DOI:
10.1039/C6RA03795J
(Communication)
RSC Adv., 2016,
6, 38494-38498
Synthesis and property of a Helwingia-structured nickel nitride/ nickel hydroxide nanocatalyst in hydrazine decomposition†
Received
10th February 2016
, Accepted 7th April 2016
First published on 11th April 2016
Abstract
Unique Helwingia-structured nickel nitride nanoparticles on nickel hydroxide nanosheets (H–Ni3N/Ni(OH)2) were prepared using hydrothermal synthesis of Ni(OH)2 nanosheets followed by partial phase transformation to Ni3N via controlled nitridation. The H–Ni3N/Ni(OH)2 was characterized for its structural information and studied for catalytic properties. It exhibited both good activity and excellent stability in aqueous phase and low temperature hydrazine decomposition, demonstrating its potential as a catalyst for the reaction. Mechanisms behind the catalytic property of the H–Ni3N/Ni(OH)2 structure were discussed based on careful kinetics studies and characterizations.
Introduction
Hydrazine can find important applications both as a liquid fuel and as a hydrogen storage medium due to its unique characteristics, in particular the capability of releasing large volumes of gases and generating hydrogen during decomposition. For instance, hydrazine has been widely used as a monopropellant in space applications utilizing its large gas products-to-hydrazine stoichiometry. Owing to its high hydrogen content (12.5 wt% in anhydrous hydrazine and 8 wt% in hydrazine hydrate), the hydrazine decomposition reaction has also been considered as a promising route for on-board hydrogen production and has attracted big research interest.1–4
Although the reaction is thermodynamically favoured, it can hardly occur by itself due to an activity energy barrier. In practice, catalyst materials are needed for promoting the reaction kinetics and/or controlling the product selectivity depending on the specific applications. Previous research efforts have led to the development of different types of materials, which can be primarily grouped into noble metal and non-noble transition metal-based catalysts. For instance, Ir/Al2O3 serves as one conventional catalyst for decomposition of hydrazine in monopropellant thrusters.5–7 Other noble metals, including Pt, Pd, and Rh, are also active catalysts for the reaction.8–13 Despite of their good property, the high price of these noble metals raises an inevitable cost issue for many applications. Non-noble transition metal catalysts, including Ni, Fe, and Co, can exhibit good activity in the reaction and thus have been intensively investigated.14–26 However, instability of these transition metals, caused by their susceptibility to oxidation and causing catalyst deactivation, remains a challenge. Because of the problems associated with both noble and non-noble metal catalysts, there is a desire to research new catalyst with improved property for hydrazine decomposition.
Recent studies with transition metal nitrides reported their interesting catalytic property in a number of reactions such as ammonia synthesis, carbon monoxide hydrogenation, and ethane hydrogenolysis.27–33 Mechanistic experiments discovered that the addition of nitrogen in metal nitrides induces stretch of lattice and increase in the metal–metal bond length. The lattice change together with the electron transfer effect between metal and nitrogen elements can result in contraction of the d-band of nitrides comparing to their metal counterparts, making them behave similarly to noble metals in the catalytic property. Nitrides of several metals, including cobalt, iron, and molybdenum, have been recently prepared and studied for hydrazine decomposition, which exhibited similar catalytic behaviour to Ir-based materials and suggested that metal nitrides could serve as a new group of catalyst for the reaction (Table S1†).34–41 However, all the studies were conducted for gas phase hydrazine decomposition. Their catalytic property for the reaction in liquid phase and under mild condition, which attracts more interest nowadays, still remains largely unknown.
In this study we report the synthesis of unique Helwingia-structured Ni3N/Ni(OH)2 nanomaterials, which are named H–Ni3N/Ni(OH)2 and consist of Ni3N nanoparticles converting from and positioning on the surface of Ni(OH)2 nanosheets, and the study of their catalytic property in liquid phase hydrazine decomposition. In brief, Ni(OH)2 nanosheets were first synthesized using a hydrothermal method, in which Ni acetate and hexamethylenetetramine (HMT) were dissolved in water and hydrolyzed at 120 °C for 12 h. The obtained Ni(OH)2 nanosheets were then treated at 250 °C for 20 h under NH3 atmosphere for producing the H–Ni3N/Ni(OH)2 structure (see more experimental details in the ESI†).
