DOI:
10.1039/C6RA03882D
(Paper)
RSC Adv., 2016,
6, 42770-42777
Synthesis and photoluminescence of green-emitting Ce3+,Tb3+ co-doped Al6Si2O13 phosphors with high thermal stability for white LEDs
Received
12th February 2016
, Accepted 23rd April 2016
First published on 26th April 2016
Abstract
In this article, novel green-emitting Ce3+,Tb3+ co-doped Al6Si2O13 phosphors have been successfully prepared by a high-temperature solid-state reaction method using Al2O3, SiO2, CeO2, and Tb4O7 powders as initial materials. Single-phased and good-crystallized phosphors have been obtained after calcining the mixed powders at 1470 °C under a weak reducing atmosphere. The average particle size of the as-synthesized phosphors is less than 20 μm. The optimized doping concentration of Tb3+ ion is determined to be 8 mol%. With Ce3+ co-doping as a sensitizer, the luminescence intensity of the Al6Si2O13:Ce3+/Tb3+ phosphors drastically improves as the Ce3+ doping concentration increases to 1.3 mol%. The Ce3+,Tb3+ co-doped Al6Si2O13 phosphors exhibit intense green emissions at 488, 541, 584, and 620 nm, which correspond to the characteristic level transition of 5D4-7F6, 5D4-7F5, 5D4-7F4, and 5D4-7F3 of Tb3+ ion, respectively. And Al6Si2O13:8%Tb3+,1.3%Ce3+ possesses a decay time of 31.4 ns, as well as a quantum yield of ∼45.7%. In addition, the solid-state synthesized Al6Si2O13:Ce3+/Tb3+ phosphor powders have comparable green luminescence properties and better thermal stability compared with available commercial green phosphors. In this regard, our target products, Al6Si2O13:Ce3+/Tb3+, may potentially serve as green-emitting phosphors for UV-converted white LEDs.
1. Introduction
As the next-generation of solid-state light sources, white-light-emitting diodes (WLEDs) exhibit a unique combination of favorable characteristics, including low power consumption, high luminous efficiency, reliability and environmental friendliness,1–4 which enable them to be used in a variety of fields, such as backlights, devices indicators, automobile headlights, and so on.5–8 In order to generate white light in LEDs, three methods have been employed:9–11 (1) utilizing three individual monochromatic LED chips with red, green and blue colors (tri-LEDs); (2) combining blue LED with yellow-emitting phosphors; (3) coupling ultraviolet (UV) LEDs with red, green and blue phosphor blends. For the first approach, it has high cost and complicated driver circuit, besides, it suffers from an intolerable shortcoming which is drifts of color rendering index (CRI) and color temperature (CT) due to susceptibility to the temperature of the devices.8,12 To solve these problems, phosphor-converted WLEDs (pc-WLEDs) technology is emerged. The popular method is to combine an InGaN blue LED and the yellow conversion phosphor YAG:Ce3+, but the innate deficiency of the red component results in low CRI and high CT values.13–17 Thus, the strategy of depositing tricolor (red, green, and blue) phosphors on a UV LED chip is developed. The advantage of this method is much easier to create white light with improved CRI and CT, which has provided the motivation for exploiting green-emitting phosphors suitable for UV LED excitations. Nevertheless, satisfactory green conversion phosphors for the WLED applications are not available so far. Hence, searching for novel green-emitting phosphors with superior photoluminescence is required.
To fulfill the goals of high fluorescence efficient green phosphors, the investigations on doping rare-earth (RE) ions into luminescent hosts have been carried out extensive interest.18–21 Among RE ions, Ce3+ exhibits a very high UV absorption coefficient because of the parity allowed 4f–5d electric-dipole transition. Furthermore, Ce3+ has a large Stocks shift arising from the extended radial wave functions of 5d state. Due to the strong overlap between Ce3+ emission and Tb3+ absorption in near-UV region, Ce3+ is always used as an efficient sensitizer for Tb3+ ion to enhance the green emission and improve the luminous efficiency of Tb3+ ion.22–26 Besides luminescence center, the host matrix is also important because it can be acted as a carrier for activators. Good host should be physically and chemically stable so that it can support doped ions in a fine crystalline field, wherein energy transfer can easily take place in the host lattice. Additionally, a unique aspect of pc-WLEDs is that the phosphors used in packages are in physical contact with the LED chip, and the LED chip operates at high temperatures (in the range of 100–150 °C), thereby, outstanding thermal stability is another basic requirement for the conversion phosphor.27–29 On this account, 3/2-mullite (i.e. Al6Si2O13) is an appropriate host material due to the mechanical and thermal properties that it displays. The fascinating performances of the Al6Si2O13 include low density, low thermal expansion coefficient and thermal conductivity, high elevated temperature strength and creep resistance, as well as excellent thermal and environmental stability.30,31
Inspired by its potential host applications, several works focused on the preparation of Al6Si2O13 based phosphors have been reported, using various techniques such as sol–gel route, co-precipitation method, and hydrothermal process.32–35 However, these mentioned approaches have many drawbacks, including relatively long preparation time, complex synthesis procedure, and difficult in precise control the amount of precipitate. From the practical point of view, long synthesis period, low productivity, and special apparatus are undesirable, therefore, a more convenient and effective way is needed. To our knowledge, almost no work on the preparation of Ce3+,Tb3+ co-doped Al6Si2O13 phosphor powders via solid-state reaction method has been reported. In response to this gap, single-composition Al6Si2O13:Ce3+/Tb3+ phosphors are synthesized by a high-temperature solid-state reaction method using Al2O3, SiO2, CeO2, and Tb4O7 powders as raw materials in the present study. To demonstrate the superior properties of the synthesized Ce3+,Tb3+ co-doped Al6Si2O13 phosphors, the crystal structure and microstructural features are characterized first. Then, the photoluminescence behaviors, lifetime and quantum yield of the Al6Si2O13:Ce3+/Tb3+ phosphors are investigated. Moreover, the mechanism and the efficiency of energy transfer from Ce3+ to Tb3+ in Al6Si2O13:Ce3+/Tb3+ are also given. Finally, the thermal stability of the prepared Al6Si2O13:Ce3+/Tb3+ phosphor powder is studied.
