DOI:
10.1039/C5RA27956A
(Communication)
RSC Adv., 2016,
6, 16851-16858
Controlled synthesis of highly dispersed and nano-sized Ru catalysts supported on carbonaceous materials via supercritical fluid deposition
Received
29th December 2015
, Accepted 11th January 2016
First published on 20th January 2016
Abstract
Highly dispersed Ru nanoparticles (NPs) supported on carbonaceous materials were fabricated by supercritical fluid deposition technology and characterized by various methods including high-resolution transmission electron microscopy (HRTEM), and X-ray photoelectron spectroscopy (XPS). The mean particle size was controlled in the range from 0.42 to 3.66 nm by changing the carbonaceous support or the pretreatment method of the supports. Ru NPs supported on carbon nanotubes (CNTs) presented smaller particle size, higher dispersion and catalytic activity than those on activated carbon (AC). The interactions between Ru precursors and different carbonaceous supports were characterized by hydrogen temperature programmed reduction (TPR). The ultrasonication-assisted nitric acid oxidation pretreatment method for CNTs is favorable for the dispersion of Ru NPs. The appropriate ultrasound time and the dosage of nitric acid are the prerequisites of its good performance. The optimized pretreatment conditions are ultrasound time 20 min and nitric acid dosage 1/14 (the mass ratio of CNTs to HNO3).
1. Introduction
Transition metal nanoparticles (NPs) employed as catalysts show high activities and selectivities in various reactions owing to their unique chemical and physical properties.1–3 Among all precious metals, ruthenium (Ru), which is essential to the chemical industry, has been widely used as a catalyst in various reactions including ammonia synthesis,4,5 water–gas shift reaction,6 Fischer–Tropsch synthesis,7 hydrogenolysis and hydrogenation of aldehydes and ketones. It is important to note that Ru NPs always present excellent catalytic performance for their high density of active sites. Unfortunately, the metal NPs are unstable and tend to aggregate together resulting in an increase of particle size, which is the main reason for losing their catalytic activity. It has been reported that the presence of supports can prevent the metal NPs from mobilizing and aggregating.8
It is well-known that the properties of carbon-supported metal NPs may be dramatically influenced by the pore structure and the electronic properties of carbon supports.9 In the past decade, carbon nanotubes (CNTs) have stimulated extensive interest for their wide application potential in various fields, particularly the application as supports of metal catalysts for their small size, large surface area and high chemical stability.10 In recent years, CNTs-supported metal catalysts were prepared successfully and exhibited excellent catalytic properties in various reactions. Furthermore, it is reported that electron transfer may occur between metal NPs and carbon supports, which would be followed by the promotion of catalytic activities of carbon-supported metal catalysts.11
A range of techniques, including impregnation,12,13 ion exchange,14 co-precipitation,15 chemical vapor deposition,16 have been employed in the preparation of supported metal NPs. And the average size of supported metal NPs obtained by these traditional preparation methods ranges from 2 to 10 nm, whereas the metal NPs smaller than 2 nm are hardly obtained by preparation methods mentioned above.17 Moreover, it is difficult to tailor the dispersion and the particle size of metal NPs by these traditional preparation pathways which are not in accordance with the development of green chemistry for using some poisonous and organic agents in the preparation of catalysts. Thus the development of green methods to control the particle size and the dispersion of metal NPs and obtain highly dispersed metal NPs on supports is still an important issue and a serious challenge.
In recent years, well-dispersed metal NPs supported various porous materials like CNTs,10,16,18–20 activated carbon,21 alumina (Al2O3)12,22,23 and other matrixes23,24 have been extensively prepared via a relatively novel preparation method, supercritical fluid deposition (SFD) method, which was first demonstrated by Watkins et al.25 in 1995. Supercritical fluids (SCFs) exhibit a distinctive hybrid of gas-like and liquid-like properties. Like gas, they exhibit high diffusivity, low viscosity and near zero surface tension, which can facilitate the delivery of solution to mesopores and micropores of porous materials and enable SFD technique to obtain high uniformity and well-dispersed metal NPs supported on supports; like liquid, they possess high solvation power for organic and inorganic solutes. Among all SCFs, supercritical carbon dioxide (SCCO2) is the most promising owing to their abundance, non-flammability, low cost, non-toxicity and particularly its relatively moderate critical pressure and temperature values (Tc = 31.1 °C, Pc = 7.38 MPa). In addition, SCCO2 is an environmentally benign and recycling solvent, which is good for minimizing the liquid waste problem.
