DOI:
10.1039/C6RA00243A
(Paper)
RSC Adv., 2016,
6, 37149-37159
Influence of trifluoropropyl-POSS nanoparticles on the microstructure, rheological, thermal and thermomechanical properties of PLA
Received
5th January 2016
, Accepted 6th April 2016
First published on 7th April 2016
Abstract
In this work the influence of polyhedral oligomeric silsesquioxane (POSS) content with trifluoropropyl substituents on the microstructure, rheological behavior, non-isothermal crystallization behavior, thermomechanical and thermal properties of poly(lactic acid) nanocomposites prepared via melt blending was investigated using various techniques for understanding the structure–property relationship. Morphological analysis (SEM, EDX and XRD) showed that POSS particles have a fine dispersion at low content (up to 2.5 wt%) in a polymer matrix but the imposed processing conditions were not able to prevent the formation of large POSS agglomerates at high POSS contents because of strong interaction among the POSS particles. It was observed that only the POSS nanoparticles dispersed almost at molecular level could act as a lubricant in the system since lower values for the glass transition temperature, storage modulus and complex viscosity were observed from DMA and rheological investigations. The viscosity and elasticity of PLA were improved in the presence of high contents of POSS however, the degree of enhancement was not strong enough for a transition from liquid-like to solid-like behavior. In addition, the POSS particles at low loadings had a promoting impact on the cold crystallization of PLA while at high loadings the cold crystallization was retarded. Also, it was found that the presence of POSS slightly reduced the thermal stability of the nanocomposites relative to the neat PLA. However, the thermal degradation mechanism of PLA remained unchanged.
1. Introduction
In recent years the field of organic–inorganic hybrid nanocomposite materials has attracted a great deal of attention from scientific and industrial points of view, due to their potential as suitable materials for replacing conventional nanocomposites.1,2 The enhancement of various physical properties is expected to result from the incorporation of a nano-sized inorganic component into an organic polymer matrix which arises from the synergism between the properties of the components.3 In particular, use of polyhedral oligomeric silsesquioxane (POSS) nanoparticles has been demonstrated as an efficient method for designing hybrid nanocomposite materials.4,5 POSS belongs to a wide family of silsesquioxanes, characterized by the general formula (RSiO1.5)n where R is hydrogen or an organic group, such as alkyl, alkylene, aryl, arylene or any of their derivatives. POSS compounds represent a truly hybrid (inorganic–organic) architecture that contains an inner inorganic framework which is externally enclosed by organic substituents. These substituents can be totally hydrocarbon in nature or they can have a range of polar structures with various functional groups. Therefore, depending on the functional groups, POSS can be reactive or nonreactive. Unlike traditional organic compounds, POSS chemicals release no volatile organic components, so they are odorless and environmentally friendly.6–10 The POSS derivatives can be introduced into polymer matrix via copolymerization and grafting or by physical blending. Copolymerization is an efficient approach through which POSS with reactive functional groups may form chemical link with the monomer, and thus can raise glass transition temperature and enhance mechanical performance and thermal stability of polymer.11–13 However, thanks to advantages of physical blending such as low cost and easy implementation in the industrial process, it has attracted huge research interest from the practical point of view. In this approach, in contrast to copolymerization and grafting, there are no covalent POSS–polymer linkages and there is possibility of crystal formation and aggregation (the crystallization is often hindered in the chemically grafted systems). Several polymers such as polyethylene (PE),14,15 polypropylene (PP),16,17 ethylene–propylene copolymer,18 polycarbonate (PC),19 polystyrene (PS),20 poly(methyl methacrylate) (PMMA)21 and poly(vinylidene fluoride) (PVDF)22,23 have been physically blended with POSS.
Nowadays, as a result of environmental pollution and increasing of plastic waste, biodegradable and renewable materials have been in focus of attention.24,25 Poly(lactic acid) (PLA) which is one of the commercialized biodegradable polymers with excellent properties for various applications, has been emerged as an alternative to conventional petroleum based polymeric materials.26 However, in order to compete with most of commonly used polymers, the performances of PLA, such as impact strength, elongation at break, and crystallization and degradation rate, must be improved without compromising its inherent sustainability.27,28 Indeed, the dispersion of proper nanofillers within PLA can significantly improve the polymer matrix properties. Many, organic and inorganic nanomaterials such as carbon nanotube (1D), graphene (2D), layered silicates and nanocellulose have been incorporated into PLA to obtain desired properties due to their unique structural characteristics. So far carbonaceous-based PLA nanocomposites have extensively been investigated and many reports about its various aspects such as distribution and surface modification of filler and also properties of the nanocomposite are available in the literature. For example, according to the literature by incorporating of carbon materials a significant improvement in electrical conductivity, mechanical properties (tensile strength and modulus), flame retardancy, nucleating and crystallization ability of PLA has been observed. In addition to the carbon materials, a widespread research has been done on layered silicate-based and nanocellulose-based PLA nanocomposites by various scientists.24,29,30 However, there are several nanofillers including polyhedral oligomeric silsesquioxanes (POSS), silica nanoparticles and magnetite nanoparticles (Fe3O4) that have scarcely been investigated in the design of PLA-based nanocomposites in contrast to layered silicates or carbon materials.24 By comparison with most of commercially available nanofillers, POSS nanoparticles have the smallest and monodisperse size, together with a low density. It has an advantage that can be readily applied to a wide range of polymers through simple blending approach. A few reports are available in the literature about the physical incorporation of different types of POSS into PLA matrix. Qiu et al.31–34 investigated PLA/POSS nanocomposites using different types of POSS having octamethyl, octavinyl, octaisobutyl substituents prepared via solution and melt compounding methods with a special emphasis on the crystallization behavior of PLA. It was reported that the overall crystallization rates in PLLA/POSS nanocomposites increased with increasing POSS content while the crystal structure of PLA remained unchanged. The storage modulus and hydrolytic degradation rates for PLA matrix were also enhanced in the PLA/POSS nanocomposites as compared to neat PLA. Zhang et al.35 reported the utilization of octa(3-chloropropylsilsesquioxane) with eight chloropropyl groups in PLA. In addition to the nucleating effect, the POSS nanoparticles acted as plasticizer too. Also, tensile results showed that the neat brittle PLA attained ductile nature as strain at break was remarkably improved. In other work, improvement of biodegradation rate and thermal stability of PLA in presence of octaphenyl-POSS was reported.36 The mechanical, thermal, and morphological properties of melt compounded aminopropylisobutyl–POSS/PLA nanocomposites were investigated by Turan et al.37 They found that the addition of POSS to the PLA reduced the melt viscosity of the composites and increased modulus and elongation at break as well as the crystallinity of PLA. A comparative study about the effect of four types of POSS (reactive and non-reactive) on the mechanical and thermal properties of PLA has been reported.38,39 The results showed that the glass transition temperature of PLA was decreased with the addition of POSS particles and toughness-related properties such as impact strength and elongation at break were improved. POSS particles also enhanced the decomposition temperature of PLA.
