DOI:
10.1039/C5RA19965D
(Paper)
RSC Adv., 2016,
6, 3176-3185
Excellent properties and extrusion foaming behavior of PPC/PS/PTFE composites with an in situ fibrillated PTFE nanofibrillar network
Received
27th September 2015
, Accepted 18th December 2015
First published on 22nd December 2015
Abstract
In this work, we compounded polystyrene (PS) and polytetrafluoroethylene (PTFE) with poly(propylene carbonate) (PPC) via a triple-screw extruder to prepare multiphase composites that possess special properties and to improve the extrusion foaming ability of PPC. It was found that PS was immiscible with PPC and formed a dispersion phase, and PTFE was in situ fibrillated into the nanofibrillar network within the PPC/PS matrix. The introduction of rigid PS domains and PTFE nanofibrils showed remarkable effects on the properties of PPC. Compared with neat PPC, the PPC/PS/PTFE composites had a 12 °C higher glass transition temperature, 292% higher storage modulus in the glassy state characterized by dynamic mechanical analysis, and 1576% higher initial viscosity. Moreover, the physical network formed by PTFE nanofibrils effectively prevented the shear-thinning behavior of the polymer matrix. A significant influence of PTFE on the cell morphology was found in the extrusion foaming process. The cell density of PPC/PS/PTFE foams was four orders of magnitude higher than PPC foams. The compressive modulus and strength of the foamed PPC/PS/PTFE composites were 58 and 34 times higher than that of PPC foams, respectively. The great improvement in the mechanical performance was attributed to the synergistic effects of the enhanced CO2 affinity, the heterogeneous nucleation effect, and the changes in system melt viscosity.
1. Introduction
Polymeric foams have been widely used in many applications due to their advantages such as lightweight, buoyancy, cushioning performance, thermal and acoustic insulation, impact damping, and cost reduction.1,2 Traditional polymers such as polystyrene (PS),3 polyurethane (PU),4 polyethylene (PE),5,6 polypropylene (PP),7 polyvinylchloride (PVC)8 are extensively used in the production of foamed products. However, white pollution problems have been proposed due to their undegradability.9 To address these problems, biodegradable polymers have been developed, such as poly(lactic acid) (PLA),10 polyhydroxy-butyrate-velerate (PHBV)11 and poly(propylene carbonate) (PPC).12 Among them, PPC, an aliphatic polycarbonate, is composed of propylene epoxide and carbon dioxide (CO2). PPC, an amorphous polymer, possesses good transparency and can be degraded into CO2 and H2O environmentally. Although PPC has attracted great attention from scientific and industry area to reduce the greenhouse gas pollution, its poor thermal stability and mechanical properties determined by its low glass transition temperature (Tg about 35 °C) limit its wide applications.13–15 Moreover, it was found that the shear-thinning behavior of PPC was very serious in melt processing, which would affect its foaming ability using physical blowing agent.
Polymer melt compounding is an effective way to combine the advantages of two or more component polymers.16 PS has wide applications in the plastic industry because of its good thermal stability, high Young's modulus and excellent transparency.17,18 It has been reported that the thermal stability, mechanical properties and film-forming property of PPC could be significant improved by PS through melt-extrusion method.19 Moreover, PS also possesses good CO2 dissolution and the foaming abilities, thus it is widely used as polymeric foams in package, transportation, construction applications.20 Therefore, in this study, PS was melt blended with PPC at various proportions to investigate the effects of loaded PS on the thermal, mechanical and rheological properties, as well as extrusion foaming behavior of the PPC matrix polymer.
In addition, great efforts have been devoted to the preparation of PPC composites using various fillers in order to enhance the performance of PPC matrix and produce high quality PPC composite foams, such as graphene oxide (GO),14 montmorillonite,21 lignocellulose fiber,22 glass fiber,23 calcium carbonate.24 For example, with the addition of GO, the Tg and the storage modulus of PPC could be improved significantly and the foamed samples showed better dimension stability.14 CaCO3 nano particles could act as nucleation agent in PPC matrix and the highest cell density could be obtained at 3 wt% loading level.24 Chemical blowing agent such as N,N′-dinitrosopentamethylene tetramine (DPT) has been used to prepare PPC/nano-CaCO3 composite foams.1 However, the decomposition products of these foaming agents are believed to be harmful for the environment. In recent years, microcellular foaming using physical blowing agents, such as CO2 and N2, has been attracting attentions from both academic and industry fields. Although batch foaming technique provides uniform cell structure, it is difficult to industrialize due to its low productive efficiency.
