DOI:
10.1039/C5RA24908B
(Paper)
RSC Adv., 2016,
6, 18483-18489
Controlled growth of MoS2 nanopetals and their hydrogen evolution performance†
Received
24th November 2015
, Accepted 26th January 2016
First published on 28th January 2016
Abstract
Edge-oriented MoS2 nanopetals complexed with basal-oriented MoS2 thin films have been mildly grown through a simple atmospheric pressure chemical vapor deposition (APCVD) process with the reaction of MoO3 and S. Dense nanopetals with hexagonal structures exposed numerous chemically reactive edge sites. The roles of growth temperature, time and S/MoO3 mass ratio have been carefully investigated to tune the morphology and density of the as-grown products. Importantly, the carbon nanotube (CNT) films were used as substrates for growing MoS2 nanopetals. The MoS2/CNT composites, used directly as working electrodes, showed remarkable and stable electrocatalytic activity in the hydrogen evolution reaction (HER), as manifested with a low onset overpotential of ∼100 mV and a small Tafel slope of 49.5 mV per decade. The development of the MoS2/CNT electrode provides a promising way to fabricate other multifunctional electrodes.
1 Introduction
In recent years, two-dimensional (2D) layered transition-metal dichalcogenides (TMDCs), especially MoS2, have become the focus of research because of their inherent structure, presenting unique properties different from their three-dimensional (3D) bulk counterparts.1–3 Various synthetic methods have been gradually developed to synthesize MoS2 of different morphologies.4–9 Chemical vapor deposition (CVD) is considered to be a simple and efficient method for synthesizing MoS2 via the sulphurization or decomposition of pre-deposited metal-based precursors, or the one-step reaction and deposition of gaseous metal and chalcogen feedstocks.10–16 Conventional researches have focused on horizontal MoS2 atomic layers, which are promising for optoelectronics due to their indirect-to-direct bandgap transition17–20 and large on/off current ratios (>1010).20 Recently vertically aligned MoS2 layers have also attracted great attentions because of their exposed chemically reactive edge sites beneficial for electrochemical catalysis.21,22 Theoretical and experimental studies have indicated that exposed edges of MoS2 nanostructure are the active sites for HER.23–28 Exposing more edges of MoS2 by controlling its nanostructure allows the formation of a more active HER electrocatalyst. Such observation implies that dense edge-oriented MoS2 nanopetals would be advantageous to design as an efficient HER catalyst. At the same time, small radii of curvature makes its highly promising for electron field emitter applications.29 While there are less studies on growing MoS2 nanopetals by CVD methods. 3D MoS2 and WS2 nanoflowers, composed of tens to hundreds of self-assembled nanopetals, have been selectively prepared through APCVD process at 650 °C with the reaction of chlorides and sulfur.30 The mechanism of forming slightly curved nanopetals is not clear.
In this work, we described a facile way to synthesize edge-oriented MoS2 nanopetals complexed with basal-oriented MoS2 thin films via APCVD method at 650–950 °C with the reaction of MoO3 and S. The mechanism of forming slightly curved nanopetals had been preliminary studied. The roles of growth temperature, time, and S/MoO3 mass ratio had been carefully investigated to tune the morphology and density of the as-grown products. In addition, MoS2 nanopetals were directly grown on the working electrodes, the CNT films, as comparable and stable electrocatalytic catalysts for HER. The MoS2/CNT film electrodes were manifested with a small onset overpotential of ∼100 mV and a low Tafel slope of 49.5 mV per decade.
2 Experimental section
2.1 Materials
Molybdenum trioxide (MoO3, 99.9% metals basis) and sulphur powder (99.5%, sublimed grade) were purchased from Aladdin Industrial Corporation. The CNT films were purchased from Suzhou Creztive Nano-carbon Co., Ltd. These chemicals were used without further purification.
2.2 Preparation of MoS2 nanopetals
MoS2 nanopetals were prepared via APCVD method. MoO3 and sulphur powder were used as precursors. Growth substrates were loaded into a 1-inch CVD furnace (Lindberg/Blue M) and placed face-down above a ceramic boat containing of MoO3 at the center of the furnace. Sulphur powder, placed near the inlet of the furnace with about 25 cm distance from the MoO3 powder, was mildly sublimated at 120 °C with independently temperature-controllable heating belts, and carried by Ar gas (500 standard cubic centimeter per minute (sccm)) to the down-stream growth zone. The gas flow of Ar was kept at 500 sccm during all the process. After purging the system with Ar gas for 5 min, the CVD system was heated to 120 °C within 3 min, held for 60 min to make the system full of sulphur vapor, stably and continuously. Then the furnace was heated to 800 °C within 30 min, held for 60 min, and then cooled to 500 °C naturally, opened furnace for rapid cooling. To investigate the effect of growth parameters, the initial mass ratio of S/MoO3 was controlled to be less than 10
:
1, 10
:
1, 30
:
1, 50
:
1 and 70
:
1, respectively. The growth temperature was set to be 650 °C, 700 °C, 800 °C, 900 °C and 950 °C, respectively, for 5 min to 120 min, when the initial mass ratio of S/MoO3 was controlled to be 30
:
1.
