DOI:
10.1039/C5RA25371C
(Paper)
RSC Adv., 2016,
6, 7364-7369
Enhanced dielectric and ferroelectric properties in PVDF composite flexible films through doping with diisopropylammonium bromide
Received
29th November 2015
, Accepted 11th January 2016
First published on 14th January 2016
Abstract
A ferroelectric compound diisopropylammonium bromide (DIPAB) was dispersed into poly(vinylidene fluoride) (PVDF) matrix to form DIPAB/PVDF composite films. The composite film with different content of DIPAB was characterized by IR, XRD, DSC and SEM. The results indicated that soluble DIPAB could be homogeneously dispersed within PVDF matrix to form almost pure β-phase PVDF composite films without obvious agglomeration, and the crystallinity of PVDF polymer increased with increasing content of DIPAB inclusion. DIPAB/PVDF composite films exhibit very high dielectric constants and relatively low dielectric loss. Both dielectric constants and dielectric loss are frequency dependent and increased with increasing DIPAB content. DIPAB/PVDF composite films also exhibit enhanced ferroelectric properties. Incorporating DIPAB into PVDF is a useful way to improve the dielectric and ferroelectric property of PVDF composite films.
Introduction
Poly(vinylidene fluoride) (PVDF) is a highly flexible and processable ferroelectric polymer material, which has attracted worldwide attention in many industrial fields due to its versatile excellent properties, especially its outstanding piezo- and pyroelectric properties.1 It has been known that PVDF possesses as least five possible types of crystal phase (α, β, γ, δ and ε), which have great effect on its properties.2 The non-polar α-phase, belonging to trans-gauche (TGTG′) conformation, is the most common phase. The polar β-phase with all-trans planar zig-zag conformation (TTTT) with all the fluorine atoms located on the same side of the polymer chains is a more attractive crystal type. This alignment of polymer chains endows β-phase PVDF with a much higher polarity than other phases, accordingly the highest piezo and pyroelectric properties as well as ferroelectric activity, which are important to the applications of energy conversion and storage involving the electroactive properties of dielectric PVDF materials.3 Many efforts have been done to produce β-phase PVDF, such as crystallization under high pressure, poling in a high electrical field, solid-state extrusion, rolling, or mechanical stretching process under certain conditions,4 but how to obtain high β-phase content of PVDF in a simple method remains still a challenge.
In addition, polymer materials with high dielectric constant have attracted increasing attention in electronic and electrical industry due to their inherent advantages in flexibility, easy processing, low cost and high breakdown strength.5 However, pure PVDF exhibits relatively low dielectric constants (e.g. <10) and consequently the electric energy density, is not adequate for the applications in electric-energy-storage capacitors and actuators.6 In order to overcome this shortcoming, two main methods have been developed to prepare polymer composites with high dielectric constant. One method focuses on dispersing conductive fillers into the PVDF matrix to achieve percolative composites, whose dielectric constant could dramatically increase near the percolation threshold according to percolation theory.7 However, they usually suffer from the drawbacks of a large increase in dielectric loss and very low breakdown strengths. Another way to improve the dielectric constant of PVDF is by incorporating high dielectric permittivity ferroelectric ceramics (such as BaTiO3, BaxSr1−xTiO3, Pb(Zr,Ti)O3) into the polymer matrix.8 However, in order to achieve the high dielectric constant, high volume fraction (>50 vol%) of ceramics will always have to be added into the composites, which suffering from several drawbacks, particularly in terms of high weight, low flexibility, and poor mechanical performance.9 In addition, insoluble inorganic ceramics are not easy to be well dispersed into PVDF matrix, and the resulting agglomeration will deteriorate the property of composites.
Diisopropylammonium bromide (DIPAB) has been found to be a ferroelectric compound with a spontaneous polarization of 23 μC cm−2, which is close to that of barium titanate (BTO)], high Curie temperature of 426 K (above that of BTO), large dielectric constant, and low dielectric loss.10 Similar diisopropylammonium salts have attracted researchers' increasing attentions.11 However, there is still a long way to go from single crystal to a practical material, such as the large single crystal size, certain mechanical strength and so on. DIPAB is soluble in many solvents including DMF etc., so it can be easily introduced into the PVDF matrix. This new type of PVDF composite will not only have the advantage of material preparation, but also provide a new perspective for changing properties of PVDF films. To date, no research on the dielectric properties of DIPAB/PVDF composite films has been reported.
