DOI:
10.1039/C6RA15126D
(Paper)
RSC Adv., 2016,
6, 90994-91001
Curing kinetics, thermal and mechanical properties of TDE-85 modified by bicyclo-benzoxazine†
Received
10th June 2016
, Accepted 28th August 2016
First published on 29th August 2016
Abstract
To reduce the curing temperature and also to enhance the mechanical properties and the heat resistance of diglycidyl-4,5-epoxy-cyclohexane-1,2-dicarboxylate (TDE-85), it was crosslinked with 4,4-diamino diphenyl sulphone (DDS) using a synthesized bicyclo-benzoxazine (BOZ) crosslinker. The kinetic parameters of the curing reaction were evaluated using Flynn–Wall–Ozawa and Kissinger's methods. The gelation time and differential scanning calorimetry (DSC) of non-isothermal testing were performed to determine the curing process of BOZ/DDS/TDE-85 systems. Fourier transform infrared spectroscopy (FTIR) was used to follow the major changes in functional groups during the curing process. The absorbance of the oxazine ring showed a significant reduction and the peak of epoxy group became very weak, indicating that the curing reaction was almost complete. The thermal properties were evaluated by heat distortion temperature (HDT) and thermogravimetric analysis (TGA), exhibiting a higher initial decomposition temperature, decreased rate of decomposition and higher char yield compared to the neat epoxy resin system. BOZ enhanced the stability of the epoxy blend, which restricted the mobility of the chain and hindered the decomposition process. The fractured surface of the cured product was observed by scanning electron microscopy (SEM). The fracture form of BOZ/DDS/TDE-85 systems belongs to typically ductile fracture compared to the neat DDS/TDE-85 system. It was found that the thermal and mechanical properties of BOZ/DDS/TDE-85 systems increased with the addition of a certain amount of BOZ. The impact, flexural, and compressive strengths increased by 43.4%, 13.1%, and 8.5%, respectively. The addition of BOZ lowered the activation energy on account of the reduced viscosity, allowing better contact of the resin with the curing agent. The reaction order and activation energy were found to be 0.92 and 63.15 kJ mol−1, respectively.
1. Introduction
Epoxy resins (EP) are used widely in surface coatings, electronic packaging materials, adhesive formulations, semiconductor encapsulation and matrix of fiber reinforced composites. These applications are based mainly on their good mechanical properties, high adhesive strength, better heat resistance and controlled electrical insulation.1–4 As a type of alicyclic glycidyl ester epoxy resin, diglycidyl-4,5-epoxy-cyclohexane-1,2-dicarboxylate (TDE-85) possesses many outstanding properties such as a higher epoxy value (0.85), low viscosity (∼1500 cp at room temperature), higher reactivity than ordinary alicyclic epoxy resin, good heat resistance, and high strength.5 However, major drawbacks, such as a poor bearing capacity to impact load and brittleness, limit its further development in high-tech aerospace fields.6 These limiting areas along with the enhancement of thermal stability of TDE-85 have been a challenging area for many research groups. Kimura7 and co-workers used benzoxazine (BOZ) as the curing agent and investigated the curing behavior and properties of the blended resin. The results indicated that EP cured by benzoxazine based bisphenol A (B-a) showed 33.3% improvement in volume resistivity, 17.4% in Tg and 0.07% degradation in water resistance compared to EP cured by the phenolic based bisphenol A. Kuo8 et al. blended EP with vinyl-terminated benzoxazine (VB-a) and studied the curing kinetics and thermal properties. The glass transition temperature (Tg), thermal degradation temperature (Td, at 20% weight loss) and activation energy (Ea, by Flynn–Wall–Ozawa method) of the EP/VB-a (75/25) system were 171.9 °C, 374.6 °C and 25.94 kJ g−1, respectively. With the increase in VB-a contents (EP/VB-a = 25/75), Tg, Td and Ea was determined to be 279.9 °C, 376.1 °C and 19.97 kJ g−1, respectively, showing an improvement in the thermal properties with a very low Ea value. The abovementioned research indicates that curing agent influences not only the curing behavior but also the performance of the final product. BOZ has attracted the attention of many researchers as a new type of phenolic resin.9 In recent years, much attention has been paid to the synthesis of BOZ and various BOZ have been developed due to their flexible molecular design.10–14 Many researchers demonstrated a variety of attractive properties including a low water absorption, high char yield, near-zero volumetric change upon curing, high thermal stability, good dielectric and mechanical properties, high Tg, and excellent solubility in common organic solvents, making BOZ an optimal candidate for high performance applications.15,16 BOZs have excellent mechanical properties as compared to epoxy resins.17–19 The high reactivity of the phenolic hydroxyl produced by the ring opening of BOZ, hydrogen bonds generated by the combination of nitrogen-atoms on the Minnich structure and oxygen atoms located on the phenolic hydroxyl remarkably improve the heat resistance.20,21 It was found that both the ortho and para position of phenolic hydroxyl can participate in the reaction, generating more crosslinking points, which can lead to the improvement of molecular weight and crosslinking density. The abovementioned characteristics reflect in good mechanical properties, heat stability, and higher Tg.
