DOI:
10.1039/C6RA03214A
(Paper)
RSC Adv., 2016,
6, 33426-33432
Rapid synthesis of macroporous graphene oxide/poly(acrylic acid-co-acrylamide) nanocomposite hydrogels with pH-sensitive behavior by frontal polymerization
Received
3rd February 2016
, Accepted 28th March 2016
First published on 29th March 2016
Abstract
Macroporous pH-sensitive graphene oxide (GO)/poly(acrylic acid-co-acrylamide) (PAA) nanocomposite hydrogels were prepared by frontal polymerization (FP) using a solvent mixture composed of DMF and a small quantity of GO water solution as a heat conductive medium. A flat frontal can be obtained. The high temperature on the propagating front evaporated water to produce many vapor bubbles, which were trapped into the hydrogel matrix and consequently formed a macroporous structure (i.e. diameter ca. 120 μm). The increase in the concentration of GO solution led to an increase in front velocity (Vf) and the highest front temperature (Tmax). Fourier transform infrared spectroscopy (FTIR) and X-ray diffraction (XRD) indicated that GO nanosheets were crosslinked into the PAA hydrogel. Scanning electron microscope (SEM) analysis illustrated that the size of pores in GO/PAA nanocomposite hydrogels highly depended on the concentration of GO solution. The macroporous structure of nanocomposite hydrogels had a significant influence on the pH-sensitive swelling behaviors of the nanocomposite hydrogels. The highest compressive strength of the GO/PAA nanocomposite hydrogel can reach 44.9 MPa.
1. Introduction
Polymeric hydrogels are three-dimensional polymer networks consisting of hydrophilic crosslinked macromolecular chains. They can swell and retain plenty of water when they are placed in an aqueous medium. Polymeric hydrogels have potential applications in environmental and biomedicine areas because that they often have high water retention, response to external stimuli and tunable mechanical properties.1–3 Recently, considerable interest has been lately focused on the macroporous polymeric hydrogels, which have a faster response rate at small changes of the external stimuli than the conventional polymeric hydrogels. In general, macroporous hydrogels can be achieved by several methods including phase separation,4 adding a pore-forming agent,5,6 porogen leaching7–9 and freeze-drying,10,11 etc. Graphene oxide (GO) is an ideal nano-fillers for polymer reinforcement because of its large theoretical special surface area. GO has a layered structure and is rich in oxygen-containing functional groups, i.e. hydroxyl and epoxide on the basal planes and carbonyl and carboxylic groups at the sheet edges. These excellent properties of GO make it a promising materials for improving the mechanical strength of the hydrogels.12 Several research groups have reported the preparation of GO based nanocomposite hydrogels with enhanced mechanical properties.13–15 Very recently, Zeng et al. prepared GO based composite hydrogel with self-assembled macroporous structures. They found that the macroporous hydrogels possessed both enhanced mechanical properties and high swelling ability.16 Pourjavadi et al. synthesized porous GO based composite hydrogels using CaCO3 particles as solid porogens. After washing with HCl, the solid porogens were removed and a porous structure was obtained. The obtained macroporous hydrogel had high adsorption ability for dyes.17
Frontal polymerization (FP) is a reaction model of converting monomer into polymer via a localized and propagating reaction, which presents obvious advantage with a fast and low energy cost to produce the polymers.18 Many polymeric hydrogels such as polyurethane, poly(N-methylolacrylamide)/polyhedral oligomeric silsesquioxane, poly(N-methylolacrylamide)/polymethylacrylamide nanocomposites, poly(HPA-co-VeoVa10) amphiphilic gels and poly(N-isopropylacrylamide) hydrogels have been prepared by FP.19–28 In the past decade, nanocomposite hydrogels have also been synthesized by FP, including those that contain graphene with improved properties.29–34
In our previous research, we synthesized PAA, PAA/activated carbon and PAA/SiO2 hydrogels by FP using single high boiling point solvent (DMF). The highest front temperature never exceeded the boiling point of DMF. Thus, a bubble-free thermal FP can be observed.35–37 Using single DMF as a solvent, the structure of the obtained hydrogel was relatively compact. Yan et al. demonstrated that FP combined with a foaming process could control the pore structure of the hydrogel. However, the mechanical properties of the hydrogel products were not reported in details.21,38
In the present study, macroporous GO/PAA nanocomposite hydrogels were prepared by FP using the mixture solvent composed of DMF and small quantity of GO water solution as heat conductive medium, instead of single high boiling point solvent (DMF). The small quantity of water in the mixture solvent acted as a dispersion agent as well as a pore-forming agent during FP. The high temperature on the propagating front can evaporate low boiling point water to produce many vapor bubbles, which caused macroporous structure in PAA hydrogel. Furthermore, GO were rapidly and well dispersed into PAA hydrogel matrix to enhance mechanical strength of hydrogels. The effect of GO solution on FP was investigated. The characterization, swelling behavior, microstructure, formation mechanism and mechanical properties of the as-synthesized macroporous GO/PAA nanocomposite hydrogels were also studied in details.
