DOI:
10.1039/C6RA19166E
(Paper)
RSC Adv., 2016,
6, 92186-92196
Nitrogen functionalized hierarchical microporous/mesoporous carbon with a high surface area and controllable nitrogen content for enhanced lead(II) adsorption
Received
28th July 2016
, Accepted 19th September 2016
First published on 21st September 2016
Abstract
Nitrogen-doped hierarchical microporous/mesoporous carbons (NHMCs) were conveniently fabricated for enhanced lead adsorption through a sol–gel method and NaOH-assisted activation with a soluble melamine–phenol–formaldehyde resin as a precursor. Characterization techniques, including Brunauer–Emmett–Teller, TEM, FTIR spectroscopy, and XPS analysis, were used to study the surface physicochemical properties of carbons. The prepared carbons feature high surface areas of up to 1463 m2 g−1, controllable nitrogen content of 0–4.27%, and an interconnected 3D microporous/mesoporous network with peak micropore width around 0.7–0.9 nm, and 3–8 nm pore channel. The nitrogen atoms were mostly bound to the carbon in forms of pyrrolic, pyridine, and amine-like nitrogen groups, providing adsorption sites for Pb(II) easily binding to the surface through strong chemisorptive bonds or ion-exchange. Compared with CMK3, NHMCs exerted excellent adsorptive removal performance toward Pb(II) in adsorption capacity (up to 212 mg g−1), equilibrium time (30 min), and adsorption conditions (pH 4.5–6). The adsorption data at various initial concentrations fit well with the Langmuir and pseudo-second order model. Even after five consecutive adsorption–desorption cycles, no obvious decrease in Pb(II) adsorption was detected, thereby implying that the nitrogen-doped 3D hierarchical NHMCs was suitable for efficient Pb(II) removal.
1. Introduction
Lead is the most widely used important heavy metal, and it is used in large amounts in many industrial branches involving electroplating, alloy manufacturing, pigments, batteries, and textile operations.1 However, it is a well-known toxin, and it can find its way to the aquatic environment through wastewater discharge. Chronic exposure to Pb(II) ions even at low levels can cause various diseases and disorders, such as anemia, malaise, liver and kidney diseases, apathy, infertility, abnormalities in pregnant women, brain damage, and anorexia because it is not biodegradable, and it tends to accumulate in living organisms directly or indirectly.2 The limit values of lead set by EU, USEPA, and WHO in drinking water and surface water intended for drinking are 0.010, 0.015, and 0.010 mg L−1, respectively.3 However, the high solubility of Pb(II) ions in wastewater complicates the remediation and purification of drinking water. Many approaches, such as chemical precipitation, membrane filtration, adsorption, electrochemical treatment technologies, biochemical methods, and biological ion exchange, have been suggested to remove Pb(II) ions from wastewater.4–6
In particular, adsorption by porous materials is considered an effective and widely used process to reduce the amount of Pb(II) ions in drinking water to levels acceptable for consumption. Thus, various adsorbents, including zeolites, clay minerals, trivalent and tetravalent metal phosphates, biosorbents, and activated carbon, have been investigated for the adsorption method.7–11 Among these adsorbents, activated carbons are widely used because of their high surface area, large pore volume, chemical inertness, good mechanical and thermal stability, ease in handling, and low-cost preparation.12,13 However, they have shown limited efficiency as an adsorbent for heavy metal uptake because of their irregular and micron-size of morphology.14 Hierarchical microporous/mesoporous carbons (HMCs) with two or more levels of porosity have been viewed as an ideal candidate, and they have attracted considerable attention because of their important role in the systematic study of structure–property relationships and their technological promise in adsorption and separation.15–17 These materials can effectively enhance the diffusion of guest molecules through the inorganic network of pores and channels, given that the large pores allow an effective molecular accessibility, whereas the small pores provide high surface areas and large pore volumes.17–20
In addition to pore structure, the surface functionalization of carbon materials is another crucial factor for the adsorption performance.21,22 In general, carbon materials are of relatively inert nature. They also lack functional groups and have poor surface wettability for aqueous solution because of high temperature carbonization, which impedes the penetration of heavy metal ions into the pores of carbons and limits their practical applications. The introduction of surface functionalization has proved to be a promising approach to improve the surface wettability and adsorption capacity of heavy metal ions.23,24 The property of carbon materials is mostly related to the nature of heteroatoms (e.g., O, N, S, P, and Cl), which can be substituted for carbon in the graphite layer and/or attached at the layer edges as functional groups.23 The enrichment of porous carbons in nitrogen mainly aims to induce special effect to the surface among various heteroatoms.25,26 The incorporated nitrogen species may be present in the form of various N-containing groups, which not only can significantly change the polarity and/or acidic–basic property of carbon materials but also can supply many active sites for the adsorption of transition metal cations involving lead ions, although the nature of the N groups with high activity is not established.24,27 Therefore, preparing new nitrogen-enriched adsorbing materials with hierarchical pore structure for pollution removal by combining the benefits of nitrogen-enriched carbons and hierarchical pore structures has been attracting great attention.
However, we believe that little attention has been paid to nitrogen-enriched carbons with 3D hierarchical microporous/mesoporous structure for enhanced lead adsorption. Therefore, our research group prepared a hierarchical microporous/mesoporous carbon (HMC) based on a simple sol–gel method, which had high surface area and pore volume.28 In this study, we speculated that the following points may be in favor of making a nitrogen-enriched 3D hierarchical microporous/mesoporous carbon (NHMC) as an ideal candidate for lead treatment: (i) the prepared carbon possesses high surface area and well-developed pore structure, which can provide numerous adsorption sites; (ii) considerably effective nitrogen-containing functional groups exist on the surface and interpore of HMC; and (iii) the interesting 3D hierarchical pore structure of carbon is well preserved even after introducing nitrogen.
Thus, this study aimed to develop a nitrogen-enriched 3D hierarchical microporous/mesoporous carbon with high surface area from melamine and phenol–formaldehyde resin through a simple sol–gel method with NaOH as the activator for lead removal. The data were compared with HMC without the introduction of nitrogen-containing functional groups. Factors that influence the adsorption process including initial concentration, solution pH, contact time, and temperature were investigated carefully in a series of experiment. The adsorption thermodynamics of lead were systematically investigated in detail, and the underlying mechanism for lead removal through adsorbents was elucidated.
