DOI:
10.1039/C6RA05857D
(Paper)
RSC Adv., 2016,
6, 42495-42501
Synthesis of TiO2-loaded silicate-1 monoliths and their application for degradation rhodamine B
Received
5th March 2016
, Accepted 20th April 2016
First published on 25th April 2016
Abstract
TiO2-loaded silicate-1 monoliths, with TiO2 (Degussa P25) nanoparticles loaded in silicate-1 crystal, were directly synthesized by combining sol–gel method and hydrothermal method. TiO2 nanoparticles were well dispersed in the system and had an intimate contact with silicate-1 zeolite. The physicochemical properties of all samples were characterized by XRD, FTIR, SEM, nitrogen sorption, microstructure, and UV-vis diffuse reflectance spectra. X-ray diffraction and SEM images showed that silicate-1 was synthesized and the surfaces of silicate-1 particles were coated with nanoparticles. UV-vis diffuse reflectance spectra, microstructure and TEM images exhibited that TiO2 nanoparticles were effectively loaded in silicate-1 crystal. BET analysis showed that all samples kept high surface area and micropore size distribution. They also allowed the quick adsorption of reaction molecules outside the surfaces and inside the micropores and showed a high efficient degradation when it is used in the oxidation of rhodamine B (RhB).
1. Introduction
Water, the world's most precious and important natural resource, is under threat from various pollutants, which are produced by many dyeing processes, such as sodium, chloride, sulphate and dye ingredients with high BOD and COD values.1 Some dyestuffs are so stable that they are not biodegradable.2 In order to overcome this weakness, various efficient solid catalysts have been widely investigated, such as ZnO,2 SnO2,3 TiO2,4 and so on. Among these, TiO2 as a promising catalyst has been widely researched and demonstrated for the complete oxidation of organic pollutants by completely converting them to CO2, H2O and harmless mineral salts.5,6 The process of oxidative degradation is the process of generating the hydroxyl radicals and valence band holes, which are generated under UV light and have a strong oxidation potential for a wide range of organic compounds.7 However, the degradation activity of TiO2 is influenced by various factors, such as band gap and electron–hole pair recombination. Both these factors are influenced by the particle size of the TiO2. For example, the recombination rate of the electron–hole pair is higher in bulk or large size semiconductor photocatalyst particles. In order to figure out these problems, many researchers have made efforts to prepare nanosized TiO2. However, when used the nanosized TiO2 materials to degrade pollutants, many difficulties have been met, such as agglomeration, separation and recovery of fine catalyst particles.8 As a result, great efforts have been made to improve the photo-efficiency of TiO2 by dispersing it on solid support materials like glass,9 optical fiber,10 silica,11 electrode,12 clays,13 stainless steel mesh,14 and zeolites.15 Among these, zeolites, as an important series of porous materials, have high specific surface area and physicochemistry stability. Moreover, they also exhibit several other specific features that make them suitable for their use as hosts for photocatalysts,16,17 such as the following: (i) transparency to UV-visible radiation above 240 nm; (ii) owning high adsorption for organic compounds from solution; (iii) the ability of the zeolite framework to participate actively in electron-transfer processes. Until now, many zeolites have been used as support, such as MCM-41 zeolite,18 5A zeolite,19 and silicate-1 zeolite.20 They are interesting hosts to disperse TiO2 on their surfaces. And the photocatalytic activity of TiO2 can be highly improved by synergistic effects.21–23 However, the conventional preparation techniques usually suffer from their inherent disadvantages. For example, TiO2 nanoparticles can deposit in pores of zeolite in most preparation processes. It often causes the greatly decrease of the surface area of porous material, which weakens the enhancement of the photocatalytic activity by means of the increase of composite surface area. What is more, there are a few reports that use silicate-1 as supporter to synthesize the TiO2-loaded silicate-1 monoliths. Therefore, the development of an immobilization technique to synthesize TiO2-loaded silicate-1 monolith which maintains a high surface area and the excellent physicochemical properties of TiO2 for photocatalysis are thus required.
