DOI:
10.1039/C6RA08047B
(Paper)
RSC Adv., 2016,
6, 61393-61401
The improvement in cryogenic mechanical properties of nano-ZrO2/epoxy composites via surface modification of nano-ZrO2
Received
29th March 2016
, Accepted 14th June 2016
First published on 21st June 2016
Abstract
This study investigated the cryogenic mechanical properties of modified nano-ZrO2 reinforced epoxy composites. Nano-ZrO2 was surface modified by (3-aminopropyl)triethoxysilane (APTES) and results of Fourier transform infrared spectroscopy (FTIR) verified that APTES was successfully grafted onto the surface of nano-ZrO2. Transmission electron microscopy (TEM) observations indicated that APTES modification was favorable to the dispersion of nano-ZrO2 in an epoxy matrix. Glass transition temperatures of the modified nano-ZrO2/epoxy composites were also improved compared with those of the neat epoxy resin and the unmodified nano-ZrO2/epoxy composite. Results of the mechanical tests showed that the modified nano-ZrO2 could improve the mechanical properties of the epoxy composites more effectively than unmodified ones. Tensile strength and failure strain of the modified nano-ZrO2/epoxy composites were at most increased by 30.2% and 49.7% at room temperature (RT), while their highest enhancements at 90 K were 26.4% and 21.1%, respectively, compared with those of the neat epoxy resin. Besides, fracture toughness at RT and 90 K were at most increased by 53.3% and 39.4%, respectively. These enhancements were mainly attributed to the strong modified nano-ZrO2/epoxy interfacial bonding and the better dispersion of the modified nano-ZrO2 in the epoxy matrix. Summarily, it could be concluded that APTES modified nano-ZrO2 is a promising filler for enhancing cryogenic mechanical properties of epoxy resins.
1. Introduction
Epoxy resins have been an ideal selection as the matrix material to manufacture fiber reinforced composites in fuel tank fabrication, the aerospace, marine and automotive industries owing to their thermosetting nature, high specific strength, good chemical and corrosion resistance.1–3 Current reusable launch vehicles require more and more lightweight materials to manufacture their structural components,4,5 including liquid oxygen tanks. After long-term exploration and unremitting efforts, carbon fiber reinforced epoxy composites have been proved to replace alloy materials to manufacture liquid oxygen tanks, resulting in 27% reduction of the total tank weight. Thus, the total vehicle dry weight reduction is 7.5%. This equals to a staggering 37% of the payload to low-earth orbit.6 However, using carbon fiber/epoxy composites as the material of liquid oxygen tanks must overcome the intrinsic brittle nature of epoxy resins, which shows poor fracture toughness or poor resistance to crack initiation and propagation, especially at liquid oxygen temperature (90 K).7–10 Many attempts have been made to improve fracture toughness of epoxy resins in the last few decades, such as by adding rubbers or thermoplastic polymers. But the addition of rubbers and thermoplastic polymers may result in the deterioration of basic mechanical properties, such as strength, modulus and glass transition temperature (Tg). Besides, using thermoplastic modifiers leads to a poor processability with a high viscosity, which is mainly caused by their poor compatibility with epoxy resins.11–13 Therefore, an alternative approach for toughening epoxy resins is proposed by incorporating some dispersed inorganic nanoparticles as a second phase into cross-linked epoxy resins to achieve epoxy based composites. Numerous papers have reported enhancing the physical and mechanical properties of epoxy resins by adding small amount of nanoparticles, such as TiO2,14 Al2O3,15 SiO2,16,17 ZnO,18 SiC,19 aluminum,20 clay,21,22 etc. It is found that nanoparticles can efficiently and simultaneously improve modulus, failure strength and fracture toughness of epoxy resins without sacrificing their original properties.23
Zirconium dioxide (ZrO2) is one of the most promising nanoparticles that can be employed to enhance mechanical properties of epoxy resins. It possesses excellent properties such as: high strength, high fracture toughness, excellent wear resistance, high hardness and excellent chemical resistance.24–26 However, few published literatures focus on the effect of ZrO2 on mechanical properties of epoxy resins, especially at cryogenic temperature.
