DOI:
10.1039/C6RA05680F
(Paper)
RSC Adv., 2016,
6, 51221-51228
Aqueous phase hydrogenation of furfural to tetrahydrofurfuryl alcohol on alkaline earth metal modified Ni/Al2O3†
Received
3rd March 2016
, Accepted 15th May 2016
First published on 20th May 2016
Abstract
Al2O3 modified by alkaline earth metals M–Al2O3 (M = Mg, Ca, Sr, Ba) was synthesised by coprecipitation method. The nickel-based catalysts supported by M–Al2O3 were prepared by impregnation method. The catalysts were characterized by TEM, N2 adsorption/desorption, XRD, H2-TPR, NH3-TPD and XPS, and used for the direct hydrogenation of furfural to tetrahydrofurfuryl alcohol (THFA) in water. The reaction was demonstrated to proceed through furfuryl alcohol as an intermediate. The modification of Al2O3 by alkaline earth metals has a significant effect on the activity and selectivity of THFA. A high yield of THFA was obtained over Ni/Ba–Al2O3 under optimized conditions. Moreover, the catalyst is recyclable and reusable at least four times without significant loss of the conversion of furfural and selectivity of THFA.
Introduction
The production of chemicals and fuels from renewable biomass is of significance for the sustainable development of chemical industry in the future.1–4 One of the most important strategies for biomass conversion is the high-valued utilization of platform molecules. Furfural, produced in millions of tons every year by the hydrolysis and dehydration of xylan contained in lignocellulose, is widely viewed as a versatile platform molecule.5–11
Tetrahydrofurfuryl alcohol (THFA), a transparent, high-boiling liquid with a mild odor and completely miscible with water,9 is one of the typical products12–20 from furfural. It can be used as a green solvent as well as for the production of dihydropyran,21 pyridine,22 and tetrahydrofuran. Moreover, recent research has revealed that THFA can be converted to 1,5-pentanediol, an important monomer in the plastics industry, in very high yield.23–26
The traditional method for production of THFA from furfural is a two-step procedure via furfuryl alcohol as the intermediate product.27–29 The high energy consumption of the two-steps strategy made the direct conversion of furfural to THFA in one step be attempted both in gas and liquid phase.30–37 Resasco et al. investigated the gas phase hydrogenation of furfural over Cu, Pd and Ni supported on SiO2 catalysts in the temperature range of 210–290 °C. The maximum yield of THFA was not more than 5% in their system.31,32 Tomishige et al. achieved a THFA yield of 94% in the gas phase catalyzed by Ni/SiO2.34 The same group also reported the hydrogenation of furfural in the aqueous phase using Ni–Pd/SiO2 or Pd–Ir/SiO2 as catalysts.30,33 The maximum yield of THFA reached 96%. Recently, a 95% yield of THFA from furfural was reported by Rode's group over Pd/MFI catalyst in isopropyl alcohol.35
The reported satisfactory results for THFA directly from furfural were usually obtained over noble metal catalysts in the liquid phase. And organic solvent was also necessary for some of the well-behaved systems. It is more interesting and attractive to achieve a good yield for THFA from furfural utilizing non-noble metal such as nickel as catalyst in water under mild conditions.
On the basis of our work on the hydrogenation of 5-hydroxymethylfurfural (HMF) and furfural,16,38 herein, the hydrogenation of furfural to THFA was reported over alkaline earth metals (Mg, Ca, Sr, Ba) modified Ni/Al2O3 in water. Very recently, Li et al. reported that the alkaline earth metals modified Pd/Al2O3 had improved decarbonylation performance for HMF.39 In this paper the modification of Al2O3 by alkaline earth metals played a significant role on improvement of both the furfural conversion and the selectivity of THFA. Furfural can be almost stoichiometric converted to THFA in water under optimal conditions. Moreover, there was no obvious change in conversion of furfural and selectivity of THFA during the recyclable experiments.
Experimental
Materials
Furfural and furfuryl alcohol were of analytic grade and distilled under reduced pressure before used. Deionized water in all experiments was purified by a Milli-Q system (Millipore). Aluminium nitrate (Al(NO3)3·9H2O), magnesium nitrate (Mg(NO3)2·6H2O), calcium nitrate (Ca(NO3)2·4H2O), strontium nitrate (Sr(NO3)2), barium nitrate (Ba(NO3)2) and THFA were of analytic grade and purchased from Aladdin Chemistry Co. Ltd. Nickel nitrate (Ni(NO3)2·6H2O) of analytic grade was obtained from Tianjin Kermel Chemical Reagent Development Centre. All other reagents were commercially available and used as received.