Over the past few years, many researchers have performed considerable research on the modification of TDE-85 epoxy resin.22 However, it is rare to see modifications that can markedly decrease the curing temperature and improve both the heat stability and the toughness of the cured products. Therefore, in this present study, BOZ was synthesized and added to DDS/TDE-85 systems. The curing reaction kinetic parameters of BOZ/DDS/TDE-85 systems were obtained adopting Kissinger and Flynn–Wall–Ozawa methods combining the differential scanning calorimetry (DSC) curves. The group changes during reaction process were monitored by FTIR spectroscopy in detail. Simultaneously, the curing process was determined and the thermal and mechanical properties were measured systematically. The results showed that the addition of BOZ reduced the curing temperature of the DDS/TDE-85 resin systems efficiently, and thus significantly improved the curing process, which reduced the requirement of the equipment during production process and lowered the cost. It can be noted that the toughness, heat resistance and stiffness were improved at the same time.
2. Experiments
2.1 Materials
4,4′-Diamino diphenyl methane (DDM) and DDS were purchased from Sinopharm chemical reagent Co., Ltd (Shanghai, China). Phenol and formaldehyde were received from Tianli Chemical Reagent Co., Ltd (Tianjin, China). TDE-85 epoxy resin with an epoxy value of 0.85 was purchased from Tianjin jingdong chemical compound material Co. Ltd (Tianjin, China).
2.2 Preparation of BOZ/DDS/TDE-85 blends
BOZ was synthesized using DDM, phenol and formaldehyde according to the previously reported procedure.23 BOZ, DDS and TDE-85 were poured into a beaker and gradually heated to 120 °C using an oil heated bath. After complete melting and mixing, the homogeneous liquid was casted into a preheated mold. For smooth casting, the pouring process was completed in a very short time. Air bubbles were removed by applying vacuum and further cured at 130 °C for 2 h, 150 °C for 2 h and 180 °C for 2 h under a constant vacuum in a vacuum oven. After cooling to room temperature, the cured sheets was taken out from the mold and cut into standard samples.
During the curing process of epoxy resin and amine curing agent, the primary amine and secondary amine mainly participate in the reaction. The theoretical dosage of the amine curing agent can be calculated using the following equation:24
|
 | (1) |
where
Wa is the quality of amine curing agent for 100 g epoxy resin,
M is the relative molecular mass of amine,
N is the number of active hydrogen atom in amine molecule,
Ac is the amine equivalent (
Ac =
M/
N), and
Ev is the epoxy value of epoxy resin.
In this study, TDE-85 and DDS are a type of epoxy resin and curing agent, respectively. From eqn (1), the theoretical quality of DDS can be calculated as 52.62 g for 100 g epoxy resin. It can be set to 50 g in practice. Therefore, the stoichiometric ratio of TDE-85
:
DDS is 100
:
50.
2.3 Characterization
HDT of the specimens was obtained according to GB/T 1634-2004 on a XRW-300HB testing instrument (Dajia Nanotek Instruments, Chengde, China). The dimensions of the specimen were (80 ± 1) × (10 ± 0.2) × (4.0 ± 0.2) mm3 and the span was 64 mm. The heating rate was chosen as 2 °C min−1. SEM was operated on a VEGA3LMH instrument (TESCAN Company, Czech Republic). The fractured surfaces of the specimens were coated with gold as a conductive medium.
FTIR spectra of BOZ/DDS/TDE-85 systems in different curing stage were obtained on a WQF-310 spectrometer using pellets mixed KBr and samples in 500–4000 cm−1. 1H-NMR spectrum was acquired on a BRUKER AM-400S (400MHZ) spectrometer using tetramethylsilane (TMS) as an internal standard and chloroform-d3 (CDCl3) as a solvent.
DSC was performed on a MDSC2910 instrument (TA Company, America). The specimens were heated at a rate of 5, 10, and 15 °C min−1 in a nitrogen atmosphere from 25 to 300 °C. The sample weight was 5–10 mg. TGA was operated on a Q-50 thermo-gravimetric analyzer (TA company, America). The samples were heated from 25 to 800 °C at a heating rate of 10 °C min−1 in a nitrogen (N2) atmosphere. The sample weight was about 5 mg and the flow velocity of gas (N2) was 20 ml min−1.
