DOI:
10.1039/C6RA10527K
(Paper)
RSC Adv., 2016,
6, 64640-64650
Enhanced aqueous oxidation activity and durability of simple manganese(III) salen complex axially anchored to maghemite nanoparticles†
Received
23rd April 2016
, Accepted 17th June 2016
First published on 17th June 2016
Abstract
Simple Mn-salen complex was anchored coordinatively to γ-Fe2O3 nanoparticles through amine functionality which provide a new magnetically recoverable nanocatalyst with high oxidation activity and stability. Catalyst characterization was performed using FT-IR, UV-Vis, XRD, EDS, TGA and ICP-AES. TEM image revealed a quasi-spherical structure with size smaller than 20 nm for nanocatalyst. A thermal stability up to around 300 °C was verified for prepared nanocatalyst based on thermogravimetric analysis. Finally, the catalytic performance of magnetically recoverable Mn-catalyst was exploited in the green oxidation of different types of functional groups including olefins, alcohols, saturated hydrocarbons and sulfur containing compounds with n-Bu4NHSO5 (TBAOX) in water under heterogeneous conditions. The salen catalyst proved to be reusable for at least eight times and the oxidant's by-product (n-Bu4NHSO4) could also be recycled.
1. Introduction
Oxyfunctionalization of organic substrates by practical and sustainable catalytic methods is of great interest from both an industrial and enzymatic point of view.1 Metal-salen complexes which are easy to prepare and are consequently cheap have attracted significant attention in research areas ranging from catalysis to development of electrochemical sensors and single-molecule magnets.2–4 They are stable in water, even at high pHs; and stable in a reasonable range of temperatures. Nevertheless, its oxidative degradation and consequently the drawbacks in separating the products and contamination by residual catalyst is the most important problem of salen ligands. Besides, the major difficulty of homogeneous catalysis is the need for separation and recovery of the metal-complexes from the reaction mixture at the end of the process. Currently, transition metal complexes immobilized on different supports to make homogeneous catalysts recyclable and economical. Although, the activity may decrease initially, immobilization may be preferred due to the increased stability of the catalyst compared with the homogeneous one which may quickly loss activity after short periods of use.5–10 Heterogeneous metal-salen complexes which are readily separable, offer the opportunity to reduce costs as well as pollutants. A variety of methodologies,11,12 including anchoring of salen-based catalysts through coordinative bond of the spacer to the metal center,13–22 have emerged for the immobilization of homogeneous metal-salen complexes.
Moreover, to increase industrial interest for both homogeneous and heterogeneous catalytic process; the replacement of harmful organic solvents with those are inherently benign is a necessity today. Among solvents, water is of particular interest because of non-toxicity, non-flammability, readily availability, and cheapness.23–29 It has also attracted much attention in both industry and academia because of facile isolation of organic compounds as well as different reactivity and selectivity patterns which may be accessed compared with those observed in common organic solvents.30–38
Magnetic nanoparticles (MNPs) offer advantages in multi-disciplinary research including biotechnology, biomedicine, magnetic resonance imaging (MRI), separation and catalysis.39–42 It is well known that the activity and selectivity of magnetic nano-catalysts can be manipulated by surface modification.43 The use of MNPs as catalysts or supports in chemical synthesis has been extensively studied in recent years as the separation of nanosized catalysts after their use is one of the most challenging features in the sustainable process development.44–47
Recently we have developed new magnetic nanocatalysts for efficient oxidation of organic compounds based on porphyrin and phthalocyanine complexes.48–50 Our promising results for stability of supported catalyst during aqueous oxidation encouraged us to evaluate the activity and stability of Mn-salen complex which is more susceptible toward oxidative degradation. Now, we wish to describe the remarkable oxidative efficiency and stability of simple and easily prepared Mn(III)-salen complex after being immobilized on functionalized nanosized γ-Fe2O3. Selective oxidation of olefins, saturated hydrocarbons, alcohols and sulfides using n-Bu4NHSO5 (TBAOX) in water successfully occurred. The survival of the heterogeneous Mn-salen catalyst was confirmed by spectroscopic data as well as its significant potential for recyclability and reuse.
2. Experimental
The procedures for the synthesis of MNP,51 SMNP,52 and silanation of silica-coated maghemite nanoparticles (ASMNP),53 as well as TBAOX,54 are given in ESI.†
2.1. Synthesis of maghemite nanoparticles supported catalyst (Mn-salen@ASMNP)
4.0 g of dry ASMNP powder were mixed with 200.0 mL ethanol to produce a homogenously mixed solution, followed by sonication the mixture for 30 min. 0.3 g of Mn-salen complex was added under mechanical stirring and the mixture was heated to 80 °C for 8 h. The free Mn-salen was removed through Soxhlet extraction with ethanol. The concentrated sample stored in refrigerator to use.
2.2. General procedure for the epoxidation of olefins and alcohols
In a typical experiment, the reaction mixtures were prepared as follows: to a mixture of 1.00 mmol olefin (or alcohol) and 0.03 g Mn-salen@ASMNP (5.0 × 10−3 mmol Mn-salen, 0.50 mol%) in 2.00 mL bidistilled water at 60 °C was added 0.70 g (2.00 mmol) freshly prepared TBAOX. After completion the reaction, the catalyst was removed with an external magnet and the aqueous suspension was extracted thrice with ethyl acetate (3 × 2.5 mL). The combined organic layers were dried over Na2SO4. The solvent was removed under reduced pressure to give the desired product (Tables 2 and 3) and the separated catalyst was washed with EtOH, H2O and used directly for a subsequent round of reaction without further purification. The purity of the products was confirmed by GC.
2.3. General procedure for the oxygenation of saturated hydrocarbons
In a typical experiment, the reaction mixtures were prepared as follows: to a mixture of 1.0 mmol of saturated hydrocarbon and 0.075 g of Mn-salen@ASMNP (1.2 × 10−2 mmol Mn-salen, 1.2 mol%) in 2.0 mL bidistilled water at 80 °C was added 0.71 g (2.0 mmol) of freshly prepared TBAOX. The catalyst was removed with an external magnet at the end of the reaction and the aqueous suspension was extracted thrice with ethyl acetate (3 × 2.5 mL). The combined organic layers were dried over Na2SO4. The solvent was removed under reduced pressure to give the desired product (Table 2) and the separated catalyst was washed with EtOH, H2O and used directly for a subsequent round of reaction without further purification. The purity of the products was confirmed by GC.
