DOI:
10.1039/C6RA10096A
(Paper)
RSC Adv., 2016,
6, 62252-62262
Production of propionic acid via hydrodeoxygenation of lactic acid over FexOy catalysts†
Received
19th April 2016
, Accepted 22nd June 2016
First published on 23rd June 2016
Abstract
The gas-phase hydrodeoxygenation of LA to propionic acid over Fe and its oxides was firstly investigated under various conditions. The catalysts were characterized by nitrogen adsorption–desorption, XRD, FT-IR, H2-TPR and SEM. Fe3O4 as active species was confirmed. Due to that reason, Fe2O3 can be efficiently transformed in situ to Fe3O4 under an atmosphere containing hydrogen derived from decarboxylation/or decarbonylation reaction of lactic acid, which offers the most excellent catalytic performance. The catalyst is sensitive to reaction temperature. LA conversion and its consumption rate increased with an increase of reaction temperature. Similarly, propionic acid selectivity also increased with reaction temperature in the range of 360–390 °C. But with further enhancement of reaction temperature from 390 to 400 °C, it drastically decreased since the formation rate of propionic acid reduced at 400 °C. The catalyst displayed an excellent adaptability in a wide range of LA LHSV except for 1.3 h−1. More importantly, at high LA LHSV of 26.3 h−1, the catalyst offered a satisfactory stability within 100 h on stream. Under the optimal reaction conditions, 96.7% of LA conversion and 46.7% of propionic acid selectivity were achieved.
Introduction
Propionic acid is currently produced in around 4
00
000 tons per year, and is widely used as a food preservative for grain, bread, cake, cheese, meat, etc.1–4 Its production mainly relies on the oxidization of propanal obtained from ethylene via hydroformylation.5–10 Other processes in propionic acid synthesis include hydrocarboxylation of ethylene,11,12 carbonylation of ethanol,13 hydrogenation of acrylic acid14,15 and hydration of acrylonitrile,16–18 and these processes are summarized in Scheme 1. However theses processes for propionic acid production are mostly based on raw materials derived from petroleum, which will become scarcer and more expensive with the rapid development of chemical industries in the long term. The search for new processes for the production of propionic acid based on sustainable feedstock is extremely urgent. Lactic acid (LA) as sustainable feedstock is widely used to synthesize various chemicals such as acrylic acid,19–24 acetaldehyde,25–27 2,3-pentanedione28,29 and polylactic acid.30,31 Except for corn starch, rich and inexpensive biomass materials such as glycerol,32–36 cellulose,37 wheat straw,38 sugars,39 and sorbitol40 have also been used to produce LA. Therefore chemicals produced from LA have displayed a potential perspective.
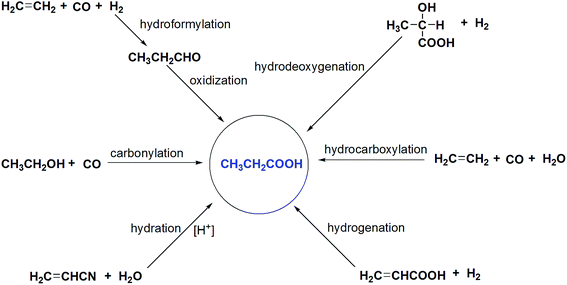 |
| Scheme 1 Paths for propionic acid production. | |
The production of propionic acid from LA dates back to 19th century using hydriodic acid as a catalyst.4 Homogeneous precious metal catalysts based on Pt, Pd and Ir, were used for this reaction.41 The reaction mechanism was thought to contain two steps: (1) dehydration of LA into acrylic acid; and (2) hydrogenation of acrylic acid into propionic acid. Among these precious metal complexes, PtH(Pet3)3 offered the best catalytic performance (around 50% yield of propionic acid) at 250 °C in water at pH = 2. Korstanje et al.4 subsequently reported that non-noble metal complexes based on molybdenum were also used to catalyze the deoxygenation of LA into propionic acid, achieving 41% yield of sodium propionate. The major problem in the homogeneous catalysis is catalyst-product separation. Thus heterogeneous catalysis which can efficiently overcome above shortcoming is becoming attractive. Among these solid catalysts are sulfates,42,43 phosphates,22,23,28,29 alkali or alkali earth metal-modified zeolites,19,44 mesoporous carbon,45 metal oxides,25,26,46 and supported platinum.47,48 The reaction temperature applied in these catalysts is usually selected in the range of 300–400 °C. So far, the best yield of propionic acid (25%) has been achieved over Pt/Nb2O5 catalyst at 350 °C and 50 bar H2 pressure.48
To the best of my knowledge, the non-noble metal catalysts are rarely used to catalyze the gas-phase hydrodeoxygenation reaction of LA into propionic acid. Especially, iron catalyst has never been investigated for this reaction. Here, we presented the use of Fe and its oxides for the selective hydrodeoxygenation of LA into propionic acid under an atmospheric pressure without additional H2.
Results and discussion
Characterization of catalysts
BET and SEM. As for a heterogeneous catalyst, its specific surface area usually has an important influence in catalytic activity. For most of heterogeneous catalysts, high specific surface area has a favorable activity. Table 1 showed the BET data of Fe and its oxides, and the adsorption isotherms were shown in Fig. S1.† It is clearly seen that Fe (0.18 m2 g−1) and FeO (0.02 m2 g−1) have lower specific surface area than Fe3O4 (78.62 m2 g−1) and Fe2O3 (24.05 m2 g−1). Similarly, the pore volume of samples increases in the following order: FeO < Fe < Fe2O3 <Fe3O4. The used catalysts were also measured, and the BET data were shown in Table S1.† All the catalysts increased their specific surface areas except for Fe3O4. The morphologic features of the catalysts were determined by scanning electron microscope, and the results were shown in Fig. 1. All samples display an irregular morphologic feature.
