DOI:
10.1039/C6RA10385E
(Paper)
RSC Adv., 2016,
6, 63667-63680
BiPO4/Bi2S3-HKUST-1-MOF as a novel blue light-driven photocatalyst for simultaneous degradation of toluidine blue and auramine-O dyes in a new rotating packed bed reactor: optimization and comparison to a conventional reactor
Received
21st April 2016
, Accepted 28th June 2016
First published on 29th June 2016
Abstract
BiPO4/Bi2S3-HKUST-1-MOF as a novel blue light active photocatalyst was synthesized and characterized by X-ray XRD, SEM, PL, BET, BJH and DRS. This novel photocatalyst was applied in a new catalytic rotating packed bed reactor for intensification of simultaneous photocatalytic degradation of toluidine blue (TB) and auramine-O (AO). In this reactor, high gravity media generated by a high rotational speed in a porous domain leads to intensification of the external mass transfer rate and significantly increases the mixing and turbulency. The central composite design (CCD) following analysis of variance (ANOVA) was applied to optimize the operational parameters including irradiation time, pH, photocatalyst dosage, rotational speed, solution flow rate, aeration flow rate, and TB and AO concentration. The optimum values were found to be 65 min, 6, 0.25 g L−1, 1300 rpm, 0.40 L min−1, 35 L min−1, 25 and 25 mg L−1 for irradiation time, pH, photocatalyst dosage, rotational speed, solution flow rate, aeration rate and initial concentration of TB and AO, respectively. At these optimum conditions, the photocatalytic degradation percentages of TB and AO were found to be 99.37% and 98.44% respectively with an overall desirability of 1.0. Replication of all experiments at optimum conditions with a conventional photocatalytic reactor shows the requirement of more photocatalyst as well as more irradiation time for operation in comparison to the rotating packed bed reactor. Results showed that the rotating packed bed is more economical, has a higher efficiency and can operate at a higher flow rate. Kinetic studies are an essential step in designing and optimizing photocatalytic reactors during scale-up processes, a pseudo first order kinetics based on the Langmuir–Hinshelwood (L–H) model was able to successfully fit the data concerning the present photodegradation approach.
1. Introduction
Dyes arrive to different ecosystem via wastewater assigned to the bleaching, textile, pharmaceutical, dyeing, paper and pulp industries1–3 and this subsequently leads to the generation of hazards like carcinogenic and mutagenic effects which change the quality and safety of the water media. In this regard, the quality of water media can be improved via preliminary pre-treatments like adsorption, sedimentation, floatation, coagulation and filtration. Some of these procedure suffer from limitations with the generation of huge amounts of waste or merely transfer these pollutants to another phase and cannot thoroughly eliminate them.4,5 An alternative approach which is able to remove or reduce the extent of these limitations is advanced oxidation processes (AOPs)6–8 that its efficiency highly related to the type and number of reactive and nonselective hydroxyl radicals (˙OH) as very good and powerful oxidizing agent.9 Generally, the photocatalytic degradation as a member of AOPs category is based on combination of semiconductors and light irradiation for degradation of pollutants. Most of recent efforts of researches for such purpose devoted to laboratory scale10–12 which is a great limitation specially in ultraviolet irradiation region. Conventional photocatalytic reactors poses limitations including poor light distribution inside the reactor and low surface areas for photocatalyst per unit volume of reactor13 that hinder from their large scale application and simply overcome by designing rotating packed bed. Rotating packed bed is an efficient equipment in the intensification of mass transfer, micro-mixing and reaction processes.14–16 In this device centrifugal force emerged from high rotational speed in a porous domain lead to improvement of mass transfer between phases.17,18 This equipment due to its smaller physical size and negligible scale-up effects compared to the conventional devices is very economic, controllable and safe. These advantages are due to higher interfacial surface area generated by high gravity field.19 The poor light distribution is compensated by using a flexible strip light-emitting-diode (LED) which installed around the periphery of the transparent reactor vessel to prepare uniform light distribution to ensure that each photocatalyst particle receives at least the minimum amount of light necessary for activation.13 Generally, the LED lamp is highly superior to ultraviolet (UV) lamps in term of very lower operational costs and better environmental friendly.20–22 Combination of rotating packed bed for reduction of external mass transfer and nano photocatalysts is proportional of reducing the internal mass transfer. Therefore, high attempts is devoted to the preparation of metal–organic frameworks (MOFs) as hybrid materials with three dimensional porous network and crystalline structures including an organic linkers and metal-oxo clusters.23–25 Some unique properties with large specific surface area, high pore volume and structural adaptivity lead to a major interest in MOFs for photocatalytic degradation process. Most attentions were focused on the construction with high performance visible light photocatalyst.26,27 Amongst, bismuth based materials such as BiPO4, BiVO4, Bi2WO6, Bi2S3 and their composite with bulk direct band gap of around of 1.5 eV (ref. 28 and 29) as sole and/or their composites are good candidate for hybridizing with MOFs to construct noble and visible light active photocatalyst. Therefore, this work describes a novel photocatalyst namely BiPO4/Bi2S3-HKUST-1-MOF which synthesized by sonochemical assisted hydrothermal method. Subsequently, this new hybrid with low band gap was used for photocatalytic degradation of binary mixture of toluidine blue (TB) and auramine-O (AO) dyes in rotating packed bed reactor equipped with blue light irradiation. Performance of current designed method with new photocatalyst materials was investigated and results were compared with conventional reactor in same conditions. Finally, central composite design (CCD) was applied for optimization of the degradation process.30–32
2. Experimental
2.1. Materials and apparatus
All reagents and chemicals were purchase from Merck and Sigma Aldrich Company (American) and used without further purification. All the solutions were prepared using deionized water. The solution concentrations were analyzed by UV-Vis spectrophotometry (model V-530, Jasco, Japan). The pH was measured using a pH/redox/temperature meter, model AL20pH (AQUALYTIC, Germany). DRS spectra were obtained with an Avant spectrophotometer (Avaspec-2048-TEC). X-ray diffraction (XRD, Philips PW 1800) was recorded using Cu Kα radiation (40 kV and 40 mA). Photoluminescence spectroscopy at room temperature was used to determine other optical properties of the samples (PL, Jobin Yvon Horiba HR 800UV, He–Cd laser). Measurement of the blue LED spectra distribution was performed using a spectrometer with a monochromator (MC) (Model 77200 from Oriel Co.). The morphology of samples was analyzed using filed emission scanning electron microscopy (FE-SEM: Sigma, Zeiss) and EDS analysis was carried out by silicon drift detector oxford instruments. Diffuse reflectance spectra (DRS) were collected with an Avant's spectrophotometer (Avaspec-2048-TEC).
2.2. Synthesis of Bi3PO4/Bi2S3-HKUST-1-MOF
Bi3PO4/Bi2S3-HKUST-1-MOF composites were prepared by a facile one-pot ultrasonic assisted hydrothermal method. In a typical procedure, 0.1 g of HKUST-1 MOF (taken from ref. 33) was well dispersed in double distillated water and subsequently, 0.242 g Bi(NO3)3·5H2O, 0.28 g Na2HPO4 and 0.1 g PVP were dispersed in dilute nitric acid (2 M). Finally, 0.1 g Na2S was added to product mixture and sonicated for 40 min. Subsequently, the mixed solution was transferred into a Teflon-lined stainless steel autoclave, sealed and maintained at 180 °C for 12 h. Finally, the obtained product was collected by centrifugation, washed with distilled water several times, and dried in oven at 70 °C.