However, nanoparticles reinforced epoxy composites usually suffer from some problems. Typically, the interfacial bonding between epoxy resin and reinforced nanoparticles is weak since nanoparticles can easily agglomerate in epoxy matrix, resulting in high stress concentration. Thus, under force cracks propagate from these weak sites, hence reducing the resultant mechanical properties of the epoxy composites.27,28 Many efforts have been devoted to develop effective methods for the dispersion of nanoparticles in epoxy resins. It is found that surface modification by organic compounds can efficiently disperse nanoparticles in epoxy matrix. It can be achieved via the direct silanization of nanoparticles by using silane coupling agents, forming a durable chemical junction between the two incompatible phases.29,30 These silicon-bearing monomers contain two different types of reactive groups: Si–OR groups that can condense with hydroxyl groups on the surface of a filler and another type of functional group that is compatible or capable of reacting with the matrix material. Thus, the two functional groups allow silanes to “couple” dissimilar materials together, and significant improvements in filler–matrix bonding strengths are often achieved. For this reason silanes have long been used as adhesion promoters in composite manufacturing and are available with functionalities to match nearly any polymer matrix material.31
The present work focuses on the performance of epoxy matrix composites containing modified ZrO2 nanoparticles. ZrO2 nanoparticles were firstly surface modified with (3-aminopropyl)triethoxysilane (APTES) and then added to bisphenol F epoxy resin to enhance the cryogenic mechanical properties of the composites. Fourier transform infrared spectroscopy (FTIR) and Transmission Electron Microscope (TEM) analysis were carried out to characterize the chemical structure and the dispersion state of the modified nanoparticles. Differential Scanning Calorimetry (DSC) was utilized to probe the effect of modified ZrO2 on glass transition temperature of the epoxy resin. Tensile properties and fracture toughness at both room temperature and 90 K of the neat epoxy resin and the epoxy composites containing unmodified and APTES modified ZrO2 nanoparticles were investigated and compared in detail. The fracture surfaces of the specimens were observed using scanning electron microscope (SEM).
2. Experimental
2.1 Materials
Bisphenol F epoxy resin with epoxy equivalent weight (EEW) of 170 g mol−1 was kindly supplied by Yueyang Chemical Co., Ltd., China. Its trade name is NPEF-170. Diaminodiphenyl methane (DDM), analytically pure, and absolute ethanol (99.7%) were purchased from Sinopharm Chemical Reagent Co., Ltd., China. ZrO2 nanoparticles (nano-ZrO2) with an average particle size of 50 nm were provided by Nanjing Tianxing New Materials Co., Ltd. (3-Aminopropyl)triethoxysilane (APTES) was obtained from Tianjin Damao Chemical Reagent Co., Ltd., China. Acetone was purchased from Beijing Chemical Works, China.
2.2 Preparation of APTES modified nano-ZrO2
In the first stage, 10 g of nano-ZrO2 were kept in a vacuum chamber for 1 h at 120 °C and then dispersed in 50 ml absolute ethanol via stirring for 1 h at ambient temperature and sonicated (KQ2200B, Kunshan Ultrasonic Instrument co., Ltd., China) for 20 min under a power of 100 W, 40 kHz frequency. In the second step, 50 wt% (5 g) APTES was gradually added to the dispersion and stirred for further 24 h at 25 °C. Finally, it was centrifuged (6000 rpm) and the residue washed with absolute ethanol for three times to remove excess APTES.
2.3 Preparation of the nano-ZrO2/epoxy composites
The epoxy resin was preheated and stirred under 70 °C to low its viscosity. Then a calculated amount of nano-ZrO2 dispersed in acetone was added slowly to the epoxy resin under vigorous stirring and stirred for 12 h at 70 °C. After degassing in vacuum under 70 °C to remove remained acetone, a stoichiometric amount of curing agent, DDM, was added to the mixture and stirred until a homogeneous state was achieved. The mixture was degassed again to remove trapped air during the mixing step, poured into a hot Teflon mold, and cured in an oven at 100 °C for 2 h, 130 °C for 2 h, and 160 °C for 4 h. After that the specimens were allowed to cool slowly to ambient temperature to prevent cracking. Various formulations for different specimens are listed in Table 1. The preparation process of the modified nano-ZrO2/epoxy composites is depicted in Fig. 1.
Table 1 Formulations of the specimens
Specimen |
NPEF-170 (g) |
DDM (g) |
Unmodified ZrO2 (g) |
Modified ZrO2 (g) |
EP |
77.5 |
22.5 |
|
|
EP-3 |
77.5 |
22.5 |
3 |
|
EP–A-1 |
77.5 |
22.5 |
|
1 |
EP–A-2 |
77.5 |
22.5 |
|
2 |
EP–A-3 |
77.5 |
22.5 |
|
3 |
EP–A-4 |
77.5 |
22.5 |
|
4 |
EP–A-5 |
77.5 |
22.5 |
|
5 |
 |
| Fig. 1 Schematic diagram of the preparation process of the modified nano-ZrO2/epoxy composites. | |
2.4 Measurements
FTIR was performed to characterize APTES modified nano-ZrO2, on a Perkin Elmer Spectrum One FTIR from 4000 to 500 cm−1. TEM (Tecnai G2 F30 S-Twin, FEI) was used to observe the dispersion state of the unmodified and modified nano-ZrO2. TEM specimens were prepared as ultrathin slices with a thickness of 50 nm that were cut with a cryo-ultramicrotome. DSC was used to obtain glass transition temperature (Tg) of the epoxy composites, with a Thermal Analysis (TA) DSC-Q10 in a nitrogen gas flow of 40 ml min−1, at a heating rate of 10 °C min−1. SEM (Quanta 450, FEI) was used to observe fracture surfaces of the specimens. The surface element compositions of the modified ZrO2 were measured using the X-ray photoelectron spectroscopy (XPS) along with an X-ray photoelectron spectrometer (PHI 5300, Perkin-Elmer) equipped with magnesium X-ray source.