Results and discussion
Fig. 1a shows schematic illustration of the H–Ni3N/Ni(OH)2 growing process, which involves Ni3N nuclei generation resultant of ammonia reaction with surface Ni(OH)2 and their continual growth into bigger nanoparticles with reaction time. Fig. 1b shows TEM of the as-synthesized Ni(OH)2 nanosheets, which were layered double hydroxide (LDH) material with two polymorph. The X-ray diffraction (XRD) pattern indicated that the Ni(OH)2 nanosheets were mostly in the α phase (Fig. S1†). The peaks located at 10.6°, 13.8°, 20.8°, 27.8°, and 34.9° can be indexed to the (003), (001), (006), (002) and (101) planes. The product also contained a small fraction of β phase, evidenced by the small peaks at 19.2°, 31°, 33.3°, and 62.2° assignable to the (001), (100), (101) and (111) diffractions.42–49 Upon being treated under the nitridation condition, the Ni(OH)2 nanosheets were found with growth of Ni3N nanoparticles on the surface (Fig. 1c–e). Ni3N nanoparticles already appeared after 2 h of reaction, evidenced by their darker image contrast comparing to the Ni(OH)2. More and bigger Ni3N particles were obtained along with the reaction time, suggesting continual nucleation and growth of the Ni3N under the reaction condition. The TEM observations were consistent with the XRD data (Fig. S2†), which showed a new set of diffractions peaks besides those for Ni(OH)2 after the reaction. These diffraction peaks were assignable to the Ni3N phase and grew continuously with reaction time. In the meantime the Ni(OH)2 diffractions had decreased intensity, confirming that the Ni3N was resultant of Ni(OH)2 conversion.
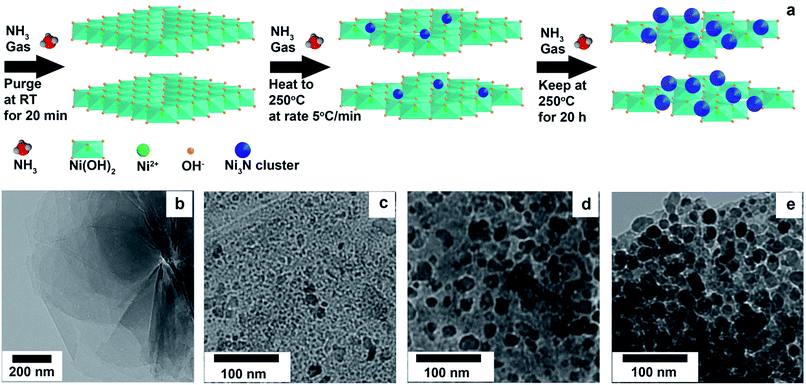 |
| Fig. 1 (a) Schematics of Ni3N formation on Ni(OH)2 nanosheets during nitridation process and TEM images of (b) as-prepared Ni(OH)2 nanosheets and H–Ni3N/Ni(OH)2 nanostructures after (c) 2 h, (d) 8 h, and (e) 20 h of nitridation at 250 °C under NH3 atmosphere. | |
High-resolution TEM (HRTEM) characterizations of individual nanoparticles showed distinct lattice fringes from that of the nanosheets (Fig. 2a–c). The measured d-spacing of 2.0 Å matched well with that for the (111) planes of hexagonal close packed (hcp) Ni3N, whereas the nanosheets showed lattice fringes corresponding to the (101) and (100) of Ni(OH)2. All the XRD peaks can be assigned to either Ni3N or Ni(OH)2 phases, suggesting the product composed of primarily Ni3N nanoparticles on the Ni(OH)2 sheets.50–54 Fig. 2e showed the X-ray photoelectron spectrum (XPS) of the freshly made sample, from which the Ni 2p3/2 spectra could be deconvoluted into several peaks. The peak located at 852.6 eV with corresponding satellite peak at 858.5 eV confirmed the presence of Ni1+ in Ni3N. The peaks at 856.4 eV and 863.8 eV were attributed to Ni2+ in Ni(OH)2 existing on the surface. Besides, there were two peaks at 854.8 and 861.5 eV, which were assigned to Ni2+ in NiO and could be resultant of slight surface oxidation of Ni3N nanoparticles after exposure to air.55 However the NiO content was little, evidenced by no observable XRD diffractions.