For the preparation of supported metal NPs, SFD process involves the dissolution of metal precursors in SCCO2, the adsorption of metal precursor on porous substrates and reduction of metal precursors to metal form by adding a reducing agent usually hydrogen into SFD system, or by subjecting the metal precursors/substrate composite to hydrogen after depressurizing the supercritical solution, or by heat reduction under inert environment.26,27 Although various metal NPs supported on porous materials have been prepared via SFD method, it is rarely reported that the systematic investigation of the influencing factors in deposition process including dissolution and adsorption process of metal precursors on the dispersion and the particle size of metal NPs for the purpose of controlled synthesis of supported metal NPs.
In this work, highly dispersed Ru NPs supported on CNTs were controllably synthesized via SFD technique. The adsorption process of organometallic Ru precursors on carbon supports is a pivotal step, which determines the dispersion and the particle size of Ru NPs. Consequently, the effect of different carbon supports and different pretreatment methods of carbon supports on the dispersion and the particle size were systematically studied.
2. Experimental
2.1 Materials
Triruthenium dodecacarbonyl (Ru3(CO)12, 99%) was obtained from J&K Scientific Ltd. Activated Carbon (AC) was provided by Tangshan New Activated Carbon Co., China. And Multi-walled carbon nanotubes (purity, >95%; diameter, 40–60 nm; length, 5–15 μm; special surface area, 40–300 m2 g−1) synthesized by catalytic decomposition of CH4 (ref. 28) were supplied by Shenzhen Nanoport Co. Ltd. AC and CNTs were employed as the templates on which Ru NPs were attached. Prior to use, the CNTs and AC was vacuum dried at 100 °C and 10 mbar for 8 h to remove any adsorbents on the surface. Nitric acid (68%), ethanol (99.9%), ethyl acetate (99.9%) and butanone (99.9%) were purchased from Tianjin Jiangtian Chemical Technology Co. Acetaldehyde aqueous solution (40%) was supplied by Tianjin Standard Co. and CO2 (>99.9%) and H2 (99.999%) were provided by Tianjin Liufang Gas Co. With the exception of the AC and CNTs, all the gases, reagents and materials were used as received without further treatment.
2.2 Fabrication and characterization of the supported Ru NPs
2.2.1 The preparation of the ruthenium catalyst precursors. The metal Ru precursors were introduced onto the pore surfaces of supports via SFD method in a variable volume autoclave (PEA-30, Thar). Before participating in the SFD process, some CNTs needs to be pretreated using a certain amount of nitric acid (68%, wt%) with or without the aid of ultrasound in an ultrasonic equipment (model C3860, TEDA chromatographic analysis instrument co., Ltd). In a typical CNTs pretreatment experiment, the CNTs and nitric acid under the desired mass ratio were firstly mixed thoroughly. Then the same amount mixture was placed into two 200 ml breakers respectively. Then one breaker was placed into the ultrasonic equipment mentioned above and the other one was just placed onto a table and exposed to the air. After twenty minutes the CNTs were washed and filtrated with de-ionized water until washing solution keeping neutral. Finally, the CNTs were dried under vacuum for 4 h and then collected in a desiccator for the further use. In a typical preparation experiment of the Ru catalyst precursors, the desired amount of Ru precursor with Ru initial loading 1%, namely the mass ratio of Ru atoms from the Ru precursors to the carbon support 1%, was dissolved in desired amount of ethanol and then the solution was mixed with 5 g carbon support. Subsequently, the mixture was placed in an autoclave (PEA-30, Thar), into which CO2 was added. The desired pressure (17 MPa) and desired temperature (45 °C) was achieved by adjusting the volume of the autoclave and the orientated temperature of water heater. The temperature and pressure were kept for 4 h and then the product was removed from the autoclave and dried under vacuum for 4 h. This product was the catalyst precursor.