The photocatalytic activity of catalyst can be tested by many ways, such as degradation of methylbenzene,24 methylene blue,25 and Rhodamine B (RhB).26 Among these, RhB, as the basic red dye of the xanthenes class, is widely used as a colorant in textiles and food stuffs. It is highly soluble in water and organic solvents, and its colour is fluorescent bluish red. Due to RhB is potentially toxic and carcinogenic, it is banned from use in foods now. So the photodegradation of RhB is important with regard to the purification of dye effluents.27
In this paper, we explored a new strategy to load TiO2 nanoparticles in the MFI-type structure of silicate-1 by combining the sol–gel method and hydrothermal synthesis method. The precursor solution was prepared by dispersing TiO2 nanoparticles in an about-to-gel solution containing silica sol, tetrapropyl ammonium bromide and sodium hydroxide. The precursor solution gelled quickly through hydrothermal treatment, in which TiO2 nanoparticles were immobilized into the three-dimensional (3D) network of silica. Then silicate-1 grains formed in the gelatin and grew up by transferring the silica gelatin into silicate-1 structure (Fig. 1). This method provides a new way to load large amounts of some materials in silicate-1 crystal. The particles size of these materials can be bigger than the pores of silicate-1. And the loading content can be easy to be controlled. Finally, the photocatalytic activity of catalyst was investigated by the photocatalytic degradation of RhB.
 |
| Fig. 1 Schematic diagram of the synthetic procedure of TiO2-loaded silicate-1 monolith (a) and the synthesized monolith (b). | |
2. Experimental
2.1 Catalyst preparation
Herein, we reported a one-step method to prepare a kind of silicate-1 monoliths loaded TiO2 nanoparticles on its surface and in its inside (denoted as TSM-1 (X); X was the mass ratio of TiO2/SiO2) by employing silica sol, a cheap and homogeneous solution, as Si source, TiO2 (Degussa P25) as Ti source, tetrapropyl ammonium bromide (TPABr) as template. The schematic diagram of the synthetic procedure of TiO2-loaded silicate-1 catalyst is given in Fig. 1. Different amount of TiO2 (1 g, 3 g, and 5 g, respectively) was dispersed in the silica sol (30 mL, pH = 9.5, 30 wt%) containing 0.2 g sodium hydroxide and 1.5 g tetrapropyl ammonium bromide (TPABr). The mixture was continuously stirred for 3 h and then transferred into Teflon-lined autoclave for hydrothermal reaction at 180 °C for 24 h. After that, the products were cooled down, dried at 60 °C for 24 h and sintered at 550 °C for 6 h.
2.2 Characterization
The synthesized samples were characterized by powder X-ray diffraction (XRD), N2 adsorption–desorption isotherms, UV-vis diffuse reflectance spectra, and scanning electron microscopy (SEM). XRD patterns were obtained on a Bruker-AxsD8 diffractometer equipped with graphite monochromatized Cu-Kα radiation in the angular range (2θ) from 5 to 60°, generated at 40 kV, 40 mA. N2 adsorption–desorption isotherms were measured at 77 K by TriStar 3020 (Micromeritics, USA) and the related data (surface area, SBET, pore volume, pore diameter) were calculated. The micropore size distribution of the samples was determined using the Horvath–Kawazoe (HK) analysis method. The optical properties can be determined by ultraviolet-visible (UV-vis) spectrometer (UV-101 PC scanning spectrophotometer). Scanning electron microscopy (SEM) was observed by Hitachi SU-70 microscope at acceleration voltage of 5 kV. The emission scanning electron microscopic images were observed by Hitachi SU-70 microscope at acceleration voltage of 5 kV. Transmission electron microscope (TEM) was tested by TecnaiF30 at a accelerating of 300 kV. The microstructures of the samples were observed with an optical microscope (MF600D-TFBD).
