DOI:
10.1039/C5RA20776B
(Paper)
RSC Adv., 2016,
6, 20542-20550
Preparation of a nano-MnO2 surface-modified reduced graphene oxide/PVDF flat sheet membrane for adsorptive removal of aqueous Ni(II)†
Received
7th October 2015
, Accepted 15th February 2016
First published on 15th February 2016
Abstract
In this paper, nanoscale MnO2 particles were attached onto the surface of a PVDF flat sheet membrane, step by step, first through dispersion of graphene oxide (GO) in the PVDF membrane, then reduction of immobilized GO by hydroiodic acid and further micro-wave assisted oxidation of RGO (reduced graphene oxide) by KMnO4 and formation of MnO2 on GO. The SEM observation revealed an asymmetric structure with a finger-like transition layer dominating the membrane of PVDF/MnO2. The uniform distribution of MnO2 on the membrane is revealed by EDX and XPS analysis. The attached MnO2 endowed the membrane with high adsorption capacity for aqueous Ni(II). The adsorption was spontaneous and endothermic, fitting a pseudo-first-order kinetic model and Freundlich isotherm model well. The pure water flux and stable permeation flux of the PVDF/MnO2 membrane reached 31.2 L m−2 h−1 and 9.0 L m−2 h−1 under 0.1 MPa, which were 2.3 and 2.6 times those of the PVDF membrane. The analysis of the fouling resistance and flux recovery ratio indicated that the PVDF/MnO2 membrane had better antifouling properties than the PVDF membrane, attributed to the changes of membrane morphologies and surface hydrophilicity. The PVDF/MnO2 membrane had a high removal ratio (≥87.4%) of Ni2+ in dynamic adsorption. Meanwhile the Ni(II) adsorbed membrane could be easily regenerated by a 0.1 M HNO3 solution.
Introduction
Nickel is a kind of common heavy metal used primarily for electroplating, battery manufacturing and metal processing. The wastewater and exhaust gas from these industries as well as mining and smelting can bring bulk nickel into the environment. Some nickel compounds such as nickel carbonyl and nickel sulfide fumes are considered as carcinogenic substances. In addition, the exposure of nickel above the action level could also cause skin dermatitis. The nickel-containing wastewater should be treated to meet the requirement of discharge standards and the discharged concentration of total nickel in the emission of the effluents should not exceed 0.1 mg L−1 according to the published “Emission standard of pollutants for electroplating” (GB 21900-2008, China).
The conventional technologies for removal of aqueous Ni(II) include chemical precipitation,1 flocculation,2 membrane separation,3–5 electro-deionization,6,7 electro-sorption/electroplating,8 ion exchange9 and adsorption.10–13 Reverse osmosis (RO) and nanofiltration (NF) are two conventional membrane separation processes for rejection of heavy metal ions, bearing benefits from reliability, ease of operation, and efficient pollutant removal.4 However, the application of these methods is hampered by problems of high operation cost and maintenance consumptions due to high pressure operation and easy membrane fouling.
Recently, affinity membranes are developed by modifying membrane with active substance.14,15 These modified membranes also could effectively remove heavy metals under operation of ultrafiltration (UF) and micro-filtration (MF),16 which require lower pressure. As one of the widely-used membrane materials, polyvinylidene fluoride (PVDF) possesses good strength, flexibility, high chemical corrosion resistance and heat resistance. These characteristics make this material valuable in applications of membrane separation, battery and sensor. For affinity membranes, PVDF/zirconia membrane has been prepared for adsorptive removal of arsenic.17 Porous PVDF MF membrane was modified employing surface imprinting technique to prepare the Ni(II) ions selective membrane.18 Melamine-DTPA/PVDF blend membrane containing polyamine carboxylate groups was used for Ni(II) removal.19 The 8-hydroxyquinoline ligand immobilized PVDF membrane was prepared and applied for Ni(II) and Cd(II) adsorption.20
The active substance with high adhesion of Ni(II), such as MnO2,10 DTPA,12,13 EDTA12 and dimethylglyoxime21 are widely studied in the form of composite adsorbent through deposition, blending or grafting. Among them, nanoscale MnO2 exhibit superior adsorption performance due to its high surface area, polymorphic structures and adsorptive performance.10,22 However, the necessary separation has to be taken after adsorption, thus the loss of adsorbent should be reduced. Moreover, the MnO2 was difficult to be applied independently due to its easy aggregation and poor dispersion. In previous literatures,10 graphene/MnO2 composite was prepared through a microwave-assisted method. High surface area of graphene as a carrier could prevent the aggregation of MnO2.
To overcome the drawback of adsorption and membrane separation, the immobilization of MnO2 on the surface of PVDF was considered. Nanoscale MnO2 particles were uniformly coated onto the internal and external surface of PVDF membrane through a three-step synthesis route with the presence of graphene materials. The adsorptive and hydrophilic membrane can be used for UF/MF separation and removal of aqueous nickel(II) ions. The obtained membrane was used to remove aqueous Ni(II) ions, together with improved hydrophilicity and fouling reduction. Proportion of component, contact time, initial concentration and temperature were investigated in static adsorption tests for evaluation of the prepared membrane adsorption performance. The filtration and antifouling property of PVDF membrane and PVDF composite membranes were also studied. Moreover, dynamic adsorption of Ni(II) ions with PVDF/MnO2 composite membrane was further investigated.
