DOI:
10.1039/C5NJ02436F
(Paper)
New J. Chem., 2016,
40, 818-824
Fabrication of Fe3O4@Au hollow spheres with recyclable and efficient catalytic properties†
Received
(in Montpellier, France)
11th September 2015
, Accepted 18th November 2015
First published on 20th November 2015
Abstract
The preparation of catalysts with superior catalytic activity, reusability and economical processes is highly desirable. In this work, we report a route for the facile synthesis of Fe3O4@Au hollow spheres. The Fe3O4@Au hollow spheres were prepared based on Fe3O4 hollow spheres with gold nanoparticles inlaid on their surface. The Fe3O4@Au hollow nanospheres were characterized by X-ray diffraction (XRD), X-ray photoelectron spectroscopy (XPS), transmission electron microscopy (TEM) and scanning electron microscopy (SEM) with energy-dispersive X-ray spectroscopy (EDX). The Fe3O4@Au hollow spheres exhibit remarkable catalytic activity and good reusability toward the reduction of 4-nitrophenol and potassium hexacyanoferrate(III) by NaBH4 in water. In addition, the catalysts show good reusability for at least 6 successive cycles.
Introduction
Noble metal nanoparticles (NPs) have been the subject of intense research due to their unique physiochemical properties compared to their bulk counterparts and broad applications in energy conversion and storage, cancer therapy, sensing, etc., especially for catalysis.1–6 As important catalysts, noble metallic Au nanoparticles have been widely used in many typical pseudo-homogeneous catalysis,7–9 such as water splitting, hydrogenation, and coupling reactions under mild reaction conditions.10–13 However, the cost of noble metals is one of the key limitations for their practical application. One possible solution is minimum usage and reuse of the noble metal nanoparticles. To improve the efficiency and save resources, there has been an increasing trend toward the use of magnetically retrievable nanoparticles in efficient green chemical synthesis.14 Using a catalyst containing magnetic particles allows it to be recovered and reused using an external magnet, thus avoiding the need for catalyst separation by filtration. The recovery of expensive catalysts after catalytic reactions and reusing them without the loss of activity are essential features for sustainable process development. This is primarily because these types of supports display some advantageous properties, such as excellent stability, good accessibility, porosity, and the fact that tiny noble metal nanoparticles can be robustly anchored to their surfaces to provide catalytic centers. Hence, a number of efforts have been devoted to developing feasible routes for immobilizing or grafting noble metals onto magnetite supports to improve their stabilization and recycling stability. Zhao and co-workers have synthesized a kind of mesoporous Fe3O4@SiO2–Au hybrid composite material with high magnetization and catalysis.15 Ma et al. have designed Pt nanoparticles supported on carbon coated magnetic microparticle Fe3O4@C@Pt as a recyclable catalyst.16 Li and Chen prepared Pt–Pd nanoalloys supported on Fe3O4@C core–shell nanoparticles and used them as catalysts with high catalytic activity.17 More recently, Vinod and co-workers reported an Au@Ni core–shell nanoparticle with synergistic catalysis.18 Huang and Tang reported one-pot solvothermal synthesis of Au–Fe3O4 hybrid nanoparticles and used them as reusable catalysts.19 Otherwise, compared with solid metal nanostructures, hollow ones are quite distinguishable, because of their large specific surface area and high reactivity.20–22 A specific feature of hollow structures is their relatively low density, particularly, hollow structures with large surface areas, which generally make them more attractive than the corresponding core–shell particles.23 Typically, Zhao et al. reported a one-pot process via the hydrothermal method to synthesise Au–Fe3O4 hybrid hollow spheres with efficient catalysis.24 Li and co-workers prepared a Pd based catalyst supported on amine-functionalized Fe3O4 hollow spheres. Fe3O4@Pd afforded fast conversions for various aromatic nitro compounds under a H2 atmosphere in ethanol even at room temperature.25 Therefore, it is highly desirable to develop a functionalized magnetite support for immobilizing noble metal nanoparticles with a hollow structure.
In this work, we prepared Au supported Fe3O4 hollow spheres and used them as recyclable catalysts. The fabrication procedures for Fe3O4@Au hollow spheres are schematically illustrated in Scheme 1. Briefly, Fe3O4 hollow spheres were firstly prepared by using a modified solvothermal method. Then Fe3O4 hollow spheres were modified and used as templates. Gold nanoseeds were prepared and supported on the surface of the Fe3O4 hollow spheres by the function of –NH2. The Fe3O4@Au hollow spheres were generated by seeded growth in situ by directly reducing Au3+ on the surface of Fe3O4@Au nanoseeds. The gold nanoparticles immobilized on the surface of the Fe3O4 nanoparticles act as robust antennae, which could increase the area of contact with reactants. It was found that the as-prepared Fe3O4@Au hollow spheres exhibit an ultrahigh activity as catalysts for the reduction of 4-nitrophenol (4-NP) and potassium hexacyanoferrate(III) by NaBH4.
