DOI:
10.1039/C6RA04515D
(Paper)
RSC Adv., 2016,
6, 48543-48549
Gold nanoparticles encapsulated in hierarchical porous polycarbazole: preparation and application in catalytic reduction†
Received
19th February 2016
, Accepted 6th May 2016
First published on 9th May 2016
Abstract
Porous organic polymers possessing high surface area and permanent porosity are emerging as a new kind of catalyst support. In this article, surface-functionalized gold nanoparticles (AuNPs) were presynthesized and further subjected to the FeCl3-promoted oxidative coupling copolymerization with 1,3,5-tri(9H-carbazol-9-yl)benzene to afford AuNPs encapsulated in porous polycarbazole (AuNPs@CPOP) under mild conditions. Through this preparative approach, the AuNPs do not occupy the cavities of the polymer, but instead are surrounded by grown porous polymer. Furthermore, transmission electron microscopy shows that the AuNPs are homogeneously embedded in the polymeric support with a narrow size distribution. The nitrogen sorption measurements show that AuNPs@CPOP possesses high porosity, the pore size distributions are hierarchical with micro-, meso-, and macropore size. The catalytic activities of the final porous composite materials are studied by the reduction of 4-nitrophenol to 4-aminophenol. The catalytic activity of AuNPs@CPOP is found to be outstanding with an activity factor of up to 17.57 s−1 g−1. The conjugated polycarbazole-encapsulated AuNPs have potential application in the fields of environmental chemistry and catalysis.
1. Introduction
Gold nanoparticles (AuNPs) have received considerable attention owing to their catalytic applications in oxidation of carbon monooxide,1 propylene epoxidation,2 alcohol oxidation,3 and fine chemistry.4 However, the high surface energy of AuNPs makes them aggregate to bulk materials and leads to loss of catalytic activity, which limits the application of AuNPs.5 In order to overcome the challenge of AuNPs agglomeration, one of the most effective strategies is to anchor or immobilize AuNPs in different supports. AuNPs dispersed in various supports have been reported, such as mesoporous silica,6 porous carbon,7 CeO2,8 TiO2,9 Fe3O4,10 graphene oxide,11 carbon nanotubes,12 and block copolymers.13
Porous organic polymers with low skeleton density, high surface area, and permanent porous structure are emerging as promising catalyst supports.14 During the process of heterogeneous catalysis, especially when the supports are hierarchically porous, the reactant molecules diffuse through different pores to contact with the active site of nanocatalyst.15 Therefore, the nanocatalysts supported in hierarchical porous polymer are also advantageous for catalytic applications.16 It is highly desirable but still challenging to immobilize nanocatalysts within the hierarchical porous network.17 Significant interest has been shown in porous organic polymers with highly cross-linked network structures when used as supports.18 Thomas and coworkers reported that a covalent triazine framework (CTF) as support for Pd nanoparticles enhance the metal support interaction and the Pd/CTF performs better activity and better stability, compared to Pd supported on activated carbon (AC) in the liquid phase glycerol oxidation.19 Chang and co-workers applied thiol–yne reaction to prepare a microporous polymer with sulfide and thiol groups, which was incorporated with AuNPs within its cavities and surface using an in situ reduction reaction of HAuCl4 with NaBH4. The AuNPs-loaded microporous polymer shows catalytic activity in the reduction of 4-nitrophenol.20
Our group has reported that carbazole-based oxidative coupling polymerization promoted by FeCl3 is cost-effective in preparation of porous conjugated polymer. The method is featured with high yield, cheap catalyst, room-temperature conditions. Furthermore, the catalyst can be removed from the final material by a simple purification process.21 Conjugated porous polycarbazoles possess high specific surface area, permanent porosity, and good physicochemical stability, which are beneficial for gas storage22 and separation,23 and heterogeneous catalysis.24 Herein, a new bifunctional ligand Cz-LA is designed to stabilize the AuNPs and furnish AuNPs–Cz-LA (Scheme 1), in which the surface of AuNPs is functionalized by carbazole groups. The FeCl3-promoted oxidative coupling copolymerization is applied to encapsulate AuNPs–Cz-LA in the network of porous polycarbazole. Through this approach, AuNPs/porous polymer composite (AuNPs@CPOP) is prepared by encapsulating presynthesized nanoparticles in porous polycarbazole. The AuNPs do not occupy the cavities of polymer, but instead are surrounded by grown porous polymer.25 The final materials (AuNPs@CPOP) were found to be high porous with hierarchical pore size distributions. The reduction of 4-nitrophenol to 4-aminophenol is chosen to test the catalytic activity of the porous composite materials (AuNPs@CPOP). AuNP-1@CPOP that contains AuNPs ranging from 3 to 6 nm exhibits an outstanding catalytic activity with activity factor of 17.57 s−1 g−1.