2.4. General procedure for sulfide oxidation
In a typical experiment, the reaction mixtures were prepared as follows: to a mixture of 1.0 mmol of sulfide and 0.015 g of Mn-salen@ASMNP (2.5 × 10−3 mmol Mn-salen, 0.25 mol%) in 2.0 mL bidistilled water at 25 °C was added 1.07 g (3.0 mmol) of freshly prepared TBAOX. At the end of the reaction, the catalyst was removed with an external magnet and the aqueous suspension was extracted thrice with ethyl acetate (3 × 2.5 mL). The combined organic layers were dried over Na2SO4. The solvent was removed under reduced pressure to give the desired product (Table 3) and the separated catalyst was washed with EtOH, H2O, and used directly for a subsequent round of reaction without further purification. The purity of the products was confirmed by GC.
3. Results and discussion
3.1. Preparation and characterization of the Mn-salen@ASMNP
The magnetically recoverable catalyst Mn-salen@ASMNP, (salen: N,N′-bis(salicylidene)ethylenediamine) was prepared by immobilization of simple and easy-made Mn(III) salen complex on the functionalized nanosized γ-Fe2O3 (Scheme 1). Silica coated magnetic nanoparticles (SMNP) was prepared by addition of tetraethoxysilane (TEOS) and ammonia solution to as-prepared magnetic nanoparticles (MNP).51,52 The silica layered system (SMNP) then offers the binding sites (Si–OH units) for the immobilization of the molecular catalyst. For the grafting on the surface (3-aminopropyl) triethoxysilane (APTES) as chelating ligand was used.53 It was reacted with Mn(III) salen complex in ethanol to yield the desired magnetically recoverable catalyst [Mn-salen@ASMNP] (Scheme 1).
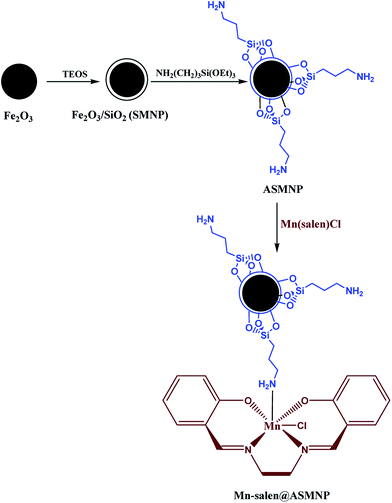 |
| Scheme 1 Preparation of Mn-salen@ASMNP. | |
The compositional analysis of the as-prepared Mn-salen@ASMNP nanocomposite was examined by energy-dispersive X-ray spectroscopy (EDS) and inductively coupled plasma atomic emission spectroscopy (ICP-AES). The distinct peaks of carbon, nitrogen, oxygen, silica, iron, and manganese in the EDS spectrum (Fig. 1) verified the incorporation of the Mn-salen complex on the surface of the synthesized nanocatalyst. According to ICP-AES analysis, the Mn loading was found to be 0.17 mmol g−1.
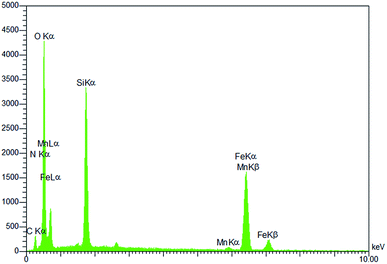 |
| Fig. 1 EDS spectrum of the as-prepared Mn-salen@ASMNP. | |
The FT-IR spectra of MNP, SMNP and the Mn-salen@ASMNP are given in Fig. 2. The bands at 582 and 634 cm−1 substantiate the presence of the maghemite core (Fig. 2a).55 The broad peaks at about 900–1200 cm−1, assigned to the Si–O–Si and Si–OH stretching vibrations, show the silica coating of maghemite nanoparticles (Fig. 2b).56,57 The bands around 3440 and 1627 cm−1 may be attributed to O–H stretching and bending of adsorbed water molecules.58 The FT-IR spectra of Mn-salen@ASMNP (Fig. 2c) shows two bands at 2874 and 2961 cm−1 related to the C–H stretching vibration of the propyl groups of APTES.15,59 The frequency of N–H stretching vibrations of the amine group fall in the 3300–3400 cm−1 range and are obscured by the water band. Immobilization of Mn-salen on amine functionalized magnetic nanoparticles (Mn-salen@ASMNP) was demonstrated by appearance of signals at about 1536, 1467, 1382 and 620 cm−1 (Fig. 2c) corresponding to the vibration modes of neat Mn(salen)Cl (Fig. 2d).15 The band at 470 cm−1 may be assigned to Mn–N bond of axial coordination of amino group into Mn-salen complex (Fig. 2c).16
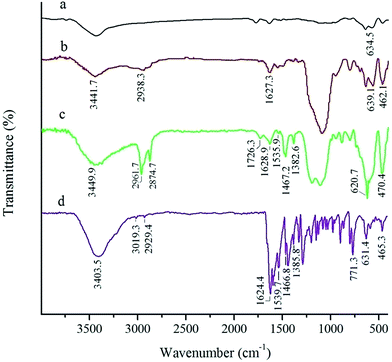 |
| Fig. 2 FT-IR spectra of MNP (a), SMNP (b), Mn-salen@ASMNP (c) and neat Mn(salen)Cl complex (d). | |
XRD revealed a cubic structure for crystalline MNP (Fig. S1†).60 The same set of characteristic peaks was observed for ASMNP (Fig. S2†) as well as Mn-salen@ASMNP (Fig. S3†), indicating the stability of the crystalline phase of the nanoparticles during the subsequent surface modification.61 The size of the particles was estimated to be 10 nm for Mn-salen@ASMNP, using the Debye–Scherrer equation according to (311) reflection.
Fig. 3 shows the transmission electron microscopy (TEM) micrograph of Mn-salen@ASMNP. The size distribution histogram shows that the maximum particle size is in the range of 8–14 nm (Fig. 3). Moreover, the TEM image revealed that the nanocatalyst preserved its morphology after recovery (Fig. S4†).