2. Experimental section
2.1 Materials preparation
Commercially available powders of Al2O3 (99.99%; Sinopharm Chemical Reagent Co. Ltd., Beijing, China), SiO2 (99.99%; Damao Reagent Co. Ltd., Tianjin, China), CeO2 (99.99%; Sinopharm Chemical Reagent Co. Ltd., Beijing, China), and Tb4O7 (99.99%; Sinopharm Chemical Reagent Co. Ltd., Beijing, China) were selected as starting materials for synthesizing Al6Si2O13:Ce3+/Tb3+ phosphors. RE-doping species were X mol% Tb4O7 (X = 2, 4, 6, 8, 10, 12) and Y mol% CeO2 (Y = 0.9, 1.1, 1.3, 1.5, 1.7, 1.9). All the chemical reagents were used without any further purification. Before the experiment, all of the raw materials were dried at 60 °C in an oven for 90 min in order to avoid moisture absorption. Detailed procedures can be described as follows. First of all, those dried reactant powders were accurately weighted using an electronic balance according to the stoichiometric ratio and then thoroughly mixed in an agate mortar for 10–15 min. Afterward, these mixtures were placed into a boron nitride crucible and calcined at 1470 °C for 5 h under a weak reducing atmosphere (H2/N2 = 5/95) by 50 sccm in an electric tube furnace. Finally, the Ce3+,Tb3+ co-doped Al6Si2O13 phosphor powders were obtained after cooling down to room temperature (RT) along with the furnace. The resulting samples were ground once more for further characterizations.
2.2 Characterization methods
Phase identification and crystallinity were examined in the 2θ range from 10° to 70° using an X-ray diffractometer (XRD; Rigaku D/max 2500, Tokyo, Japan) with CuKα radiation (λ = 1.54178 Å). The tube voltage, current, step size, and scanning rate were set at 40 kV, 200 mA, 0.02°, and 4° min−1, respectively. Phase compositions were determined with the help of Jade 6.0 software (Material data Inc., USA). The raw XRD data were further analyzed using the Rietveld method to confirm the formation of the title phase. The microstructure and morphology of the as-synthesized phosphors were observed using a field emission scanning electron microscope (FE-SEM, Hitachi S-4700, Tokyo, Japan) equipped with an energy dispersive spectroscopy (EDS) system at an accelerating voltage of 15 kV. For SEM observation, the phosphor powders were dispersed in distilled water using an ultrasonic apparatus, and then a drop of the dispersed powder/water mixture was deposited on the conductive paste. The conductive paste was dried at ambient temperature in air and subsequently gold-coated for 50 s. The diffuse reflection spectra were performed by an ultraviolet-visible (UV-VIS) spectrophotometer (Shimadzu UV-2600, Tokyo, Japan) using BaSO4 as the reference standard. The steady-state photoluminescence excitation and emission spectra were recorded on a spectrofluorometer (Hitachi F-7000, Tokyo, Japan) using a continuous 150 W Xenon lamp as the static excitation source. The time-resolved decay curve and quantum yield were measured by an Edinburgh Instrument FLS980 spectrofluorometer using a pulsed nanosecond flash lamp as the dynamic excitation source. The CIE-1931 chromaticity coordinates were calculated by using GoCIE software. For comparison, all of the measurements were conducted at RT with the same experimental parameters.
