DOI:
10.1039/C5RA28058C
(Paper)
RSC Adv., 2016,
6, 16314-16318
Millimeter-sized carbon/TiO2 beads fabricated by phase inversion method for oil and dye adsorption†
Received
30th December 2015
, Accepted 21st January 2016
First published on 26th January 2016
Abstract
Millimeter-sized composite polyethersulfone/TiO2 beads were fabricated with different amounts of TiO2 and the surfactant F127 by a modified phase inversion method and the resulting composite carbon beads were obtained after calcination. The composite carbon/TiO2 beads were tested for oil adsorption and rhodamine B (RB) adsorption. For the adsorption of corn oil, the volume gains for composite carbon/TiO2 beads prepared with 2–4 g TiO2 and 0–1 g surfactant F127 were in the range of 46–77%. In the adsorption of linear paraffin oil and silicone oil, composite carbon/TiO2 beads (CB-4 and CB-4-1F) prepared with 4 g TiO2 exhibited volume gains of oil of 74–77%. CB-4 and CB-4-1F also exhibited enhanced adsorption of RB, and only 22% and 16% of RB remained in solution after 24 h of adsorption, respectively. This study provides an easy and low-cost method for preparing millimeter-sized carbon/TiO2 sorbents for oil and dye adsorption.
1. Introduction
Wastewater containing dyes and/or pigments is harmful to the environment and hazardous to human health. Numerous treatment technologies have been developed to treat dye wastewater, from physicochemical to biological processes.1 Among these, adsorption has been found to be superior to others in terms of its simplicity, low cost, acceptable removal efficiency and ease of operation. Activated carbon has been the most widely used adsorbent because of its high capacity for the adsorption of organic species.2 For the clean-up of oil spills, natural sorbents, such as straw, wood fibers and cotton fibers, always display a low oil adsorption capacity and more efforts have been made with synthetic sorbent materials. Among the various sorbent materials, carbon materials have been considered to be the most promising sorbents for oil because they exhibit a high capacity for the uptake of oil and are environmentally acceptable.3–7 However, these carbon materials, including spongy graphene and carbon nanotubes, require complex preparation procedures under strict conditions or surface modification before the sorption process. Such processes restrict the practical application of these carbon-based sorbents.6,7
Millimeter-sized beads are easy to handle and recover. A series of techniques have been developed to prepare such large beads. Water-swellable polymer network (WSPN) beads in the size range of 0.5–2.5 mm were prepared by a sedimentation polymerization method, wherein droplets of an aqueous monomer solution were introduced by a syringe into a heated oil medium for sedimentation.8,9 Emulsion-templated polymer beads with an average size of 2.16 mm were prepared by oil-in-water-in-oil sedimentation polymerization.10,11 Hydrophobic mesoporous silica spheres containing transition metals coordinatively bound to aminosilane groups were synthesized in a one-step procedure from functionalized silicon alkoxides by an injection method.12 Aminosilane functional groups are the active sites for anchoring transition metals such as Co, Cu, Fe, Mn and V. Uniform, hierarchically porous inorganic beads (SiO2, Al2O3, TiO2, and ZrO2) have been produced using various polymer beads as templates.13 The inorganic beads were prepared by simply immersing polymer scaffold beads in a range of inorganic precursor solutions, followed by sol–gel condensation in air and subsequent calcination of the polymer phase. Millimeter-sized gold beads, silica–gold nanoparticle (GNP) beads and alumina–GNP beads were also prepared by a similar method as above.14,15 In our previous study, a phase inversion method was introduced for the preparation of millimeter-sized porous polymer composite beads and hollow carbon composite beads.7,16,17 Zeolitic imidazolate framework-8 (ZIF-8)16 and silica (including tetraethyl orthosilicate)7,17 were added to the polymer precursor solution and composite polymer beads were obtained immediately by injecting the solution into a non-solvent phase (water) through a syringe.
Titanium dioxide (TiO2) has been widely investigated as a prime photocatalyst due to its abundance, low toxicity, relatively high efficiency and excellent photostability. However, even when TiO2 is used as a photocatalyst, the adsorption of pollutants on TiO2 also plays an important role as a prerequisite for their effective photodegradation.18,19 The low adsorption capacity of TiO2 restricts its further applications as an adsorbent due to its intrinsic disadvantages such as a narrow pore size, a small surface area and fewer active sites. One effective method to improve the adsorption performance of TiO2 is to graft functional groups such as carboxylate groups onto a TiO2 surface to change its chemical properties.20,21 TiO2/carbon and TiO2/silica composites have also been prepared and exhibited enhanced photocatalytic properties and dye adsorption performance.22,23 In this study, millimeter-sized polymer/TiO2 beads were prepared by a phase inversion method and the resulting carbon/TiO2 composite beads were obtained after carbonization. The surfactant F127 was also used to modify the porous structure of composite carbon beads and the carbon beads were used as adsorbents to adsorb several oils and rhodamine B (RB).