2. Materials and methods
2.1 Preparation of nitrogen-doped HMC
NHMC was prepared through a sol–gel method and NaOH-assisted activation with a soluble melamine–phenol–formaldehyde resin as the precursor and Pluronic F108 as template. First, 4 g of phenol was melted at 40 °C in a flask and mixed with 1.1 g of 20 wt% NaOH aqueous solution under stirring for 10 min. Subsequently, 12 g of formalin (37 wt% formaldehyde) was added dropwise below 50 °C. After approximately 15 min of reaction, melamine with different amounts (i.e., 0.3, 0.7, and 1 g) was added. The mixture (melamine–phenol–formaldehyde resin) was cooled to room temperature and dissolved in ethanol after continuous stirring for 1 h at 70–75 °C, and the pH value was adjusted to approximately 7.0 with 0.6 M HCl solution.
Afterward, 10 g of block copolymer Pluronic F108 was added to the melamine–phenol–formaldehyde resin ethanol solution and stirred for 2 h. Then, the mixture was transferred into dishes. The ethanol was evaporated for 5–8 h at room temperature and heated at 100 °C for 24 h and 160 °C for 6 h in an oven for thermopolymerization. The as-made flaxen and transparent product were collected, ground, and mixed with NaOH in the same quantity. Calcination was performed in a tubular furnace at 350 °C for 2 h and 800 °C for 3 h under N2 flow with a heating rate of 1 °C min−1.
Finally, the produced materials were cooled in the inert atmosphere and grinded to obtain the carbon sample. The resulting carbons were denoted as HNMC03, HNMC07, and HNMC10, where HNMC represents melamine–phenol–formaldehyde-based mesoporous carbon and the following three numerals represent the addition of melamine mass. Before using, the prepared samples were washed several times with 0.1 M HCl solution, subsequently cleaned with deionized water until the pH value of the filtrate reached 7.0, and then dried at 60 °C for 12 h. For comparison, a carbon (HMC) without nitrogen doping is prepared from phenol–formaldehyde resin without addition of melamine through the same procedure as that for NHMC samples.
2.2 Characterization
Nitrogen isotherms were obtained with N2 at −196 °C after degassing the carbons at 150 °C under N2 atmosphere for 3 h. The surface area was calculated with Brunauer–Emmett–Teller (BET) model. The total pore volume (Vtot) was obtained by converting the nitrogen adsorption amount at a relative pressure of 0.98 to the liquid nitrogen volume. The average pore width (Dp) was calculated from 4Vtot/SBET. The mesopore and micropore size distribution were calculated from N2 adsorption data through Barrett–Joyner–Halenda (BJH) method and Horvath–Kawazoe (H–K) method. The mesopore volume (Vmeso) and micropore volume (Vmicro) of the samples were deduced through BJH and H–K method, respectively.
The carbon, hydrogen, and nitrogen percentage content of the carbons were analyzed with a CHN-O-RAPID Element Analyzer (Heraeus Co., Germany). The pH drift method was used to measure the point of zero charge (PZC) of the activated carbons. The functional groups of the carbons were examined through Fourier-transform infrared (FTIR) spectroscopy, which was performed with a Thermal Scientific apparatus (Model Nicolet 6700). The X-ray photoelectron spectroscopy (XPS) spectra were obtained on an Axis ultra-spectrometer (Kratos, Manchester, UK) with a mono Al-K (1486.6 eV) X-ray source at a power of 225 W (15 kV, 15 mA).
2.3 Adsorption experiments
2.3.1 Effect of pH. The prepared adsorbents were used to study the pH effect on Pb(II) ion adsorption. As the pH is more than 6, soluble lead ion species become fewer and subsequently the precipitation of lead hydroxide species occurs. Hence, the effect of pH was studied in the range of 1.5–6.0. About 0.05 g adsorbent was mixed with 50 mL 200 mg L−1 Pb(II) solutions for 4 h oscillation at 25 °C. The desired pH of the suspensions in each flask was adjusted with 0.1 mol L−1 HNO3 or NaOH solution. After consideration of the precipitation of lead hydroxide species as pH > 6, all subsequent experiments were carried out in a pH 4.5 medium.
2.3.2 Effect of time. The effect of time on the adsorption was investigated by shaking the flasks in different contact times (0–240 min) at 25 °C. For each experiment, 0.5 g NHMC10 was added to 500 mL Pb(II) ion solution with different initial concentrations of 50, 100, and 200 mg L−1 (the pH of the Pb(II) solution was adjusted to 4.5 through 0.01 mol L−1 NaOH or HNO3 solution).
2.3.3 Effect of temperature. The effect of temperature was investigated with different initial Pb(II) concentrations (at the range of 30–300 mg L−1) by contact with 0.05 g adsorbent for 4 h (the pH of the Pb(II) solution was adjusted to 4.5 through 0.01 mol L−1 NaOH or HNO3 solution). The experiments were conducted at different temperatures of 25 °C, 35 °C, and 45 °C. The solution samples were analyzed with the atomic absorption spectrometer AAS-3 (Carl Zeiss). The removal rate (R, %) and the amount of Pb(II) ions bounded by the adsorbent were calculated from the following equations: |
R (%) = (C0 − Ce)/C0 × 100,
| (1) |
where C0 (mg L−1) is the initial Pb(II) ion concentration, Ce (mg L−1) is the Pb(II) ion concentration at the equilibrium liquid phase, V (L) is the volume of the solution, and W (g) is the mass of adsorbent used.
2.4 Desorption and recyclability
NHMC10 was first saturated with Pb(II) by placing 0.5 g adsorbent in 500 mL of 100 mg L−1 Pb(II) solution to evaluate regeneration capacity. The mixture was stirred for 4 h at 25 °C. The final metal ion concentration in the aqueous solution was analyzed. The Pb–carbon mixtures were collected from the desorption process, and subsequently were regenerated thoroughly with 1 mol L−1 HNO3, washed with deionization water, dried under vacuum at 105 °C, and used in next adsorption experiment. The adsorption–desorption process was investigated in five cycles with the same carbon sample. The desorption ratio (D%) was calculated as follows: |
 | (3) |
3. Results and discussion
3.1 Physical properties of the adsorbents
The pore-structure properties of the as-prepared carbon samples are investigated with N2 adsorption–desorption analysis at −196 °C. The nitrogen adsorption–desorption isotherms for the HMC and NHMCs (i.e., NHMC03, NHMC07, and NHMC10) and the corresponding mesopore and micropore size distributions obtained via BJH and HK method for HMC and NHMC are shown in Fig. 1. The nitrogen adsorption–desorption isotherms of the HMC and NHMC samples show typical IV class isotherm with an obvious H2-type hysteresis loop. A progressive increase in adsorbed nitrogen volume below the relative pressure of 0.1 indicates the formation of a large amount of micropores (less than 2 nm) in the samples, which are thought to be generated via NaOH activation. Given that the size of lead ion is centered at 0.1–0.2, the presence of microporous pores is propitious to pollutant removal. Meanwhile, the desorption isotherm exhibits an obvious deviation from the adsorption isotherm, thereby demonstrating the presence of bottle neck-type or slit-type mesopores. The pore parameters of the carbons of HMC and the three NHMC samples are shown in Table 1. From Table 1, the total pore volume and the BET surface area of the NHMC samples are in the range of 0.85–1.20 cm3 g−1 and 1159–1770 m2 g−1, respectively, which gradually decrease with the melamine dose increasing from 0.3 to 1 g. In addition, the average pore size (Dp) of the prepared samples are increasing with melamine dose, implying that the introduction of nitrogen does not contribute to the formation of micropores under NaOH activation at high temperature. However, the fractions of mesoporous volume and microporous volume of the samples are all more than 50%, confirming the microporous/mesoporous structure of NHMCs.