3. Results and discussion
3.1 Crystal structure, phase identification, and microstructure
Al6Si2O13 belongs to the family of mullite-type crystal structures. Al6Si2O13 crystallizes in an orthorhombic structure with the space group Pbam.31 On the basis of the Fischer and Schneider principles,36,37 the backbone of mullite-type crystal structures are single chains of edge-sharing octahedra in a tetragonal arrangement in its highest topological symmetry. For Al6Si2O13, its crystal structure is consisted of chains of edge-sharing AlO6 octahedra running parallel to the crystallographic c-axis. These chains are cross-linked by tetrahedral M2O5 (M = Al3+, Si4+) groups forming double chains.38 In Al6Si2O13, part of the Si4+ ions is replaced by Al3+ ions. The compensation of substitution induced charge deficiency is achieved by removal of a number of O atoms bridging the tetrahedral M2O5 groups. This leads to the formation of oxygen vacancies according to the coupled substitution:31 |
2Si4+ + O2− → 2Al3+ + vacancy(□)
| (1) |
The loss of the O atoms causes the two cations of the tetrahedral site (Si4+, Al3+ site) to occupy the neighbouring positions of the second tetrahedral site.34
In order to determine the optimized calcination temperature of Al6Si2O13:Ce3+/Tb3+, the synthesis temperature for preparing pure Al6Si2O13 was investigated first. The XRD patterns of the Al6Si2O13 powders synthesized at different temperatures of 1270–1520 °C, together with the standard PDF diffraction pattern of pure Al6Si2O13 are exhibited in Fig. 1. For the sample heated at 1270 °C (Fig. 1(a)), only those peaks related to initial powders, i.e. Al2O3 and SiO2, are identified, suggesting that no reaction has occurred between Al2O3 and SiO2 until 1270 °C. Further increasing the calcination temperature to 1320 °C, 1370 °C and 1420 °C (Fig. 1(b–d)), in addition to SiO2 and Al2O3, small amounts of cristobalite are also detected via XRD. These weak diffraction peaks of cristobalite located at 2θ = 21.8° may be responsible for the reconstruction changes of crystal structure during heating. In the sample heated up to 1470 °C (Fig. 1(e)), only single phase Al6Si2O13 is presented, which agrees well with the JCPDS card (PDF 82-0037). Meanwhile, diffraction peaks of Al2O3, SiO2 and cristobalite totally vanish. Thus, it is reasonable to choose 1470 °C for the synthesis of Al6Si2O13:Ce3+/Tb3+ phosphors hereafter. Furthermore, no diffraction peaks of other impurity phases can be detected in the sample heated to 1520 °C (Fig. 1(f)), implying that Al6Si2O13 is stable at this temperature.
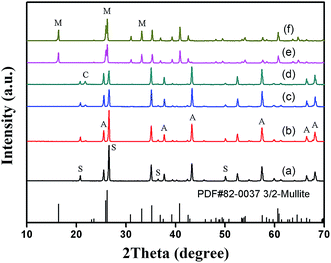 |
| Fig. 1 XRD patterns of Al6Si2O13 powders prepared at different temperature of 1270 °C (a), 1320 °C (b), 1370 °C (c), 1420 °C (d), 1470 °C (e), and 1520 °C (f): M = Al6Si2O13, A = Al2O3, S = SiO2, and C = cristobalite. | |
Based on the above results, we fabricate Al6Si2O13:Ce3+/Tb3+ phosphors under a weak reducing atmosphere of 5% H2/95% N2 for 5 h at 1470 °C. To confirm the calcined powder is single-composition Al6Si2O13:Ce3+/Tb3+ and to determine its crystallinity, the 1470 °C prepared Al6Si2O13:8%Tb3+,1.3%Ce3+ sample as a model was examined by XRD, together with the XRD pattern of pure Al6Si2O13, as plotted in Fig. 2, from which one can see that the peak positions between the Al6Si2O13 and Al6Si2O13:8%Tb3+,1.3%Ce3+ coincide well, besides, the Ce3+ and Tb3+ cannot be detected. This result indicates that the Ce3+ and Tb3+ are fully doped in the Al6Si2O13 host lattice and further proves that 1470 °C is the synthesis temperature for single-phased Al6Si2O13:Ce3+/Tb3+ phosphors. Also, the observation from Fig. 2 indicates that Ce3+ and Tb3+ are incorporated in the lattice and does not change the crystal structure of Al6Si2O13. This can be interpreted as below. According to the structural description aforementioned, the only available lattice site in Al6Si2O13 is 4-coordinated or 6-coordinated Si4+/Al3+ sites. However, the larger sized Ce3+ and Tb3+ ions cannot occupy these low coordination sites, and always prefer a site with coordination number ≥ 8.34 So, the possible site for Ce3+ and Tb3+ in Al6Si2O13 is a “structural cavity” wherein Ce3+ and Tb3+ can have more than eight nearest-neighbour O atoms. As a result, the crystal structure between Al6Si2O13 and Al6Si2O13:Ce3+/Tb3+ remains the same. The samples derived from various X and Y values have similar XRD pattern to the Al6Si2O13:8%Tb3+,1.3%Ce3+ and are not shown here for brevity. Then, we optimize the crystal structure of the as-prepared Al6Si2O13:Ce3+/Tb3+ using the validate XRD data. The refined lattice parameters are a = 7.5217 Å, b = 7.6798 Å, c = 2.8870 Å, and V = 166.77 Å3. Moreover, it can be seen from Fig. 2 that the Al6Si2O13:Ce3+/Tb3+ phosphor powders calcined at 1470 °C for 5 h are well crystalline. All the above results demonstrate that single-component and good-crystalline Ce3+,Tb3+ co-doped Al6Si2O13 phosphors are successfully prepared via high-temperature solid-state reaction method.
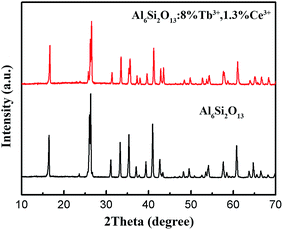 |
| Fig. 2 XRD patterns of the Al6Si2O13 powders and the Al6Si2O13:8%Tb3+,1.3%Ce3+ phosphors calcined at 1470 °C for 5 h under a weak reducing atmosphere. | |
The microstructure and morphology of the high-temperature solid-state synthesized Al6Si2O13:8%Tb3+,1.3%Ce3+ phosphors are shown in Fig. 3. SEM observation reveals that the as-obtained sample exhibit elliptical-like morphology with relatively smooth surfaces. Even though the product appears agglomeration to some extent due to absorbing water in the air easily, a multitude of Al6Si2O13:8%Tb3+,1.3%Ce3+ particles are dispersed relatively regularly, with an average particle size of less than 20 μm. After obtaining single-phased and good-crystallized Al6Si2O13:Ce3+/Tb3+ phosphor, its photoluminescence properties are investigated. The results are described and discussed in the following sections.