2.3 Photocatalytic degradation experiments
The photocatalytic activity of catalysts was evaluated by measuring the decrease in concentration of RhB in the reaction solution. The photocatalytic degradation setup consists of a Philips UV lamp, which emits UV-light with a main wavelength range of 250–270 nm and fixed in the top of square box with side length of 30 cm. The power of every lamp is 40 W. The catalysts were ground into powders and were maintained in suspension in the dye solution by continuously stirring. Prior to commencing illumination, the suspension containing 0.1 g of the catalyst and 100 mL of an aqueous solution of ca. 5 ppm of RhB was stirred continuously for 30 min in the dark in order to establish the adsorption–desorption equilibrium between RhB and the catalyst. Afterwards, the suspension was irradiated with UV-light for 90 min. To determine the change in RhB concentration in solution during the process, a few milliliters of the solution was withdrawn from the reactor, centrifuged to remove the catalyst before measuring. The fractional degradation efficiency (DR) of RhB was calculated by the following equation:
where C0 is the initial concentration of RhB and Ct is the concentration at definite interval of time, respectively.
3. Results and discussion
3.1 Characterization of the TiO2-loaded silicate-1 monolith
Fig. 2 shows the XRD patterns of silicate-1 monolith and TiO2-loaded silicate-1 monoliths with different TiO2/SiO2 mass ratio. All the TiO2-loaded silicate-1 monoliths show five distinct peaks at 7.98°, 8.82°, 23.18°, 24.02°, and 24.46° ascribable to (101), (020), (503), (151), and (303) reflection, respectively,28,29 which are characteristic of MFI-type structure, similar to silicate-1 monolith without adding TiO2. With the increase of TiO2 content, the peak intensity at 25.23°, 37.82°, 48.05° and 53.91°, which correspond to (101), (112), (200) and (105) reflections of anatase TiO2, is enhanced. However, the peak intensity corresponding to silicate-1 declines, indicating that the addition of TiO2 results in the reduction of silicate-1 crystallinity. In a rough calculation from the variation of peak intensity in the XRD patterns, assuming crystallinity of 100% for the silicate-1 monolith without TiO2, the relative crystallinity of the TiO2-loaded silicate-1 monoliths series are 85%, 66% and 52% with a TiO2/SiO2 mass ratio of 1
:
10, 3
:
10 and 5
:
10, respectively. These changes are to be expected due to the lower amounts of silicalite-1 in the composition of the materials.
 |
| Fig. 2 XRD patterns of (a) TSM-1(0), (b) TSM-1(1), (c) TSM-1(3), (d) TSM-1(5). | |
The FT-IR spectra of silicate-1 monolith and TiO2-loaded silicate-1 monolith with different TiO2 content are shown in Fig. 3. For all these samples, the FT-IR is characterized by a broadband between 3600 and 3300 cm−1, which can be attributed to the stretching vibrations of O–H bonds of surface adsorbed water molecules.30 Fig. 3a is the FT-IR spectra of silicate-1 monolith without loading TiO2, which shows vibration bands at around 475, 546, 795, 950, and 1119 cm−1. The bands at 1119 cm−1 and 795 cm−1 are due to the internal asymmetric stretching vibration and external symmetric stretching of Si–O–Si bonds of zeolite, respectively.31 Furthermore, the band at 950 cm−1 is attributed to the stretching vibration of the Si–OH group.32 The absorption peak at around 546 cm−1 is ascribed to the five membered ring of pentasil zeolite structure.33,34 Finally, the band at 475 cm−1 is due to the bending vibration of SiO4. Fig. 4b–d are the FT-IR spectra of TiO2-loaded silicate-1 monolith series with the TiO2/SiO2 mass ration of 1
:
10, 3
:
10, 5
:
10, respectively. All of the TiO2-loaded monolith series, exhibiting the vibration band at 475, 546, 795, 950, and 1119 cm−1 of MFI-structured zeolite, show similarly FT-IR spectra to the silicate-1 monolith without adding TiO2 (Fig. 3a). In Fig. 3b, the absorption peak corresponding to Ti–O–Ti bond, a wide band from 504 to 657 cm−1, is not obvious. It may be the reason that the TiO2 content is low. With the increase of TiO2, the characteristic peaks of silicate-1 always exist, and the absorption intensity of wide vibration band from 504 to 657 cm−1 of TiO2-loaded silicate-1 monolith becomes more and more evidence, which is in consistent with the results of XRD characterization.