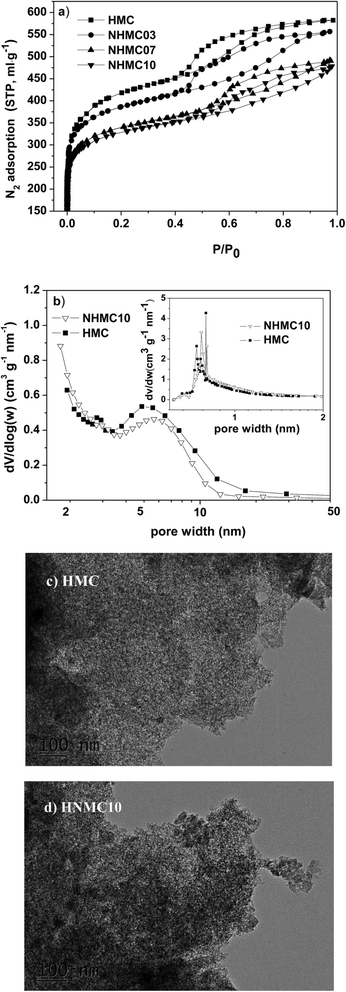 |
| Fig. 1 Nitrogen adsorption–desorption isotherms (a) and pore size distribution curves (b) of the samples, and TEM images for HMC (c) and NHMC10 (d). | |
Table 1 Pore properties of HMC and NHMCsa
Sample |
SBET (m2 g−1) |
Vtot (cm3 g−1) |
Vmes (cm3 g−1) |
Rmes (%) |
Vmicro (cm3 g−1) |
Rmicro (%) |
Dw (nm) |
Elemental composition (wt%) |
C |
H |
N |
O |
Rmes, fraction of the mesopores; Rmicro, fraction of the micropores. |
HMC |
1770 |
1.160 |
0.651 |
56.11 |
0.688 |
59.31 |
2.62 |
92.61 |
2.79 |
0.21 |
4.39 |
NHMC03 |
1463 |
0.992 |
0.517 |
52.12 |
0.619 |
62.40 |
2.71 |
91.33 |
2.53 |
2.86 |
3.28 |
NHMC07 |
1216 |
0.898 |
0.463 |
51.56 |
0.449 |
50.00 |
2.95 |
86.35 |
2.27 |
3.56 |
7.82 |
NHMC10 |
1159 |
0.869 |
0.452 |
52.01 |
0.436 |
50.17 |
2.99 |
83.27 |
2.61 |
4.27 |
9.85 |
The distribution curves of the samples further corroborate the preceding results of N2 analysis. For example, the pore size distribution of HMC and NHMC10 are shown in Fig. 1b. The size of the majority of mesopores concentrates in the range of 3–8 nm for HMC and NHMC10 according to the BJH pore size distribution. The most probable micropore sizes exist at 0.742, 0.766 and 0.798 nm for HMC, and at 0.770 and 0.803 nm for NHMC10 from the H–K micropore size distribution, respectively. Evidently, the pore size distribution curves demonstrate a narrow and well-defined pore size distribution, indicating that the prepared samples are hierarchical microporous/mesoporous system. The visual evidence is provided with TEM images in large domains (Fig. 1b and c). The micrographs in Fig. 1b and c show that NHMC10 and HMC particles contain a large number of channels that are regular in diameter and present a 3D structure with an mesopore diameter of approximately 4–8 nm, although they lack long-range packing order (wormhole-like structure). This interpenetrating network 3D structure may provide a suitable diffusion channel for Pb(II) ions into the interior of the copolymer beads when it is used in the adsorption of Pb(II) ions in aqueous solution.29
3.2 Chemical properties of the adsorbents
The chemical compositions of the NHMCs and HMC determined from elemental analysis are listed in Table 1. The N content of the carbons increases with increasing melamine for the preparation of melamine–phenol–formaldehyde resin. For example, the N contents of HMC and NHMC10 are 0.21% and 4.27%, respectively. The nitrogen-containing groups can be effectively controlled by adapting the initial content of melamine. The surface nitrogen functional groups of the activated carbons are also studied with FTIR analysis, and the resultant spectra of HMC, NHMC03, NHMC07, and NHMC10 are shown in Fig. 2. Compared with the FTIR spectrum of the sample HMC, which shows two main bands at 1500 cm−1 because of C–OH stretching and at 3430 cm−1 because of the stretching vibration of hydrogen bond or the O–H in-plane deformation vibration,30–33 the FTIR spectra of NHMC03, NHMC07, and NHMC10 show some new peaks at 1640 cm−1 possibly because of the O–H deformation of water or C
O stretching vibration, which translates into N–H vibration coupled with C
N bending vibration bond or C–N stretching mode after incorporation with nitrogen from quadrant stretching of pyridine.34 The signal at approximately 1400 cm−1 is a sharp peak, which belongs to NH2 stretching modes of amide or s-triazine derivatives. The broad peaks in the region between 1000 and 1200 cm−1 can be assigned to the C–N or C–O stretching vibration. In addition, the strong broad band at 3460 cm−1 on NHMCs can be assigned to N–H antisymmetric stretching vibration in pyrroles.35 The preceding result from the FTIR spectra preliminarily demonstrates the presence of N–H and C–N nitrogen species, such as pyrrolic and pyridinic-like groups in the NHMCs.
