DOI:
10.1039/C5NJ02018B
(Paper)
New J. Chem., 2016,
40, 295-301
Synthesis and optical–electrochemical gas sensing applications of Ni-doped LiFePO4 nano-particles†
Received
(in Montpellier, France)
31st July 2015
, Accepted 25th October 2015
First published on 27th October 2015
Abstract
Ni-doped LiFePO4 particles synthesized with high purity by a one-step hydrothermal method were used for xylene detection in a self-assembled optical waveguide (OWG) and WS-30A electro-chemical gas sensors. The optical waveguide was fabricated by spin-coating a thin film of LiFe0.995Ni0.005PO4 on the surface of tin-diffused glass. Upon exposing the sensor to xylene gas, a significant change in the output light intensity was observed due to variations in the refractive index, thickness, and absorption coefficient of the film. For a range of xylene concentrations from 10 ppb to 1000 ppm, the sensor showed fast response and recovery times in addition to good reversibility and repeatability. Other substances, when present in concentrations less than 1 ppm, did not interfere with the detection of xylene gas. However, at room temperature, the LiFe0.995Ni0.005PO4 sensing film, when measured by WS-30A electro-chemical gas sensing apparatus, detected a small response (resistance change) to 100 ppm of xylene. The trends of output light changes were consistent with the changes in resistance.
1. Introduction
The synthesis and physio-chemical investigation of materials responsive to changes in gaseous environment are of great interest because of their utility in the fabrication of gas sensors. In particular, semiconductors are widely used as gas sensors because of their outstanding features such as low cost, high sensitivity, long lifetime, fast response, and recovery.1–4 As a semiconductor, lithium iron phosphate (LiFePO4) has attracted great interest for its application in rechargeable lithium-ion batteries and lithium ion sensors.5–7 Although tremendous efforts have been made to overcome the low electronic conductivity and slow diffusion of lithium ions by doping8,9 and using LiFePO4 thin film electrodes,10 there are very few reports on its optical properties.11 Since 2008, our laboratory has been working on the optical and gas sensing properties of LiFePO4 thin films.11–14 After a series of thorough experiments, the numerous advantages of LiFePO4 thin films, such as the excellent optical transparency, easy fabrication, high refractive index (n = 1.88), and significant response to pollutant gases like xylene (detection limit of 50 ppm) were confirmed. However, in this study, Ni was chosen as a dopant to enhance the sensitivity of the film.
The nickel dopant improves the electrochemical performance, and reduces the particle size of LiFePO4, thereby effectively improving the lithium-ion transition rate.15 It generally takes several steps to prepare Ni-doped LiFePO4. However, in this study, the new sensing material (LiFe0.995Ni0.005PO4) was synthesized by a one-step hydrothermal method.
Gas sensing devices fall into two major categories, namely, electro-chemical and optical gas sensors, depending on the sensing mechanism.16 Electro-chemical gas sensors involve the chemisorption of oxygen on the surface of the sensing element at high temperatures. This creates a layer of space charge around the particles followed by a charge transfer during the interaction between the chemisorbed oxygen and the target gas molecules, thus causing a change in the surface resistance of the sensor element.17
Optical gas sensors, in comparison to their electro-chemical counterparts, do not require to be heated and therefore can work at room temperature. This feature expands their applications.18,19 A variety of sensing mechanisms for optical sensors, such as whispering-gallery-mode,20 reverse symmetry waveguides,21 surface Plasmon resonance,22 Fabry–Perot interferometers,23 photonic crystals,24 fiber Bragg gratings,25 and Raman scattering,26 have been proposed.
Among several such methods, planar optical waveguides have several merits such as immunity to electromagnetic interference,27 high sensitivity, high mechanical stability, and reduced size. The basic operational principle of sensors based on planar waveguides is to measure the changes in the refractive index that occur close to the surface of the waveguide film.28 Usually, a change in the refractive index of sensitive materials (films), when exposed to different vapors or gases, leads to a change in the transmitted light intensity (output light intensity).29 Apart from the refractive index, there are many other optical parameters that can affect the light intensity, such as the input light angle (θi), change of film thickness, and the absorption coefficient.