2.3. Reactor set-up and photodegradation operation
Designed rotating packed bed reactor for photocatalytic process (Fig. 1) consists of stationary cylindrical transparent casing, porous bed, magnet pump (VIGOR, model: MD-15R), blue LED (SMD 5050 Flexible Strips, 14.4 W m−1), flowmeter (LZB-6WB, Glass pier), stirrer (DC motor, SERVO Co., Japan), aeration pump (Side Channel Blower, RT-3009-1), distributor, sampling valve, control box, tank and motor. The most important section of reactor is the rotor which is an annular cylindrical porous bed that made of stainless steel with porosity of 0.9 and high surface area of 800 m2 m−3. The rotor connects to a high speed motor via a shaft and could be operated from 300 rpm to 1800 rpm. The inner and outer diameter of the porous bed were 30 mm and 80 mm respectively, and its axial height was 50 mm. The packing in the RPB were 50 mm and 150 mm respectively, and the axial height of the packing was 53 mm. According to the experimental design, a certain amount of photocatalyst dissolved to deionized water and well mixed, then added to binary mixture of dyes with certain concentration and stored in a tank with 7 liter capacity. The pH of solution was adjusted at the desired value by 0.1 M HCl and/or NaOH solutions. The prepared solution in tank was pumped into the reactor with a certain flow rate. The solution passes through a distributor and jetted onto the inner edge of the rotor. The inlet of the distributor has a diameter of 0.25 in., and its outlet has 16 holes, with diameter of 0.04 in. The variation between inlet and outlet diameter of distributor lead to increasing in the outlet velocity, so solution is sprayed with a high velocity and collides with the porous rotating bed. Under this condition, thick solution film is split into micro or nano-droplets and thin film lead to increasing in interfacial surface area between photocatalyst particles and pollutions, and significantly intensification of mass transfer and mixing processes.34 The rotating porous bed was placed in a stationary cylindrical transparent casing which is surrounded by a blue strip LED to ensure getting uniform light distribution. The spectral distribution of stripe blue LED was indicated that this LED had irradiation wavelength in the range of 465–470 nm (Fig. 2). Rotation of the rotor with high speed creates a high gravity environment lead to photocatalyst particles and dyes thrown towards the light source and efficient amount of light necessary for photocatalyst activation be supplied. Therefore, in this reactor light distribution improved as well as mass transfer rate. Operation was done in continuous flow mode. For comparison operation was performed into the proposed photoreactor and conventional photoreactors, so that before switching the LED, the reactors operate was kept for 30 min in the dark condition to ensure complete equilibration of adsorption/desorption of dyes on the photocatalyst surface (the amount of dye adsorbed on the catalyst surface in the dark-condition for proposed reactor was obtained 9.0 and 7.0% for TB and AO dyes, respectively, while in conventional photoreactors this value was obtained to be 10 and 7.0% for TB and AO dyes, respectively). During the experiments temperature of was maintained at 25 °C. According to the experiment design, at specific time, sample was withdrawn from sampling valve and centrifuged at 4000 rpm for 15 min to separate the photocatalyst particles and then subjected to analysis using a UV-Vis spectrophotometer. The photocatalytic degradation efficiency was calculated by using the following equation: |
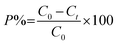 | (1) |
where P is the photocatalytic degradation efficiency (%), C0 (mg L−1) is the concentration of dyes after adsorption equilibrium in the dark (t = 0), and Ct (mg L−1) is the concentration of dyes at reaction time t (min). Temporal UV-Vis absorption spectral changes during the operation and absorbance spectra of TB and AO in single and binary solution (Fig. 3) were taken in a wide range of wavelength (λ) UV-Vis spectrophotometer.
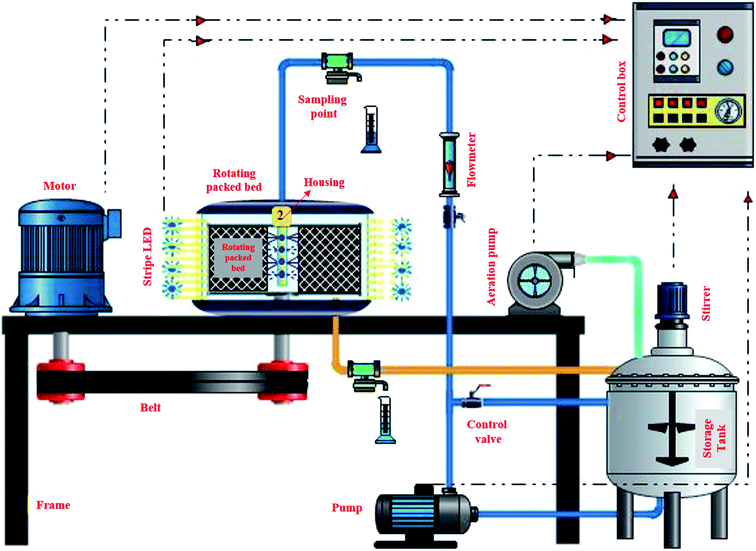 |
| Fig. 1 Schematic of rotating packed bed photocatalytic rector. | |
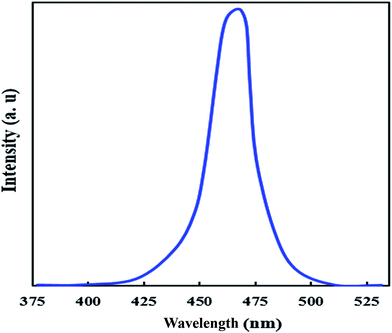 |
| Fig. 2 Spectral distribution of strip blue LED. | |
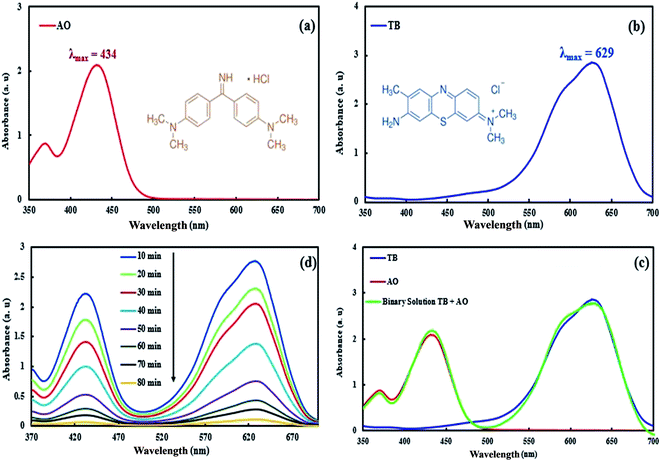 |
| Fig. 3 UV-Vis spectra with chemical structure (a) AO, (b) TB, (c) binary solution of AO + TB, (d) typical absorption spectra for binary mixture of dyes. | |
2.4. OH˙ radical's generation experiments
The contents of OH˙ radicals over HKUST-1 and BiPO4/Bi2S3-HKUST-1-MOF under blue light irradiation were investigated via a fluorescence process. Fluorescence spectra of 2,4-dicarboxylic acid were measured. The OH˙ radical trapping experiments were carried out as follow: 2,4-dicarboxylic acid (16.6 mg) was first dissolved in 200 mL of a dilute NaOH solution (2 × 10−3 M), followed by addition of 100 mg of HKUST-1 and/or BiPO4/Bi2S3-HKUST-1-MOF, and stirred for 30 min in the dark. The suspensions (contain HKUST-1 and/or BiPO4/Bi2S3-HKUST-1-MOF) was irradiated with a blue light for different time in proposed rotating packed bed reactor and conventional reactor. The fluorescence emission spectrum of the solutions was measured every 30 min during illumination of blue LED. At a defined time, interval, the concentration of the solution in the system was analyzed by spectrofluorometer.
