DOI:
10.1039/C7FD00178A
(Paper)
Faraday Discuss., 2017,
202, 521-529
Penrose triangles of the fossil-to-bio-based transition
Received
16th July 2017
, Accepted 25th July 2017
First published on 27th July 2017
Abstract
Transition within the chemical industry from fossil to green feedstocks is a complex process characterized by the generation of commercially viable feedstock–process–product triangles. The research in this area encompasses a great diversity of relevant topics. A number of those topics have been addressed within this volume of Faraday Discussions and are summarized in this paper. They are categorized and discussed along with seven general questions arising from the feedstock–process–product triangles. Opportunities are identified that should make more of these triangles technically and economically feasible. The future role of renewable electricity as the primary energy source for the bio-based industry is emphasized.
Introduction
The transition from a fossil-based to a bio-based chemical industry is a global process occurring in the context of sustainable development of our planet. Although the process itself is inevitable and irreversible, the vast majority of researchers working in the field agree that the pace at which it is proceeding is still far from satisfactory. The essence of the fossil-to-bio transition lies in fact in the successful generation of commercially viable feedstock–process–product triangles that offer clear benefits to the stakeholders concerned (farmers, industry, governments, end-users, consumers, etc.). Unfortunately, for the time being, many of these triangles still appear to be a kind of “Penrose Triangle”† (Fig. 1), described by Lionel and Roger Penrose1 as “impossibility in its purest form”. What challenges need to be met and what questions need to be answered in order to make more of these triangles viable? The Faraday Discussion “Bio-Resources: Feeding a Sustainable Chemical Industry” has allowed debate of the latest developments in science and technology that address those questions and challenges and create new opportunities.
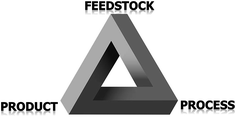 |
| Fig. 1 Penrose triangle for a fossil-to-bio transition. | |
From fossil-based to bio-based: important differences
Before more deeply discussing the challenges occurring in the transition from a fossil-based to bio-based industry, it is good to realize some important characteristic features and differences between the two types of industry. These features and differences are briefly described below. Some of them may present additional challenges when it comes to development of a viable bio-based process.
Feedstock diversity and variability
Generally speaking, the variability of bio-feedstocks in terms of chemical composition and physical properties is much greater than in fossil fuels. Although both natural gas and crude oil stocks occur in different grades and compositions, the feedstocks for the bioprocesses are more diverse ranging from crops, through to wood, algae, industrial wastewaters, municipal organic wastes, animal wastes, food wastes, etc.2 Furthermore, within biologically the same feedstock differences in the composition and properties are often seen, depending on the climate and water/soil conditions in which the feedstock has been grown. The diversity of the bio-feedstocks is usually considered a drawback because of the increased flexibility of the processing plant that is required to deal with varying feedstocks. However, it can also be seen as an opportunity to bring a more diverse range of products to the market.
Diversity of processes and operations
Usually, a biorefinery includes more diverse types of processes and operations than an oil refinery. Next to “conventional” chemical and catalytic processes that occur in a liquid or gas phase, biorefineries often include mechanical/chemical pre-processing of solid feedstocks, aerobic and anaerobic fermentations, enzymatic reactions, plus a range of microbial processes.3 This brings additional challenges related to process plant and site integration.
Transporting feedstocks
Contrary to the transport of gas and oil, which largely occurs via pipeline infrastructures, the vast majority of bio-feedstocks need to be transported on land or water from the place of harvest to the processing location. Two alternative transport scenarios (centralized plant versus decentralized plant) have been considered in the literature,4 but for both cases transport remains an important cost.
Feedstock versus market – regionalization
Since the long-distance transport of biomass is troublesome and expensive, regionalization of bio-based production will occur. Contrary to the current situation, where many oil refineries are built and operated in regions and countries that do not have oil deposits themselves, with a bio-based economy, countries lean in biomass, such as the Gulf states, will have to import bio-based platform chemicals from elsewhere. Furthermore, since the product portfolio of a biorefinery depends strongly on the type of feedstock it converts,4,5 and the feedstocks often have local character, the manufacturing of certain types of bio-based chemical products will occur locally.