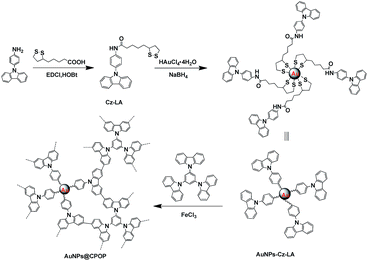 |
| Scheme 1 Synthesis routes to AuNPs@CPOP. | |
2. Experimental
2.1. Materials
Carbazole was purchased from J&K Scientific Co. Ltd. 1-Fluoro-4-nitrobenzene, NaH, α-lipoic acid, chloroauric acid (HAuCl4·4H2O), NaBH4, FeCl3, NH2NH2·H2O (85%), and Pd/C (5%, dry) were purchased from Sinopharm Chemical Reagent Co. Ltd. 1-Ethyl-3-(3-dimethylaminopropyl)carbodiimidehydrochloride (EDCI) and 1-hydroxybenzotrizole (HOBt) were purchased from Energy Chemical Co. Ltd. All the solvents were purchased from Beijing Chemical Works. All the commercially available chemicals were used as received without any purification. N-(4-Nitrophenyl)carbazole and N-(4-aminophenyl)carbazole were prepared according to the reported literature.26 1,3,5-Tri(9H-carbazol-9-yl)benzene (TCB) was prepared according to the previous report.23
2.2. Instrumental characterization
The 1H and 13C NMR spectra were performed on a Bruker DMX400 NMR spectrometer (Bruker, Germany). Mass spectrum was performed on a Microflex LRF MALDI-TOF mass spectrometer (Bruker, Germany). Gas sorption isotherms were measured with ASAP 2420 M+C (Micromeritics, USA) accelerated surface area and porosimetry analyzer at a set temperature. The sample was degassed for 12 h at 120 °C. The obtained adsorption–desorption isotherm was calculated to obtain Brunauer–Emmett–Teller (BET) specific surface area, pore volume, and pore size. The nonlocal density function theory (NLDFT) method is applied to calculate the pore size distribution (PSD) from the adsorption branch. TEM observation was performed on a Tecnai G2 20 S-TWIN microscope (FEI, USA) at an accelerating voltage of 200 kV. SEM observation was carried out on a S-4800 microscope (Hitachi Ltd., Japan) at an accelerating voltage of 6.0 kV associated with a Horiba energy dispersive X-ray (EDX) spectrometer. The actual loading capacity of gold element in porous polymer was measured by thermogravimetric analyses (TGA), which was conducted on the Pyris Diamond thermogravimetric/differential thermal analyzer (Perkin-Elmer Instruments Co. Ltd, USA) by heating the sample to 800 °C at a heating rate of 10 °C min−1 in the air atmosphere. Fourier transform infrared (FTIR) spectra were performed on a Spectrum One FTIR spectrometer (Perkin-Elmer Instruments Co. Ltd, USA) in KBr pellets in the range of 400–4000 cm−1. The UV-Vis absorption spectra were acquired with the UV-2600 spectrophotometer (Shimadzu, Japan).
2.3. Preparation
Synthesis of Cz-LA. To a round bottom flask (100 mL) were added α-lipoic acid (230 mg, 1.10 mmol) and a solution of EDCI (580 mg, 3.04 mmol) and HOBt (23 mg, 0.17 mmol) in trichloromethane (50 mL). After being stirred at room temperature for 10 m, a solution of N-(4-aminophenyl)carbazole (260 mg, 1.00 mmol) in trichloromethane (10 mL) was added to the reaction mixture. The resulting solution was allowed to stir for 12 h at room temperature until TLC showed that the reaction was finished. The resulting mixture was dried in vacuum to give dark yellow oil, which was diluted in trichloromethane (30 mL) and then washed with brine (3 × 50 mL). The separated organic layer was evaporated under vacuum and was purified by column chromatography with eluent (PE/EA = 1/3) to give the desired product as a light yellow solid (290 mg, yield 65%). 1H NMR (400 MHz, CDCl3): δ 8.15 (d, J = 8.0 Hz, 2H), 7.77 (d, J = 8.0 Hz, 2H), 7.55 (d, J = 8.0 Hz, 2H), 7.43–7.38 (m, 4H), 7.38–7.34 (m, 2H), 3.66–3.61 (m, 1H), 3.20–3.13 (m, 2H), 2.50–2.46 (m, 3H), 1.99–1.59 (m, 8H). 13C NMR (100 MHz, CDCl3): δ 171.6, 141.1, 137.3, 133.7, 128.1, 126.2, 123.2, 121.3, 120.4, 120.0, 109.7, 56.5, 38.6, 37.4, 34.7, 34.5, 29.0, 28.7, 25.4. MS (MALDI-TOF) m/z: calculated for C26H26N2OS2: 446.1 [M]; found: 446.1 [M], 469.1 [M + Na].
Synthesis of AuNPs–Cz-LA. The AuNPs–Cz-LA was prepared according to the modified literature procedure.27 Typically, to a round bottom flask (100 mL) were added Cz-LA (28 mg, 0.063 mmol), NaBH4 (230 mg, 6.22 mmol) in DMSO (20 mL), and then a solution of HAuCl4·4H2O (160 mg, 0.39 mmol) in DMSO (20 mL). The color of the solution was becoming dark. The resulting mixture was allowed to be stirred at room temperature for 24 h. Acetonitrile (40 mL) was added into the mixture and then the precipitate was collected by centrifugation, washed two times with acetonitrile (60 mL) and ethanol (60 mL) and dried under vacuum at 60 °C overnight to afford AuNP-1–Cz-LA. Using the same method, AuNP-2–Cz-LA was synthesized with the different amount of Cz-LA and NaBH4 shown in Table S2 (ESI†).
