DOI:
10.1039/C6RA21545A
(Paper)
RSC Adv., 2016,
6, 96245-96249
Effect of hyperbranched polyethyleneimine grafting functionalization of carbon nanotubes on mechanical, thermal stability and electrical properties of carbon nanotubes/bismaleimide composites
Received
28th August 2016
, Accepted 3rd October 2016
First published on 3rd October 2016
Abstract
Hyperbranched polyethyleneimine (PEI) grafted CNTs (CNTs-PEI) were used to reinforce bismaleimide (BMI) composites. The effect of CNTs-PEI on mechanical properties, thermal resistance and electrical conductivity of composites was investigated. Evaluation of mechanical properties showed that the mechanical properties of CNTs-PEI/BMI composites were higher than that of CNTs/BMI composites. A maximum increase of impact strength up to 44% compared with that of pure BMI was observed in CNTs-PEI/BMI composites. The flexural strength of CNTs-PEI/BMI composites reached the maximum of 205 MPa which was much higher than that of CNTs/BMI composites. Similar tendency on the flexural modulus of the composites was observed. The maximum Tg of CNTs/BMI composites and CNTs-PEI/BMI composites were 224 °C and 240 °C respectively. Electrical conductivity of CNTs-PEI/BMI composites increased by 14 magnitude compared with pure BMI, while only 8 magnitude increased in CNTs/BMI composites.
1. Introduction
Bismaleimide (BMI) resins possess excellent thermal stability, dielectric properties, mechanical properties and an attractive cost/performance ratio, and have been widely applied in the fields of electronics, insulation, adhesives and other areas.1,2 However, the inherent brittleness and low thermal conductivity of the BMI matrix have limited its broader applications especially in the fields of electronic and micro-mechanical devices. With the efforts of researchers, many methods have been proposed to improve the toughness and thermal conductivity of the BMI matrix. Among them, carbon nanotubes (CNTs) as a modifier and reinforcement of BMI matrix have attracted intensive attention.
CNTs have been regarded as the ultimate reinforcement material because of its ultrahigh length to diameter ratio, outstanding mechanical properties, excellent thermal properties and electrical properties, which have attracted intensive attention in nanocomposites, electrochimica, sensor, catalyst, and other areas.3–5 However, CNTs are hard to disperse well in almost all kinds of polymer composites due to its large surface areas and strong intrinsic van der Waals forces.6,7 The advantages of CNTs, especially the mechanical properties, cannot fully show up because of the weak interface between CNTs and matrix.8,9 All of these mentioned above restricts the performance and the application of CNTs in polymer composites.
For many years, researchers have made a lot of efforts to make CNTs uniformly dispersed in polymer matrix and to enhance the interfacial property of CNTs and polymer10–12 to improve the mechanical property,13,14 thermal property,15,16 electrical property17–19 of CNTs/polymer composites. Some mechanical methods, such as calendaring process, ball milling, stir and extrusion, are used during mixing process of CNTs and the matrix.20,21 In addition to the improvement of processing technology, functionalization of CNTs, such as surface atoms replacement, surface grafting and surface coating, is universally used to change the surface chemical structure of CNTs.22–27 Surface grafting with hyperbranched polymers is an efficient method for functionalization of CNTs, because hyperbranched polymers have highly branched, non-entangle architecture, a large number of terminal groups, low viscosity, high rheological behavior and good solubility. CNTs grafted hyperbranched polymer can not only improve dispersibility of CNTs, but also enhance the compatibility and interface adhesion between polymer matrix and CNTs.28 Hyperbranched polyethylenimine (PEI), as a hyperbranched polymers composed of plenty of amine groups on the linear type macromolecular chains, is suitable for the modification of CNTs/polymer composites.29 In present study, a strategy by grafting PEI on the surface of CNTs and disperse them well in BMI matrix was studied. PEI grafted CNTs (CNTs-PEI) could not only improve the dispersion of CNTs but also improve the interface adhesion between BMI matrix and CNTs by the reaction of BMI and amino groups of PEI. CNTs were functionalized by surface oxidized firstly. PEI as the medium phase was grafted onto the surface of acid treated CNTs to form a functional layer. BMI and ortho-diallyl bisphenol A (BA) were chosen as matrix and toughening agent, respectively. Flexural and impact strength of the composites with different weight content of functionalized CNTs were discussed to study the influence of CNTs on the mechanical properties of composites. The influence of CNTs on the thermal resistance and electric property of material was also studied.
