DOI:
10.1039/C5RA26898B
(Communication)
RSC Adv., 2016,
6, 16640-16644
Ultrasound-assisted recovery of free-standing high-aspect-ratio micropillars
Received
16th December 2015
, Accepted 2nd February 2016
First published on 3rd February 2016
Abstract
High-aspect-ratio polymer micropillar arrays are widely employed in microfluidics and microdevices. The collapse of polymer micropillars, however, would induce device degradation, which calls for a recovery method for the collapsed micropillars to restore their performances. In this communication, we propose a cost-effective and robust approach for recovery of free-standing high-aspect-ratio micropillars by ultrasonic-assisted technology. The collapsed micropillar array immersed in a low-surface-energy solution will recover its upright state by ultrasonic stimulation and keep standing steadily due to the low-surface-energy treatment. The collapsed micropillars treated by the proposed approach are entirely able to spring back to their original upright position.
Introduction
High-aspect-ratio micropillar arrays are receiving considerable attention due to their excellent properties of large surface area as well as good modulability of light and electromagnetism.1 By exploiting these features, researchers have been developing micropillar arrays for a wide range of applications, including electron collection enhancement in solar cells,2 cell detection and particle separation3 in biomedicine, superoleophobics4 and superhydrophobics5,6 in functional coatings, light trapping in optics,7 lab-on-a-chip in microfluidics,8 etc. So far, these above mentioned applications almost are dependent on the motionless micropillar arrays. When the polymer micropillar arrays are actuated by outside stimuli, based on the static performances the dynamic properties of the moveable micropillar arrays can also be acquired.
Therefore the unique characteristics may have enormous potential for new-concept technological applications. For example, the forces on the substrate generated by cells can be acquired through the deformation of moveable polymer micropillars.9 In addition, the magnetic micropillars could be manipulated to move and induce tissue patterning or cell distribution.10 Due to the prominently dynamic performances, the moveable micropillar arrays are widely employed in soft robotic tentacles,11 microfluidic mixing,12 single microbial cell encapsulation,13 as well as airflow sensors14 and pressure sensors.15
The above microdevices performances depend critically on the structural stability of polymer micropillar arrays. However, it is most susceptible to deformation or collapse of high-aspect-ratio micropillar array. Previous researches on stability of polymer micropillar arrays have been done. For example, Alexander Bietsch and Bruno Michel16 proposed that the collapse of micropillars may take place in the adjacent zones of micropillar arrays when the surface energy of micropillars is larger than that of the mold. Furthermore, comprehensive analyses on the mechanism of different collapse modes of micropillars are presented by Nicholas J. Glassmaker et al.17,18 In addition, a recent work by Shu Yang et al.19–21 has researched on the mechanisms of collapsed micropillar array induced by the adhesive force or capillary force. Although theoretical and experimental researches on stability of polymer micropillar arrays have been addressed, few studies focus on the recovery of collapsed micropillar arrays. It is generally known that the fabrication of high-aspect-ratio micropillars is complicated and difficult. In addition, the microdevices with polymer micropillar array as their key parts would lose their functions once the micropillars collapse. Therefore it is worthy to make the collapsed micropillars spring back to their original upright position. This communication aims to demonstrate the ultrasound-assisted recovery of free-standing high-aspect-ratio micropillars. The highlight is that the collapsed micropillar array can be recovered by a simple way of ultrasonic-assisted technology. The collapsed micropillars immersed in the low-surface-energy solution will be recovered by ultrasonic and remained standing steadily due to the micropillars with low-surface-energy modification. The collapsed polymer micropillars treated by this approach will be entirely able to spring back to their original upright position.
Experimentation process
Silicon mold fabrication
The fabrication of silicon mold with microhole array was involved the following procedures, including photolithography and deep reactive etching. Firstly, a promoter of adhesion (e.g. hexamethyldisilazane (HMDS)) was applied to the cleaned silicon surface by spin-coating and then baked. Secondly, a thin film (1.5 μm thickness) of positive photoresist (e.g. EPG535) was achieved by spin-coating on the HDMS surface and then pre-baked. Thirdly, the exposure (e.g. 9 s), post-exposure bake and development (e.g. 8‰ NaOH developer solution, 35 s) of the substrate, were conducted successively, then the photoresist pattern was acquired. After that, the aluminum layer (0.6 μm thickness) was deposited onto the silicon substrate using magnetron sputtering tool, Explorer 14, Denton Vacuum, USA, and, subsequently, the lift-off procedure was performed to obtained aluminum layer patterning. Then the deep etching of silicon was fulfilled by the ICP etch tool, Oxford Instrument ICP180 dry etching equipment, UK. The deep reactive etching of silicon substrate was exposed to the following gases, including sub-cycles of C4F8 for passivation and SF6 for etching. The final silicon mold with microhole array (10 μm in diameter and 100 μm in height) was achieved by removal of aluminum layer.