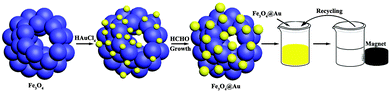 |
| Scheme 1 View of the preparation process and the evaluation of the catalysis activity of Fe3O4@Au hollow spheres. | |
Experimental section
Chemicals
All chemicals used were of analytical grade or of the highest purity available. Ferric chloride hexahydrate (FeCl3·6H2O), sodium acetate anhydrous (NaAc), potassium carbonate (K2CO3), trisodium citrate (C6H5O7Na3·2H2O) and formaldehyde (HCHO) were obtained from Fengchuan Chemical Company (Tianjin, China). Polyethylene glycol 2000 (PEG-2000) was purchased from Tianjin Guangfu Technology Development Co., Ltd (Tianjin, China). Ethylene glycol (EG), ethanolamine (ETA) and ethanol were provided by Sinopharm Chemical Reagent Co., Ltd (Shanghai, China). Hydrogen tetrachloroaurate(III) trihydrate (HAuCl4·3H2O, 99.9%), 3-aminopropyl-triethoxysilane (APTES) and sodium borohydride (NaBH4, 98%) were obtained from Aladin and used as received. Potassium hexacyanoferrate(III) (K3Fe(CN)6, 99%) and 4-nitrophenol (4-NP) were supplied by Shanghai Chemical Corp. All glassware was thoroughly cleaned with freshly prepared 3
:
1 HCl/HNO3 (aqua regia) and rinsed thoroughly with Milli-Q (18.2 MΩ cm−1 resistance) water prior to use. Milli-Q water was used to prepare all the solutions in this study.
Characterization
The morphology and the size of the Fe3O4 hollow spheres and Au NPs were characterized using a JEM-2010 (Japan) transmission electron microscope (TEM) operated at 200 kV. Scanning electron microscopy (SEM) images and energy-dispersive X-ray spectroscopy (EDX) analysis were obtained by using a Hitachi Su-70 electron microscope at an acceleration voltage of 20 kV. X-ray powder diffraction (XRD) patterns were obtained by using a Rigaku DMax-2600 PC diffraction meter using monochromatic Cu K radiation. X-ray photoelectron spectroscopy (XPS) spectra were recorded on an Axis Ultra DLD (SHIMADZU, Japan), and the C1s line at 284.6 eV was used as the binding energy reference. The magnetic properties of the samples were measured using a vibrating sample magnetometer (VSM, Lake-shore 7410) at room temperature. Absorption spectra were recorded by UV-vis spectroscopy using a UV-2550 spectrophotometer (SHIMADZU, Japan) at room temperature.
Preparation of Fe3O4 hollow spheres
The monodisperse Fe3O4 hollow spheres were synthesized according to the reported literature26,27 with slight modifications. In detail, 1.5 g of FeCl3·6H2O was dissolved in 40 mL of solvent containing EG (30 mL) and ETA (10 mL) to form a stable orange solution. 4.0 g of NaAc and 1.0 g of PEG-2000 were added into the above solution under vigorous magnetic stirring until they were completely dissolved. The homogeneous solution obtained was transferred to a Teflon-lined stainless-steel autoclave (50 mL), sealed and heated at 200 °C for 8 h. After the reaction, the autoclave was cooled to ambient temperature naturally, and the solid products were collected by applying a magnet, and were washed with water and ethanol several times. The products were dried under vacuum at 60 °C for 12 h.
APTES-modified Fe3O4 hollow spheres
The Fe3O4 hollow spheres should be modified by APTES to stabilize the resultant Au nanoseeds. According to the reported literature,15,28 100 mg of Fe3O4 hollow nanospheres was dispersed into 40 mL of ethanol, and then the suspension was ultrasonicated for at least 20 min to ensure uniform dispersion of the magnetic Fe3O4 hollow nanospheres. Then, 400 μL of APTES was added into the suspension under continuous mechanical stirring for 3 h at room temperature. Finally, with the help of a magnet, the APTES-modified Fe3O4 hollow nanospheres were harvested, repeatedly washed with ethanol and deionized water, and redispersed in water (50 mL) to form a homogeneous dispersion.
Synthesis of Fe3O4@Au nanoseeds and Fe3O4@Au hollow spheres
Firstly, 3.5 nm gold nanoseeds were prepared by using NaBH4 as a reductant.29 Typically, a 20 mL aqueous solution containing 2.5 × 10−4 M HAuCl4 and 2.5 × 10−4 M trisodium citrate was prepared in a conical flask. Next, 0.6 mL of ice-cold, freshly prepared 0.1 M NaBH4 solution was added to the solution while stirring. The solution turned pink immediately after adding NaBH4, indicating the particle formation for further use. For the preparation of Fe3O4@Au nanoseeds,30 30 mL of the Au nanoparticle solution was mixed with 50 mL of an aqueous dispersion of APTES-Fe3O4 hollow nanospheres by quick ultrasonication in a water bath. The mixture was subjected to mechanical stirring for 2 h, and the Fe3O4@Au nanoseeds were collected with a magnet, washed with ethanol and deionized water 3 times and redispersed in water (5 mL) to form a homogeneous dispersion.