2. Experimental
2.1 Materials
CNTs were supplied by America Cheap Tubes Co., Ltd, which has the length between 2 and 20 μm with the diameter about 5–10 nm and the purity larger than 95%. BMI and BA were produced by Hubei Honghu New Materials Co., Ltd. Polyethyleneimine (PEI) was provided by Sigma-Aldrich Co., Ltd. 1-Ethyl-3-(3-dimethylaminopropyl) carbodiimide hydrochloride (EDC·HCl) and N-hydroxysulfosuccinimide sodium salt (NHS) were provided by Shanghai Covalent Chemical Co., Ltd.
2.2 Preparation of functionalized CNTs
Fig. 1 showed the schematic of manufacturing processes for functionalized CNTs. The raw CNTs were oxidized by mixed acid (H2SO4
:
HNO3 = 3
:
1) at 50 °C for 2 h firstly. The acid treated CNTs (CNTs-COOH) were washed by de-ionized water until the filtrate was neutral. Then, CNTs-COOH were dispersed in de-ionized water by ultrasonication (sonic power 300 W, sonic frequency 40 kHz) with stirring for 30 min to obtain stable suspension with the concentration of 0.01 g mL−1. EDC·HCl and NHS with the same mass as CNTs-COOH were added into the suspension in succession with an interval of 15 minutes to activate the carbonyl groups and hydroxyl groups. Finally, PEI was added into the reaction system for 24 h at room temperature to prepare PEI grafted CNTs (CNTs-PEI). The content of PEI in this reaction system was 1.0 wt%.
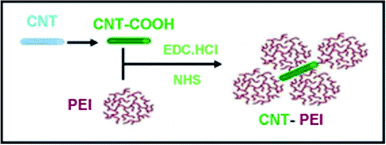 |
| Fig. 1 Schematic of preparation processes for functionalized CNTs. | |
2.3 Preparation of CNTs/BMI composites
Firstly, 1 g CNTs-PEI was added into 150 mL ethanol by ultrasonic dispersion (300 W, 40 kHz) for 30 min. Secondly, sticky and ethanol soluble BA was dropwise added into the suspension under the condition of ultrasonic dispersion. Thirdly, the ethanol in suspension was dried with stirring at 80 °C for 24 h to form CNTs-PEI/BA hybrid. BMI powder monomer was added into CNTs-PEI/BA melt to prepare the prepolymer at 140 °C for 30 min. Then the prepolymer was poured into mould to cure at 150 °C/2 h + 180 °C/2 h + 200 °C/2 h to prepare CNTs-PEI/BMI composite.
2.4 Characterization and testing
Transmission electron microscope (TEM) images (JEM-2100F, JEOL, 200 kV) were used to observe the morphologies of CNTs-PEI. The morphologies of the impact fracture of CNTs/BMI and CNTs-PEI/BMI could be obtained from scanning electron microscope (SEM, FEG Quanta 200F, 20 kV). Netzsch STA449C simultaneous dynamic mechanical analysis (DMA) was used to study the glass transition temperature (Tg) of the composites with heating rate at 3 °C min−1 under air condition. Electrical conductivities were measured using a four probe resistivity meter (RTS-8, China) and a super megohmmeter (SM-820, Japan). Three-point bending testing was used to measure the flexural properties following by the standard ASTM D 790-97 and the impact testing was carried out according to ASTM D 256.
