DOI:
10.1039/C6RA13237E
(Review Article)
RSC Adv., 2016,
6, 106964-106979
Microencapsulation: an emerging technique in the modern coating industry
Received
22nd May 2016
, Accepted 16th October 2016
First published on 25th October 2016
Abstract
The protection of a metal from corrosion is a topic of great interest, for which a variety of methods has been implemented in the past such as organic–inorganic protective coatings, the use of corrosion inhibitors, sol–gel coatings, self healing coatings etc. Out of these, self healing coating is an emerging and broad field that is categorised into three types; namely, microencapsulation, vascular based and intrinsic materials. Microencapsulation is an advanced and well established technique for corrosion protection of metals but still has not received adequate attention from industries to date. The main purpose of encapsulation is to control the release of active agent, when an external condition such as mechanical stress or energy triggers the microcapsules to break, rupture or melt. Along with corrosion inhibition, microencapsulation can be used to enhance other performance properties of coatings such as mechanical strength, impermeability, aesthetic appearance, UV resistance etc. Considering these advantages and the need for microencapsulation, in the present article we discuss the principles and morphologies of microcapsules, the purpose of microencapsulation, physical and chemical techniques of microencapsulation, healing mechanisms, applications and the latest developments in microencapsulation for the coating industry.
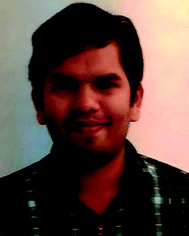 Kunal Wazarkar | Kunal Wazarkar Born in 1991, Kunal completed his Master's degree in the field of Surface Coating Technology from the Institute of Chemical Technology, Mumbai. He worked on flame retardant coatings for his Master's thesis under the guidance of Dr Anagha Sabnis. He joined Dr Sabnis's research group as a PhD research scholar in 2013. He is currently working on modification of bio based monomers for coating applications. Other areas of his research include flame retardant coatings, organic–organic and organic–inorganic hybrid coatings, polyurethane dispersions, and unsaturated polyester composites etc. |
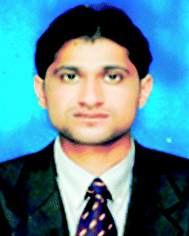 Deepak Patil | Deepak Patil Born in 1989, Deepak completed a Master's degree in technology in the field of surface coating technology from the Institute of Chemical Technology, Mumbai. He worked on anti-corrosive coating compositions for his Master's thesis under the guidance of Dr A. Sabnis. He was recently awarded a junior research fellowship and has joined Dr S. T Mhaske's research group as a Ph.D. candidate. His current areas of research include utilization of bio-based materials for synthesis of novel monomers and polymers for UV curable, fire protective, anti-corrosive and anti-microbial coatings. |
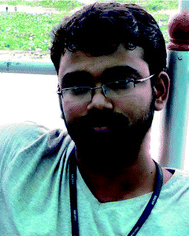 Ajay Rane | Ajay Rane He is a Doctoral Research Fellow at the Durban University of Technology, Durban, South Africa. He received his M. Tech in 2014 in Green Technology from the Institute of Chemical Technology (ICT), Mumbai, India under supervision of Dr Anagha Sabnis, Faculty of Polymer and Surface Engineering. His specialized areas of polymers which include Polymer blends, Fibre filled polymer composites, Particulate filled polymer composites and their morphological characterization, Ageing and degradation, Green Chemistry, Polymer Recycling. He has presented his research work in 9 International and National Conferences. He is author of few International and National Publications, and his 11 book chapters are accepted for Elsevier, John Wiley and Sons and Pan Stanford Publishers. Currently he is working in area of bionanocomposites for mass transit application with guidance of Professor Krishnan Kanny, South Africa and Professor Sabu Thomas, India and Dr Mohan Turup Pandurangan, South Africa as co-supervisors. |
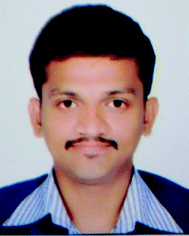 Dinesh Balgude | Dinesh Balgude Born in 1987, has completed a Doctorate of Philosophy in Technology in the field of Surface Coating Technology from the Institute of Chemical Technology, Mumbai. He worked on “Modifications of Renewable Resources for Coating Applications” for his Ph.D. thesis under the guidance of Dr A. S. Sabnis. He was awarded a Prime Minister's Fellowship by government of India for his doctoral research. His current areas of research include utilization of bio-based materials for coating application and exploration of these materials for cost effective paint formulations as per customer's requirements. He is also interested in the field of specialty coatings such as super-hydrophobic nano materials for textile, glass and wood substrates. |
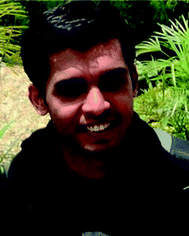 Mukesh Kathalewar | Mukesh Kathalewar Born in 1987, has completed his PhD in the field of Surface coating Technology last year under the guidance of Dr Sabnis from ICT, Mumbai. He has published 23 papers in international peer reviewed journals and 4 national papers. His areas of research include utilization of biobased materials for coating applications, recycling of polymer waste for synthesis of novel monomers and polymers, flame retardant coatings, emulsion polymers etc. |
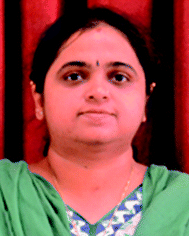 Anagha Sabnis | Anagha Sabnis Born in 1975, has done her Bachelor's, Master's and PhD in technology in the field of Surface Coating Technology at ICT, Mumbai. After gaining two years of industrial experience, she joined Dept. of Polymer and Surface Engineering as an assistant professor. She has 30 publications in well-known international peer reviewed journals with over 200 citations. She has guided 15 Master's and 2 PhD student so far and currently supervising 5 Master's and 2 PhD students. Her major research areas include synthesis of various resins including alkyd, epoxy, polyurethane etc., waterborne coatings, emulsion polymerization, flame retardant coatings, recycling of polymeric waste, non-isocyanate route for polyurethane synthesis etc. |
Introduction
Any material from plastic to metal will eventually fail if not maintained properly. Nowadays, metallic materials have been used in many engineering fields. However, the long term durability and reliability of materials are still problematic when they are used in structural applications.1 When exposed to harsh environments, these materials undergo corrosion and eventually fail. Traditionally, this problem is solved by inspection and replacing the damaged parts. However, this is a quite tedious, time consuming and expensive method.2 Recently, various protective coatings were developed, including organic–inorganic coatings and sol gel coatings to protect metal from corrosion.3,4 These protective coatings, during their service life, are always subjected to unexpected damages and crack formation through which corrosion occurs gradually. Corrosion of metals causes substantial financial losses and requires great efforts to control its impact.5 Therefore, it becomes necessary to develop a method by means of which this crack formation can be avoided or even if crack is formed, it should get healed automatically. For any material, crack formation is inevitable and the most appropriate solution is to heal the crack automatically and restore original coating properties. Inspired from biological systems that have inherent ability to repair damage via healing mechanisms,6,7 scientists and researchers have started working on developing such systems and call them “Self healing systems”. These systems have the ability to repair the damage caused due to mechanical stress or energy and to recover their functionality using resources inherently available to them.
In case of biological systems, healing mechanism includes three main processes viz., inflammatory response, cell proliferation and matrix remodelling. At first, damage that causes injury triggers the first response inflammation and blood clotting, after that matrix is deposited at the site of injury and finally matrix remodelling process to develop new tissue. Similar to this, synthetic systems are developed with the advantage that the healing process is quite faster than that of biological systems.8,9 Till now, self healing process is explained by three approaches namely capsule based, vascular based and intrinsic materials.10
Vascular based approach uses vessels to transfer healing agent from the reservoir to damaged area.11 Main advantage of this method is its ability to heal and sustain repetitive damage.12,13 Intrinsic healing materials are those which are free from healing agent14 and do not require any external energy to trigger the response. They can repair the mechanical damage spontaneously avoiding rupture and corrosion of underlying substrate.15,16 Capsule based systems contain healing agent in tiny capsules and are dispersed uniformly in the coating. Healing occurs through breaking of capsules at the damaged site. This technique possesses lot of advantages over others including protection of reactive substances from corroding environment, controlled evaporation of substances, separation of incompatible components for functional reasons, masking undesired properties of substances, safe handling of toxic substances and controlled release of the active components for delayed release or long acting release.17–19
Microencapsulation
Microencapsulation is a technique by which solids, liquids or gases can be enclosed in microscopic particles or droplets by formation of thin coating of wall material (polymer) around the substance, which are responsible to give more useful properties to the coating.20 The size of microcapsules varies from microns to few millimetres.21
Classification of microcapsules22
On the basis of morphology; microcapsules are classified into 3-types viz. monocore, polycore and matrix (as shown in Fig. 1).10
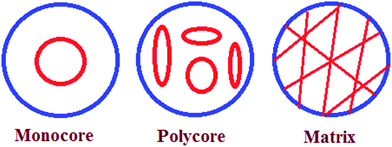 |
| Fig. 1 Morphologies of microcapsules. | |
Monocore microcapsules consist of only one core enclosed in the shell, while polycore capsules have many cores enclosed within the shell. On the other hand, in matrix encapsulation, the core material is distributed homogeneously into the shell material. In addition to these three basic morphologies, microcapsules can also be mononuclear with multiple shells.23–28
Techniques of microencapsulation
Active ingredient can be encapsulated in protective matrix through variety of techniques. These techniques can be merged into two main categories viz. Physical and Chemical. The detailed techniques included in physical as well as chemical methods are shown in Fig. 2 and are described in Table 1.