Experimental
Materials
Nickel nitrate hexahydrate (Ni(NO3)2·6H2O, 99%) was supplied by Aladdin Co. Ltd and diluted by deionized water to 1173.8 mg L−1 as the Ni(II) stock solution, which was further diluted as required. PVDF (FR904) was obtained from Shanghai 3F Co., Ltd. Graphite powder (99.85%, 30 μm) was purchased from Sinopharm Chemical Reagent Co., Ltd. Bovine serum albumin (BSA, purity > 98%) was obtained from Beijing Aoboxing Biotechnological Co., Ltd. Other reagents such as HI, KMnO4 and dimethyl formamide (DMF) were all of analytical grade. All the materials were used as received without further purification.
Preparation of composite membrane
Graphene oxide (GO) was prepared according to a modified Hummer's method and further dried to obtain graphene oxide.23 The preparation procedure for PVDF composite membranes was illustrated in Fig. 1. The PVDF/GO membrane was prepared by phase inversion method. Graphite oxide (0, 1.0, 2.0 and 4.0 wt% based on the weight of PVDF) were ultrasonically dispersed in DMF. PVDF (15.0 wt%) were added into the GO/DMF solution and the mixtures were stirred at 333 K for 20 h to obtain homogeneous casting solutions. After cooling to room temperature and vacuum degassing, the solutions were cast on glass plate using a casting knife with a thickness of 200 μm. Exposing to air for 10 s, the casted films were immersed in a coagulation bath of pure water for 24 h to complete phase inversion and the obtained solidified membrane, labeled as PVDF, PVDF/GO-1, PVDF/GO-2, PVDF/GO-4, respectively.
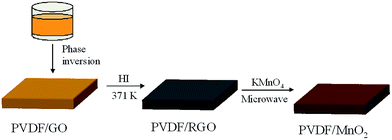 |
| Fig. 1 Schematic illustration of the preparation process of PVDF/GO, PVDF/RGO and PVDF/MnO2 membranes. | |
For preparing PVDF/RGO, HI solution was heated and maintained at 371 K, and PVDF/GO membranes prepared as above mentioned were immersed into the solution. It was observed that the membranes changed immediately from yellow to black due to the reduction of GO to RGO. After 40 s of reaction, the reduced membranes were immersed into ethanol to remove remaining HI, then further washed with DI water and named as PVDF/RGO-1, PVDF/RGO-2, PVDF/RGO-4, respectively.
Before attachment of MnO2, PVDF/RGO membranes were immersed into 150 mL KMnO4 (9.482 g L−1) solution. After 3 h of adsorption, the mixtures were transferred into a household microwave oven (Midea, 2450 MHz, 700 W) and heated for 5 min. The brown products were rinsed several times with ethanol and DI water, marked as PVDF/MnO2-1, PVDF/MnO2-2, and PVDF/MnO2-4.
Characterization
The surface and cross-section morphology of the membranes were observed via scanning electron microscope (SEM, NOVA NanoSEM 450). The water contact angle of the membranes was measured by drop shape analysis system (DSA100, Kruss). The BET measurement was recorded using Quantachrome NOWA 4000 apparatus using N2 adsorption (77.3 K). Changes of characteristic groups and elements during the preparation process were recorded using attenuated total reflectance Fourier transform infrared spectroscopy (ATR-FTIR, Shimadzu 8400s spectrometer) and energy dispersive X-ray (EDX, FEI Quanta 200 FEG), respectively. The elemental compositions of membrane were measured by X-ray photoelectron spectroscopy (XPS, ESCALAB MK) with an Al Kα X-ray source.
Static adsorption tests
Static adsorption tests were conducted by soaking a piece of wet membrane (3 × 3 cm2) in 50 mL of Ni(II) solution (whose concentration ranged from 17.0 to 64.3 mg L−1) at pH 7.0, for 24 h at a certain temperature (298, 308 and 318 K) and with shaking at 150 rpm. The adsorption kinetics was studied by taking solution samples in series of adsorption time (5–180 min). The membrane after adsorption was rinsed by DI water, vacuum dried and weighed. The concentrations of Ni(II) in water samples were measured by flame atomic absorption spectrometry.
The adsorption capacity of Ni(II) by adsorption was calculated by eqn (1):
|
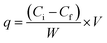 | (1) |
where
Ci and
Cf are initial and final Ni(
II) concentration (mg L
−1), respectively.
V is the volume of Ni(
II) solution (L) and
W is weight of dried membrane (g).
In desorption test, the membrane was soaked in 50 mL of Ni(II) solution (29.3 mg L−1) for 24 h. And before second adsorption, the Ni(II) loaded membrane was regenerated by immersing in 30 mL of HNO3 solution (0.1 M) for 12 h. The operation above was repeated at 298 K.
To investigate the effect of competitive ions and the practical applicability of PVDF/MnO2 composite membrane, a simulated electroplating wastewater containing 16.8 mg L−1 Ni(II) was prepared according to previous literature.24 The composition listed in Table 1 and solution pH was adjusted to 4.5.