The impact strength was measured according to part 5.4 of GB/T 2567-2008 on a ZBC-50B testing instrument (Shenzhen SANS Testing Detection Co., Ltd, China). The specimens were unnotched with dimensions of (80 ± 1) × (10 ± 0.2) × (4.0 ± 0.2) mm3. The span was chosen as 60 mm. The flexural properties were determined according to part 5.3 of GB/T 2567-2008 on a CMT6303 testing instrument (Shenzhen SANS Testing Detection Co., Ltd, China). The dimensions of the specimens were (80 ± 1) × (15 ± 0.2) × (4.0 ± 0.2) mm3. The span to thickness ratio was (16 ± 1)
:
1 and the test speed was 2 mm min−1. The compressive properties were performed according to part 5.2 of GB/T 2567-2008 on a CMT7204 testing instrument (Shenzhen SANS Testing Detection Co., Ltd, China). The specimens were in the form of a cylinder, whose diameter and height were (10 ± 0.2) mm and (25 ± 0.5) mm, respectively.
The water absorption of BOZ/DDS/TDE-85 systems was performed according to GB/T 1462. The specimens with dimensions of 50 × 50 × 4 mm3 were dried before and then immersed in water at 50 and 25 °C. The water absorption was calculated as the following equation:
|
 | (2) |
where
W0 is the weight of dried specimen;
Wt is the weight of specimen immersed in water for
t day.
3. Results and discussion
3.1 Characterization of BOZ
The chemical structure of BOZ was characterized by FT-IR and 1H-NMR spectroscopy. The FTIR and 1H-NMR spectra of BOZ are presented in Fig. S1 and S2,† respectively.
Fig. S1† shows that the presence of cyclic ether of benzoxazine structure, which was confirmed by the absorbance peak at 1228 cm−1 assigned to the asymmetric stretching mode of the C–O–C group. Benzene with an attached oxazine ring was confirmed by the vibration peak at 941 cm−1. The stretching vibration peak of R–O on the oxazine ring is located at 1034 cm−1. The stretching vibration peak of the bond between the benzene ring and oxygen is located at 1250 cm−1. By the abovementioned results, it can be preliminarily determined that BOZ had been synthesized.
Fig. S2† shows that the characteristic signals of oxazine ring assigned to Ar–CH2–N-(2 and 2′) and –O–CH2–N-(1 and 1′) protons appeared at 4.75 ppm and 5.33 ppm. The aromatic protons were identified in the 6.5–7.5 ppm range.
Combining FTIR and 1H-NMR results, it can be determined that BOZ had been synthesized successfully and the productivity reached 68%.
3.2 Solubility of BOZ
BOZ is a type of light yellow powder. Table 1 lists the solubility of BOZ in several solvents. It shows that BOZ possesses good solubility in CCl3, THF, CHCl2, 1,4-dioxane, and DMF, whereas it is insoluble in acetone. The information of solubility plays an important role in the application of BOZ.
Table 1 Solubility of BOZa
|
CCl3 |
THF |
CHCl2 |
1,4-Dioxane |
DMF |
DMSO |
Acetone |
Note: ++soluble; +−partially soluble; −−insoluble. |
5 min |
++ |
++ |
++ |
++ |
++ |
−− |
−− |
24 h |
++ |
++ |
++ |
++ |
++ |
+− |
−− |
3.3 Curing behavior of BOZ/DDS/TDE-85 systems
The time that resin systems require from fusion to gel in a given temperature is called the gel time, which provides strong evidence for a determination of the curing behavior.25 Fig. 1 shows the gel time of DDS/TDE-85 and BOZ/DDS/TDE-85 systems. It is obvious that the BOZ/DDS/TDE-85 system has a lower gel time compared to that of DDS/TDE-85 at the same temperature. The gel time of BOZ/DDS/TDE-85 below 130 °C was longer and the system was stable. When the abovementioned two systems were heated above 160 °C, the gel time decreased rapidly. At the temperature of 180 °C, the gel time was less than 10 min. The abovementioned data indicated that the curing rate of resin system is sensitive to the temperature at 130–180 °C.
 |
| Fig. 1 Gel time of neat DDS/TDE-85 and BOZ/DDS/TDE-85 systems. | |
The reaction process of epoxy resin system is quite complex. It is known that the curing rate, time and temperature are the main factors of curing process.26 With the aid of DSC curves, the study of the curing process can be simplified significantly. Table S1† shows the temperatures of characteristic peaks according to the DSC curves presented in Fig. S3(a)† at a heating rate (β) of 5, 10 and 15 °C min−1. Fig. S3(a)† shows that the values of Ti, Tp and Tf (where Ti is the initial reaction temperature, Tp is the peak temperature, and Tf is the final temperature) increase with increasing scanning rate. This phenomenon was due to the increased heat generated by per unit time with the increase in heating rate.
