Emerging investigators series: pyrolysis removes common microconstituents triclocarban, triclosan, and nonylphenol from biosolids†
Received
2nd October 2015
, Accepted 3rd December 2015
First published on 3rd December 2015
Abstract
Reusing biosolids is vital for the sustainability of wastewater management. Pyrolysis is an anoxic thermal degradation process that can be used to convert biosolids into energy rich py-gas and py-oil, and a beneficial soil amendment, biochar. Batch biosolids pyrolysis (60 minutes) revealed that triclocarban and triclosan were removed (to below quantification limit) at 200 °C and 300 °C, respectively. Substantial removal (>90%) of nonylphenol was achieved at 300 °C as well, but 600 °C was required to remove nonylphenol to below the quantification limit. At 500 °C, the pyrolysis reaction time to remove >90% of microconstituents was less than 5 minutes. Fate studies revealed that microconstituents were both volatilized and thermochemically transformed during pyrolysis; microconstituents with higher vapor pressures were more likely to volatilize and leave the pyrolysis reactor before being transformed than compounds with lower vapor pressures. Reductive dehalogenation products of triclocarban and suspected dehalogenation products of triclosan were identified in py-gas. Application of biosolids-derived biochar to soil in place of biosolids has potential to minimize organic microconstituents discharged to the environment provided appropriate management of py-gas and py-oil.
Water impact
Reuse of biosolids is critical for sustainable water resource recovery. Biosolids carry organic microconstituents, such as pharmaceuticals, antimicrobials, and other consumer product chemicals, that cause concern when land applying biosolids. This research demonstrates that pyrolysis could be used to remove organic microconstituents from biosolids.
|
Introduction
Land application of wastewater biosolids is often an economical and beneficial way to reuse nutrients.1 Although land application can be beneficial, constituents other than nutrients are released to the environment.2,3 Many organic microconstituents, including antimicrobials, surfactants, hormones, pharmaceuticals, and personal care products are not removed during conventional biosolids handling processes, such as anaerobic digestion, and are discharged to the environment following land application of biosolids.4–9 The fate of microconstituents is variable following land application as they remain in soil,10 are sequestered by plants,10–13 biodegraded,14 transferred in runoff,15 and bioaccumulate into earthworms.16 New solids management processes that remove microconstituents and produce a beneficial soil conditioner would provide wastewater treatment utilities with a viable option if they desired to reuse biosolids while minimizing release of these organic microconstituents to the environment.
Pyrolysis is a thermal process that occurs in the absence of oxygen and is gaining interest for biosolids management.17,18 Pyrolysis produces a beneficial soil conditioner, biochar, as well as pyrolysis-gas and pyrolysis-liquid (a.k.a. bio-oil), both of which have energy content and can be used as fuel.19–21 Depending on operating conditions and feedstock volatile solids concentration, the pyrolysis gas can yield enough energy to offset the energy required for the pyrolysis process.22 The energy available in py-gas and py-oil is enough to cover the energy costs of the pyrolysis process and offset some of the energy required to dry biosolids.23 Biochar is used for different land-application purposes than biosolids because biochar has less available nutrients and carbon.24 Still, biochar has many benefits when used as a soil conditioner. For instance, biochar contributes to carbon sequestration when land-applied because the carbon does not readily degrade; the mean residence time of carbon in biochars made at 550 °C was estimated to be over 1000 years.25 Additionally, biochar can increase water holding capacity, crop yields and soil quality on less fertile soils, and can reduce nutrient runoff from land via adsorbtion.19,21,26,27
A potential benefit of pyrolysis is that the biochar product might contain substantially less organic microconstituents compared to biosolids. While previous research has not determined the impact of biosolids pyrolysis on microconstituents such as antimicrobials, pharmaceuticals and personal care products, surfactants, or hormones, the impact of pyrolysis on legacy organic pollutants has been investigated. Pyrolysis of wastewater biosolids at 450 °C removed polychlorinated biphenyls (PCBs) by 75% from industrial organic residue,28 and pyrolysis of contaminated sediment at 800 °C removed greater than 99% of dioxins and PCBs.29 Hu et al. (2007) attributed the removal to volatilization, while Bridle et al. (1990) suspected, but did not confirm that dehalogenation occurred when the chlorinated compounds volatilized; they presumed that the hydrogen gas created a reductive environment for dehalogenation to occur.28,29 Pyrolysis of the PCB mixture, Aroclor 1254, with methane as an added reactant, resulted in dehalogenation.30 Dehalogenation has also been confirmed in pyrolysis of brominated compounds.31 Dioxins and PCBs have lower vapor pressures than several common microconstituents, such as triclosan for example, which is also a chlorinated aromatic compound (see ESI† section ES7, Table ES7-1). Therefore, we hypothesized that pyrolysis would also remove organic microconstituents from biosolids by volatilization since the microconstituents have higher vapor pressures than dioxins and PCBs.