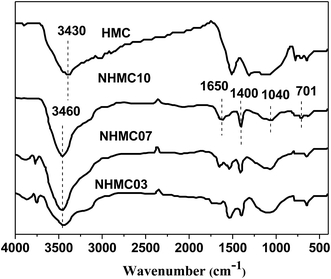 |
| Fig. 2 FTIR spectra of HMC and NHMCs. | |
XPS is employed to analyze the surface chemical composition and to qualify the nature of the nitrogen functional groups of HMC and NHMC10 (Fig. 3). Fig. 3 shows that carbon, oxygen, and nitrogen are the predominant elements for the NHMC10 observed on the surface from the binding energies at 285 eV (C 1s), 400.2 eV (N 1s), and 533 eV (O 1s). According to the spectra and references, the N 1s is deconvoluted into five different types of N-containing species: N1 (pyridine, ∼398.7 eV), N2 (imine/amide/amine, ∼399.5 eV), N3 (pyrrolic, ∼400.2 eV), N4 (quaternary N, ∼401.3 eV), and N5 (N-oxide, ∼403.1 eV).36 The surface nitrogen content of the NHMCs increases with increasing melamine. The highest content of the total nitrogen (4.27%) is observed in NHMC10. Fig. 3b shows that the N 1s spectra of NHMC10 are composed of several binding energies, which are deconvoluted into three peaks of 400.2, 399.2, 398.6 eV, and are assigned as pyrrolic, pyridine, and amine-like nitrogen, respectively.36,37 No nitrogen N 1s peak is observed from the XPS spectra for HMC, although strong carbon and oxygen peaks appear. This finding suggests that nitrogen-containing groups, including pyridine, pyrrolic and amine nitrogen, are successfully introduced on the exterior and pore surface of NHMC10. The presence of nitrogen-containing functional groups demonstrates a possibility of using NHMCs as the absorbent for the capture of heavy metals from aqueous solutions.
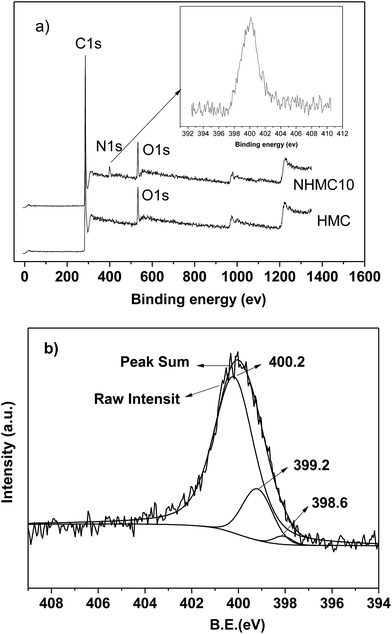 |
| Fig. 3 XPS of HMC and NHMC10 (a) and N 1s XPS spectra of NHMC10 (b). | |
3.3 Adsorption studies
3.3.1 Effect of pH on Pb(II) adsorption. Solution pH, connected with the adsorption mechanism, is one of the important parameters in controlling Pb(II) adsorption. It causes the change of surface charge of the sorbent, of conversion of lead species and other ions present in the solution, and of dissociation extent of functional groups on the active sites of the adsorbent.38 For lead aqueous solution, the distribution of lead ion species depends on both the total concentration of lead ion and pH value of the equilibrium solution. Pb(II) may exist in the aqueous phase in several anionic forms, such as Pb2+ (<5), Pb(OH)+ (6–8), and Pb(OH)2, Pb(OH)3−, Pb(OH)42−, Pb2(OH)3−, Pb3(OH)42− (>9) in aqueous solutions.39Thus, we investigate different processes when the pH ranged from 1.5 to 6.0, and the results are shown in Fig. 4. The adsorption capacity of HMC and NHMCs is significantly increased when the pH of Pb(II) solution increases from 1.5 to 4.5, and the optimum pH appears to be approximately 4.5–6.0. Thus, the surface properties of the adsorbents are highly sensitive to the pH of aqueous phase. At low pH, the majority of the nitrogen-containing functional groups, such as –NH– and –NH2, are protonated, and the competition of H+ with Pb(II) for adsorption reduces the active sites.40,41 The electrostatic repulsion between Pb(II) and the positively charged functional groups may prevent the adsorption of Pb(II) onto the surface of the adsorbents. By contrast, deprotonation starts with increasing pH, and the surface of adsorbents gradually develops negative electricity, thereby attracting the lead ions and greatly raising the absorption capacity of Pb(II) for both HMC and NHMCs.
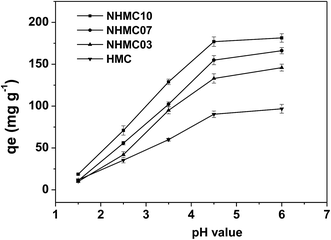 |
| Fig. 4 Effect of solution pH on the adsorption of Pb(II). | |
Fig. 4 also clearly shows that the introduction of nitrogen has a significant influence on the Pb(II) adsorption capacity for the carbon samples at the broad pH range of 2.5–6, and the order is NHMC10, NHMC07, NHMC03, and HMC. This finding indicates that N-doped mesoporous carbon (i.e., NHMC10, NHMC07, and NHMC03) provides considerably better Pb(II) uptake performance than the N-free carbon (i.e., HMC). The adsorption amount of metal ions adsorbed on the function of the porous material depends not only on the extent of diffusion inside the porous material but also on the chemical nature of the surface features (such as complexing capacity, steric effect, and hydrophilicity).42,43 The sample NHMC10 with the highest nitrogen content prepared in this study also displays the highest Pb(II) adsorption capacity among the three N-doped samples at different pH values despite its relatively small surface area and pore volume. This finding indicates the crucial role of nitrogen-containing groups on Pb(II) adsorption.
The Pb(II) adsorption capacity of NHMC10 is the greatest, and the adsorption amount is kept at the optimum level of 4.5–6.0. Consequently, the rest of the adsorption experiments are performed with NHMC10 at pH 4.5 of lead ion solution.
3.3.2 Effect of initial concentration. Fig. 5 illustrates the adsorption capacity and removal rate of NHMC10 and HMC for Pb(II) at different initial concentrations at 25 °C. The adsorption amount increases significantly with the initial concentration, and NHMC10 shows better adsorption capacity for Pb(II) than HMC. Nearly all of Pb(II) ions are removed via NHMC10 with the Pb(II) concentration of <125 mg L−1, whereas 47–67% of the Pb(II) is removed via NHMC. The Pb(II) adsorption amount reaches 178 mg g−1 on NHMC10, at a Pb(II) concentration of 200 mg L−1, which is nearly twice more than that on HMC (90 mg g−1). With the increase of the initial concentration of Pb(II), even when the concentration reaches 250 mg L−1, the removal rate of Pb(II) ions is maintained at a high level by NHMC10. The removal rate of Pb(II) ions is also higher than 60%, whereas the removal rate is less than 39% on HMC. The nitrogen-doped 3D carbon can be effectively used for Pb(II) removal in a broad range of Pb(II) initial concentrations.