The curing degrees of the neat epoxy resin and the epoxy composites were measured. The specimen was firstly ground into powder. The weighed powder and 150 ml acetone were then transfer into flask with a reflux condenser. The flask was heated under reflux at 80 °C for 3 h. After cooling to room temperature, the undissolved epoxy polymer was collected and dried in a vacuum oven at 105 °C for 3 h and weighed again. The curing degree was determined by the following equation:
|
 | (1) |
where CD represents the curing degree,
A represents the weight of the powder before the reaction, and
B represents the weight of the power after the reaction and drying process.
Tensile properties of the cured epoxy resins at room temperature (RT) and liquid oxygen temperature (90 K) were measured by an SDS-100 electro-hydraulic servo testing machine (Changchun Research Institute for Mechanical Science Co., Ltd., China), with a crosshead speed of 1 mm min−1 according to ASTM D638-99. During the cryogenic tensile tests, an environmental test chamber (Changchun Fangrui Technology Co., Ltd., China) with a temperature controller was employed to simulate the cryogenic environment in our laboratory, as shown in Fig. 2. For safety concern, we used liquid nitrogen to replace liquid oxygen as cooling medium. By spraying and evaporating liquid nitrogen, the temperature of the environmental chamber was gradually lowered to 90 K and kept at that temperature for 5 min to reach the thermal equilibrium condition before the cryogenic mechanical testing.
 |
| Fig. 2 Photographs of the environmental test chamber. | |
Fracture toughness (KIC) at RT and 90 K was determined using a single-edge notch bend (SENB) test with a crosshead speed of 1 mm min−1, according to ASTM D5045-14. For measuring fracture toughness at 90 K, specimens were firstly immersed in liquid oxygen for over 10 min so that they could be precooled down to 90 K. Then the specimen was quickly put into a test box filled with liquid nitrogen which was designed in our laboratory. After that, the test was conducted immediately. The consumption of liquid nitrogen could be significantly reduced by this test method compared to using the environmental test chamber. The schematic diagram of the cryogenic SENB test is given in Fig. 3. KIC value was calculated using the following equation.
|
 | (2) |
where
f(
a/
W) is the polynomial geometrical correction factor and given as:
|
 | (3) |
where
Pm is the maximum load at crack extension,
S is the span of the specimen (32 mm),
D is the specimen thickness (4 mm),
W is the specimen width (8 mm) and
a is the crack length.
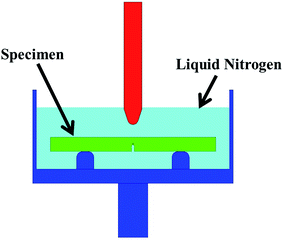 |
| Fig. 3 Schematic diagram of the cryogenic SENB test. | |
3. Results and discussion
3.1 FTIR and XPS analysis
Fig. 4 shows the FTIR spectra of APTES, APTES modified and neat ZrO2. For the modified ZrO2, the strong peak at 3425 cm−1 can be ascribed to the stretch vibration of –OH on the surface of ZrO2. The absorption peaks at 2923 cm−1 and 2850 cm−1 can be attributed to the stretch vibration of C–H in APTES. Besides, the bending vibration of C–H can be detected at 1492 cm−1 and 1452 cm−1. The characteristic peak of N–H bending vibration in APTES is observed at 1601 cm−1. The peak at 1049 cm−1 indicates the existence of Zr–O–Si. The peaks of Zr–O–Zr stretch vibration are found at 752 cm−1 and 697 cm−1.32,33 As outlined above, it can be concluded that APTES was successfully grafted on the surface of ZrO2.
 |
| Fig. 4 FTIR spectra of APTES, APTES modified and neat ZrO2. | |
XPS spectrum of the modified ZrO2 is shown in Fig. 5. The Si2p and Si2s peaks are located at 102 eV and 153 eV, respectively. The C1s and N1s peaks are observed at 285 eV and 400 eV, respectively. These phenomena prove that nano-ZrO2 was successfully modified by APTES.
