DOI:
10.1039/C6RA03429B
(Paper)
RSC Adv., 2016,
6, 33419-33425
Synthesis and characterization of highly defective mesoporous carbon and its potential use in electrochemical sensors
Received
5th February 2016
, Accepted 20th March 2016
First published on 22nd March 2016
Abstract
A highly defective mesoporous carbon (DMC) was synthesized via a facile mass producible method for the fabrication of electrochemical sensing devices. The preparation of DMC with desired structural defects was conducted using nanosilica as a hard template, sucrose as a carbon source, and KNO3 as a defect causing agent. During the carbonization process, the oxygen gas released from the decomposition of KNO3, which was coated on a nanosilica template, reacts with carbon atoms and provides a highly defective mesoporous carbon. Raman spectroscopy was used to evaluate defect density while the porous structure and surface morphology of the synthesized materials were investigated with N2-adsorption/desorption, XRD, SEM and TEM techniques. Cyclic voltammetry and electrochemical impedance spectroscopy studies were performed on a fabricated renewable mesoporous carbon paste electrode (MCPE). The highly defective MCPE showed a superior improvement in heterogeneous electron transfer rate of different redox systems when compared with electrodes based on graphite, multi walled carbon nanotubes, and graphene. The experimental findings are valuable for the design and fabrication of efficient carbon based electrochemical sensing devices.
1. Introduction
During the last two decades, carbon-based nanomaterials such as carbon nanotubes, graphene, mesoporous carbon, and carbon quantum dots have been receiving great interest due to their unique properties of large surface-to-volume ratio, good electrical & thermal conductivity, and mechanical strength, which make them suitable for applications in various fields such as water purification,1,2 energy storage,3–6 catalysis,7,8 chemical & electrochemical sensing9–17 and so on.
Structural defects have a crucial influence on the properties of carbon nanostructures and are inevitably generated during production processes or intentionally induced by chemical treatments and ion irradiation.18–20 The presence of defects detrimentally affects the electrical and thermal conductivity, mechanical strength and transparency.20–22 On the other hand, the enhanced reactivity of defective carbon nanomaterials was reported to be beneficial for energy storage and sensing applications. For example, the results of theoretical efforts based on different techniques predicted favorable adsorption of Li ions,23,24 Na ions,25,26 and metallic nanoclusters27,28 on the surface of defective graphene. Also, the beneficial impact of structural defect on the electrochemical activity was proved by study of heterogeneous electrochemical reactions of ferrocenemethanol,29 oxygen,30 and nitrate31 at the surface of nanocarbon based electrodes.
Recently, mesoporous carbons, classified as carbon nanostructures, have been of particular interest for the electrochemical applications32–40 owing to their high surface area, high specific pore volume, tunable pore diameters in the mesopore range, and wide electrochemical stability window. For instances, Ren et al. reported a glassy carbon electrode modified with mesoporous carbon for the direct electrocatalytic and simultaneous determination of four DNA bases.38 In another work, Hosseini et al. constructed a NADH sensor based on gold nanoparticle modified mesoporous carbon composite.39 In addition, Liu et al. showed that the electrode modified with CeO2-embedded ordered mesoporous carbon has strong electrocatalytic effect towards the oxidation of hydrazine.40
In the present study; contrary to other published works;41–43 we introduce a simple, cost effective and mass producible method for synthesize of mesoporous carbon with controllable defect density. In order to examine the electrochemical activity of synthesized materials, cyclic voltammetry and electrochemical impedance spectroscopy were performed at the surface of renewable MCPEs and the obtained results were compared with those of the conventional graphite, carbon nanotube and graphene paste electrodes.
2. Experimental
2.1. Materials
Commercial grade of fumed silica (N-20; average particle size: 15 nm; surface area: 185 m2 g−1) was supplied from Wacker, Germany. Graphite (extra pure; particle size < 50 μM), multiwall carbon nanotubes (purity > 99%; length 50 μM) and graphene (purity > 99%; length 5–15 μM) were provided by Merck, NanoLab Inc. and XG Sciences respectively. Paraffin oil was of analytical reagent grade and was purchased from Samchun Chemical Co., Ltd., South Korea. All other chemicals were of analytical reagent grade and were used as received.