The objective of this work was to determine the impact of pyrolysis on the antimicrobials triclosan (TCS) and triclocarban (TCC), and the surfactant mixture nonylphenol (NP) in biosolids. The antimicrobials TCS and TCC were investigated as target microconstituents to remove because of their high abundance in biosolids, their biological impacts on organisms, and their potential impacts on antibiotic resistance.3,32–35 NP was investigated because it is also found in high abundance in biosolids and is an endocrine disrupting compound.3,4,36–38
Materials and methods
Pyrolysis temperature and reaction time experiments
Biosolids thermal treatment was performed between 100 and 600 °C by adding approximately 1.5 grams of biosolids to 50 mL flasks in triplicate. The biosolids material was a heat-dried blend of waste activated sludge and anaerobically digested primary solids from a municipal water resource recovery facility (Milorganite®, Milwaukee Metropolitan Sewerage District, Milwaukee, WI). These biosolids were chosen over wet biosolids because a drying step was not needed in the lab prior to pyrolysis and because dried biosolids have been commercially pyrolyzed at full scale in the past.39 The flasks were sparged for five minutes with argon, covered with aluminum foil, and heated in a muffle furnace (Fischer-Scientific Isotemp®, Waltham MA) for one hour. A room temperature control was prepared in the same manner and placed in the oven with no heat for one hour. Multiple pyrolysis experiments were also conducted at 500 °C with reaction times of 2.5, 5, 10, and 60 minutes to determine the impact of reaction time.
Volatilization and transformation of microconstituents during pyrolysis
Microconstituent fate experiments were performed in a closed pyrolysis system to categorize microconstituent volatilization and chemical transformation (Fig. 1). A stainless steel pyrolysis reactor (110 mL) was loaded with Ottawa sand (Fischer Scientific, Ottawa, Ontario) to act as a controlled solid state carrier for the microconstituents. Sand was used so that the only organic reactions taking place would be from heat and the microconstituents added. These experiments were performed to determine a baseline fate when the organic microconstituents are heated under anoxic conditions. However, biosolids are composed of a complex matrix of organic and inorganic material, all of which could alter chemical reactions of organic microconstituents. The sand was spiked with 1 mg each of TCS, TCC, and NP via addition of a methanol (HPLC grade) stock solution and then exposed to air for 12 hours to allow methanol to evaporate. TCS (sold as Irgasan, ≥97%), TCC (≥97%), and NP (technical grade mixture) were purchased from Sigma-Aldrich (St. Louis, MO). The reactor was sealed with a high-temperature graphite flange gasket (McMaster-Carr, Elmhurst, IL) and bolted stainless steel cover and placed in a tube furnace (model 55642, Thermo Fisher Scientific, Waltham MA). The system was tested for leaks, and then argon gas was passed through the reactor at a flow rate of 60 mL min−1. Heating was initiated, and the temperature was maintained at 500 °C for two hours. Stainless steel piping leading out of the reactor was connected to norprene tubing that led to five glass impingers, each filled with approximately 100 mL of methanol, connected by norprene tubing (Fig. 1). The first two impingers were housed in an ice bath to cool vapour and condense products, and the final three impingers were at room temperature. The microconstituents present in methanol represented the microconstituents that would be present in pyrolysis-oil and pyrolysis-gas. The system cooled to ambient temperature overnight. Subsequently, microconstituents were extracted from the stainless steel piping and norprene tubing using methanol. Several rinses utilizing 15 mL of methanol were conducted after the first pyrolysis run to determine the volume of methanol required to extract microconstituents within piping and tubing. It was found that 15 mL and 90 mL of methanol were required to rinse the piping and tubing to and from the reactor, respectively, and extract the remaining analytes. Microconstituents were extracted from the sand as described below.
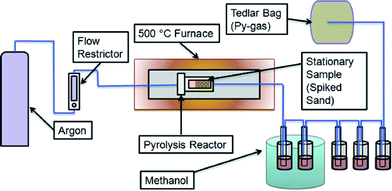 |
| Fig. 1 Microconstituent fate study experimental setup. Stainless steel piping is used to introduce argon into the stainless steel pyrolysis reactor. Methanol was added to impingers to collect volatilized microconstituents that are pushed out of the reactor via slow, but constant argon gas flow. A Tedlar bag was used to close the system. | |
A room temperature control experiment was conducted using the closed pyrolysis system to verify that removal of microconstituents could be attributed to pyrolysis and not experimental artifacts. In addition, a negative control experiment was conducted in which clean sand (no microconstituents added) was pyrolyzed to verify that no false positives appeared from heat reactions with the norprene tubing or other components.
