DOI:
10.1039/C6RA02858F
(Paper)
RSC Adv., 2016,
6, 36954-36960
Three dimensional manganese oxide on carbon nanotube hydrogels for asymmetric supercapacitors†
Received
31st January 2016
, Accepted 30th March 2016
First published on 1st April 2016
Abstract
In this article, we report the development of manganese oxide (Mn3O4) on carbon nanotube (CNT) hydrogels as binder-free electrodes for asymmetric supercapacitors. The CNT hydrogels consisting of three dimensionally inter-connected nanotubes are prepared via a facile sol–gel method. Afterwards, flower-like Mn3O4 is incorporated into CNT hydrogels using a pulse electrochemical deposition. Satisfactory electrochemical performance with a high specific capacitance of 182 F g−1 (473 mF cm−2) is achieved. When employing activated carbon as negative electrodes, the assembled asymmetric supercapacitor exhibits a high potential window of 2 V to reach a specific energy of 26.6 W h kg−1 and a specific power of 5.2 kW kg−1. These results are much better compared with the results from pure Mn3O4. The remarkable performance of our composites can be ascribed to a highly conducting CNT micro-scaffold and pseudocapacitive Mn3O4.
1. Introduction
The current global economy heavily relies on the consumption of traditional fossil fuels such as coal and petroleum. However, these non-renewable sources are expected to be depleted by the end of this century.1 Besides that, the combustion of fossil fuels exacerbates global warming by emitting large amounts of greenhouse gases.2 To address these challenges, various renewable energy sources such as solar, wind and geothermal energy have been explored.3 Their power output, however, naturally fluctuates under diverse environmental situations, which increases the difficulty of an effective energy harvest.4 In the light of this, electrochemical energy storage (EES) units are essential for better energy balance and coordination. Among various storage devices such as batteries and fuel cells, supercapacitors have drawn great attentions due to their moderate power and energy density.5
Supercapacitors can be categorized into electrochemical double layer capacitor (EDLC) and pseudocapacitor based on two different working mechanisms.6 The first one takes an advantage of an electrochemical double layer formed at the electrode/electrolyte interface to store energy, while the second one utilizes fast redox chemical reactions.7 For its resemblance to capacitors, the second category is named as ‘pseudocapacitors’.8 Various types of activated carbon (AC) have been extensively investigated as electrode materials for EDLC due to their high surface area.9–11 Regardless of possessing ultrahigh cycling stability, AC suffers from a low specific capacitance. On the other hand, metal oxides/hydroxides and conducting polymers are widely used as pseudocapacitive materials because of their large theoretical capacitances.12–14 Nevertheless, the poor cycling life and compromised power performance greatly limit their future development.15 Therefore, it is essential to develop versatile composites to combine the merits of EDLC and pseudocapacitive materials.
Carbon nanotubes (CNTs), being the one-dimensional carbon allotrope with fantastic intrinsic properties, are widely used as a conductivity strengthening phase in composite design. To date, Ni(OH)2/CNT,16,17 MnO2/CNT,18,19 Co3O4/CNT,20,21 and NiCo2O4/CNT22 composite materials have been thoroughly investigated as supercapacitor electrode materials. Synthesized from the traditional routines, these composites exist in form of powders in which additional polymer binders have to be used for electrode fabrication. It is believed that the insulating nature of these polymer binders greatly hinders material performance.23 In order to overcome this problem, binder-free CNT composites with three-dimensional (3D) architectures have been proposed. Generally, nickel and copper metal foams are used as the macro-scaffolds to grow CNTs, followed by incorporating pseudocapacitive materials into their 3D structure.24–27
Tang et al.28 grew CNT on the nickel foam via chemical vapor deposition (CVD) and then successively synthesized Ni(OH)2 on the nanotubes using a chemical bath deposition. As a result, a core/shell structure with ultrahigh capacitance (3300 F g−1) has been achieved. Similar methods have been used by Wu et al. to prepare 3D nickel cobalt oxide NiCo2O4/CNT nanostructure.29 However, these methods only form a thin CNT film on nickel scaffold, leading to a small mass loading. By proper coating of these empty macro-pores, electrochemical performance of the supercapacitors can be further improved. From this perspective, Bryning et al. applied a sol–gel method to grow 3D CNT gels without using any metal foams thereby reached high porosity and electrical conductivity.30 Unfortunately, these CNT gels suffered from low mechanical rigidity. Previously, we developed the Ni(OH)2/CNT gels in which CNTs were used as a micro-scaffold and the nickel foam was used as a macro-scaffold.31 Compared with the Ni(OH)2, Mn3O4 has a larger potential window, better cycling stability and higher natural abundance and, thus, can serve as an ideal candidate for supercapacitor applications.7
In this work, we successfully developed Mn3O4/CNT hydrogels using a pulse electrochemical deposition method. The composite has achieved a balanced gravimetric capacitance of 182 F g−1 based on the total mass of the composite and areal capacitance of 473 mF cm−2 based on the geometric area of electrode. When using commercial AC as negative electrode material, the asymmetric supercapacitor can reach a stable potential as large as 2 V. It is found that a high specific energy of 26.6 W h kg−1 and specific power of 5.2 kW kg−1 can be realized. To the best of our knowledge, it is the first application of the 3D CNT hydrogel with Mn3O4 for supercapacitors.