2.2. Synthesis of defective mesoporous carbon (DMC)
DMC was synthesized using nanosilica as a hard template, sucrose as a carbon precursor, and KNO3 as a defect causing agent. Typically, 2 grams of sucrose and 0–5.0 grams of KNO3 were dissolved in 100 ml deionized water and then 4 grams of nanosilica was added. The resultant mixture was stirred in room temperature for 2 hours and then dried in 80 °C oven overnight. After precarbonization at 140 °C for 3 hours, the obtained solids were carbonized at 800 °C for 1 h under Ar flow with a heating rate of 5 min−1. Finally, after etching the template by reflux at 80 °C in 1 M NaOH solution, the desired carbon powders were washed with copious amounts of deionized water and dried at 100 °C. Corresponding to different addition amounts of KNO3 (0, 1.5, 3.0, 4.0, 5.0 g), the final products were denoted as DMC-1, DMC-2, DMC-3, DMC-4 and DMC-5, respectively.
2.3. Characterization methods
The structures of the samples were characterized by Raman spectroscopy (Almega thermo Nicolet dispersive Raman spectrometer, excited by a 532 nm laser), SEM (Tescan Vega microscope, 20 kV) and TEM (JEM-2100, 200 kV). Powder X-ray diffraction (XRD) patterns were recorded on Bruker AXS-D8 Advance diffractometer (40 kV, 30 mA) using Ni-filtered Cu Kα radiation. N2-adsorption/desorption isotherms were measured at 77 K, using a Belsorp Mini II analyzer. Samples were degassed at 523 K for 8 h before measurements. Specific surface areas were calculated using the Brunauer–Emmett–Teller (BET) model.44 Pore volumes were estimated at a relative pressure of 0.94 (P/P0), assuming full surface saturation with nitrogen. The electrochemical measurements were carried out by the potentiostat/galvanostat (SP150, Biologic, France). A traditional three-electrode system was used including carbon paste electrodes as the working electrode, Ag/AgCl electrode (KCl 3 M) as the reference electrode and platinum wire as the auxiliary electrode.
2.4. Preparation of working electrodes
In order to study electrochemical behavior of synthesized materials, the appropriate carbon paste electrodes were constructed. The desired MCPEs were prepared by hand-mixing of graphite powder, carbon nanomaterials, and mineral oil in a mortar and pestle for about 30 minute. The obtained paste composite mixture was packed firmly into one end of a polyamide tube (diameter 2.1 mm). The electrical contact was provided by inserting a copper wire into the carbon paste. The DMC modified electrodes were constructed by mixing 0.15 g of DMC materials, 0.35 g of graphite powder, and 0.5 g of paraffin oil, while for achieving similar homogeneity, the graphene and MWCNT modified electrodes was prepared by mixing of 0.55, 0.15 and 0.30 g graphite powder, carbon nanostructure and mineral oil, respectively. The conventional graphite paste electrode was prepared by mixing of 0.75 g graphite and 0.25 g mineral oil for the sake of comparison. When necessary, a new surface of electrodes was obtained by pushing an excess of the paste into the cavity of the tube then polished by rubbing on a weighing paper.
3. Results and discussion
3.1. Structural and morphology characterization
Thanks to decomposition of KNO3 at temperature of 650–790 °C,45 we used KNO3 as defect causing agent. During carbonization process, the oxygen gas released from the decomposition of KNO3, which is coated on nanosilica template, reacts with carbon atoms and provides a defective mesoporous carbon. It is therefore expected to increase the number of point defects (vacancies in carbon lattice) in final products by increasing the amount of added KNO3.