Preparation of catalysts
Al2O3. The Al2O3 was prepared by the precipitation method. In a typical procedure, Al(NO3)3·9H2O was dissolved in deionized water. Then ammonium carbonate aqueous solution was added to the above solution drop by drop under vigorous agitation. After vigorous stirring for 30 min at room temperature, the mixture was kept stand for 24 h at the same temperature. The resulting precipitate was washed by deionized water for 3 times and then dried overnight at 120 °C. The solid was grinded and sieved and then calcinated at 600 °C under air to afford the Al2O3 support.
M–Al2O3. The M–Al2O3 (M = Mg, Ca, Sr, Ba) was prepared using a method similar to the preparation of Al2O3. Firstly, the Al(NO3)3·9H2O and alkaline earth metals nitrates was dissolved in deionized water. Then the subsequent process was the same as the preparation process for Al2O3.
Ni/Al2O3. The Ni/Al2O3 was prepared by the impregnation method. A typical procedure was described as follows. 2.00 g of Ni(NO3)·6H2O was dissolved in 6.40 g deionized water and then 4.00 g of Al2O3 was added to the solution. The mixture was stirred and kept stand overnight. After dried at 120 °C for 12 h, the sample was calcinated at 500 °C for 4 h under air atmosphere. Before used the catalyst was reduced under H2 atmosphere for 2 h.
Ni/M–Al2O3. The Ni/M–Al2O3 (M = Mg, Ca, Sr, Ba) was prepared using a method the same as the preparation of Ni/Al2O3. The Al2O3 was replaced by M–Al2O3 (M = Mg, Ca, Sr, Ba).
Characterization of catalysts
N2 physical adsorption/desorption measurement was carried out at liquid nitrogen temperature using Autosorb-1 Quantachrome instrument. Water and other physically adsorbed species were removed by pre-degassing the sample at 300 °C for about 10 h. The BET surface area (SBET) was calculated using the Brunauer–Emmett–Teller equation (relative pressure between 0.05 and 0.25). The desorption branches of the nitrogen isotherms were used to calculate the pore size distribution employing the Barrett–Joyner–Halenda (BJH) model.
Temperature programmed reduction (TPR) profiles were obtained on a Micromeritics AutoChem II 2920 Instrument with a thermal conductivity detector (TCD). Typically, 50 mg sample of the calcinated catalyst was degassed at 200 °C under atmosphere of Ar for 2 h. After the sample was cooled to a temperature of 50 °C under Ar flow, the in-line gas was switched to 10% H2/Ar, and the sample was heated to 800 °C at a rate of 10 °C min−1. The H2 consumption was monitored by a TCD detector.
The X-ray powder diffraction (XRD) patterns were obtained using Rigaku D/Max 2500/PC powder diffractometer with Cu Kα radiation (λ = 0.15418 nm) at 40 kV and 200 mA in a scanning rate of 5° min−1.
The microstructure of the materials was examined by transmission electron microscopy (TEM) on a JEOLJEM-2000EX electron microscopy. The distribution of particle size was obtained by measuring about 200 particles in different TEM images.
The X-ray photoelectron spectroscopy (XPS) measurements were done in a Thermo ESCALAB 250Xi by using Mg Kα (1253.6 eV) radiation source and a chamber pressure lower than 5 × 10−10 mbar. The binding energy (BE) was adjusted by the binding energy of C1s.
Temperature-programmed desorption of ammonia (NH3-TPD) was performed on a Micromeritics AutoChem II 2920 Instrument with a thermal conductivity detector (TCD) and MS detector to monitor the desorbed NH3. After degassed, the sample was saturated with NH3 at 373 K by a flow of He. After the physical adsorbed NH3 was removed, the temperature was increased from 373 to 1073 K in an atmosphere of He.
Inductively coupled plasma atomic emission spectroscopy (ICP-AES) was conducted on CPS-8100, SHIMADZU.
Typical procedure for catalytic hydrogenation of furfural
Catalytic hydrogenation of furfural was performed in a 60 mL stainless steel autoclave equipped with a magnetic stirrer, a pressure gauge and automatic temperature control apparatus. The reactor was connected to a hydrogen cylinder of the reaction pressure. In a typical experiment, 10.0 g aqueous solution of furfural (0.5 g, 5.2 mmol) and catalyst (0.2 g) were loaded into the reactor. Then the reactor was sealed and purged with H2 for 4 times to exclude air. H2 was charged into the reactor, when the autoclave was heated to the desired temperature. After reaction, the autoclave was cooled. The liquid reaction mixture was centrifuged, diluted and analyzed by gas chromatography (GC) after adding the internal standard.
