DOI:
10.1039/C6RA05193F
(Paper)
RSC Adv., 2016,
6, 41181-41188
Low-temperature catalytic oxidation of CO over highly active mesoporous Pd/CeO2–ZrO2–Al2O3 catalyst†
Received
27th February 2016
, Accepted 11th April 2016
First published on 13th April 2016
Abstract
Mesoporous nano Pd/CeO2, Pd/CeO2–ZrO2 and Pd/CeO2–ZrO2–Al2O3 catalysts were prepared via a soft template-assisted hydrothermal method and employed in low-temperature catalytic CO oxidation. Almost 100% of CO conversion could be obtained by the optimal Pd/CeO2–ZrO2–Al2O3 catalyst at 60 °C. Addition of Zr and Al into Pd/CeO2 lead to an increase of the pore volume, average size of mesopores, the surface Ce3+/Ce4+ atomic ratios and Oadsorbed/Olattice, while the activation energy (Ea) decreased in the order Pd/CeO2 (50.4 kJ mol−1) > Pd/CeO2–ZrO2 (40.7 kJ mol−1) > Pd/CeO2–ZrO2–Al2O3 (32.4 kJ mol−1). The low-temperature CO catalytic conversion increased with the decreased activation energy (Ea).
1. Introduction
Catalytic oxidation of CO has been widely employed in indoor air cleaning, industrial catalytic CO combustion, automotive exhaust abatement and academic research.1,2 Various transition metal oxides,3 Ag,4 Au,5 and platinum-group metals (PGMs)6 components have been widely explored in CO catalytic oxidation. Spinal Co3O4,7 MnOx,8 supported Ag, Au and Pd catalysts exhibit excellent low-temperature CO oxidation performance. Among them, supported Pd catalysts have been employed in industrial applications for decades because of their long life cycles and moisture and thermal stability.9 To date, researchers continue focusing on light-off temperature, durability, thermal stability and the cost of the Pd-containing catalysts for their catalytic combustion of low-caloric-value industrial CO-containing waste gases. Light-off temperature is closely related to low-temperature catalytic activity.10 In addition, to promote surface palladium species dispersion is rather critical to enhance the catalytic activity and reduce the content and cost of palladium over the supported palladium catalysts.10,11 Great amounts of study have been carried out to promote Pd dispersion and enhance the supports durability, thermal stability and redox properties.11 A CeO2 component, with excellent oxygen-storing capacity (OSC), has been employed in various catalytic oxidation processes,12 while its remaining challenges are to improve the CeO2 specific surface area (SSA) and thermal stability. Researchers continue to focus on mixing metal and silicon components with CeO2 to improve the durability, thermal stability, OSC and SSA.13 Although OSC and CeO2 thermal stability could be enhanced with the CeO2–ZrO2 (CZ) solid solution formation by introducing Zr into the CeO2 lattice,14 promoting SSA on the CZ support remains a great challenge. While an increase of SSA is critical to improve Pd dispersion of CZ supported Pd catalysts. It is reported that CeO2 mixed with Zr and Al oxides (CeO2–ZrO2–Al2O3) are regarded as a new generation of oxygen-storing and thermal-stable materials for the catalytic process in the presence of oxygen.15 Improved thermal stability, durability, high SSA of Al2O3 and good OSC of CZ could be simultaneously maintained by introducing Al2O3 into CeO2–ZrO2 solid solution on the nanometer scale.16,17
In general, mesoporous materials with uniform pore-size distribution and large surface area are preferably employed as a catalyst support18 because of their promotion effect on noble metal dispersion. Compared with ordered silica materials (MCM-41),19 non-silica mesoporous CeO2–ZrO2–Al2O3 catalysts support exhibited superior thermal stability and OSC. Soft and hard templates are employed to synthesize mesoporous metal oxides catalysts.20 Hard templates are used to synthesize shape-controlled mesoporous materials,21,22 but time and energy consumption, a high thermal treating temperature (more than 650 °C22), or the relatively low yield23 of the product are great disadvantages for the industrial application of this method. Compared with hard templates, a facile hydrothermal method reported24 using commercially-available surfactants as a soft template is industrially achievable. In addition, it was found in our previous study25 that the hydrothermal method has the advantage of improving the specific surface area (SSA), pore volume and catalytic activity.
The present study has attempted to employ a soft template-assisted hydrothermal method to synthesize mesoporous Pd/CeO2, Pd/CeO2–ZrO2 and Pd/CeO2–ZrO2–Al2O3 catalysts for CO catalytic oxidation. Further explorations of the porous properties, kinetic behavior, as well as the active species surface abundance were conducted.
