DOI:
10.1039/C6RA13830F
(Communication)
RSC Adv., 2016,
6, 67992-67996
Two-step cycle for producing multiple anodic aluminum oxide (AAO) films with increasing long-range order†
Received
27th May 2016
, Accepted 9th July 2016
First published on 11th July 2016
Abstract
Nanoporous anodic aluminum oxide (AAO) membranes are being used for an increasing number of applications. However, the original two-step anodization method in which the first anodization is sacrificial to pre-pattern the second is still widely used to produce them. This method provides relatively low throughput and material utilization as half of the films are discarded. An alternative scheme that relies on alternating anodization and cathodic delamination is demonstrated that allows for the fabrication of several AAO films with only one sacrificial layer thus greatly improving total aluminum to alumina yield. The thickness for which the cathodic delamination performs best to yield full, unbroken AAO sheets is around 85 μm. Additionally, an image analysis method is used to quantify the degree of long-range ordering of the unit cells in the AAO films which was found to increase with each successive iteration of the fabrication cycle.
Introduction and motivation
Porous nanostructured alumina films grown by aluminum anodization have been studied for several decades.1 Because these anodic aluminum oxide (AAO) films have a well-ordered nanoscale structure and are relative easy to fabricate, their application has grown tremendously with wide ranging uses such as templates for making nanowires or nanoholes,2–8 membrane filtration with further functionalization to fine tune their size, chemical, or biological selectivity,9–12 fabricating magnetic nanomaterials,4,13 optical devices,14,15 supports for lipid bilayers for making spectroscopic measurements,16,17 and other biomedical applications.12,18–21 A recent review covers the growth and some applications of AAO to templated nanostructures.22
AAOs are commonly produced by anodizing a piece of aluminum in an oxalic acid electrolyte. A two-step process, in which the first oxide film is selectively dissolved, is widely used because the second film has a much more regular structure due to the pre-patterning of the substrate by the first anodization.6,13,21,23–33 The microstructure on the metal surface prior to anodization affects the ordering of the subsequent oxide film, and it has been shown that using a lithographically produced stamp to pre-pattern the aluminum results in highly ordered AAOs.5,34 When the desired AAO film growth is complete, it is still attached to the aluminum substrate from which it was grown. The original published methods for removing the alumina film from its substrate involved selective dissolution of the aluminum in HgCl2 or CuCl2 solution.2,6,24,35 Due to the inefficient use of aluminum and the use of toxic metals, other methods for alumina delamination were developed that utilized higher potential anodic pulses to remove the barrier layer23,31–33 or further anodization in an electrolyte to etch away the surface of the underlying aluminum.24 A drawback to these methods is that they distort the metal microstructure from its steady-state growth conditions. Cathodic delamination, on the other hand, relies on the build-up of pressure between the metal and the oxide as protons are reduced to hydrogen gas. This method has been reported as a way of reducing the number of processing steps and chemical baths used.23 If the delamination step is carried out in the original electrolyte bath, however, the build-up of Al3+ formed during the anodization leads to redeposition of Al0, which produces the undesirable result of filling in the patterned microstructure. Recently, cathodic delamination has been demonstrated as a means to produce multiple AAO films from a single starting sheet of Al.27 The process reported in that study utilized a sacrificial first anodization before each useable film was created.