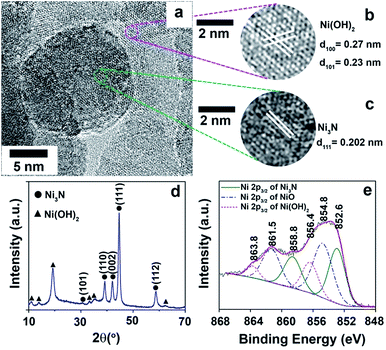 |
| Fig. 2 (a–c) HRTEM, (d) XRD pattern, and (e) XPS spectrum of as-prepared H–Ni3N/Ni(OH)2. | |
The catalytic property of the H–Ni3N/Ni(OH)2 was studied for hydrazine decomposition in a semi-batch flask reactor which contained 30 mg of catalyst powders dispersed in 3 ml of aqueous solution of 0.1 M hydrazine and was connected with gas burette for volumetrically measuring the gas generation. Fig. 3a showed the gas products-to-hydrazine ratio, nN2+H2/nN2H4,0, as a function of time at different reaction temperature. The initial gas production rates, −r′N2+H2,0, were calculated based on the nN2+H2/nN2H4,0-t curves and plotted against the reaction temperature (Fig. 3b). The H–Ni3N/Ni(OH)2 exhibited an initial mass activity of 13.9 μmol s−1 g−1 at 30 °C, which had a significant increase to 86.8 μmol s−1 g−1 at 70 °C, implying improved kinetics with reaction temperature. For comparison, Ni/C nanoparticle catalyst was prepared and tested under a same reaction condition, and exhibited significantly less values of 3.9 and 20.3 μmol s−1 g−1 at 30 and 70 °C respectively (Fig. S3, S4† and 3b). The activation energy using the H–Ni3N/Ni(OH)2 was determined to be 41.2 kJ mol−1 from the Arrhenius plot, which was close to that using the Ni/C (36.9 kJ mol−1). The ratio between hydrogen and nitrogen was quantified to be 1.49 by analysing the gas products using gas chromatography (Fig. S5†), which represented approximately 50% selectivity towards hydrogen generation. The low selectivity was in consistence with that of gas phase hydrazine decomposition on metal nitrides in previous studies and attributed to significant ammonia production.35,39 However no ammonia was detected using GC, which could readily dissolve in the reaction solution after generation.
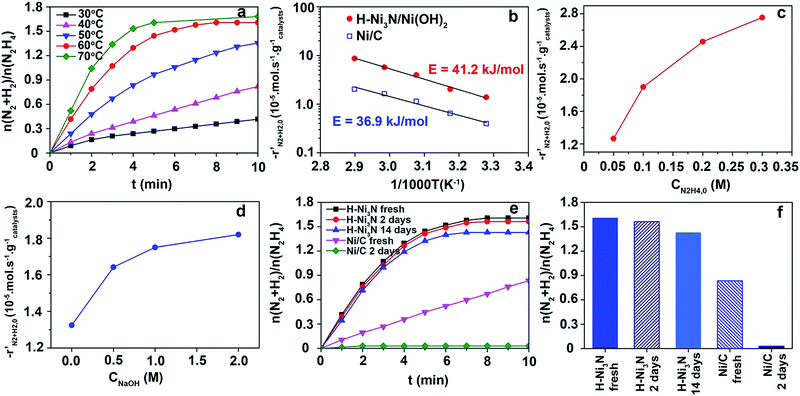 |
| Fig. 3 (a) Gas products-to-hydrazine ratio as function of reaction time and (b) Arrhenius plots using the H–Ni3N/Ni(OH)2 catalyst in 0.1 M hydrazine and 1 M NaOH, effects of (c) hydrazine and (d) NaOH concentration on the activity for hydrazine decomposition reaction using the H–Ni3N/Ni(OH)2 catalyst at 60 °C, and stability experiments using the aged H–Ni3N/Ni(OH)2 for measuring the (e) nN2+H2/nN2H4,0-t plots and (f) nN2+H2/nN2H4,0 values after 10 min of reaction in 0.1 M hydrazine and 1 M NaOH at 60 °C. The amount of catalyst was 30 mg for all experiments. | |