2. Experimental
2.1 Catalyst preparation
2.1.1 Preparation of CeO2–ZrO2–Al2O3. 3.5 g of Pluronic F127 (Ma 12, 600, Sigma-Aldrich), 0.009 mol of cerium nitrate, 0.009 mol of zirconium nitrate and 0.002 mol of aluminum nitrate (molar ratios of Ce
:
Zr
:
Al = 0.45
:
0.45
:
0.1) and urea (0.08 mol) were sequentially dissolved into 200 mL of deionized water at 60 °C. The resulting solution was then transferred to a stainless steel Teflon-lined autoclave and heated at 140 °C for 12 h. The final products were washed with distilled water, dried at 100 °C and calcined at 425 °C for 3 h in static air with a 3 °C min−1 heating rate.
2.1.2 Preparation of CeO2–ZrO2. 3.5 g of Pluronic F127 (Ma 12600, Sigma-Aldrich), 0.01 mol of cerium nitrate, 0.01 mol of zirconium nitrate (molar ratios of Ce
:
Zr = 1
:
1) and urea (0.08 mol) were sequentially dissolved into 200 mL of deionized water at 60 °C. The resulting solution was then transferred to a stainless steel Teflon-lined autoclave and heated at 140 °C for 12 h. The final products were washed, dried and calcined, as described in 2.1.1.
2.1.3 Preparation of CeO2. CeO2 was prepared as described in 2.1.1 and 2.1.2, using 0.02 mol of cerium nitrate as the precursor and 3.5 g of Pluronic F127 (Ma 12600, Sigma-Aldrich) as soft template.
2.1.4 Preparation of Pd/CeO2, Pd/CeO2–ZrO2 and Pd/CeO2–ZrO2–Al2O3. CeO2, CeO2–ZrO2 and CeO2–ZrO2–Al2O3 supported Pd catalysts were prepared by the wet impregnation method using an aqueous palladium nitrate solution as the precursor with 1% (wt%) Pd content. The impregnated samples were dried at 60 °C and calcined at 350 °C for 2 h. The catalysts are denoted as Pd/CeO2, Pd/CeO2–ZrO2 and Pd/CeO2–ZrO2–Al2O3, respectively.
2.2 Catalyst characterization
The X-ray diffraction (XRD) analysis was performed on a Bruker D8 Advance diffractometer system at 40 kV and 40 mA using Cu-Kα radiation (λ = 1.5406 Å). N2 adsorption–desorption tests were carried out on a Tristar II 3020 specific surface area and porosity analyzer. The samples were evacuated at 300 °C for 4 h and then tested at liquid N2 temperature (−196 °C). Transmission electron microscopy (TEM) was carried out on a FEI Tecnai G220 apparatus operated at 200 kV. Gatan Digital Micrograph (Version 3.9) software was employed to analyze the catalysts crystal structure and morphology. Low-temperature H2-temperature programmed reduction (H2-TPR) analyses were carried out in a U-shaped tube reactor (i.d. 3.0 mm). 50 mg of the sample (60–80 mesh) was pre-treated under N2 flow at 300 °C for 1 h and then cooled to 0 °C in an ice-water bath followed by the shifted flow of H2/Ar (5 vol% of H2, 30 mL min−1) and a linear heating rate of 2 °C min−1. A thermal conductivity detector (TCD) was used to record the consumption of H2 signals. XPS experiments were carried out on an ULVAC PHI 5000 Versa Probe-II equipped with an Al Kα UHV. The C 1s peak (284.8 eV) was used for calibrating the binding energy values.
2.3 Catalytic performance of CO oxidation
The catalytic activity of CO oxidation was carried out in a down-flow quartz-tube fixed bed reactor (i.d. 4 mm) filled with 200 mg of samples (60–80 mesh). Prior to the reaction, the catalysts were pretreated in an anhydrous air flow at 250 °C for 40 min. The reaction gas components were 1.0 vol% CO, 10.5 vol% O2, and N2 balanced, at a 50 mL min−1 total flow rate. The effluent gas was measured by an online gas chromatograph (GC) equipped with a flame ionization detector (FID) (equipped with a methanation conversion furnace) under steady-state conditions. The CO conversion was calculated as follows:
where [CO]in represents the CO concentration in the feed gas, [CO]out represents the CO concentrations in the effluent gases. T100, T90 and T50 were introduced to record the reaction temperature when CO conversion was 100%, 90% and 50%, respectively.