2. Experimental section
2.1 Materials
CNTs (single-walled) composed of one third metallic and two thirds of semiconducting nanotubes were obtained from Chengdu Organic Chemicals Co Ltd. Manganese acetate tetrahydrate (Mn(CH3COO)2·4H2O), sodium dodecylbenzene sulfonate (SDBS), activated carbon (AC) and sodium sulfate (Na2SO4) were purchased from Sigma-Aldrich. Absolute ethanol and hydrochloric acid (HCl 37%) were obtained from Merck Pte Ltd. Nickel foams with thickness of 1.2 mm were bought from MTI Co. CNTs were purified by immersing into diluted HCl solution before use. Other chemicals were directly used without further purification.
2.2 Synthesis
Firstly, homogeneous dispersion consisting of CNTs (3 mg mL−1) and SDBS (15 mg mL−1) was prepared using probe sonication (60 W) for 30 min followed by 30 min bath sonication. Afterwards, cleaned nickel foams with area of 1 × 1 cm2 were immersed in the as-prepared CNT dispersion under sonication for 10 min. Next, the CNT-coated nickel foams underwent aging for two days to form inter-connected CNT hydrogels (nanotube micro-scaffolds). The prepared hydrogels were subsequently washed using copious deionized (DI) water for a week to remove remaining surfactants. To obtain the Mn3O4/CNT hybrid hydrogels, plating solution consisting of 100 mM Na2SO4 and 10 mM Mn(CH3COO)2 was prepared in advance. The CNT hydrogels were immersed in the plating solution for 2 h to exchange the water inside with plating solutions. Next, pulse electrochemical deposition was carried out under a current of 2 mA cm−2 with an ON/OFF ratio of 10 s/20 s. After 150 cycles of deposition, the Mn3O4/CNT hydrogels were washed with DI water and stored in water overnight. For characterizations, the Mn3O4/CNT hydrogels were dried using critical carbon dioxide to maintain their original structure. Typically, the mass loadings of the CNT were 0.3–0.5 mg cm−2 and those of composites were in range of 2.2–2.6 mg cm−2. For comparison, pure Mn3O4 was also deposited directly on the nickel foam based on the same protocols in the absence of CNTs.
2.3 Characterizations
The crystal structure of the Mn3O4/CNTs aerogels was determined by the X-ray diffractometer (XRD Shimazu 6000) with Cu Kα radiation. Sample morphology was investigated using the field emission scanning microscopy (FESEM Hitachi S4300). Transmission electron microscopy (TEM) analysis together with selected area electron diffraction (SAED) was performed on the JEOL 2010 transmission electron microscope for further investigation of the sample microstructures.