Herein, we report a simple and effective route to obtain almost pure β-phase PVDF composite films with enhanced dielectric and ferroelectric properties by the addition of DIPAB. The effects of the loading content of DIPAB on the dielectric property of the DIPAB/PVDF composites have also been investigated.
Experimental
Materials and methods
All the chemicals used in this reaction were analytical grade and used as purchased from Shanghai Adamas Reagent Co., Ltd (Shanghai, China). PVDF (–CH2–CF2–)n of molecular weight 534
000 and N,N-dimethyl formamide (DMF) (C3H7NO) for the fabrication of polymer composite film. DIPAB was prepared by the reaction of diisopropylamine and HBr in aqueous solution.
X-ray diffraction (XRD; Bruker D8 Advance System, Germany) was performed at room temperature with Cu-target Kα radiation (λ = 0.154 nm). Fourier transform infrared spectroscopy (FTIR, Nicolet 6700, thermoscientific USA) was carried out over a range of 500–4000 cm−1. The melting and crystallization behaviours of PVDF composites with different contents of DIPAB were carried out on a differential scanning calorimeter DSC Q2000 TA Instruments. The sample was heated to 200 °C at a rate of 10 °C min−1 and held at 200 °C for 5 min to erase heating history, and then cooled to 30 °C at a rate of 10 °C min−1 to record the non-isothermal melting and crystallization behavior. Complex dielectric permittivity was performed using automatic impedance TongHui 2828 Analyzer. The measuring AC voltage was 1 V. The electric hysteresis loops were recorded on a Ferroelectric Tester Multiferroic made by Radiant Technologies, Inc. For dielectric and ferroelectric measurements, silver electrodes (area of 1 cm × 1 cm) were vacuum-evaporated onto both surfaces of the samples. The morphologies were observed with field emission scanning electron microscope (FE-SEM) performed on JEOL JSM-6700F.
Preparation of DIPAB/PVDF composite films
The PVDF powder was dissolved in DMF at 60 °C by magnetic stirring to yield a 10 wt% solution. Then 0.04 g silicone coupling agent KH-570 and different amount of DIPAB were added into 20 g above PVDF solution. The mixture solution was magnetic agitated in a 60 °C water bath for 1 h and sonicated for 30 minutes to ensure the complete dissolution and dispersion of DIPAB. Before casting, the mixture was degassed under vacuum for several hours to eliminate the air bubbles. Subsequently, the solutions were cast on glass substrates and incubated in an oven at 70 °C for 30 min to ensure the removal of solvent traces. In order to investigate the effects of the loading content of DIPAB, 0.04 g, 0.08 g, 0.12 g, 0.16 g and 0.20 g of DIPAB were added into 20 g PVDF/DMF solution (10 wt%), respectively. Samples were denoted as 0.02D, 0.04D, 0.06D, 0.08D and 0.10D according to the weight ratio of DIPAB to PVDF. The thickness of the films was in the range of 50–70 μm.
Results and discussion
X-ray diffraction
Fig. 1 shows the X-ray diffraction patterns of DIPAB, PVDF and DIPAB/PVDF composite films. All the PVDF composite films display a strong crystalline peak at 2θ = 20.5° assigned to β-phase and a very weak peak at 18.4° assigned to α-phase, suggesting the sample is β-phase dominated.12 With the incorporation of DIPAB, the intensity of α-phase characteristic peak is becoming weaker and almost indistinguishable, while the intensity of β-phase characteristic peak gets stronger. Under the same preparing condition, pure PVDF gives an obvious α-phase characteristic peak, although it is also β-phase dominated. This indicates that the addition of DIPAB facilitates the formation of β-phase PVDF. The diffraction peaks at 2θ = 12.5°, 17.0°, 22.4°, 25.2°, 27.6°, which are the characteristics of DIPAB, become more and more prominent with increase of DIPAB inclusion. It confirms the incorporation of DIPAB in PVDF matrix and a small shift (shown as red dash line in Fig. 1) in the 2θ values indicates the interaction of DIPAB with PVDF. Euler and his coauthors13 has reported that using a hydrated salt in the casting solvent could reproducibly form films with high β-phase content, and we found that DIPAB may be a more competitive candidate to prepare PVDF in high β-phase content.