The mentioned literature review shows that based on the type of organic section of POSS, it can have reinforcing effect or it may act as a plasticizer. Moreover, the main focus of the reported works on PLA/POSS system has been on role of POSS in enhancing the toughness and improving mechanical properties of PLA however, the role of fluorinated type of POSS (trifluoropropyl-POSS) having excellent properties such as high strength, high molecular weight, high sublimation temperature and low surface energy,40 on various properties of PLA especially on its rheological features and microstructure have not been investigated so far. The novelty of the present work is two folds; first, development of a new type of PLA composites based on a fluorinated kind of POSS via a simple melt mixing method. The second novelty lies in performing a comprehensive study for the first time on various features of the system with main focus on rheological properties and its correlation with microstructure of the PLA/trifluoropropyl-POSS system.
Therefore, the main objective of this work is to understand the influence of organic–inorganic nanofiller (trifluoropropyl-POSS) incorporation on the microstructure, rheological, thermal and thermomechanical properties of PLA. It is expected that this research will be of interest for a better understanding of the structure–properties relationship and extending practical applications of this important class of hybrid biodegradable polymer nanocomposites in the field of biomedical and packaging industries.
2. Experimental section
2.1. Materials
PLA (Ingeo 4043D grade) with density of 1.24 g cm−3, weight average molecular weight of 100
000 g mol−1 and isomeric form of L/D = 98/2 was purchased from Nature Works (USA). The POSS-derivative used in this study was FL0578-trifluoropropyl POSS® Cage Mixture (where R = CH2CH2CF3) with molecular formula of (C3H4F3)n (SiO1.5)n (n = 8, 10, 12) in powder form and purchased from Hybrid Plastics, Inc. (USA). It has a molecular weight of 1193.16 g mol−1. The molecular structure of trifluoropropyl-POSS for n = 8 is presented in Fig. 1. Prior to melt blending, all the materials were dried for 4 hour at 80 °C in a vacuum oven.
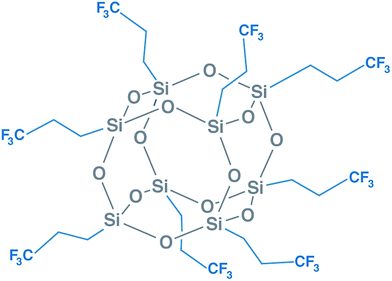 |
| Fig. 1 Molecular structure of trifluoropropyl-POSS (n = 8). | |
2.2. Sample preparation
A conical twin screw DACA micro-compounder (DACA Instruments) with a processing temperature of 190 °C, a screw speed of 200 rpm, and a mixing time of 5 min was used for preparation of all the nanocomposites. The extruded strands were cooled on an aluminum tray in air. Various amounts of POSS were incorporated into PLA via one step melt mixing. For brevity, the nanocomposites containing 1, 2.5, 5, 10 and 20 wt% of POSS are abbreviated as POSS-1, POSS-2.5, POSS-5, POSS-10 and POSS-20 from now on.
2.3. Characterization techniques
2.3.1. Morphology.
2.3.1.1. Scanning electron microscopy (SEM). The cryo-fractured surface morphology of various nanocomposite samples was studied by a TESCAN Vega 3 SBU (Czech Republic) scanning electron microscopy (SEM), which is equipped with an energy dispersive X-ray spectrometer (EDX) for automatic quantitative elemental analysis. This technique was used to trace distribution of Si element throughout the PLA matrix. The low operating voltage of 10 kV was selected due to sensitivity of PLA to degradation. The specimens were gold sputtered prior to examination to avoid charging during electron irradiation.
2.3.1.2. Wide-angle X-ray scattering (WAXS). The WAXS patterns of the samples were recorded on Siemens, Model D5000 (Germany) X-ray diffractometer operating at 35 kV and 30 mA employing Cu Kα radiation with a wavelength of l.54056 Å, over the angular region of 2θ between 4 and 35° at steps of 0.02° s−1.
2.3.2. Oscillatory rheological measurements. The dynamic rheometry in the melt state was carried out with an ARES rheometer (Rheometric Scientific, Inc.), using small-amplitude oscillatory frequency sweeps. The selected geometry for frequency sweeps and heating/cooling sweeps in the molten state was the parallel plate geometry (gap of about 2 mm and diameter of 25 mm). The rheological measurements were performed on compression-molded disks of pure PLA and its nanocomposites containing different amounts of POSS under dry nitrogen atmosphere in order to prevent the oxidative degradation and also hydrolysis of PLA. Dynamic frequency sweep experiments were then performed at strain of 5% (linear viscoelastic region) and in frequency range of 0.03–100 rad s−1. All the measurements were carried out at fixed temperature of 190 °C.
2.3.3. Differential scanning calorimetry (DSC). Crystallization and melting behaviors of prepared samples in non-isothermal mode were studied using DSC Q2000 (TA Instruments). All operations were performed under nitrogen purge. A sample of about 5 mg from each composition was scanned in a cycle of heating–cooling–heating from 0 to 220 °C at rate of 10 °C min−1. In order to produce a uniform thermal history, the samples were held at 220 °C for 5 min. The glass transition temperature, the cold crystallization onset temperature, cold crystallization peak temperature and melting temperature of neat PLA and its nanocomposites were read from the second heating traces.
