DOI:
10.1039/C6RA05068A
(Paper)
RSC Adv., 2016,
6, 36211-36217
Facile synthesis of hybrid Cu2O/Pd–Fe3O4 nanocatalysts for C–H arylation of 4-nitroimidazoles†
Received
25th February 2016
, Accepted 1st April 2016
First published on 5th April 2016
Abstract
A facile synthetic strategy for a hybrid Cu2O/Pd–Fe3O4 nanocomposite via controlled thermal decomposition of Fe(CO)5 and reduction of Pd(OAc)2 and Cu(acac)2 was developed. The Pd precursor and amount of reducing agent used during the synthetic process controlled the morphology of the Cu2O/Pd–Fe3O4 nanocomposites. The prepared Cu2O/Pd–Fe3O4 nanocomposites showed excellent catalytic performance for C–H arylation, which can be attributed to the synergetic catalytic system formed from the catalytically effective Pd and Cu2O. Moreover, to the best of our knowledge, the C–H arylation of 4-nitroimidazoles with aryl iodides catalyzed by heterogeneous nanocatalysts has not been reported in the literature.
Introduction
Hybrid Pd–Fe3O4 nanostructures have many advantages, such as their high catalytic activity and magnetic recyclability, which are due to the Pd and Fe3O4 components, respectively, of the nanocomposites. There have been many reports of the synthesis of hybrid Pd–Fe3O4 nanocomposites using various synthetic procedures.1–3 For example, Hyeon et al.4 have reported a simple synthesis of Pd–Fe3O4 heterodimer nanocrystals for cross-coupling reactions, and Wang et al.5 have reported the use of carbon-coated Fe3O4 microspheres as a magnetic support for palladium nanoparticles (NPs).
Recently, the immobilization of copper or copper oxide NPs onto various metal oxides such as Co3O4,6 Fe3O4 (ref. 7) and ZnO8 has attracted increasing attention because of the tunable properties of the composites produced. It can modify the catalytic activity and optical properties of these hybrid nanocomposites. Furthermore, Cu-doped ZnO nanomaterials as diluted magnetic semiconductors, which are of huge interest owing to their potential applications in spintronics, have also been reported.9,10 However, the development of hybrid Pd–Fe3O4 nanocomposites with copper oxide has not been reported, except for those developed by our group.11 The research about Cu2O/Pd–Fe3O4 nanocomposites are important since these ternary hybrid systems can exhibit higher catalytic activities than single-metal catalytic systems for many organic reactions, because of electron transfer across the metal-oxide interface.12,13
Transition-metal-catalyzed C–H activation reactions have been the subject of intensive study in modern organic chemistry.14,15 The regioselectivity of C–H activation reactions containing two or more reactive C–H bonds is controlled by the presence of functional groups in the substrate.16,17 However, the use of compounds containing nitroazole functionality in this reaction has been rarely reported, despite the importance of nitroazoles in medicinal chemistry and materials science.18–20 To the best of our knowledge, the C–H arylation of 4-nitroimidazoles catalyzed by heterogeneous nanocatalysts has not been reported in the literature. The presence of the nitro group confers the C5 positions of imidazoles with electrophilicity and acidity, allowing for efficient reactions.21 In this work, we report the development a facile one-pot synthesis of hybrid nanocomposites of Cu2O/Pd–Fe3O4. These hybrid Cu2O/Pd–Fe3O4 nanocomposites show high catalytic activities and stabilities in the C–H arylation of 4-nitroimidazoles.
Experimental
Synthesis of Cu2O/Pd–Fe3O4 and Pd–Fe3O4 nanocomposites11
Pd(OAc)2 (0.112 g) was dissolved in a mixture of oleylamine (OAm) (10 mL) and 1-octadecene (ODE) (10 mL). The flask was heated to 60 °C and further heated to 120 °C at a heating rate of 6 °C min−1. The mixture was maintained at this temperature for 30 min. Fe(CO)5 (0.15 mL) was then added under Ar, and the solution was further heated to 160 °C at a heating rate of 4 °C min−1 and maintained at this temperature for 30 min. A Cu(acac)2/OAm solution (32 mg/5 mL) was then added dropwise, and the reaction temperature was raised to 240 °C at a heating rate of 2.7 °C min−1, where it was maintained for 30 min. The heating source was then removed, and the solution was allowed to cool to room temperature. A black product was precipitated by adding ethanol and hexane, and separated by centrifugation.