Our alternative process proposed in Scheme 1 allows for a higher yield of AAOs to be produced from a single sheet of aluminum since only one initial anodization step is required. This process involves multiple anodizations on a single piece of aluminum with alternating cathodic delamination to remove each film in a separate bath of 0.1 mol L−1 nitric acid, which preserves the pre-patterning on the aluminum. Because the microstructure is preserved, no additional steps are necessary before proceeding to the subsequent anodization. This two-step cycle can be repeated until the aluminum substrate is consumed. The reasons for using a separate nitric acid bath are threefold. First, using a separate bath avoids the re-deposition of aluminum that accompanies use of the original anodization bath. Second, the delamination mechanism requires a source of protons as the precursor to the hydrogen bubble, which the nitric acid bath provides. And third, both aluminum and alumina are stable in nitric acid.36
A beneficial feature of this scheme is that it delaminates the alumina with the barrier layer intact, unlike the anodic voltage pulse schemes.23,24,31,32 The barrier layer can be left in place for applications such as creating nanoscopic vesicles20,37 or a variety of barrier layer removal techniques can be used to obtain open, through-hole pores. Barrier layer removal techniques include wet etching with phosphoric acid,28,34 floating the barrier layer on top of a basic solution,27 dry etching,30 or focused ion beam milling.29
Experimental
High purity, 99.999% aluminum sheets were purchased with dimensions 50 mm × 50 mm × 1 mm and were sheared to 25 mm × 50 mm × 1 mm. Because the shearing warps and bends the aluminum near the tooling marks, the aluminum pieces were repressed to flat in a vice. All electrochemical processes were run with two 20 V power supplies wired in series, which is necessary to achieve voltages greater than 35 V. Further pretreatment of the aluminum pieces consisted of sonicating in acetone for several minutes, followed by electropolishing in a mixture of 800 mL of ethanol mixed with 200 mL of perchloric acid at 10 V (45 mA cm−2 to 115 mA cm−2) for two minutes total with the aluminum sheet being about two-thirds of the way submerged in the solution and being rotated by 90° every 30 s to ensure more even polishing of the surface. Following this procedure, the aluminum was thoroughly rinsed in distilled water. The final aluminum piece had a mirror-like shine. For both electropolishing and alumina film growth, a copper wire coil was used as the cathode, the solution was gently stirred with a stir bar at 1.7 Hz, and a 1 L water jacketed beaker and recirculating water bath were used to hold the solution at 4 °C. Alumina film growth was performed in 0.3 mol L−1 oxalic acid, made from oxalic acid and distilled water, at 40 V (1.9 mA cm−2 at steady state) for between 8 h to 32 h. In order to build statistics, three aluminum sheets were anodized simultaneously in the same bath. The pieces were symmetrically arranged around the cathode in the center of the bath. Between successive rounds of alumina growth, a fresh batch of oxalic acid solution was prepared to avoid changing the reaction kinetics due to Al3+ build-up in the electrolyte. Additionally, a thin layer of silicone oil was floated on top of the oxalic acid solution, which prevented corrosion of the aluminum sheet at the solution/air interface. Following completion of an anodization step, the sheets were rinsed with distilled water.
Cathodic delamination was performed in 1 L of 0.1 mol L−1 nitric acid at room temperature at 30 V using Pt foil as the anode. Before delamination occurs, and depending on the alumina thickness, the current ranged from 1 mA cm−2 to 4 mA cm−2, and a few small bubbles could be seen escaping through the alumina film. Depending on the thickness of the oxide film, an audible popping was heard as the alumina starts to delaminate 30 s to 90 s after the voltage had been applied. After delamination occurs and the oxide film cracks, the acid solution is able to reach the aluminum uninhibited and the current jumps up to 50 mA cm−2 to 120 mA cm−2 at which point the power supply was turned off. The alumina film was rinsed with distilled water, dried at 120 °C and pieces were broken off and sputter coated with 2 nm of Pt for scanning electron microscopy (SEM) analysis. For the thinner alumina samples that cracked and did not fully delaminate, the residual alumina was dissolved in a phosphoric acid/sodium dichromate bath at 60 °C for a few minutes to yield a clean metal surface before the next anodization.
