DOI:
10.1039/C5PY01572C
(Minireview)
Polym. Chem., 2016,
7, 11-25
Synthesis, properties and performance of organic polymers employed in flocculation applications
Received
29th September 2015
, Accepted 31st October 2015
First published on 3rd November 2015
Abstract
Flocculation is a common technique that is widely used in many industrial applications to promote solid–liquid separation processes. The addition of a polymeric flocculant allows for the destabilization of suspended colloidal particles, and thus significantly increases their sedimentation rate. Polymeric flocculants are generally divided into four categories, which include non-ionic, cationic, anionic, and amphoteric polymers. This minireview article summarises important information on the recent design and synthesis of polymeric materials from these four categories. In addition, their properties and flocculation efficiency are also presented and discussed.
 Vu H. Dao | Vu Dao received his Bachelor of Engineering (Honours) and Bachelor of Science from Monash University, Australia, in 2014. His major areas of study were in the fields of Chemical Engineering and Chemistry. He is currently undertaking his PhD studies in polymer chemistry, under the supervision of Dr Kei Saito and Professor Neil Cameron at Monash University. His research interests are focused on the design and synthesis of novel polymeric materials for usage in a wide range of industrial applications. |
 Neil R. Cameron | Neil Cameron undertook his BSc and PhD at the University of Strathclyde in Glasgow. Following two post-doctoral periods, first in Eindhoven then at Heriot Watt University, he was appointed as a Lecturer (Assistant Professor) at Durham University in 1997. In 2005 he was promoted to Reader (Associate Professor) and in October 2008 he took up the position of Professor of Bioactive Chemistry in the same department. In September 2014 he became the Monash Warwick Professor of Polymer Materials based at Monash University (Australia) and the University of Warwick (UK). His research is focused on the preparation of novel polymeric materials, with particular emphasis on scaffolds for tissue engineering, self-assembling polypeptides, peptide-synthetic polymer hybrids and sugar-containing polymers (glycopolymers). |
 Kei Saito | Dr Kei Saito is currently a Lecturer at the School of Chemistry, Faculty of Science, Monash University, Australia. He received his BEng. (2000), MEng. (2002) and Ph.D. (2004) degrees from Waseda University, Tokyo, Japan. From 2004–2005, he was a Research Associate at the 21COE Centre for Practical Nano-Chemistry, Department of Applied Chemistry, Waseda University, Japan. From 2005–2007, he was a Postdoctoral fellow, at the Centre for Green Chemistry, University of Massachusetts Lowell, USA. His research interests are in developing new synthesis and production methods for novel sustainable/environment benign polymeric materials. |
1. Introduction
Over the past few decades, a higher demand for industrial products has led to a significant increase in generation rate of industrial effluents. The wastewater coming from these industrial processes contains large quantities of finely dispersed solids, organic and inorganic particles, as well as metal ions and other impurities.1,2 Separation and removal of these particles is challenging due to their small particle size and the presence of surface charges, which create interparticle repulsion, and thus a stable colloidal suspension is established over an extended period of time.3–5 Amongst numerous solid–liquid separation processes, flocculation is commonly used to promote and optimize solid–liquid separation of colloidal suspensions in many industrial processes, such as mining and mineral processing, wastewater treatment, pulp and paper processing, and biotechnology.6
1.1. Type of flocculants
The term flocculant generally includes both natural and synthetic water-soluble polymers, and the latter has gained tremendous interest from industry due to their ability to create strong and large solid aggregates, allowing for the solid flocs to be easily removed from the wastewater.6 In addition, these flocculants are highly cost efficient due to their low dosage requirement and easy handling process.7,8 However, as synthetic flocculants are usually non-biodegradable, the majority of recent studies have extensively focused on combining the best properties of both synthetic and natural polymers, to potentially create environmentally friendly flocculants, while having longer shelf life and higher efficiency compared to traditional natural flocculants.2 The term flocculation efficiency used in this review refers to a polymer's ability to induce optimal flocculation, and this factor is typically evaluated based on two main factors: clarity of the upper flow and settlement rate of the flocculated particles.9
Polymeric flocculants are typically classified based on their ionic character: non-ionic, cationic, anionic and amphoteric.2 Commercial flocculants are often based on polyacrylamide (PAM) and its derivatives since acrylamide (AM) is one of the most reactive monomers to undergo radical polymerization, thus allowing ultra-high molecular weight polymers to be built easily.5 In addition, AM is cost effective and highly soluble in water (2150 g L−1 at 30 °C).5 Apart from PAM, non-ionic flocculants are also based on polyethylene oxide (PEO), polyvinyl alcohol and polyvinylpyrrolidone.6 Cationic flocculants are often based on polydiallyldimethylammonium chloride, cationic polyacrylamide (CPAM) and polyethylene imine, and most anionic flocculants are homopolymers or AM copolymers of ammonium or alkali metal salts of acrylic acid (AA).1,6 Anionic monomers such as methacrylic acid and 2-acrylamido-2-methyl-1-propanesulfonic acid (AMPS) are also often used in copolymerization with AM to produce anionic flocculants.1 Amphoteric polymers contain both cationic and anionic functional groups, and have recently emerged as promising candidates for flocculation applications.
1.2. Mechanisms of flocculation
Numerous mechanisms for flocculation have been studied and reported in various literatures; the most common of which include charge neutralization, polymer bridging and electrostatic patch.1–3,6,8 Charge neutralization is most effective when the polymer has an opposite charge to that of the colloidal particles.6 This therefore allows for neutralization of the particle's surface charge, and hence destabilizes the colloidal suspension to promote agglomeration.1 Numerous practical cases have shown that hydrophobic colloidal particles and other impurities commonly have negatively charged surface, and therefore cationic polymers favour charge neutralization as the main flocculation mechanisms.2
When a long chain polymer is added into the colloidal suspension, adsorption of the polymer onto the surface of the contaminant occurs through hydrogen bonding, electrostatic interaction, van der Waals forces, or chemical bonding.1 Polymer bridging is most effective when the polymer has a linear structure and a high molecular weight.2,8 Once adsorbed, extensive elongation of the dangling polymer chains into the aqueous environment allow for interaction and polymer bridging between contaminant particles, which would then induce flocculation.8 As different types of polymer adsorb differently, ionic strength can also have a major impact on the effectiveness of polymer bridging.8
Electrostatic patch mechanism occurs when a lower molecular weight polymer with high charge density and opposite charge as the colloidal particles is used. The high charge density allows the polymeric chain to be readily adsorbed onto weakly charged negative surface.3,8 This then induces localised charge reversal on each particle, thereby allowing ‘patches’ or localised areas with opposite charge between different particles to interact and form flocs.2 The schematic views of these mechanisms are outlined in Scheme 1.
 |
| Scheme 1 Schematic representation of colloidal suspension flocculation by: (a) charge neutralization, (b) polymer adsorption and bridging, and (c) electrostatic patch. | |
1.3. Aim and scope of the review
The present review article will present and summarize important information on the synthesis of organic polymers that were tested as flocculants in recent studies. This review is arranged into four main sections based on the ionic characteristics of these flocculants. It is aimed to provide a summary and quick insight into recent developments on the design and synthesis of polymeric flocculants. In addition, the important properties and flocculation efficiency of these polymers are also presented and discussed.
2. Non-ionic flocculants
Polymers are considered as non-ionic flocculants if they contain less than 1% of charged functional groups.10 This almost-neutral overall charge arises from a small degree of hydrolysis that can occur during the synthesis of the polymer.8 Non-ionic polymers are commonly used as flocculants in mineral processing, as well as the treatment of industrial effluents and potable wastewater.1,3
Table 1 provides a summary of the polymerization technique and the flocculation testing medium for non-ionic polymeric flocculants 1–26.
