DOI:
10.1039/C6RA04943E
(Paper)
RSC Adv., 2016,
6, 48737-48744
Conversion of bis(2-hydroxyethylene terephthalate) into 1,4-cyclohexanedimethanol by selective hydrogenation using RuPtSn/Al2O3
Received
24th February 2016
, Accepted 12th May 2016
First published on 12th May 2016
Abstract
1,4-Cyclohexanedimethanol (CHDM) is a highly valued and widely used monomer in the polymer industry. Bis(2-hydroxyethylene terephthalate) (BHET), the product of glycolysis of waste PET, is an excellent raw material for the preparation of CHDM. Herein, a series of monometallic, bimetallic and trimetallic supported catalysts were prepared for the one-pot conversion of BHET into CHDM by the impregnation method and good performance was found over trimetallic RuPtSn/Al2O3 catalysts containing various active sites to catalyze the hydrogenation of the phenyl and carbonyl groups. The influences of various reaction parameters including temperature, pressure and time on the hydrogenation reaction were studied, and 100% conversion and 87.1% yield of CHDM were obtained with the trimetallic supported catalyst with Ru/Sn 1.5. Moreover, through the comparison between various methods for the preparation of CHDM, the conversion of BHET into CHDM by the one-pot method is considered one of the most competitive methods.
1. Introduction
1,4-Cyclohexanedimethanol (CHDM) has been extensively used in the polymer industry for modifying fibers and polyesters to produce amorphous copolyesters with excellent chemical resistance and physical strength.1,2 Currently, CHDM is produced from dimethyl terephthalate (DMT) by a two-step process in industry. The first step is the hydrogenation of the phenyl group by a Pd-based catalyst at a temperature range of 160–180 °C and a H2 pressure range of 30–48 MPa,3,4 which converts DMT into dimethyl cyclohexane dicarboxylates (DMCD). The second step is the hydrogenation of the carboxylic group to the corresponding hydroxyl group by a conventional Cu–Cr catalyst at 200 °C with 4 MPa H2,5,6 which converts intermediate DMCD into CHDM. However, the two steps require different reactors and increase the operational complexity and production costs. Besides, some other methods have also been reported for the production of CHDM in recent years. Zhu et al.7 reported that terephthalic acid (TPA) could be converted into CHDM with high yield in the presence of a bimetallic Ru–Sn supported catalyst that was prepared by a co-impregnation method. Yoshinori et al.8 prepared the carbon-supported RuSnPt catalyst which used activated carbon treated by nitric acid as the support for the conversion of 1,4-cyclohexanedicarboxylic acid (CHDA) into CHDM. The results showed that the incorporation of Pt could depress the loss of Sn and accelerate the reaction rate.
However, the raw materials used for the production of CHDM are all derived from the conventional petrochemical industry. Due to limited petroleum reserves, it is significant to find a substitution which can be derived from waste materials for the production of CHDM. In our previous work,9 CHDM could be obtained from BHET by a two-step process. Bis(2-hydroxyethylene terephthalate) (BHET), which is the monomer of the poly(ethylene terephthalate) (PET), could be easily obtained from the glycolysis of waste PET.10 The glycolysis reaction is catalyzed by zinc chloride, sodium carbonate, urea, sulfated cobalt oxide (SO42−/Co3O4)11–15 and ionic liquids16–20 with an excess of ethylene glycol under 180–240 °C at atmospheric pressure. As known, noble metals and some transition metals such as Ru, Rh, Pt21–23 and Ni24 are widely used as catalysts for the hydrogenation of phenyl group at mild conditions. Conventional Cu-based catalysts are used for the hydrogenation of esters and carboxylic acids into corresponding alcohols.25,26 In the two-step process, the hydrogenation reaction is catalyzed by Pd/C and Cu–Cr catalysts. The conversion of BHET and final yield of CHDM are 100% and 78.0% respectively, which indicates that BHET is an excellent raw material for the preparation of CHDM. But the pollution of Cr element has drawn much attention owing to environmentally harmful effect and strict reaction condition. Moreover, it is difficult to separate the intermediate product for further hydrogenation.
In this paper, an one-pot conversion process of BHET into CHDM by selective hydrogenation is introduced and the reaction path-way is shown in Scheme 1. The phenyl group and the carbonyl group of BHET are hydrogenated simultaneously in a reactor by multi-functional catalyst that contains different active sites. Thomas et al.5,27,28 reported that a series of bimetallic and trimetallic catalysts such as Ru5Pt, Ru12Cu4 and Ru5PtSn were prepared for the one-step conversion of DMT into CHDM at mild reaction conditions, but the yield was too low for use. As new efficient catalysts, Ru–Sn supported catalysts have revealed good performance in the hydrogenation of esters and carboxylic acids, in which Sn could activate the carboxylic group of esters and carboxylic acids as Lewis acid and increase the selectivity of alcohol, as Ru is beneficial for the activation of hydrogen and the hydrogenation of phenyl group. Since the incorporation of Pt could depress the loss of Sn and accelerate the reaction rate, a series of monometallic, bimetallic and trimetallic supported catalysts were prepared by the impregnation method for one-pot conversion of BHET into CHDM. Moreover, influences of various reaction parameters including temperature, pressure and time on the hydrogenation reaction were studied. Meanwhile, the supported catalysts were characterized by temperature programmed reduction and X-ray diffraction to investigate their effects on the reaction.