 |
| Fig. 3 FT-IR spectra of (a) TSM-1(0), (b) TSM-1(1), (c) TSM-1(3), (d) TSM-1(5). | |
 |
| Fig. 4 Nitrogen sorption isotherms and pore size distribution of (a) TSM-1(0), (b) TSM-1(1), (c) TSM-1(3), (d) TSM-1(5). | |
The effect of TiO2 content on the surface area and pore structure parameters was studied by measuring silicate-1 monolith and TiO2-loaded silicate-1 monoliths with various amounts of TiO2 using N2 adsorption–desorption isotherms and pore size distribution. The BET surface area and micropore surface of all samples were measured from the BET method and t-plot method. The micropore volume and micropore size distribution were calculated using the Horvath–Kawazoe (HK) analysis method. The textural properties of the obtained samples are listed in Table 1. As measured by the BET method and t-plot method, the BET surface area and micropore surface area of TSM-1(0) are 302.8 m2 g−1 and 177.8 m2 g−1, respectively. The micropore volume and pore size distribution are 0.1254 cm3 g−1 and 0.52 nm, as calculated by the HK method. With the increase of TiO2 content, the BET surface areas and the external surface areas of the TiO2-loaded silicate-1 monolith decrease. Maybe the decreases in the surface area with respect to the pure silicalite-1 are due to the difference between the specific surface area of silicalite-1 (303 m2 g−1) and that of the P25 (65 m2 g−1). However, it can be noted that with the increase of TiO2 loading, all samples almost show a micropore diameter of 0.52 nm. It indicates that TiO2 nanoparticles do not disperse in the pore of the silicate-1 zeolite. TiO2 nanoparticles are mainly loaded on the outside surface and in the inter structure of silicate-1.
Table 1 Textural properties of the TiO2-loaded silicate-1 monoliths
Sample |
SBET (m2 g−1) |
Sest (m2 g−1) |
Vtotal (mL g−1) |
DHK (nm) |
TSM-1(0) |
303 |
177.8 |
0.09 |
0.52 |
TSM-1(1) |
276 |
167.0 |
0.08 |
0.52 |
TSM-1(3) |
254 |
166.4 |
0.08 |
0.52 |
TSM-1(5) |
226 |
145.7 |
0.07 |
0.51 |
The N2 sorption isotherms and pore size distribution of TiO2-loaded silicate-1 monolith synthesized with various amounts of TiO2 are shown in Fig. 4. It can clearly be observed that the N2 adsorption–desorption isotherms of silicate-1 monolith exhibits a type I isotherm pattern and shows a significant high uptake in P/P0 < 0.1 region, which is characteristic of well-defined microporous materials.35 The loading of TiO2 nanoparticles into the silicate-1 monolith does not change the shape of the N2 adsorption–desorption isotherms. But the value of the significant high uptake in P/P0 < 0.1 region decreases with the increase of TiO2 content. It may be caused by the decrease of the crystallinity (Fig. 2). However, it can be clearly noted that with the increase of the TiO2 loading, all samples almost keep the same micropore size distribution and have a very narrow micropore size distribution with a mean pore diameter of 0.5–0.55 nm, which is comparable to the pore diameter of the crystallographic five membered ring of silicate-1.
Fig. 5 shows the scanning electron microscopy (SEM) analysis of silicate-1 monolith powders and TiO2-loaded silicate-1 monoliths. Fig. 5a and b are the pictures of silicate-1 monolith particles, we can see that the sample shows uniform small particles with the size of 20–50 nm. Also, there are some nanoparticles attaching on its crystal surface (Fig. 5d). From Fig. 2b, we can know that except silicate-1, there are no other phases. So the nanoparticles, attaching on the crystal face, may be the amorphous silica. Fig. 5c–f are the images of TiO2-loaded silicate-1 monolith's powders with different TiO2/SiO2 mass ratio, all the samples also show uniform particles sizes about 20–50 μm, with twinned hexagonal crystal shape, which are similar to the one without adding TiO2.
 |
| Fig. 5 SEM images of (a and b) TSM-1(0), (c) TSM-1(1), (d) TSM-1(3), (e and f) TSM-1(5). | |
Further, with the increase of TiO2 content, the morphology of the silicate-1 monolith powders changes to be more nanoparticles attaching on its crystal face, which is in consistent with the results of XRD characterization, with a low crystallinity (52%).