2.3.4. Dynamic mechanical analysis (DMA). The dynamic mechanical properties in the solid state were examined by a Q800 DMA (TA Instruments) to determine the viscoelastic properties in bending mode. Rectangular bar specimens with dimension of 10 mm × 30 mm × 0.5 mm were employed for testing. Samples were heated from −20 to 140 °C with a heating rate of 3 °C min−1 at a frequency of 1 Hz. The samples were scanned for their viscoelastic responses including storage modulus (E′), loss modulus (E′′), and loss factor (tan
δ).
2.3.5. Thermogravimetric analysis (TGA). The thermal stability of the PLA and its nanocomposites were analyzed by thermogravimetric analysis (TGA) using a TGA Q 5000 of TA Instruments with a heating rate of 10 °C min−1. The temperature was scanned from room temperature to 650 °C under nitrogen atmosphere.
3. Results and discussion
3.1. Morphology
It is well-understood that the dispersion level of POSS in the polymer matrix has an important role on physical properties of a biodegradable polymer. In this regard morphological analysis was performed by means of SEM equipped with EDX and XRD measurements. To investigate the PLA microstructure before and after formation of nanocomposites WAXS patterns with a scattering angle (2θ) varying from 4 to 35° were employed. The normalized WAXS patterns of pure POSS powder, neat PLA and their corresponding nanocomposites are presented in Fig. 2. It is seen from Fig. 2 that pure trifluoropropyl-POSS is highly crystalline, showing three characteristic diffraction peaks at around 7.8°, 19.3° and 20.2° while neat PLA is in the amorphous state and hence no peak is detectible at room temperature. This is fully in line with DSC results, discussed in the subsequent section, which indicate that PLA crystallization does not occur during the cooling step. By considering the WAXS patterns of the nanocomposites the characteristic dominant POSS peaks appear for nanocomposites with high content of nanofiller, suggesting that POSS nanoparticles do not have a molecular level dispersion state and mainly form crystalline aggregates. In samples with low contents of POSS (i.e. POSS-1 and POSS-2.5) the WAXS patterns show no detectable crystalline peaks. This may imply a good dispersion of POSS nanoparticles at low content in PLA matrix however, it should be noted that due to WAXS limitation the low amounts of POSS may not be detectable by this technique. Therefore additional morphological evidences based on SEM and EDX analysis should be provided to precisely define the microstructure of developed nanocomposites.
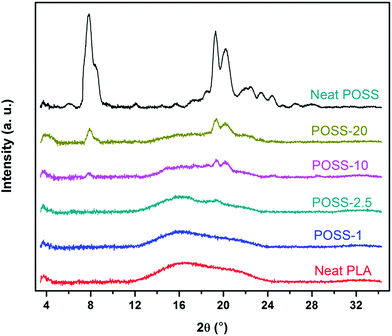 |
| Fig. 2 Normalized wide-angle X-ray scattering patterns of pure POSS, PLA and its nanocomposites (the plots were shifted for more clarity). | |
The SEM images in Fig. 3 show cryo-fractured surface morphology of PLA nanocomposite samples with similar magnification (2000×). By focusing on the fracture surfaces, it is obvious from the images that the POSS-1 has a comparatively smooth surface but much rougher surfaces are observed for the nanocomposites with higher contents of POSS. Presence of POSS induces the stretched and wrapped patterns to the fracture surface. Regarding POSS dispersion level, it can be seen that the compatibility between the POSS and PLA matrix is good up to 2.5 wt% but it decreases at higher content of POSS, leading to formation of micro-aggregates that are homogeneously dispersed throughout the matrix. Also, extent of formation of micro-aggregates systematically intensifies with increased loading of POSS. Consequently, many small crystallites of POSS, as well as its large agglomerates (≈10 μm), are clearly observed predominantly at high loadings of POSS.
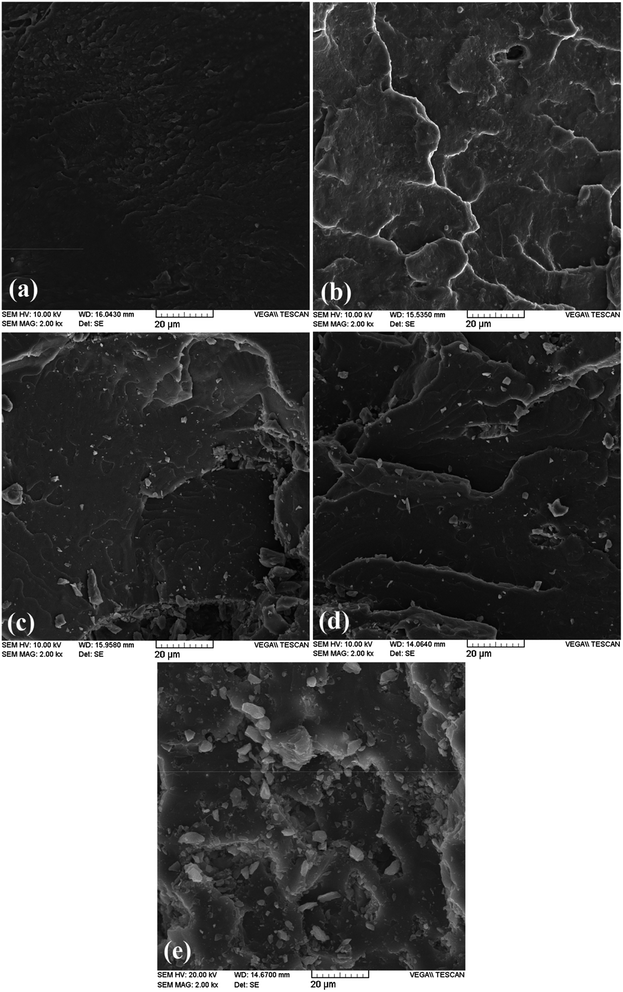 |
| Fig. 3 SEM images of fractured surface of (a) POSS-1, (b) POSS-2.5, (c) POSS-5, (d) POSS-10 and (e) POSS-20 nanocomposite samples. | |
According to the POSS structure displayed in Fig. 1, the trifluoropropyl functional groups induce a very non-reactive nature to the surface of POSS nanoparticles. This helps in formation of aggregates between the POSS cages as a result of weak interaction with PLA. Hence, the dominant driving force behind homogeneous distribution of micro-aggregates is the imposed shear forces during mixing process. EDX results of PLA/POSS composites presented in Fig. 4 reveal the dispersion state of silicon element within the polymer matrix. The white spots in the dark background indicate the location of silicon element within the hybrid composites, which can reflect the dispersion of POSS because only POSS component possesses silicon element in the hybrids. As shown in Fig. 4, the distribution of silicon element is uniform in POSS-1 sample which ascertains a good dispersion of filler in PLA matrix but compact spots are detected in some regions at high loadings that may be attributed to existence of micro-aggregates. In summary based on the SEM and EDX analysis it can be concluded that POSS is dispersed near to molecular level in low content (POSS-1 and POSS-2.5) however, at high loadings a homogeneous distribution of micro-aggregates is observed within the polymeric matrix. It is worthwhile to mention that according to the literature, dispersion of octamethyl-POSS was better in PLA34 than in some other polymer matrices such as linear low-density PE (LLDPE)14 and PP.16 Also, a slightly better dispersion was attained for PLA/octaisobutyl-POSS nanocomposites prepared via solution and coagulation method31 in comparison with solution casting method.32 Therefore, the aggregation of POSS in the polymer matrix not only depends on the type of POSS but also on the polymer matrix type and nanocomposite preparation method.