2. Experimental
2.1. Materials
Acrylic acid (AA) was purchased from Tianjin Chemical Reagent Co. (Tianjin, China) and was distilled before use. Acrylamide (AM), potassium persulfate (KPS), N,N′-methylenebisacrylamide (MBA), N,N-dimethylformamide (DMF), sodium nitrate, potassium permanganate and hydrogen peroxide were purchased from Shanghai Reagent Co. (Shanghai, China). The graphite was purchased from Huadong Graphite Co., China. All the reagents were of analytical grade and used as received without any further purification.
2.2. Preparation of GO
GO was prepared according to modified Hummers' method.39 Briefly, 1.25 g of sodium nitrate was stirred with 2.5 g of natural graphite in an ice-water bath for 10 minutes. Once the mixture was well-mixed, 60 mL of sulfuric acid was added gradually into the mixture. The mixture was kept between the temperature range of 0 °C to 5 °C in the ice-water bath as a safety precaution. While maintaining vigorous agitation, 7.5 g of potassium permanganate was added into the suspension gradually. The rate of addition was controlled to prevent the temperature of the mixture from exceeding 20 °C. The mixture was kept mixing for a total of 2 hours with the temperature of the ice-water bath kept at ≤5 °C. The ice-water bath was then removed and the mixture was stirred overnight at room temperature. As the reaction progressed, the mixture gradually thickened. After a night of stirring, the mixture became pasty and it became brownish grey in color. Thereafter, 135 mL of deionized water was slowly stirred into the paste and this resulted in violent effervescence and a temperature hike to 98 °C. A watch glass was used to minimize evaporation and the level of the mixture was maintained at 250 mL with periodical addition of deionized water for 1 hour. Subsequently, the heater was turned off and the mixture was then left to cool for 1 hour to room temperature. Once completed, 25 mL of hydrogen peroxide was added dropwise to reduce the residual permanganate and manganese dioxide to colorless soluble manganese sulfate. After the filtration of the mixture, the residue was washed by HCl solution four times and ultrapure water five times. The product was dialyzed by deionized water for one week. Then, it was dried at 60 °C and stored for further use. To prepare fully exfoliated GO nanosheets with different concentration (0.5, 2 and 4 mg mL−1, respectively), different amount of GO powder was dispersed into 100 mL deionized water, followed by an ultrasonic for 30 min to form a yellow-brown stable GO solution (Fig. 1a).
 |
| Fig. 1 Schematic representation of the preparation of macroporous GO/PAA nanocomposite hydrogels by FP. (a) GO aqueous solution, (b) AA, AM, MBA and DMF mixture solution, (c) hydrogel before FP, (d) hydrogel in FP, (e) hydrogel after FP. | |
2.3. Preparation of GO/PAA and PAA hydrogels via FP
For the preparation of GO/PAA hydrogels, firstly, 2 mL GO (0, 0.5, 2 and 4 mg mL−1) water solution with different concentration was added into 18 mL DMF and mixed with stoichiometric quantity of AA, AM, MBA, and KPS (AA/AM (wt/wt) = 3
:
7, MBA (wt%) = 1.2, KPS (wt%) = 0.1, DMF = 18 mL). Then, the mixture was sonicated for 10 min and became homogenized black without stratification. Then, it was poured into a glass test tube (25 mL; 12.8 mm diameter). In order to monitor the temperature change, a K-type thermocouple connected to a digital thermometer was immersed into the mixture at about 3 cm from the bottom of the tube. The filled tube was clamped into a holder 1 cm from the top of the tube and kept at ambient temperature. The upper side of the mixture containing monomers and GO solution was heated by a soldering iron until the hot propagating front commenced. After the completion of the reaction, the sample was removed from the tube and cut into small pieces and immersed in deionized water over 3 days to dissolve soluble materials. The obtained nanocomposite hydrogel products were dried in vacuum at 60 °C to a constant weight and stored for further use. PAA hydrogel was synthesized using the same method without GO solution. The hydrogels with different concentration of GO (0, 0.5, 2 and 4 mg mL−1) were designed as FP0, FP1, FP2 and FP3, respectively.