Table 1 BET data of catalysts
Catalyst |
SBET (m2 g−1) |
Vol (cm3 g−1) |
Fe |
0.18 |
3.66 × 10−4 |
FeO |
0.02 |
1.13 × 10−4 |
Fe3O4 |
78.62 |
0.43 |
Fe2O3 |
24.05 |
0.21 |
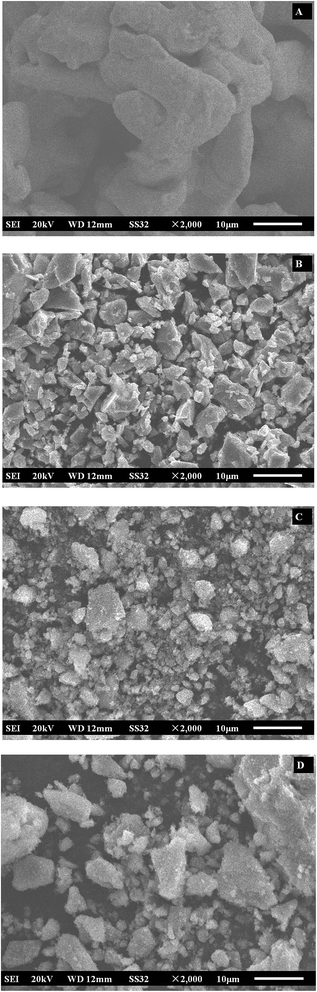 |
| Fig. 1 SEM images of catalysts (A: Fe; B: FeO; C: Fe3O4 and D: Fe2O3). | |
XRD and FT-IR. Fig. 2A showed the XRD patterns of fresh samples. Fresh Fe displays two characteristic diffraction peaks centered at 2θ = 44.7° and 65.0°, indexed to (110) and (200), respectively, which accords with the standard Fe sample, JCPDS no. 65-4899. Fresh FeO displays four characteristic diffraction peaks centered at 2θ = 36.0°, 41.9°, 60.6° and 72.7°, indexed to (111), (200), (220), and (311), respectively, which accords with the standard FeO sample, JCPDS no. 06-0615. Fresh Fe3O4 displays six characteristic diffraction peaks centered at 2θ = 30.1°, 35.4°, 43.1°, 53.4°, 56.9° and 62.5°, indexed to (220), (311), (400), (422), (511) and (440), respectively, which accords with the standard Fe3O4 sample, JCPDS no. 65-3107. Fresh Fe2O3 displays eight characteristic diffraction peaks centered at 2θ = 24.0°, 33.1°, 35.5°, 40.8°, 49.5°, 54.1°, 62.4° and 63.9°, indexed to (012), (104), (110), (113), (024), (116), (214) and (300), respectively, which accords with the standard Fe2O3 sample, JCPDS no. 33-0664. In order to understand the active species for hydrodeoxygenation reaction of LA to propionic acid, the used catalysts for 8 h reaction were also determined with XRD characterization, and the results were given in Fig. 2B. It is clearly observed that all the used catalysts display conformable characteristic diffraction peaks index to Fe3O4 (JCPDS no. 65-3107). However, Fe and FeO have only a small part transformed into Fe3O4 and others still remain. Interestingly, as for Fe2O3, it has completely transformed to Fe3O4, showing nearly 5 times of intensities of characteristic diffraction peaks stronger than the used Fe3O4. Subsequently, we further investigate the course of Fe2O3 transformed into Fe3O4 under the reaction conditions, and the results were shown in Fig. 3. Indeed, it quickly transformed into Fe3O4. For example, only minor part of Fe2O3 exists in the sample after 0.5 h of reaction, whereas it has completely transformed into Fe3O4 when the reaction time lengthened to 1.0 h. FT-IR techniques were also used to investigate the catalysts, and the results were shown in Fig. 4. Comparison of the fresh catalysts (before reaction) with the used catalysts (after reaction) suggests that characteristic absorption band (around 580 cm−1) indexed to Fe3O4 existed in the used catalysts, indicating that Fe and FeO transform in part to Fe3O4, whereas Fe2O3 has completely transformed into Fe3O4. This result accords with that obtained with XRD.
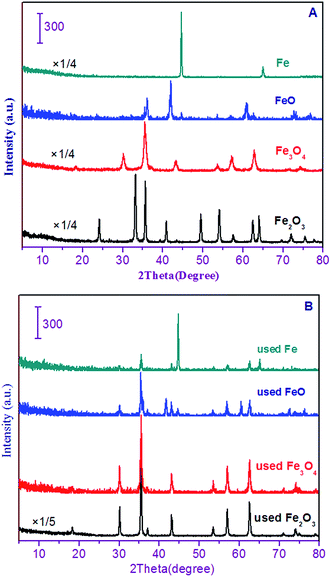 |
| Fig. 2 XRD patterns of fresh catalysts (A) and their corresponding used catalysts for 8 h reaction (B). | |
 |
| Fig. 3 XRD patterns of fresh catalyst (Fe2O3) and its used catalysts (experienced after 0.5–1.0 h reaction). | |
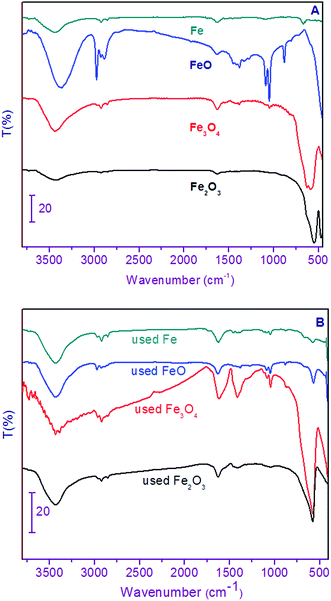 |
| Fig. 4 FT-IR spectra of fresh catalysts (A) and their corresponding used catalysts for 8 h reaction (B). | |
H2-TPR. Fig. 5A showed the TPR profiles of fresh catalysts. FeO does not display low temperature H2-consumption peak, and only displays high temperature H2-consumption peak. Both Fe3O4 and Fe2O3 display two H2-consumption peaks at low temperature and high temperature, respectively. For that reason, it is easy to understand that Fe3+ is easily reduced to Fe2+ under the H2-containing atmosphere. But, in contrast, Fe2+ is difficultly reduced to Fe metal. This result means that it is easy to construct a recycle between Fe3+ and Fe2+ under the redox atmosphere. We further investigated the reducibility of the used Fe2O3 and the results were shown in Fig. 5B. Compared with fresh Fe2O3, the H2-consumption peak of the used Fe2O3 at low temperature moved toward lower temperature, close to fresh Fe3O4. Notably, its H2-consumption peak at low temperature becomes smaller; and this indicates that small amount of H2 can reduce the catalyst. In addition, we further calculated the H2-consumption on fresh Fe2O3, Fe3O4 and their corresponding used catalysts, and the results were shown in Table S2.† Interestingly, the two used catalysts (Fe2O3 and Fe3O4) almost displayed the coincident results.
