
- R. Willi, R. A. Köppel and A. Baiker, Ind. Eng. Chem. Res., 1997, 36, 3013–3018 CrossRef CAS
.
- C. Hoang-Van, O. Zegaoui and P. Pichat, J. Non-Cryst. Solids, 1998, 225, 157–162 CrossRef CAS
.
- M. I. Kim, D. W. Park, S. W. Park, X. Yang, J. S. Choi and D. J. Suh, Catal. Today, 2006, 111, 212–216 CrossRef CAS
.
- M. Kang, J. Choi, Y. Kim, E. Park, C. Shin, D. Suh and J. Yie, Korean J. Chem. Eng., 2009, 26, 884–889 CrossRef CAS
.
- D. A. Ward and E. I. Ko, Chem. Mater., 1993, 5, 956–969 CrossRef CAS
.
- D. J. Suh and T.-J. Park, Chem. Mater., 1996, 8, 509–513 CrossRef CAS
.
- M. J. Hudson and J. A. Knowles, J. Mater. Chem., 1996, 6, 89–95 RSC
.
- A. F. Bedilo and K. J. Klabunde, Nanostruct. Mater., 1997, 8, 119–135 CrossRef CAS
.
- Y. Cao, J.-C. Hu, Z.-S. Hong, J.-F. Deng and K.-N. Fan, Catal. Lett., 2002, 81, 107–112 CrossRef CAS
.
- R. Sui, A. S. Rizkalla and P. A. Charpentier, Langmuir, 2006, 22, 4390–4396 CrossRef CAS PubMed
.
- C. Stöcker and A. Baiker, J. Sol-Gel Sci. Technol., 1997, 10, 269–282 CrossRef
.
- C. Stöcker and A. Baiker, J. Non-Cryst. Solids, 1998, 223, 165–178 CrossRef
.
- Y. W. Zeng, G. Fagherazzi, F. Pinna, S. Polizzi, P. Riello and M. Signoretto, J. Non-Cryst. Solids, 1993, 155, 259–266 CrossRef CAS
.
- A. Benedetti, G. Fagherazzi, P. Riello, Y. W. Zeng, F. Pinna and M. Signoretto, J. Appl. Crystallogr., 1993, 26, 717–720 CrossRef CAS
.
- O.-T. Nathalie, L. André, L. Pascal and D. Alain, J. Phys.: Condens. Matter, 2000, 12, 7547–7557 CrossRef
.
- G. M. Pajonk and A. E. Tanany, React. Kinet. Catal. Lett., 1992, 47, 167–175 CrossRef CAS
.
- Y. Y. Huang, B. Y. Zhao and Y. C. Xie, Appl. Catal., A, 1998, 172, 327–331 CrossRef CAS
.
- Y. Lee, J.-W. Choi, D. J. Suh, J.-M. Ha and C.-H. Lee, Appl. Catal., A, 2015, 506, 288–293 CrossRef CAS
.
- L. Zhang, J. Xu, L. Sun, J. Ma, K. Yang, Z. Liang, L. Zhang and Y. Zhang, Anal. Bioanal. Chem., 2011, 399, 3399–3405 CrossRef CAS PubMed
.
- L. W. Hrubesh and R. W. Pekala, J. Mater. Res., 1994, 9, 731–738 CrossRef CAS
.
- R. A. Boyse and E. I. Ko, Catal. Lett., 1997, 49, 17–23 CrossRef CAS
.
- Y.-y. Huang, B.-y. Zhao and Y.-c. Xie, Appl. Catal., A, 1998, 172, 327–331 CrossRef CAS
.
- A. F. Bedilo and K. J. Klabunde, J. Catal., 1998, 176, 448–458 CrossRef CAS
.
- M. Signoretto, L. Oliva, F. Pinna and G. Strukul, J. Non-Cryst. Solids, 2001, 290, 145–152 CrossRef CAS
.
- N. Kamoun, M. K. Younes, A. Ghorbel, A. S. Mamede and A. Rives, J. Porous Mater., 2012, 19, 375–381 CrossRef CAS
.
- S. Raissi, M. K. Younes and A. Ghorbel, Mater. Sci. Eng., A, 2014, 3, 105–111 Search PubMed
.
- N. Kamoun, M. K. Younes, A. Ghorbel, A. S. Mamede and A. Rives, Ionics, 2015, 21, 221–229 CrossRef CAS
.
- K. Saravanan, B. Tyagi and H. C. Bajaj, Appl. Catal., B, 2016, 192, 161–170 CrossRef CAS
.
- P. A. Sermon, V. A. Self and Y. Sun, J. Sol-Gel Sci. Technol., 1997, 8, 851–856 CAS
.
- Z. Zhao, D. Chen and X. Jiao, J. Phys. Chem. C, 2007, 111, 18738–18743 CAS
.
- L. Chen, J. Hu and R. M. Richards, ChemPhysChem, 2008, 9, 1069–1078 CrossRef CAS PubMed
.
- Y. Sun and P. A. Sermon, Top. Catal., 1994, 1, 145–151 CrossRef CAS
.
- K. Kohama, H. Imai, H. Hirashima, H. Hamada and M. Inaba, J. Sol-Gel Sci. Technol., 1998, 13, 1033–1036 CrossRef CAS
.
- J. G. Weissman, E. I. Ko and S. Kaytal, Appl. Catal., A, 1993, 94, 45–59 CrossRef CAS
.
- S. Utamapanya, K. J. Klabunde and J. R. Schlup, Chem. Mater., 1991, 3, 175–181 CrossRef CAS
.
- H. Itoh, S. Utamapanya, J. V. Stark, K. J. Klabunde and J. R. Schlup, Chem. Mater., 1993, 5, 71–77 CrossRef CAS
.
- P. Jeevanandam and K. J. Klabunde, Langmuir, 2002, 18, 5309–5313 CrossRef CAS
.
- R. M. Richards, A. M. Volodin, A. F. Bedilo and K. J. Klabunde, Phys. Chem. Chem. Phys., 2003, 5, 4299–4305 RSC
.
- W. Dong, S.-P. Yen, J.-A. Paik and J. Sakamoto, J. Am. Ceram. Soc., 2009, 92, 1011–1016 CrossRef CAS
.
- A. Feinle, A. Heugenhauser and N. Hüsing, J. Supercrit. Fluids, 2015, 106, 133–139 CrossRef CAS
.
- V. Štengl, S. Bakardjieva, M. Maříková, J. Šubrt, F. Opluštil and M. Olšanská, Open Chem., 2004, 2, 16–33 Search PubMed
.
- H. Nur, I. Misnon and H. Hamdan, Catal. Lett., 2009, 130, 161–168 CrossRef CAS
.
- I. Mishakov, E. Ilyina, A. Bedilo and A. Vedyagin, React. Kinet. Catal. Lett., 2009, 97, 355–361 CrossRef CAS
.
- E. V. Ilyina, I. V. Mishakov, A. A. Vedyagin, S. V. Cherepanova, A. N. Nadeev, A. F. Bedilo and K. J. Klabunde, Microporous Mesoporous Mater., 2012, 160, 32–40 CrossRef CAS
.
- I. Sádaba, M. Ojeda, R. Mariscal, R. Richards and M. López Granados, ChemPhysChem, 2012, 13, 3282–3292 CrossRef PubMed
.
- T. Skapin, J. Non-Cryst. Solids, 2001, 285, 128–134 CrossRef CAS
.
- T. Skapin and E. Kemnitz, J. Non-Cryst. Solids, 1998, 225, 163–167 CrossRef CAS
.
