DOI:
10.1039/C6RA20599B
(Paper)
RSC Adv., 2016,
6, 114052-114060
Probing the synergism of halloysite nanotubes and electrospinning on crystallinity, polymorphism and piezoelectric performance of poly(vinylidene fluoride)†
Received
15th August 2016
, Accepted 29th November 2016
First published on 29th November 2016
Abstract
Poly(vinylidene fluoride) (PVDF) nanofibers have tremendous potential in nano-sensing and energy scavenging applications. In this study, uniaxially aligned nanofibers were developed from halloysite nanotubes (HNT)/PVDF nanocomposite using electrospinning technique. Incorporation of HNT into PVDF not only reduced the diameter of the electrospun nanofibers, but, also improved their morphology. Fourier transform infrared spectroscopy, wide angle X-ray diffraction and differential scanning calorimetry techniques were used to characterize the crystallinity, polymorphism and polymer–filler interaction in the nanocomposite nanofibers. A force sensor was indigenously designed to study the piezoelectric responses of the nanocomposite nanofibers. At 10 wt% of HNT loading, the sensor produced the highest voltage output, which can be ascribed to its highest β-phase content. Incorporation of HNT and use of electrospinning synergistically enhanced the β-phase content and hence the piezoelectric behavior of PVDF. Hence, these nanofibers could be promising and prominent materials in sensor and actuator applications.
1. Introduction
Poly(vinylidene fluoride) (PVDF) has been recognized as one of the most versatile and promising polymers because of its wide range of applications such as in the chemical, mechanical, biomedical and electronics fields. It is a multiferroic material, which has superior piezoelectric, pyroelectric and ferroelectric properties. For these reasons, PVDF has always attracted researchers in the field of sensors and actuators. PVDF-based nanocomposites have extensively gained a lot of attention for their improved physical properties. It is a semi-crystalline polymer and has a very simple repeating unit of –(CH2–CF2)–. It exists in five distinct phases corresponding to its different chain conformations namely α, β, γ, δ and ε.1 These phases can be qualitatively understood on the basis of trans–gauche conformational transitions. Among the five different forms, α and ε are non-polar while β, γ and δ are polar. α-Phase is known to be the most stable one and has TGTG (trans–gauche–trans–gauche) conformations. β and γ phases are the two most electroactive phases, which have all TTT (trans-planar zigzag) and T3GT3G′ (trans chain conformations), respectively. The other two polymorphs δ and ε made of TGTG′ and T3GT3G′ conformations, respectively are unstable and are rarely seen. In β-phase, all the fluorine and hydrogen atoms are on opposite sides of the backbone, which leads to a non-net zero dipole moment. As a result, piezoelectric and pyroelectric responses are observed.2,3
For obtaining the β and γ phases, there are different approaches such as mechanical stretching,4 drawing,5 annealing at high force,6 high voltage poling7 and addition of nanofillers such as nanoclay,8 graphene,9 barium titanate,10 lead zirconate titanate11 and carbon nanotubes (CNT).12 Addition of CNT into electrospun PVDF nanofibers enhances β-phase by acting as a nucleating agent in the crystallization process. With the increase in CNT concentration, β-phase increases due to the conducive charge accumulation. Electrospun mats experienced piezoelectric vertical displacements due to an applied sine wave voltage.13 Electrospun mats of PVDF were used to measure heartbeat and respiratory signals. Pulsating vibrations from heartbeat were converted into output voltage signals due to piezoelectric response. These output signals were well in agreement with the commercially available electrocardiographs.14 Non woven mats of PVDF fibers have been fabricated for energy harvesting applications. Voltages and current was generated for the corresponding pressure applied. Further, the energy was stored to power electronic devices.15 Lee et al.16 studied the effect of substrate on the piezoelectric properties of electrospun PVDF nanofibers. Due to the spinning and stretching of fibers, β-phase was formed and the fibers were bead free. Piezoelectric performances of fibers spun on different substrates were measured. Thickness of the mat and substrate had large influence on the output voltage. Uniaxially aligned PVDF/BaTiO3 nanocomposite nanofibers were produced by electrospinning. With an increase in filler content, β-phase content increased. The composite nanofibers exhibited 1.7 times greater piezoelectric response than pure PVDF nanofibers.17 A transducer consisting of PVDF nanofibers was developed to detect humidity and ethanol at room temperature. At various concentrations the performance of PVDF sensor was measured. It was found that the sensor can be used up to 100
000 ppm level of ethanol.18 PVDF/graphene/PANI(polyaniline) based nanocomposite nanofibers were fabricated for super capacitor application. Due to electrospinning and the high surface area of graphene and PANI, a high current density and high capacitance were observed in PVDF nanofibers.19