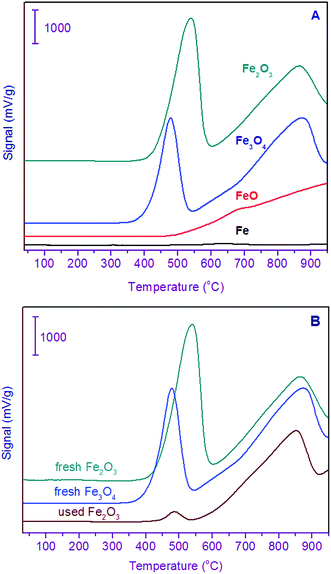 |
| Fig. 5 H2-TPR profiles of fresh catalysts (A) and the used Fe2O3 catalyst together with its fresh Fe2O3 and fresh Fe3O4 (B). | |
Evaluation of catalysts
Screening of catalysts. Catalytic reactions for gas phase hydrodeoxygenation of LA over the Fe and its oxides were performed at 390 °C with LA concentration (20 wt%) and feed flow rate (1 mL h−1), and the results were shown in Fig. 6A and B and Table 2. To compare the results obtained over the catalysts, the blank experiment was also performed at the identical conditions. Obviously, the LA conversion (47.5%) is far lower than those (86.1–96.7%) observed over the catalysts. Furthermore, it is clearly seen from the data shown in Table 2 that LA conversion gradually increases from 86.1% to 96.7% with change of catalysts from Fe to Fe2O3. Relatively low conversions of LA obtained over the Fe and FeO catalysts can be ascribed to their low specific surface areas (ca. 0.18 m2 g−1 and 0.02 m2 g−1, respectively, far lower than Fe3O4 (78.62 m2 g−1) and Fe2O3 (24.05 m2 g−1)). As for propionic acid selectivity, it is drastically influenced by Fe species. It is well known that propionic acid is obtained through hydrodeoxygenation of LA, ascribing to reduction reaction. Ordinarily, the Fe species with low chemical valence favors to reduction reaction. Accordingly, Fe and FeO catalysts should display better catalytic performances than Fe3O4 and Fe2O3. But the opposite results actually were obtained. It is obviously observed from the data shown in Table 2 and Fig. 6B that Fe3O4 and Fe2O3 catalysts offer better selectivity of propionic acid than Fe and FeO catalysts. It is noteworthy that the selectivity of propionic acid obtained over the Fe2O3 catalyst (46.7%) is slightly higher than Fe3O4 (42.5%). However, the former has stronger oxidation property than the latter. As mentioned above, the reaction on hydrodeoxygenation of LA to propionic acid is ascribed to reduction reaction. Evidently, Fe2O3 catalyst can not display better catalytic performance than Fe3O4. On the contrary, Fe2O3 catalyst indeed displayed better activity for hydrodeoxygenation of LA to propionic acid than Fe3O4 and others. Similarly, the higher selectivity of propionic acid over the silica supported heteropolyacid (H4PVMo11O40) catalyst in which metals such as V (+5) and Mo (+6) have high oxidation state than others was also observed by katryniok and co-workers.27 Unfortunately, the reasons why the catalysts with high oxidation state displayed high activity for this reaction have been short of further discussion so far. In order to search for the evidences, the catalysts were characterized by XRD and H2-TPR techniques, and the results were shown in Fig. 2, 3 and 5. Compared the XRD patterns of fresh catalysts (before reaction) shown in Fig. 2A with those shown in Fig. 2B (after reaction for 8 h), their diffraction peaks changed evidently except for Fe3O4 catalyst, indicating that Fe species were transformed under the catalytic reaction conditions. We further analyzed XRD patterns of the used catalysts using MDI Jade 5.0 software. Fe2O3 catalyst has been completely transformed into Fe3O4, and the intensity of its diffraction peaks indexed to Fe3O4 is about 5 times stronger than the used Fe3O4 catalyst. Fe and FeO catalysts have partly been transformed into Fe3O4 species, and others still existed in Fe and FeO samples, respectively. Interestingly, Fe3O4 catalyst has not changed, and still retained Fe3O4 phase. In four used catalysts, the used Fe2O3 displayed the strongest intensity of characteristic diffraction peaks indexed to Fe3O4 phase. Furthermore, the highest selectivity of propionic acid was also achieved over the Fe2O3 catalyst. It is noted that Fe and FeO catalysts in which small Fe3O4 phase existed displayed worse selectivity of propionic acid than Fe3O4 and Fe2O3 catalysts. Based on these evidences, we can conclude that Fe3O4 is active species for catalytic hydrodeoxygenation of LA into propionic acid. Since Fe3O4 is viewed as active species, we have further investigated the transformation of catalysts by reaction time course (shown in Fig. 3). Most of Fe2O3 has been transformed into Fe3O4 after 0.5 h of reaction, and it has been completely transformed into Fe3O4 when the reaction lengthened 0.5 h. This experiment further proved that Fe2O3 can be in situ rapidly transformed into Fe3O4 under the reaction conditions. Except for XRD characterization, XPS was also used to investigate the fresh catalysts and their corresponding used catalysts, and the results were given in Fig. S2.† High-resolution XPS profiles of Fe 2p for fresh catalysts (Fe2O3 and Fe3O4) displayed two obvious peaks at about 724.5 eV and 710.9 eV which corresponded to the binding energies of Fe 2p1/2 and Fe 2p3/2. But slight difference existed in the XPS profiles of the fresh catalysts, suggesting that Fe showed different oxidation states in the fresh catalysts. From high-resolution XPS profiles of Fe 2p in the used catalysts, two obvious peaks occurred at the same binding energies (724.5 eV and 710.9 eV), indicating that Fe2O3 was completely transformed into Fe3O4 during the catalytic reaction. In addition, H2-TPR characterization was also used to investigate the redox properties of catalysts, and the results were shown in Fig. 5A and B. From the H2-TPR profiles shown in Fig. 5A, it is clearly seen that both Fe3O4 and Fe2O3 catalysts display a low temperature peak for H2 consumption in the range of 350–600 °C, which are centered at 476 °C and 539 °C, respectively. However, FeO had no low temperature peak for H2 consumption to be replaced by high temperature peak for H2 consumption, suggesting that FeO is difficult to reduce into Fe in H2 atmosphere. It is easily concluded that Fe3+ species can be easily transformed into Fe2+ species under the reductive atmosphere (ca. H2). It happens to meet with an H2 atmosphere in catalytic process since a large quantity of acetaldehyde formed through decarboxylation/or decarbonylation of LA accompanying with formation of H2 together with CO2 as by-product.19,23–26 Thus Fe2O3 can be in situ rapidly transformed into Fe3O4 as active species during the catalytic reaction. Again, from the H2-TPR graphs of the used Fe2O3 shown in Fig. 5B, low temperature peak for H2 consumption more drastically reduced than fresh Fe2O3 and Fe3O4, indicating that the used catalyst is easily reduced in the presence of a small quantity of H2. Just right, H2 as a reductive atmosphere existed in the reaction system can reduce Fe3+ to Fe2+, and Fe2+ captures an oxygen atom from LA molecule to form one molecule of propionic acid (product), and then it is oxidized to Fe3+. H2 reduces Fe3+ to Fe2+ through drawing on an oxygen atom from iron oxide to form a water molecule. Besides, another interesting phenomenon was also observed from the data shown in Table 2. The selectivities of acetic acid over the Fe3O4 and Fe2O3 catalysts are 13.3% and 14.2%, respectively, far more than those of Fe and FeO catalysts (2.1% and 2.0%, respectively). Acetic acid is possibly formed via catalytic oxidization of acetaldehyde obtained from LA by Fe3+ species,45 which is reduced to Fe2+ species. Besides, acetic acid is also possibly formed through hydration of acetaldehyde accompanying with formation of hydrogen, which can also reduce Fe3+ to Fe2+. As mentioned above, Fe2+ species favors to catalyze hydrodeoxygenation of LA to propionic acid. In order to further learn about the catalytic performances, lower reaction temperature (360 °C) was chosen, and the results were given in Table S3.† Similar results were obtained at 360 °C. However, there is also a little difference in which the selectivity of propionic acid over the Fe3O4 is slightly higher than Fe2O3. This
result further demonstrated that Fe3O4 is active species.