Results & discussion
Voltage used for delamination
The mechanism of cathodic delamination relies on the reduction of protons to hydrogen gas at the aluminum/alumina interface. The barrier layer of alumina is permeable to ionic species, which is necessary for the alumina growth4,38 but also allows protons to diffuse through from the bulk acidic electrolyte to the aluminum surface. The pressure from the hydrogen gas bubble pushes the aluminum and alumina apart. Different voltages were tried for the cathodic delamination step before settling on 30 V. Voltages below 30 V draw less current and produce hydrogen at a slower rate with some or all of it escaping through the barrier layer. If the rate of hydrogen escaping through the membrane is comparable to the rate of its production, the pressure does not build up at the metal/oxide interface and delamination does not occur. On the other hand, voltages above 30 V produce the hydrogen more rapidly and build up pressure faster, which can lead to alumina film cracking instead of delamination across the whole surface. Three quarters of the voltage used for the anodization provides a good balance between these two extremes and was tested on some other AAO films grown at both 10 V and 20 V. This ratio is similar to the slightly lower voltage ratios of 0.60 to 0.68 used by Hong et al.27
Thickness dependence of delamination success
Five iterations of anodization were performed, each for a different amount of time in order to produce AAO films with varying thicknesses. A plot of AAO film thickness versus anodization time is shown in the ESI, Fig. S1.† Two observed trends are that the current prior to delamination decreases and the amount of time before delamination increases with increasing film thickness. Both trends are due to the diffusion of protons through the narrow pores, with the thicker films providing more resistance to the flux of protons to the metal surface from the bulk solution than their thinner counterparts.39 During the delamination process, the pressure of hydrogen builds up between the aluminum and alumina film until it forces the oxide off. For the thinner, weaker films this pressure bubble causes the film to brittle fracture in many places across the face yielding pieces smaller than 1 cm2. Depending on the application, the smaller, fractured pieces could still be used, or machined into a more desirable shape. Alternatively, to reduce the chance of fracture for the thinner films, a smaller starting piece of aluminum could be used, or possibly an additional supporting layer that is ionically conducting could be added on top before the delamination step to increase its mechanical strength. The fourth iteration alumina films were approximately 85 μm thick and each face delaminated in a full, unbroken sheet. The thickest alumina films were approximately 102 μm thick and were strong enough that the pressure bubble was unable to break off all of the faces cleanly. Some of these thick films had fractures across the film, although to a lesser degree than the thinner films. It may be possible to extend the thickness range in which the alumina film delaminates in one piece by selectively anodizing the face23,35 so that the oxide film does not wrap around the aluminum substrate.
Microstructures of the aluminum and alumina
The alumina films and the aluminum surface were characterized by SEM after each iteration and the resulting microstructures are shown in Fig. 1. The top surface of the alumina film after the first anodization (uppermost left corner) does not have a well-defined periodic structure which is why this layer is usually discarded. For the second and subsequent iterations the pore size remains constant as shown in the ESI, Fig. S8.† The bottom of the first film and the aluminum surface exhibit the characteristic honeycomb pattern. By preserving this microstructure on the aluminum, the sequential iterations have better ordering than the previous, due to further evolution of the self-ordering processes described previously.1,40,41 This trend can be easily distinguished in the larger images shown in the ESI in Fig. S6† and in the inlays in Fig. 2.