Microconstituent extraction and analysis
Analytes were extracted from biosolids, biochar, and sand using an accelerated solvent extractor (ASE) (ASE 350, ThermoFisher Scientific, Waltham, MA). Approximately one gram of sample was mixed with Ottawa Sand (Fischer Scientific, Ottawa, Canada) and added to a 10 mL ASE extraction cell. Methanol was selected as the extraction solvent after determining it provided the greatest recovery for the suite of analytes tested (see ESI,† section ES1 for solvent combinations tested). The extraction conditions included an oven heating time of 5 minutes followed by two extraction cycles at an oven temperature of 60 °C and pressure of 1500 psi. Each extraction cycle consisted of a static time of 5 minutes and a flush volume of 60% of the extraction cell volume. The ASE cell was cleaned using a robust procedure modified from Anger et al., (2013) to minimize background concentrations and cross-contamination between extractions with minor modifications.40 Briefly, ASE end caps and ASE cells were triple rinsed with DI water and methanol, sonicated in acetone for 10 minutes, and triple rinsed again with methanol.
Microconstituent concentrations in extracts from the temperature experiments were determined by liquid chromatography-tandem mass spectrometry (LC-MS/MS) using a Shimadzu Prominence HPLC coupled to an AB Sciex tandem mass spectrometer. Method details, quantification limits, and quality assurance/quality control measures are provided in the ESI,† section ES2. Spike-and-recovery tests results are shown in the ESI,† section ES2 Table ES2-1. Microconstituent concentrations in extracts from the time experiments and sand experiments were determined by liquid chromatography-mass spectrometry (LC-MS) using a Shimadzu LCMS-2020 (Shimadzu Scientific Instruments, Columbia MD). Method details, quantification limits, and quality assurance/quality control measures are provided in the section ES3.† Spike-and-recovery test results are shown in the ESI,† section ES3, Table ES3-1. None of the analytes were detected above the quantification limits in method blanks.
Results and discussion
Pyrolysis temperature and reaction time
The impact of temperature on the removal of TCC, TCS, and NP from wastewater biosolids was determined in batch pyrolysis experiments. Pyrolysis is typically performed at temperatures of 450 °C or greater, and in these experiments pyrolysis removed all three microconstituents from the resultant biochar (Fig. 2). In fact, lower temperature thermal processing at 200 and 300 °C removed TCC and TCS, respectively, to below the quantification limit (0.10 mg kg−1 for both compounds). Greater than 95% removal of NP was also achieved at 300 °C, but pyrolysis at 500 °C was required for NP in two of the three samples to be below quantification limit (0.25 mg kg−1) and 600 °C was required to remove NP to below the quantification limit in all three samples. Previous research demonstrated that increasing pyrolysis temperature from 500 °C to 700 °C had minimal effect on the percent of carbon in biochar, but it did decrease the amount of available nutrients in the biochar.41 These results indicate that biosolids pyrolysis could decrease the amount of TCC, TCS, and NP released to the environment when land applying biosolids-derived biochar relative to land application of biosolids. The py-oil and py-gas also must be appropriately managed to ensure that compounds that transition to these phases are not transferred to the environment.
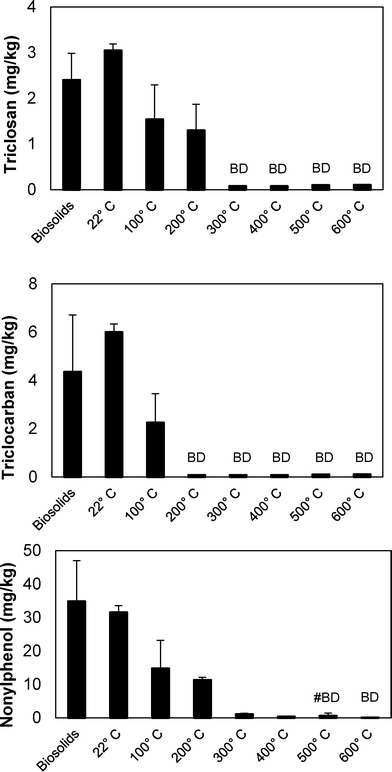 |
| Fig. 2 Impact of temperature on removal of triclosan (top), triclocarban (middle), and nonylphenol (bottom) during thermal processing/pyrolysis. Data points represent the average concentration and error bars represent the standard deviation among the triplicate experiments (n = 3). The “biosolids” bar represents the feed biosolids that was not pyrolyzed (n = 9). Non-detects were plotted as detection limits and are marked with “B.D.” to indicated below detection limit. The #BD marker indicates that two of the three samples were below detection limit. | |
At 500 °C, the pyrolysis reaction time required to remove the majority of microconstituents from biochar was less than 5 minutes (Fig. 3). Both TCC and TCS were removed to below quantification limit (0.10 mg kg−1 for both chemicals) from biochar after five minutes. NP, however, was still present after 60 minutes of pyrolysis at 500 °C. The NP concentrations at each time point were statistically different from each other (ANOVA, p-value < 0.0001); the NP concentrations at 2.5, 5, 10, and 60 minutes were statistically different from the feed (posthoc Tukey's multiple comparisons test, all p-values < 0.05), but were not statistically different from each other (posthoc Tukey's multiple comparisons test, all p-values > 0.05). Average NP removal across the four time points was approximately 90%. The fact that NP remained after 60 minutes in these experiments conducted at 500 °C corresponds to the data presented in Fig. 2, i.e., 600 °C was required to remove NP to below quantification limits.