- T. Skapin, J. Mater.
Chem., 1995, 5, 1215–1222 RSC
.
- T. Skapin and E. Kemnitz, Catal. Lett., 1996, 40, 241–247 CrossRef CAS
.
- H. Bozorgzadeh, E. Kemnitz, M. Nickkho-Amiry, T. Skapin and J. M. Winfield, J. Fluorine Chem., 2001, 110, 181–189 CrossRef CAS
.
- H. Bozorgzadeh, E. Kemnitz, M. Nickkho-Amiry, T. Skapin and J. M. Winfield, J. Fluorine Chem., 2003, 121, 83–92 CrossRef CAS
.
- M. Abecassis-Wolfovich, H. Rotter, M. V. Landau, E. Korin, A. I. Erenburg, D. Mogilyansky and E. Gartstein, J. Non-Cryst. Solids, 2003, 318, 95–111 CrossRef CAS
.
- H. Rotter, M. V. Landau, M. Carrera, D. Goldfarb and M. Herskowitz, Appl. Catal., B, 2004, 47, 111–126 CrossRef CAS
.
- H. Rotter, M. V. Landau and M. Herskowitz, Environ. Sci. Technol., 2005, 39, 6845–6850 CrossRef CAS PubMed
.
- M. K. Younes and A. Ghorbel, Appl. Catal., A, 2000, 197, 269–277 CrossRef CAS
.
- R. J. Willey, H. Lai and J. B. Peri, J. Catal., 1991, 130, 319–331 CrossRef CAS
.
- J. Ping Chen, R. Willey and S. Teichner, J. Porous Mater., 1997, 4, 113–119 CrossRef
.
- C.-T. Wang, J. Non-Cryst. Solids, 2007, 353, 1126–1133 CrossRef CAS
.
- W. Dong and B. Dunn, J. Non-Cryst. Solids, 1998, 225, 135–140 CrossRef CAS
.
- W. Dong and B. Dunn, J. Mater. Chem., 1998, 8, 665–670 RSC
.
- W. Dong, A. N. Mansour and B. Dunn, Solid State Ionics, 2001, 144, 31–40 CrossRef CAS
.
- Z. Novak, P. Kotnik and Ž. Knez, J. Non-Cryst. Solids, 2004, 350, 308–313 CrossRef CAS
.
- S. Qiang-Qiang, X. Maowen, B. Shu-Juan and L. Chang Ming, Nanotechnology, 2015, 26, 115602 CrossRef PubMed
.
-
C. J. Brinker, K. J. Ward, K. D. Keefer, E. Holupka, P. J. Bray and R. K. Pearson, in Aerogels, ed. J. Fricke, Springer, Berlin Heidelberg, 1986, ch. 7, vol. 6, pp. 57–67 Search PubMed
.
- L. Zhang, G. Chen, B. Chen, T. Liu, Y. Mei and X. Luo, Mater. Lett., 2013, 104, 41–43 CrossRef CAS
.
- M. Krumm, C. L. Pueyo and S. Polarz, Chem. Mater., 2010, 22, 5129–5136 CrossRef CAS
.
- L. El Mir, J. El Ghoul, S. Alaya, M. Ben Salem, C. Barthou and H. J. von Bardeleben, Phys. B, 2008, 403, 1770–1774 CrossRef CAS
.
- J. E. Ghoul, A. Alaya, L. E. Mir, C. Barthou, M. Saadoun and S. Alaya, Int. J. Nano Biomater., 2009, 2, 273–278 CrossRef
.
- R. Slama, F. Ghribi, A. Houas, C. Barthou and L. El Mir, Thin Solid Films, 2011, 519, 5792–5795 CrossRef CAS
.
- J. El Ghoul, C. Barthou and L. El Mir, Physica E, 2012, 44, 1910–1915 CrossRef CAS
.
- P. G. Harrison and A. Guest, J. Chem. Soc., Faraday Trans., 1987, 83, 3383–3397 RSC
.
- N.-L. Wu, L.-F. Wu, Y.-C. Yang and S.-J. Huang, J. Mater. Res., 1996, 11, 813–820 CrossRef CAS
.
- R. Huang, L. Hou, B. Zhou, Q. Zhao and S. Ren, J. Non-Cryst. Solids, 2005, 351, 23–28 CrossRef CAS
.
- J. H. Harreld, J. Sakamoto and B. Dunn, J. Power Sources, 2003, 115, 19–26 CrossRef CAS
.
- S. M. Maurer and E. I. Ko, J. Catal., 1992, 135, 125–134 CrossRef CAS
.
- J. L. Gasser-Ramirez, B. C. Dunn, D. W. Ramirez, E. P. Fillerup, G. C. Turpin, Y. Shi, R. D. Ernst, R. J. Pugmire, E. M. Eyring, K. A. Pettigrew, D. R. Rolison and J. M. Harris, J. Non-Cryst. Solids, 2008, 354, 5509–5514 CrossRef CAS
.
- J. W. Long, K. E. Swider-Lyons, R. M. Stroud and D. R. Rolison, Electrochem. Solid-State Lett., 2000, 3, 453–456 CrossRef CAS
.
- H. Tang, Y. Sui, X. Zhu and Z. Bao, Nanoscale Res. Lett., 2015, 10, 260 CrossRef PubMed
.
- C. A. Frederick, A. C. Forsman, J. F. Hund and S. A. Eddinger, Fusion Sci. Technol., 2009, 55, 499–504 CrossRef CAS
.
- R. J. Willey, S. A. Oliver, G. Oliveri and G. Busca, J. Mater. Res., 1993, 8, 1418–1427 CrossRef CAS
.
- H. Shimooka and M. Kuwabara, J. Am. Ceram. Soc., 1996, 79, 2983–2985 CrossRef CAS
.
- H. Shimooka, K.-I. Yamada, S. Takahashi and M. Kuwabara, J. Sol-Gel Sci. Technol., 1998, 13, 873–876 CrossRef CAS
.
- D. Demydov and K. J. Klabunde, J. Non-Cryst. Solids, 2004, 350, 165–172 CrossRef CAS
.
- P. Löbmann, W. Glaubitt, J. Gross and J. Fricke, J. Non-Cryst. Solids, 1995, 186, 59–63 CrossRef
.
- R. P. Maloney, H. J. Kim and J. S. Sakamoto, ACS Appl. Mater. Interfaces, 2012, 4, 2318–2321 CAS
.
- V. Sydorchuk, V. Zazhigalov, S. Khalameida, E. Diyuk, J. Skubiszewska-Zięba, R. Leboda and L. Kuznetsova, Mater. Res. Bull., 2010, 45, 1096–1105 CrossRef CAS
.
- U. Kersen and R. Keiski, J. Nanosci. Nanotechnol., 2005, 5, 1734–1736 CrossRef CAS PubMed
.
- C. Hu, Q. Zhu and Z. Jiang, Powder Technol., 2009, 194, 109–114 CrossRef CAS
.
- S. Bag, I. U. Arachchige and M. G. Kanatzidis, J. Mater. Chem., 2008, 18, 3628–3632 RSC
.
- S. Bag, P. N. Trikalitis, P. J. Chupas, G. S. Armatas and M. G. Kanatzidis, Science, 2007, 317, 490–493 CrossRef CAS PubMed
.
- V. Stanić, T. H. Etsell, A. C. Pierre and R. J. Mikula, Mater. Lett., 1997, 31, 35–38 CrossRef
.