2.4 Electrochemical measurements
For electrochemical tests with three-electrode configuration, as-prepared Mn3O4/CNT composites were directly used as the working electrodes. Platinum (1 × 1 cm2 in area) and saturated calomel electrode (SCE) were selected as the counter and reference electrodes, respectively. For the assembly of asymmetric supercapacitor, AC was used as the negative electrodes and Mn3O4 or Mn3O4/CNT hydrogel was used as the positive electrodes. The mass ratio between AC and Mn3O4/CNT was 2
:
1 and the ratio between the AC and Mn3O4 was 3
:
2 based on charge balance.32 The asymmetric cells were assembled in swagelok cells with porous cellulose membrane as separators. All electrochemical measurements were carried out in 0.5 M Na2SO4 electrolyte. Cyclic voltammetry (CV), galvanostatic charge/discharge (GCD) and electrochemical impedance spectroscopy (EIS) were conducted on the Solartron 1287 electrochemical workstation. Calculations of the specific capacitance, specific energy and specific power were based on followed equations:33 |
 | (1) |
|
 | (2) |
|
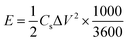 | (3) |
|
 | (4) |
where Cs is the specific capacitance (F g−1), I is the current (A), υ is the scan rate (V s−1) in CV tests, ΔV is the potential window (V), Δt is the discharge time (s), E is the specific energy (W h kg−1) and P is the specific power (W kg−1). For asymmetric supercapacitor tests, m is the total mass (g) of AC and composites on both electrodes.
3. Results and discussions
3.1 Structures and morphologies
The hydrogel composites are synthesized according to the procedure illustrated in Fig. 1. The CNT dispersion undergoes the stage of gelation in ambient atmosphere for two days to form the inter-connected structure, which is reported in our previous work.31 The formation of the CNT 3D network is caused by the strong van der Waals interactions between nanotubes. When placing the CNT hydrogel at the anode for deposition, manganese ions dissolved in water were oxidized under the positive voltage to give Mn3O4 precipitation at the CNT hydrogels described by following equation:34 |
4H2O + 3Mn2+ = Mn3O4 + 2e− + 8H+
| (5) |
 |
| Fig. 1 Schematic illustration of preparation of the Mn3O4/CNT composite. | |
Different from the galvanostatic or potentiostatic depositions, we apply a pulse deposition technique to tune Mn3O4 properties (Fig. S1†). During the “ON” period, the Mn3O4 are grown on the CNTs under a constant current. At the “OFF” stage, the current is set to zero to facilitate the ion diffusion from the central plating solution, considering the large thickness of the prepared hydrogels. As a result, morphology can be carefully controlled to avoid any unwanted agglomerations of active materials.
Fig. 2 presents morphology of the Mn3O4 and Mn3O4/CNT composites. Without the 3D inter-connected CNT networks, Mn3O4 merely stay at the surface of nickel foam, leaving majority of the macro-pores in the nickel foams unoccupied (Fig. 2a). With high magnification shown in Fig. 2b, we can see that the Mn3O4 is composed of severely stacked nanoparticles. This kind of agglomerations will not only hinder the ion diffusion but also extend the electron pathways, leading to poor electrochemical performance.35 For the pristine CNT hydrogels deposited inside the nickel foam, they presented a network consisting of bundled nanotubes (Fig. S2†), which also can be found in our previous report.31 While for the Mn3O4/CNT, the hydrogel fully occupies the macro-pores inside the nickel foams (Fig. 2c). In this architecture, CNT hydrogel serves as a micro-scaffold for electron transport and Mn3O4 plays a role of capacitance enhancer. The CNT micro-scaffold and Mn3O4 with higher magnification can be seen in the Fig. 2d. The CNT micro-scaffold presents the three-dimensional (3D) random inter-connected structure with homogeneously deposited Mn3O4 nano-flowers with a typical size of 300–400 nm. The flower-like Mn3O4 morphology can be ascribed to a controlled pulse deposition method in which Mn3O4 replicates the CNT patterns. The high transparency of Mn3O4 also indicates their ultrathin nature. The mesopores woven from CNTs are believed to effectively facilitate the ion diffusion process and boost the device performance. It is also worth noting that the CNT hydrogel not only fill the macropores inside the nickel foam but also cover the nickel foam backbones as thin layers (Fig. S3†). As a result, CNTs are inclined to grow on nanotubes both inside nickel foam and on nickel foam backbone surface.