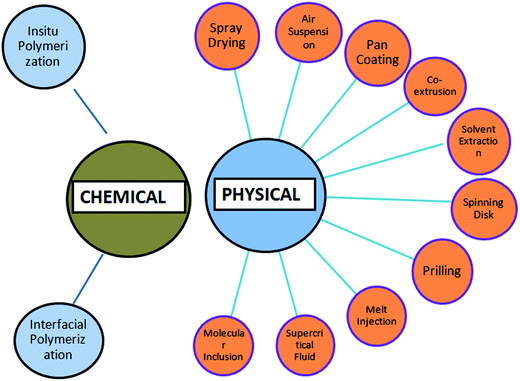 |
| Fig. 2 Techniques of microencapsulation. | |
Table 1 Various techniques of microencapsulation
Methods |
Advantages |
Disadvantages |
Spray drying29–32 |
Continuous process, rapid solvent evaporation |
Multi step process |
Air suspension33–35 |
Any form of solution can be applied including emulsion, suspension or melt |
Only solid cores can be encapsulated |
Pan coating28,36 |
Easy and simple |
Expensive and applicable for coating large particles only |
Co-extrusion27,37 |
Simple, low cost and reproducibility |
Slow productivity, only small microcapsules can be prepared |
Solvent extraction38,39 |
Solvent is extracted so no need to apply temperature |
Tedious process since stable emulsion of desired particle size has to be prepared by mixing core and matrix with continuous phase |
Solvent evaporation40,41 |
Simple process as compared to solvent extraction |
Higher temperature is required for evaporation of solvent |
Spinning disk42–44 |
Rapid, cost effective, simple and high production rate |
— |
Vibrating nozzle45 |
Suitable for producing large particles (>300 microns) |
Too many parameters to control the size and shape of capsules such as nozzle diameter, frequency of vibration, viscosity of liquid |
Spray chilling46–48 |
— |
Low encapsulation efficiency, expulsion of core materials during storage |
Melt injection49 |
Production rate is high |
Higher temperature is required |
Melt extrusion50 |
Production rate is high |
Higher temperature is required |
![[thin space (1/6-em)]](https://www.rsc.org/images/entities/char_2009.gif) |
Supercritical fluid technology51–55 |
(a) Rapid expansion of supercritical solution56–60 |
Uniform, monodispersed microcapsules |
Not suitable for producing larger microcapsules |
(b) Gas anti-solvent61,62 |
Simple and rapid |
Organic solvent is required |
(c) Particles from gas saturated solution63–65 |
Particles with variety of morphologies can be produced |
No need of organic solvent |
Freeze drying66–68 |
Water is major component thus process is cheap |
Tedious process as it involves four steps to obtain particle with desired size |
Molecular inclusion69–71 |
Molecular cavities protect the core material from oxidation and light induced decomposition |
— |
In situ polymerization72,73 |
Fast and convenient |
Too many parameters to control the particle size |
Interfacial polymerization74–77 |
Uniform size of capsules |
Too many parameters to control the particle size |
Progress in self-healing coating
With the advancement in coating technologies, number of authors have developed various microencapsulation techniques, chemistries for encapsulations, different types of core and shell materials etc. and is described in this section.
Self-healing system via ring opening metathesis polymerization (ROMP)
In a microcapsule-catalyst self-healing system (see Fig. 3), the healing agent is encapsulated in the capsules and the appropriate catalyst is dispersed without further encapsulation. This approach was firstly demonstrated by White et al. using dicyclopentadiene (DCPD) as a liquid healing agent encapsulated in urea-formaldehyde (UF) microcapsules. The DCPD microcapsules and Grubbs' first-generation catalyst were then distributed in an epoxy coating matrix for self-healing application.78,79
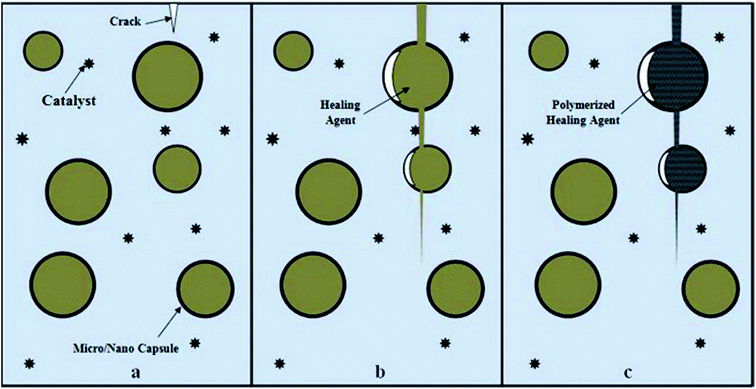 |
| Fig. 3 Autonomic healing concept consisting of healing agent encapsulated in UF microcapsules and catalyst incorporated into an epoxy matrix: (a) crack formation due to damage event. (b) Crack increases and ruptures the capsules releasing the healing agent into the crack volume. (c) The healing agent polymerizes upon contact with catalyst healing the crack. | |
When micro crack propagates through the material, it ruptures the microcapsules and releases the healing agent DCPD80 which on contact with Grubbs' catalyst starts ring opening metathesis polymerization (ROMP) and a highly cross-linked tough polycyclopentadiene is formed that seals the crack (as shown in Fig. 4). Low viscosity of the DCPD monomer helps it to flow into the crack plane.81,82 Later on, significant additional work was carried out by several research groups that have focused on optimization of reaction parameters, monomer selection and catalysts for ROMP based healing agent systems.83
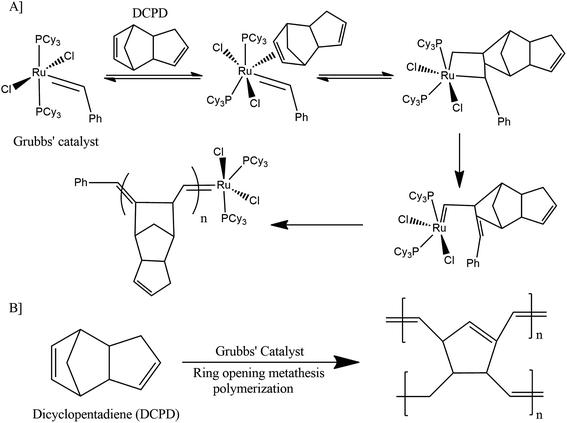 |
| Fig. 4 [A] Mechanism of action of Grubbs catalyst with DCPD; [B] formation of DCPD polymer through ring opening metathesis polymerization (ROMP). | |
Commercially available endo-DCPD was the first healing agent utilized in ROMP self-healing system.84,85 Crack healing and the rate of full recovery of mechanical toughness was slower in the endo-DCPD self-healing system.86 All these facts encouraged the researchers to develop more effective healing agents for ROMP-based self-healing systems which would possess fast curing at ambient temperature and impart high rigidity after curing. Two ROMP-based monomers that have received significant attention as more rapid healing agents are ethylidene norbornene (ENB) and the exo-DCPD.87 exo-DCPD and ENB were introduced to shorten the curing time as exo-DCPD undergoes ROMP nearly 20 times faster than endo-DCPD.88,89 ENB is also one of the popular healing agents for ROMP due to low cost, easy availability and rapid rate of bulk polymerization.90–92 Another promising approach of blending endo-DCPD with very active ENB was evaluated by Liu and co-authors. It was demonstrated that such system reacted faster than pure endo-DCPD at lower catalyst loading and simultaneously had higher rigidity after curing. Mariusz Majchrzak et al. reported a self-healing process at ambient temperature based on the ROMP of mono and di-functional norbornene dicarboximides encapsulated by urea formaldehyde.92
A number of attempts were made in order to improve performance of healing agent and healing efficiency of ROMP via modification in Grubbs' catalyst. Self-healing systems require complete coverage of crack plane with polymerized healing agent for optimal recovery of mechanical integrity. If the required amount of catalyst is not present in crack plane it leads to partial polymerization of healing agent and poor mechanical recovery. Catalyst availability is determined by the competing rates of dissolution of the catalyst and polymerization of the healing agent. The crystal morphology and dissolution kinetics of Grubbs' catalyst also affect self-healing efficiency.93 In epoxy self-healing coatings containing DCPD microcapsules, higher loading of catalyst and poor dispersion are the major issues. This poor dispersion of catalyst leads to crack regions on the crack plane where no catalyst is available to cure the DCPD and healing is incomplete. Secondly, epoxy curing agent diethylenetriamine (DETA) destructively attacks Grubbs' catalyst and reduces the concentration of catalyst in the system. To overcome these issues Rule et al. embedded Grubbs' catalyst in wax microspheres to protect its activity and to enhance the dispersability in the epoxy matrix.94
Several ROMP catalysts were developed in view of studying their effectiveness for DCPD self-healing system. In this regards, 2nd generation Grubbs' and Hoveyda–Grubbs' catalysts were invented. Even though catalysts showed significantly faster rate of initial polymerization as compared to that of the 1st generation Grubbs' catalyst, both of them failed to improve self-healing ability. The Hoveyda–Grubbs' catalyst exhibited high ROMP activity but that led to self-limiting polymerization and inefficient use of the catalyst. The authors also observed the best thermal stability of the 2nd generation Grubbs' catalyst and its capability to polymerize all the healing agents studied. The chemical structures of ROMP catalysts are shown in Fig. 5.