The microstructures of TSM-1(0) and TSM-1 (5) are observed with an optical microscope and shown in Fig. 6. From Fig. 6a, it can be seen that there are no void spaces and particles within silicate-1 crystal. Some amorphous SiO2 adheres on the surface of silicate-1 crystal. Silicate-1 crystal and amorphous SiO2 are all transparent. Fig. 6b is the microstructure of TSM-1(5). TiO2 nanoparticles are well dispersed in silicate-1 crystal and amorphous SiO2.
 |
| Fig. 6 Microstructures of (a) TSM-1(0), (b) TSM-1(5). | |
When the precursor solution with the sol composition of 30 mL silica sol
:
0.2 g NaOH
:
1.5 g TPABr
:
5 g TiO2 was crystallized at 180 °C for 3 h, it converted into monolith. Fig. 7 shows XRD patterns of TiO2 and TSM-1(1) crystallized at 180 °C for 3 h. From Fig. 7b, it can be found that the sample shows the characteristic peaks of TiO2 at about 25.23°, 37.82°, 48.05° and 53.91°, which are ascribable to (101), (112), (200), and (105) reflection, respectively. A wide range diffraction at about 20–25° belongs to the amorphous SiO2. There are no characteristic peaks of silicate-1. It indicates that silicate-1 is not formed.
 |
| Fig. 7 XRD patterns of TiO2 (a) and sample crystallized for 3 h (b). | |
Fig. 8 shows TEM images of TSM-1(5) crystallized at 180 °C for 3 h. From Fig. 8a, it can be seen that TiO2 nanoparticles with a particle size range of 20–50 nm are uniformly distributed in the system. But there are also appearing trace amounts of aggregation. The high magnification TEM image shows that TiO2 nanoparticles are coated and bonded together with a layer of amorphous SiO2 (Fig. 8b), which is in agreement with Fig. 6b. With an increase of crystallization time (24 h), silicate-1 particles are formed (Fig. 5e). In the process of crystallization, TiO2 nanoparticles are surrounded by SiO2 gelatin. It indicates that the formation of silicate-1 is the process of continuous transformation amorphous SiO2 into silicate-1. And TiO2 nanoparticles are encapsulated in silicate-1 particles and/or on silicate-1 surface.
 |
| Fig. 8 TEM images of sample crystallized for 3 h. | |
Fig. 9 shows the UV-vis diffuse reflectance spectra of silicate-1 monolith and the TiO2-loaded silicate-1 monoliths with different TiO2/SiO2 mass ratio. Silicate-1 monolith just shows a gentle absorption band at about 250–280 nm (Fig. 9a). The others show a broad absorption band at about 325–400 nm. It indicates the existence of TiO2 on the final catalyst.36 Fig. 9b–d are the UV-vis diffuse reflectance spectra of TSM-1(1), TSM-1(3), TSM-1(5). The intensity of the band corresponding to TiO2 becomes more and more higher with the increase of TiO2 content loading on the final sample, and the absorption band also appears minor variations. According to Fig. 9b, the band gap of TSM-1(1) is 3.05 eV,37 which is bigger than TiO2 (Degussa P25, 3.03 eV). It indicates that the size of TiO2 particles in TSM-1(1) is smaller than TiO2 (Degussa P25). It may be the reason that during the process of hydrothermal reaction, part of TiO2 is dissolved in the alkaline solution. With the increase of TiO2 content, the band gaps of TSM-1(3) and TSM-1(5) are 3.02 eV and 3.01 eV, respectively. The band gaps of both samples are smaller than TiO2 (Degussa P25). It indicates that the TiO2 particles appear trace amounts of aggregation with the increase of the TiO2 content (Fig. 8).38,39