Products analysis
Gas chromatography measurements were conducted on Agilent 7890A GC with autosampler and a flame ionization detector. HP-5 capillary column (30 m × 530 μm × 1.5 μm) was used for separation of reaction mixtures. The temperature of the column was initially kept at 80 °C for 3 min, and then was increased at a rate of 20 °C min−1 to 220 °C. 1,2,4,5-Tetramethylbenzene (TMB) were used as the internal standard. The products were identified by Agilent 6890N GC/5973MS as well as by comparison with the retention times of the respective standards in GC traces.
The quantification of products were determined based on GC data using internal standard method. The conversion of furfural (mol%) and selectivity (mol%) of main products were calculated as below.
Results and discussion
Catalyst characterization
The porous properties of as-synthesized Al2O3-based supports were examined by N2 adsorption/desorption analysis. As shown in Fig. S1† and Table 1, the five samples showed characteristics of typical type IV physisorption isotherms according to IUPAC classifications, indicating the mesoporous structure. The significantly increase of adsorbed volume at relatively high pressure was the characteristic of the H3 type hysteresis loop indicated the existence of slit-shaped pores with a large pore size. The pore size distribution calculated from the Barrett–Joyner–Halenda (BJH) model showed that mesopore and macropore were both present in the as-synthesized Al2O3-based supports. The Al2O3, Mg–Al2O3 and Ca–Al2O3 also exhibited a narrow mesopore diameter centered at around 5 nm (Fig. S1a–c†). The BET surface area of Al2O3, Mg–Al2O3, Ca–Al2O3, Sr–Al2O3 and Ba–Al2O3 were 424, 383, 336, 258 and 402 m2 g−1, respectively. The modification of Al2O3 caused the decline in BET surface area as well as pore volume.
Table 1 Porosity of the as-synthesized Al2O3-based supports
Entry |
Supports |
SBETa (m2 g−1) |
PVb (m3 g−1) |
Surface area calculated from adsorption isotherms using the BET equation. Total pore volume calculated from nitrogen adsorption at P/P0 = 0.99. |
1 |
Al2O3 |
424 |
2.32 |
2 |
Mg–Al2O3 |
383 |
1.01 |
3 |
Ca–Al2O3 |
336 |
1.03 |
4 |
Sr–Al2O3 |
258 |
0.72 |
5 |
Ba–Al2O3 |
402 |
1.76 |
Fig. 1 showed the XRD patterns of nickel-based catalysts. All the five samples showed diffraction peaks of zero-valent nickel. This proved that the nickel precursor was reduced to nickel metal during the preparation process of the catalysts. The as-synthesized Al2O3 were mainly identified as γ-Al2O3 crystal according to the diffraction patterns of supports. The XRD patterns of Ni/Ca–Al2O3 and Ni/Sr–Al2O3 also showed diffraction peaks attributed to CaO and SrO, respectively. While the Ni/Mg–Al2O3 and Ni/Ba–Al2O3 showed no corresponding alkaline earth metal oxide diffraction peaks. This would be the reason that the Al2O3 modified by Mg or Ba had larger BET surface areas than modified by Ca and Sr.
 |
| Fig. 1 XRD patterns of nickel-based catalysts. | |
Fig. 2 was the H2-TPR profiles of nickel-based catalyst. The TPR profile of Ni/Al2O3 showed a wide hydrogen evolution peak centering around 600 °C. A smaller hydrogen evolution peak appeared between 700 and 800 °C was also observed, showing the strong metal-support interaction between Ni and Al. A new hydrogen evolution peak arose at lower temperature between 300 and 400 °C when the Al2O3 modified by alkaline earth metals. This could be attributed that the existence of the alkaline earth metals partly changed the interaction between Ni and Al. In addition, the intensity of the new peak increased and the reduced temperature decreased in the order of Mg, Ca, Sr, and Ba.
 |
| Fig. 2 H2-TPR profiles of nickel-based catalysts. | |
The surface acidity of the catalysts was detected by the NH3-TPD (Fig. 3). All samples showed a broad desorption peak around 500 K. This could be attributed to weak acid sites. And the desorption peak around 780 K was due to medium and strong acid sites. The intensity of a specific peak represents the amount of ammonia desorbed from the sample. Thus the intensity can be used to quantify the acidity of a sample. It can be seen from Fig. 4 that the intensity of desorbed NH3 on modified Ni/Al2O3 were lower than that of on unmodified Ni/Al2O3 in all the temperature range except that the Ni/Mg–Al2O3 and Ni/Sr–Al2O3 desorbed more NH3 around 423 K. This showed that the medium and strong acid sites of the catalyst were masked by the addition of alkaline earth metal.