In order to grow the gold nanoparticles on the surface of the Fe3O4 hollow spheres,31 1.5 mL of 1% HAuCl4 solution was added to 100 mL of 2 mM potassium carbonate aqueous solution, under vigorous stirring for 30 min, and the yellow colored solution became colorless gradually. The solution aged overnight to form Au(OH)4− ions in a refrigerator at 4 °C. In the Au growth step, Fe3O4@Au nanoseed solution was added into 20 mL of gold hydroxide solution, and then 80 μL of formaldehyde was added to the solution with mechanical stirring. The bigger gold nanoparticles formed in situ based on Au nanoseeds on the surface of the Fe3O4 hollow spheres. Finally, the Fe3O4@Au hollow spheres were separated with a magnet, washed with deionized water and dried in a vacuum at 50 °C for 6 h.
Catalytic reduction of 4-nitrophenol (4-NP)
The catalytic properties of the Fe3O4@Au hollow spheres were systematically examined by two experiments, the reduction of 4-NP32 and K3Fe(CN)6.33 For the catalytic reduction of 4-NP, aqueous solutions of 4-NP (0.01 M, 0.03 mL) and freshly prepared aqueous NaBH4 solution (0.5 M, 0.2 mL) were mixed with water (2.5 mL) in a quartz cuvette without stirring. Then the Fe3O4@Au hollow sphere aqueous suspension (25 μL, 2.8 mg mL−1) was injected without any stirring. The reaction was monitored by taking absorption spectra. To further test the reusability of the catalysts, the used Fe3O4@Au hollow spheres were separated from the solution with a magnet for the next cycle of catalytic reaction after the reduction process was complete. Similar to the above mentioned procedure the cycle was repeated 6 times. In order to ensure the quantity of catalyst was enough to centrifuge in the process of recycling, 100 μL of 2.8 mg mL−1 Fe3O4@Au hollow spheres was added into reaction solution.
Catalytic reduction of K3Fe(CN)6
The reduction of K3Fe(CN)6 was also performed in a quartz cuvette and monitored using UV-vis spectroscopy at room temperature.33,34 The reduction of K3Fe(CN)6 was carried out according to a typical reaction, 0.4 mL of 8 × 10−3 M K3Fe(CN)6 was added into 1.2 mL of deionized water, then 25 μL of 2.8 mg mL−1 Fe3O4@Au hollow spheres was added, followed by the rapid addition of 0.8 mL of 0.040 M ice-cold fresh NaBH4 solution. To further investigate the reusability of the Fe3O4@Au hollow spheres as catalysts, the used Fe3O4@Au hollow spheres were separated from the solution with a magnet after the whole reduction process was completed. In order to ensure that the quantity of catalyst was enough to separate and reuse in the process of recycling, 100 μL of 2.8 mg mL−1 Fe3O4@Au hollow spheres was added into the reaction solution. Similar to the above reduction process recycling was carried out 12 times.
Results and discussion
Representative transmission electron microscopy (TEM) images were recorded to examine the morphology, size and hollow structure of the magnetic Fe3O4 hollow spheres, Fe3O4@Au nanoseeds, and Fe3O4@Au hollow spheres. As shown in Fig. 1a, the diameter of the as-synthesized Fe3O4 hollow spheres was between 100 and 120 nm. The Fe3O4 hollow spheres were composed of many nanoparticles with diameters of about 25–30 nm. The hollow hole of the Fe3O4 spherical structure can be seen clearly from the magnified image shown in the inset. The Fe3O4@Au nanoseeds can be observed in Fig. 1b, which indicate that many Au nanoseeds with a diameter of 3.5 nm were stuck on the surface of the Fe3O4 hollow spheres. And the nanoseeds can be observed inlaid in the wall of the Fe3O4 hollow spheres from the enlarged image of the inset. After the growth of Au nanoseeds, the surface of the hollow spheres was relatively rough, which indicated that they were composed of tiny primary nanoparticles. The diameter of the gold nanoparticles was up to around 6 nm, which is indicated in Fig. 1c. Meanwhile, from Fig. 1d, which is magnified from Fig. 1c, it can also be concluded that the gold nanoparticle size distribution (Fig. S1, ESI†) was centred at 6 nm. The hollow structures were filled with the gold nanoparticles which can be seen in the enlarged image (Fig. 1d).