2.3 Characterizations
Raman spectra were recorded using a LabRAM HR Raman Spectrometer (LabRAM HR, Horiba-JY) fitted with a 532.2 nm laser. Field Emission Scanning Electron Microscope (FESEM, Hitachi S-4800, 5 kV), Atomic Force Microscopy (AFM, Dimension 3100), X-ray Energy Dispersive Spectrometer (EDS, Apollo 40SDD) and Transmission Electron Microscope (TEM, Tecnai G2 F20 S-Twin) were used to investigate the morphology and nanostructures of the samples. High-resolution transmission electron microscope (HRTEM) was performed at an acceleration voltage of 200 kV. The crystal structure was characterized by X-ray diffraction (XRD, D8 Advance, Bruker AXS). Electrochemical tests were performed with a model CH Instrument 660C electrochemical workstation (Shanghai Chenhua Equipment).
2.4 Electrochemical measurements
A three-electrode cell was set up, consisting of our MoS2/CNT films directly used as the working electrode, Pt and silver chloride electrode (Ag/AgCl (saturated KCl)) as the counter electrode and reference electrode, respectively. In 0.5 M H2SO4 solution, potentials were referenced to a reversible hydrogen electrode (RHE) by adding a value of 0.197 V.31 Linear sweep voltammetry (LSV) was conducted at a scan rate of 5 mV s−1 in 0.5 M H2SO4 (deaerated by N2). During the durability test, scan rate of cyclic voltammetry (CV) was 100 mV s−1 in 0.5 M H2SO4.
3 Results and discussions
In the APCVD process of growing MoS2, we used MoO3 and sulphur powder as precursors. MoO3 was reduced by sulphur vapor into the target product. In order to achieve MoS2 nanopetals, we believe that it is important to control the concentration of MoS2 by adjusting the growth parameters. When the growth temperature is as low as 650 °C, the resulting nucleation density is less, leading to the growth of 2D horizontal MoS2 triangular flakes for 30 min (Fig. 1a).9,10 By increasing the growth time to 60 min while keeping other growth parameters identical, the coverage of MoS2 increases, and triangular MoS2 flakes become denser and smaller (Fig. 1b).12,13 Further increasing the growth time to 90 min, the concentration of MoS2 would increase so much that the growth in horizontal direction cannot keep up with its mass transport, starting to germinate in 3D direction. Some novel structures like nanopetals appear on horizontal MoS2 flakes (Fig. 1c). Further extension of the growth time to 120 min, the nanopetals become bigger and their amount increases. Obviously, they are slightly curved and exposed sharp edges. But the density is still rare (Fig. 1d). As shown in Fig. 1d and S1,† obvious features of spiral growth coincide well with the result of AFM phase diagram (Fig. 1h), suggesting that there exists screw dislocations in films.32 Extension of the growth time, continuous mass transport sustains unrestricted spiral growth, leading to the generation of nanopetals exposed active edges with small radii of curvature.
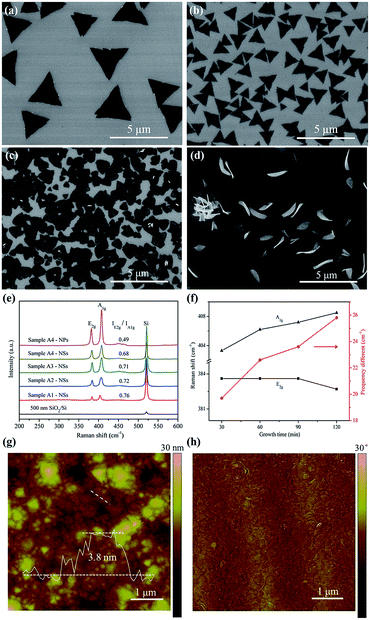 |
| Fig. 1 SEM images of MoS2 grown on 500 nm SiO2/Si with the S/MoO3 mass ratio of 30 : 1, at 650 °C for different growth time. (a–d) SEM images of sample A1, A2, A3 and A4 grown for 30 min, 60 min, 90 min and 120 min, respectively. (e) Raman spectra of MoS2 nanosheets (NSs) and nanopetals (NPs) shown in (a–d). (f) Corresponding Raman shifts of E2g and A1g peaks and their gap differences of MoS2 nanosheets. AFM height map (g) and phase diagram (h) of MoS2 thin film shown in (d). | |
Raman measurements (Fig. 1e and f) show the frequency difference (Δ) of sample A1 is 19.7 cm−1 between the two typical vibrational modes of A1g and E2g, suggestive of the uniform monolayer nature. The Δ of sample A2 and A3 is 22.6 and 23.6 cm−1, respectively, corresponding to the nature of few-layer MoS2. While the Δ of sample A4 is 25.5 cm−1, implicating of the property of multilayer MoS2. The thickness of MoS2 film is about 3.8 nm observed from the AFM height map in Fig. 1g. The relative E2g/A1g ratio calculated from the Raman results can be used to distinguish between basal- and edge-oriented MoS2.33,34 As shown in Fig. 1e, the E2g/A1g ratios of horizontal MoS2 layers observed from sample A1, A2, A3 and A4 are 0.76, 0.72, 0.71 and 0.68, respectively, indicating that deposited horizontal MoS2 layers are basal-oriented, consistent with the XRD results in Fig. S2.