2.5. Experimental design
The CCD was applied to investigate the effect of 8 parameters (Table 1) including irradiation time (X1), pH (X2), photocatalyst dosage (X3), rotational speed (X4), solution flow rate (X5), aeration rate (X6), TB concentration (X7) and AO concentration (X8) on the simultaneous photocatalytic degradation of TB and AO with at least number of experiments35,36 which in present research 52 experimental runs was conducted (Table 2). The RSM including mathematical and statistical techniques was employed to evaluate the individual and combined effects of 8 operation parameters. Based on the RSM following analysis of variance (ANOVA), a second-order polynomial equation was correlated the response of both dyes to significant terms.37,38 The desirability function (DF) based on the STATISTICA software (version 10.0) was applied to find the best optimum values for operational parameters to reach a maximum photocatalytic degradation efficiency. DF is a function between 0 and 1 corresponding to a completely undesirable and ideal situation which desirability close to 1.0 shows the desired conditions.39,40
Table 1 Operational parameters in CCD
Parameters |
Levels |
Low (−1) |
Central (0) |
High (+1) |
−α |
+α |
X1: time (min) |
35 |
50 |
65 |
20 |
80 |
X2: pH |
4 |
6 |
8 |
2 |
10 |
X3: photocatalyst dosage (g L−1) |
0.20 |
0.25 |
0.30 |
0.15 |
0.35 |
X4: rotational speed (rpm) |
700 |
1000 |
1300 |
400 |
1600 |
X5: solution flow rate (L min−1) |
0.30 |
0.40 |
0.50 |
0.20 |
0.6 |
X6: aeration rate (L min−1) |
20 |
30 |
40 |
10 |
50 |
X7: TB concentration (mg L−1) |
15 |
20 |
25 |
10 |
30 |
X8: AO concentration (mg L−1) |
15 |
20 |
25 |
10 |
30 |
Table 2 Experimental design matrix of process independent variables and responses
Run |
Block |
X1 |
X2 |
X3 |
X4 |
X5 |
X6 |
X7 |
X8 |
P%TB |
P%AO |
1 |
1 |
35 |
4 |
0.20 |
700 |
0.30 |
20 |
15 |
15 |
35.79 |
33.18 |
2 |
1 |
50 |
6 |
0.25 |
1000 |
0.40 |
30 |
20 |
20 |
92.81 |
90.08 |
3 |
1 |
35 |
4 |
0.30 |
1300 |
0.50 |
40 |
15 |
15 |
56.14 |
53.62 |
4 |
1 |
65 |
8 |
0.30 |
700 |
0.30 |
40 |
25 |
25 |
53.72 |
52.25 |
5 |
1 |
65 |
4 |
0.20 |
700 |
0.30 |
40 |
15 |
15 |
53.81 |
51.57 |
6 |
1 |
50 |
6 |
0.25 |
1000 |
0.40 |
30 |
20 |
20 |
92.55 |
90.19 |
7 |
1 |
35 |
8 |
0.20 |
700 |
0.50 |
40 |
25 |
15 |
25.45 |
35.01 |
8 |
1 |
65 |
8 |
0.20 |
1300 |
0.30 |
40 |
15 |
25 |
84.81 |
74.14 |
9 |
1 |
65 |
8 |
0.30 |
700 |
0.50 |
20 |
15 |
25 |
43.51 |
34.37 |
10 |
1 |
35 |
8 |
0.30 |
1300 |
0.30 |
40 |
15 |
15 |
64.27 |
62.21 |
11 |
1 |
35 |
4 |
0.20 |
700 |
0.50 |
20 |
25 |
25 |
26.58 |
24.36 |
12 |
1 |
35 |
8 |
0.20 |
1300 |
0.30 |
20 |
15 |
25 |
45.72 |
35.45 |
13 |
1 |
35 |
8 |
0.30 |
1300 |
0.50 |
40 |
15 |
15 |
63.85 |
59.76 |
14 |
1 |
35 |
4 |
0.30 |
1300 |
0.50 |
20 |
15 |
25 |
54.97 |
43.85 |
15 |
1 |
50 |
6 |
0.25 |
1000 |
0.40 |
30 |
20 |
20 |
92.25 |
90.34 |
16 |
1 |
35 |
4 |
0.30 |
700 |
0.50 |
20 |
15 |
15 |
45.78 |
43.08 |
17 |
1 |
50 |
6 |
0.25 |
1000 |
0.40 |
30 |
20 |
20 |
92.65 |
90.22 |
18 |
1 |
65 |
8 |
0.30 |
1300 |
0.50 |
20 |
25 |
15 |
73.55 |
84.16 |
19 |
1 |
35 |
8 |
0.20 |
700 |
0.50 |
20 |
25 |
25 |
24.32 |
22.26 |
20 |
1 |
65 |
8 |
0.20 |
1300 |
0.30 |
20 |
25 |
15 |
63.47 |
73.42 |
21 |
1 |
65 |
4 |
0.30 |
700 |
0.30 |
40 |
25 |
25 |
54.17 |
51.95 |
22 |
1 |
65 |
4 |
0.30 |
1300 |
0.30 |
20 |
25 |
15 |
72.68 |
84.25 |
23 |
1 |
65 |
4 |
0.20 |
1300 |
0.50 |
40 |
15 |
25 |
86.33 |
75.43 |
24 |
1 |
65 |
4 |
0.20 |
1300 |
0.50 |
20 |
25 |
15 |
63.52 |
73.18 |
25 |
1 |
35 |
4 |
0.30 |
1300 |
0.30 |
40 |
25 |
25 |
53.71 |
52.62 |
26 |
1 |
65 |
4 |
0.20 |
700 |
0.50 |
40 |
25 |
25 |
43.23 |
40.11 |
27 |
1 |
35 |
4 |
0.20 |
700 |
0.30 |
40 |
25 |
15 |
35.21 |
44.32 |
28 |
1 |
35 |
8 |
0.30 |
700 |
0.30 |
20 |
25 |
25 |
33.92 |
31.35 |
29 |
1 |
65 |
4 |
0.30 |
1300 |
0.50 |
20 |
25 |
15 |
74.41 |
86.25 |
30 |
1 |
65 |
8 |
0.30 |
700 |
0.30 |
40 |
15 |
15 |
61.77 |
58.82 |
31 |
1 |
65 |
8 |
0.20 |
700 |
0.50 |
40 |
15 |
15 |
53.31 |
51.01 |
32 |
1 |
35 |
8 |
0.30 |
700 |
0.50 |
40 |
25 |
15 |
45.15 |
43.65 |
33 |
1 |
65 |
4 |
0.30 |
700 |
0.30 |
20 |
15 |
25 |
52.04 |
42.39 |
34 |
1 |
35 |
8 |
0.20 |
1300 |
0.50 |
40 |
25 |
25 |
45.02 |
41.24 |
35 |
2 |
50 |
6 |
0.25 |
1000 |
0.20 |
30 |
20 |
20 |
73.07 |
71.65 |
36 |
2 |
50 |
6 |
0.35 |
1000 |
0.40 |
30 |
20 |
20 |
83.66 |
81.94 |
37 |
2 |
50 |
2 |
0.25 |
1000 |
0.40 |
30 |
20 |
20 |
74.07 |
71.31 |
38 |
2 |
20 |
6 |
0.25 |
1000 |
0.40 |
30 |
20 |
20 |
56.37 |
54.71 |
39 |
2 |
50 |
6 |
0.25 |
1000 |
0.40 |
50 |
20 |
20 |
92.11 |
89.67 |
40 |
2 |
80 |
6 |
0.25 |
1000 |
0.40 |
30 |
20 |
20 |
98.43 |
97.33 |
41 |
2 |
50 |
6 |
0.15 |
1000 |
0.40 |
30 |
20 |
20 |
69.38 |
67.23 |
42 |
2 |
50 |
6 |
0.25 |
1000 |
0.40 |
30 |
20 |
20 |
99.37 |
97.57 |
43 |
2 |
50 |
10 |
0.25 |
1000 |
0.40 |
30 |
20 |
20 |
78.76 |
76.42 |
44 |
2 |
50 |
6 |
0.25 |
1000 |
0.40 |
30 |
20 |
20 |
99.25 |
97.71 |
45 |
2 |
50 |
6 |
0.25 |
1000 |
0.40 |
30 |
20 |
10 |
92.31 |
98.44 |
46 |
2 |
50 |
6 |
0.25 |
1000 |
0.60 |
30 |
20 |
20 |
71.31 |
68.15 |
47 |
2 |
50 |
6 |
0.25 |
1000 |
0.40 |
30 |
30 |
20 |
76.83 |
87.04 |
48 |
2 |
50 |
6 |
0.25 |
1000 |
0.40 |
10 |
20 |
20 |
71.88 |
69.53 |
49 |
2 |
50 |
6 |
0.25 |
400 |
0.40 |
30 |
20 |
20 |
51.35 |
49.05 |
50 |
2 |
50 |
6 |
0.25 |
1600 |
0.40 |
30 |
20 |
20 |
92.22 |
89.47 |
51 |
2 |
50 |
6 |
0.25 |
1000 |
0.40 |
30 |
20 |
30 |
92.21 |
89.39 |
52 |
2 |
50 |
6 |
0.25 |
1000 |
0.40 |
30 |
10 |
20 |
98.78 |
93.82 |
3. Results and discussion
3.1. Characterization of samples
Characterization of new photocatalyst was undertaken by XRD, FE-SEM, SEM, PL and DRS analysis. The powder XRD pattern of HKUST-1 (Fig. 4a) shows three sharp peaks at 2θ of 44°, 51° and 74° assigned to (111), (200) and (220) which confirm crystal planes of the pure solid phase copper (PDF card no. 04-0836). In comparison to the pure HKUST-1 sample, the intensity of the main diffraction peaks of HKKUST-1 MOF in the composites lead to decrease in other peaks observed in the composite patterns which is corresponded to formation of BiPO4/Bi2S3. The XRD pattern of BiPO4/Bi2S3-HKUST-1-MOF (Fig. 4b) shows the main peak positions appear at 2θ = 14.6, 20.06, 25.47, 29.5, 31.3, 37.85, 39.38, 41.86, 44.92, 52.38, 54.67 and 74.33° were marked as (100), (101), (110), (200), (102), (012), (112), (210), (211), (300), (220), (310) and (322) planes of BiPO4, respectively. It is apparent that all the obtained peaks were successfully indexed to the hexagonal crystalline structure of BiPO4 correspond to standard pattern (JCPDS no. 00-015-0766). As well as, in these samples the main peak positions appear at 2θ = 16.51, 18.16, 25.42, 29.16, 32.05, 36.19, 39.31, 42.82, 46.78, 49.78, 54.23 and 63.20° were corresponded to (200), (101), (310), (320), (400), (420), (041), (421), (501), (610), (061) and (551) planes of Bi2S3, respectively. It is apparent that all the obtained peaks were successfully indexed to the orthorhombic crystalline structure of Bi2S3 in with the standard pattern (JCPDS no. 00-003-0362).