Polymer micropillars fabrication
The polymer micropillar array was fabricated by replication from the silicon mold with microhole array. Firstly, the PDMS prepolymer (Dow Corning, Sylgard 184) was prepared by mixing PDMS base with a curing agent in a 10
:
1 ratio by weight and then the mixture was placed in a vacuum environment until the bubbles generated during stirring disappeared. Secondly, the bubble-free PDMS mixture was poured over the silicon mold with microhole array, degassed again, cured at 75 °C for 1.5 hour and peeled off to gain polymer micropillars with a diameter of 10 μm and a height of 100 μm.
Ultrasound-assisted recovery processes of the collapsed polymer micropillars
To make the collapsed polymer micropillars recovered, an effortless and novel way is proposed by using polymer fluororesin with low surface energy. Firstly, the fluororesin prepolymer was prepared by mixing fluororesin base (DAIKIN, GK 570) and a curing agent (TPA 90SB) with brittleness modifier (TEGO Protect 5001) in a ratio of 10
:
1
:
1 by weight, with 10 minute stirring at room temperature followed by 10 minute vacuumed to remove the air bubbles. Then, the bubble-free mixture was poured over the surface of collapsed PDMS micropillar array, degassed again (e.g. 15 minutes) after pouring under a vacuum environment to ensure sufficient contact between the two of them. To drive the collapsed micropillars to spring back to their original upright position, ultrasonic is employed to provide the collapsed micropillars with an initial movement. The collapsed micropillars entirely immersed in the fluororesin solution were treated with ultrasonic for 15 minutes, cured at 80 °C for 30 minutes. After fully cured, the fluororesin is peeled off from the PDMS micropillars, and the as-collapsed PDMS micropillars can be fully recovered.
Result and discussion
Mechanism of the collapsed polymer micropillars
The micropillar collapse consists of lateral collapse and ground collapse. High-aspect-ratio polymer micropillars can lead to adhesion between micropillars if they are close enough (lateral collapse) or collapse to the ground (ground collapse).
The micropillar array fabricated with soft elastomeric polymer PDMS has a high aspect ratio of 10 in this communication. In these cases, both ground collapse and lateral collapse would occur. Firstly we investigate the lateral collapse of the micropillars. According to theoretical prediction for the lateral collapse of neighboring micropilays due to adhesion proposed by Glassmaker et al.17,18 the critical aspect ratio (h/d)c is
|
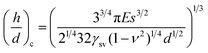 | (1) |
where
h is the height of micropillar,
d is the diameter of micropillar,
E is Young's modulus of material,
s is the lateral separation between adjacent micropillars,
γsv is the surface energy of the micropillars material,
ν is the Poisson's ratio of material. The physical parameters of PDMS will be shown as below, the diameter of micropillar is 10 μm, Young's modulus is 1.7 MPa, the lateral separation between adjacent micropillars is 80 μm, the surface energy of the PDMS is 22 mN m
−1, the Poisson's ratio is 0.5.
22 Therefore we can obtain the critical aspect ratio (
h/
d)
c for stability of PDMS micropillar array with 10 μm diameter can be up to 15.23, which is considerably larger than 10. In addition, the critical interpose spacing of PDMS micropillar array (10 μm in diameter and 100 μm in height) is up to 34.47 μm, which is less than 80 μm. Hence, the lateral collapse did not happen here.
Next the mechanism of ground collapse will be investigated as following. It could be described by eqn (2) in terms of the stability analysis following the approach used by Hui et al.20 and Glassmaker et al.17,18
|
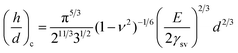 | (2) |
Similarly, the critical aspect ratio of ground collapse achieved by calculation is 5.76, which is lower than the experimental aspect ratio of 10. It apparently shows that the ground collapse occurred due to the instability of micropillars (Fig. 1(a)).