† All peaks in the XRD pattern can be indexed as the pure hexagonal MoS2 phase with lattice constants: a = 3.161 Å and c = 12.29 Å (PDF No. 37-1942). A strong sharp (002) diffraction peak is observed at 2θ = 14.5°, indicating that horizontal MoS2 films expose the basal plane. Higher order peaks (004), (006) and (008) of MoS2 are observed, confirming that MoS2 thin films are highly basal-oriented.35 No extra peaks are observed. The sharp diffraction peaks imply good crystallinity of the obtained MoS2 products. The E2g/A1g ratio of MoS2 nanopetals observed from sample A4 is 0.49 (Fig. 1e), different from that of horizontal MoS2 films, which is attributed to the existence of vertically aligned MoS2 layers in the nanopetals.36 With the increase of the growth time, mass transport in both horizontal and vertical direction is enhanced, resulting that as-grown products have been changed from monolayer triangular flakes to continuous multilayer films and curved nanopetals.
In order to achieve more nanopetals, the growth temperature was raised to 700 °C and the growth time was set to be 60 min and 120 min (refer to sample B1 and B2, respectively). As shown in Fig. 2a–c, the density of nanopetals is substantially increased. Surprisingly, some nanopetals are assembled into nanoflowers, which presents a 3D morphology with an open structure providing a huge specific surface. The proportion of nanopetals, distributed on MoS2 thin films individually and independently, is much larger than that of nanoflowers. The longer growth time (120 min) results in higher density of MoS2 nanopetals (Fig. 2a and c). The characteristic Raman peaks corresponding to the E2g and A1g vibration modes can be observed as two prominent peaks at about 380 and 405 cm−1 in Fig. 2d, respectively. The Δ is 25 cm−1 acquired from sample B1 and sample B2, consistent with that of multilayer MoS2. The E2g/A1g ratio of sample B2 and B1 is 0.46 and 0.44, respectively, indicating that the as-grown nanopetals and nanoflowers are edge-oriented.34 Additionally, the overall Raman intensity of sample B2 is threefold to fivefold of that of sample A4, suggesting sample B2 has better quality.35 TEM images of sample B2 demonstrate that there are strong interconnections between nanopetals and nanoflowers. Ripples and corrugations are considerably well-defined during the ultrasonic treatment of 1 h, as displayed in Fig. S3a† and Fig. 2e, revealing good structural stability. Fig. S3b† depicts a selected-area electron diffraction (SAED) pattern taken from an individual nanoflower. (103), (105), (108), (206) and (00 14) crystal planes can be well-indexed to hexagonal MoS2 (PDF No. 37-1942). EDS analysis (Fig. 2f) demonstrates that the nanoflowers are composed of Mo and S. The S/Mo ratios is 2.19, indicated that there are abundant unsaturated ligands S-dangling on the edges of the MoS2 catalyst.37 Due to layered structure of MoS2, the dangling bonds can incorporate atoms directly from the gaseous precursors, which favors lateral growth of the nanopetals. Representative HRTEM micrographs were shown in Fig. 2g. The (002) basal plane fringes with a lattice spacing of 0.615 nm can be clearly seen. While the edge is (103) plane with a lattice spacing of 0.228 nm. The number of layers gradually decreases from central core towards edge and is 4 to 8 near the edge of 2–5 nm. Experimental and computational studies have indicated that the exposed edges are the active sites for HER, while the basal plane of MoS2 is catalytically inert.38–40 Therefore, the as-grown edge-oriented samples would have promising HER performance. HRTEM images taken along the [001] projection were shown in Fig. 2h, in which the spatial periodicity of the Moiré fringes with 1.3 nm can be discerned. According to the FFT pattern, the large-angle rotation about 9–11° existing between the (100) edge plane layers with an interlayer spacing of 0.274 nm was calculated, which is caused by weak interlayer (van der Waals) interactions in MoS2. Because of the screw dislocation, the difference in layer curvature is also a reason for the occurrence of interlayer rotation.