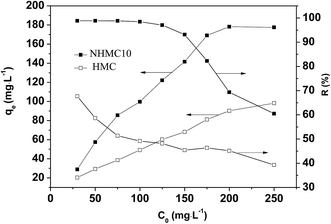 |
| Fig. 5 Adsorption of Pb(II) and removal rate for HMC and NHMC10. | |
3.3.3 Effect of contact time. The effect of contact time on Pb(II) adsorption on NHMC10 is studied at pH 4.5 with three different initial Pb(II) concentrations of 50, 100, and 200 mg L−1 at 25 °C. The adsorption time varies from 5 min to 240 min. Fig. 6 shows the change in the amount of Pb(II) adsorbed onto NHMC10 as a function of time. The adsorption increases rapidly in the first 15 min with 84–90% of the total Pb(II) having been adsorbed at all studied concentrations and is nearly complete by 30 min. This fast adsorption rate of NHMC10 for Pb2+ may be explained by the presence of numerous vacant adsorption sites homogeneously distributed across the NHMC10 surface and the inner porous structure. These sites are all available for adsorption during the initial stages, thereby leading to the rapid increase in Pb2+ uptake. The sites have a high affinity for Pb2+, and Pb2+ can easily reach the adsorption sites where they are trapped, thereby rapidly filling these sites. Hence, the time required for rapid equilibrium is 30 min. However, a contact time of 240 min is used for other studies.
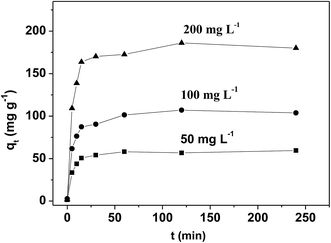 |
| Fig. 6 Effect of contact time on the adsorption of Pb(II). | |
3.3.4 Effect of temperature. Lead uptake as a function of temperature is shown in Fig. 7. The adsorption capacity of Pb(II) increases from 177 mg g−1 to 218 mg g−1 as temperature increases from 25 °C to 45 °C, suggesting that the increasing temperature favors the adsorption, and the adsorption process probably undergoes chemical rather than physical interaction.
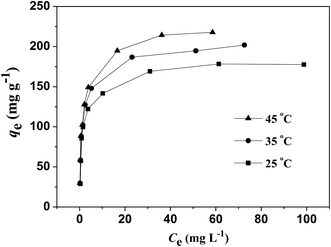 |
| Fig. 7 Pb(II) uptake as a function of temperature on NHMC10. | |
The adsorption potential energy (E) of Pb(II) adsorption may be estimated with Dubinin–Kaganer–Radushkevich (D–K–R) equation,44 as follows:
|
ln qe = ln qm − βε2,
| (4) |
where
qe is the equilibrium adsorption capacity (mol g
−1),
qm is the adsorption capacity on each monomolecular layer (mol g
−1),
β is the relative constant of the adsorption energy (mol
2 J
−2), and
ε is the Polanyi adsorption potential. Its form is as follows:
|
ε = RT ln(1/ce),
| (5) |
where
R is the gas constant (8.314 J (mol K)
−1),
T is the absolute temperature (K), and
ce is the equilibrium adsorption concentration (mol g
−1). According to ln
qe and
ε2, the slope is the value, and the adsorption capacity can be derived according to the intercept. The following is Hobson formula:
|
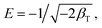 | (6) |
where
β and
E meet the relational expression, and
E is the adsorption potential energy (kJ mol
−1).
The fitting results of the isothermal adsorption data through D–K–R equation are shown in Table 2. The table shows that the R2 values at different temperatures are all higher than 0.89, indicating that the adsorption can be descripted with the model. The maximum adsorption capacity qm on the monomolecular layer increased with increasing temperature, thereby implying that this adsorption was an endothermic reaction. Thus, the increase in temperature promoted the adsorption. The adsorption potential energy in the ranges of 1–8 kJ mol−1 and 9–16 kJ mol−1 corresponds to the physical adsorption and chemical adsorption, respectively. The adsorption potential energy of Pb(II) adsorption on NHMC10 at 25 °C, 35 °C, and 45 °C was higher than 9 kJ mol−1, further implying that the adsorption is a chemical reaction process.
Table 2 Isotherm parameters of Pb(II) on NHMC10 at different temperatures
Isotherms |
Parameters |
HMC |
NHMC |
25 °C |
25 °C |
35 °C |
45 °C |
Langmuir qe = bq0Ce/(1 + bCe) |
q0 (mg g−1) |
135 |
175 |
197 |
212 |
B (L mg−1) |
0.0104 |
0.805 |
0.830 |
0.883 |
R2 |
0.973 |
0.970 |
0.982 |
0.967 |
Δqe |
11.20 |
12.89 |
7.14 |
12.74 |
Freundlich qe = KFCe1/n |
KF (L mg−1) |
6.607 |
80 |
89 |
96 |
n |
1.89 |
5.18 |
4.86 |
4.50 |
R2 |
0.953 |
0.861 |
0.889 |
0.921 |
Δqe |
8.81 |
41.85 |
41.30 |
38.53 |
Redlich–Peterson qe = KRCe/(1 + aCeƍ) |
KR (L mg−1) |
1.218 |
175 |
222 |
325 |
aR (L mg−1) |
4.89 |
1.21 |
1.43 |
2.19 |
ƍ |
1.50 |
0.949 |
0.936 |
0.898 |
R2 |
0.972 |
0.977 |
0.994 |
0.992 |
Δqe |
14.54 |
16.06 |
7.34 |
6.77 |
Temkin y = β ln A + B ln x |
AT (L mg−1) |
0.1359 |
22 |
21 |
22 |
βT (L mg−1) |
30 |
25 |
28 |
31 |
R2 |
0.931 |
0.941 |
0.969 |
0.988 |
Δqe |
21.04 |
26.70 |
15.91 |
9.44 |
Dubinin–Kaganer–Radushkevich ln qe = ln qm − βε2 |
βD (mol2 J−2) |
5.45 × 10−9 |
5.44 × 10−9 |
5.36 × 10−9 |
5.17 × 10−9 |
qm (mg g−1) |
978 |
202 |
234 |
253 |
R2 |
9.03 |
8.976 |
0.944 |
0.962 |
E (kJ mol−1) |
9.58 |
9.58 |
9.66 |
9.83 |
3.3.5 Isotherms and thermodynamic. Adsorption isotherms allow evaluating the applicability of the adsorption process as a unit operation, estimating the maximum adsorption capacities of adsorbent materials, and defining the characteristic of the adsorption process between liquid and solid phases when it reaches the equilibrium state. Thus, the adsorption isotherm study shows Langmuir, Freundlich, Redlich–Peterson, and Temkin isotherm models.45,46 The equations and parameters of the isotherm models are listed in Table 2. The normalized standard deviation Δqe (%) is calculated with the following equation: |
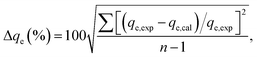 | (7) |
where qe,exp and qe,cal are the experimental and calculated adsorption capacity values, respectively, and n is the number of experiments.The experimental isotherm data at different temperatures (Fig. 7) was fitted with the nonlinear equations of Langmuir, Freundlich, Temkin, and Redlich–Peterson models by Origin 9.0 software. The fitted values of isotherm parameters, the maximum adsorption capacity (qm), the determination coefficient (R2), and the normalized standard deviation (Δqe) are listed in Table 2. The equilibrium data are described best with Redlich–Peterson model for Pb(II) on NHMC10, based on the highest correlation coefficients (R2) and low values of Δqe. Redlich–Peterson model consists of the combination of Langmuir and Freundlich models, which are distinguished with the exponent ƍ. The isotherm resembles Freundlich model with values of ƍ close to 0, whereas the isotherm has the behavior of the Langmuir model when the value of ƍ is close to 1. In consideration of the ƍ values in the range of 0.898–0.949, the isotherm behaves according to the Langmuir model, and the adsorption process occurs on a homogeneous surface,47 which is further confirmed with the highest correlation coefficients (R2) and values of Δqe lower than those for Freundlich model. According to the theoretical foundation of Langmuir isotherm model, the adsorption process is monolayer adsorption onto NHMC10 surface with finite number of identical sites, which are homogeneously distributed over the adsorbent surface.