3. Results and discussion
3.1 Catalytic activity
It can be observed from Fig. 1 that T100, T90 and T50 of the various catalysts increased in the order Pd/CeO2–ZrO2–Al2O3 < Pd/CeO2–ZrO2 < Pd/CeO2. Therefore, it can be concluded that the addition of zirconia and aluminum oxide into Pd/CeO2 can obviously enhance the low-temperature CO catalytic activity. Over 99% of the CO conversion could be obtained by the optimal Pd/CeO2–ZrO2–Al2O3 catalyst at 60 °C. In addition, over 99% of CO conversion could be maintained at 70 °C for over 48 h (Fig. 2), indicating superior durability and industrial application potential of the Pd/CeO2–ZrO2–Al2O3 catalyst. Further research indicated that catalytic activity (ESI Fig. S1†) of the CeO2–ZrO2–Al2O3 supported palladium catalysts could be adjusted when different soft templates were used to synthesize Pd/CeO2–ZrO2–Al2O3 (ESI S1.1 and S1.2 and Fig. S1†).
 |
| Fig. 1 Conversion of low-temperature CO catalytic oxidation over various catalysts. | |
 |
| Fig. 2 Stability test for the Pd/CeO2–ZrO2–Al2O3 catalyst at 70 °C (reaction gas components: 1.0 vol% CO, 10.5 vol% O2, N2 balanced). | |
3.2 XRD analysis
It can be observed from Fig. 3 that no obvious diffraction peaks of aluminum and palladium species could be observed, indicating that aluminum and palladium species existed in the forms of highly dispersed or amorphous phase with low aluminum and palladium species content. Pd/CeO2 showed the highest CeO2 diffraction peaks, while the addition of zirconia and aluminum oxide into Pd/CeO2 obviously decreased the CeO2 crystallinity. Shoulders of asymmetric peaks between peak of CeO2 (111) at 2θ = 28.549° and ZrO2 (111) at 2θ = 30.119° indicated the formation of CexZr1−xO2 (0 < x < 1) solid solutions, which was reported to be critical for enhancing the OSC and catalytic activity.26 However, the present XRD analysis contained inadequate structure and texture information of CexZr1−xO2 (0 < x < 1) solid solutions. Further XPS analysis contained inadequate structure and texture information for the CexZr1−xO2 (0 < x < 1) solid solutions. The addition of aluminum into Pd/CeO2–ZrO2 further enhanced catalytic conversion of CO oxidation (Fig. 1) despite the increased CeO2 crystallinity and ZrO2 over the Pd/CeO2–ZrO2–Al2O3 catalyst. Therefore, it could be inferred that the CeO2 and ZrO2 crystallinity were not the determining factors in the experimental conditions.
 |
| Fig. 3 XRD patterns of various catalysts. | |
3.3 N2 adsorption–desorption tests
N2 adsorption–desorption isotherms and NL-DFT pore size distribution curves of the various catalysts are shown in Fig. 4. All the catalysts exhibited typical desorption curves of IUPAC IV and the hysteresis of H2, indicating the characteristics of a mesoporous structure with a wide pore size distribution. All samples showed uptakes of 16–19 cm3 (g STP)−1, indicating the presence of a minority of micro pores. It was notable that the N2 adsorption–desorption isotherms of Pd/CeO2–ZrO2–Al2O3 exhibited the lowest uptake around P/P0 = 0, indicating the highest ratio of mesorpores over the Pd/CeO2–ZrO2–Al2O3 catalyst (ESI Table S2†).
 |
| Fig. 4 N2 adsorption–desorption isotherms and pore size distribution of various catalysts. | |
It can be observed from Table 1 that addition of Zr and Al oxides into CeO2 can slightly improve the SSA of the catalysts. However, comparing with Pd/CeO2–ZrO2–Al2O3, Pd/CeO2–ZrO2 exhibited no significant SSA within systematic errors. Thus, it may be concluded that SSA are not the determining factors influencing catalytic activity (Fig. 1). Adding Zr oxide and further adding Al oxides could gradually increase the pore volume and average pore size, as well as the ratios and mesopore sizes over these cerium-based palladium catalysts. Pore-size distributions over the Pd/CeO2–ZrO2 and Pd/CeO2–ZrO2–Al2O3 catalysts were gradually extended as well (Fig. 4). Further studies indicated that a porous structure (ESI Fig. S2 and Table S3†) and SSA (ESI Table S3) of CeO2–ZrO2–Al2O3 supported palladium catalysts could be adjusted when different soft templates were used to synthesize Pd/CeO2–ZrO2–Al2O3 (ESI S1.1, S1.2, Fig. S2 and Table S3†).