- V. Stanić, A. C. Pierre, T. H. Etsell and R. J. Mikula, J. Non-Cryst. Solids, 1997, 220, 58–62 CrossRef
.
- V. Stanić, A. C. Pierre, T. H. Etsell and R. J. Mikula, J. Mater. Res., 1996, 11, 363–372 CrossRef
.
- V. Stanić, A. C. Pierre, T. H. Etsell and R. J. Mikula, J. Am. Ceram. Soc., 2000, 83, 1790–1796 CrossRef
.
- J. S. Sanghera, C. Scotto, S. Bayya and I. D. Aggarwal, J. Non-Cryst. Solids, 1999, 256–257, 31–35 CrossRef
.
- M. Shafaei-Fallah, J. He, A. Rothenberger and M. G. Kanatzidis, J. Am. Chem. Soc., 2011, 133, 1200–1202 CrossRef CAS PubMed
.
- Y. Oh, C. D. Morris and M. G. Kanatzidis, J. Am. Chem. Soc., 2012, 134, 14604–14608 CrossRef CAS PubMed
.
- K. S. Subrahmanyam, C. D. Malliakas, D. Sarma, G. S. Armatas, J. Wu and M. G. Kanatzidis, J. Am. Chem. Soc., 2015, 137, 13943–13948 CrossRef CAS PubMed
.
- Y. Oh, S. Bag, C. D. Malliakas and M. G. Kanatzidis, Chem. Mater., 2011, 23, 2447–2456 CrossRef CAS
.
- S. Bag and M. G. Kanatzidis, J. Am. Chem. Soc., 2010, 132, 14951–14959 CrossRef CAS PubMed
.
- M. Shafaei-Fallah, A. Rothenberger, A. P. Katsoulidis, J. He, C. D. Malliakas and M. G. Kanatzidis, Adv. Mater., 2011, 23, 4857–4860 CrossRef CAS PubMed
.
- K. Polychronopoulou, C. D. Malliakas, J. He and M. G. Kanatzidis, Chem. Mater., 2012, 24, 3380–3392 CrossRef CAS
.
- S. Bag, A. F. Gaudette, M. E. Bussell and M. G. Kanatzidis, Nat. Chem., 2009, 1, 217–224 CrossRef CAS PubMed
.
- S. Coste, E. Gautier, M. Evain, M. Bujoli-Doeuff, R. Brec, S. Jobic and M. G. Kanatzidis, Chem. Mater., 2003, 15, 2323–2327 CrossRef CAS
.
- S. M. Islam, K. S. Subrahmanyam, C. D. Malliakas and M. G. Kanatzidis, Chem. Mater., 2014, 26, 5151–5160 CrossRef CAS
.
- A. Banerjee, B. D. Yuhas, E. A. Margulies, Y. Zhang, Y. Shim, M. R. Wasielewski and M. G. Kanatzidis, J. Am. Chem. Soc., 2015, 137, 2030–2034 CrossRef CAS PubMed
.
- B. D. Yuhas, A. L. Smeigh, A. P. S. Samuel, Y. Shim, S. Bag, A. P. Douvalis, M. R. Wasielewski and M. G. Kanatzidis, J. Am. Chem. Soc., 2011, 133, 7252–7255 CrossRef CAS PubMed
.
- B. D. Yuhas, C. Prasittichai, J. T. Hupp and M. G. Kanatzidis, J. Am. Chem. Soc., 2011, 133, 15854–15857 CrossRef CAS PubMed
.
- B. D. Yuhas, A. L. Smeigh, A. P. Douvalis, M. R. Wasielewski and M. G. Kanatzidis, J. Am. Chem. Soc., 2012, 134, 10353–10356 CrossRef CAS PubMed
.
- Y. Shim, B. D. Yuhas, S. M. Dyar, A. L. Smeigh, A. P. Douvalis, M. R. Wasielewski and M. G. Kanatzidis, J. Am. Chem. Soc., 2013, 135, 2330–2337 CrossRef CAS PubMed
.
- Y. Shim, R. M. Young, A. P. Douvalis, S. M. Dyar, B. D. Yuhas, T. Bakas, M. R. Wasielewski and M. G. Kanatzidis, J. Am. Chem. Soc., 2014, 136, 13371–13380 CrossRef CAS PubMed
.
- B. J. Riley, J. Chun, J. V. Ryan, J. Matyas, X. S. Li, D. W. Matson, S. K. Sundaram, D. M. Strachan and J. D. Vienna, RSC Adv., 2011, 1, 1704–1715 RSC
.
- B. J. Riley, J. Chun, W. Um, W. C. Lepry, J. Matyas, M. J. Olszta, X. Li, K. Polychronopoulou and M. G. Kanatzidis, Environ. Sci. Technol., 2013, 47, 7540–7547 CrossRef CAS PubMed
.
- B. J. Riley, D. A. Pierce, J. Chun, J. Matyáš, W. C. Lepry, T. G. Garn, J. D. Law and M. G. Kanatzidis, Environ. Sci. Technol., 2014, 48, 5832–5839 CrossRef CAS PubMed
.
- B. J. Riley, D. A. Pierce, W. C. Lepry, J. O. Kroll, J. Chun, K. S. Subrahmanyam, M. G. Kanatzidis, F. K. Alblouwy, A. Bulbule and E. M. Sabolsky, Ind. Eng. Chem. Res., 2015, 54, 11259–11267 CrossRef CAS
.
- E. Ahmed and A. Rothenberger, Microporous Mesoporous Mater., 2014, 199, 74–82 CrossRef CAS
.
- E. Ahmed, J. Khanderi, D. H. Anjum and A. Rothenberger, Chem. Mater., 2014, 26, 6454–6460 CrossRef CAS
.
- E. Ahmed and A. Rothenberger, Microporous Mesoporous Mater., 2016, 220, 247–252 CrossRef CAS
.
- E. Ahmed and A. Rothenberger, J. Mater. Chem. A, 2015, 3, 7786–7792 CAS
.
- M. Rousseas, A. P. Goldstein, W. Mickelson, M. A. Worsley, L. Woo and A. Zettl, ACS Nano, 2013, 7, 8540–8546 CrossRef CAS PubMed
.
- T. Pham, A. P. Goldstein, J. P. Lewicki, S. O. Kucheyev, C. Wang, T. P. Russell, M. A. Worsley, L. Woo, W. Mickelson and A. Zettl, Nanoscale, 2015, 7, 10449–10458 RSC
.
- A. Harley-Trochimczyk, T. Pham, J. Chang, E. Chen, M. A. Worsley, A. Zettl, W. Mickelson and R. Maboudian, Adv. Funct. Mater., 2016, 26, 433–439 CrossRef CAS
.
- K. Chen, X. Huang, Z. Zhang, A. Du, B. Zhou, Y. Xu, Z. Zhou and Y. Wang, J. Mater. Chem. A, 2015, 3, 11745–11749 CAS
.
- H. Wang, Y. Wang, J. Zhang, N. Gaponik and A. L. Rogach, Mater. Sci. Eng., B, 2014, 179, 48–51 CrossRef CAS
.
- A. Stefancic, D. Primc, G. Tavcar and T. Skapin, Dalton Trans., 2015, 44, 20609–20617 RSC
.
- A. E. Gash, T. M. Tillotson, J. H. Satcher, J. F. Poco, L. W. Hrubesh and R. L. Simpson, Chem. Mater., 2001, 13, 999–1007 CrossRef CAS
.