Raman spectroscopy is a powerful technique widely used to distinguish structural defects of carbon materials. Typically, the Raman spectrum of carbon based materials consists of two predominant G and D bands. The G band at around 1590 cm−1 is assigned to the E2g phonon of stretching vibration modes of C
C bonds of typical graphite layers, while D band at around 1390 cm−1 is attributed to the breathing mode of aromatic rings arising due to the defect in the sample.46,47 In order to examine the defect extent of synthesized carbons, Raman spectra were taken and are shown in the Fig. 1. As shown in the figure, ID/IG value for DMC-1, DMC-2, DMC-3, DMC-4 and DMC-5 was calculated as 0.85, 1.1, 1.35, 1.55 and 1.6 respectively. Along with increasing the ID/IG, the sharpness of the D and G bands were decreased. The obtained results confirm that KNO3 act as defect causing agent at carbonization step. Therefore the preparation of mesoporous carbon with different defect density is easily accessible by adding various amounts of KNO3.
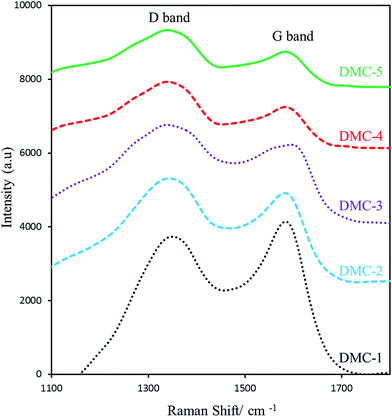 |
| Fig. 1 Raman spectra of synthesized defective mesoporous carbons. | |
The porosity of the synthesized materials was analyzed by N2 adsorption/desorption technique. As shown in Fig. 2, the N2 adsorption/desorption isotherm of the nanosilica template belongs to a type II suggesting its nonporous structure, whereas DMC-1, DMC-4 and DMC-5 similarly are of typical type IV isotherms demonstrating mesoporous structure of synthesized materials. The mean pore size and specific surface area of synthesized carbons was estimated from the adsorption branch by BJH and BET models respectively and the mean pore size of 14.1, 14.8, 14.9 nm and specific surface area of 1060, 1120, 1140 m2 g−1 were calculated respectively for DMC-1, DMC-4 and DMC-5.
 |
| Fig. 2 Adsorption/desorption isotherms of defective mesoporous carbons. | |
As shown in the Fig. 3, wide angle XRD patterns of synthesized materials display two peaks around 2θ = 24, 42 indexed to (0 0 2) and (1 0 0) diffraction patterns of typical graphite, respectively. The relatively broad peaks attributed to defective structure of synthesized materials. The interlayer spacing (d002) of DMC-1, DMC-4 and DMC-5 was calculated by Bragg's equation (nλ = 2d
sin
θ) and was determined as 0.357, 0.366 and 0.368 nm respectively. The obtained results indicate that the interlayer distance slightly increased by increasing defect density.