 |
| Scheme 1 Conversion of BHET into CHDM by one-pot hydrogenation process. | |
2. Experimental
2.1 Materials
BHET (≥99%) was obtained by the degradation of waste PET in our laboratory as reported previously.29 Sodium borohydride (AR) and sodium hydroxide (AR) were obtained from Sinopharm Chemical Reagent Co., Ltd, China. Stannous chloride (99.9%) and γ-Al2O3 were obtained from Aladdin Industrial Co., Ltd, China. Ruthenium(III) chloride hydrate (99.9%) and chloroplatinic acid hexahydrate (99.9%) were obtained from J&K Scientific Ltd, China. The materials were used without any further purification.
2.2 Preparation of catalysts
The catalysts were synthesized according to the procedures described in the literature with slight modification.30 The supported catalysts were prepared by a conventional impregnation method. The γ-Al2O3 support was calcined at 500 °C under air before use. A certain amount of three metal precursor salts, RuCl3·nH2O, SnCl2·2H2O and H2PtCl6·6H2O were dissolved by deionized water in a beaker to obtain Sn and Pt contents of 3.0 and 1.5 wt% by the carrier respectively. The acquired amount of pretreated γ-Al2O3 support was added and the mixture was stirred for 4 h, then the paste was obtained after aging at room temperature for 24 h. The paste was dried at 80 °C in a vacuum oven for 12 h and then calcined at 500 °C under air for 4 h. Then, an excessive amount of NaBH4 was dissolved in NaOH solution with pH value of 9 and the catalyst samples were reduced. After the reduction, the catalyst samples were washed several times by deionized water until pH value reached 7. Finally, the samples were dried under Ar at 80 °C for 10 h. Besides, a series of catalysts including monometallic and bimetallic as well as trimetallic samples with different Ru contents were prepared by the same method. Herein, all the catalysts were signed as RuxPtySnz, in which x, y and z represented the molar ratio of Ru, Pt and Sn.
2.3 Characterization
The property of reducibility and hydrogen absorption of catalysts were investigated by temperature programmed reduction (TPR) with an AutoChem II 2920 instrument. The XRD patterns of the catalysts were determined by a Bruker D8-Advance X-ray powder diffractometer with Cu Kα radiation (λ = 0.154 nm) at 40 kV and 30 mA with 2θ angle range of 20–75° and a scanning rate of 10° min−1. The morphology of the catalysts were observed using a TEM (JEM 2100-F) operated at 200 keV. XPS data were recorded using an ESCALAB 250Xi with an Al Kα radiation operated at a pass energy of 20.0 eV. The catalysts before and after use were dissolved in hot aqua regia and the Sn content was determined by inductively coupled plasma optical emission spectrometer (ICPE-9000, Shimadzu).
2.4 Reaction
All hydrogenation reactions were carried out in a stainless steel reactor equipped with magnetic stirring. In a typical experiment, the reactor was charged with 1.0 g BHET as substrate and 0.1 g catalyst. The reactor was purged with H2 three times to remove air and then pressurized H2 to the pressure of 5 MPa. Subsequently, the reactor was heated to 170 °C under stirring of 500 rpm. After 2 h, the temperature was raised to 260 °C and kept for 6 h.