Pd–Fe3O4 nanocomposites were also synthesized by the same method, but without the addition of the Cu(acac)2/OAm mixture. After the Fe(CO)5 was injected, the solution was further heated to 160 °C at a heating rate of 4 °C min−1 and kept at this temperature for 30 min. The heating source was then removed, and the solution was cooled to room temperature. A black product was precipitated by adding ethanol and hexane, and separated by centrifugation. The Pd–Fe3O4 nanocomposites were used as a control.
General procedure for synthesis of 1-butyl-4-nitro-1H-imidazole19
To a stirred solution of 4-nitroimidazole (1.00 g, 8.84 mmol) in DMF (6.00 mL) at 25 °C were added K2CO3 (1.47 g, 10.6 mmol) and 1-iodobutane (10.6 mmol). After stirring for 16 h at 25 °C, the reaction mixture was treated with water (15 mL) and EtOAc (20 mL) and transferred to a 125 mL separation funnel. The organic layer was collected and the aqueous layer was extracted with EtOAc (25 mL × 2). The combined organic layers were washed with brine (20 mL), dried over sodium sulfate and filtered. The filtrate was concentrated, and the residue was purified by flash column chromatography to provide the corresponding 1-butyl-4-nitro-1H-imidazole.
General procedure for C–H arylation of 4-nitroimidazoles
The Cu2O/Pd–Fe3O4 (Pd base: 5.0 mol%), 1-butyl-4-nitro-1H-imidazole (0.085 g, 0.5 mmol, 1.0 equiv.), iodobenzene (0.112 mL, 1 mmol, 2 equiv.), sodium acetate (0.164 g, 1.0 mmol, 2.0 equiv.) and DMSO (5.0 mL) were mixed in a glass vial. The mixture was vigorously stirred at 140 °C. After the reaction, the catalyst was filtered and the reaction mixture was extracted with EtOAc and water. Drying with MgSO4, filtration, and solvent evaporation of the filtrate afforded the reaction products.
Recyclability tests
After the reaction, the catalyst was separated from the clean solution by centrifugation, and decanted using an external magnet. The recovered particles were reused as the catalyst in the next reaction.
Characterization
The morphology of each sample was characterized by transmission electron microscopy (TEM) (Omega EM912 operated at 120 kV, Korea Basic Science Institute, and a Tecnai G2 F30 operated at 300 kV, KAIST) by placing a few drops of the corresponding colloidal solution onto a carbon-coated copper grid (200 mesh, F/C coated, Ted Pella Inc., Redding, CA, USA). Field emission scanning electron microscopy (FE-SEM) (Hitachi S-4800, National Nanofab Center, South Korea) was also used for analyses. X-ray powder diffraction (XRD) patterns were recorded on a Rigaku D/MAX-RB (12 kW) diffractometer. X-ray photoelectron spectroscopy (XPS) (Theta Probe, Thermo) was employed to measure the structural and chemical properties of the nanocomposites. The contents of the each metal element were determined using an inductively coupled plasma-atomic emission spectrometer (ICP-AES) (iCAP 6300). The surface area and pore-size distribution of the samples were calculated by using the Brunauer–Emmett–Teller (BET) equation and the BJH method, respectively. Magnetization data were taken using a superconducting quantum interference device (SQUID) (MPMS-7, Quantum design). The reaction products were analyzed by 1H NMR spectroscopy using a Varian Mercury Plus (300 MHz). Chemical shift values were recorded in parts per million (ppm) relative to tetramethylsilane as an internal standard unless otherwise indicated, and coupling constants are given in Hz.