 |
| Fig. 3 Powder XRD pattern of defective mesoporous carbons. | |
The morphology and pore structure of highly defective mesoporous carbon was examined by SEM and TEM. The representative SEM images of DMC-5 are shown in Fig. 4a and b. While the image with low magnification (Fig. 4a) demonstrates aggregate microparticles, the high resolution imaging on the surface (Fig. 4b) clearly proves porous nature of synthesized material. The internal pore structure of DMC-5 was observed by TEM imaging. As revealed in Fig. 4c and d, many three dimensionally interconnected mesopores are randomly located to construct a loosely packed nanostructure. The obtained results are in agreement with that obtained from nitrogen adsorption/desorption analysis.48,49
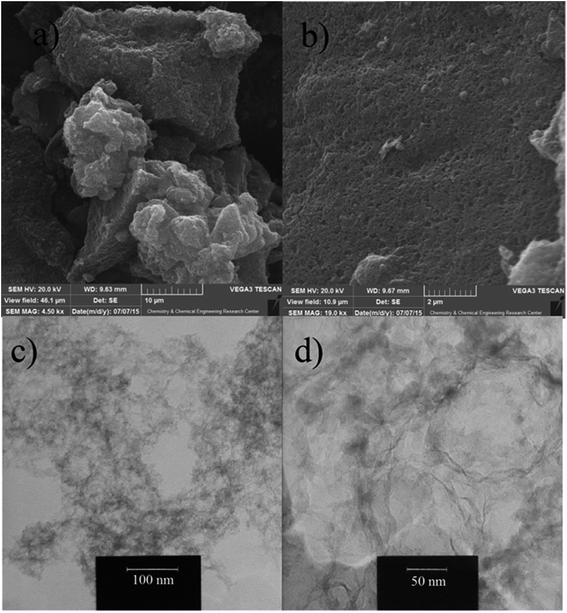 |
| Fig. 4 SEM (a and b) and TEM (c and d) images of DMC-5. | |
3.2. Electrochemical characterization
Electrochemical behavior of prepared paste electrodes was investigated by cyclic voltammetry and electrochemical impedance spectroscopy in Fe(CN)63−/4− solution as an defect sensitive electrochemical probe. The obtained cyclic voltammograms are illustrated in Fig. 5a. A couple of well-resolved peaks were observed for all the electrodes. However, significant differences were observed for peak to peak potential separation (ΔEp) and peak current (Ip). As shown in the Table 1, the ΔEp value for DMC-1, DMC-2, DMC-3, DMC-4 and DMC-5 paste electrodes were calculated as 110, 76, 71, 60 and 60 mV, respectively, suggesting that increasing defect density significantly improved electron transfer kinetic. At the same experimental situation, ΔEp for bare graphite, MWCNT, and graphene paste electrodes were calculated as 116, 96 and 82 mV, respectively. The obtained results demonstrate superior electron transfer kinetics at the surface of highly defective mesoporous carbons (DMC-4 & DMC-5) electrodes. Also the effective heterogeneous electron transfer rate constants (K0) quantitatively were determined by fitting of simulated CVs to the experimentally obtained data using EC-lab version 10.40. As mentioned in the Table 1, while increasing the density of structural defects, a remarkable improvement was observed in the effective heterogeneous electron transfer (K0) constant. The obtained value for K0 at the surface of highly defective mesoporous carbons (DMC-4 & DMC-5) were evaluated as about 0.42 cm s−1 which is approximately 145, 75 and 50 times higher in magnitude than graphite, MWCNT and graphene respectively. At the same time along with increasing effective heterogeneous rate constant, the CVs also showed the enhanced current response, indicating increased electrochemical active sites of defective mesoporous carbons. It is worth mentioning that the obtained K0 (0.42 cm s−1) at the surface of highly defective mesoporous carbon presented in this work is higher than those of other reported carbon based electrodes such as edge plane HOPG (0.10 cm s−1),50 SWCNT (0.003 cm s−1),51 and glassy carbon (0.029 cm s−1).52
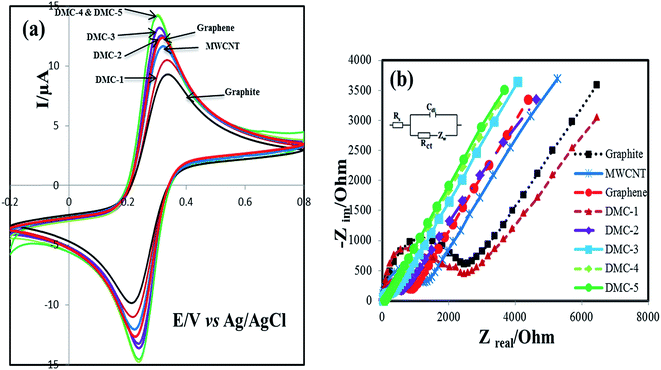 |
| Fig. 5 (a) Cyclic voltammograms (second scan) (b) Nyquist plots for 1 mM Fe(CN)63−/4− in a solution containing of 1 M KCl at the surface of prepared electrodes. Scan rate: 100 mV s−1; EIS condition: frequency range: 200 kHz to 0.1 Hz; perturbation amplitude: 5 mV. Inset of (b) is the equivalent Randles circuit compatible with the Nyquist diagrams. | |