 |
| Fig. 1 SEM micrographs showing the microstructures of the top and bottom of the alumina film and the aluminum substrate after each iteration of anodization. The scale bar for the top surface of the alumina after the first iteration is 200 nm (top left corner). All other micrographs are scaled to the 1 μm scale bar shown in the bottom right. | |
 |
| Fig. 2 Plot of characteristic domain size versus total anodization time. Characteristic domain size comes from the exponential fit to the domain size histograms; uncertainties are the standard error. The inlay on the upper left shows the domains highlighted by orientation overlaid on the bottom side SEM image after the first iteration. The inlay on the lower right shows the same after the fifth iteration. The scale bar in both inlays is 1 μm. | |
Quantification of long-range ordering
In order to characterize the long-range ordering of the unit cells after each iteration, large area scanning electron microscopy (SEM) images were obtained and analyzed to find the regions with similar orientations that are defined as a domain. The analysis starts with identification of unit cells followed by Delaunay triangulation similar to previously described methods.42–44 Details of the analysis technique can be found in the ESI.† Hundreds of domains were characterized from the alumina films from each iteration. The domains within each iteration have an exponential size distribution so that fitting of the domain size histogram to y = Ae−x/k, determines the characteristic domain size, k. These data are shown in the ESI in Fig. S7.† From this analysis, it is clear that the characteristic domain size increases after each iteration as the total anodization time increases (Fig. 2). This trend is possible because the patterning in the aluminum is preserved during the delamination process. For the first few iterations, the trend is linear, and then the trend starts to plateau. This plateau could be due to the finite size of the SEM images used in the analysis; as the domain sizes grow, they are truncated by the edges of the image. Discarding the domains with edge boundaries from the analysis, however, significantly reduces the total number of domains for the later iterations and biases the distribution as large domains are more likely to be removed. The general trend is that there is a monotonic increase in domain size with each iteration, even if the characteristic domain size increase is not fully linear. This analysis method is an improvement in tracking this trend, which was reported previously by changing the time of the first sacrificial anodization but was reported in arbitrary units40 or required manually picking out individual domains by hand.41
Advantages of Scheme 1 over traditional methods for producing AAO
The traditional method for making an ordered AAO film involves growing a first, sacrificial alumina film that is dissolved selectively and keeping only the second alumina film.6,13,21,23–33 Obviously, to produce many AAO films, sacrificial dissolution of the first alumina film (grown for a long time) to obtain one highly ordered film is impractical. Our method depicted in Scheme 1 is beneficial because the sacrificial film is made once and is independent of the number of subsequent anodizations. Use of 1 mm thick aluminum sheets in our experiments limited the number of iterations we could perform because the aluminum became too thin and weak, making further alumina film growths impractical. By starting with a thicker piece of aluminum, however, this process could be extended for many more iterations. The process described by Hong et al.27 which is similar to ours, involves an additional etching step that removes the patterning on the aluminum, thus necessitating a sacrificial pre-anodization for each cycle. These extra steps prevent an increase in long range ordering with each cycle. In these respects, our method is advantageous because it does not require etching and sacrificial pre-anodization at each cycle, which also increases domain size after each iteration.
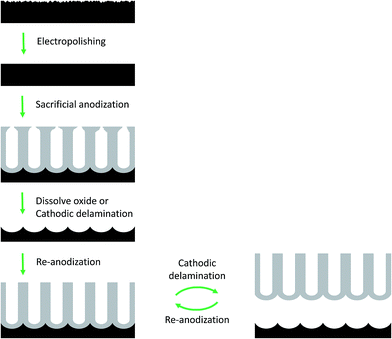 |
| Scheme 1 Diagram showing the proposed route to preserving and reusing the patterning on the aluminum after each anodization. Anodization is performed in an oxalic acid solution whereas cathodic delamination is done in a separate nitric acid bath. | |
Additional considerations and future possibilities
Although the anodizations for this work were performed under mild conditions, it is likely that this scheme could be combined with the faster growth associated with the hard anodization technique described by Lee et al.39 to increase the yield and speed of AAO production significantly. Additionally, if the degree of ordering is important, another possibility to further increase the long range ordering would be to anneal the Al sheet prior to anodization35 or to pre-pattern the aluminum with a lithographically produced stamp,5,34 neither or which was done in this study. Further, for the starting aluminium geometry used in this study, only the films that were around 85 μm thick delaminated in full, unbroken sheets, with the thinner and thicker films fracturing into smaller fragments during delamination. For applications requiring large area, thin alumina films, such as for dry etching masks, further optimization of the delamination process is required, possibly including the use of a temporary support layer.