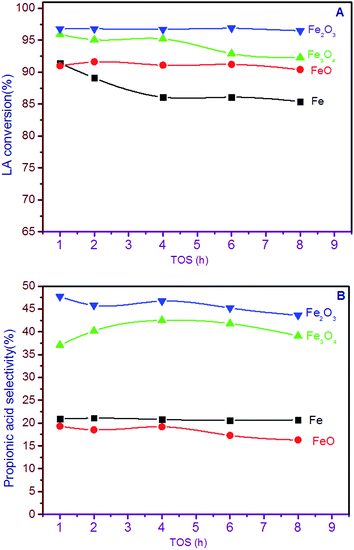 |
| Fig. 6 Performance of Fe and its oxides by the time course of LA conversion (A) and propionic acid selectivity (B). aCatalysts: Fe, 1.24 g, FeO, 0.99 g, Fe3O4, 0.32 g, Fe2O3, 0.44 g; carrier gas N2, 1 mL min−1; feed flow rate 1 mL h−1, LA feedstock 20 wt%; reaction temperature, 390 °C. bLA: lactic acid. | |
Table 2 Screening of catalystsa
Catalystsc |
LA conv. (%) |
Sel.b (%) |
PA |
AD |
AA |
PD |
ACA |
Catalyst: 0.38 mL, Fe, 1.24 g, FeO, 0.99 g, Fe3O4, 0.32 g, Fe2O3, 0.44 g; carrier gas N2 1 mL min−1; feed flow rate 1 mL h−1, LA feedstock 20 wt%; reaction temperature, 390 °C; TOS, 3–4 h. LA: lactic acid, PA: propionic acid, AD: acetaldehyde, AA: acrylic acid, PD: 2,3-pentanedione, ACA: acetic acid. Carbon recovery is above 93% except for Fe and FeO catalysts (around 85%). |
Blank |
47.5 |
7.3 |
26.5 |
1.6 |
0.5 |
2.1 |
Fe |
86.1 |
20.8 |
17.1 |
1.4 |
1.1 |
2.1 |
FeO |
91.1 |
19.2 |
19.8 |
1.3 |
1.1 |
2.0 |
Fe3O4 |
95.2 |
42.5 |
13.2 |
2.0 |
1.1 |
13.3 |
Fe2O3 |
96.7 |
46.7 |
12.7 |
2.2 |
0.9 |
14.2 |
Reaction temperature. According to the discussion on Fe and its oxides for catalytic hydrodeoxygenation of LA to propionic acid, Fe3O4 as active species has been confirmed. More importantly, Fe2O3 as precursor can be easily in situ transformed into active species of Fe3O4 and offers the best catalytic performance. Therefore, effect of reaction temperature on catalytic performances such as LA conversion, propionic acid selectivity and area-specific catalytic rate was investigated over the Fe2O3 as precursor, and the results were shown in Fig. 7A and B. In the range of 360–400 °C, LA conversion slightly increases with an enhancement of reaction temperature. For example, LA conversion is 90.7% at 360 °C, and it rises to 98.4% at 400 °C, which increases only 7.7%. As for propionic acid selectivity, it is clearly seen that propionic acid selectivity drastically increases from 28.1% to 46.7% with an increase of reaction temperature from 360 to 390 °C. However it rapidly decreases to 19.5% with further increase of reaction temperature from 390 to 400 °C, suggesting that reaction rates of side reactions increase more quickly than formation rate of propionic acid. In order to fully understand this view, we correlated area-specific catalytic rate with reaction temperature, and the result was depicted in Fig. 7B. LA consumption rate always increases with an increase of reaction temperature, whereas propionic acid formation rate firstly increases with an increase of reaction temperature, and it subsequently decreases with further increase of reaction temperature. This result further supports on the above view, i.e., reaction rate of side reactions rise more quickly than formation rate of propionic acid at higher reaction temperature. Thus 390 °C is chosen as an optimal reaction temperature considering LA conversion and propionic acid selectivity.
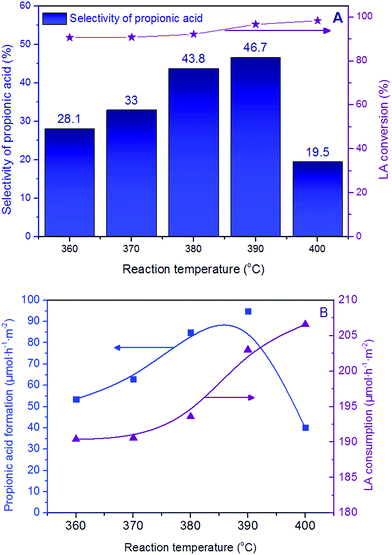 |
| Fig. 7 Effect of reaction temperature on reaction performances: LA conversion and propionic acid selectivity (A); and area-specific catalytic rate (B). aCatalyst: 0.38 mL, Fe2O3, 0.44 g; carrier gas N2, 1 mL min−1; feed flow rate, 1 mL h−1, LA feedstock 20 wt% ; TOS, 3–4 h. bLA: lactic acid. | |
Liquid hourly space velocity (LHSV). It is known that liquid hourly space velocity (LHSV) is a vital factor for evaluation of solid catalysts.20,42,49,50 The influence of LA LHSV on reaction performance was shown in Fig. 8. The reactions were conducted at 390 °C with flow rate of LA changed from 0.5 to 15 mL h−1 (corresponding LHSV = 1.3–39.5 h−1). Other operation conditions such as the flow rate of carrier gas N2 (1 mL min−1) and LA concentration (20 wt%) were retained. It is clearly seen from the results given in Fig. 9 that propionic acid selectivity drastically increases from 33.4% to 46.7% as LA LHSV increases from 1.3 to 2.6 h−1. Subsequently, propionic acid selectivity remains on around 43–46% with further increase of LA LHSV. On the other hand, LA conversion slightly decreases from 98.4% to 88.4% as the LA LHSV increases from 1.3 to 39.5 h−1, indicating that hydrodeoxygenation reaction of LA to propionic acid is a fast reaction.