From the scatter plot obtained by T (T is Ti, Tp, Tf) versus β, the fitting curves can be obtained, as shown in Fig. S3(b).† In general, the gel temperature (Tgel), curing temperature (Tcure) and post-treatment temperature (Ttreat) can be deduced by the T–β fitting curves when β is extrapolated to zero thus removing the influence of the heating rate on the curing temperature.27 Tgel = 105 °C, Tcure = 154 °C and Ttreat = 228 °C were deduced from the intercept of T–β extrapolating curves. Combining the gelation time and T–β fitting curves, the curing process of BOZ/DDS/TDE-85 systems was determined as 130 °C/2 h + 150 °C/2 h + 180 °C/2 h.
3.4 Non-isothermal curing reaction kinetics
The curing reaction of thermosetting resins is exothermic and the curing reaction degree is a direct ratio to the reaction heat. As the apparent activation energy (Ea) reflects the difficulty level of the curing reaction intuitively, it is necessary to investigate the kinetic parameters of curing reaction, such as Ea and frequency factor A, which are important to research the relationship between the structure and properties of thermosetting resins.28 In general, the research on kinetic reaction is mainly conducted by non-isothermal and isothermal methods.29–31 Nevertheless, the non-isothermal method is widely accepted for the advantages of no knowledge of reaction mechanism required ahead of schedule.32 In this study, the DSC tests of BOZ/DDS/TDE-85 systems blends were performed at the scanning rate of 5, 10, 15 and 20 °C min−1. The kinetic parameters, such as Ea and A, were obtained with the aid of Kissinger's and Flynn–Wall–Ozawa methods.
Kissinger's method33. The dynamic model of thermosetting resins can be divided into macro and micro model in essence.34 The macro level model proposed by Arrhenius and Van't Hoff in the 19th century has been used widely, which is a semi-empirical model applicable to the curing reaction of thermosetting resins and not refer to the chemical ratio of the systems. The equations of this model are as follows:35 |
 | (3) |
|
 | (4) |
where T is the absolute temperature, α is the curing degree, R is ideal gas constant, Ea is the apparent activation energy, A is the frequency factor, β is the heating rate; f(α) is the differential conversion function, and k(T) is a temperature-dependent reaction rate constant.Combining eqn (3) with (4), eqn (5) was obtained as follows:
|
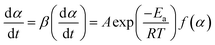 | (5) |
In the condition of d2α/dt2 = 0 (the maximum reaction rate), the fundamental equation using Kissinger method was deduced from eqn (5) as follows:
|
 | (6) |
where
α is the curing degree and
Tp is the peak temperature. The kinetic parameters (such as
Ea and
A) of the curing reaction can be calculated using different computing methods.
36–38 With the Kissinger method, a straight line is obtained by plotting ln(
β/
Tp2) against 1/
Tp, from which the value of
A (5.68 × 10
4) can be deduced by the intercept at the
Y-axis and
Ea (61.0 kJ mol
−1) from the slope, respectively.
Flynn–Wall–Ozawa method39. The integral equation by Flynn–Wall–Ozawa is usually shown as follows: |
 | (7) |
where the meanings of parameters, such as R, Tp, Ea and β, are the same as in eqn (3) and (4).A straight line fitting from the scatter data plotted by ln
β versus 1/Tp can be obtained. Ea (65.3 kJ mol−1) can be estimated from the slope of −1.052Ea/R. The average value of Ea obtained from the two methods can be seen as the activation energy (Ea = 63.15 kJ mol−1) of BOZ/DDS/TDE-85 systems. Fig. 2(a) shows the DSC curves of 5 phr BOZ/DDS/TDE-85 systems at four different heating rates, and the related parameters are listed in Table 2. Linear fitting plots of 5 phr BOZ/DDS/TDE-85 systems by Flynn–Wall–Ozawa and Kissinger's methods are shown in Fig. 2(b). The equation of the linear plot, Ea and A obtained from the fitting plots are listed in Table S2.† The results of Ea deduced by these two methods have a little difference. The curing process of thermosetting resins mainly includes two processes, one is the chemical reaction occurring ahead of the gel and the other is the dispersion process. Therefore, the modification of the current kinetic equation is very necessary if accurate kinetic parameters are needed. After evaluating the value of Ea, the relationship between the reaction order n and β can be given as the following equation:40
|
 | (8) |
where
n is the reaction order, and the other parameters are the same as the equation of Kissinger's. When
Ea/
nR is much larger than 2
Tp, 2
Tp can be ignored.
