DOI:
10.1039/C6RA09950E
(Paper)
RSC Adv., 2016,
6, 56458-56466
Ni-SMTU@boehmite: as an efficient and recyclable nanocatalyst for oxidation reactions
Received
17th April 2016
, Accepted 6th June 2016
First published on 7th June 2016
Abstract
Boehmite nanoparticles were prepared via a simple and inexpensive procedure in water using commercially available materials, and furthermore a novel type of recoverable nanocatalyst was prepared via immobilization of the S-methylisothiourea complex of nickel on the surface of boehmite nanoparticles (Ni-SMTU@boehmite). This organometallic catalyst was characterized by FT-IR spectroscopy, TGA, XRD, ICP-OES, EDS and SEM techniques. Ni-SMTU@boehmite was applied as an efficient, recoverable and stable heterogeneous organometallic catalyst for the selective oxidation of sulfides to sulfoxides and oxidative coupling of thiols to corresponding disulfides. Metal leaching and heterogeneity test of this catalyst was examined by the ICP-OES technique, which showed that this catalyst can be recovered and reused for several times without significant loss of its catalytic efficiency or nickel leaching.
1 Introduction
Nanoparticles due to their high surface area and facile recovery, have recently emerged as catalyst supports.1,2 One of the novel nanomaterial supports is boehmite (γ-AlOOH) containing hydroxyl groups attached to its surface. Boehmite has important applications in the preparation of catalysts in petrochemical and petroleum refining processes.3 Another important application of boehmite is the production of α-Al2O3 by calcinations at high temperatures.4 Boehmite has a structure that consists of double sheets of octahedral shape with aluminum ions at their centers and the sheets themselves are composed of octahedral chains and have a cubic orthorhombic structure.5 Boehmite (γ-AlOOH) is also used as adsorbent, catalyst, cosmetic products, coatings, vaccine adjuvants and composite reinforcement material in ceramics,6–8 due to its unique properties such as good porosity and thermal stability, high specific surface area (>120 m2 g−1) and mesoporous properties.4,9 It is well known that boehmite is possesses excellent mechanical, electrical, thermal and optical properties, excellent biocompatibility, chemical resistance, low cost and corrosion resistance and controllable synthesis.10,11 A major advantage of boehmite nanoparticles is availability on a large industrial scale.12 Therefore, several methods have been described for preparation of boehmite nanoparticles such as hydrothermal,13 sol–gel,14 and hydrolysis of aluminum.15 But, most of them have focused on the morphologies, chemical and physical properties of the prepared particles; meanwhile, there is little literatures on the modification of nanoboehmite surface as heterogeneous support.16–18 Hence, an attempt has been made to modify of boehmite nanoparticles in this work. In order to regard of this issue, nickel S-methylisothiourea complex has been immobilized on boehmite nanoparticles and further applied as an excellent nano organometal catalyst for the selective oxidation of sulfides to sulfoxides and oxidative coupling of thiols to corresponding disulfides. Because oxidation of sulfides to sulfoxides and oxidative coupling of thiols into corresponding disulfides are useful in the synthesis of new molecules, as well as for various medical, chemical, biological, materials, and nanotechnological applications.19–24
2 Results and discussion
2.1 Catalyst preparation
In order to preparation of Ni-SMTU@boehmite, initially the boehmite nanoparticles was prepared according to new reported procedure25 and then modified using (3-chloropropyl)trimethoxysilane (CPTES). Subsequently, the terminal Cl functionals were successfully reacted with S-methylisothiourea hemisulfate salt (SMTU) through substation reaction to synthesis of nanoboehmite immobilized S-methylisothiourea (SMTU@boehmite). Finally nickel particles has been grafted on SMTU@boehmite via coordination of nickel on SMTU@boehmite (Scheme 1). This catalyst has been characterized by Fourier transform infrared spectroscopy (FT-IR), thermogravimetric analysis (TGA), scanning electron microscopy (SEM), energy-dispersive X-ray spectroscopy (EDS), X-ray diffraction (XRD), and inductively coupled plasma atomic emission spectroscopy (ICP-OES).