To date, the sensing mechanism of an optical waveguide sensor has generally been explained by a single optical parameter. The ammonia sensing principle, using absorption coefficient variation was proposed by Aissam Airoudj et al.,30 while Akira Yamaguchi et al.31 studied the sensor response by observing the changes in the complex refractive index of the sensing layer. In our previous studies,11,32 the sensing principle focused on the change of the refractive index of the sensing film or molecular absorption power (Pabs). In this study, the sensing principle involves the optical and electrical parameters such as the refractive index, thickness, and resistance variations of the sensing film.
In this study, in order to improve the sensitivity of LiFePO4, Ni doped LiFePO4 was synthesized using a one-step hydrothermal method, and was subsequently utilized in benzene, toluene, and xylene and styrene (BTXS) sensing. The gas sensing performance of LiFe0.995Ni0.005PO4 was monitored by a planar optical waveguide and a resistance-type gas testing system (WS-30A). The sensing principle involved measuring the changes in the refractive index, thickness, and resistance of the sensing film.
2. Experimental
2.1 Preparation of LiFe0.995Ni0.005PO4 particles
LiFe0.995Ni0.005PO4 particles were prepared following the methods reported earlier.14 Briefly, FeSO4·7H2O, 85 wt% H3PO4, and LiOH·H2O, all analytically pure, were mixed in a molar ratio of 1
:
1
:
3. Then, Ni(NO3)2 (Ni
:
LiFePO4 = 0.5
:
99.5) and 0.1 g of ascorbic acid were added, respectively. The resulting mixture was placed in a hydrothermal reactor (inner volume: 100 ml), and the hydrothermal synthesis was carried out at 150 °C for 15 h. After allowing it to cool naturally and filtering, the prepared sample was dried under vacuum at 120 °C for 1 h. X-ray diffraction (XRD) patterns were recorded on an X-ray diffractometer (DPMax 2400, Japan) using graphite-monochromatized Cu Kα radiation (λ = 1.5418 Å). Elemental analyses of the obtained powders were performed using an Oxford 2000 energy disperse spectroscope (EDS). The morphological study was carried out using a transmission electron microscope (model: HITACHI H600). In addition, the average grain sizes of the products were also calculated (Table S1, ESI†).
2.2 Fabrication of the sensing films and the measurement of their attenuation, thickness, and refractive index
The sensing films were prepared as follows: (1) the LiFe0.995Ni0.005PO4 powder (0.012 g) was dissolved in 10 cm3 of solvent [a mixture of phosphate acid (4 wt%), and polyvinyl alcohol (1.5 wt%)]. (2) The obtained LiFe0.995Ni0.005PO4 solution was coated onto the surface of a tin-diffused glass OWG (n = 1.52 with the guiding layer being 1 and 2 μm deep) using a spin-coater over a period of 25 s at a rotation speed of 1700 rpm. (3) After the spin-coating process, the coated film was placed in a vacuum desiccator for 24 h at room temperature.
The thickness and refractive index of the sensing film were determined using a Tianjin SGC-10 ellipsometer. The attenuation in the thin film due to absorption and scattering was measured using the cut back method.14,33
2.3 Gas sensing measurement
The gas sensing measurement of LiFe0.995Ni0.005PO4 was performed using a self-assembled optical waveguide (OWG) gas testing apparatus and a WS-30A electro-chemical gas sensor device, respectively.
The OWG gas testing apparatus14 (see Fig. S1, ESI†) contained compressed air sources, a LiFe0.995Ni0.005PO4 thin film-based OWG gas-sensitive element, a laser source (650 nm), a flow meter, a reflector, a diffusion tube, a light detector (photo multiplier), and a recorder (computer). The LiFe0.995 Ni0.005PO4 thin film-based OWG gas-sensitive element was fixed to the detection cell. For each measurement, a new syringe was used to inject 20 cm3 of the gas sample into the flow chamber, and then flowed out from the vent. In order to transfer the sample gas into the sensor, dry air was flowed through the cell at a constant rate of 60 cm3 min−1. Further, it functioned as a carrier and dilution gas. All measurements were performed at room temperature.