Table 1 Characterization of synthetic wastewater samples
|
Metal ions |
Cr(VI) |
Cu(II) |
Pb(II) |
Zn(II) |
Initial concentration (mg L−1) |
36.1 |
7.9 |
2.1 |
12.9 |
Permeation test
The permeation tests were carried out in a dead-end system (300 mL) with effective membrane area of 34.2 cm2. The feed solution (298 K) was stirred at 150 rpm and driven through the membrane with pressurized nitrogen. The operational process was described in the literature.25 After stabilization of membrane flux under 0.15 MPa, the trans-membrane pressure was adjusted to 0.1 MPa, and the quantity of water permeated (Q) was measured at certain time intervals for calculating the flux (J) of membrane by following equation: |
 | (2) |
where A and Δt are the membrane area (m2) and sampling time interval (h).
The pure water flux (JW1) under steady-state flow was measured. Then for evaluating the antifouling property of membrane, the feed solution was changed with 0.1 g L−1 BSA solution (pH 7.4 buffered by 0.1 M PBS) and the permeate flux (Jp) as function of time was recorded. Meanwhile the BSA concentrations in feed and permeate were determined on a UV-spectrophotometer (tech-comp UV-1000, China) at wavelength 280 nm. After filtration, the membrane was rinsed with DI water for three times and the recovered water flux (JW2) was measured using DI water.
To evaluate the antifouling property of membrane, the flux recovery ratio was calculated from the following expression:
|
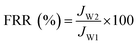 | (3) |
The total resistance Rt (m−1) during filtration includes intrinsic membrane resistance Rm (m−1), cake layer resistance Rc (m−1) and inner fouling (pore plugging and irreversible adsorption of foulants) resistance Rf (m−1), and was calculated using Darcy equation:26
|
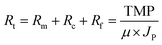 | (4) |
where TMP is the
trans-membrane pressure (0.1 MPa),
μ is the dynamic viscosity of permeate liquid (Pa s).
The rejection was calculated by:
|
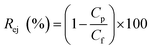 | (5) |
where
Cp and
Cf are concentration of BSA in permeate and feed liquid (mg L
−1).
For investigating rejection of Ni(II), dynamic adsorption test was carried out using 50 mL of 5.9 mg L−1 Ni(II) solution (pH 7.0) as feed solution under 0.1 MPa, and Ni(II) concentrations of the permeate samples at certain time intervals were measured. The effect of BSA on rejection of Ni(II) was also studied with 50 mL feeding solution contained 5.9 mg L−1 Ni(II) and 0.1 g L−1 BSA (pH 7.0).
All the experiments were repeated three times and the standard deviation was ±5%.
Results and discussion
Characterization of the prepared membrane materials
In Fig. S1,† the optical images of prepared PVDF, PVDF/GO, PVDF/RGO and PVDF/MnO2 membrane are shown. The color of pure PVDF membrane is white, the color of membrane changes to yellow with the incorporation of GO. The uniform yellow suggests the homogeneous dispersion of GO and darkens with the increased addition of GO. The membrane color turns to black after reduction of GO by HI solution. In microwave-assisted reaction, KMnO4 was reduced by RGO to nano-scale MnO2, deposited on the membrane. And the PVDF/MnO2 was obtained as brown membrane.
The cross-section morphology of PVDF, PVDF/GO-4, PVDF/RGO-4 and PVDF/MnO2-4 characterized by SEM are shown in Fig. 2. All the PVDF membranes display the characteristics of asymmetric membranes, consisting of a thin and dense skin layer, a finger-like transition layer and a spongy-like porous support layer. The spongy-like porous support layer dominates in the structure of pure PVDF membrane. With the addition of GO, the transition layer develops and expands toward the bottom region of the membrane (Fig. 2b). Meanwhile fibre-network structures were observed in the bottom surface of GO or RGO contained membranes (Fig. S2†).
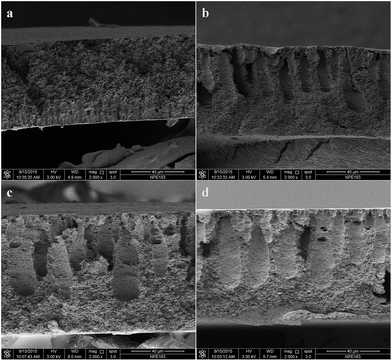 |
| Fig. 2 Cross-section SEM images of (a) PVDF, (b) PVDF/GO, (c) PVDF/RGO and (d) PVDF/MnO2. | |
The remarkable difference in porous structure is also reflected by the measurement of porous structure parameters through BET method. As shown in Table S1,† the BET surface area of PVDF/GO composite membrane is nearly 5 times that of PVDF membrane. Both pore volume and average surface pore size are increased with the addition of GO. The result may be interpreted by the fast exchange of solvent (DMF) with non-solvent (water) in the phase inversion process due to the hydrophilic GO. And the more developed lean polymer phase and coalescence caused the larger finger-like pores.27 In addition, according to SEM and BET analysis, the cross-section of PVDF/GO-4, PVDF/RGO-4 and PVDF/MnO2-4 show very similar morphologies, which would have lower permeate resistance. There were no apparent differences for the cross section morphologies caused by formation of RGO and MnO2. However, differences between PVDF/MnO2 and other membranes in the upper surface exist (Fig. 3). For PVDF/MnO2 membrane, due to the dispersion of graphene nanosheet in membrane, the nanoscale MnO2 particles are present on the surface of the membrane (Fig. 3d).