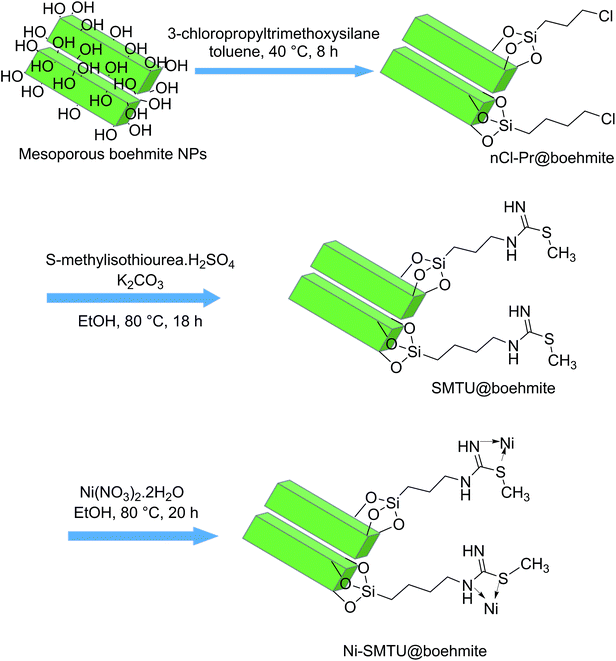 |
| Scheme 1 Synthesis of Ni-SMTU@boehmite. | |
2.2 Catalyst characterizations
The size of the catalyst was evaluated using SEM technique. The SEM image of Ni-SMTU@boehmite was shown that the catalyst was formed of nanometre-sized particles (Fig. 1).
 |
| Fig. 1 SEM image of Ni-SMTU@boehmite. | |
Also the size and morphology of Ni-SMTU@boehmite was studied by TEM technique. As shown in Fig. 2, the unit cells of Ni-SMTU@boehmite was obtained in cubic orthorhombic structures with about 20–40 nm in size.
 |
| Fig. 2 TEM images of Ni-SMTU@boehmite. | |
To indicate the supporting nickel metal on boehmite surface, the EDS analysis of Ni-SMTU@boehmite was carried out. The EDS patterns of Ni-SMTU@boehmite is shown in Fig. 3. As shown, EDS spectrum of Ni-SMTU@boehmite shows the presence of Al, O, Si, C, S and N and as well as Ni specie in the catalyst. Also, to obtained amount of nickel in Ni-SMTU@boehmite, ICP-OES analysis was performed. In this analysis, the amount of nickel in catalyst was found to be 1.64 × 10−3 mol g−1 based on ICP-OES.
 |
| Fig. 3 EDX spectrum of Ni-SMTU@boehmite. | |
In order to determine the percent of organic functional groups chemisorbed onto the surface of boehmite nanoparticles, the TGA analysis of Ni-SMTU@boehmite was performed. Fig. 4 shows the TGA curves for bare boehmite nanoparticles, nCl-Pr@boehmite, SMTU@boehmite and the Ni-SMTU@boehmite. In the all samples, the first step of weight loss (below 200 °C) is owing to the removal of the surface hydroxyl groups or physically and chemically adsorbed solvents, and the other weight loss is appeared in the range of 200–800 °C corresponds to the decomposition of the organic fragments and organic ligands on boehmite nanoparticles.26 The decomposition of organic layer and Ni-complex on boehmite nanoparticles (a weight loss about 47%) was occurred in TGA curve of the catalyst from 200 to 800 °C. Meanwhile, weight loss about 29% and 41% from 200 to 800 °C is occurred for nCl-Pr@boehmite and SMTU@boehmite, respectively.