Extrusion foaming using supercritical CO2 is an economic continuous foaming method with high productivity and it is also environmental friendly.25 To date, there is no study reported the extrusion foaming behavior of PPC, PPC blends or PPC composites. During foaming, it was found that the CO2 absorption ability of PPC was low and the melt viscosity of PPC was easily decreased, which were not favorable for physical blowing. The addition of PS into PPC matrix may help to alter the melt viscosity and the CO2 affinity, and further assist the continuous extrusion foaming process. In addition, polytetrafluoroethylene (PTFE) has been found can deform into high aspect ratio fibrillar structure under loading conditions to dissipate energy and stabilize a crack tip by bridging, which forms interconnected physically networks.26,27 It has been reported that PTFE particles could in situ fibrillated into networks within PP polymer matrix under high shear stress field in twin screw extrusion. The formation of this network within polymer matrix is expected to reinforce the composite and improve its rheological response significantly. The fluoroalkyl functional groups existed in PTFE are responsible for strong thermodynamic affinity for CO2 and are expected to promote CO2 dissolution in the matrix.28,29 The in situ fibrillation characters of PTFE and their CO2-philic attributes have been thoroughly reported by Park et al. in their recent publications.28,30 Inspired by the special characters of PTFE, it was used as fillers to prepare PPC/PS/PTFE ternary composites. We expect the introduction of PS sub-domain and in situ fibrillated PTFE nanofibrillar network can alter and enhance the extrusion foaming property of PPC.
In this work, PS and PTFE were melt blended with PPC using a triple-screw extruder to prepare the PPC/PS/PTFE composites. The morphology of PS and PTFE in the PPC matrix was examined by scanning electron microscope (SEM), the thermal, dynamic mechanical, and rheological properties of the blends and composites were investigated as well. Furthermore, the extrusion foaming behavior and compressive properties of foams were studied and analyzed in detail.
2. Experimental
2.1 Materials
Commercial available poly(propylene carbonate) (PPC) with melt flow rate (MFR) = 1.618 g/10 min (at 170 °C/2.16 kg load) was purchased from Bangfeng Co. Ltd. It was used as polymer matrix in this study. Polystyrene (PS, N1841H) was purchased from Hong Kong Petrochemical Co. Ltd, in the form of pellets and used as received. Its melt flow index (MFI) is 10 g/10 min with a density of 1.04 g cm−3. Commercial grade polytetrafluoroethylene (PTFE) powder (Metablen™ A-3000) supplied by Mitsubishi Rayon was used as additive. All materials were used as received without further purification. Carbon dioxide (purity, 99%) used as physical blowing agent was obtained from Shengtong Co. Ltd.
2.2 Melt compounding
PPC and PS were pre-dried in an oven for 3 h under 50 °C and 80 °C, respectively. In order to prevent the agglomeration of PTFE particles, they were pre-dried for 3 h under 100 °C, then dispersed with a high speed grinder (Tester Instrument, Tianjin, China) and immediately used. PPC, PS and PTFE were blended at determined ratio via a triple-screw extruder manufactured by Guangzhou POTOP Co. Ltd, China equipped with a screw of D = 25 mm diameter and L/D = 40 length to diameter ratio. The rotor speed was 50 rpm and the temperature profile from hopper to die was set from 150 °C to 170 °C. The blends were extruded using a four-strand die, then led into a water cooling bath and pelletized. Neat PPC was also processed following the same processing parameters to ensure same thermal history. The compositions of the prepared PPC/PS/PTFE composites are listed in Table 1.
Table 1 Compositions of PPC/PS blends, and PPC/PS/PTFE composites
Code |
PPC |
PS |
PTFE |
PPC |
100 |
— |
— |
90–10 |
90 |
10 |
— |
70–30 |
70 |
30 |
— |
100–0.3 |
100 |
— |
0.3 |
70–30–0.3 |
70 |
30 |
0.3 |
70–30–3 |
70 |
30 |
3 |
2.3 Extrusion foaming
Extrusion foaming of the prepared composites were conducted by pumping SC-CO2 through a syringe pump (ISCO-260D, USA) into a single screw extruder (D = 45 mm; L/D = 29) with a die diameter of 1.5 mm and ratio of length to diameter of 10. A pressure transducer mounted near the die entrance was used to record the pressure. A metered amount of SC-CO2 was injected into the melt through an injection point located at the middle of the extruder. Foaming of the polymer melt occurred at the die exit where the polymer/gas solution was subject to rapid depressurization resulting in the phase separation of the gas and the melt. The temperature profile used in the experiment was 140 °C, 155 °C, 155 °C, and 150 °C from hopper to the extrusion die. The extrusion temperature was critical since there is a large melting temperature difference between PS and PPC. The foaming of PPC/PS blends and PPC/PS/PTFE composites would be unstable when the die temperature either higher than 155 °C or lower than 145 °C. The processing temperatures were the same for all sample groups to avoid additional variable factors. The rotor speed was also optimized to 16.5 rpm for all sample groups. The content of CO2 was constant at 1 wt% of the matrix material. The 70–30–3 composite was not used for extrusion foaming because its stiffness was too high for our single screw extruder to process.
2.4 Characterization
2.4.1 Scanning electron microscopy. To investigate the morphology development of PTFE after melt compounding, the extrudates were first cryo-fractured in liquid nitrogen, then the fractured surface was exposed to chloroform to remove the polymer matrix. The treatment preferentially etches the polymer matrix which is soluble in dichloromethane, leading to the exposure of PTFE component.To observe the morphology of the foams, the extrusion foamed samples were first immersed in liquid nitrogen for 2 h to maintain the cell structure and then fractured in cross section; all samples were sputter-coated with a thin layer of gold (220 nm) before examination. The cell size was determined from the SEM micrographs by using Image Pro Plus software while the cell density N0 (cells per cm3), the number of cells in 1 cubic centimeter of the foamed polymer, was determined from the eqn (1).31
|
 | (1) |
where
n is the number of cells in the SEM micrograph obtained from the Image Pro Plus software;
M is the magnification factor; and
A is the area of the micrograph (cm
2).