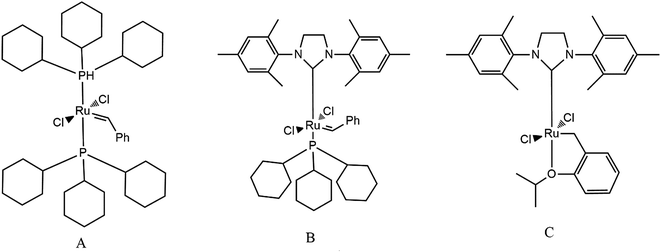 |
| Fig. 5 (A) 1st generation Grubbs' catalyst, (B) 2nd generation Grubbs' catalyst and (C) Hoveyda–Grubbs' catalyst. | |
Although the DCPD and Grubbs' catalyst system have been the most carefully studied ones till date, due to the stability and cost issues associated with Grubbs' catalyst other alternative systems have begun to be developed with the same basic principle for self-healing application.95
Silane based self-healing systems
In this sense, silicone chemistry was introduced to environmentally stable self-healing system and reveal the concept of phase separated healing agents in polymer matrix. Phase separation of the healing agent is an approach that may be applicable to a broad class of new healing chemistries for structural polymers. For example, ethyl cellulose microcapsules filled with rapseed oil were incorporated in carboxylated styrene/butadiene copolymer latex films. The microcapsules showed self plasticizing effect and also improved the toughness and modulus of the coating.96 Another most widely studied and popular phase separation approach is by using siloxane chemistry. The siloxane-based healing agent mixture is not encapsulated but is phase-separated in the matrix while the catalyst is encapsulated. Based on this, chemically stable self-healing materials system based on tin-catalyzed polycondensation of phase-separated droplets containing hydroxyl functionalized polydimethylsiloxane (HOPDMS) and polydiethoxysiloxane (PDES) was introduced by Cho et al. (2006). Further, PDMS healing agent along with di-n-butyl tin dilaurate (DBTL) containing microcapsules was embedded in vinyl ester matrix. The resultant system showed excellent improvement in fracture toughness of the materials.
The advantages related to poly(dimethyl siloxane) (PDMS) include stability at high temperature, low cure temperature, possibility to change functional groups, low price, optical transparency, biocompatibility and easy encapsulation making a promising component for self healing systems.97,98 Keller et al. developed self healing systems based on vinyl terminated PDMS elastomer obtained by incorporation of microencapsulated PDMS resin and microencapsulated crosslinker into PDMS matrix. Results have shown that tear strength recovery of 70% was achievable with the PDMS system capable of producing healing efficiencies of 100% or greater.99 The same system was later on studied for torsional fatigue loading and was observed to exhibit 25% total reduction in crack growth.100 In another work, PDMS was dispersed in epoxy resins through vigorous mixing. Phase separated PDMS existed in the form of liquid droplets in epoxy after matrix polymerization and was used as healing agent in case of damage. This system possessed number of advantages including healing process occurring at various atmospheric conditions; humid or wet environments and at elevated temperature (>100 °C). The healing efficiencies ranged from 11 to 35% and increased as the molecular weight of the PDMS resin increased. Similarly, with the use of silane coupling agent healing efficiency upto 51% was achieved.101
The need to have a two-component healing agent is a drawback of this approach since the probability of having both ingredients present at the same time and in the required ratio at the damage site significantly limits the available options. Considering this fact, self-healing anticorrosive organic coating based on a reactive silyl ester as a new organic healing agent; with poly (urea formaldehyde) as shell material was prepared by García et al. Experimental results revealed that the silyl ester was successfully used in self-healing anticorrosive organic coating systems as they possess the capability to react with water/humidity and metallic substrates, removing the necessity of presence of a crosslinker or catalyst in the system unlike traditional encapsulated approaches. But the synthesis of silyl ester increased the complexity and cost of the procedure.102,103 In a more recent work, first of its kind, extrinsic photoinduced self-healing system was developed by Young Song et al. methacryloyloxypropyl terminated polydimethoxy silane (MAT-PDMS) healing agent was enclosed in polyurea formaldehyde shell along with benzoin isobutyl ether photo initiator.104 These microcapsules were then embedded in a sol gel matrix based on triethylorthosilicate. When crack was generated in the coating, photoinitiator activated the MAT-PDMS resin in the presence of sunlight and photopolymerization reaction then healed the crack. Fig. 6 represents siloxane cores incorporated in various resin matrix. Recently, sol gel poly-condensation technique was used to encapsulate castor oil as well as bis(diphenyl phosphate) in a silica shell. Microencapsulation was performed by pickering and classical emulsion methods and influence of both the cores and emulsifiers on the stability of emulsion was investigated. Moreover, the thermal stability associated with the two cores and two different kinds of emulsions was observed to be excellent. Presence of silica shell helped in improving the thermal stability of this system further.105
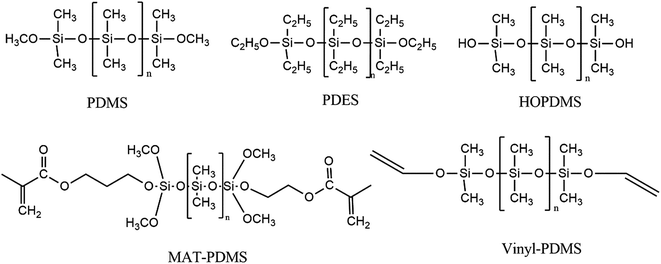 |
| Fig. 6 Various cores based on polydimethoxy silane (PDMS). | |
Huang et al. reported new silane microcapsules containing 1H,1H,2H,2H-perfluorooctyl triethoxysilane (POTS) for self-healing corrosion-resistant coating. There are several advantages of this coating system over the existing self-healing materials. The film formation is possible even in wet environment through hydrolysis of silane compounds and there is no need of any catalyst for self-healing to occur. Also, the film formed after hydrolysis and condensation of POTS is hydrophobic which repels aqueous solutions thereby reducing corrosion of metal. Electrochemical impedance spectroscopy and SEM images of salt spray test (as shown in Fig. 7) revealed excellent anticorrosive properties of the POTS encapsulated coating as compared to that of a bare metal as well as control sample.106 In a recent work, Cotting et al. developed the polystyrene microcapsule containing octylsilanol and Ce(III) ions as a corrosion inhibitor. 30% w/w microcapsules were incorporated in epoxy coating and evaluated for anticorrosive and self-healing performance. EIS Tafel and accelerated salt spray tests confirmed excellent anticorrosive behaviour of the coating.107
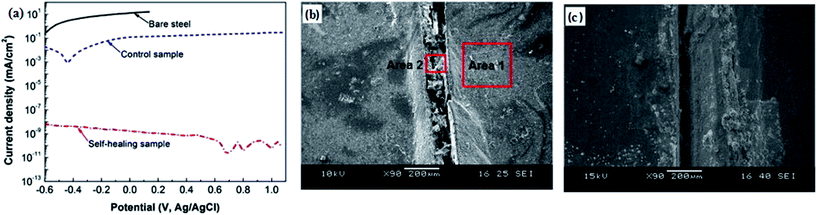 |
| Fig. 7 (a) Electrochemical test; SEM image of sample (b) before (c) after 48 h immersion in 10% NaCl. | |
Catalysts free self-healing system
Limitations of two component systems encouraged scientists to develop a system containing single healing agent which was able to react with the environment upon damage leading to a much more stable self-healing system.103 One of the possible approaches is to use microcapsules filled with core which have tendency to react with moisture such as drying oil, isocyanates etc. The catalyst free self-healing mechanism is showed in Fig. 8.