 |
| Fig. 4 TGA diagram of boehmite nanoparticles (a), nCl-Pr@boehmite (b), SMTU@boehmite (c) and Ni-SMTU@boehmite (d). | |
The XRD patterns of boehmite nanoparticles is shown in Fig. 5. As shown in Fig. 5, the boehmite phase was characterized by the peak positions at 14.41 (0 2 0), 28.40 (1 2 0), 38.56 (0 3 1), 46.45 (1 3 1), 49.56 (0 5 1), 51.95 (2 0 0), 56.01 (1 5 1), 59.35 (0 8 0), 65.05 (2 3 1), 65.55 (0 0 2), 68.10 (1 7 1), and 72.40 (2 5 1) from the XRD patterns, which all the peaks can be confirmed the crystallization of boehmite with an orthorhombic unit cell.16
 |
| Fig. 5 The XRD pattern of boehmite nanoparticles. | |
FT-IR spectrums of boehmite, nPr-Cl@boehmite, SMTU@boehmite and Ni-SMTU@boehmite are shown in Fig. 6. As shown in FT-IR spectrum of the boehmite nanoparticles (spectrum a), two strong bands at 3086 and 3308 cm−1 are related to the both symmetrical and asymmetrical modes of the hydroxyl groups on the surface of boehmite nanoparticles.27 In FT-IR spectrums (a)–(d), several peaks that appear about 480, 615 and 735 cm−1 can be corresponds to the absorption of Al–O bonds.5 Also, the nitrate impurity vibration by a peak at 1637 cm−1 and the hydrogen bands (OH⋯OH) by two absorption bands at 1164 and 1069 cm−1 were observed in FT-IR spectrums.7,8 In the FT-IR spectra of nPr-Cl@boehmite (spectrum b), the presence of the anchored chloropropyltrimethoxysilane is authenticated by C–H stretching vibrations that appears at 2955 cm−1 and also O–Si stretching vibration modes that appear at 1073 cm−1. In the FT-IR spectra of SMTU-boehmite (spectrum c), the existence of the grafted S-methylisothiourea groups is identified by C
N vibrations that appear at 1638 cm−1.
 |
| Fig. 6 FT-IR spectra of boehmite nanoparticles (a), nCl-Pr@boehmite (b), SMTU@boehmite (c) and Ni-SMTU@boehmite (d). | |
The nitrogen adsorption–desorption isotherms of boehmite nanoparticles and Ni-SMTU@boehmite are shown in Fig. 7. It can be seen that the BET surface decrease after immobilization of organic layers and Ni-complex on boehmite nanoparticles. The decrease in surface area of Ni-SMTU@boehmite is attributed to the immobilization of organic layers and Ni-complex on the boehmite. These results are strong evidences that Ni-complex was bonded on the boehmite nanoparticles.
 |
| Fig. 7 Nitrogen adsorption–desorption isotherms of boehmite nanoparticles (a) and Ni-SMTU@boehmite (b). | |
2.3 Catalytic activity
After characterization of the prepared and characterized of catalyst, we tested the catalytic activity of Ni-SMTU@boehmite in the oxidation of sulfides to sulfoxides (Scheme 2). In order to optimize the reaction conditions, we examined the oxidation of methyl phenyl sulfide as a model compound in various solvents, in the presence of different amount of catalyst and using different amount of hydrogen peroxide (H2O2). The results of these study are summarized in Table 1. As shown in Table 1, H2O2 (0.4 mL) in the presence of catalytic amount of Ni-SMTU@boehmite (0.004 g, 0.66 mol%) under solvent-free condition at room temperature was found to be ideal the reaction conditions for the conversion of methyl phenyl sulfide to methyl phenyl sulfoxide. Also, inferior results were obtained in acetonitrile, ethanol and ethylacetate as solvent.