In recent times, incorporation of nanoclay into PVDF has become a center of focus. Nanoclay interacts with the negatively charged fluorine atoms of PVDF, which leads to the formation of β and γ phases.20 Introduction of nanoclay promotes the formation of β-phase and also provides dimensional stability.21 PVDF forms smaller crystallites in β-phase compared to α-phase, thus crystallinity in β-phase decreases. By the addition of montmorillonite clay to PVDF, piezoelectric properties, effective surface area and ionic conductivities of the resultant gel polymer electrolytes have been enhanced.22–24
Electrospinning is a versatile technique that promotes the formation of β-phase by in situ electrical poling and drawing the PVDF nanofibers at a high voltage.25 Earlier works proved that polymorphism of electrospun PVDF fibers depends on processing parameters that lead to higher stretching of the solution jet and straining of the fibrils.26,27 This can be ascribed to the fact that during fiber elongation the polymer is subject to two competing forces: the electrostatic force acts to elongate the fiber, while the viscoelastic force retards it. It was reported that electrospinning magnifies the nucleating activity of clays. Also, by dispersing nanoclay into electrospun PVDF solution, the diameter of resultant nanofibers decreased dramatically as clay contributed more ionic charges in the spinning solution. In short, by changing quantity of dispersed clay the properties of PVDF nanofibers, such as polymorphism, degree of crystallinity and morphology can be altered.26,27
Compared with other nanoparticles such as fumed silica, montmorillonite and CNT, halloysite nanotubes (HNT) are more easily dispersed in polymer matrix by shearing due to their rod-like geometry and limited intertubular contact area.28 Incorporating HNT into PVDF matrix by melt compounding promoted the formation of β and γ phases accompanied by a significant reinforcement and dimensional stability improvement.29 PVDF has flexibility, light weight, spinnability and multiferroicity. Porous PVDF membrane exhibiting piezoelectric behavior is suitable for incorporation into textiles as a power source for wearable electronic devices. Nanofibers made from PVDF and nanoclays have potential to be a smart material, because of higher level of β-phase formation in PVDF and improvement in piezoelectric properties. Hence, in the present study the combined effects of HNT and electrospinning on the crystallinity, polymorphism and piezoelectric performance of PVDF were explored in detail for flexible force sensor application.
2. Materials and methods
2.1. Materials
PVDF powder of weight average molecular weight
w of 534
000 was purchased from Alfa Aesar, Hyderabad, India. Dimethyl sulfoxide (DMSO) of purity in excess of 99.5% was purchased from Central drug house, New Delhi, India. HNT was purchased from Sigma-Aldrich, Bangalore, India (product ID: 685445; diameter: 30–70 nm and length: 1–3 μm).
2.2. Electrospinning of HNT/PVDF nanocomposite nanofibers
18 w/v% solution of PVDF in DMSO was prepared. For the synthesis of nanocomposite nanofibers, HNT was added to the polymer solution at different loadings (0, 2.5, 5, 7.5, 10 and 20 wt% based on the wt of PVDF). HNT was suspended in the solution by ultrasonication for one hour. The mixture was then loaded into a 10 mL syringe with (0.5 mm inner diameter) bevel edge needle. The pure PVDF solution and that containing HNT were electrospun under the following optimized conditions: solution flow rate: 0.5 mL h−1; relative humidity: 55%; temperature: 32 °C; voltage: 20 kV; tip to collector distance: 20 cm [several experiments were done for optimizing the electrospinning parameters to get bead-free and uniform nanofibers with smaller average fiber diameter (see the ESI†)]. For producing aligned fibers, an aluminum foil-wrapped rotating drum collector (2000 rpm) was used. A vertical electrospinning setup (e-spin Nano, Physics Equipment Co., Chennai, India) was used. When the solution started dripping through the needle, it was charged due to the positive voltage applied in the needle. Taylor cone formed when the critical potential was exceeded, resulting in the formation of fibers. When sufficient quantity of fibers got collected, the nanofiber mat was peeled off from the aluminum foil. PVDF film was also prepared by solution casting for a comparison of their physical characteristics with that of the electrospun nanocomposite nanofibers (NCNF).
2.3. Characterization
The morphology of the nanofibers was studied using a scanning electron microscope (SEM) (JEOL JSM-6380LA, Japan) at an accelerating voltage of 20 kV. A thin layer of gold was sputtered onto the surface of nanofibers prior to the investigation. Image-J tool was used for the analysis of images and measurement of fiber diameters. The diameter of an individual fiber was calculated by taking an average of three values measured. To measure the average fiber diameter, at least, 50 fiber diameters were obtained and then the standard deviation along with average fiber diameter has been reported.