Standard xylene gas was obtained by vaporizing a given amount of a xylene solution (99.5%) inside a standard vessel (600 cm3). The concentration of the xylene gas was confirmed using a commercial xylene gas detection tube (Gastec, with a working range of 2–200 ppm, manufactured by Beijing Municipal Institute). Different amounts of the standard xylene gas were diluted with dry air in a second standard vessel (600 cm3) in order to obtain the desired concentrations. Using this standard-vessel-dilution method, very low concentrations of xylene (in the ppb range) could be obtained.
Resistance measurement. A static test system made by Zhengzhou Weisheng Electronics Co. Ltd was used for the examination of the resistance change of the LiFe0.995 Ni0.005PO4 film, when it was exposed to xylene. In the test process, the alumina ceramic tube, assembled using platinum wire electrodes for electrical contacts, was dipped into the LiFe0.995Ni0.005PO4 solution several times to form the sensing film. The films were placed in a vacuum desiccator for 24 h at room temperature. Then, a Ni–Cr heater was inserted into the alumina ceramic tube to supply the operating temperature in the range of 80–450 °C. The alumina ceramic tube was used directly without the Ni–Cr heater for measurements at room temperature. The resistance of the sensor was measured using a conventional circuit, in which the element was connected to an external resistor in series at a circuit voltage of 10 V.
3. Results and discussion
3.1 Characterization of LiFe0.995Ni0.005PO4 particles
The synthesized sample was characterized by using XRD with a Cu Kα source, EDS and TEM (Fig. 1). The XRD pattern shows that all the diffraction peaks follow the standard crystal structure patterns (JCPDS data of LiFePO4).9 Diffraction peaks for Ni were not observed because of its low concentration (≤0.5 wt%). The fact that the peaks were so similar to the standard ones for LiFePO4 suggested the absence of significant amounts of any byproducts in the samples, and the existence of an orthorhombic olivine crystal structure. The EDS measurement reveals the existence of Fe, P, O, and trace levels (0.48%) of Ni in the products. These results confirm that Ni-doped LiFePO4 can be synthesized with high purity by a one-step hydrothermal method. From TEM images in Fig. 1(c), it is seen that the sample shows for about 50 nm sized particles, and are composed of orthorhombic nanoparticles.
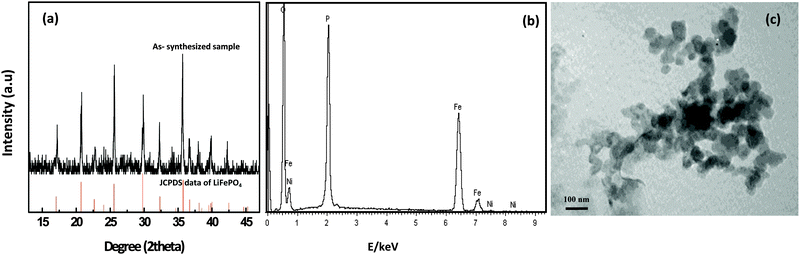 |
| Fig. 1 (a) X-ray diffraction pattern; (b) energy dispersion spectra; (c) TEM image of LiFe0.995Ni0.005PO4. | |
The average grain sizes of the products were calculated using the Scherrer formula, and the calculated results (see Table S1, ESI†) show that upon Ni doping with small concentrations, the average size of the particles decreases. This is one reason for an increased sensitivity of the sensor.
3.2 Characteristics of the LiFe0.995Ni0.005PO4 thin film
In an OWG sensor, the sensing film's refractive index, thickness, and attenuation are the major factors that affect its sensitivity. A sensing film with low attenuation and a high refractive index generally exhibits higher sensitivity. The film has lower attenuation with 10.9 dB mm−1, and the thickness and refractive index (at λ = 650 nm) were 239.2 nm and 1.7203, respectively; the average of three consecutive tests using ellipsometry, and the standard deviation was 1.11 × 10−4 nm. The surface morphology of the sensing film was investigated by atomic force microscopy (AFM), and the images are shown in Fig. 2. The average surface roughness of the sensing film in the measured area of 2 × 2 μm was 3 nm, which indicates that it is dense and relatively smooth.