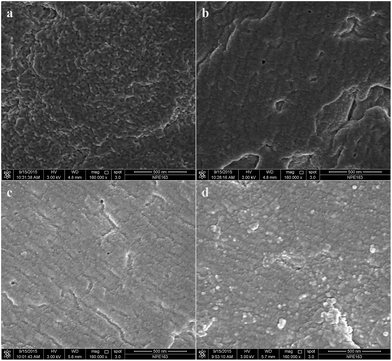 |
| Fig. 3 Upper surface SEM images of (a) PVDF, (b) PVDF/GO, (c) PVDF/RGO and (d) PVDF/MnO2. | |
The elemental mappings of PVDF/MnO2 membrane (Fig. S3b and c†) further indicate the homogeneous distribution of manganese and oxygen on the entire surface. Especially for cross-section of PVDF/MnO2, the corresponding elemental mappings show the inner-surface of membrane is also coated evenly with manganese and oxygen. The results of elemental analysis of various membranes are summarized in Table S2† and the standard deviations are ±3%. The Mn percentage increases with the increasing addition of GO, and the oxygen percentage reaches maximum in PVDF/MnO2 membrane because of the formation of MnO2. For PVDF/MnO2 membrane, the Mn content in upper surface is higher than that in cross-section. MnO2 formed from interface chemical reaction more likely attach on the external and internal surface of membrane than inside the membrane PVDF matrix, which is beneficial to improving surface utilization.
In Fig. S4,† the ATR-FTIR spectra of PVDF/GO-4, PVDF/RGO-4 and PVDF/MnO2-4 membrane are shown. Compared with ATR-FTIR spectrum of PVDF in previous literature,25 the characteristic bands of PVDF are very intensive in all spectra of composite membrane, i.e. deformation and stretching vibrations of C–H and the C–F stretching vibration at 1400, 2978 and 1171 cm−1, β phase vibration at 1275 cm−1, amorphous phase at 875 and 841 cm−1, indicating the skeleton structure of PVDF in PVDF/GO has not changed during reaction with HI and KMnO4. However, the intensity and width of peak at ∼3400 cm−1, reflecting the –OH content, increase in accordance with the orders of PVDF/MnO2-4 > PVDF/GO-4 > PVDF/RGO-4. It indicates PVDF/MnO2-4 possesses the highest –OH due to the formation of hydrated manganese dioxide.
The wettability involving the interaction between water and solid in contact plays an important role in permeation flux and antifouling performance of membrane. The contact angle measurement reflecting the wettability is shown in Fig. S5.† As the added GO increases from 0% to 4%, the contact angle of PVDF membrane drops from 78.5° ± 0.8° to 68.7° ± 0.4°. The GO with abundant –OH disperses homogeneously on the membrane surface and results in the increase of wettability.25 While most of –OH are eliminated by HI, the contact angle of membrane increases to 84.1° ± 0.2°, further demonstrating the role of –OH in wettability. After coating of MnO2, the contact angle decreases back to 76.7° ± 1.9° and the membrane becomes more hydrophilic. It should be attributed to the hydrophilic functional group (i.e., –OH) introduced by the modification of MnO2.28
Static adsorption study of the adsorbents
Optimal of composite component. The effect of GO on the Ni(II) adsorption on PVDF composite is shown in Fig. 4. The Ni(II) adsorption capacity of PVDF membrane increases with increased addition of GO. The carboxyl and hydroxyl groups on the GO sheets increase the capacity of PVDF/GO composite membrane to adsorb Ni(II),29 which is proved by the decreased adsorption capacity of PVDF/RGO membrane. After reaction with excessive KMnO4, a significant promotion is observed in the Ni(II) adsorption by the formation of adsorptive MnO2. By comparing the Ni(II) adsorption on PVDF/GO membrane, MnO2 possess better adsorption property for Ni(II). The adsorption capacity increases with the initial GO content in PVDF/GO membrane, because the MnO2 content on PVDF/MnO2 is dependent on the RGO content on PVDF/MnO2.
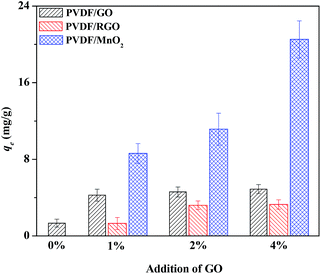 |
| Fig. 4 Comparison of Ni(II) adsorption on PVDF membrane and PVDF composite membranes. | |
Adsorption kinetics. The Ni(II) adsorption on PVDF/MnO2-4 as function of contact time is shown in Fig. 5. A rapid adsorption is observed in 60 min, and then the adsorption capacity increases slowly until the equilibrium is reached at 90 min.
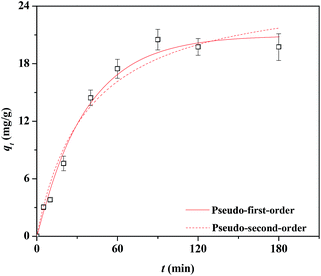 |
| Fig. 5 Adsorption kinetics of Ni(II) on PVDF/MnO2 membrane modeling with pseudo-first-order and pseudo-second-order equations. | |
The kinetics data were fitted with pseudo-first-order (eqn (6)) and pseudo-second-order (eqn (7)) kinetic model described as follows:
|
ln(qe − qt) = ln qe − k1t
| (6) |
|
 | (7) |
where
qt and
qe are the Ni(
II) adsorption capacity (mg g
−1) on PVDF/MnO
2-4 at time
t (min) and equilibrium, respectively.
k1 (min
−1) and
k2 (g mg
−1 min
−1) are the adsorption rate constants of pseudo-first-order and pseudo-second-order adsorption, respectively.