Fourier transform infrared (FTIR) spectra (Jasco FTIR-4200, Japan) were acquired by KBr pellet method at an average of 32 scans in the wavenumber range of 4000–400 cm−1 at a spectral resolution of 0.5 cm−1. The β-phase content of HNT/PVDF NCNF webs was determined by comparing the vibration bands of samples corresponding to their phases. The β-phase content (Xβ) was obtained from FTIR spectra using the equation proposed by Peppas30
|
 | (1) |
where,
a and
b are the heights of two neighboring bands arising from β and amorphous phases, respectively. Additionally, the ratio of area under two neighboring bands arising from β and amorphous phases was also used in the quantification of
Xβ.
27
Wide angle X-ray diffraction (WAXD) (JEOL DX-GE-2P X-ray diffractometer, Japan) measurements were carried out to determine the PVDF phases of NCNF webs. Samples were scanned at a speed of 0.5° min−1 in the 2θ range of 10–35°. % crystallinity (Xc) of the NCNF webs was calculated by the deconvolution method and the following equation was used in the calculation:
|
 | (2) |
where,
Ia corresponds to amorphous phase and
Ic corresponds to crystalline phases.
The interplanar distances (d) were obtained by the following equation:
|
 | (3) |
To understand the thermal decomposition behaviors of the NCNF webs, thermogravimetric analysis (TGA) was carried out. Analyses were carried out at a heating rate of 10 °C min−1 under nitrogen atmosphere at a flow rate of 25 mL min−1. Around 5 mg of sample was used to perform the TG analysis (TGA Q5000 V3.10 Build 258; TA instruments, New Castle, Delaware, USA).
Differential scanning calorimetric (DSC) analysis was carried out to study the crystallinity, melting point, heat of fusion and phase study of NCNF webs. About 5 mg of the samples were kept in hermetically sealed aluminum pans. DSC scans (822e – Mettler Toledo, USA) were done from 0 °C to 200 °C at a heating rate of 10 °C min−1. Nitrogen gas was purged through the furnace at a flow rate of 50 mL min−1. The degree of crystallinity was calculated from the peak area using eqn (4).
|
 | (4) |
where,
Xc = % crystallinity, Δ
Hm is the apparent enthalpy of fusion, J g
−1,

= enthalpy of fusion per gram for 100% crystallinity, 104.5 J g
−1.
A transmission electron microscope (TEM) (JEOL JEM-2010, Japan) was used to image HNTs and a single nanofiber. Fibers were directly electrospun on a carbon coated 200 mesh copper grid for about 30 s and dried in a vacuum oven at 40 °C for 24 hours. The main aim of doing the TEM analysis was to observe the orientation of HNTs in NCNF webs and to determine the polymorphs of PVDF.
2.4. Measurement of the piezoelectric response of the nanocomposite nanofibers
Fig. 1 shows the schematic illustration of the indigenous setup used to explore the potential of the NCNF webs for force sensor application. Two copper electrodes were supported by non-conducting columns. Rubber dampers were provided over the periphery of the copper electrode so as to avoid contact with another copper electrode and help in rebounding the copper electrode when the load is removed from the sample. Copper electrodes were connected to a multi-function digital multimeter (MECO Meters Pvt. Ltd., Mumbai, India) for accurately measuring the piezoelectric voltage output of the NCNF webs. The nanofibrous mats were placed between the copper electrodes. Uniform thickness of NCNF webs was maintained for all the samples. Progressively increasing loads were applied on the top electrode and the voltage output was noted down.
 |
| Fig. 1 Schematic of the setup used in piezoelectric evaluation. | |
3. Results and discussion
3.1. SEM results
Fig. 2a–f shows the SEM micrographs of HNT/PVDF NCNF webs with different HNT loading. In the pristine PVDF webs, the fibers were smooth and randomly distributed. The outer surface of HNT is chemically similar to SiO2 while its inner cylinder core is related to Al2O3. The charge (zeta potential) behavior of HNT can be roughly described by superposition of mostly negative surface potential of SiO2, with a small contribution from the positive Al2O3 inner surface. These charged surfaces enhance the electrostatic conductivity of the solution. Thus incorporation of HNT into PVDF increases charge density on the surface of the solution jet during electrospinning. The accumulated charges overcome cohesive forces resulting in long, homogenous and defect-free nanofibers.28,29,31 Also, these nanofibers were expectantly stretched by the rotation of the high speed drum collector. Interestingly, many of these nanofibers were not uniformly aligned. It has been reported earlier that DMSO might cause jet instability as its high dielectric constant leads to misalignment of fibers.32,33 The average fiber diameter (AFD) as well as the standard deviation of fiber diameter (SD) decreased with an increase in HNT loading in the fibers (Table 1). AFD for pure PVDF fibers was 302 nm with a SD of 85 nm. Smallest AFD measured was 202 nm, which was obtained at a HNT loading of 10 wt%. This indicates that HNT could be used as a processing aid for PVDF that can lead to finer electrospun fibers.