2.4.2 Fourier transform infrared (FTIR). FTIR spectra were recorded in transmittance mode using a NEXUS 670 in a spectrometer in a range of 4000–400 cm−1 with a range resolution of 4 cm−1. The extrudates were compressed into thin films with the thickness of 2 mm before characterization.
2.4.3 Differential scanning calorimetry (DSC). Thermal property measurements were performed on a DSC 204C (Netzsch, Germany). The samples sliced from the extruded pellets were first heated from room temperature to 190 °C at a heating rate of 10 °C min−1 and kept isothermally for 5 min to eliminate any thermal history, cooled to 0 °C at a rate of 10 °C min−1 and then reheated to 190 °C at the same rate.
2.4.4 Dynamic mechanical analysis. Thermal dynamical properties of the samples were examined by a flexural mode in a dynamic mechanical analyzer (DMA983, TA instrument). The rectangular samples with a dimension of 60 × 10 × 1 mm (length × width × thickness) were machined from the compressed plates using the blended pellets. Samples were heated from −20 °C to 80 °C at a heating rate of 3 °C min−1 with a frequency of 1 Hz.
2.4.5 Rheological measurements. The rheological properties of all of the samples under oscillatory shear flow were investigated with a Bohlin Gemini 200 Rheometer. A parallel-plate geometry (ϕ = 25 mm) with a fixed gap of 1 mm was selected for all of the tests. The samples were first cut into 25 mm diameter circular films with the thickness of 1 mm. For the frequency sweep and time sweep modes, the strain amplitude was set as 1% to make sure all the samples were tested in the linear viscoelastic region. The frequency sweep was run from high-to-low frequency mode at an angular range of 0.1–100 rad s−1 at a temperature of 160 °C. The time sweep were performed at 160 °C for 30 min, with the angular frequency of 1 rad s−1.
3. Results and discussion
3.1 Morphology of PPC/PS and PPC/PS/PTFE fibrillar blends
The phase morphologies of PPC/PS blends with various PS contents are shown in Fig. 1. The neat PPC (Fig. 1(a)) showed a clear flat surface, while the PPC/PS blends (Fig. 1(b) and (c)) showed clearly two phases indicating immiscibility between PPC and PS. The size of the PS domains was of micrometer order when the PS content was 10% of the blends. As the PS content increased to 30%, the shape of the PS particles evolved from spherical to ellipsoidal particles and some PS domains even formed small continuous domains with zonal distribution. It should be noted that there was no gap between the two phases and their phase boundaries were not very obvious. This means that PPC and PS still have strong interfaces even though they were immiscible.
 |
| Fig. 1 Microstructure of PPC/PS blends: (a) neat PPC, (b) PPC/PS 90/10 and (c) PPC/PS 70/30. The scale bar is 5 μm in the images. | |
Fig. 2(a) is the received PTFE powder and Fig. 2(b) shows the SEM microgram of PTFE particles. It was found that the particles were agglomerated into small clusters and connected with some fibrils rather than separated individually. This means that the original synthesized PTFE was small aggregates instead of nano fibril morphology. However, it has been reported that the PTFE particles would be fibrillated once they are processed with a certain force field.26,32
 |
| Fig. 2 (a) Picture of PTFE powder, (b) morphology of PTFE powder. | |
In this study, the PTFE powder was added into neat PPC and PPC/PS blends as additive and processed using a triple-screw extruder which could provide high shear force during extrusion. The morphologies of the PPC/PS/PTFE composites were shown in Fig. 3. It was noticed from Fig. 3(a) that only a few fibrils could be observed for the 70–30–0.3 sample. This was because the PTFE content was low and most PTFE have been buried in the polymer matrix. Whereas, for the composites with 3 wt% PTFE, as shown in Fig. 3(b), much more PTFE thin fibrils appeared on the surface of the composites. Moreover, there was no agglomerated PTFE particles could be seen from the phase morphology images anymore of these PPC/PS/PTFE composites, which meant that PTFE particles had gone through a fibrillation process during the melt compounding.