The hydrazine decomposition was found to increase monotonously with concentrations of hydrazine and sodium hydroxide (Fig. S6, S7,† 3c and d). The −r′N2+H2,0 was determined to be 41.6 μmol s−1 g−1 with 0.05 M hydrazine at 60 °C, and had a significant increase to 78.8 μmol s−1 g−1 with a higher hydrazine concentration of 0.3 M. At the same temperature, the −r′N2+H2,0 was limited to a low value of 36.2 μmol s−1 g−1 in absence of NaOH, whereas a higher 57.5 μmol s−1 g−1 was obtained when 1 M NaOH was added to the reaction mixture. Previous studies have proposed possible reaction mechanism for the catalytic hydrazine decomposition and suggested that the first deprotonation of adsorbed hydrazine on active sites could be rate-determining.9,11,15 According to the Le Chatelier's principle, more adsorbed hydrazine molecules are resulted with a higher hydrazine concentration, which helps to promote their deprotonation and finally the overall reaction rates.56 The promoting effect of NaOH on kinetics of the hydrazine decomposition reaction has also been extensively studied in previous literatures, in which NaOH was found to shift the equilibrium between hydrazine molecules and N2H5+ ions to the hydrazine side.16,57,58
The stability of the H–Ni3N/Ni(OH)2 was evaluated by testing the catalyst after elongated time of exposure to air and investigating the hydrazine decomposition activity decay. Fig. 3c and f showed the nN2+H2/nN2H4,0-t plots and the measured nN2+H2/nN2H4 values using the H–Ni3N/Ni(OH)2 aged for 2 and 14 days. The data for the fresh H–Ni3N/Ni(OH)2 and the Ni/C catalysts were also included for comparison. Only slight decreases in the activity was observed for the H–Ni3N/Ni(OH)2, indicating excellent stability of the catalytic structure. In sharp contrast, the Ni/C became almost inactive after 2 days. The rapid activity loss of the Ni/C has been attributed to instability of Ni, which is susceptible to oxidation and can readily transform to inactive NiO. TEM and HRTEM characterizations of the aged H–Ni3N/Ni(OH)2 found distinct behaviour of the Ni3N particles (Fig. 4a and b). Only very thin and amorphous NiO layers were observed on the Ni3N surface even after 14 days of air exposure, revealing its good resistance to oxidation. Therefore hydrazine molecules could still diffuse through the NiO layer and reach the Ni3N surface for reaction. Previous studies have also reported excellent chemical stability of Ni3N phase and attributed it to its ordered lattice structure and high bond strength, which can effectively suppress the surface oxidation and the permeation of oxygen into the lattice.51,53 The aged H–Ni3N/Ni(OH)2 still showed large fraction of Ni3N on the surface, evidenced by the Ni1+ peak on the XPS spectrum (Fig. 4c). Comparing to the spectrum of the fresh H–Ni3N/Ni(OH)2, the NiO peak only had small increase in the relative intensity comparing to the Ni1+ peak. Thus the excellent stability of the H–Ni3N/Ni(OH)2 can be attributed to the good chemical inertness of Ni3N, which maintained its chemical integrity and consequently the catalytic activity.