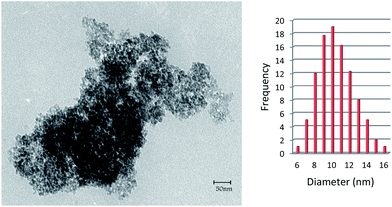 |
| Fig. 3 TEM micrograph and size distribution histograms of as-prepared Mn-salen@ASMNP. | |
The thermal behavior of Mn-salen@ASMNP (Fig. 4A) shows that the catalyst is stable up to around 300 °C and after that the degradation of Mn-salen occurred (Fig. 4B). A decrease in the weight percentage at about 100 °C related to desorption of water molecules from the catalyst surface. The organic parts were decomposed completely at 500 °C. From the TGA, the amount of Mn-salen was evaluated to be 0.164 mmol g−1, which is in agreement with the value determined by ICP-AES (0.170 mmol g−1).
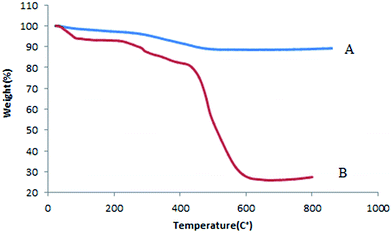 |
| Fig. 4 TGA thermograms of Mn-salen@ASMNP (A) and Mn-salen (B). | |
Fig. 5 shows the hysteretic M–H curves of the pristine γ-Fe2O3 and Mn-salen@ASMNP at 298
K. No remanence effect (superparamagnetic property) was observed for MNPs with saturation magnetization of about 60 emu g−1. The as-prepared Mn-salen@ASMNP nanocatalyst exhibited superparamagnetic properties with decreased saturation magnetization about 35 emu g−1. The superparamagnetic properties of Mn-salen@ASMNP prevents aggregation and enables them to redisperse rapidly when the magnetic field is removed.
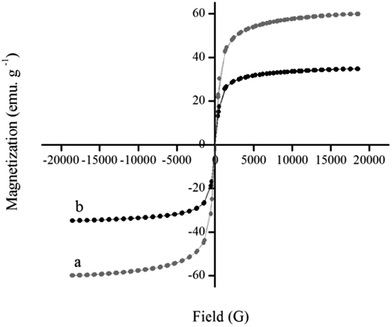 |
| Fig. 5 Magnetic hysteresis curves of the pristine γ-Fe2O3 (a) and Mn-salen@ASMNP (b) at 298 K. | |
3.2. Olefin epoxidation activity
The experiments were initiated with oxidation of cyclooctene (0.20 mmol) with TBAOX (0.40 mmol) in neat water under air, which did not proceed in the absence of catalyst at room temperature as well as at higher temperatures. When 0.5 mol% of free Mn(salen)Cl was added to this aqueous reaction mixture at 60 °C, cyclooctene conversion was 22 and 95% within 1 and 12 h, respectively. Nevertheless, the use of small amount of supported catalyst (Mn-salen@ASMNP, 0.2 mol%) improved markedly the reaction rate and 49, 58 and 69% cyclooctene were converted within 3 h at 25, 40 and 60 °C respectively using 1 equiv. TBAOX. When the oxidant/cyclooctene molar ratio increased up to 1.5 and 2 the conversion reached to 73 and 100% at 60 °C respectively using 0.2 mol% of catalyst at the same conditions. Our investigation revealed that the reaction rate is dependent on the catalyst concentration (Fig. 6). The best performance was obtained when 0.5 mol% of the supported catalyst was used. It led to complete conversion of the cyclooctene within 1 h with the formation of 95% of the pertinent epoxide (12, 46 and 57 cyclooctene epoxide after 15, 30 and 45 min, respectively). The very slow oxidation activity of parent materials, MNP, SMNP, ASMNP (10–15% cyclooctene oxide after 12 h), substantiated that the Mn-salen complex attached to magnetic support acts as active site of catalyst.
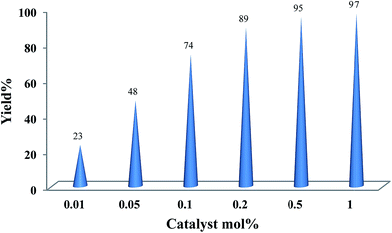 |
| Fig. 6 Catalyst concentration effect screening on the cyclooctene epoxidation. The reactions were run for 3 h using 1 mmol cyclooctene, 2 mmol TBAOX, in 2.5 mL water at 60 °C except for reactions using 0.5 and 1 mol% catalyst which monitored after 1 h. | |
It should be noted that the addition of additives (10 times vs. catalyst), such as imidazole (44%, 30 min), pyridine (46%, 30 min), and sodium dodecyl sulfate under CMC conditions (0.008 mol L−1) (51%, 30 min), as well as performing the reaction in an inert atmosphere (Ar, 48 and 94%, after 30 and 60 min) did not change the epoxide yield under optimized conditions. The standard buffered solutions were also used at 25 °C to screen the pH effect on the oxidation performance. Cyclooctene conversions were 66, 70, 60, 70 and 77% at pH 2, 4, 6, 7, 9 respectively after 3 h.
The oxidizing potential of other common oxidants was also screened in the oxidation of cyclooctene under optimized conditions. As depicted in Table 1, actually no activity was observed using O2, H2O2, perborate, percarbonate and PhI(OAc)2 and only trace amounts of the cyclooctene oxide was observed in the presence of t-butylhydroperoxide (TBHP), Oxone®, NaIO4 and UHP. Nevertheless, the addition of an equimolar amount of n-Bu4NHSO4 (TBAHSO4) to Oxone® improved the oxidation rate and a 31% yield of the epoxide was obtained within 60 min. When the reaction was carried out using TBAOX, the conversion of cyclooctene and the yield of its epoxide reached to 100 and 95% respectively. The good dispersity of Mn-salen@ASMNP in the aqueous solution of TBAOX seems to be the most important factor that affects the efficiency as described for the improved catalytic activity of neat CuPc,62 as well as CuSPcS@ASMNP,49 in water. TBAOX, as a quaternary salt, acts as a stabilizer which improves the dispersibility of the magnetic nanoparticles which are prone to aggregate.