- A. E. Gash, T. M. Tillotson, J. H. Satcher Jr, L. W. Hrubesh and R. L. Simpson, J. Non-Cryst. Solids, 2001, 285, 22–28 CrossRef CAS
.
- T. M. Tillotson, W. E. Sunderland, I. M. Thomas and L. W. Hrubesh, J. Sol-Gel Sci. Technol., 1994, 1, 241–249 CrossRef CAS
.
- A. E. Gash, J. H. Satcher and R. L. Simpson, Chem. Mater., 2003, 15, 3268–3275 CrossRef CAS
.
- J. W. Long, M. S. Logan, C. P. Rhodes, E. E. Carpenter, R. M. Stroud and D. R. Rolison, J. Am. Chem. Soc., 2004, 126, 16879–16889 CrossRef CAS PubMed
.
- Y. Zhang, C. P. Chai, Y. J. Luo, L. Wang and G. P. Li, Mater. Sci. Eng., B, 2014, 188, 13–19 CrossRef CAS
.
- Y. Kido, K. Nakanishi, A. Miyasaka and K. Kanamori, Chem. Mater., 2012, 24, 2071–2077 CrossRef CAS
.
- S. Bali, G. C. Turpin, R. D. Ernst, R. J. Pugmire, V. Singh, M. S. Seehra and E. M. Eyring, Energy Fuels, 2008, 22, 1439–1443 CrossRef CAS
.
- S. Bali, F. E. Huggins, G. P. Huffman, R. D. Ernst, R. J. Pugmire and E. M. Eyring, Energy Fuels, 2009, 23, 14–18 CrossRef CAS
.
- A. Khaleel and A. Al-Marzouqi, Mater. Lett., 2012, 68, 385–387 CrossRef CAS
.
- A. E. Gash, J. H. Satcher Jr and R. L. Simpson, J. Non-Cryst. Solids, 2004, 350, 145–151 CrossRef CAS
.
- T.-Y. Wei, C.-H. Chen, H.-C. Chien, S.-Y. Lu and C.-C. Hu, Adv. Mater., 2010, 22, 347–351 CrossRef CAS PubMed
.
- T. F. Baumann, A. E. Gash, S. C. Chinn, A. M. Sawvel, R. S. Maxwell and J. H. Satcher, Chem. Mater., 2005, 17, 395–401 CrossRef CAS
.
- L. Gan, Z. Xu, Y. Feng and L. Chen, J. Porous Mater., 2005, 12, 317–321 CrossRef CAS
.
- Y. Tokudome, K. Nakanishi, K. Kanamori, K. Fujita, H. Akamatsu and T. Hanada, J. Colloid Interface Sci., 2009, 338, 506–513 CrossRef CAS PubMed
.
- Y. Guo, W. Meyer-Zaika, M. Muhler, S. Vukojević and M. Epple, Eur. J. Inorg. Chem., 2006, 4774–4781 CrossRef CAS
.
- S. Gill, P. Brown, M. Ogundiya and L. Hope-Weeks, J. Sol-Gel Sci. Technol., 2010, 53, 635–640 CrossRef CAS
.
- C. N. Chervin, B. J. Clapsaddle, H. W. Chiu, A. E. Gash, J. H. Satcher and S. M. Kauzlarich, Chem. Mater., 2005, 17, 3345–3351 CrossRef CAS
.
- C. N. Chervin, B. J. Clapsaddle, H. W. Chiu, A. E. Gash, J. H. Satcher and S. M. Kauzlarich, Chem. Mater., 2006, 18, 4865–4874 CrossRef CAS
.
- X. Li, Y. Jiao, H. Ji and X. Sun, Integr. Ferroelectr., 2013, 146, 122–126 CrossRef CAS
.
- H. Schäfer, S. Brandt, B. Milow, S. Ichilmann, M. Steinhart and L. Ratke, Chem. – Asian J., 2013, 8, 2211–2219 CrossRef PubMed
.
- L. Zhong, X. Chen, H. Song, K. Guo and Z. Hu, RSC Adv., 2014, 4, 31666–31671 RSC
.
- T. F. Baumann, S. O. Kucheyev, A. E. Gash and J. H. Satcher, Adv. Mater., 2005, 17, 1546–1548 CrossRef CAS
.
- Y. P. Gao, C. N. Sisk and L. J. Hope-Weeks, Chem. Mater., 2007, 19, 6007–6011 CrossRef CAS
.
- B. Chen, G. Chen, T. Zeng, T. Liu, Y. Mei, Y. Bi, X. Luo and L. Zhang, J. Porous Mater., 2013, 20, 1051–1057 CrossRef CAS
.
- B. Chen, X. Wang, S. Zhang, C. Wei and L. Zhang, J. Porous Mater., 2014, 21, 1035–1039 CrossRef CAS
.
- M. Davis, W. M. Hikal, C. Gumeci and L. J. Hope-Weeks, Catal. Sci. Technol., 2012, 2, 922–924 CAS
.
- K. Ellmer, Nat. Photonics, 2012, 6, 809–817 CrossRef CAS
.
- L. Luo, D. Bozyigit, V. Wood and M. Niederberger, Chem. Mater., 2013, 25, 4901–4907 CrossRef CAS
.
- W. A. Badawy, J. Adv. Res., 2015, 6, 123–132 CrossRef CAS PubMed
.
- A. Vu, Y. Qian and A. Stein, Adv. Energy Mater., 2012, 2, 1056–1085 CrossRef CAS
.
- Z. Zhang, J. Liu, J. Gu, L. Su and L. Cheng, Energy Environ. Sci., 2014, 7, 2535–2558 CAS
.
- M. Davis, K. Zhang, S. Wang and L. J. Hope-Weeks, J. Mater. Chem., 2012, 22, 20163–20165 RSC
.
- J. P. Correa Baena and A. G. Agrios, ACS Appl. Mater. Interfaces, 2014, 6, 19127–19134 CAS
.
- J. P. Correa Baena and A. G. Agrios, J. Phys. Chem. C, 2014, 118, 17028–17035 CAS
.
- S. O. Kucheyev, T. van Buuren, T. F. Baumann, J. H. Satcher, T. M. Willey, R. W. Meulenberg, T. E. Felter, J. F. Poco, S. A. Gammon and L. J. Terminello, Phys. Rev. B: Condens. Matter Mater. Phys., 2004, 69, 245102 CrossRef
.
- J. Choi, C. B. Shin and D. J. Suh, J. Mater. Chem., 2009, 19, 7704–7709 RSC
.
- G. R. Peterson, F. Hung-Low, C. Gumeci, W. P. Bassett, C. Korzeniewski and L. J. Hope-Weeks, ACS Appl. Mater. Interfaces, 2014, 6, 1796–1803 CAS
.
- R. A. Reibold, J. F. Poco, T. F. Baumann, R. L. Simpson and J. H. Satcher Jr, J. Non-Cryst. Solids, 2003, 319, 241–246 CrossRef CAS
.
- H. D. Zhang, B. Li, Q. X. Zheng, M. H. Jiang and X. T. Tao, J. Non-Cryst. Solids, 2008, 354, 4089–4093 CrossRef CAS
.
- B. Clapsaddle, B. Neumann, A. Wittstock, D. Sprehn, A. Gash, J. Satcher, Jr., R. Simpson and M. Bäumer, J. Sol-Gel Sci. Technol., 2012, 64, 381–389 CrossRef CAS
.
- H. Schäfer, B. Milow and L. Ratke, RSC Adv., 2013, 3, 15263–15272 RSC
.