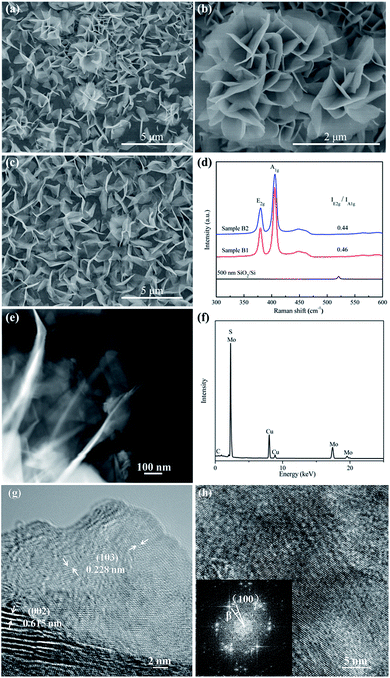 |
| Fig. 2 SEM images of MoS2 nanopetals and nanoflowers synthesized at 700 °C for different growth time. (a and b) SEM images of sample B1 grown for 60 min. (c) SEM image of sample B2 grown for 120 min. (d) Raman spectra of MoS2 nanopetals and nanoflowers shown in (a–c). (e) STEM image of a MoS2 nanoflower. (f) EDS analysis of MoS2 nanoflower shown in (e). (g and h) HRTEM images of MoS2 nanoflower. Inset: corresponding Fast Fourier Transform (FFT) pattern. | |
Further increasing the growth temperature to 800 °C, we set the growth time to be 30 min and 60 min (refer to sample C1 and C2, respectively). At relative longer growth time (60 min), as shown in Fig. 3b, the density of nanopetals is highly increased. Dense nanopetals are close-packed and exposed numerous edge sites (Fig. 3a and b). Cross-section SEM image (Fig. S1c†) of sample C2 clearly shows the features of MoS2 nanopetals through the spiral growth. From horizontal to vertical growth, synthesized MoS2 nanopetals exposed active edges with small radii of curvature. The E2g/A1g ratio of sample C1 and C2 is 0.43 and 0.41 (Fig. 3c), respectively, consistent with that of edge-oriented MoS2 nanopetals. Sometimes some particles or sheets which arise from the incomplete sulfuration can be observed either at the roots or among the nanopetals (Fig. S4a†). Influenced by dense S atmosphere, the products still remain the nanopetal nanostructure with similar size but would be integrated into the large layer. The edges are hided (Fig. S4b and c†). All of them are adverse to HER.
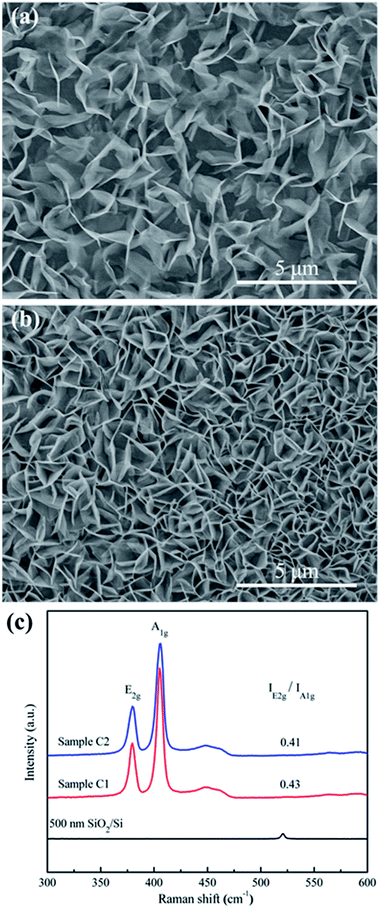 |
| Fig. 3 SEM images of MoS2 nanopetals synthesized at 800 °C for different growth time. (a) SEM image of sample C1 grown for 30 min. (b) SEM image of sample C2 grown for 60 min. (c) Raman spectra of MoS2 shown in (a and b). | |
At higher temperature of 900 °C and 950 °C, the growth time was set to be 5 min (refer to sample D and E, respectively). As shown in Fig. 4a and b, the density of the products is so intense that nanoflowers are spreaded over the crowded nanopetals. The sizes of the products become larger, ranging from hundreds of nanometers to a few micrometres in width and several nanometers to hundreds of nanometers in thickness, which are not conducive for the HER.41 Cross-section SEM images of sample D and E (Fig. S5†) can clearly defined the boundary between vertical MoS2 nanopetals, horizontal MoS2 films and 500 nm SiO2 layer. Therefore, we calculated the ratio of vertically aligned MoS2 nanopetals/total MoS2 (F). With the increase of the growth temperature from 900 to 950 °C, the value of F decreases from 82.1% to 79.5%. At the same time, the E2g/A1g ratio of sample D and E decreases from 0.38 to 0.36 (Fig. 4c), indicating the increase of the size.22 In conclusion, the growth temperature and time dependent studies revealed that the ideal conditions for growing thinner, high-density, vertically-oriented MoS2 nanopetals should be at 800 °C for 60 min.