Preparation of AuNPs@CPOP. The preparation of AuNPs@CPOP was followed to the previous method with modification.23 Typically, to a two neck round bottom flask (100 mL) was added a mixture of ferric chloride (120 mg, 0.74 mmol) and anhydrous chloroform (5 mL). The solution of TCB (50 mg, 0.09 mmol) in 8 mL of anhydrous chloroform was added dropwise into the flask. Subsequently, a solution of AuNP-1–Cz-LA (15 mg) in anhydrous chloroform (15 mL) was added to the mixture. The resulting solution was stirred under nitrogen protection for 24 h at room temperature. Methanol (30 mL) was added and the resulting mixture was kept vigorously stirring for another hour. The precipitate was collected by filtration and being washed with chloroform, methanol, and water. The solid was extracted in a Soxhlet extractor with methanol for 1 d, and with tetrahydrofuran for another day. The desired product was collected and dried in vacuum oven at 80 °C overnight with a yield of 90%. The AuNP-2@CPOP was prepared from AuNP-2–Cz-LA according to the same method mentioned above.
Catalytic reduction of 4-nitrophenol to 4-aminophenol. The reduction of 4-nitrophenol to 4-aminophenol with excess NaBH4 was chosen to test the catalytic activity of AuNPs@CPOP at room temperature. Typically, 4-nitrophenol (200 μL, 0.79 M) and freshly prepared aqueous NaBH4 solution (3.0 mL, 0.13 M) were added in a quartz cuvette (1 cm of optical path, volume 4 mL). An aqueous suspension (3.0 mL) of AuNP-1@CPOP (1.4 mg) was ultrasonicated in advance. The suspension of AuNP-1@CPOP (500 μL) was injected into the quartz cuvette by micropipette. The UV-Vis spectra were measured to monitor the reaction progress by recording absorbance ranging from 250 to 550 nm with defined time intervals at room temperature. The test of catalytic activity of AuNP-2@CPOP was followed the same procedure.
3. Results and discussion
The synthesis routes to porous polycarbazole-encapsulated AuNPs (AuNPs@CPOP) are shown in Scheme 1. In this approach, a novel ligand Cz-LA is prepared from condensation reaction of N-(4-aminophenyl)carbazole and α-lipoic acid. Its chemical structure is further confirmed by 1H NMR, 13C NMR, and mass spectra. The Cz-LA possesses two functional groups, lipoic acid and carbazole. Due to high surface energy of AuNPs, AuNPs are usually stabilized by ligands with functional group such as thiol to obtain stable AuNPs of small size.28 The moiety of lipoic acid is reduced to –SH by NaBH4,29 while the gold resource HAuCl4·4H2O is simultaneously reduced to Au(0). The strong interaction between thiol and Au would protect the AuNPs from agglomeration to grow into larger particles. As a result, the preparation and surface functionalization of AuNPs are achieved in one step at mild condition, which is very effective and without introducing other impurity. With carbazole-bearing AuNPs in hand, TCB is chosen as monomer to couple with AuNPs–Cz-LA via carbazole-based oxidative coupling copolymerization at mild condition to afford AuNPs@CPOP, in which AuNPs do not occupy the pores of porous polycarbazole, but instead are surrounded by grown polycarbazole. AuNPs are embedded in the porous polymeric support by covalent bonds to enhance the interaction between metal nanoparticles and porous conjugated polycarbazole.
TEM image of AuNP-1–Cz-LA (Fig. 1a) indicates that AuNPs are stabilized by the Cz-LA with similar size and no agglomeration is observed. As shown in Fig. 1b, UV-Vis spectrum also confirms that the Cz-LA was immobilized on the surface of AuNPs. For AuNP-1–Cz-LA, besides the absorption bands of ligand Cz-LA at 245 and 295 nm, a new characteristic absorption band at about 520 nm is the localized surface plasmon resonance (LSPR) band of AuNPs.30 Fig. 1c displays the FTIR spectra of Cz-LA, AuNP-1–Cz-LA, and AuNP-1@CPOP. The characteristic peak at 2850 and 2921 cm−1 are CH and CH2 stretching of saturated alkyl group coming from lipoic acid and the peak at 1232 cm−1 is assigned to vibration of S–CH2. In addition, the bands at 1458 and 1504 cm−1 are attributed to vibration of the aromatic ring skeletons. The FTIR spectrum of AuNP-1@CPOP possesses the characteristic bands of lipoic acid and polycarbazoles, which further prove that the preparation of porous conjugated polycarbazole encapsulated AuNPs is feasible and effective.