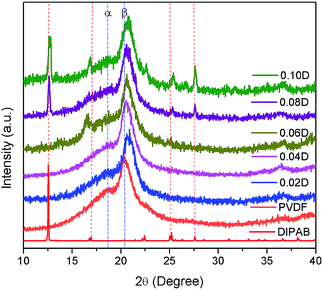 |
| Fig. 1 XRD patterns of DIPAB, PVDF and DIPAB/PVDF composite films. | |
FTIR measurement
In order to further confirm the crystalline structures of PVDF composite films with different concentrations of DIPAB, FTIR testing was also performed. On the basis of the reported data in literature,14 the vibration band at 840 cm−1 (CH2 rocking and CF2 asymmetric stretching vibration) should be assigned to β-phase, whereas the vibration bands at 763 cm−1 (CF2 bending and skeletal bending) should be assigned to α-phase. As shown in Fig. 2, the intensity of vibration band at 840 cm−1 representing β-crystal is very high, whereas no vibration band at 763 cm−1 assigned for α-phase is found, which indicates that the sample is almost pure β-phase. This is consistent with the result obtained from X-ray diffraction patterns. Due to the absence of vibration band at 763 cm−1, the β-phase content in crystalline PVDF matrix can not be calculated from FTIR spectra according to the previously reported method.15 It is normal that the pure PVDF is β-phase dominated as the solution casting temperature is below 80 °C, which favours the formation of β-phase.16
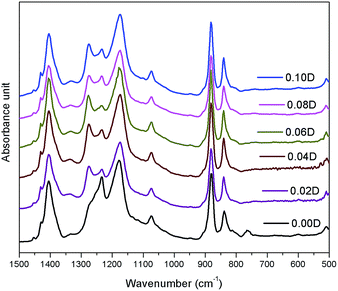 |
| Fig. 2 FTIR spectra of DIPAB/PVDF composite films. | |
Morphology characterization
The dispersion state of DIPAB in PVDF matrix was examined by SEM. As shown in Fig. 3(a–c), DIPAB appears as cubic microcrystal (particle diameter less then 0.5 μm) homogeneously dispersed within the polymer matrix and no obvious agglomeration is observed when DIPAB weight percentage is below 6%. A small quantity of microcrystal can be found on the surface in Fig. 3(d–f), when the weight percentage of DIPAB is up to 10%. After that, this phenomenon becomes more and more obvious. In other words, DIPAB can not be unlimitedly introduced into the PVDF matrix due to its good crystallinity and the absence of specific interfacial interaction between DIPAB and PVDF chains. So, only those composite films with low DIPAB contents (below 10 wt%) were investigated by us.
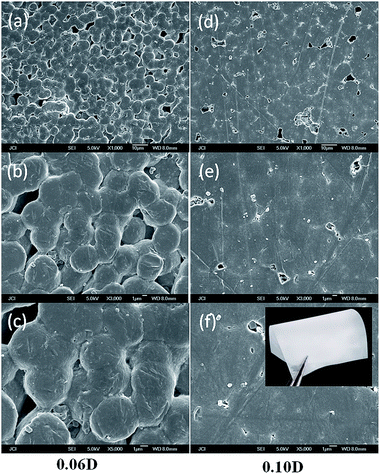 |
| Fig. 3 SEM images of DIPAB/PVDF composite films. (a–c) are the SEM images of 0.06D with a magnification of 1000, 3000 and 5000 times, respectively; (d–f) are the SEM images of 0.10D with a magnification of 1000, 3000 and 5000 times, respectively; the superior flexibility of DIPAB/PVDF composite (10 wt%) is demonstrated by a macroscopic image shown in the inset of (f). | |
DSC analysis
DSC test was adopted to investigate the effect of loading DIPAB on the crystallinity of PVDF matrix. Fig. 4 shows the heating and cooling curves of the samples 0.02D, 0.06D and 0.10D. The samples exhibit the same crystallization temperature at 133 °C, but an increase of melting temperatures for composite can be observed with increasing content of DIPAB, which may be related to the initial crystallinity of samples. According to the literature,17 the crystallinity can be calculated according to the following eqn (1): |
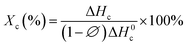 | (1) |
where ΔHc is the melting heat of samples,
is the weight percentage of DIPAB in the PVDF matrix, ΔH0c is the melting heat of 100% crystalline PVDF, which is 93.07 and 130.40 J g−1 for pure α- and β-phase PVDF, respectively. Based on the results obtained from XRD diffractions and FTIR spectra, 130.40 J g−1 is used to calculate the crystallinity for the samples. The calculated results reveal that the crystallinity (Xc) of 0.02D, 0.06D and 0.10D is 34.54%, 39.09% and 46.21%, respectively. With DIPAB content increasing, the crystallinity of PVDF composite greatly increased. It is manifest that the incorporation of DIPAB has the effect of increasing the crystallinity of PVDF matrix, which is probably related to the heterogeneous nuclei effect with DIPAB as nuclei centers for the crystallization of PVDF.