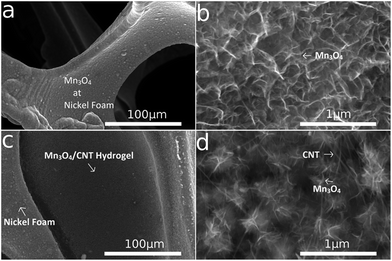 |
| Fig. 2 FESEM images of Mn3O4 on the nickel foam at (a) low and (b) high magnification; the Mn3O4/CNT hydrogel at (c) low, and (d) high magnification. | |
More detailed micro-structure information of materials is investigated by TEM. For the nickel foam directly coated with Mn3O4 (Fig. 3a), manganese oxide phase consists of aggregated secondary particles with an average size around 50 nm. For the Mn3O4/CNT composite (Fig. 3b), we see that nanotubes form several bundles with a diameter around 10 nm, composing a micro-scaffold. The bundling of CNTs is probably caused by capillary force during the gelation period. This kind of micro-scaffold not only will improve the electrical conductivity of the electrode materials but also be effective in preventing Mn3O4 aggregation. Moreover, Mn3O4 is presented as the ultrathin flakes in the composite indicated by their curled peripheral edges. From the SAED images in Fig. 3c and d, the diffraction patterns can be ascribed to (103), (004), (224) crystal planes of Mn3O4 (JCPDS no. 18-0803). No diffraction pattern from CNTs is found due to their low content in the composite.
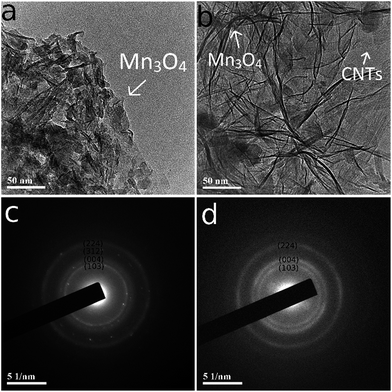 |
| Fig. 3 TEM images of the (a) Mn3O4, (b) Mn3O4/CNT hydrogel; SAED patterns of (c) Mn3O4, and (d) Mn3O4/CNT composites. | |
Typical XRD patterns of the pure Mn3O4 and Mn3O4/CNT hydrogel composite are presented in Fig. S4.† Three main peaks coming from the nickel foam can be easily identified. With a careful observation, peaks located at 34.7°, 39.1° can be ascribed to the tetragonal-phase Mn3O4.36 Compared with peaks from the nickel foam, the Mn3O4 peaks have much smaller intensity, which might be attributable to two aspects. One possible reason is that the hydrogels have a low density, making them highly transparent to the X-rays. The other possible reason is the poor crystallinity of Mn3O4, which is synthesized at room temperature.37 The composition of the samples are also confirmed by the energy-dispersive X-ray spectroscopy (EDX) in which the atomic ratios between manganese and oxygen are closed to 3
:
4 (Fig. S5 and S6†).
3.2 Electrochemical performances
Fig. 4 presents the electrochemical performance of the Mn3O4 and Mn3O4/CNT composites tested with three-electrode configuration. Fig. 4a displays the CV curves of the Mn3O4 and Mn3O4/CNT at 5 mV s−1. Compared with the Mn3O4, our developed 3D hydrogel composite exhibits a larger enclosed area, suggesting a higher specific capacitance. A pair of anodic/cathodic peaks of Mn3O4/CNT is found at 0.62 and 0.47 V, respectively, due to the redox nature of Mn3O4.38 We interestingly find this pair of peak does not appear in the pure Mn3O4 because of a large resistance in the absence of the conductive CNTs. CV curves at different scan rates from 5 to 100 mV s−1 of the Mn3O4/CNT are given in Fig. 4b. A mirror-image feature demonstrates a good reversibility of the electrode materials. Contributed to high electrical conductivity of the 3D CNT structure, the CV loop still maintains almost a rectangular shape at a high scan rate of 100 mV s−1. The calculated specific capacitances are 182 at 2 mV s−1 and 91 F g−1 at 100 mV s−1, respectively. It is worth noting that the specific capacitances of manganese oxides are strongly related to the thickness of the materials.39 Depositing thin layer material can dramatically improve the gravimetric capacitance. Unfortunately, this strategy usually results in an ultralow areal and volumetric capacitance, limiting the application of materials. For example, specific capacitances of more than 200 F g−1 have been reported for Mn3O4 previously, they either calculated capacitance merely based on Mn3O4 or applied a strategy on a basis of ultralow mass loading (<1 mg cm−2) of active materials,40–43 suffering a low areal capacitance. Nevertheless, for our composite, due to a large mass loading over ∼2 mg cm−2, high areal capacitance of 400 mF cm−2 can be reached (Fig. S7†). For our composites, the main roles of the CNTs in this composite are to enhance the conductivity and prevent Mn3O4 agglomeration, instead of the capacitance provider. GCD curves above of Mn3O4/CNT with different specific currents from 0.38 to 19.22 A g−1 are given in the Fig. 4c. The near-linear charge and discharge curves with negligible curvature reflect ideal capacitor behaviour. As seen in Fig. 4d, in contrast to pure Mn3O4 materials, the Mn3O4/CNT composite not only presents a higher capacitance at low discharge rate but also a good retention (71.6%) at high discharge rate.