- H. Ren, L. Zhang, C. Shang, X. Wang and Y. Bi, J. Sol-Gel Sci. Technol., 2010, 53, 307–311 CrossRef CAS
.
- M. Davis, C. Gümeci, C. Kiel and L. Hope-Weeks, J. Sol-Gel Sci. Technol., 2011, 58, 535–538 CrossRef CAS
.
- P. D. Brown, S. K. Gill and L. J. Hope-Weeks, J. Mater. Chem., 2011, 21, 4204–4208 RSC
.
- J. Eid, A. C. Pierre and G. Baret, J. Non-Cryst. Solids, 2005, 351, 218–227 CrossRef CAS
.
- R. A. Reibold, J. F. Poco, T. F. Baumann, R. L. Simpson and J. H. Satcher Jr, J. Non-Cryst. Solids, 2004, 341, 35–39 CrossRef CAS
.
- J. Yoo, Y. Bang, S. J. Han, S. Park, J. H. Song and I. K. Song, J. Mol. Catal. A: Chem., 2015, 410, 74–80 CrossRef CAS
.
- P. Brown and L. Hope-Weeks, J. Sol-Gel Sci. Technol., 2009, 51, 238–243 CrossRef CAS
.
- P. Brown, D. Cearnaigh, E. Fung and L. Hope-Weeks, J. Sol-Gel Sci. Technol., 2012, 61, 104–111 CrossRef CAS
.
- C. N. Chervin, J. S. Ko, B. W. Miller, L. Dudek, A. N. Mansour, M. D. Donakowski, T. Brintlinger, P. Gogotsi, S. Chattopadhyay, T. Shibata, J. F. Parker, B. P. Hahn, D. R. Rolison and J. W. Long, J. Mater. Chem. A, 2015, 3, 12059–12068 CAS
.
- C. N. Chervin, B. J. Clapsaddle, H. W. Chiu, A. E. Gash, J. H. Satcher and S. M. Kauzlarich, Chem. Mater., 2006, 18, 1928–1937 CrossRef CAS
.
- J. W. Long, M. S. Logan, E. E. Carpenter and D. R. Rolison, J. Non-Cryst. Solids, 2004, 350, 182–188 CrossRef CAS
.
- K. A. Pettigrew, J. W. Long, E. E. Carpenter, C. C. Baker, J. C. Lytle, C. N. Chervin, M. S. Logan, R. M. Stroud and D. R. Rolison, ACS Nano, 2008, 2, 784–790 CrossRef CAS PubMed
.
- Y. Zhu, X. Zhang, Z. Lan, H. Li, X. Zhang and Q. Li, Mater. Des., 2016, 93, 503–508 CrossRef CAS
.
- A. Du, B. Zhou, J. Shen, S. Xiao, Z. Zhang, C. Liu and M. Zhang, J. Non-Cryst. Solids, 2009, 355, 175–181 CrossRef CAS
.
- A. Du, B. Zhou, J. Shen, J. Gui, Y. Zhong, C. Liu, Z. Zhang and G. Wu, New J. Chem., 2011, 35, 1096–1102 RSC
.
- A. Du, B. Zhou, Y. Zhong, X. Zhu, G. Gao, G. Wu, Z. Zhang and J. Shen, J. Sol-Gel Sci. Technol., 2011, 58, 225–231 CrossRef CAS
.
- Y. T. Bi, H. B. Ren, B. W. Chen and L. Zhang, Adv. Mater. Res., 2011, 335–336, 368–371 CrossRef CAS
.
- B. C. Tappan, S. A. Steiner and E. P. Luther, Angew. Chem., Int. Ed., 2010, 49, 4544–4565 CrossRef CAS PubMed
.
- N. Kränzlin and M. Niederberger, Adv. Mater., 2013, 25, 5599–5604 CrossRef PubMed
.
- N. Kränzlin, S. Ellenbroek, D. Durán-Martín and M. Niederberger, Angew. Chem., Int. Ed., 2012, 51, 4743–4746 CrossRef PubMed
.
- M. Staniuk, O. Hirsch, N. Kränzlin, R. Böhlen, W. van Beek, P. M. Abdala and D. Koziej, Chem. Mater., 2014, 26, 2086–2094 CrossRef CAS
.
- C. N. Sisk and L. J. Hope-Weeks, J. Mater. Chem., 2008, 18, 2607–2610 RSC
.
- A. M. Shobe, S. K. Gill and L. J. Hope-Weeks, J. Non-Cryst. Solids, 2010, 356, 1337–1343 CrossRef CAS
.
- R. M. Allaf and L. J. Hope-Weeks, J. Nanomater., 2014, 2014, 491817 Search PubMed
.
- R. Baghi, G. R. Peterson and L. J. Hope-Weeks, J. Mater. Chem. A, 2013, 1, 10898–10902 CAS
.
-
Y. T. Bi, H. B. Ren and L. Zhang, in High Performance Structures and Materials Engineering, Pts 1 and 2, ed. M. Zhou, Trans Tech Publications Ltd, Stafa-Zurich, 2011, vol. 217–218, pp. 1165–1169 Search PubMed
.
- Y. Bi, H. Ren, B. Chen, G. Chen, Y. Mei and L. Zhang, J. Sol-Gel Sci. Technol., 2012, 63, 140–145 CrossRef CAS
.
- Y. Bi, L. He, Y. Zhang, S. He, H. Ren and L. Zhang, J. Sol-Gel Sci. Technol., 2014, 72, 415–420 CrossRef CAS
.
- Y. Bi, H. Ren, L. He, Y. Zhang, S. He and L. Zhang, Mater. Lett., 2015, 139, 205–207 CrossRef CAS
.
- N. Leventis, N. Chandrasekaran, C. Sotiriou-Leventis and A. Mumtaz, J. Mater. Chem., 2009, 19, 63–65 RSC
.
- S. Mahadik-Khanolkar, S. Donthula, A. Bang, C. Wisner, C. Sotiriou-Leventis and N. Leventis, Chem. Mater., 2014, 26, 1318–1331 CrossRef CAS
.
- N. Leventis, S. Donthula, C. Mandal, M. S. Ding and C. Sotiriou-Leventis, Chem. Mater., 2015, 27, 8126–8137 CrossRef CAS
.
- W. Xu, A. Du, J. Xiong, Z. Zhang, J. Shen and B. Zhou, Mater. Des., 2016, 97, 93–97 CrossRef CAS
.
- M. Schneider and A. Baiker, Catal. Rev., 1995, 37, 515–556 CAS
.
- G. M. Pajonk, Catal. Today, 1997, 35, 319–337 CrossRef CAS
.
- A. Vallribera and E. Molins, Nanopart. Catal., 2008, 161–194 CAS
.
- B. Hosticka, P. M. Norris, J. S. Brenizer and C. E. Daitch, J. Non-Cryst. Solids, 1998, 225, 293–297 CrossRef CAS
.
- M. J. Burchell, G. Graham and A. Kearsley, Annu. Rev. Earth Planet. Sci., 2006, 34, 385–418 CrossRef CAS
.
- L. W. Hrubesh, J. Non-Cryst. Solids, 1998, 225, 335–342 CrossRef CAS
.
- P. C. Thapliyal and K. Singh, J. Mater., 2014, 2014, 127049 Search PubMed
.
- R. J. Ayen and P. A. Iacobucci, Rev. Chem. Eng., 1988, 5, 157–198 CAS
.
- H. D. Gesser and P. C. Goswami, Chem. Rev., 1989, 89, 765–788 CrossRef CAS
.