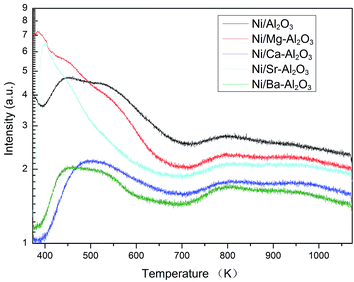 |
| Fig. 3 NH3-TPD profiles of nickel-based catalysts. | |
 |
| Fig. 4 TEM image of nickel-based catalysts Ni/Ba–Al2O3. | |
The morphology and the corresponding particle size distribution of nickel-based catalysts were presented in Fig. 4 and S2.† The particle size of nickel metal nanoparticles showed a range between 2 and 14 nm for all the catalysts. The Ni/Mg–Al2O3 also had a wider size range between 14 and 20 nm.
The chemical states of nickel-based catalysts were researched by XPS. The results were shown in Fig. 5. The binding energy at 852.9, 855.4 and 856.8 eV corresponded to Ni, NiO and NiAl2O4, respectively.40,41 It can be seen from Fig. 5 that, the binding energy of Ni decreased after the addition of alkaline earth metals (Table S1†), indicating that the interaction between Ni and Al was changed by the introduction of alkaline earth metals. This was agree with the results of H2-TPR. The relative area of Ni species in the XPS spectra was used to estimate the relative contents (Table S1†). The contents of Ni, NiO and NiAl2O4 was 9.0%, 29.0% and 62.0% for Ni/Al2O3. After the addition of alkaline earth metals, the relative contents of NiAl2O4 decreased and that of Ni and NiO increased correspondingly.
 |
| Fig. 5 XPS spectra of nickel-based catalysts. | |
Hydrogenation of furfural over nickel-based catalysts
The results of hydrogenation of furfural over nickel-based catalysts were summarized in Table 2. Only 16% selectivity of THFA was obtained when the hydrogenation of furfural catalyzed by Ni/Al2O3 in water at 140 °C (Table 2, entry 1). The by-products were mainly cyclopentanone (CPO) and cyclopentanol (CPL). However, after the modification of Al2O3 support by alkaline earth metals, the selectivity of THFA increased significantly. The selectivity of THFA increased from 16% to 74% when Ni/Mg–Al2O3 instead of Ni/Al2O3 was used as catalyst (Table 2, entry 2). Correspondingly, the selectivity of CPO and CPL decreased to 4% and 8%, respectively. More than 95% selectivities of THFA were achieved when the catalysts were modified by Ca, Sr or Ba and no CPO or CPL was detected under the same reaction conditions (Table 2, entries 3–5). Almost stoichiometric furfural was converted to THFA when Ni/Ba–Al2O3 was used. The modification of Al2O3 by alkaline earth metals did also improve the reaction activity significantly. The initial TOF was calculated based on the conversion of furfural at 5 minutes. A TOF of 24 h−1 was obtained when Ni/Al2O3 was used as catalyst. The TOF of Ni/Mg–Al2O3, Ni/Ca–Al2O3 and Ni/Sr–Al2O3 were 28, 38, 62 h−1, respectively. The TOF of Ni/Ba–Al2O3 was 68 h−1 which was almost three times as much as that of Ni/Al2O3.