Thermodynamic parameters, including Gibbs free energy change (ΔG0), enthalpy change (ΔH0), and entropy change (ΔS0) for Pb(II) adsorption, are evaluated with the following equations:
|
ΔG0 = −RT ln KD,
| (8) |
|
ln KD = ΔS0/R − (ΔH0/R)/T,
| (9) |
where
R (8.314 J (mol K)
−1) and
T (K) are the universal gas constant and the temperature in Kelvin, respectively. ln
KD is calculated by plotting ln(
qe/
ce)
versus qe and extrapolating
qe to zero.
The thermodynamic parameters for the adsorption of Pb(II) on NHMC10 are presented in Table 3. The negative values of ΔG and the positive value of enthalpy change ΔH0 indicate that the Pb(II) adsorption on NHMC10 is a feasible and spontaneous endothermic process. The decrease in ΔG0 with increasing temperature suggests that adsorption is favorable at high temperature. Meanwhile, the positive values of ΔS0 indicate that the degrees of freedom increase at the solid solution interface during the adsorption of Pb(II) on NHMC10 and reflect the possible structural changes or interaction between Pb(II) ions and NHMC10.
Table 3 Adsorption thermodynamic parameters of Pb(II) on NHMC
T (°C) |
ΔG0 (kJ mol−1) |
ΔH0 (kJ mol−1) |
ΔS0 (J mol−1 K−1) |
25 |
−15.35 |
14.07 |
99 |
35 |
−16.39 |
14.07 |
99 |
45 |
−17.33 |
14.07 |
99 |
3.4 Adsorption mechanism
The Pb(II) capacity of NHMC10, as discussed in the previous section, is nearly twice higher than that of HMC. Four kinds of adsorption binding affinity may exist for the enlarged Pb(II) binding to the NHMC10 surface, such as van der Waals force, electrostatic attraction, ion-exchange, and chelation. The electrostatic interactions between NHMC10 and Pb ions are obviously repulsive under acidic condition, given that solution pH is lower than the pHPZC, thereby preventing the metal ions from coming in contact with the adsorbent surfaces rather than promoting the adsorption. In addition, the surface area, total pore volume, mesopore volume, and micropore volume of the NHMC10 are smaller than those of HMC, whereas the average pore sizes of the two adsorbent are close, indicating that the van der Waals force is not responsible for the increment of Pb(II) adsorption on NHMC10 than HMC.
XPS analysis is applied to determine the adsorption mechanisms by characterizing the changes of functional groups before and after adsorbing Pb(II) (denoted as NHMC10 and NHMC10-Pb2+, Fig. 8). Compared with the pristine NHMC10, two significant Pb(II) peaks, which are located at 139.5 and 144.3 eV and correspond to the Pb 4f, are observed in the survey spectrum of NHMC10-Pb2+. This observation indicates that Pb(II) can be adsorbed on the NHMC10 with two types of binding sites (e.g., C–N and R–N–H). The XPS of Pb 4f of NHMC10-Pb2+ shows a slight shift to the lower binding energy for Pb 4f5/2 at 144.3 eV and 4f7/2 at 139.5 eV in comparison with the studied Pb(NO3)2 centered at 145 eV for 4f5/2 and 139.9 eV for 4f7/2. The results indicate that the specific capture for Pb(II), not merely electrostatic interaction, can account for the mechanism of Pb(II) adsorption onto the prepared NHMC10, and the interaction is ascribed to Pb–N binding. The results of XPS spectrum analyses effectively demonstrate that the adsorption of Pb(II) is mainly attributed to nitrogen-containing functional groups (e.g., C–N and R–N–Hχ) as well as π electron system of pyrrolic or pyridinic units. The delocalized π electron systems of carbon–nitrogen ring (–Cχ–Ny–) units in pyrrolic and pyridinic-like compounds can act as Lewis base, whereas the metal ions act as Lewis acid.48 Therefore, the adsorption of heavy metal ions on NHMC10 is also ascribed to the strong surface complexation between NHMC10 and metal ions through Lewis acid base interaction.
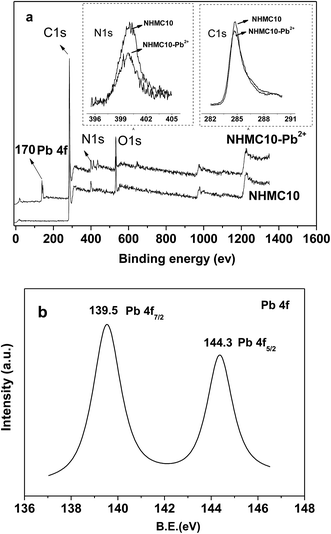 |
| Fig. 8 XPS of NHMC10 before (a) and after (b) Pb(II) adsorption. | |
3.5 Comparison of NHMC adsorbent performance with other mesoporous carbons
As shown in Table 4, compared with other mesoporous carbons, such as the ordered carbon CMK-3 and the nitrogen-doped CMK-3,49,50 NHMC10 exerts excellent adsorptive removal performance toward Pb(II) in adsorption capacity, adsorption conditions, and equilibrium time. This superior adsorption performance should be most probably caused by a high binding affinity between Pb(II) and its binding sites, resulting from the combined effect of both the particular 3D hierarchical microporous/mesoporous structure and the introduced nitrogen-containing functions. The formed interpenetrating network structure may provide suitable diffusion channel for Pb(II) ions into the interior of the carbon during the Pb(II) adsorption process, thereby shortening the path of Pb(II) to the basic sites (e.g., C–N and R–N–H) and micropore adsorption sites and raising the adsorption efficiency and capacity.