- J. Fricke and T. Tillotson, Thin Solid Films, 1997, 297, 212–223 CrossRef CAS
.
- Y. K. Akimov, Instrum. Exp. Tech., 2003, 46, 287–299 CrossRef CAS
.
- D. R. Rolison and B. Dunn, J. Mater. Chem., 2001, 11, 963–980 RSC
.
- A. Feinle and N. Hüsing, J. Supercrit. Fluids, 2015, 106, 2–8 CrossRef CAS
.
- N. Gaponik, A.-K. Herrmann and A. Eychmüller, J. Phys. Chem. Lett., 2012, 3, 8–17 CrossRef CAS
.
- F. J. Heiligtag, M. J. I. Airaghi Leccardi, D. Erdem, M. J. Süess and M. Niederberger, Nanoscale, 2014, 6, 13213–13221 RSC
.
- F. Rechberger, F. J. Heiligtag, M. J. Süess and M. Niederberger, Angew. Chem., Int. Ed., 2014, 53, 6823–6826 CrossRef CAS PubMed
.
- J. L. Mohanan, I. U. Arachchige and S. L. Brock, Science, 2005, 307, 397–400 CAS
.
- F. J. Heiligtag, M. D. Rossell, M. J. Süess and M. Niederberger, J. Mater. Chem., 2011, 21, 16893–16899 RSC
.
- F. Rechberger, G. Ilari and M. Niederberger, Chem. Commun., 2014, 50, 13138–13141 RSC
.
- G. Zeng, N. Shi, M. Hess, X. Chen, W. Cheng, T. Fan and M. Niederberger, ACS Nano, 2015, 9, 4227–4235 CrossRef CAS PubMed
.
- B. H. Rainwater, M. Liu and M. Liu, Int. J. Hydrogen Energy, 2012, 37, 18342–18348 CrossRef CAS
.
- M. Niederberger, Acc. Chem. Res., 2007, 40, 793–800 CrossRef CAS PubMed
.
- A. E. Danks, S. R. Hall and Z. Schnepp, Mater. Horiz., 2016, 3, 91–112 RSC
.
- H. Dong, Y. C. Chen and C. Feldmann, Green Chem., 2015, 17, 4107–4132 RSC
.
- C. de Mello Donegá, P. Liljeroth and D. Vanmaekelbergh, Small, 2005, 1, 1152–1162 CrossRef PubMed
.
- J. van Embden, A. S. R. Chesman and J. J. Jasieniak, Chem. Mater., 2015, 27, 2246–2285 CrossRef CAS
.
- M. Rajamathi and R. Seshadri, Curr. Opin. Solid State Mater. Sci., 2002, 6, 337–345 CrossRef CAS
.
-
R. R. Paul and C. Hiemenz, Principles of Colloid and Surface Chemistry, Third Edition, Revised and Expanded, CRC Press, 1997 Search PubMed
.
- G. M. Whitesides and M. Boncheva, Proc. Natl. Acad. Sci. U. S. A., 2002, 99, 4769–4774 CrossRef CAS PubMed
.
-
S. L. Lee, Self-Assembly and Nanotechnology: A Force Balance Approach, Wiley-VCH, Weinheim, 2008 Search PubMed
.
- N. Gaponik, A. Wolf, R. Marx, V. Lesnyak, K. Schilling and A. Eychmüller, Adv. Mater., 2008, 20, 4257–4262 CrossRef CAS
.
- K. G. S. Ranmohotti, X. Gao and I. U. Arachchige, Chem. Mater., 2013, 25, 3528–3534 CrossRef CAS
.
- G. Hayase, K. Nonomura, G. Hasegawa, K. Kanamori and K. Nakanishi, Chem. Mater., 2014, 27, 3–5 CrossRef
.
- K. A. Dawson, Curr. Opin. Colloid Interface Sci., 2002, 7, 218–227 CrossRef CAS
.
- V. Trappe and P. Sandkühler, Curr. Opin. Colloid Interface Sci., 2004, 8, 494–500 CrossRef CAS
.
- H. Wu and M. Morbidelli, Particuology, 2014, 14, 1–11 CrossRef CAS
.
- E. Dickinson, J. Chem. Soc., Faraday Trans., 1997, 93, 111–114 RSC
.
- P. J. Lu, E. Zaccarelli, F. Ciulla, A. B. Schofield, F. Sciortino and D. A. Weitz, Nature, 2008, 453, 499–503 CrossRef CAS PubMed
.
- T. Gacoin, L. Malier and J.-P. Boilot, Chem. Mater., 1997, 9, 1502–1504 CrossRef CAS
.
- T. Gacoin, L. Malier and J. P. Boilot, J. Mater. Chem., 1997, 7, 859–860 RSC
.
- L. Malier, J. P. Boilot and T. Gacoin, J. Sol-Gel Sci. Technol., 1998, 13, 61–64 CrossRef CAS
.
- T. Gacoin, K. Lahlil, P. Larregaray and J. P. Boilot, J. Phys. Chem. B, 2001, 105, 10228–10235 CrossRef CAS
.
- J. L. Mohanan and S. L. Brock, J. Non-Cryst. Solids, 2004, 350, 1–8 CrossRef CAS
.
- I. U. Arachchige and S. L. Brock, J. Am. Chem. Soc., 2006, 128, 7964–7971 CrossRef CAS PubMed
.
- K. K. Kalebaila, D. G. Georgiev and S. L. Brock, J. Non-Cryst. Solids, 2006, 352, 232–240 CrossRef CAS
.
- H. Yu, Y. Liu and S. L. Brock, ACS Nano, 2009, 3, 2000–2006 CrossRef CAS PubMed
.
- J. Mohanan and S. Brock, J. Sol-Gel Sci. Technol., 2006, 40, 341–350 CrossRef CAS
.
- H. Yu and S. L. Brock, ACS Nano, 2008, 2, 1563–1570 CrossRef CAS PubMed
.
- H. Yu, R. Bellair, R. M. Kannan and S. L. Brock, J. Am. Chem. Soc., 2008, 130, 5054–5055 CrossRef CAS PubMed
.
- I. U. Arachchige, J. L. Mohanan and S. L. Brock, Chem. Mater., 2005, 17, 6644–6650 CrossRef CAS
.
- I. U. Arachchige and S. L. Brock, J. Am. Chem. Soc., 2007, 129, 1840–1841 CrossRef CAS PubMed
.
- L. Korala and S. L. Brock, J. Phys. Chem. C, 2012, 116, 17110–17117 CAS
.
- L. Korala, L. Li and S. L. Brock, Chem. Commun., 2012, 48, 8523–8525 RSC
.
- A. Eychmüller, Angew. Chem., Int. Ed., 2005, 44, 4839–4841 CrossRef PubMed
.
- S. L. Brock, I. U. Arachchige and K. K. Kalebaila, Comments Inorg. Chem., 2006, 27, 103–126 CrossRef CAS
.
- I. U. Arachchige and S. L. Brock, Acc. Chem. Res., 2007, 40, 801–809 CrossRef CAS PubMed
.
- Q. Yao, I. U. Arachchige and S. L. Brock, J. Am. Chem. Soc., 2009, 131, 2800–2801 CrossRef CAS PubMed
.
- K. K. Kalebaila and S. L. Brock, Z. Anorg. Allg. Chem., 2012, 638, 2598–2603 CrossRef CAS
.
- S. Ganguly and S. L. Brock, J. Mater. Chem., 2011, 21, 8800–8806 RSC
.