 |
| Fig. 3 SEM results of PPC/PS/PTFE composites: (a) PPC/PS/PTFE (70–30–0.3), (b) the morphology of PTFE after etching the polymer phase, (c) PPC/PS/PTFE (70–30–3) and (d) the morphology of PTFE after etching the polymer phase. The scale bar in the insert images in figure (b) and (d) is 500 nm. | |
To observe the morphology of PTFE in the composites, the blends were subjected to a solvent etching process using dichloromethane to dissolve the PPC and PS components. The residual sample was rinsed three times with distilled water followed by drying, gold sputtering and SEM imaging. The images are shown in Fig. 3(b) and (d). The fibrillar morphology of PTFE confirms that PTFE undergoes plastic deformation under elevated temperature and displays nanofibrillar structures with large aspect ratio (diameter less than 200 nm and length longer than 10 μm). Moreover, the PTFE nanofibrils in the matrix polymer entangled and formed a physical nanofibrillar network in the composites. Based on previous studies, when the temperature is above 19 °C, PTFE crystals will show the first transition order from triclinic to hexagonal form which is featured with a brittle-to-ductile transition in the crack propagation behavior. The increases in fracture toughness lead to the formation of stable fibril occurred from the immediate point of precrack tip when the PTFE crystals in hexagonal form are exposed to a small amount of shear, which can cause the packed PTFE crystals to unwind.26,32 Therefore, PTFE in hexagonal phase is able to initiate the stable formation of fibrils for locally shear deform in a continuous extrusion process. The detailed mechanism of fibrillation of solid PTFE have been reported in the previous studies and once these stable fibril is formed, the fibrillar morphology in the matrix cannot be destructed until the blending temperature is increased to above the melting temperature of PTFE.28,33
3.2 Fourier transform infrared spectroscopy analysis
FTIR was used to identify the components and the molecular interactions of the prepared blends and composites.34 Fig. 4 shows the FTIR spectra of neat PPC, PS, PPC/PS blends and PPC/PS/PTFE composites. The characteristic peak of PPC located at 1747 cm−1 ascribed to the stretching vibrations of C
O.35 After blending with PS, the characteristic peaks of PPC were detected in the blends and there were no obvious shifting for the peaks, which indicated that there was no molecular interaction between PPC and PS occurred. This result was consistent with the phase morphology of the PPC/PS blends. For the PPC/PS/PTFE composites as shown in Fig. 4(b), PTFE made little difference on the FTIR spectra of the PPC/PS blends, which might because the content of PTFE was low and most PTFE fibrils were entrapped in the polymer matrix.
 |
| Fig. 4 FTIR spectra of neat PS, PPC, PPC/PS blends and PPC/PS/PTFE composites. | |
3.3 Thermal property analysis
The thermal properties of the PPC/PS blends and PPC/PS/PTFE composites were analyzed via DSC and the second heating segments curves were shown in Fig. 5. Since both PPC and PS were amorphous, the cooling cycle was not measured. The results showed that the Tg for PPC/PS blends slightly shifted to higher temperature with the increase of PS in the blends (from 27.4 °C for neat PPC to 28.9 °C for PPC/PS 70–30). However, after loading PTFE in the polymer matrix, the Tg changed dramatically. It was 28.9 °C for PPC/PS 70–30 sample, while it raised to 34.1 °C for 70–30–0.3 sample and 37.1 °C for 70–30–3 sample, respectively. It was noted that the Tg for PPC/PTFE blends increased slightly by 1 °C, from 27.4 °C to 28.4 °C. The improvement of the Tg of the composites demonstrated that the physical nanofibrillar network formed by PTFE fibrils hindered the movement of polymer molecules, resulting in a higher glass transition temperature of the composites. Moreover, the test also revealed that solely addition of SP or PTFE into the PPC matrix would not affect the thermal property significantly.
 |
| Fig. 5 DSC results of neat PPC, PPC/PS blends, PPC/PTFE composite and PPC/PS/PTFE composites. | |
3.4 Dynamic mechanical analysis
DMA is a very useful technique to study the viscoelastic response of the polymers as well as their composites in a wide range of temperatures. The temperature independence of storage modulus and loss tangent (tan
δ) of the prepared PPC/PS blends and PPC/PS/PTFE composites were measured via DMA and the results are shown in Fig. 6. The storage modulus of all samples declined with increasing temperature, and a sudden reduction occurred in the glass transition region of PPC around 30 °C for all samples. In the glassy state region at −20 °C, the storage modulus of neat PPC was 1806 MPa, while it was 2094 MPa for 90–10 sample and 2731 MPa for 70–30 sample, respectively. When PTFE was incorporated, the storage modulus was further increased. It slightly increased to 2525 MPa for 100–0.3 sample and 3207 MPa for 70–30–0.3 sample, respectively. A dramatic improvement of 392% compared with neat PPC was achieved for 70–30–3 sample. This distinct improvement of storage modulus is barely achieved for PPC composites.