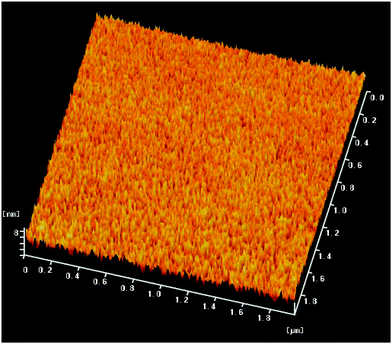 |
| Fig. 2 Atomic force microscope image of the LiFe0.995Ni0.005PO4 thin film. | |
3.3 Gas sensing properties of the LiFe0.995Ni0.005PO4 thin film based OWG
The response of the LiFe0.995 Ni0.005PO4 thin film/tin-diffused-glass-based OWG to 1000 ppm of Volatile Organic Compounds (VOCs) is shown in Fig. 3. The sensing element was tested by benzene, toluene, xylene, styrene, formaldehyde, alcohols, and chloroform. The sensor exhibited a high response to BTXS, while there were small responses to alcohol, dichloromethane, chloroform, or formaldehyde vapours. The sensing performance of the OWG sensor is related to the molar refractive index (RD) of the target gas; the RD of xylene, styrene, toluene, and benzene were 35.8, 35.2, 31.1, and 26.2, respectively. Because of its higher molar refractive index, xylene exhibited higher absorption performance.34
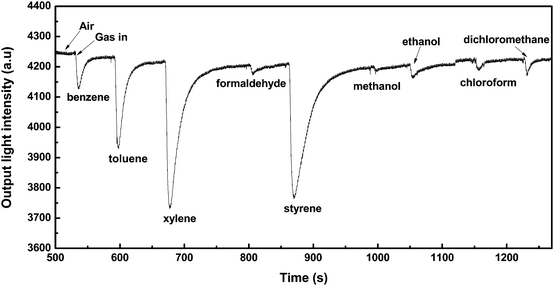 |
| Fig. 3 Response of the LiFe0.995Ni0.005PO4 thin film/tin diffused glass optical waveguide sensing element to 1000 ppm of VOCs. | |
Fig. 4(a) shows the typical response of the LiFe0.995Ni0.005PO4 thin film/tin-diffused glass- based OWG sensor to different concentrations of xylene gas. Here, it can be seen that upon exposure to xylene, the optical properties (refractive index or transmittance, Fig. 4b) of the sensing film change, thus decreasing the output light intensity rapidly. When the xylene gas was removed, the output light intensity returned to its original level, similar to that of dry air. The detection limits for the LiFe0.995 Ni0.005PO4 thin film/tin-diffused-glass-based OWG sensor were 10 ppb–1000 ppm. The response and recovery times were fast (less than 5 s and 50 s, respectively). The responses of a typical sensor repeatedly exposed to dry air and xylene gas with a concentration of 100 ppb are shown in Fig. 4(a). The responses (changes in the output light intensity) remained constant and were fully reversible after each injection of 100 ppb of xylene gas. These results demonstrate the reproducibility of the response of the OWG sensor to xylene gas.