The fitting curves are shown in Fig. 5 and the results obtained from both models are summarized in Table 2. With higher regression correlation coefficients, the pseudo-first-order model is found to better match the kinetic data. In addition, the value of equilibrium adsorption capacity calculated from pseudo-first-order model (20.9 mg g−1) nearly matches that recorded experimentally (19.7 mg g−1).
Table 2 Kinetic parameters for the adsorption of Ni(II) on PVDF/MnO2-4 membrane
Kinetics equation |
Kinetic parameters |
PVDF/MnO2 |
Pseudo-first-order |
qe (mg g−1) |
20.9 |
k1 (min−1) |
0.0274 |
R2 |
0.986 |
Pseudo-second-order |
qe (mg g−1) |
26.2 |
k2 (g mg−1 min−1) |
0.0010 |
R2 |
0.967 |
Adsorption isotherm. The isotherm of Ni(II) adsorption on PVDF/MnO2-4 was carried out to investigate the transport of Ni(II) from bulk solution to membrane adsorbent. Fig. 6 shows the Ni(II) adsorption versus the equilibrium concentration at temperature of 298, 308 and 318 K. There is an increase of adsorption capacity as the increase of temperature.
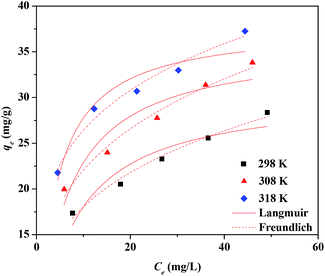 |
| Fig. 6 Adsorption isotherms of Ni(II) on PVDF/MnO2 membrane modeling with Langmuir and Freundlich equation. | |
All the experimental data show non-linear characters and were fitted using Langmuir (eqn (8)) and Freundlich (eqn (9)) isotherm models described as follows:
|
 | (8) |
qm is the theoretical maximum adsorption capacity (mg g
−1) and
b represent equilibrium constant of Langmuir isotherm (L mg
−1). In Freundlich equation,
KF and
n are constants related to adsorption capacity and adsorption intensity of the adsorbents.
The parameters and regression correlation coefficients obtained from the modeling of isotherm data (Fig. 6) are listed in Table 3. With the higher regression correlation coefficient, Freundlich model better describes and simulates adsorption performance under all experimental condition, indicating a homogeneous distribution of active sites on the PVDF/MnO2-4. In addition, the KF showing the adsorption capacity of Ni(II) on PVDF/MnO2-4 membrane increases as the temperature increased from 298 K to 318 K.
Table 3 Isotherm parameters for the adsorption of Ni(II) on PVDF/MnO2-4 membrane
T (K) |
Langmuir |
Freundlich |
qm (mg g−1) |
b (L mg−1) |
R2 |
KF |
n |
R2 |
298 |
30.7 |
0.143 |
0.866 |
9.60 |
3.66 |
0.981 |
308 |
36.6 |
0.154 |
0.740 |
11.87 |
3.72 |
0.979 |
318 |
37.9 |
0.272 |
0.904 |
15.83 |
4.51 |
0.974 |
The thermodynamic equilibrium constant K0 is dependent on temperature and calculated according to the literature.30 And Gibbs free energy change (ΔG0), enthalpy change (ΔH0) and entropy change (ΔS0) for the Ni(II) adsorption on PVDF/MnO2-4 membrane were determined by equations as follows:
|
ΔG0 = −RT ln K0
| (10) |
|
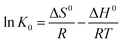 | (11) |
where
R and
T are the gas constant (8.314 J mol
−1 L
−1) and absolute solution temperature (K).
The values of thermodynamic parameters are summarized in Table S3.† The positive value of ΔH0 suggests that the adsorption process of Ni(II) on PVDF/MnO2-4 is endothermic, supported by the increasing adsorption of Ni(II) with the increase of temperature. The negative value of ΔG0 and the positive value of ΔS0 change reveal that the adsorption process is spontaneous.
Synthetic wastewater tests. The prepared PVDF/MnO2 composite membrane was tested to remove Ni(II) in single Ni(II) solution and synthetic Ni(II) containing wastewater. As shown in Fig. S6,† the PVDF/MnO2 composite membrane has lower adsorption capacity (7.9 mg g−1) in simulated wastewater than that (11.5 mg g−1) in single solution, which can be attributed to the competitive adsorption by other metal ions. At same time, some other heavy metal (especially lead ions) in simulated wastewater can also be well removed by prepared composite membrane.
Regeneration study
To evaluate the desorption and regeneration potential of PVDF/MnO2-4 membrane, the Ni(II) desorption was tested after equilibrium adsorption of the membrane. Since the adsorption of Ni(II) on MnO2 is pH-dependent and a suppressive adsorption occurs at low pH,10 30 mL of 0.1 M HNO3 solution was used as eluent solution. The adsorption capacity of Ni(II) on PVDF/MnO2-4 membrane for five consecutive adsorption–desorption cycles are shown in Fig. S7.† The recycled composite membrane reserves 92.67% Ni(II) adsorption capacity after forth desorption, indicating the good regeneration property and stability of PVDF/MnO2-4 membrane with 0.1 M HNO3 solution as eluent solutions.