2.4. Characterization
The morphologies of samples were observed by a SEM (FEI Siron 200) with an acceleration voltage of 10 kV. The phase structure was examined by X-ray diffraction (XRD) using a Philips PW1140/90 diffractometer with Cu Kα radiation (25 mA and 40 kV) at a scan rate of 2° min−1 with a step size of 0.02°. Fourier-transform infrared (FTIR) spectra were recorded on a Perkin Elmer Fourier-transform infrared spectrometer in the region of 400–4000 cm−1 by using the KBr wafer technique. The front velocities were confirmed by measuring the front position as a function of time. Temperature profiles were determined by measuring the temperature at a fixed point as a function of time, using a K-type thermocouple and converted to spatial ones using front velocities. After the completion of the reaction, the samples were cooled to room temperature and removed from the tube for further investigation.
2.5. Swelling studies of hydrogels
The swelling properties of the as-prepared hydrogels were performed by gravimetric analysis. Briefly, the dry nanocomposite hydrogel was immersed in the swelling medium at 25 °C. At regular time intervals, the gels were removed from the medium, the weight of the swollen nanocomposite hydrogel was determined after the removal of the surface water through blotting with filter paper. The measurements were continued until the weight of hydrogels reached a constant value. The swelling ratio (SR) was calculated by the following eqn:where, Wt is the mass of the swollen hydrogels at t, and W0 is the initial mass of dry hydrogel. All of the experiments were triplicated.
2.6. Compressive test of hydrogels
Compressive strength of the swollen hydrogels was tested using a self-prepared equipment described earlier.40 Compressive strength (Ss) was calculated as follows:where, F is force applied, S is the surface area of the swollen hydrogel.
3. Results and discussion
3.1. Synthesis of macroporous GO/PAA nanocomposite hydrogels by FP
Macroporous GO/PAA nanocomposite hydrogels were prepared by FP using the mixture solvent composed of DMF and small quantity of GO water solution as heat conductive medium. Fig. 1 shows the schematic representation of the preparation of macroporous GO/PAA nanocomposite hydrogels by FP. As shown in Fig. 1, firstly, two types of homogeneous solutions were prepared. One was GO water solution (Fig. 1a), the other was the mixture composed of AA, AM and MBA in DMF (Fig. 1b). Then, they were fully mixed together. Before mixing, GO water solution was transparent and yellow brown, while monomer (AA, AM and MBA) solution was transparent and white. However, when the mixture was further sonicated for 10 minutes, a highly homogeneous black mixture can be obtained (Fig. 1c). This illustrated that hydrophilic GO nanosheets had been well dispersed into the monomers reaction mixture containing a small quantity of water by this method.