Table 1 Screening of various oxidant in the epoxidation of cyclooctenea
Entry |
Oxidant |
Conversion (%) |
Reaction were run using cyclooctene (0.2 mmol), oxidant (0.4 mmol), catalyst (0.006 g) in water (0.4 mL) at 60 °C for 1 h. GC yield. |
1 |
O2 |
0 |
2 |
H2O2 |
0 |
3 |
NaBO3·4H2O |
0 |
4 |
Na2CO3·1.5H2O2 |
0 |
5 |
PhI(OAc)2 |
0 |
6 |
TBHP |
5 |
7 |
Oxone® |
8 |
8 |
NaIO4 |
10 |
9 |
UHP |
13 |
10 |
Oxone + Bu4NHSO4 |
31 |
11 |
TBAOX |
100 (95)b |
Finally, the influence of organic solvents on the efficiency of cyclooctene oxidation in this catalytic system was probed. After 1 h, actually trace amount of epoxidation product was appeared at 60 °C in commonly used solvents such as ethyl acetate (10%), chloroform (23%), methanol (27%) and acetonitrile (31%). The only exception was ethanol, which gave 85% cyclooctene oxide under optimized conditions. Obviously, the use of water as a standard “green” reaction medium is a remarkable advantage, especially due to the very low solubility of the organic compounds in water, providing easy separation of the products.
Having proved the activity of Mn-salen@ASMNP in the model reaction, the context of protocol was subsequently employed to a range of olefins as shown in Table 2. Desired conversions and remarkable selectivity to epoxides were obtained for different olefins. It led to complete conversion of cyclooctene, norbornene, indene, α-pinene and cyclohexene with the formation of the corresponding epoxides as sole products (entries 1–5). No allylic oxidation products were detected in the case of cyclohexene. A salient feature of title epoxidation system is moderate yields of 1,2-epoxyoctane resulting from less reactive terminal linear aliphatic olefin (entry 6), while no activity was observed in the presence of Mn–porphyrin and Cu–phthalocyanine catalysts in our previous related reports.48,49 The method possesses novelty regarding chemoselectivity. The hydroxyl group which is sensitive to oxidation remained completely intact producing the pertinent epoxides in high yields (entries 7 and 8). To confirm our claim, a competitive reaction between cyclooctene and benzyl alcohol was run. After 1 h, only trace amount of benzaldehyde (4%) was appeared in association with 93% cycloocteneoxide. However, the oxidation of styrenes gave exclusively the related carbonyl compounds with excellent conversions, indicating that the epoxides undergo ring-opening reactions (entries 9–12). It seems that benzaldehydes and acetophenone are favorably formed at high temperatures in the oxidation of styrene, 4-substituted styrenes and α-methylstyrene, respectively, because the high temperature will supply enough energy to break the C
C bond.63 These results are further supported by the oxidation of styrene oxide as a substrate under the same conditions. Benzaldehyde was formed solely in 93% yield within 60 min.
Table 2 The aqueous oxygenation of olefins using TBAOX catalyzed by Mn-salen@ASMNPa
Entry |
Substrate |
Product |
Yieldb/% |
Time/h |
The reactions were run under air in bidistilled water at 60 °C and the molar ratio of the olefin : TBAOX : catalyst was 200 : 400 : 1. GC yield based on internal standard. The selectivity of the products were >99% according to GC analysis. |
1 |
 |
 |
95 |
1 |
2 |
 |
 |
85 |
2 |
3 |
 |
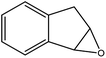 |
80 |
3 |
4 |
 |
 |
70 |
2 |
5 |
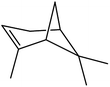 |
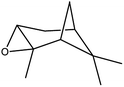 |
97 |
5 |
6 |
 |
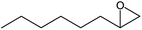 |
34 |
5 |
7 |
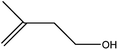 |
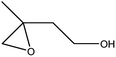 |
74 |
5 |
8 |
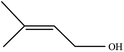 |
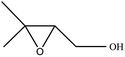 |
89 |
5 |
9 |
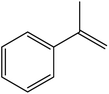 |
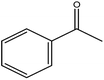 |
90 |
1 |
10 |
 |
 |
94 |
5 |
11 |
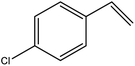 |
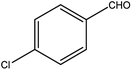 |
91 |
3 |
12 |
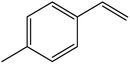 |
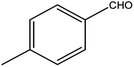 |
93 |
3 |
3.3. Oxidation of alcohols and saturated hydrocarbons
When the above epoxidation protocol (200/400/1 molar ratio for substrate
:
TBAOX
:
catalyst, in water at 60 °C) was employed for oxidation of different alcohols, moderate to high yields and excellent selectivity of pertinent carbonyl compounds were observed (Table 3, entries 1–8). 1-Phenylethanol as a secondary benzylic alcohol oxidized easily and acetophenone was obtained quantitatively (10, 30, 60 and 88% yields after 15, 30, 45 and 60 min respectively). However, less reactivity was observed for primary benzylic alcohols, so that after 2 h oxidation of benzyl alcohol 72% benzaldehyde was observed (entry 4). Inspection of the results in Table 3 clearly showed the significance influence of electronic and steric properties of the molecules on the oxidation rates. Sterically demanding alcohols such as benzhydrol (entry 2, 60%/3 h) and 4-t-butylbenzylalcohol (entry 6, 30%/3 h) showed less oxidation reactivity than the related unhindered molecules (entries 1 and 4). Moreover, higher conversion rate and production were observed for electron-rich 4-methoxybenzyl alcohol (entry 3, 82%/2 h) than that of benzyl alcohol with no group on the ring (entry 4, 71%/2) and especially substituted with an electron-deficient group (entry 5, 40%/3 h). Moderate to good yields of carbonyl products were achieved in the oxidation of saturated alcohols (entries 7 and 8, 34–62%). It should be noted that no trace of ester and benzoic acid was observed resulting from over oxidation of secondary and primary alcohols, respectively.