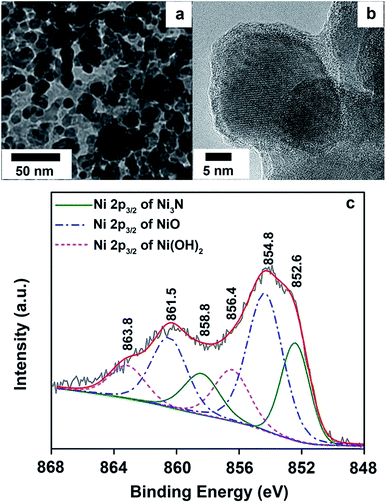 |
| Fig. 4 (a) TEM, (b) HRTEM, and (c) XPS spectrum of the H–Ni3N/Ni(OH)2 after 14 days of air exposure. | |
Conclusions
In summary, the Helwingia-structured Ni3N-nanoparticles-on-Ni(OH)2-nanosheets catalyst has been prepared and studied for the hydrazine decomposition reaction in aqueous solution and under mild condition. Interestingly, the H–Ni3N/Ni(OH)2 catalyst exhibited promoted activity and much improved stability comparing to the Ni/C. The good activity could be associated with its low activation energy, which was measured to be 41.2 kJ mol−1. The excellent stability was attributed to the good resistance of Ni3N against oxidation, which was evidenced by HRTEM and XPS characterizations of aged catalyst and showed only very limited surface oxide formation. The results demonstrated excellent property of the unique H–Ni3N/Ni(OH)2 structure and point to the possibility of using metal nitrides-based nanocatalysts for liquid phase and low temperature hydrazine decomposition.
Acknowledgements
This work was supported by the University of Akron fund (Z. P.). The HRTEM data were obtained at the (cryo) TEM facility at the Liquid Crystal Institute, Kent State University, supported by the Ohio Research Scholars Program Research Cluster on Surfaces in Advanced Materials. The authors would like to thank Dr Min Gao for technical support with the HRTEM experiments.
References
- H.-L. Jiang, S. K. Singh, J.-M. Yan, X.-B. Zhang and Q. Xu, ChemSusChem, 2010, 3, 541–549 CrossRef CAS PubMed.
- Q. Xiao, J. Li, J. Han, K.-X. Xu, Z.-X. Huang, J. Hu and J.-J. Sun, RSC Adv., 2015, 5, 71139–71143 RSC.
- Q.-L. Zhu and Q. Xu, Energy Environ. Sci., 2015, 8, 478–512 CAS.
- S. K. Singh and Q. Xu, Catal. Sci. Technol., 2013, 3, 1889–1900 CAS.
- N. K. Janjua, N. Firdous, A. S. Bhatti and Z. S. Khan, Appl. Catal., A, 2014, 479, 9–16 CrossRef CAS.
- S. J. Cho, J. Lee, Y. S. Lee and D. P. Kim, Catal. Lett., 2006, 109, 181–187 CrossRef CAS.
- J. Contour and G. Pannetier, J. Catal., 1972, 24, 434–445 CrossRef CAS.
- S. K. Singh, X. Zhang and Q. Xu, J. Am. Chem. Soc., 2009, 131, 9894–9895 CrossRef CAS PubMed.
- F.-Z. Song, Q.-L. Zhu and Q. Xu, J. Mater. Chem. A, 2015, 3, 23090–23094 CAS.
- S. K. Singh and Q. Xu, Chem. Commun., 2010, 46, 6545–6547 RSC.
- J. Wang, X.-B. Zhang, Z.-L. Wang, L.-M. Wang and Y. Zhang, Energy Environ. Sci., 2012, 5, 6885–6888 CAS.
- W. Luo, P. Zhao, N. Cao and G. Cheng, J. Mater. Chem. A, 2015, 3, 12468–12475 Search PubMed.
- J. B. Yoo, H. S. Kim, S. H. Kang, B. Lee and N. H. Hur, J. Mater. Chem. A, 2014, 2, 18929–18937 CAS.
- L. He, B. Liang, L. Li, X. Yang, Y. Huang, A. Wang, X. Wang and T. Zhang, ACS Catal., 2015, 5, 1623–1628 CrossRef CAS.
- J. Wang, Y. Li and Y. Zhang, Adv. Funct. Mater., 2014, 24, 7073–7077 CAS.