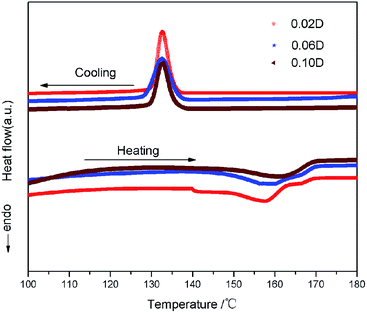 |
| Fig. 4 DSC curves of DIPAB/PVDF composite films. | |
Dielectric and ferroelectric properties
The frequency-dependent properties of dielectric constant and dielectric loss of PVDF composite films with the different volume proportion of DIPAB in the frequency range of 200 Hz to 1 MHz at the room temperature are shown in Fig. 5 and 6, respectively. As shown in Fig. 5, DIPAB/PVDF composite films with various DIPAB concentrations exhibit obviously enhanced dielectric constants. The dielectric constant is still up to 27.2 even at the high frequency of 106 Hz with 0.02D, which is about 3.4 times higher than that of the pure PVDF.18 The result indicates that the incorporation of DIPAB could significantly improve the dielectric constant of PVDF composites. The following reasons may account for this phenomenon. Firstly, a large quantity of microcapacitors can be formed because DIPAB is well dispersed in PVDF matrix according to SEM analysis, which is helpful to enhance the dielectric constant of composites. Secondly, charges can be accumulated at the interfaces between DIPAB and PVDF matrix, the interfacial polarization (namely Maxwell–Wagner–Sillars effect) could make a remarkable contribution to the enhancement of dielectric constant in the low frequency range. Thirdly, ionic polarization and orientation polarization can also lead to the improvement of dielectric constant of composites because DIPAB is an ionic ferroelectric. So the dielectric constants increase with increasing loading content of DIPAB due to the increasing interfacial polarization, ionic polarization and orientation polarization.
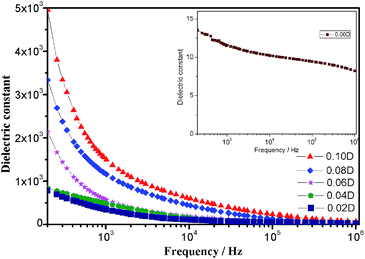 |
| Fig. 5 Frequency dependence of dielectric constants of DIPAB/PVDF composite films with frequency range between 200 and 106 Hz at room temperature; insert is for pure PVDF (0.00D). | |
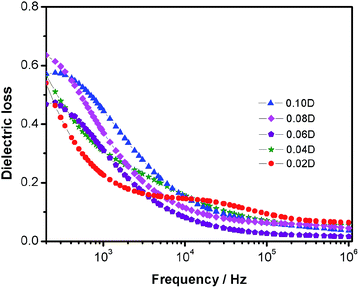 |
| Fig. 6 Frequency dependence of dielectric loss of DIPAB/PVDF composite films with frequency range between 200 and 106 Hz at room temperature. | |
In addition, it can be seen from Fig. 5 that the strong frequency-dependence is also an obvious characteristic of the dielectric constant of DIPAB/PVDF composite films. Below 1 × 104 Hz, the dielectric constants quickly dropped with increasing frequencies, and after that they decreased slowly. The dielectric relaxation should be related to various kinds of polarization. It is known that the dielectric constant of a material is related to the degree of polarization, which mainly includes electronic polarization, ionic polarization, orientation polarization and interfacial polarization. In the low frequency range (below 1 × 104 Hz), all these polarization can make positive contributions to improving dielectric constants, but interfacial polarization gradually can't keep up with the frequency change after the frequency of 1 × 104 Hz, so dielectric constants of the DIPAB/PVDF composite films are obviously frequency-dependent.