Table 1 Summary of the polymerization technique and the testing medium of non-ionic polymeric materials which were utilised as flocculating agents in previous studies
Entry |
Polymer structurea |
T.o.Pb |
Testing medium |
Ref. |
Abbreviations: Ag, agar; Bar, barley; Cas, casein; CMCs, carboxymethyl chitosan; CMG, carboxymethyl guar gum; CMS, carboxymethyl starch; CMT, carboxymethyl tamarind; Cs, chitosan; Dex, dextran; Dxt, dextrin; GGh, gum ghatti; HPMC, hydroxypropyl methyl cellulose; In, inulin; kCr, k-carrageenan; Oat, oatmeal; Psy, psyllium; SA, sodium alginate; St, starch; TKP, tamarind kernel polysaccharide.
Type of polymerization (T.o.P) abbreviations: CRG, conventional redox grafting; FRP, free radical polymerization; GRR, gamma ray radiation; MWA, microwave assisted; MWI, microwave initiated.
|
1 |
|
CRG |
Municipal sewage wastewater |
12
|
MWI |
2 |
|
MWA |
0.25 wt% kaolin suspension |
11
|
3 |
|
FRP |
0.25 wt% kaolin suspension; 0.25 wt% iron ore suspension; mine wastewater |
14
|
4 |
|
CRG |
Municipal sewage wastewater; 0.25 wt% kaolin suspension; methylene blue solution |
18, 19
|
MWA |
5 |
|
MWA |
Municipal sewage wastewater; 0.25 wt% kaolin suspension |
20
|
6 |
|
GRR |
0.25 wt% kaolin suspension |
21
|
7 |
|
CRG |
0.10 wt% kaolin suspension |
23
|
8 |
|
FRP |
1 wt% coal fine suspension |
22
|
9 |
|
FRP |
1 wt% coal fine suspension |
24
|
10 |
|
CRG |
Municipal sewage wastewater; 0.25 wt% kaolin suspension |
25, 26
|
MWA |
11 |
|
MWI |
Municipal sewage wastewater; 0.25 wt% kaolin suspension; 1 wt% coal fine suspension; river water |
27, 28
|
MWA |
12 |
|
CRG |
0.25 wt% kaolin suspension; dyeing wastewater |
29, 30
|
13 |
|
MWA |
1 wt% coal fine suspension |
31
|
14 |
|
FRP |
1 wt% coal fine suspension |
32
|
15 |
|
FRP |
1 wt% coal fine suspension |
33
|
16 |
|
CRG |
1 wt% kaolin suspension |
34
|
17 |
|
MWA |
3 wt% kaolin suspension |
35
|
18 |
|
MWA |
1 wt% coal fine suspension |
36
|
19 |
|
MWI |
0.25 wt% kaolin suspension; 1 wt% coal fine suspension |
37
|
20 |
|
MWA |
0.25 wt% kaolin suspension |
38
|
21 |
|
CRG |
Municipal sewage wastewater; 0.25 wt% kaolin suspension; 1 wt% coal fine suspension; 1 wt% iron ore suspension |
39
|
22 |
|
CRG |
Municipal sewage wastewater; 0.25 wt% kaolin suspension |
40
|
23 |
|
CRG |
1 wt% coal fine suspension |
41
|
24 |
|
CRG |
Municipal sewage wastewater; textile industry wastewater; 0.25 wt% kaolin suspension |
42, 43
|
MWI |
MWA |
25 |
|
CRG |
0.25 wt% kaolin suspension |
44
|
26 |
|
MWI |
1 wt% coal fine suspension |
45
|
2.1. Modified starch
Graft copolymerization of natural polysaccharides such as starch has become an important foundation for the development of polymeric materials with applications across many fields of science and technology.11 Several research groups have attempted to synthesize grafted polysaccharides in order to improve the flocculation efficiency of the respective natural biopolymer. Sen et al. reported the synthesis of polymer 1 by grafting PAM onto carboxymethyl starch using both a conventional redox grafting (CRG) method and a microwave initiated (MWI) method.12 Similarly, a recent study conducted by Mishra et al. reported microwave assisted (MWA) synthesis of PAM grafted natural starch to produce polymer 2.11 All of these methods involved the initial formation of free radicals on the polysaccharide backbone prior to the polymerization of the monomer (Scheme 2).11,12 The same notation used in Scheme 2 will be used for subsequent natural polymers in this review article. MWI/MWA synthesis of both polymers 1 and 2 was shown to be quicker, more reliable and reproducible compared to the CRG method. In addition, this method produced higher quality copolymer products with higher molecular weight, thereby higher flocculation efficiency was observed.11,12
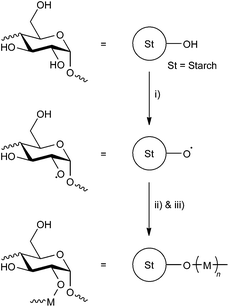 |
| Scheme 2 Example mechanistic pathway for the synthesis of starch graft copolymer via: (i) formation of free radical on the polysaccharide backbone, (ii) propagation of monomer M, and (iii) termination of graft copolymerization. | |
Polymers 1 and 2 were also shown to have better flocculation efficiency compared to carboxymethyl starch and natural starch, respectively.11,12 These results were in agreement with Singh's Easy Approachability Model.7,13 This model stated that grafted polysaccharides have superior performance in comparison to its respective unmodified polysaccharide due to them having a “comb” like structure, which allowed the grafted chains to further approach and capture metallic and non-metallic contaminants at a significantly higher efficiency.13
2.2. Modified cellulose
A few studies have directed their focus on modifying cellulose-based materials to develop high performance water-soluble polymeric flocculants. For example, PAM chains were grafted onto a hydroxypropyl methyl cellulose (HPMC) backbone using free radical polymerization (FRP) with multiple reaction parameters to generate different grades of polymer 3.14 A particular grade of 3 was found to be much more effective as a flocculant compared to the rest, as well as unmodified HPMC and synthetic PAM, due to its high percentage of grafting and large hydrodynamic radius.14 This was in agreement with a flocculation model previously developed by the same group (Brostow, Pal and Singh Model of Flocculation), which suggested that a large radius of gyration would correspond to high flocculation efficiency.15 In addition, the type of grafted synthetic polymer can affect the solvency of the original natural polymer.16 For example, poly(methyl acrylate) grafted onto cellulose showed significantly lower affinity towards polar solvents. This was ascribed to blockage of hydroxyl groups which shielded active sites from interacting with hydrophilic solvents.16
2.3. Modified gum
Guar gum and its derivatives such as carboxymethyl guar gum are versatile naturally-occurring polymers with various applications in the oil and textile industries.17 Minimal attention was directed towards using modified guar gum as flocculant until Pal et al. and Adhikary et al. introduced the synthesis of polymer 4 by using both the CRG and MWA methods.18,19 Apart from guar gum, flocculation efficiency of grafted gum ghatti was also investigated by Rani et al. where AM was used to produce polymeric flocculant 5.20 As expected, 4 and 5 demonstrated better flocculation efficiency than their original polysaccharides, especially when the MWA method was used. In addition to other advantageous factors, compared to CRG, grafting with microwave irradiation does not generate the free radical by chain opening of the polysaccharide backbone; therefore the product polymer retains its rigidity, allowing for further extension of the PAM chains into the aqueous solution to capture more contaminants.18
2.4. Modified chitosan