Table 1 Specific surface area (SSA), pore volume and pore size of the various catalysts
Samples |
SSA (m2 g−1) |
Pore volume (cm3 g−1) |
Average pore size (nm) |
Pd/CeO2 |
98 |
0.084 |
3.9 |
Pd/CeO2–ZrO2 |
106 |
0.115 |
5.0 |
Pd/CeO2–ZrO2–Al2O3 |
105 |
0.127 |
5.5 |
3.4 TEM analysis
TEM images of the various catalysts are shown in Fig. 5. No obvious characteristic lattice fringes of aluminum oxides and aggregated palladium particles could be observed from the TEM analysis, indicating high dispersion and low crystallinity of aluminum oxides and palladium species, which is consistent with the XRD analysis. Projected images of Pd/CeO2 (Fig. 5(b)) exhibited compactly accumulated non-uniform particles with 15 to 80 nm particle size. Projected images of Pd/CeO2–ZrO2 (Fig. 5(d)) exhibited accumulated nanoparticles with single particles sized 5–25 nm, while Pd/CeO2–ZrO2–Al2O3 (Fig. 5(f)) exhibited uniform dispersed nanoparticles with particles sized 5–10 nm. Therefore, it can be inferred that addition of Zr into the Pd/CeO2 can decrease supports particle size. Further addition of Al into the Pd/CeO2–ZrO2 could lead to formation of uniformly dispersed nanoparticles and the support particle size could be further decreased as well. In terms of particle size over these cerium-based catalysts supports, the particle size decrease and uniform dispersed nanoparticles are preferred to enhance the low-temperature catalytic CO conversion.22,27
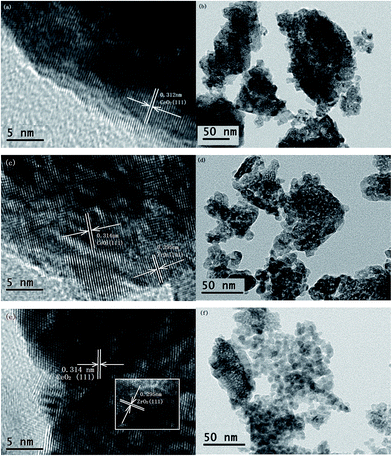 |
| Fig. 5 TEM images of (a) and (b) Pd/CeO2; (c) and (d) Pd/Ce–ZrO2; (e) and (f) Pd/CeO2–ZrO2–Al2O3 catalysts. | |
In addition, all catalysts listed (Fig. 5(b), (d) and (f)) possessed characteristics of interparticle space and sponge-like pore (with a pore size below 10 nm) networks with mesoporous size homogeneously distributed within the particles, indicating a mesoporous catalyst structure, which is consistent with our XRD and N2 adsorption desorption analysis. The lattice fringes of all the catalysts listed (Fig. 5(a), (c) and (e)) with a 0.314 nm interplanar distance revealed the (111) lattice plane of the cubic CeO2 structure. Pd/CeO2–ZrO2 and Pd/CeO2–ZrO2–Al2O3 with 0.295 nm interplanar distances (Fig. 5(c) and (e)) could be attributed to lattice planes of ZrO2 (111), indicating the existence of the ZrO2 structure.
3.5 Low-temperature H2-TPR analysis
Low-temperature H2-TPR profiles of various catalysts are shown in Fig. 6. The peaks denoted with α for Pd/CeO2–ZrO2 and Pd/CeO2–ZrO2–Al2O3 could be attributed to reduction of the surface exposed oxygen-containing PdO species.28 A shoulder in Pd/CeO2–ZrO2–Al2O3, denoted with β indicates the surface dissociated trans-state hydrogen (H–Pd–H) assisted reduction of surface exposed PdxM1−xO2−δ (M = Ce, Zr) structure;28,29 Pd/CeO2–ZrO2–Al2O3 showed overall higher H2 consumption than Pd/CeO2–ZrO2 from 0 to 80 °C, indicating a higher surface active Pd site dispersion over the Pd/CeO2–ZrO2–Al2O3 catalyst, while no obvious uptake of H2 consumption could be observed from the low-temperature H2-TPR profile of Pd/CeO2, indicating that palladium species over Pd/CeO2 catalyst might be incompletely exposed or the exposed palladium species over Pd/CeO2 are harder to be activated than that of Pd/CeO2–ZrO2 and Pd/CeO2–ZrO2–Al2O3 below 80 °C. Further study of H2-TPR (provided in the ESI Fig. S5†) indicated uptake of H2 consumption could be observed above 100 °C. Thus, it could be concluded that different abundances of surface exposed active palladium species and surface activation behavior of oxygen and CO may exist among these catalysts. Therefore, to determine the ratios of the surface exposed palladium species and activation energy over these palladium-containing catalysts, further surface XPS analysis, as well as a kinetic study was performed to explore the potential influencing factors and kinetic behaviors of the Pd/CeO2, Pd/CeO2–ZrO2 and Pd/CeO2–ZrO2–Al2O3 catalysts.