Results
Synthesis of the hybrid Cu2O/Pd–Fe3O4 catalyst
The Cu2O/Pd–Fe3O4 nanocomposites were synthesized by facile decomposition of Fe(CO)5 and reduction of Pd(OAc)2 and Cu(acac)2 in OAm and ODE (Scheme 1). In the synthesis, the mixture of Pd(OAc)2 (0.114 g), OAm (10 mL) and ODE (10 mL) were stirred at 60 °C and then heated to 120 °C at a heating rate of 6 °C min−1. The mixture was maintained at this temperature for 30 min. Fe(CO)5 (0.15 mL) was then added under Ar gas, and the solution was heated to 160 °C at a heating rate of 4 °C min−1, and maintained at 160 °C for 30 min. A solution of Cu(acac)2 (32 mg) in OAm (5 mL) was then added, and the reaction temperature was raised to 240 °C at a rate of 2.7 °C min−1. After 30 min, the mixture was cooled to room temperature. The reaction mixture was centrifuged in ethanol and hexane, affording a black precipitate. The Pd
:
Fe
:
Cu atomic ratio of the Cu2O/Pd–Fe3O4 nanocomposites was estimated to be 30
:
63
:
7 by ICP-AES.
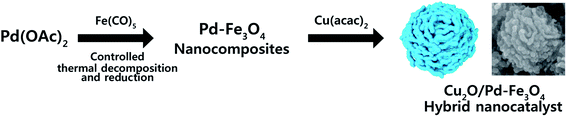 |
| Scheme 1 Synthetic scheme of Cu2O/Pd–Fe3O4 nanocomposites. | |
The Cu2O/Pd–Fe3O4 hybrid nanocomposites were characterized using SEM and TEM (Fig. 1) and shown to have an average diameter of 173 nm. These microspheres consist of some nanosheets growing out of the small seed particles in the center. For control experiments, Pd–Fe3O4 nanocomposites were also synthesized without addition of the Cu(acac)2 precursor (Fig. S1†), and exhibited almost identical morphology to that of Cu2O/Pd–Fe3O4.
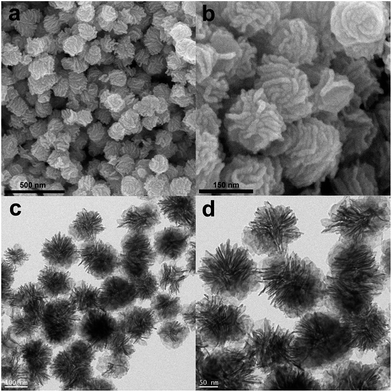 |
| Fig. 1 SEM (a and b) and TEM (c and d) images of Cu2O/Pd–Fe3O4 hybrid nanocomposites. | |
Crystal structural studies were carried out using XRD (Fig. 2a). The XRD patterns of the Cu2O/Pd–Fe3O4 nanocomposites confirm the face-centered cubic (fcc) Pd crystal structure (JCPDS no. 46-1043) and cubic spinel structure of Fe3O4 (JCPDS no. 19-0629). The high-resolution TEM (HR-TEM) image shown in Fig. 2b indicates that highly crystalline Pd and Fe3O4 particles with lattice fringes are formed in the synthesis. The line spacings of 0.22 nm and 0.30 nm can be indexed to the Pd (111) and Fe3O4 (220) reflections of the fcc (Pd) and cubic spinel (Fe3O4) structures, respectively. Amorphous Cu2O particles are not indicated by the XRD patterns or the HR-TEM images. However, in the high-angle annular dark-field scanning transmission electron microscopy (HAADF-STEM) images, and the corresponding elemental mapping images, it is clearly shown that the Pd, Fe, and Cu contents are uniformly distributed throughout the entire nanocomposite, confirming the hybrid Cu2O/Pd–Fe3O4 structure (Fig. 3). The SQUID data show the magnetic curves as a function of the applied field at 300 K (Fig. S2†). The saturation magnetization value of the Cu2O/Pd–Fe3O4 nanocomposite was 28 emu g−1. Moreover, both the remanence and coercivity of the nanocomposite were close to zero, indicating superparamagnetism.