After that, the obtained highly homogeneous mixture was poured into a glass test tube to carry out FP. In detail, the FP process was initiated by application of a soldering iron to the top of the test tube until a hot propagating front was formed. Interestingly, we found that the stable FP experiments both in PAA and GO/PAA could be carried out easily. However, there was an obvious difference in PAA and GO/PAA FP experiments. For PAA, it can be seen that FP proceeded very smoothly and there was no bubbles on the propagating front when using single high boiling point DMF as heat conductive medium. The frontal temperature was always under the boiling point of the single high boiling point solvent, DMF (152.8 °C). However, for GO/PAA, it was found that the propagating front with many vapor bubbles traveled down the tube when using the mixture solvent containing DMF and small quantity of GO water solution as heat conductive medium. The frontal temperature increased gradually with the development of FP. When the frontal temperature increased over the low boiling point solvent, water (100 °C), the water in the mixture solvent became vapor gradually and resulted in many bubbles on the propagating front. When these bubbles were trapped in the viscose reaction mixture, many macropores produced in the hydrogel matrix.41,42
The amount of water in the mixture solvent had an important effect on the FP. Ge et al. synthesized a series of starch-graft-poly(acrylic acid) hydrogels using single solvent-water as a heat conductive medium.41,42 They found that 1 mg of water can result in about 1.7 cm3 of water vapor at the front temperature of 100 °C and ambient pressure. When larger water was used as solvent, bubbles occasionally interfered by making it difficult to initiate a front if a large bubbles collected under the front, insulating the reactant and preventing propagation.43 On the other hand, larger amount of water could affect the heat conduction and resulted in some vapor bubbles escaping from the tube, which made part of heat lost in FP. Thus, FP can be stopped due to the lack of full heat energy.43 Since the concentration of GO was very low in our FP experiments, the volume of GO water solution can be looked as the volume of water approximatively. So, we explored to add different volumes of GO solution into DMF (for all FP, the volume of DMF was 18 mL) as pore-forming agents to carry out FP, respectively. The amount of vapor bubbles depended on the volume of GO solution. When the volume of GO solution was less than 1 mL, the bubble produced was very lower. However, when the volume of GO solution was more than 3 mL, the FP experiment was difficult to be controlled. Thus, we chose 2 mL GO water solution as a pore-forming agent to prepare macroporous nanocomposite hydrogel by FP. As a result, a stable thermal front with constant frontal velocity can be obtained.
In our FP experiments, an obvious interface between the nanocomposite and mixture containing unreacted monomers and GO solution can be observed. The upper solid layer was the polymerized porous GO/PAA nanocomposite hydrogel, and the lower liquid layer was the non-polymerized mixture containing unreacted monomers and GO solution. Furthermore, the front moved downward steadily with the increase in time. FP can finish in no more than 10 minutes.
A constant velocity is one important character of FP without simultaneous spontaneous polymerization (SP).27,28 Fig. 2 shows a typical curve for the position of thermal propagating front as a function of time (Fig. 2a) and temperature profile (Fig. 2b). The experimental data were well fitted by a straight line, indicating that the front velocity was a constant, 0.85 cm min−1. And there was a constant temperature before the propagating front reached its junction, meaning SP was not occurring simultaneously.35
 |
| Fig. 2 (a) Front position as a function of time and (b) temperature profile for FP2 nanocomposite hydrogel. | |
The effect of concentration of GO solution on Vf and Tmax is shown in Fig. 3. It was found that Vf increased from 0.08 cm min−1 to 0.96 cm min−1 as the concentration of GO solution increased from 0 to 4 mg mL−1 (Fig. 3a). The increase in the concentration of GO solution also led to the increase in Tmax from 87 °C to 104 °C (Fig. 3b). This may be attributed to the fact that more GO could act as an additional crosslinking agent and increased the liquid viscosity of reaction mixture and resulted in a higher front temperature. Therefore, the higher the polymerization temperature was, the faster the Vf was. Similar results are reported in the previous literatures.44
 |
| Fig. 3 Front positions versus time (a) and front temperature profile (b) for hydrogels. | |
3.2. Characterization and formation mechanism of macroporous GO/PAA nanocomposite hydrogels