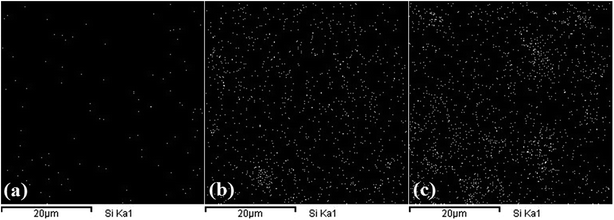 |
| Fig. 4 EDX mapping scanning for Si element in (a) POSS-1, (b) POSS-10 and (c) POSS-20. | |
3.2. Rheological analysis
Melt rheology of neat PLA and its nanocomposites containing various amounts of POSS nanoparticles were carried out under small amplitude oscillatory shear for evaluation of linear viscoelastic behavior of the samples. As it was mentioned in introduction there is no detailed rheology analysis of PLA/POSS system and most of the investigations are concerned with the mechanical properties and toughening issues. The linear viscoelastic (LVE) region for each polymer is characterized by the onset of the strain dependent behavior using dynamic strain sweep measurements.41 This region for PLA has been reported in literature.30,42 Therefore, a constant strain of 5% was used for dynamic frequency sweeps of all samples. The complex viscosity (η*) of PLA and its nanocomposites is shown in Fig. 5a. As it can be seen, a Newtonian behavior for all samples is detectible since the value of viscosity experiences an insignificant change with increasing the shear rate up to about 5 rad s−1. The value of complex viscosity drops at lower POSS content (POSS-1 and POSS-2.5) and thereafter increases with increasing POSS loading. To observe it clearly, the influence of POSS content on complex viscosity at two frequencies of 0.1 and 10 rad s−1 is shown in Fig. 5b. First of all, it is clearly evident that the difference between the values of complex viscosity at two frequencies rises with increasing of the POSS content. This means that the dependency of viscosity on shear rate (frequency) becomes more dominant at high content of POSS, indicating more deviation from Newtonian behavior. The reduction of viscosity with respect to neat PLA in nanocomposites containing low amount of nanofiller implies that the POSS nanoparticles have a lubrication effect. This can be interpreted based on the dispersion state and also the strength of interactions between filler–filler and filler–polymer. As observed from the SEM images presented in Fig. 3 POSS has a good dispersion state at low content particularly in the case of POSS-1 which seems to have a molecular level dispersion state. Also there is no strong interaction between nanoparticles and polymer matrix such as chemical linkage or hydrogen bonding because of inherent non-reactive nature of trifluolorpropyl substituents. So, by considering the obtained molecular level dispersion state and also very insignificant interaction of POSS with PLA, the mobility of PLA chains enhances due to the reduction in entanglement density and more free volume in the melt due to voluminous POSS molecules. Similar trend (lubrication role) has also been observed in some polymer nanocomposites based on POSS such as PVDF/POSS nanocomposites.23 Also a comparative study on effect of different types of POSS molecules on the viscosity of PLA and plasticized PLA exists in the literature. However, for trace of viscosity change detailed rheological analysis was not carried out in those works, besides this, a vertical force measurement (torque) was used as a measure of melt viscosity of the materials processed as a function of composition which is not so accurate. Consistent with our results, it was revealed that the viscosity of PLA and also plasticized PLA was reduced when it was physically blended with various kinds of POSS including aminopropylisobutyl-, glycidylisobutyl-, trisilanolisobutyl- and octaisobutyl-POSS.38,39 The lubrication effect of POSS is diminished with increasing its concentration. POSS-5 and POSS-10 show almost same viscosity with neat PLA but a noticeable change is observed just in the case of POSS-20. The morphology analysis illustrated formation of remarkable POSS aggregates at these concentrations. These micro-aggregates are expected to oppose with drop of viscosity due to the imposed hindrance effect on mobility of polymer chains. The reason of unchanged viscosity can be very weak interaction with matrix and also lubricating role of a portion of POSS nanoparticles. However, POSS-20 displays higher viscosity due to dominant restriction effect on chain mobility.