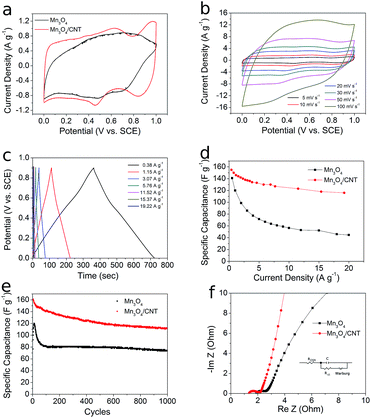 |
| Fig. 4 Electrochemical performance of Mn3O4 and Mn3O4/CNT: (a) CV curves at low scan rate of 5 mV s−1, (b) CV of the Mn3O4/CNT hydrogel at different scan rates, (c) GCD curve of Mn3O4/CNT at different current densities, (d) specific capacitance calculated from tests, (e) long term cycling performance, and (f) EIS results. | |
The cycling performance of the Mn3O4 and Mn3O4/CNT are shown in Fig. 4e. Mn3O4/CNT presents a gradual capacitance drop to 1000th cycles with a final retention of 68.9%. For Mn3O4, a sharp capacitance drop is found after the initial activation capacitance. Then the specific capacitance keeps stable at about 80 F g−1. The final specific capacitance is only 61.7% of the stable capacitance. Fig. 4f shows the EIS results of the Mn3O4 and Mn3O4/CNT composite. Based on the embedded equivalent circuit, the equivalent series resistances (ESR) of Mn3O4 and Mn3O4/CNT are 1.95 and 1.41 ohm, which represent the internal resistance of electrode, electrolyte and connecting wires.44 The smaller ESR of the Mn3O4 is attributable to the good host/guest materials interface between CNTs and Mn3O4, which effectively facilitates the electron transport process.
Considering a scalable production, AC is chosen as the negative electrode material to assembly an asymmetric supercapacitor. The CV curves at 30 mV s−1 of negative (AC) and positive (Mn3O4/CNT) electrode are presented in Fig. 5a. The AC processes a working potential ranging from −1 to 0 V and at the same time the Mn3O4/CNT hydrogel can successfully work within a potential range of 0–1 V. Therefore, the potential window of the asymmetric supercapacitor should be around 2 V. In order to demonstrate this estimation, CV tests of Mn3O4/CNT based asymmetric supercapacitor are carried out as given in the Fig. 5b. Rectangular loops can be observed with a potential window extending from 1 to 2 V, suggesting a good stability under higher potential. The larger working potential range also increased specific capacitance, indicated by a current increasing. The improved electrochemical performance under higher potential is related to the deeper activated Mn3O4. The GCD profiles of asymmetric supercapacitors using Mn3O4/CNT composites are displayed in Fig. 5c. A potential as high as 2 V can be guaranteed at the discharge rate from 0.5 to 10 A g−1. Higher specific capacitance of Mn3O4/CNT compared with Mn3O4 benefits from the better electrochemical performance of positive electrode (Fig. 5d).