- L. He, Y. Huang, A. Wang, X. Wang and T. Zhang, AIChE J., 2013, 59, 4297–4302 CrossRef.
- L. He, Y. Huang, A. Wang, X. Wang, X. Chen, J. J. Delgado and T. Zhang, Angew. Chem., Int. Ed., 2012, 51, 6191–6194 CrossRef CAS PubMed.
- K. V. Manukyan, A. Cross, S. Rouvimov, J. Miller, A. S. Mukasyan and E. E. Wolf, Appl. Catal., A, 2014, 476, 47–53 CrossRef CAS.
- W. Gao, C. Li, H. Chen, M. Wu, S. He, M. Wei, D. G. Evans and X. Duan, Green Chem., 2014, 16, 1560–1568 RSC.
- H.-L. Wang, J.-M. Yan, S.-J. Li, X.-W. Zhang and Q. Jiang, J. Mater. Chem. A, 2015, 3, 121–124 CAS.
- D. G. Tong, W. Chu, P. Wu, G. F. Gu and L. Zhang, J. Mater. Chem. A, 2013, 1, 358–366 CAS.
- D. G. Tong, D. M. Tang, W. Chu, G. F. Gu and P. Wu, J. Mater. Chem. A, 2013, 1, 6425–6432 CAS.
- J. Zhang, Q. Kang, Z. Yang, H. Dai, D. Zhuang and P. Wang, J. Mater. Chem. A, 2013, 1, 11623–11628 CAS.
- S. K. Singh, A. K. Singh, K. Aranishi and Q. Xu, J. Am. Chem. Soc., 2011, 133, 19638–19641 CrossRef CAS PubMed.
- H. Yang, X. Zhong, Z. Dong, J. Wang, J. Jin and J. Ma, RSC Adv., 2012, 2, 5038–5040 RSC.
- D. G. Tong, W. Chu, P. Wu and L. Zhang, RSC Adv., 2012, 2, 2369–2376 RSC.
- R. Michalsky, A. M. Avram, B. A. Peterson, P. H. Pfromm and A. A. Peterson, Chem. Sci., 2015, 1–10 Search PubMed.
- W. Yang, S. Rehman, X. Chu, Y. Hou and S. Gao, ChemNanoMat, 2015, 1, 376–398 CrossRef CAS.
- M.-S. Balogun, W. Qiu, W. Wang, P. Fang, X. Lu and Y. Tong, J. Mater. Chem. A, 2015, 3, 1364–1387 CAS.
- B. Cao, G. M. Veith, R. E. Diaz, J. Liu, E. A. Stach, R. R. Adzic and P. G. Khalifah, Angew. Chem., Int. Ed., 2013, 52, 10753–10757 CrossRef CAS PubMed.
- W.-F. Chen, J. T. Muckerman and E. Fujita, Chem. Commun., 2013, 49, 8896–8909 RSC.
- W. F. Chen, K. Sasaki, C. Ma, A. I. Frenkel, N. Marinkovic, J. T. Muckerman, Y. Zhu and R. R. Adzic, Angew. Chem., Int. Ed., 2012, 51, 6131–6135 CrossRef CAS PubMed.
- A.-M. Alexander and J. S. J. Hargreaves, Chem. Soc. Rev., 2010, 39, 4388–4401 RSC.
- R. Brayner, G. Djéga-Mariadassou, G. M. da Cruz and J. A. J. Rodrigues, Catal. Today, 2000, 57, 225–229 CrossRef CAS.
- M. Zheng, X. Chen, R. Cheng, N. Li, J. Sun, X. Wang and T. Zhang, Catal. Commun., 2006, 7, 187–191 CrossRef CAS.
- M. Zheng, Y. Shu, J. Sun and T. Zhang, Catal. Lett., 2008, 121, 90–96 CrossRef CAS.
- X. Chen, T. Zhang, L. Xia, T. Li, M. Zheng, Z. Wu, X. Wang, Z. Wei, Q. Xin and C. Li, Catal. Lett., 2002, 79, 21–25 CrossRef CAS.