 |
| Fig. 2 SEM images (magnification 5000× and scale bar = 5 μm) of electrospun NCNF webs with HNT loading of (a) 0% (neat PVDF) (b) 2.5% (c) 5% (d) 7.5% (e) 10% and (f) 20%. | |
Table 1 AFD and SD of electrospun NCNF webs
% HNT |
AFD |
SD |
0 (pure PVDF) |
302 |
85 |
2.5 |
278 |
78 |
5 |
280 |
69 |
7.5 |
252 |
61 |
10 |
202 |
58 |
20 |
210 |
54 |
3.2. Crystallinity and polymorphism of HNT/PVDF NCNF webs
3.2.1. FTIR spectroscopy. The combined effects of HNT and electrospinning on the polymorphism of PVDF were probed using FTIR spectroscopy. FTIR spectra of unstretched PVDF film, electrospun pure PVDF and NCNF webs are shown in Fig. 3. From literature2,5,8,22,23,27,34,35 the spectral peaks were identified and their respective phases and vibrational modes are shown in Table 2. In the spectrum of the unstretched film, all the bands are related to TGTG′ conformations. Bands at 630, 707, 816, 859, 950, 1017, 1143, 1357 and 1653 cm−1 correspond to α-phase. For electrospun pure PVDF nanofibers, there is a remarkable decrease in the intensities of peaks corresponding to the α-phase. Moreover, a number of new bands were observed at 467, 680, 840, 1021, 1194, 1286 and 1402 cm−1. These bands can be attributed to the β-phase, which has TTT conformation.
 |
| Fig. 3 FTIR spectra of unstretched PVDF film, electrospun PVDF and HNT/PVDF NCNF webs (the vibrational bands used for calculating Xβ are highlighted). | |
Wave number (cm−1) |
Phase |
Vibration modes |
435 |
β |
CF2 bending |
464 |
β |
CF2 bending + CH2 wagging |
491 |
β |
CF2 wagging |
513 |
β |
CF2 bending |
606 |
α |
CF2 bending |
678 |
α |
Polymer chain defect due to head to head and tail to tail linkage |
840 |
β |
CH2 bending + CF2 out of plane deformation |
859 |
α |
CH2 out of plane deformation |
954 |
α |
CH2 out of plane deformation |
1020 |
α |
CH2 out of plane deformation |
1031 |
β |
CF2 bending |
1080 |
β |
CH2 wagging |
1191 |
α |
CF2 stretching |
1286 |
β |
CF2 stretching |
1400 |
β |
CH2 wagging |
As mentioned in Section 2.3, Peppas equation was used for the calculation Xβ; the values for ‘a’ and ‘b’ were respectively the heights of the bands at 840 cm−1 (corresponding to CH2 bending + CF2 out of plane deformation of the β-phase) and 870 cm−1 (corresponding to C–C–C asymmetric stretching in the amorphous phase).36
The area under the peak at 840 cm−1 (A840) is indicative of the β-phase content in the case of electrospun fibers.27 The area under the peak at 870 cm−1 (A870) is indicative of the amount of the amorphous phase in PVDF.33 The A840/A870 ratio was also used for the quantification of Xβ.27
β-Phase content of PVDF increased remarkably by the synergistic effects of HNT and electrospinning. β-Phase content increased continuously up to a HNT loading of 10 wt% after which there was a decrease in it. This may be attributed to the excess of HNT loading which leads to reduced polymer–filler interaction. The highest β-phase content was 81% at 10 wt% of HNT loading (Table 3).
Table 3 WAXD and FTIR results of NCNF webs
HNT loading (wt%) |
2θ (°) |
d-Spacing (nm) |
Xc (%) |
Xβ (%) |
Peppas method |
Peak area ratio method |
This sample was prepared to check if the β-phase content and piezoelectric response improve beyond 10 wt% HNT loading. Hence, only FTIR spectroscopy was performed on this sample. |
0 |
20.36 |
0.43 |
38.8 |
34.6 |
30.4 |
2.5 |
20.53 |
0.43 |
37.5 |
52.0 |
47.6 |
5 |
20.54 |
0.43 |
35.4 |
59.4 |
54.2 |
7.5 |
20.56 |
0.42 |
34.2 |
62.4 |
57.1 |
10 |
20.83 |
0.42 |
31.0 |
81.1 |
79.4 |
15 |
a |
a |
a |
44.0 |
36.5 |
20 |
20.57 |
0.43 |
35.1 |
28.4 |
26.6 |
C–H bonds in PVDF repeating units are partially positively charged. This could result in ion–dipole interaction with the negatively charged HNT surface, which may lead to an enhancement of β-phase content as in nanoclay/PVDF composites.36,37 For the present system, a plausible polymer–filler interaction mechanism has been proposed in Section 3.5. In literature, it has been reported that after addition of nano clay into PVDF, γ-phase was observed.20,27,28,37 But, there is no significant amount of γ-phase present in the NCNF webs prepared in this study.