2. Experimental
2.1 Carbon bead preparation
Carbon beads were prepared by a modified phase inversion method, as reported in our previous study.7,16,17 Typically, 3 g polyethersulfone (PES, E6020P, Mw: ∼51
000, BASF) was dissolved in 17 g N-methyl-2-pyrrolidone (NMP) to form a clear polymer solution under stirring for 4–6 h. Then, 0.4–4.0 g commercial P25 TiO2 (Degussa) and 0–2 g F127 were added to the abovementioned polymer solution to form a uniform solution. Polymer beads were formed immediately by vertically pumping the polymer solution into deionized water with an air gap of 4 cm through a stainless steel syringe (20 G) at a flow rate of 1 mL min−1. After further solvent/non-solvent exchange in water overnight, the resulting polymer beads were washed with deionized water to remove residual NMP and dried at 80 °C overnight. The carbon beads were obtained by carbonizing the polymer beads via a heating program consisting of a heating rate of 1 °C min−1, 200 °C for 2 h, and 650 °C for 5 h under high-purity flowing nitrogen gas. The polymer beads and carbon beads were denoted as PB-x(-yF) and CB-x(-yF), respectively, where x stands for the amount of TiO2 (g) used and y stands for the amount of surfactant F127 (g) used. For example, CB-2 and CB-2-2F are carbon beads prepared with 2 g of TiO2 without surfactant and 2 g of TiO2 with 2 g of surfactant F127, respectively.
2.2 Characterisation
X-ray diffraction (XRD) patterns of the samples were obtained on an Ultima IV diffractometer with Cu Kα radiation at a scan rate of 2° min−1 with a step size of 0.02°. Nitrogen adsorption–desorption isotherms were measured at liquid-nitrogen temperature (77 K) using a volumetric adsorption analyzer (Micromeritics ASAP 2020). Surface areas were determined by the Brunauer–Emmett–Teller (BET) method. Scanning electron microscopy (SEM) images were taken with a Quanta 200 microscope (FEI, USA).
2.3 Volume shrinkage rate and oil and dye adsorption
The volume shrinkage rate of carbon beads was calculated by the equation as follows:
Volume shrinkage rate (%) = (Vp − Vc)/Vp × 100% |
where Vp and Vc are the volumes of polymer beads and carbon beads, respectively. The diameter of polymer and carbon beads was measured by a digital caliper. The average diameter was determined by testing 30 beads and the volume was calculated assuming that the beads were regular spheres.
In a typical oil adsorption capacity test,7 0.05 g of carbon beads were immersed in various oils (corn oil, bean oil, turpentine oil, paraffin oil and silicone oil) for 20 min, wiped with paper and then weighed by a balance. The measurements were carried out very quickly to avoid evaporation of the oil. The volume gain (volume proportion of oil adsorbed on the carbon beads) of the carbon beads was calculated as follows:
where
Ws is the weight of the hollow carbon beads after adsorption of oil,
Wc is the initial weight of the carbon beads before sorption,
ρc is the bulk density of the carbon beads, and
ρo is the density of the oil.
RB was selected for dye adsorption testing. Initially, 0.5 g of composite carbon beads were added to 40 mL of 20 mg L−1 RB solution (pH: ∼7) under gentle stirring at room temperature (20 °C). The absorbance intensity of each solution was measured by a Unico UV-2802S UV-vis spectrophotometer at a defined wavelength. The equilibrium adsorption of RB on the carbon beads was determined by applying the equation as follows:
where
qe is the equilibrium adsorption capacity (mg g
−1),
Co and
Ce are the initial and equilibrium concentrations of the RB solution (mg L
−1), respectively,
V is the volume of the RB solution (mL), and
m is the mass of the carbon beads (mg).