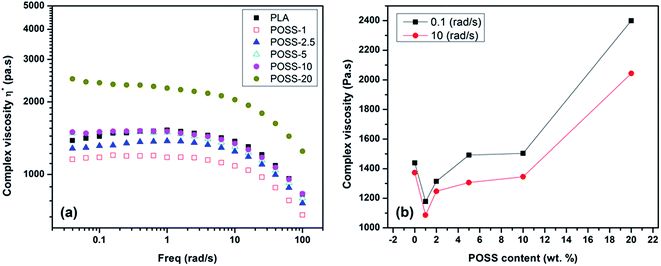 |
| Fig. 5 The plots of complex viscosity (a) as a function of frequency for all samples and (b) as a function of POSS content for two frequencies. | |
To further understand the effect of POSS on the viscoelastic properties of PLA and possibility of physical network formation, the relationship between the POSS concentration and frequency dependence of the shear storage modulus (G′) and loss modulus (G′′) is shown in Fig. 6. It can be seen from Fig. 6a that at high frequencies the value of storage modulus is almost independent of POSS concentration. Thus, the frequency dependence of the relaxation behavior in the high frequency region in PLA/POSS nanocomposites is not noticeably affected by the addition of POSS molecules. In contrast, in the low frequency region, effect of POSS content on storage modulus is more pronounced. To state clear, in low frequencies it can be seen that the slope of the plot decreases in comparison with neat PLA at high content of POSS. Also the values of G′ for POSS-20 are higher than that of neat PLA, indicating more elasticity which is consistent with the result of viscosity. However, according to Fig. 6b influence of POSS content on the values of loss modulus is similar at all frequencies. Although POSS-20 has higher elasticity but it is clear from the inserted plot in Fig. 6b that there is no cross section point even in this sample and G′ has lower value than G′′ at all range of frequency. So according to the results, it can be concluded that only at high content of POSS (20 wt%) the elasticity of PLA is slightly improved but the degree of enhancement is not in the range of transition from liquid-like to solid-like behavior. In addition to the mentioned reasons such as weak interaction and lubrication effect, it should be noticed that the geometry of filler has also a contribution on rheological behavior of PLA/POSS nanocomposites. In contrast to layered nanostructures, POSS has low aspect ratio and the formation of interconnection structures does not occur even at 20 wt% of POSS content. Therefore, the rheological behavior is just affected by occurrence of some agglomerations.
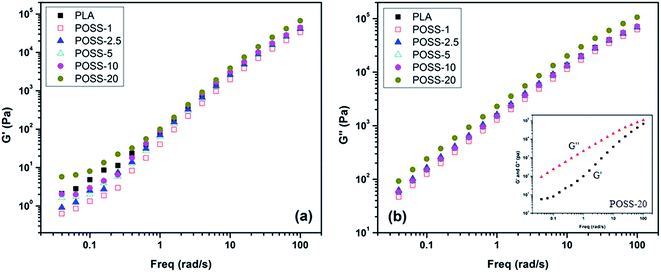 |
| Fig. 6 Frequency dependence of (a) storage modulus and (b) loss modulus of unfilled PLA and its nanocomposites. | |
3.3. Non-isothermal crystallization
Generally, theoretical analysis of crystallization process is done in the situations where the external conditions are constant since in this case the problems associated with the cooling rate and the variation of physical parameters with temperature and also the problems originated from instrumental lags and thermal gradients within the samples are limited. However, industrial processes are carried out generally under non-isothermal conditions. In this regard it is important to study crystallization process in a continuously changing environment.43,44 So, in order to investigate the effect of POSS nanoparticles on the crystallization of PLA matrix, non-isothermal crystallization of neat PLA and its nanocomposites with varying POSS loadings was studied at cooling and heating rate of 10 °C min−1. The DSC thermograms are shown in Fig. 7 and the characteristic data obtained from those thermograms have been tabulated in Table 1. The cooling step of DSC experiment is plotted in Fig. 7a. It is clear from the figure that there is not any exothermic peak for both the neat PLA and its nanocomposites during the cooling step. This suggests that it was too fast for PLA to crystallize at a cooling rate of 10 °C min−1. However, in the sample containing 20 wt% of POSS a very insignificant peak is detectible at around 106 °C with crystallization enthalpy of 0.7 J g−1 and about 1% crystallinity. As a result of low crystallizability, this is a typical behavior for PLA at cooling run. In this regard many efforts have been devoted to improve the crystallization behavior of PLA using various nucleation agents and plasticizers.28 When there is not adequate time during cooling, the opportunity exists for polymer to crystallize during subsequent heating step. Fig. 7b displays the subsequent heating run for PLA and its nanocomposites having different POSS contents. An endothermic peak is recognized near the glass transition temperature (around 60 °C) which is associated with relaxation process. After that a remarkable exothermic peak appears around 113 °C which is associated to cold crystallization process. By considering the peak temperature (TCC) it can be seen that incorporation of low amount of POSS nanoparticles induces a little shift to lower temperatures region from 113 to 110 °C and to 112 °C for POSS-1 and POSS-2.5, respectively. In addition, the onset temperature (T0) decreases in these samples. This trend can be originated from two sources: first, enhancement of nucleation phenomenon as a result of nucleating role of POSS nanoparticles, second, improvement in polymer chain mobility because of lubrication effect of nanoparticle. According to the Fig. 7 it is obvious that the presence of nanoparticles does not considerably alter the crystallization behavior of PLA and just has little influence in low content of nanoparticles. Then by taking into account the previous results, it can be claimed that lubrication effect and ease of segmental motion is the dominant reason for promoting the cold crystallization phenomenon. On the other hand, the weak nucleation activity of this particular grade of POSS (trifluoropropyl-POSS) may emanate from its low surface energy and non-reactive nature as a result of having CF3 units in its structure. Degree of crystallinity is another important parameter for characterization of crystallization properties of polymers. On the basis of the heat of fusion of 100% crystalline PLA (93 J g−1),28 the degree of crystallinity (XC) of neat PLA and its nanocomposites are determined by the ratio of crystallization enthalpy of the samples to that of 100% crystalline PLA. It is clear from Table 1 that its value stays unchanged for POSS-1 and POSS-2.5 but decreases in the presence of higher POSS loadings. The descending trend in degree of crystallinity with further increasing of POSS concentration is due to the increased viscosity and aggregates formation and hence difficulty in transportation of PLA chains to crystal-growing surface. In another work, it has been observed that well dispersed octamethyl-POSS acts as an effective nucleating agent and hence increases the degree of crystallinity of PLA in the non-isothermal crystallization from 8.3 to 42.4% in the presence of 2 wt% of octamethyl-POSS.34 On the other hand, the double melting peaks located at lower (149 °C) and higher (156 °C) temperatures relate to the less organized crystals and well organized crystals of pure PLA, respectively.45 By considering intensity of the two melting peaks, it can be seen that extent of well organized crystals in POSS-1 and POSS-2.5 is higher than PLA which implies again the promoting effect of POSS on cold crystallization at low loadings.