After reaction, the reaction mixture was dissolved in methanol and centrifuged. Then the undissolved substance was removed to get the liquid sample. The collected catalyst was washed with ethanol to remove the residues on the surface and dried at 80 °C for 12 h. The amount of BHET was adjusted to keep the ratio of the catalyst to BHET content. The liquid sample was analyzed by gas chromatography on a GC-2014 instrument (Shimadzu Corporation) equipped with a HP-5 chromatographic column and a flame ionization detector (FID). The initial oven temperature was set at 40 °C for 2 min, and programmed to 200 °C at 15 °C min−1 and held at 200 °C for 2 min, then the oven temperature was programmed to 260 °C at 20 °C min−1 and held for 3 min. FID temperature was 280 °C and inlet temperature was 270 °C. The amount of the product was determined by the external standard method. The conversion and yield of products were calculated by eqn (1) and (2) as follows:
|
 | (1) |
|
 | (2) |
3. Results and discussion
3.1 The characterization of catalysts
TPR profiles of supported catalysts with different metal elements are presented in Fig. 1. For the Ru/Al2O3 (Fig. 1e) catalyst, the consumption peak around 150 °C can be ascribed to the reduction of Ru specie, which is in accordance with results obtained in other studies.31 For the Sn/Al2O3 (Fig. 1d) catalyst, the TPR profile shows two consumption peaks between 400 °C and 600 °C, which indicates that there are two different interactions between the reduction of Sn species and the alumina support in the catalyst.32 Similarly, it can be seen two consumption peaks between 80 °C and 200 °C for the Pt/Al2O3 (Fig. 1c) catalyst, which may correspond to the presence of free Pt and the platinum oxide. Three consumption peaks are observed for the Ru4PtSn4/Al2O3 (Fig. 1b) and Ru6PtSn4/Al2O3 (Fig. 1a) catalysts. The temperature of the first and second peaks are mainly between 60 °C and 200 °C, and the last one that is not distinct is in the temperature range of 300–400 °C. Compared with Ru4PtSn4/Al2O3 catalyst, the maximum reduction temperature of the first and second peaks that may be ascribed to the Pt metal interacted with Ru shift gradually lower for the Ru6PtSn4/Al2O3 (Fig. 1a) catalyst. This phenomenon may be closely related to the hydrogen spillover on Ru metal surface.33 The high temperature reduction peak between 300 and 400 °C is ascribed to the formation of PtSn alloy, which is also reported in literature.34
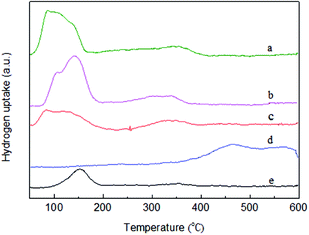 |
| Fig. 1 H2-TPR profiles of various supported monometallic or trimetallic catalysts (a) Ru6PtSn4/Al2O3; (b) Ru4PtSn4/Al2O3; (c) Pt/Al2O3; (d) Sn/Al2O3; (e) Ru/Al2O3. | |
The X-ray powder diffraction patterns of the monometallic and trimetallic supported catalysts are shown in Fig. 2. The Al2O3 (Fig. 2f) sample exhibits the characteristic diffraction peaks at 2θ of 32.8°, 36.8°, 39.5°, 45.5° and 67.2°, which can also be observed in other samples. This evidence indicates that the initial support nature is preserved after some treatments during the preparation of the catalysts. For the Ru/Al2O3 (Fig. 2e) catalyst, the diffraction peaks at 2θ of 28.0°, 34.9° and 54.1° are attributed to RuO2 phase. However, Ru peaks are not detected which may be caused by the oxidation in the air. The diffraction peaks of SnO2 at 2θ of 26.9°, 34.1° and 52.2° are prominent and sharp for the Sn/Al2O3 (Fig. 2c) catalyst, which is ascribed to the formation of large particles. It is due to the strong interaction between SnO2 and the support which leads to the bad distribution. The diffraction of Pt and PtO2 is not distinct due to the low load and the shield of the support for the Pt/Al2O3 (Fig. 2d) catalyst. The diffraction peaks of RuO2 and SnO2 become gradually broad and less prominent with the addition of Pt for the trimetallic samples, due to the decrease of the particle size.30 As the Ru content increases, there is no obvious change observed for the Ru6PtSn4/Al2O3 (a) catalyst, which reflects that the Ru content does not have distinct effect on the dispersion of the metal particles on the support.
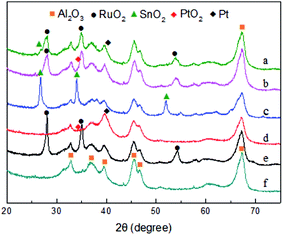 |
| Fig. 2 XRD patterns of various supported monometallic or trimetallic catalysts (a) Ru6PtSn4/Al2O3; (b) Ru4PtSn4/Al2O3; (c) Sn/Al2O3; (d) Pt/Al2O3; (e) Ru/Al2O3; (f) Al2O3. | |
Similarly, TEM analysis was also conducted for Ru6PtSn4/Al2O3 to have a better understanding of the morphological feature. In Fig. 3, uniform dispersion of the metal particles can be observed on the Al2O3 support. However, special morphology is not observed, because the support used in the experiments is amorphous. Well dispersed metal particles on the support are considered as active sites for the hydrogenation of BHET into CHDM.
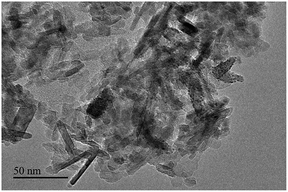 |
| Fig. 3 TEM image of Ru6PtSn4/Al2O3 catalyst. | |
The XPS measurements were carried out on the Ru6PtSn4/Al2O3 catalyst and the results were shown in Fig. 4. For the Ru 3d5/2 spectra of the catalyst, the binding energy at 280.1 eV can be ascribed to the Ru(0) species, but the result is not very clear because the peaks of Ru 3d and C 1s overlap each other.7 The binding energy of the Sn 3d5/2 XPS spectra at 487.2 eV is corresponding to Sn(II) and/or Sn(IV). However, it is difficult to distinguish the peaks of Sn(II) and Sn(IV) due to a very small difference in the binding energy of both oxidation states.8 The binding energy at 486.1 eV is consistent with metallic Sn, which confirms the exist of PtSn alloy.35 For the Pt 4f7/2 spectra of the catalyst, the binding energy at 71.8 and 73.5 eV are attributed to Pt(0) and Pt(IV) respectively, which is also reported by others.36 According to these results, the surface of the catalyst is composed of reduced state and oxidized state, which is in agreement with the TPR and XRD results.