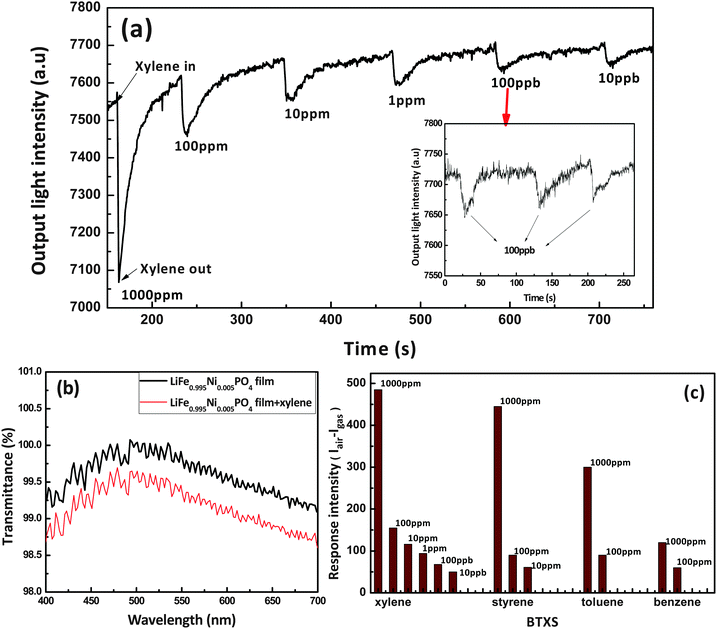 |
| Fig. 4 (a) Typical response of the LiFe0.995Ni0.005PO4 thin film/tin diffused glass OWG to xylene vapor in pure air; (b) transmittance change of the LiFe0.995Ni0.005PO4 thin film, when it is exposed to xylene; (c) the response of the LiFe0.995Ni0.005PO4 thin film OWG to xylene, styrene, toluene and benzene gas with different concentrations. | |
The output light intensity (transmitted light intensity) is related to the adsorption coefficient, refractive index, and thickness of the sensing film,35 given by the expression
where
I is the transmitted light intensity (output light),
I0 is the input light intensity,
a is the absorption coefficient,
N (=
L/2
d![[thin space (1/6-em)]](https://www.rsc.org/images/entities/char_2009.gif)
tg
θγ) is the reflectance number of the guided wave on the surface of the optical waveguide at a distance
L and depth of the waveguide
d,
de (=2
df/cos
θγ) is the length of the actual path of light in the sensing film of thickness
df. Here, the transmitted light intensity decreased when the absorption coefficient, refractive index, and thickness of the sensing film were increased.
The changes in the refractive index, thickness, and transmittance of the LiFe0.995Ni0.005PO4 thin film on exposure to saturated xylene gas were monitored and the test results are shown in Table 1. The refractive index and thickness changes were measured using a SGC-10 ellipsometer, and transmittance was measured by an ultraviolet spectrophotometer (UV-2450 Japan). Upon xylene gas exposure, the refractive index, thickness, and adsorption coefficient of the LiFe0.995Ni0.005PO4 thin film were expected to increase, leading to a subsequent decrease in the output light intensity.
Table 1 The change of the refractive index, thickness, and transmittance of the LiFe0.995Ni0.005PO4 sensing film, when it was exposure to xylene (λ = 650 nm)
|
Refractive index (n) |
Thickness (nm) |
Transmittance (%) |
Before exposure to xylene |
1.7203 |
239.2(1.11 × 10−4) |
99.4 |
After exposure to xylene |
1.8286 |
242.2(1.11 × 10−4) |
98.9 |
Furthermore, the response of the LiFe0.995Ni0.005PO4 thin film-based OWG sensor to various concentrations of benzene, toluene, and styrene was studied. From Fig. 4c, it can be concluded that when the concentration decreased to 10 ppm, the remaining BTXS vapors caused no interference with the detection of xylene vapor, except for the case of styrene. On the other hand, when the concentration was further reduced to below 1 ppm, all other substances caused no interference with the detection of xylene vapor.
3.4 Resistance change of the LiFe0.995Ni0.005PO4 thin film
In an n-type semiconductor, the oxidation reaction at the surface between the reducing gas and the negatively charged surface-adsorbed oxygen (O− or O2−) leads to the injection of electrons from the surface to the semiconducting core.36 This decreases the sensor resistance in proportion to gas concentration. In contrast, in a p-type semiconductor, the electron injection from the reaction between the reducing gas and the negatively charged surface oxygen increases the sensor resistance by decreasing the major charge carrier (hole) concentration.