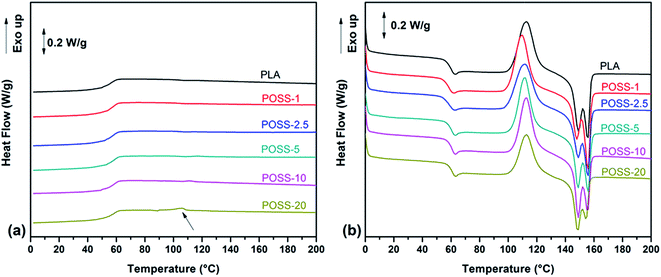 |
| Fig. 7 DSC (a) cooling and (b) heating traces of PLA and its nanocomposites at 10 °C min−1. | |
Table 1 DSC data of PLA and POSS containing composites obtained from second heating in non-isothermal crystallization
Samples |
T0 (°C) |
TCC (°C) |
ΔHC (J g−1) |
Tm1 (°C) |
Tm2 (°C) |
ΔHm (J g−1) |
XC (%) |
PLA |
101 |
113 |
29.4 |
149 |
156 |
29.6 |
31.6 |
POSS-1 |
99 |
110 |
29.3 |
148 |
156 |
30.1 |
31.5 |
POSS-2.5 |
99 |
112 |
29.6 |
149 |
156 |
28.2 |
31.8 |
POSS-5 |
101 |
112 |
26.6 |
149 |
156 |
27.5 |
28.6 |
POSS-10 |
102 |
113 |
26.6 |
149 |
156 |
27.5 |
28.6 |
POSS-20 |
102 |
113 |
21.2 |
149 |
155 |
23.6 |
22.8 |
3.4. Dynamic mechanical analysis
It was illustrated that trifluoropropyl-POSS has a softening effect on the melt-state properties of PLA and reduces the complex viscosity. Its effect on the solid-state properties is also interesting since it can reveal how the materials will behave at room temperature and below.46 To further study about the influence of low and high contents of POSS on solid-state properties, dynamic mechanical analysis was performed on the neat PLA and its nanocomposites. The recorded storage modulus (E′) and loss tangent (tan
δ = E′′/E′) at a frequency of 1 Hz have been plotted as a function of temperature in Fig. 8. It is seen that the magnitude of glassy modulus of POSS-1 is lower than that of its pure polymer (PLA). Also transition into rubbery region occurs at lower temperatures in presence of low content of POSS which is in consistency with its explained plasticizing effect. Incorporation of higher amounts of nanofiller donates more stiffness to the PLA. To state quantitatively, the storage modulus values at room temperature are 2081, 1916 and 2155 MPa for neat PLA, POSS-1 and POSS-20, respectively. As it can be observed in figure, enhancement of modulus for POSS-20 sample is pronounced at temperatures between 50 and 80 °C. This stiffening is caused by phase-separated POSS micro-aggregates that reinforce the sample like a rigid filler and make it stiffer than the pure matrix material.
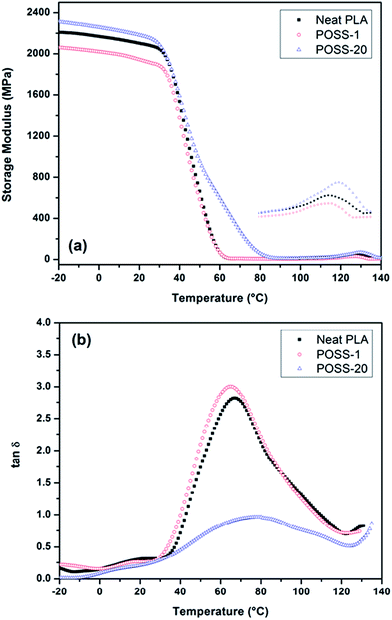 |
| Fig. 8 (a) Storage modulus and (b) tan δ as a function of temperature for PLA and POSS containing composites. | |
Furthermore, an increment in modulus values is detectible at higher temperatures starting from 110 °C. As mentioned in the results of DSC experiment, this behavior attributed to the formation of crystal phase during heating. It is obvious in Fig. 8a that the modulus enhancement of for POSS-1 takes place earlier than that of PLA, indicating again the lubrication effect of POSS. According to the plot of loss tangent (Fig. 8b), the glass transition temperature slightly reduces at low POSS content and thereafter increases by increasing POSS loading. Also, the intensity of tan
δ decreases significantly for POSS-20 due to its aforementioned higher stiffness particularly at glass transition region. As reported in literature, presence of POSS in a polymer can increase or decrease Tg and modulus by the following mechanisms: (i) restriction of polymer chain mobility due to presence of solid POSS cage which leads to an increase in Tg and a local chain reinforcement or (ii), increase in free volume due to voluminous POSS molecule which results in acceleration of the chain dynamics and reduction of Tg as well as modulus. Therefore, POSS can represent reinforcing effect or it may act as a plasticizer.47
3.5. Thermal stability
Influence of POSS nanoparticles on the thermal stability of PLA was evaluated by means of TGA analysis. Fig. 9 shows the TGA and DTG thermograms of neat PLA and its nanocomposites in nitrogen ambient. As introduced in the experimental section, all the samples were heated from room temperature to 650 °C with the rate of 10 °C min−1. It is seen that except for the POSS-20, all the neat PLA and its nanocomposites have similar one step degradation profile. This means that the presence of POSS does not alter the degradation mechanism of PLA matrix. The most important characteristic data obtained from TGA experiment such as temperatures for 5% and 50% weight loss (T0.05 and T0.5) and also the maximum degradation rate temperature (Tmr) have been summarized in Table 2. As it can be observed from Fig. 9 and Table 2 the values of T0.05, T0.5 and Tmr slightly decrease with increasing the POSS content in the nitrogen atmosphere, indicating that the incorporation of POSS nanoparticles reduces slightly the thermal stability of the PLA matrix, especially at high POSS loading. This reduction is due to much lower thermal stability of the POSS nanoparticles than that of PLA and also reflects that there is no chemical bond or strong interaction between POSS and the PLA matrix. As it has been reported, the maximum degradation rate for POSS is occurred at about 320 °C.48 Similar behavior has been also found in the PVDF/POSS nanocomposites where the same type of POSS was incorporated into PVDF matrix. Initial weight loss of neat PVDF took place at 460 °C but this temperature shifted to about 300 °C as a result of POSS degradation.48 It seems that the POSS-20 has two-step degradation pattern. The first weight loss with maximum degradation rate at 322 °C can be assigned to volatilization of entrapped POSS phase in the polymer matrix. Unlike most other POSS compounds, fluorinated POSS volatilize rather than decompose and no residue remains after heating under either nitrogen or dry air.49 After this step, degradation process of POSS-20 becomes similar to other materials. This can be explained in this way that when the suitable temperature for the degradation of the matrix is reached, a negligible amount of POSS is present in the composite. By comparing the previously reported results about the effect of POSS on the thermal stability of PLA, it can be claimed that dependent on the type of POSS it may enhance or reduce thermal stability of PLA. For instance, incorporation of 5 wt% of octamethyl-POSS (T0.05 = 222 °C)34 and octaphenyl-POSS (T0.05 = 522 °C)36 into PLA results in 42 °C reduction and 38.5 °C improvement in thermal stability of PLA, respectively.