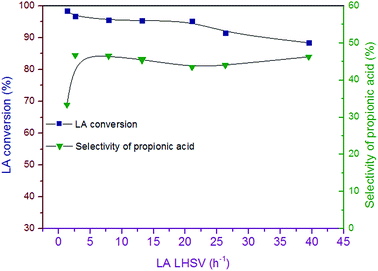 |
| Fig. 8 Effect of LA LHSV on the reaction performance. aCatalyst: 0.38 mL, Fe2O3, 0.44 g; carrier gas N2, 1 mL min−1; reaction temperature, 390 °C; LA feedstock 20 wt%; TOS, 3–4 h. b LA: lactic acid. | |
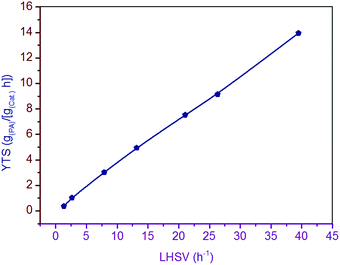 |
| Fig. 9 Time space yield of propionic acid at different LA LHSV. | |
The time space yield (YTS) of propionic acid was calculated according to the following equation.42,49
where
m(PA) is the mass of produced propionic acid (g);
m(Cat) is the mass of catalyst; and
t is the reaction time (h). Plotted in
Fig. 10 is the YTS of propionic acid
versus LA liquid hourly space velocity. From
Fig. 9, YTS of propionic acid rapidly increases with an increase of LA LHSV. But, as the LA LHSV is above 26.3 h
−1, LA conversion evidently decreases. A case in point is that the residue of LA accounts for 8.5% at LA LHSV of 26.3 h
−1. LA can not be fully converted at high LA LHSV since LA becomes difficult to be evaporated due to transfer limitation of heat. It is known that hydrodeoxygenation reaction of LA into propionic acid is a typical gas–solid catalytic reaction. Unevaporated LA in the reaction system does not favor the reaction, resulting in a low LA conversion. Therefore, it is a key factor for choosing a suitable LA LHSV to achieve a long-term stability for catalytic hydrodeoxygenation reaction of LA to propionic acid at 390 °C.
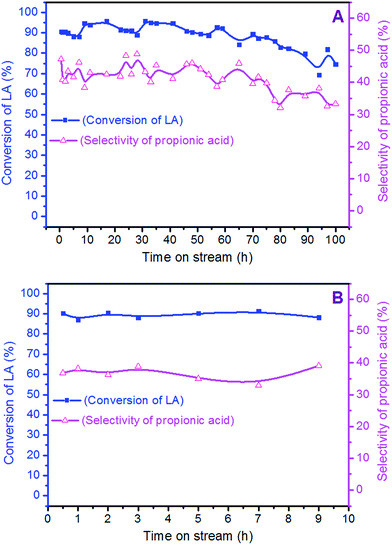 |
| Fig. 10 Durability of catalyst (A: fresh catalyst, 0.43 g and B: the used catalyst calcined at 500 °C for 5 h, 0.34 g). aCatalyst: 0.38 mL, Fe2O3; carrier gas N2, 1 mL min−1; reaction temperature, 390 °C; LA feedstock 20 wt%, feed flow rate, 10 mL h−1. b LA: lactic acid. | |
Durability and recovery. Long-term stability is a very important characteristic for a heterogeneous catalyst.51–55 The catalytic stability of Fe3O4 catalyst in situ transformed from Fe2O3 was investigated at 390 °C and LA feed flow rate of 10 mL h−1 (corresponding LA LHSV = 26.3 h−1), and the results were depicted in Fig. 10A and B. With regard to variation tendency of LA conversion with time on stream, it slowly gradually decreases with an increase of time on stream. For example, LA conversion reduces with only 26.4% (from 95.7% to 69.3%) within 100 h on stream. Similarly, propionic acid selectivity also slowly gradually decreases with time on stream. It is noted that LA feed flow rate of 10 mL h−1 (corresponding LA LHSV = 26.3 h−1) is far more than previous reports on LA conversion into chemicals such as acrylic acid and acetaldehyde.21,24,26,45,56 Besides, the used catalyst was calcined under air atmosphere at 500 °C for 5 h, and evaluated the catalytic performance again; and the result was shown in Fig. 10B. The catalytic performance can be almost recovered by a simple calcination considering that the used catalyst reduced from 0.43 g (fresh catalyst) to 0.34 g (the used catalyst). Therefore the stability experiment suggests that the catalyst offer excellent durability and recovery.
Mechanistic studies. In order to fully understand the observed reactivities, we performed several discriminating experiments on reaction mechanism of propionic acid from LA over the Fe and its oxides. The possible reaction paths can be depicted in Scheme 2. Path 1: the acrylic acid is believed as an intermediate, which is obtained through dehydration of LA, and subsequently it is hydrogenated with H2 to form propionic acid. If this path is true, the catalyst should have at least two functions including catalytic dehydration, and catalytic hydrogenation. But from the product distribution data (represented using product selectivity data) shown in Table 2, the acrylic acid selectivity is low, around 1.3–2.2%, suggesting that the intermediate concentration is low, which is unfavorable to formation of propionic acid. The other possibility is that hydrogenation rate of acrylic acid is faster than dehydration rate of LA, resulting in a low acrylic acid concentration. To discriminate the true or not on this view, we performed an experiment using only acrylic acid (10 wt%) as a substrate, and H2 (flow rate, 3 mL min−1) as carrier gas at 390 °C over the Fe2O3 to synthesize propionic acid. Acrylic acid conversion is 40%, and propionic acid selectivity is 31.6%, whereas under LA as a substrate and N2 (1 mL min−1) as a carrier gas, LA conversion is 96.7%, and propionic acid selectivity is 46.7%. This result suggests that hydrogenation rate of acrylic acid is not enough high. In other words, the path 1 is not major path for propionic acid from LA, and only a minor path. The path 2: LA is converted to propionic acid via a direct hydrodeoxygenation (C–OH cleavage). Since path 1 is a minor path, path 2 should become a major path. In order to further investigate the effect of external H2, we also performed an experiment using H2 (flow rate, 3 mL min−1) as a carrier gas substituted for N2, and other reaction conditions were retained. LA conversion is almost unchanged, and propionic acid is slightly enhanced, suggesting that the catalyst offered a poor activity for external H2 (molecular hydrogen), and an excellent activity for in situ hydrogen including an atomic hydrogen (H) or ionized hydrogen (H+ or H−).