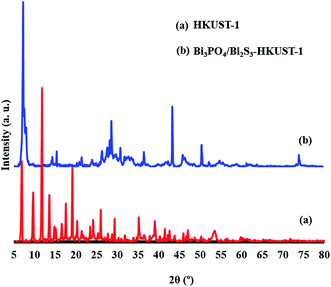 |
| Fig. 4 XRD pattern of HKUST-1 MOF (a) and BiPO4/Bi2S3-HKUST-1-MOF (b). | |
The morphology of HKUST-1 MOF and BiPO4/Bi2S3-HKUST-1-MOF are studied by SEM and FE-SEM micrograph (Fig. 5) that shows approximate HKUST-1 MOF size of about 1.5 μm (Fig. 5a). The FE-SEM image of BiPO4/Bi2S3-HKUST-1-MOF (Fig. 5b) show higher surface area of BiPO4/Bi2S3 composite with HKUST-1 which is related to its nanorod structure and expected to increase its efficiency for photodegradation of dyes. The EDS analysis reveal contribution of elements of C, O, Cu, Bi, S and P in BiPO4/Bi2S3-HKUST-1-MOF structure (Fig. 5c).
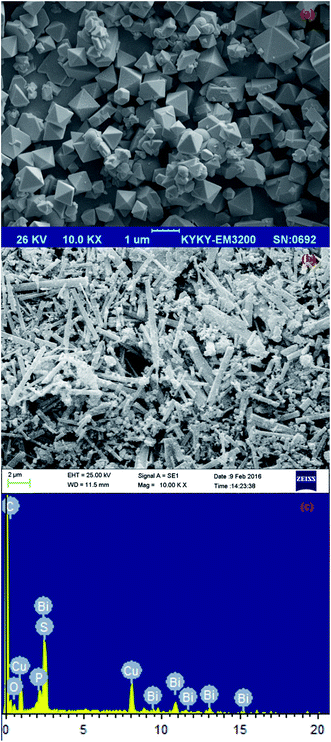 |
| Fig. 5 SEM image of HKUST-1 MOF (a) and BiPO4/Bi2S3-HKUST-1-MOF (b) and EDS of BiPO4/Bi2S3-HKUST-1-MOF (c). | |
Diffuse reflectance spectra analysis (Fig. 6a) based on well-known equation following plotting (αhν)2 versus hν and tracing the figures to intercept (hν = 0) show that direct band gap was estimated to be 2.6 eV and 1.97 eV for HKKUST-1 and BiPO4/Bi2S3-HKUST-1-MOF, respectively.
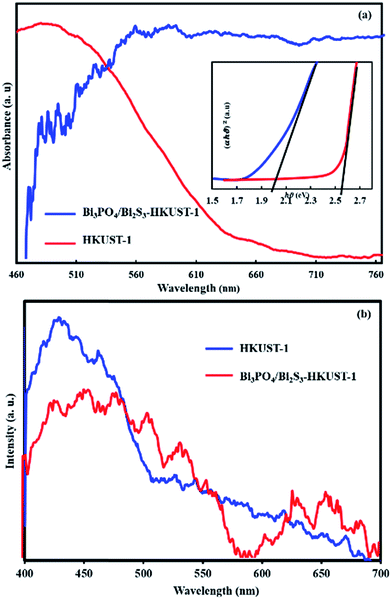 |
| Fig. 6 DRS (a) and PL (b) of HKUST-1-MOF and BiPO4/Bi2S3-HKUST-1-MOF (the plot of (αhν)2 versus hν for calculating the band gap of samples inset in this (a)). | |
The comparison of PL spectra (Fig. 6b) of HKUST-1 and BiPO4/Bi2S3-HKUST-1-MOF composite at room temperature shows broad blue-green emission peak at maximum wavelength of 430 nm. It was found that PL emission intensity of the BiPO4/Bi2S3-HKUST-1-MOF composite was dramatically weakened compared with HKUST-1, and this peak was shifted to higher wavelength which clearly indicates recombination of photogenerated charge carriers between the hybrid orbital is greatly inhibited by the heterojunction nanocomposite.41,42 In other words, the coupling of HKUST-1 and BiPO4/Bi2S3 is helpful to separate the photogenerated charge carriers. The slower recombination process of photogenerated charges (the less the PL intensity) can facilitate the enhancement of photocatalytic activity of BiPO4/Bi2S3-HKUST-1-MOF composite.
The textural and physicochemical properties of HKUST-1 and BiPO4/Bi2S3-HKUST-1-MOF composites such as the pore diameter (BJH), the BET surface area and total pore volume (Vtotal), are given in Table 3. HKUST-1 and BiPO4/Bi2S3-HKUST-1-MOF nitrogen adsorption–desorption measurements indicate BET surface area of 855 (taken from our previous report) and 670 m2 g−1, respectively. The decrease in the BET surface area, the mesoporous volume and average pore diameter after the modification indicate the successful formation of composite. The high BET surface area, mesoporous volume and average pore diameter of BiPO4/Bi2S3-HKUST-1-MOF means the composite can facilitate the enhancement of photocatalytic activity (Table 3).
Table 3 Textural and physicochemical properties of samples
Sample |
BET surface area (m2 g−1) |
Pore diameter (BJH) (nm) |
Total pore volume (m3 g−1) |
HKUST-1-MOF |
855 |
3.50 |
1.32 |
BiPO4/Bi2S3-HKUST-1-MOF |
670 |
2.61 |
1.10 |
3.2. Analysis of variance (ANOVA)
Analysis of variance was applied to evaluate the significance of the quadratic model based on sequential model sum of squares, lack of fit and model summary statistics.43 For each individual parameter and their interactions, the Prob > F value of p < 0.05 and lack of fit > 0.05 indicate that model is significant.44 ANOVA of the experimental data confirms that the model Prob > F is less than 0.05 as well as lack of fit > 0.05 and model was significant (Table 4). Based on the ANOVA a second-order polynomial equation was achieved at 95% confidence level (p < 0.05) for each photocatalytic degradation of TB and AO as responses as follow: |
P%TB = +95.90 + 10.52X1 + 1.21X2 + 3.60X3 + 10.22X4 − 0.50X5 + 5.06X6 − 5.49X7 − 0.77X1X2 − 3.00X1X3 + 7.45X1X4 + 0.96X1X5 + 1.38X1X6 − 2.27X1X7 − 0.92X1X8 − 1.21X2X3 + 2.44X2X4 − 0.67X2X5 + 1.77X2X6 + 0.42X2X7 + 1.88X3X4 − 1.27X3X5 + 2.31X3X6 + 1.80X3X7 − 3.50X3X8 + 2.81X4X5 − 0.84X4X6 + 1.81X4X7 − 2.57X4X8 − 1.46X5X6 − 2.54X5X7 + 0.72X5X8 + 4.76X6X7 − 1.45X6X8 − 1.07X7X8 − 5.45X12 − 5.69X22 − 5.67X32 − 6.85X42 − 6.75X52 − 4.30X62 − 2.85X72 − 1.73X82
| (2) |
|
P%AO = 93.93 + 10.66X1 + 1.28X2 + 3.68X3 + 10.10X4 − 0.89X5 + 5.04X6 − 1.69X7 − 2.26X8 − 1.37X1X2 − 1.16X1X3 + 8.35X1X4 + 0.96X1X5 − 0.14X1X6 − 1.03X1X7 − 0.28X1X8 − 0.93X2X3 + 2.60X2X4 − 1.66X2X5 + 1.25X2X6 + 0.57X2X7 + 0.29X2X8 + 3.20X3X4 − 1.50X3X5 + 1.86X3X6 + 0.84X3X7 − 2.41X3X8 + 2.13X4X5 − 1.77X4X6 + 2.96X4X7 − 0.99X4X8 − 1.67X5X6 − 3.17X5X7 − 0.14X5X8 + 2.47X6X7 − 1.11X6X8 − 0.81X7X8 − 5.41X12 − 5.95X22 − 5.77X32 − 7.10X42 − 6.94X52 − 4.52X62 − 1.81X72 − 0.94X82
| (3) |
where P%TB and P%AO represents the process responses (i.e., photocatalytic degradation percentage) for TB and AO, respectively.