Fig. 2(b) shows a plot obtained from ln
β versus 1/
Tp and from the slope of the fitting curve; the value of
n can be derived directly. The linear fitting equation is as follows:
|
ln β = −8269 × (1/Tp) + 16.34
| (9) |
 |
| Fig. 2 (a) DSC curves of BOZ/DDS/TDE-85 systems at different scanning rates and (b) Kissinger's and Ozawa plot for curing of TDE-85/DDS with 5 phr BOZ. | |
Table 2 Curing kinetic parameters obtained from DSC analysis of BOZ/DDS/TDE-85 systems
β |
Tp/K |
−ln(β/Tp2)/(K−1 s−1) |
ln β/(K s−1) |
103 Tp−1/K−1 |
K min−1 |
K s−1 |
5 |
0.083 |
439.5 |
14.66 |
−2.489 |
2.275 |
10 |
0.167 |
455.5 |
14.03 |
−1.790 |
2.195 |
15 |
0.250 |
466.0 |
13.67 |
−1.386 |
2.146 |
20 |
0.333 |
476.2 |
13.43 |
−1.100 |
2.100 |
Combining eqn (8) with (9), the reaction order n is derived as 0.92. The kinetics equation of the curing reaction of the BOZ/DDS/TDE-85 systems is obtained as follows:
|
 | (10) |
The abovementioned results show that BOZ/DDS/TDE-85 systems have a lower Ea value and the reaction is first order.
3.5 Curing mechanism
To speculate the curing mechanism, it is necessary to observe the changes in groups during the curing process. Fig. 3 shows the FTIR spectrum of 5 phr BOZ/DDS/TDE-85 systems under a sequential cure condition. The intensity of the benzene ring absorption peak at 1500 cm−1 did not change with the progress of curing reaction. At the initial reaction stage from (A) to (C), the peak intensity of oxazine ring at 941 cm−1 was reduced gradually, and the phenolic hydroxyl peak appeared at 1230 cm−1, and the peak at 908 cm−1 for the epoxy group remained almost unchanged. The ring opening of oxazine ring occurred at about 200 °C, as the active hydrogen on amino group catalyzed oxazine ring opening at this stage. With increasing time and temperature (from D to E), the absorption peak of oxazine ring almost disappeared and the intensity of absorption peak for epoxy group weakened gradually. In addition, the secondary hydroxyl group peak appeared at 1100 cm−1, indicating that curing reaction mainly occurred in ring opening of epoxy group at this stage. At the last stage (F), the absorption peak of oxazine ring disappeared and the peak of epoxy group became very weak (but did not disappear because the epoxy group connecting to the alicyclic is difficult to open), indicating that the curing reaction was almost complete. The proposed reaction mechanism of BOZ/DDS/TDE-85 systems has been illustrated in Fig. S4† as follows:
 |
| Fig. 3 FTIR spectra of BOZ/DDS/TDE-85 systems in different curing stages. (A) un-curing, (B) pre-polymer, (C) 120 °C/1 h, (D) 120 °C/2 h, (E) 120 °C/2 h + 150 °C/2 h and (F) 120 °C/2 h + 150 °C/2 h + 180 °C/2 h, respectively. | |
3.6 Improvement of curing process
Fig. 4 shows the DSC curves of the neat BOZ, DDS/TDE-85 and BOZ/DDS/TDE-85 systems at a scanning rate of 10 °C min−1. The exothermic peak temperature of BOZ self-curing and TDE-85/DDS resin systems was 222.6 and 210.5 °C, respectively. Compared to the system of BOZ and TDE-85/DDS, the peak temperature of BOZ/TDE-85/DDS system (182.5 °C) was 28 and 40.1 °C lower than that of the TDE-85/DDS and neat BOZ system, respectively. The curing temperature is an important parameter during the curing process. The abovementioned data indicates that the addition of BOZ has optimized the curing process significantly.
 |
| Fig. 4 DSC curves of BOZ, DDS/TDE-85 and BOZ/DDS/TDE-85 system at the same scanning rate (10 °C min−1). | |
3.7 Mechanical and thermal properties
Tensile and compressive stresses generated by the three point bending test are similar to the stresses that exist in the real life applications of a composite.41 Fig. 5 shows the flexural, impact and compressive strength of different BOZ/DDS/TDE-85 systems. As the content of BOZ increased from 3 to 5 phr, the mechanical properties and HDT of DDS/TDE-85 systems increased first and then decreased. However, the properties of all the systems modified by BOZ were higher than that of the neat DDS/TDE-85. The maximum values of impact strength (38.44 kJ m−2) and HDT (172.2 °C) were obtained at 5 phr BOZ and flexural strength (207.4 MPa) and compressive strength (169.6 MPa) were obtained at 7 phr BOZ, which were increased by 43.4%, 11.5 °C, 13.1%, and 8.5%, respectively, compared to the properties of neat DDS/TDE-85. Table 3 shows the properties of the BOZ/DDS/TDE-85 systems with different BOZ contents. In general, the backbone of the molecular chain has tremendous effect on the strength of final products. The strength can be improved obviously with heterocyclic groups and a moderate crosslinking. Fig. S5† shows the DSC curves for the BOZ/DDS/TDE-85 systems with different contents of BOZ. With the addition of 5 phr BOZ, the maximum Tg values (183.0 °C) of BOZ/DDS/TDE-85 systems were obtained, which improved 8.1% compared with Tg (169.3 °C) of neat DDS/TDE-85 systems. This behavior was consistent with HDT results. The increase in a certain amount of rigid benzene in the BOZ structure generated higher HDT and Tg of BOZ/DDS/TDE-85 systems. The curing reactions of BOZ, DDS and TDE-85 are complex. It has been reported that DDS can cause a ring opening polymerization reaction with BOZ and epoxy resins, producing reactive groups, such as secondary amino group, phenolic hydroxyl, and alcoholic hydroxyl. The intermediate products produced by BOZ and epoxy resin can further react with the other components. From Fig. 4 and S4,† it can be noted that the reaction of BOZ, DDS and TDE-85 systems may occur between BOZ and DDS first. Under the promotion of tertiary amine located on the Minnich structure, the epoxy group can react with phenolic hydroxyl generated by the oxazine ring opening. It is speculated that the generation of the C–O–C structure makes the polymer chain more flexible. The C–O–C structure can also increase the chemical junction and a suitable amount of BOZ content can improve the overall performance. When the content of BOZ was lower than 5 phr, a few chemical junctions were produced that were insufficient for a complete curing reaction. When the BOZ content was more than 7 phr, the super abundant chemical junctions produced by the C–O–C structure may lead to a higher crosslinking density of the network structure formed in BOZ/DDS/TDE-85 systems, decreasing the overall properties to some extent.