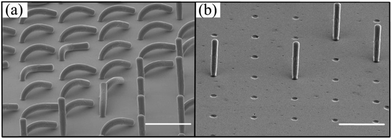 |
| Fig. 1 (a) Micropillars fabricated with PDMS are mostly collapsed on the ground (10 μm in diameter and 100 μm in height); (b) few micropillars fabricated with fluororesin are upright, most of them are fractured near the roots of micropillars (10 μm in diameter and 100 μm in height). Scale bars indicate 100 μm. | |
Based on the theoretical analysis of lateral collapse and ground collapse of high-aspect-ratio micropillars, we can take some effective measures to improve the stability of micropillars. For example, in eqn (2), the critical aspect ratio for ground collapse would be smaller as γsv increases, which implies that lower-surface-energy treatment can effectively reduce the possibility of ground collapse. Fluororesin is an excellent material with lower surface energy (11 mN m−1) and high Young's modulus (10 MPa to 2 GPa).23–26 According to the eqn (2), the critical aspect ratio for the fluororesin micropillars can be up to 67.3 (10 MPa in Young's modulus), much larger than that of PDMS micropillars (which is 10, experimentally). In experiments, however, only few high-aspect-ratio fluororesin micropillars can be alive, accompanying with amount of fractured micropillars in the silicon mold, which can be attributed to its high brittleness, as shown in Fig. 1(b).
To explain the ground collapse of high-aspect-ratio micropillars, a model is built as depicted in Fig. 2(a), which composes of a length L of deformation part curved in a semicircle of radius R and a length t of undeformed part adhered to the surface of ground. The energy of adhesion UA can be obtained by17,18,27
where 2
a is the width of the contact area between micropillar and the ground,
W is the work of adhesion of the material to itself (
W = 44 mN m
−1).
28 According to the Johnson–Kendall–Roberts theory of adhesion,
29 the
a can be calculated by
|
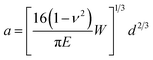 | (4) |
where
ν is the Poisson's ratio of material (0.5),
W is the work of adhesion of the material to itself (
W = 44 mN m
−1),
E is Young's modulus of material (1.7 MPa),
d is the diameter of micropillar (10 μm). The elastic energy could be calculated by the equation
30where
E is Young's modulus of material (1.7 MPa),
I = π
d4/64 is the moment of inertia of a circular cross-section,
L is the length of deformation part curved in a semicircle of radius
R, and
L = π
R. There are two types of ground collapse, including the head collapse (as
Fig. 2(b) shows) and complete collapse (as
Fig. 2(c) shows). For the head collapse, the length
t is close to zero and the length
L should be approximate to 100 μm. Thus, we can obtain
UE is 4.12 × 10
−11 Joules and
UA is 0 Joules. For the completely collapse, the length
t will be approximate to 100 μm and the length
L can be considered as zero, and
UE tends to infinity while
UA is 1.89 × 10
−11 Joules. Theorically, for elastic materials (
e.g., PDMS), the collapsed micropillars should entirely spring back to their original upright position when elastic energy
UE is greater than the work of adhesion
UA. In experiments, however, for both of the collapse situation (
Fig. 2(b) and (c)), the micropillars keep in their collapse states. The above phenomena may be attributed to the behaviour of molecular chains in collapse. The molecular chains of PDMS are highly convoluted and spatially helical due to the flexibility of silicon–oxygen bond, therefore, the molecular forces between the segments is weak, so that the molecules are easily vibrative and motional. Hence, a conclusion can be drawn that the molecular force will be decreased with the increase of molecular spacing. In other words, the molecular force is mainly determined by the deformation of micropillar. The deformation of micropillar is considered to be elastically deformed under small deformation and will be recovered when the load is removed. For large deformation, both the recoverable elastic deformation and non-recoverable plastic deformation occur in the micropillars deformation after removal of the external force.
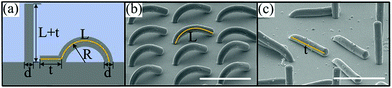 |
| Fig. 2 (a) Schematic of geometrical model for the theoretical calculations; (b) the heads of PDMS micropillars collapsed to the ground, and the length L is approximate to the height (100 μm); (c) PDMS micropillars completely collapsed to the ground, and the length t is roughly equal to the height (100 μm). Scale bars indicate 100 μm. | |
Mechanism of ultrasound-assisted recovery of the collapsed polymer micropillars
It is well known that PDMS is a promising candidate material for high-aspect-ratio micropillars fabrication by micromolding rather than brittle fluororesin. However, it is susceptible to collapse for PDMS micropillar array because of its low modulus, which leads to high fabrication cost. Furthermore, the microdevices with polymer micropillar array as their key parts would lose their functions once the micropillars collapse. To reduce costs and ensure the normal performance of microdevices, it is valuable to recover the collapsed micropillars to their original states. A simple and effective method is proposed to drive the collapsed micropillars to spring back to their original upright position. The specific measures for implementation as mentioned above.