- Q. Yao and S. L. Brock, Inorg. Chem., 2011, 50, 9985–9992 CrossRef CAS PubMed
.
- S. Ganguly, C. Zhou, D. Morelli, J. Sakamoto and S. L. Brock, J. Phys. Chem. C, 2012, 116, 17431–17439 CAS
.
- I. R. Pala, I. U. Arachchige, D. G. Georgiev and S. L. Brock, Angew. Chem., Int. Ed., 2010, 49, 3661–3665 CrossRef CAS PubMed
.
- S. Pawsey, K. K. Kalebaila, I. Moudrakovski, J. A. Ripmeester and S. L. Brock, J. Phys. Chem. C, 2010, 114, 13187–13195 CAS
.
- S.-H. Jeong, J. W. Lee, D. Ge, K. Sun, T. Nakashima, S. I. Yoo, A. Agarwal, Y. Li and N. A. Kotov, J. Mater. Chem., 2011, 21, 11639–11643 RSC
.
- Y. Qinghong and L. B. Stephanie, Nanotechnology, 2010, 21, 115502 CrossRef PubMed
.
- I. R. Pala and S. L. Brock, ACS Appl. Mater. Interfaces, 2012, 4, 2160–2167 CAS
.
- J. N. De Freitas, L. Korala, L. X. Reynolds, S. A. Haque, S. L. Brock and A. F. Nogueira, Phys. Chem. Chem. Phys., 2012, 14, 15180–15184 RSC
.
- A. Hitihami-Mudiyanselage, K. Senevirathne and S. L. Brock, ACS Nano, 2013, 7, 1163–1170 CrossRef CAS PubMed
.
- A. Hitihami-Mudiyanselage, K. Senevirathne and S. L. Brock, Chem. Mater., 2014, 26, 6251–6256 CrossRef CAS
.
- S. K. Gill, P. Brown and L. J. Hope-Weeks, J. Sol-Gel Sci. Technol., 2011, 57, 68–75 CrossRef CAS
.
- S. K. Gill and L. J. Hope-Weeks, Chem. Commun., 2009, 4384–4386 RSC
.
- X. Qiangfeng, W. Ding, Y. Zhenglong, J. Garay, Z. Minjuan and L. Yunfeng, Nano Res., 2010, 3, 685–693 CrossRef
.
- S. Sánchez-Paradinas, D. Dorfs, S. Friebe, A. Freytag, A. Wolf and N. C. Bigall, Adv. Mater., 2015, 27, 6152–6156 CrossRef PubMed
.
- S. Naskar, J. F. Miethe, S. Sánchez-Paradinas, N. Schmidt, K. Kanthasamy, P. Behrens, H. Pfnür and N. C. Bigall, Chem. Mater., 2016, 28, 2089–2099 CrossRef CAS
.
- N. Gaponik, J. Mater. Chem., 2010, 20, 5174–5181 RSC
.
- V. Lesnyak, S. V. Voitekhovich, P. N. Gaponik, N. Gaponik and A. Eychmüller, ACS Nano, 2010, 4, 4090–4096 CrossRef CAS PubMed
.
- V. Lesnyak, A. Wolf, A. Dubavik, L. Borchardt, S. V. Voitekhovich, N. Gaponik, S. Kaskel and A. Eychmüller, J. Am. Chem. Soc., 2011, 133, 13413–13420 CrossRef CAS PubMed
.
- T. Hendel, V. Lesnyak, L. Kühn, A.-K. Herrmann, N. C. Bigall, L. Borchardt, S. Kaskel, N. Gaponik and A. Eychmüller, Adv. Funct. Mater., 2013, 23, 1903–1911 CrossRef CAS
.
- A. Wolf, V. Lesnyak, N. Gaponik and A. Eychmüller, J. Phys. Chem. Lett., 2012, 3, 2188–2193 CrossRef CAS PubMed
.
- J. Yuan, D. Wen, N. Gaponik and A. Eychmüller, Angew. Chem., Int. Ed., 2013, 52, 976–979 CrossRef CAS PubMed
.
- V. Sayevich, B. Cai, A. Benad, D. Haubold, L. Sonntag, N. Gaponik, V. Lesnyak and A. Eychmüller, Angew. Chem., Int. Ed., 2016, 55, 6334–6338 CrossRef CAS PubMed
.
- H. Kawasaki, Nanotechnol. Rev., 2013, 2, 5–25 CAS
.
-
http://www.aerogel.org, (accessed September 2016).
- N. C. Bigall, A.-K. Herrmann, M. Vogel, M. Rose, P. Simon, W. Carrillo-Cabrera, D. Dorfs, S. Kaskel, N. Gaponik and A. Eychmüller, Angew. Chem., Int. Ed., 2009, 48, 9731–9734 CrossRef CAS PubMed
.
- N. C. Bigall and A. Eychmüller, Philos. Trans. R. Soc., A, 2010, 368, 1385–1404 CrossRef CAS PubMed
.
- A.-K. Herrmann, P. Formanek, L. Borchardt, M. Klose, L. Giebeler, J. Eckert, S. Kaskel, N. Gaponik and A. Eychmüller, Chem. Mater., 2013, 26, 1074–1083 CrossRef
.
- W. Liu, A.-K. Herrmann, D. Geiger, L. Borchardt, F. Simon, S. Kaskel, N. Gaponik and A. Eychmüller, Angew. Chem., Int. Ed., 2012, 51, 5743–5747 CrossRef CAS PubMed
.
- W. Liu, P. Rodriguez, L. Borchardt, A. Foelske, J. Yuan, A.-K. Herrmann, D. Geiger, Z. Zheng, S. Kaskel, N. Gaponik, R. Kötz, T. J. Schmidt and A. Eychmüller, Angew. Chem., Int. Ed., 2013, 52, 9849–9852 CrossRef CAS PubMed
.
- D. Wen, W. Liu, A.-K. Herrmann and A. Eychmüller, Chem. – Eur. J., 2014, 20, 4380–4385 CrossRef CAS PubMed
.
- D. Wen, A.-K. Herrmann, L. Borchardt, F. Simon, W. Liu, S. Kaskel and A. Eychmüller, J. Am. Chem. Soc., 2014, 136, 2727–2730 CrossRef CAS PubMed
.
- C. Zhu, D. Du, A. Eychmüller and Y. Lin, Chem. Rev., 2015, 115, 8896–8943 CrossRef CAS PubMed
.
- W. Liu, A.-K. Herrmann, N. C. Bigall, P. Rodriguez, D. Wen, M. Oezaslan, T. J. Schmidt, N. Gaponik and A. Eychmüller, Acc. Chem. Res., 2015, 48, 154–162 CrossRef CAS PubMed
.
- D. Wen, W. Liu, D. Haubold, C. Zhu, M. Oschatz, M. Holzschuh, A. Wolf, F. Simon, S. Kaskel and A. Eychmüller, ACS Nano, 2016, 10, 2559–2567 CrossRef CAS PubMed
.
- B. Cai, D. Wen, W. Liu, A.-K. Herrmann, A. Benad and A. Eychmüller, Angew. Chem., Int. Ed., 2015, 54, 13101–13105 CrossRef CAS PubMed
.
- C. Ziegler, S. Klosz, L. Borchardt, M. Oschatz, S. Kaskel, M. Friedrich, R. Kriegel, T. Keilhauer, M. Armbrüster and A. Eychmüller, Adv. Funct. Mater., 2016, 26, 1014–1020 CrossRef CAS
.