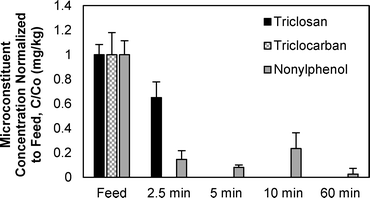 |
| Fig. 3 Impact of pyrolysis reaction time on removal of TCS, TCC, and NP from biosolids during pyrolysis at 500 °C. Data points represent the average concentration and error bars represent the standard deviation among the triplicate experiments (n = 3). | |
The data from Fig. 2 and 3 indicate that pyrolysis can be used to substantially remove these organic microconstituents from biosolids, and these data correspond to what others have observed. Pyrolysis of contaminated biosolids at 450 °C for 30 minutes removed more than 85% of PCB's.28 Pyrolysis of sediment also removed dioxins by volatilization, albeit these experiments were performed at 800 °C for 30 minutes29 Biosolids pyrolysis would most likely be conducted at temperatures of at least 450 °C with retention times of five minutes or more to optimize production of biochar and py-gas.39,41 Based on results from this study, biosolids pyrolysis systems would remove organic microconstituents from solids to create a beneficial biochar soil amendment that contains substantially less microconstituent mass compared to dried biosolids. In a full-scale system, the amount of time required for pyrolysis would be dependent on the mass of biosolids processed, and a longer pyrolysis reaction time may be required depending on the amount of biosolids processed. Additionally, more energy inputs would initially be required to heat more biosolids, but there is potential that the energy available in py-gas and py-oil would offset energy needs for pyrolysis. The enthalpy of pyrolysis of biosolids was previously estimated to be −1130 kJ kg−1 at 500 °C,23 and other work found that pyrolysis of biosolids can be exothermic or endothermic.22 More research should be conducted to determine how energy inputs and outputs of pyrolysis change as a function of temperature.
Fate of microconstituents during pyrolysis
TCS, TCC, and NP were spiked into a reactor loaded only with sand and heated for two hours at 500 °C to determine if the microconstituents volatilized and/or transformed during pyrolysis. A room temperature control experiment was conducted; the recovery of TCS, TCC, and NP in the sand was 58%, 62%, and 42%, respectively, and none of the microconstituents were detected downstream in the methanol collection system (see ESI,† section ES4, Fig. ES6). After pyrolysis at 500 °C, none of the microconstituents were detected in the sand, which corroborates the findings above that biosolids pyrolysis removed these organic microconstituents from the solid phase. In the sand-spiked experiments, a substantial portion of TCS and NP mass was recovered in methanol within the impinger system (approximately 40%), but less than 5% of TCC was detected in the methanol (Fig. 4).