The LiFe0.995Ni0.005PO4 sensing element was fixed in the WS-30A gas testing system, and its response to 100 ppm of xylene at room temperature was measured (Fig. 5a). Before each round of measurement, the sensor was exposed to air and the measured resistance of the sensor was Ra (response of the sensor to air). A desired amount of xylene gas was injected into the chamber before each round of measurement. The measured resistance changed gradually. After a certain time, the resistance changed very slowly, almost reaching a stable value, Rg, corresponding to the response of the sensor to xylene gas. The glass chamber was then removed from the sensor to expose it to air again. In this case, the measured resistance reached its original value, Ra. The response curve indicates that the resistance of the sensor decreases when it is exposed to xylene gas (electron-donor). This suggests that LiFe0.995Ni0.005PO4 behaves as an n-type semiconductor. In addition, we note that the LiFe0.995Ni0.005PO4 thin film exhibits a weak response to xylene gas at room temperature (Fig. 5b), while displaying a maximum response at the operating temperature of 350 °C.
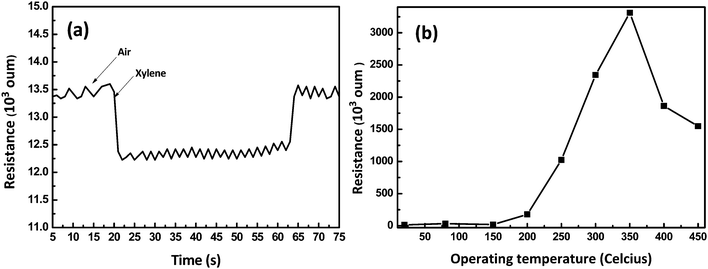 |
| Fig. 5 (a) Gas sensing transient of the LiFe0.995Ni0.005PO4 film upon exposure to 100 ppm xylene at room temperature; (b) above room temperature. | |
For semiconductor materials, the refractive index (n) of sensing materials is related to the conductivity (σ) given by:37
|  | (2) |
where
σ is conductivity,
ε0 is the dielectric constant, and
ω is laser frequency.
Besides, the conductivity is inversely proportional to resistance, given by
and
From the relations in eqn (2), (3), and (4), it can be derived that the refractive index is inversely proportional to resistance, given by
Overall, when a LiFe
0.995Ni
0.005PO
4 thin film is exposed to electron donor gases such as xylene, there is an increase in the charge carrier concentration, leading to a decrease in resistance. This leads to an increase in the refractive index, causing a decrease in output light intensity. The trends of output light changes are consistent with the resistance changes.
3.5 Influence of doping amount
In order to analyze the influence of doping amounts on the sensing properties of the film, LiFe1−0.01xNi0.01xPO4 powder with different concentrations (x = 1, 2) of the dopant Ni was prepared in high purity via a one-step hydrothermal method, and the grain size was calculated (see Table S1, ESI†). The average grain size of particles was 49.6 nm for LiFe0.99Ni0.01PO4 and 50.5 nm for LiFe0.98Ni0.02PO4. The LiFe1−0.01xNi0.01xPO4 and LiFePO4 thin film-based OWGs were prepared similarly to the LiFe0.995Ni0.005PO4 thin film OWG, and were used to test the VOCs. From the testing results (Fig. 6), it can be seen that all of the LiFe1−0.01xNi0.01xPO4 thin film-based OWGs exhibited a large response to BTXS, while having a small response to others such as formaldehyde, methanol, and ethanol. Further, the response intensity (ΔI = Iair − Igas) of these sensors decreased with an increase in the dopant concentration. This was largely because of the increase in attenuation (11.2 dB mm−1 for LiFe0.99Ni0.01PO4 and 13.5 dB mm−1 for LiFe0.98Ni0.02PO4) and average grain size of the sensing materials with an increase in the dopant concentration.