3.2.2. WAXD results. In the WAXD patterns of unstretched PVDF film, electrospun PVDF nanofibers and the NCNF webs (Fig. 4) characteristic peaks for different phases were present. Peaks at 17.7°, 18.4°, 19.9° and 26.6° are characteristic of the α-phase. Peaks at 17.7°, 18.4°, 19.9° and 26.6° correspond to (100), (020), (110) and (021) planes of PVDF, respectively. For electrospun fibers, these peaks almost diminished and a new peak was observed at 20.36° that corresponds to the (110)/(200) crystal plane of β-phase with an interplanar spacing of 0.43 nm. Broader peaks were seen for nanofibers, which may be due to a decrease in the crystallinity of PVDF. β-Phase content increased proportionately with HNT loading up to 10 wt% beyond which there was a decrease in it. At 20 wt% HNT loading, β-phase content decreased and the peak around 20° began to shift towards left and a new peak at 24.56° appeared; this may be attributed to the reformation of α-crystals due to an overdose of HNT into PVDF (Table 3).
 |
| Fig. 4 WAXD patterns of unstretched PVDF film, electrospun PVDF and NCNF webs. | |
3.2.3. DSC analysis. The DSC traces of NCNF webs are shown in Fig. 5. In DSC curves of pristine electrospun PVDF two peaks were observed. The first peak at 112.6 °C corresponds to the magnetic transition of PVDF from ferroelectric to paraelectric, which is the curie transition (Tc).35 The second one at 142.1 °C corresponds to the crystalline melting point (Tm) of PVDF.
 |
| Fig. 5 DSC traces of electrospun PVDF and NCNF webs. | |
For the NCNF webs, Tc increased in comparison with pure electrospun PVDF fibers. Moreover, the Tc peak overlapped Tm peak. For pure PVDF nanofibers, the Tm is 142.5 °C, but, there is a shift in the Tm for the HNT loaded PVDF nanofibers to a higher temperature. This is attributable to the rearrangement of PVDF crystals and the resultant increase in β-phase content. The shifting and overlapping of Tc and Tm peaks is associated with a significant change in crystallinity of PVDF. Due to the synergistic effect of electrospinning and nucleation by HNT, the PVDF chains in the NCNF webs get polarized, which induces the formation of the β-phase. The degree of crystallinity of PVDF (Xc) tends to decrease with an increase in the dosage of HNT (Table 4), which is in line with the XRD results. Clays in general play a dual role in influencing the crystallization process of PVDF, which depends on both their quantity and state of dispersion. Clay not only acts as a nucleating agent, but, also is a physical obstacle to the motion of polymer chains.8 In the present study, HNT acted as a nucleating agent up to 10 wt% HNT loading beyond which there was a decrease in the β-phase content and an increase in the Xc of PVDF. Difference in Xc obtained from DSC and XRD results is due to ineluctable error which may happen during the calculation process. In DSC, the error may be due to the baseline correction carried out during evaluation of heat of fusion; in XRD analysis, it may be linked with the separation of amorphous and crystalline region from the diffraction.38
Table 4 DSC results of NCNF webs
HNT loading (wt%) |
ΔHm (J g−1) |
Tm (°C) |
Xc (%) |
0 |
41.3 |
142.0 |
39.6 |
2.5 |
39.2 |
145.6 |
38.5 |
5 |
37.3 |
146.0 |
37.5 |
7.5 |
36.1 |
146.1 |
37.3 |
10 |
34.4 |
146.2 |
36.6 |
20 |
33.1 |
145.2 |
39.5 |
3.3. TGA results
TGA curves and the corresponding differential thermal curves (DTG) of the nanofiber webs are shown in Fig. 6 and 7, respectively. PVDF was stable up to 400 °C and above this temperature it underwent weight loss continuously up to 775 °C. However, a major loss in weight was observed at 467 °C. This weight loss may be attributed to the chain stripping of monomers. PVDF degrades rapidly, which results in the formation of hydrogen fluoride along with the monomers.
 |
| Fig. 6 TGA curves electrospun pure PVDF and NCNF webs. | |
 |
| Fig. 7 DTG curves for electrospun pure PVDF and NCNF webs. | |
In the NCNF webs, thermal degradation took place in two steps. Weight loss for nanocomposite nanofibers starts at a very low temperature i.e., 130 °C due probably to dehydration of HNT. Addition of HNT resulted in a decrease in the onset of decomposition temperature of PVDF (inset in Fig. 6). When the HNT loaded PVDF is exposed to heat, it generates free radicals from HNT that could accelerate the chain scissoring of the PVDF chain and further separating CH and CF bonds.39 Char formation was observed for the NCNF webs and the amount of char residue increased with HNT loading.