3. Results and discussion
3.1 Preparation of polymer and carbon beads
Polyethersulfone composite beads were prepared via a phase inversion method by injecting a polymer solution through a stainless steel syringe. As reported in our previous study, tetraethyl orthosilicate and silica particles were added to the polymer solution to retain the structure of the carbon spheres after carbonization.7,17 As P25 TiO2 is one of the best photocatalysts and a promising adsorbent, 0.4–4 g of P25 TiO2 was added to a PES solution to form composite polymer beads (Fig. 1), wherein the TiO2 powder would strengthen the structure of the beads after carbonization and also act as a functional agent. Fig. 1a shows polymer composite beads with 0.4 g of TiO2 (PB-0.4). The average bead size is ∼2.4 mm. With an increase in the amount of TiO2 from 0.9 to 1.6 g (PB-0.9, PB-1.2, PB-1.6), the beads have almost the same sizes, in the range of 2.35–2.44 mm. The polymer beads prepared with 2.0 and 4.0 g of TiO2 have sizes of 2.4 and 2.1 mm, respectively, with a tail. The tail attached to the bead should arise from the relatively higher density of the PES/TiO2 composite solution, which led to a high dropping rate from the syringe tip and also obtains a small bead size of 2.1 mm for PB-4.
 |
| Fig. 1 Digital images of polyethersulfone/TiO2 beads: PB-0.4 (a), PB-0.9 (b), PB-1.2 (c), PB-1.6 (d), PB-2 (e), and PB-4 (f). | |
All the composite polymer beads were carbonized and their digital images are shown in Fig. 2. For the samples prepared with 0.4 and 0.9 g TiO2, the resulting CB-0.4 and CB-0.9 could not retain a spherical structure as the macroporous structure produced during the phase inversion process was destroyed after carbonization. For the composite polymer beads prepared with more than 0.9 g of TiO2, the resulting carbon beads have the same spherical structure as their precursors, only with some shrinkage. The bead sizes are 1.47, 1.48, 1.61 and 1.88 mm for CB-1.2, CB-1.6, CB-2 and CB-4, respectively. CB-1.2 and CB-1.6 display similar volume shrinkage rates of ∼77%. The volume shrinkage rates of CB-2 and CB-4 become smaller and are ∼70% and 28%, respectively.
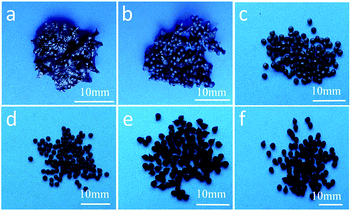 |
| Fig. 2 Digital images of carbon/TiO2 composite beads: CB-0.4 (a), CB-0.9 (b), CB-1.2 (c), CB-1.6 (d), CB-2 (e), and CB-4 (f). | |
The surfactant F127 could increase the surface pore size of polymer beads.16,22 F127 was added to the PES/TiO2 solution to modify the porous structure of the resulting polymer and carbon beads. Fig. 3a shows polymer composite beads with the addition of 2 g TiO2 and 1 g F127 (PB-2-1F). The polymer beads exhibit good spherical geometry without a tail. The bead size is about 2.23 mm in diameter. After carbonization, the resulting carbon beads CB-2-1F also display excellent spherical geometry with a bead size of about 1.51 mm in diameter. The volume shrinkage rate is 69%, which is almost the same as that of CB-2 prepared without F127. With an increase in the amount of F127 used to 2 g, the polymer beads PB-2-2F have a bead size of 2.26 mm, and the bead size of the corresponding CB-2-2F is about 1.61 mm with a volume shrinkage of 64% (Fig. 3b and e). A small volume shrinkage will obtain high porosity of the final carbon beads. For the samples prepared with 4 g of TiO2 and 1 g of F127, the volume shrinkage rate is about 50% with bead sizes of PB-4-1F and CB-4-1F of 2.0 and 1.59 mm, respectively (Fig. 3c and f). As compared with CB-4 prepared without F127, CB-4-1F exhibits an increase in volume shrinkage, which indicates that the surfactant F127 really helped to disperse TiO2 nanoparticles in the polymer beads.