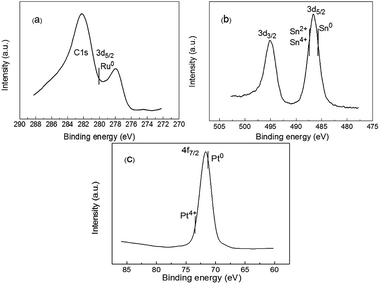 |
| Fig. 4 XPS spectra of Ru6PtSn4/Al2O3 catalyst (a) Ru 3d spectra; (b) Sn 3d spectra; (c) Pt 4f spectra. | |
3.2 Influence of catalyst on the conversion of BHET into CHDM
The conversion of BHET into CHDM was obtained successfully by the hydrogenation of the phenyl group to cyclohexane and the carbonyl group corresponding to hydroxyl group. As a diol, hydrogenolysis,4 oligomerization and polymerization37 may also occur in the present reaction system at high temperature and hydrogen pressure. As a result, the conversion of BHET not only depends on the hydrogenation activity of catalyst, but also depends on the side reactions. However, the selectivity of CHDM shows quite distinct difference with different catalysts. In order to obtain the efficient catalyst, a series of monometallic, bimetallic and trimetallic supported catalysts were prepared by the impregnation method for the conversion of BHET into CHDM.
3.2.1 Influence of various active metal. The selective hydrogenation of BHET into CHDM was carried out using various metal catalysts to determine the optimal metal component of catalyst. The main by-products are shown in Scheme 2 and the catalytic results are shown in Table 1. As it can be seen, the conversion of BHET is above 90% for the supported monometallic, bimetallic and trimetallic samples, while the selectivity of CHDM depends on the metal component of catalyst. As shown, the main by-product for Ru and Pt catalysts is BHCD, which is the product of the hydrogenation of the phenyl group. It indicates that Ru and Pt metal are responsible for the hydrogenation of the phenyl group.
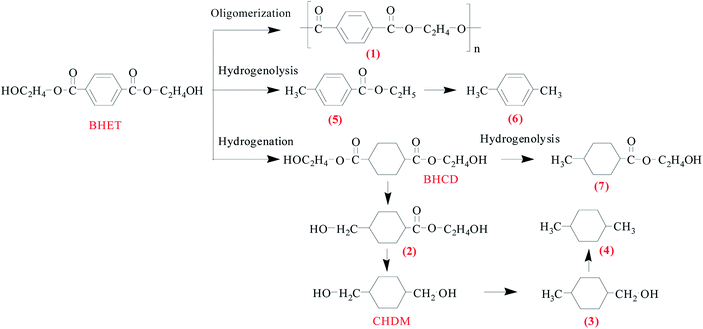 |
| Scheme 2 The possible reaction path-way for the conversion of BHET into CHDM. Some by-products are trace amount and they are ignored. | |
Table 1 Influence of various metal catalysts on the selective hydrogenationa
Catalyst |
Conversion of BHET (%) |
Yield of CHDM (%) |
Main byproducts |
Reaction conditions: 1.0 g BHET, 0.1 g catalyst. H2 5 MPa, 500 rpm, initially at 170 °C for 2 h, then 260 °C for 6 h. |
Ru/Al2O3 |
97.2 |
— |
BHCD (82.7%), 5 + 6 (12.8%) |
Pt/Al2O3 |
95 |
— |
BHCD (69.4%), 5 + 6 (18.1%), 2 (5.7%) |
Sn/Al2O3 |
94.6 |
— |
1 (94.6%) |
Ru4Pt/Al2O3 |
99.7 |
— |
BHCD (74.5%), 5 + 6 (13.5%), 3 + 4 (9.6%) |
Ru4Sn4/Al2O3 |
99.6 |
14.7 |
5 + 6 (70.6%), 2 (7.3%), 3 + 4 (5.6%) |
PtSn4/Al2O3 |
99.8 |
5.3 |
5 + 6 (79.2%), 2 (10.7%) |
Ru4PtSn4/Al2O3 |
99.3 |
78.4 |
5 + 6 (13.3%), 3 + 4 (4.7%) |
The Sn catalyst shows little activity for the hydrogenation of BHET because no other product was detected except for the peaks of methanol and ethylene glycol in the gas chromatogram. It is attributed to the oligomerization and polymerization of BHET as the corresponding products have not dissolved in methanol.