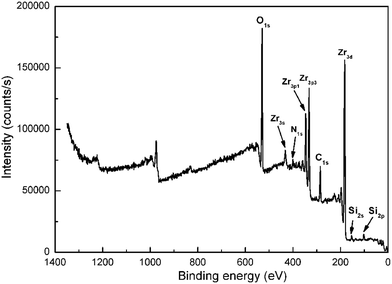 |
| Fig. 5 XPS spectrum of the APTES modified ZrO2. | |
3.2 TEM analysis
Transmission electron microscopy (TEM) was used to assess the dispersion state of nano-ZrO2 within the epoxy matrix. Fig. 6 shows the TEM images of the epoxy composites reinforced with unmodified (3 wt%) and APTES modified (3 and 5 wt%) nano-ZrO2 respectively. It could be seen that unmodified nano-ZrO2 in the epoxy matrix exhibited severe agglomeration, as shown in Fig. 6. Hydroxyl groups on the surface of nanoparticles promoted them to aggregate to form hydrogen bonds. Besides, their large specific surface area and high surface energy also contributed to the agglomeration.34 After the nanoparticles were modified by APTES, the agglomeration degree was significantly decreased, as shown in Fig. 6. This was because ethoxy groups in APTES could react with hydroxyl groups on the surface of the nanoparticles, then the organic groups would be grafted on the nanoparticles, resulting in enhanced compatibility of nanoparticles within epoxy matrix. In addition, amine groups of APTES grafted nanoparticles could participate in the curing process along with the epoxy–amine system. The more nanoparticles were in contact with the polymer, the higher was the interaction degree.35 Thus, the interfacial adhesion between modified nanoparticles and resin matrix would be stronger than unmodified ones. These factors could effectively prevent particle agglomeration. When the modified nanoparticle loading further increased to 5 wt%, the obtained epoxy composite still possessed lower agglomeration degree than the one containing 3 wt% of unmodified nanoparticles. It could be concluded that APTES modification is favorable to the dispersion of nano-ZrO2 in epoxy resins.
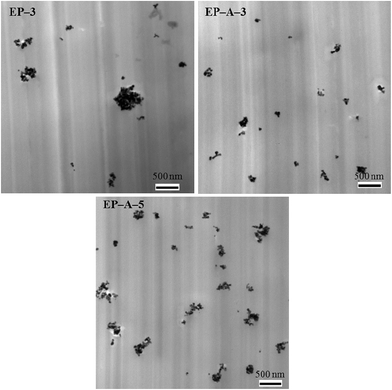 |
| Fig. 6 TEM images of the specimens. | |
3.3 DSC analysis and curing degree
Glass transition temperatures (Tg) of the neat and nano-ZrO2 reinforced epoxy resins were measured by DSC and their DSC curves are depicted in Fig. 7. Values of Tg, taken as the midpoint of the heat capacity transition between the upper and lower points of deviation from the extrapolated liquids and glass lines, are listed in Fig. 7. In Fig. 7, the DSC curves of all the specimens are flat and do not show any endothermic and exothermic peaks, indicating they were cured completely. Tg of the neat epoxy resin was 139.7 °C. When 3 wt% of unmodified nano-ZrO2 was introduced into the epoxy resin, Tg was slightly decreased to 138.8 °C. This might be attributed to the aggregation of the nanoparticles. The aggregated nanoparticles with relatively larger dispersion size could hinder the curing reaction and reduce the curing degree, resulting in the decrease of cross-linking density of the epoxy composite.36 However, all the epoxy composites reinforced with APTES modified nano-ZrO2 (1–5 wt%) demonstrated elevated Tg compared to the neat epoxy resin. It is known that amine groups on APTES can react with epoxy groups, establishing chemical bonds between nanoparticles and epoxy matrix. Thus, the interfacial reaction between nanoparticles and epoxy matrix could be significantly enhanced. The domain size of nanoparticles was reduced and then their dispersion degree was improved. The free space among macromolecules decreased and therefore the mobility of chain segments was restricted, leading to increased Tg of epoxy composites.27 Besides, it could be noted that Tg was increased with the increase of the modified nanoparticle content until it reached to 3 wt%. After that, Tg demonstrated decreased tendency. The reason might be that higher nanoparticle content inevitably caused the aggregation of nanoparticles even they were modified by APTES. The decrease of cross-linking density and the enhancement of interfacial reaction were two competing factors. As the nanoparticle content increasing, the decrease of cross-linking density gradually dominated, leading to the decrease of Tg.