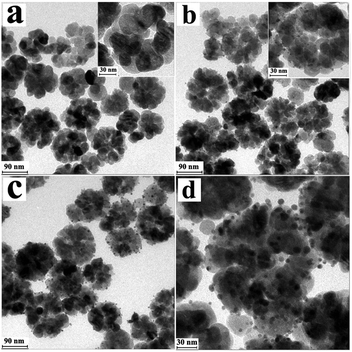 |
| Fig. 1 TEM images of (a) Fe3O4 hollow spheres, (b) Fe3O4@Au nanoseeds, and (c) Fe3O4@Au hollow spheres and (d) magnified image of (c). | |
SEM analysis was also performed to confirm the shape, morphology and internal structure of the Fe3O4 hollow spheres, Fe3O4@Au nanoseeds and Fe3O4@Au hollow spheres for detailed investigation of the final product. From the SEM of the Fe3O4 hollow spheres (Fig. 2a), Fe3O4 hollow spheres with a uniform and non-aggregated nature revealed a relatively coarse surface and a mean diameter of ∼100 nm, and are composed of small primary nanoparticles with an average size of 25–30 nm. And the obvious hollow hole can be observed in the Fe3O4 spheres which was consistent with TEM. Fig. 2b and c indicate that the small Au nanoseeds and Au NPs were supported on the surface of the Fe3O4 hollow spheres, which was also consistent with TEM. From SEM, it can be deduced that the amount of Au loaded was much less than the reported structure.21Fig. 2d shows a typical EDX spectrum of the Fe3O4@Au hollow spheres, which indicates the existence of Au, Fe and O. Other signals in the EDX spectrum arise from silicon slices. The amount of Au NPs in the Fe3O4@Au hollow spheres was 2.54% tested by ICP measurements, which was less compared to a similar reported structure.17,24,31 The result was consistent with the EDX spectrum. Owing to the less expensive noble metal materials, the method of synthesis of Fe3O4@Au hollow spheres was economical. The nitrogen adsorption–desorption isotherms of three materials (Fig. S2, ESI†) were recorded and the BET surface area was calculated to be 41.71 m2 g−1, 42.67 m2 g−1 and 37.57 m2 g−1, respectively.
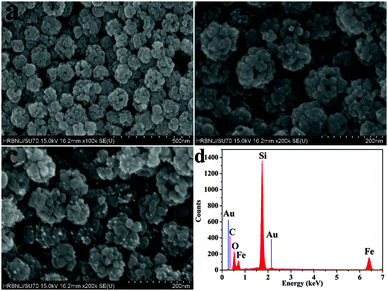 |
| Fig. 2 SEM images of (a) Fe3O4 hollow spheres, (b) Fe3O4@Au nanoseeds, and (c) Fe3O4@Au hollow spheres, and (d) EDX spectrum analysis of (c). | |
Fig. 3 shows diffraction signals of Fe3O4, Fe3O4@Au nanoseeds and Fe3O4@Au hollow spheres in XRD analysis. The sharp diffraction peaks were indexed to (112), (211), (202), (220), (312), (303), (224), (332) and (143) Bragg reflections of crystalline cubic inverse spinel of bulk Fe3O4, respectively (JCPDS no. 75-1609).26 Due to the high dispersity and low loading of Au, there are no obvious characteristic Au peaks in the diffraction pattern of the Fe3O4@Au nanoseeds and Fe3O4@Au hollow spheres. The presence of Au can be proved by the EDX and ICP measurement.
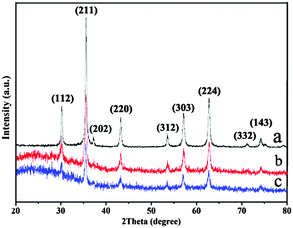 |
| Fig. 3 XRD patterns of (a) Fe3O4 hollow spheres, (b) Fe3O4@Au nanoseeds, and (c) Fe3O4@Au hollow spheres. | |
XPS was performed to investigate the electronic state of Au on the surface of the Fe3O4@Au hollow spheres. The XPS survey spectrum of the Fe3O4@Au hollow spheres showed peaks due to C1s (284.6 eV), O1s (532.6 eV) and Au4f (84.0 eV). As shown in Fig. 4, the high-resolution XPS Au 4f spectrum displayed two peaks corresponding to 4f7/2 and 4f5/2 doublets at 83.4 and 86.95 eV, respectively. The XPS binding energy of Au 4f7/2 was consistent with zerovalent Au.35
 |
| Fig. 4 High-resolution XPS of the Au4f spectrum of Fe3O4@Au hollow spheres. | |
In our experiments, freshly prepared Fe3O4@Au hollow spheres showed their strong magnetic properties and can be easily collected using a permanent magnet (inset of Fig. 5). In order to quantify the magnetism and make sure whether the Fe3O4@Au hollow spheres would bring serious decay to their magnetism, the magnetic hysteresis loop was measured using a vibrating sample magnetometer. As illustrated in Fig. 5, all of the samples were superparamagnetic and both the remanent magnetizations and coercivities were close to zero. The magnetization saturation value of the Fe3O4 hollow spheres was 84.93 emu g−1. After modifying the gold nanoseeds and growth in Au3+, the magnetization saturation value of Fe3O4@Au nanoseeds and Fe3O4@Au hollow spheres was 81.23 emu g−1 and 76.36 emu g−1, respectively. As a result, the decoration of gold nanoseeds and the further growth of gold nanoparticles could weaken the magnetic saturation value of the sample. However, the magnetic saturation value of the Fe3O4@Au nanoseeds and Fe3O4@Au hollow spheres still remained at a high level which possesses a magnetic saturation value of 89.9% of freshly prepared Fe3O4 hollow spheres. Therefore, the magnetic actuation of the Fe3O4 hollow spheres was feasible.