Chitosan is considered to be a biodegradable and non-toxic material.21 In spite of this, chitosan is only readily soluble in acidic solution due to its strong inter- and intramolecular hydrogen bonding, and therefore there are restrictions in exploiting it for industrial applications such as flocculation.21,22 Chitosan and carboxymethyl chitosan's solubility and flocculation efficiency have been improved by multiple research groups, through grafting of PAM,21,23N,N-dimethylacrylamide (DMA),22 and N-vinylpyrrolidone (NVP),24 to synthesize polymers 6–9. In contrast to previous grafting approaches, 6 was synthesized using a gamma ray radiation (GRR) method due to its high efficiency and low level of contaminations by chemical initiators.21 Both 8 and 9 were synthesized by FRP in acetic acid using potassium peroxymonosulfate and potassium bromate as initiators, respectively.22,24
2.5. Other modified natural polymers
Apart from starch, cellulose, gum and chitosan, previous studies had also focused on the synthesis and flocculation efficiency of various synthetic polymers grafted onto other polysaccharides such as agar (10, 11),25–28 sodium alginate (12, 13),29–31 k-carrageenan (14, 15),32,33 dextran (16),34 dextrin (17),35 inulin (18),36 psyllium (19, 20),37,38 oatmeal (21, 22),39,40 barley (23),41 tamarind kernel polysaccharide (24),42,43 carboxymethyl tamarind (25),44 In addition to these polysaccharides, Sinha et al. conducted a graft polymerization of an amphiphilic protein, casein, to produced polymer 26.45 Various monomers including AM, DMA, NVP, 2-hydroxyethylmethacrylate, and methyl methacrylate (MMA) were used in these studies for the synthesis of grafted polysaccharide polymers. An optimum dosage was often observed for each of the polymeric flocculants.25,27 This behaviour was ascribed to the polymer bridging mechanism associated with flocculation. Beyond the optimum dosage, there is insufficient space for polymer bridging between particles, which leads to a reduction in flocculation efficiency.25,27
It is difficult to present an accurate comparison between these non-ionic flocculants, as well as subsequent cationic, anionic and amphoteric flocculants mentioned in this review article. Flocculation is a complex process and the flocculation efficiency is significantly dependent on a variety of factors, including but not limited to pH and ionic strength of the solution, agitation rate, particle size, charge density, molecular weight and dosage of the polymer.10,46,47 In addition, the mineral composition, and type and addition sequence of the flocculating agents also play an important role in successful destabilization of the colloidal particles.9 Any attempt at comparing these flocculants against one another would be inadequate as there are many inconsistencies in flocculation performance analysis across different studies.
3. Cationic flocculants
Water-soluble cationic polymers are typically categorised into three groups: ammonium, sulfonium and phosphonium quaternaries.10 Cationic polymers can bind strongly to negatively charged particles, and thus these polymers are often used in a wide range of industrial applications. These include wastewater and sludge treatment, paper production industry, oily water clarification, textile industry, paint manufacturing, dairy processing, and biotechnology.1,3,10
Table 2 provides a summary of the polymerization technique and the flocculation testing medium for cationic polymeric flocculants 27–59.
Table 2 Summary of the polymerization technique and the testing medium of cationic polymeric materials which were utilised as flocculating agents in previous studies
Entry |
Polymer structurea |
T.o.Pb |
Testing medium |
Ref. |
Abbreviations: Amp, amylopectin; CC, corn cob; CMCs, carboxymethyl chitosan; CMG, carboxymethyl guar gum; Cs, chitosan; GG, guar gum; Gly, glycogen; In, inulin; Pul, pullulan; Sal, salep; St, starch; TKP, tamarind kernel polysaccharide; Xyl, xylan.
Type of polymerization (T.o.P) abbreviations: ADP, aqueous dispersion polymerization; CRG, conventional redox grafting; EP, emulsion polymerization; FRP, free radical polymerization; GRR, gamma ray radiation; IEP, inverse emulsion polymerization; MFRP, micellar free radical polymerization; N/A, not applicable; UVI, ultraviolet irradiation.
|
27 |
|
IEP |
Reactive brilliant red X-3B dye; 0.10 wt% kaolin suspension |
50
|
28 |
|
MFRP |
Oily wastewater |
51
|
29 |
|
IEP |
Reactive brilliant red X-3B dye |
52
|
30 |
|
UVI |
Textile sewage sludge; waste-activated sludge |
53, 54
|
31 |
|
ADP |
Oily wastewater |
55
|
32 |
|
ADP |
0.25 wt% kaolin suspension |
56, 57
|
33 |
|
FRP |
River water |
58
|
34 |
|
EP |
Clay slurry; municipal biological sludge; polymer plant sludge; refinery wastewater |
5
|
35 |
|
FRP |
0.30 wt% bentonite solution; 2 wt% suspension of animal slurries |
59
|
36 |
|
N/A |
Reactive brilliant red KE-3B dye |
60
|
37 |
|
N/A |
C.I. reactive red 141 dye; C.I. acid blue 341 dye; C.I. acid red 1 dye |
61
|
38 |
|
FRP |
Refinery wastewater; paper mill wastewater |
62
|
39 |
|
GRR |
0.60 wt% kaolin suspension |
63
|
40 |
|
FRP |
Municipal sewage and sludge; 2 wt% kaolin suspension |
64–66
|
41 |
|
FRP |
0.25 wt% kaolin suspension |
67
|
42 |
|
FRP |
Synthetic copper and/or tetracycline wastewaters |
68
|
43 |
|
N/A |
Synthetic copper and/or tetracycline wastewaters |
69
|
44 |
|
GRR |
0.25 wt% kaolin suspension |
70
|
45 |
|
GRR |
0.10 wt% and 0.25 wt% kaolin suspensions; pulp mill wastewater; kaolin – humic acid solution |
71–73
|
FRP |
46 |
|
CRG |
C.I. reactive orange 5 dye; C.I. reactive blue 19 dye |
74
|
47 |
|
FRP |
1 wt% coal fine suspension |
75
|
48 |
|
CRG |
Oily wastewater |
76
|
49 |
|
N/A |
Chlorella sp. CB4 microalgae; chlamydomonas sp. CRP7 microalgae |
77
|
50 |
|
FRP |
1 wt% coal fine suspension |
17
|
51 |
|
FRP |
Cement suspension |
78
|
52 |
|
N/A |
0.25 wt% kaolin suspension; Alexandrium tamarense algae |
79, 80
|
53 |
|
N/A |
0.25 wt% iron ore suspension |
81
|
54 |
|
FRP |
0.25 wt% kaolin suspension |
82
|
55 |
|
N/A |
0.10 wt% clay suspension |
83
|
56 |
|
FRP |
0.10 wt% clay suspension |
84
|
57 |
|
N/A |
Fresh water green algae |
85
|
58 |
|
FRP |
Reactive orange 16 dye |
86
|
59 |
|
N/A |
Textile industry wastewater |
87
|
3.1. Synthetic acrylamide-based copolymers
There are very few commercially available monomers with cationic functional groups due to problems associated with accessibility and/or stability.48 Quaternary ammonium is one of the most commonly reported cationic structures amongst these groups. Therefore, cationic flocculants are often developed based on copolymerization between AM and monomers containing quaternary ammonium functional groups.48 Methacryloyloxyethyl trimethylammonium chloride (DMC) and acryloyloxyethyl trimethylammonium chloride (DAC) are two of the most known comonomers used alongside AM to produce CPAM for flocculation purposes.49