 |
| Fig. 6 Low-temperature H2-TPR profiles of the various catalysts. | |
3.6 XPS analysis
The Pd electronic state is critical for catalytic activity for many catalytic process over Pd-based catalysts30,31 and X-ray photoelectron spectroscopy (XPS) analysis was employed to explore the Pd electronic state. XPS spectra of Pd 3d and Zr 3p32 are shown in Fig. 7. It can also be observed in Fig. 7 that all palladium existed in the Pd(II) form (surface PdO and strong metal-support interacted Pd(II) (PdxM1−xO2−δ)),33,34 which is consistent with the low-temperature H2-TPR analysis (Fig. 6). Previous studies on positively charged Pd(II) species indicated that surface PdO exhibited a higher catalytic activity of CO oxidation than PdIMSI.27,35 In the present study, however, it was hard to obtain a quantitative analysis for surface PdO and PdxM1−xO2−δ from the XPS analysis as the influence of the Zr 3p peaks at 331.7 eV and 345.3 eV were less than 1.5 eV from the PdIMSI Pd 3d peak. Despite the lack of quantitive analysis of the different Pd(II) species, the low-temperature H2-TPR analysis (Fig. 6) indicated the existence of hydrogen-activated surface PdO species over both Pd/CeO2–ZrO2 and Pd/CeO2–ZrO2–Al2O3 below 80 °C and in the absence of surface hydrogen-activated PdO species over Pd/CeO2 at 0 to 80 °C.
 |
| Fig. 7 Pd 3d and Zr 3p XPS spectra. | |
XPS spectra of the Ce 3d are shown in Fig. 8. The BE peaks marked as v′0 (902.2 eV), v′1 (908.3 eV) and v′2 (917.5 eV) arise from Ce4+ 3d3/2, while the BE peaks labeled as v0 (882.5 eV), v1 (889.1 eV) and v2 (898.4 eV) arise from Ce4+ 3d5/2. The u′0 (904.5 eV) and u0 (885.4 eV), refer to the 3d3/2 and 3d5/2 orbitals, respectively, suggesting the presence of a Ce3+ final state.36–38 The O 1s XPS spectra of the catalysts can be resolved into two peaks, as shown in Fig. 9. The peaks at around 529.5 eV (denoted with Olattice) are the characteristic peak of metal–oxygen (the lattice oxygen O2−) and the peak at 531.5 eV (denoted with Oadsorbed) is usually associated with surface adsorbed oxygen (chemisorbed oxygen OH− or CO32−).39,40 It has been reported26,41,42 that surface molar ratios of Ce3+/Ce4+ and Oadsorbed/Olattice have an important influence on the oxygen storing and releasing capacity in the presence of oxygen due to the dynamic balance of
between the losses of electron from CO and gains of electrons from gaseous, adsorbed and lattice oxygen.9,26,29,41,42 In the present study, the surface molar ratios of Ce3+/Ce4+ and Oadsorbed/Olattice were analyzed over various catalysts using ULVAC-PHI MultiPak™ Software Manual (Version 9, ULVAC-PHI Inc.) and XPS PeakFit (Version 4.0, AISN Software Inc.) software.
 |
| Fig. 8 Ce 3d XPS spectra. | |
 |
| Fig. 9 O 2s XPS spectra. | |
The surface atomic ratios of Ce3+/Ce4+ were determined according to the following equation:
where
S1,
S2,
S3,
S4,
S5,
S6,
S7 and
S8 represent the peak areas of the corresponding
v0,
u0,
v1,
v2,
v′
0,
u′
0,
v′
1 and
v′
2 lines, respectively.
The surface atomic ratios of Oadsorbed/Olattice were calculated according to the following formula:
Oadsorbed/Olattice = Sadsorbed/Slattice, |
where
Sadsorbed and
Slattice are the peak areas corresponding to O
2− and OH
−/CO
32−, respectively.
Surface atomic ratios of Ce3+/Ce4+ and Oadsorbed/Olattice are listed in Table 2. With the addition of zirconium and aluminum into the Pd/CeO2, surface Ce3+/Ce4+ and Oadsorbed/Olattice, as well as the low-temperature catalytic activity (Fig. 1) increased in the order Pd/CeO2 < Pd/CeO2–ZrO2 < Pd/CeO2–ZrO2–Al2O3 (Table 2).