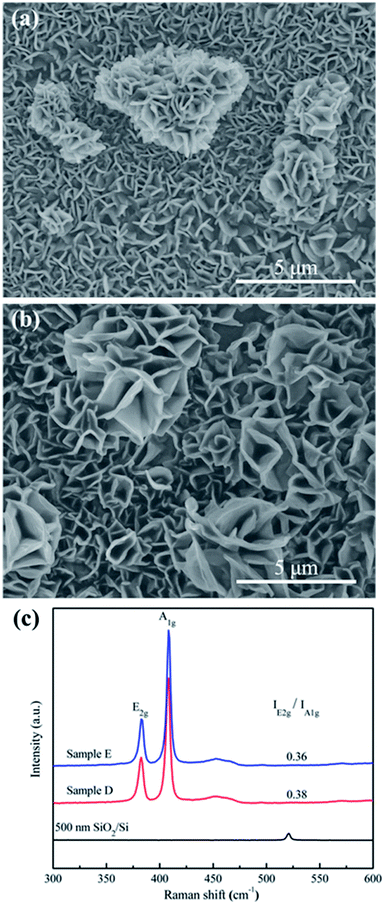 |
| Fig. 4 SEM images of MoS2 nanopetals and nanoflowers synthesized at different growth temperature for 5 min. (a) SEM image of sample D grown at 900 °C. (b) SEM image of sample E grown at 950 °C. (c) Raman spectra of MoS2 shown in (a and b). | |
Furthermore, the S/MoO3 mass ratio was studied to optimize the preparation condition. Enough sulfur must be placed in the upstream side of the tube. Otherwise MoO3 cannot be sulfurized completely, and a intermediate product of MoO2 is detected. When the S/MoO3 mass ratio is less than 10
:
1, hexagonal nanosheets with straight edges can be observed (Fig. 5a). As shown in Fig. 5b and S6,† except the main peaks indicating the formation of MoS2, peaks of MoO2 are simultaneously observed in Raman and XRD results, proposing a stepwise reduction and sulfurization process determined by the diffusion of sulfur (see eqn (1) and (2)). To realize the full sulfuration, we increased the mass of sulphur powder and studied the role of S/MoO3 mass ratio on the morphology of as-grown MoS2 nanostructures. As the S/MoO3 mass ratio increased to 10
:
1, dense MoS2 nanopetals are grown on the substrates shown in Fig. 5c. Steadily increasing the MoO3/S mass ratio from 10
:
1 to 70
:
1, high supersaturation of reactive precursors facilitates the formation of dense nuclei, resulting that the thickness of MoS2 nanostructures was increased from nanometer to micrometer (Fig. 5c–f). To make sure the reaction absolutely completed and the final products had appropriate sizes, we set S/MoO3 mass ratio to be 30
:
1. From the above results, it is obvious that growth parameters of the growth temperature, time and S/MoO3 mass ratio play very important roles in controlling growth of edge-oriented MoS2 nanopetals.
|
2MoO3 + S — 2MoO2 + SO2
| (1) |
|
MoO2 + 3S — MoS2 + SO2
| (2) |
 |
| Fig. 5 SEM images of MoS2 nanostructures synthesized with different S/MoO3 mass ratio. (a) SEM image of products synthesised with S/MoO3 mass ratio less than 10 : 1. (b) Raman analysis of products shown in (a). (c–f) SEM images of MoS2 nanostructures synthesized with different S/MoO3 mass ratio: 10 : 1 (c), 30 : 1 (d), 50 : 1 (e) and 70 : 1 (f), respectively. | |
High density of MoS2 nanopetals exposed numerous thin edges throughout the large areas make them as perfect candidates for HRE. However, the catalytic performance of MoS2 is greatly compromised by its poor conductivity and high electrical resistance which hinders charge transfer kinetics.42,43 Therefore, the key challenge to apply MoS2 in HER lies in the compensation for the conductivity while maintaining its nanostructures. The CNT films possess many outstanding properties, such as good conductivity, chemical durability, large surface area and so on. The combination of the CNT films with MoS2 appears to be a promising way to realize further application in HER by increasing the conductivity. A freestanding electrode would be more convenient and preferable. Therefore, we chose the CNT films as conductive substrate to grow MoS2 nanopetals at 800 °C for 1 h. Dense products are observed on the CNT films (Fig. S7a and b†). Raman analysis (Fig. S7c†) demonstrates that products on the CNT films are edge-oriented MoS2 nanopetals. There exists a strong connection between the interface of MoS2 and CNTs, through which efficient electron transfer may occur (Fig. S8†). The electrocatalytic hydrogen evolution activities of the MoS2/CNT films, the CNT films and Pt were investigated and compared based on the polarization and Tafel plots. The linear regions of the Tafel plots (Fig. 6c) fit well to the Tafel equation η = b
log
j + a, where j is the current density and b is the Tafel slope. As shown in Fig. 6a and b, the MoS2/CNT film electrodes exhibit a small onset overpotential at about 100 mV. The low onset potential means that there are abundant active edge sites for reaction.37,44 The Tafel slope of the MoS2/CNT film was measured to be 49.5 mV per decade, much lower than that of CNT films (195.7 mV per decade). As it is known, Tafel slope is an inherent property of the catalyst. Three possible principle steps have been proposed for the HER mechanism in acidic medium, which are illustrated as follows:45