Table 4 Analysis of variance values of the fitted polynomial model for photocatalytic degradation process
Source of variation |
DFa |
TB |
AO |
Sum of squares |
Mean square |
F-Value |
p-Value |
Sum of squares |
Mean square |
F-Value |
p-Value Prob > F |
Degree of freedom. |
Block |
1 |
6825.11 |
6825.11 |
|
|
6839.21 |
6839.21 |
|
|
Model |
44 |
16 867.23 |
383.35 |
8.02 × 103 |
<0.0001 |
18 435.69 |
418.99 |
53 035.01 |
<0.0001 |
X1 |
1 |
884.52 |
884.52 |
18 507.31 |
<0.0001 |
908.23 |
908.23 |
1.15 × 105 |
<0.0001 |
X2 |
1 |
13.69 |
13.69 |
286.35 |
<0.0001 |
15.37 |
15.37 |
1945.29 |
<0.0001 |
X3 |
1 |
111.64 |
111.64 |
2.34 × 103 |
<0.0001 |
116.93 |
116.93 |
14 800.49 |
<0.0001 |
X4 |
1 |
835.18 |
835.18 |
17 474.88 |
<0.0001 |
816.89 |
816.89 |
1.03 × 105 |
<0.0001 |
X5 |
1 |
3.1 |
3.1 |
64.79 |
0.0002 |
9.65 |
9.65 |
1221.23 |
<0.0001 |
X6 |
1 |
204.63 |
204.63 |
4281.51 |
<0.0001 |
202.81 |
202.81 |
25 671.12 |
<0.0001 |
X7 |
1 |
240.9 |
240.9 |
5040.5 |
<0.0001 |
22.98 |
22.98 |
2909.28 |
<0.0001 |
X8 |
1 |
5.00 × 10−3 |
5.00 × 10−3 |
0.1 |
0.7573 |
40.95 |
40.95 |
5183.5 |
<0.0001 |
X1X2 |
1 |
3.6 |
3.6 |
75.41 |
0.0001 |
11.59 |
11.59 |
1467.53 |
<0.0001 |
X1X3 |
1 |
36.31 |
36.31 |
759.74 |
<0.0001 |
5.46 |
5.46 |
691.39 |
<0.0001 |
X1X4 |
1 |
144.85 |
144.85 |
3030.78 |
<0.0001 |
182.14 |
182.14 |
23 055.08 |
<0.0001 |
X1X5 |
1 |
3.16 |
3.16 |
66.16 |
0.0002 |
3.15 |
3.15 |
399.07 |
<0.0001 |
X1X6 |
1 |
5.09 |
5.09 |
106.41 |
<0.0001 |
0.054 |
0.054 |
6.84 |
0.0399 |
X1X7 |
1 |
7.31 |
7.31 |
152.97 |
<0.0001 |
1.51 |
1.51 |
191.06 |
<0.0001 |
X1X8 |
1 |
2.98 |
2.98 |
62.46 |
0.0002 |
0.27 |
0.27 |
34.29 |
0.0011 |
X2X3 |
1 |
10.42 |
10.42 |
218.07 |
<0.0001 |
6.08 |
6.08 |
770.19 |
<0.0001 |
X2X4 |
1 |
32.06 |
32.06 |
670.88 |
<0.0001 |
36.16 |
36.16 |
4577.16 |
<0.0001 |
X2X5 |
1 |
1.93 |
1.93 |
40.44 |
0.0007 |
11.74 |
11.74 |
1485.57 |
<0.0001 |
X2X6 |
1 |
17.19 |
17.19 |
359.65 |
<0.0001 |
8.49 |
8.49 |
1074.7 |
<0.0001 |
X2X7 |
1 |
0.84 |
0.84 |
17.53 |
0.0058 |
1.51 |
1.51 |
191.41 |
<0.0001 |
X2X8 |
1 |
0.055 |
0.055 |
1.15 |
0.3242 |
0.69 |
0.69 |
87.11 |
<0.0001 |
X3X4 |
1 |
10.81 |
10.81 |
226.12 |
<0.0001 |
31.5 |
31.5 |
3986.95 |
<0.0001 |
X3X5 |
1 |
4.58 |
4.58 |
95.93 |
<0.0001 |
6.47 |
6.47 |
818.79 |
<0.0001 |
X3X6 |
1 |
23.57 |
23.57 |
493.07 |
<0.0001 |
15.37 |
15.37 |
1945.33 |
<0.0001 |
X3X7 |
1 |
9.68 |
9.68 |
202.5 |
<0.0001 |
2.08 |
2.08 |
263.91 |
<0.0001 |
X3X8 |
1 |
66.26 |
66.26 |
1386.33 |
<0.0001 |
31.38 |
31.38 |
3972.15 |
<0.0001 |
X4X5 |
1 |
35.65 |
35.65 |
745.83 |
<0.0001 |
20.46 |
20.46 |
2590.16 |
<0.0001 |
X4X6 |
1 |
2.23 |
2.23 |
46.7 |
0.0005 |
9.85 |
9.85 |
1246.36 |
<0.0001 |
X4X7 |
1 |
6.07 |
6.07 |
127.08 |
<0.0001 |
16.28 |
16.28 |
2060.28 |
<0.0001 |
X4X8 |
1 |
18.31 |
18.31 |
383.21 |
<0.0001 |
2.72 |
2.72 |
344.52 |
<0.0001 |
X5X6 |
1 |
28.58 |
28.58 |
598.02 |
<0.0001 |
37.61 |
37.61 |
4760.55 |
<0.0001 |
X5X7 |
1 |
31.32 |
31.32 |
655.35 |
<0.0001 |
48.84 |
48.84 |
6181.8 |
<0.0001 |
X5X8 |
1 |
4.13 |
4.13 |
86.49 |
<0.0001 |
0.17 |
0.17 |
21.09 |
0.0037 |
X6X7 |
1 |
39.86 |
39.86 |
834.02 |
<0.0001 |
10.73 |
10.73 |
1358.69 |
<0.0001 |
X6X8 |
1 |
3.67 |
3.67 |
76.72 |
0.0001 |
2.16 |
2.16 |
272.96 |
<0.0001 |
X7X8 |
1 |
2.48 |
2.48 |
5.20 × 101 |
0.0004 |
1.42 |
1.42 |
179.26 |
<0.0001 |
X12 |
1 |
947.82 |
947.82 |
1.98 × 104 |
<0.0001 |
934.67 |
934.67 |
1.18 × 105 |
<0.0001 |
X22 |
1 |
1035.43 |
1035.43 |
2.17 × 104 |
<0.0001 |
1130.07 |
1130.07 |
1.43 × 105 |
<0.0001 |
X32 |
1 |
1025.91 |
1025.91 |
2.15 × 104 |
<0.0001 |
1062.73 |
1062.73 |
1.35 × 105 |
<0.0001 |
X42 |
1 |
1499.12 |
1499.12 |
3.14 × 104 |
<0.0001 |
1609.74 |
1609.74 |
2.04 × 105 |
<0.0001 |
X52 |
1 |
1455.14 |
1455.14 |
30 446.75 |
<0.0001 |
1538.02 |
1538.02 |
1.95 × 105 |
<0.0001 |
X62 |
1 |
590.28 |
590.28 |
12 350.84 |
<0.0001 |
651.03 |
651.03 |
82 405.59 |
<0.0001 |
X72 |
1 |
258.84 |
258.84 |
5415.88 |
<0.0001 |
104.38 |
104.38 |
13 212.49 |
<0.0001 |
X82 |
1 |
95.95 |
9.60 × 101 |
2007.61 |
<0.0001 |
28.03 |
28.03 |
3547.33 |
<0.0001 |
Residual |
6 |
0.29 |
4.80 × 10−2 |
|
|
0.047 |
7.90 × 10−3 |
|
|
Lack of fit |
2 |
0.11 |
0.056 |
1.3 |
0.3678 |
3.33 × 10−3 |
1.66 × 10−3 |
0.15 |
0.8646 |
Pure error |
4 |
0.17 |
0.043 |
|
|
0.044 |
0.011 |
|
|
Cor total |
51 |
23 692.62 |
|
|
|
25 274.95 |
|
|
|
3.3. 3D response surface graphs
The relationship between most statistical significant operational parameters was investigated using three-dimensional (3D) response surface graphs (Fig. 7). Results show that rotational speed has a positive effect on photocatalytic degradation percentage (Fig. 7b). Higher rotational speed causes to split the thick solution film into micro- or nano-droplets and thin film. In addition, it increases the renewal rate of liquid–solid interface. Consequently it leads to an increase in interfacial surface area between photocatalyst particles and pollutants which significantly improves the mass transfer and mixing processes.45,46 Moreover, the increase in rotational speed improves the dispersion and distribution of oxygen inserted in the solution, which leads to the enhancement in radical generation. The investigation on the influence of solution flow rate (Fig. 7a) showed that the photodegradation efficiency is not considerable at lower solution flow rates, which is attributed to the non-uniform distribution of solution in porous bed. By increasing the flow rate, the solution exits from distributor holes as a jet stream and collides to rotating bed with higher speed, which causes the breaking of thick films to thin layers and droplets and thus a larger interface between photocatalyst particles and dyes is created that enhances photodegradation. Results show that the efficiency decreases as flow rate exceeds a certain value. This behavior is probably due to the increase in the residence time of reactant in the reactor under illumination in addition to the creation of thick films in higher flows. As known, there is a depth limit for the penetration of light in films. Therefore, photocatalysts located behind this limit cannot be activated and thus the photodegradation percentage decreases. Initial dyes concentration negatively affects the photodegradation efficiency (Fig. 7b and c). The higher the concentration of dyes, the lower the photodegradation efficiency is achieved which is due to the reduction in the number of available and activated photocatalyst sites and the enhancement in the light screening by the dye molecules. Following the investigation on photocatalytic degradation at pH values in the range of 2–10 (Fig. 7d), the maximum photocatalytic degradation percentage of dyes was achieved at pH of 6.0. As shown in Fig. 7d, at high photocatalyst dosages, the photocatalytic degradation increases due to the increase in available surface area and larger generation of OH radicals which enhances the mass transfer and process efficiency. For photocatalyst dosages higher than 0.25 g L−1, lower degradation percentage is achieved because the light penetration depth decreases due to more light scattering and absorption. The effect of aeration rate on the photocatalytic degradation percentage was found to be positive (Fig. 7c). Higher aeration rate leads to more mixing and turbulence in the reactor that causes an increase in contact between free OH-radicals generated during the illumination of blue light and dyes molecules. Moreover, available dissolved oxygen may trap the electrons from hydroxyl radical, which leads to the creation of more electron–holes on the photocatalyst surface. Irradiation time positively affected the photocatalytic degradation (Fig. 7a).