 |
| Fig. 7 DSC curves of the specimens. | |
The curing degrees of the neat epoxy resin and the epoxy composites were also determined. The results are depicted in Fig. 8. The curing degree of the neat epoxy resin was as high as 96.9%. After introducing 3 wt% ZrO2, the curing degree decreased to 94.3%. This decrease was attributed to the agglomeration of ZrO2 which would hinder the curing reaction. The epoxy composites containing the modified ZrO2 (1–3%) exhibited the curing degrees of 96.7%, 97.1% and 96.6%, respectively, indicating that the modified ZrO2 with excellent dispersion state did not obviously influence the curing degree of the epoxy resin. However, as the nanoparticle content further increased, the curing degrees of the epoxy composites showed the decreasing trend. This was also due to that the agglomeration inevitably happened at higher nanoparticle content.
 |
| Fig. 8 Curing degrees of the specimens. | |
3.4 Mechanical properties
Effects of unmodified and APTES modified nano-ZrO2 on tensile properties of the epoxy resin at both room temperature (RT) and 90 K were investigated. Tensile stress–strain curves of all the specimens are illustrated in Fig. 9. Due to the existence of many noise data, the curves for 90 K were smoothed by Nonlinear Curve Fit in OriginPro 8.5 commercial software without sacrificing their original tendency. The detailed data including tensile strength, failure strain are summarized in Table 2. At RT, tensile strength and failure strain of the neat epoxy resin were 79.6 MPa and 4.57%, respectively. When 3 wt% of unmodified nanoparticles were introduced to the epoxy resin, the strength slightly increased to 79.9 MPa, but the strain reduced to 3.40%. After the nanoparticles were modified by APTES, the obtained epoxy composite only containing 1 wt% of nanoparticles exhibited obviously enhanced strength and strain, which increased to 89.8 MPa and 4.76%, respectively. When the content of APTES modified nanoparticles increased to 3 wt%, tensile strength and failure strain of the epoxy composite reached to their maximums of 103.6 MPa and 6.84%, increased by as much as 30.2% and 49.7%, respectively, compared with those of the neat epoxy resin. These results indicated that APTES modified nano-ZrO2 improved tensile properties of the epoxy composites more effectively than unmodified one, which was mainly attributed to the better dispersion of modified nanoparticles, the increase of cross-linking degree of the epoxy composite and the enhanced interfacial force between nanoparticles and epoxy matrix. Enhanced dispersion state implies large contact areas between nanoparticles and epoxy matrix, which benefit an efficient stress transfer through weak epoxy matrix to strong nanoparticles and result in improved tensile strength and failure strain. Moreover, the quality of interface in epoxy composites usually plays an important role in capability of materials to transfer stresses and elastic deformation from matrix to fillers. Amine groups of APTES modified nanoparticles participated in the curing process along with epoxy–amine system, leading to interfacial adhesion between modified nanoparticles and resin matrix, which would be stronger than unmodified ones.37 As a result of strong adhesion, nanoparticles were able to carry any part of external load. Hence, increased tensile strength and failure strain in modified nano-ZrO2/epoxy composites reveals that the stresses were efficiently transferred via more powerful interface. However, tensile strength and failure strain were decreased with further increasing the modified nanoparticle content. This phenomenon was caused by the fact that higher nanoparticle content inevitably resulted in more agglomerations and weakened interfacial adhesion, which would induced higher stress concentration in the epoxy composite.
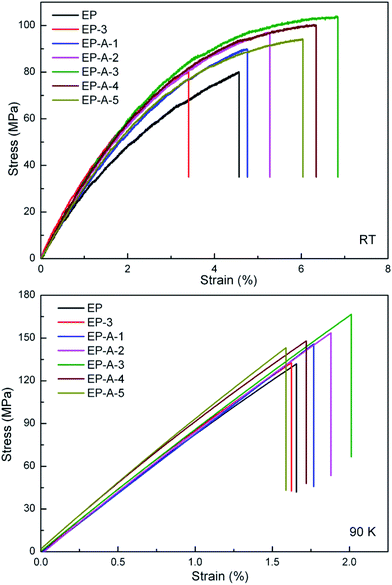 |
| Fig. 9 Tensile stress–strain curves of the specimens at RT and 90 K. | |
Table 2 Mechanical properties of the specimens
Specimen |
Tensile strength (MPa) |
Young's modulus (GPa) |
Failure strain (%) |
KIC (MPa m1/2) |
RT |
90 K |
RT |
90 K |
RT |
90 K |
RT |
90 K |
EP |
79.6 |
131.8 |
2.82 |
8.63 |
4.57 |
1.66 |
1.65 |
2.36 |
EP-3 |
79.9 |
132.6 |
3.48 |
8.86 |
3.40 |
1.62 |
1.61 |
2.43 |
EP–A-1 |
89.8 |
145.8 |
3.05 |
8.37 |
4.76 |
1.77 |
1.96 |
2.65 |
EP–A-2 |
96.9 |
153.6 |
3.24 |
8.74 |
5.28 |
1.88 |
2.17 |
3.07 |
EP–A-3 |
103.6 |
166.6 |
3.42 |
8.70 |
6.84 |
2.01 |
2.53 |
3.29 |
EP–A-4 |
99.8 |
147.9 |
3.34 |
9.29 |
6.34 |
1.72 |
2.45 |
2.93 |
EP–A-5 |
94.1 |
143.2 |
3.11 |
9.36 |
6.04 |
1.59 |
2.28 |
2.71 |