Susceptibility to the force of nature
Lastly, but definitely not least, natural disasters such as floods, droughts, wildfires or agriculture and forest pests can affect the availability of the biomass in a given region and consequently the prices of the respective bio-based products, both regionally and globally. In the long term, climate change will also influence the dynamics of the bio-based economy.
Questions arising from feedstock–process–product triangles
Numerous questions arise within each feedstock–process–product triangle and these questions need to be adequately addressed. The papers presented in this volume of Faraday Discussions can be categorized according to seven general questions dealing with various elements of the triangle, located either at its vertices or between them.
Question 1 (feedstock): how to improve the analytical tools and develop standardized methods for the evaluation of feedstocks?
The need for improvement of the current analytical tools has been addressed by Galkin et al. (DOI: 10.1039/C7FD00046D), who have pointed out the shortcomings of the current analytical techniques used for biomass evaluation in the pulping industry. The authors postulated development of analytical tools for targeting all the wood components, including the generated fractions, as well as standardized methods for evaluating and reporting yields. In another paper by Hayes et al. (DOI: 10.1039/C7FD00081B), near-infrared spectroscopy was proposed as a suitable method for rapid, low-cost analysis of the major lignocellulosic components of waste paper/cardboard.
Question 2 (feedstock ↔ product): how to select a suitable feedstock for the desired products?
The importance of this issue was demonstrated in the paper by Wood et al. (DOI: 10.1039/C7FD00044H) where eight different feedstocks (hardwood, softwood, cereal straws and dicotyledonous crops) were exposed to microwave-assisted liquid hot water pre-treatment. The paper shows that fundamental differences in the cell wall composition resulted in considerable differences in feedstock suitability with regard to the quantity of released products.
Question 3 (feedstock ↔ process): how to pretreat and process feedstocks?
Selection of a pre-treatment technology is of fundamental importance to the entire process economics. Currently, steam-explosion is the most commonly used method for the pre-treatment of the lignocellulosic biomass. Seidel et al. (DOI: 10.1039/C7FD00066A) have pointed out that the explosive decompression at the end of this step could enhance the enzymatic cellulose digestibility of hardwood and herbaceous plants. Weigand et al. (DOI: 10.1039/C7FD00059F) proposed the use of protic low-cost ionic liquids in order to increase enzymatic glucose yields from willow biomass. In addition, Ferrini et al. (DOI: 10.1039/C7FD00069C) have shown the importance of solvent effects during functionalization of the propyl side-chain in lignin oil obtained from the deconstruction of lignocellulosic materials via catalytic upstream biorefining. Microwave-assisted acidolysis of the lignocellulosic biomass presents an effective approach to produce high purity lignin and fermentable chemicals from softwood, as demonstrated by Zhou et al. (DOI: 10.1039/C7FD00102A). Importantly, the lignin was isolated largely intact and retained the original structure of the native lignin in the feedstock. Interesting findings with regard to microalgae biomass were presented by Zhou et al.(DOI: 10.1039/C7FD00065K). These authors pyrolized raw biomass samples along with samples pre-treated through extraction of the lipids or saccharides. It appeared that fractional pyrolysis of the pretreated microalgae not only increased the bio-oil yield but also improved its quality.
Question 4 (feedstock ↔ process ↔ product): how to develop a new process?