3.4. TEM analysis
Fig. 8a shows the TEM micrograph of pristine HNT in which its inner and outer walls are clearly visible. Inside a single NCNF, some HNTs are seen that are oriented along the fiber axis; their orientation happens during the formation of nanofibers in electrospinning due to process induced alignment (Fig. 8b). The HNT are finely dispersed in the PVDF matrix due to an excellent polymer–filler interaction as discussed in Section 3.5. Selected area electron diffraction (SAED) pattern allows determination of crystal plane orientation in the nanofibers (Fig. 8c). The dot patterns were indexed and the interplanar distance for (110)/(200) crystal planes was found to be 0.43 nm, corresponding to the β-phase of PVDF. Interplanar distances of 0.44 nm and 0.3 nm for (020) and (002) planes respectively relate to HNT crystal;40 (110) crystal plane with an interplanar distance of 0.37 nm corresponds to α-phase crystallites of PVDF. These results are in good agreement with WAXD results.
 |
| Fig. 8 TEM images of (a) pristine HNT and (b) 10% HNT/PVDF NCNF webs; and (c) SAED patterns of 10% HNT/PVDF NCNF webs. | |
3.5. Polymer–filler interaction mechanism in NCNF webs
The surface of HNT is made of Si–O–Si groups and the inner walls are made of Al–OH groups. Thus, a strong interaction between the hydrogen atoms of PVDF chains and negatively charged surface of HNT can be expected. Fig. 9 shows the FTIR spectra of pure PVDF, pristine HNT and 10 wt% HNT-loaded NCNF webs. In pristine HNT spectrum, peaks at 3697 cm−1 and 3515 cm−1 correspond to the stretching vibration of Al–OH groups in the inner surface. 1028 cm−1 and 909 cm−1 peaks correspond to Si–O stretching and Al–OH bending vibrations, respectively.38 In the spectrum of NCNF, peak at 1028 cm−1 shifted to a lower wave number i.e., 1027 cm−1. Similarly, the peak at 3697 cm−1 shifted to 3693 cm−1, which may be attributed to intermolecular hydrogen bonding between the F-atoms of PVDF and OH groups of HNT. Also, a peak at 909 cm−1 that represents OH groups in HNT seems to have moved towards the lower wave number and merged with the neighboring PVDF peak. This may also be due to hydrogen bonding between F-atoms of PVDF and OH groups of HNT, which led to the formation of long TTT conformation.8 In pure PVDF, a peak at 487 cm−1 corresponds to CH2 wagging vibration and in pristine HNT, a peak at 466 cm−1 corresponds to Si–O bending vibration. In the spectrum of the NCNF web, the Si–O peak overlapped with that of the CH2 groups of PVDF. Along with this overlapping, the Si–O peak shifted to a lower wave number (i.e., 464 cm−1). This may be attributed to the interaction between CH2 bonds of PVDF with negatively charged surface of HNT that induce formation of long TTT conformations.
 |
| Fig. 9 FTIR spectra of pure PVDF, pristine HNT and 10% HNT/PVDF NCNF webs. | |
Fig. 10 shows the schematic of a plausible filler–polymer interaction mechanism in the NCNF webs. The interactions between hydrogen, fluorine and negatively charged ions tends to align the PVDF chains in the planar zigzag chain, which induces the formation of β-phase.37
 |
| Fig. 10 Plausible interaction mechanism between HNT and PVDF in the NCNF webs. | |
3.6. Piezoelectric performance of HNT/PVDF NCNF webs
The piezoelectric voltage outputs of the NCNF webs for different loads are shown in Fig. 11. PVDF generates voltage only when the fibers are compressed and then relaxed from all the loads. Performance of the NCNF webs is directly proportional to the β-phase content. NCNF webs with 10% HNT loading exhibited the highest voltage output of 955 mV under a load of 100 g. For NCNF webs with 15 and 20% HNT loading, the voltage outputs were very low due to their low β-phase content.