Table 1 The obtained parameters from cyclic voltammetry and EIS studies
Electrode |
Ipa |
Ipc |
Peak separation (mV) |
Effective K0 (cm s−1) |
Active surface area (mm2) |
Charge transfer resistance (ohm) |
Graphite |
10.5 |
10.8 |
110 |
(2.87 ± 0.25) × 10−3 |
3.22 |
(2.19 ± 0.19) × 103 |
MWCNT |
12.8 |
12.9 |
94.1 |
(5.56 ± 0.97) × 10−3 |
3.58 |
(1.01 ± 0.17) × 103 |
Graphene |
13.1 |
13.2 |
82.1 |
(9.15 ± 0.97) × 10−3 |
3.52 |
(7.50 ± 1.30) × 102 |
DMC-1 |
12.7 |
13.0 |
107 |
(3.10 ± 0.70) × 10−3 |
3.46 |
(1.71 ± 0.22) × 103 |
DMC-2 |
13.8 |
13.9 |
71.3 |
(1.25 ± 0.72) × 10−2 |
3.77 |
(5.90 ± 0.95) × 102 |
DMC-3 |
15.0 |
15.4 |
68.8 |
(3.05 ± 1.32) × 10−2 |
3.90 |
(2.05 ± 0.75) × 102 |
DMC-4 |
16.3 |
16.4 |
60.4 |
(4.14 ± 1.71) × 10−1 |
4.19 |
(5.02 ± 1.01) × 101 |
DMC-5 |
16.5 |
16.3 |
60.2 |
(4.29 ± 1.95) × 10−1 |
4.20 |
(3.54 ± 1.04) × 101 |
The obtained EIS curves of constructed electrodes are shown in Fig. 5b. As depicted in this figure, the obtained curves include a semicircular part and a linear part. The semicircle observed at high frequencies values in the Nyquist plots is related to the charge-transfer limiting processes, and its diameter corresponds to the charge transfer resistance (Rct) of the redox probe at the interfacial surface, while the linear portion represents the diffusion process. As depicted in this figure, the diameter of semicircle part is decreased as defect density was increased and no clear semicircle can be observed in the cases of DMC-4 and DMC-5 electrodes, which indicate increased electron transfer at their surface. The quantitative values of parameter Rct is calculated by fitting the impedance spectra to the well-known Randles circuit (inset of Fig. 5b) and the obtained results are summarized in the Table 1. It can be observed that Rct is much lower for the cases of DMC-4 & DMC-5 compared with the Rct of the other electrodes.
Favorable electroanalytical behavior of highly defective mesoporous carbon toward fabrication of electrochemical sensors were further explored by study the CVs of some important biological and environmental species such as ascorbic acid, uric acid, dopamine, paracetamol, hydroquinone, and bisphenol A. Fig. 6 compares the CV responses for selected species recorded at the surface of graphite, MWCNT, graphene and DMC-5 paste electrodes. Apparently, the DMC-5 exhibited preferable responses for all those redox systems. For example, the overpotential for oxidation of ascorbic acid was significantly decreased to 180 mV at the surface of DMC-5 electrode compared to 345, 352 and 415 mV at graphene, MWCNT and graphite electrodes, respectively. Also, the smallest peak separation for uric acid, dopamine, paracetamol, and hydroquinone were observed at the surface of highly defective mesoporous carbon electrode. Hence, more favorable electron transfer kinetic and higher electrochemical reactivity of highly defective mesoporous carbon in comparison to the common used electrode materials makes this nanocarbon as promising electrochemical sensing and biosensing platform for electrocatalysis of variety of electroactive compounds.