This short question actually hides a multitude of situations, strategies and approaches. In some cases, plant flexibility is the central issue when feedstocks (and sometimes also products) vary. In other cases, the optimum process configuration needs to be found for a narrowly defined feedstock and product. Lapkin et al. (DOI: 10.1039/C7FD00073A) have proposed an interesting generic method for automation of route identification and optimisation based on data-mining and network analysis. The method was applied to generate multiple possible reaction routes for converting limonene into paracetamol. In the future, this approach should enable rapid concurrent optimization of the reaction network and the corresponding processes. The paper by Coma et al. (DOI: 10.1039/C7FD00070G) focusses on flexibility issues during development of a process for converting a highly variable feedstock (organic waste) into platform chemicals. The key to success is having flexible anaerobic fermentation and hydrothermal processes that can treat complex biomass as a whole to obtain a range of products within an integrated biorefinery concept. Cárdenas-Fernández et al. (DOI: 10.1039/C7FD00094D) have presented a concept for developing an integrated biorefinery to convert sugar beet pulp into chemicals and pharmaceutical intermediates. The process is based on steam explosion (thermal hydrolysis) of wet sugar beet pulp, followed by bioethanol fermentation, enzyme-membrane fractionation of the sugar beet pectin, and bioconversion of D-galacturonic acid (transaminase) and L-arabinose (transketolase). Another integrated process, to synthesize 1,5-pentanediol (PDO) and 1,6-hexanediol (HDO) from lignocellulosic biomass, has been proposed by He et al. (DOI: 10.1039/C7FD00036G). The route goes via furfural and terahydrofuran-dimethanol, respectively, and techno-economic analysis demonstrated that this approach could produce HDO and PDO at a minimum selling price of $4090 per ton. In addition, Bajracharya et al. (DOI: 10.1039/C7FD00050B) have studied bioelectrochemical conversion of carbon dioxide, as a sustainable feedstock, into chemicals using microorganisms as the catalyst. This microbial electrosynthesis-based process produces acetate as the primary product.
Question 5 (process): how to improve the effectiveness of the reactions?
The most common answer to this question is through development of new, better catalysts. Liu et al. (DOI: 10.1039/C7FD00041C) have disclosed Pt nanoparticles supported on bamboo shoot-derived porous heteroatom doped carbon materials as highly active catalysts for controlled hydrogenation of furfural in aqueous media. They have shown that the product selectivity could be easily modulated by controlling the carbonization temperature of the porous heteroatom doped carbon support and the reaction conditions (temperature and H2 pressure). Albert (DOI: 10.1039/C7FD00047B) has investigated optimization of polyoxometalate catalysts for a fractionated oxidation of lignocellulosic biomass to produce formic acid and high-grade cellulose. One of those catalysts, the Lindqvist-type POM K5V3W3O19, has been shown to catalyse selective oxidation of only the hemicellulose and lignin to formic acid, while the cellulose fraction remained untapped. Finally, Huang et al. (DOI: 10.1039/C7FD00039A) have investigated the role of acid co-catalysts during selective production of mono-aromatics from lignocellulose over a Pd/C catalyst and they found that HCl and H2SO4 showed superior catalytic performances over H3PO4 and CH3COOH.
Question 6 (process): how to improve the product separation?
New and interesting methods for improved product separation have been disclosed within this current volume of Faraday Discussions. Xia and Matharu (DOI: 10.1039/C7FD00035A) have reported, for the first time in the literature, an acid-free subcritical water extraction of pectin from mango peel. Yields of up to 18.34%, with the degree of esterification exceeding 70%, were reported. Lorenz et al. (DOI: 10.1039/C7FD00053G) have suggested hydrolyzing cellulose with HCl vapour, in order to facilitate the isolation of cellulose nano-crystals.
Question 7 (product): how to increase the market share of bio-based products?