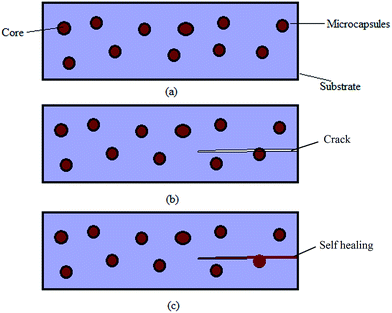 |
| Fig. 8 Catalyst free self healing mechanism. | |
Vegetable drying oils have a great potential for self-healing coating application as they have film forming ability via atmospheric oxidation.108,109 Number of authors have developed various self-healing systems with microcapsules containing drying oil along with driers.110 Healing mechanism of air drying oil is shown in Fig. 9. Effectiveness of linseed oil filled microcapsules encapsulated in UF shell for healing of cracks generated in coatings was investigated by Suryanarayana et al. Authors concluded that the epoxy paint films containing microcapsules withstood 72 hours of salt spray exposure while epoxy films without microcapsules showed corrosion after 48 hours of exposure.111 Further, the effect of addition of cobalt octoate (drier) and octadecylamine (ODA; corrosion inhibitor) in linseed oil was studied. It was observed that, cobalt octoate efficiently reduced the drying time as compared to that of ODA coatings. However, ODA coatings exhibited excellent anticorrosion properties than that of linseed oil containing cobalt octoate coatings.112 Similarly, excellent anticorrosion behaviour was obtained when linseed oil and mercaptobenzothiazole (MBT) was encapsulated in polyaniline formaldehyde and urea formaldehyde shell individually. Both the systems showed impedance values as high as 107 to 108 even after 15 days of exposure in 3.5 wt% NaCl solution.113,114 This could be due to formation of a polymerized protective layer formed by linseed oil after being released from the capsules at the damaged sites as studied by Pilbath et al. through scanning electrochemical microscope (SECM).115 The protective effect of the microcapsule incorporated linseed oil along the scratched surface of the steel was also investigated. The SECM tip measured the oxidation and reduction currents participating in the corrosion process. By comparing the corrosion-produced Fe2+ concentration and the oxygen consumption in scratched samples with and without the microcapsulated linseed oil, it was concluded that the encapsulated material shows self-healing properties. To increase the anticorrosive properties further, Jadhav et al. developed multi core microcapsules by encapsulating linseed oil and corrosion inhibitor in phenol formaldehyde shell material crosslinked with resorcinol via in situ polymerization.116 It was observed that multicore microcapsules showed excellent corrosion resistance and sustained 480 hours of salt spray exposure which was much higher than that of the reported work. It can be related to the combined effect of microcapsule and corrosion inhibitor that improved the mechanical and barrier properties of the coating. In another study, Miguel et al. performed a single stage acidic polymerization to encapsulate linseed oil in poly(urea-formaldehyde) shell. Unlike the conventional two stage process wherein the dispersion of shell material is added to the core material, in one stage process urea was dissolved in surfactant solution followed by the addition of linseed oil. The mixture was then stirred uniformly and stabilised. Finally, formaldehyde was added to obtain linseed oil microcapsules. This method was carried out in an acidic medium to avoid undesirable formation of UF particles could have taken place.117
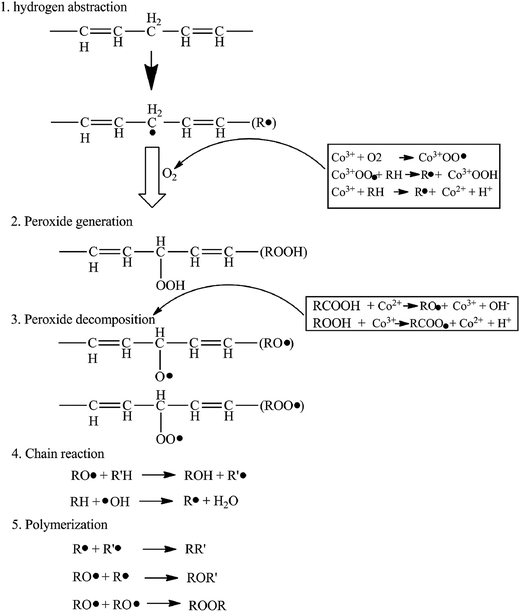 |
| Fig. 9 Reaction mechanism of drying oil. | |
In another work, polyurea microcapsules loaded with MBT were incorporated in sol–gel hybrid coating to protect aluminium AA2024. The addition of microcapsules preserved the barrier properties of the coating and improved corrosion protection as well as adhesion to the sol–gel matrix. This could be due to the presence of two “unreacted groups” (isocyanates and amines) from the polyurea polymer used in the encapsulation of MBT and the consequent formation of microcapsules. These two groups can react with sol–gel matrix, acting not only as filler but also as crosslinking agent, improving their protective properties.148
Healing efficiency of microcapsules has been studied by many authors and it is mainly depending on polymeric shell strength. Microcapsules should have sufficient mechanical strength to withstand shear stress generated during processing and application of paint. Hence, the selection of a suitable shell material is the most important parameter in self-healing coatings. A number of polymers have been used as shell materials including phenol-formaldehyde, urea–melamine–formaldehyde, urea–formaldehyde, polyurethane and melamine–formaldehyde.111,112,118 To further improve the properties of shell material, novel self-healing microcapsules were prepared by melamine modified urea–formaldehyde resin as shell material. After modification with melamine, the water-resistance, heat resistance, solvent resistance and chemical resistance were improved due to presence of triazine ring in melamine resulting in long storage time for microcapsule at room temperature.119 Similarly, nanoclays are also added into the shell wall to improve performance properties of the shell. For example, Montmorillonite and LAPONITE® were incorporated into the polyurea shell containing dimethyl phthalate (DMP) plasticizer. Although, addition of clay improved the fracture strength of the composites, it reduced the release of DMP.120 The size of the microcapsule also plays an important role in the self-healing performance of the coating. The size of microcapsules depend on reaction parameters such as stirrer geometry, agitation rate, temperature and stabilizer concentration. The size of microcapsules is affected the most by rate of stirring during the reaction.101 Boura et al. prepared linseed oil UF microcapsules via in situ polymerization under ultrasonic action to decrease their diameter size. The ultrasonic energy broke linseed oil droplets into finer ones and provided smaller spherical surface for the polymerization of urea and formaldehyde.121
Samadzadeh et al. encapsulated air drying tung oil in UF shell material via in situ polymerization and incorporated in epoxy coatings for anticorrosive application.122 In another study, encapsulation of plant oil as core in ethyl cellulose (EC) shell materials was carried out by two stage solvent evaporation method.123 In the first stage, EC powder was dissolved in ethyl acetate under magnetic stirring for at least 2 h at ambient temperature. Then oil was added in drop wise manner to an aqueous solution of surfactant under mechanical mixing at 800 rpm. The microcapsules were separated and dried and were observed to have regular spherical geometry.
Apart from vegetable oils, other component which is used in catalyst free self-healing systems is isocyanate. It is very reactive towards moisture and can be used as a healing agent to generate one-part catalyst-free self-healing materials. Jinglei Yang et al. successfully initiated the catalyst-free self-healing polymer for use in humid or wet environments by encapsulating isophorone diisocyanate (IPDI) via interfacial polymerization of polyurethane (PU).124 Isocyanates reaction with moisture is demonstrated in Fig. 10.125 Prepolymer reacts with water-soluble diol which serves as a chain extender for the capsule shell wall. In interfacial polymerization, polymer formation takes place at the liquid–liquid interface when two solutions are brought in contact or stirred together (as shown in Fig. 11).