 |
| Scheme 2 Ni-SMTU@boehmite catalysed the oxidation of sulfides to sulfoxides. | |
Table 1 Optimization of reaction conditions for the oxidation of methylphenyl sulfide in the presence of Ni-SMTU@boehmite using H2O2

|
Entry |
Ni-SMTU@boehmite (mg) |
Solvent |
H2O2 (mL) |
Time (min) |
Yielda (%) |
Isolated yield. The reaction in the absence of catalyst. |
1 |
— |
Solvent-free |
0.4 |
130 |
Traceb |
2 |
2 |
Solvent-free |
0.4 |
75 |
53 |
3 |
3 |
Solvent-free |
0.4 |
75 |
78 |
4 |
4 |
Solvent-free |
0.4 |
75 |
97 |
5 |
5 |
Solvent-free |
0.4 |
70 |
96 |
6 |
6 |
Solvent-free |
0.4 |
65 |
98 |
7 |
4 |
Acetonitrile |
0.4 |
75 |
50 |
8 |
4 |
Ethanol |
0.4 |
75 |
81 |
9 |
4 |
Ethyl acetate |
0.4 |
75 |
42 |
10 |
4 |
Solvent-free |
0.5 |
60 |
98 |
11 |
4 |
Solvent-free |
0.3 |
75 |
45 |
The generality of this approach has been demonstrated by a facile oxidation of various sulfides. The result of this study was shown in Table 2. The sulfoxides were obtained in high yields. As shown, a variety of sulfides such as dialkyl sulfides, alkyl aryl sulfides, and other sulfides with different functional groups were successfully employed to prepare the corresponding sulfoxides in excellent yields. Therefore, the results revealed that this methodology is effective for a wide range of sulfides.
Table 2 Oxidation of sulfides catalyzed by Ni-SMTU@boehmite using H2O2
Entry |
Sulfide |
Time (min) |
Yielda (%) |
Melting point °C |
Isolated yield. |
1 |
 |
75 |
97 |
29–31 |
2 |
 |
5 |
97 |
Oil |
3 |
 |
5 |
95 |
Oil |
4 |
 |
10 |
95 |
Oil |
5 |
 |
15 |
92 |
134–136 |
6 |
 |
120 |
86 |
Oil |
7 |
 |
70 |
89 |
115–117 |
8 |
 |
300 |
90 |
Oil |
9 |
 |
60 |
91 |
Oil |
Also, we examined the catalytic activity of Ni-SMTU@boehmite for the oxidative coupling of thiols into corresponding disulfides. Oxidative coupling of thiols into disulfides using H2O2 in the present of this catalyst was shown in Scheme 3. For optimization of the reaction conditions, we examined the oxidative coupling of 4-methylthiophenol as a model compound in the presence of different amount of catalyst and using different amount of H2O2 (Table 3). To choose the best reaction conditions, various solvents such as ethanol, dichloromethane, acetonitrile, and as well as solvent-free condition were used and the best results were obtained in ethanol. As shown in Table 3, 4-methylthiophenol (1 mmol) in the presence of catalytic amount of Ni-SMTU@boehmite (0.008 g, 1.3 mol%) in ethanol using 0.4 mL of H2O2 at room temperature was found to be ideal the reaction conditions for the formation of 1,2-di-p-tolyldisulfane (Table 3, entry 2).
 |
| Scheme 3 Ni-SMTU@boehmite catalysed the oxidative coupling of thiols into disulfides. | |
Table 3 Optimization of the reaction conditions for the oxidative coupling of 4-methylthiophenol (1 mmol) in the presence of different amounts of Ni-SMTU@boehmite at room temperature in various solvents using H2O2

|
Entry |
Ni-SMTU@boehmite (mg) |
Solvent |
H2O2 (mL) |
Time (min) |
Yielda (%) |
Isolated yield. |
1 |
7 |
Ethanol |
0.4 |
80 |
75 |
2 |
8 |
Ethanol |
0.4 |
80 |
94 |
3 |
9 |
Ethanol |
0.4 |
60 |
95 |
4 |
8 |
Acetonitrile |
0.4 |
80 |
43 |
5 |
8 |
CH2Cl2 |
0.4 |
80 |
Trace |
6 |
8 |
Solvent-free |
0.4 |
80 |
Trace |
7 |
8 |
Ethanol |
0.5 |
75 |
96 |
8 |
8 |
Ethanol |
0.3 |
80 |
72 |
The generality of this approach has been demonstrated by a facile oxidative coupling of aromatic and aliphatic thiols as shown in Table 4. In all the reactions no any byproducts was observed, and all products were obtained in high to excellent yields in the short reaction time.