In order to prepare GO/PAA nanocomposite hydrogel, GO nanosheets were prepared via the oxidation of pristine graphite by a modified Hummer's method.39 Subsequently, macroporous GO/PAA nanocomposite hydrogels were synthesized by FP in the presence of a small quantity of GO water solution as mentioned above. Fig. 4 shows the XRD patterns for pristine graphite, GO, FP0 and FP2 hydrogels. As seen from Fig. 4, a diffraction peak of GO can be observed at 9.8°, while the diffraction peak of graphite at 26.6° disappeared. This indicated that the structure of the as-synthesized GO nanosheets were accordant with the previous report.39 In addition, FP0 (PAA) showed a broad characteristic diffraction peak. Comparing with FP0, although some GO nanosheets were added into the hydrogel, there was no characteristic diffraction peak around 2θ = 9.8° in FP2. This indicated that GO in FP2 had been crosslinked into the hydrogel networks.45
 |
| Fig. 4 XRD patterns of graphite, GO, FP0 and FP2 hydrogel. | |
Fig. 5 shows the FTIR spectra of GO, FP0 and FP2 hydrogels. In the spectrum of GO, the peak at 3490 cm−1 was assigned to the –OH vibration stretching. It also showed the characteristic bands of carboxyl C
O and C–O (1650 and 1451 cm−1), epoxy C–O (1260 cm−1) and alkoxy C–O (1100 cm−1) groups situated at the edges of the GO nanosheets. In spectra of PAA and GO/PAA, it can be observed that the band with a weak shoulder at 2926 and a medium band at 1459 cm−1 were belonged to the stretching of aliphatic –CH2– and –CHR– groups, respectively. The characteristic band around 3480 cm−1 assigned to the –NH2 and –OH groups could be observed. Comparing with FTIR spectra of PAA hydrogel, it was found the band around 3480 cm−1 (–OH stretching vibration) became broader in FP2. This was attributed to the intermolecular hydrogen bonding interaction between GO and PAA, which may enhance PAA hydrogel network.46
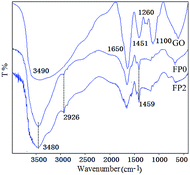 |
| Fig. 5 FTIR spectra of GO, FP0 and FP2 hydrogels. | |
The rapid increase in temperature resulted in many bubbles on the propagating front will affect the microstructure of the nanocomposite hydrogels. To confirm this presumption, the microscopic morphologies of FP0, FP1, FP2 and FP3 hydrogels were measured by SEM (Fig. 6). It is clear that all hydrogels were porous. But the sizes of pores in the different samples were different. Comparing with FP1, FP2, FP3 hydrogels, the sizes of pores in FP0 (diameter ca. 20 μm) was much compacter. The main reason was that the reactions proceeded smoothly. The highest front temperature never exceeded the single high boiling point solvent (DMF). There were no bubbles on the propagating front. Thus, the obtained hydrogel was compact (Fig. 6). The larger sizes of pores of FP1 (diameter ca. 120 μm), FP2 (diameter ca. 80 μm) and FP3 (diameter ca. 40 μm) can be attributed to that, in FP, the mixture solvent was composed of DMF and small quantity of GO water solution, instead of single high boiling point solvent (DMF). The high synthesis temperature and rapid temperature increased at the propagating front, which evaporated low boiling point water to produce many vapor bubbles. These vapor bubbles were trapped by sticky reaction mixture and consequently formed interconnected capillary channels in the hydrogel matrix. Therefore, the resulting hydrogel product was macroporous (Fig. 6). The different formation mechanism of PAA and macroporous GO/PAA nanocomposite hydrogels are shown in Fig. 7.
 |
| Fig. 6 SEM images of FP0, FP1, FP2 and FP3 hydrogels. | |
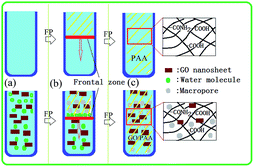 |
| Fig. 7 Formation mechanisms of PAA and macroporous GO/PAA nanocomposite hydrogels. | |
In addition, the size of pore of FP3 was much smaller than that of FP2 and FP1 because that GO could act as an additional crosslinking agent, which led to many fresh chemical crosslinking points in hydrogel formation that can increase crosslinking density and decrease in porosity.47 Therefore, we can design and synthesize various macroporous GO based nanocomposite hydrogels with excellent properties by adjusting the concentration of GO water solution in FP.
3.3. Swelling behavior of macroporous GO/PAA nanocomposite hydrogels
The pH value of the external media had a profound influence on the swelling behavior of these macroporous GO/PAA nanocomposite hydrogels. Fig. 8 shows the swelling kinetics of FP0, FP1, FP2 and FP3 hydrogels in various pH ranging from 2.2 to 8.0. As shown in Fig. 8, all hydrogels exhibited extremely low SR in the pH 2.2 and high SR in pH 7.0 and 8.0. The SR of hydrogel increased with the increase from 5.0 to 8.0. The low SR may be attributed to that the carboxyl groups on the hydrogel almost unionized. When the pH value in creased, the carboxyl groups became ionized. The ionization of carboxyl groups increased the osmotic swelling pressure and resulted in relaxation of polymeric chain due to repulsion among similarly charged carboxyl groups on the hydrogel.48 Additionally, at the same pH values, the SR of nanocomposite hydrogels firstly increased with the increase in the concentration of GO. Then, when the concentration of GO continued to increase, a decrease in SR can be observed. It is probable due to the fact that the macroporous structure can enhance the swelling of hydrogels, while the additional crosslink of GO can decrease the size of pores.