The incorporation of Sn to Ru- and Pt-catalysts can achieve the conversion of BHET into CHDM, although the selectivity is still lower. As known, Sn metal plays a crucial role in the activation of the carbonyl group, but would restrain the hydrogenation capability of Ru catalyst,38 which leads to the appearance of by-products 5 and 6. The hydrogenolysis of ester group is also cause of the appearance of by-products 5 and 6. The reason for the poor performance of the bimetallic PtSn catalyst can be attributed to the formation of Pt–Sn alloy, which leads to the decrease of the hydrogenation selectivity and enhances of the hydrogenolysis. For the RuPt catalyst, the main product is BHCD, along with some by-products generated from hydrogenolysis of ester group.
When Pt metal is added to the bimetallic RuSn catalyst, the ability of the hydrogenation of phenyl group is enhanced and the yield of CHDM increases obviously. It indicates that the synergistic effect among three metal elements in the catalyst has a positive effect on the selective hydrogenation of BHET into CHDM. The by-products 3 and 4 are formed by excessive hydrogenation of product. Moreover, the possible reaction path-way for the conversion of BHET into CHDM is shown in Scheme 2 according to the main by-products distribution.
3.2.2 Influence of the Ru content. In order to present the influence of the Ru content on the selective hydrogenation, a series of catalysts with various Ru/Sn ratio were prepared for the hydrogenation of BHET into CHDM, and the results are shown in Fig. 5. The conversion of BHET is high with no distinct change for all the trimetallic catalysts, whereas the yield of CHDM strongly depends on the composition of the catalysts. When the Ru content is low, the hydrogenation of the phenyl group is restrained and many by-products which mainly contain the phenyl group such as 5 and 6 are formed leading to the low selectivity of CHDM. With the increase of the Ru content, the yield of CHDM shows an increase from 53.5% to 87.1% simultaneously and the maximum is obtained when the atomic ratio of Ru/Sn is 1.5. Meanwhile, the byproducts 5 and 6 decrease gradually. However, the further addition of Ru leads to the decrease in the yield of CHDM. It is well known that the Ru metal is beneficial for the activation of hydrogen. When the Ru content increases, more activated hydrogen can be produced for the selective hydrogenation. But the excessive activated hydrogen can lead to the reduction of hydroxyl group, which results in further hydrogenation of CHDM into by-products such as 3 and 4. The results show that the appropriate Ru content in the supported trimetallic catalyst plays a crucial role in the selective hydrogenation of BHET into CHDM.
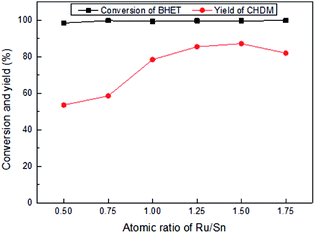 |
| Fig. 5 Influence of the Ru content on the selective hydrogenation. Reaction conditions: 1.0 g BHET, 0.1 g catalyst. H2 5 MPa, 500 rpm, initially at 170 °C for 2 h, then 260 °C for 6 h. | |
3.3 Influence of reaction condition on the conversion of BHET into CHDM
3.3.1 Influence of reaction temperature. Reaction temperature is shown to be a crucial parameter for the hydrogenation reaction. As known, the phenyl group is hydrogenated to cyclohexane easily compared with the carbonyl group to corresponding hydroxyl group. To verify the possibility of hydrogenating BHET into CHDM by single reaction temperature, the catalytic performance of Ru6PtSn4/Al2O3 is investigated as shown in Table 2. When the reaction is carried out at low temperature 170 °C, the main product is BHCD and the yield is 87.8% without CHDM. It means that the phenyl group is conserved to cyclohexane easily at this condition, while it is not feasible for the hydrogenation of the carbonyl group to corresponding alcohol. At the temperature 230 °C, CHDM can be obtained with low yield of 47.2%. The main by-products are 2 and 5 which increase obviously. As the temperature reaches to 260 °C, the yield of CHDM is only 28.5%. The main by-products 5 and 6 are caused by the hydrogenolysis of ester group, along with little 3 and 4 from the excessive hydrogenation. The above reaction results indicate that it is difficult for the hydrogenation of BHET into CHDM in excellent yield through single temperature process.
Table 2 Influence of single reaction temperature on the selective hydrogenationa
Temperature (°C) |
Conversion of BHET (%) |
Yield of CHDM (%) |
Main by-products |
Reaction conditions: 1.0 g BHET, 0.1 g catalyst. H2 5 MPa, 500 rpm, 8 h. |
170 |
99.6 |
— |
BHCD (87.8%), 2 (5.6%) |
230 |
99.4 |
47.2 |
5 + 6 + 7 (35.2%), 2 (13.4%) |
260 |
99.7 |
28.5 |
5 + 6 (57.6%), 3 + 4 (7.6%) |
Fig. 6 shows the influence of reaction temperature on the conversion of BHET and yield of CHDM catalyzed by Ru6PtSn4/Al2O3 through a two-temperature process. For the first stage temperature, it shows that the yield of CHDM initially increases and then decreases with the raise of the reaction temperature. It is concluded that the first stage temperature is beneficial for the activation of the carbonyl group, because the by-products are mainly 5 and 6. For the second stage, the low temperature is not beneficial for the hydrogenation of the carbonyl group because of the appearance of by-product 2. The high temperature may be intensify the hydrogenolysis of ester group, which inhibits the main reaction of the conversion of BHET into CHDM. So the optimal reaction temperature is 170/260 °C for the hydrogenation of BHET into CHDM.