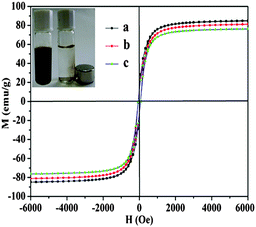 |
| Fig. 5 Magnetization curves of the (a) Fe3O4 hollow spheres, (b) Fe3O4@Au nanoseeds, and (c) Fe3O4@Au hollow spheres. The insets show their suspensions before and after magnetic separation by an external magnet. | |
Catalysis
Among the transition metal-catalyzed redox reactions, the reduction of nitroaromatics is one of the most crucial ones. Noble metal nanoparticle catalysts are widely employed for the reduction of 4-NP to 4-AP.31,32 Catalytic reduction of 4-NP by borohydride ions (BH4−) in the presence of a metal catalyst has become one of the model reactions for evaluating the catalytic activity of noble metallic nanoparticles. In order to test the catalysis of the Fe3O4@Au nanoseeds and Fe3O4@Au hollow spheres, the reactions of reduction of 4-NP were performed under the same conditions. An equal quantity of different catalysts was added into the reaction pool, and the whole reaction can be monitored spectroscopically. Although the reaction is thermodynamic, without catalyst, no reaction occurred after the addition of the freshly prepared NaBH4 solution. After addition of a small amount of catalyst (Fe3O4@Au nanoseeds and Fe3O4@Au hollow spheres), 4-NP was reduced to 4-AP by NaBH4 with the change of the color of the solution. 4-NP showed a distinct spectral profile with an absorption maximum at 317 nm in neutral or acidic solution which can be detected in Fig. S3 (ESI†). The addition of NaBH4 deprotonates the OH group of 4-NP, and the absorption peak shifts to 400 nm immediately (Fig. S3, ESI†), which is due to the formation of 4-nitrophenolate ions.29,30 In order to estimate the efficiency of the catalyst, the predetermined calibration curve has been confirmed in Fig. S4 (ESI†). The reduction kinetics was monitored by UV-vis absorption spectroscopy of the reaction mixture after the addition of the catalyst. When the reduction of 4-NP is started, the absorption peak at 400 nm gradually decreases in intensity. Meanwhile, a small shoulder at 300 nm gradually rises, which is attributed to the absorption of 4-AP. As observed, the reduction of 4-NP to 4-AP was finished within 200 s using the Fe3O4@Au hollow spheres as catalysts (Fig. 6c), which was much shorter than that of the as-prepared Fe3O4@Au nanoseeds (400 s, Fig. 6a). The catalytic reduction of 4-NP can generally be considered to be a pseudo-first-order reaction with regard to the reactant alone on the basis of the almost unchanged concentration of NaBH4 during catalysis, since the concentration of NaBH4 was much higher than that of 4-NP. The reaction rate constant k is calculated from the slope of the linear section of the plots of ln(Ct/C0) versus t (Fig. 6b and d).36 Compared with the as-prepared Fe3O4@Au nanoseeds (k: 9.99 × 10−3 s−1), the Fe3O4@Au hollow spheres exhibit a better catalytic activity for the 4-AP reduction (k: 20.15 × 10−3 s−1). Remarkably, the k value is also higher than those of the Au–Fe3O4 hybrid nanoparticles, the Fe3O4@Au core shell and so on (Table S1, ESI†). The results indicated that Fe3O4@ Au hollow spheres were good catalysts with high efficiency.
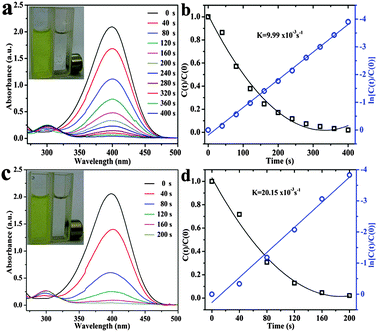 |
| Fig. 6 UV-vis spectra and kinetic rate of the reduction of 4-NP by NaBH4 in the presence of Fe3O4@Au nanoseeds (a and b) and Fe3O4@Au hollow spheres (c and d). The inset pattern is a photograph of the change in the color of the solution before and after reaction and the magnetic separation. | |
Because the reusability of the catalyst was one important issue for practical applications, the reusability of the Fe3O4@Au hollow spheres was tested in detail (Fig. 7 and Fig. S5, ESI†). To further test the reusability of the catalysts, six successive cycles of catalytic reduction were carried out with the Fe3O4@Au hollow spheres. According to the UV-vis spectra of reduction (Fig. S5, ESI†), the kinetic rate was calculated to be 35.66 × 10−3 s−1, 8.6 × 10−3 s−1, 5.34 × 10−3 s−1, 4.48 × 10−3 s−1, 3.65 × 10−3 s−1 and 2.88 × 10−3 s−1, respectively. The catalysts can be successfully recycled and reused for at least six successive cycles of reaction with a stable conversion efficiency of around 100%. Through the above analysis, it is concluded that the Fe3O4@Au hollow spheres have excellent catalytic activity for the reduction of 4-NP, which may be attributed to the synergistic effect between Au and Fe3O4 nanoparticles and the rich edges and corner atoms derived from the Au NPs on the surface of the hollow spheres.24 Otherwise, the hollow structure of the catalyst was active for the catalytic reaction, which is mainly due to the hollow structure that was composed of the small Fe3O4 NPs with Au NPs, so as to improve the catalysis efficiency. The Fe3O4@Au hollow spheres were well-dispersed and exposed inside and outside surfaces of gold nanoparticles, allowing effective contact between the reactants with the catalyst of the reaction. Thus, the Fe3O4@Au hollow spheres exhibited a good reusable catalytic activity.