Fig. 6 is the dielectric loss of the DIPAB/PVDF composite films with varied DIPAB concentrations. The dielectric loss for all samples are relatively low (below 0.7) and gradually decrease with increasing frequencies, but the loading content of DIPAB has no obvious influence upon the dielectric loss.
The DC resistivity was measured to investigate the influence of loading DIPAB upon the electric property. As shown in Fig. 7, although adding DIPAB could lead to the decrease of DC resistivity to a certain extent, it is still in a very high level and could not bring about the artificial increase of dielectric constant. It has to be admitted that the dielectric loss is a little large at lower frequency, so the dielectric constant value might have some error for it is approximated as the magnitude of the complex permittivity (sin
θ ≈ θ). But when the frequency is higher than 1 × 104 Hz, the dielectric loss is basically lower than 0.1, this error can be neglected. This phenomenon that PVDF films exhibit very high dielectric constant at lower frequency has also been found in some cases such as PVDF composite films modified with rare earth salts,19 copper nanowire/PVDF,20 PVDF–MWCNT composites,21 NaTNO/PVDF nanocomposites22 and so on.
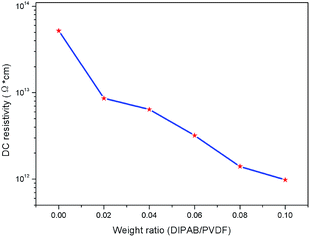 |
| Fig. 7 DC resistivity of DIPAB/PVDF composite film. | |
Temperature dependence of dielectric constants and dielectric loss for the sample 0.10D are shown in Fig. 8. It can be seen that an obvious dielectric anomaly appears at about 140 °C, which should be related to the ferroelectric phase transition of DIPAB.10 The dielectric loss also begins to sharply increase after 140 °C. The dielectric temperature dependence properties further confirmed that DIPAB has been incorporated into PVDF matrix.
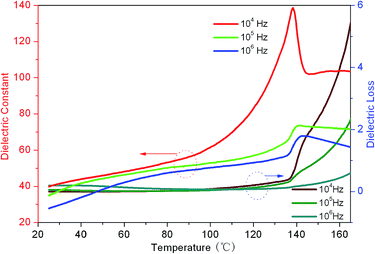 |
| Fig. 8 Temperature dependence of dielectric constants and dielectric loss of DIPAB/PVDF composite film 0.10D. | |
The ferroelectric behaviours of PVDF composite films doping with different content DIPAB were examined given that both PVDF and DIPAB are ferroelectric materials. The P–E hysteresis loops were shown in Fig. 9. The well-shaped P–E loops obviously indicate the ferroelectric behaviour, and give a remnant polarization (Pr) range from 54 to 110 mC m−2 and Ec of range from 133 to 145 MV m−1 at the electric filed of ca. 200 MV m−1. The value of Pr is very close to that of Ps. The Pr or Ps values for composite films are obviously higher than those of pure PVDF but lower than those of pure DIPAB, and gradually increase with increasing DIPAB content. The results indicated that doping with DIPAB could also be a useful way to improve the ferroelectric properties of PVDF films.
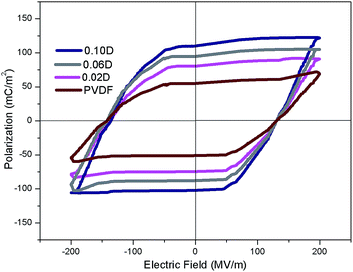 |
| Fig. 9 P–E hysteresis loops of DIPAB/PVDF composite films at the same electric field. | |
Conclusions
In summary, a ferroelectric compound DIPAB was successfully dispersed into PVDF matrix to form a new type of composite films (DIPAB/PVDF). The introduction of DIPAB contributes to form almost pure β-phase PVDF composite films and increase the crystallinity of PVDF polymer. Importantly, DIPAB/PVDF composite films exhibit very high dielectric constants and relatively low dielectric loss. Incorporating DIPAB into PVDF is a useful way to improve the dielectric and ferroelectric property of PVDF composite films.