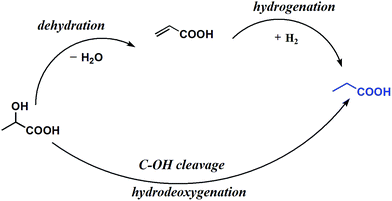 |
| Scheme 2 The possible reaction paths for propionic acid synthesis from LA. | |
Whether the reaction on propionic acid converted from LA follows path 1 or 2, hydrogen is necessary. According to previous investigations,27,44,46 hydrogen can be formed via decarboxylation of LA given acetaldehyde, CO2 and H2, or decarbonylation of LA given acetaldehyde, CO and H2O, followed with a water-gas shift reaction to produce hydrogen (shown in Scheme 3). The tail gas was analyzed by GC with a packed column of TDX-01 connected to TCD detector, and it was found that CO2/CO molar ratio is close to 4
:
1, suggesting that decarboxylation rate of LA is faster than the decarbonylation rate of LA, or CO is fast converted to CO2 through a water-gas shift reaction. These processes accompany with producing hydrogen. Another source is that hydrogen is produced via hydration of acetaldehyde to produce acetic acid45 (also shown in Scheme 3). As for the latter source, it is strongly supported by the data on acetic acid selectivity shown in Table 2. Acetic acid selectivities over the Fe2O3 (14.2%) and Fe3O4 (13.3%) are far higher than Fe (2.1%) and FeO (2.0%). Besides, organic compounds can also partly react with water to form CO, CO2, and H2 at high reaction temperature,57–63 which can provide hydrogen for propionic acid synthesis from LA.
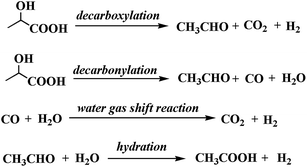 |
| Scheme 3 The possible paths for hydrogen formation. | |
Just right, the in situ formed H2 as a reductive atmosphere can reduce Fe3+ to Fe2+, and Fe2+ captures an oxygen atom from LA molecule to form one molecule of propionic acid (product), and then it is oxidized to Fe3+. Then H2 again reduces Fe3+ to Fe2+ through drawing on an oxygen atom from iron oxide to form a water molecule.
Experimental section
Materials
Lactic acid (analytic grade, 85–90 wt%) was purchased from Chengdu Kelong Chemical Reagent Co. and was used for the synthesis of propionic acid without further purification. Triple-distilled water was prepared in the laboratory and was used to dilute lactic acid for desired concentration. Reduced iron powder (Fe), ferrous oxide (FeO), ferric nitrate (Fe(NO3)3·9H2O), ferric chloride (FeCl3) and ferrous chloride (FeCl2·4H2O) were purchased from Alfa Aesar. Ammonia water (25–28 wt%), propionic acid, acetaldehyde, acrylic acid, acetic acid, 2,3-pentanedione and n-butanol, together with hydroquinone were purchased from Sinopharm Chemical Reagent Co., Ltd. Propionic acid, acrylic acid, acetic acid, 2,3-pentanedione and acetaldehyde were used for gas chromatograph reference materials, and n-butanol was utilized as internal standard material. Hydroquinone (0.3 wt%) was used as a polymerization inhibitor.
Preparation of catalysts
Fe2O3 was prepared with a precipitation method using ammonia water as a precipitant. In a typical experiment, 8.08 g Fe(NO3)3·9H2O was fully dissolved in 100 mL distilled water under a stirring state for 1 h at room temperature. Next, the resultant solution was adjusted to pH = 8–9 to form a reddish-brown precipitate by dropwise addition of ammonia water (25 wt%). The resulting precipitate was filtered, completely rinsed with distilled water, dried at 120 °C for around 5 h, and calcined in muffle furnace at 500 °C for 6 h. Fe3O4 was prepared with a similar method. In a typical experiment, 4.09 g FeCl2·4H2O and 5.00 g FeCl3 were fully dissolved in 100 mL distilled water under a stirring state for 1 h at room temperature. Next, the resultant solution was adjusted to pH = 11 to form a precipitate by dropwise addition of ammonia water (25 wt%). The resulting precipitate was filtered, completely rinsed with absolute ethanol. It was dried in the tubular furnace under the argon atmosphere at 100 °C for around 10 h.
Catalyst characterization
Powder X-ray diffraction measurement was conducted on a Dmax/Ultima IV diffractometer operated at 40 kV and 20 mA with Cu-Kα radiation. The FT-IR spectra of the catalysts were recorded in the range of 500–4000 cm−1 on a Nicolet 6700 spectrometer. The morphologic features of the catalysts were determined by scanning electron microscope (SEM, JSM-6510). The specific surface areas of catalysts were measured through nitrogen adsorption at 77 K using Autosorb IQ instrument. Prior to adsorption, the samples were treated at 250 °C under vacuum for 6 h and the specific surface area was calculated according to the Brunauer–Emmett–Teller (BET) method. X-ray photoelectron spectroscopy (XPS) measurements were performed using a Thermo ESCALAB 250XI spectrometer. Spectra were obtained using an aluminium anode (Al Kα = 1486.6 eV) operating at 150 W and a spot size of 500 μm. Redox properties of the samples were estimated by H2-TPR on a Quantachrome Instrument. The sample (ca. 50–60 mg) was purged with dry Ar (50 mL min−1, purity > 99.999 vt%) at 500 °C for 1.0 h, followed by reducing the furnace temperature to 30 °C, and switching to a flow of 8.0 vt% H2/Ar to execute H2-TPR in the range of 30–950 °C at a rate of 10 °C min−1.
Catalyst evaluation
The synthesis of propionic acid from lactic acid over the catalysts was carried out in a fixed-bed quartz reactor with a 4 mm inner diameter operated at an atmospheric pressure without additional H2. The catalyst (ca. 440 mg, 20–40 meshes) was placed in the middle of the reactor and quartz wool was placed in both ends. Firstly, the catalyst was pretreated at the required reaction temperature (ca. 390 °C) for 1.0 h under N2 with high purity (0.1 MPa, 1.0 mL min−1). The feedstock (20 wt% solution of LA) was then pumped into the reactor (LA aqueous solution flow rate, 1.0 mL h−1) and driven through the catalyst bed by nitrogen. The contact time of reactant over the catalyst is around 0.5 s, and the contact time is estimated according to eqn (1).42,43,49 The liquid products were condensed using ice-water bath and analyzed off-line using a SP-6890 gas chromatograph with a FFAP capillary column connected to a FID. Quantitative analysis of the products was carried out by the internal standard method using n-butanol as the internal standard material. GC-MS analyses of the samples were performed using Agilent 5973N Mass Selective Detector attachment. The reaction tail gas was analyzed using GC with a packed column of TDX-01 connected to TCD detector. The conversion of LA and the selectivity toward propionic acid or other by-products were calculated according to eqn (2) and (3). |
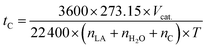 | (1) |
tC: contact time (s); Vcat.: catalyst volume (mL); nLA: the moles of lactic acid passed per hour; n(H2O): the moles of water in lactic acid aqueous solution feed passed per hour; nC: the moles of carrier gas passed per hour; T: reaction temperature (K). |
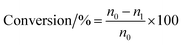 | (2) |
|
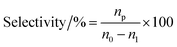 | (3) |
where n0 is the molar quantity of LA fed into reactor, n1 is the molar quantity of LA in the effluent, and n2 is the molar quantity of lactic acid converted to propionic acid or other byproducts such as acetaldehyde, acrylic acid, acetic acid and 2,3-pentanedione.