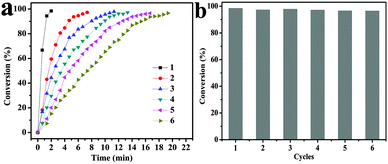 |
| Fig. 7 (a) Relationship of the conversion (%) of 4-NP and the reaction time over Fe3O4@Au hollow sphere catalysts after 1–6 reuses, respectively. (b) The reusability of Fe3O4@Au hollow spheres as catalysts for the reduction of 4-NP with NaBH4. | |
In order to evaluate the stability of the materials in the reaction of catalysis, SEM images and EDX spectra of the catalyst after reusing 1, 3, and 6 times were recorded and are shown in Fig. S6 (ESI†). As can be seen in the SEM images (Fig. S6a, ESI†), the structure and morphology of the Fe3O4@Au hollow spheres after 1 cycle have no obvious change compared with Fig. 2c. After 3 recycles, though the Fe3O4@Au hollow spheres still retained the group of orbicular nanospheres, a small amount of gold nanoparticles could not be found on the surface of the Fe3O4 hollow spheres (Fig. S6b, ESI†). When the reaction was recycled 6 times, the hollow structure of Fe3O4@Au hollow spheres collapsed (Fig. S6c, ESI†). Accompanying the process of reaction, deduced from EDX reports, the components of Au and Fe increased gradually due to the collapsing of the structure. After recycling six times, as catalysts, the Fe3O4@Au hollow spheres still maintained their catalytic activity. The seventh reaction of catalysis has been studied, and 4-NP can be degraded completely (Fig. S7, ESI†), and the kinetic rate K was calculated to be 1.97 × 10−3 s−1. So, the above results indicated that the catalyst shows good reusability for at least 6 successive cycles.
Since the K3Fe(CN)6 reduction was considered as a model electron-transfer reaction, to further study the catalytic properties, the reduction of K3Fe(CN)6 with NaBH4 was selected for monitoring the catalytic activity of Fe3O4@Au towards an inorganic reaction. The light yellow aqueous K3Fe(CN)6 solution shows absorption at 420 nm. After the addition of NaBH4, the intensity of absorption can decrease gradually due to the formation of K4Fe(CN)6 within 12 h (Fig. S8, ESI†). However, after the addition of 25 μL of catalyst, the absorption peak at 420 nm significantly decreased and the reaction process totally completed within 240 s and 150 s, respectively. UV-vis investigations demonstrate that the catalytic activity of Fe3O4@Au hollow spheres was also better than that of the as-prepared Fe3O4@Au nanoseeds (Fig. 8), indicating that the Fe3O4@Au hollow spheres also have excellent catalytic activity for the reduction of K3Fe(CN)6.35 In all runs, the concentration of NaBH4 was chosen to exceed the concentration of hexacyanoferrate(III). In this way, the kinetics of the reduction process can be treated as a pseudo-first-order reaction in hexacyanoferrate.22 The reaction rate constant k is calculated from the slope of the linear section of the plots of ln(Ct/C0) versus t (inset of Fig. 8a and b), 18.65 × 10−3 s−1 and 36.55 × 10−3 s−1, respectively. Compared with the reported work,23,33,34 the Fe3O4@Au hollow spheres exhibited a better catalytic activity. The results indicated the high catalytic activity of Fe3O4@Au toward the reduction of [Fe(CN)6]3− to [Fe(CN)6]4− ions.
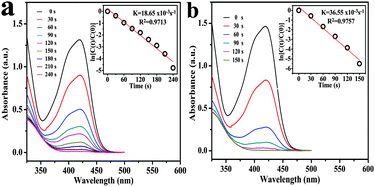 |
| Fig. 8 UV-vis spectra and kinetic rate of the reduction of K3Fe(CN)6 by NaBH4 in the presence of (a) Fe3O4@Au nanoseeds and (b) Fe3O4@Au hollow spheres. Insets: the corresponding ln(Ct/C0) versus reaction time for reduction of K3Fe(CN)6. | |
Though the size of nanoseeds was much smaller than the gold nanoparticles, however, comparing the two processes of catalysis, the Fe3O4@Au hollow sphere was a better catalyst. From the BET of these two catalysts, there is little difference in comparison. But the amount of gold nanoseeds and gold nanoparticles supported on the Fe3O4 was calculated to be 1.034 × 10−3 mg and 1.778 × 10−3 mg in the process of catalysis. So, the most possible reason was that the amount of gold supported on the Fe3O4@Au hollow spheres was much higher than nanoseeds.