 |
| Fig. 10 Basic mechanism for moisture curing of diisocyanate monomers. | |
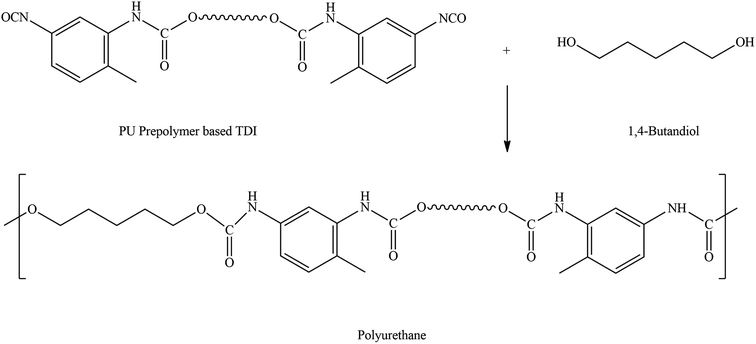 |
| Fig. 11 Reaction scheme of PU microencapsulation. | |
Huang et al. prepared microcapsules with hexamethylene diisocyanate (HDI) as a core enclosed in a PU shell synthesized via interfacial polymerization of methylene diphenyl diisocyanate (MDI) prepolymer and 1,4-butanediol.126 The prepared microcapsules were integrated into an epoxy resin to create a self-healing coating. Self-healing and anti-corrosion performance was evaluated by salt spray and EIS studies.127 In the same line of work Kardar et al. encapsulated IPDI using various polyols such as 1,4-butanediol, 1,6-hexanediol and glycerol via interfacial polymerization of PU.128 It was observed that microcapsule size as low as 1.7 and 3 microns could be obtained using 1,4-butanediol and 1,6-hexandiol respectively.129 Similarly, polyurea microcapsules were prepared from diisocyanate and diamine via interfacial polycondensations. IPDI and TDI were used as wall-forming materials and their effect on mean particle size, size distribution and thermal properties was studied by Hong et al. The results showed that the particle size distribution of polyurea microcapsules was broader with increasing TDI content due to its superior reactivity than IPDI. From TGA and SEM results, it was seen that polyurea microcapsules prepared from IPDI had a higher thermal stability and smoother surface compared to those prepared from TDI.130 Same authors further studied the effect of H12MDI, IPDI and TDI on thermal properties of microcapsules. The results revealed that melting temperature and heat capacity of the microcapsules increased slightly in the order H12MDI > IPDI > TDI.131 In another study, the effect of diamine on particle size, morphologies, and release behaviour of core materials of the resulting microcapsules were studied. Two diamines namely ethylene diamine (EDA) and 1,6-hexane diamine (HDA) were chosen for polyurea microcapsules synthesis. Preliminary observation showed that EDA-based polyurea microcapsules had a wider particle size distribution and a much rougher surface compared to the HDA-based microcapsules. Loading content of core in the EDA-based samples also was more due to rapid wall-forming by EDA, but the release rate was lower due to their higher wall thickness.132 With ongoing development in single walled microcapsules, couple of authors have developed double-walled microcapsules from PU/PUF for use in self-healing materials.133 Caruso et al. combined two chemistries to form more robust capsule shell walls in a single operation. Robust capsules were formed as long as the aromatic polyisocyanate prepolymer was soluble in the core liquid and the core liquid was compatible with isocyanates. Compared to a standard UF encapsulation, the modified encapsulation resulted in capsules with an increase in shell wall thickness as a function of the amount of PU added to the core liquid. Thermal stability of PU/UF microcapsules prepared with varying amounts of PU was better as compared to UF microcapsules. The second inner shell wall led to PU/UF EPA microcapsules with improved mechanical properties.134 In a more recent work, a novel approach for synthesizing double shelled microcapsules was developed by Sun et al. Microcapsules containing 4,4′-bis-methylene cyclohexane diisocyanate was first coated with polyurea matrix through interfacial polymerization followed by a layer of poly (ureaformaldehyde) shell via in situ polymerization. It was concluded that polymeric coatings containing microcapsules possessed superior anticorrosion performance even after immersion in water for 30 days.135
Some of the authors also utilised epoxy resin for self-healing application. Main advantage of such systems is that the self-healing process would produce the same material that comprises the matrix of the composite, ensuring good adhesion between the healing material and the coating matrix. For healing to occur a second component, a hardener, is also needed to be incorporated into the coating matrix. In the process of crack formation and propagation, the epoxy capsules would be ruptured and upon exposure of this epoxy to the hardener, polymerization would occur, filling the crack and restoring the strength of coating. In this regards, Jin et al. developed a new approach of dual microcapsule for self-healing application in thermoset epoxy. One capsule contained a modified aliphatic polyamine while the second capsule contained a diluted epoxy monomer. When crack incurred in the coating, capsules released the core and healed the damage.136 In another study, epoxy and its hardener mercaptan were encapsulated in polymeric shell of MF. As mercaptan is very active and not many polymers are suitable for encapsulating it, melamine-formaldehyde was chosen as it is inert towards mercaptan. Encapsulation of mercaptan was carried out in an oil-in-water emulsion by in situ polymerization. The resultant capsules had high core content. To further improve the self-healing performance, dual microcapsules; one containing epoxy prepolymer and other containing mercaptan (pentaerythritol tetrakis (3-mercaptopropionate))/tertiary amine (benzyl dimethylamine) hardener was embedded in epoxy composites. Along with self-healing, the dual microcapsules induced toughening, hydrodynamic pressure crack tip shielding and improvement in adhesion bonding.137 In order to increase heat resistance for high performance application same authors utilised melamine formaldehyde as a shell material and same dual microcapsules of epoxy and mercaptan but different catalyst 2,4,6-tris(dimethylaminomethyl)phenol (DMP-30) were used. Due to higher thermal stability of the resin component and lower volatility of DMP-30 catalyst, the healing agent and the self-healing composite not only survived high-temperature curing and thermal exposure, but also offered satisfactory capability of restoring self-healing properties.138 Mcllroy et al. developed microcapsules containing a reactive amine with potential applications in self-healing polymers. Microcapsules with amine as a core were prepared by interfacial polymerization of an isocyanate and an amine stabilized by an inverse pickering emulsion.139 Microcapsules were successfully isolated, dried, and re-dispersed in epoxy. Capsules released the core material upon rupture and were able to cure epoxy to form a polymer film. In other work, Maleimide chemistry involving amines and thiols is presented (see Fig. 12.) and evaluated for the design of autonomous self-healing epoxy materials. Model reactions showed that amines react rapidly with maleimide compounds at room temperature via Michael addition reaction. Moreover, thiols and maleimides react readily in the presence of tertiary amines that are present in the epoxy material. The maleimide conjugation reaction with residual amines in the epoxy material ensures chemical bonding of the newly formed network with the original materials during crack healing.140
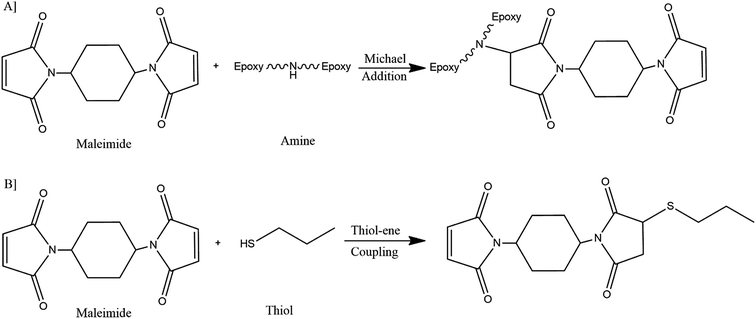 |
| Fig. 12 [A] Michael addition reaction of maleimide and amine [B] thiol addition across maleimide. | |
Microencapsulation technique was also used for developing intumescent flame retardant systems. Polyurethane–phosphate combinations are known to form flame retardant (FR) intumescent systems. The intumescent formulation is not permanent due to water solubility and migration of the phosphate. This problem might be solved by the technique of microencapsulation, for example encapsulation of di-ammonium hydrogen phosphate (DAHP) was carried out via two methods, interfacial polymerization (IP) and solvent evaporation (SP), in two types of polymeric shells viz. polyether–polyurethane and polyester–polyurethane.141 TGA studies revealed that the thermal stability of SP microcapsules was lower than that of IP microcapsules. Additionally, both the systems showed good flame retardant behaviour but still inferior compared to pure DAHP containing coatings.
Miscellaneous
Recently, Niu et al. attempted microencapsulation of carbon microspheres by poly(ethylene terephthalate) to prepare flame retardant composites. The in situ polymerization technique resulted in capsule shell thickness of 50 nm. They have concluded that microencapsulated carbon microspheres/PET systems exhibited better mechanical and flame retardant properties as compared to that of pristine PET as well as PET/carbon microspheres systems.142
Surface modification of microcapsules
Self-healing coatings have many excellences and give a reasonable and reliable response to the industrial association for autonomous crack repairing. Kumar et al. investigated the effect of microcapsule addition on adhesion strength and life time of the coating. It was concluded that weak interfacial adhesion between capsules and coating matrix imparts negative effect on mechanical and healing efficiency of coatings.143,118 Thus to overcome the problems, many researches focused on developing new techniques which would improve the compatibility of microcapsules and resin matrix. Surface modification of microcapsules with various additives is one such technique. Amongst various additives, silane coupling agents gained more attention due to their special chemical structure with dual functionality. Surface modification of microcapsules was carried out by reacting silane coupling agent via trialkoxy functional group of silane coupling agents with hydroxyl groups of microcapsules surface. The remaining functional groups of silane, which are generally ethylene, amine, and epoxy etc. are used for reaction with polymer matrix and improve their compatibility during processing and storing.144,145 Surface modification of microcapsules was first initiated by Haiyan Li et al. in which linseed oil microcapsules with UF shell were prepared by in situ polymerization method and the surface properties of microcapsules were modified with 3-aminopropyltriethoxy silane-coupling agent. Surface hydroxyl groups of microcapsules react with silanol group of silane coupling agent which forms the covalent bonds or the hydrogen bond.143 The reaction mechanism of silane modification is demonstrated in Fig. 13. FTIR and X-ray photoelectron spectra (XPS) showed that the silane-coupling agent binds strongly to PUF microcapsules surface. In another work, Wang et al. modified the microcapsule surface by using glycidoxypropyltrimethoxy silane and the surface treated microcapsules were incorporated in epoxy matrix. The epoxy group of capsules surface react with coating hardener to improve the interfacial bonding between microcapsules and coating matrix.144 Haghi et al. prepared ethyl cellulose (EC) microcapsules by solvent evaporation method. EC microcapsules were further surface modified using three different types of silane coupling agents such as 3-aminopropyl-trimethoxysilane (APS), [3-(methacryloyloxy)-propyl]-trimethoxysilane (MPS), and [3-(2,3-epoxypropoxy)-propyl]–trimethoxysilane, (EPS). Silane-treated Si–O–EC interactions and hydrogen bonding between silane with OH groups of EC were confirmed by FTIR and NMR techniques. EC microcapsules prepared in this study had the potential to increase the compatibility of microcapsules with polymeric matrix in the coating formulation.146 Poly(melamine–urea–formaldehyde) (MUF) microcapsules filled with epoxy resin were modified using 3-aminopropyltriethoxy silane-coupling agent147 and the modified microcapsules were incorporated in unsaturated polyester composites. The interfacial adhesion effect between MUF microcapsules and unsaturated polyester matrix was investigated by Tong et al. The silane-coupling agent plays an important role in improving the interfacial performance between microcapsules and unsaturated polyester matrix thereby enhancing mechanical properties of the composite significantly.118
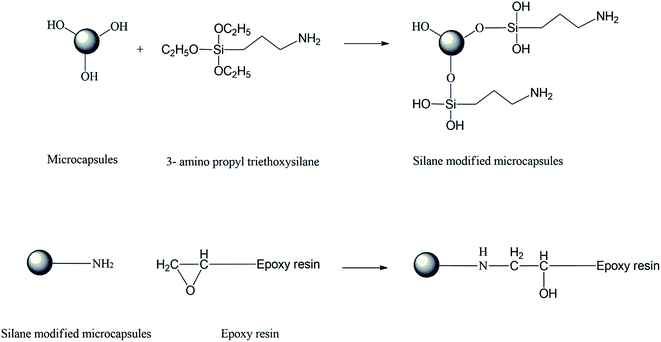 |
| Fig. 13 Silane modification on microcapsule surface. | |
Limitations of microencapsulation technique
Every method has its own advantages and disadvantages. In spite of numerous benefits of microencapsulation technique, there are some limitations or problems which cannot be unattained. Most difficult problem is to control the size of microcapsules during synthesis. It is very difficult to achieve microcapsules of uniform size no matter how precisely one controls the reaction parameters. Another and perhaps the most common problem related to many microencapsulation techniques is the agglomeration of capsules during wall formation. As the wall materials change from liquid to solid form they often go through a sticky stage which makes agglomeration difficult to be avoided. To minimize this difficulty the use of chemical hardening agents, careful selection of wall materials and solvents, and application of mechanical devices to physically separate the capsules is suggested. Another disadvantage of microencapsulation is that it works for single local healing unlike the vascular based system which allows multiple local healing events.