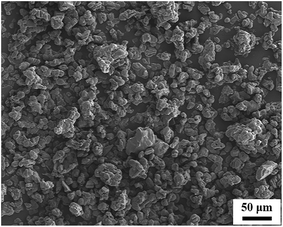 |
| Fig. 3 SEM image of the solid-state-derived Al6Si2O13:8%Tb3+,1.3%Ce3+ phosphors. | |
3.2 Photoluminescence (PL) and energy transfer behavior
Since the concentration of activator greatly affects the emission intensity, the effect of the concentration of Tb3+ on the PL intensity was studied. First, we fix the concentration of Tb3+ for 8 mol%, that is, Al6Si2O13:8%Tb3+, its excitation and emission spectra are shown in Fig. 4(a). There is a strong excitation peak at about 217 nm and a number of absorption bands at 320–500 nm (see inset of Fig. 4(a)) in excitation spectra (λem = 541 nm). The former is assigned to the spin-allowed 4f–5d transition of Tb3+ ion, and the latter is ascribed to the forbidden f–f transition of Tb3+ ion.39 Meanwhile, Al6Si2O13:8%Tb3+ sample displays a strong green emission under λex = 217 nm. The typical green emission peaks of Tb3+ ion at 488, 541, 584, and 620 nm are corresponded to the 5D4-7F6, 5D4-7F5, 5D4-7F4, and 5D4-7F3 transitions, respectively.40 Then, we change the doping concentration of Tb3+ from 4 mol% to 12 mol% upon the excitation wavelength of 217 nm, as presented in Fig. 4(b). It can be seen that the emission intensity visibly increases with the increasing concentration of Tb3+, reaches a saturation when the concentration of Tb3+ ion is 8 mol%, and then decreases as the Tb3+ concentration increases (see inset of Fig. 4(b)). This is attributed to the fact that more activators are introduced with the increasing of Tb3+ doping concentration, whereas, further increasing Tb3+ dopant content results in a concentration quenching phenomenon linked to the cross-relaxation of Tb3+ ion.35,41,42 Therefore, the optimal concentration of Tb3+-doped for Al6Si2O13:Ce3+/Tb3+ is 8 mol%.
 |
| Fig. 4 (a) Excitation and emission spectra of Al6Si2O13:8%Tb3+ (λem = 541 nm), the inset exhibits the magnified region between 320 and 500 nm. (b) Emission spectra (λex = 217 nm) of Al6Si2O13:XTb3+ with changed X values (0.04–0.12), the inserted map shows the emission intensity as a function of Tb3+ doping concentration. | |
Besides the activator, the sensitizer also plays a crucial role in the photoluminescence process because it not only enhances the emission intensity but also improves the luminous efficiency of the phosphors. After investigating the effect of the concentration of Tb3+ ion, we explore the influence of the concentration of Ce3+ on the PL intensity. Fig. 5(a) portrays the emission intensity of Al6Si2O13:8%Tb3+,YCe3+ phosphors as a function of the concentration of Ce3+ (λex = 297 nm). Similarly, the emission intensity systematically increases with the increasing dosage of Ce3+ ion, achieves a maximum value when the concentration of Ce3+ is 1.3 mol%, and then declines as the Ce3+ concentration increases (see inset of Fig. 5(a)). This drop of fluorescence intensity is caused by the co-operative down-conversion and resonance-type energy transfer.35 Hence, the optimal concentration of Ce3+-doped for Al6Si2O13:Ce3+/Tb3+ is 1.3 mol%.
 |
| Fig. 5 (a) Emission spectra (λex = 297 nm) of Al6Si2O13:8%Tb3+,YCe3+ with varied Y values (0.009–0.019), the inserted photo displays the emission intensity as a function of Ce3+ doping concentration. (b) Luminescence intensity of the Al6Si2O13:Ce3+/Tb3+ sample and that of the Al6Si2O13:Tb3+ sample under 297 nm excitation, the inserted picture shows the luminescence color of the as-prepared Al6Si2O13:8%Tb3+,1.3%Ce3+ sample excited by 297 nm. | |
Fig. 5(b) compares the luminescence intensity of the Ce3+,Tb3+ co-doped Al6Si2O13 sample and that of the Tb3+ single-doped Al6Si2O13 sample (λex = 297 nm). As expected, the intensity of the Al6Si2O13:Ce3+/Tb3+ is obviously higher than that of the Al6Si2O13:Tb3+, which completely supports that Ce3+ is a very efficient sensitizer for Tb3+ to enhance the emission of Tb3+ ion. Moreover, the luminescence color of Al6Si2O13:8%Tb3+,1.3%Ce3+ sample excited by 297 nm is characterized by Commission International de I'Eclairage (CIE) chromaticity diagram and illustrated in the inserted photograph of Fig. 5(b). From inset of Fig. 5(b), it is apparent that the synthesized Al6Si2O13:8%Tb3+,1.3%Ce3+ phosphor locates in the green region with the CIE-1931 chromaticity coordinate of (0.244, 0.592), which is comparable to the commercial green-emitting phosphors such as GY520-L and G2762. This bright chromatic Al6Si2O13:8%Tb3+,1.3%Ce3+ green phosphor is positive to promote its WLED applications.