Table 4 Oxidative coupling of thiols catalyzed by Ni-SMTU@boehmite
Entry |
Thiol |
Time (min) |
Yielda (%) |
Melting point °C |
Isolated yield. |
1 |
 |
80 |
94 |
38–40 |
2 |
 |
30 |
91 |
Oil |
3 |
 |
10 |
95 |
Oil |
4 |
 |
90 |
88 |
87–89 |
5 |
 |
5 |
93 |
174–175 |
6 |
 |
80 |
85 |
275–278 |
7 |
 |
225 |
95 |
57–59 |
8 |
 |
125 |
97 |
140–142 |
9 |
 |
15 |
94 |
57–58 |
To show the chemoselectivity of the presented protocol, the sulfides and thiols containing other functional groups were subjected to the oxidation reaction. These functional groups remained intact during the conversion of sulfides to sulfoxides and thiols to disulfides (Scheme 4).
 |
| Scheme 4 Chemoselective oxidative coupling of thiols and oxidation of sulfides in the presence of other functional groups using Ni-SMTU@boehmite as catalyst. | |
Because these heterogeneous oxidation systems was performed in mild conditions, overoxidation for oxidation of sulfides or oxidative coupling of thiols was not observed (Scheme 5).
 |
| Scheme 5 Chemoselective oxidation of sulfides and thiols in the presence Ni-SMTU@boehmite using H2O2 without overoxidation. | |
On the basis of the literatures, a plausible reaction mechanism for oxidation of sulfides and oxidative coupling of thiols in the presence of Ni-SMTU@boehmite is shown in Scheme 6.28,29 Reaction of H2O2 with Ni-catalyst leads to the intermediate A which is converted to active oxidant B. Next, nucleophilic attack of the sulfide or thiol on this intermediate gives cation C1 or C2 which, in turn, produce the corresponding products.
 |
| Scheme 6 Proposed mechanism for oxidation of sulfides and oxidative coupling of thiols in the presence of Ni-SMTU@boehmite using H2O2. | |
The reusability of the catalysts is one of their most important advantages, which makes them useful for commercial applications. We have found that Ni-SMTU@boehmite was rapidly recovered and demonstrated remarkably excellent recyclability. In order to investigate this issue, the recyclability of this catalyst was examined in the oxidation of tetrahydrothiophene. After the completion of the reaction, the catalyst was separated, washed with ethanol to remove residual product and was dried. Then, fresh substrates was added to remaining catalyst and employed for the next reaction. As shown in Fig. 8, this catalyst can be recycled up to 10 runs without any significant loss of their catalytic activity or Ni leaching.
 |
| Fig. 8 The recycling experiment of Ni-SMTU@boehmite in the oxidation of tetrahydrothiophene. | |
In order to find the leaching of the catalyst, the amount of Ni in recovered catalyst was calculated by ICP-OES after 10 runs reused. The amount of Ni in recovered catalyst was found to be 1.31 × 10−3 mol g−1 based on ICP-OES after 10 times. Therefore the catalyst can be reused without any significant leaching of nickel metal. Based on ICP-OES results, amount of Ni in the catalyst after 10 runs recycled is comparable with fresh catalyst (1.64 × 10−3 mol g−1 for fresh Ni-SMTU@boehmite) that confirmed the leaching of nickel in reaction mixture is negligible.
2.4 Comparison of the catalyst
In order to examine the efficiency of this procedure, we compared the results of the coupling oxidative of methyl(phenyl)sulfide in the presence of Ni-SMTU@boehmite with the previous methods in the literatures (Table 5). It is obvious that described procedure in this research project shows good reaction time and higher yield than the other catalysts, which has been reported previously. Also this new catalyst is comparable in terms of price, non-toxicity, stability and easy separation. In addition, the number of the recyclability of this catalyst is more than the previously reported catalysts.