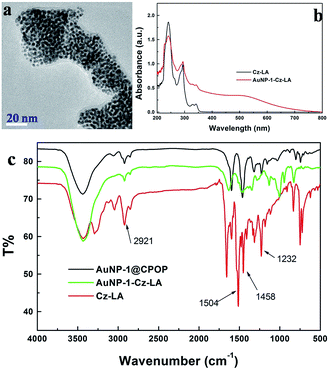 |
| Fig. 1 (a) TEM image of AuNP-1–Cz-LA. (b) UV-Vis spectra of Cz-LA and AuNP-1–Cz-LA. (c) FTIR spectra of Cz-LA, AuNP-1–Cz-LA, and AuNP-1@CPOP. | |
As shown in the SEM image of AuNP-1–Cz-LA in Fig. 2a, the material consists of irregular solid submicrometer particles with sizes from 50 to 200 nm. TEM image in Fig. 2b shows that AuNPs are embedded in the porous polycarbazole and homogeneously dispersed with the diameter of narrow size distribution ranging from 3 to 6 nm (Fig. S1, ESI†). Due to the synergy protection of Cz-LA and the porosity of the porous organic polymer, there is no obvious aggregation of AuNPs during the copolymerization of AuNP-1–Cz-LA and TCB. The presence of AuNPs in the polymeric support is further confirmed by EDX spectrum of AuNP-1@CPOP as shown in Fig. 2c. The characteristic peaks of Au element are located at about 2.2 and 9.7 keV, which is consistent with previous report.31 All the data reveal that the preparation of AuNPs encapsulated in porous conjugated polycarbazole by FeCl3-promoted oxidative coupling polymerization at room temperature is effective and porous conjugated polycarbazole can be used as a suitable support for AuNPs. The actual loading capacity of Au was investigated by TGA in the presence of air with a heating rate of 10 °C min−1 to 800 °C. The loading capacity of Au in AuNP-1@CPOP is 10.5 wt% (Fig. S2, ESI†). Meanwhile, AuNP-1@CPOP exhibits good thermal stability and ∼5% mass loss at about 365 °C in the air atmosphere.
 |
| Fig. 2 (a) SEM image of AuNP-1@CPOP. (b) TEM image of AuNP-1@CPOP. (c) Typical EDX spectrum of AuNP-1@CPOP. | |
The synthesis of AuNP-2–Cz-LA with bigger particle size is following the same method as to AuNP-1–Cz-LA but tuning the amounts of Cz-LA and NaBH4. Similarly, AuNP-2@CPOP was prepared from AuNP-2–Cz-LA and TCB via carbazole-based oxidative coupling copolymerization. The size of AuNPs is mainly at 6.5 ± 1.5 nm, TEM images of AuNP-2–Cz-LA and AuNP-2@CPOP with size distribution of AuNPs are shown in Fig. S3 (ESI†).
To investigate the porosity parameters of AuNPs@CPOP, nitrogen is used as the sorbate molecule to perform sorption analysis. Nitrogen adsorption–desorption isotherms at 77 K are shown in Fig. 3 and S4 (in ESI†). According to the IUPAC classification, both AuNPs@CPOP exhibit a combination of type I and II nitrogen sorption isotherms. The obtained porous materials show a rapid uptake at low relative pressure (0–0.10), which is characteristic of a permanent microporous nature. A hysteresis loop at entire relative pressure range and the increase of nitrogen uptake at a high relative pressure above 0.90 may result from interparticulate porosity and void associated with meso- and macrostructures of AuNPs@CPOP. The PSD profiles of the materials are shown in the inset of Fig. 3 and S4 (in ESI†), in which the dominant pore size of AuNP-1@CPOP is located between 2.0 and 10.8 nm according to NLDFT method from nitrogen adsorption branch. The average pore size is 5.36 nm according to the adsorption branch by the Barrett–Joyner–Halenda method in porosity study. Both the nitrogen adsorption–desorption isotherm and the PSD profile demonstrate that AuNP-1@CPOP are hierarchical porous with micro-, meso- and macropores. As to AuNP-2@CPOP, it exhibits similar dominant PSD. The BET specific surface area and pore volume of AuNP-1@CPOP are 930 m2 g−1 and 0.799 cm3 g−1, respectively. The BET specific surface area of AuNP-2@CPOP and pore volume are 1460 m2 g−1 and 0.564 cm3 g−1 (Table S1, ESI†). The hierarchical PSD of obtained materials is advantageous for heterogeneous catalytic application. The meso- and macroporous structures in AuNPs@CPOP accelerate the mass transfer of reactants and products, while micropore size is beneficial for anchoring AuNPs.32 The porous polycarbazole composites with high surface area and hierarchical pores are beneficial for adsorption and diffusion in heterogeneous catalysis.