Conclusion
Microencapsulation is one of the quality preservation techniques of sensitive substances and a method for production of materials with new valuable properties. Microencapsulated substances may resolve many problems in coating industries which are often unnoticeable. Limitations like high reactivity, high volatility, pressure sensitivity, fast releasing, environmental and human toxicity, solubility and oxygen sensitivity can be easily eliminated by incorporating microencapsulated additives. Microencapsulation technology makes it possible to add materials that would have a shorter operating time or are incompatible with other components in coatings. Overall, it can be concluded that microencapsulation technique hold good potential in modern coating industry and many developments in microencapsulation method can be expected in coming years.
References
- Y. C. Yuan, T. Yin, M. Z. Rong and M. Q. Zhang, eXPRESS Polym. Lett., 2008, 2, 238–250 CrossRef CAS.
- S. R. White, B. J. Blaiszik, L. B. S. Kramer, S. C. Olugebefola, J. S. Moore and R. N. Sottos, Am. Sci., 2011, 99, 392–399 Search PubMed.
- A. Stankiewicz, I. Szczygiel and B. Szczygiel, J. Mater. Sci., 2013, 48, 8041–8051 CrossRef CAS.
- Z. M. Abdolah, S. V. Zwaag and S. J. Garcia, Self-Healing Mater., 2013, 1, 1–18 CrossRef.
- M. Samadzadeh, S. H. Boura, M. Peikari, S. M. Kasiriha and A. Ashrafi, Prog. Org. Coat., 2010, 68, 159–164 CrossRef CAS.
- N. M. Pugno and T. Abdalrahman, International Space Elevator Consortium, CLIMB, 2011, vol. 1, pp. 77–84 Search PubMed.
- S. George, D. Evans and S. A. Marchette, A biological programming model for self-healing, ACM Press., USA, 2003, pp. 72–81 Search PubMed.
- B. J. Blaiszik, S. L. B. Kramer, S. C. Olugebefola, J. S. Moore, N. R. Sottos and S. R. White, Annu. Rev. Mater. Res., 2010, 40, 179–211 CrossRef CAS.
- R. S. Trask, H. R. Williams and I. P. Bond, Bioinspiration Biomimetics, 2007, 2, 1–9 CrossRef PubMed.
- S. K. Ghosh, Self-Healing Materials: Fundamentals, Design Strategies, and Applications, Wiley-vch Verlag GmbH & Co. KGaA, Weinheim, 2009 Search PubMed.
- H. R. Williams, R. S. Trask and I. P. Bond, Compos. Sci. Technol., 2008, 68, 3171–3177 CrossRef CAS.
- C. J. Hansen, W. Wu, K. S. Toohey, N. R. Sottos, S. R. White and J. A. Lewis, Adv. Mater., 2009, 21, 4143–4147 CrossRef CAS.
- A. R. Hamilton, N. R. Sottos and S. R. White, Adv. Mater., 2010, 22, 5159–5163 CrossRef CAS PubMed.
- M. Q. Zhang and M. Z. Rong, Polym. Chem., 2013, 4, 4878–4884 RSC.
- Y. Chen, A. M. Kushner, G. A. Williams and Z. Guan, Nat. Chem., 2012, 4, 467–472 CrossRef CAS PubMed.
- M. D. Hager, P. Greil, C. Leyens, S. V. Zwaag and U. S. Schubert, Adv. Mater., 2010, 22, 5424–5430 CrossRef CAS PubMed.
- N. Agnihotri, R. Mishra, C. Goda and M. Arora, Indo Global J. Pharm. Sci., 2012, 2, 1–20 CAS.
- A. N. Rajalakshmi and B. Bhuvaneswari, Int. J. Pharm. Sci. Res., 2012, 2, 1–18 Search PubMed.
- D. Poncelet, Surface Chemistry in Biomedical and Environmental Science, 2006, pp. 23–34 Search PubMed.
- P. Venkatesan and R. K. Manavalan, J. Pharm. Sci. Res., 2009, 1, 26–35 CAS.
- H. Umer, H. Nigam, A. M. Tamboli and M. S. Nainar, Int. J. Pharma Bio Sci., 2011, 2, 474–481 Search PubMed.
- S. Jyothi, A. Seethadevi, K. S. Prabha, P. Muthuprasanna and P. Pavitra, Int. J. Pharma Bio Sci., 2012, 3, 509–531 Search PubMed.
- R. Dubey, T. C. Shami and K. U. Bhasker Rao, Def. Sci. J., 2009, 59, 82–95 CAS.
- H. Nack, J. Soc. Cosmet. Chem., 1970, 21, 85–98 Search PubMed.
- C. Roy, S. P. Bedi, R. Gupta and M. U. Khan, Journal of Pharmaceutics
and Cosmetology., 2012, 2, 76–86 Search PubMed.
- K. P. S. Kumar, S. K. Tejbe, S. Banu, P. Naga Lakshmi and D. Bhowmik, Indian J. Res. Pharm. Biotechnol., 2013, 1, 324–328 CAS.
- N. J. Zuidam and E. Shimoni, Overview of Microencapsulates for Use in Food Products or Processes and Methods to Make Them, Springer Science & Business Media, LLC., 2010, vol. 2, pp. 3–29 Search PubMed.
- M. N. Singh, K. S. Y. Hemant, M. Ram and H. G. Shivakumar, Res. Pharm. Sci., 2010, 5, 65–77 CAS.
- M. I. Re, Drying Technol., 1998, 6, 1195–1236 CrossRef.
- W. Kolanowski, M. Z. J. Weibrodt, B. Kunz and G. Laufenberg, Eur. Food Res. Technol., 2005, 222, 336–342 CrossRef.
- A. Gharsallaoui, G. Roudaut, O. Chambin, A. Voilley and R. Saurel, Food Res. Int., 2007, 40, 1107–1121 CrossRef CAS.
- L. B. Petrovic, V. J. Sovilj, J. M. Katona and J. L. Milanovic, J. Colloid Interface Sci., 2010, 342, 333–339 CrossRef CAS PubMed.
- D. Semyonov, O. Ramon, A. Kovacs, L. Friedlander and E. Shimoni, Drying Technol., 2012, 30, 1918–1930 CrossRef CAS.
- S. Gouin, J. Microencapsulation, 2005, 22, 829–839 CrossRef CAS PubMed.
- N. V. Naga Jyothi, P. M. Prasanna, S. N. Sakarkar, K. S. Prabha, P. S. Ramaiah and G. Y. Srawan, J. Microencapsulation, 2010, 27, 187–197 CrossRef PubMed.
- S. Rathore, P. M. Desai, C. V. Liew, L. W. Chan and P. W. S. Heng, J. Food Eng., 2013, 116, 369–381 CrossRef CAS.
- S. Freitas, H. P. Merkle and B. Gander, J. Controlled Release, 2005, 102, 313–332 CrossRef CAS PubMed.
- H. Y. Im, J. Kim and H. Sah, Biomacromolecules, 2010, 11, 776–786 CrossRef CAS PubMed.