3. Results and discussion
3.1 Surface morphology analysis of CNTs-PEI
As depicted in Fig. 1, the CNTs were modified by hyperbranched and water soluble PEI. In Fig. 2, the surface of CNTs was smooth while there was a thick layer on the surface of CNTs-PEI which meant that a large amount of PEI was grafted on the surface of CNTs-PEI. This functionalized layer was designed as a dispersant that made the CNTs-PEI particles disperse well and be a bridge that connected CNTs with BMI by chemical bonds.
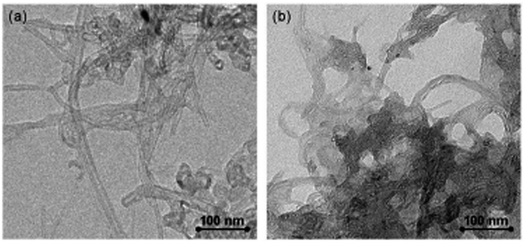 |
| Fig. 2 TEM images of CNTs: (a) CNTs, (b) CNTs-PEI. | |
3.2 Mechanical properties of CNTs-PEI/BMI composites
Impact strength of BMI composites with different content of CNTs and CNTs-PEI was shown in Fig. 3. The maximum increase of impact strength up to 44% compared with that of pure BMI was observed in CNTs-PEI/BMI composites while only 24% was observed in CNTs/BMI composites. The highest impact strength of CNTs-PEI/BMI composites and CNTs/BMI composites was 9.1 kJ m−2 and 7.8 kJ m−2 respectively. Typical impact fracture morphologies of CNTs/BMI and CNTs-PEI/BMI composites were shown in Fig. 4. From Fig. 4(a), it can be seen that the CNTs agglomeration phenomenon was obvious, the agglomeration places would be the defects of the composites and resulted in a great decrease in impact strength even worse than that of the pure BMI because of stress concentration. There was something different when it came to CNTs-PEI/BMI composites, as shown in Fig. 4(b), the CNTs-PEI particles dispersed well in the whole cross section, agglomeration phenomenon of CNTs-PEI was not observed, which proved that CNTs grafted by PEI was an efficient way to improve the dispersion of CNTs in BMI matrix. What's more, a large number of non reactive terminal amino groups of PEI could react with BMI to form a chemical cross-linked structure. The cross-linked structure could increase the interfacial property of CNTs-PEI and BMI dramatically because of the well wettability of CNTs-PEI and the chemical bonds between CNTs and BMI. Flexural properties of the composite obtained from three point bending tests were shown in Fig. 5. From Fig. 5(a), it can be seen that the flexural strength of CNTs-PEI/BMI composites increased with the increase of the content of CNTs-PEI from 0 to 3 wt% and reached the maximum with 3 wt% CNTs-PEI, while decreased with further increase of CNTs-PEI content. This is because that more content of CNTs-PEI resulted in poor dispersibility. In the case of composite materials with CNTs, the maximum flexural strength increased up to 19% with 1.0 wt% CNTs. The more the CNTs added, the more serious the agglomeration was, which resulted in the gradual decrease of the flexural strength of the composites. Flexural modulus occurred a different change tendency shown in Fig. 5(b). The flexural modulus of CNTs-PEI/BMI composite increased by 72%, which was much more than the 39% increment of CNTs/BMI compared with that of pure BMI. As the flexural modulus was decided by the initial rather than the final ratio of stress and strain, the agglomeration of CNTs did not influence the flexural modulus directly but as a reinforcement of BMI matrix. Therefore the flexural modulus of CNTs/BMI and CNTs-PEI/BMI composites almost all increased with the increasing content of CNTs.