The enormous variety of bio-based products results in a multitude of answers to the above question and related strategies. According to Bomtempo et al. (DOI: 10.1039/C7FD00052A), new platform chemicals derived from biomass should fulfil several criteria, in that they should: “be an intermediate molecule, have a flexible structure to make a wide range of derivatives possible, be cost competitive at the level of the platform molecule and at the level of the derivatives, be capable of generating scale and scope economies in the value chain, be organized within an innovation ecosystem and have associated well-developed mechanisms of governance”. Jin et al. (DOI: 10.1039/C7FD00049A) have proposed a 10-step procedure that should be applied when developing new bio-based solvents. The procedure includes various functional, technical and economic criteria that a bio-based solvent needs to fulfil, in order to become a marketable product. Bio-based solvents are an example of bio-based products that have been developed for use in chemical manufacturing. Other examples of such products include catalysts and sorbents. In this context, Golikova et al. (DOI: 10.1039/C7FD00042A) have studied a new biocatalyst based on glucose oxidase, while Zuin et al. (DOI: 10.1039/C7FD00056A) have presented polysaccharide-derived mesoporous materials (Starbon® materials) as sustainable sorbents for solid-phase extraction of naturally-occurring bioactive phenolic compounds. In the case of bio-based polymeric materials, which are closer to the consumer market, new functionalities or improved properties are usually the deciding factor with respect to their commercial success. An example is the polymeric materials composed only of methylated softwood lignin derivatives reported by Wang et al. (DOI: 10.1039/C7FD00083A) that can exhibit better tensile behaviour than polystyrene. As pointed out by these authors, mistaken assumptions from the past about the lignin configuration have hindered the development of these materials for more than 50 years. In another paper, Pérocheau Arnaud et al. (DOI: 10.1039/C7FD00057J) have presented novel polyesters with higher glass transition temperatures that are based on branched diols from biomass, while Alberts and Rothenberg (DOI: 10.1039/C7FD00054E) have described the development and commercialization of Plantics-GX: a plant-based biodegradable thermoset plastic.
Michael Faraday and the bio-world
The ground-breaking fundamental works of Michael Faraday on electricity and electromagnetism, originally published as a series of articles in the Philosophical Transactions of the Royal Society of London,6,7 have largely contributed to the utilization of electricity in technology. The link between electricity and the bio-world is clear, at least hypothetically. The works of Miller and Urey8,9 as well as some later studies (e.g. by the group of Bada10,11) point at electricity as the “Mother of All Bio” as an electric spark discharged circa 3.5 billion years ago converted the primordial soup into the first amino acids. In other words: “no electricity = no bio”. Back to the 21st century, electricity-based technologies attract more and more interest from researchers working in the area of bio-based processing. Electric fields have been investigated in the context of electro-fermentation (e.g. Schievano et al.12 and Chandrasekhar et al.13). Pulsed electric fields have various bio-related applications including within algae treatment, large-scale biomass (e.g. sugar beets) processing or the recovery of valuable products from plants and microorganisms (Golberg et al.,14 Frey et al.15). Algae are harvested using electromagnets and submicron-sized magnetic particles (e.g. Xu et al.16 and Cerff et al.17). Induction heating has been proposed for fast pyrolysis of different types of biomass, including rice straw, sugarcane bagasse, coconut shells, Napier grass, pinewood sawdust and sewage sludge (e.g. Tsai18,19 and Muley20). The heating rates in those reactors are as high as 500 °C min−1, which leads to higher quality bio-oils being obtained and lower carbon deposition. Biomass pyrolysis can also be advantageously performed using microwaves21,22 (a conventional microwave oven is a Faraday cage!). Microwave heating is also applicable to other bio-based processes, for instance esterifications23 or plant extraction,24 while a microwave-induced plasma can be used for gasification of waste biomass to synthesis gas.25 Finally, another form of electromagnetic radiation – light – is widely used in the cultivation of microalgae.26,27
On July 7, 1855, Michael Faraday took a short boat trip on the River Thames. That trip resulted in a famous letter, written on the same day, addressed to the Editor of The Times. In this letter, Faraday expressed his deep concerns about pollution of the river, calling it “a real sewer”. Two weeks later Punch magazine illustrated this with a cartoon of the famous scholar giving his card to the “Dirty Fellow” – Father Thames. If Michael Faraday were with us today, he would be happy to see that electricity-based processing methods can deliver promising results in the context of wastewater management and sewage treatment. Some of those methods go beyond only treatment and convert sewage sludge into useful products. Examples include production of pyrolytic liquids from industrial sewage sludge using induction heating,28 production of bio-fuels via microwave-assisted pyrolysis of sewage sludge29 or plasma gasification of sewage sludge.30,31
Concluding remarks
The contributions present in this volume of Faraday Discussions not only address some of the questions and challenges of the fossil-to-bio-based transition but also demonstrate new opportunities which, if properly addressed and developed further, should lead to novel, commercially attractive concepts. Electricity-based technologies that build on Michael Faraday’s scientific legacy are examples of such opportunities. In the long term, electricity is destined to play the key role in process industries, especially if obtained from a fully renewable source, as it is the most widely available and most flexible form of energy. This also holds true for the fossil-to-bio-based transition, where energy consumption is presently one of the most important challenges. Bioprocesses are often highly energy-demanding and the energy cost significantly affects the process economy. A bio-based industry that utilizes fossil fuel energy will never be really “green” and a gradual shift to cheap, renewable electricity as the primary energy source is needed. In the long term, such a shift, along with the introduction of modularity during plant design, should result in a dramatic change in the bio-process economy. Future bio-processing plants will be modular and green electricity-driven (Fig. 2). Such an evolution will further help in converting the “Penrose” triangles of today that are associated with the fossil-to-bio-based transition into viable feedstock–process–product solutions.