Conclusions
The gas-phase hydrodeoxygenation of LA to propionic acid over Fe and it oxides was firstly investigated at the various conditions. Fe3O4 as active species has been confirmed. Due to that reason, Fe2O3 can be efficiently in situ transformed to Fe3O4, which offers the most excellent catalytic performance. The catalyst is sensitive to reaction temperature. LA conversion and its consumption rate increased with an increase of reaction temperature. Similarly, propionic acid selectivity also increased with reaction temperature in the range of 360–390 °C. But with further enhancement of reaction temperature from 390 to 400 °C, it drastically decreased since the formation rate of propionic acid reduced at 400 °C. The catalyst displayed an excellent adaptability in a wide range of LA LHSV except for 1.3 h−1. More importantly, at high LA LHSV of 26.3 h−1, the catalyst offered a satisfactory stability within 100 h on stream.
Acknowledgements
This work was supported by Scientific Research Fund of Chemical Synthesis and Pollution Control Key Laboratory of Sichuan Province with project number of CSPC-2014-3-1, Scientific Research Fund of China West Normal University with project number of 12B019 and Scientific Research Fund of Sichuan Provincial Educational Department with project number of 14ZA0128, 16ZA0175.
Notes and references
- E. Maier, K. Kurz, M. Jenny, H. Schennach, F. Ueberall and D. Fuchs, Food Chem. Toxicol., 2010, 48, 1950–1956 CrossRef CAS PubMed.
- W. K. Coblentz and M. G. Bertram, J. Dairy Sci., 2012, 95, 340–352 CrossRef CAS PubMed.
- W. K. Coblentz, K. P. Coffey, A. N. Young and M. G. Bertram, J. Dairy Sci., 2013, 96, 2521–2535 CrossRef CAS PubMed.
- T. J. Korstanje, H. Kleijn, J. Jastrzebski and R. Gebbink, Green Chem., 2013, 15, 982–988 RSC.
- L. Huang and Y. D. Xu, Appl. Catal., A, 2001, 205, 183–193 CrossRef CAS.
- V. I. Zapirtan, B. L. Mojet, J. G. van Ommen, J. Spitzer and L. Lefferts, Catal. Lett., 2005, 101, 43–47 CrossRef CAS.
- H. Hanh Nguyen Thi, D. Duc Truong, D. Thang Vu, L. Minh Thang, A. Riisager and R. Fehrmann, Catal. Commun., 2012, 25, 136–141 CrossRef.
- Y. Diao, J. Li, L. Wang, P. Yang, R. Yan, L. Jiang, H. Zhang and S. Zhang, Catal. Today, 2013, 200, 54–62 CrossRef CAS.
- N. Navidi, J. W. Thybaut and G. B. Marin, Appl. Catal., A, 2014, 469, 357–366 CrossRef CAS.
- J. Liu, L. Yan, Y. Ding, M. Jiang, W. Dong, X. Song, T. Liu and H. Zhu, Appl. Catal., A, 2015, 492, 127–132 CrossRef CAS.
- J. R. Zoeller, E. M. Blakely, R. M. Moncier and T. J. Dickson, Catal. Today, 1997, 36, 227–241 CrossRef CAS.
- E. G. Chepaikin, A. P. Bezruchenko and A. A. Leshcheva, Kinet. Catal., 1999, 40, 313–321 CAS.
- Q. Zhang, H. Wang, G. Sun, K. Huang, W. Fang and Y. Yang, Catal. Commun., 2009, 10, 1796–1799 CrossRef CAS.
- S.-F. Zhu, Y.-B. Yu, S. Li, L.-X. Wang and Q.-L. Zhou, Angew. Chem., Int. Ed., 2012, 51, 8872–8875 CrossRef CAS PubMed.
- Y. Li, K. Dong, Z. Wang and K. Ding, Angew. Chem., Int. Ed., 2013, 52, 6748–6752 CrossRef CAS PubMed.
- Y. Wang, H. F. Liu and N. Toshima, J. Phys. Chem., 1996, 100, 19533–19537 CrossRef CAS.
- J. Li, J. Chen, Y. Wang, G. Luo and H. Yu, Bioresour. Technol., 2014, 169, 416–420 CrossRef CAS PubMed.
- J. Li, L. Yang, X. Ding, J. Chen, Y. Wang, G. Luo and H. Yu, RSC Adv., 2015, 5, 79164–79171 RSC.
- X. Zhang, L. Lin, T. Zhang, H. Liu and X. Zhang, Chem. Eng. J., 2016, 284, 934–941 CrossRef CAS.
- B. Yan, L. Z. Tao, Y. Liang and B. Q. Xu, ACS Catal., 2014, 4, 1931–1943 CrossRef CAS.
- B. Yan, L. Z. Tao, Y. Liang and B. Q. Xu, ChemSusChem, 2014, 7, 1568–1578 CrossRef CAS PubMed.
- C. M. Tang, J. S. Peng, X. L. Li, Z. J. Zhai, N. Jiang, W. Bai, H. J. Gao and Y. W. Liao, RSC Adv., 2014, 4, 28875–28882 RSC.
- C. M. Tang, J. S. Peng, G. C. Fan, X. L. Li, X. L. Pu and W. Bai, Catal. Commun., 2014, 43, 231–234 CrossRef CAS.
- J. S. Peng, X. L. Li, C. M. Tang and W. Bai, Green Chem., 2014, 16, 108–111 RSC.
- C. M. Tang, J. S. Peng, X. L. Li, Z. J. Zhai, W. Bai, N. Jiang, H. J. Gao and Y. W. Liao, Green Chem., 2015, 17, 1159–1166 RSC.
- C. M. Tang, Z. J. Zhai, X. L. Li, L. W. Sun and W. Bai, J. Catal., 2015, 329, 206–217 CrossRef CAS.
- B. Katryniok, S. Paul and F. Dumeignil, Green Chem., 2010, 12, 1910–1913 RSC.
- G. C. Gunter, R. H. Langford, J. E. Jackson and D. J. Miller, Ind. Eng. Chem. Res., 1995, 34, 974–980 CrossRef CAS.
- G. C. Gunter, D. J. Miller and J. E. Jackson, J. Catal., 1994, 148, 252–260 CrossRef CAS.