Acknowledgements
This work was supported by National Natural Science Foundation of China (21361012 and 21461012), Department of Science and Technology of Jiangxi Province (20133ACG70007, and 20144BCB23038), Education Department of Jiangxi Province (KJLD12034).
Notes and references
- M. Wang, J. H. Shi, K. P. Pramoda and S. H. Goh, Nanotechnology, 2007, 18, 235701 CrossRef CAS; Z. M. Dang, J. K. Yuan, S. H. Yao and R. J. Liao, Adv. Mater., 2013, 25, 6334–6365 CrossRef; B. Chu, X. Zhou, K. Ren, B. Neese, M. Lin, Q. Wang, F. Bauer and Q. M. Zhang, Science, 2006, 313, 334–336 CrossRef PubMed; Y. N. Hao, X. H. Wang, S. O'Brien, J. Lombardi and L. T. Li, J. Mater. Chem. C, 2015, 3, 9740–9747 RSC.
- L. L. Sun, B. Li, Z. G. Zhang and W. H. Zhong, Eur. Polym. J., 2010, 46, 2112–2119 CrossRef CAS; E. Kar, N. Bose, S. Das, N. Mukherjee and S. Mukherjee, Phys. Chem. Chem. Phys., 2015, 17, 22784–22798 RSC.
- H. J. Ye, L. Yang, W. Z. Shao, S. B. Sun and L. Zhen, RSC Adv., 2013, 3, 23730–23736 RSC; S. Yu, W. Zheng, W. Yu, Y. Zhang, Q. Jiang and Z. Zhao, Macromolecules, 2009, 42, 8870–8874 CrossRef CAS.
- S. L. Hsu, F. J. Lu, D. A. Waldman and M. Muthukumar, Macromolecules, 1985, 18, 2583–2587 CrossRef CAS; P. Sajkiewicz, A. Wasiak and Z. Golclowski, Eur. Polym. J., 1999, 35, 423–429 CrossRef.
- Z. M. Dang, J. K. Yuan, S. H. Yao and R. J. Liao, Adv. Mater., 2013, 25, 6334–6365 CrossRef CAS PubMed.
- W. Zhou, Q. Chen, X. Sui, L. Dong and Z. Wang, Composites, Part A, 2015, 71, 184–191 CrossRef CAS; L. Y. Xie, X. Y. Huang, Y. H. Huang, K. Yang and P. K. Jiang, J. Phys. Chem. C, 2013, 117, 22525–22537 Search PubMed.
- D. R. Wang, T. Zhou, J.-W. Zha, J. Zhao, C.-Y. Shi and Z.-M. Dang, J. Mater. Chem. A, 2013, 1, 6162–6168 Search PubMed; X. Kuang, Z. Liu and H. Zhu, J. Appl. Polym. Sci., 2013, 129, 3411–3416 CrossRef CAS; J. Fu, Y. D. Hou, Q. Y. Wei, M. P. Zheng, M. K. Zhu and H. Yan, J. Appl. Phys., 2015, 118(23), 235502 CrossRef; R. A. C. Amoresi, A. A. Felix, E. R. Botero, N. L. C. Domingues, E. A. Falcao, M. A. Zaghete and A. W. Rinaldi, Ceram. Int., 2015, 41, 14733–14739 CrossRef; K. Prabakaran, A. K. Palai, S. N. Mohanty and K. Sanjay, RSC Adv., 2015, 5(82), 66563–66574 RSC; A. Thakre, H. Borkar, B. P. Singh and A. Kumar, RSC Adv., 2015, 5(71), 57406–57413 RSC.