 |
| Fig. 8 Swelling kinetics of FP0, FP1, FP2 and FP3 hydrogels in different pH values of buffer solutions. | |
The effect of pH values on the equilibrium SR of nanocomposite hydrogels was investigated in different pH buffer solutions. Fig. 9 shows the change of the equilibrium SR of hydrogels with various pH. It can be seen that the equilibrium SR showed a sharp increase when the pH value changed from 3.0 to 7.0. This is mainly attributed to carboxyl groups on the hydrogels became ionized.48 However, the ability of sharp increase in SR of different hydrogels was different. The pH sensitivity of FP1 was the highest among all hydrogels due to the largest size of porous as stated above.
 |
| Fig. 9 Plot of the SR of FP0, FP1, FP2 and FP3 hydrogels versus pH values of the buffer solutions. | |
To evaluate the swelling–deswelling ability of hydrogels, the hydrogels were put in pH 2.2 buffer solution, then transferred to pH 8.0 buffer solution (Fig. 10), all hydrogels showed swelling–deswelling ability and pH sensitivity. But FP1 showed the best pH sensitivity due to the largest size of pore. After a cycle of reversible swelling–deswelling, all nanocomposite hydrogels showed good stability and there were no damage due to the fact that the introduction of GO can improve the mechanical strength of PAA hydrogel.
 |
| Fig. 10 Swelling and deswelling of GO/PAA nanocomposite hydrogels as a function of times in pH 2.2 and pH 8.0 buffer solutions. | |
3.4. Mechanical properties of macroporous GO/PAA nanocomposite hydrogels
Fig. 11 shows photographs of FP0 and FP2 hydrogels under pressure, and rapid shape recovery of FP2 hydrogel. As can be seen, the pure FP0 hydrogel became broken in compression, while FP2 hydrogel was tough enough to withstand high deformations in compression without any damage (Fig. 11a). Upon removing of the compression force, FP2 hydrogel could recover its original shape rapidly (Fig. 11b). This indicated the as-synthesized macroporous FP2 hydrogel had high compressive strength and good ductility.
 |
| Fig. 11 Photographs of FP2 and FP0 hydrogels under pressure (a), and rapid shape recovery of FP2 hydrogel (b). | |
The effect of concentration of GO on the mechanical properties of the hydrogels were further investigated by compressive tests (Fig. 12). As shown in Fig. 12, the compressive strength of the FP0, FP1, FP2 and FP3 hydrogel were 12.9, 17.8, 32.6 and 44.9 MPa, respectively. This meant the compressive strength of hydrogels increased with the increase in the concentration of GO. For FP0 hydrogel, the compressive strength was only 12.9 MPa, while for FP3 nanocomposite hydrogel, it can reach 44.9 MPa. It appeared that the introduction of GO nanosheets was favorable for improving the compressive strength of the PAA hydrogel.
 |
| Fig. 12 Compressive strength of FP0, FP1, FP2 and FP3 hydrogels. | |
4. Conclusions
In conclusion, we have developed a novel technique to rapidly synthesize macroporous GO/PAA nanocomposite hydrogels by FP using the mixture solvent composed of DMF and small quantity of GO water solution as heat conductive medium, instead of single DMF. A stable thermal propagating front can be obtained. The data of front velocity and front temperature implied that the FP had occurred. The increase in the concentration of GO solution led to an increase of Vf and Tmax. The structures of pores can be controlled by tuning the concentration of GO water solution. The vapor bubbles caused from water evaporation in FP were trapped in the viscose reaction mixture and resulted in the formation of macroporous GO/PAA nanocomposite hydrogels. SEM analysis revealed the macroporous structures in the hydrogel. It was found that all GO/PAA nanocomposite hydrogels showed excellent swelling–deswelling ability and pH sensitivity. The mechanical strength of hydrogels was enhanced due to the incorporation of GO nanosheets in the hydrogel networks. The as-synthesized macroporous GO/PAA nanocomposite hydrogels with good pH sensitivity and mechanical strength have potential applications in drug delivery.