 |
| Fig. 6 Dynamic viscoelastic properties of neat PPC, PPC/PS blends, PPC/PTFE composite and PPC/PS/PTFE composites: (a) storage modulus vs. temperature and (b) tan δ vs. temperature. | |
The storage modulus detected by DMA is known to be related to the stiffness of the polymers. The increase of the storage modulus indicated that the stiffness of composites was improved with the incorporation of PS and PTFE. The results suggested that the presence of well dispersed PS particles (recall Fig. 1) could act as rigid fillers, leading to the enhancement of stiffness. Moreover, the remarkable improvement of the 70–30–3 sample was due to the existence of physical nanofibrillar network formed by PTFE at 3 wt% concentration which stored larger deformation energy.36 At high temperature, in the high elastic state region, the storage modulus curve of neat PPC, 90–10 sample and 100–0.3 sample became flat and the value approached to 10 MPa. However, the storage modulus curves of 70–30 sample and PPC/PS/PTFE composites showed a lower convex in the high-elastic region. This phenomena was resulted from the reinforcement effect of increased PS domains and the physical nanofibrillar network formed by PTFE fibrils in the composites, which effectively hindered the movement of polymer molecular chains in the high-elastic region.37
tan
δ is the ratio of loss and storage moduli and the results are shown in Fig. 6(b). The temperature corresponding to the peak of tan
δ curve is considered as the glass transition temperature (Tg). As can be seen from the figure, with the addition of PS and PTFE in the PPC matrix, the peak shifted to higher temperature due to the reduction of the molecular chain mobility by the PS domain and the PTFE nanofibrillar network, which is agree with the results from DSC test. Moreover, the area underneath the tan
δ curve decreased with the addition of PS in the composites compared with that of neat PPC indicating that the filled composites have less energy absorbing ability than neat PPC.38 However, with the addition of PTFE in the composites, the area underneath the tan
δ curve was increased compared with the PPC/PS blends, demonstrating the damping ability of the material was enhanced due to the physical nanofibrillar network formed by PTFE nanofibrils in the composites.39
3.5 Rheological properties
The rheological properties of the samples were studied to investigate the effects of PS and PTFE on the PPC matrix. As shown in Fig. 7(a), the storage modulus (G′) was enhanced after blending PS into PPC matrix in the whole scan frequency, and the blends with more PS content showed higher G′. When 0.3% PTFE was added in the PPC matrix, the G′ did not enhance much which may because of the low melt strength of PPC or the PTFE failed to form interconnected network. Noticeably, the G′ of the composites was significantly improved after introducing PTFE into the PPC/PS system. The G′ of 70–30–3 composite was about 30 times higher than neat PPC. This was attribute to the rigid PS domains and the physical nanofibrillar network of PTFE nanofibrils in the composites. Similar trends were found for the viscosity (η) results as shown in Fig. 7(b). The viscosities of the PPC/PS/PTFE composites were more than 10 times higher than neat PPC. It is well known that the η of suspension increases with the increase of the solid participate content. Therefore, the PPC/PS/PTFE composites depicted the largest η due to the addition of rigid PS and PTFE fillers. The rheological properties were closely related to the foaming behavior of the polymers and the cells would collapse if the melt strength was too weak as a result from low melt viscosity. The formation of the physical nanofibrillar network of PTFE nanofibrils within the polymer matrix resist the matrix molecular chain movement by topological constraints or physical entanglements, thus bring to the melt strength of polymers an enhancement via strain-induced hardening effect.37 This strain-induced hardening effect, which could prevent CO2 gas escaping and cell rupture and collapse, is highly favorable in the foaming process according to the research conducted by C. B. Park et al.28
 |
| Fig. 7 Rheological properties in frequency sweep mode of neat PPC and PPC/PS/PTFE composites. | |
Fig. 8(a) and (b) show the time sweep results of G′ and η respectively, from which it was found that the G′ and η results showed the same trends for different samples. As the test time increase, G′ and η of neat PPC decreased rapidly indicating molecular chain relaxation, which was ascribed to the pseudoplastic fluid behavior of PPC. This pronounced viscosity reduction across time of PPC was unfavorable for foaming process. With the addition of PS and especially PTFE, the G′ and η were not only improved, but also became more stable. The G′ and η of the 70–30–0.3 sample was one order higher than that of neat PPC. The significant improvement of rheological properties by PTFE was because the physical nanofibrillar network endowed by PTFE fibrils prevented the disentangles of polymer molecular chains, which would be favorable for the foaming properties of the composites. These results demonstrated that the loading of PS and PTFE played a pivotal role in affecting the rheological behavior of the composites, and the dramatic viscosity enhancement of PPC was never achieved in other publications.
 |
| Fig. 8 Time sweep results of (a) storage modulus and (b) viscosity as a function of time. | |
3.6 Extrusion foaming behavior
As discussed above, the dispersed rigid PS domain and the PTFE nanofibrillar network within PPC matrix caused significant improvement in thermal, dynamic mechanical, and rheological properties. This special morphology, therefore, may be influential for extrusion foaming behavior. The cell morphology images, corresponding cell diameter distribution, and average cell diameter and cell density statistical results of the extrusion foamed samples were shown in Fig. 9, 10, and 11 respectively. Expectably, neat PPC (Fig. 9(a)) showed small cells with thick cell walls because of its low melt strength and CO2 solubility. For the 90–10 foam (Fig. 9(b)), the size of cells was increased and the cell wall thickness was reduced. When the PS content increased to 30%, the cell size was further increased and the cell density was decreased according to Fig. 11. This improvement was attribute to the PS phase which enhanced the melt strength and the CO2 solubility of the system during extrusion process. Moreover, the interphases between PS and PPC would act as heterogeneous nucleation sites where cells are easier to nucleate and grow up.40,41 The cell density distribution of 70–30 foams was wider than neat PPC and 90–10 foams as shown in Fig. 10. This might be caused by the unequal size of the dispersed PS domains. In addition, it was surprisingly found from Fig. 9(d) and (e) that the average cell diameter was greatly reduced and the cell density was significantly increased after addition of 0.3 wt% PTFE. With the involvement of PTFE nanofibrillar network, the average cell diameter of 70–30–0.3 foams remarkably reduced to 1.2 μm compared with 44.5 μm for neat PPC, and the cell density achieved enhancement about four orders of magnitude.