|
H3O+ + e− — Hads + H2O
| (3) |
|
Hads + H3O+ + e− — H2 + H2O
| (4) |
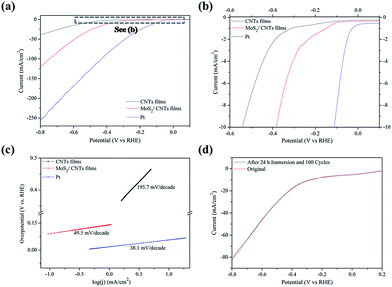 |
| Fig. 6 HER characteristics of as-grown MoS2 nanostructures on the CNT films synthesized at 800 °C for 1 h. (a and b) Polarization curves of the MoS2/CNT films, the CNT films and Pt. (c) Corresponding Tafel plots. (d) Durability test of the MoS2/CNT films electrode. | |
The first is a primary discharge step (Volmer reaction, 120 mV per decade, eqn (3)): a proton combines with an electron to form an adsorbed H atom; which is followed by either the electrochemical desorption step (Heyrovsky reaction, 40 mV per decade, eqn (4)): adsorbed H atom reacts with a hydrated proton from the electrolyte while receiving an electron; or the recombination step (Tafel reaction, 40 mV per decade, eqn (5)): adsorbed H atom combines directly with another adsorbed H atom. For a complete HER, the combinations of Volmer–Heyrovsky or Volmer–Tafel mechanism should be involved to produce molecular hydrogen. The Tafel slope of our samples is 49.5 mV per decade (Fig. 6c), suggesting that the rate-determining step of the HER mechanism is the Volmer–Heyrovsky reaction. These result are well correlated with previous reports that the range of the Tafel slope is from 40–120 mV per decade.46,47 Moreover, the MoS2/CNT film electrodes exhibit good stability with negligible current loss (∼2.3%) after 24 h immersion and 100 cycles of the durability test (Fig. 6d). That can be attributed to the intimate interconnection between MoS2 and CNTs by chemical and electromic coupling.42 The good durability and electrochemical performance of the freestanding and flexible MoS2/CNT film electrodes show advantages of that as one kind of HER electrode.
4 Conclusions
In summary, we described a facile way to synthesize novel MoS2 nanostructures that consist of both basal-oriented thin films and edge-oriented nanopetals via APCVD method. Slightly curved nanopetals were generated through the spiral growth mechanism. The roles of growth temperature, time and S/MoO3 mass ratio have been carefully studied to tune the morphology and density of MoS2. In the concentrated S atmosphere, high supersaturation of reactive precursors facilitates the formation of dense nuclei. Extension of the growth time, continuous deposition of precursors in horizontal direction cannot keep up with its mass transport, leading to the formation of vertically oriented MoS2 nanopetals. Further increasing the growth temperature, the amount of precursors dramatically increased, resulting in a increased growth rate of MoS2. The size and density of vertically aligned MoS2 nanopetals and horizontal films increased. The high surface curvature of MoS2 nanopetals exposes a large fraction of edge sites along with its high surface area, which leads to excellent activity for HER. Furthermore, the freestanding, flexible and durable MoS2/CNT films were prepared as a direct HER electrode, showing remarkable electrocatalytic performance and good stability. Importantly, the development of the MoS2/CNT film electrode provides a promising way to fabricate other multifunctional electrodes.
Conflict of interest
The authors declare no competing financial interest.
Acknowledgements
This work was supported by the National Natural Science Foundation of China (No. 51372265 and No. 51522211) and the Science and Technology Project of Suzhou, China (No. SZS201508).
References
- A. Splendiani, L. Sun, Y. Zhang, T. Li, J. Kim, C. Y. Chim, G. Galli and F. Wang, Nano Lett., 2010, 10, 1271 CrossRef CAS PubMed.
- T. Cao, G. Wang, W. Han, H. Ye, C. Zhu, J. Shi, Q. Niu, P. Tan, E. Wang, B. Liu and J. Feng, Nat. Commun., 2012, 3, 177 Search PubMed.