Shang et al. developed a hydrophobically modified cationic terpolymer consisted of AM, DMC and methacryloxypropyl trimethoxysilane (MAPMS).50 Terpolymer 27 was synthesized from these monomers by inverse emulsion polymerization (IEP) to allow for adequate dissolution of the hydrophobic monomer.50 In addition, IEP is an advantageous polymerization technique which produces polymers with high MW and high solid content.48 The easy handling of the inverse latexes also allow for a simple post-treatment process.48,50 For cationic flocculants, charge neutralization is hypothesized as the major mechanism.2 Therefore, an increase in the dosage of 27 led to better flocculation due to neutralization of the negative charges on the particle surface. However, excess dosing of the flocculant resulted in restabilization of the colloidal suspension, where the overall particle surface charge changed from negative to positive.50 Apart from 27, numerous research groups have also directed their attention towards developing and utilizing hydrophobically modified cationic polymers as flocculants. Cationic terpolymers 28–32 were synthesized through copolymerization between AM and various monomers, including diallyldimethylammonium chloride (DADMAC),51,52 vinyltrimethoxysilane (VTMS),52 butylacrylate (BA),51,53,54 DAC,53,54 DMC,55 MMA,55 and acryloylamino-2-hydroxypropyl trimethylammonium chloride.56,57
The presence of MAPMS in 27 and VTMS in 29 was observed to impose a positive effect on the flocculation efficiency. Hydrolysis of the SiOCH3 functional group generated SiOH moieties, which lead to crosslinking between the molecular chains (Fig. 1).50,52 This subsequently enhanced the chain length and built three dimensional networks, thus allowing for better capture and containment of the contaminant particles. However, a decrease in water solubility of the polymers was observed when the ratios of MAPMS and VTMS were increased.50,52 Other hydrophobic monomers such as BA can reportedly increase the flocculation efficiency of a polymer. This was ascribed to higher intrinsic viscosity caused by the number of hydrophobic segments and their respective average length within the polymeric chain.53 This subsequently allows for better interactions between the hydrophobic segments and the solid contaminants.49,53,54
 |
| Fig. 1 Example showing crosslinked structure of MAPMS groups on terpolymer 27. | |
3.2. Synthetic acrylamide-free copolymers
Although PAM is one of the chemicals with the largest production volume, the high toxicity associated with AM is of environmental and human health concerns. It is a challenging process to design and develop non-AM-based flocculants with similar performance and cost compared to the current commercial ones.5 Nasr et al. developed a cationic terpolymer 33 which consisted of dimethylaminoethyl methacrylate, NVP and vinyl acetate.58 Another cationic polymer 34 based on the emulsion copolymerization between methyl acrylate (MA) and DAC was synthesized by Lu et al.5 More recently, the flocculation efficiency of a cationic copolymer 35 consisting of only DMA and DADMAC was reported by Abdiyev et al.59
P(MA-co-DAC) 34 with 55% charge density (CD) was compared to a P(AM-co-DAC) sample with the same CD (widely used for flocculation of biological sludge).5 The results obtained showed that 34 had good water solubility and comparable or slightly better performance against the AM-based polymer at various concentrations.5 Therefore this would potentially allow 34 to be a comparable competitor to AM-based flocculants, as well as being more beneficial for having less strict environmental regulations.5
3.3. Cationically-modified polysaccharides
Cationic starches are commonly used in wastewater treatment, paper production, textile industry, oil drilling, and the cosmetic industry. These biodegradable materials are classified into graft copolymerized starch, esterified starch, and etherified starch.60 Jiang et al. and Shi et al. recently reported the synthesis of cationic flocculants 36 and 37, based on the etherification of starch with methylene dimethylamine hydrochloride and 2,4-bis(dimethylamino)-6-chloro-[1,3,5]-triazine, respectively.60,61 Both polymers were found to be effective in flocculation and removal of anionic dyestuffs from wastewater.60,61 Flocculation efficiency of cationic graft copolymerized starches (38–41) were also reported by multiple research groups where different monomers were employed, including AM,62,63 DAC,62 allyltriphenylphosphonium bromide,63 DADMAC,64–66 and DMC.67
Chitosan and its derivatives are prominent biopolymers for this category due to its high cationic charge density from the presence of the amino groups.2 Recent studies conducted by Yang and coworkers introduced temperature-responsive polymers 42 and 43 for flocculation of copper and tetracycline from wastewater.68,69 Multiple other studies have reported the grafting of DMC onto chitosan backbone to produce polymers 44–46.70–73 However, in polymer 46, the chitosan backbone was also modified by ring-opening reaction with glycidyl methacrylate prior to the graft polymerization process.74 Apart from DMC, monomers such as N-vinyl formamide (NVF), and dimethyl acryloyloxyethyl benzyl ammonium chloride were grafted onto chitosan to develop cationic polymers 47 and 48, respectively.75,76
Cationic moieties such as N-3-chloro-2-hydroxypropyl trimethylammonium chloride, N-alkyl-N,N-dimethyl-N-2-hydroxypropyl ammonium chloride, 3-acrylamidopropyl trimethylammonium chloride, 3-methacryloylaminopropyl trimethylammonium chloride, NVF and DMC were used in modification of many different polysaccharides, including guar gum (49),77 carboxymethyl guar gum (50),17 salep (51),78 corn cob (52),79,80 glycogen (53),81 amylopectin (54),82 dextran (55),83 pullulan (56),84 inulin (57),85 xylan (58),86 and tamarind kernel polysaccharide (59).87
4. Anionic flocculants
The majority of commercial anionic flocculants contain carboxylate and sulfonate ions as the anionic functional group, and this can range from 1 to 100% of the monomer units.10 Anionic polymers are most commonly used as flocculants in mineral processing applications.1,3 Optimal flocculation is possible due to strong ionic interaction between the active anionic groups on the polymer chain and the divalent cations (primarily calcium and magnesium) available on the suspended particles.1 Apart from mineral processing, anionic polymers can also be used in the treatment of municipal wastewaters and sludges, tanning industry, paper production, foundries and metal working, sugar processing, and gravel washing.1,3,10
Table 3 provides a summary of the polymerization technique and the flocculation testing medium for anionic polymeric flocculants 60–72.
Table 3 Summary of the polymerization technique and the testing medium of anionic polymeric materials which were utilised as flocculating agents in previous studies
Entry |
Polymer structurea |
T.o.Pb |
Testing medium |
Ref. |
Abbreviations: Amp, amylopectin; Cell, cellulose; CMC, carboxymethyl cellulose; CMI, carboxymethyl inulin; Cs, chitosan; CSt, crosslinked starch; Dex, dextran; GGh, gum ghatti; KGM, Konjac glucomannan; St, starch.
Type of polymerization (T.o.P) abbreviations: CRG, conventional redox grafting; EP, emulsion polymerization; FRP, free radical polymerization; MWI, microwave initiated; N/A not applicable; UVI, ultraviolet irradiation.