By analyzing the photoluminescence behaviors of the Al6Si2O13:8%Tb3+,1.3%Ce3+ phosphors, we can find that energy transfer (ET) may take place from Ce3+ to Tb3+. To prove this conjecture, the excitation and emission spectra of Ce3+,Tb3+ single-doped and co-doped specimens are depicted in Fig. 6. The Ce3+ single-doped sample under 297 nm excitation shows a board emission at 390 nm (Fig. 6(a)), while the Tb3+ single-doped sample (λem = 541 nm) displays a strong absorption peak at 217 nm and several absorption lines at 320–500 nm (Fig. 6(b)). Namely, there is a conspicuous partly spectral overlap between Ce3+ emission and Tb3+ absorption, which means that the presence of ET from Ce3+ to Tb3+ is possible.43–45 From Fig. 6(c), it is clearly to see that excitation spectrum monitored at emission of Tb3+ (λem = 541 nm) ranging from 250–350 nm, corresponding to electron transitions from 4f state to 5d level of Ce3+. Additionally, excited by 297 nm light, a lot of emission peaks for Ce3+,Tb3+ co-doped sample are observed in Fig. 6(d), whereas, almost no emission is detected for Tb3+ single-doped sample. These above results provide evidence for the energy transfer probability from Ce3+ ions to Tb3+ ions. This conclusion can be further approved in terms of the diffuse reflection investigation. Fig. 7 exhibits the diffuse reflection spectra of the Al6Si2O13:XTb3+,1.3%Ce3+ samples with varied X values (0.02–0.08). It is noticed that there are two visible peaks at 221 and 297 nm which are assigned to the f–d transitions of Tb3+ and Ce3+, respectively. With the X value increases from 0.02 to 0.08, the reflectivity (at 221 nm) is declined due to the increasing content of Tb3+ ion in the host matrix. For maintaining Ce3+ doping concentration, the decreasing reflectivity (at 297 nm) is predominantly caused by the energy transition of the Ce3+ to the Tb3+.46,47 All the described observations strongly confirm that the ET process from Ce3+ to Tb3+ in Al6Si2O13 host indeed takes place.
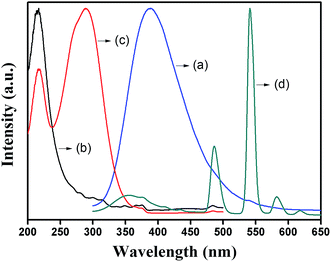 |
| Fig. 6 Excitation and emission spectra of Ce3+,Tb3+ single-doped and co-doped specimens: (a) emission spectrum of Ce3+ single-doped sample (λex = 297 nm), (b) excitation spectrum of Tb3+ single-doped sample (λem = 541 nm), (c) excitation spectrum of Ce3+,Tb3+ co-doped sample (λem = 541 nm), (d) emission spectrum of Ce3+,Tb3+ co-doped sample (λex = 297 nm). | |
 |
| Fig. 7 Diffuse reflection spectra of the Al6Si2O13:XTb3+,1.3%Ce3+ samples with changing the X value from 0.02 to 0.08. | |
3.3 Decay curve, luminescence lifetime and quantum yield
To shed light on the mechanism of energy transfer from Ce3+ to Tb3+ and study the lifetime and quantum yield of the synthesized Al6Si2O13:Ce3+/Tb3+ phosphor powders, we measure the decay curves of the Ce3+ emission in the Al6Si2O13:1.3% Ce3+, XTb3+ (X = 0, 2%, 4%, and 8%) upon excitation at 290 nm, as shown in Fig. 8. The raw data can be well fitted using a double-exponential function as:8,27,48,49 |
 | (2) |
where τ1 and τ2 are short and long decay components, respectively, and parameters A1 and A2 are the fitting constants, respectively. Using the eqn (2), the average lifetimes (τ) can be further evaluated by the following equation: |
 | (3) |
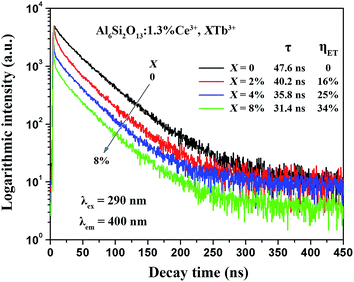 |
| Fig. 8 Decay curves and average lifetime of the Ce3+ together with the energy transfer efficacy from Ce3+ to Tb3+ in Al6Si2O13:1.3% Ce3+, XTb3+ (X = 0, 2%, 4%, 8%) phosphors (λex = 290 nm, λem = 400 nm) measured at room temperature. | |
The average lifetimes against a function of Tb3+ concentration are determined in the order of 47.6, 40.2, 35.8, and 31.4 ns for X = 0, 2%, 4%, and 8%, respectively. These results further prove the existence of energy transfer process from Ce3+ to Tb3+. Besides, the shorter decay lifetimes of our products are beneficial to avoid fluorescence scintillating.50 Additionally, we estimate the efficiency of energy transfer using the following formula:
|
 | (4) |
where
τ0 and
τ are the luminescence lifetimes of the sensitizer (Ce
3+) in the absence and presence of the activator (Tb
3+), respectively. The energy transfer efficiency from Ce
3+ to Tb
3+ in Al
6Si
2O
13:Ce
3+/Tb
3+ phosphors are calculated as a function of Tb
3+ content and are exhibited in the inset of
Fig. 8. Obviously, the energy transfer efficiency increases with the heightened Tb
3+ concentration, and the maximum value is approximately 34% at
X = 8%. Generally, energy transfer can be due to radiative transfer and due to non-radiative transfer. If resonant radiative transfer involves, the lifetime of the donor (Ce
3+) should maintain constant in the presence of the acceptor (Tb
3+).