- S. Z. Butler, S. M. Hollen, L. Cao, Y. Cui, J. A. Gupta, H. R. Gutiérrez, T. F. Heinz, S. S. Hong, J. Huang, A. F. Ismach, E. Johnston-Halperin, M. Kuno, V. V. Plashnitsa, R. D. Robinson, R. S. Ruoff, S. Salahuddin, J. Shan, L. Shi, M. G. Spencer, M. Terrones, W. Windl and J. E. Goldberger, ACS Nano, 2013, 7, 2898 CrossRef CAS PubMed.
- Z. Zeng, Z. Yin, X. Huang, H. Li, Q. He, G. Lu, F. Boey and H. Zhang, Angew. Chem., Int. Ed., 2011, 50, 11093 CrossRef CAS PubMed.
- K. K. Liu, W. Zhang, Y. H. Lee, Y. C. Lin, M. T. Chang, C. Y. Su, C. S. Chang, H. Li, Y. Shi, H. Zhang, C. S. Lai and L. J. Li, Nano Lett., 2012, 12, 1538 CrossRef CAS PubMed.
- H. Nam, S. Wi, H. Rokni, M. Chen, G. Priessnitz, W. Lu and X. Liang, ACS Nano, 2013, 7, 5870 CrossRef CAS PubMed.
- Y. Yao, L. Tolentino, Z. Yang, X. Song, W. Zhang, Y. Chen and C. P. Wong, Adv. Funct. Mater., 2013, 23, 3577 CrossRef CAS.
- T. A. J. Loh and D. H. C. Chua, ACS Appl. Mater. Interfaces, 2014, 6, 15966 CAS.
- A. M. van der Zande, P. Y. Huang, D. A. Chenet, T. C. Berkelbach, Y. M. You, G. H. Lee, T. F. Heinz, D. R. Reichman, D. A. Muller and J. C. Hone, Nat. Mater., 2013, 12, 554 CrossRef CAS PubMed.
- S. Wang, Y. Rong, Y. Fan, M. Pacios, H. Bhaskaran, K. He and J. H. Warner, Chem. Mater., 2014, 26, 6371 CrossRef CAS.
- S. Najmaei, Z. Liu, W. Zhou, X. Zou, G. Shi, S. Lei, B. I. Yakobson, J. C. Idrobo, P. M. Ajayan and J. Lou, Nat. Mater., 2013, 12, 754 CrossRef CAS PubMed.
- B. Liu, L. Chen, G. Liu, A. N. Abbas, M. Fathi and C. Zhou, ACS Nano, 2014, 8, 5304 CrossRef CAS PubMed.
- J. Shi, D. Ma, G. F. Han, Y. Zhang, Q. Ji, T. Gao, J. Sun, X. Song, C. Li, Y. Zhang, X. Y. Lang, Y. Zhang and Z. Liu, ACS Nano, 2014, 8, 10196 CrossRef CAS PubMed.
- Q. Ji, Y. Zhang, Y. Zhang and Z. Liu, Chem. Soc. Rev., 2015, 44, 2587 RSC.
- Y. Shi, H. Li and L. J. Li, Chem. Soc. Rev., 2015, 44, 2744 RSC.
- H. F. Liu, S. L. Wong and D. Z. Chi, Chem. Vap. Deposition, 2015, 21, 241 CrossRef CAS.
- W. Wu, L. Wang, Y. Li, F. Zhang, L. Lin, S. Niu, D. Chenet, X. Zhang, Y. Hao, T. F. Heinz, J. Hone and Z. L. Wang, Nature, 2014, 514, 470 CrossRef CAS PubMed.
- O. Lopez-Sanchez, D. Lembke, M. Kayci, A. Radenovic and A. Kis, Nat. Nanotechnol., 2013, 8, 497 CrossRef CAS PubMed.
- W. Wu, D. De, S. C. Chang, Y. Wang, H. Peng, J. Bao and S. S. Pei, Appl. Phys. Lett., 2013, 102, 142106 CrossRef.
- Y. Yoon, K. Ganapathi and S. Salahuddin, Nano Lett., 2011, 11, 3768 CrossRef CAS PubMed.
- D. Kong, H. Wang, J. J. Cha, M. Pasta, K. J. Koski, J. Yao and Y. Cui, Nano Lett., 2013, 13, 1341 CrossRef CAS PubMed.
- Y. Jung, J. Shen, Y. Liu, J. M. Woods, Y. Sun and J. J. Cha, Nano Lett., 2014, 14, 6842 CrossRef CAS PubMed.
- T. F. Jaramillo, K. P. Jørgensen, J. Bonde, J. H. Nielsen, S. Horch and I. Chorkendorff, Science, 2007, 317, 100 CrossRef CAS PubMed.
- C. Tsai, K. Chan, J. K. Nørskov and F. Abild-Pedersen, Surf. Sci., 2015, 640, 133 CrossRef CAS.
- Y. Zheng, Y. Jiao, M. Jaroniec and S. Z. Qiao, Angew. Chem., Int. Ed., 2015, 54, 52 CrossRef CAS PubMed.