 |
| Fig. 3 Digital images of polymer/TiO2 composite beads prepared with F127: PB-2-1F (a), PB-2-2F (b), and PB-4-1F (c), and the corresponding carbon/TiO2 beads: CB-2-1F (d), CB-2-2F (e), and CB-4-1F (f). | |
The composite carbon beads were analyzed by nitrogen adsorption–desorption (Fig. 4a). The BET surface area of CB-2 is 31 m2 g−1. With an increase in the amount of TiO2, CB-4 has an increased BET surface area of 173 m2 g−1. The BET surface areas of carbon beads prepared with an amount of TiO2 less than 1.6 g were not detectable, which is probably due to the bead surfaces being too dense and the fact that some organic residues could not be totally removed during carbonization. With the introduction of the surfactant F127, CB-2-2F displays an increased BET surface area of 227 m2 g−1. However, for CB-4-1F, the BET surface area (134 m2 g−1) exhibits a slight decrease, which is associated with the high volume shrinkage (50% compared with 28% for CB-4) of the sample. Fig. 4b shows the XRD patterns of CB-2, CB-2-2F, CB-4 and CB-4-1F. All the samples display almost the same phase structure, which is very similar to that of pure P25 TiO2 with an anatase/rutile molar ratio of 80/20.24
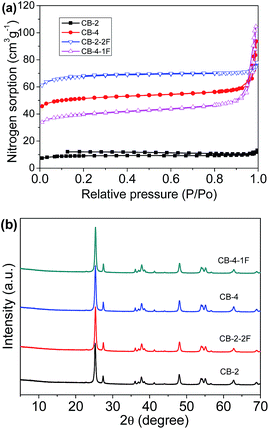 |
| Fig. 4 Nitrogen adsorption–desorption isotherms (a) and XRD patterns (b) of CB-2, CB-4, CB-2-2F and CB-4-1F. | |
SEM images of CB-2-2F, CB-4 and CB-4-1F are displayed in Fig. S1 (ESI†). Macroporous structures are found both on the bead surfaces and inside the beads. The carbon beads are confirmed to be an ideal substrate for the immobilization of nano-sized TiO2.25–27
3.2 Oil and dye adsorption
The composite carbon/TiO2 beads were investigated for adsorbing five oils: corn oil, bean oil, turpentine oil, paraffin oil and silicone oil. For corn oil, the volume gain on oil adsorption increased with an increase in the loading of TiO2 from 25% for CB-1.2 to 77% for CB-4.0. Although the BET surface areas of CB-1.2 and CB-1.6 were not detectable, they could still adsorb oil with volume gains of 25–32%. CB-4.0 has the lowest bulk density of 0.575 g cm−3 and a relatively high BET surface area. Both of these are beneficial for a high volume gain on corn oil adsorption. For the CB-2-2F sample, its volume gain with corn oil (70%) was very similar to that of CB-4 (77%) and higher than that of CB-2 (46%), which is mainly because of the high porosity of CB-2-2F and its low bulk density (0.595 g cm−3 for CB-2-2F and 0.687 g cm−3 for CB-2). For the CB-4-1F sample, the volume gain with corn oil was 63%, which is a little smaller than that of CB-4 and should arise from the low porosity of CB-4-1F. For the adsorption of the other four oils, the volume gains with bean oil, turpentine oil, paraffin oil and silicone oil show similar trends as that with corn oil. Turpentine oil is composed of terpenes, mainly α-pinene and β-pinene, and gave rise to the lowest volume gain compared with the other four oils. In the adsorption of linear paraffin oil and silicone oil, the composite carbon beads CB-4 and CB-4-1F exhibited similar oil volume gains of 74–77%, which are higher than that of the hollow carbon beads reported in our previous study (<60%).7 The composite carbon beads CB-2-2F, CB-4 and CB-4-1F exhibit competitive uptake capacities compared with spongy graphene (73%)4 and carbon nanotube sponge (61%)6 in the adsorption of long-chain oils. The abovementioned results also indicate that the porosity of carbon beads (owing to the use of F127) has no obvious effects on the adsorption of linear paraffin oil (Fig. 5).
 |
| Fig. 5 Oil adsorption capacities of carbon/TiO2 composite beads for a range of oils in terms of volume gain. | |
The composite carbon beads CB-4 were investigated for adsorbing paraffin oil floating on the surface of water. As shown in Fig. 6, when some composite CB-4 beads were added to a paraffin oil droplet labeled with oil red O, they floated on the surface of the water and quickly adsorbed all the oil in about 5 s. Furthermore, the composite carbon/TiO2 beads can be refreshed after oil adsorption and then reused. Paraffin oil was used in a recycling test and the composite beads (CB-2-2F) were refreshed by washing with n-hexane. The uptake capacities of CB-2-2F over five cycles remained constant.