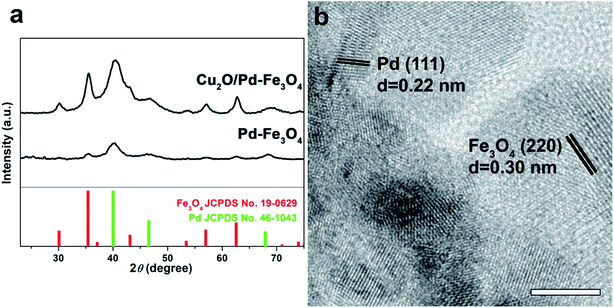 |
| Fig. 2 (a) XRD patterns of Pd–Fe3O4 and Cu2O/Pd–Fe3O4 and (b) HR-TEM image of Cu2O/Pd–Fe3O4. The bar in the (b) represents 5 nm. | |
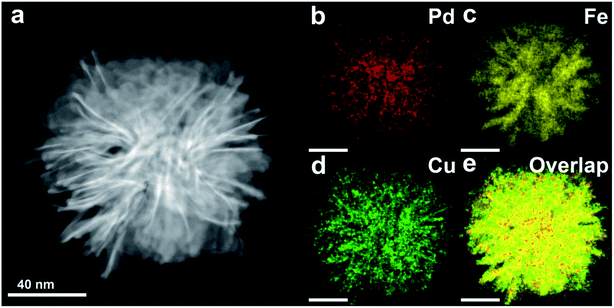 |
| Fig. 3 (a) HAADF-STEM image of Cu2O/Pd–Fe3O4 and elemental mapping of (b) Pd, (c) Fe, (d) Cu and (e) overlap. | |
The specific surface areas of the Pd–Fe3O4 and Cu2O/Pd–Fe3O4 nanocomposites were measured by the BET method, and are 23.8 and 28.2 m2 g−1, respectively. This value is much higher than that of the previously reported hollow (12.27 m2 g−1) and solid sphere-like (5.43 m2 g−1) Fe3O4 microspheres because of the nanosheets of Pd–Fe3O4.22 XPS analysis indicates the elemental composition and existence of Cu2O (Fig. 4). The wide-scan XPS spectra of Cu2O/Pd–Fe3O4 shows photoelectron lines at a binding energy of ca. 284.5 eV, attributed to C 1s (Fig. 4a). There are two Cu 2p3/2 peaks for Cu2O and CuO, and the binding energy of the Cu2O peak (931.4 eV) is lower than that of Cu metal (932.3 eV) because of the binding between Pd and Cu particles (Fig. 4b).23 In the Fe 2p spectrum (Fig. 4c), the Fe 2p3/2 peaks are located at 710.0 eV, indicating the formation of Fe3O4.24 For Pd, the most intense peaks are observed at binding energies of ca. 334.8 eV (3d5/2), indicating the presence of metallic Pd (Fig. 4d). The effect of the precursor on the reaction kinetics and final morphology of the Cu2O/Pd–Fe3O4 nanostructures was studied. It has been previously reported that different Pd precursors can be reduced to Pd atoms at different rates.25 As shown in Fig. 5, Cu2O/Pd–Fe3O4 nanostructures with different shapes and sizes were obtained under the same conditions, except for the use of different precursors. When Pd(CF3COO)2 is used as the precursor, only plate-like structures are obtained, and not spherical particles, suggesting that the faster reaction kinetics of Pd(CF3COO)2 affects the final morphology of Cu-doped Pd–Fe3O4.26 Fig. S3† shows TEM images of Cu2O/Pd–Fe3O4 nanocomposites synthesized with different amounts of solvents (OAm and ODE). When only OAm (20 mL) is used without addition of ODE, spherical nanocomposites that consist of small particles are synthesized (Fig. S3a and c†). However, when only ODE (20 mL) is used, the nanocomposites do not grow well, demonstrating that OAm is a crucial reducing agent for synthesizing Cu2O/Pd–Fe3O4 (Fig. S3b and d†).