- T. Ansari, M. S. Farheen Hasnain, M. N. Hoda and A. Nayak, Elixir Pharmacy, 2012, 47, 8821–8827 Search PubMed.
- S. Tiwari and P. Verma, Int. J. Pharm. Life Sci., 2011, 2, 998–1005 CAS.
- C. Duchesneau, S. Saha, M. Malhotra, I. Kahouli and S. Prakash, J. Pharm., 2013, 1–19 Search PubMed.
- K. C. Cochrum, US Pat., 6001387, 1999, pp. 1–7.
- R. Dubey, T. C. Shami and K. U. Bhasker Rao, Def. Sci. J., 2009, 59, 82–95 CAS.
- M. Whelehan and I. W. Marison, J. Microencapsulation, 2011, 28, 669–688 CrossRef CAS PubMed.
- E. P. Herrero, E. M. Martın Del Valle and M. A. Galan, Chem. Eng. J., 2006, 117, 137–142 CrossRef CAS.
- K. O. Paula, E. Fernando and S. F. Carmen, Food Technol. Biotechnol., 2013, 51, 171–182 Search PubMed.
- D. L. Pedroso, M. Dogenski, M. Thomazini, R. J. B. Heinemann and C. S. Favaro Trindade, Braz. J. Microbiol., 2013, 44, 777–783 CrossRef CAS PubMed.
- P. Kaushik, K. Dowling, C. J. Barrow and B. Adhikari, J. Funct. Foods, 2014, 19, 1–14 Search PubMed.
- A. Gryczke, S. Schminke, M. Maniruzzamana, J. Beckc and D. Douroumis, Colloids Surf., B, 2011, 86, 275–284 CrossRef CAS PubMed.
- K. Mishima, K. Matsuyama, D. Tanabe, S. Yamauchi, T. J. Young and K. P. Johnston, Materials, Interfaces, And Electrochemical Phenomena, 2000, 46, 857–865 CAS.
- Y. Chernyak, F. Henon, R. B. Harris, R. D. Gould, R. K. Franklin, J. R. Edwards, J. M. DeSimone and R. G. Carbonell, Ind. Eng. Chem. Res., 2001, 40, 6118–6126 CrossRef CAS.
- J. Kim, T. E. Paxton and D. L. Tomasko, Biotechnol. Prog., 1996, 12, 650–661 CrossRef CAS.
- S. Taki, E. Badens and G. Charbit, J. Supercrit. Fluids, 2001, 21, 61–70 CrossRef CAS.
- R. Bodmeier, H. Wang, D. J. Dixon, S. Mawson and K. Johnston, Pharm. Res., 1995, 12, 1211–1217 CrossRef CAS.
- T. J. Young, S. Mawson, K. P. Johnston, I. B. Henriksen, G. W. Pace and A. K. Mishra, Biotechnol. Prog., 2000, 16, 402–407 CrossRef CAS PubMed.
- M. Charoenchaitrakool, F. Dehghani, N. R. Foster and H. K. Chan, Ind. Eng. Chem. Res., 2000, 39, 4794–4802 CrossRef CAS.
- B. Helfgen, P. Hils, C. Holzknecht, M. TuK rk and K. Schaber, J. Aerosol Sci., 2001, 32, 295–319 CrossRef CAS.
- K. Matsuyama, K. Mishima, H. Umemoto and S. Yamaguchi, Environ. Sci. Technol., 2001, 35, 4149–4155 CrossRef CAS PubMed.
- K. Matsuyama, K. Mishima, K. Hayashi, H. Ishikawa, H. Matsuyama and T. Harada, J. Appl. Polym. Sci., 2003, 89, 742–752 CrossRef CAS.
- L. Sze Tu, F. Dehghani and N. R. Foster, Powder Technol., 2002, 126, 134–149 CrossRef.
- J. Bleich and B. W. Muller, J. Microencapsulation, 1996, 13, 131–139 CrossRef CAS PubMed.
- M. Fraile, A. Martin, D. Deodato, S. Rodriguez-Rojo, I. D. Nogueira, A. L. Simplicio, M. J. Cocero and C. M. M. Duarte, J. Supercrit. Fluids, 2013, 81, 226–235 CrossRef CAS.
- J. Yun, H. Lee, A. K. M. Asaduzzaman and B. Chun, J. Ind. Eng. Chem., 2013, 19, 686–691 CrossRef CAS.
- V. S. S. Goncalves, S. Rodriguez-Rojo, A. A. Matias, A. V. M. Nunes, I. D. Nogueira, D. Nunes, E. Fortunato, A. P. Alves de Matos, M. J. Cocero and C. M. M. Duarte, Int. J. Pharm., 2014, 478, 9–18 CrossRef PubMed.
- R. Kumar and A. Kar, Indo Global J. Pharm. Sci., 2014, 4, 47–51 CrossRef CAS.
- P. N. Ezhilarasi, D. Indrani, B. S. Jena and C. Anandharamakrishnan, J. Food Eng., 2013, 117, 513–520 CrossRef CAS.
- S. Saikia, N. Mahnot and C. L. Mahanta, Food Chem., 2015, 171, 144–152 CrossRef CAS PubMed.
- M. Choi, A. Soottitantawat, O. Nuchuchua, S. Min and U. Ruktanonchai, Food Res. Int., 2009, 42, 148–156 CrossRef CAS.
- E. Seo, S. Min and M. Choi, J. Microencapsulation, 2010, 27, 496–505 CrossRef CAS PubMed.
- T. Furuta, Microencapsulation of flavors and oil by cyclodextrin, Tottory university, Japan, pp. 9–16 Search PubMed.
- G. Erkan, M. Sariisik and N. K. Pazarlioglu, J. Appl. Polym. Sci., 2010, 118, 3707–3714 CrossRef CAS.
- W. Luo, W. Yang, S. Jiang, J. Feng and M. Yang, Polym. Degrad. Stab., 2007, 92, 1359–1364 CrossRef CAS.
- H. Mao, C. Wang, K. Zhang and S. Fu, Polym. Bull., 2011, 67, 1379–1391 CrossRef CAS.
- D. Torres, B. Seijo, G. Garcia-Encina, A. Mjose and J. L. Vila-Jato, Int. J. Pharm., 1990, 59, 9–17 CrossRef CAS.
- H. B. Scher, M. Rodson and K. Lee, Pestic. Sci., 1998, 54, 394–400 CrossRef CAS.
- N. Tsuda, T. Ohtsubo and M. Fuji, Adv. Powder Technol., 2012, 23, 724–730 CrossRef CAS.
- R. C. Mehta, B. C. Thanoo and P. P. DeLuca, J. Controlled Release, 1996, 41, 249–257 CrossRef CAS.
- E. N. Brown, N. R. Sottos and S. R. White, J. Mater. Sci., 2004, 39, 1703–1710 CrossRef CAS.
- M. Samadzadeh, S. H. Boura, M. Peikari, S. M. Kasiriha and A. A. Ashrafi, Prog. Org. Coat., 2010, 68, 159–164 CrossRef CAS.
- G. O. Wilson, S. Moore, R. White, R. Sottos and H. M. Andersson, Adv. Funct. Mater., 2008, 18, 44–52 CrossRef CAS.
- J. D. Rule, N. R. Sottos and S. R. White, Polymer, 2007, 48, 3520–3529 CrossRef CAS.
- M. R. Kessler, J. Aero. Eng., 2007, 221, 479–486 CAS.
- K. J. Ivin and J. C. Mol, Olefin metathesis and metathesis polymerisation, Academic Press, London, 1997 Search PubMed.
- H. Ren, J. Z. Sun, B. J. Wu and Q. Y. Zhou, Polymer, 2006, 47, 8309–8316 CrossRef CAS.
- X. Liu, J. K. Lee, S. H. Yoon and M. R. Kessler, J. Appl. Polym. Sci., 2006, 101, 1266–1272 CrossRef CAS.
- T. C. Mauldin, J. D. Rule, N. R. Sottos, S. R. White and J. S. Moore, J. R. Soc. Interface, 2007, 4, 389–393 CrossRef CAS.
- G. L. Nelson and C. L. Kuo, Synthesis, 1975, 2, 105–106 CrossRef.
- J. D. Rule and J. S. Moore, Macromolecules, 2002, 35, 7878–7882 CrossRef CAS.
- J. K. Lee, S. J. Hong, X. Liu and S. H. Yoon, Macromol. Res., 2004, 12, 478–483 CrossRef CAS.
- G. E. Larin, N. Bernklau, M. R. Kessler and J. C. DiCesare, Polym. Eng. Sci., 2006, 46, 1804–1811 CAS.
- J. K. Lee, X. Liu, S. H. Yoon and M. R. Kessler, J. Polym. Sci., Part B: Polym. Phys., 2007, 45, 1771–1780 CrossRef CAS.
- M. Majchrzak, P. J. Hine and E. Khosravi, Polymer, 2012, 53, 5251–5257 CrossRef CAS.
- T. Nesterova, K. Dam-Johansen and S. Kiil, Prog. Org. Coat., 2011, 70, 342–352 CrossRef CAS.