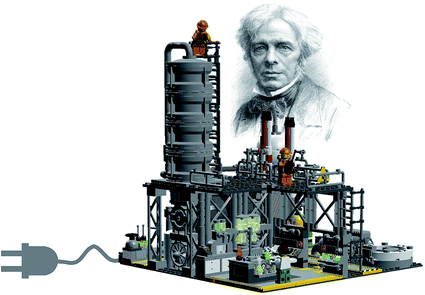 |
| Fig. 2 Future bioprocessing plant: modular and green electricity-driven (plant model designed by LEGO® Ideas member Ymarilego). Image used by permission, ©2017 The LEGO Group; source for the portrait of Michael Faraday: “Michael Faraday” by John Hall Gladstone (3rd edn, Macmillan and Co., London, 1874). | |
References
- L. S. Penrose and R. Penrose, Br. J. Psychol., 1958, 49, 31–33 CrossRef CAS PubMed.
-
J. S. Golden and R. B. Handfield, Why Biobased? Opportunities in the Emerging Bioeconomy, 2014, https://www.biopreferred.gov/files/WhyBiobased.pdf Search PubMed.
- S. K. Maity, Renewable Sustainable Energy Rev., 2015, 43, 1427–1445 CrossRef CAS.
- T. T. H. Nguyen, Y. Kikuchi, M. Noda and M. Hiraoa, Environ. Prog. Sustainable Energy, 2016, 35, 174–182 CrossRef CAS.
- V. Chambost and P. R. Stuart, Ind. Biotechnol., 2007, 3, 112–119 CrossRef.
-
M. Faraday, Experimental Researches in Electricity, Richard and John Edward Taylor, London, 1839, vol. I Search PubMed.
-
M. Faraday, Experimental Researches in Electricity, Richard and John Edward Taylor, London, 1844, vol. II Search PubMed.
- S. L. Miller, Science, 1953, 117, 528–529 CAS.
- S. L. Miller and H. C. Urey, Science, 1959, 130, 245–251 CAS.
- A. P. Johnson, H. J. Cleaves, J. P. Dworkin, D. P. Glavin, A. Lazcano and J. L. Bada, Science, 2008, 322, 404 CrossRef CAS PubMed.
- E. T. Parker, H. J. Cleaves, J. P. Dworkin, D. P. Glavinc, M. Callahan, A. Aubrey, A. Lazcano and J. L. Bada, Proc. Natl. Acad. Sci. U. S. A., 2011, 108, 5526–5531 CrossRef CAS PubMed.
- A. Schievano, T. Pepé Sciarria, K. Vanbroekhoven, H. De Wever, S. Puig, S. J. Andersen, K. Rabaey and D. Pant, Trends Biotechnol., 2016, 34, 866–878 CrossRef CAS PubMed.
- K. Chandrasekhar, K. Amulya and S. Venkata Mohan, Waste Manag., 2015, 45, 57–65 CrossRef CAS PubMed.
- A. Golberg, M. Sack, J. Teissie, G. Pataro, U. Pliquett, G. Saulis, T. Stefan, D. Miklavcic, E. Vorobiev and W. Frey, Biotechnol. Biofuels, 2016, 9, 94 CrossRef PubMed.