 |
| Fig. 9 SEM micrographs of the extrusion foamed samples: (a) PPC; (b) PPC/PS (90–10); (c) PPC/PS (70–30); (d) PPC/PTFE (100–0.3); (e) PPC/PS/PTFE (70–30–0.3) and (f) the enlarged image of figure (e). The scale bars are 100 μm for image (a) to (e). The scale bar for image (f) is 5 μm and it is 500 nm for the inset high magnification image. | |
 |
| Fig. 10 Cell diameter distribution of the extrusion foamed samples: (a) PPC; (b) PPC/PS (90–10); (c) PPC/PS (70–30); (d) PPC/PTFE (100–0.3) and (e) PPC/PS/PTFE (70–30–0.3). | |
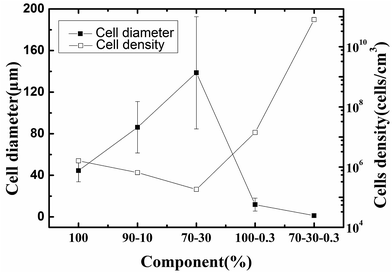 |
| Fig. 11 The average cell diameter and cell density statistical results of various extrusion foams. | |
This prominent change in foaming behavior after involving PTFE nanofibrils can be elucidated with the classical nucleation theory.40 It is presumed that the polymer/gas solution is dilute prior to cell nucleation, there is a free energy (ΔG) barrier required for cell nucleation to initiate. It is also believed that the nuclei size have to exceed a critical radius (Rcr) in order to grow into cells, otherwise, they will collapse spontaneously. The ΔG and Rcr were given by eqn (2) and (3) in the previous studies:40,42–44
|
 | (2) |
|
 | (3) |
where,
γlg is the surface tension at polymer/gas interface,
F(
θc) is a geometric factor that equals to the ratio of the volume of a heterogeneously nucleated bubble to that of a spherical bubble having the same radius of curvature,
H is the Henry's law constant,
C is the gas concentration,
Psys is the system pressure and Δ
Plocal is the local pressure variations.
According to eqn (2) and (3), it is expected that the free energy barrier for cell nucleation and critical radius can be reduced by increasing the gas concentration in the system, which would result in incensement of cell density. The introduction of PTFE nanofibrillar network, on one hand, may have improved the gas absorption due to its CO2-philic property as reported elsewhere.28 On the other hand, the topological constraints given by PTFE nanofibrillar network may have prevented the fibrils flow along the polymer melts. Consequently, the PTFE network was faced with a macroscopic strain which generated a tensile stress.28,37,45 When the tensile stress was applied to the flow of polymer matrix, a negative local pressure occurs, i.e. ΔPlocal < 0. As a result, the cell nucleation efficiency was enhanced for PPC/PS/PTFE composites. Furthermore, the presence of the solid-state PTFE nanofibrils could increase the number of the cell nucleation cites to reduce the heterogeneous nucleation energy barrier (ΔG), which could further enhance the cell density. While the network of PTFE fibrils imposed the topological constraints on the cell growth by improving the system viscosity. By comparing 100–0.3 and 70–30–0.3 foams, the effect of PS component could be further emphasized. PPC alone could not sustain CO2 expansion and prevent CO2 diffusing out of the matrix even with the addition of PTFE. The composite storage modulus and viscosity were enhanced dramatically when 30% of PS component was blended in the matrix. The melt strength as well as the CO2 affinity provided by PS portion is important to enhance the system foamability. Consequently, the PPC/PS/PTFE composites containing PS dispersed domains and PTFE nanofibrillar network achieved the small cell size with greatly improved cell density, which supposed to be influential for mechanical property enhancement.
Moreover, the steady pressure monitored at the die entrance for various materials was listed in Table 2. Normally, high system pressure results in high cell density for the same material because of the limited premature cell growth under high pressure. Noticeably, in this study, the change of pressure was in the same trend of viscosity variation, which meant that the system viscosity, which determined by the material combination, significantly affected the die pressure in single screw extrusion foaming process under the same processing conditions. This results suggested that the material components were the most important factor that determines the foaming behavior.