Table 4 Comparison of Pb(II) removal performance of various mesoporous carbons
Adsorbent |
N (%) |
SBET (m2 g−1) |
Qm (mg g−1) |
Equilibrium (min) |
Adsorption condition |
References |
P-CMK3 |
0.1 |
1254 |
120 |
75 |
pH = 5, T = 20 °C |
18 |
O-CMK3 |
— |
970 |
177 |
75 |
pH = 5, T = 20 °C |
18 |
A-CMK3 |
12.2 |
15 |
177 |
75 |
pH = 5, T = 20 °C |
18 |
CMK-3E |
— |
944 |
94 |
— |
pH = 5, T = 25 °C |
49 |
OMC |
— |
— |
113 |
90 |
pH = 7.0, T = 30 °C |
50 |
Fe/OMC |
— |
523 |
136 |
90 |
pH = 7.0, T = 30 °C |
50 |
N-Fe/OMC |
— |
886 |
160 |
90 |
pH = 7.0, T = 30 °C |
50 |
NHMC10 |
4.27 |
1159 |
212 |
30 |
pH = 4.5, T = 45 °C |
This study |
3.6 Desorption efficiency and recyclability
The regeneration of sorbent is a crucial factor in the practical application of the sorbent. Regeneration and adsorption by 1 mol L−1 HNO3 are repeated five times. Table 5 shows the results of five adsorption–regeneration cycles of Pb(II) on sample NHMC10. Table 5 shows that the D% of the NHMC10 carbon is 98.1, 97.6, 96.8, 98.6 and 97.5 for first, second, third, fourth and fifth desorption process, respectively. The adsorption capacity of the NHMC10 for the fifth adsorption is 93 mg g−1, which means 10.47% loss of adsorption capacity of the initial use. The Pb(II) adsorption capacity of the carbon does not show a significant loss for each repeated adsorption–desorption cycles. These results are ascribed to the high specific surface area and hierarchical pore structure of NHMC10. Thus, NHMC10 can be reused nearly without a significant decrease in the adsorption capacity and the recover efficiency after quite a number of cycles.
Table 5 Adsorption and desorption capacities of NHMC10
Cycle |
Adsorption capacity (mg g−1) |
Desorption (%) |
1 |
104 |
98.1 |
2 |
102 |
97.6 |
3 |
99 |
96.8 |
4 |
95 |
98.6 |
5 |
93 |
97.5 |
4. Conclusions
In this study, a series of NHMCs with controllable doping contents (∼4.27%) and consistent pore structure (fraction of the mesopores around 52%) are prepared with a general sol–gel route and NaOH-assisted activation. The nitrogen atoms on the carbon surface can be adjusted by controlling the dosage of melamine, which shows different states and valence states (pyrrolic, pyridine, and amine-like nitrogen), thereby providing adsorption sites for easy Pb(II) binding to the surface through strong chemisorptive bonds or ion exchange. The Pb(II) adsorption capacities of NHMC materials are greatly proportional to the nitrogen contents, which results in accessible basic sites. The highest Pb(II) adsorption capacity of 212 mg g−1 is achieved via NHMC10 with a nitrogen content of 4.27%, which is two times higher than that of nondoped carbon HMC. The adsorption rate is relatively fast, and the adsorption equilibrium nearly reaches about 30 min. These adsorption performances are superior to those in the literature for mesoporous carbons, such as ordered mesoporous carbon CMK3 and nitrogen-doped CMK3, which is probably caused by a high binding affinity between Pb(II) and its binding sites on the 3D hierarchical microporous/mesoporous structure. Even after five consecutive adsorption–desorption cycles, no obvious decrease in Pb(II) adsorption is detected. This observation implies that the prepared NHMC10 can be a potential adsorbent for efficient Pb(II) removal, and the usefulness of the obtained nitrogen-doped 3D hierarchical microporous/mesoporous carbons toward the removal of heavy metal ions from waters and wastewaters is indicated.
Acknowledgements
The authors gratefully acknowledge the research grant provided by China under the Natural Science Foundation (No. 51102136), the Fundamental Research Funds for the Central Universities (No. 2015NJAUG02), and China Postdoctoral Science Fund (No. 2014M560429).
References
- Ihsanullah, A. Abbas, A. M. Al-Amer, T. Laoui, M. J. Al-Marri, M. S. Nasser, M. Khraisheh and M. A. Atieh, Sep. Purif. Technol., 2016, 157, 141–161 CrossRef CAS
. - A. Abou-Shady, C. Peng, J. Bi, H. Xu and J. Almeria O, Desalination, 2012, 286, 304–315 CrossRef CAS
. - R. A. Abu-Zurayk, R. Z. Al Bakain, I. Hamadneh and A. H. Al-Dujaili, Int. J. Miner. Process., 2015, 140, 79–87 CrossRef CAS
. - M. R. Awual, Chem. Eng. J., 2016, 289, 65–73 CrossRef CAS
. - G. Hong, L. Xiong, L. Shen, W. Min, C. Wang, X. Yu and X. Wang, J. Hazard. Mater., 2015, 295, 161–169 CrossRef CAS PubMed
. - S. Li, Y. Wei, Y. Kong, Y. Tao, C. Yao and R. Zhou, Synth. Met., 2014, 199, 45–50 CrossRef
. - I. Emmanuelawati, J. Yang, J. Zhang, H. Zhang, L. Zhou and C. Yu, Nanoscale, 2013, 5, 6173–6180 RSC
. - S. Purwajanti, L. Zhou, Y. Ahmad Nor, J. Zhang, H. Zhang, X. Huang and C. Yu, ACS Appl. Mater. Interfaces, 2015, 7, 173–183 Search PubMed
. - A. A. Taha, M. A. Shreadah, A. M. Ahmed and H. F. Heiba, J. Environ. Chem. Eng., 2016, 4, 1166–1180 CrossRef CAS