- X. Gao, R. J. Esteves, T. T. H. Luong, R. Jaini and I. U. Arachchige, J. Am. Chem. Soc., 2014, 136, 7993–8002 CrossRef CAS PubMed
.
- L. Nahar, R. J. A. Esteves, S. Hafiz, Ü. Özgür and I. U. Arachchige, ACS Nano, 2015, 9, 9810–9821 CrossRef CAS PubMed
.
- G. Nyström, M. P. Fernández-Ronco, S. Bolisetty, M. Mazzotti and R. Mezzenga, Adv. Mater., 2016, 28, 472–478 CrossRef PubMed
.
- S. L. Brock, M. Sanabria, J. Nair, S. L. Suib and T. Ressler, J. Phys. Chem. B, 2001, 105, 5404–5410 CrossRef CAS
.
- N. Pinna and M. Niederberger, Angew. Chem., Int. Ed., 2008, 47, 5292–5304 CrossRef CAS PubMed
.
-
R. Deshmukh and M. Niederberger, The Sol–Gel Handbook, Wiley-VCH Verlag GmbH & Co. KGaA, 2015, pp. 29–70 Search PubMed
.
- C. A. Morris, M. L. Anderson, R. M. Stroud, C. I. Merzbacher and D. R. Rolison, Science, 1999, 284, 622–624 CrossRef CAS PubMed
.
- M. L. Anderson, C. A. Morris, R. M. Stroud, C. I. Merzbacher and D. R. Rolison, Langmuir, 1999, 15, 674–681 CrossRef CAS
.
- M. L. Anderson, R. M. Stroud, C. A. Morris, C. I. Merzbacher and D. R. Rolison, Adv. Eng. Mater., 2000, 2, 481–488 CrossRef
.
- N. Leventis, I. A. Elder, G. J. Long and D. R. Rolison, Nano Lett., 2002, 2, 63–67 CrossRef CAS
.
- F. J. Heiligtag, W. Cheng, V. R. de Mendonça, M. J. Süess, K. Hametner, D. Günther, C. Ribeiro and M. Niederberger, Chem. Mater., 2014, 26, 5576–5584 CrossRef CAS
.
- F. J. Heiligtag, N. Kränzlin, M. J. Süess and M. Niederberger, J. Sol-Gel Sci. Technol., 2014, 70, 300–306 CrossRef CAS
.
- R. O. da Silva, F. J. Heiligtag, M. Karnahl, H. Junge, M. Niederberger and S. Wohlrab, Catal. Today, 2015, 246, 101–107 CrossRef CAS
.
- J. Polleux, N. Pinna, M. Antonietti and M. Niederberger, Adv. Mater., 2004, 16, 436–439 CrossRef CAS
.
- J. Polleux, N. Pinna, M. Antonietti, C. Hess, U. Wild, R. Schlögl and M. Niederberger, Chem. – Eur. J., 2005, 11, 3541–3551 CrossRef CAS PubMed
.
- E. R. Leite, T. R. Giraldi, F. M. Pontes, E. Longo, A. Beltran and J. Andres, Appl. Phys. Lett., 2003, 83, 1566–1568 CrossRef CAS
.
- E. J. H. Lee, C. Ribeiro, E. Longo and E. R. Leite, Chem. Phys., 2006, 328, 229–235 CrossRef CAS
.
- Z. Zhuang, J. Zhang, F. Huang, Y. Wang and Z. Lin, Phys. Chem. Chem. Phys., 2009, 11, 8516–8521 RSC
.
- V. Müller, M. Rasp, G. Stefanic, J. Ba, S. Günther, J. Rathousky, M. Niederberger and D. Fattakhova-Rohlfing, Chem. Mater., 2009, 21, 5229–5236 CrossRef
.
- F. Rechberger, R. Städler, E. Tervoort and M. Niederberger, J. Sol-Gel Sci. Technol., 2016 DOI:10.1007/s10971-016-4156-3
.
- D. Taroata, W.-J. Fischer, T. A. Cheema, G. Garnweitner and G. Schmid, IEEE Trans. Dielectr. Electr. Insul., 2012, 19, 298–304 CrossRef CAS
.
- S. Liu, L. Huang, W. Li, X. Liu, S. Jing, J. Li and S. O'Brien, Nanoscale, 2015, 7, 11766–11776 RSC
.
- R. Deshmukh, G. Zeng, E. Tervoort, M. Staniuk, D. Wood and M. Niederberger, Chem. Mater., 2015, 27, 8282–8288 CrossRef CAS
.
- R. Deshmukh, E. Tervoort, J. Käch, F. Rechberger and M. Niederberger, Dalton Trans., 2016, 45, 11616–11619 RSC
.
- Y. Xia, P. Yang, Y. Sun, Y. Wu, B. Mayers, B. Gates, Y. Yin, F. Kim and H. Yan, Adv. Mater., 2003, 15, 353–389 CrossRef CAS
.
- C. N. R. Rao and A. Govindaraj, Adv. Mater., 2009, 21, 4208–4233 CrossRef CAS
.
- M. Osada and T. Sasaki, Adv. Mater., 2012, 24, 210–228 CrossRef CAS PubMed
.
- J. N. Coleman, M. Lotya, A. O'Neill, S. D. Bergin, P. J. King, U. Khan, K. Young, A. Gaucher, S. De, R. J. Smith, I. V. Shvets, S. K. Arora, G. Stanton, H.-Y. Kim, K. Lee, G. T. Kim, G. S. Duesberg, T. Hallam, J. J. Boland, J. J. Wang, J. F. Donegan, J. C. Grunlan, G. Moriarty, A. Shmeliov, R. J. Nicholls, J. M. Perkins, E. M. Grieveson, K. Theuwissen, D. W. McComb, P. D. Nellist and V. Nicolosi, Science, 2011, 331, 568–571 CrossRef CAS PubMed
.
- S. M. Jung, H. Y. Jung, M. S. Dresselhaus, Y. J. Jung and J. Kong, Sci. Rep., 2012, 2, 849 Search PubMed
.
- Y. Tang, K. L. Yeo, Y. Chen, L. W. Yap, W. Xiong and W. Cheng, J. Mater. Chem. A, 2013, 1, 6723–6726 CAS
.
- W. Cheng, F. Rechberger and M. Niederberger, Nanoscale, 2016, 8, 14074–14077 RSC
.
- W. Lei, V. N. Mochalin, D. Liu, S. Qin, Y. Gogotsi and Y. Chen, Nat. Commun., 2015, 6, 8849 CrossRef CAS PubMed
.
- Z. Liu, K. Xu, P. She, S. Yin, X. Zhu and H. Sun, Chem. Sci., 2016, 7, 1926–1932 RSC
.
- S. Chen, G. Liu, H. Yadegari, H. Wang and S. Z. Qiao, J. Mater. Chem. A, 2015, 3, 2559–2563 CAS
.
- W. Cheng, F. Rechberger and M. Niederberger, ACS Nano, 2016, 10, 2467–2475 CrossRef CAS PubMed
.
- M. A. Worsley, S. J. Shin, M. D. Merrill, J. Lenhardt, A. J. Nelson, L. Y. Woo, A. E. Gash, T. F. Baumann and C. A. Orme, ACS Nano, 2015, 9, 4698–4705 CrossRef CAS PubMed
.
- G. A. Ozin, Energy Environ. Sci., 2015, 8, 1682–1684 CAS
.
|
This journal is © The Royal Society of Chemistry 2017 |
Click here to see how this site uses Cookies. View our privacy policy here.