Permeate study
Antifouling properties. The filtration performance as well as antifouling property was investigated using BSA solution as feed solution and the flux of PVDF membrane and PVDF composite membranes as function of time is shown in Fig. 7a. Due to low value, the flux of PVDF membrane reaches a steady state quickly. The incorporation of GO promotes the membrane flux greatly and the initial flux of PVDF/GO is nearly 7.7 times that of PVDF membrane. Although the high initial flux is advantageous for forming cake layer causing the membrane flux declined sharply, the flux of PVDF composite membranes with low structural resistance are obviously better than that of PVDF membrane. The values of membrane flux at different stages are summarized in Fig. 7b. For all of JW1, Jp and JW2, PVDF/GO membrane and PVDF membrane have the highest and lowest value, respectively. The JW1, Jp and JW2 of PVDF/MnO2 are close to that of PVDF/RGO, which are 2.3, 2.6 and 3.2 times those of PVDF membrane. In addition, PVDF composite membranes have higher BSA rejection than PVDF membrane. The membrane flux is related to filtration resistances and further analysis is shown in Fig. 7c. PVDF membrane with a support layer dominated with spongy pores has the maximum membrane resistance. Meanwhile the poor hydrophilicity and high surface roughness of PVDF membrane ease the formation of cake layer and increase membrane fouling.25 For PVDF composite membrane, the membrane resistance decreases with the development of finger-like transition layer. The filtration resistance of PVDF/GO is lowest due to the hydrophilic membrane surface and improvement in surface roughness. The importance of wettability is demonstrated by the filtration resistances of PVDF/RGO membrane. It is noted that the PVDF/MnO2 membrane possesses better wettability but higher filtration resistances than PVDF/RGO. The MnO2 nanoparticles coated on the membrane surface are considered similar to certain foultants which increase membrane filtration resistance. The flux recovery ratio reflecting the antifouling property of membrane is shown in Fig. 7d. With 84.7% of flux recovery ratio, the PVDF/GO membrane exhibits the best antifouling property. The flux recovery ratio PVDF/MnO2 membrane is 76.8%, which is much higher than that of PVDF membrane (57.2%).
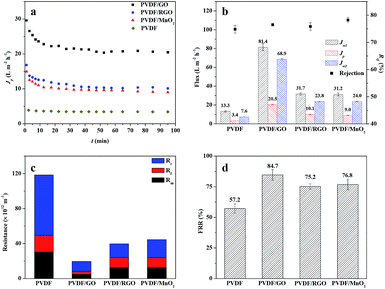 |
| Fig. 7 Comparison of filtration and antifouling performance of PVDF membrane and PVDF composite membranes: (a) curves of permeate flux as function of filtration time, (b) results of pure water flux, permeate flux and recovered flux, (c) analysis of the filtration resistances and (d) flux recovery ratio. | |
Dynamic adsorption of Ni(II). Dynamic adsorption of Ni(II) on PVDF membrane and PVDF composite membranes was carried out in a dead-end system and the Ni(II) loaded membrane was regenerated by immersing in 40 mL of 0.1 M HNO3 solution before re-adsorption. As shown in Fig. 8a, a slight decline is observed for the rejection ratio as the filtration time increase. The highest rejection ratio and treatment effect are achieved with PVDF/MnO2 membrane. At pH7.0, the predominant specie of nickel is Ni2+ (99.88% nickel) calculated by MINEQL+. It is observed that the Ni(II) rejection ratio correlates positively with Ni(II) adsorption capacity of the membrane and PVDF membrane could hardly remove Ni(II) from feed solution, indicating adsorption plays the key role in Ni(II) rejection by PVDF composite membrane rather than intrinsic membrane rejection. The MnO2 modification endows the PVDF membrane the Ni(II) rejection ability during UF/MF operation. Although the removal of Ni(II) from 5.9 mg L−1 Ni(II)-containing feed liquid decreases slightly with the increasing of filtration times, the rejection ratio remains at a level higher than 87.4% after second regeneration. In addition, the PVDF/MnO2 membrane possesses well chemical and physical stability, which is proved by the stable flux (32.8, 34.1 and 30.4 L m−2 h−1) after each regeneration with 0.1 M HNO3.
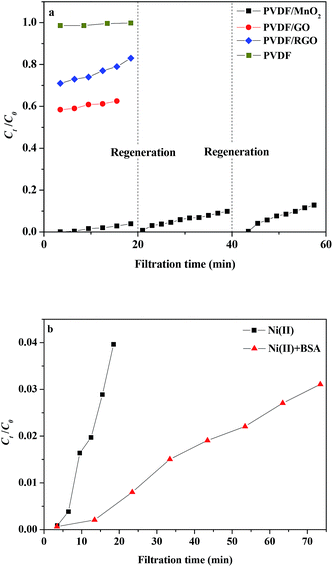 |
| Fig. 8 (a) Ni(II) removal by PVDF membrane and PVDF composite membranes with continuous filtration mode and (b) effect of BSA on Ni(II) removal by PVDF/MnO2 composite membrane with continuous filtration mode. | |
When the mixture of BSA and Ni(II) was used as feeding solution, the ratio of effluent Ni(II) concentration to initial Ni(II) concentration as function of filtration time is shown in Fig. 8b. For 50 mL feeding solution, the filtration time is longer and the removal ratio is better at the present of BSA. Although adsorptive sites on the surface of membrane may partly be covered with intercepted BSA, the complexation between Ni(II) and N-terminal site of BSA31 and extended adsorption time could be responsible for the increased Ni(II) rejection ratio.