- J. D. Rule, E. N. Brown, N. R. Sottos, S. R. White and J. S. Moore, Adv. Mat., 2004, 17, 205–208 CrossRef.
- E. B. Murphy and F. Wudl, Prog. Polym. Sci., 2010, 35, 223–251 CrossRef CAS.
- S. M. Mirabedini, I. Dutilc, L. Gauquelin, N. Yan and R. R. Farnood, Prog. Org. Coat., 2015, 85, 168–177 CrossRef CAS.
- T. K. Kim, K. K. Jeong and O. K. Jeong, Microelectron. Eng., 2011, 88, 1982–1985 CrossRef CAS.
- J. C. Lotters, W. Olthuis, P. H. Veltink and P. Bergveld, J. Micromech. Microeng., 1997, 7, 145–147 CrossRef CAS.
- M. W. Keller, S. R. White and N. R. Sottos, Adv. Funct. Mater., 2007, 17, 2399–2404 CrossRef CAS.
- M. W. Keller, S. R. White and N. R. Sottos, Polymer, 2008, 49, 3136–3145 CrossRef CAS.
- C. L. Mangun, A. C. Mader, N. R. Sottos and S. R. White, Polymer, 2010, 51, 4063–4068 CrossRef CAS.
- S. J. Garcia, H. R. Fischer and S. van der Zwaag, Prog. Org. Coat., 2011, 72, 211–221 CrossRef CAS.
- S. J. Garcia and X. Wu, International Conference on Self Healing Materials, 2013, pp. 731–734 Search PubMed.
- Y. Song, Y. Jo, Y. Lim, S. Cho, H. Yu, B. Ryu, S. Lee and C. Chung, ACS Appl. Mater. Interfaces, 2013, 5, 1378–1384 CAS.
- C. Butstraen, F. Salaün and E. Devaux, Powder Technol., 2015, 284, 237–244 CrossRef CAS.
- M. Huang, H. Zhang and J. Yang, Corros. Sci., 2012, 65, 561–566 CrossRef CAS.
- F. Cotting and I. V. Aoki, Surf. Coat. Technol., 2016, 303, 310–318 CrossRef CAS.
- M. Alam, D. Akram, E. Sharmin, F. Zafar and S. Ahmad, Arabian J. Chem., 2014, 7, 469–479 CrossRef CAS.
- B. Z. Dlugogorski, E. M. Kennedy and J. C. Mackie, Fire Sci. Rev., 2012, 1:3, 1–36 Search PubMed.
- R. S. Jadhav, D. G. Hundiwale and P. P. Mahulikar, J. Appl. Poly. Sci., 2011, 119, 2911–2916 CrossRef CAS.
- C. Suryanarayana, K. C. Rao and D. Kumar, Prog. Org. Coat., 2008, 63, 72–78 CrossRef CAS.
- T. Szabo, J. Telegdi and L. Nyikos, Prog. Org. Coat., 2015, 84, 136–142 CrossRef CAS.
- T. Siva and S. Sathiyanarayanan, Prog. Org. Coat., 2015, 82, 57–67 CrossRef CAS.
- J. Yamuna, T. Siva, S. S. Sreeja Kumari and S. Sathiyanarayanan, RSC Adv., 2016, 6, 79–86 RSC.
- A. Pilbath, T. Szabo, J. Telegdi and L. Nyikos, Prog. Org. Coat., 2012, 75, 480–485 CrossRef CAS.
- R. S. Jadhav, V. Mane, A. V. Bagle, D. G. Hundiwale, P. P. Mahulikar and G. Waghoo, Int. J. Ind. Chem., 2013, 4, 1–9, DOI:10.1186/2228-5547-4-31.
- M. Miguel, R. Ollier, V. Alvarez and C. Vallo, Prog. Org. Coat., 2016, 97, 194–202 CrossRef.
- X. Tong, M. Zhang, M. Wang and Y. Fu, J. Appl. Polym. Sci., 2013, 127, 3954–3961 CrossRef CAS.
- X. Tong, T. Zhang, M. Yang and Q. Zhang, Colloids Surf., A, 2010, 371, 91–97 CrossRef CAS.
- S. B. Jagtap, M. S. Mohan and P. G. Shukla, Polymer, 2016, 83, 27–33 CrossRef CAS.
- S. H. Boura, M. Peikari, A. Ashrafi and M. Samadzadeh, Prog. Org. Coat., 2012, 75, 292–300 CrossRef.
- M. Samadzadeh, S. H. Boura, M. Peikari, A. Ashrafi and M. Kasiriha, Prog. Org. Coat., 2011, 70, 383–387 CrossRef CAS.
- S. M. Mirabedini, I. Dutil and R. R. Farnood, Colloids Surf., A, 2012, 394, 74–84 CrossRef CAS.
- J. Yang, M. W. Keller, J. S. Moore, S. R. White and N. R. Sottos, Macromolecules, 2008, 41, 9650–9655 CrossRef CAS.
- M. W. Keller, K. Hampton and B. McLaury, Wear, 2013, 307, 218–225 CrossRef CAS.
- M. Huang and J. Yang, J. Mater. Chem., 2011, 21, 11123–11130 RSC.
- M. Huang and J. Yang, Prog. Org. Coat., 2014, 77, 168–175 CrossRef CAS.
- P. Kardar, Prog. Org. Coat., 2015, 89, 271–276 CrossRef CAS.
- E. Jabbari, Iran. Polym. J., 2001, 10, 33–43 CAS.
- K. Hong and S. Park, J. Mater. Sci., 1999, 34, 3161–3164 CrossRef CAS.
- K. Hong and S. Park, J. Appl. Polym. Sci., 2000, 78, 894–898 CrossRef CAS.
- K. Hong and S. Park, Mater. Res. Bull., 1999, 34, 963–969 CrossRef CAS.
- B. Di Credico, M. Levi and S. Turri, Eur. Polym. J., 2013, 49, 2467–2476 CrossRef CAS.
- M. M. Caruso, B. J. Blaiszik, H. Jin, S. R. Schelkopf, D. S. Stradley, N. R. Sottos, S. R. White and J. S. Moore, ACS Appl. Mater. Interfaces, 2010, 2, 1195–1199 CAS.
- D. Sun, H. Zhang, X. Tang and J. Yang, Polymer, 2016, 91, 33–40 CrossRef CAS.
- H. Jin, C. L. Mangun, D. S. Stradley, J. S. Moore, N. R. Sottos and S. R. White, Polymer, 2012, 53, 581–587 CrossRef CAS.
- Y. C. Yuan, M. Z. Rong, M. Q. Zhang, G. C. Yang and J. Q. Zhao, eXPRESS Polym. Lett., 2011, 5, 47–59 CrossRef CAS.
- Y. C. Yuan, X. Ji Ye, M. Z. Rong, M. Q. Zhang, G. C. Yang and J. Q. Zhao, ACS Appl. Mater. Interfaces, 2011, 3, 4487–4495 CAS.
- D. A. McIlroy, B. J. Blaiszik, M. M. Caruso, S. R. White, J. S. Moore and N. R. Sottos, Macromolecules, 2010, 43, 1855–1859 CrossRef CAS.
- S. Billiet, W. V. Camp, X. K. D. Hillewaere, H. Rahier and F. E. Prez, Polymer, 2012, 53, 2320–2326 CrossRef CAS.
- S. Giraud, S. Bourbigot, M. Rochery, I. Vroman, L. Tighzert, R. Delobel and F. Poutch, Polym. Degrad. Stab., 2005, 88, 106–113 CrossRef CAS.
- M. Niu, X. Wang, Y. Yang, W. Hou, J. Dai, X. Liu and B. Xu, Prog. Org. Coat., 2016, 95, 79–84 CrossRef CAS.
- H. Li, R. Wang, H. Hu and W. Liu, Appl. Surf. Sci., 2008, 255, 1894–1900 CrossRef CAS.
- R. Wang, H. Li, W. Liu and X. He, J. Macromol. Sci., Part A: Pure Appl. Chem., 2010, 47, 991–995 CrossRef CAS.
- M. Abdelmouleh, S. Boufi, M. N. Belgacem, A. P. Duart, A. B. Salah and A. Gandini, Int. J. Adhes. Adhes., 2004, 24, 43–54 CrossRef CAS.
- H. Es-haghi, S. M. Mirabedini, M. Imani and R. R. Farnood, Colloids Surf., A, 2014, 477, 71–80 CrossRef.
- M. Williams, B. Olland, S. P. Armes, P. Verstraete and J. Smets, J. Colloid Interface Sci., 2015, 460, 71–80 CrossRef CAS PubMed.
- F. Maia, K. A. Yasakau, J. Carneiro, S. Kallip, J. Tedim, T. Henriques, A. Cabral, J. Venancio, M. L. Zheludkevich and M. G. S. Ferreira, Chem. Eng. J., 2016, 283, 1108–1117 CrossRef CAS.
|
This journal is © The Royal Society of Chemistry 2016 |
Click here to see how this site uses Cookies. View our privacy policy here.