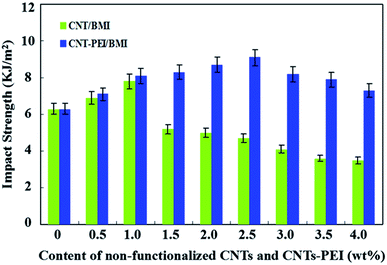 |
| Fig. 3 Impact strength of CNTs/BMI and CNTs-PEI/BMI composites. | |
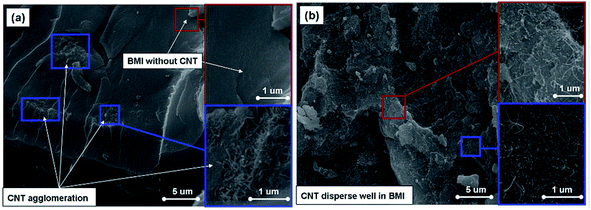 |
| Fig. 4 Typical impact cross section morphologies: (a) SEM of composite with 2.5 wt% non-functionalized CNTs, (b) SEM of composite with 2.5 wt% CNTs-PEI. | |
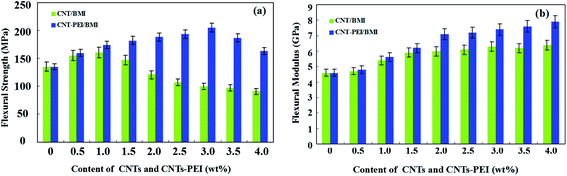 |
| Fig. 5 Flexural properties of composites, (a) flexural strength of BMI composites with content of CNTs and CNTs-PEI from 0 wt% to 4 wt%; (b) flexural modulus of BMI composites with content of CNTs and CNTs-PEI from 0 wt% to 4 wt%. | |
3.3 Thermal properties of CNTs-PEI/BMI composites
The thermal properties of CNTs reinforced BMI composites was analyzed by DMA, as shown in Fig. 6. As shown in Fig. 6(a), the storage modulus increased with the increasing content of CNTs in the composites which matched with the results of the flexural modulus in Fig. 5(b). The peak of Tan Delta can be considered as the Tg of the composites as shown in Fig. 6(b). It could be known that the Tg of CNTs/BMI composites increased with the increase of the content of CNTs and reached the maximum of 224 °C. Similar tendency was observed in CNTs-PEI reinforced composites as shown in Fig. 7. The initial storage modulus of composites was corresponding with the flexural modulus shown in Fig. 5(b). From Fig. 7(b), it can be seen that the Tg of CNTs-PEI/BMI composites were higher than that of CNTs/BMI composites. The maximum Tg of CNTs-PEI/BMI composites reached 240 °C while only 224 °C could be found in the CNTs/BMI composites. Two reasons could account for the results. Firstly, the rigid CNTs-PEI particles could restrict the movement of molecular chain segments of BMI at high temperature because the CNTs-PEI could be dispersed well in BMI. Secondly, the amino groups on PEI layer of CNTs-PEI could react with BMI molecular to form cross-linking structure, which further restricted the movement of molecular chain segments of BMI.