Table 2 Surface atomic ratios, activation energy (Ea) and T50 of the various catalysts
Samples |
Surface ceriuma |
Surface oxygena |
Eab (kJ mol−1) |
T50 (°C) |
Ce3+/Ce4+ |
Oadsorbed/Olattice |
Derived from XPS analysis, calculated by ULVAC-PHI MultiPak™ Software Manual (Version 9, ULVAC-PHI Inc.) and XPS PeakFit (Version 4.0, AISN Software Inc.). Calculated from the CO oxidation Arrhenius dependencies (Fig. 11). |
Pd/CeO2–ZrO2–Al2O3 |
0.215 |
1.398 |
32.4 |
42 |
Pd/CeO2–ZrO2 |
0.212 |
0.923 |
40.7 |
55 |
Pd/CeO2 |
0.196 |
0.862 |
50.4 |
68 |
3.7 Kinetic study of CO oxidation over supported Pd catalysts
Fig. 10 shows the effect of CO concentration on the reaction rate at different temperatures. In these kinetic experiments, temperature was varied in the range of 313–323 K to keep CO conversion below 20%, i.e., a differential reactor approach could be assumed.43
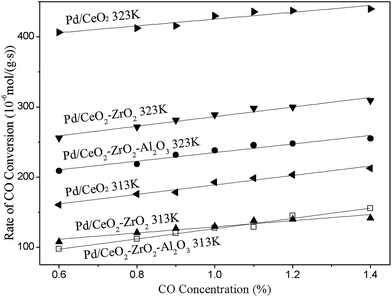 |
| Fig. 10 Effects of CO concentration and temperature on the CO oxidation rate, with Pd/CeO2, Pd/CeO2–ZrO2 and Pd/CeO2–ZrO2–Al2O3, in the 313–323 K range. (The concentration of O2 was maintained constant). | |
The effects of CO concentration and temperature on the CO oxidation rate at 313–323 K indicated that the reaction rate increased monotonically with CO concentration (Fig. 10). Therefore, it may inferred that the reaction was not inhibited by the CO concentration, despite the low-temperature catalytic oxidation (LTO) of CO over pure noble-metal catalysts under vacuum conditions generally occurring by the Langmuir–Hinshelwood (L–H) or Eley–Rideal (E–R) mechanisms44,45 based on a single site for CO and O2 adsorption. However, it has been reported46 that the reaction order with respect to oxygen should approach zero, while a positive order with respect to CO is expected. Because CO could be first adsorbed on the surface active sites of the supported noble-metal catalysts and react on the surface (set to control steps) to form CO2,3,9,29 followed by CO2 desorption, the reaction can be simplified to zero order with respect to oxygen and +1 with respect to CO for low CO concentrations.40 The reaction rate was calculated using the formula:43,47 W(molecules per cm2 per s) = (C0CO × X × VRM)/(m × Ssp), where C0CO is the initial concentration of CO (molecules per cm3), X is the CO conversion, VRM is the reaction mixture flow rate (cm3 s−1), m is the catalyst weight (g), and Ssp is the specific surface area (cm2 g−1).
Arrhenius dependences of the CO oxidation rate for various catalysts are shown in Fig. 11. The calculated activation energies48 of the various catalysts decreased in the order Pd/CeO2 (Ea = 50.4 kJ mol−1) > Pd/CeZrO2 (Ea = 40.7 kJ mol−1) > Pd/CeO2–ZrO2–Al2O3 (Ea = 32.4 kJ mol−1) (Table 2). Taking the significant differences of Ea (Table 2), H2-TPR (Fig. 6) results and previous reports3,9,29,47 into consideration, the dramatic catalytic activity differences over these catalysts may be caused by different adsorption and (or) activation behaviors of CO. However, further mechanistic study into this is expected.
 |
| Fig. 11 Arrhenius dependences of CO oxidation rate over various catalysts. | |
4. Conclusions
Mesoporous nano CeO2, CeO2–ZrO2 and CeO2–ZrO2–Al2O3 supported palladium catalysts were prepared and employed in low-temperature CO catalytic oxidation. The optimal Pd/CeO2–ZrO2–Al2O3 catalyst exhibited over 99% CO conversion at 70 °C for more than 48 hours. The surface atomic ratios of Ce3+/Ce4+ and Oadsorbed/Olattice, pore volume, average pore size and low-temperature CO catalytic conversion gradually increased with the addition of Zr into the Pd/CeO2 and with further addition of Al into Pd/CeO2–ZrO2, while particle size of these cerium-based support decreased with the addition of Zr into Pd/CeO2 and further addition of Al into Pd/CeO2–ZrO2. In addition, the activation energy (Ea) decreased in the order Pd/CeO2 (50.4 kJ mol−1) > Pd/CeZrO2 (40.7 kJ mol−1) > Pd/CeO2–ZrO2–Al2O3 (32.4 kJ mol−1), which was critical to the increased low-temperature CO catalytic conversion.
