Layered/spinel heterostructured Li-rich materials synthesized by a one-step solvothermal strategy with enhanced electrochemical performance for Li-ion batteries†
Received
1st September 2015
, Accepted 11th November 2015
First published on 12th November 2015
Abstract
Li-rich materials, Li1.140Mn0.622Ni0.114Co0.124O2, of a layered/spinel heterostructure were synthesized by a one-step solvothermal route with subsequent moderate heat treatment. The as-prepared materials consist of hierarchical microspheres and an integral layered/spinel heterostructure. The effects of calcination time on both the structure and electrochemical performance of materials have been studied systematically. It has been found that the formation of the spinel structure could be controlled by adjusting the calcination time at 650 °C, and the materials calcined at this temperature for 24 hours present the optimal electrochemical performance. High initial efficiencies of 101% at 0.2C and 92% at 2C, as well as high discharge capacities of 280, 256, 234 and 206 mA h g−1 respectively at 1C, 2C, 5C and 10C have been achieved. The empty 16c octahedral site and 3D Li+ diffusion channel provided by the spinel have been regarded as the key to the improvement of electrochemical performances.
Introduction
Lithium ion batteries (LIBs) with high energy and high power density have played a critical role in recent energy storage devices.1,2 High-voltage Li-rich and Mn based cathode materials have attracted wide attention due to their high capacity (>250 mA h g−1), which is significantly superior to the conventional cathode materials, such as layered LiCoO2, spinel LiMn2O4, olivine LiFePO4 and layered LiMn1/3Ni1/3Co1/3O2.2–5 Moreover, the high contents of Mn and Ni elements instead of Co in the materials offer advantages of low cost and improved safety.6–9 These features make Li-rich materials promising cathode candidates for next generation LIBs.
In spite of these superiorities, high-capacity Li-rich materials suffer from some fatal inherent problems, including poor rate capacity and low initial coulombic efficiency caused by low electronic conductivity and especially the extraction of Li2O at charge potentials above 4.5 V for the activation of Li2MnO3.3,5,7,10–12 Much effort has been made to address these problems and improve the electrochemical performance of Li-rich materials. On the one hand, compositing Li-rich materials with lithium-free insertion hosts (V2O5, Li4Mn5O12, LiV3O8 and MoO3)7,13,14 and mild acid treatment15,16 have been demonstrated to limit the initial capacity loss; on the other hand, the design of hierarchical micro/nanostructures8,17 and increasing the exposure of {010} active planes4,18 are effective routes to enhance the rate capability of Li-rich materials.
Recently, much effort has been made to illustrate that the formation of a “layered (R
m)–layered (C2/m)–spinel (Fd
m)” heterostructure in Li-rich materials could significantly improve the rate capability,12,19–24 in which the 3D Li+ diffusion channels provided by the spinel structure could greatly enhance the Li-ion diffusion rate.19,20 One possible strategy to prepare a composite structure of Li-rich cathodes is to grind mechanically the layered and spinel materials,25,26 which provides only average performance of the two components but is limited to further improvement of the electrochemical performance.
Another feasible approach to synthesize heterostructured materials is via surface modification, i.e. AlF3 coating, which contributes to the overall improvement of the electrochemical performance of Li-rich materials and has been demonstrated to stimulate the transformation of the layered to spinel structure in the surface region.22,27,28 Wu et al. have successfully revealed the merits of spinel membrane-encapsulated layered Li-rich materials that presented outstanding rate capabilities of 219 mA h g−1 at 5C between 2 and 4.8 V, but delivered an inferior initial efficiency lower than 80% at 0.1C.19,23 The study of Wei and co-workers pointed out that a co-precipitation method with dopamine coating could be applied to fabricate layered@spinel@carbon Li-rich materials with high discharge capacity as well as superior rate capability.29 The designed layered/spinel heterostructured Li-rich cathode materials via surface modification exhibit also enhanced electrochemical kinetic properties.30,31 Although these surface-modified approaches have significantly boosted rate performance, their processes of post-treatment are complex and expensive.