 |
| Fig. 9 UV-vis spectra of (a) TSM-1(0), (b) TSM-1(1), (c) TSM-1(3), (d) TSM-1(5). | |
3.2 Photocatalytic activities of the TiO2-loaded silicate-1 monolith
As we know, the photocatalytic reaction occurs when TiO2 is irradiated under the light which has higher energy than the TiO2 band gap. The schematic diagram for the adsorption and photocatalytic degradation of RhB molecules on catalyst is shown in Fig. 10. Under UV light irradiation, TiO2 can generate the hydroxyl radicals and valence band holes, which have a strong oxidation potential for a wide range of organic compounds. However, when the TiO2 is immobilized on silicate-1, the substrate adsorption onto the TSM-1 should also be considered. The elementary reaction equations are expressed as follows: |
RhB + TSM ↔ (RhB + TSM)adsorption
| (1) |
|
O2− + (TSM + TiO2)adsorption → Pi
| (5) |
|
˙OH + (TSM + TiO2)adsorption → Pi
| (6) |
where RhB is rhodamine B molecule, TSM is the TSM-1 series catalysts, (RhB + TSM)adsorption is the rhodamine B molecule adsorbed on the surface of TSM-1 series catalysts. Pi is the degradation product. The photocatalytic reaction experiment is initiated after the adsorption/desorption equilibrium is established. This equilibrium is considered to be maintained under irradiation.40 The adsorption of the zeolites and photocatalysis of the deposited TiO2 have been combined, resulting in synergistic effects in improving the photocatalytic efficiency of titanium dioxide.
 |
| Fig. 10 The schematic diagram for the adsorption and photocatalytic degradation of RhB molecules on catalyst. | |
Before turning on the lamp to irradiate the catalyst, a dark adsorption step has been launched for 30 min to make sure organic molecules reaching adsorption–desorption equilibrium between catalyst and the dye. Fig. 11 shows the photocatalytic degradation of all samples and five photocatalytic degradation cycles of TSM-1(5) under UV light. From Fig. 11a, it can be noted that after equilibrium adsorption, the concentration of RhB in the high TiO2 content catalyst is higher than the low TiO2 content catalyst, which coincides with the surface area of all samples. At time 0 min, the lamp was turned on and irradiated for 1 h. From the photocatalytic decomposition curves of TSM-1(0) catalyst, it can be clearly observed that the degradation of RhB was very low after 1 h irradiation (only ca. 5.6% decomposition). TSM-1(1) displayed a removal ratio of RhB with ca. 63.8% in 1 h irradiation. Whereas within the same time interval, it is found that, as the TiO2 dosage loaded on silicate-1 monolith increases from 1 to 3 g, the degradation efficiency of RhB also increases from 63.8% to 94.8%. It can be owed to an increment of TiO2 loaded on catalyst which can generate radicals under UV irradiation and then oxidate RhB molecules. Continual increase TiO2 dosage loaded on the catalyst (from 3 g to 5 g) results in an increase for degradation efficiency (from 94.8% to 98.3%). In order to investigate the stability of photocatalytic performance, TSM-1(5) was used to degrade RhB solution in five repeated cycles (Fig. 11b). It is noteworthy that the photocatalytic performance of TSM-1(5) exhibits well photostability under UV light, where the photocatalytic efficiency reduces only by 2.7% after five cycles.