Table 3 The aqueous oxygenation of alcohols and hydrocarbons using TBAOX catalyzed by Mn-salen@ASMNPa
Entry |
Substrate |
Product |
Yieldb (%) |
Time (h) |
The reactions were run under air at 60 °C for entries 1–8 with molar ratio of 200 : 400 : 1 for alcohol : TBAOX : catalyst and at 80 °C for entries 9–14 with molar ratio of 100 : 200 : 1 for hydrocarbon : TBAOX : catalyst. GC yield based on internal standard. The numbers in parentheses are the yield of isolated products. The selectivity of the products were >99% according to GC analysis. |
1 |
 |
 |
88 (80) |
1 |
2 |
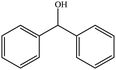 |
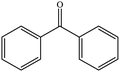 |
60 (54) |
3 |
3 |
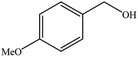 |
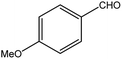 |
82 (78) |
2 |
4 |
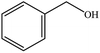 |
 |
72 (65) |
3 |
5 |
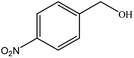 |
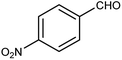 |
40 |
3 |
6 |
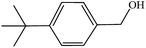 |
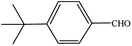 |
30 |
3 |
7 |
 |
 |
62 |
2 |
8 |
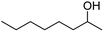 |
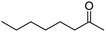 |
34 |
2 |
9 |
 |
 |
90 (86) |
6 |
10 |
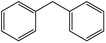 |
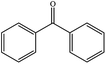 |
94 (88) |
6 |
11 |
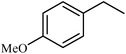 |
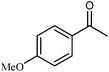 |
40 |
6 |
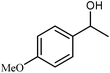 |
50 |
12 |
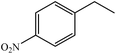 |
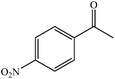 |
60 (55) |
6 |
13 |
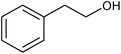 |
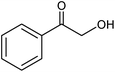 |
87 (80) |
6 |
14 |
 |
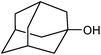 |
94 |
6 |
We also checked the activity of heterogeneous catalyst towards oxidation of saturated benzylic hydrocarbon and promising results were obtained using 2 equiv. TBAOX in water at 80 °C containing 1 mol% of catalyst (Table 3, entry 9–14). Under these conditions ethylbenzene was converted completely to acetophenone within 6 h (30, 45, 57, 80 and 89% after 1, 2, 3, 4 and 5 h, respectively). 4-Nitroethylbenzene, as an electron-deficient benzylic hydrocarbon gave solely the pertinent ketone in moderate yield (entry 12, 60%), while, its electron-rich counterpart, 4-ethylanisole (entry 11) converted to approximately equal yield of the corresponding alcohol (40%) and ketone (50%). Attractive results were observed for selectivity of the procedure which are of extreme interest from an industrial point of view.64 2-Phenyl ethanol selectively oxidized to 2-hydroxy acetophenone while, hydroxyl group was tolerated in the reaction (entry 13). Moreover, oxidation of adamantane gave absolutely 1-adamantanol in excellent yield (entry 14). It should be noted that, when the supported Mn-salen catalyst provided herein was replaced by neat Mn(salen)Cl complex, the efficiency of oxidation reactions reduced significantly (50 and 58% yield of acetophenone were detected in the oxidation of 1-phenylethanol and ethylbenzene after 1 and 6 h, respectively).
3.4. Sulfide oxidation
Aqueous oxidation of thioanisole (1 mmol) using 3 equiv. of TBAOX at 25 °C, under catalyst-free conditions gave a mixture of the related sulfoxide (60%) and sulfone (30%) after 3 h. Nevertheless, small amount of Mn-salen@ASMNP (0.2 mol%) resulted complete conversion of thioanisole and the pertinent sulfone produced solely within 3 h (67 and 88% sulfone selectivity after 1 and 2 h). Selective production of sulfoxide product under different conditions such as lesser amount of catalyst (50% selectivity using 0.1 mol% of catalyst and 3 equiv. TBAOX) and oxidant (65% selectivity using 0.2 mol% catalyst and 1 equiv. TBAOX) failed. The sulfone selectivity dropped to 20% when the catalyst was replaced by neat Mn(salen)Cl complex with the same quantity. Under the catalytic influence of heterogeneous Mn-salen@ASMNP, different sulfides were oxidized completely to sulfone products with >80% selectivity at 25 °C (Table 4). The promising results were observed for the chemoselectivity of the method making it a proper alternative for sulfone production. Sulfides having a benzylic C–H bond (entry 3), carbon–carbon double bond (entries 4 and 5) were transformed into the corresponding sulfones in excellent yield without formation of any epoxide, alcohol and carbonyl by-products. Completive reactions between thioanisole and equimolar amount of other substrates used in this study such as cyclooctene, 1-phenylethanol and ethylbenzene under conditions optimized for sulfide oxidation gave methyl phenyl sulfone as sole product confirming our claim about chemoselectivity of the procedure. Finally, under the same conditions, phenyl disulfide (entry 8), and 4-methylbenzenethiol (entry 9) were oxidized selectively to the pertinent thiosulfonates which are biologically and medicinally importantcompounds.65
Table 4 Aqueous oxidation of organosulfur compounds using TBAOX catalyzed by Mn-salen@SMNPa
Entry |
Substrate |
Productb |
Yieldc,d % |
The reactions were run under air in water at 25 °C for 3 h and the molar ratio of substrate/TBAOX/catalyst was 500 : 1000 : 1. The products were identified by comparison with authentic samples.66 The yield of isolated products. The selectivity of the products were >99% according to GC analysis, except for entry 2 and 3 which gave 20 and 5% of the related sulfoxides, respectively. |
1 |
 |
 |
93 |
2 |
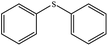 |
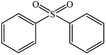 |
75 |
3 |
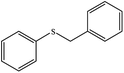 |