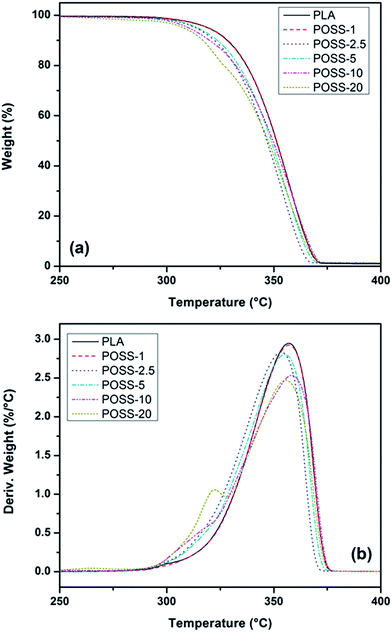 |
| Fig. 9 TGA and DTG thermograms in nitrogen atmosphere of neat PLA and its POSS containing nanocomposites. | |
Table 2 TGA data of PLA and POSS containing composites obtained during heating at 10 °C min−1
Samples |
Nitrogen atmosphere |
T0.05 (°C) |
T0.5 (°C) |
Tmr (°C) |
PLA |
319 |
352 |
357 |
POSS-1 |
319 |
351 |
357 |
POSS-2.5 |
314 |
347 |
353 |
POSS-5 |
314 |
349 |
355 |
POSS-10 |
310 |
350 |
358 |
POSS-20 |
308 |
347 |
322/356 |
4. Conclusions
In the present investigation, an inorganic–organic hybrid nanofiller (trifluoropropyl-POSS) was incorporated into PLA matrix using traditional melt-blending process. Three techniques namely SEM, EDX spectrometer and XRD were employed to explore the microstructure of samples. The results showed that POSS particles have a fine dispersion near to molecular level at low content (up to 2.5 wt%) in polymer matrix while at higher contents large micro-agglomerates (≈10 μm) were observed because of weak interaction between POSS and PLA matrix due to nonreactive nature of trifluoropropyl-POSS surface and also the strong interaction among POSS molecules. To correlate microstructure with properties, the influence of POSS content on rheological behavior, non-isothermal crystallization behavior, thermomechanical properties and on thermal stability of PLA nanocomposites were evaluated using melt rheology, DSC, DMA and TGA techniques. From the rheological analysis it was found that when POSS molecularly dispersed in PLA the complex viscosity and elasticity decrease due to the reduction in entanglement density and more free volume in the melt. This lubrication role was diminished with increased amount of POSS as a result of imposed hindrance effect on mobility of segments which caused by existence of large micro-aggregates. Also, there was no intersection between storage and loss moduli for all compositions, suggesting that the transition from liquid-like to a solid like behavior did not occur even at 20 wt% of POSS loading. The softening effect of POSS at low loadings was also confirmed by DMA analysis when stiffness and glass transition temperature of PLA reduced indicating PLA became more flexible in the presence of POSS. Furthermore, the POSS particles at low loadings had a promoting impact on the cold crystallization of PLA and reduced the cold crystallization temperature due to easier chain transportation to the crystal growth surface. On the other hand, formation of micro-aggregates at high loadings induced a negative effect on cold crystallization which manifested itself in reduced value of crystallinity by about 10%. TGA results revealed that thermal stability of the PLA matrix was slightly reduced by incorporation of POSS nanoparticles especially at high POSS loading. However, POSS did not alter the thermal degradation mechanism of PLA.
References
- C. Sanchez, B. Julian, P. Belleville and M. Popall, J. Mater. Chem., 2005, 15, 3559–3592 RSC.
- M. Joshi and B. S. Butola, J. Macromol. Sci., Part C: Polym. Rev., 2004, 44, 389–410 CrossRef.
- G. Kickelbick, Prog. Polym. Sci., 2003, 28, 83–114 CrossRef CAS.
- G. Li, L. Wang, H. Ni and C. Pittman Jr, J. Inorg. Organomet. Polym., 2001, 11, 123–154 CrossRef CAS.
- H.-x. Zhang, H.-y. Lee, Y.-j. Shin, K.-b. Yoon, S.-K. Noh and D.-h. Lee, Polym. Int., 2008, 57, 1351–1356 CrossRef CAS.
- S. H. Phillips, T. S. Haddad and S. J. Tomczak, Curr. Opin. Solid State Mater. Sci., 2004, 8, 21–29 CrossRef CAS.
- J. Wu and P. T. Mather, Polym. Rev., 2009, 49, 25–63 CrossRef CAS.
- S.-W. Kuo and F.-C. Chang, Prog. Polym. Sci., 2011, 36, 1649–1696 CrossRef CAS.
- G. Li and C. U. Pittman, in Macromolecules Containing Metal and Metal-Like Elements, John Wiley & Sons, Inc., 2005, pp. 79–131, DOI:10.1002/0471712566.ch5.
- E. Ayandele, B. Sarkar and P. Alexandridis, Nanomaterials, 2012, 2, 445 CrossRef CAS.
- Z. Zhou, L. Cui, Y. Zhang, Y. Zhang and N. Yin, Eur. Polym. J., 2008, 44, 3057–3066 CrossRef CAS.
- A.-L. Goffin, E. Duquesne, S. Moins, M. Alexandre and P. Dubois, Eur. Polym. J., 2007, 43, 4103–4113 CrossRef CAS.