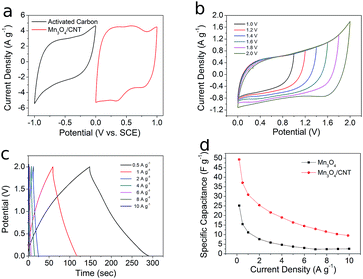 |
| Fig. 5 Electrochemical performance of the asymmetric supercapacitor: (a) comparative CV of AC (black) and the Mn3O4/CNT hydrogel (red) at 30 mV s−1, (b) CV of the asymmetric supercapacitor measured at different potentials at 30 mV s−1, (c) GCD curves of the asymmetric supercapacitor at different current densities, and (d) specific capacitances from GCD tests. | |
The cycling stability of two kinds of the asymmetric supercapacitors is shown in Fig. 6a. Initial activations are found for both Mn3O4 and Mn3O4/CNT which are associated with the electrolyte infiltration. After the short activation process, the Mn3O4/CNT composite could reach a stable specific capacitance above 25 F g−1 and achieved a good retention of 103.9% after 1000th cycling. While for Mn3O4, only 84.0% of original capacitance is reserved. It is interesting to find there is a discrepancy of cycling stability tested with two-electrode and three-electrode configuration. We propose there two reasons to explain. Firstly, in three-electrode configuration, the composite was connected to the electrical wire using a simple conducting alligator and there is no other external force between the testing material and outer circuit. As a result, the any kind of fracture of materials due to cycling will directly drop into the electrolyte, causing the capacitance degradation. While in two-electrode configuration, the negative electrode, separator and positive electrodes were assembled in a swagelok cell. Under a tightening force from screw thread, even the fractured material is still in contact with the nickel foam, leading to a better cycling stability. Secondly, though the three-electrode cell was sealed using parafilm during the cycling performance, the sealing capability is not as good as ones with swagelok cell. Thus the degradation of the electrolyte might cause the cycling drop. To understand the power and energy performance of the assembled asymmetric supercapacitors, Ragone plot is given in Fig. 6b. High specific energy of 26.6 W h kg−1 and 5.6 kW kg−1 are achieved for Mn3O4/CNT, which is better than the pure Mn3O4 and other related reports.44–49
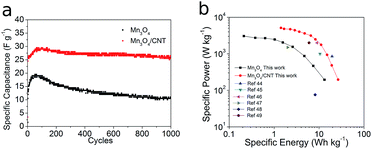 |
| Fig. 6 (a) Cycling stability and (b) Ragone plot of asymmetric supercapacitors. | |
To further reveal the degradation mechanism of the electrode materials, we have characterized our sample using FESEM after cycling tests (Fig. 7). As can be seen in Fig. 7a, a large number of the tiny surface agglomerations have been observed for Mn3O4. The large surface changes compared to the pristine Mn3O4 can be attributed to the structural changes from surficial ion intercalation in the long term cycling test. For the Mn3O4/CNT composite (Fig. 7b), we can also observe morphology changes with bundled CNTs. This kind of morphology evolution is responsible for the capacitance degradation after activation period (∼100th cycle). However, due to the electron pathways established by CNTs and the ultrathin nature of Mn3O4, the composite is still capable to maintain its majority of its original capacitance.
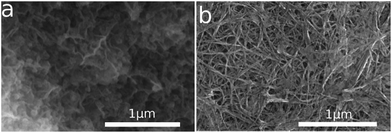 |
| Fig. 7 FESEM images of (a) Mn3O4 and (b) the Mn3O4/CNT hydrogel after cycling. | |
4. Conclusions
In summary, we have successfully developed the Mn3O4/CNT hydrogels for supercapacitor applications. By utilizing a pulse electrochemical deposition, a high areal capacitance above 473 mF cm−2 can be achieved. The assembled asymmetric supercapacitor can reach a potential as high as 2 V in the aqueous electrolyte. Compared with the single-component Mn3O4 deposited on nickel foams, Mn3O4/CNT hydrogel has shown superior electrochemical performance both in higher capacitance and better cycling stability. This improvement can be attributed to the advantages of the CNT micro-scaffold, which (1) serving as electron transport highway and (2) inhibiting serious aggregation of active materials. We believe our prepared composites may also have applications in the field of battery electrodes and electrochemical catalysis.
Acknowledgements
We would like to take this opportunity to thanks Environmental Technology Program R-265-000-450-490 and Defence Research and Technology of MINDEF-R-394-001-077-232 for financial support. We are also grateful to Prof Lu Li from Department of Mechanical Engineering, NUS, for helpful discussion.