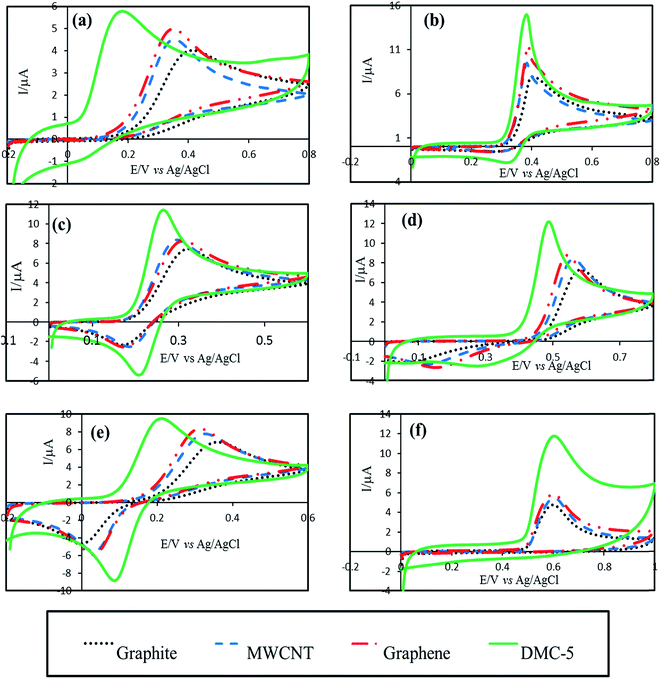 |
| Fig. 6 Cyclic voltammograms of 0.5 mM (a) ascorbic acid, (b) uric acid, (c) dopamine, (d) paracetamol, (e) hydroquinone and (f) bisphenol A, recorded at the surface of different electrodes with scan rate of 50 mV s−1. | |
The long-term stability of the DMC-5 paste electrodes was tested over a three months period. Our investigation showed reproducible results for the modified electrode when stored in atmosphere at room temperature. Peak potentials for the tested analytes were unchanged and the current signals showed less than 2% decrease relative to the initial response.
4. Conclusions
Mesoporous carbon with high density of structural defect, as an advanced electrode material, have been successfully synthesized by using nanosilica as a hard template, sucrose as a carbon precursor, and KNO3 as a defect causing agent. Structural properties and electrochemical activity of prepared material were examined by various characterization methods including Raman spectroscopy, BET, CV, and EIS. The optimal effective heterogeneous rate constant for ferri/ferrocyanide redox probe at the surface of highly defective mesoporous carbon was determined as 0.42 cm s−1 which is about 145, 75 and 50 fold faster than graphite, MWCNT and graphene, respectively. Moreover, the study of CVs of different redox species verified the excellent electrochemical performance of the synthesized highly defective nanocarbon. The obtained results are believed to be beneficial for fabrication of effective electrochemical devices toward practical applications with advanced carbon-based materials.
Conflict of interest
The authors have declared that there is no conflict of interest.
Acknowledgements
The authors gratefully acknowledge the financial support for this research by Iranian Research & Development Center for Chemical Industries (IRDCI).
References
- I. Mohmood, C. B. Lopes, I. Lopes, I. Ahmad, A. C. Duarte and E. Pereira, Environ. Sci. Pollut. Res., 2013, 20, 1239–1260 CrossRef CAS PubMed.
- H. Huang, Y. Ying and X. Peng, J. Mater. Chem. A, 2014, 2, 13772–13782 CAS.
- L. Dai, D. W. Chang, J. B. Beak and W. Lu, Small, 2012, 8, 1130–1166 CrossRef CAS PubMed.
- Y. He, W. Chen, C. Gao, J. Zhou, X. Li and E. Xie, Nanoscale, 2013, 5, 8799–8820 RSC.
- H. Nishihara and T. Kyotani, Adv. Mater., 2012, 24, 4473–4498 CrossRef CAS PubMed.
- L. Ma, K. E. Hendrickson, S. Wei and L. A. Archer, Nano Today, 2015, 10, 315–338 CrossRef CAS.