-
W. Frey, C. Gusbeth, T. Sakugawa, M. Sack, G. Mueller, J. Sigler, E. Vorobiev, N. Lebovka, I. Àlvarez, J. Raso, L. C. Heller, M. A. Malik, C. Eing and J. Teissie, in Bioelectrics, ed. H. Akiyama and R. Heller, Springer Japan, Tokyo, 2017, ch. 6, pp. 389–486 Search PubMed.
- L. Xu, C. Guo, F. Wanga, S. Zheng and C.-Z. Liu, Bioresour. Technol., 2011, 102, 10047–10051 CrossRef CAS PubMed.
- M. Cerff, M. Morweiser, R. Dillschneider, A. Michel, K. Menzel and C. Posten, Bioresour. Technol., 2012, 118, 289–295 CrossRef CAS PubMed.
- W. T. Tsai, M. K. Lee and Y. M. Chang, J. Anal. Appl. Pyrolysis, 2006, 76, 230–337 CrossRef CAS.
- M. K. Lee, W.-T. Tsai, Y.-L. Tsai and S. H. Lin, J. Anal. Appl. Pyrolysis, 2010, 88, 110–116 CrossRef CAS.
- P. D. Muley, C. Henkel, K. K. Abdollahi and D. Boldor, Energy Fuels, 2015, 29, 7375–7385 CrossRef CAS.
- Y.-F. Huang, P.-T. Chiueh and S.-L. Lo, Sustainable Environ. Res., 2016, 26, 103–109 CrossRef.
- H. Marion Morgan Jr, Q. Bu, J. Liang, Y. Liu, H. Mao, A. Shi, H. Lei and R. Ruan, Bioresour. Technol., 2017, 230, 112–121 CrossRef PubMed.
- N. Azcan and A. Danisman, Fuel, 2008, 87, 1781–1788 CrossRef CAS.
-
R. B. Mato Chain, J. Monzó-Cabrera and K. Solyom, in Alternative Energy Sources for Green Chemistry, ed. G. Stefanidis and A. Stankiewicz, RSC, Cambridge, 2016, ch. 2, pp. 34–63 Search PubMed.
- G. S. J. Sturm, A. Navarrete Muñoz, P. V. Aravind and G. D. Stefanidis, IEEE Trans. Plasma Sci., 2016, 44, 670–678 CrossRef CAS.
- M. Glemser, M. Heining, J. Schmidt, A. Becker, D. Garbe, R. Buchholz and T. Brück, Appl. Microbiol. Biotechnol., 2016, 100, 1077–1088 CrossRef CAS PubMed.
- C.-Y. Chen, K.-L. Yeh, R. Aisyah, D.-J. Lee and J.-S. Chang, Bioresour. Technol., 2011, 102, 71–81 CrossRef CAS PubMed.
- W.-T. Tsai, J.-H. Chang, K.-J. Hsien and Y.-M. Chang, Bioresour. Technol., 2009, 100, 406–412 CrossRef CAS PubMed.
- W. Zuo, Y. Tian and N. Ren, Waste Manag., 2011, 31, 1321–1326 CrossRef CAS PubMed.
- J. Balgaranova, Waste Manage. Res., 2003, 21, 38–41 CrossRef CAS PubMed.
- A. Mountouris, E. Voutsas and D. Tassios, Energy Convers. Manage., 2008, 49, 2264–2271 CrossRef CAS.
Footnote |
† Triangular object made of three straight bars that have a square cross-section, which meet at right angles at the vertices of the triangle they form. Also called an “impossible tribar”, since such a combination of properties cannot be realized by any three-dimensional object in ordinary Euclidean space. First created by the Swedish artist Oscar Reutersvärd and described by the British psychiatrist Lionel Penrose and his son, mathematician Sir Roger Penrose.1 |
|
This journal is © The Royal Society of Chemistry 2017 |
Click here to see how this site uses Cookies. View our privacy policy here.