Table 5 Comparison of Ni-SMTU@boehmite for the oxidation of methyl(phenyl)sulfide with previously reported procedure
Entry |
Substrate |
Catalyst |
Time (min) |
Yielda (%) [reference] |
Isolated yield. |
1 |
Ph-SCH3 |
SiO2–W2–Im |
150 |
91.9 [ref. 30] |
2 |
Ph-SCH3 |
Polymer-anchored Cu(II) |
180 |
90 [ref. 31] |
3 |
Ph-SCH3 |
VO2F(dmpz)2 |
300 |
95 [ref. 32] |
4 |
Ph-SCH3 |
Cd-salen-MCM-41 |
150 |
98 [ref. 33] |
5 |
Ph-SCH3 |
TsOH |
240 |
88 [ref. 34] |
6 |
Ph-SCH3 |
Ni-salen-MCM-41 |
156 |
95 [ref. 33] |
7 |
Ph-SCH3 |
Heterocyclic amine salts of Keggin heteropolyacids |
120 |
95 [ref. 35] |
8 |
Ph-SCH3 |
NBS |
270 |
93 [ref. 36] |
9 |
Ph-SCH3 |
DSA@MNPs |
360 |
98 [ref. 37] |
10 |
Ph-SCH3 |
Ni-SMTU@boehmite |
75 |
97 [this work] |
3 Conclusions
In summary, we have demonstrated that Ni-SMTU@boehmite can be used as an efficient and reusable nanocatalyst for the oxidative coupling of a wide range of thiols into disulfides and also oxidation of sulfides to sulfoxides using H2O2 at room temperature. This catalyst can be prepared by a simple procedure from commercially available and cheap materials. More importance, nanoboehmite is new support for heterogenization of homogeneous catalysts, which has several advantages such as high surface area, easily and readily available material to prepare, thermal and mechanical stability, ease of surface modification, easy and inexpensive procedure of preparation. The catalyst has been characterized by SEM, EDS, ICP-OES, XRD, FT-IR and TGA.
4 Experimental
4.1 Preparation of catalyst
The solutions of NaOH (6.490 g) in 50 mL of distilled water was added to solutions of Al(NO3)3·9H2O (20 g) in 30 mL distilled water as drop to drop under vigorous stirring. The resulting milky mixture was subjected to mixing in the ultrasonic bath for 3 h at 25 °C. The resulted nanoboehmite was filtered and washed by distilled water and were kept in the oven at 220 °C for 4 h. The obtained boehmite nanoparticles (1.5 g) was dispersed in 50 mL toluene by sonication for 30 min, and then 2.5 mL of (3-choloropropyl)triethoxysilane (CPTES) was added to mixture. The reaction mixture was stirred at 40 °C for 24 h. Then, the prepared nanoparticles (nCl-Pr@boehmite) was filtered, washed with ethanol and dried at room temperature. The obtained nCl-Pr@boehmite (1 g) were dispersed in 50 mL ethanol for 20 min, and then S-methylisothiourea hemisulfate salt (2.5 mmol) and potassium carbonate (2.5 mmol) were added to the reaction mixture and stirred for 28 h at 80 °C. Then, the resulting nanoparticles (SMTU@boehmite) was filtered, washed with ethanol and dried at room temperature. The obtained SMTU@boehmite (0.5 g) was dispersed in 25 mL ethanol by sonication for 20 min, and then Ni(NO3)2·6H2O (1 mmol) was added to the reaction mixture. The reaction mixture was stirred at 80 °C for 20 h. The final product (Ni-SMTU@boehmite) was filtered, washed by ethanol and dried at room temperature.