|
60 |
|
UVI |
Waste sludge; DEP and DOP simulated wastewaters |
88–90
|
61 |
|
EP |
Clay slurry |
5
|
62 |
|
CRG |
5 wt% kaolin suspension with Cu2+ ions |
91, 92
|
63 |
|
MWI |
River water |
93
|
64 |
|
N/A |
ZnO suspension; Fe2O3 (hematite) suspension |
94
|
65 |
|
N/A |
ZnO suspension; Fe2O3 (hematite) suspension |
94
|
66 |
|
FRP |
1 wt% coal fine suspension |
95
|
67 |
|
FRP |
50 ppm kaolin solution |
96
|
68 |
|
CRG |
CuCl2 solution |
97
|
69 |
|
FRP |
0.25 wt% iron ore suspension |
98
|
70 |
|
CRG |
1 wt% kaolin suspension |
99
|
71 |
|
FRP |
Mining industry wastewater; 5 wt% iron ore suspension; 5 wt% manganese suspension; 5 wt% kaolin suspension |
100
|
72 |
|
N/A |
Municipal sewage wastewater; 0.25 wt% kaolin suspension |
101
|
4.1. Synthetic acrylamide-based copolymers
Commercial anionic flocculants are often synthesized based on the copolymerization between AM and anionic monomers such as AA and AMPS.1 All three of these monomers were employed to synthesize terpolymer 60via ultraviolet irradiation (UVI) polymerization.88–90 With respect to other types of initiation, UVI is an environmentally friendly and easily operated process. In addition, it has other advantages, including higher MW products, less initiator consumption, and faster reaction at lower reaction temperature.53,54,88 Terpolymer 60's flocculation efficiency was tested in diethyl phthalate (DEP), dioctyl phthalate (DOP) simulated wastewater, and dewatering of waste sludge.88–90 Better flocculation efficiency was observed in the sludge dewatering experiment for terpolymer 60, when compared to a commercial PAM sample. The results showed that the filter cake moisture content was decreased from 94.6% to 65.1% by terpolymer 60 while only 72.8% was achieved when the commercial PAM sample was used.88
4.2. Synthetic acrylamide-free copolymers
The same research group which synthesized AM-free cationic flocculant 34 also developed an anionic derivative using MA as a non-ionic comonomer.5 Polymeric flocculant 61 was also synthesized via the emulsion polymerization (EP) method, with AA employed as the anionic comonomer. This polymer was able to reduce the turbidity of the clay suspension by a hundredfold with only 2 ppm dosage.5 In addition, this polymer exhibited comparable flocculation performance to a commercial PAM sample (with slightly higher intrinsic viscosity and lower CD). However, its solvency in water is not as high as AM-based polymers due to relatively poorer solubility of MA.5
4.3. Anionically-modified polysaccharides
Chang et al. reported the development of a crosslinked starch-based flocculant with PAM and sodium xanthate (SX) grafted onto its backbone.91 The flocculation efficiency of polymer 62 was tested based on turbidity reduction as well as removal of Cu2+ ions in kaolin suspension.91,92 SX-grafted crosslinked starch (CSX) and AM-grafted crosslinked starch (CSA) were also synthesized separately in this study for flocculation comparison purposes. CSA was observed to have significantly lower Cu2+ removal rate compared to 62 and CSX; whereas CSX showed only slightly lower Cu2+ removal rate with respect to 62.91 The studies also concluded that the presence of high solution turbidity and Cu2+ ions in the simulated wastewater complemented each other. The xanthate functional group on the flocculant underwent complexation with Cu2+ ions to form precipitates, which were observed to be entrained by large flocs as they settled down and vice versa for fine suspended solid particles.91,92 In addition, Cu2+ ions also neutralized the negative charges on the suspended solids, which decreased the repulsion between the particles and the polymeric chains, hence enhanced the flocculation efficiency.91
Mishra et al. reported another modified polysaccharide 63, this time, focused on polyacrylic acid grafted onto carboxymethyl cellulose by MWI synthesis.93 Recent work by Ghimici and Suflet tested the flocculation efficiency of phosphorylated derivatives of cellulose (P-Cell) 64 and dextran (P-Dex) 65 in zinc oxide and hematite suspensions.94 The results obtained from this study showed that P-Dex performed better in zinc oxide suspension compared to P-Cell. In addition, P-Dex showed significantly better flocculation performance in hematite fines suspension compared to unmodified dextran.94
A non-traditional anionic monomer was used by Yadav et al. in the synthesis of chitosan-based polymer 66. This was achieved by graft copolymerization of 2-acrylamidoglycolic acid onto a chitosan backbone by the FRP method.95 Apart from starch, cellulose and chitosan, grafted polysaccharides based on gum ghatti (67),96 Konjac glucomannan (68),97 and amylopectin (69–71),98–100 and carboxymethyl inulin (72)101 were also reported in recent studies.
5. Amphoteric flocculants
Amphoteric polymers contain both cationic and anionic functional groups and currently have little uses as flocculants in industrial applications.1 However, these polymers have recently proved to be promising candidates for flocculation in the near future due to the positive properties attributed to both cationic and anionic functional groups.
Table 4 provides a summary of the polymerization technique and the flocculation testing medium for amphoteric polymeric flocculants 73–82.
Table 4 Summary of the polymerization technique and the testing medium of amphoteric polymeric materials which were utilised as flocculating agents in previous studies
Entry |
Polymer structurea |
T.o.Pb |
Testing medium |
Ref. |
Abbreviations: Amp, amylopectin; CMC, carboxymethyl cellulose; Cs, chitosan; St; starch.
Type of polymerization (T.o.P) abbreviations: IEP, inverse emulsion polymerization; FRP, free radical polymerization; MWA, microwave assisted; MWI, microwave initiated; N/A, not applicable.
|
73 |
|
FRP |
Simulated heavy metal wastewater (Cu2+, Cd2+, Pb2+, Zn2+ or Ni2+ ions) |
102–104
|
74 |
|
FRP |
1 wt% montmorillonite suspension |
105
|
75 |
|
IEP |
Dyeing wastewater; paper mill wastewater; refinery wastewater |
108
|
76 |
|
MWI |
Methyl violet solution |
109
|
77 |
|
FRP |
0.10 wt% kaolin suspension; 0.10 wt% hematite suspension |
106
|
78 |
|
N/A |
6 wt% kaolin suspension |
112
|
79 |
|
N/A |
0.25 wt% kaolin suspension |
107
|
80 |
|
N/A |
Algal turbid water |
110
|
81 |
|
MWA |
5 wt% iron ore suspension; 3 wt% kaolin suspension; methylene blue solution |
111
|
82 |
|
FRP |
0.25 wt% kaolin suspension |
82
|
5.1. Synthetic copolymers
Polymeric chelating agents have gained recent attention as flocculants in the treatment of heavy metal wastewater.102 Interaction between the anionic groups on these agents and heavy metal ions can lead to precipitation and formation of small flocs, as demonstrated by flocculant 62 and 68. In addition, the presence of metal ions allows for possible crosslinking between polymer chains, thus enabling small flocs to combine and form larger flocs.102 However, steric hindrance and spatial mismatch problems associated with polymeric chelating agents can result in formation of loose flocs and therefore poor flocculation performance is often observed.102
Liu et al. reported multiple studies on the development of a amphoteric chelating polymer in an attempt to tackle this problem.102–104 Amphoteric polymer 73 was synthesized via three main reaction sequences: FRP to form a copolymer between DADMAC and AM; grafting of triethylenetetramine onto the polymer sidechain; and xanthogenation reaction with carbon disulfide.102 The flocculation efficiency of chelating polymer 73 was subsequently tested with simulated wastewater that contained various heavy metal ions, including Cu2+, Cd2+, Pb2+, Zn2+ or Ni2+.102–104 The results from these studies indicated that chelation–flocculation efficiency was at its maximum when the molar ratio of –CSS− to the heavy metal ions (Cd2+ > Cu2+ > Pb2+ > Ni2+ > Zn2+) was approximately 2
:
1.103 As expected, the heavy metal ions removal rate increased with higher pH levels, and the flocs produced were observed to be highly stable at low concentration of acid.103 The chelation–flocculation mechanism was improved by the presence of positive charges from DADMAC units within the polymer chain. This was ascribed to the neutralization of excess negative flocs caused by steric hindrance and spatial mismatch that occurred during chelation.102,103 In addition, these positive charges also interacted with negative charges on other flocs which resulted in the formation of thicker and denser flocs.103
More recently, an amphoteric hydrophobically-modified flocculant 74 was prepared by copolymerization of AM, AA and dimethylbenzyl aminoethyl acrylate chloride.105 This flocculant was shown to have comparable performance to commercial CPAM and better performance than anionic PAM in montmorillonite simulated wastewater. The effect of Na+, Ca2+, Zn2+ and Al3+ ions were also tested and the results showed that 74 exhibited high salt tolerance with possible potential applications in high-salinity wastewater.105
5.2. Modified polysaccharides
Most modified polysaccharide studies so far have mainly directed their focus on non-ionic, cationic or anionic-based polymers. Amphoteric polysaccharides have gained recent interest from various research groups due to their beneficial characteristics obtained from the presence of both cationic and anionic moieties, as well as the positive flocculation properties associated with grafted branches.106 In addition, these types of polymers can also behave as effective flocculating agents across a wide range of pH levels.107
Song et al. synthesized an amphoteric starch-based polymer 75, and its flocculation efficiency in various types of wastewater was shown to be better in comparison to CPAM, hydrolytic PAM and amphoteric PAM that were used in the study.108 Another study incorporated non-conventional cationic quaternary ammonium and anionic phosphate moieties onto a starch backbone to develop polymer 76.109 A common trend was observed in subsequent amphoteric polysaccharide studies, where either etherification or graft copolymerization, or a combination of both were employed to introduce separate cationic and anionic groups onto the polysaccharide backbone.106,107,110–112 Apart from starch-based polymers 75–78, other studies have also synthesized amphoteric carboxymethyl cellulose (79),107 chitosan (80),110 and amylopectin (81, 82).82,111
6. Future challenges for flocculation
It is clear from this review that the environmental problems associated with current commercially available synthetic flocculation are of great concerns. Only very few of the current industrial processes utilize starch, dextran, carboxymethyl cellulose, guar gum, and chitosan-based polymers for flocculation purposes.3,10 The majority of the flocculation studies mentioned in this review have combined synthetic and natural polymers together through graft copolymerization. Although this is a positive step towards the synthesis of ‘greener’ flocculants, further studies are required to push the limit of these polymers when it comes to their biodegradability and flocculation efficiency. This would potentially result in greater interests from industries that have the ability to commercialize these polymers for flocculation applications.