Notes and references
- N. Armaroli and V. Balzani, Energy Environ. Sci., 2011, 4, 3193–3222 Search PubMed.
- A. Laurent and N. Espinosa, Energy Environ. Sci., 2015, 8, 689–701 Search PubMed.
- M. Z. Jacobson, Energy Environ. Sci., 2009, 2, 148–173 CAS.
- Z. Yang, J. Zhang, M. C. W. Kintner-Meyer, X. Lu, D. Choi, J. P. Lemmon and J. Liu, Chem. Rev., 2011, 111, 3577–3613 CrossRef CAS PubMed.
- M. Winter and R. Brodd, Chem. Rev., 2004, 104, 4245–4269 CrossRef CAS PubMed.
- B. E. Conway, Electrochemical Supercapacitors, Kluwer Academic/Plenum Press, New York, 1999 Search PubMed.
- P. Simon and Y. Gogotsi, Nat. Mater., 2008, 7, 845–854 CrossRef CAS PubMed.
- L. L. Zhang and X. S. Zhao, Chem. Soc. Rev., 2009, 38, 2520–2531 RSC.
- J. Chang, Z. Gao, X. Wang, D. Wu, F. Xu, X. Wang, Y. Guo and K. Jiang, Electrochim. Acta, 2015, 157, 290–298 CrossRef CAS.
- F. Gao, G. Shao, J. Qu, S. Lv, Y. Li and M. Wu, Electrochim. Acta, 2015, 155, 201–208 CrossRef CAS.
- D. Liu, W. Zhang, H. Lin, Y. Li, H. Lu and Y. Wang, RSC Adv., 2015, 5, 19294–19300 RSC.
- J. Yan, Q. Wang, T. Wei and Z. Fan, Adv. Energy Mater., 2014, 4, 1300816 Search PubMed.
- W. Wei, X. Cui, W. Chen and D. G. Ivey, Chem. Soc. Rev., 2011, 40, 1697–1721 RSC.
- K. K. Lee, W. S. Chin and C. H. Sow, J. Mater. Chem. A, 2014, 2, 17212–17248 CAS.
- G. S. Snook, P. Kao and A. S. Best, J. Power Sources, 2011, 196, 1–12 CrossRef CAS.
- H. Cheng, A. D. Su, S. Li, S. T. Nguyen, L. Lu, C. Y. H. Lim and H. M. Duong, Chem. Phys. Lett., 2014, 601, 168–173 CrossRef CAS.
- D. P. Dubal, G. S. Gund, C. D. Lokhande and R. Holze, ACS Appl. Mater. Interfaces, 2013, 5, 2446–2454 CAS.
- D. Z. W. Tan, H. Cheng, S. T. Nguyen and H. M. Duong, Mater. Technol., 2014, 29, A107–A113 CrossRef CAS.
- J. Kim, K. H. Lee, L. J. Overzet and G. S. Lee, Nano Lett., 2011, 11, 2611–2617 CrossRef CAS PubMed.
- Y. Shan and L. Gao, Mater. Chem. Phys., 2007, 103, 206–210 CrossRef CAS.
- X. Wang, M. Li, Z. Chang, Y. Yang, Y. Wu and X. Liu, ACS Appl. Mater. Interfaces, 2015, 7, 2280–2285 CAS.
- X. Wang, X. Han, M. Lim, N. Singh, C. L. Gan, M. Jan and P. S. Lee, J. Phys. Chem. C, 2012, 116, 12448–12454 CAS.
- H. Xia, J. Feng, H. Wang, M. O. Lai and L. Lu, J. Power Sources, 2010, 195, 4410–4413 CrossRef CAS.
- D. Zhao, Z. Yang, L. Zhang, X. Feng and Y. Zhang, Electrochem. Solid-State Lett., 2011, 14, A93 CrossRef CAS.
- Y. Fang, F. Jiang, H. Liu, X. Wu and Y. Lu, RSC Adv., 2012, 2, 6562–6569 RSC.
- X. Li, W. Sun, L. Wang, Y. Qi, T. Guo, X. Zhao and X. Yan, RSC Adv., 2014, 5, 7976–7985 RSC.