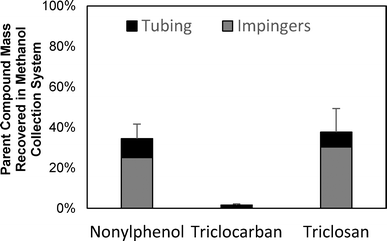 |
| Fig. 4 The impact of pyrolysis on the fate of microconstituents spiked into sand. No microconstituents were detected in sand following pyrolysis at 500 °C for two hours. Following pyrolysis the mass recovered in the methanol collection system (tubing + impingers) was highest for NP and TCS which had the highest vapor pressures. The error bars represent the standard deviation observed among the total amounts of mass recovered for each microconstituent between the triplicate runs (n = 3). | |
The substantially lower recovery of TCC may be a result of chemical transformation during pyrolysis. The recovery of microconstituents in the experimental system after pyrolysis, a potential indicator of transformation, correlated to the vapor pressures of the microconstituents. Microconstituents with higher vapor pressures volatilized and were recovered in the methanol collection system at rates similar to the negative control experiments (approximately 40%), while microconstituents with lower vapor pressures were barely recovered (<2%) in the methanol collection system (see Fig. 4 and Table 1). The lower vapor pressures of TCC may result in TCC having longer retention times under pyrolytic conditions because they do not volatilize as quickly and are therefore exposed to higher temperatures for extended periods of time. The reaction time for transformations to occur would be greater for low-vapor-pressure microconstituents compared to high-vapor-pressure microconstituents. More complete transformation would result in a decrease in recovery for low-vapor-pressure microconstituents. Hu et al. (2007) attributed the high pollutant recovery in their pyrolysis system to the quick volatilization and exiting of the compounds from the pyrolysis reactor.29 They postulated that, if the pollutants remained in the reactor longer, then the pollutants would have transformed during the higher temperatures at longer reaction times. Miskolczi et al. (2008) also found that flame retardant plastics underwent dehalogenation to a greater extent in a lengthened pyrolysis tube reactor when compared to typical fluidized bed and fixed bed reactors due to long residence times achieved in tube reactors.42
Table 1 Microconstituent estimated vapor pressure from the US EPA Estimations Program Interface Suite (EPI Suite v4.11)
Microconstituent |
Vapor pressure (mm Hg) |
Nonylphenol |
6.86 × 10−4 |
Triclosan |
4.65 × 10−6 |
Triclocarban |
3.61 × 10−9 |
Reductive dechlorination was a suspected chemical transformation mechanism for TCC and TCS. Both compounds are polychlorinated (see Table 2) and susceptible to biological reductive dehalogenation,43–46 implying that they could also be susceptible to abiotic reductive dehalogenation under appropriate conditions. Indeed, lesser chlorinated TCC homologs, 1-(3,4-dichlorophenyl)-3-phenylurea and 1-(4-chlorophenyl)-3-phenylurea, were detected in methanol in the impinger system after pyrolysis (Table 2). Standards for these chemicals were available (Sigma Aldrich, St. Louis, MO) to confirm the peaks on the LC-MS, and are shown in the ESI,† section ES5. The moles of 1-(3,4-dichlorophenyl)-3-phenylurea recovered were nearly equal to the moles of TCC recovered (Table 2). The moles of dechlorinated products recovered in the condenser system did not account for a substantial portion of the parent compound molar mass spiked into the system, but their detection indicated that thermochemical reductive dehalogenation occurred during pyrolysis.
Table 2 Triclosan, triclocarban, and dechlorinated product structures
Compound |
Structure |
Percent of moles found in condenser system normalized to moles of parent compound spiked |
Denotes triplicate runs.
Denotes duplicate runs.
NA denotes standards not available.
|
Triclocarban |
|
1.3a |
1-(3,4-Dichlorophenyl)-3-phenylurea |
|
0.97b |
1-(4-Chlorophenyl)-3-phenylurea |
|
0.02b |
|
|
|
Triclosan |
|
40.7a |
5-Chloro-2-(4-chlorophenoxy)phenol |
|
NAc |
5-Chloro-2-phenoxyphenol |
|
NA |
Lesser chlorinated TCS homologs, 5-chloro-2-(4-chlorophenoxy)phenol and 5-chloro-2-phenoxyphenol, were also suspected in methanol in the impinger system (see ESI,† section ES6). Standards were not commercially available for these two TCS homologs, but LC-MS analytes were detected having mass/charge (m/z) ratios expected for these lesser chlorinated homologs. The analyte retention times were shorter than TCS, indicating a decrease in hydrophobicity that would be expected when chlorine atoms are replaced by hydrogen atoms. These compounds ostensibly are more soluble than their parent compounds and, if released, more easily transported throughout the environment; therefore, management of the py-oil and py-gas is important to minimize the release of microconstituents back to the environment. These transformation products were not detected in the biochar.
A hydrogen source is required for reductive dechlorination of TCC and TCS to occur.31 These experiments were carried out with microconstituents spiked into sand, so hydrogen available to exchange with chlorine during decholorination would be from fragments of other decomposed microconstituents within the system. The dechlorination reaction rate may have been limited by the lack of hydrogen. In actual biosolids, dechlorination of microconstituents during pyrolysis could occur more rapidly because the organic fraction of biosolids would undergo decomposition and release more hydrogen into the gas phase. While the results from these experiments indicate that organic microconstituents are removed from biosolids by either thermochemical transformation or volatilization, future work should investigate the role of biosolids constituents, such as metals and organic matter, on chemical transformation products.
Finally, in the negative control heat was applied to the system but sand was not spiked with microconstituents; microconstituents were not detected in impinger methanol or piping/tubing extracts, indicating that heating the system did not yield an experimental artifact in which microconstituents were produced. The negative control and room temperature experiments along with the pyrolysis heated experiments confirmed that pyrolysis was responsible for removing microconstituents from the sand and transporting parent compounds and transformation products to the py-gas.