- C. Tsai, F. Abild-Pedersen and J. K. Nørskov, Nano Lett., 2014, 14, 1381 CrossRef CAS PubMed.
- Z. Lu, W. Zhu, X. Yu, H. Zhang, Y. Li, X. Sun, X. Wang, H. Wang, J. Wang, J. Luo, X. Lei and L. Jiang, Adv. Mater., 2014, 26, 2683 CrossRef CAS PubMed.
- S. Xu, D. Li and P. Wu, Adv. Funct. Mater., 2015, 25, 1127 CrossRef CAS.
- Y. B. Li, Y. Bando and D. Golberg, Appl. Phys. Lett., 2003, 82, 1962 CrossRef CAS.
- X. L. Li, J. P. Ge and Y. D. Li, Chem.–Eur. J., 2004, 10, 6163 CrossRef CAS PubMed.
- R. K. Das, Y. Wang, S. V. Vasilyeva, E. Donoghue, I. Pucher, G. Kamenov, H. P. Cheng and A. G. Rinzler, ACS Nano, 2014, 8, 8447 CrossRef CAS PubMed.
- B. Heying, E. J. Tarsa, C. R. Elsass, P. Fini, S. P. DenBaars and J. S. Speck, J. Appl. Phys., 1999, 85, 6470 CrossRef CAS.
- Y. Yang, H. Fei, G. Ruan, C. Xiang and J. M. Tour, Adv. Mater., 2014, 26, 8163 CrossRef CAS PubMed.
- S. M. Tan, A. Ambrosi, Z. Sofer, Š. Huber, D. Sedmidubský and M. Pumera, Chem.–Eur. J., 2015, 21, 7170 CrossRef CAS PubMed.
- M. R. Laskar, L. Ma, S. Kannappan, P. S. Park, S. Krishnamoorthy, D. N. Nath, W. Lu, Y. Wu and S. Rajan, Appl. Phys. Lett., 2013, 102, 252108 CrossRef.
- G. Xu, X. Wang, Y. Sun, X. Chen, J. Zheng, L. Sun, L. Jiao and J. Li, Nano Res., 2015, 8, 2946 CrossRef CAS.
- Z. H. Deng, L. Li, W. Ding, K. Xiong and Z. D. Wei, Chem. Commun., 2015, 51, 1893 RSC.
- B. Hinnemann, P. G. Moses, J. Bonde, K. P. Jørgensen, J. H. Nielsen, S. Horch, I. Chorkendorff and J. K. Nørskov, J. Am. Chem. Soc., 2005, 127, 5308 CrossRef CAS PubMed.
- M. A. Lukowski, A. S. Daniel, F. Meng, A. Forticaux, L. Li and S. Jin, J. Am. Chem. Soc., 2013, 135, 10274 CrossRef CAS PubMed.
- J. Kibsgaard, Z. Chen, B. N. Reinecke and T. F. Jaramillo, Nat. Mater., 2012, 11, 963 CrossRef CAS PubMed.
- Y. Yu, S. Y. Huang, Y. Li, S. N. Steinmann, W. Yang and L. Cao, Nano Lett., 2014, 14, 553 CrossRef CAS PubMed.
- P. Ge, M. D. Scanlon, P. Peljo, X. Bian, H. Vubrel, A. O'Neill, J. N. Coleman, M. Cantoni, X. Hu, K. Kontturi, B. H. Liu and H. H. Girault, Chem. Commun., 2012, 48, 6484 RSC.
- D. Voiry, M. Salehi, R. Silva, T. Fujita, M. Chen, T. Asefa, V. B. Shenoy, G. Eda and M. Chhowalla, Nano Lett., 2013, 13, 6222 CrossRef CAS PubMed.
- D. Y. Chung, S. K. Park, Y. H. Chung, S. H. Yu, D. H. Lim, N. Jung, H. C. Ham, H. Y. Park, Y. Piao, S. J. Yoo and Y. E. Sung, Nanoscale, 2014, 6, 2131 RSC.
- D. Wang, Z. Pan, Z. Wu, Z. Wang and Z. Liu, J. Power Sources, 2014, 264, 229 CrossRef CAS.
- X. Li, G. Zhu, Q. Kang, Z. D. Huang, X. Feng, Y. Li, R. Liu and Y. Ma, RSC Adv., 2015, 5, 55396 RSC.
- S. Dou, J. Wu, L. Tao, A. Shen, J. Huo and S. Wang, Nanotechnology, 2016, 27, 045402 CrossRef PubMed.
Footnote |
† Electronic supplementary information (ESI) available: More SEM, XED, TEM and Raman datas of as-grown products. See DOI: 10.1039/c5ra24908b |
|
This journal is © The Royal Society of Chemistry 2016 |
Click here to see how this site uses Cookies. View our privacy policy here.