The ultrasonic can urge the liquid to generate tens of thousands of tiny bubbles with diameter of 50–500 μm, and the tiny bubbles in the liquid fluororesin keep vibrating under the sound field. The energy generated by the vibrative bubbles will exert on the collapsed micropillars through the medium of liquid fluororesin, which can drive the micropillars swinging in the solution. The swinging of each micropillar will separate it from the ground (for ground collapse) or adjacent micropillars (for lateral collapse). The ultrasonic plays a vital role in providing the collapsed micropillars with an initial movement. The specific steps are just as demonstrated in Fig. 3.
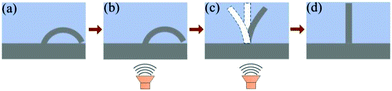 |
| Fig. 3 Schematic view of the ultrasound-assisted recovery of the collapsed polymer micropillars. (a) collapsed PDMS micropillars, (b) collapsed micropillars separated from the ground under ultrasonic treatment, (c) the swing of micropillars under ultrasonic treatment, (d) recovered micropillars after fluororesin solidification. | |
It is attractive for the collapsed PDMS micropillars treated with fluororesin to recover by ultrasonic-assisted technology. This phenomenon can be explained by the surface energy effect. The collapsed PDMS micropillars immersed into the fluororesin solution are totally coated with a film of fluororesin. And then the surface energy of collapsed micropillars will be sharply reduced.
According to the eqn (2), the diameter dependence of the critical aspect ratios (h/d)c for stability of PDMS micropillar array can be achieved, so does for the (h/d)c′ of PDMS micropillars treated with fluororesin, as Fig. 4 shows. Obviously, because of the surface-coating with fluororesin which has lower surface energy, (h/d)c′ are much greater than the ones (h/d)c. The micropillars fabricated by PDMS will remain upright when the aspect ratios (h/d) are below the (h/d)c, and would collapse when (h/d) over (h/d)c. For the micropillars surface-coated with fluororesin, the micropillars keep upright when the aspect ratios (h/d) are below (h/d)c′. Therefore, it is possible to recover the collapsed PDMS micropillars to the upright state by surface-treated with fluororesin if (h/d) is in the range from (h/d)c to (h/d)c′. In addition, the micropillars surface-coated with fluororesin will not be recovered when the aspect ratios (h/d) are greater than the (h/d)c′. For example, the experimental aspect ratio (10) is greater than calculated critical value (h/d)c (5.76) but less than (h/d)c′ (11.53), the collapsed micropillars are observed to be recovered through treating with fluororesin (in Fig. 5). Therefore, it indicates that the experimental results are well consistent with the theoretical prediction.
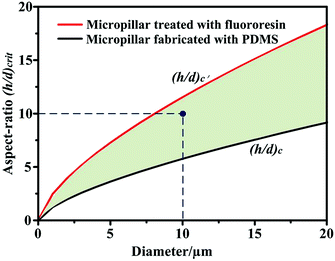 |
| Fig. 4 A plot of critical aspect ratios (h/d) vs. different diameters of micropillars. (h/d)c′ indicates the critical aspect ratios for stability of PDMS micropillars treated with fluororesin, and (h/d)c indicates the critical aspect ratios for stability of PDMS micropillar array. | |
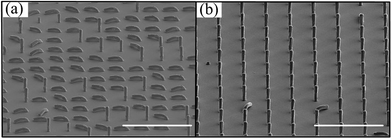 |
| Fig. 5 SEM micrographs for (a) collapsed micropillars fabricated with PDMS, and (b) recovered micropillars after treating with fluororesin. Scale bars indicate 300 μm. | |
Stability analysis of ultrasound-assisted recovery of the collapsed polymer micropillars
The stability of the recovered micropillars should be evaluated through some measures. For example, treatment with other material, i.e. the recovered micropillar array is immersed into high-surface-energy photoresist solution. It is found that the recovered micropillars are collapsed again. The main reason could attribute to the high surface energy of photoresist. When the collapsed micropillars are treated by fluororesin in the same way as shown in Fig. 2, the original appearance of the collapsed micropillars would be recovered. The SEM image is shown in Fig. 6.