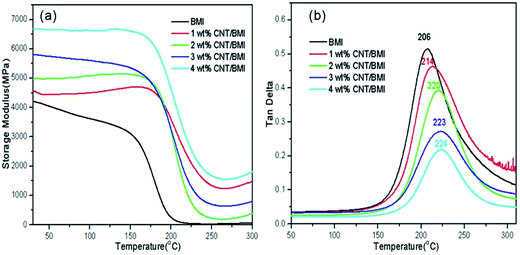 |
| Fig. 6 DMA analysis of CNTs/BMI composites. | |
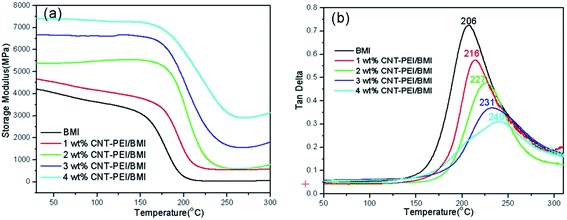 |
| Fig. 7 DMA analysis of CNTs-PEI reinforced BMI composites. | |
3.4 Electrical conductivity of CNTs-PEI/BMI composites
An ultra megohmmeter and a four-probe unit were performed to measure the electrical conductivities of CNTs/BMI and CNTs-PEI/BMI composites. As shown in Fig. 8, the electrical conductivity increased with the increasing addition of CNTs. A sharp increase about 8 magnitude happened when the content of CNTs-PEI increased from 0.5 wt% to 1.0 wt% compared with that of CNTs/BMI composites. This was suggested that the an electrical percolation networks had been established in CNTs-PEI/BMI composites which was beneficial to charge mobility and then improved the electrical conductivity. A percolation threshold was appeared when enough CNTs were added into BMI. However, the percolation threshold appeared later for CNTs/BMI composites because of the lower dispersion of CNTs than that of CNTs-PEI.
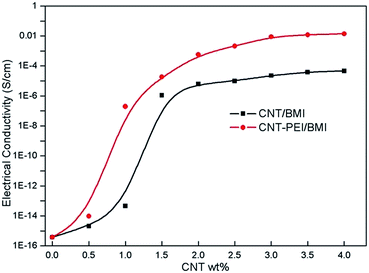 |
| Fig. 8 Electrical conductivity of BMI composites with content of CNTs and CNTs-PEI from 0 wt% to 4 wt%. | |
4. Conclusion
CNTs/BMI composites and CNTs-PEI/BMI composites were prepared in this study, the results showed that functionalization of CNTs with grafting PEI improved the dispersion of CNTs in BMI matrix and formed a cross-linked structure between functionalized CNTs and BMI by PEI as a bridge. CNTs-PEI/BMI composites possessed better mechanical properties, thermal properties and electrical conductivity than CNTs/BMI composites. The results were attributed to the facts that grafting PEI on the surface of CNTs enhanced the dispersion of CNTs in BMI matrix and improved the compatibility and interface adhesion between BMI matrix and CNTs.
Acknowledgements
This work was supported by the Natural Science Foundation of China (51173133) and the Key Basic Research Project of Shanghai (13JC1405300).
References
- J. W. Gu, C. B. Liang, J. Dang, X. D. Meng, L. Tang, Y. Li and Q. Y. Zhang, RSC Adv., 2016, 6, S7357 Search PubMed
. - J. W. Gu, C. B. Liang, J. Dang, W. C. Dong and Q. Y. Zhang, RSC Adv., 2016, 6, 35809 RSC
. - X. Y. Guan, G. Q. Zheng, K. Dai, C. T. Liu, X. R. Yan, C. Y. Shen and Z. H. Guo, ACS Appl. Mater. Interfaces, 2016, 8, 14150–14159 CAS
. - H. J. Chen, T. Liu, J. Ren, H. C. He, Y. H. Cao, N. Wang and Z. H. Guo, J. Mater. Chem. A, 2016, 4, 3238–3244 CAS
. - H. Liu, W. J. Huang, J. C. Gao, K. Dai, G. Q. Zheng, C. T. Liu, C. Y. Shen, X. R. Yan, J. Guo and Z. H. Guo, Appl. Phys. Lett., 2016, 108, 011904 CrossRef