4.2 General procedure for the oxidation of sulfides
A mixture of sulfide (1 mmol), H2O2 (0.4 mL) and Ni-SMTU@boehmite (0.004 g, 0.66 mol%) was stirred at room temperature under solvent-free condition and the progress of the reaction was monitored by TLC. After completion of the reaction, catalyst was separated using filtration and washed with ethyl acetate, and the product was extracted with ethyl acetate. The organic layer was dried over anhydrous Na2SO4 (1.5 g). Finally, the organic solvents were evaporated, and products were obtained in good to high yield.
4.3 General procedure for the oxidative coupling of thiols
Ni-SMTU@boehmite (0.008 g, 1.3 mol%) was added to a mixture of thiol (1 mmol) and H2O2 (0.4 mL) in ethanol (4 mL). Then the mixture was stirred for the appropriate time at room temperature. The progress of reaction was monitored by TLC. After completion of the reaction, the catalyst was separated by filtration and the mixture was washed with ethyl acetate. The product was extracted with ethyl acetate. The organic layer was dried over anhydrous Na2SO4 (1.5 g). The products were obtained in good to high yield.
4.4 Selected spectral data
Tetrahydrothiophene 1-oxide (Table 2, entry 2). 1H NMR (400 MHz, CDCl3): δ = 2.25 (t, J = 7.61 Hz, 2H), 3.06 (t, J = 7.6 Hz, 2H) ppm.
1,2-Di-p-tolyldisulfane (Table 4, entry 1). 1H NMR (400 MHz, CDCl3): δ = 2.35 (s, 6H), 7.14 (d, J = 7.9 Hz, 4H), 7.42 (d, J = 7.9 Hz, 4H) ppm.
2,2′-Disulfanediyldiethanol (Table 4, entry 3). 1H NMR (400 MHz, CDCl3): δ = 2.60 (br, 2H), 2.89 (t, J = 5.6 Hz, 4H), 3.91 (t, J = 5.6 Hz, 4H) ppm.
Acknowledgements
This work was supported by the research facilities of Ilam University, Ilam, Iran.
References
- V. Polshettiwar and R. S. Varma, Green Chem., 2010, 12, 743 RSC.
- M. Hajjami and B. Tahmasbi, RSC Adv., 2015, 5, 59194 RSC.
- A. Islama, E. S. Chanc, Y. H. Taufiq-Yapa, S. H. Teoa and Md. A. Hoque, Ceram. Int., 2014, 40, 3779 CrossRef.
- F. Granados-Correa and J. Jimenez-Becerril, J. Hazard. Mater., 2009, 162, 1178 CrossRef CAS PubMed.
- V. Vatanpoura, S. S. Madaeni, L. Rajabi, S. Zinadini and A. A. Derakhshan, J. Membr. Sci., 2012, 401–402, 132 CrossRef.
- B. Xu, J. Wang, H. Yu and H. Gao, J. Environ. Sci., 2011, 23, S49 CrossRef.
- A. Ghorbani-Choghamarani and B. Tahmasbi, New J. Chem., 2016, 40, 1205 RSC.
- L. Rajabi and A. A. Derakhshan, Sci. Adv. Mater., 2010, 2, 163 CrossRef CAS.
- N. V. Garderen, F. J. Clemens, C. G. Aneziris and T. Graule, Ceram. Int., 2012, 38, 5481 CrossRef.
- M. B. Gholivanda, G. Malekzadehb and A. A. Derakhshan, Sens. Actuators, B, 2014, 201, 378 CrossRef.
- Y. Zheng, S. Ji, H. Liu, M. Li and H. Yang, Particuology, 2012, 10, 751 CrossRef CAS.
- C. Esposito Corcione and M. Frigione, Prog. Org. Coat., 2012, 74, 781 CrossRef.
- X. Y. Chen, H. S. Huh and S. W. Lee, Nanotechnology, 2007, 18, 285608 CrossRef.
- S. M. Kim, Y. J. Lee, K. W. Jun, J. Y. Park and H. S. Potdar, Mater. Chem. Phys., 2007, 104, 56 CrossRef CAS.