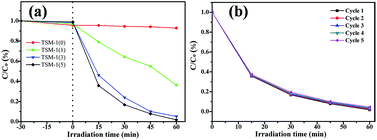 |
| Fig. 11 Photocatalytic degradation (a), and five photocatalytic degradation cycles (b) of RhB solution under UV light with a catalyst content of 1 g L−1, C0 = 5 mg L−1. | |
4. Conclusions
TiO2-loaded silicate-1 monoliths, with TiO2 (Degussa P25) nanoparticles loaded on the structure and surface of silicate-1, have been successfully synthesized using silica sol as Si source, P25 as Ti source and tetrapropyl ammonium bromide as template by combining sol–gel method and hydrothermal synthesis method. TiO2 content has great influence on the physicochemical properties and catalytic activity of TiO2-physicochemical properties and catalytic activity of TiO2-loaded silicate-1 monolith. With the increase of TiO2 content, the crystallinity and specific surface area of the sample decrease. But all of the samples have a very high specific surface area and external surface area. TiO2 nanoparticles are well loaded on the surface and in the internal of silicate-1 particles. With the increase of TiO2 content loading in silicate-1 monolith (1 g to 5 g), the band gaps of TiO2-loaded silicate-1 monolith just appear minor variations (from 3.045 to 3.008 eV). When the catalyst contains 5 g of TiO2, its degradation efficiency can be 98.3%. And it exhibits well photostability after five cycles (95.6%).
Acknowledgements
We are very grateful for the technical guidance from Li Wen professor.
References
- A. K. Kondru, P. Kumar and S. Chand, J. Hazard. Mater., 2009, 166, 342–347 CrossRef CAS PubMed.
- P. X. Hou, B. Yu, Y. Su, C. Shi, L. L. Zhang, C. Liu, S. S. Li, J. H. Du and H. M. Cheng, J. Mater. Chem. A, 2014, 2, 1159–1164 CAS.
- J. H. Jou, H. H. Yu, Y. X. Lin, J. R. Tseng, S. H. Peng, Y. C. Jou, C. H. Lin, S. M. Shen, C. Y. Hsieh, M. K. Wei, D. H. Lin, C. C. Wang, C. C. Chen, F. C. Tung, S. H. Chen and Y. S. Wang, J. Mater. Chem. C, 2013, 1, 5110–5115 RSC.
- S. G. Kumar and L. G. Devi, J. Phys. Chem. A, 2011, 115, 13211–13241 CrossRef CAS PubMed.
- V. Augugliaro, M. Litter, L. Palmisano and J. Soria, J. Photochem. Photobiol., C, 2006, 7, 127–144 CrossRef CAS.
- S. Bangkedphol, H. E. Keenan, C. M. Davidson, A. Sakultantimetha, W. Sirisaksoontorn and A. Songsasen, J. Hazard. Mater., 2010, 184, 533–537 CrossRef CAS PubMed.
- W. Choi, Catal. Surv. Asia, 2006, 10, 16–28 CrossRef CAS.
- L. Andronic, D. Perniu and A. Duta, J. Sol-Gel Sci. Technol., 2013, 66, 472–480 CrossRef CAS.
- Y. Hu and C. W. Yuan, J. Cryst. Growth, 2005, 274, 563–568 CrossRef CAS.
- R. D. Sun, A. Nakajima, I. Watanabe, T. Watanabe and K. Hashimoto, J. Photochem. Photobiol., A, 2000, 136, 111–116 CrossRef CAS.
- W. Choi, J. Y. Ko, H. Park and J. S. Chung, Appl. Catal., B, 2001, 31, 209–220 CrossRef CAS.
- A. A. Belhekar, S. V. Awate and R. Anand, Catal. Commun., 2002, 3, 453–458 CrossRef CAS.
- F. Li, Y. Jiang, M. Xia, M. Sun, B. Xue and X. Ren, J. Hazard. Mater., 2009, 165, 1219–1223 CrossRef CAS PubMed.
- H. Yoshida, T. Kawase, Y. Miyashita, C. Murata, C. Ooka and T. Hattori, Chem. Lett., 1999, 715–716, DOI:10.1246/cl.1999.715.
- J. Chen, L. Eberlein and C. H. Langford, J. Photochem. Photobiol., A, 2002, 148, 183–189 CrossRef CAS.
- M. Matsuoka and M. Anpo, J. Photochem. Photobiol., C, 2003, 3, 225–252 CrossRef CAS.
- S. Hashimoto, J. Photochem. Photobiol., C, 2003, 4, 19–49 CrossRef CAS.