. - Z. J. Yang, L. L. Yuan, Y. Z. Gu, M. Li, Z. J. Sun and Z. G. Zhang, J. Appl. Polym. Sci., 2013, 130, 1447–1488 Search PubMed
. - N. Nosbi and H. M. Akil, Appl. Surf. Sci., 2015, 340, 78–88 CrossRef CAS
. - G. Ziyatdinova, E. Ziganshina and H. Budnikov, Electrochim. Acta, 2014, 145, 209–216 CrossRef CAS
. - J. Huang and D. Rodrigue, Mater. Des., 2014, 55, 653–663 CrossRef CAS
. - W. Yu, L. L. Wang, Y. Qi, L. F. Chen, L. J. Wang and H. Q. Xi, Thermochim. Acta, 2015, 617, 163–168 CrossRef CAS
. - J. Bouchard, A. Cayla, V. Lutz, E. Devaux and C. Campagne, Text. Res. J., 2012, 82, 2106–2115 CrossRef
. - E. Y. Choi, C. R. Sang and C. K. Kim, Carbon, 2014, 72, 160–168 CrossRef CAS
. - M. Sánchez, M. Campo, A. Jiménez-Suárez and A. Ureña, Composites, Part B, 2013, 45, 1613–1619 CrossRef
. - M. Y. Zhang, Z. H. Zhai, M. C. Li, T. L. Cheng, C. Wang, D. W. Jiang, L. Chen, Z. J. Wu and Z. H. Guo, J. Compos. Mater., 2015, 1–10 Search PubMed
. - F. Gardea and D. C. Lagoudas, Composites, Part B, 2014, 56, 611–620 CrossRef CAS
. - E. T. Thostenson, Z. F. Ren and T. W. Chou, Compos. Sci. Technol., 2001, 61, 1899–1912 CrossRef CAS
. - H. Liu, J. C. Gao, W. J. Huang, K. Dai, G. Q. Zheng, C. T. Liu, C. Y. Chen, X. R. Yan, J. Guo and Z. H. Guo, Nanoscale, 2016, 8, 12977–12980 RSC
. - S. Yesil and G. Bayram, J. Appl Polym. Sci., 2013, 127, 982–991 CrossRef CAS
. - J. Bouchard, A. Cayla, E. Devaux and C. Campagne, Compos. Sci. Technol., 2013, 86, 177–184 CrossRef CAS
. - J. N. Coleman, U. Khan, W. J. Blau and Y. K. Gun'Ko, Carbon, 2006, 44, 1624–1652 CrossRef CAS
. - C. R. Sang, E. Y. Choi, Y. S. Choi and C. K. Kim, Polymer, 2014, 55, 1527–1536 CrossRef
. - Y. S. Tang, J. Kong, J. W. Gu and G. Z. Liang, Polym.-Plast. Technol. Eng., 2009, 48, 359–366 CrossRef CAS
. - Y. N. Liu, M. Li, Y. Z. Gu, Y. Y. Zhang, Q. W. Li and Z. G. Zhang, Compos. Sci. Technol., 2015, 117, 176–182 CrossRef CAS
. - E. Y. Choi, Y. K. Ji and C. K. Kim, Polymer, 2015, 60, 18–25 CrossRef CAS
. - E. Y. Choi, Y. K. Ji and C. K. Kim, Carbon, 2015, 95, 91–99 CrossRef CAS
. - J. Cha, S. Jin, J. H. Shim, S. P. Chong, H. J. Ryu and S. H. Hong, Mater. Des., 2016, 95, 1–8 CrossRef CAS
. - X. Zhang, X. R. Yan, Q. L. He, H. G. Wei, J. Long, J. Guo, H. Gu, J. F. Yu, J. J. Liu and D. W. Ding, ACS Appl. Mater. Interfaces, 2015, 7, 6125–6133 CAS
. - J. T. Sun, C. Y. Hong and C. Y. Pan, Polym. Chem., 2011, 2, 998–1007 RSC
. - B. Qiu, J. Guo, X. Zhang, D. Z. Sun, H. B. Gu, Q. Wang, H. W. Wang, X. F. Wang, X. Zhang, B. L. Weeks, Z. H. Guo and S. Y. Wei, ACS Appl. Mater. Interfaces, 2014, 6, 19816 CAS
.
|
This journal is © The Royal Society of Chemistry 2016 |
Click here to see how this site uses Cookies. View our privacy policy here.