Table 2 Hydrogenation of furfural over nickel-based catalystsa
Entry |
Catalysts |
TOFb (h−1) |
Conv. (%) |
Selectivity (%) |
THFA |
CPO |
CPL |
Othersc |
Reaction conditions: 10 g 5 wt% furfural aqueous solution, 0.2 g catalyst (10 wt% nickel), the content of alkaline earth metals in the support was 10 mol%, 140 °C, 4 MPa H2, 4 h, THFA: tetrahydrofurfuryl alcohol, CPO: cyclopentanone, CPL: cyclopentanol. The TOF was calculated based on the conversion at 5 min. The others are mainly 2-methyltetrahydrofuran and unidentified products. |
1 |
Ni/Al2O3 |
24 |
>99 |
16 |
20 |
26 |
38 |
2 |
Ni/Mg–Al2O3 |
28 |
>99 |
74 |
4 |
8 |
14 |
3 |
Ni/Ca–Al2O3 |
38 |
>99 |
95 |
— |
— |
5 |
4 |
Ni/Sr–Al2O3 |
62 |
>99 |
97 |
— |
— |
3 |
5 |
Ni/Ba–Al2O3 |
68 |
>99 |
99 |
— |
— |
1 |
Effect of Ba content
Ni/Ba–Al2O3 gave the best activity and selectivity among the four alkaline earth metals modified catalysts. Thus, the influence of the content of Ba in the supports was further studied. The results were presented in Table 3. The content of Ba was controlled by changing the quantity of barium nitrate during the preparation of support. It was found that the selectivity of THFA increased with the increase of Ba content in the support. Even 1 mol% content of Ba in the support had significant promoting effect on the distribution of the products. The selectivity of THFA increased from 16% to 75% when the Al2O3 was modified by 1 mol% content Ba (Table 2, entry 1 and Table 3, entry 1). 81% selectivity of THFA was obtained when the mole content of Ba was 2%. 96% or more selectivity of THFA was achieved when the content of Ba was equal to or more than 4%.
Table 3 Effect of Ba content in the support on the hydrogenation of furfural in watera
Entry |
Ba contentb (mol%) |
Conv. (%) |
Selectivity (%) |
THFA |
CPO |
CPL |
Others |
Reaction conditions: 10 g 5 wt% furfural aqueous solution, 0.2 g Ni/Ba–Al2O3 (10 wt% nickel), 140 °C, 4 MPa H2 4 h. The mole content of Ba in the support. |
1 |
1 |
>99 |
75 |
11 |
8 |
6 |
2 |
2 |
>99 |
81 |
6 |
7 |
6 |
3 |
4 |
>99 |
96 |
— |
<1 |
3 |
4 |
6 |
>99 |
97 |
— |
1 |
2 |
5 |
10 |
>99 |
99 |
— |
— |
1 |
Effect of reaction time
The time dependence of hydrogenation of furfural on Ni/Ba–Al2O3 was conducted to investigate the possible intermediates and reaction pathway. The results were shown in Fig. 6. For the first half an hour, 79% of furfural was converted with selectivity of 87% to furfuryl alcohol (FA) and 11% to THFA. The conversion of furfural and the selectivity of THFA increased along with reaction proceeding. The selectivity of FA decreased with the reaction time prolonging. While the total selectivities of THFA and FA were almost the same during the whole reaction, revealing that the THFA was obtained from further hydrogenation of furfuryl alcohol. No furfuryl alcohol was detected after reaction time of 4 h and the selectivity of THFA reached 96%. When the reaction time was extended to 5 h, the selectivity of THFA decreased slightly to 94%. The time profiles revealed that FA was the intermediate for the conversion of furfural to THFA. The hydrogenation of furfural to THFA mainly via a two-steps procedure. The first step was the hydrogenation of furfural to furfuryl alcohol and the second step was the hydrogenation of furfuryl alcohol to THFA.
 |
| Fig. 6 Time-course of furfural hydrogenation. Reaction conditions: 10 g 5 wt% furfural aqueous solution, 0.2 g Ni/Ba–Al2O3 (10 wt% nickel, 4 mol% Ba), 140 °C, 4 MPa H2. FA: furfuryl alcohol. | |
Effect of temperature
The effect of temperature on the hydrogenation of furfural in water was investigated and the results were shown in Table 4. The hydrogenation of furfural was conducted at the temperature range from 100 to 160 °C. The completed conversion of furfural was almost obtained at all the investigated temperature range after the reaction lasted for 4 h in water. The main products were FA and THFA. Only less than 10% of the by-products were detected, that was very amazing considering that the furfural and furfuryl alcohol is not stable in hot water. FA was detected only at lower temperature (100–130 °C). 81% selectivity of FA and 17% selectivity of THFA were obtained when the reaction was performed at 100 °C (Table 4, entry 1). The selectivity of THFA increased while that of FA decreased with the increase of the temperature. The 96% selectivity of THFA was gained when the reaction temperature was up to 140 °C (Table 4, entry 5). Higher temperature leads to a little decrease in the selectivity of THFA (Table 4, entries 6 and 7). This would be ascribed to the side reaction of furfural and FA or the instability of THFA at higher temperature.