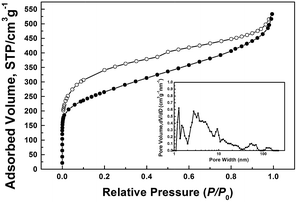 |
| Fig. 3 Nitrogen adsorption–desorption isotherm of AuNP-1@CPOP at 77 K and the inset PSD profile calculated by NLDFT (the adsorption and desorption branches are labeled with solid and open dot, respectively). | |
The nitro-aromatic compounds are commonly produced during the industrial manufacture of pharmaceuticals, agrochemicals, and dyes, which usually exist in waste water and are harmful to environment and human health. However, they can be reduced into the corresponding useful and less hazardous aromatic amines in the presence of metallic nanoparticles. It is reported that AuNPs can promote the reduction of 4-nitrophenol to 4-aminophenol in the presence of BH4−.33 Both the reactants and products are easily monitored by UV-Vis spectroscopy without any formation of appreciable byproduct. The catalytic activity of AuNPs@CPOP is tested by the reduction of 4-nitrophenol to 4-aminophenol at room temperature with an excess amount of NaBH4 as the reducing reagent.34 The color of the solution changes to yellow quickly in the presence of NaBH4 because of the formation of 4-nitrophenolate ion. The reaction progress is monitored by recording the UV-Vis absorbance ranging from 250 to 550 nm. The absorption peak at 400 nm is the characteristic peak of 4-nitrophenolate ion. When the AuNPs@CPOP is added into the mixture, the peak intensity at 400 nm is gradually decreasing with time. A new peak at 300 nm, assigned to 4-aminophenol ion, is emerging as time going on. Fig. 4a shows the time-dependent normalized absorption results for the reduction of 4-nitrophenol catalyzed by the low amount of AuNP-1@CPOP. The reaction can be finished within 850 s at 293 K with conversion of 97%, demonstrating the high catalytic activity of AuNP-1@CPOP. Fig. S5a (ESI†) shows the time-dependent normalized absorption results for the reduction of 4-nitrophenol catalyzed by the low amount of AuNP-2@CPOP. The reaction can be finished within 1395 s at 293 K with conversion of 95% under catalysis of AuNP-2@CPOP.
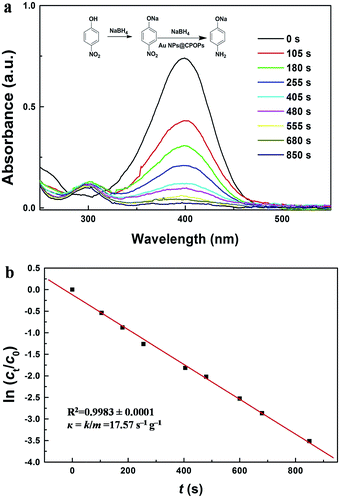 |
| Fig. 4 (a) Time-dependent normalized absorption spectra of 4-nitrophenol reduced by NaBH4 in the presence of AuNP-1@CPOP (the inset is the catalytic reduction of 4-nitrophenol to 4-aminophenol). (b) Plot of ln(ct/c0) against the reaction time t. | |
Using excess NaBH4, the reduction rates can be treated as being independent of the concentration of aqueous NaBH4 solution. So the reduction of 4-nitrophenol is regarded as pseudo-first-order shown in the following eqn (1).
|
ln(ct/c0) = ln(At/A0) = kappt
| (1) |
where
t is the reaction time, the UV-Vis absorbance values of
A0 and
At are corresponding to the concentration of 4-nitrophenol at
c0 and
ct,
c0 is the initial concentration and
ct is the concentration of 4-nitrophenol at the reaction time
t,
kapp represents the apparent rate constant. To quantitatively depict the reaction kinetics,
Fig. 4b shows the plot of a good linear correlation between ln(
ct/
c0) and the reaction time
t at 293 K. From the plot,
kapp is calculated to be 4.04 × 10
−3 s
−1 from the slope of the linear fit. In general, it is more reasonable to apply the activity factor
κ (
κ =
kapp/
m,
m is the total mass of the catalyst) to judge the activity of catalyst.
35 AuNP-1@CPOP is highly active catalyst and has good performance in the catalytic reduction of 4-nitrophenol with high value of catalytic activity factor of 17.57 s
−1 g
−1. AuNP-2@CPOP is also active in the catalytic reduction of 4-nitrophenol. Fig. S5b (ESI
†) exhibits the plot of a good linear correlation between ln(
ct/
c0) and the reaction time
t at 293 K. The apparent reaction rate
kapp of AuNP-2@CPOP in reduction of 4-nitrophenol is 2.31 × 10
−3 s
−1, then the catalytic factor
κ is 10.04 s
−1 g
−1. The detailed information for related catalytic behaviors of corresponding polymers in reduction are exhibited in Table S2 (ESI
†). Although the rate of AuNP-2@CPOP is smaller than that of AuNP-1@CPOP, as heterogeneous catalysts, they both have good performance in the catalytic reduction of 4-nitrophenol. The high catalytic activity may result from mono-dispersed AuNPs of small size encapsulated within pore channels, the high specific surface area, and hierarchical pore size distribution of the materials.