- Y. Zhai, Z. Zhu and S. Dong, ChemCatChem, 2015, 7, 2806–2815 CrossRef CAS.
- K. Zhu, J. Sun, H. Zhang, J. Liu and Y. Wang, J. Nat. Gas Chem., 2012, 21, 215–232 CrossRef CAS.
- S. Mao, G. Lu and J. Chen, J. Mater. Chem. A, 2014, 2, 5573–5579 CAS.
- T. V. Vineesh, S. Alwarappan and T. N. Narayanan, Nanoscale, 2015, 7, 6504–6509 RSC.
- Z. Wang and Z. Dai, Nanoscale, 2015, 7, 6420–6431 RSC.
- A. Walcarius, TrAC, Trends Anal. Chem., 2012, 38, 79–97 CrossRef CAS.
- M. Zhou and S. Guo, ChemCatChem, 2015, 7, 2744–2764 CrossRef CAS.
- X. Feng, Y. Zhang, J. Zhou, Y. Li, S. Chen, L. Zhang, Y. Ma, L. Wang and X. Yan, Nanoscale, 2015, 7, 2427–2432 RSC.
- R. N. Goyal, V. K. Gupta, N. Bachheti and R. A. Sharma, Electroanalysis, 2008, 20, 757–764 CrossRef CAS.
- V. K. Gupta, R. Jain, K. Radhapyari, N. Jadon and S. Agarwal, Anal. Biochem., 2011, 408, 179–196 CrossRef CAS PubMed.
- R. N. Goyal, V. K. Gupta and S. Chatterjee, Electrochim. Acta, 2008, 53, 5354–5360 CrossRef CAS.
- P. T. Araujo, M. Terrones and M. S. Dresselhaus, Mater. Today, 2012, 15, 98–109 CrossRef CAS.
- F. Banhart, J. Kotakoski and A. V. Krasheninnikov, ACS Nano, 2011, 5, 26–41 CrossRef CAS PubMed.
- J. Haskins, A. Kınaci, C. Sevik, H. Sevinc, G. Cuniberti and T. Cagin, ACS Nano, 2011, 5, 3779–3787 CrossRef CAS PubMed.
- A. Lherbier, S. Roche, O. A. Restrepo, Y. M. Niquet, A. Delcorte and J. C. Charlier, Nano Res., 2013, 6, 326–334 CrossRef CAS.
- L. Vicarelli, S. J. Heerema, C. Dekker and H. W. Zandbergen, ACS Nano, 2015, 9, 3428–3435 CrossRef CAS PubMed.
- D. Datta, J. Li, N. Koratkar and V. B. Shenoy, Carbon, 2014, 80, 305–310 CrossRef CAS.
- X. Fan, W. T. Zheng and J. L. Kuo, ACS Appl. Mater. Interfaces, 2012, 4, 2432–2438 CAS.
- D. Datta, J. Li and V. B. Shenoy, ACS Appl. Mater. Interfaces, 2014, 6, 1788–1795 CAS.
- P. C. Tsai, S. C. Chung, S. K. Lin and A. Yamada, J. Mater. Chem. A, 2015, 3, 9763–9768 CAS.
- D. Xu, J. Zhao and X. Wang, J. Nanopart. Res., 2013, 15, 1590–1603 CrossRef.
- I. Fampiou and A. Ramasubramaniam, J. Phys. Chem. C, 2012, 116, 6543–6555 CAS.
- J. H. Zhong, J. Zhang, X. Jin, J. Y. Liu, Q. Li, M. H. Li, W. Cai, D. Y. Wu, D. Zhan and B. Ren, J. Am. Chem. Soc., 2014, 136, 16609–16617 CrossRef CAS PubMed.
- D. H. Lim and J. Wilcox, J. Phys. Chem. C, 2012, 116, 3653–3660 CAS.
- K. Kamiya, K. Hashimoto and S. Nakanishi, ChemElectroChem, 2014, 1, 858–862 CrossRef CAS.