Table 4 Effect of temperature on the hydrogenation of furfural in watera
Entry |
Temperature (°C) |
Conv. (%) |
Selectivity (%) |
THFA |
FA |
Others |
Reaction conditions: 10 g 5 wt% furfural aqueous solution, 0.2 g Ni/Ba–Al2O3 (10 wt% nickel, 4 mol% Ba), 4 MPa H2, 4 h. |
1 |
100 |
99 |
17 |
81 |
2 |
2 |
110 |
>99 |
37 |
62 |
1 |
3 |
120 |
>99 |
64 |
34 |
2 |
4 |
130 |
>99 |
93 |
3 |
4 |
5 |
140 |
>99 |
96 |
— |
4 |
6 |
150 |
>99 |
92 |
— |
8 |
7 |
160 |
>99 |
94 |
— |
6 |
Effect of H2 pressure
Table 5 showed the effect of H2 pressure on the hydrogenation of furfural in water. A more than 99% conversion of furfural was obtained under 1 MPa after 4 h revealing the high activity of the catalyst. The main product was FA with 75% selectivity, while the selectivity of THFA was very low (Table 5, entry 1). However, when the H2 pressure was increased to 2 MPa the selectivity of THFA reached 91% (Table 5, entry 2). This was very close to the best results acquired under the H2 pressure of 4 MPa (Table 5, entry 4). The effect of temperature and H2 pressure on the hydrogenation of furfural could be interpreted as follows. FA was the intermediate of the conversion of furfural to THFA. When the reaction was performed at lower reaction temperature or H2 pressure, the reaction only conducted the first step at the same reaction time. As a result the main product was FA. However, when the reaction conditions were strengthened the in situ formed FA can be further hydrogenated to THFA during the same reaction time.
Table 5 Effect of H2 pressure on the hydrogenation of furfural in watera
Entry |
Pressure (MPa) |
Conv. (%) |
Selectivity (%) |
THFA |
FA |
Others |
Reaction conditions: 10 g 5 wt% furfural aqueous solution, 0.2 g Ni/Ba–Al2O3 (10 wt% nickel, 4 mol% Ba), 140 °C, H2, 4 h. |
1 |
1 |
>99 |
8 |
75 |
17 |
2 |
2 |
>99 |
91 |
4 |
5 |
3 |
3 |
>99 |
94 |
0 |
6 |
4 |
4 |
>99 |
96 |
0 |
4 |
Catalyst recycling
Fig. 7 showed the recyclability of the Ni/Ba–Al2O3 catalyst. The catalyst was centrifuged and fully washed with ethanol and water after each cycle. After dried at 80 °C under vacuum, the catalyst was directly used for the next run. There was no noticeable decrease in the conversion of furfural and selectivity of THFA in all the four consecutive runs. This illustrated the catalyst was stable under the reaction conditions. Longer reaction time (6 h) was needed at the fourth cycle due to the loss of catalyst during the reuse process. The leaching of Ni and Ba was detected by ICP-AES after each cycle. The leaching of Ni was not detected during the whole cycle experiments (Table S2†). 13.2% of Ba loss from the catalyst after the first use. The reason was the soluble of barium oxide in water. However, the leaching of Ba was very little after the first use (smaller than 0.4%, Table S2†).
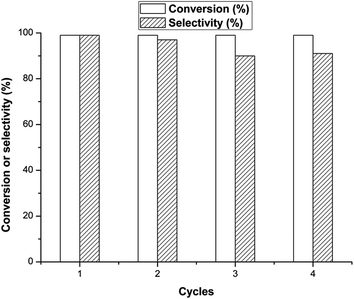 |
| Fig. 7 Cycle experiments of the hydrogenation of furfural in water. Reaction conditions: 10 g 5 wt% furfural aqueous solution, Ni/Ba–Al2O3 (10 wt% nickel, 10 mol% Ba), 140 °C, 4 MPa H2, 4 h, and 6 h for the fourth cycle. | |
Role of alkaline earth metals
It is interesting to discuss the role of alkaline earth metals for the high activity and selectivity and it could be interpreted as follows. The resinification of furfural or FA is easily occurred in hot water, especially in the presence of acids according to the results of literature6 and our previous work.16 The acid sites of the catalyst were attenuated by the alkaline earth metals. As a result, the side reaction of furfural or FA was inhibited, which was proved in Table 1. Few or no CPO or CPL was detected when the modified Ni/Al2O3 was employed as catalyst. The high activity of modified Ni/Al2O3 could be ascribed to the changed interaction of Ni and support which was revealed by the H2-TPR and XPS. This lead to the change in the adsorption ability of H2 over Ni which was proved by the H2-TPR. The decrease of NiAl2O4 after the modification was also responsible for the high activity. The relative contents was 62.0% for Ni/Al2O3 and 56.4%, 54.2%, 48.3%, 48.5% for Mg, Ca, Sr, Ba modified Ni/Al2O3 respectively (Table S1†). The NiAl2O4 had no hydrogenation activity. Consequently, the decrease of NiAl2O4 species will lead to the increase in hydrogenation activity.