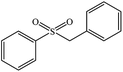 |
90 |
4 |
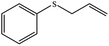 |
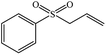 |
96 |
5 |
 |
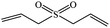 |
93 |
6 |
 |
 |
89 |
7 |
 |
 |
91 |
8 |
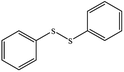 |
 |
92 |
9 |
 |
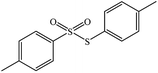 |
88 |
3.5. The catalyst activity, reusability and stability
To evaluate the activity of Mn-salen@ASMNP in this oxidation reactions, TOF of different types of substrates were determined. The desired TOF/h of 190, 176 and 240 were obtained in the oxidation of cyclooctene, 1-phenyl ethanol and thioanisole, respectively. Comparison of the results obtained for cyclooctene epoxidation (190/h) than some of those previously reported methods demonstrated well that Mn-salen@ASMNP is more efficient (Table 5).67–73
Table 5 Comparison of results for epoxidation of cyclooctene catalyzed by catalyst 1 and comparison with some catalysts reported in the literature
Entry |
Catalyst |
Cat. (mol%) |
Time (h) |
Yield (%) |
TOF (h−1) |
Ref. |
1 |
Mn-salen@ASMNP |
0.5 |
1 |
95 |
190 |
This work |
2 |
[Mn(salophen)Cl]@SiIm-Fe |
1.6 |
1 |
100 |
62.5 |
21 |
3 |
[Mn(TPP)Cl@ABI-MWCNT] |
3.2 |
2.5 |
99 |
12.38 |
67 |
4 |
[Mn(TPP)Cl@APy-MWCNT] |
3.8 |
2.5 |
98 |
10.26 |
68 |
5 |
PVMo@MCM-41-Im |
0.6 |
25 |
92.8 |
12.27 |
69 |
6 |
[W(CO)5@APy-MWCNT] |
1.2 |
3 |
98 |
27.2 |
70 |
7 |
[W(CO)6@DAB-MWCNT] |
0.6 |
2 |
98 |
81.7 |
71 |
8 |
[Mn(salophen)Cl]@amine-MWCNT |
6, 3.3 |
2.5 |
97–100 |
6.6–8 |
20 |
9 |
[Mn(TNH2PP)Cl]@WCNT |
5 |
2 |
95 |
9.5 |
72 |
10 |
Mn(TPyP)/SiO2–Fe3O4 |
1.9 |
2.75 |
97 |
18.65 |
73 |
Recovery of Mn-salen@ASMNP catalyst was easy and efficient. When the magnetic stirring was stopped, the catalyst absorbed onto the magnetic stirring bar. The catalyst was recovered by decantation of the reaction mixture in the presence of an external magnet. It was then washed with ethyl acetate or ethanol as safe solvents, dried under vacuum. To avoid errors resulting from loss of the catalyst during work up, the recovered catalyst was weighted before using in the next run. The ease of recovery, combined with the inherent stability of the silica-protected Fe2O3 nanoparticle constituent, allowed the catalyst to be retrieved efficiently over at least eight times in the oxidation of cyclooctene with only a 7% decrease in the epoxide yield (Table S1†). Using a hot filtration method, the Mn content in the filtrates was analyzed by ICP-AES after each run. Negligible quantities of Mn were found only at the first two runs (0.87 and 0.12% Mn leached at first and second run respectively), and no trace of Mn dissolved in the filtrate was detected for next runs (Table S1†), confirming that the complex was firmly anchored to the SMNP support. When the filtrate charged by new samples of cyclooctene and TBAOX, the conversion was about 9% after 12 h under the optimized conditions. The comparison of the FT-IR spectra of fresh and used Mn-salen@ASMNP (Fig. 7), UV-Vis (Fig. S5†) and EDS spectrum (Fig. 1 and S6†) demonstrated that the catalyst preserved its structure after multiple reuses. It is worth to mention that, the oxidant by-product (TBAHSO4) could be separated by lyophilizing of the aqueous phase (>90%) and reused in the preparation of TBAOX. Therefore, the use of water as a standard green media which also provides easy isolation of hydrophobic organic products, the repeated catalyst recycling and reuse as well as the absence of additives, toxic reagents, or solvents provide many appropriate conditions to make a sustainable method. The additional advantage of reported magnetic nanocatalyst relates to facile and inexpensive synthesis of Mn-salen catalyst compared with porphyrin and phthalocyanine counterparts used in our previous related works.48–50 Moreover, different types of functional groups including olefins, alcohols, saturated hydrocarbons and sulfur containing compounds were oxidized successfully in aquase media regardless of reaction type.
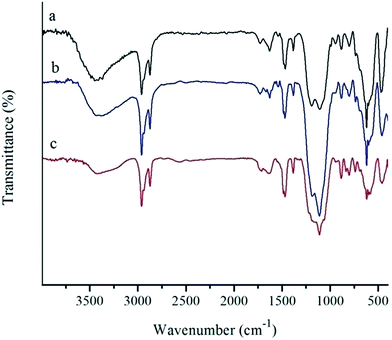 |
| Fig. 7 FT-IR spectra of fresh Mn-salen@ASMNP (a) and after recovering from cyclooctene (b) and 1-phenylethanol (c) oxidation reactions according to the procedures reported in Tables 2 and 3. | |
4. Conclusion
In summary, axial anchoring of simple Mn-salen complex to amine-functionalized silica coated magnetic nanoparticles provided a robust and magnetically recoverable nanocatalyst (8–14 nm). Using an aqueous solution of TBAOX, the oxidation of olefins, saturated hydrocarbons and alcohols proceeded well in the presence of a low catalyst loading of heterogeneous Mn-salen nanocatalyst. In addition, an appropriate alternative for selective oxidation of sulfides to the sulfones in neat water was developed using Mn-catalyst provided herein. Surfactants, additives, toxic reagents or solvents, and by-products removed from the presented procedures. Besides these advantageous, the use of water as a standard “green” solvent providing easy and safe work-up procedure, comfortable and inexpensive synthesis of Mn-salen complex, easily catalyst and oxidant separation and recycling, and lack of by-products, make title methodologies cost effective and eco-friendly systems which may be amenable to industrial uses.
Acknowledgements
Support for this work by Research Council of University of Birjand is highly appreciated. We also thank “Iran Science Elites Federation” for Partial support of this work.
References
- R. A. Sheldon and J. K. Kochi, Metal-Catalyzed Oxidations of Organic Compounds, Academic, New York, 1981 Search PubMed.