- T. Zhou, J. W. Zha, R. Y. Cui, B. H. Fan, J. K. Yuan and Z. M. Dang, ACS Appl. Mater. Interfaces, 2011, 3, 2184–2188 Search PubMed; W. M. Xia, Z. Xu, F. Wen and Z. C. Zhang, Ceram. Int., 2012, 38, 1071–1075 CrossRef CAS; Z. D. Liu, Y. Feng and W. L. Li, RSC Adv., 2015, 5, 29017–29021 RSC; B. C. Luo, X. H. Wang, Y. P. Wang and L. T. Li, J. Mater. Chem. A, 2014, 2, 510–519 Search PubMed; J. Anjana, K. J. Prashanth, K. S. Asheesh, J. Arpit and P. N. Rashmi, Polym. Eng. Sci., 2015, 55, 1589–1616 Search PubMed; A. Srivastava, K. K. Jana, P. Maiti, D. Kumar and O. Parkash, Mater. Res. Bull., 2015, 70, 735–742 CrossRef; N. Kamezawa, D. Nagao, H. Ishii and M. Konno, Eur. Polym. J., 2015, 66, 528–532 CrossRef; S. Adireddy, V. S. Puli, T. J. Lou, R. Elupula, S. C. Sklare, B. C. Riggs and D. B. Chrisey, J. Sol-Gel Sci. Technol., 2015, 73(3), 641–646 CrossRef.
- N. Levi, R. Czerw, S. Y. Xing, P. Lyer and D. L. Carroll, Nano Lett., 2004, 4(7), 1267–1271 CrossRef CAS.
- D.-W. Fu, H.-L. Cai, Y. Liu, Q. Ye, W. Zhang, Y. Zhang, X.-Y. Chen, G. Giovannetti, M. Capone, J. Li and R.-G. Xiong, Science, 2013, 339, 425–428 CrossRef CAS PubMed.
- K. Gao, C. Liu, Z. Cui, J. Zhu, H. Cai and X. Wu, CrystEngComm, 2015, 17, 2429–2432 RSC; J. S. Zhu, K. G. Gao, S. Y. Xiao, X. B. Qiu, H.-L. Cai and X. S. Wu, Phys. Chem. Chem. Phys., 2015, 17, 4029–4033 RSC.
- W. Ma, J. Zhang and X. Wang, Appl. Surf. Sci., 2008, 254, 2947–2954 CrossRef CAS; J. R. Gregorio, J. Appl. Polym. Sci., 2006, 100(4), 3272–3279 CrossRef; T. Prabhakaran and J. Hemalatha, Mater. Chem. Phys., 2013, 137, 781–787 CrossRef.
- M. Benz, W. B. Euler and O. J. Gregory, Macromolecules, 2002, 35, 2682–2688 CrossRef CAS.
- Y. Bormashenko, R. Pogreb, O. Stanevsky and E. Bormashenko, Polym. Test., 2004, 23, 791–796 CrossRef CAS; A. Salimi and A. A. Yousefi, Polym. Test., 2003, 22, 699–704 CrossRef.
- L. Yang, J. Qiu, H. Ji, K. Zhu and J. Wang, Composites, Part A, 2014, 65, 125–134 CrossRef CAS.
- P. Martins, A. C. Lopes and S. Lanceros-Mendez, Prog. Polym. Sci., 2014, 39(4), 683–706 CrossRef CAS; L. Yang, J. H. Qiu, H. L. Ji, K. J. Zhu and J. Wang, J. Mater. Sci.: Mater. Electron., 2014, 25(5), 2126–2137 CrossRef.
- P. Costa, J. Silva, V. Sencadas, C. M. Costa, F. W. J. van Hattum, J. G. Rocha and S. Lanceros-Mendez, Carbon, 2009, 47, 2590–2599 CrossRef CAS.
- S. Liu, S. Xue, W. Zhang, J. Zhai and G. Chen, J. Mater. Chem. A, 2014, 2, 10840–10846 Search PubMed.
- P. Thakur, A. Kool, B. Bagchi, N. A. Hoque, S. Das and P. Nandy, RSC Adv., 2015, 5, 28487–28496 RSC.
- A. B. da Silva, M. Arjmand, U. Sundararaj and R. E. S. Bretas, Polymer, 2014, 55, 226–234 CrossRef.
- R. Ram, M. Rahaman and D. Khastgir, Composites, Part A, 2015, 69, 30–39 CrossRef CAS.
- D. Bhadra, S. C. Sarkar and B. K. Chaudhuri, RSC Adv., 2015, 5(46), 36924–36932 RSC.
|
This journal is © The Royal Society of Chemistry 2016 |
Click here to see how this site uses Cookies. View our privacy policy here.