Conclusions
A new method is demonstrated to produce many AAO films from a starting sheet of aluminum. This scheme utilizes cathodic delamination in a separate bath containing 0.1 mol L−1 nitric acid, which allows the alumina and aluminum to be separated without distorting the microstructure on the substrate. In order to get the full faces to delaminate in a single sheet, the alumina film thickness should be approximately 85 μm thick. Because of the preservation of the aluminum microstructure, only a single sacrificial anodization needs to be performed, regardless of the number of subsequent iterations. Finally, with each successive cycle, the long-range ordering of the unit cells in the AAO film increases, which is demonstrated by a quantitative image analysis method of large area SEM images.
References
- F. Keller, M. S. Hunter and D. L. Robinson, J. Electrochem. Soc., 1953, 100, 411–419 CrossRef CAS.
- H. Masuda and K. Fukuda, Science, 1995, 268, 1466–1468 CAS.
- F. Liu, J. Y. Lee and W. Zhou, J. Phys. Chem. B, 2004, 108, 17959–17963 CrossRef CAS.
- S. Shingubara, J. Nanopart. Res., 2003, 5, 17–30 CrossRef CAS.
- J. Zou, X. Qi, L. Tan and B. J. H. Stadler, Appl. Phys. Lett., 2006, 89, 093106 CrossRef.
- J. Zhang and G. Hong, J. Solid State Chem., 2004, 177, 1292–1296 CrossRef CAS.
- B. R. Martin, D. J. Dermody, B. D. Reiss, M. Fang, L. A. Lyon, M. J. Natan and T. E. Mallouk, Adv. Mater., 1999, 11, 1021–1025 CrossRef CAS.
- V. M. Cepak and C. R. Martin, Chem. Mater., 1999, 11, 1363–1367 CrossRef CAS.
- I. Vlassiouk, A. Krasnoslobodtsev, S. Smirnov and M. Germann, Langmuir, 2004, 20, 9913–9915 CrossRef CAS PubMed.
- L. Velleman, G. Triani, P. J. Evans, J. G. Shapter and D. Losic, Microporous Mesoporous Mater., 2009, 126, 87–94 CrossRef CAS.
- A. M. Md Jani, D. Losic and N. H. Voelcker, Prog. Mater. Sci., 2013, 58, 636–704 CrossRef CAS.
- M. E. Warkiani, A. A. S. Bhagat, B. L. Khoo, J. Han, C. T. Lim, H. Q. Gong and A. G. Fane, ACS Nano, 2013, 7, 1882–1904 CrossRef CAS PubMed.
- S. Thongmee, H. L. Pang, J. Ding and J. Y. Lin, J. Magn. Magn. Mater., 2009, 321, 2712–2716 CrossRef CAS.
- M. S. Akselrod, A. E. Akselrod, S. S. Orlov, S. Sanyal and T. H. Underwood, J. Fluoresc., 2003, 13, 503–511 CrossRef CAS.
- T. D. Lazzara, K. H. A. Lau, A. I. Abou-Kandil, A.-M. Caminade, J.-P. Majoral and W. Knoll, ACS Nano, 2010, 4, 3909–3920 CrossRef CAS PubMed.
- H. C. Gaede, K. M. Luckett, I. V. Polozov and K. Gawrisch, Langmuir, 2004, 20, 7711–7719 CrossRef CAS PubMed.
- O. Wattraint, A. Arnold, M. Auger, C. Bourdillon and C. Sarazin, Anal. Biochem., 2005, 336, 253–261 CrossRef CAS PubMed.
- S. P. Adiga, C. Jin, L. A. Curtiss, N. A. Monteiro-Riviere and R. J. Narayan, Wiley Interdiscip. Rev.: Nanomed. Nanobiotechnol., 2009, 1, 568–581 CrossRef CAS PubMed.
- J. M. Moon, D. Akin, Y. Xuan, P. D. Ye, P. Guo and R. Bashir, Biomed. Microdevices, 2009, 11, 135–142 CrossRef PubMed.
- H. Neubacher, I. Mey, C. Carnarius, T. D. Lazzara and C. Steinem, Langmuir, 2014, 30, 4767–4774 CrossRef CAS PubMed.