2.2.2 Reduction of the ruthenium catalyst precursors. The Ru catalyst precursors were reduced in H2–N2 (V%, 10–90%) for 3 h in a fixed bed reactor at 350 °C. The resulting products were stored in a desiccator.
2.2.3 Characterization of the catalysts. The morphology and microstructure of the obtained Ru/C catalysts or catalyst precursors were examined by means of high-resolution transmission electron microscopy (HRTEM, FEI, Tecnai G2F20). The average size and size distribution of the Ru NPs were determined from the HRTEM images with statistical analysis, where the total number of Ru NPs used to analyze was 500. The XPS measurements were performed on a Pekinelmer Phi ESCA 5500 system equipped with a monochromated 450 W Al Kα source. And the XPS data analysis was carried out with the XPS-Peak 4.1 program and a Shirley function was employed to subtract the background. The temperature programmed reduction (TPR) was also carried out with the AutoChemII2920 chemisorption analyzer. Thermogravimetric profiles of CNTs pretreated with different methods were measured with a TGA/DSTA851 (METTLER).
2.3 Catalytic activity measurements
The catalytic activity for hydrogenation was determined in a stirred autoclave (Parr, 4575). The feed stock simulated a reaction mixture of industrial synthesize of ethyl acetate using ethanol. It includes acetaldehyde (0.36%, mol%), butanone (0.23%, mol%), H2O (1.67%, mol%), ethanol (74.09%, mol%), and ethyl acetate (23.65%, mol%). The reaction condition of the hydrogenation of butanone is pressure 4 MPa, temperature 120 °C and the mass ratio of catalyst to the feed stock is 1
:
100. When the reaction time reached to 3 h, the reaction mixture was sampled and analyzed by GC-MS (Agilent 5973-6890).
3. Results and discussions
3.1 The influence of different carbon supports on the size, reducibility and catalytic activity of Ru NPs
In this work, two common carbon supports, activated carbon (AC) and carbon nanotubes (CNTs), were used to support Ru NPs. The morphology and the metal particle size of Ru/AC and Ru/CNTs catalysts were displayed in Fig. 1. It indicates that the mean size (2.14 nm) of Ru NPs supported on AC is larger than that (0.42 nm) of Ru NPs on CNTs. Furthermore, it is worth to note that the Ru NPs with average size 0.42 nm have not been reported in earlier papers to the best of our knowledge.
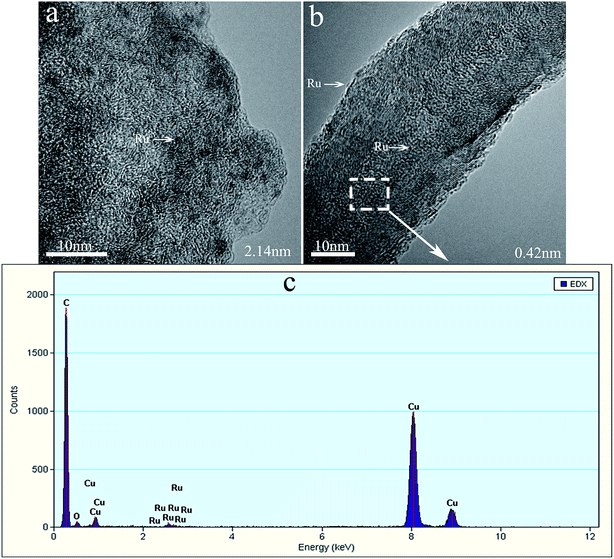 |
| Fig. 1 TEM-EDX images of catalysts prepared using different carbon supports ((a)-sample 1, Ru/AC; (b)-sample 2, Ru/CNTs; (c)-the EDX pattern of sample 2 ) (deposition conditions: 17 MPa, 45 °C, ethanol 2 ml, not pretreated carbon supports). | |
The lattice image and the electron diffraction pattern of Ru NPs supported on CNTs are shown in Fig. 2, which provides further insight into the morphologies and microstructure of Ru/CNTs composites. The lattice image presents the crystalline structure of Ru NPs.29 The aligned lattice fringes of the Ru nanoparticles are clearly illustrated in the image with adjacent fringe spacing of approximately 0.214 nm. This value is consistent with the separation between (002) plates in Ru crystal.30 The electron diffraction pattern of corresponding selected area in the inset of Fig. 5 reveals clear diffraction spots, implying the appearance of metal Ru crystal.31
 |
| Fig. 2 The lattice image and the electron diffraction pattern of Ru NPs in sample 2. | |
The complete reduction of Ru precursors was further confirmed by XPS analysis, despite the assignment of Ru binding energy is not univocal in previous reports. Since the C 1s peak covers the Ru 3d3/2 signal and partially overlaps the Ru 3d5/2 peak, the Ru 3p was chosen for the analysis. The Ru 3p spectra are composed of two components Ru 3p3/2 and Ru 3p1/2. Ru in metallic state is characterized by Ru 3p3/2 peak at about 462.3 eV and Ru 3p1/2 peak at about 484.5 eV whereas the Ru(IV) is characterized by two peaks at about 463.7 eV and 486.2 eV respectively.32 Hence, the Ru 3p3/2 region was selected for the analysis. The sample shown in Fig. 5b contained only ruthenium in the metallic state characterized by Ru 3p3/2 at 462.7 eV, as evidenced in Fig. 3.