 |
| Fig. 5 Mechanical and thermal properties of DDS/TDE-85 with different BOZ contents: (a) impact strength; (b) flexural strength; (c) compressive strength and (d) HDT. | |
Table 3 Mechanical and thermal properties of different BOZ/DDS/TDE-85 systems
Content of BOZ/phr |
Impact strength/kJ m−2 |
Flexural strength/MPa |
Flexural modulus/GPa |
Compressive strength/MPa |
Compressive modulus/GPa |
HDT/°C |
0 |
26.81 |
183.4 |
3.96 |
158.7 |
3.01 |
160.5 |
3 |
36.21 |
194.3 |
3.89 |
163.1 |
3.17 |
165.2 |
5 |
38.44 |
204.9 |
4.08 |
167.2 |
3.36 |
172.2 |
7 |
37.20 |
207.4 |
4.15 |
169.6 |
3.05 |
170.1 |
10 |
34.74 |
189.6 |
4.06 |
164.6 |
3.13 |
169.0 |
15 |
32.78 |
182.5 |
4.05 |
161.8 |
3.10 |
168.3 |
The effects of different contents of BOZ on DDS/TDE-85 resin systems can be observed by the surface morphology of impact fracture. Fig. 6 shows a SEM image of the impact fracture morphology for both of the neat DDS/TDE-85 and BOZ/DDS/TDE-85 systems with 5 phr BOZ contents. Fig. 6(a) shows that the fracture surface of the neat DDS/TDE-85 is smooth and has a single crack direction, indicating a typical brittle fracture. After the addition of 5 phr BOZ, the fractured surface showed tough dimples and the cracks propagated in different directions forming branching phenomena conducive to concentrated massive elastic stored energy. All the abovementioned descriptions have been revealed in Fig. 6(b), indicating that the addition of BOZ has enhanced the toughness of DDS/TDE-85 systems to a great extent.
 |
| Fig. 6 Effect of the BOZ content on the morphology of an impact fractured surface with BOZ content: (a) 0 phr and (b) 5 phr. | |
3.8 Thermal stability of BOZ/DDS/TDE-85 systems
To investigate the heat stability, TGA tests of TDE-85 cured with DDS and different amounts of BOZ were performed under nitrogen atmosphere and shown in Fig. 7. It can be seen in Fig. 7 and Table S3† that the char yield of BOZ/DDS/TDE-85 systems at 600 °C increased from 20.8% to 24.7% with increasing BOZ content increased from 0 to 7 phr, whereas the degradation temperature at 5% and 10% mass loss (T5%, T10%) showed little change. The abovementioned results indicated that the addition of BOZ improved the thermal stability of DDS/TDE-85 systems to some extent. When the temperature was below T5%, the weight loss of the BOZ/DDS/TDE-85 systems was mainly due to the release of small molecules produced during the polymerization reactions. When the temperature increased up to T10%, the discharge of gaseous molecules led to the mass loss of the system and the network structure of the cured resin changed to a more compact structure. At a higher temperature, the cured resin decomposed quickly and the char yield of BOZ/DDS/TDE-85 systems containing 7 phr BOZ was 24.7% at 600 °C. The thermal stability improved mainly due to the condensed aromatic rings in the special structure of BOZ and the increased crosslinking density caused by oxazine ring opening.
 |
| Fig. 7 TGA curves of DDS/TDE-85 resin systems with different content of BOZ. | |
The HDT of the 5 phr BOZ/DDS/TDE-85 systems disposed at different times under 200 °C are listed in Fig. S6.† With the prolonged time, HDT showed a growing trend due to the post-cure, indicating that the resin system containing BOZ has good thermal stability.