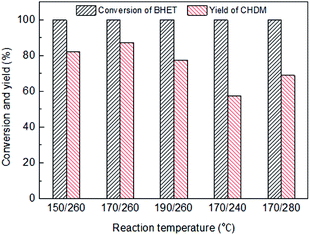 |
| Fig. 6 Influence of reaction temperature on the conversion of BHET and yield of CHDM. Reaction conditions: 1.0 g BHET, 0.1 g catalyst. H2 5 MPa, 500 rpm, initial time for 2 h, then for 6 h. | |
3.3.2 Influence of hydrogen pressure. The influence of hydrogen pressure on the conversion of BHET into CHDM is shown in Fig. 7. As shown, the hydrogen pressure plays an important role in the reaction. It may not only accelerate the reaction rate, but also impel the equilibrium to the desired direction. The hydrogenolysis of ester group is carried out more easily with low hydrogen pressure, which leads to the low selectivity of CHDM. With the increase of hydrogen pressure, the yield of CHDM increases simultaneously. It can be concluded that the yield of desired product is proportional to the hydrogen pressure in the range of 3 to 7 MPa. However, the high cost and safety problems might also arise due to the high pressure. As the yield of CHDM has not increased obviously when hydrogen pressure is above 5 MPa, 5 MPa is chosen as the optimal hydrogen pressure condition in consideration of economy and safety.
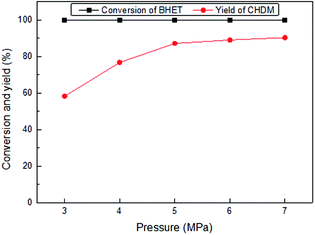 |
| Fig. 7 Influence of pressure on the conversion of BHET and yield of CHDM. Reaction conditions: 1.0 g BHET, 0.1 g catalyst. 500 rpm, initially at 170 °C for 2 h, then 260 °C for 6 h. | |
3.3.3 Influence of reaction time. Fig. 8 shows the influence of reaction time on the conversion of BHET and yield of CHDM. The conversion of BHET is high and close to 100%. The reason is that the hydrogenolysis and hydrogenation of BHET can occur simultaneously in the present reaction system at high temperature and hydrogen pressure. For the first stage, the yield of CHDM increases with the extension of reaction time. When the first stage reaction time is short, the hydrogenolysis of BHET can occur more easily which may lead to production of by-products 5 and 6. It indicates that the first stage reaction time may also play an important role on the activation of the carbonyl group. Conversely, with the increase of the second stage reaction time, the yield of CHDM decreases gradually. It may be caused by the excessive hydrogenation of CHDM which results in the formation of by-products 3 and 4. Compared with the hydrogenation of the phenyl group, it takes more reaction time for the carbonyl group to be hydrogenated to alcohol. It is not appropriate for the conversion of BHET into CHDM by prolonging the total reaction time without limit. As a result, the optimal reaction time is 2/6 h.
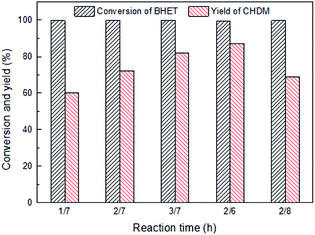 |
| Fig. 8 Influence of reaction time on the conversion of BHET and yield of CHDM. Reaction conditions: 1.0 g BHET, 0.1 g catalyst. H2 5 MPa, 500 rpm, initially at 170 °C, then 260 °C. | |
3.4 Recycling experiments
The catalyst after use was recovered to determine the reusability. Unfortunately, the results of the recycling experiments were not satisfactory. The main by-products were 5 and 6 while the targeted product CHDM was low. The Sn content of catalysts before and after use were characterized by ICP-OES. The results showed that the Sn content in the catalyst before use was 3.1%, which was almost in accordance with the theoretical value. However, the Sn content in the used catalyst decreased to 2.6%. It indicated that the amount of Sn elution was noteworthy. As reported, the Sn played an important role in the activation of the carboxylic group of esters and carboxylic acids, which was also easy to be eluted.31 The amount of Sn elution was so noticeable that it might lead to the low hydrogenation activity, which indicated that further improvement was needed to enhance the stability of the catalyst.