In the cryogenic cases the epoxy composites also displayed increased tensile strength, failure strain and modulus compared with the neat epoxy resin. Both tensile strength and failure strain reached their maximums at 3 wt% of APTES modified nanoparticle content, which were increased by as much as 26.4% and 21.1%, respectively, compared with those of the neat epoxy resin. Table 2 exhibits that tensile strength was higher at 90 K than that at RT with the same material composition. The reason was that on the one hand, when the temperature decreased from RT to 90 K, the chemical bond and molecules of epoxy matrix would shrink and the binding forces between molecules would become strong. Thus, a larger load would be needed to break epoxy matrix at 90 K, leading to a higher strength of epoxy matrix at 90 K than at RT. On the other hand, thermal contraction of epoxy matrix due to the decrease of temperature increased the clamping stress to nano-ZrO2 at 90 K, this would lead to a stronger ZrO2–epoxy interfacial bonding.7
From Fig. 9 and Table 2, it can be seen that all the epoxy composites possessed higher tensile modulus than the neat epoxy resin, which resulted from higher modulus of the nanoparticles than the epoxy matrix. At RT, Young's modulus of the modified epoxy composites firstly increased and then decreased with the increase of modified nano-ZrO2 content. This was because higher nanoparticle content induced more agglomerations which would result in the decrease of the crosslinking density, thus Young's modulus decreased. At 90 K, Young's modulus of the modified epoxy composites increased with the increase of modified nano-ZrO2 content. The cryogenic environment would induce the contraction of the molecular of the epoxy matrix. Thus the nanoparticles were wrapped more tightly by the epoxy matrix. The effect of the agglomerations on Young's modulus would be reduced.
Comparisons of fracture toughness (KIC) of the neat epoxy resin and the nano-ZrO2/epoxy composites at both RT and 90 K were carried out using the SENB test. KIC values are depicted as a broken line graph in Fig. 10 and summarized in Table 2. It shows that the role of unmodified nano-ZrO2 in improving the fracture toughness was weak and fracture toughness of the epoxy composite containing 3 wt% of unmodified nanoparticles was almost same to that of the neat epoxy resin. In contrast to unmodified nano-ZrO2, APTES modified nano-ZrO2 played an important role in improving the fracture toughness of the epoxy composites. It can be seen from Fig. 10 that fracture toughness at both RT and 90 K were increased with increasing the modified nanoparticle content and reached the maximum at 3 wt% content with an increase of 53.3% and 39.4%, respectively, compared with the neat epoxy resin. This was because modified nanoparticles with a good dispersion could resist the propagation of cracks in epoxy matrix by the toughening mechanism of crack path deflection, leading to fracture resistance improvement of epoxy composites.12 However, more nanoparticle aggregations would take place as the nano-ZrO2 content was further increased. Thus, KIC demonstrated a decreased trend after 3 wt% of nano-ZrO2 content since the negative deteriorating effect of aggregations could overwhelm the toughening effect of modified nanoparticles at high nanoparticle content.
 |
| Fig. 10 Broken line graph of KIC. | |
In addition, Table 2 also shows that fracture toughness was higher at 90 K than at RT. Kim et al. reported that epoxy resins can have higher fracture toughness at cryogenic temperature than at RT since the free spaces defined as the unoccupied ones within the molecules still exist and the intermolecular forces between shrunk networks are increased with the temperature decrease.38
3.5 Fracture surface analysis
Fracture surfaces of the neat epoxy resin and the nano-ZrO2 reinforced epoxy composites were observed using SEM. As shown in Fig. 11, the fracture surfaces of the neat epoxy resin were smooth and exhibited river lines which were the typical characteristics of brittle fracture at RT and 90 K,39 accounting for its relatively poor fracture resistance. Compared to the neat epoxy resin, the epoxy composite with 3 wt% of unmodified nano-ZrO2 showed rough surfaces as a result of presence of nanoparticles. However, much rougher fracture surfaces at both RT and 90 K were clearly observed for the epoxy composites containing modified nano-ZrO2, which corresponded to the significantly improved mechanical properties. Obviously, modified nano-ZrO2 generated greater fracture areas through the development of rougher surfaces, which allowed them to resist crack propagation. Thus, the fracture energy was effectively dissipated, and the toughness as well as failure strain increased in the polymer matrix. This leads to the conclusion that the addition of nanoparticles to the polymer matrix significantly affects the roughness of fracture surface and, in consequence, the balance between tough and brittle behavior of the matrix. Besides, rough fracture surfaces indicate deflection of crack propagation, namely crack paths deviate from their original planes because of bonded nanoparticles making greater resistance to crack propagation.7,40 This phenomenon also reveals that modified nano-ZrO2 were embedded and tightly held by epoxy matrix and they were broken instead of being pulled out during the mechanical test. This further verifies the existence of strong interfacial bonding between the two phases.