3.9 Water absorption
When a cured epoxy resin absorbs moisture, the mechanical properties reduce and the Tg will be lowered in most of instances. Moreover, both the service life and the insulation level will be reduced.42,43 It can be seen from Fig. 8(a) and (b) that the water absorption decreased both at room temperature and 50 °C with increasing BOZ contents. The water absorption rate is high at the initial stage and slows down after 10 d. The saturated water absorption of neat DDS/TDE-85 systems is 2.29%, whereas it becomes 1.48% for the BOZ/DDS/TDE-85 systems with the addition of 7 phr BOZ content at room temperature. It was mainly because of the high crosslinking density caused by BOZ, which depressed the chain motion in the cured resin system. The water absorption rate is decided primarily by the free volume and polar groups. In the early stage of water absorption, the water molecules infiltrate the area of low crosslinking density, which has larger free volume, leading to an easy entrance of water molecules in a short period of time. Thereafter, it begins to enter in a high crosslinking density area but very slowly as the permeating rate of water molecules become slow due to the compact crosslinking network and the equilibrium is reached very soon. At a high temperature, the groups on the backbone of the polymer move more easily, leading to a larger space in molecular chains, resulting in higher water sorption at 50 °C than that at room temperature.
 |
| Fig. 8 Water absorption of DDS/TDE-85 with different contents of BOZ: (a) at room temperature (∼25 °C) and (b) dipped in water at 50 °C. | |
4. Conclusions
In this study, a high-performance resin system with good thermal, mechanical properties and lower water absorption was prepared by the addition of BOZ to DDS/TDE-85 epoxy system. DSC analysis indicated that the addition of BOZ decreased the curing temperature by 28 °C compared to that of the neat DDS/TDE-85. Kissinger's, Flynn–Wall–Ozawa and Crane methods were adopted for investigating the curing kinetic of BOZ/DDS/TDE-85 systems. The results showed that the apparent Ea, A and n were 63.15 kJ mol−1, 5.68 × 104 and 0.92, respectively. In addition, TGA further verified the thermal stability of the final products, indicating that the char yield of the products containing 7 phr BOZ was 24.7% higher than that of the neat DDS/TDE-85 system. SEM showed that the BOZ/DDS/TDE-85 systems had a typical characteristic of ductile fracture. The BOZ/DDS/TDE-85 system blends can be used as the matrix for high performance composite materials reinforced by carbon or glass fibers, thereby, improving the overall performance of structural materials.
Acknowledgements
The authors acknowledge the financial support from the (CX201627) Innovation Foundation for Doctor Dissertation of Northwestern Polytechnical University.
References
- N. Hameed, P. Sreekumar, B. Francis, W. Yang and S. Thomas, Composites, Part A, 2007, 38, 2422–2432 CrossRef
. - F.-L. Jin, S.-Y. Lee and S.-J. Park, Carbon letters, 2013, 14, 76–88 CrossRef
. - F.-L. Jin, X. Li and S.-J. Park, J. Ind. Eng. Chem., 2015, 29, 1–11 CrossRef CAS
. - Y. Zhou, L. Li, Y. Chen, H. Zou and M. Liang, RSC Adv., 2015, 5, 98472–98481 RSC
. - Z.-H. Li, Y.-P. Ke, D.-Y. Ren and Z.-Q. Zheng, J. Cent. South Univ. Technol., 2007, 14, 753–758 CrossRef CAS
. - Z.-H. Li, Y.-P. Huang, D.-Y. Ren and Z.-Q. Zheng, J. Cent. South Univ. Technol., 2008, 15, 305–308 CrossRef CAS
. - H. Kimura, A. Matsumoto, K. Hasegawa, K. Ohtsuka and A. Fukuda, J. Appl. Polym. Sci., 1998, 68, 1903–1910 CrossRef CAS