Acknowledgements
This study is supported by the National Natural Science Foundation of China (No. 21307047).
References
- P. Doggali, H. Kusaba, H. Einaga, S. Bensaid, S. Rayalu, Y. Teraoka and N. Labhsetwar, J. Hazard. Mater., 2011, 186, 796 CrossRef CAS PubMed.
- Y. Xu, J. Q. Ma, Y. F. Xu, L. Xu, L. Xu, H. X. Li and H. Li, RSC Adv., 2013, 3, 851 RSC.
- S. Y. Wang, N. Li, L. F. Luo, W. X. Huang, Z. Y. Pu, Y. J. Wang, G. S. Hu, M. F. Luo and J. Q. Lu, Appl. Catal., B, 2014, 144, 325 CrossRef CAS.
- X. D Zhang, Z. P. Qu, F. L Yu and Y. Wang, Chin. J. Catal., 2013, 34, 1277 CrossRef.
- I. X. Green, W. J. Tang, M. Neurock and J. T. Yates Jr, Science, 2011, 333, 736 CrossRef CAS PubMed.
- T. S. Nguyen, F. Morfin, M. Aouine, F. Bosselet, J. L. Rousset and L. Piccolo, Catal. Today, 2015, 253, 106 CrossRef CAS.
- X. Xie, Y. Li, Z. Q. Liu, M. Haruta and W. Shen, Nature, 2009, 458, 746 CrossRef CAS PubMed.
- V. Iablokov, K. Frey, O. Geszti and N. Krus, Catal. Lett., 2010, 134, 210 CrossRef CAS.
- G. N. Li, L. Li, Y. Yuan, J. J. Shi, Y. Y. Yuan, Y. S. Li, W. R. Zhao and J. L. Shi, Appl. Catal., B, 2014, 341, 158–159 Search PubMed.
- Y. Zhou, Z. Wang and C. Liu, Catal. Sci. Technol., 2015, 5, 69 CAS.
- G. N. Li, L. Li and D. Jiang, J. Phys. Chem. C, 2015, 119, 12502 CAS.
- J. Guzman, S. Carrettin and A. Corma, J. Am. Chem. Soc., 2005, 127, 3286 CrossRef CAS PubMed.
- B. M. Reddy and A. Khan, Catal. Surv. Asia, 2005, 9, 155 CrossRef CAS.
- Y. Nagai, T. Nonaka, A. Suda and M. Sugiura, R&D Review of Toyota CRDL, 2002, 37, 21 Search PubMed.
- T. Suzuki, A. Morikawa, A. Suda, H. Sobukawa, M. Sugiura, T. Kanazawa, J. Suzuki and T. Takada, R&D Review of Toyota CRDL, 2002, 37, 28 CAS.
- T. Kanazawa, J. Suzuki, T. Takada, T. Suzuki, A. Morikawa, A. Suda, H. Sobukawa and M. Sugiura, Stud. Surf. Sci. Catal., 2003, 145, 415 CrossRef CAS.
- A. Morikawa, T. Suzuki, T. Kanazawa, K. Kikuta, A. Suda and H. Shinjo, Appl. Catal., B, 2008, 78, 210 CrossRef CAS.
- A. Corma, Chem. Rev., 1997, 6, 2373 CrossRef.
- A. Taguchi and F. Schüth, Micropor. Mesopor. Mat., 2005, 77, 1 CrossRef CAS.
- Y. D. Liu, J. Goebl and Y. D. Yin, Chem. Soc. Rev., 2013, 42, 2610 RSC.
- W. Han, G. Zhang, G. Lu and Z. Tang, RSC Adv., 2015, 5, 59666 RSC.
- M. F. Luo, Y. P. Song, X. Y. Wang, G. Q. Xie, Z. Y. Pu, P. Fang and Y. L. Xie, Catal. Commun., 2007, 8, 834 CrossRef CAS.
- Y. Ren, Z. Ma, R. E. Morris, Z. Liu, F. Jiao, S. Dai and P. G. Bruce, Nat. Commun., 2013, 4, 2015 Search PubMed.
- M. F. Luo, J. M. Ma, J. Q. Lu, Y. P. Song and Y. J. Wang, J. Catal., 2007, 246, 52 CrossRef CAS.