27,51,52 From
Fig. 8, the decay curves owing to Ce
3+ in Al
6Si
2O
13:Ce
3+/Tb
3+ exhibit that the lifetime decreases monotonically with the increasing of Tb
3+ concentration. Thus, the energy transfer process between Ce
3+ and Tb
3+ should be mainly due to resonant non-radiative transfer.
Quantum yield (QY) is a very important performance for a given phosphor powder, however, the QY of this system is seldom reported. We therefore measure the QY of the samples Al6Si2O13:1.3% Ce3+, XTb3+ (X = 0, 2%, 4%, 8%, and 12%) using an integrating sphere principle, as illustrated in Fig. 9(a). The quantum yield is defined as the ratio of the number of emitted photons (Iem) to the number of absorbed photons (Iabs), and can be calculated by the following equation:53–55
|
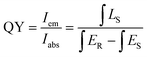 | (5) |
where
ES,
ER are the spectra of the excitation light with and without the sample in the integrating sphere, respectively,
LS is the luminescence emission spectrum of the sample in the integrating sphere. The excitation wavelength used for QY test in all samples is 290 nm. All the recorded spectroscopic data are corrected with the correction files supplied by the manufacturer.
Fig. 9(b) plots the dependences of QY on Tb
3+ content, from which one can find that the quantum yield is initially strengthened with the increased Tb
3+ dopant content, and achieve a maximum QY value of 45.7% at
X = 8%. Once the concentration of Tb
3+ exceeds 8%, a rapid decrease in QY can be observed because of emission quenching appearance.
8,52 Thus, the optimal concentration of Tb
3+ is 8%, which is fairly in agreement with the intensity analysis.
 |
| Fig. 9 (a) Schematic representation of the integrating sphere setup. (b) Quantum yield of the Al6Si2O13:1.3%Ce3+, XTb3+ (X = 0, 2%, 4%, 8%, and 12%) specimens under excitation wavelength of 290 nm. | |
3.4 Thermal stability of green Al6Si2O13:Ce3+/Tb3+ phosphors
When considering real applications, thermal stability is another crucial parameter for the phosphors because it remarkably affects the lifespan and chromaticity of the phosphors. Fig. 10(a) describes the luminescence spectra of as-prepared Al6Si2O13:8%Tb3+,1.3%Ce3+ phosphors versus the temperature. When the temperature increases from 30 °C to 260 °C, little changes in the luminescence intensity can be observed, and their peak positions are identical, indicating that Al6Si2O13:8%Tb3+,1.3%Ce3+ phosphor is highly thermally stable. Fig. 10(b) shows the luminescence properties variations of Al6Si2O13:8%Tb3+,1.3%Ce3+ phosphors as a function of temperature, accompanying with those of the commercial green phosphors such as GY520-L and G2762 for comparison. As can be seen, all the specimens display a declined trend in luminescence properties with the increasing temperature. When the temperature raises from 30 °C up to 260 °C, the loss of the luminescence intensity of Al6Si2O13:8%Tb3+,1.3%Ce3+ is only 9%, this value is ∼55% lower than G2762, and ∼88% smaller than GY520-L, which demonstrates the advantage of Al6Si2O13:8%Tb3+,1.3%Ce3+ phosphors for WLEDs. The excellent chromaticity, high thermal stability combined with superior photoluminescence properties endow Al6Si2O13:8%Tb3+,1.3%Ce3+ being a very promising converting phosphor for UV LED chip to generate white light.
 |
| Fig. 10 (a) Luminescence spectra of the Al6Si2O13:8%Tb3+,1.3%Ce3+ phosphors versus the temperature. (b) Variation of the luminescence properties of Al6Si2O13:8%Tb3+,1.3%Ce3+, GY520-L, and G2762 phosphors as a function of the temperature. | |
4. Conclusions
In summary, single-composition Al6Si2O13:Ce3+/Tb3+ phosphors can be successfully produced via a high-temperature solid-state reaction method. The experimental results demonstrate that the introduction of rare-earth ions has no effect on the crystal structure. Investigations based on the excitation and emission spectra reveal that the optimized Ce3+ and Tb3+ dopant content are 1.3 mol% and 8 mol%, respectively. Under excitation wavelength of 217 nm, strong green emissions centered at 488, 541, 584, and 620 nm are observed, which are assigned to the Tb3+ ion transitions of 5D4-7F6, 5D4-7F5, 5D4-7F4, and 5D4-7F3, respectively. Energy transfer process from Ce3+ to Tb3+ in Al6Si2O13 host can be confirmed through spectra and decay time curves analyses. Furthermore, the Ce3+,Tb3+ co-doped Al6Si2O13 phosphors has high thermal stability and superior photoluminescence properties. Our results suggest that green-emitting Al6Si2O13:Ce3+/Tb3+ can be considered as a potential converting phosphor applied in UV-pumped white LEDs.