Acknowledgements
The project sponsored by the Scientific Research Foundation for the Returned Overseas Chinese Scholars, National Technology Support Program (2015BAB07B04), China.
References
- D. Das and S. Pal, RSC Adv., 2015, 5, 25014–25050 RSC.
- Q. Yang, N. Ardrus, F. Tomicki and M. Ulbricht, J. Mater. Chem., 2011, 21, 2783–2811 RSC.
- A. Fakhari and J. A. Subramony, J. Controlled Release, 2015, 220, 465–475 CrossRef CAS PubMed.
- M. M. Ozmen and O. Oguz, React. Funct. Polym., 2008, 68, 1467–1475 CrossRef.
- S. Li, X. Liu, T. Zou and W. Xiao, Clean: Soil, Air, Water, 2010, 38, 378–386 CrossRef CAS.
- X. Zhang, X. Xu, S. Cheng and R. Zhuo, Soft Matter, 2008, 4, 385–391 RSC.
- X. S. Wu, A. S. Hoffman and P. Yager, J. Polym. Sci., Part A: Polym. Chem., 1992, 30, 2121–2129 CrossRef CAS.
- T. Serizawa, K. Wakita, T. Kaneko and M. Akashi, J. Polym. Sci., Part A: Polym. Chem., 2002, 40, 4228–4235 CrossRef CAS.
- K. Varaprasad, N. Narayana Reddy, S. Ravindra, K. Vimala and K. Mohana Raju, Int. J. Polym. Mater., 2011, 60, 490–503 CrossRef CAS.
- L. Shapiro and S. Cohen, Biomaterials, 1997, 18, 583–590 CrossRef CAS PubMed.
- E. S. Dragan, M. Cazacu and A. Nistor, J. Polym. Sci., Part A: Polym. Chem., 2009, 47, 6801–6813 CrossRef CAS.
- H. Chang and H. Wu, Energy Environ. Sci., 2013, 6, 3483–3507 CAS.
- J. Fan, Z. Shi, M. Lian, H. Li and Y. Jie, J. Mater. Chem. A, 2013, 1, 7433–7443 CAS.
- Z. Tai, J. Yang, Y. Qi, X. Yan and Q. Xue, RSC Adv., 2013, 3, 12751–12757 RSC.
- S. Jian, B. Yan, T. Li, Y. Long, N. Li and M. Ye, Soft Matter, 2012, 8, 1831–1836 RSC.
- Y. Huang, M. Zeng, Z. Feng, D. Yin, Q. Xu and L. Fan, RSC Adv., 2016, 6, 3561–3570 RSC.
- A. Pourjavadi, M. Nazari, B. Kabiri, S. Hassan Hosseini and C. Bennett, RSC Adv., 2016, 6, 10430–10437 RSC.
- J. A. Pojman, J. Am. Chem. Soc., 1991, 113, 6284–6286 CrossRef CAS.
- S. Fiori, A. Mariani, L. Ricco and S. Russo, Macromolecules, 2011, 36, 2674–2679 CrossRef.
- Z. Zhou, C. Yu, X. Wang, W. Tang, C. Wang and S. Chen, J. Mater. Chem. A, 2013, 1, 7326–7331 CAS.
- Q. Yan, G. Lu, W. Zhang, X. Ma and C. Ge, Adv. Funct. Mater., 2007, 17, 3355–3362 CrossRef CAS.
- Q. Li, W. Zhang, C. Wang and S. Chen, RSC Adv., 2015, 5, 102294–102299 RSC.
- Y. Liu, C. Wang and S. Chen, RSC Adv., 2015, 5, 30514–30521 RSC.
- V. Alzari, O. Monticelli, D. Nuvoli, J. Kenny and A. Mariani, Biomacromolecules, 2009, 10, 2672–2677 CrossRef CAS PubMed.
- C. Yu, J. Zhou, C. Wang, L. Chen and S. Chen, J. Polym. Sci., Part A: Polym. Chem., 2010, 48, 2000–2005 CrossRef.
- N. Liu, H. Shao, C. Wang, Q. Chen and S. Chen, Colloid Polym. Sci., 2013, 51, 1871–1879 Search PubMed.
- Q. Feng, F. Li, Q. Yan, Y. Zhu and C. Ge, Colloid Polym. Sci., 2010, 288, 915–921 CAS.