Since AuNPs are the catalytic sites, the catalytic properties of composite materials are closely relevant to the particle of AuNPs. AuNPs@CPOP with different AuNPs sizes are expected to have different catalytic activity.36 The catalytic activity of AuNPs@CPOP decreases with the increase in the size of AuNPs. Due to the smaller particles possessing a large numbers of surface atoms available in heterogeneous catalysis, the decrease in catalytic rate with increase in particle size is noticeable for particles of small size. It is demonstrated that, in heterogeneous catalysis, the reaction rate decreases with the particle size increasing.37
The possible mechanism of catalytic activity of AuNPs@CPOP can be explained in terms of the Langmuir–Hinshelwood (LH) model.34 Firstly, both reactants must be adsorbed on the surface of the nanoparticles and this process is modeled as an equilibrium process described by the classical Langmuir isotherm. 4-Nitrophenol is adsorbed in the networks of AuNPs@CPOP via π–π stacking interaction between the benzene moieties of 4-nitrophenol and the aromatic rings of AuNPs@CPOP.38 The adsorbed 4-nitrophenol is accessible to the surface of AuNPs. Borohydride ions adsorb on the surface of AuNPs before the reaction, which are reversible and can be modeled as a Langmuir isotherm.39 Secondly, the adsorbed species can react with each other on the surface of nanoparticles. BH4− reacts with H2O and transfer a hydrogen species to the surface of the AuNPs to form Au–H, and the adsorbed 4-nitrophenol reacts with the Au–H bonds to give 4-aminophenol.40 The highly porous polymers encapsulating mono-dispersed AuNPs in their hierarchical pores are supposed to accelerate the formation of Au–H and the reaction between 4-nitrophenol and Au–H. Finally, the product dissociates from the surface, that is 4-aminophenol diffuses from the catalyst to the aqueous solution. The amino group in 4-aminophenol is an electron-donating group. Whereas, the nitryl group in 4-nitrophenol is an electron-accepting group. As a result, the π–π stacking of 4-aminophenol is relatively weaker than that of 4-nitrophenol, and the affinity of 4-aminophenol and aqueous solvent is stronger than that of 4-nitrophenol.38 It is easy for 4-aminophenol to diffuse from channels of AuNPs@CPOP to the aqueous solution after the reaction. The related schematic mechanism for catalytic reduction of 4-nitrophenol by AuNPs@CPOP in the presence of NaBH4 was shown in Fig. S6 (ESI†). In the heterogeneous catalysis of AuNPs@CPOP, the reaction between the Au–H bonds and 4-nitrophenol is the rate-limiting step. Compared with the reaction on the AuNP surface, the diffusion and adsorption of the reactants as the desorption of 4-aminophenol are fast.34,40 AuNPs are the catalytic sites in the reduction of 4-nitrophenol. As a result, the size of AuNPs is the dominant factor in the catalytic activity.
4. Conclusions
In summary, we developed an approach to fabricate the presynthesized AuNPs encapsulated in the network of porous polycarbazole with hierarchical pores. A novel ligand Cz-LA is used to stabilize the AuNPs without introducing other impurities to the system. TEM image and UV-Vis spectrum of AuNPs–Cz-LA indicate that surface functionalized AuNPs by carbazole with similar size are obtained, which can be further encapsulated in the network of porous polycarbazole by FeCl3-promoted oxidative coupling copolymerization to afford AuNPs/porous polymer composite AuNPs@CPOP at room temperature. The obtained materials possess high porosity and excellent catalytic activity in heterogeneous catalysis. Specifically, porous composite material containing AuNPs size distribution from 3 to 6 nm (AuNP-1@CPOP) shows outstanding catalytic reduction of 4-nitrophenol with activity factor of 17.57 s−1 g−1, which can be expected for further application in other catalytic filed and environmental chemistry. The high catalytic activity may result from mono-dispersed AuNPs of small size encapsulated within pore channel, the high specific surface area, and hierarchical pore size distribution. Using this method, various metal nanoparticles encapsulated in the network of porous organic polymer have been prepared, their related functions and properties are under investigation.
Acknowledgements
The financial support of the National Natural Science Foundation of China (Grants 21274033, 21374024, 21574032, and 21574031) is acknowledged.
Notes and references
-
(a) M. Haruta, T. Kobayashi, H. Sano and N. Yamada, Chem. Lett., 1987, 16(2), 405–408 CrossRef;
(b) M. Li, Z. Wu and S. H. Overbury, J. Catal., 2011, 278(1), 133–142 CrossRef CAS;
(c) M. Haruta and M. Datéb, Appl. Catal., A, 2011, 222(1–2), 427–437 Search PubMed.
-
(a) T. Hayashi, K. Tanaka and M. Haruta, J. Catal., 1998, 178(2), 566–575 CrossRef CAS;
(b) M. Okumura, T. Fujitani, J. Huang and T. Ishida, ACS Catal., 2015, 5(8), 4699–4707 CrossRef CAS.
- L. Prati and M. Rossi, J. Catal., 1998, 176(2), 552–560 CrossRef CAS.
-
(a) Y. Zhang, X. Cui, F. Shi and Y. Deng, Chem. Rev., 2012, 112(4), 2467–2505 CrossRef CAS PubMed;
(b) A. Arcadi, Chem. Rev., 2008, 108(8), 3266–3325 CrossRef CAS PubMed;
(c) M. Stratakis and H. Garcia, Chem. Rev., 2012, 112(8), 4469–4506 CrossRef CAS PubMed.
- C. Burda, X. Chen, R. Narayanan and M. A. El-Sayed, Chem. Rev., 2005, 105(4), 1025–1102 CrossRef CAS PubMed.