 |
| Fig. 4 The XPS spectra of Cu2O/Pd–Fe3O4 nanocomposites. | |
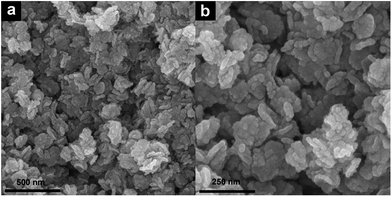 |
| Fig. 5 Cu2O/Pd–Fe3O4 nanocomposites synthesized by Pd(CF3COO)2 precursors. | |
C–H arylation of 1-butyl-4-nitro-1H-imidazoles
The catalytic activity of Cu2O/Pd–Fe3O4 was examined for the C–H arylation of 1-butyl-4-nitro-1H-imidazoles with iodobenzenes as the benchmark substrates (Table 1). First, in order to determine the solvent system most suitable for the catalyst, several experiments were conducted in the presence of Pd–Fe3O4 at 130 °C for 18 h (Table 1, entries 1–3). It was expected that the reaction conditions would be affected by the solubilities of the reactant and catalyst in the reaction medium, resulting in increased conversion in the more polar solvent (DMSO). The effect of the base (NaOAc, LiOAc, or Cs2CO3) in the standard reaction was also investigated (Table 1, entries 3–5). Higher conversion is obtained with NaOAc (62%) than with LiOAc or Cs2CO3. Moreover, in terms of turnover frequency (TOF), the hybrid Cu2O/Pd–Fe3O4 (1.87) catalyst exhibits better catalytic activity than Pd–Fe3O4 (0.69) because of the electron transfer across the metal-oxide interface (Table 1, entries 3 and 6). The optimal conditions for the reaction are the use of DMSO as the reaction media and NaOAc as the base, in the presence of 5.0 mol% of the Cu2O/Pd–Fe3O4 catalyst at 140 °C (Table 1, entry 7). Conversion is almost unchanged when time is decreased to 9 h (Table 1, entry 8). As expected, the conversion is lower (76%) when a short reaction time (4.5 h) and a smaller amount of catalyst (Pd base: 2.5 mol%), respectively, are used (Table 2, entries 9 and 10). In the same condition with entry 9, we checked the catalytic activity of Pd/charcoal (69%), Fe3O4/charcoal (0%) and Cu2O NPs (0%) which is previously reported heterogeneous catalyst by our group27,28 (Table 1, entries 11–13) and this catalyst showed less activity than Cu2O/Pd–Fe3O4, meaning that hybrid catalysts could enhance catalytic activity because of synergetic effect. Furthermore, the C–H arylation reaction was not progressed by only Fe3O4 and Cu2O nano catalyst. The Cu2O/Pd–Fe3O4 catalyst was reclaimed after the reaction using a magnet, and the separated catalysts were used for the reaction at least four further times. A conversion of >70% is maintained during recycling. In the Pd and Cu leaching tests, the hot filtered solution after the catalytic reaction was analyzed by ICP-AES, but the Pd and Cu contents of the solution, measured to be 7.77 ppm and 0.19 ppm, respectively, are too small to confirm the leaching degree. We conclude that the high catalytic activity and stability of the composites is confirmed through the recycling and leaching tests.
Table 1 C–H arylation of 1-butyl-4-nitro-1H-imidazolesa

|
Entry |
Catalyst |
Temp. (°C) |
Time (h) |
Base |
Solvent |
Conv.a (%) |
Reaction condition: Cu2O/Pd–Fe3O4 catalyst (Pd base: 5.0 mol%), 1-butyl-4-nitro-1H-imidazole (0.5 mmol), iodobenzene (0.55 mmol), base (1.0 mmol), solvent (3.0 mL). a Determined by using 1H-NMR spectroscopy. b Iodobenzene (1.0 mmol), NaOAc (2.0 mmol) and DMSO (5 mL) were used. c 2.5 mol% of catalyst was used. |
1 |