3.5 Comparison among various methods for the preparation of CHDM
For comparison, various methods for the preparation of CHDM are listed in Table 3. The raw materials for the preparation of CHDM are mainly DMT, TPA and BHET. DMT and TPA are all derived from the conventional petrochemical industry. However, petroleum reserve is limited. One-step conversion of DMT into CHDM at mild reaction conditions is obtained by nanoparticle catalysts, but the preparation of catalyst is difficult. Above all, the selectivity is low. Two-step conversion of DMT into CHDM can get high conversion and selectivity, and the catalysts used in the hydrogenation reaction can easily be obtained by conventional methods such as impregnation method and precipitation method. However, the procedure is complicated caused by the separation of the intermediate product before further hydrogenation. Being similar to DMT, one-step and two-step conversion of TPA into CHDM have same disadvantages. Besides, TPA may corrode the equipments, which makes it necessary to find new methods for the preparation of CHDM. BHET can easily be obtained from the glycolysis of waste PET, which is sustainable and environmental friendly. Compared with two-step conversion of BHET into CHDM, one-pot method not only can get the high conversion and selectivity, but is also simple. Overall consideration, the conversion of BHET to CHDM through one-pot method is more competitive.
Table 3 Comparison among various methods for the preparation of CHDM
Raw material |
Source |
Method |
Catalyst |
Procedure |
Conversion and selectivity |
References |
DMT |
Petrochemical industry |
One-step |
Noble metal |
Simple |
Low |
5 |
Two-step |
Noble metal & non-noble metal |
Complicated |
High |
39 |
TPA |
Petrochemical industry |
One-step |
Noble metal |
Simple |
Low |
40 |
Two step |
Noble metal & non-noble metal |
Complicated |
High |
41 |
BHET |
Waste PET |
One-pot |
Noble metal |
Simple |
High |
This work |
Two-step |
Noble metal & non-noble metal |
Complicated |
High |
9 |
4. Conclusions
By the impregnation method, a series of monometallic, bimetallic and trimetallic supported catalysts were prepared for the hydrogenation of BHET into CHDM. As a result, one-pot conversion of BHET derived from waste PET into CHDM by selective hydrogenation was obtained successfully, and good performance was found with supported trimetallic RuPtSn/Al2O3 catalysts. The results indicated that Ru was beneficial for the activation of hydrogen, and incorporation of Pt had both effects on the hydrogenation of the phenyl group as well as the decrease of metal particle size. The influences of various reaction parameters including temperature, pressure and time on the hydrogenation reaction were studied, and 100% conversion and 87.1% yield of CHDM were obtained with the trimetallic supported catalyst with Ru/Sn of 1.5. For the recycling experiments, the catalyst showed a poor reusability due to the leaching of Sn, which indicated that further improvement was needed to enhance the stability of the catalyst. Moreover, through the comparison between various methods for the preparation of CHDM, the conversion of BHET into CHDM by one-pot method is considered as one of the most competitive methods.
Acknowledgements
This research was supported financially by International S&T Cooperation Program of China (2014DFA61670), the National Natural Science Foundation of China (No. 91434203, No. 21336002, No. 21476234, No. 21276260, No. 21576269), Key Project of Natural Science Foundation of Beijing of China (No. 2131005) and CAS/SAFEA International Partnership Program for Creative Research Teams (20140491518).
Notes and references
- S. R. Turner, J. Polym. Sci., Part A: Polym. Chem., 2004, 42, 5847–5852 CrossRef CAS
. - H. J. Bang, H. Y. Kim, F. L. Jin and S. J. Park, J. Ind. Eng. Chem., 2011, 17, 805–810 CrossRef CAS
. - F. Z. Zhang, J. L. Chen, P. Chen, Z. Y. Sun and S. L. Xu, AIChE J., 2012, 58, 1853–1861 CrossRef CAS