Conclusions
In conclusion, the direct hydrogenation of furfural to THFA was investigated over nickel-based catalysts Ni/M–Al2O3 (M = Mg, Ca, Sr, Ba) in water. The kinetic study proved that FA was an intermediate. The modification of Al2O3 by alkaline earth metals significantly improved both the activity and selectivity of THFA. Furfural could be converted to THFA with 98% yield over Ni/Ba–Al2O3 under optimized conditions. The catalyst can be used at least 4 times with no obvious decrease in the conversion of furfural and selectivity of THFA.
Acknowledgements
This work was supported by the National Natural Science Foundation of China (21233008 and 21473184) and the “Strategic Priority Research Program-Climate Change: Carbon Budget and Related Issues” of the Chinese Academy of Sciences (XDA05010203).
Notes and references
- A. Corma, S. Iborra and A. Velty, Chem. Rev., 2007, 107, 2411 CrossRef CAS PubMed.
- J. Q. Bond, D. M. Alonso, D. Wang, R. M. West and J. A. Dumesic, Science, 2010, 327, 1110 CrossRef CAS PubMed.
- R. J. van Putten, J. C. van der Waal, E. de Jong, C. B. Rasrendra, H. J. Heeres and J. G. de Vries, Chem. Rev., 2013, 113, 1499 CrossRef CAS PubMed.
- A. J. J. Straathof, Chem. Rev., 2014, 114, 1871 CrossRef CAS PubMed.
- J. P. Lange, E. van der Heide, J. van Buijtenen and R. Price, ChemSusChem, 2012, 5, 150 CrossRef CAS PubMed.
- K. Zeitsch, The Chemistry and Technology of Furfural and itsMany By-Products Elsevier Science, Amsterdam, 2000 Search PubMed.
- T. Zhang, R. Kumar and C. E. Wyman, RSC Adv., 2013, 3, 9809 RSC.
- C. Garcia-Sancho, I. Sadaba, R. Moreno-Tost, J. Merida-Robles, J. Santamaria-Gonzalez, M. Lopez-Granados and P. Maireles-Torres, ChemSusChem, 2013, 6, 635 CrossRef CAS PubMed.
- K. Yan, G. Wu, T. Lafleur and C. Jarvis, Renewable Sustainable Energy Rev., 2014, 38, 663 CrossRef CAS.
- V. Choudhary, S. I. Sandler and D. G. Vlachos, ACS Catal., 2012, 2, 2022 CrossRef CAS.
- A. S. Mamman, J.-M. Lee, Y.-C. Kim, I. T. Hwang, N.-J. Park, Y. K. Hwang, J.-S. Chang and J.-S. Hwang, Biofuels, Bioprod. Biorefin., 2008, 2, 438 CrossRef CAS.
- J. Chen, F. Lu, J. Zhang, W. Yu, F. Wang, J. Gao and J. Xu, ChemCatChem, 2013, 5, 2822 CrossRef CAS.
- B. M. Nagaraja, A. H. Padmasri, B. David Raju and K. S. Rama Rao, J. Mol. Catal. A: Chem., 2007, 265, 90 CrossRef CAS.
- Rodiansono, S. Khairi, T. Hara, N. Ichikuni and S. Shimazu, Catal. Sci. Technol., 2012, 2, 2139 CAS.
- S. Iqbal, X. Liu, O. F. Aldosari, P. J. Miedziak, J. K. Edwards, G. L. Brett, A. Akram, G. M. King, T. E. Davies, D. J. Morgan, D. K. Knight and G. J. Hutchings, Catal. Sci. Technol., 2014, 4, 2280 CAS.