- M. D. Hobday and T. D. Smith, Coord. Chem. Rev., 1973, 9, 311–337 CrossRef CAS.
- P. G. Cozzi, Chem. Soc. Rev., 2004, 33, 410–421 RSC.
- S. Bellemin-Laponnaz and S. Dagorne, Patai's Chemistry of Functional Groups, John Wiley & Sons, 2012 Search PubMed.
- C. E. Song and S. Lee, Chem. Rev., 2002, 102, 3495–3524 CrossRef CAS PubMed.
- Q.-H. Fan, Y.-M. Li and A. S. C. Chan, Chem. Rev., 2002, 102, 3385–3466 CrossRef CAS PubMed.
- L. Canali and D. C. Sherrington, Chem. Soc. Rev., 1999, 28, 85–93 RSC.
- K. C. Gupta and A. K. Sutar, Coord. Chem. Rev., 2008, 252, 1420–1450 CrossRef CAS.
- S. Natarajan, G. K. Venkataramanan and R. Seenivasan, Coord. Chem. Rev., 2005, 249, 1249–1268 CrossRef.
- C. Baleizao and G. Hermenegildo, Chem. Rev., 2006, 106, 3987–4043 CrossRef CAS PubMed.
- A. Orejón, A. M. Masdeu-Bultó, P. Salagre, S. Castillón, C. Claver, A. Padilla, B. Almena and F. L. Serrano, Ind. Eng. Chem. Res., 2008, 47, 8032–8036 CrossRef.
- P. McMorn and G. J. Hutchings, Chem. Soc. Rev., 2004, 33, 108–122 RSC.
- X. Huang, X. Fu, X. Wu and Z. Jia, Tetrahedron Lett., 2013, 54, 4041–4044 CrossRef CAS.
- F. Jutz, J.-D. Grunwaldt and A. Baiker, J. Mol. Catal. A: Chem., 2008, 279, 94–103 CrossRef CAS.
- L. Saikia, D. Srinivas and P. Ratnasamy, Microporous Mesoporous Mater., 2007, 104, 225–235 CrossRef CAS.
- Z. Zhang, F. Guan, X. Huang, Y. Wang and Y. Sun, J. Mol. Catal. A: Chem., 2012, 363–364, 343–353 CrossRef CAS.
- A. R. Silva, V. Budarin, J. H. Clark, B. de Castro and C. Freire, Carbon, 2005, 43, 2096–2105 CrossRef CAS.
- P. Das, A. R. Silva, A. P. Carvalho, J. Pires and C. Freire, Colloids Surf., A, 2008, 329, 190–197 CrossRef CAS.
- J. Huang, X. Fu, G. Wang, Q. Miao and G. Wang, Dalton Trans., 2012, 41, 10661–10669 RSC.
- S. Tangestaninejad, M. Moghadam, V. Mirkhani, I. Mohammadpoor-Baltork and M. S. Saeedi, Appl. Catal., A, 2010, 381, 233–241 CrossRef CAS.
- M. Torki, S. Tangestaninejad, V. Mirkhani, M. Moghadam, I. Mohammadpoor-Baltork and A. R. Khosropour, J. Inorg. Organomet. Polym., 2013, 23, 923–929 CrossRef CAS.
- P. Das, A. R. Silva, A. P. Carvalho, J. Pires and C. Freire, Catal. Lett., 2009, 129, 367–375 CrossRef CAS.
- C. J. Li and T. K. Chan, Organic Reactions in Aqueous Media, John Wiley & Sons, New York, 1997 Search PubMed.
- P. A. Grieco, Organic Synthesis in Water, Blackie Academic and Professional, London, 1998 Search PubMed.
- N. Parikh, D. Kumar, S. R. Roy and A. K. Chakraborti, Chem. Commun., 2011, 47, 1797–1799 RSC.
- G. Sharma, R. Kumar and A. K. Chakraborti, Tetrahedron Lett., 2008, 49, 4269–4271 CrossRef CAS.
- A. K. Chakraborti, S. Rudrawar, K. B. Jadhav, G. Kaur and S. V. Chankeshwara, Green Chem., 2007, 9, 1335–1340 RSC.
- S. V. Chankeshwara and A. K. Chakraborti, Org. Lett., 2006, 8, 3259–3262 CrossRef CAS PubMed.
- G. L. Khatik, R. Kumar and A. K. Chakraborti, Org. Lett., 2006, 8, 2433–2436 CrossRef CAS PubMed.
- R. Breslow, Acc. Chem. Res., 1991, 24, 159–164 CrossRef CAS.
- S. Otto and J. B. F. N. Engberts, Org. Biomol. Chem., 2003, 1, 2809–2820 CAS.
- C. J. Li and L. Chen, Chem. Soc. Rev., 2006, 35, 68–82 RSC.
- U. M. Lindstrom and F. Andersson, Angew. Chem., Int. Ed., 2006, 45, 548–551 CrossRef PubMed.
- M. C. Pirrung, Chem.–Eur. J., 2006, 12, 1312–1317 CrossRef CAS PubMed.
- A. Manna and A. Kumar, J. Phys. Chem. A, 2013, 117, 2446–2454 CrossRef CAS PubMed.
- B. R. Goldsmith, T. Hwang, S. Seritan, B. Peters and S. L. Scott, J. Am. Chem. Soc., 2015, 137, 9604–9616 CrossRef CAS PubMed.
- E. Levin, E. Ivry, C. E. Diesendruck and N. G. Lemcoff, Chem. Rev., 2015, 115, 4607–4692 CrossRef CAS PubMed.
- A. Rezaeifard, R. Haddad, M. Jafarpour and M. Hakimi, J. Am. Chem. Soc., 2013, 135, 10036–10039 CrossRef CAS PubMed.
- T. H. Shin, Y. Choi, S. Kim and J. Cheon, Chem. Soc. Rev., 2015, 44, 4501–4516 RSC.
- R. Dalpozzo, Green Chem., 2015, 17, 3671–3686 RSC.
- M. Mahmoudi, H. Hosseinkhani, M. Hosseinkhani, S. Boutry, A. Simchi, W. S. Journeay, K. Subramani and S. Laurent, Chem. Rev., 2011, 111, 253–280 CrossRef CAS PubMed.