Adsorption mechanism
The chemical composition of PVDF/MnO2 composite membrane before and after adsorption of Ni(II) was investigated by XPS (Fig. S8†). Fig. S8a† shows the high-resolution XPS spectrum for C 1s which is divided into graphene C–C peak (284.6 eV), PVDF C–C peak (285.8 eV) and C–F peak (290.8 eV).32 The result indicates the graphene-like material in the PVDF/MnO2 membrane exists mainly in the form of reduced graphene oxide. The presence of MnO2 is evidenced by Mn 2p spectrum along with O 1s spectrum. In the Mn 2p region (Fig. S8b†), the binding energy peaks of Mn 2p3/2 and Mn 2p1/2 are located at 641.5 eV and 653.2 eV (Δ = 11.7 eV), which are characteristic of Mn(IV).33 The O 1s signal in XPS of virgin PVDF/MnO2 membrane (Fig. S8c†) can be deconvoluted into three major peaks around at 529.6 eV, 531.3 eV and 533.1 eV, which are assigned to metal oxide (M–O), hydroxyl boned to metal (M–O–H) and adsorbed H2O.34,35 After adsorption of Ni(II), two main peaks observed at 855.7 and 873.3 eV in the Ni 2p region (Fig. S8d†), corresponding to Ni 2p3/2 and Ni 2p1/2, yielding a spin-energy separation of 17.6 eV, which is in accordance with the characteristic of Ni(II).36 Similar to Fig. S8c,† the three peaks referring to M–O, M–O–H and H2O are shown in Fig. S8e.† The area ratio of peak at 529.6 eV assigned to M–O increased by 5.26% (from 56.88% to 62.14%). While the area ratio of peak at 531.3 eV assigned to M–O–H decreases by 4.94% (from 42.25% to 37.31%). These changes means the oxygen atoms in the forms of Mn–O and Mn–O–H participated in the Ni(II) adsorption process. Moreover, solution pH was observed to drop from 6.99 to 4.48 in 14 min after addition of PVDF/MnO2 membrane (0.1044 g) into 64 mL of Ni(II) solution (76.4 mg L−1). As described in previous study,22,37 the adsorption of Ni(II) on oxygen containing groups involves complex mechanism including ion exchange (outer-sphere surface complexation) and inner-sphere surface complexation. The inner-sphere surface complexation illustrates the Ni(II) adsorbed onto MnO2 through six-fold coordination. And the ion exchange reactions could be described as eqn (12)–(15): |
MnO− + Ni2+ ↔ MnONi+
| (12) |
|
MnOH + Ni2+ ↔ MnONi+ + H+
| (13) |
|
MnO− + Ni2+ + H2O ↔ MnONiOH + H+
| (14) |
|
MnOH + Ni2+ + H2O ↔ MnONiOH + 2H+
| (15) |
Conclusions
In this paper, GO nanosheet was firstly well dispersed in PVDF membrane as reaction sites for following formation of the nanoscale MnO2 particles, which uniformly attached in PVDF/MnO2 membrane through a microwave-assisted reaction. The MnO2 endowed PVDF membrane high removal capacity for the aqueous Ni(II). The Ni(II) adsorption process was well explained by pseudo-first-order kinetic model. The isotherm data fitted well with Freundlich isotherm model, and the adsorption process was spontaneous and endothermic. Although the attachment of MnO2 may increase the filtration resistance, the hydrophilic MnO2 and optimized membrane structure made the PVDF/MnO2 possessed nice filtration and antifouling performance. The dynamic adsorption test indicated the PVDF/MnO2 membrane had high removal ratio of Ni(II) from continuous feed solution (5.9 mg L−1 Ni(II)). In addition, the Ni(II) loaded membrane could be regenerated well with 0.1 M HNO3 solution. The high efficiency and adsorption capacity brought by PVDF/MnO2 membrane make ultrafiltration/micro-filtration particularly attractive and practically applicable in removal and remediation of Ni(II) pollution. Its other applications are to be further explored, such as treatment of wastewater containing suspends particles, COD and nickel ions.
Acknowledgements
The financial supports from the National Natural Science Foundation of China (No. 21177018) and the Program of Introducing Talents of Discipline to Universities (B13012) are greatly acknowledged.
Notes and references
- A. Papadopoulos, D. Fatta, K. Parperis, A. Mentzis, K.-J. Haralambous and M. Loizidou, Sep. Purif. Technol., 2004, 39, 181–188 CrossRef CAS.
- C. Morlay, M. Cromer and O. Vittori, Water Res., 2000, 4, 455 CrossRef.
- J. Qin, M. Oo, M. Wai, C. M. Ang, F. Wong and H. Lee, Water Res., 2003, 37, 3269 CrossRef CAS PubMed.
- Z. V. P. Murthy and L. B. Chaudhari, J. Hazard. Mater., 2008, 160, 70 CrossRef CAS PubMed.
- C. Gherasim, K. Hanckova, J. Palarcik and P. Mikulasek, J. Membr. Sci., 2015, 490, 46 CrossRef CAS.