Pd–Fe3O4 |
130 |
18 |
NaOAc |
Toluene |
Trace |
2 |
Pd–Fe3O4 |
130 |
18 |
NaOAc |
DMA |
45 |
3 |
Pd–Fe3O4 |
130 |
18 |
NaOAc |
DMSO |
62 |
4 |
Pd–Fe3O4 |
130 |
18 |
LiOAc |
DMSO |
59 |
5 |
Pd–Fe3O4 |
130 |
18 |
Cs2CO3 |
DMSO |
N.D. |
6 |
Cu2O/Pd–Fe3O4 |
130 |
18 |
NaOAc |
DMSO |
73 |
7 |
Cu2O/Pd–Fe3O4 |
140 |
18 |
NaOAc |
DMSO |
85b |
8 |
Cu2O/Pd–Fe3O4 |
140 |
9 |
NaOAc |
DMSO |
84b |
9 |
Cu2O/Pd–Fe3O4 |
140 |
4.5 |
NaOAc |
DMSO |
76b |
10 |
Cu2O/Pd–Fe3O4 |
140 |
9 |
NaOAc |
DMSO |
76b,c |
11 |
Pd/charcoal |
140 |
4.5 |
NaOAc |
DMSO |
69b |
12 |
Fe3O4/charcoal |
140 |
4.5 |
NaOAc |
DMSO |
0b |
13 |
Cu2O |
140 |
4.5 |
NaOAc |
DMSO |
0b |
Reaction condition: Cu2O/Pd–Fe3O4 catalyst (Pd base: 5.0 mol%), 1-butyl-4-nitro-1H-imidazole (0.5 mmol), iodobenzene (1.0 mmol), NaOAc (2.0 mmol), DMSO (5.0 ml). |
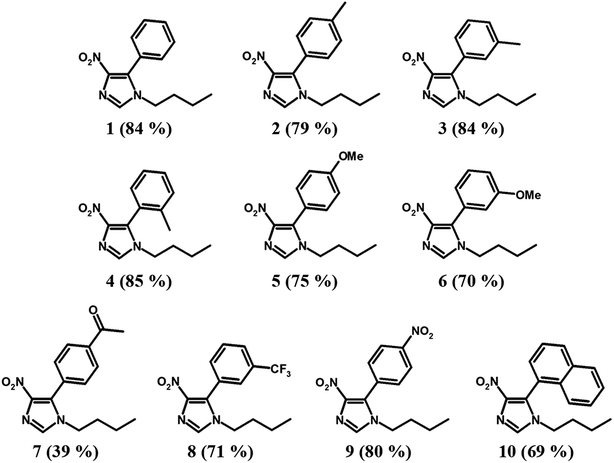 |
Substrate effects in the C–H arylations
The optimized reaction conditions using the Cu2O/Pd–Fe3O4 catalyst were applied to various substituted aryl iodides with good conversion, as shown in Table 2. In our catalytic system, substrates with electron-donating substituents, such as Me and OMe, as well as sterically hindered aryl halides, are readily coupled with 4-nitroimidazoles in good conversion (Table 2, entries 2–6). Moreover, reactions with electron-deficient substrates, such as those containing CF3, NO2, and naphthalene functional groups, proceed readily with high reactivity. The exception to this trend is substrates containing the COMe group (Table 2, entries 7–10).
Conclusion
In conclusion, we successfully developed a one-pot synthesis of Cu2O/Pd–Fe3O4 hybrid nanocomposites through the controlled thermal decomposition of Fe(CO)5 and reduction of Pd(OAc)2 and Cu(acac)2. The morphology of the Cu2O/Pd–Fe3O4 nanocomposites was affected by the Pd precursor and amount of reducing agent used during the synthesis. The synthesized Cu2O/Pd–Fe3O4 hybrid catalyst showed high catalytic activity in the C–H arylation of 4-nitroimidazoles. The same concept could be applied to other multi-metallic NP systems, making it possible to tune NP catalysis for many different chemical reactions.
Acknowledgements
This research was supported by Basic Science Research Program through the National Research Foundation of Korea (NRF) funded by the Ministry of Science, ICT & Future Planning (NRF-2015R1D1A1A02060684 and NRF-2013R1A1A2012960) and GCRC-SOP (No.2011-0030013). K. H. P thanks to the TJ Park Junior Faculty Fellowship and LG Yonam Foundation.
References
- H. Woo, J. C. Park, S. Park and K. H. Park, Nanoscale, 2015, 7, 8356–8360 RSC.
- J. Shin, H. Kim and I. S. Lee, Chem. Commun., 2008, 44, 5553–5555 RSC.
- S. Chen, R. Si, E. Taylor, J. Janzen and J. Chen, J. Phys. Chem. C, 2012, 116, 12969–12976 CAS.
- Y. Jang, J. Chung, S. Kim, S. W. Jun, B. H. Kim, D. W. Lee, B. M. Kim and T. Hyeon, Phys. Chem. Chem. Phys., 2011, 13, 2512–2516 RSC.
- L. Kong, X. Lu, X. Bian, W. Zhang and C. Wang, ACS Appl. Mater. Interfaces, 2011, 3, 35–42 CAS.
- W. Yang, J. Salim, C. Ma, Z. Ma, C. Sun, J. Li, L. Chen and Y. Kim, Electrochem. Commun., 2013, 28, 13–16 CrossRef CAS.
- R. K. Sharma, Y. Monga, A. Puri and G. Gaba, Green Chem., 2013, 15, 2800–2809 RSC.