. - Y. Q. Huang, Y. Ma, Y. W. Cheng, L. J. Wang and X. Li, Ind. Eng. Chem. Res., 2014, 53, 4604–4613 CrossRef CAS
. - R. Raja, T. Khimyak, J. M. Thomas, S. Hermans and B. F. G. Johnson, Angew. Chem., Int. Ed., 2001, 40, 4638–4642 CrossRef CAS
. - J. L. Chen, X. Liu and F. Z. Zhang, Chem. Eng. J., 2015, 259, 43–52 CrossRef CAS
. - Z. Q. Zhu, Z. H. Lu, B. Li and S. Z. Guo, Appl. Catal., A, 2006, 302, 208–214 CrossRef CAS
. - Y. Hara and K. Endou, Appl. Catal., A, 2003, 239, 181–195 CrossRef CAS
. - X. N. Guo, J. Y. Xin, X. M. Lu, B. Z. Ren and S. J. Zhang, RSC Adv., 2015, 5, 485–492 RSC
. - N. George and T. Kurian, Ind. Eng. Chem. Res., 2014, 53, 14185–14198 CrossRef CAS
. - N. D. Pingale, V. S. Palekar and S. R. Shukla, J. Appl. Polym. Sci., 2010, 115, 249–254 CrossRef CAS
. - N. D. Pingale and S. R. Shukla, Eur. Polym. J., 2008, 44, 4151–4156 CrossRef CAS
. - R. L. Fonseca, I. D. Ingunza, B. Rivas, S. Arnaiz and J. I. G. Ortiz, Polym. Degrad. Stab., 2010, 95, 1022–1028 CrossRef
. - Q. Wang, X. Q. Yao, S. F. Tang, X. M. Lu, X. P. Zhang and S. J. Zhang, Green Chem., 2012, 14, 2559–2566 RSC
. - M. L. Zhu, Z. X. Li, Q. Wang, X. Y. Zhou and X. M. Lu, Ind. Eng. Chem. Res., 2012, 51, 11659–11666 CrossRef CAS
. - H. Wang, Y. Q. Liu, Z. X. Li, X. P. Zhang, S. J. Zhang and Y. Q. Zhang, Eur. Polym. J., 2009, 45, 1535–1544 CrossRef CAS
. - H. Wang, Z. X. Li, Y. Q. Liu, X. P. Zhang and S. J. Zhang, Green Chem., 2009, 11, 1568–1575 RSC
. - H. Wang, R. Y. Yan, Z. X. Li, X. P. Zhang and S. J. Zhang, Catal. Commun., 2010, 11, 763–767 CrossRef CAS
. - Q. Wang, Y. R. Geng, X. M. Lu and S. J. Zhang, ACS Sustainable Chem. Eng., 2015, 3, 340–348 CrossRef CAS
. - Q. F. Yue, C. X. Wang, L. N. Zhang, Y. Ni and Y. X. Jin, Polym. Degrad. Stab., 2011, 96, 399–403 CrossRef CAS
. - S. K. Sharma, K. B. Sidhpuria and R. V. Jasra, J. Mol. Catal. A: Chem., 2011, 335, 65–70 CrossRef CAS
. - H. Duan, D. Wang, Y. Kou and Y. Li, Chem. Commun., 2013, 49, 303–305 RSC
. - L. J. Simon, J. G. Ommen, A. Jentys and J. A. Lercher, J. Catal., 2001, 201, 60–69 CrossRef CAS
. - Y. Li, L. Zhu, K. Yan, J. Zheng, B. H. Chen and W. Wang, Chem. Eng. J., 2013, 226, 166–170 CrossRef CAS
. - P. Kasinathan, D. W. Hwang, U. H. Lee, Y. K. Hwang and J.-S. Chang, Catal. Commun., 2013, 41, 17–20 CrossRef CAS
. - J. L. Gong, H. R. Yue, Y. J. Zhao, S. Zhao, L. Zhao, J. Lu, S. P. Wang and X. B. Ma, J. Am. Chem. Soc., 2012, 134, 13922–13925 CrossRef CAS PubMed
. - A. B. Hungria, R. Raja, R. D. Adams, B. Captain, J. M. Thomas, P. A. Midgley, V. Golovko and B. F. G. Johnson, Angew. Chem., Int. Ed., 2006, 45, 4782–4785 CrossRef CAS PubMed
. - J. M. Thomas, B. F. G. Johnson, R. Raja, G. Sankar and P. A. Midgley, Acc. Chem. Res., 2003, 36, 20–30 CrossRef CAS PubMed
. - Y. R. Geng, T. Dong, P. T. Fang, X. M. Lu and S. J. Zhang, Polym. Degrad. Stab., 2015, 117, 30–36 CrossRef CAS
. - X. F. Li, Z. Y. Sun, J. L. Chen, Y. Zhu and F. Z. Zhang, Ind. Eng. Chem. Res., 2014, 53, 619–625 CrossRef CAS
. - D. A. Echeverri, J. M. Marin, G. M. Restrepo and L. A. Rios, Appl. Catal., A, 2009, 366, 342–347 CrossRef CAS
. - X. Liu, W. Z. Lang, L. L. Long and Y. J. Guo, Chem. Eng. J., 2014, 247, 183–192 CrossRef CAS
. - W. C. Conner and J. L. Falconer, Chem. Rev., 1995, 95, 759–788 CrossRef CAS
. - A. E. Aksoylu, M. M. A. Freitas and J. L. Figueiredo, Appl. Catal., A, 2000, 192, 29–42 CrossRef CAS
. - F. Coloma, A. E. Sepulveda and G. L. Fierro, Appl. Catal., A, 1996, 136, 231–248 CrossRef CAS
. - F. Coloma, A. E. Sepulveda and G. L. Fierro, Appl. Catal., A, 1996, 148, 63–80 CrossRef CAS
. - M. A. Alnaqbi, M. A. Mohsin, R. M. Busheer and Y. Haik, J. Appl. Polym. Sci., 2015, 132, 41666–41673 Search PubMed
. - B. A. Riguetto, C. E. Rodrigues, M. A. Morales, E. Payen and C. M. Marques, Appl. Catal., A, 2007, 318, 70–78 CrossRef CAS
. - M. Nobuyuki, I. Youji, M. Hiroya and T. Takeshi, JP 10-045645, 1998
. - H. Yoshinori, JP 2000-007596, 2000
. - I. Satoru, K. Masato and I. Shigeru, JP 2001-181223, 2001
.
|
This journal is © The Royal Society of Chemistry 2016 |