. - S. W. Kuo and W. C. Liu, J. Appl. Polym. Sci., 2010, 117, 3121–3127 CAS
. - L. Dumas, L. Bonnaud, M. Olivier, M. Poorteman and P. Dubois, J. Mater. Chem. A, 2015, 3, 6012–6018 CAS
. - A. Chernykh, T. Agag and H. Ishida, Polymer, 2009, 50, 382–390 CrossRef CAS
. - Y. Liu, Z. Hao, S. Lv, J. Huang, C. Liao and M. Run, Polymer, 2015, 57, 29–38 CrossRef CAS
. - M. W. Wang, R. J. Jeng and C. H. Lin, Macromolecules, 2015, 48, 530–535 CrossRef CAS
. - Y.-X. Wang and H. Ishida, Macromolecules, 2000, 33, 2839–2847 CrossRef CAS
. - K. Zhang and H. Ishida, Polymer, 2015, 66, 240–248 CrossRef CAS
. - M. G. Mohamed, K.-C. Hsu and S.-W. Kuo, Polym. Chem., 2015, 6, 2423–2433 RSC
. - Y. Wang, K. Kou, G. Wu, A. Feng and L. Zhuo, RSC Adv., 2015, 5, 58821–58831 RSC
. - N. Ghosh, B. Kiskan and Y. Yagci, Prog. Polym. Sci., 2007, 32, 1344–1391 CrossRef CAS
. - H. Ishida and C. M. Krus, Macromolecules, 1998, 31, 2409–2418 CrossRef CAS
. - X. Liu and Y. Gu, J. Appl. Polym. Sci., 2002, 84, 1107–1113 CrossRef CAS
. - H. Ishida and D. J. Allen, Polymer, 1996, 37, 4487–4495 CrossRef CAS
. - K. Kou, M. Chao, L. Zhuo and J. Zhang, J. Wuhan Univ. Technol., Mater. Sci. Ed., 2013, 28, 261–264 CrossRef
. - Z.-H. Li, Z.-Q. Zheng, D.-Y. Ren and Y.-P. Huang, J. Cent. South Univ. Technol., 2007, 14, 296–300 CrossRef CAS
. - Y. Liu, C. Liao, Z. Hao, X. Luo, S. Jing and M. Run, React. Funct. Polym., 2014, 75, 9–15 CrossRef CAS
. - Z. L. G. Li and L. Gi, Epoxy adhesives and application technology, Chemical industry press, 2007, pp. 44–45 Search PubMed
. - H. Jiang, R. Wang, S. Farhan, M. Wang and S. Zheng, High Perform. Polym., 2016, 28, 669–681 CrossRef
. - H. Jiang, R. Wang, S. Farhan and S. Zheng, J. Appl. Polym. Sci., 2015, 132, 41829 Search PubMed
. - R. Bindu, C. Nair and K. Ninan, J. Polym. Sci., Polym. Chem. Ed., 2000, 38, 641–652 CrossRef CAS
. - J. Hu, J. Shan, J. Zhao and Z. Tong, Thermochim. Acta, 2015, 606, 58–65 CrossRef CAS
. - J. H. Flynn and L. A. Wall, J. Polym. Sci., Polym. Lett. Ed., 1966, 4, 323–328 CrossRef CAS
. - H. L. Friedman, J. Appl. Polym. Sci.: Appl. Polym. Symp., 1964, 6, 183–195 CrossRef
. - T. Hsieh and A. Su, J. Appl. Polym. Sci., 1990, 41, 1271–1280 CrossRef CAS
. - C. Jubsilp, K. Punson, T. Takeichi and S. Rimdusit, Polym. Degrad. Stab., 2010, 95, 918–924 CrossRef CAS
. - H. E. Kissinger, Anal. Chem., 1957, 29, 1702–1706 CrossRef CAS
. - K. de la Caba, P. Guerrero, I. Mondragon and J. M. Kenny, Polym. Int., 1998, 45, 333–338 CrossRef
. - S. Vyazovkin and N. Sbirrazzuoli, Macromol. Chem. Phys., 1999, 200, 2294–2303 CrossRef CAS
. - R. Hardis, J. L. Jessop, F. E. Peters and M. R. Kessler, Composites, Part A, 2013, 49, 100–108 CrossRef CAS
. - J. Mijovic and S. Andjelic, Macromolecules, 1996, 29, 239–246 CrossRef CAS
. - R. Seifi and M. Hojjati, J. Compos. Mater., 2005, 39, 1027–1039 CrossRef CAS
. - T. Ozawa, Bull. Chem. Soc. Jpn., 1965, 38, 1881–1886 CrossRef CAS
. - L. Crane, P. Dynes and D. Kaelble, J. Polym. Sci., Polym. Lett. Ed., 1973, 11, 533–540 CrossRef CAS
. - M. Naebe, J. Wang, A. Amini, H. Khayyam, N. Hameed, L. H. Li, Y. Chen and B. Fox, Sci. Rep., 2014, 4, 4375 Search PubMed
. - D. N. Dang, S. Cohendoz, S. Mallarino, X. Feaugas and S. Touzain, J. Appl. Polym. Sci., 2013, 129, 2451–2463 CrossRef CAS
. - S. K. Karad, D. Attwood and F. R. Jones, Composites, Part A, 2002, 33, 1665–1675 CrossRef
.
Footnote |
† Electronic supplementary information (ESI) available. See DOI: 10.1039/c6ra15126d |
|
This journal is © The Royal Society of Chemistry 2016 |
Click here to see how this site uses Cookies. View our privacy policy here.