Apart from the above mentioned strategies, a one-step preparation without any following modification is regarded as an effective, energy-saving and labour-saving approach, in considering the direct formation of a layered/spinel heterostructure during the synthesis process and the synthetic effects of the two components. For example, hierarchical structured Li-rich materials of a “layered (R
m)–layered (C2/m)–spinel (Fd
m)” composite phase prepared by Amine et al. using a co-precipitation method presented excellent rate capabilities of 159 mA h g−1 at 5C in a voltage range of 2–4.8 V.21 Li et al. reported a new spinel–layered Li-rich microsphere synthesized by a solvothermal-precursor method with urea as a precipitating agent, which could deliver a high rate capability of 184 at 5C between 2 and 4.6 V.20 These reported materials nevertheless exhibited a poor initial coulombic efficiency below 70%. Current efforts usually tend to focus on the effects of the calcination temperature on the emergence of a heterostructure,12,20 while the dramatic influence of the calcination time on layered/spinel heterostructured materials should not be ignored.
Herein, with the aim to reveal the effects of the calcination time on materials, we report a solvothermal strategy to one-step synthesize Li-rich microspheres, Li1.140Mn0.622Ni0.114Co0.124O2, of a layered/spinel heterostructure. This strategy is an optimization of our previously reported oxalate-precursor route,8,17 by which Li-rich materials with porous hierarchical microstructure were successfully prepared. Such an improved method owns advantages of stimulation to form heterostructures at moderate calcination temperatures. The synthesized samples have a general formula of Li1.140Mn0.622Ni0.114Co0.124O2. Such a composition is determined by ICP-OES analysis, in which the element proportion, Li
:
Mn
:
Ni
:
Co of 1.140
:
0.622
:
0.114
:
0.124, is very close to the proportion of metal ions (Li
:
Mn
:
Ni
:
Co = 1.16
:
0.60
:
0.12
:
0.12) in starting compounds.
The results suggest that the formation of a spinel phase has been controlled along with the extension of calcination time. Besides, for the first time, the unmodified materials show the merits of impressive high initial coulombic efficiency and remarkable rate capability at the same time. The materials obtained by 24 hour calcination at 650 °C exhibit the optimal electrochemical performance, including a high initial coulombic efficiency of 101% at 0.2C and an excellent rate capacity of 280, 256, 234 and 206 mA h g−1 at 1C, 2C, 5C and 10C, respectively. To the best of our knowledge, such excellent performance is the best among Li-rich materials reported so far.
Experimental
Materials preparation
Integral layered/spinel heterostructured Li-rich materials, Li1.140Mn0.622Ni0.114Co0.124O2, were prepared from the same precursors prepared by a solvothermal method. The strategy can effectively preserve the raw material from loss, i.e. ensuring a stoichiometric element amount proportion of starting compounds. Mn(CH3OO)2·H2O, Ni(CH3OO)2·H2O, and Co(CH3OO)2·H2O as the starting materials with stoichiometric amounts (0.6
:
0.12
:
0.12) were first dissolved in ethanol solution with a metal ion concentration of 1 M, and then a double quantity of oxalic acid was added as a precipitating agent. Finally, 5% excess of Li(CH3OO) was introduced as a lithium source. All the raw materials were of analytical purity grade. After stirring vigorously for hours, the mixed solution was pre-treated in a Teflon container at 180 °C for 12 h. Then the obtained solvothermal precursors were evaporated to dryness with continuous stirring at 80 °C. The dried mixture was first calcined at 450 °C for 6 h and then at 650 °C for 12, 24 or 36 h in air before it is naturally cooled down to room temperature. The samples are denoted as T12, T24, and T36 according to their calcination times.
Characterization
The chemical compositions of the synthesized materials have been determined by using an inductively coupled plasma-optical emission spectrometer (ICP-OES, Thermo Electron IRIS Intrepid II XSP). The morphology of materials was observed by scanning electron microscopy (SEM, Hitachi S-4800 SEM) and transmission electron microscopy (TEM, JEOL JEM-2100 microscope). The crystal structure was characterized by powder X-ray diffraction (XRD) patterns recorded on an automated Philips X'Pert Pro Super X-ray diffractometer with Cu Kα radiation. Data were collected over the 2 theta range of 10–80° with a scan rate of 1° min−1. XRD refinement was conducted by a Rietveld method using PDXL program (Rigaku Corporation, PDXL 2.1). Raman spectroscopic studies were carried out on an XploRA (HORIBA) using a 532 nm excitation line with a laser power of 0.1 mW on the sample surface.