-
(a) Z. Kónya, V. F. Puntes, I. Kiricsi, J. Zhu, J. W. Ager, M. K. Ko, H. Frei, P. Alivisatos and G. A. Somorjai, Chem. Mater., 2003, 15(6), 1242–1248 CrossRef;
(b) B. S. Uphade, S. Tsubota, T. Hayashi and M. Haruta, Chem. Lett., 1998, 27(12), 1277–1278 CrossRef;
(c) L. Xu, Y. Ren, H. Wu, Y. Liu, Z. Wang, Y. Zhang, J. Xu, H. Peng and P. Wu, J. Mater. Chem., 2011, 21(29), 10852–10858 RSC.
-
(a) Z. Dong, X. Le, Y. Liu, C. Dong and J. Ma, J. Mater. Chem. A, 2014, 2(44), 18775–18785 RSC;
(b) H. Hosseini, M. Behbahani, M. Mahyari, H. Kazerooni, A. Bagheri and S. Ahmad, Biosens. Bioelectron., 2014, 59(15), 412–417 CrossRef CAS PubMed;
(c) Z. Ma, X. Jia, J. Hu, F. Zhou and B. Dai, RSC Adv., 2014, 4(4), 1853–1856 RSC;
(d) Y. Bide, M. R. Nabid and F. Dastar, RSC Adv., 2015, 5(78), 63421–63428 RSC.
- V. Evangelista, B. Acosta, S. Miridonov, E. Smolentseva, S. Fuentes and A. Simakov, Appl. Catal., B, 2015, 166–167, 518–528 CrossRef CAS.
- S. M. Yoo, S. B. Rawal, J. E. Lee, J. Kim, H.-Y. Ryu, D.-W. Park and W. I. Lee, Appl. Catal., A, 2015, 499, 47–54 CrossRef CAS.
- R. Liu, Y. Guo, G. Odusote, F. Qu and R. D. Priestley, ACS Appl. Mater. Interfaces, 2013, 5(18), 9167–9171 CAS.
-
(a) H. Kang, M. Kim and K. H. Park, Appl. Catal., A, 2015, 502, 239–245 CrossRef CAS;
(b) W. Liu, D. Sun, J. Fu, R. Yuan and Z. Li, RSC Adv., 2014, 4(21), 11003–11011 RSC.
- C. Fernandes, C. Pereira, A. Guedes, S. L. H. Rebelo and C. Freire, Appl. Catal., A, 2014, 486, 150–158 CrossRef CAS.
-
(a) N. Yao, W. Lin, X. Zhang, H. Gu and L. Zhang, J. Polym. Sci., Part A: Polym. Chem., 2016, 54(1), 186–196 CrossRef CAS;
(b) A. Leiva, I. Fuentes, E. Bossel, M. Urzúa, M. Méndez, M. Pino, D. Radić, V. Márquez and F. D. González-Nilo, J. Polym. Sci., Part A: Polym. Chem., 2014, 52(21), 3069–3079 CrossRef CAS.
-
(a) S. Xu, Y. Luo and B. Tan, Macromol. Rapid Commun., 2013, 34(6), 471–484 CrossRef CAS PubMed;
(b) P. Kaur, J. T. Hupp and S. T. Nguyen, ACS Catal., 2011, 1(7), 819–835 CrossRef CAS;
(c) Q. Wen, T.-Y. Zhou, Q.-L. Zhao, J. Fu, Z. Ma and X. Zhao, Macromol. Rapid Commun., 2015, 36(4), 413–418 CrossRef CAS PubMed.
- F. Rodeiquez-Reinoso, Carbon, 1998, 36(3), 159–175 CrossRef.
- H. Yang, K. Nagai, T. Abe, H. Homma, T. Norimatsu and R. Ramaraj, ACS Appl. Mater. Interfaces, 2009, 1(9), 1860–1864 CAS.
- X. Kang, J. Zhang, W. Shang, T. Wu, P. Zhang, B. Han, Z. Wu, G. Mo and X. Xing, J. Am. Chem. Soc., 2014, 136(10), 3768–3771 CrossRef CAS PubMed.
-
(a) H. Kim, M. C. Cha, H. W. Park and J. Y. Chang, J. Polym. Sci., Part A: Polym. Chem., 2013, 51(24), 5291–5297 CrossRef CAS;
(b) Q. Liang, J. Liu, Y. Wei, Z. Zhao and M. J. MacLachla, Chem. Commun., 2013, 49(79), 8928–8930 RSC.
- C. E. Chan-Thaw, A. Villa, P. Katekomol, D. Su, A. Thomas and L. Prati, Nano Lett., 2010, 10(2), 537–541 CrossRef CAS PubMed.
- H. Lee, H. Kim, T. J. Choi, H. W. Park and J. Y. Chang, Chem. Commun., 2015, 51(48), 9805–9808 RSC.
- Q. Chen, D.-P. Liu, M. Luo, L.-J. Feng, Y.-C. Zhao and B.-H. Han, Small, 2014, 10(2), 308–315 CrossRef CAS PubMed.