The flocculation efficiency of many polymers decreases with an increase in salt content. This is a result of a reduction in the hydrodynamic radius due to the interaction between the salt and the active functional groups on the polymer chain, rendering the polymer impaired or inactive for flocculation.105 As this interaction is unavoidable, flocculation in high salinity substrates remains a difficult challenge to overcome.
The synthesis of hydrophobically-modified polymeric flocculants is also challenging due to issues associated with the insolubility of hydrophobic monomers in water.50 This drawback could therefore complicate the synthesis process. In addition, hydrophobically-modified polymers are less soluble in water compared to the conventional polymeric flocculants, and thus their positive properties can be irrelevant if they are poorly soluble in aqueous substrates.
7. Conclusions
In this review, we have described the synthesis techniques and flocculation efficiency associated with several non-ionic (1–26, cationic (27–59), anionic (60–72) and amphoteric (73–82) polymers, and a summary of each type of polymeric flocculant is presented in Tables 1–4, respectively. The development of synthetically-modified polysaccharide-based materials was observed to be of significant research interest recently due to their aforementioned biodegradable characteristics compared to synthetic flocculants. In addition, the flocculation efficiency of these modified polymers was better with respect to their original unmodified polysaccharide. This was in agreement with Singh's Easy Approachability Model and the Brostow, Pal and Singh Model of Flocculation. Synthetic polymeric flocculants have been the minor focus of recent studies due to the current abundance of commercially available synthetic flocculants. However, most synthetic flocculants were observed to be hydrophobically-modified as this can enhance the interaction between the polymer chain and the solid contaminants. The polymeric materials reported in this paper have shown comparable or better flocculation efficiency compared to the current commercial ones, and thus have strong potential as efficient flocculating agents in the near future.
Acknowledgements
We would like to thank the Chemicals and Plastics Manufacturing Innovation Network and Training Program, supported by Monash University, the Plastics and Chemicals Industries Association (PACIA) and the Victorian Government.
Notes and references
-
H. Burkert and J. Hartmann, in Ullmann's Encyclopedia of Industrial Chemistry, Wiley-VCH Verlag GmbH & Co. KGaA, Federal Republic of Germany, 2000, vol. 15, pp. 199–210 Search PubMed.
- C. S. Lee, J. Robinson and M. F. Chong, Process Saf. Environ. Prot., 2014, 92, 489–508 CrossRef CAS.
-
G. M. Moody, in Handbook of Industrial Water Soluble Polymers, ed. P. A. Williams, John Wiley & Sons, Oxford, The United Kingdom, 2008, pp. 134–173 Search PubMed.
- M. S. Nasser and A. E. James, Sep. Purif. Technol., 2006, 52, 241–252 CrossRef CAS.
- L. Lu, Z. Pan, N. Hao and W. Peng, Water Res., 2014, 57, 304–312 CrossRef CAS PubMed.
- J. Gregory and S. Barany, Adv. Colloid Interface Sci., 2011, 169, 1–12 CrossRef CAS PubMed.
- R. P. Singh, G. P. Karmakar, S. K. Rath, N. C. Karmakar, S. R. Pandey, T. Tripathy, J. Panda, K. Kanan, S. K. Jain and N. T. Lan, Polym. Eng. Sci., 2000, 40, 46–60 CAS.
- B. Bolto and J. Gregory, Water Res., 2007, 41, 2301–2324 CrossRef CAS PubMed.
- E. Sabah and I. Cengiz, Water Res., 2004, 38, 1542–1549 CrossRef CAS PubMed.
- T. Tripathy and B. R. De, J. Phys. Sci., 2006, 10, 93–127 Search PubMed.
- S. Mishra, A. Mukul, G. Sen and U. Jha, Int. J. Biol. Macromol., 2011, 48, 106–111 CrossRef CAS PubMed.
- G. Sen, R. Kumar, S. Ghosh and S. Pal, Carbohydr. Polym., 2009, 77, 822–831 CrossRef CAS.
-
R. P. Singh, in Polymers and Other Advanced Materials: Emerging Technologies and Business Opportunities, ed. P. N. Prasad, J. E. Mark and T. J. Fai, Springer US, New York, The United States of America, 1995, pp. 227–249 Search PubMed.
- R. Das, S. Ghorai and S. Pal, Chem. Eng. J., 2013, 229, 144–152 CrossRef CAS.
- W. Brostow, S. Pal and R. P. Singh, Mater. Lett., 2007, 61, 4381–4384 CrossRef CAS.
- V. K. Thakur, M. K. Thakur and R. K. Gupta, Carbohydr. Polym., 2013, 98, 820–828 CrossRef CAS PubMed.
- M. M. Mishra, D. K. Mishra, P. Mishra and K. Behari, Carbohydr. Polym., 2015, 115, 776–784 CrossRef CAS PubMed.
- S. Pal, S. Ghorai, M. K. Dash, S. Ghosh and G. Udayabhanu, J. Hazard. Mater., 2011, 192, 1580–1588 CrossRef CAS PubMed.
- P. Adhikary, S. Krishnamoorthi and R. P. Singh, J. Appl. Polym. Sci., 2011, 120, 2621–2626 CrossRef CAS.
- P. Rani, G. Sen, S. Mishra and U. Jha, Carbohydr. Polym., 2012, 89, 275–281 CrossRef CAS PubMed.
- J.-P. Wang, Y.-Z. Chen, S.-J. Zhang and H.-Q. Yu, Bioresour. Technol., 2008, 99, 3397–3402 CrossRef CAS PubMed.
- J. Tripathy, D. K. Mishra, M. Yadav and K. Behari, Carbohydr. Polym., 2010, 79, 40–46 CrossRef CAS.