Conclusions
Pyrolysis of biosolids could minimize the discharge of microconstituents to the environment via land application of the residual solids. Microconstituents can be removed from the resulting biochar when 1.5 g of heat-dried biosolids are pyrolyzed at 500 °C for 2.5 minutes. In a full-scale system, the microconstituents detected would be transferred to the pyrolysis gas and pyrolysis oil as either the parent compound or a transformation product. Both the pyrolysis-gas and pyrolysis-oil could be combusted for energy recovery if properly refined. If complete combustion occurs, then the microconstituents in the oil and gas would be mineralized. Future work should be conducted to determine the fate of microconstituents during combustion of pyrolysis-gas and pyrolysis-oil to ensure that these microconstituents are not released to the environment during handling of these pyrolysis products. In summary, pyrolysis could be added as a biosolids processing step that reduces the amount of organic microconstituents discharged to the environment with residual solids.
Acknowledgements
Funding for J. J. Ross was provided by the Industry University Collaborative Research Program for Water Equipment & Policy in Milwaukee, Wisconsin, USA, under NSF Grant number 0968844, a grant by the Lafferty Family Foundation, and by Marquette University.
References
- Q. Lu, Z. L. He and P. J. Stoffella, Land application of biosolids in the USA: A review, Appl. Environ. Soil Sci., 2012, 2012, 1–11 CrossRef.
- A. K. Venkatesan, B. F. G. Pycke and R. U. Halden, Detection and Occurrence of N - Nitrosamines in Archived Biosolids from the Targeted National Sewage Sludge Survey of the U.S. Environmental Protection Agency, Environ. Sci. Technol., 2015, 48, 5085–5092 CrossRef PubMed.
- K. Mcclellan and R. U. Halden, Pharmaceuticals and personal care products in archived U. S. biosolids from the 2001 EPA national sewage sludge survey, Water Res., 2010, 44, 658–668 CrossRef CAS PubMed.
- P. J. McNamara, C. A. Wilson, M. T. Wogen, S. N. Murthy, J. T. Novak and P. J. Novak, The effect of thermal hydrolysis pretreatment on the anaerobic degradation of nonylphenol and short-chain nonylphenol ethoxylates in digested biosolids, Water Res., 2012, 46, 2937–2946 CrossRef CAS PubMed.
- C. Kinney, E. Furlong and S. Zaugg, Survey of organic wastewater contaminants in biosolids destined for land application, Environ. Sci. Technol., 2006, 40, 7207–7215 CrossRef CAS PubMed.
- J. Heidler, A. Sapkota and R. U. Halden, Partitioning, persistence, and accumulation in digested sludge of the topical antiseptic triclocarban during wastewater treatment, Environ. Sci. Technol., 2006, 40, 3634–3639 CrossRef CAS PubMed.
- J. Heidler and R. U. Halden, Fate of organohalogens in US wastewater treatment plants and estimated chemical releases to soils nationwide from biosolids recycling, J. Environ. Monit., 2009, 11, 2207 RSC.
- J. Heidler and R. U. Halden, Mass balance assessment of triclosan removal during conventional sewage treatment, Chemosphere, 2007, 66, 362–369 CrossRef CAS PubMed.
- J. Heidler and R. U. Halden, Meta-Analysis of Mass Balances Examining Chemical Fate during Wastewater Treatment, Environ. Sci. Technol., 2008, 42, 6324–6332 CrossRef CAS PubMed.
- E. F. Davis, C. K. Gunsch and H. M. Stapleton, Fate of flame retardants and the antimicrobial agent triclosan in planted and unplanted biosolid-amended soils, Environ. Toxicol. Chem., 2014, 34, 968–976 CrossRef PubMed.
- H. Lee, A. G. Tevlin and S. A. Mabury, Fate of polyfluoroalkyl phosphate diesters and their metabolites in biosolids-applied soil: Biodegradation and plant uptake in greenhouse and field experiments, Environ. Sci. Technol., 2014, 48, 340–349 CrossRef CAS PubMed.
- A. C. Blaine, C. D. Rich, E. M. Sedlacko, L. S. Hundal, K. Kumar, C. Lau, M. A. Mills, K. M. Harris and C. P. Higgins, Perfluoroalkyl acid distribution in various plant compartments of edible crops grown in biosolids-amended soils, Environ. Sci. Technol., 2014, 48, 7858–7865 CrossRef CAS PubMed.
-
R. S. Prosser, S. Trapp and P. K. Sibley, Modeling Uptake of Selected Pharmaceuticals and Personal Care Products into Food Crops from Biosolids-Amended Soil, 2014 Search PubMed.