- J. A. J. Rodrigues, G. M. Cruz, G. Bugli, M. Boudart and G. Djéga-Mariadassou, Catal. Lett., 1997, 45, 1–3 CrossRef CAS.
- X. Chen, T. Zhang, M. Zheng, Z. Wu, W. Wu and C. Li, J. Catal., 2004, 224, 473–478 CrossRef CAS.
- P. Zhang, X. Wang, W. Wang, X. Lei and H. Yang, J. Mater. Chem. A, 2015, 3, 6464–6469 CAS.
- H. Cheng, Y. Huang, A. Wang, X. Wang and T. Zhang, Top. Catal., 2009, 52, 1535–1540 CrossRef CAS.
- G. Jiang, M. Zhang, X. Li and H. Gao, RSC Adv., 2015, 5, 69365–69370 RSC.
- S. Jiang, Z. Gui, G. Chen, D. Liang and J. Alam, ACS Appl. Mater. Interfaces, 2015, 7, 14603–14613 CAS.
- Z. Li, J. Han, L. Fan, M. Wang, S. Tao and R. Guo, Chem. Commun., 2015, 51, 3053–3056 RSC.
- X. Ma, J. Liu, C. Liang, X. Gong and R. Che, J. Mater. Chem. A, 2014, 2, 12692–12696 CAS.
- H. B. Li, M. H. Yu, F. X. Wang, P. Liu, Y. Liang, J. Xiao, C. X. Wang, Y. X. Tong and G. W. Yang, Nat. Commun., 2013, 4, 1894 CrossRef CAS PubMed.
- J. T. Zhang, S. Liu, G. L. Pan, G. R. Li and X. P. Gao, J. Mater. Chem. A, 2014, 2, 1524–1529 CAS.
- Z. Wu, X.-L. Huang, Z.-L. Wang, J.-J. Xu, H.-G. Wang and X.-B. Zhang, Sci. Rep., 2014, 4, 3669 Search PubMed.
- Y. Zhu, C. Cao, S. Tao, W. Chu, Z. Wu and Y. Li, Sci. Rep., 2014, 4, 5787 CrossRef CAS PubMed.
- Y. Yu, W. Gao, Z. Shen, Q. Zheng, H. Wu, X. Wang, W. Song and K. Ding, J. Mater. Chem. A, 2015, 3, 16633–16641 CAS.
- M. Shalom, D. Ressnig, X. Yang, G. Clavel, T. P. Fellinger and M. Antonietti, J. Mater. Chem. A, 2015, 3, 8171–8177 CAS.
- G. Clavel, V. Molinari, A. Kraupner and C. Giordano, Chem.–Eur. J., 2014, 20, 9018–9023 CAS.
- F. Gillot, J. Oró-Solé and M. R. Palacín, J. Mater. Chem., 2011, 21, 9997–10002 RSC.
- Y. Jia, H. Pan, H. Meng, H. Liu, Z. Wang, X. Li, L. Zhu, P. Chai and C. Gong, RSC Adv., 2015, 5, 14061–14064 RSC.
- K. Xu, P. Chen, X. Li, Y. Tong, H. Ding, X. Wu, W. Chu, Z. Peng, C. Wu and Y. Xie, J. Am. Chem. Soc., 2015, 137, 4119–4125 CrossRef CAS PubMed.
- K. Patil and T. Rattan, Inorganic Hydrazine Derivatives: Synthesis, Properties and Applications, John Wiley & Sons, Ltd, UK, 2014 Search PubMed.
- Y.-J. Zhong, H.-B. Dai, Y.-Y. Jiang, D.-M. Chen, M. Zhu, L.-X. Sun and P. Wang, J. Power Sources, 2015, 300, 294–300 CrossRef CAS.
- D. Bhattacharjee, K. Mandal and S. Dasgupta, J. Power Sources, 2015, 287, 96–99 CrossRef CAS.
Footnote |
† Electronic supplementary information (ESI) available: Experimental details and characterizations. See DOI: 10.1039/c6ra03795j |
|
This journal is © The Royal Society of Chemistry 2016 |
Click here to see how this site uses Cookies. View our privacy policy here.