- G. Zhu, Z. He, J. Chen, J. Zhao, X. Feng, Y. Ma, Q. Fan, L. Wang and W. Huang, Nanoscale, 2014, 6, 1079–1085 RSC.
- Z. Tang, C. Tang and H. Gong, Adv. Funct. Mater., 2012, 22, 1272–1278 CrossRef CAS.
- J. Wu, P. Guo, R. Mi, X. Liu, H. Zhang, J. Mei, H. Liu, W. M. Lau and L. M. Liu, J. Mater. Chem. A, 2015, 3, 15331–15338 CAS.
- M. B. Bryning, D. E. Milkie, M. F. Islam, L. A. Hough, J. M. Kikkawa and A. G. Yodh, Adv. Mater., 2007, 19, 661–664 CrossRef CAS.
- H. Cheng and H. M. Duong, RSC Adv., 2015, 5, 30260–30267 RSC.
- F. Wang, S. Xiao, Y. Hou, C. Hu, L. Liu and Y. Wu, RSC Adv., 2013, 3, 13059–13084 RSC.
- C. Yang, M. Zhou and Q. Xu, Phys. Chem. Chem. Phys., 2013, 15, 19730–19740 RSC.
- H. Xia, M. Lai and L. Lu, JOM, 2011, 63, 54–59 CrossRef CAS.
- D. Li, F. Meng, X. Yan, L. Yang, H. Heng and Y. Zhu, Nanoscale Res. Lett., 2013, 8, 1–8 CrossRef PubMed.
- G. Jian, Y. Xu, L. C. Lai, C. Wang and M. R. Zachariah, J. Mater. Chem. A, 2014, 2, 4627–4632 CAS.
- J. X. Feng, S. H. Ye, X. F. Lu, Y. X. Tong and G. R. Li, ACS Appl. Mater. Interfaces, 2015, 7, 11444–11451 CAS.
- L. Yang, S. Cheng, X. Ji, Y. Jiang, J. Zhou and M. Liu, J. Mater. Chem. A, 2015, 7338–7344 CAS.
- Q. Wang, J. Yan and Z. Fan, Energy Environ. Sci., 2016, 9, 729–762 CAS.
- D. P. Dubal, D. S. Dhawale, R. R. Salunkhe, S. M. Pawar and C. D. Lokhande, Appl. Surf. Sci., 2010, 256, 4411–4416 CrossRef CAS.
- J. Yang, X. Yang, Y. L. Zhong and J. Y. Ying, Nano Energy, 2015, 13, 702–708 CrossRef CAS.
- F. Yang, M. Zhao, Q. Sun and Y. Qiao, RSC Adv., 2015, 5, 9843–9847 RSC.
- J. Kim, K. H. Lee, L. J. Overzet and G. S. Lee, Nano Lett., 2011, 11, 2611–2617 CrossRef CAS PubMed.
- Z. Lei, J. Zhang and X. S. Zhao, J. Mater. Chem., 2012, 22, 153–160 RSC.
- Y. Jin, H. Chen, M. Chen, N. Liu and Q. Li, ACS Appl. Mater. Interfaces, 2013, 5, 3408–3416 CAS.
- L. Li, Z. A. Hu, N. An, Y. Y. Yang, Z. M. Li and H. Y. Wu, J. Phys. Chem. C, 2014, 118, 22865–22872 CAS.
- Y. Cheng, S. Lu, H. Zhang, C. V. Varanasi and J. Liu, Nano Lett., 2012, 12, 4206–4211 CrossRef CAS PubMed.
- Y. Li and X. M. Li, RSC Adv., 2013, 3, 2398–2403 RSC.
- W. Xing, S. Z. Qiao, R. G. Ding, F. Li, G. Q. Lu, Z. F. Yan and H. M. Cheng, Carbon, 2006, 44, 216–224 CrossRef CAS.
Footnote |
† Electronic supplementary information (ESI) available: Including additional SEM images, XRD patterns, EDX results and areal capacitances. See DOI: 10.1039/c6ra02858f |
|
This journal is © The Royal Society of Chemistry 2016 |
Click here to see how this site uses Cookies. View our privacy policy here.