- Z. Q. Lei, Y. B. Bai and S. F. Wang, Chin. Sci. Bull., 2005, 50, 2390–2392 CrossRef CAS.
- A. J. Amass, K. L. R. N'Goala, B. J. Tighe and F. Schue, Polymer, 1999, 40, 5073–5078 CrossRef CAS.
- L. S. Sharninghausen, J. Campos, M. G. Manas and R. H. Crabtree, Nat. Commun., 2014, 5, 1–9 Search PubMed.
- R. K. P. Purushothaman, J. van Haveren, I. Melian-Cabrera, E. R. H. van Eck and H. J. Heeres, ChemSusChem, 2014, 7, 1140–1147 CrossRef PubMed.
- M. Dusselier, P. Van Wouwe, A. Dewaele, E. Makshina and B. F. Sels, Energy Environ. Sci., 2013, 6, 1415–1442 Search PubMed.
- P. Maki-Arvela, I. L. Simakova, T. Salmi and D. Y. Murzin, Chem. Rev., 2014, 114, 1909–1971 CrossRef CAS PubMed.
- I. Delidovich, P. J. C. Hausoul, L. Deng, R. Pfutzenreuter, M. Rose and R. Palkovits, Chem. Rev., 2016, 116, 1540–1599 CrossRef CAS PubMed.
- Y. L. Wang, W. P. Deng, B. J. Wang, Q. H. Zhang, X. Y. Wan, Z. C. Tang, Y. Wang, C. Zhu, Z. X. Cao, G. C. Wang and H. L. Wan, Nat. Commun., 2013, 4, 1–7 Search PubMed.
- Y. M. Zhang, X. R. Chen, J. Q. Luo, B. K. Qi and Y. H. Wan, Bioresour. Technol., 2014, 158, 396–399 CrossRef CAS PubMed.
- D. Esposito and M. Antonietti, ChemSusChem, 2013, 6, 989–992 CrossRef CAS PubMed.
- C. A. Ramirez-Lopez, J. R. Ochoa-Gomez, S. Gil-Rio, O. Gomez-Jimenez-Aberasturi and J. Torrecilla-Soria, J. Chem. Technol. Biotechnol., 2011, 86, 867–874 CrossRef CAS.
- B. Odell, G. Earlam and D. J. Cole-Hamilton, J. Organomet. Chem., 1985, 290, 241–248 CrossRef CAS.
- Z. J. Zhai, X. L. Li, C. M. Tang, J. S. Peng, N. Jiang, W. Bai, H. J. Gao and Y. W. Liao, Ind.
Eng. Chem. Res., 2014, 53, 10318–10327 CrossRef CAS.
- J. F. Zhang, J. P. Lin and P. L. Cen, Can. J. Chem. Eng., 2008, 86, 1047–1053 CrossRef CAS.
- P. Sun, D. H. Yu, K. M. Fu, M. Y. Gu, Y. Wang, H. Huang and H. H. Ying, Catal. Commun., 2009, 10, 1345–1349 CrossRef CAS.
- C. M. Tang, J. S. Peng, X. L. Li, Z. J. Zhai, H. J. Gao, W. Bai, N. Jiang and Y. W. Liao, Korean J. Chem. Eng., 2016, 33, 99–106 CrossRef CAS.
- C. M. Tang, Z. J. Zhai, X. L. Li, L. W. Sun and W. Bai, J. Taiwan Inst. Chem. Eng., 2016, 58, 97–106 CrossRef CAS.
- J. C. Serrano-Ruiz and J. A. Dumesic, Green Chem., 2009, 11, 1101–1104 RSC.
- J. C. Serrano-Ruiz and J. A. Dumesic, ChemSusChem, 2009, 2, 581–586 CrossRef CAS PubMed.
- J. F. Zhang, Y. L. Zhao, M. Pan, X. Z. Feng, W. J. Ji and C. T. Au, ACS Catal., 2011, 1, 32–41 CrossRef CAS.
- J. H. Hong, J. M. Lee, H. Kim, Y. K. Hwang, J. S. Chang, S. B. Halligudi and Y. H. Han, Appl. Catal., A, 2011, 396, 194–200 CrossRef CAS.
- M. S. Holm, S. Saravanamurugan and E. Taarning, Science, 2010, 328, 602–605 CrossRef CAS PubMed.
- M. Behrens, F. Studt, I. Kasatkin, S. Kuhl, M. Havecker, F. Abild-Pedersen, S. Zander, F. Girgsdies, P. Kurr, B. L. Kniep, M. Tovar, R. W. Fischer, J. K. Norskov and R. Schlogl, Science, 2012, 336, 893–897 CrossRef CAS PubMed.
- J. M. Sun, K. K. Zhu, F. Gao, C. M. Wang, J. Liu, C. H. F. Peden and Y. Wang, J. Am. Chem. Soc., 2011, 133, 11096–11099 CrossRef CAS PubMed.
- L. Deiana, Y. Jiang, C. Palo-Nieto, S. Afewerki, C. A. Incerti-Pradillos, O. Verho, C. W. Tai, E. V. Johnston and A. Cordova, Angew. Chem., Int. Ed., 2014, 53, 3447–3451 CrossRef CAS PubMed.
- X. J. Jin, K. Yamaguchi and N. Mizuno, Angew. Chem., Int. Ed., 2014, 53, 455–458 CrossRef CAS PubMed.
- J. F. Zhang, X. Z. Feng, Y. L. Zhao, W. J. Ji and C. T. Au, J. Ind. Eng. Chem., 2014, 20, 1353–1358 CrossRef CAS.
- A. Seretis and P. Tsiakaras, Renewable Energy, 2016, 85, 1116–1126 CrossRef CAS.
- R. L. Manfro and M. M. V. M. Souza, Catal. Lett., 2014, 144, 867–877 CrossRef CAS.
- P. V. Tuza, R. L. Manfro, N. F. P. Ribeiro and M. Souza, Renewable Energy, 2013, 50, 408–414 CrossRef CAS.
- R. Tungal and R. Shende, Energy Fuels, 2013, 27, 3194–3203 CrossRef CAS.
- R. L. Manfro, T. P. M. D. Pires, N. F. P. Ribeiro and M. M. V. M. Souza, Catal. Sci. Technol., 2013, 3, 1278–1287 Search PubMed.
- F. J. Gutierrez Ortiz, A. Serrera, S. Galera and P. Ollero, Energy, 2013, 56, 193–206 CrossRef CAS.
- P. Sengupta, A. Khan, M. Abu Zahid, H. Ibrahim and R. Idem, Energy Fuels, 2012, 26, 816–828 CrossRef CAS.
Footnote |
† Electronic supplementary information (ESI) available. See DOI: 10.1039/c6ra10096a |
|
This journal is © The Royal Society of Chemistry 2016 |
Click here to see how this site uses Cookies. View our privacy policy here.