- Y. Yang, Z. Du, Y. Huang, F. Lu, F. Wang, J. Gao and J. Xu, Green Chem., 2013, 15, 1932 RSC.
- M. Hronec and K. Fulajtarová, Catal. Commun., 2012, 24, 100 CrossRef CAS.
- B. Zhang, Y. Zhu, G. Ding, H. Zheng and Y. Li, Green Chem., 2012, 14, 3402 RSC.
- F. Dong, Y. Zhu, G. Ding, J. Cui, X. Li and Y. Li, ChemSusChem, 2015, 8, 1534 CrossRef CAS PubMed.
- W. Xu, H. Wang, X. Liu, J. Ren, Y. Wang and G. Lu, Chem. Commun., 2011, 47, 3924 RSC.
- S. Sato, J. Igarashi and Y. Yamada, Appl. Catal., A, 2013, 453, 213 CrossRef CAS.
- J. H. Choi and W. Y. Lee, Appl. Catal., A, 1993, 98, 21 CrossRef CAS.
- S. Koso, H. Watanabe, K. Okumura, Y. Nakagawa and K. Tomishige, Appl. Catal., B, 2012, 111–112, 27 CrossRef CAS.
- M. Chia, Y. J. Pagan-Torres, D. Hibbitts, Q. Tan, H. N. Pham, A. K. Datye, M. Neurock, R. J. Davis and J. A. Dumesic, J. Am. Chem. Soc., 2011, 133, 12675 CrossRef CAS PubMed.
- S. Koso, N. Ueda, Y. Shinmi, K. Okumura, T. Kizuka and K. Tomishige, J. Catal., 2009, 267, 89 CrossRef CAS.
- S. Koso, I. Furikado, A. Shimao, T. Miyazawa, K. Kunimori and K. Tomishige, Chem. Commun., 2009, 2035 RSC.
- Y. Nakagawa, M. Tamura and K. Tomishige, ACS Catal., 2013, 3, 2655 CrossRef CAS.
- M. Besson, P. Gallezot and C. Pinel, Chem. Rev., 2014, 114, 1827 CrossRef CAS PubMed.
- R. Rao, A. Dandekar, R. T. K. Baker and M. A. Vannice, J. Catal., 1997, 171, 406 CrossRef CAS.
- Y. Nakagawa, K. Takada, M. Tamura and K. Tomishige, ACS Catal., 2014, 4, 2718 CrossRef CAS.
- S. Sitthisa, T. Sooknoi, Y. Ma, P. B. Balbuena and D. E. Resasco, J. Catal., 2011, 277, 1 CrossRef CAS.
- S. Sitthisa and D. E. Resasco, Catal. Lett., 2011, 141, 784 CrossRef CAS.
- Y. Nakagawa and K. Tomishige, Catal. Commun., 2010, 12, 154 CrossRef CAS.
- Y. Nakagawa, H. Nakazawa, H. Watanabe and K. Tomishige, ChemCatChem, 2012, 4, 1791 CrossRef CAS.
- N. S. Biradar, A. M. Hengne, S. N. Birajdar, P. S. Niphadkar, P. N. Joshi and C. V. Rode, ACS Sustainable Chem. Eng., 2014, 2, 272 CrossRef CAS.
- S. Sitthisa, T. Pham, T. Prasomsri, T. Sooknoi, R. G. Mallinson and D. E. Resasco, J. Catal., 2011, 280, 17 CrossRef CAS.
- N. Merat, C. Godawa and A. Gaset, J. Chem. Technol. Biotechnol., 1990, 48, 145 CrossRef CAS.
- Y. Yang, Z. Du, J. Ma, F. Lu, J. Zhang and J. Xu, ChemSusChem, 2014, 7, 1352 CrossRef CAS PubMed.
- Q. Meng, C. Qiu, G. Ding, J. Cui, Y. Zhu and Y. Li, Catal. Sci. Technol., 2016 10.1039/c5cy02248g.
- J. Juan-Juan, M. C. Román-Martínez and M. J. Illán-Gómez, Appl. Catal., A, 2004, 264, 169 CrossRef CAS.
- Z. Y. Hou, O. Yokota, T. Tanaka and T. Yashima, Appl. Catal., A, 2003, 253, 381 CrossRef CAS.
Footnote |
† Electronic supplementary information (ESI) available. See DOI: 10.1039/c6ra05680f |
|
This journal is © The Royal Society of Chemistry 2016 |
Click here to see how this site uses Cookies. View our privacy policy here.