- K. M. Lee, P. T. Knight, T. Chung and P. T. Mather, Macromolecules, 2008, 41, 4730–4738 CrossRef CAS.
- M. J. Hato, S. S. Ray and A. S. Luyt, Macromol. Mater. Eng., 2008, 293, 752–762 CrossRef CAS.
- M. Joshi, B. S. Butola, G. Simon and N. Kukaleva, Macromolecules, 2006, 39, 1839–1849 CrossRef CAS.
- A. Fina, D. Tabuani, A. Frache and G. Camino, Polymer, 2005, 46, 7855–7866 CrossRef CAS.
- Z. Zhou, Y. Zhang, Y. Zhang and N. Yin, J. Polym. Sci., Part B: Polym. Phys., 2008, 46, 526–533 CrossRef CAS.
- B. X. Fu, M. Y. Gelfer, B. S. Hsiao, S. Phillips, B. Viers, R. Blanski and P. Ruth, Polymer, 2003, 44, 1499–1506 CrossRef CAS.
- Y. Zhao and D. A. Schiraldi, Polymer, 2005, 46, 11640–11647 CrossRef CAS.
- Y. Feng, Y. Jia, S. Guang and H. Xu, J. Appl. Polym. Sci., 2010, 115, 2212–2220 CrossRef CAS.
- E. T. Kopesky, T. S. Haddad, G. H. McKinley and R. E. Cohen, Polymer, 2005, 46, 4743–4752 CrossRef CAS.
- J. N. Martins, T. S. Bassani and R. V. B. Oliveira, Mater. Sci. Eng. C, 2012, 32, 146–151 CrossRef CAS.
- J. Martins, O. Bianchi, C. Wanke, C. Castel and R. B. Oliveira, J. Polym. Res., 2015, 22, 1–10 CrossRef CAS.
- J.-M. Raquez, Y. Habibi, M. Murariu and P. Dubois, Prog. Polym. Sci., 2013, 38, 1504–1542 CrossRef CAS.
- V. Asadi, S. H. Jafari, H. A. Khonakdar, L. Hauler and U. Wagenknecht, RSC Adv., 2016, 6, 4925–4935 RSC.
- L. T. Lim, R. Auras and M. Rubino, Prog. Polym. Sci., 2008, 33, 820–852 CrossRef CAS.
- D. Garlotta, J. Polym. Environ., 2001, 9, 63–84 CrossRef CAS.
- S. Saeidlou, M. A. Huneault, H. Li and C. B. Park, Prog. Polym. Sci., 2012, 37, 1657–1677 CrossRef CAS.
- M. R. Aghjeh, M. Nazari, H. A. Khonakdar, S. H. Jafari, U. Wagenknecht and G. Heinrich, Mater. Des., 2015, 88, 1277–1289 CrossRef CAS.
- M. R. Aghjeh, V. Asadi, P. Mehdijabbar, H. A. Khonakdar and S. H. Jafari, Composites, Part B, 2016, 86, 273–284 CrossRef CAS.
- H. Pan and Z. Qiu, Macromolecules, 2010, 43, 1499–1506 CrossRef CAS.
- Z. Qiu and H. Pan, Compos. Sci. Technol., 2010, 70, 1089–1094 CrossRef CAS.
- J. Yu and Z. Qiu, Ind. Eng. Chem. Res., 2011, 50, 12579–12586 CrossRef CAS.
- J. Yu and Z. Qiu, ACS Appl. Mater. Interfaces, 2011, 3, 890–897 CAS.
- X. Zhang, J. Sun, S. Fang, X. Han, Y. Li and C. Zhang, J. Appl. Polym. Sci., 2011, 122, 296–303 CrossRef CAS.
- J. Sun, Q. Q. Zhao, Z. Y. Cao, H. N. Lv, C. Q. Wang and Z. S. Cai, Adv. Mater. Res., 2015, 1120–1121, 352–356 CrossRef.
- D. Turan, H. Sirin and G. Ozkoc, J. Appl. Polym. Sci., 2011, 121, 1067–1075 CrossRef CAS.
- H. Sirin, M. Kodal and G. Ozkoc, Polym. Compos., 2014 DOI:10.1002/pc.23319.
- M. Kodal, H. Sirin and G. Ozkoc, Polym. Eng. Sci., 2014, 54, 264–275 CAS.
- Z. Fan-lin, S. Yi, Z. Yu and L. Qing-kun, Modell. Simul. Mater. Sci. Eng., 2011, 19, 025005 CrossRef.
- M. Razavi Aghjeh, H. A. Khonakdar, S. H. Jafari, C. Zschech, U. Gohs and G. Heinrich, RSC Adv., 2016, 6, 24651–24660 RSC.
- S. Singh, A. K. Ghosh, S. N. Maiti, S. Raha, R. K. Gupta and S. Bhattacharya, Polym. Eng. Sci., 2012, 52, 225–232 CAS.
- M. L. Di Lorenzo and C. Silvestre, Prog. Polym. Sci., 1999, 24, 917–950 CrossRef CAS.
- C. Vasile, Handbook of Polyolefins, CRC Press, 2nd edn, 2000 Search PubMed.
- R.-y. Chen, W. Zou, C.-r. Wu, S.-k. Jia, Z. Huang, G.-z. Zhang, Z.-t. Yang and J.-p. Qu, Polym. Test., 2014, 34, 1–9 CrossRef CAS.
- M. R. Aghjeh, H. A. Khonakdar and S. H. Jafari, Composites, Part B, 2015, 79, 74–82 CrossRef CAS.
- L. Matějka, P. Murias and J. Pleštil, Eur. Polym. J., 2012, 48, 260–274 CrossRef.
- Y. Liu, Y. Sun, F. Zeng, Y. Chen, Q. Li, B. Yu and W. Liu, Polym. Eng. Sci., 2013, 53, 1364–1373 CAS.
- J. M. Mabry, A. Vij, S. T. Iacono and B. D. Viers, Angew. Chem., Int. Ed., 2008, 47, 4137–4140 CrossRef CAS PubMed.
|
This journal is © The Royal Society of Chemistry 2016 |
Click here to see how this site uses Cookies. View our privacy policy here.