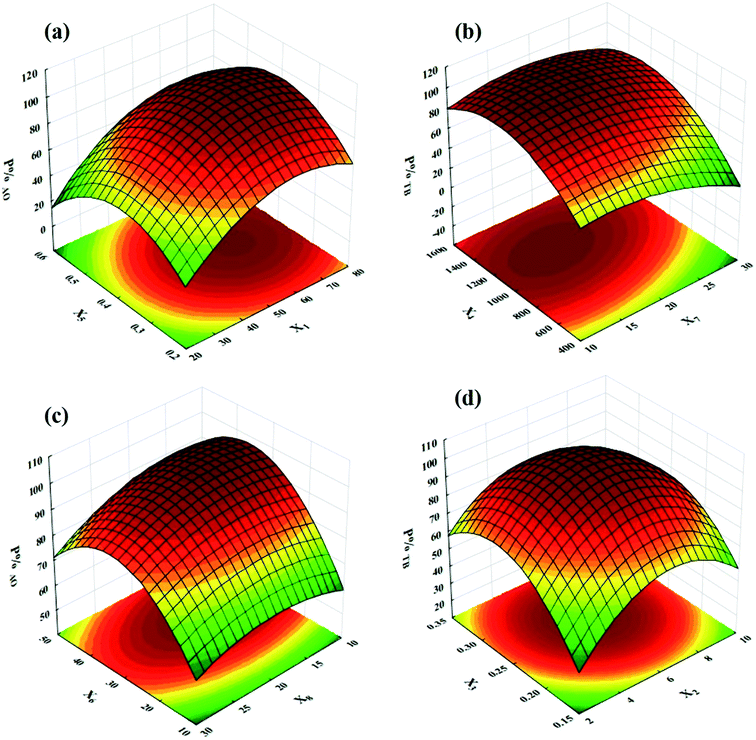 |
| Fig. 7 Response surface (3D) plots for photocatalytic degradation process versus between independent variables. (a) Solution flow rate (X5) with irradiation time (X1); (b) rotational speed (X4) with TB concentration (X7); (c) aeration rate (X6) with AO concentration (X8); (d) photocatalyst dosage (X3) with pH (X2). | |
3.4. Optimization
The desirability function of response for each dye versus operational parameters was evaluated using STATISTICA software (ver. 10.0) to obtain the optimum values of parameters at which the photocatalytic degradation efficiency is maximum. It is well-known that the desirability is a function that vary from 0.0 (undesirable) to 1.0 (very desirable).47 From the desirability profile for simultaneous photocatalytic degradation of TB and AO (Fig. 8), the optimum values were found to be 65 min, 6, 0.25 g L−1, 1300 rpm, 0.40 L min−1, 35 L min−1, 25 mg L−1 and 25 mg L−1 for the irradiation time, pH, photocatalyst dosage, rotational speed, solution flow rate, aeration rate as well as the initial TB and AO concentrations, respectively. At optimum condition, the photocatalytic degradation percentages of TB and AO were found to be 99.37% and 98.44%, respectively with overall desirability of 1.0.
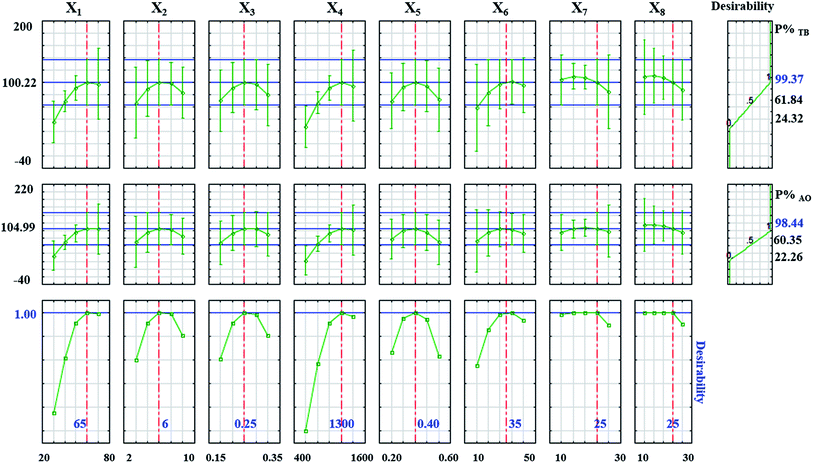 |
| Fig. 8 Profiles for predicated values and desirability function for photocatalytic percentage of binary mixture of dyes (using rotating packed bed reactor). Dashed line showed optimized parameters values. | |
3.5. OH˙ radical's generation results for samples
The contents of OH˙ radicals over HKUST-1 and BiPO4/Bi2S3-HKUST-1-MOF under blue light irradiation were investigated via a fluorescence process at a different time (see Fig. 9). As seen that the fluorescence intensity at 433 nm increased linearly with photoreaction time demonstrating that OH˙ radicals were indeed generated in the HKUST-1 and BiPO4/Bi2S3-HKUST-1-MOF, while, the OH˙ radicals generated for BiPO4/Bi2S3-HKUST-1-MOF is larger than to HKUST-1 (see Fig. 9a and b). Finally, for comparison of OH-radicals generated in the rotating packed bed photocatalytic rector than to generated in the conventional photoreactor the above OH trapping experiments was performed and results are shown in Fig. 9c and d. As seen that the OH˙ radicals generated for BiPO4/Bi2S3-HKUST-1-MOF in proposed rotating packed bed photoreactor is larger than to conventional photoreactor (see Fig. 9c and d).
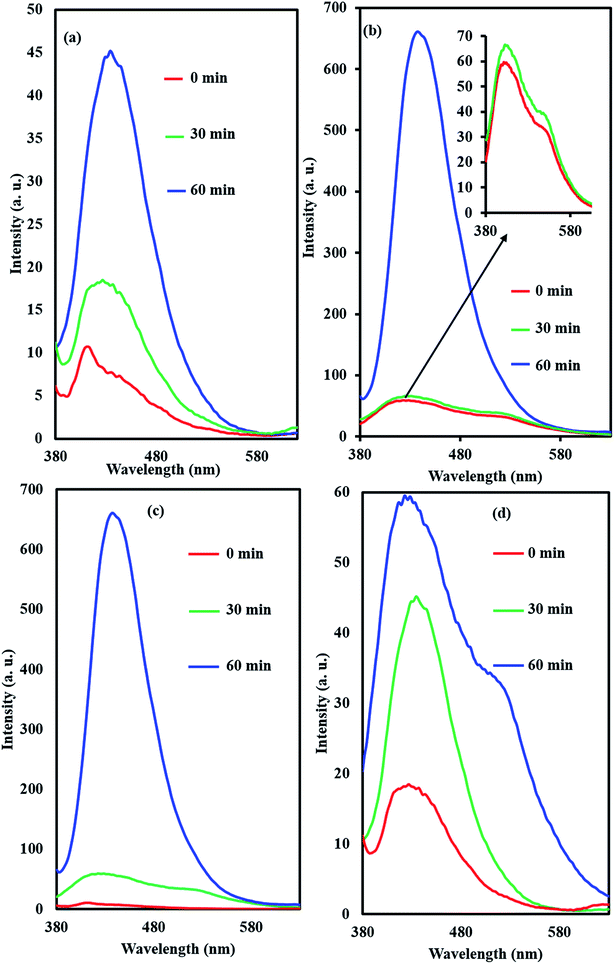 |
| Fig. 9 OH˙ trapping photoluminescence (PL) spectra of HKUST-1-MOF (a) and BiPO4/Bi2S3-HKUST-1-MOF (b) on TA solution under blue light illumination in proposed rotating packed bed reactor and OH-radicals generated of BiPO4/Bi2S3-HKUST-1-MOF in the rotating packed bed photocatalytic rector (c) and the conventional photoreactor (d) under the optimum test-conditions. | |
3.6. Kinetics study
Investigation of photocatalytic degradation rate based on kinetics studies is an essential step in the design and optimization of photocatalytic reactor for scale-up process.7,48 Moreover, the selection of an appropriate kinetic model can lead to the minimization of non-illuminated reactor volume. The photocatalytic degradation process obeyed the following pseudo first order kinetics based on Langmuir–Hinshelwood (L–H) model which is the most common kinetic model for the degradation process of many organic compounds including dyes, pesticides, herbicides and phenolic compounds:49–51 |
 | (4) |
where C is the concentration (mg L−1) and k (min−1) is the apparent rate constant. Integrating eqn (4), the following concentration–time equation is obtained: |
 | (5) |
This linear form can be used to fit the experimental data by plotting ln(C0/Ct) versus time, while slope of this equation equals the apparent rate constant for each process (Fig. 10).