To further test the reusability in the reduction of K3Fe(CN)6, twelve successive cycles of catalytic reduction were carried out with the Fe3O4@Au hollow spheres as catalysts. As can be seen in Fig. 9, the catalyst can be reused at the end of the reaction, but the effect of the recovered catalyst on the reaction time of subsequent reaction is depressed gradually from 150 s to 690 s after 10 cycles, and a maximum of 1170 s after 12 cycles (Fig. 9 and Fig. S9, ESI†). Using an external magnetic field, the catalyst can be easily recycled, and long-life and high reusability are demonstrated without a visible decrease in the catalytic performance after running even for more than 12 times. As expected, linear correlation of ln(Ct/C0) versus t of the all runs was obtained and is indicated in Fig. S9 (ESI†). The kinetic constant k was up to 54.01 × 10−3 s−1 in the first cycle, 15.61 × 10−3 s−1 after 6 cycles, and 2.75 × 10−3 s−1 after 12 turns, which was higher than that for other Au catalysts.34 All the above results indicated that the Fe3O4@Au hollow spheres can be used as recyclable and efficient catalysts.
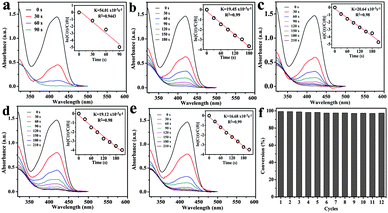 |
| Fig. 9 The UV-vis spectra and kinetic rate of the reduction of K3Fe(CN)6 by NaBH4 under the catalysis of Fe3O4@Au for 1–5 times (a–e); the rate constant k is 54.01 × 10−3, 19.45 × 10−3, 20.64 × 10−3, 19.12 × 10−3, and 16.68 × 10−3 s−1, respectively. (f) The reusability of Fe3O4@Au hollow spheres as catalysts for the reduction of K3Fe(CN)6 with NaBH4. | |
Conclusions
We have demonstrated a facile synthesis of Fe3O4@Au hollow spheres. The preparation of Fe3O4@Au was economical due to the fact that the amount of loading was much less. Due to the large specific surface area provided by the hollow structure with high reactivity, the as-prepared Fe3O4@Au catalysts exhibited an excellent activity for the catalytic reduction of 4-NP and K3Fe(CN)6 by NaBH4. Owing to the incorporation of Fe3O4 nanoparticles, the catalysts could be quickly recycled using a magnet, and hence they exhibited good reusability. We also anticipate that the Fe3O4@Au hollow spheres may provide a platform for broad potential in the reduction of Ag, Pt and Pd, and will be useful for discovering low-cost, highly efficient catalysts for industrially important chemical reactions.
Acknowledgements
The authors gratefully acknowledge financial support from the National Natural Science Foundation of China (21205024), the National Science Foundation for Post-doctoral Scientists of China (2012M520659, 2013T60307), the Natural Science Foundation of Heilongjiang Province (B201305), the Harbin Science and Technology bureau (2014RFQXJ151) and the Program for Scientific and Technological Innovation Team Construction in Universities of Heilongjiang (2011TD010).
Notes and references
- N. L. Rosi and C. A. Mirkin, Chem. Rev., 2005, 105, 1547–1562 CrossRef CAS PubMed.
- P. K. Jain, X. Huang, I. H. El-Sayed and M. A. El-Sayed, Acc. Chem. Res., 2008, 41, 1578–1586 CrossRef CAS PubMed.
- Y. G. Guo, J. S. Hu and L. J. Wan, Adv. Mater., 2008, 20, 2878–2887 CrossRef CAS.
- H. Zhang, M. Jin and Y. Xia, Chem. Soc. Rev., 2012, 41, 8035–8049 RSC.
- C. Gao, Z. Lu, Y. Liu, Q. Zhang, M. Chi, Q. Cheng and Y. Yin, Angew. Chem., Int. Ed., 2012, 51, 5629–5633 CrossRef CAS PubMed.
- A. M. Alkilany, S. E. Lohse and C. J. Murphy, Acc. Chem. Res., 2013, 46, 650–661 CrossRef CAS PubMed.
- M. C. Daniel and D. Astruc, Chem. Rev., 2004, 104, 293–346 CrossRef CAS PubMed.
- M. Rudolph and A. S. Hashmi, Chem. Soc. Rev., 2012, 41, 2448–2462 RSC.
- D. T. Thompson, Nano Today, 2007, 2, 40–43 CrossRef.
- K. Maeda, K. Teramura, D. Lu, N. Saito, Y. Inoue and K. Domen, Angew. Chem., Int. Ed., 2006, 45, 7806–7809 CrossRef CAS PubMed.