Table 2 Pressure monitored at the die entrance for extrusion foaming of various samples
Sample |
PPC |
90–10 |
70–30 |
100–0.3 |
70–30–0.3 |
Die pressure (MPa) |
5 |
7 |
10 |
8 |
17 |
3.7 Compressive properties of the foams
The compressive properties of the extrusion foamed materials were measured and results are showed in Fig. 12. Remarkable improvement of compressive property was achieved for the PPC/PS blended and PPC/PS/PTFE composite foams compared with neat PPC and PPC/PTFE foams. It was noticed from Fig. 12(a) that the 70–30 and 70–30–0.3 samples showed clear yield peaks at about 8% strain indicating the presence of elastic deformation before yielding, which means these foams can sustain high compressive force at small deformation. The yielding was absent for PPC and 100–0.3 foams, which may due to the lacking of high modulus PS phase. The strength at 8% strain for the 70–30–0.3 foam was 34 times higher than that of neat PPC. From the statistical data, we found both compressive modulus and compressive strength at 50% strain were significantly enhanced after addition of PS and PTFE in the PPC matrix. There are two possible reasons for this distinct improvement. First, the introduced PS rigid domains and the PTFE nanofibrillar network enhanced the stiffness substrate material just as the improvement showed in the dynamic mechanical tests. Second, the significantly increased cell density for the PPC/PS/PTFE composite foams could result in rapid and homogenous stress transfer which correspond to the improvement of compressive property.
 |
| Fig. 12 Compression test results of extrusion foams: (a) representative stress vs. strain curves; (b) compressive modulus and strength statistical results. | |
4. Conclusions
In this study, we introduced PS and PTFE into PPC matrix by melt compounding via a triple-screw extruder. PS was immiscible with PPC and formed dispersion phase, and PTFE were in situ fibrillated into nanofibrillar network within PPC/PS matrix. With this special ternary phase morphology, remarkable changes in various properties of the PPC/PS/PTFE composites were achieved. The DSC results demonstrated that the Tg of PPC was increased by 12 °C in the composites compared with neat PPC. The rigid PS dispersion domain and the physical network formed by PTFE nanofibrils resulted in significant improvement of the dynamic mechanical property and rheological property. For the PPC/PS/PTFE composite containing 30% PS and 3 wt% PTFE, its storage modulus in DMA test was 392% higher and its complex viscosity was 1676% higher than that of neat PPC. Moreover, the physical network formed by PTFE nanofibrils effectively prevented the shear-thinning behavior of the polymer matrix, which is favorable for preventing cell collapse and cell rupture during foaming. The average cell diameter of the PPC/PS/PTFE composites extrusion foams was 1.2 μm, while it was 44.5 μm for PPC foams. On the contrary, the cell density of PPC/PS/PTFE foams was four orders of magnitude increase compared with PPC foams. The compressive modulus and strength of the PPC/PS/PTFE composites foams were 58 and 34 times higher than that of neat PPC foams. Therefore, in this study, we not only purposed a method to prepare PPC/PS/PTFE ternary composites with excellent thermal, rheological and dynamic mechanical properties, but also solved the foaming problems of PPC in a continuous method and provided high performance PPC/PS/PTFE composite foams.
Acknowledgements
The authors would like to acknowledge the financial support from the National Science Foundation of China (21174044, 51573063 and 51503069), the Guangdong Nature Science Foundation (S2013020013855), the Guangdong Public Welfare Research Fund (2014B010104004), the National Basic Research Development Program 973 in China (2012CB025902), and the Fundamental Research Funds for the Central Universities (2015ZM093 and 2015ZM099).
References
- L. T. Guan, F. G. Du, G. Z. Wang, Y. K. Chen, M. Xiao, S. J. Wang and Y. Z. Meng, J. Polym. Res., 2007, 14, 245–251 CrossRef CAS.
- A. Salerno, E. Di Maio, S. Iannace and P. A. Netti, J. Supercrit. Fluids, 2011, 58, 158–167 CrossRef CAS.
- K. A. Arora, A. J. Lesser and T. J. McCarthy, Macromolecules, 1998, 31, 4614–4620 CrossRef CAS.
- X. Cao, L. J. Lee, T. Widya and C. Macosko, Polymer, 2005, 46, 775–783 CrossRef CAS.
- S. Doroudiani, C. B. Park and M. T. Kortschot, Polym. Eng. Sci., 1998, 38, 1205–1215 Search PubMed.
- M. Lee, C. Tzoganakis and C. B. Park, Polym. Eng. Sci., 1998, 38, 1112 CAS.
- C. B. Park and L. K. Cheung, Polym. Eng. Sci., 1997, 37, 1 CAS.
- M. Y. Wang, N. Q. Zhou and S. P. Wen, Polym.-Plast. Technol. Eng., 2009, 48, 303–309 CrossRef CAS.
- Y. Chen, R. Ye, X. Li and J. Wang, Ind. Crops Prod., 2013, 49, 81–87 CrossRef CAS.
- D. Garlotta, J. Polym. Environ., 2001, 9, 63–84 CrossRef CAS.
- D. Sendil, I. Gürsel, D. L. Wise and V. Hasırcı, J. Controlled Release, 1999, 59, 207–217 CrossRef CAS PubMed.
- G. A. Luinstra and E. Borchardt, Adv. Polym. Sci., 2012, 245, 29–48 Search PubMed.
- L. T. Guan, M. Xiao, Y. Z. Meng and R. K. Y. Li, Polym. Eng. Sci., 2006, 46, 153–159 CAS.
- G. Yang, J. Su, J. Gao, X. Hu, C. Geng and Q. Fu, J. Supercrit. Fluids, 2013, 73, 1–9 CrossRef CAS.
- S. Lin, W. Yu, X. Wang and C. Zhou, Ind. Eng. Chem. Res., 2014, 53, 18411–18419 CrossRef CAS.