 |
| Fig. 3 XPS spectrum (Ru 3p1/2 and Ru 3p3/2) of sample 2. | |
The reducibility of the corresponding samples including naked supports and catalyst precursors were systematically investigated and shown in Fig. 4 to understand the interactions between Ru precursors and carbon supports and the formation mechanism of Ru NPs better. In addition, according to the morphology of catalytic precursors shown in Fig. 5, nearly all of the Ru3(CO)12 was attached on the carbon supports. Consequently, the TPR profiles would not be influenced by the Ru precursors which are free from the carbon supports. Compared with CNTs, the reduction curve of AC has a characteristic peak for the hydrogen consumption by oxygen containing groups on the surface of the AC at 649.4 °C, which is in agreement with the previously reported results from our group.33 Ru3(CO)12/AC have lower reduction peak temperature and larger peak area than Ru3(CO)12/CNTs, which could be due to the weak interaction between Ru3(CO)12 and the oxygen containing groups on the surface of AC and the overlap between the hydrogenation consumption peak of Ru3(CO)12 and that of oxygen containing groups, respectively. It is well known that there are only two places in carbon supports, at which the metals or metal precursors were attached, one is the oxygen containing group on the pore surface and the other is the defect in the carbon structure. In the case of CNTs, the Ru3(CO)12 were attached on the CNTs, mainly, by the interaction between Ru3(CO)12 and the defects in the crystal structure of CNTs for the absence of oxygen containing groups on the surface of CNTs demonstrated by the TPR curve of naked CNTs. However, AC possesses both defects and oxygen containing groups, which have different interaction with AC and distinct stability. As a consequence, Ru3(CO)12 can interact with not only the defects but also the oxygen containing groups. According to the TPR curves of Ru3(CO)12/AC and Ru3(CO)12/CNTs, the reduction peak temperature of Ru3(CO)12/AC is lower than that of Ru3(CO)12/CNTs. It indicates that the interaction between Ru3(CO)12 and the oxygen containing groups in AC is weaker than that between Ru3(CO)12 and defects in CNTs. Consequently, for Ru3(CO)12/AC, the reduction of oxygen containing groups can result in the separation of Ru3(CO)12 from AC and then adsorption and distribution again on the surface of AC, which may enhance the probability of collision among Ru3(CO)12 molecules and finally result in the formation of bigger Ru NPs. Furthermore, the catalytic performance of Ru/AC and Ru/CNTs were also investigated and shown in Fig. 6. It reveals that the catalytic activity of Ru NPs with average particle size 2.14 nm supported on AC is much lower than the ones with average particle size 0.42 nm supported on CNTs.