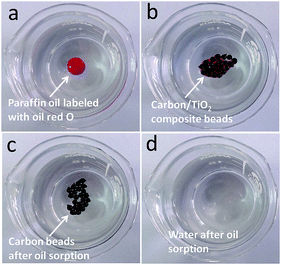 |
| Fig. 6 The adsorption process of paraffin oil using the carbon/TiO2 composite CB-4. The oil is labeled by oil red O and the whole process took about 5 s. | |
In the dye adsorption test, four different carbon/TiO2 beads were used as adsorbents to adsorb RB. Fig. 7 shows the adsorption capabilities for RB using CB-2, CB-2-2F, CB-4 and CB-4-1F. CB-2 has the lowest adsorption performance. At 1 h, the RB concentration was about 98% and remained constant with an increase in the adsorption time from 2 to 24 h. For CB-2-2F, the RB concentration was about 94% at 1 h and slowly decreased to 54% at 24 h. For the adsorbents CB-4 and CB-4-1F, the RB concentrations were 75% for both CB-4 and CB-4-1F at 1 h. With an increase in the adsorption time, the RB concentrations kept on decreasing and reached 22% for CB-4 and 16% for CB-4-1F at 24 h. The composite carbon/TiO2 beads prepared with the surfactant F127 and more loading of TiO2 (which forms hydrogen bonds with RB28) have better adsorption performance for RB. The equilibrium adsorptions of RB on CB-4 and CB-4-1F were 1.25 and 1.34 mg g−1, respectively. The adsorption isotherm of RB on CB-4-1F was studied (details in the ESI†). The adsorption fits the Langmuir model well and the maximum adsorption capacity for RB on CB-4-1F was about 2.79 mg g−1. CB-4-1F has a low adsorption capacity for RB compared with most adsorbents reported in the literature such as 381.7 mg g−1 for mesoporous SiO2 nanosheets.29 However, the synthesis method for millimeter-sized composite carbon beads is simple and easy to scale up for practical applications.
 |
| Fig. 7 Rhodamine B adsorption using four different carbon/TiO2 composite beads as a function of time. | |
4. Conclusions
Millimeter-sized composite polyethersulfone/TiO2 beads were prepared through a stainless steel syringe by a phase inversion method and composite carbon/TiO2 beads were then obtained after carbonization. CB-2 and CB-4 have BET surface areas of 31 and 173 m2 g−1, respectively. The surfactant F127 was used to modify the textural structure of composite carbon/TiO2 beads. CB-2-2F prepared with 2 g TiO2 and 2 g F127 has a much higher BET surface area of 227 m2 g−1. The composite carbon/TiO2 beads were tested for oil adsorption and CB-4, CB-2-2F and CB-4-1F exhibited better performance for oil adsorption than other composite beads. For the adsorption of corn oil, the volume gains were 46%, 77%, 70% and 63% for CB-2, CB-4, CB-2-2F and CB-4-1F, respectively. In the adsorption of linear paraffin oil and silicone oil, the composite carbon/TiO2 beads CB-4 and CB-4-1F exhibited similar oil volume gains of 74–77%. CB-4 and CB-4-1F exhibited enhanced adsorption of rhodamine B compared with CB-2 and CB-2-2F and only 22% and 16% of RB remained in solution after 24 h adsorption time using CB-4 and CB-4-1F as adsorbents, respectively. This study provides an easy and low-cost method to prepare millimeter-sized carbon/TiO2 beads and has the potential to prepare other carbon composites for oil and dye adsorption.
Acknowledgements
The authors are grateful for the financial support of Jiangsu Specially-Appointed Professor Program and Natural Science Key Project of the Jiangsu Higher Education Institutions (15KJA220001).
References
- X. Y. Zhang, J. F. Yao, D. Li, X. D. Chen, H. T. Wang, L. Y. Yeo and J. R. Friend, Mater. Res. Bull., 2014, 55, 13–18 CrossRef CAS.
- A. Gurses, S. Karaca, C. Dogar, R. Bayrak, M. Acikyildiz and M. Yalcin, J. Colloid Interface Sci., 2004, 269, 310–314 CrossRef CAS PubMed.
- H. W. Liang, Q. F. Guan, L. F. Chen, Z. Zhu, W. J. Zhang and S. H. Yu, Angew. Chem., Int. Ed., 2012, 51, 5101–5105 CrossRef CAS PubMed.
- H. Bi, X. Xie, K. Yin, Y. Zhou, S. Wan, L. He, F. Xu, F. Banhart, L. Sun and R. S. Ruoff, Adv. Funct. Mater., 2012, 22, 4421–4425 CrossRef CAS.