- Z. Yang, B. Yuan, X. Huang, J. Zhou, J. Cai, H. Yang, A. Li and R. Cheng, Water Res., 2012, 46, 107–114 CrossRef CAS PubMed.
- A. Srivastava, D. K. Mishra and K. Behari, Carbohydr. Polym., 2010, 80, 790–798 CrossRef CAS.
- S. Mishra, G. Sen, G. U. Rani and S. Sinha, Int. J. Biol. Macromol., 2011, 49, 591–598 CrossRef CAS PubMed.
- G. U. Rani, S. Mishra, G. Sen and U. Jha, Carbohydr. Polym., 2012, 90, 784–791 CrossRef CAS PubMed.
- G. U. Rani, S. Mishra, G. Pathak, U. Jha and G. Sen, Int. J. Biol. Macromol., 2013, 61, 276–284 CrossRef CAS PubMed.
- G. Sen, G. U. Rani and S. Mishra, Front. Chem. Sci. Eng., 2013, 7, 312–321 CrossRef CAS.
- K. Xu, X. Xu, Z. Ding and M. Zhou, China Part., 2006, 4, 60–64 CrossRef CAS.
- T. Tripathy and R. P. Singh, J. Appl. Polym. Sci., 2001, 81, 3296–3308 CrossRef CAS.
- P. Rani, S. Mishra and G. Sen, Carbohydr. Polym., 2013, 91, 686–692 CrossRef CAS PubMed.
- D. K. Mishra, J. Tripathy and K. Behari, Carbohydr. Polym., 2008, 71, 524–534 CrossRef CAS.
- M. M. Mishra, A. Sand, D. K. Mishra, M. Yadav and K. Behari, Carbohydr. Polym., 2010, 82, 424–431 CrossRef CAS.
- S. Krishnamoorthi, P. Adhikary, D. Mal and R. P. Singh, J. Appl. Polym. Sci., 2010, 118, 3539–3544 CrossRef CAS.
- S. Pal, T. Nasim, A. Patra, S. Ghosh and A. B. Panda, Int. J. Biol. Macromol., 2010, 47, 623–631 CrossRef CAS PubMed.
- R. Rahul, U. Jha, G. Sen and S. Mishra, Carbohydr. Polym., 2014, 99, 11–21 CrossRef CAS PubMed.
- G. Sen, S. Mishra, G. U. Rani, P. Rani and R. Prasad, Int. J. Biol. Macromol., 2012, 50, 369–375 CrossRef CAS PubMed.
- S. Mishra, S. Sinha, K. P. Dey and G. Sen, Carbohydr. Polym., 2014, 99, 462–468 CrossRef CAS PubMed.
- S. Bharti, S. Mishra and G. Sen, Carbohydr. Polym., 2013, 93, 528–536 CrossRef CAS PubMed.
- S. Bharti, S. Mishra, L. V. Narendra, T. Balaraju and K. Balraju, Desalin. Water Treat., 2015, 1–16 CrossRef.
- G. Sen, S. Mishra, K. Prasad Dey and S. Bharti, J. Appl. Polym. Sci., 2014, 131, 41046 CrossRef.
- S. Ghosh, G. Sen, U. Jha and S. Pal, Bioresour. Technol., 2010, 101, 9638–9644 CrossRef CAS PubMed.
- S. Ghosh, U. Jha and S. Pal, Bioresour. Technol., 2011, 102, 2137–2139 CrossRef CAS PubMed.
- G. Sen and S. Pal, Macromol. Symp., 2009, 277, 100–111 CrossRef CAS.
- S. Sinha, S. Mishra and G. Sen, Int. J. Biol. Macromol., 2013, 60, 141–147 CrossRef CAS PubMed.
- J. M. Henderson and A. D. Wheatley, Coal Prep., 1987, 4, 1–49 CrossRef CAS.
- J. M. Henderson and A. D. Wheatley, J. Appl. Polym. Sci., 1987, 33, 669–684 CrossRef CAS.
- W. Jaeger, J. Bohrisch and A. Laschewsky, Prog. Polym. Sci., 2010, 35, 511–577 CrossRef CAS.
- Z. Abdollahi, M. Frounchi and S. Dadbin, J. Ind. Eng. Chem., 2011, 17, 580–586 CrossRef CAS.
- H. Shang, J. Liu, Y. Zheng and L. Wang, J. Appl. Polym. Sci., 2009, 111, 1594–1599 CrossRef CAS.
- Z. L. Yang, B. Y. Gao, C. X. Li, Q. Y. Yue and B. Liu, Chem. Eng. J., 2010, 161, 27–33 CrossRef CAS.
- H. Shang, Y. Zheng and J. Liu, J. Appl. Polym. Sci., 2011, 119, 1602–1609 CrossRef CAS.
- H. Zheng, Y. Sun, C. Zhu, J. Guo, C. Zhao, Y. Liao and Q. Guan, Chem. Eng. J., 2013, 234, 318–326 CrossRef CAS.
- H. Zheng, Y. Sun, J. Guo, F. Li, W. Fan, Y. Liao and Q. Guan, Ind. Eng. Chem. Res., 2014, 53, 2572–2582 CrossRef CAS.
- T. Lü, D. Qi, H. Zhao and Y. Cheng, Polym. Eng. Sci., 2015, 55, 1–7 Search PubMed.
- L.-J. Wang, J.-P. Wang, S.-J. Yuan, S.-J. Zhang, Y. Tang and H.-Q. Yu, Chem. Eng. J., 2009, 149, 118–122 CrossRef CAS.
- L.-J. Wang, J.-P. Wang, S.-J. Zhang, Y.-Z. Chen, S.-J. Yuan, G.-P. Sheng and H.-Q. Yu, Sep. Purif. Technol., 2009, 67, 331–335 CrossRef CAS.
- H. E. Nasr, A. A. Farag, S. M. Sayyah and S. H. Samaha, J. Dispersion Sci. Technol., 2010, 31, 427–437 CrossRef CAS.
- K. Z. Abdiyev, Z. Toktarbay, A. Z. Zhenissova, M. B. Zhursumbaeva, R. N. Kainazarova and N. Nuraje, Colloids Surf., A, 2015, 480, 228–235 CrossRef CAS.
- Y. Jiang, B. Ju, S. Zhang and J. Yang, Carbohydr. Polym., 2010, 80, 467–473 CrossRef CAS.
- Y. Shi, B. Ju and S. Zhang, Carbohydr. Polym., 2012, 88, 132–138 CrossRef CAS.
- H. Song, Carbohydr. Polym., 2010, 82, 768–771 CrossRef CAS.
- W. Song, Z. Zhao, H. Zheng and G. Wang, Water Sci. Technol., 2013, 68, 1778–1784 CrossRef CAS PubMed.
- S. Lv, T. Sun, Q. Zhou, J. Liu and H. Ding, Carbohydr. Polym., 2014, 103, 285–293 CrossRef CAS PubMed.
- M. A. A. Razali and A. Ariffin, Appl. Surf. Sci., 2015, 351, 89–94 CrossRef CAS.
- M. A. A. Razali, H. Ismail and A. Ariffin, Ind. Crops Prod., 2015, 65, 535–545 CrossRef CAS.
- J.-P. Wang, S.-J. Yuan, Y. Wang and H.-Q. Yu, Water Res., 2013, 47, 2643–2648 CrossRef CAS PubMed.
- Z. Yang, S. Jia, N. Zhuo, W. Yang and Y. Wang, Chemosphere, 2015, 141, 112–119 CrossRef CAS PubMed.