- P. Ning, Z. Song, H. Li, Q. Zhang, X. Liu, J. Zhang, X. Tang and Z. Huang, Appl. Surf. Sci., 2015, 332, 130 CrossRef CAS.
- S. Bedrane, C. Descorme and D. Duprez, Catal. Today, 2002, 75, 401 CrossRef CAS.
- S. Hinokuma, H. Fujii, M. Okamoto, K. Ikeue and M. Machida, Chem. Mater., 2010, 22, 6183 CrossRef CAS.
- B. H. Yue, R. X. Zhou, Y. J. Wang and X. M. Zheng, J. Mol. Catal. A Chem., 2005, 238, 241 CrossRef CAS.
- L. Meng, A. P. Jia, J. Q. Lu, L. F. Luo, W. X. Huang and M. F. Luo, J. Phys. Chem. C, 2011, 115, 19789 CAS.
- X. Yuan, G. Sun, H. Asakura, T. Tanaka, X. Chen, Y. Yuan, G. Laurenczy, Y. Kou, P. J. Dyson and N. Yan, Chem. Eur. J., 2013, 19, 1227 CrossRef CAS PubMed.
- B. Zhang, Y. Yuan, K. Philippot and N. Yan, Catal. Sci. Technol., 2015, 5, 1683 CAS.
- L. Y. Chen, H. R. Chen and Y. W. Li, Chem. Commun., 2014, 50, 14752 RSC.
- S. Sharma, B. D. Mukri and M. S. Hegde, Dalton Trans., 2011, 40, 11480 RSC.
- K. R. Priolkar, P. Bera, P. R. Sarode, M. S. Hegde, S. Emura, R. Kumashiro and N. P. Lalla, Chem. Mater., 2002, 14, 2120 CrossRef CAS.
- L. Meng, J. J. Lin, Z. Y. Pu, L. F. Luo, A. P. Jia, W. X. Huang, M. F. Luo and J. Q. Lu, Appl. Catal., B, 2012, 119–120, 117 CrossRef CAS.
- L. H. Xiao, K. P. Sun, X. L. Xu and X. N. Li, Catal. Commun., 2005, 6, 796 CrossRef CAS.
- R. V. Gulyaev, A. I. Stadnichenko, E. M. Slavinskaya, A. S. Ivanova, S. V. Koscheev and A. I. Boronin, Appl. Catal., A, 2012, 439–440, 41 CrossRef CAS.
- J. Fan, X. D. Wu, X. D. Wu, Q. Liang, R. Ran and D. Weng, Appl. Catal., B, 2008, 81, 38 CrossRef CAS.
- S. Ponce, M. A. Peña and J. L. G. Fierro, Appl. Catal., B, 2000, 24, 193 CrossRef CAS.
- H. Najjar, J. F. Lamonier, O. Mentre, J. M. Giraudon and H. Batis, Appl. Catal., B, 2011, 106, 149 CAS.
- S. A. Ghom, C. Zamani, S. Nazarpour, T. Andreu and J. R. Morante, Sens. Actuators, B, 2009, 140, 216 CrossRef CAS.
- G. Preda, A. Migani, K. M. Neyman, S. T. Bromley, F. Illas and G. Pacchioni, J. Phys. Chem. C, 2011, 115, 5817 CAS.
- R. V. Gulyaev, E. M. Slavinskaya, S. A. Novopashin, D. V. Smovzh, A. V. Zaikovskii, D. Y. Osadchii, O. A. Bulavchenko, S. V. Korenev and A. I. Boronin, Appl. Catal., B, 2014, 147, 132 CrossRef CAS.
- S. H. Oh, G. B. Fisher, J. E. Carpenter and D. W. Goodman, J. Catal., 1986, 100, 360 CrossRef CAS.
- C. H. F. Peden, D. W. Goodman, M. D. Weisel and F. M. Hoffmann, Surf. Sci., 1991, 253, 44 CrossRef CAS.
- J. L. Ayastuy, A. Gurbani, M. P. González-Marcos and M. A. Gutierrez-Ortiz, Ind. Eng. Chem. Res., 2009, 48, 5633 CrossRef CAS.
- Y. Guo, C. Li, S. Lu and C. Zhao, RSC Adv., 2015, 5, 59666 RSC.
- Z. Wu, L. Zhang, Q. Guan, M. Fu, D. Ye and T. Wu, Mater. Res. Bull., 2015, 70, 567 CrossRef CAS.
Footnote |
† Electronic supplementary information (ESI) available. See DOI: 10.1039/c6ra05193f |
|
This journal is © The Royal Society of Chemistry 2016 |
Click here to see how this site uses Cookies. View our privacy policy here.