- M. Toyoda and M. Inagaki, Carbon, 2000, 38, 199–210 CrossRef CAS.
- X. C. Gui, J. Q. Wei, K. L. Wang, A. Y. Cao, H. W. Zhu, Y. Jia, Q. K. Shu and D. H. Wu, Adv. Mater., 2010, 22, 617–621 CrossRef CAS PubMed.
- Y. Zeng, K. Wang, J. F. Yao and H. T. Wang, Carbon, 2014, 69, 25–31 CrossRef CAS.
- E. Ruckenstein and L. Hong, Chem. Mater., 1996, 8, 546–553 CrossRef CAS.
- E. Ruckenstein and L. Hong, Polymer, 1995, 36, 2857–2860 CrossRef CAS.
- H. Zhang and A. I. Cooper, Chem. Mater., 2002, 14, 4017–4020 CrossRef CAS.
- H. F. Zhang and A. I. Cooper, Soft Matter, 2005, 1, 107–113 RSC.
- T. Foerster, S. Scholz, Y. Zhu and J. A. Lercher, Microporous Mesoporous Mater., 2011, 142, 464–472 CrossRef CAS.
- H. Zhang, G. C. Hardy, Y. Z. Khimyak, M. J. Rosseinsky and A. I. Cooper, Chem. Mater., 2004, 16, 4245–4256 CrossRef CAS.
- H. F. Zhang, I. Hussain, M. Brust and A. I. Cooper, Adv. Mater., 2004, 16, 27–30 CrossRef CAS.
- H. F. Zhang, I. Hussain, M. Brust and A. I. Cooper, Chem. Commun., 2006, 2539–2541, 10.1039/b604392e.
- L. X. Li, J. F. Yao, P. Xiao, J. Shang, Y. Feng, P. A. Webley and H. T. Wang, Colloid Polym. Sci., 2013, 291, 2711–2717 CAS.
- Y. Zeng, K. Wang, J. F. Yao and H. T. Wang, Chem. Eng. Sci., 2014, 116, 704–709 CrossRef CAS.
- L. Xiong, W. Sun, Y. Yang, C. Chen and J. Ni, J. Colloid Interface Sci., 2011, 356, 211–216 CrossRef CAS PubMed.
- M. T. Nguyen-Le and B. K. Lee, Chem. Eng. J., 2015, 281, 20–33 CrossRef CAS.
- Y. Liu, C. Y. Liu and Z. Y. Zhang, Chem. Eng. J., 2008, 138, 596–601 CrossRef CAS.
- J. Feng, J. Zhu, W. Lv, J. Li and W. Yan, Chem. Eng. J., 2015, 269, 316–322 CrossRef CAS.
- N. P. Wickramaratne and M. Jaroniec, J. Colloid Interface Sci., 2015, 449, 297–303 CrossRef CAS PubMed.
- P. V. Messina and P. C. Schulz, J. Colloid Interface Sci., 2006, 299, 305–320 CrossRef CAS PubMed.
- H. Q. Lu, B. B. Zhao, D. Zhang, Y. L. Lv, B. P. Shi, X. C. Shi, J. Wen, J. F. Yao and Z. P. Zhu, J. Photochem. Photobiol., A, 2013, 272, 1–5 CrossRef CAS.
- A. Y. Khan and D. W. Mazyck, Carbon, 2006, 44, 182–184 CrossRef CAS.
- M. E. Rincon, M. E. Trujillo-Camacho, A. K. Cuentas-Gallegos and N. Casillas, Appl. Catal., B, 2006, 69, 65–74 CrossRef CAS.
- G. Xue, H. Liu, Q. Chen, C. Hills, M. Tyrer and F. Innocent, J. Hazard. Mater., 2011, 186, 765–772 CrossRef CAS PubMed.
- T. Maneerung, J. Liew, Y. Dai, S. Kawi, C. Chong and C.-H. Wang, Bioresour. Technol., 2016, 200, 350–359 CrossRef CAS PubMed.
- J. Y. Shen, Y. N. Wu, B. R. Zhang and F. T. Li, Clean Technol. Environ., 2015, 17, 2289–2298 CrossRef CAS.
Footnote |
† Electronic supplementary information (ESI) available: SEM images and adsorption isotherm of RB on CB-4-1F. See DOI: 10.1039/c5ra28058c |
|
This journal is © The Royal Society of Chemistry 2016 |
Click here to see how this site uses Cookies. View our privacy policy here.