- G. E. J. Poinern, N. Ali and D. Fawcett, Materials, 2011, 4, 487 CrossRef.
- W. Lee and S.-J. Park, Chem. Rev., 2014, 114, 7487–7556 CrossRef CAS PubMed.
- W. Chen, J.-S. Wu, J.-H. Yuan, X.-H. Xia and X.-H. Lin, J. Electroanal. Chem., 2007, 600, 257–264 CrossRef CAS.
- L. Gao, P. Wang, X. Wu, S. Yang and X. Song, J. Electroceram., 2008, 21, 791–794 CrossRef CAS.
- T. T. Xu, R. D. Piner and R. S. Ruoff, Langmuir, 2003, 19, 1443–1445 CrossRef CAS.
- M. Hideki and S. Masahiro, Jpn. J. Appl. Phys., 1996, 35, L126 Search PubMed.
- Y. K. Hong, B. H. Kim, D. I. Kim, D. H. Park and J. Joo, RSC Adv., 2015, 5, 26872–26877 RSC.
- M. Lillo and D. Losic, J. Membr. Sci., 2009, 327, 11–17 CrossRef CAS.
- M. Lillo and D. Losic, Mater. Lett., 2009, 63, 457–460 CrossRef CAS.
- T. Xu, G. Zangari and R. Metzger, Nano Lett., 2002, 2, 37–41 CrossRef CAS.
- J. H. Yuan, W. Chen, R. J. Hui, Y. L. Hu and X. H. Xia, Electrochim. Acta, 2006, 51, 4589–4595 CrossRef CAS.
- J. H. Yuan, F. Y. He, D. C. Sun and X. H. Xia, Chem. Mater., 2004, 16, 1841–1844 CrossRef CAS.
- S. Zhao, K. Chan, A. Yelon and T. Veres, Nanotechnology, 2007, 18, 245304 CrossRef.
- H. Masuda, H. Yamada, M. Satoh, H. Asoh, M. Nakao and T. Tamamura, Appl. Phys. Lett., 1997, 71, 2770 CrossRef CAS.
- O. Jessensky, F. Müller and U. Gösele, Appl. Phys. Lett., 1998, 72, 1173 CrossRef CAS.
- V. M. Petrusevski, M. Bukleski, M. Stojanovska and P. Hodder, Chemistry Education in New Zealand, 2011, 7–9 Search PubMed.
- T. D. Lazzara, C. Carnarius, M. Kocun, A. Janshoff and C. Steinem, ACS Nano, 2011, 5, 6935–6944 CrossRef CAS PubMed.
- J. P. O'Sullivan and G. C. Wood, Proc. R. Soc. London, Ser. A, 1970, 317, 511–543 CrossRef.
- W. Lee, R. Ji, U. Gosele and K. Nielsch, Nat. Mater., 2006, 5, 741–747 CrossRef CAS PubMed.
- S. Shingubara, O. Okino, Y. Sayama, H. Sakaue and T. Takahagi, Jpn. J. Appl. Phys., Part 1, 1997, 36, 7791–7795 CrossRef CAS.
- F. Li, L. Zhang and R. M. Metzger, Chem. Mater., 1998, 10, 2470–2480 CrossRef CAS.
- R. Hillebrand, F. Müller, K. Schwirn, W. Lee and M. Steinhart, ACS Nano, 2008, 2, 913–920 CrossRef CAS PubMed.
- L. Zaraska, W. J. Stępniowski, E. Ciepiela and G. D. Sulka, Thin Solid Films, 2013, 534, 155–161 CrossRef CAS.
- L. Zaraska, W. J. Stępniowski, M. Jaskuła and G. D. Sulka, Appl. Surf. Sci., 2014, 305, 650–657 CrossRef CAS.
Footnote |
† Electronic supplementary information (ESI) available. See DOI: 10.1039/c6ra13830f |
|
This journal is © The Royal Society of Chemistry 2016 |
Click here to see how this site uses Cookies. View our privacy policy here.