- E. Walters, K. McClellan and R. U. Halden, Occurrence and loss over three years of 72 pharmaceuticals and personal care products from biosolids-soil mixtures in outdoor mesocosms, Water Res., 2010, 44, 6011–6020 CrossRef CAS PubMed.
- Y. Y. Yang, J. L. Gray, E. T. Furlong, J. G. Davis, R. C. ReVello and T. Borch, Steroid hormone runoff from agricultural test plots applied with municipal biosolids, Environ. Sci. Technol., 2012, 46, 2746–2754 CrossRef CAS PubMed.
- C. A. Kinney, E. T. Furlong, D. W. Kolpin, M. R. Burkhardt, S. D. Zaugg, S. L. Werner, J. P. Bossio and M. J. Benotti, Bioaccumulation of pharmaceuticals and other anthropogenic waste indicators in earthworms from agricultural soil amended with biosolid or swine manure, Environ. Sci. Technol., 2008, 42, 1863–1870 CrossRef CAS PubMed.
- D. Woolf, J. Lehmann, E. M. Fisher and L. T. Angenent, Biofuels from Pyrolysis in Perspective: Trade-offs between Energy Yields and Soil-Carbon Additions, Environ. Sci. Technol., 2014, 48(11), 6492–6499 CrossRef CAS PubMed.
-
L. Gildea, Technology Spotlight: Kore Infrastructure, Water Environment Research Foundation athttp://<http://www.werf.org/lift/docs/LIFT_Notes_Docs/Technology_Spotlight_5-14-15.aspx> Search PubMed.
- D. Woolf, J. Lehmann, E. M. Fisher and L. T. Angenent, Biofuels from Pyrolysis in Perspective: Trade-offs between Energy Yields and Soil-Carbon Additions, Environ. Sci. Technol., 2014, 48, 6492–6499 CrossRef CAS PubMed.
- J. G. Rogers and J. G. Brammer, Estimation of the production cost of fast pyrolysis bio-oil, Biomass Bioenergy, 2012, 36, 208–217 CrossRef CAS.
- D. A. Laird, R. C. Brown, J. E. Amonette and N. National, Review of the pyrolysis platform for coproducing bio-oil and biochar, Biofuels, Bioprod. Biorefin., 2009, 3(5), 547–562 CrossRef CAS.
- M. K. Hossain, V. Strezov and P. F. Nelson, Thermal characterisation of the products of wastewater sludge pyrolysis, J. Anal. Appl. Pyrolysis, 2009, 85, 442–446 CrossRef CAS.
-
P. J. McNamara, J. Koch and D. Zitomer, Pyrolysis of Wastewater Biosolids: Lab-Scale Experiments and Modeling, in Proceedings of the Water Environment Federation, 2014, pp. 1–14 Search PubMed.
- M. K. Hossain,
v.
Strezov, K. Y. Chan, A. Ziolkowski and P. F. Nelson, Influence of pyrolysis temperature on production and nutrient properties of wastewater sludge biochar, J. Environ. Manage., 2011, 92, 223–228 CrossRef CAS PubMed.
- B. P. Singh, A. L. Cowie and R. J. Smernik, Biochar carbon stability in a clayey soil as a function of feedstock and pyrolysis temperature, Environ. Sci. Technol., 2012, 46, 11770–11778 CrossRef CAS PubMed.
- J. Lehmann, J. Gaunt and M. Rondon, Bio-char Sequestration in Terrestrial Ecosystems – A Review, Mitig. Adapt. Strateg. Glob. Chang., 2006, 11, 395–419 CrossRef.
- D. A. Laird,
et al., Impact of biochar amendments on the quality of a typical Midwestern agricultural soil, Geoderma, 2010, 158, 443–449 CrossRef CAS.
- T. R. Bridle, I. Hammerton and C. K. Hertle, Control of heavy metals and organochlorines using the oil from sludge process, Water Sci. Technol., 1990, 22, 249–258 CAS.
- Z. Hu, R. Navarro, N. Nomura, H. Kong, S. Wijesekara and M. Matsumura, Changes in chlorinated organic pollutants and heavy metal content of sediments during pyrolysis, Environ. Sci. Pollut. Res., 2007, 14, 12–18 CrossRef CAS PubMed.
- D. Evans, M. Pirbazari, B. Sidney, T. Tsotsis and J. Devinny, Pyrolytic destruction of polychlorinated biphenyls in a reductive atmosphere, J. Hazard. Mater., 1991, 27, 253–257 CrossRef CAS.