Electrochemical tests
Electrodes were made of a mixture of the active material, BLACK PEARLS 2000 carbon black and polyvinylidenedifluoride (PVDF) binder at a weight ratio of 80
:
10
:
10 on a Al foil current collector. The electrode area was about 1.13 cm2 and the loading density of the active material was about 3–4 mg cm−2. Electrochemical experiments were carried out using 2025 coin cells with lithium metal foil as counter electrodes and conducted on a Land battery tester (LAND-V2001A, Land Electronic Co., Ltd., Wuhan). The electrolyte was 1 M LiPF6 dissolved in ethylene carbonate and dimethyl carbonate (EC
:
DMC = 1
:
1 v/v). The current density of 1C, in our definition, was based on a capacity of 200 mA g−1 and the test voltage range was between 2.0 and 4.8 V (vs. Li/Li+). Electrochemical tests have been carried out at 30 °C. The potentiostatic intermittent titration technique (PITT) experiments have been conducted on a CHI660D electrochemical working station. In the initial charge–discharge process, after charging to 4.8 V, the as-prepared materials were subjected to successive potential steps to record chronoamperometric curves (I–t) in the initial discharge process. In each step the potential difference is ΔE = −50 mV and the time span is 3600 s.
Results and discussion
Morphology characterization
Little difference could be observed from the morphology and particle size between samples calcined at the same temperature, since temperature has been reported to be the main factor for the variation of morphology.2,20 As indicated in Fig. 1a and b, both T24 and T36 present the morphologies of microsphere aggregation. The different calcination times have an inconspicuous effect on the average particle size of primary particles, which are both about 20–30 nm in diameter (Fig. 1c and d). The microspheres have been further verified by TEM as shown in Fig. 1e and f. The hierarchical microsphere structure is beneficial for the electrolyte penetration, which can effectively shorten the Li+ diffusion distance and improve the Li+ migration rate.8 Additionally, the enhancement of the stability owing to the hierarchical structure could boost structural integrity without collapsing and reconstruction during electrochemical tests.
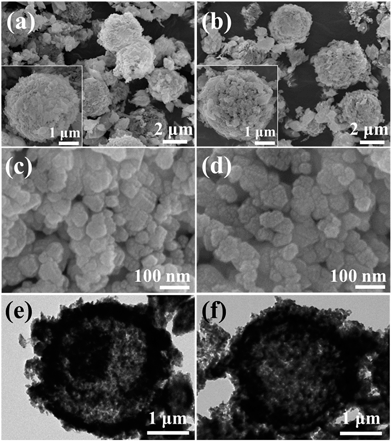 |
| Fig. 1 SEM images (a and b) and their surface magnified images (c and d) of T24 and T36 microspheres; typical TEM images of a single microsphere of T24 (e) and T36 (f). | |
To further confirm the layered/spinel heterostructure formed during the synthesis process, T24 has been characterized in the corresponding selected area electron diffraction (SAED) pattern and high-resolution TEM (HRTEM) images. Polycrystalline electron diffraction rings were carefully analysed and indexed (Fig. 2b). The two diffraction rings indexed to the (220) and (442) plane could only be indexed to the spinel structure (Fd
m).20,24,29 The lattice ring of the (020) plane corresponds to the monoclinic structure (C2/m) of Li2MnO3.8 And other diffraction rings could be ascribed to both layered (R
m) and spinel (Fd
m) structures. The SAED result indicates the formation of the layered (R
m)–layered (C2/m)–spinel (Fd
m) heterostructure.
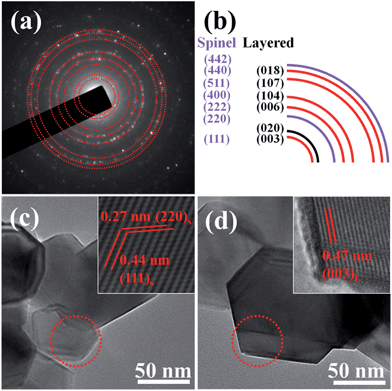 |
| Fig. 2 Polycrystalline SAED pattern (a) and index of the diffraction rings (b) corresponding to a single microsphere of T24. TEM images (c) and (d) of the frontal view of nanobricks of T24 and their FFT or HRTEM images. | |
The relevant fast Fourier transform (FFT, Fig. 2c) of the corresponding region marked by a red circle reveals two sets of clear lattice fringes with a d-spacing of 0.44 nm and 0.27 nm, corresponding to the planes (111) and (220) of the spinel phase. Besides, HRTEM images (Fig. 2d) indicate a d-spacing of about 0.47 nm that is ascribed to the plane (003) of the layered structure on another nanobrick. These results, which could be similarly found in T36, demonstrate that the particles with spinel and layered structures are scattered in microspheres,20 which could enhance the electrochemical performance of the as-prepared samples owing to the synergic effect resulting from the integral heterostructure among particles.