. - J. Liu, N. P. Wickramaratne, S. Z. Qiao and M. Jaroniec, Nat. Mater., 2015, 14, 763–774 CrossRef CAS PubMed
. - Z. Chang, Z. Yu, G. Zeng, B. Huang, H. Dong, J. Huang, Z. Yang, J. Wei, H. Liang and Z. Qi, Chem. Eng. J., 2015, 284, 247–259 Search PubMed
. - H. Tian, J. Liu, K. O'Donnell, T. Liu, X. Liu, Z. Yan, S. Liu and M. Jaroniec, J. Colloid Interface Sci., 2016, 476, 55–61 CrossRef CAS PubMed
. - J. Tang, J. Liu, C. Li, Y. Li, M. O. Tade, S. Dai and Y. Yamauchi, Angew. Chem., Int. Ed. Engl., 2015, 54, 588–593 CAS
. - K.-Y. Shin, J.-Y. Hong and J. Jang, J. Hazard. Mater., 2011, 190, 36–44 CrossRef CAS PubMed
. - T. Yang, R. Zhou, D. W. Wang, S. P. Jiang, Y. Yamauchi, S. Z. Qiao, M. J. Monteiro and J. Liu, Chem. Commun., 2014, 51, 2518–2521 RSC
. - H. Vijwani, M. N. Nadagouda, V. Namboodiri and S. M. Mukhopadhyay, Chem. Eng. J., 2015, 268, 197–207 CrossRef CAS
. - X. Sun, L. Yang, H. Xing, J. Zhao, X. Li, Y. Huang and H. Liu, Colloids Surf., A, 2014, 457, 160–168 CrossRef CAS
. - M. Barczak, K. Michalak-Zwierz, K. Gdula, K. Tyszczuk-Rotko, R. Dobrowolski and A. Dąbrowski, Microporous Mesoporous Mater., 2015, 211, 162–173 CrossRef CAS
. - G. S. Shao, L. Liu, T. Y. Ma and Z. Y. Yuan, Chem. Eng. J., 2011, 174, 452–460 CrossRef CAS
. - J. Zou, D. Ying, W. Xue, Z. Ren, C. Tian, P. Kai, S. Li, M. Abuobeidah and H. Fu, Bioresour. Technol., 2013, 142C, 209–217 CrossRef PubMed
. - J. Goscianska, A. Olejnik, I. Nowak, M. Marciniak and R. Pietrzak, Chem. Eng. J., 2016, 290, 209–219 CrossRef CAS
. - J. Dobor, K. Perényi, I. Varga and M. Varga, Microporous Mesoporous Mater., 2015, 217, 63–70 CrossRef CAS
. - M. Machida, B. Fotoohi, Y. Amamo and L. Mercier, Appl. Surf. Sci., 2012, 258, 7389–7394 CrossRef CAS
. - S. Geng, J. Liu, W. Chen, L. Dong and T. Liang, Appl. Surf. Sci., 2015, 351, 911–919 CrossRef CAS
. - G. Shen, X. Sun, H. Zhang, Y. Liu, J. Zhang, A. Meka, L. Zhou and C. Yu, J. Mater. Chem. A, 2015, 3, 24041–24048 CAS
. - H. Tian, M. Saunders, A. Dodd, K. O'Donnell, M. Jaroniec, S. Liu and J. Liu, J. Mater. Chem. A, 2016, 4, 3721–3727 CAS
. - Y. Song, G. Ye, J. Chen, D. Lv and J. Wang, Appl. Surf. Sci., 2015, 357, 1578–1586 CrossRef CAS
. - K. Q. L. E. B. Xu, Z. Q. Zhu, J. Q. Jia and X. H. Wang, Environ. Chem., 2015, 34, 7 Search PubMed
. - Q. Zhao, R. Lin, H. Zhou, C. Tian and C. Peng, Chem. Eng. J., 2014, 250, 6–13 CrossRef CAS
. - S. Biniak, G. Szymański, J. Siedlewski and A. Ś. j. m. Tkowski, Carbon, 1997, 35, 1799–1810 CrossRef CAS
. - M. Danish, R. Hashim, M. N. M. Ibrahim and O. Sulaiman, J. Anal. Appl. Pyrolysis, 2013, 104, 418–425 CrossRef CAS
. - M. H. Kasnejad, A. Esfandiari, T. Kaghazchi and N. Asasian, J. Taiwan Inst. Chem. Eng., 2012, 43, 736–740 CrossRef
. - M. H. Mahaninia, P. Rahimian and T. Kaghazchi, Chin. J. Chem. Eng., 2015, 59, 50–56 CrossRef
. - Y. Pang, G. Zeng, L. Tang, Y. Zhang, Y. Liu, X. Lei, Z. Li, J. Zhang and G. Xie, Desalination, 2011, 281, 278–284 CrossRef CAS
. - S. Shin, J. Jang, S. H. Yoon and I. Mochida, Carbon, 1997, 35, 1739–1743 CrossRef CAS
. - S. Kundu, W. Xia, W. Busser, M. Becker, D. A. Schmidt, M. Havenith and M. Muhler, Phys. Chem. Chem. Phys., 2010, 12, 4351–4359 RSC
. - G. Yang, H. Chen, H. Qin and Y. Feng, Appl. Surf. Sci., 2014, 293, 299–305 CrossRef CAS
. - K. Li and X. Wang, Bioresour. Technol., 2009, 100, 2810–2815 CrossRef CAS PubMed
. - K. Li, Z. Zheng and L. Ye, J. Hazard. Mater., 2010, 181, 440–447 CrossRef CAS PubMed
. - V. Hernández-Morales, R. Nava, Y. J. Acosta-Silva, S. A. Macías-Sánchez, J. J. Pérez-Bueno and B. Pawelec, Microporous Mesoporous Mater., 2012, 160, 133–142 CrossRef
. - L. Yang, Y. Li, X. Jin, Z. Ye, X. Ma, L. Wang and Y. Liu, Chem. Eng. J., 2011, 168, 115–124 CrossRef CAS
. - D. M. Burke, M. A. Morris and J. D. Holmes, Sep. Purif. Technol., 2013, 104, 150–159 CrossRef CAS
. - S. Yamanaka, M. Machida, M. Aikawa and H. Tatsumoto, Carbon, 2008, 46, 4644–4651 CrossRef
. - F. R. Chaspoul, M. F. L. Droguene, G. Barban, J. C. Rose and P. M. Gallice, Waste Manag., 2008, 28, 1324–1330 CrossRef CAS PubMed
. - M. Ahmaruzzaman and S. L. Gayatri, Chem. Eng. J., 2010, 158, 173–180 CrossRef CAS
. - R. I. Yousef, B. El-Eswed and A. A. H. Al-Muhtaseb, Chem. Eng. J., 2011, 171, 1143–1149 CrossRef CAS
. - X. Huang and M. Pan, J. Mol. Liq., 2016, 215, 410–416 CrossRef CAS
. - X. Song, H. Liu, C. Lei and Y. Qu, Desalination, 2010, 255, 78–83 CrossRef CAS
. - R. Moreno-Tovar, E. Terrés and J. R. Rangel-Mendez, Appl. Surf. Sci., 2013, 303, 373–380 CrossRef
. - G. Yang, T. Lin, G. Zeng, C. Ye, T. Jing, Y. Pang, Y. Zhou, Y. Liu, J. Wang and Z. Sheng, Chem. Eng. J., 2015, 259, 854–864 CrossRef CAS
.
|
This journal is © The Royal Society of Chemistry 2016 |
Click here to see how this site uses Cookies. View our privacy policy here.