- J. E. Mondloch, X. Yan and R. G. Finke, J. Am. Chem. Soc., 2009, 131, 6389–6396 CrossRef CAS PubMed.
- S. Wu, J. Dzubiella, J. Kaiser, M. Drechsler, X. Guo, M. Ballauff and Y. Lu, Angew. Chem., Int. Ed., 2012, 51, 2229–2233 CrossRef CAS PubMed.
- A. Corma and P. Serna, Science, 2006, 313, 332–334 CrossRef CAS PubMed.
- M. Xie, F. W. Zhang, Y. Long and J. T. Ma, RSC Adv., 2013, 3, 10329–10334 RSC.
- Y. H. Deng, Y. Cai, Z. K. Sun, J. Liu, C. Liu, J. Wei, W. Li, C. Liu, Y. Wang and D. Y. Zhao, J. Am. Chem. Soc., 2010, 132, 8466–8473 CrossRef CAS PubMed.
- M. Xie, F. W. Zhang, Y. Long and J. T. Ma, RSC Adv., 2013, 3, 10329–10334 RSC.
- P. Zhang, R. Li, Y. M. Huang and Q. W. Chen, ACS Appl. Mater. Interfaces, 2014, 6, 2671–2678 CAS.
- A. B. Vysakh, C. L. Babu and C. P. Vinod, J. Phys. Chem. C, 2015, 119, 8138–8146 CAS.
- X. W. Meng, B. Li, X. L. Ren, L. F. Tan, Z. B. Huang and F. Q. Tang, J. Mater. Chem. A, 2013, 1, 10513–10517 CAS.
- X. Guo, W. Ye, H. Y. Sun, Q. Zhang and J. Yang, Nanoscale, 2013, 5, 12582–12588 RSC.
- L. Gao, J. Fei, J. Zhao, H. Li, Y. Cui and J. Li, ACS Nano, 2012, 6, 8030–8040 CrossRef CAS PubMed.
- H. Liu, J. Qu, Y. Chen, J. Li, F. Ye, J. Y. Lee and J. Yang, J. Am. Chem. Soc., 2012, 134, 11602–11610 CrossRef CAS PubMed.
- I. Pastoriza-Santos, J. Pérez-Juste, S. Carregal-Romero, P. Hervés and L. M. Liz-Marzán, Chem. – Asian J., 2006, 1, 730–736 CrossRef CAS PubMed.
- Q. Gao, A. W. Zhao, H. Y. Guo, X. C. Chen, Z. B Gan, W. Y. Tao, M. F. Zhang, R. Wu and Z. X. Li, Dalton Trans., 2014, 43, 7998–8006 RSC.
- P. Wang, H. X. Zhu, M. M. Liu, J. R. Niu, B. Yuan, R. Li and J. T. Ma, RSC Adv., 2014, 4, 28922–28927 RSC.
- Y. C. Zhu, J. Lei and Y. Tian, Dalton Trans., 2014, 43, 7275–7281 RSC.
- H. Deng, X. Li, Q. Peng, X. Wang, J. Chen and Y. Li, Angew. Chem., Int. Ed., 2005, 44, 2782–2785 CrossRef CAS PubMed.
- X. M. Zhang, S. S. Ye, X. Zhang and L. P. Wu, J. Mater. Chem. C, 2015, 3, 2282–2290 RSC.
- N. R. Jana, L. Gearheart and C. J. Murphy, Langmuir, 2011, 17, 6782–6786 CrossRef.
- S. N. Abdollahi, M. Naderi and G. Amoabediny, Colloids Surf., A, 2013, 436, 1069–1075 CrossRef CAS.
- Z. U. Rahman, Y. H. Ma, J. Hu, Y. Y. Xu, W. F. Wang and X. G. Chen, RSC Adv., 2014, 4, 5012–5020 RSC.
- Z. Jin, M. Xiao, Z. H. Bao, P. Wang and J. F. Wang, Angew. Chem., Int. Ed., 2012, 51, 6406–6410 CrossRef CAS PubMed.
- X. M. Miao, T. T. Wang, F. Chai, X. L. Zhang, C. G. Wang and W. D. Sun, Nanoscale, 2011, 3, 1189–1194 RSC.
- D. Y. Du, J. S. Qin, T. T. Wang, S. L. Li, Z. M. Su, K. Z. Shao, Y. Q. Lan, X. L. Wang and E. B. Wang, Chem. Sci., 2012, 3, 705–710 RSC.
- H. L. Yang, S. W. Li, X. Y. Zhang, X. Y. Wang and J. T. Ma, J. Mater. Chem. A, 2014, 2, 12060–12067 CAS.
- R. P. Zhao, M. X. Gong, H. M. Zhu, Y. Chen, Y. W. Tang and T. H. Lu, Nanoscale, 2014, 6, 9273–9278 RSC.
Footnote |
† Electronic supplementary information (ESI) available. See DOI: 10.1039/c5nj02436f |
|
This journal is © The Royal Society of Chemistry and the Centre National de la Recherche Scientifique 2016 |
Click here to see how this site uses Cookies. View our privacy policy here.