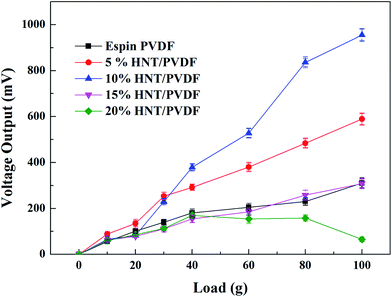 |
| Fig. 11 Piezoelectric responses of electrospun pure PVDF and NCNF webs at different loads. | |
Flexible, self-powered materials are highly sought after for various applications, such as energy harvesting, robotic devices, and lab-on-a chip medical diagnostics. Self-powered materials are based on piezoelectric nano generators, which are powered by their enormous kinetic energy or renewable energy. These materials rely on the presence of piezoelectric potential generated by the material. However, simple flexibility alone does not guarantee their conformal bonding to nonplanar substrates. Therefore, it is mandatory to focus on electrospun nanofibers for use in highly stretchable devices. Due to their high piezoelectric voltage outputs, the HNT/PVDF nanofiber webs developed in the present study could possibly be used in flexible nanogenerator and nano-pressure sensors.
4. Conclusions
Finer PVDF nanofibers can be produced by electrospinning of PVDF solution containing HNT. Crystallinity of PVDF decreases upon the addition of HNT, while the β-phase content increases simultaneously. The highest β-phase content was observed in the NCNF webs containing 10 wt% of HNT. HNTs are oriented along the axis of the fiber and there is a strong interaction between HNTs and PVDF. The onset temperature of thermal degradation of the NCNF webs decreases compared with that of pure PVDF nanofibers due to the catalytic action of HNT in chain scissoring. The piezoelectric response of PVDF is also enhanced appreciably due to the synergism of HNT and electrospinning. This study proves that the interplay between the effects brought about by HNT and electrospinning could be used to engineer the crystallinity, polymorphism and piezoelectric behavior of PVDF for advanced applications, such as flexible nanosensors and nanogenerators.
Acknowledgements
M. K. thanks the department of Metallurgical and Materials Engineering (MME), National Institute of Technology Karnataka (NITK) for a research fellowship. The authors thank Dr Udaya Bhat, department of MME, NITK for providing the TEM facility. The authors are grateful to Ms Rashmi and Mr Vinayak for their assistance in SEM and TEM imaging, respectively.
References
- A. Salimi and A. A. Yousefi, Polym. Test., 2003, 22, 699–704 CrossRef CAS.
- G. M. Bartenev, A. A. Remizova, I. V. Kuleshov, M. A. Martynov and T. N. Sarminskaya, Polym. Sci. U.S.S.R., 1975, 17, 2381–2388 CrossRef.
- A. J. Lovinger, J. Polym. Sci., Polym. Phys. Ed., 1980, 18, 793–809 CrossRef CAS.
- V. Sencadas, M. V. Moreira, S. Lanceros-Méndez, A. S. Pouzada and R. Gregório Filho, in Materials science forum, Trans Tech Publ, 2006, vol. 514, pp. 872–876 Search PubMed.
- W. A. Yee, M. Kotaki, Y. Liu and X. Lu, Polymer, 2007, 48, 512–521 CrossRef CAS.
- Y.-C. Hu, W.-L. Hsu, Y.-T. Wang, C.-T. Ho and P.-Z. Chang, Sensors, 2014, 14, 6877–6890 CrossRef PubMed.
- T. Kaura, R. Nath and M. M. Perlman, J. Phys. D: Appl. Phys., 1991, 24, 1848 CrossRef CAS.
- L. Yu and P. Cebe, Polymer, 2009, 50, 2133–2141 CrossRef CAS.
- L. Huang, C. Lu, F. Wang and L. Wang, RSC Adv., 2014, 4, 45220–45229 RSC.
- Y. N. Hao, X. H. Wang, S. O'Brien, J. Lombardi and L. T. Li, J. Mater. Chem. C, 2015, 3, 9740–9747 RSC.
- J. Chang, Y. Shen, X. Chu, X. Zhang, Y. Song, Y. Lin, C.-W. Nan and L. Li, RSC Adv., 2015, 5, 51302–51307 RSC.
- H. Liu, C. T. Pan, L. W. Lin and H. W. Lai, Sens. Actuators, A, 2013, 193, 13–24 CrossRef.
- Y. Ahn, J. Y. Lim, S. M. Hong, J. Lee, J. Ha, H. J. Choi and Y. Seo, J. Phys. Chem. C, 2013, 117, 11791–11799 CAS.
- Y.-Y. Chiu, W.-Y. Lin, H.-Y. Wang, S.-B. Huang and M.-H. Wu, Sens. Actuators, A, 2013, 189, 328–334 CrossRef CAS.