- Y. Dong, X. Fei, H. Zhang and L. Yu, J. Adv. Oxid. Technol., 2015, 18, 322–330 CAS.
- C. Zhao, Y. Zhou, D. J. de Ridder, J. Zhai, Y. Wei and H. Deng, Chem. Eng. J., 2014, 248, 280–289 CrossRef CAS.
- W. J. Li and M. O. Coppen, Chem. Mater., 2005, 17, 4560 CrossRef CAS.
- Y. Liu, S. Yang, J. Hong and C. Sun, J. Hazard. Mater., 2007, 142, 208–215 CrossRef CAS PubMed.
- H. Ichiura, T. Kitaoka and H. Tanaka, Chemosphere, 2003, 50, 79–83 CrossRef CAS PubMed.
- V. Belessi, D. Lambropoulou, I. Konstantinou, A. Katsoulidis, P. Pomonis, D. Petridis and T. Albanis, Appl. Catal., B, 2007, 73, 292–299 CrossRef CAS.
- X. F. Qian, T. Kamegawa, K. Mori, H. X. Li and H. Yamashita, J. Phys. Chem. C, 2013, 117, 19544–19551 CAS.
- R. J. Tayade, R. G. Kulkarni and R. V. Jasra, Ind. Eng. Chem. Res., 2007, 46, 369–376 CrossRef CAS.
- C. Li, J. Wang, S. Feng, Z. Yang and S. Ding, J. Mater. Chem. A, 2013, 1, 8045–8054 CAS.
- N. Barka, S. Qourzal, A. Assabbane, A. Nounah and Y. Ait-Ichou, J. Photochem. Photobiol., A, 2008, 195, 346–351 CrossRef CAS.
- A. E. Persson, B. J. Schoeman, J. Sterte and J. E. Otterstedt, Zeolites, 1995, 15, 611–619 CrossRef CAS.
- Y. F. Yeong, A. Z. Abdullah, A. L. Ahmad and S. Bhatia, J. Membr. Sci., 2009, 341, 96–108 CrossRef CAS.
- P. Castaldi, M. Silvetti, S. Enzo and P. Melis, J. Hazard. Mater., 2010, 175, 172–178 CrossRef CAS PubMed.
- J. R. Sohn, S. J. DeCanio, J. H. Lunsford and D. J. O'Donnell, Zeolites, 1986, 6, 225–227 CrossRef CAS.
- T. Blasco, A. Corma, M. T. Navarro and J. P. Pariente, J. Catal., 1995, 156, 65–74 CrossRef CAS.
- C. E. A. Kirschhock, R. Ravishankar, F. Verspeurt, P. J. Grobet, P. A. Jacobs and J. A. Martens, J. Phys. Chem. B, 1999, 103, 4965–4971 CrossRef CAS.
- M. Mehdipourghazi, A. Moheb and H. Kazemian, Microporous Mesoporous Mater., 2010, 136, 18–24 CrossRef CAS.
- N. Tsunoji, S. Yuki, Y. Oumi, M. Sekikawa, Y. Sasaki, M. Sadakane and T. Sano, ACS Appl. Mater. Interfaces, 2015, 7, 24360–24369 CAS.
- A. M. Busuioc, V. Meynen, E. Beyers, M. Mertens, P. Cool, N. Bilba and E. F. Vansant, Appl. Catal., A, 2006, 312, 153–164 CrossRef CAS.
- W. Zhang, Y. Li, C. Wang and P. Wang, Desalination, 2011, 266, 40–45 CrossRef CAS.
- L. Korosi and I. Dekany, Colloids Surf., A, 2006, 280, 146–154 CrossRef.
- M. P. Moret, R. Zallen, D. P. Vijay and S. B. Desu, Thin Solid Films, 2000, 366, 8–10 CrossRef CAS.
- Q. Wang, C. Chen, D. Zhao, W. Ma and J. Zhao, Langmuir, 2008, 24, 7338–7345 CrossRef CAS PubMed.
|
This journal is © The Royal Society of Chemistry 2016 |
Click here to see how this site uses Cookies. View our privacy policy here.