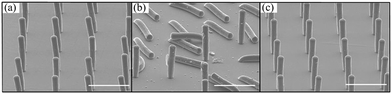 |
| Fig. 6 (a) The micropillars remain upright state; (b) the micropillars are collapsed on the ground through treating with photoresist solution; (c) the collapsed micropillars are recovered after surface-treating with the fluororesin. Scale bars indicate 100 μm. | |
The method of ultrasound-assisted recovery is also available for the lateral collapse of micropillars. In most cases, the micropillars are exposed to the liquid. In general, the torque generated by the capillary force is much larger than that from adhesion force. Therefore the lateral collapse could be easily induced due to the capillary force as the liquid evaporates off the surface of micropillars. When treated with fluororesin in the same way as shown in Fig. 2, the lateral collapse of micropillar array finally can return to its original position as shown in Fig. 7. Experiments indicate that, this approach is robust and available both for the ground collapse and lateral collapse.
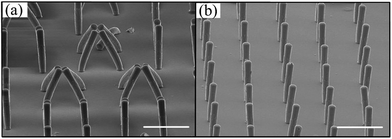 |
| Fig. 7 (a) The lateral collapse of micropillars resulted from the capillary force, (b) the recovery of the lateral collapse of micropillars treated with the fluororesin. | |
Conclusion
In summary, we proposed a cost-effective and robust approach for recovery of free-standing high-aspect-ratio micropillars by ultrasonic-assisted technology. The collapsed micropillars can be recovered to their upright position by ultrasonic when immersed in the low-surface-energy fluororesin solution, and keep standing steadily due to the low-surface-energy treatment after taken out from the solvent. The collapsed PDMS micropillar with high aspect ratio of 10 (over its critical aspect ratio, 5.76), can be recovered by the ultrasonic-assisted approach in fluororesin solution (the critical aspect ratio is up to 11.53 by fluororesin treatment). This approach is robust and available both for the ground collapse and lateral collapse, which can be indicated by the recovery of induced micropillar clustering by capillary force. The proposed approach is promising for recovery or functions-restoring of various devices with high-aspect-ratio micropillars.
Acknowledgements
The authors gratefully appreciate the financial supports by the National Natural Science Foundation of China (No. 51427805, 51305337, 51275400, 61404103). This work is partially sponsored by the China Postdoctoral Science Foundation funded project (2014T70912).
Notes and references
- X. Li, H. Tian, J. Shao, Y. Ding and H. Liu, Langmuir, 2013, 29, 1351–1355 CrossRef CAS PubMed.
- Z. Yang, T. Xu, S. Gao, U. Welp and W. K. Kwok, J. Phys. Chem. C, 2010, 114, 19151–19156 CAS.
-
(a) Z. Geng, Y. Ju, Q. Wang, W. Wang and Z. Li, RSC Adv., 2013, 3, 14798–14806 RSC;
(b) L. Yu, S. R. Ng, Y. Xu, H. Dong, Y. J. Wang and C. M. Li, Lab Chip, 2013, 13, 3163–3182 RSC;
(c) X. Gao, Y. Y. Chau, J. Xie, J. Wan, Y. Ren, J. Qin and W. Wen, RSC Adv., 2015, 5, 22916–22922 RSC;
(d) R. Ramji, N. T. Khan, A. Muñoz-Rojas and K. Miller-Jensen, RSC Adv., 2015, 5, 66294–66300 RSC;
(e) G. Perozziello, P. Candeloro, F. Gentile, A. Nicastri, A. Perri, M. L. Coluccio, A. Adamod, F. Pardeoa, R. Catalanoa, E. Parrottac, H. D. Espinosab, G. Cuda and H. D. Espinosa, RSC Adv., 2014, 4, 55590–55598 RSC.
- D. Wu, S. Z. Wu, Q. D. Chen, S. Zhao, H. Zhang, J. Jiao, J. A. Piersol, J. N. Wang, H. B. Sun and L. Jiang, Lab Chip, 2011, 11, 3873–3879 RSC.
- K. Liu, Y. Tian and L. Jiang, Prog. Mater. Sci., 2013, 58, 503–564 CrossRef CAS.
- S. Y. Lee, Y. Rahmawan and S. Yang, ACS Appl. Mater. Interfaces, 2015, 7, 24197–24203 CAS.