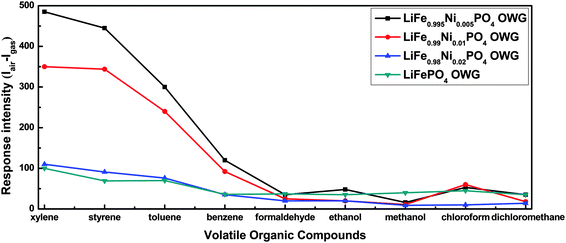 |
| Fig. 6 Response of LiFe1−0.01xNi0.01xPO4 and the LiFePO4 thin film/tin diffused glass optical waveguide sensor to 1000 ppm of VOCs. | |
4. Conclusions
In conclusion, the synthesis, optical properties, and sensing applications of a new sensing material, Ni-doped LiFePO4, are described. LiFe0.995Ni0.005PO4 was synthesized using a one-step hydrothermal method, and was utilized in BTXS gas sensing. In an OWG gas testing apparatus, the response of the LiFe0.995Ni0.005PO4 thin film to xylene gas was higher compared to others. The LiFe0.995Ni0.005PO4 thin film-based OWG sensor could easily detect 10 ppb of xylene gas with a response time of less than 5 s. In this study, the sensing principle is based on the changes of the refractive index, thickness, and absorption coefficient of the sensing film. At low concentrations (below 1 ppm), other substances did not cause any interference with the detection of xylene gas. The sensitivity of the LiFe1−0.01xNi0.01x PO4 thin film OWGs decreased with an increase in the dopant concentration. Using an electrochemical gas sensing apparatus, the LiFe0.995Ni0.005PO4 thin film can exhibit a small response to xylene gas at room temperature. The trends of output light changes are consistent with the resistance changes. The LiFe0.995Ni0.005PO4 thin film-based gas sensor, with its fast response and high sensitivity to xylene gas, is also inexpensive and reusable and therefore is a promising sensor for detecting VOC gases.
Acknowledgements
The authors would like to acknowledge the National Natural Science Foundation of China and the Doctoral Natural Science Foundation of Xinjiang University for the support of this project under the 21265020 and 209-61371 grants.
References
- D. Chen, X. Hou, H. Wen, Y. Wang, H. Wang, X. Li, R. Zhang, H. Lu, H. Xu, S. Guan, J. Sun and L. Gao, J. Nanotechnol., 2010, 21, 035501 CrossRef PubMed
.
- Q. Ahsanulhaq, Y. Toshinari, E. M. ElMaghraby and K. Toshio, Appl. Phys. Lett., 2009, 95, 153 Search PubMed
.
- Y. Zhang, J. Xu, P. Xu, Y. Zhu, X. Chen and W. Yu, J. Nanotechnol., 2010, 21, 285 Search PubMed
.
- C. Junchen and X. Jiaqiang, Sens. Actuators, B, 2011, 157, 494 CrossRef
.
- F. Sauvage, J. M. Tarascon and E. Baudrin, Anal. Chim. Acta, 2008, 622, 163 CrossRef CAS PubMed
.
- C. S. Li and S. Y. Zhang, Nano Res., 2008, 1, 242 CrossRef CAS
.
- K. Zaghib, A. Mauger and F. Gendron, Ionics, 2008, 14, 271 CrossRef CAS
.
- C. Legrand, L. Dupont, K. Tang, H. Li, X. J. Huang and E. Baudrin, Thin Solid Films, 2010, 518, 5447 CrossRef CAS
.
- K. S. Park, J. T. Son and H. T. Chung, Solid State Commun., 2004, 129, 311 CrossRef CAS
.
- L. Hui and X. Jingying, J. Mater. Process. Technol., 2009, 209, 477 CrossRef
.
- P. Nizamidin, A. Yimit, W. Ji De and K. Itoh, Thin Solid Films, 2012, 520, 6250 CrossRef CAS
.
- P. Nizamidin, A. Yimit and W. Ji De, Curr. Anal. Chem., 2012, 8, 557 CrossRef CAS
.
- P. Nizamidin, A. Yimit, M. Momin and W. Ji De, Chin. J. Anal. Chem., 2011, 39, 1871 Search PubMed
.
- P. Nizamidin, A. Yimit, A. Abdurrahman and K. Itoh, Sens. Actuators, B, 2013, 176, 460 CrossRef CAS
.