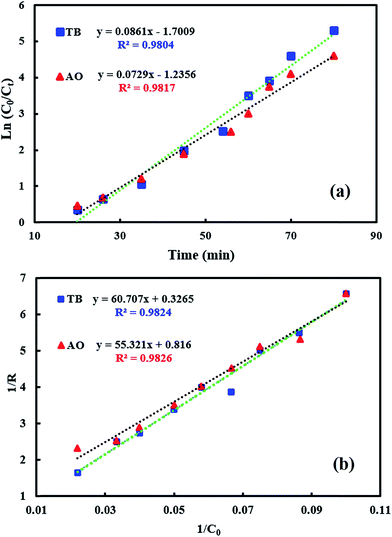 |
| Fig. 10 Plot of the Langmuir–Hinshelwood (L–H) kinetics model. (a) ln(C0/Ct) vs. t, (b) 1/R vs. 1/C0. | |
The well fitted empirical data with R2 > 0.98 indicated that the empirical data obey to pseudo-first order kinetics. L–H kinetic model can describe the reaction at solid–liquid interface between photocatalyst particles and dyes mixture as follows:52
|
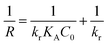 | (6) |
where
kr (mg min
−1 L
−1) is the apparent photodegradation rate constant and
KA (L mg
−1) is defined as

.
K and
Ks are the coefficients of adsorption of the dyes and the solvent, respectively.
The applicability of L–H model was evaluated by plotting the inverse of the initial rate (1/R) against the inverse of the initial concentration (1/C0) of each dye (Fig. 10b). A linear plot provides the intercept and slope attributed to 1/kr and 1/krKA, respectively. According to eqn (5) and (6), L–H kinetic model well fitted experimental data.
3.7. Intensification process
Performance of the photocatalytic rotating packed-bed reactor for intensifying the photodegradation process was evaluated by its comparison with that of a conventional reactor at same conditions. Therefore, a conventional photocatalytic reactor was designed with same size and volume (Fig. 11) followed by running the experiments at same condition. All part of conventional reactor is similar to rotating packed-bed except it has no rotating section. The effect of operational parameters including illumination time (X1), pH (X2), photocatalyst dosage (X3), solution flow rate (X4), aeration rate (X5), TB concentration (X6) and AO concentration (X7) on the photocatalytic dyes degradation was investigated. In case of conventional reactor, the optimal photocatalytic degradation percentages of TB and AO were found to be 81.22% and 83.78% for TB and AO, respectively (Fig. 12). These efficiencies were achieved at 200 min, 6, 0.30 g L−1, 0.30 L min−1, 40 L min−1 and 25 mg L−1 for time, pH, photocatalyst dosage, solution flow rate, aeration rate and concentration of each dye, respectively. Compared to rotating packed bed, at same condition, conventional reactor consumed more photocatalyst and required more irradiation time, which means that rotating packed bed is more efficient and cost-effective. Moreover, rotating packed bed can operate at higher flow rate. These advantages are attributed to the centrifugal forces generated by high rotational speed leading to intensification of mixing and mass transfer operations as mentioned above.
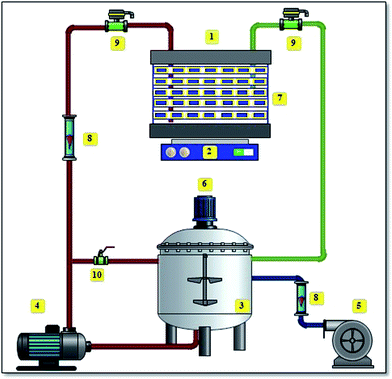 |
| Fig. 11 Conventional photocatalytic reactor. (1) Housing; (2) magnet stirrer; (3) reservoir tank; (4) pump; (5) aeration pump; (6) stirrer; (7) blue strip LED; (8) flowmeter; (9) sampling point; (10) control valve. | |
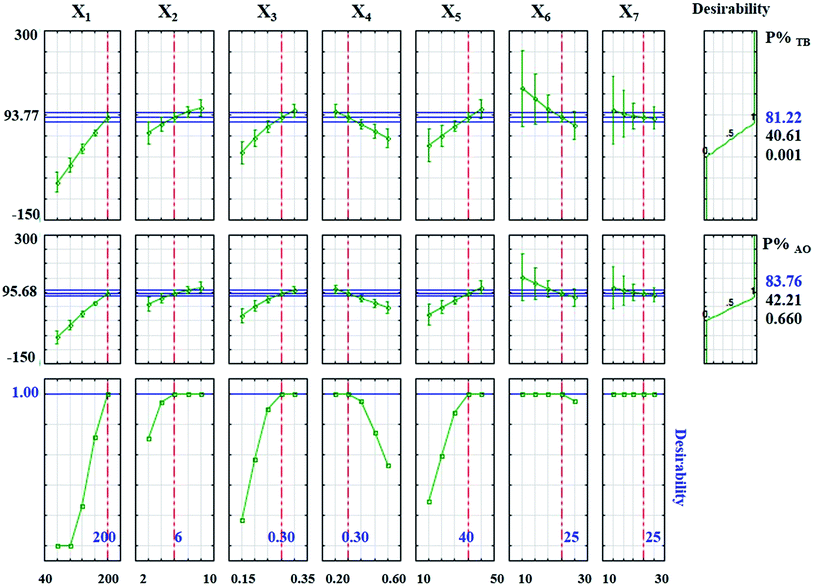 |
| Fig. 12 Profiles for predicated values and desirability function for photocatalytic percentage of binary mixture of dyes (using conventional reactor). Dashed line showed optimized parameters values. | |
3.8. Stability and reusability
The investigation of stability and reusability of BiPO4/Bi2S3-HKUST-1-MOF was carried out the additional experiments to degrade TB and AO for 4.0 times at optimum condition (see Fig. 13). After every cycle, the catalyst was washed and heated at 50 °C for 10 h, then was used in to next cycle photodegradation procedure. As seen, TB and AO dyes is quickly degraded after every injection of the TB and AO binary solution, and the BiPO4/Bi2S3-HKUST-1-MOF photocatalyst is good stable under repeated photocatalytic reaction with a nearly constant photodecomposition rate. These results revealed that BiPO4/Bi2S3-HKUST-1-MOF photocatalyst is a very stable under visible-light photocatalyst due to effective anchoring of BiPO4/Bi2S3 on HKUST-1 MOF would inhibit leaching of BiPO4 and Bi2S3 into the solution and hence increase the stability because of structural integrity. Therefore, it can be proposed that proposed photocatalyst is a stable and superior catalyst with enhanced photocatalytic activity.
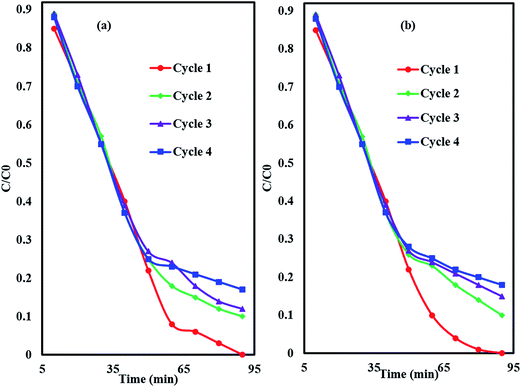 |
| Fig. 13 The cycling degradation efficiency for TB (a) and AO (b) of BiPO4/Bi2S3-HKUST-1-MOF under visible-light irradiation. | |
4. Conclusion
The simultaneous photocatalytic degradation of TB and AO was successfully performed using rotating packed bed photocatalytic reactor in the presence of BiPO4/Bi2S3-HKUST-1-MOF as a novel visible light-driven photocatalyst. The working pH was found to be 6.0 as neutral pH is an advantage of this work. This makes the process more environmental-friendly, practical with no requirement on the use of specific material for reactor construction. On the other hand, the performance of rotating packed bed reactor was compared with a conventional one at same conditions which proved the rotating packed bed reactor to be more efficient because of its lower consumption of photocatalyst and shorter illumination time. Moreover, it is worth mentioning that the use of visible light instead of UV is advantageous because of less energy consumption and more environmental-friendly entity.
Acknowledgements
The authors thank the Research Council of the Yasouj University and Iran National Science Foundation (Grant No. 94/
/41301) for their financial support.
References
- R. Chauhan, A. Kumar and R. P. Chaudhary, J. Lumin., 2014, 145, 6–12 CrossRef CAS.
- M. Mittal, M. Sharma and O. Pandey, Sol. Energy, 2014, 110, 386–397 CrossRef CAS.