- E. Garnett and P. Yang, Nano Lett., 2010, 10, 1082–1087 CrossRef CAS PubMed.
- Y. C. Toh, T. C. Lim, D. Tai, G. Xiao, D. van Noort and H. Yu, Lab Chip, 2009, 9, 2026–2035 RSC.
- F. Khademolhosseini and M. Chiao, J. Microelectromech. Syst., 2013, 22, 131–139 CrossRef CAS.
- J. le Digabel, N. Biais, J. Fresnais, J. F. Berret, P. Hersen and B. Ladoux, Lab Chip, 2011, 11, 2630–2636 RSC.
- R. V. Martinez, J. L. Branch, C. R. Fish, L. Jin, R. F. Shepherd, R. M. D. Nunes, Z. Suo and G. M. Whitesides, Adv. Mater., 2013, 25, 205–212 CrossRef CAS PubMed.
- B. Zhou, W. Xu, A. A. Syed, Y. Chau, L. Chen, B. Chew, O. Yassine, X. Wu, Y. Gao, J. Zhang, X. Xiao, J. Kosel, X. X. Zhang, Z. Yao and W. Wen, Lab Chip, 2015, 15, 2125–2132 RSC.
- K. J. Park, K. G. Lee, S. Seok, B. G. Choi, M. K. Lee, T. J. Park, J. Y. Park, D. H. Kim and S. J. Lee, Lab Chip, 2014, 14, 1873–1879 RSC.
- J. Paek and J. Kim, Nat. Commun., 2014, 5, 3324 Search PubMed.
- H. Park, Y. R. Jeong, J. Yun, S. Y. Hong, S. Jin, S. J. Lee, G. Zi and J. S. Ha, ACS Nano, 2015, 9, 9974–9985 CrossRef CAS PubMed.
- A. Bietsch and B. Michel, J. Appl. Phys., 2000, 88, 4310–4318 CrossRef CAS.
- K. G. Sharp, G. S. Blackman, N. J. Glassmaker, A. Jagota and C. Y. Hui, Langmuir, 2004, 20, 6430–6438 CrossRef CAS PubMed.
- N. J. Glassmaker, A. Jagota, C. Y. Hui and J. Kim, J. R. Soc., Interface, 2004, 1, 23–33 CrossRef CAS PubMed.
- D. Chandra and S. Yang, Acc. Chem. Res., 2010, 43, 1080–1091 CrossRef CAS PubMed.
- Y. Zhang, C. W. Lo, J. A. Taylor and S. Yang, Langmuir, 2006, 22, 8595–8601 CrossRef CAS PubMed.
- S. F. Chini and A. Amirfazli, Langmuir, 2010, 26, 13707–13714 CrossRef CAS PubMed.
- P. Roca-Cusachs, F. Rico, E. Martinez, J. Toset, R. Farré and D. Navajas, Langmuir, 2005, 21, 5542–5548 CrossRef CAS PubMed.
- H. Lan, Soft UV Nanoimprint Lithography and Its Applications, in Updates in Advanced Lithography, ed. S. Hosaka, InTech, Japan, 2013, vol. 7, pp. 169–195 Search PubMed.
- J. Tsibouklis, M. Stone, A. A. Thorpe, P. Graham, T. G. Nevell and R. J. Ewen, Langmuir, 1999, 15, 7076–7079 CrossRef CAS.
- D. H. Kaelble, J. Adhes., 1970, 2, 66–81 CrossRef CAS.
- M. J. Rosen and J. T. Kunjappu, Surfactants and interfacial phenomena, John Wiley & Sons, New Jersey, 2012 Search PubMed.
- C. Y. Hui, A. Jagota, Y. Y. Lin and E. J. Kramer, Langmuir, 2002, 18, 1394–1407 CrossRef CAS.
- M. K. Chaudhury and G. M. Whitesides, Langmuir, 1991, 7, 1013–1025 CrossRef CAS.
- M. K. Chaudhury, T. Weaver, C. Y. Hui and E. J. Kramer, J. Appl. Phys., 1996, 80, 30–37 CrossRef CAS.
- S. H. Crandall, T. J. Lardner, R. R. Archer, N. H. Cook and N. C. Dahl, An introduction to the mechanics of solids, McGraw-Hill, Singapore, 1978 Search PubMed.
|
This journal is © The Royal Society of Chemistry 2016 |
Click here to see how this site uses Cookies. View our privacy policy here.