 |
| Fig. 4 TPR profiles of catalyst precursor prepared using different carbon supports (deposition conditions: 17 MPa, 45 °C, ethanol 2 ml, not pretreated carbon supports). | |
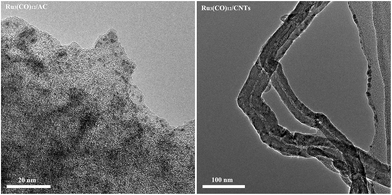 |
| Fig. 5 The morphology of different catalytic precursors (deposition conditions: 17 MPa, 45 °C, ethanol 2 ml, not pretreated carbon supports). | |
 |
| Fig. 6 The catalyst activity of Ru NPs supported on different carbon supports. | |
3.2 The effect of pretreatment method of CNTs on size and dispersion of Ru NPs
CNTs with many exceptional properties are the most promising supports for many metal nano-catalysts. However, the application attempts in the field of catalyst have been greatly limited by the poor dispersion and the inert surfaces of CNTs. It is well known that CNTs tend to aggregate together to form large bundles or big ropes, which significantly hinders the uniform distribution of metal NPs on the exterior surfaces and the inner cavities of CNTs. Although some researchers have tried to promote the dispersion of CNTs with the aid of ultrasound, the CNTs aggregate together again when the ultrasound are suspended. Many attempts in the chemical functionalization including the oxidation treatment with nitric acid for the inert surfaces of CNTs have already been reported in literature.34,35 However, a part of outer surfaces and inner cavities of CNTs could not be oxidized for their agglomerate state.
In this study, ultrasonication-assisted oxidation pretreatment with nitric acid (68%, wt%) was used to pretreat the CNTs before the SFD process was carried out. Moreover, the effect of the ultrasound time and the dosage of nitric acid on the morphology and particle size of Ru/CNTs composites were systematically investigated. The morphology of Ru/CNTs composites obtained by varying the ultrasound time from 0 h to 1 h was observed by TEM and shown in Fig. 7. From Fig. 7a and b, the particle size (2.07 nm) of Ru NPs supported on CNTs oxidized by nitric acid is larger than that (1.23 nm) of Ru NPs on CNTs oxidized by the same amount of nitric acid with the aid of ultrasound. It indicates that the synergistic effect between nitric acid and ultrasound can make it better to oxidize uniformly the outer surface and inner cavities of CNTs and further to obtain the uniformity in Ru particle size. It is well known ultrasound waves consist of compression and rarefaction cycles, in which the cavitation takes place.36 The extreme physical environment from the cavitation effect can significantly cause the increase in the lattice imperfection in the lattice structure of CNTs, which can result in the increase of the metal loading defined as the mass ratio of metals to the supports. Furthermore, the interaction between metal precursors and lattice defects of CNTs is so strong that the metal NPs are difficult to aggregate together during both the catalyst preparation and the catalytic reactions, which is beneficial to enhance the dispersion of metal NPs and the stability of catalysts. Comparing Fig. 7b with 7c, we can find three differences: the first one is regarding the difference in particle size which varies from 1.23 to 3.66 nm with the increase of ultrasound time from 20 min to 1 h; the aggregation phenomenon of CNTs pretreated by ultrasonication-assisted oxidation for 1 h is more serious than that of CNTs pretreated by ultrasonication-assisted oxidation for 20 min; compared with the Ru NPs shown in Fig. 7b, almost all of Ru NPs are free from the CNTs pretreated by ultrasonication-assisted oxidation for 1 h. It indicates that appropriate ultrasound time is a necessary requisite to the good performance of the ultrasonication-assisted oxidation. Too long ultrasound time is unfavorable to the dispersion of metal NPs and CNTs. The reason may be that the mechanical energy inputted into the pretreatment system continuously increases with further increasing ultrasound time, which makes the CNTs wind each other and aggregate together again. Furthermore, some unstable oxygen containing groups, such as hydroxy, carbonyl and carboxyl groups could be firstly introduced into the surfaces of CNTs and then fall off from the surfaces of CNTs during the process of the nitric acid oxidation37 for too long ultrasound time, which could be proved by the difference in weight loss ratio of sample 2# and 3# listed in Table 1. Finally, as shown in Fig. 7c, the Ru NPs are free from CNTs rather than adsorb on the surface of CNTs for the absence of functional groups acted as the specific sites for metal particle nucleation.32