Structure features
The as-prepared layered/spinel heterostructured materials were also characterised by powder X-ray diffraction (XRD) and Raman spectroscopy. As shown in Fig. 3a and S2a,† all synthesized materials exhibit a typical hexagonal α-NaFeO2 layered structure except the weak diffraction peaks between 20° and 25° due to the cation ordering of monoclinic Li2MnO3.8 Moreover, the shoulder peaks (111), (220), (422) and (511) in the T24 and T36 samples marked by “*” are attributed to featured diffraction peaks of the spinel-phase structure.19,20,23,29 Comparatively, T12 exhibits another couple of peaks (400) and (440) (Fig. S1a, ESI†), which also belong to the spinel phase. Nevertheless, the overlapped (006) and (012) peaks indicate that the T12 fails to form a well-organized hexagonal layered lattice structure, which could be related with the insufficient calcination process (Fig. S1a, ESI†). The huge difference among the samples is obtained by the intensity ratio of I003/I104, which reflects the Li+/Ni2+ replacement in the hexagonal layered structure.32–34 As listed in Table 1, the I003/I104 ratio of T24 (equal to 0.95) is much smaller than that of T36 (equal to 1.53), indicating that the calcination time has a great effect on cation distribution. The Rietveld refinement results (Table 1) also reveal that the significantly high Li+/Ni2+ replacement of T24 (12.3%) is in contrast to that of T36 (3.3%), resulting in the shrinking of lattice parameters a and c of the hexagonal layered structure.32,33 However, when comparing the (003) diffraction peak site between the patterns, an obvious small negative shift of T24 could be observed as illustrated in the magnified image between 18° and 20° (inset of Fig. 3a), signifying a larger apparent cell parameters than T36.32 This phenomenon should be attributed to the higher spinel content (22%) and much larger cubic lattice parameter a (9.8467 Å) of the spinel-phase structure in T24 (Table 1). Therefore, samples T24 could offer wider 3D Li-ion diffusion channels than T36. Although the T12 sample also exhibits a large cubic lattice parameter a (9.0070 Å) in terms of its cation-mixing structure, too much Li+/Ni2+ replacement (28%) and the lowest spinel content (8%) will result in the shrinking of the integral lattice structure (Fig. S1b, ESI†).
Table 1 Results of XRD Rietveld refinement for T24 and T36
|
T24 |
T36 |
Lattice parameter (Å) |
a
hex
|
2.8490 |
2.8505 |
c
hex
|
14.2367 |
14.2464 |
a
cub
|
9.8467 |
8.0979 |
I
003/I104 |
|
0.95 |
1.53 |
Ni2+% (Ni3b2+/Nitotal2+) |
|
12.3 |
3.3 |
Spinel (wt%) |
|
22 |
12 |
R
wp (%) |
|
1.86 |
1.57 |
R
p (%) |
|
1.23 |
0.98 |
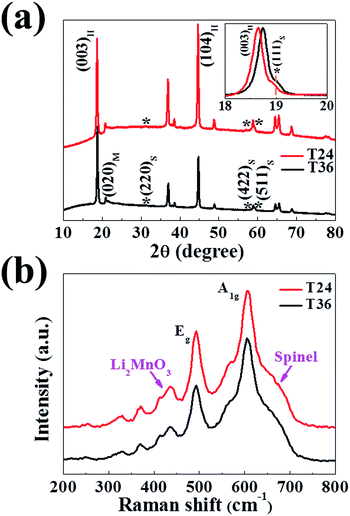 |
| Fig. 3 Powder X-ray diffraction patterns (a) and Raman spectra (b) of T24 and T36. | |
Additionally, Raman spectra were recorded to further confirm the formation of the spinel phase (Fig. 3b). It is clear that the as-prepared samples have two broad bands at 493 and 604 cm−1, which can be attributed to the Eg and A1g vibrations of the Raman-active layered structure with an R
m space group, respectively.35 A narrow and weak band is observed at about 430 cm−1, which is known to be the fingerprint vibration of Li2MnO3.36 Besides, an obvious shoulder band, appearing in the spectra of both T24 and T36, indicated by an arrow emerges around 650 cm−1 is correlated with the spinel-phase band.18,23 These results of structural features all demonstrate that the spinel structure has been formed definitely, accompanying layered components to yield the integral heterostructure.