- T. Y. Ma, L. Liu and Z. Y. Yuan, Chem. Soc. Rev., 2013, 42, 3977–4003 RSC.
- Y. P. Zhu, Y. Liu, Y. P. Liu, T. Z. Ren, G. H. Du, T. Chen and Z. Y. Yuan, J. Mater. Chem. A, 2015, 3, 11725–11729 CAS.
- Y. P. Zhu, Y. Liu, Y. P. Liu, T. Z. Ren, T. Chen and Z. Y. Yuan, ChemCatChem, 2015, 7, 2903–2909 CrossRef CAS.
- M. Chen, L. L. Shao, H. B. Yang and Z. Y. Yuan, Electrochim. Acta, 2015, 168, 59–68 CrossRef CAS.
- M. Chen, L. L. Shao, Y. Liu and Z. Y. Yuan, J. Power Sources, 2015, 283, 305–313 CrossRef CAS.
- T. Z. Ren, L. Liu, Y. Zhang and Z. Y. Yuan, J. Solid State Electrochem., 2013, 17, 927–935 CrossRef CAS.
- S. Ren, H. Wang, H. Zhang, L. Yu, M. Li and M. Li, J. Electroanal. Chem., 2015, 750, 65–73 CrossRef CAS.
- H. Hosseini, M. Behbahani, M. Mahyari, H. Kazerooni, A. Bagheri and A. Shaabani, Biosens. Bioelectron., 2014, 59, 412–417 CrossRef CAS PubMed.
- Y. Liu, Y. Lia and X. He, Anal. Chim. Acta, 2014, 819, 26–33 CrossRef CAS PubMed.
- M. M. Lucchese, F. Stavale, E. H. Martins Ferreira, C. Vilani, M. V. O. Moutinho, R. B. Capaz, C. A. Achete and A. Jorio, Carbon, 2010, 48, 1592–1597 CrossRef CAS.
- M. M. Ugeda, I. Brihuega, F. Guinea and J. M. Gómez-Rodríguez, Phys. Rev. Lett., 2010, 104, 096804–096811 CrossRef CAS PubMed.
- M. A. Hoefer and P. R. Bandaru, J. Appl. Phys., 2010, 1, 108–115 Search PubMed.
- S. Brauner, P. H. Emmet and E. Teller, J. Am. Chem. Soc., 1938, 60, 309–319 CrossRef.
- E. S. Freeman, J. Am. Chem. Soc., 1957, 79, 838–842 CrossRef CAS.
- M. S. Dresselhaus, A. Jorio, A. G. Souza Filho and R. Satio, Philos. Trans. R. Soc., A, 2010, 368, 5355–5377 CrossRef CAS PubMed.
- L. G. Cancado, A. Jorio, E. H. Martins Ferreira, F. Stavale, C. A. Achete, R. B. Capaz, M. V. O. Moutinho, A. Lombardo, T. S. Kulmala and A. C. Ferrari, Nano Lett., 2011, 11, 3190–3196 CrossRef CAS PubMed.
- W. Li, D. Chen, Z. Li, Y. Shi, Y. Wan, J. Huang, J. Yang, D. Zhao and Z. Jiang, Electrochem. Commun., 2007, 9, 569–573 CrossRef CAS.
- G. Yang, H. Han, T. Li and C. Du, Carbon, 2012, 50, 3753–3765 CrossRef CAS.
- R. L. McCreery, Chem. Rev., 2008, 108, 2646–2687 CrossRef CAS PubMed.
- M. Pacios, M. D. Valle, J. Bartroli and M. J. Esplandiu, Electroanal. Chem., 2008, 619, 117–124 CrossRef.
- L. Tang, Y. Wang, Y. Li, H. Feng, J. Lu and J. Li, Adv. Funct. Mater., 2009, 19, 2782–2789 CrossRef CAS.
|
This journal is © The Royal Society of Chemistry 2016 |
Click here to see how this site uses Cookies. View our privacy policy here.