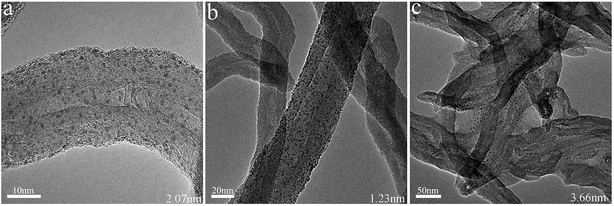 |
| Fig. 7 Effect of ultrasound time on morphology of Ru/CNTs catalyst ((a)-0 h; (b)-1/3 h; (c)-1 h; ultrasonic power-120 w) (deposition conditions: 17 MPa, 45 °C, ethanol 2 ml, the mass ratio of CNTs to HNO3 1/14). | |
Table 1 H2-TG characterization results of CNTs pretreated by different methods
The number of sample |
The pretreatment conditions of CNTs |
The weight loss ratio/% |
1# |
Untreated |
2.34 |
2# |
Treated with HNO310 ml and no-ultrasound- |
9.07 |
3# |
Treated with HNO310 ml and ultrasound time 20 min |
6.64 |
4# |
Treated with HNO3 100 ml and ultrasound time 20 min |
5.11 |
5# |
Treated with HNO3100 ml and ultrasound time 1 h |
3.26 |
The effect of the nitric acid consumption reflected by the mass ratio of CNTs to nitric acid on the morphology of Ru/CNTs was illustrated in Fig. 8. It indicates that when the dosage of nitric acid increases tenfold, the average particle size slightly increases and the metal loading shown in the local areas decreases. The reason of the experimental phenomenon may be that the functional groups such as carboxyl groups were further oxidized to carbon dioxide due to the presence of excess nitric acid. This explanation could be evidenced by the decrease of the amount of the functional groups, which is reflected by the decrease of weight loss ratio of pretreated CNTs with the increase in the dosage of nitric acid.
 |
| Fig. 8 Effect of nitric acid dosage on morphology of Ru/CNTs catalyst ((a)-1/140, wt%; (b)-1/14, wt%; ultrasound time 20 min; ultrasound power 120 w). | |
According to the discussions mentioned above, the ultrasonication-assisted nitric acid oxidation pretreatment method for CNTs is more favorable to the dispersion of Ru NPs than the separate utilization of ultrasonication or nitric acid oxidation. However, the appropriate ultrasound time and the dosage of nitric acid are the prerequisites of its good performance. Both too long ultrasound time and too much dosage of nitric acid are unfavorable to the dispersion of metal particles. The optimized pretreatment conditions are ultrasound time 20 min and nitric acid dosage 1/14 (the mass ratio of CNTs to nitric acid).
3.3 The highlights of this work
3.3.1 Smaller Ru NPs. As mentioned above, the mean particle size of Ru NPs could be controlled in the range of 0.42–3.66 nm, which is much smaller than that (2–10 nm) of Ru NPs reported in the previous reports. Considering the particle size, metal dispersion, and metal loading, the Ru NPs supported on the CNTs pretreated by ultrasonication-assisted nitric acid oxidation at the optimized ultrasound time and the dosage of nitric acid were chosen as the optimum composite (Fig. 9a) in this work.
 |
| Fig. 9 The comparison of pre-prepared Ru/CNTs composites with that reported in literature ((a)-Ru/CNTs prepared in this work; (b)-Ru/CNTs prepared by SFD with CNTs pretreated by nitric acid;38 (c)-Ru/CNTs prepared by impregnation method39). | |
3.3.2 The utilization of SFD method. It is well known that impregnation method is a mostly used method to prepare the supported metal NPs. The mean particle size of Ru NPs supported on CNTs prepared by impregnation method and shown in Fig. 9c is about 7.5 nm, which is larger than that of supported Ru NPs prepared by SFD method and shown in Fig. 9a and b. Moreover, the impregnation method has a difficulty in tailoring the dispersion and the particle size of metal NPs. The utilization of some poisonous and organic agents in the preparation of catalysts using the impregnation method is not in accordance with the development of green chemistry. However, supercritical fluid deposition method is a novel environmental-friendly preparation method of supported metal NPs, which has drawn many attentions from many researchers for the utilization of the supercritical fluids. They exhibit a distinctive hybrid of gas-like and liquid-like properties. Like gas, they exhibit high diffusivity, low viscosity and near zero surface tension, which can facilitate the delivery of solution to mesopores and micropores of porous materials and enable SFD technique to obtain high uniformity and well-dispersed metal NPs supported on supports; like liquid, they possess high solvation power for organic and inorganic solutes, which is favorable to the full dissolution of metal precursors.