Acknowledgements
The present work was supported by National Natural Science Foundation of China (Grant No. 50902028), Natural Science Foundation of Guangdong Province (Grant No. 9451805707003351), Shenzhen Science and Technology Plan Supported Project (Grant No. JCYJ20140616172915497, No. JCYJ20150625142543479).
Notes and references
- H. Daicho, T. Iwasaki, K. Enomoto, Y. Sasaki, Y. Maeno, Y. Shinomiya, S. Aoyagi, E. Nishibori, M. Sakata, H. Sawa, S. Matsuishi and H. Hosono, Nat. Commun., 2012, 3, 1132–1141 CrossRef PubMed.
- R. Zhang, H. Lin, Y. L. Yu, D. Q. Chen, J. Xu and Y. S. Wang, Laser Photonics Rev., 2014, 8, 158–164 CrossRef CAS.
- J. Chen, Y. G. Liu, H. Liu, D. Yang, H. Ding, M. Fang and Z. Huang, RSC Adv., 2014, 4, 18234–18239 RSC.
- X. F. Li, J. D. Budai, F. Liu, J. Y. Howe, J. H. Zhang, X. J. Wang, Z. J. Gu, C. J. Sun, R. S. Meltzer and Z. W. Pan, Light: Sci. Appl., 2013, 2, E50–E59 CrossRef.
- C. C. Lin and R. S. Liu, J. Phys. Chem. Lett., 2011, 2, 1268–1277 CrossRef CAS PubMed.
- E. F. Schubert and J. K. Kim, Science, 2005, 308, 1274–1278 CrossRef CAS PubMed.
- R. J. Xie and N. Hirosaki, Sci. Technol. Adv. Mater., 2007, 8, 588–600 CrossRef CAS.
- F. W. Kang, M. Y. Peng, Q. Y. Zhang and J. R. Qiu, Chem.–Eur. J., 2014, 20, 11522–11530 CrossRef CAS PubMed.
- R. Mueller-Mach, G. O. Mueller, M. R. Krames and T. Trottier, IEEE J. Sel. Top. Quantum Electron., 2002, 8, 339–345 CrossRef CAS.
- U. Kaufmann, M. Kunzer, K. Kohler, H. Obloh, W. Pletschen, P. Schlotter, J. Wagner, A. Ellens, W. Rossner and M. Kobusch, Phys. Status Solidi A, 2002, 192, 246–253 CrossRef CAS.
- R. J. Xie and N. Hirosaki, Sci. Technol. Adv. Mater., 2007, 8, 588–600 CrossRef CAS.
- M. Y. Peng, X. W. Yin, P. A. Tanner, M. G. Brik and P. F. Li, Chem. Mater., 2015, 27, 2938–2945 CrossRef.
- D. Kang, H. S. Yoo, S. H. Jung and D. Y. Jeon, J. Phys. Chem. C, 2011, 115, 24334–24340 CAS.
- R. F. Wei, H. Zhang, F. Li and H. Guo, J. Am. Ceram. Soc., 2012, 95, 34–36 CrossRef CAS.
- Y. Q. Li, A. C. A. Delsing, G. de With and H. T. Hintzen, Chem. Mater., 2005, 17, 3242–3248 CrossRef CAS.
- C. H. Hsu, S. Das and C. H. Lu, J. Electrochem. Soc., 2012, 159, J193–J199 CrossRef CAS.
- M. M. Shang, C. X. Li and J. Lin, Chem. Soc. Rev., 2014, 43, 1372–1386 RSC.
- Q. M. Yu, Mater. Sci. Forum, 2011, 663, 177–182 Search PubMed.
- H. S. Kang, Y. C. Kang, H. D. Park and Y. G. Shul, Appl. Phys. A: Mater. Sci. Process., 2005, 80, 347–351 CrossRef CAS.
- J. Yang, J. Gong, H. Fan and L. Yang, J. Mater. Sci., 2005, 40, 3725–3728 CrossRef CAS.
- J. S. Liao, D. Zhou, H. Y. You, H. R. Wen, Q. H. Zhou and B. Yang, Optik, 2013, 124, 1362–1365 CrossRef CAS.
- C. C. Mi, H. Y. Gao, F. Li and S. K. Xu, Colloids Surf., A, 2012, 395, 152–156 CrossRef CAS.
- D. M. Yang, G. G. Li, X. J. Kang, Z. Y. Cheng, P. A. Ma, C. Peng, H. Z. Lian, C. X. Li and J. Lin, Nanoscale, 2012, 4, 3450–3459 RSC.
- J. Sun, J. Lai, Z. Xia, X. Zhang, H. Liu and H. Du, Appl. Phys. B: Lasers Opt., 2012, 107, 827–831 CrossRef CAS.
- J. Y. Sun, X. Y. Zhang, Z. G. Xia and H. Y. Du, J. Electrochem. Soc., 2011, 158, J368–J371 CrossRef CAS.