- S. J. Yoo, S. H. Lee, M. Jeon, H. S. Lee and W. N. Kim, Macromol. Res., 2013, 21, 1182–1187 CrossRef CAS.
- J. Yang, M. Wu, F. Chen, Z. Fei and M. Zhong, J. Supercrit. Fluids, 2011, 56, 201–207 CrossRef CAS.
- P. Yu, G. Liu, K. Li, A. Huang, B. Chen, H. Mi, S. Zhang and X. Peng, Polym. Compos., 2015 DOI:10.1002/pc.23361.
- L. Huihong, P. Lisha, L. Qiang, X. Nai, L. Lingbin, P. Sujuan and F. Songbao, e-Polym., 2010, 10, 390–398 Search PubMed.
- X. Han, K. W. Koelling and D. L. Tomasko, Polym. Eng. Sci., 2002, 42, 2094 CAS.
- J. Xu, R. K.-Y. Li and Y. Meng, Mater. Res. Bull., 2006, 41, 244–252 CrossRef CAS.
- X. Li, Y. Meng, S. Wang, A. V. Rajulu and S. Tjong, J. Polym. Sci., Part B: Polym. Phys., 2004, 42, 666–675 CrossRef CAS.
- W. Chen, M. Pang, M. Xiao, S. Wang, L. Wen and Y. Meng, J. Reinf. Plast. Compos., 2010, 29, 1545–1550 CrossRef CAS.
- P. Yu, H. Y. Mi, A. Huang, X. Liu, B. Y. Chen, S. D. Zhang and X. F. Peng, J. Appl. Polym. Sci., 2015, 132 DOI:10.1002/app.42248.
- M. S. Widmer, P. K. Gupta, L. Lu, R. K. Meszlenyi, G. R. Evans, K. Brandt, T. Savel, A. Gurlek, C. W. Patrick and A. G. Mikos, Biomaterials, 1998, 19, 1945–1955 CrossRef CAS PubMed.
- E. N. Brown and D. M. Dattelbaum, Polymer, 2005, 46, 3056–3068 CrossRef CAS.
- Q. Wang, F. Cao and Q. Chen, Green Chem., 2005, 7, 733 RSC.
- A. Rizvi, A. Tabatabaei, M. R. Barzegari, S. H. Mahmood and C. B. Park, Polymer, 2013, 54, 4645–4652 CrossRef CAS.
- Z. Huang, C. Shi, R. Enick and E. Beckman, Chem. Mater., 2002, 14, 4273–4280 CrossRef CAS.
- A. Rizvi, R. K. M. Chu, J. H. Lee and C. B. Park, ACS Appl. Mater. Interfaces, 2014, 6, 21131–21140 CAS.
- X. Han, C. Zeng, L. J. Lee, K. W. Koelling and D. L. Tomasko, Polym. Eng. Sci., 2003, 43, 1261–1275 CAS.
- E. Clark and L. Muus, Z. Kristallogr.-Cryst. Mater., 1962, 117, 119–127 CrossRef CAS.
- M. A. B. M. Ali, S. Nobukawa and M. Yamaguchi, Pure Appl. Chem., 2011, 83, 1819–1830 CrossRef.
- S. Peng, X. Wang and L. Dong, Polym. Compos., 2005, 26, 37–41 CrossRef CAS.
- B. Fei, C. Chen, S. Peng, X. Zhao, X. Wang and L. Dong, Polym. Int., 2004, 53, 2092–2098 CrossRef CAS.
- S. R. Raghavan and J. F. Douglas, Soft Matter, 2012, 8, 8539 RSC.
- T. Yokohara, S. Nobukawa and M. Yamaguchi, J. Rheol., 2011, 55, 1205–1218 CrossRef CAS.
- A. Javadi, A. J. Kramschuster, S. Pilla, J. Lee, S. Gong and L.-S. Turng, Polym. Eng. Sci., 2010, 50, 1440 CAS.
- L. A. Pothan, Z. Oommen and S. Thomas, Compos. Sci. Technol., 2003, 63, 283–293 CrossRef CAS.
- J. W. Gibbs, The scientific papers of J. Willard Gibbs, Longmans, Green and Company, 1906 Search PubMed.
- G. Zhang, Y. Wang, H. Xing, J. Qiu, J. Gong, K. Yao, H. Tan, Z. Jiang and T. Tang, RSC Adv., 2015, 5, 27181–27189 RSC.
- S. N. Leung, A. Wong, C. B. Park and J. H. Zong, J. Appl. Polym. Sci., 2008, 108, 3997–4003 CrossRef CAS.
- S. N. Leung, A. Wong, Q. Guo, C. B. Park and J. H. Zong, Chem. Eng. Sci., 2009, 64, 4899–4907 CrossRef CAS.
- C. Ward and A. Tucker, J. Appl. Phys., 1975, 46, 233–238 CrossRef CAS.
- H. M. Laun, Colloid Polym. Sci., 1984, 262, 257–269 CAS.
|
This journal is © The Royal Society of Chemistry 2016 |
Click here to see how this site uses Cookies. View our privacy policy here.