3.3.3 The novelty of pretreatment method of carbon supports. According to the Ru NPs shown in Fig. 9a and b, the mean particle size of Ru NPs supported on the CNTs pretreated with nitric acid is much smaller than that of Ru NPs supported on the CNTs pretreated by ultrasonication-assisted nitric acid method. It is well known that the tendency of aggregation and the inert properties of surface have greatly limited the employment of CNTs as the supports of metal NPs. Although some researchers have tried to promote the dispersion of CNTs with the aid of ultrasound, the CNTs aggregate together again when the ultrasound are suspended. The nitric acid oxidation treatment has already been tried to activate their inert surface, whereas the performance is not well. A part of outer surface and inner cavities of CNTs could not be fully oxidized for their agglomerate rate. The simultaneous utilization of ultrasonication and nitric acid oxidation could solve the problems above very well.
4. Conclusions
In this work, highly dispersed Ru NPs supported on the carbonaceous supports was synthesized by an environmental-friendly SFD method. Compared with impregnation method, it is more easily to control the dispersion of Ru NPs. Here, the particle size of Ru NPs could be controlled in the range of 0.42–3.66 nm by varying carbon supports and the pretreatment methods of supports. Compared with AC, CNTs is more favorable to the dispersion of the Ru NPs on the pore surfaces of carbon supports. Compared with the separate utilization of ultrasonication or nitric acid oxidation, the synergy of ultrasonication and nitric acid oxidation is more favorable to the dispersion of Ru NPs. However, the performance of the new pretreatment method is sensitive to the pretreatment conditions including the ultrasound time and the dosage of nitric acid. The optimized pretreatment conditions are ultrasound time 20 min and the dosage of nitric acid 1/14 (the mass ratio of CNTs to the nitric acid). The results obtained in this work may have a positive influence on the extensive application of supported metal NPs in the chemical industry.
References
- D. Astruc, Nanoparticles and catalysis, Wiley Online Library, 2008 Search PubMed.
- D. Astruc, F. Lu and J. R. Aranzaes, Angew. Chem., Int. Ed., 2005, 44, 7852–7872 CrossRef CAS PubMed.
- M. Zahmakıran and S. Özkar, Nanoscale, 2011, 3, 3462–3481 RSC.
- C. H. Liang, Z. B. Wei, Q. Xin and C. Li, Appl. Catal., A, 2001, 208, 193–201 CrossRef CAS.
- A. Kotarba, J. Dmytrzyk, W. Raróg-Pilecka and Z. Kowalczyk, Appl. Surf. Sci., 2003, 207, 327–333 CrossRef CAS.
- J. J. Verdonck, P. A. Jacobs and J. B. Uytterhoeven, J. Chem. Soc., Chem. Commun., 1979, 4, 181–182 RSC.
- M. Vannice, Journal of Catalysi, 1975, 37, 449–461 CrossRef CAS.
- L. Zhou, X. Qi, X. Jiang, Y. Zhou, H. Fu and H. Chen, J. Colloid Interface Sci., 2013, 392, 201–205 CrossRef CAS PubMed.
- A. F. E. Auer, J. Pietsch and T. Tacke, Appl. Catal., A, 1998, 173, 259–271 CrossRef.
- Z. Sun, Z. Liu, B. Han, Y. Wang, J. Du, Z. Xie and G. Han, Adv. Mater., 2005, 17, 928–932 CrossRef CAS.
- J. Wehrli, A. Baiker, D. Monti and H. Blaser, J. Mol. Catal., 1990, 61, 207–226 CrossRef CAS.
- H. Can and Ö. Metin, Appl. Catal., B, 2012, 125, 304–310 CrossRef CAS.
- H. Q. Tang and J. L. Li, J. Fuel Chem. Technol., 2011, 39, 615–620 CrossRef CAS.
- C. M. Yang, P. H. Liu, Y. F. Ho, C. Y. Chiu and K. J. Chao, Chem. Mater., 2003, 15, 275–280 CrossRef CAS.
- G. H. Li, L. J. Hu and J. M. Hill, Appl. Catal., A, 2006, 301, 16–24 CrossRef CAS.