- F. Ahmedchekkat, M. S. Medjram, M. Chiha and A. M. A. Al-Bsoul, Chem. Eng. J., 2011, 178, 244–251 CrossRef CAS.
- N. Ghows and M. Entezari, Ultrason. Sonochem., 2013, 20, 386–394 CrossRef CAS PubMed.
- M. Shirzad-Siboni, M. Farrokhi, R. Darvishi Cheshmeh Soltani, A. Khataee and S. Tajassosi, Ind. Eng. Chem. Res., 2014, 53, 1079–1087 CrossRef CAS.
- M. N. Chong, B. Jin, C. W. Chow and C. Saint, Water Res., 2010, 44, 2997–3027 CrossRef CAS PubMed.
- N. Kaur, S. Kaur and V. Singh, Desalin. Water Treat., 2015, 1–10 CrossRef.
- X. Meng, Z. Zhang and X. Li, J. Photochem. Photobiol., C, 2015, 24, 83–101 CrossRef CAS.
- Z. Rahmani, M. Kermani, M. Gholami, A. J. Jafari and N. M. Mahmoodi, Iran. J. Environ. Health Sci. Eng., 2012, 9, 1 CrossRef PubMed.
- W.-K. Jo and R. J. Tayade, Chin. J. Catal., 2014, 35, 1781–1792 CrossRef CAS.
- A. Manassero, M. L. Satuf and O. M. Alfano, Environ. Sci. Pollut. Res., 2015, 22, 926–937 CrossRef CAS PubMed.
- N. Stamatis, M. Antonopoulou and I. Konstantinou, Catal. Today, 2015, 252, 93–99 CrossRef CAS.
- A. K. Ray and A. A. Beenackers, Catal. Today, 1998, 40, 73–83 CrossRef CAS.
- W. Z. Jiao, Y. Z. Liu and G. S. Qi, Ind. Eng. Chem. Res., 2010, 49, 3732–3740 CrossRef CAS.
- K. Guo, Z. Zhang, H. Luo, J. Dang and Z. Qian, Ind. Eng. Chem. Res., 2014, 53, 4052–4058 CrossRef CAS.
- Y. Luo, G.-W. Chu, H.-K. Zou, Z.-Q. Zhao, M. P. Dudukovic and J.-F. Chen, Ind. Eng. Chem. Res., 2012, 51, 16320–16325 CrossRef CAS.
- Z.-y. Yan, C. Lin and Q. Ruan, Ind. Eng. Chem. Res., 2012, 51, 10472–10481 CrossRef CAS.
- Y.-S. Chen, C.-C. Lin and H.-S. Liu, Ind. Eng. Chem. Res., 2005, 44, 1043–1051 CrossRef CAS.
- S. Mosleh, M. Rahimi, M. Ghaedi, K. Dashtian and S. Hajati, RSC Adv., 2016, 6, 17204–17214 RSC.
- X. Wang and T.-T. Lim, Appl. Catal., B, 2010, 100, 355–364 CrossRef CAS.
- H. Hossaini, G. Moussavi and M. Farrokhi, Water Res., 2014, 59, 130–144 CrossRef CAS PubMed.
- S. Dominguez, P. Ribao, M. J. Rivero and I. Ortiz, Appl. Catal., B, 2014, 178, 165–169 CrossRef.
- J.-J. Du, Y.-P. Yuan, J.-X. Sun, F.-M. Peng, X. Jiang, L.-G. Qiu, A.-J. Xie, Y.-H. Shen and J.-F. Zhu, J. Hazard. Mater., 2011, 190, 945–951 CrossRef CAS PubMed.
- C. G. Silva, A. Corma and H. García, J. Mater. Chem., 2010, 20, 3141–3156 RSC.
- J. Saien, H. Delavari and A. Solymani, J. Hazard. Mater., 2010, 177, 1031–1038 CrossRef CAS PubMed.
- H. Wang, D. Peng, T. Chen, Y. Chang and S. Dong, Ceram. Int., 2016, 42, 4406–4412 CrossRef CAS.
- A. Yousef, R. M. Brooks, M. El-Halwany, M. H. EL-Newehy, S. S. Al-Deyab and N. A. Barakat, Ceram. Int., 2016, 42, 1507–1512 CrossRef CAS.
- Z. Zhang, W. Wang, L. Wang and S. Sun, ACS Appl. Mater. Interfaces, 2012, 4, 593–597 CAS.
- X. Gao, H. B. Wu, L. Zheng, Y. Zhong, Y. Hu and X. W. D. Lou, Angew. Chem., 2014, 126, 6027–6031 CrossRef.
- S. E. Mousavinia, S. Hajati, M. Ghaedi and K. Dashtian, Phys. Chem. Chem. Phys., 2016, 18, 11278–11288 RSC.
- J.-K. Im, I.-H. Cho, S.-K. Kim and K.-D. Zoh, Desalination, 2012, 285, 306–314 CrossRef CAS.
- M. Jamshidi, M. Ghaedi, K. Dashtian, A. M. Ghaedi, S. Hajati, A. Gudarzi and E. Alipanahpour, Spectrochim. Acta, Part A, 2016, 153, 257–267 CrossRef CAS PubMed.
- S. Mosleh, M. R. Rahimi, M. Ghaedi, K. Dashtian and S. Hajati, RSC Adv., 2016, 6, 61516–61528 RSC.
- D. Ge, Z. Zeng, M. Arowo, H. Zou, J. Chen and L. Shao, Chemosphere, 2016, 146, 413–418 CrossRef CAS PubMed.
- A. Zuorro, M. Fidaleo and R. Lavecchia, J. Environ. Manage., 2013, 127, 28–35 CrossRef CAS PubMed.
- F. Gomez and M. Sartaj, Int. Biodeterior. Biodegrad., 2014, 89, 103–109 CrossRef CAS.
- M. Asadollahzadeh, H. Tavakoli, M. Torab-Mostaedi, G. Hosseini and A. Hemmati, Talanta, 2014, 123, 25–31 CrossRef CAS PubMed.
- A. Asfaram, M. Ghaedi, S. Hajati, M. Rezaeinejad, A. Goudarzi and M. K. Purkait, J. Taiwan Inst. Chem. Eng., 2015, 53, 80–91 CrossRef CAS.
- S. Petrović, S. Stojadinović, L. Rožić, N. Radić, B. Grbić and R. Vasilić, Surf. Coat. Technol., 2015, 269, 250–257 CrossRef.
- S. Mosleh, M. R. Rahimi, M. Ghaedi and K. Dashtian, Ultrason. Sonochem., 2016, 32, 387–397 CrossRef CAS PubMed.
- W.-S. Wang, H. Du, R.-X. Wang, T. Wen and A.-W. Xu, Nanoscale, 2013, 5, 3315–3321 RSC.
- Q. Zhu, W.-S. Wang, L. Lin, G.-Q. Gao, H.-L. Guo, H. Du and A.-W. Xu, J. Phys. Chem. C, 2013, 117, 5894–5900 CAS.
- T. Olmez-Hanci, I. Arslan-Alaton and G. Basar, J. Hazard. Mater., 2011, 185, 193–203 CrossRef CAS PubMed.
- D. Hou, R. Goei, X. Wang, P. Wang and T.-T. Lim, Appl. Catal., B, 2012, 126, 121–133 CrossRef CAS.
- Q. Wei, S. Qiao, B. Sun, H. Zou, J. Chen and L. Shao, RSC Adv., 2015, 5, 93386–93393 RSC.
- Z.-Q. Zeng, J.-F. Wang, Z.-H. Li, B.-C. Sun, L. Shao, W.-J. Li, J.-F. Chen and H.-K. Zou, Ozone: Sci. Eng., 2013, 35, 101–108 CrossRef CAS.
- M. Ghaedi, H. Mazaheri, S. Khodadoust, S. Hajati and M. Purkait, Spectrochim. Acta, Part A, 2015, 135, 479–490 CrossRef CAS PubMed.
- M. N. Chong, H. Y. Zhu and B. Jin, Chem. Eng. J., 2010, 156, 278–285 CrossRef CAS.
- N. G. Asenjo, R. Santamaría, C. Blanco, M. Granda, P. Álvarez and R. Menéndez, Carbon, 2013, 55, 62–69 CrossRef CAS.
- M. E. Leblebici, J. Rongé, J. A. Martens, G. D. Stefanidis and T. Van Gerven, Chem. Eng. J., 2015, 264, 962–970 CrossRef CAS.
- J. Kasanen, J. Salstela, M. Suvanto and T. T. Pakkanen, Appl. Surf. Sci., 2011, 258, 1738–1743 CrossRef CAS.
- M. Montazerozohori, M. Nasr-Esfahani and S. Joohari, Environ. Prot. Eng., 2012, 38, 45–55 CAS.
|
This journal is © The Royal Society of Chemistry 2016 |
Click here to see how this site uses Cookies. View our privacy policy here.