- H. Yu, W. W. Zi, S. Lan, S. C. Gan, H. F. Zou, X. C. Xu and G. Y. Hong, Opt. Laser Technol., 2012, 44, 2306–2311 CrossRef CAS.
- W. W. Hu, Q. Q. Zhu, L. Y. Hao, X. Xu and S. Agathopoulos, Mater. Res. Bull., 2014, 51, 224–227 CrossRef CAS.
- Y. C. Tian, J. Solid State Light., 2014, 1, 11–25 CrossRef.
- J. Y. Sun, Q. M. Di and D. P. Cui, Mater. Res. Bull., 2014, 60, 201–205 CrossRef CAS.
- A. Aksay, D. M. Dabbs and M. Sarikaya, J. Am. Ceram. Soc., 1991, 74, 2342–2358 CrossRef.
- H. Schneider, R. X. Fischer and J. Schreuer, J. Am. Ceram. Soc., 2015, 98, 2948–2967 CrossRef CAS.
- G. Blasse, Prog. Solid State Chem., 1988, 18, 79–171 CrossRef CAS.
- B. Li, Y. H. Shi and S. J. Sun, J. Jilin Univ., Sci. Ed., 1996, 3, 87–90 Search PubMed.
- T. R. N. Kutty and M. Nayak, Mater. Chem. Phys., 2000, 65, 158–165 CrossRef CAS.
- L. Zhang, J. S. Wang, H. C. Yao and Z. J. Li, Mater. Lett., 2009, 63, 1175–1176 CrossRef CAS.
- R. X. Fischer, A. Gaede-Kohler, J. Birkenstock and H. Schneider, Int. J. Mater. Res., 2012, 103, 402–407 CrossRef CAS.
- R. X. Fischer and H. Schneider, Mullite, ed. H. Schneider and S. Komarneni, WILEY-VCH, Weinheim, 2005 Search PubMed.
- H. Schneider, J. Schreuer and B. Hildmann, J. Eur. Ceram. Soc., 2008, 28, 329–344 CrossRef CAS.
- R. F. Wei, H. Zhang, F. Li and H. Guo, J. Am. Ceram. Soc., 2012, 95, 34–36 CrossRef CAS.
- T. W. Kuo and T. M. Chen, J. Electrochem. Soc., 2010, 157, J216–J220 CrossRef CAS.
- C. K. Duan, C. C. Ko, G. H. Jia, X. Y. Chen and P. A. Tanner, Chem. Phys. Lett., 2011, 506, 179–182 CrossRef CAS.
- J. K. Park, M. A. Lim, C. H. Kim, H. D. Park and S. Y. Choi, J. Electrochem. Soc., 2003, 150, H246–H249 CrossRef CAS.
- H. Jiao and Y. Wang, J. Electrochem. Soc., 2009, 156, J117–J120 CrossRef CAS.
- H. Guo, H. Zhang, J. J. Li and F. Li, Opt. Express, 2010, 18, 27257–27262 CrossRef CAS PubMed.
- G. Zhang, J. Wang, Y. Chen and Q. Su, Opt. Lett., 2010, 35, 2382–2384 CrossRef CAS PubMed.
- M. Y. Yin, Y. G. Liu, L. F. Mei, M. S. Molokeev, Z. H. Huang and M. H. Fang, RSC Adv., 2015, 5, 73077–73082 RSC.
- M. Guan, H. Zheng, L. Mei, M. S. Molokeev, J. Xie, T. Yang, X. Wu, S. Huang, Z. Huang and A. Setlur, J. Am. Ceram. Soc., 2015, 98, 1182–1187 CrossRef CAS.
- F. W. Kang and M. Y. Peng, Dalton Trans., 2014, 43, 277–285 RSC.
- F. W. Kang, M. Y. Peng, S. H. Xu, Z. J. Ma, G. P. Dong and J. R. Qiu, Eur. J. Inorg. Chem., 2014, 8, 1373–1380 CrossRef.
- Q. F. Wang, Y. Liu, Y. Wang, W. X. Wang, Y. Wan, G. G. Wang and Z. G. Lu, J. Alloys Compd., 2015, 625, 355–361 CrossRef CAS.
- G. Blasse and B. C. Grabmeyer, Luminescent Materials, Springer-Verlag, Berlin, 1994 Search PubMed.
- D. W. Wen, H. Yang, G. H. Yang, J. X. Shi, M. M. Wu and Q. Su, J. Solid State Chem., 2014, 213, 65–71 CrossRef CAS.
- D. Cervantes-Vásquez, O. E. Contreras and G. A. Hirata, J. Lumin., 2013, 143, 226–232 CrossRef.
- S. Leyre, E. Coutino-Gonzalez, J. J. Joos, J. Ryckaert, Y. Meuret, D. Poelman, P. F. Smet, G. Durinck, J. Hofkens, G. Deconinck and P. Hanselaer, Rev. Sci. Instrum., 2014, 85, 123115 CrossRef CAS PubMed.
- X. J. Zhang, L. Huang, F. J. Pan, M. M. Wu, J. Wang, Y. Chen and Q. Su, ACS Appl. Mater. Interfaces, 2014, 6, 2709–2717 CAS.
|
This journal is © The Royal Society of Chemistry 2016 |
Click here to see how this site uses Cookies. View our privacy policy here.