 |
| Fig. 11 Fracture surfaces of the specimens. | |
4. Conclusions
In the present study, nano-ZrO2 was surface modified by APTES and then added to epoxy resin to enhance its cryogenic mechanical properties. The results of FTIR verified that APTES was successfully grafted on the surface of nano-ZrO2. TEM observations indicated that APTES modification is favorable to the dispersion of nano-ZrO2 in epoxy matrix. Glass transition temperatures of the modified nano-ZrO2/epoxy composites were also improved compared with those of the neat epoxy resin and the unmodified nano-ZrO2/epoxy composite due to the enhanced interfacial reaction between modified nano-ZrO2 and epoxy matrix. Tensile properties and fracture toughness of the epoxy composites and the neat epoxy resin at both room temperature (RT) and cryogenic temperature (90 K) were investigated and compared. It was shown that APTES modified nano-ZrO2 improved mechanical properties of the epoxy composites more effectively than unmodified one. Tensile strength and failure strain of the epoxy composites were at most increased by 30.2% and 49.7% at RT, while at 90 K the maximum increases were 26.4% and 21.1%, respectively, compared with those of the neat epoxy resin. Besides, fracture toughness of the modified epoxy composites at RT and 90 K were at most increased by 53.3% and 39.4%, respectively. These enhancements were mainly attributed to the strong modified nano-ZrO2/epoxy interfacial bonding and the better dispersion of modified nano-ZrO2 in epoxy matrix. Summarily, it could be concluded that APTES modified nano-ZrO2 is a promising filler for enhancing cryogenic mechanical properties of epoxy resins for liquid oxygen tank applications.
Acknowledgements
This work was supported by the National Natural Science Foundation of China (11172053, 91016024, 51102031 and 11302036), the New Century Excellent Talents in University (NCET110055) and the Fundamental Research Funds for the Central Universities (DUT12LK33, DUT14LK26).
References
- C. Hamciuc, T. Vlad-Bubulac, D. Serbezeanu, I. Carja, E. Hamciuc, G. Lisa and V. F. Pérez, RSC Adv., 2016, 6, 22764–22776 RSC
. - S. R. Kumar, J. Dhanasekaran and S. K. Mohan, RSC Adv., 2015, 5, 3709–3719 RSC
. - L. Pan, S. Lu, X. Xiao, Z. He, C. Zeng, J. Gao and J. Yu, RSC Adv., 2015, 5, 3177–3186 RSC
. - Q. Zhang, S. Liang, G. Sui and X. Yang, RSC Adv., 2015, 5, 25208–25214 RSC
. - L. Guadagno, M. Raimondo, U. Vietri, L. Vertuccio, G. Barra, B. De Vivo, P. Lamberti, G. Spinelli, V. Tucci, R. Volponi, G. Cosentino and F. De Nicola, RSC Adv., 2015, 5, 6033–6042 RSC
. - M. J. Robinson, J. M. Stoltzfus and T. N. Owens, 42nd AIAA/ASME/ASCE/AHS/ASC Structures, Structural Dynamics, and Materials Conference and Exhibit, Seattle, April, 2001 Search PubMed
. - Y. Zhao, Z. Chen, Y. Liu, H. Xiao, Q. Feng and S. Fu, Composites, Part A, 2013, 55, 178–187 CrossRef CAS
. - Z. Chen, J. Yang, Q. Ni, S. Fu and Y. Huang, Polymer, 2009, 50, 4753–4759 CrossRef CAS
. - J. Yang, Z. Chen, Q. Feng, Y. Deng, Y. Liu, Q. Ni and S. Fu, Composites, Part B, 2012, 43, 22–26 CrossRef
. - X. Shen, Y. Liu, H. Xiao, Q. Feng, Z. Yu and S. Fu, Compos. Sci. Technol., 2012, 72, 1581–1587 CrossRef CAS