- Q. Feng, Q. Yan and C. Ge, Colloid Polym. Sci., 2013, 291, 1163–1170 CAS.
- J. D. Mota-Morales, M. C. Gutiérrez, M. L. Ferrer, I. C. Sanchez, E. A. Elizalde-Peña, J. A. Pojman, F. D. Monte and G. Luna-Bárcenas, J. Polym. Sci., Part A: Polym. Chem., 2013, 51, 1767–1773 CrossRef CAS.
- S. P. Davtyan, A. O. Tonoyan, A. Z. Varderesyan and S. C. M. ϋller, Eur. Polym. J., 2014, 57, 182–186 CrossRef CAS.
- V. Alzari, A. Mariani, O. Monticelli, L. Valentini, D. Nuvoli, M. Piccinini, S. Scognamillo, S. B. Bon and J. Illescas, J. Polym. Sci., Part A: Polym. Chem., 2010, 48, 5375–5381 CrossRef CAS.
- J. Illescas, P. Sanna, V. Alzari, D. Nuvoli, M. Casu, E. Rivera and A. Mariani, J. Polym. Sci., Part A: Polym. Chem., 2013, 51, 4618–4625 CAS.
- J. D. Mota-Morales, M. C. Gutierrez, M. L. Ferrer, R. Jimenez, P. Santiago, I. C. Sanchez, M. Terrones, F. Del Monte and G. Luna-Barcenas, J. Mater. Chem. A, 2103, 1, 3970–3976 RSC.
- V. Alzari, D. Nuvoli, S. Scognamillo, M. Piccinini, E. Gioffredi, G. Malucelli, S. Marceddu, M. Sechi, V. Sanna and A. Mariani, J. Mater. Chem., 2011, 21, 8727–8733 RSC.
- S. Li, H. Zhang, J. Feng, R. Xu and X. Liu, Desalination, 2011, 280, 95–102 CrossRef CAS.
- S. Li, H. Huang, M. Tao, X. Liu and T. Chen, J. Appl. Polym. Sci., 2013, 129, 3737–3745 CrossRef CAS.
- S. Li, H. Wang, W. Huang and X. Liu, Colloid Polym. Sci., 2014, 292, 107–113 CAS.
- G. Lu, Q. Yan and C. Ge, Polym. Int., 2007, 56, 1016–1020 CrossRef CAS.
- D. C. Marcano, D. V. Kosynkin, J. M. Berlin, A. Sinitskii, Z. Sun, A. Slesarev, L. B. Alemany, W. Lu and J. M. Tour, ACS Nano, 2010, 4, 4806–4814 CrossRef CAS PubMed.
- S. Li, Y. Yang, H. Li, X. Yang and H. Xu, J. Appl. Polym. Sci., 2007, 106, 3792–3799 CrossRef CAS.
- Q. Yan, W. Zhang, G. Lu, X. Su and C. Ge, Chem.–Eur. J., 2005, 11, 6609–6615 CrossRef CAS PubMed.
- Q. Yan, W. Zhang, G. Lu, X. Su and C. Ge, Chem.–Eur. J., 2006, 12, 3303–3309 CrossRef CAS PubMed.
- P. M. Potzmann, F. J. L. Villanueva and R. Lisker, Macromolecules, 2015, 48, 8738–8745 CrossRef CAS.
- V. Alzari, D. Nuvoli, S. Scognamillo, M. Piccinini, E. Gioffredi, G. Malucelli, S. Marceddu, M. Sechi, V. Sanna and A. Mariani, J. Mater. Chem. A, 2011, 21, 8727–8733 RSC.
- Y. Piao and B. Chen, RSC Adv., 2016, 6, 6171–6181 RSC.
- M. Ionita, M. A. Pandele and H. Lovu, Carbohydr. Polym., 2013, 94, 339–344 CrossRef CAS PubMed.
- S. Jian, B. Yan, T. Li, Y. Long, N. Li and M. Ye, Composites, Part A, 2012, 43, 1476–1481 CrossRef.
- S. K. Bajpai and S. Dubby, React. Funct. Polym., 2005, 62, 93–104 CrossRef CAS.
|
This journal is © The Royal Society of Chemistry 2016 |
Click here to see how this site uses Cookies. View our privacy policy here.