- M. Thiruchitrambalam, V. R. Palkar and V. Gopinathan, Mater. Lett., 2004, 58, 3063 CrossRef CAS.
- A. Ghorbani-Choghamarani, B. Tahmasbi, F. Arghand and S. Faryadi, RSC Adv., 2015, 5, 92174 RSC.
- M. Mirzaee, B. Bahramian and A. Amoli, Appl. Organomet. Chem., 2015, 29, 593 CrossRef CAS.
- K. Bahrami, M. M. Khodaei and M. Roostaei, New J. Chem., 2014, 38, 5515 RSC.
- Z. Zhang, W. Li, J. Liu, X. Chen and Y. Bu, J. Organomet. Chem., 2012, 706–707, 89 CrossRef CAS.
- A. Ghorbani-Choghamarani, Z. Darvishnejad and B. Tahmasbi, Inorg. Chim. Acta, 2015, 435, 223 CrossRef CAS.
- Y. Liu, H. Wang, C. Wang, J. P. Wan and C. Wen, RSC Adv., 2013, 3, 21369 RSC.
- M. Nikoorazm, A. Ghorbani-Choghamarani and N. Noori, Appl. Organomet. Chem., 2015, 29, 328 CrossRef CAS.
- Q. Zeng, W. Weng and X. Xue, Inorg. Chim. Acta, 2012, 388, 11 CrossRef CAS.
- A. Rostami, B. Tahmasbi, F. Abedi and Z. Shokri, J. Mol. Catal. A: Chem., 2013, 378, 200 CrossRef CAS.
- M. Hajjami, A. Ghorbani-Choghamarani, R. Ghafouri-Nejad and B. Tahmasbi, New J. Chem., 2016, 40, 3066 RSC.
- F. Havasi, A. Ghorbani-Choghamarani and F. Nikpour, Microporous Mesoporous Mater., 2016, 224, 26 CrossRef CAS.
- A. Ghorbani-Choghamarani, B. Tahmasbi and P. Moradi, Appl. Organomet. Chem., 2016, 30, 422 CrossRef CAS.
- R. Das and D. Chakraborty, Tetrahedron Lett., 2010, 51, 6255 CrossRef CAS.
- B. Karami, M. Montazerozohori, M. Moghadam, M. H. Habibi and K. Niknam, Turk. J. Chem., 2005, 29, 539 CAS.
- S. Thurow, V. A. Pereira, D. M. Martinez, D. Alves, G. Perin, R. G. Jacob and E. J. Lenardão, Tetrahedron Lett., 2011, 52, 640 CrossRef CAS.
- S. M. Islam, A. S. Roy, P. Mondal, K. Tuhina, M. Mobarak and J. Mondal, Tetrahedron Lett., 2012, 53, 127 CrossRef CAS.
- S. Hussain, D. Talukdar, S. K. Bharadwaj and M. K. Chaudhuri, Tetrahedron Lett., 2012, 53, 6512 CrossRef CAS.
- M. Nikoorazm, A. Ghorbani-Choghamarani, H. Mahdavi and S. M. Esmaeili, Microporous Mesoporous Mater., 2015, 211, 174 CrossRef CAS.
- B. Yu, C. X. Guo, C. L. Zhong, Z. F. Diao and L. N. He, Tetrahedron Lett., 2015, 55, 1818 CrossRef.
- A. G. Sathicq, G. P. Romanelli, V. Palermo, P. G. Vazquez and H. J. Thomas, Tetrahedron Lett., 2008, 49, 1441 CrossRef CAS.
- B. Karimi and D. Zareyee, J. Iran. Chem. Soc., 2008, 5, Sl03 Search PubMed.
- A. Ghorbani-Choghamarani, H. Rabiei, B. Tahmasbi, B. Ghasemi and F. Mardi, Res. Chem. Intermed., 2016, 42, 5723 CrossRef CAS.
|
This journal is © The Royal Society of Chemistry 2016 |
Click here to see how this site uses Cookies. View our privacy policy here.