- N. Y. Garces, L. Wang, L. Bai, N. C. Giles, L. E. Halliburton and G. Cantwell, Appl. Phys. Lett., 2002, 81, 622–624 CrossRef CAS.
- T. S. Herng, S. P. Lau, S. F. Yu, H. Y. Yang, L. Wang, M. Tanemura and J. S. Chen, Appl. Phys. Lett., 2007, 90, 032509 CrossRef.
- S. A. Wolf, D. D. Awschalom, R. A. Buhrman, J. M. Daughton, S. V. Molnar, M. L. Roukes, A. Y. Chtchelkanova and D. M. Treger, Science, 2001, 294, 1488–1495 CrossRef CAS PubMed.
- H. Woo, D. Kim, J. C. Park, J. W. Kim, S. Park, J. M. Lee and K. H. Park, J. Mater. Chem. A, 2015, 3, 20992–20998 CAS.
- M. S. Chen and D. W. Goodman, Science, 2004, 306, 252–255 CrossRef CAS PubMed.
- J. Zheng, Y. Dong, W. Wang, Y. Ma, J. Hu, X. Chen and X. Chen, Nanoscale, 2013, 5, 4894–4901 RSC.
- T. Brückl, R. D. Baxter, Y. Ishihara and P. S. Baran, Acc. Chem. Res., 2012, 45, 826–839 CrossRef PubMed.
- N. Kuhl, M. N. Hopkinson, J. Wencel-Delord and F. Glorius, Angew. Chem., Int. Ed., 2012, 51, 10236–10254 CrossRef CAS PubMed.
- N. Ghavtadze, F. S. Melkonyan, A. Gulevich, C. Huang and V. Gevorgyan, Nat. Chem., 2014, 6, 122–125 CrossRef CAS PubMed.
- P. B. Arockiam, C. Bruneau and P. H. Dixneuf, Chem. Rev., 2012, 112, 5879–5918 CrossRef CAS PubMed.
- L. Caron, L. C. Campeau and K. Fagnou, Org. Lett., 2008, 10, 4533–4536 CrossRef CAS PubMed.
- P. Guo, J. M. Joo, S. Rakshit and D. Sames, J. Am. Chem. Soc., 2011, 133, 16338–16341 CrossRef CAS PubMed.
- V. O. Iaroshenko, A. Gevorgyan, O. Davydova, A. Villinger and P. Langer, J. Org. Chem., 2014, 79, 2906–2915 CrossRef CAS PubMed.
- H. Jung, S. Bae, H.-L. Jang and J. M. Joo, Bull. Korean Chem. Soc., 2014, 35, 3009–3014 CrossRef CAS.
- Q. Q. Xiong, J. P. Tu, Y. Lu, J. Chen, Y. X. Yu, Y. Q. Qiao, X. L. Wang and C. D. Gu, J. Phys. Chem. C, 2012, 116, 6495–6502 CAS.
- B. L. Gustafson and P. S. Wehner, Appl. Surf. Sci., 1991, 52, 261–270 CrossRef CAS.
- V. Chandra, J. Park, Y. Chun, J. W. Lee, I.-C. Hwang and K. S. Kim, ACS Nano, 2010, 4, 3979–3986 CrossRef CAS PubMed.
- X. Huang, H. Zhang, C. Guo, Z. Zhou and N. Zheng, Angew. Chem., Int. Ed., 2009, 48, 4808–4812 CrossRef CAS PubMed.
- Y. Wang, S.-I. Choi, X. Zhao, S. Xie, H.-C. Peng, M. Chi, C. Z. Huang and Y. Xia, Adv. Funct. Mater., 2014, 24, 131–139 CrossRef CAS.
- H. Woo, K. Lee, J. C. Park and K. H. Park, New J. Chem., 2014, 38, 5626–5632 RSC.
- J. Y. Kim, J. C. Park, A. Kim, A. Y. Kim, H. J. Lee, H. Song and K. H. Park, Eur. J. Inorg. Chem., 2009, 2009, 4219–4223 CrossRef.
Footnote |
† Electronic supplementary information (ESI) available. See DOI: 10.1039/c6ra05068a |
|
This journal is © The Royal Society of Chemistry 2016 |
Click here to see how this site uses Cookies. View our privacy policy here.