- Y. S. Dzyazko, L. N. Ponomaryova, L. M. Rozhdestvenskaya, S. L. Vasilyuk and V. N. Belyakov, Desalination, 2014, 342, 43 CrossRef CAS.
- Ö. Arar, Ü. Yüksel, N. Kabay and M. Yüksel, Desalination, 2014, 342, 16 CrossRef.
- A. Brennsteiner, J. W. Zondlo, A. H. Stiller, P. G. Stansberry, D. C. Tian and Y. Xu, Energy Fuels, 1997, 11, 348 CrossRef CAS.
- B. Alyüz and S. Veli, J. Hazard. Mater., 2009, 167, 482 CrossRef PubMed.
- Y. Ren, N. Yan, Q. Wen, Z. Fan, T. Wei, M. Zhang and J. Ma, Chem. Eng. J., 2011, 175, 1 CrossRef CAS.
- C. Chen and X. Wang, Ind. Eng. Chem. Res., 2006, 45, 9144 CrossRef CAS.
- E. Repo, T. A. Kurniawan, J. K. Warchol and M. E. T. Sillanpää, J. Hazard. Mater., 2009, 171, 1071 CrossRef CAS PubMed.
- X. Zhao, L. Song, Z. Zhang, R. Wang and J. Fu, J. Mol. Struct., 2011, 986, 68 CrossRef CAS.
- H. Bessbousse, J. F. Verchere and L. Lebrun, J. Membr. Sci., 2010, 364, 167 CrossRef CAS.
- E. Katsou, S. Malamis, K. J. Haralambous and M. Loizidou, J. Membr. Sci., 2010, 360, 234 CrossRef CAS.
- E. Klein, J. Membr. Sci., 2000, 179, 1 CrossRef CAS.
- Y. Zheng, S. Zou, K. G. N. Nanayakkara, T. Matsuura and J. P. Chen, J. Membr. Sci., 2011, 374, 1 CrossRef CAS.
- V. Vatanpour, S. S. Madaeni, S. Zinadini and H. R. Rajabi, J. Membr. Sci., 2011, 373, 36 CrossRef CAS.
- L. Song, X. Zhao, J. Fu, X. Wang, Y. Sheng and X. Liu, J. Hazard. Mater., 2012, 199–200, 433 CrossRef CAS PubMed.
- E. Salehi, S. S. Madaeni and F. Heidary, Sep. Purif. Technol., 2012, 94, 1 CrossRef CAS.
- A. Nezamzadeh-Ejhieh and M. Kabiri-Samani, J. Hazard. Mater., 2013, 260, 339 CrossRef CAS PubMed.
- G. Sheng, J. Sheng, S. Yang, J. Hu and X. Wang, J. Radioanal. Nucl. Chem., 2011, 289, 129 CrossRef CAS.
- W. S. Hummers and R. E. Offeman, J. Am. Chem. Soc., 1958, 80, 1339 CrossRef CAS.
- M. Ajmal, R. A. K. Rao, R. Ahmad and J. Ahmad, J. Hazard. Mater., 2000, 79, 117 CrossRef CAS PubMed.
- C. Zhao, X. Xu, J. Chen and F. Yang, J. Environ. Chem. Eng., 2013, 1, 349 CrossRef CAS.
- L. Liu, C. Zhao and F. Yang, Water Res., 2012, 46, 1969 CrossRef CAS PubMed.
- V. Vatanpour, S. S. Madaeni, R. Moradian, S. Zinadini and B. Astinchap, Sep. Purif. Technol., 2012, 90, 69 CrossRef CAS.
- Y. Fu, J. Yu, Y. Zhang and Y. Meng, Appl. Surf. Sci., 2014, 317, 84 CrossRef CAS.
- Y. Wu, H. Luo, H. Wang, L. Zhang, P. Liu and L. Feng, J. Colloid Interface Sci., 2014, 436, 90 CrossRef CAS PubMed.
- J. Zhang, H. Fu, X. Lv, J. Tang and X. Xu, Biomass Bioenergy, 2011, 35, 464 CrossRef CAS.
- Y. Zhang and D. E. Wilcox, J. Biol. Inorg. Chem., 2002, 7, 327 CrossRef CAS PubMed.
- R. Li, C. Chen, J. Li, L. Xu, G. Xiao and D. Yan, J. Mater. Chem. A, 2014, 2, 3057 CAS.
- D. Sun, Z. Wang, K. Huang, X. Wang, H. Wang, C. Qing, B. Wang and Y. Tang, Chem. Phys. Lett., 2015, 638, 38 CrossRef CAS.
- J. Zhang and X. S. Zhao, Carbon, 2013, 52, 1 CrossRef CAS.
- E. L. Ratcliff, J. Meyer, K. X. Steirer, A. Garcia, J. J. Berry, D. S. Ginley, D. C. Olson, A. Kahn and N. R. Armstrong, Chem. Mater., 2011, 23, 4988 CrossRef CAS.
- J. Matienzo, L. I. Yin, S. O. Grim and W. E. Swartz Jr, Inorg. Chem., 1973, 12, 2762 CrossRef CAS.
- X. Wang, J. Radioanal. Nucl. Chem., 2013, 295, 2301 CrossRef CAS.
Footnote |
† Electronic supplementary information (ESI) available. See DOI: 10.1039/c5ra20776b |
|
This journal is © The Royal Society of Chemistry 2016 |
Click here to see how this site uses Cookies. View our privacy policy here.