- S. Jia, Z. Yang, W. Yang, T. Zhang, S. Zhang, X. Yang, Y. Dong, J. Wu and Y. Wang, Chem. Eng. J., 2016, 283, 495–503 CrossRef CAS.
- J.-P. Wang, Y.-Z. Chen, Y. Wang, S.-J. Yuan, G.-P. Sheng and H.-Q. Yu, RSC Adv., 2012, 2, 494–500 RSC.
- J.-P. Wang, Y.-Z. Chen, X.-W. Ge and H.-Q. Yu, Chemosphere, 2007, 66, 1752–1757 CrossRef CAS PubMed.
- J.-P. Wang, Y.-Z. Chen, S.-J. Yuan, G.-P. Sheng and H.-Q. Yu, Water Res., 2009, 43, 5267–5275 CrossRef CAS PubMed.
- Z. Yang, H. Li, H. Yan, H. Wu, H. Yang, Q. Wu, H. Li, A. Li and R. Cheng, J. Hazard. Mater., 2014, 276, 480–488 CrossRef CAS PubMed.
- X. Jiang, K. Cai, J. Zhang, Y. Shen, S. Wang and X. Tian, J. Hazard. Mater., 2011, 185, 1482–1488 CrossRef CAS PubMed.
- D. K. Mishra, J. Tripathy, A. Srivastava, M. M. Mishra and K. Behari, Carbohydr. Polym., 2008, 74, 632–639 CrossRef CAS.
- T. Lü, H. Zhao, D. Qi and Y. Chen, Adv. Polym. Technol., 2015, 0, 21502 Search PubMed.
- C. Banerjee, S. Ghosh, G. Sen, S. Mishra, P. Shukla and R. Bandopadhyay, Carbohydr. Polym., 2013, 92, 675–681 CrossRef CAS PubMed.
- A. Pourjavadi, S. M. Fakoorpoor and S. H. Hosseini, Carbohydr. Polym., 2013, 93, 506–511 CrossRef CAS PubMed.
- Y. Pang, Y. Ding and B. Sun, Procedia Environ. Sci., 2013, 18, 602–609 CrossRef CAS.
- Y. Pang, Y. Ding, J. Chen and W. Gong, Agric. Sci., 2013, 4, 23–28 CAS.
- S. Pal, D. Mal and R. P. Singh, Colloids Surf., A, 2006, 289, 193–199 CrossRef CAS.
- K. Kumar, P. Adhikary, N. C. Karmakar, S. Gupta, R. P. Singh and S. Krishnamoorthi, Carbohydr. Polym., 2015, 127, 275–281 CrossRef CAS PubMed.
- L. Ghimici and M. Nichifor, Bioresour. Technol., 2010, 101, 8549–8554 CrossRef CAS PubMed.
- L. Ghimici, M. Constantin and G. Fundueanu, J. Hazard. Mater., 2010, 181, 351–358 CrossRef CAS PubMed.
- R. Rahul, S. Kumar, U. Jha and G. Sen, Int. J. Biol. Macromol., 2015, 72, 868–874 CrossRef CAS PubMed.
- S. Wang, Q. Hou, F. Kong and P. Fatehi, Carbohydr. Polym., 2015, 124, 229–236 CrossRef CAS PubMed.
- S. Pal, S. Ghosh, G. Sen, U. Jha and R. P. Singh, Int. J. Biol. Macromol., 2009, 45, 518–523 CrossRef CAS PubMed.
- J. Ma, H. Zheng, M. Tan, L. Liu, W. Chen, Q. Guan and X. Zheng, J. Appl. Polym. Sci., 2013, 129, 1984–1991 CrossRef CAS.
- J. Ma, H. Zheng, X. Tang, W. Chen, W. Xue, Y. Liao, Q. Guan and Y. Liao, Appl. Mech. Mater., 2013, 361, 726–729 CrossRef.
- H. Zheng, J. Ma, C. Zhu, Z. Zhang, L. Liu, Y. Sun and X. Tang, Sep. Purif. Technol., 2014, 123, 35–44 CrossRef CAS.
- Q. Chang, X. Hao and L. Duan, J. Hazard. Mater., 2008, 159, 548–553 CrossRef CAS PubMed.
- X. Hao, Q. Chang and X. Li, J. Appl. Polym. Sci., 2009, 112, 135–141 CrossRef CAS.
- S. Mishra, G. Usha Rani and G. Sen, Carbohydr. Polym., 2012, 87, 2255–2262 CrossRef CAS.
- L. Ghimici and D. M. Suflet, Sep. Purif. Technol., 2015, 144, 31–36 CrossRef CAS.
- M. Yadav, A. Sand and K. Behari, Int. J. Biol. Macromol., 2012, 50, 1306–1314 CrossRef CAS PubMed.
- H. Mittal, R. Jindal, B. S. Kaith, A. Maity and S. S. Ray, Carbohydr. Polym., 2014, 114, 321–329 CrossRef CAS PubMed.
- J. Duan, Q. Lu, R. Chen, Y. Duan, L. Wang, L. Gao and S. Pan, Carbohydr. Polym., 2010, 80, 436–441 CrossRef CAS.
- S. Pal and A. Pal, Polym. Bull., 2012, 69, 545–560 CrossRef CAS.
- P. Adhikary and S. Krishnamoorthi, J. Appl. Polym. Sci., 2012, 126, E313–E318 CrossRef CAS.
- A. K. Sarkar, N. R. Mandre, A. B. Panda and S. Pal, Carbohydr. Polym., 2013, 95, 753–759 CrossRef CAS PubMed.
- R. Rahul, U. Jha, G. Sen and S. Mishra, Int. J. Biol. Macromol., 2014, 63, 1–7 CrossRef CAS PubMed.
- L. Liu, J. Wu, Y. Ling, X. Li and R. Zeng, J. Appl. Polym. Sci., 2013, 127, 2082–2094 CrossRef CAS.
- L. Liu, J. Wu, X. Li and Y. Ling, Sep. Purif. Technol., 2013, 103, 92–100 CrossRef CAS.
- L. Liu, Y. Li, X. Liu, Z. Zhou and Y. Ling, Spectrochim. Acta, Part A, 2014, 118, 765–775 CrossRef CAS PubMed.
- C. Liu, B. Hong, K. Xu, M. Zhang, H. An, Y. Tan and P. Wang, Polym. Bull., 2014, 71, 3051–3065 CrossRef CAS.
- Z. Yang, H. Wu, B. Yuan, M. Huang, H. Yang, A. Li, J. Bai and R. Cheng, Chem. Eng. J., 2014, 244, 209–217 CrossRef CAS.
- H. Kono and R. Kusumoto, React. Funct. Polym., 2014, 82, 111–119 CrossRef CAS.
- H. Song, D. Wu, R.-Q. Zhang, L.-Y. Qiao, S.-H. Zhang, S. Lin and J. Ye, Carbohydr. Polym., 2009, 78, 253–257 CrossRef CAS.
- Q. Lin, S. Qian, C. Li, H. Pan, Z. Wu and G. Liu, Carbohydr. Polym., 2012, 90, 275–283 CrossRef CAS PubMed.
- C. Dong, W. Chen and C. Liu, Bioresour. Technol., 2014, 170, 239–247 CrossRef CAS PubMed.
- R. P. Singh, S. Pal, V. K. Rana and S. Ghorai, Carbohydr. Polym., 2013, 91, 294–299 CrossRef CAS PubMed.
- E. Lekniute, L. Peciulyte, R. Klimaviciute, J. Bendoraitiene and A. Zemaitaitis, Colloids Surf., A, 2013, 430, 95–102 CrossRef CAS.
|
This journal is © The Royal Society of Chemistry 2016 |
Click here to see how this site uses Cookies. View our privacy policy here.