- N. Popovska, K. Danova, I. Jipa and U. Zenneck, Powder Technol., 2011, 207, 17–25 CrossRef CAS.
- R. J. White, R. Luque, V. L. Budarin, J. H. Clark and D. J. Macquarrie, Chem. Soc. Rev., 2009, 38, 481–494 RSC.
- C. Y. Chen, K. Y. Lin, W. T. Tsai, J. K. Chang and C. M. Tseng, Int. J. Hydrogen Energy, 2010, 35, 5490–5497 CrossRef CAS.
- S. P. Somani, P. R. Somani, A. Sato and M. Umeno, Diamond Relat. Mater., 2009, 18, 497–500 CrossRef CAS.
- C. Antonetti, M. Oubenali, A. M. Raspolli Galletti, P. Serp and G. Vannucci, Appl. Catal., A, 2012, 421, 99–107 CrossRef.
- O. Sawai and Y. Oshima, J. Supercrit. Fluids, 2008, 47, 240–246 CrossRef CAS.
- G. I. Garrido, F. Patcas, G. Upper, M. Türk, S. Yilmaz and B. Kraushaar-Czarnetzki, Appl. Catal., A, 2008, 338, 58–65 CrossRef CAS.
- S. Haji, Y. Zhang and C. Erkey, Appl. Catal., A, 2010, 374, 1–10 CrossRef CAS.
- M. Alibouri, S. Ghoreishi and H. Aghabozorg, J. Supercrit. Fluids, 2009, 49, 239–248 CrossRef CAS.
- J. J. Watkins and T. J. McCarthy, Chem. Mater., 1995, 7, 1991–1994 CrossRef CAS.
- Y. Zhang, D. F. Kang, M. Aindow and C. Erkey, J. Phys. Chem., 2005, 109, 2617–2624 CrossRef CAS PubMed.
- Y. Zhang and C. Erkey, J. Supercrit. Fluids, 2006, 38, 252–267 CrossRef CAS.
- Q. Liang, B. C. Li, S. H. Tang, Z. J. Li, Q. Li, L. Z. Gao, B. L. Zhang and Z. L. Yu, Acta Chim. Sin., 2000, 58, 1336–1339 CAS.
- J. Chen, Z. L. Tao and S. L. Li, J. Am. Chem. Soc., 2004, 126, 3060–3061 CrossRef CAS PubMed.
- M. C. Lafont, L. F. Juarez and C. Vahlas, Scr. Mater., 2004, 51, 699–703 CrossRef CAS.
- Z. Y. Sun, Z. M. Liu, B. X. Han, Y. Wang, J. M. Du, Z. L. Xie and G. J. Hang, Adv. Mater., 2005, 17, 928–932 CrossRef CAS.
- C. Antonetti, M. Oubenali, A. M. R. Galletti, P. Serp and G. Vannucci, Appl. Catal., A, 2012, 421, 99–107 CrossRef.
- Y. M. Zhang, H. X. Jiang, Y. H. Wang and M. H. Zhang, Ind. Eng. Chem. Res., 2014, 53, 6380–6387 CrossRef CAS.
- L. P. Zhao and L. Gao, Carbon, 2004, 42, 3269–3272 CrossRef CAS.
- L. P. Zhao and L. Gao, Carbon, 2004, 42, 1858–1861 CrossRef CAS.
- Z. Y. Sun, Z. Li, C. L. Huang, Y. F. Zhao, H. Y. Zhang, R. T. Tao and Z. M. Liu, Carbon, 2011, 49, 4376–4384 CrossRef CAS.
- E. T. Dujardin, H. Hiura and K. Tanigaki, Science, 1994, 265, 1850–1852 CAS.
- X. R. Ye, Y. H. Lin, C. M. Wang, M. H. Engelhand, Y. Wang and C. M. Wai, J. Mater. Chem., 2004, 14, 908–913 RSC.
- J. X. Pan, J. H. Li, C. Wang and Z. Zhang, React. Kinet. Catal. Lett., 2007, 90, 233–242 CrossRef CAS.
|
This journal is © The Royal Society of Chemistry 2016 |
Click here to see how this site uses Cookies. View our privacy policy here.