- H. Amiri, K. Saeidi, P. Borhani, A. Manafirad, M. Ghavami and V. Zerbi, ACS Chem. Neurosci., 2013, 4, 1417–1429 CrossRef CAS PubMed.
- R. B. N. Baig and R. S. Varma, Chem. Commun., 2013, 49, 752–770 RSC.
- R. S. Varma, Sustainable Chem. Processes, 2014, 2, 11 CrossRef.
- M. B. Gawande, A. K. Rathi, P. S. Branco and R. S. Varma, Appl. Sci., 2013, 3, 656–674 CrossRef CAS.
- M. B. Gawande, P. S. Branco and R. S. Varma, Chem. Soc. Rev., 2013, 2, 3371–3393 RSC.
- B. Reddy Vaddula, A. Saha, J. Leazer and R. S. Varma, Green Chem., 2012, 14, 2133–2136 RSC.
- A. Rezaeifard, M. Jafarpour, P. Farshid and A. Naeimi, Eur. J. Inorg. Chem., 2012, 5515–5524 CrossRef CAS.
- A. Rezaeifard, M. Jafarpour, A. Naeimi and R. Haddad, Green Chem., 2012, 14, 3386–3394 RSC.
- A. Rezaeifard, P. Farshid, M. Jafarpour and G. Kardan Moghaddam, RSC Adv., 2014, 4, 9189–9196 RSC.
- B. Z. Tang, Y. Geng, J. W. Y. Lam, B. Li, X. Jing, X. Wang, F. Wang, A. B. Pakhomov and X. X. Zhang, Chem. Mater., 1999, 11, 1581–1589 CrossRef CAS.
- M. Shokouhimehr, Y. Piao, J. Kim, Y. Jang and T. Hyeon, Angew. Chem., Int. Ed., 2007, 46, 7039–7043 CrossRef CAS PubMed.
- B. Karimi and E. Farhangi, Chem.–Eur. J., 2011, 17, 6056–6060 CrossRef CAS PubMed.
- B. R. Travis, B. P. Ciaramitaro and B. Borhan, Eur. J. Org. Chem., 2002, 3429–3434 CrossRef CAS.
- C. Pecharromfin, T. Gonzfilez-Carrefio and J. E. Iglesias, Phys. Chem. Miner., 1995, 22, 21–29 Search PubMed.
- K. D. Kim, S. S. Kim, Y. H. Choa and H. T. Kim, J. Ind. Eng. Chem., 2007, 13, 1137–1141 CAS.
- J. H. Cai, J. W. Huang, P. Zhao, Y. J. Ye, H. C. Yu and L. N. Ji, J. Sol-Gel Sci. Technol., 2009, 50, 430–436 CrossRef CAS.
- C. Yuan, Z. Huang and J. Chen, Catal. Lett., 2011, 141, 1484–1490 CrossRef CAS.
- P. Das, A. R. Silva, A. P. Carvalho, J. Pires and C. Freire, J. Mater. Sci., 2009, 44, 2865–2875 CrossRef CAS.
- B. Z. Tang, Y. Geng, J. W. Y. Lam, B. Li, X. Jing, X. Wang, F. Wang, A. B. Pakhomov and X. X. Zhang, Chem. Mater., 1999, 11, 1581–1589 CrossRef CAS.
- M. Jafarpour, A. Rezaeifard, V. Yasinzadeh and H. Kargar, RSC Adv, 2015, 5, 38460–38469 RSC.
- A. Rezaeifard, M. Jafarpour, A. Naeimi and K. Mohammadi, J. Mol. Catal. A: Chem., 2012, 357, 141–147 CrossRef CAS.
- B. Tyagi, U. Sharma and R. V. Jasra, Appl. Catal., A, 2011, 408, 171–177 CrossRef CAS.
- J. E. Backvall, Modern Oxidation Methods, WILEY-VCH, Weinheim, 2004 Search PubMed.
- N. Benkeblia and V. Lanzotti, Food, 2007, 1, 193–201 Search PubMed.
- N. Iranpoor, D. Mohajer and A. Rezaeifard, Tetrahedron Lett., 2004, 45, 3811–3815 CrossRef CAS.
- M. Zakeri, M. Moghadam, I. Mohammadpoor-Baltork, S. Tangestaninejad, V. Mirkhani and A. R. Khosropour, J. Coord. Chem., 2012, 65, 1144–1157 CrossRef CAS.
- M. Zakeri, M. Moghadam, I. Mohammadpoor-Baltork, S. Tangestaninejad, V. Mirkhani, A. R. Khosropour and M. Alizadeh, Transition Met. Chem., 2012, 37, 45–53 CrossRef CAS.
- R. Hajian, S. Tangestaninejad, M. Moghadam, V. Mirkhani, I. Mohammadpoor-Baltork and A. R. Khosropour, J. Coord. Chem., 2011, 64, 4134–4144 CrossRef CAS.
- M. Nooraeipour, M. Moghadam, S. Tangestaninejad, V. Mirkhani, I. Mohammadpoor-Baltork and S. M. Nabavizadeh, Transition Met. Chem., 2011, 36, 861–866 CrossRef CAS.
- M. Nooraeipour, M. Moghadam, S. Tangestaninejad, V. Mirkhani, I. Mohammadpoor-Baltork and N. Iravani, J. Coord. Chem., 2012, 65, 226–238 CrossRef CAS.
- M. Moghadam, I. Mohammadpoor-Baltork, S. Tangestaninejad, V. Mirkhani, H. Kargar and N. Zeini-Isfahani, Polyhedron, 2009, 28, 3816–3822 CrossRef CAS.
- M. S. Saeedi, S. Tangestaninejad, M. Moghadam, V. Mirkhani, I. Mohammadpoor-Baltork and A. R. Khosropour, Polyhedron, 2013, 49, 158–166 CrossRef CAS.
Footnote |
† Electronic supplementary information (ESI) available: Experimental procedures, XRD, TEM image, UV-Vis, EDS and the results for recycling of catalyst. See DOI: 10.1039/c6ra10527k |
|
This journal is © The Royal Society of Chemistry 2016 |
Click here to see how this site uses Cookies. View our privacy policy here.