. - Z. Chen, G. Yang, J. Yang, S. Fu, L. Ye and Y. Huang, Polymer, 2009, 50, 1316–1323 CrossRef CAS
. - M. Zamanian, M. Mortezaei, B. Salehnia and J. E. Jam, Eng. Fract. Mech., 2013, 97, 193–206 CrossRef
. - W. Thitsartarn, X. Fan, Y. Sun, J. C. C. Yeo, D. Yuan and C. He, Compos. Sci. Technol., 2015, 118, 63–71 CrossRef CAS
. - H. A. Al-Turaif, Prog. Org. Coat., 2010, 69, 241–246 CrossRef CAS
. - W. Jiang, F. L. Jin and S. J. Park, J. Ind. Eng. Chem., 2012, 594–596 CrossRef CAS
. - H. Shi, F. Liu, L. Yang and E. Han, Prog. Org. Coat., 2008, 62, 359–368 CrossRef CAS
. - B. Wei, S. Song and H. Cao, Mater. Des., 2011, 32, 4180–4186 CrossRef CAS
. - B. Ramezanzadeh and M. M. Attar, Prog. Org. Coat., 2011, 71, 242–249 CrossRef CAS
. - H. Alamri and I. M. Low, J. Appl. Polym. Sci., 2012, 126, 221–231 CrossRef
. - S. C. Zunjarrao and R. P. Singh, Compos. Sci. Technol., 2006, 66, 2296–2305 CrossRef CAS
. - A. Mirmohseni and S. Zavareh, Mater. Des., 2010, 31, 2699–2706 CrossRef CAS
. - M. Silani, S. Z. Rad, M. Esfahanian and V. B. C. Tan, Composite Structures, 2012, 3142–3148 CrossRef
. - M. Wang, X. Fan, W. Thitsartarn and C. He, Polymer, 2015, 58, 43–52 CrossRef CAS
. - M. Behzadnasab, S. M. Mirabedini, K. Kabiri and S. Jamali, Corros. Sci., 2011, 53, 89–98 CrossRef CAS
. - M. Behzadnasab, S. M. Mirabedini and M. Esfandeh, Corros. Sci., 2013, 75, 134–141 CrossRef CAS
. - S. M. Mirabedini, M. Behzadnasab and K. Kabiri, Composites, Part A, 2012, 43, 2095–2106 CrossRef CAS
. - Z. S. Pour and M. Ghaemy, Prog. Org. Coat., 2014, 77, 1316–1324 CrossRef CAS
. - M. Sabzi, S. M. Mirabedini, J. Zohuriaan–Mehr and M. Atai, Prog. Org. Coat., 2009, 65, 222–228 CrossRef CAS
. - M. Bazzar, M. Ghaemy and R. Alizadeh, Polym. Degrad. Stab., 2012, 97, 1690–1703 CrossRef CAS
. - M. Takafuji, S. Ide, H. Ihara and Z. Xu, Chem. Mater., 2004, 16, 1983–1997 CrossRef
. - D. Vennerberg, Z. Rueger and M. R. Kessler, Polymer, 2014, 55, 1854–1865 CrossRef CAS
. - T. Huang, Y. Su, T. Yeh, H. Huang, C. Wu, K. Huang, Y. Chou, J. Yeh and Y. Wei, Electrochim. Acta, 2011, 56, 6142–6149 CrossRef CAS
. - A. T. Ravichandran, K. Catherine Siriya Pushpa, K. Ravichandran, K. Karthika, B. M. Nagabhushana, S. Mantha and K. Swaminathan, Superlattices Microstruct., 2014, 75, 533–542 CrossRef CAS
. - T. S. Radoman, J. V. Džunuzović, K. B. Jeremić, B. N. Grgur, D. S. Miličević, I. G. Popović and E. S. Džunuzović, Mater. Des., 2014, 62, 158–167 CrossRef CAS
. - A. A. Javidparvar, B. Ramezanzadeh and E. Ghasemi, Prog. Org. Coat., 2016, 90, 10–20 CrossRef CAS
. - S. Sprenger, M. H. Kothmann and V. Altstaedt, Compos. Sci. Technol., 2014, 105, 86–95 CrossRef CAS
. - S. Ponyrko, L. Kobera, J. Brus and L. Matějka, Polymer, 2013, 54, 6271–6282 CrossRef CAS
. - B. C. Kim, S. W. Park and D. G. Lee, Composite Structures, 2008, 86, 69–77 CrossRef
. - T. Sun, H. Fan, Z. Wang, X. Liu and Z. Wu, Mater. Des., 2015, 87, 10–16 CrossRef CAS
. - S. Liu, X. Fan and C. He, Compos. Sci. Technol., 2016, 125, 132–140 CrossRef CAS
.
|
This journal is © The Royal Society of Chemistry 2016 |
Click here to see how this site uses Cookies. View our privacy policy here.