- A. Hornung, A. I. Balabanovich, S. Donner and H. Seifert, Detoxification of brominated pyrolysis oils, J. Anal. Appl. Pyrolysis, 2003, 70, 723–733 CrossRef CAS.
- D. E. Carey, D. H. Zitomer, K. Hristova, A. D. Kappell and P. J. McNamara, Triclocarban influences antibiotic resistance and alters anaerobic digester microbial community structure, Environ. Sci. Technol., 2015 DOI:10.1021/acs.est.5b03080.
- P. J. McNamara, T. M. LaPara and P. J. Novak, The impacts of triclosan on anaerobic community structures, function, and antimicrobial resistance, Environ. Sci. Technol., 2014, 48, 7393–7400 CrossRef CAS PubMed.
- G. Cherednichenko, R. Zhang, R. A. Bannister, V. Timofeyev, N. Li, E. Fritsch, W. Feng, G. C. Barrientos, N. H. Schebb, B. D. Hammock, K. G. Beam, N. Chiamvimonvat and I. N. Pessah, Triclosan impairs excitation-contraction coupling and Ca2+ dynamics in striated muscle, Proc. Natl. Acad. Sci. U. S. A., 2012, 109, 14158–14163 CrossRef CAS PubMed.
- D. E. Carey and P. J. McNamara, The impact of triclosan on the spread of antibiotic resistance in the environment, Front. Microbiol., 2015, 5, 1–11 Search PubMed.
- A. K. Venkatesan and R. U. Halden, National inventory of alkylphenol ethoxylate compounds in U.S. sewage sludges and chemical fate in outdoor soil mesocosms, Environ. Pollut., 2013, 174, 189–193 CrossRef CAS PubMed.
- H. Masuyama, Y. Hiramatsu, M. Kunitomi, T. Kudo and P. N. MacDonald, Endocrine disrupting
chemicals, phthalic acid and nonylphenol, activate Pregnane X receptor-mediated transcription, Mol. Endocrinol., 2000, 14, 421–428 CrossRef CAS PubMed.
- M.-L. Janex-Habibi, A. Huyard, M. Esperanza and A. Bruchet, Reduction of endocrine disruptor emissions in the environment: the benefit of wastewater treatment, Water Res., 2009, 43, 1565–1576 CrossRef CAS PubMed.
- T. R. Bridle and S. Skrypski-Mantele, Experience and lessons learned from sewage sludge pyrolysis in Australia, Water Sci. Technol., 2004, 49(10), 217–223 CAS.
- C. T. Anger, C. Sueper, D. J. Blumentritt, K. McNeill, D. R. Engstrom and W. A. Arnold, Quantification of Triclosan, Chlorinated Triclosan Derivatives, and their Dioxin Photoproducts in Lacustrine Sediment Cores, Environ. Sci. Technol., 2013, 47, 1833–1843 CrossRef CAS PubMed.
- M. K. Hossain, V. Strezov Vladimir, K. Y. Chan, A. Ziolkowski and P. F. Nelson, Influence of pyrolysis temperature on production and nutrient properties of wastewater sludge biochar, J. Environ. Manage., 2011, 92, 223–228 CrossRef CAS PubMed.
- N. Miskolczi, W. J. Hall, A. Angyal, L. Bartha and P. T. Williams, Production of oil with low organobromine content from the pyrolysis of flame retarded HIPS and ABS plastics, J. Anal. Appl. Pyrolysis, 2008, 83, 115–123 CrossRef CAS.
- T. R. Miller,
et al., Fate of triclosan and evidence for reductive dechlorination of triclocarban in estuarine sediments, Environ. Sci. Technol., 2008, 42, 4570–4576 CrossRef CAS PubMed.
- P. J. Mcnamara and M. J. Krzmarzick, Triclosan enriches for Dehalococcoides-like Chloroflexi in anaerobic soil at environmentally relevant concentrations, FEMS Microbiol. Lett., 2013, 344, 48–52 CrossRef CAS PubMed.
- M. J. Krzmarzick and P. J. Novak, Removal of chlorinated organic compounds during wastewater treatment: achievements and limits, Appl. Microbiol. Biotechnol., 2014, 98(14), 6233–6242 CrossRef CAS PubMed.
- B. F. G. Pycke, I. B. Roll, B. J. Brownawell, C. A. Kinney, E. T. Furlong, D. W. Kolpin and R. U. Halden, Transformation products and human metabolites of triclocarban and triclosan in sewage sludge across the United States, Environ. Sci. Technol., 2014, 48, 7881–7890 CrossRef CAS PubMed.
Footnote |
† Electronic supplementary information (ESI) available. See DOI: 10.1039/c5ew00229j |
|
This journal is © The Royal Society of Chemistry 2016 |
Click here to see how this site uses Cookies. View our privacy policy here.