- A. Gheibi, R. Bagherzadeh, A. A. Merati and M. Latifi, J. Polym. Res., 2014, 21, 571 CrossRef.
- B.-S. Lee, B. Park, H.-S. Yang, J. W. Han, C. Choong, J. Bae, K. Lee, W.-R. Yu, U. Jeong, U.-I. Chung, J.-J. Park and O. Kim, ACS Appl. Mater. Interfaces, 2014, 6, 3520–3527 CAS.
- C. Lee, D. Wood, D. Edmondson, D. Yao, A. E. Erickson, C. T. Tsao, R. A. Revia, H. Kim and M. Zhang, Ceram. Int., 2016, 42, 2734–2740 CrossRef CAS.
- E. Zampetti, A. Bearzotti and A. Macagnano, Procedia Eng., 2014, 87, 1509–1512 CrossRef CAS.
- A. Rose, N. Raghavan, S. Thangavel, B. Uma Maheswari, D. P. Nair and G. Venugopal, Mater. Sci. Semicond. Process., 2015, 31, 281–286 CrossRef CAS.
- A. C. Lopes, C. M. Costa, C. J. Tavares, I. C. Neves and S. Lanceros-Mendez, J. Phys. Chem. C, 2011, 115, 18076–18082 CAS.
- L. Priya and J. P. Jog, J. Polym. Sci., Part B: Polym. Phys., 2002, 40, 1682–1689 CrossRef CAS.
- J. Yang, J. Wang, Q. Zhang, F. Chen, H. Deng, K. Wang and Q. Fu, Polymer, 2011, 52, 4970–4978 CrossRef CAS.
- M. Deka and A. Kumar, J. Power Sources, 2011, 196, 1358–1364 CrossRef CAS.
- M. Rezaei, A. F. Ismail, S. A. Hashemifard and T. Matsuura, Chem. Eng. Res. Des., 2014, 92, 2449–2460 CrossRef CAS.
- T. Senthil and S. Anandhan, Int. J. Plast. Technol., 2013, 17, 123–138 CrossRef CAS.
- E. S. Cozza, O. Monticelli, E. Marsano and P. Cebe, Polym. Int., 2013, 62, 41–48 CrossRef CAS.
- R. Neppalli, S. Wanjale, M. Birajdar and V. Causin, Eur. Polym. J., 2013, 49, 90–99 CrossRef CAS.
- K. Prashantha, M. F. Lacrampe and P. Krawczak, eXPRESS Polym. Lett., 2011, 5, 295–307 CrossRef CAS.
- B. Wang and H.-X. Huang, Composites, Part A, 2014, 66, 16–24 CrossRef CAS.
- S. K. Mallapragada and N. A. Peppas, et al., J. Polym. Sci., Part B: Polym. Phys., 1996, 34, 1339–1346 CrossRef CAS.
- A. H. Touny, J. G. Lawrence, A. D. Jones and S. B. Bhaduri, J. Mater. Res., 2010, 25, 857–865 CrossRef CAS.
- C. Guo, L. Zhou and J. Lv, Polym. Polym. Compos., 2013, 21, 449–456 CAS.
- S. Janakiraman, A. Surendran, S. Ghosh, S. Anandhan and A. Venimadhav, Solid State Ionics, 2016, 292, 130–135 CrossRef CAS.
- Y. Bormashenko, R. Pogreb, O. Stanevsky and E. Bormashenko, Polym. Test., 2004, 23, 791–796 CrossRef CAS.
- P. Martins, A. C. Lopes and S. Lanceros-Mendez, Prog. Polym. Sci., 2014, 39, 683–706 CrossRef CAS.
- H. Bai, X. Wang, Y. Zhou and L. Zhang, Prog. Nat. Sci.: Mater. Int., 2012, 22, 250–257 CrossRef.
- S. Ramasundaram, S. Yoon, K. J. Kim and C. Park, J. Polym. Sci., Part B: Polym. Phys., 2008, 46, 2173–2187 CrossRef CAS.
- G. George, M. Selvakumar, A. Mahendran and S. Anandhan, J. Thermoplast. Compos. Mater., 2015 DOI:10.1177/0892705715588802.
- L. H. Gaabour and L. H. Gaabour, J. Mater., 2015, e824859 Search PubMed.
- Y. Dong, J. Marshall, H. J. Haroosh, S. Mohammadzadehmoghadam, D. Liu, X. Qi and K.-T. Lau, Composites, Part A, 2015, 76, 28–36 CrossRef CAS.
Footnote |
† Electronic supplementary information (ESI) available. See DOI: 10.1039/c6ra20599b |
|
This journal is © The Royal Society of Chemistry 2016 |
Click here to see how this site uses Cookies. View our privacy policy here.