- Q. Chen, D.-P. Liu, J.-H. Zhu and B.-H. Han, Macromolecules, 2014, 47(17), 5926–5931 CrossRef CAS.
- Q. Chen, M. Luo, P. Hammershøj, D. Zhou, Y. Han, B. W. Laursen, C.-G. Yan and B.-H. Han, J. Am. Chem. Soc., 2012, 134(14), 6084–6087 CrossRef CAS PubMed.
- L.-J. Feng, Q. Chen, J.-H. Zhu, D.-P. Liu, Y.-C. Zhao and B.-H. Han, Polym. Chem., 2014, 5(8), 3081–3088 RSC.
- G. Lu, S. Li, Z. Guo, O. K. Farha, B. G. Hauser, X. Qi, Y. Wang, X. Wang, S. Han, X. Liu, J. S. DuChene, H. Zhang, Q. Zhang, X. Chen, J. Ma, S. C. J. Loo, W. D. Wei, Y. Yang, J. T. Hupp and F. Huo, Nat. Chem., 2012, 4(4), 310–316 CrossRef CAS PubMed.
-
(a) L. Shi, G. Tian, H. Ye, S. Qi and D. Wu, Polymer, 2014, 55(5), 1150–1159 CrossRef CAS;
(b) W.-Y. Lee, T. Kurosawa, S.-T. Lin, T. Higashihara, M. Ueda and W.-C. Chen, Chem. Mater., 2011, 23(20), 4487–4497 CrossRef CAS.
- M.-C. Saada, J.-L. Montero, D. Vullo, A. Scozzafava, J.-Y. Winum and C. T. Supuran, J. Med. Chem., 2011, 54(5), 1170–1177 CrossRef CAS PubMed.
- K. Kuroda, T. Ishida and M. Haruta, J. Mol. Catal. A: Chem., 2009, 298(1–2), 7–11 CrossRef CAS.
- A. Ookawa, S. Yokoyama and K. Soai, Synth. Commun., 1986, 16(7), 819–825 CrossRef CAS.
-
(a) Y. Ding, X. Zhang, X. Liu and R. Guo, Colloids Surf., A, 2006, 290(1–3), 82–88 CrossRef CAS;
(b) Y. Que, C. Feng, S. Zhang and X. Huang, J. Phys. Chem. C, 2015, 119(4), 1960–1970 CrossRef CAS.
- B. Li, Y. Hao, X. Shao, H. Tang, T. Wang, J. Zhu and S. Yan, J. Catal., 2015, 329, 368–378 CrossRef CAS.
- L. Pan, M.-Y. Xu, L.-J. Feng, Q. Chen, Y.-J. He and B.-H. Han, Polym. Chem., 2016, 7(12), 2299–2307 RSC.
- Y. Fang and E. Wang, Nanoscale, 2013, 5(5), 1843–1848 RSC.
- S. Wunder, F. Polzer, Y. Lu, Y. Mei and M. Ballauff, J. Phys. Chem. C, 2010, 114(19), 8814–8820 CAS.
- J. Cheng, Y. Wang, C. Teng, Y. Shang, L. Ren and B. Jiang, Chem. Eng. J., 2014, 242, 285–293 CrossRef CAS.
- X. Zhou, W. Xu, G. Liu, D. Panda and P. Chen, J. Am. Chem. Soc., 2010, 132(1), 138–146 CrossRef CAS PubMed.
-
(a) S. Panigrahi, S. Basu, S. Praharaj, S. Pande, S. Jana, A. Pal, S. K. Ghosh and T. Pal, J. Phys. Chem. C, 2007, 111(12), 4596–4605 CrossRef CAS;
(b) B. E. Hayden, D. Pletcher, M. E. Rendall and J.-P. Suchsland, J. Phys. Chem. C, 2007, 111(45), 17044–17051 CrossRef CAS.
- F. Ke, J. Zhu, L.-G. Qiu and X. Jiang, Chem. Commun., 2013, 49(13), 1267–1269 RSC.
- S. Wunder, Y. Lu, M. Albrecht and M. Ballauff, ACS Catal., 2011, 1(8), 908–916 CrossRef CAS.
-
(a) P. Zhao, X. Feng, D. Huang, G. Yang and D. Astruc, Coord. Chem. Rev., 2015, 287, 114–136 CrossRef CAS;
(b) G. Guella, B. Patton and A. Miotello, J. Phys. Chem. C, 2007, 111(50), 18744–18750 CrossRef CAS.
Footnote |
† Electronic supplementary information (ESI) available: The size distribution of AuNPs in AuNP-1@CPOP, thermal analysis of AuNP-1@CPOP under air, TEM images of AuNP-2–Cz-LA and AuNP-2@CPOP, the size distribution of AuNPs in AuNP-2@CPOP, porosity data of AuNPs@CPOP, detailed information about preparation of AuNP-2–Cz-LA and AuNP-2@CPOP, and catalytic behavior of AuNP-2@CPOP, 1H NMR, 13C NMR, and mass spectra of Cz-LA. See DOI: 10.1039/c6ra04515d |
|
This journal is © The Royal Society of Chemistry 2016 |