- G. Yucui, Y. Xuedong, L. Jing, Z. Xianfa, W. Jiawei, H. Xingguang, W. Rongshun and X. Haiming, Electrochim. Acta, 2010, 55, 5886 CrossRef
.
- K. Zakrzewska, Vacuum, 2004, 74, 335 CrossRef CAS
.
- T. Thuy Trinh, N. Han Tu, H. Hoang Le, K. Yul Ryu, K. Binh Le, K. Pillai and J. Yi, Sens. Actuators, B, 2011, 152, 73 CrossRef
.
- J. Gong, Y. H. Li, X. S. Chai, Z. S. Hu and Y. L. Deng, J. Phys. Chem. C, 2010, 114, 1293 CAS
.
- S. W. Fan, A. K. Srivastava and V. P. Dravid, Appl. Phys. Lett., 2009, 95, 142106 CrossRef
.
- J. Knittel, T. G. McRae, K. H. Lee and W. P. Bowen, Appl. Phys. Lett., 2010, 97, 123704 CrossRef
.
- R. Horvath, H. C. Pedersen, N. Skivesen, D. Selmeczi and N. B. Larsen, Appl. Phys. Lett., 2005, 86, 071101 CrossRef
.
- L. Y. Shao, Y. Shevchenko and J. Albert, Opt. Express, 2010, 18, 11464 CrossRef CAS PubMed
.
- J. Wang, B. Dong, E. Lally, J. Gong, M. Han and A. Wang, Opt. Lett., 2010, 35, 619 CrossRef CAS PubMed
.
- J. Cooper, A. Glidle and R. D. L. Rue, Opt. Photonics News, 2010, 21, 26 CrossRef CAS
.
- J. Ang, H. C. H. Li, I. Herszberg, M. K. Bannister and A. P. Mouritz, Int. J. Fatigue, 2010, 32, 762 CrossRef CAS
.
- R. Gao, N. Choi, S. I. Chang, S. H. Kang, J. M. Song, S. I. Cho, D. W. Lim and J. Choo, Anal. Chim. Acta, 2010, 681, 87 CrossRef CAS PubMed
.
- S. A. Taya, M. M. Shabata and H. M. Khalil, Optik, 2010, 121, 860 CrossRef CAS
.
- D. Kumar, S. Kumar and V. Singh, Optik, 2012, 123, 1530 CrossRef CAS
.
- A. Airoudj, B. Bêche, D. Debarnot, E. Gaviot and F. Poncin-Epaillard, Opt. Commun., 2009, 282, 3839 CrossRef CAS
.
- A. Airoudj, D. Debarnot, B. Bêche and F. Poncin-Epaillard, Anal. Chem., 2008, 80, 9188 CrossRef CAS PubMed
.
- A. Yamaguchi, K. Hotta and N. Teramae, Anal. Chem., 2009, 81, 105 CrossRef CAS PubMed
.
- H. Ablat, A. Yimit, M. Mahmut and K. Itoh, Anal. Chem., 2008, 80, 7678 CrossRef CAS PubMed
.
-
H. Nishihara, M. Haruna and T. Suhara, Integrated Optics, Japan, 1st edn, 1987, p. 251 Search PubMed
.
-
S. Kondo,T. Ishikawa and I. Abe, Adsorb science, 2nd edn, 2001, p. 155 Search PubMed
.
- G. Zhylyak, V. Ramoz-Perez, M. Linnhoff, T. Hug, D. Citterio and U. E. Spichiger-Keller, J. Opt. Lasers Eng., 2005, 43, 603 CrossRef
.
-
Y.-Y. Zhang, Semiconductor Optoelectronics, Science Press, Shanghai, 1987, p. 23 Search PubMed
.
- K. Yoon-Sung, H. In-Sung, K. Sun-Jung, L. Choong-Yong and L. Jong-Heun, Sens. Actuators, B, 2008, 135, 298 CrossRef
.
Footnote |
† Electronic supplementary information (ESI) available. See DOI: 10.1039/c5nj02018b |
|
This journal is © The Royal Society of Chemistry and the Centre National de la Recherche Scientifique 2016 |