Electrochemical tests
Fig. 4a and b display the charge–discharge curves of T24 and T36, with a particular attention to high initial coulombic efficiencies that are the highest values of unmodified Li-rich materials reported so far (Table 2).8,17,18,20,21,23,37,38 The original formation of the spinel structure, which has an empty 16c octahedral site for insertion of additional lithium ions,39 is considered as the key to the excellent initial performance. As listed in Table 2, in comparison with the initial efficiencies of 101% at 0.2C and even 92% at 2C of T24, the T36 exhibits inferior initial efficiencies of 98% at 0.2C and 86% at 2C due to the lower spinel contents (Fig. 4e). Considering the lowest spinel contents and imperfect hexagonal layered structure, it is reasonable that T12 exhibits the poorest initial coulombic efficiencies and lowest capacities at various rates (Fig. S1c and d, ESI†).
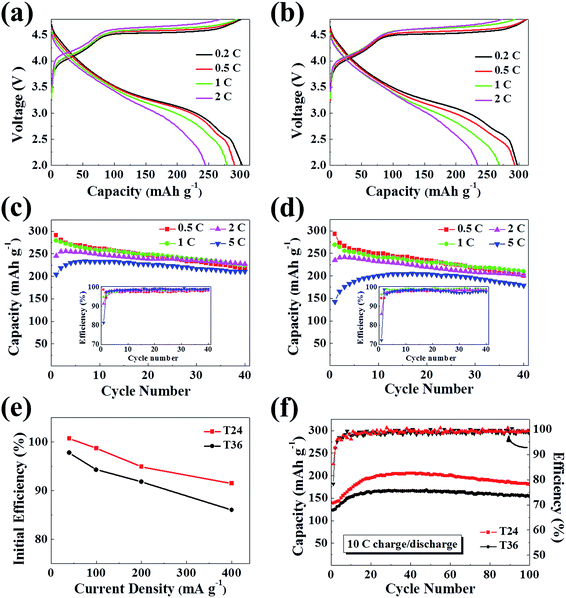 |
| Fig. 4 The initial charge–discharge curves and cycle performance at different current densities for T24 (a and c) and T36 (b and d). (e) The comparison of the initial efficiency of T24 and T36 samples at various rates; (f) the comparative cycle life test at ultra-high rates of 10C between 2.0 V and 4.8 V. | |
Table 2 The comparative data of the initial performance at different rates of T24 and T36 samples
Rates |
T24 |
T36 |
1st charge capacity (mA h g−1) |
1st discharge capacity (mA h g−1) |
Initial efficiency |
1st charge capacity (mA h g−1) |
1st discharge capacity (mA h g−1) |
Initial efficiency |
0.2C |
301 |
303 |
101% |
306 |
299 |
98% |
0.5C |
295 |
291 |
99% |
311 |
293 |
94% |
1C |
295 |
280 |
95% |
293 |
269 |
92% |
2C |
268 |
245 |
92% |
273 |
235 |
86% |
All the initial discharge curves exhibit an obvious plateau above 2.5 V for the characteristic reduction of the spinel structure.11,19,22,23,29 On the second charge, an anodic peak around 3.0 V indicated by dQ/dV plots (Fig. S2, ESI†) demonstrates that these redox peaks, including a probably overlapped reduction peak by the layered-structure of Ni4+ → Ni2+ at 4.0 V, could be attributed to the Mn4+ ↔ Mn3+ redox couple of the spinel structure.23 Besides, the absence of redox peaks above 4.55 V associated with nickel ions of the spinel phase clearly reveals the 4V Li1+xMn2O4 component of the integral heterostructure in our samples.19,23,40
Furthermore, both T24 and T36 demonstrate a very low initial capacity loss, and remarkable rate capacities as well. The T24 exhibits the maximal capacities as high as 280, 256, 234 and 206 mA h g−1 at 1C, 2C, 5C and 10C, respectively (Fig. 4a, c and f, Table 2). To the best of our knowledge, the rate performance of T24 is much higher than previously reported data.4,8,17,18,20,21,23,24,37,39 Upon cycling, especially at high rates, the discharge capacity increases to its maximum within a few initial cycles. Such a phenomenon is considered as the activation of the cell at high charge/discharge rates.2,9,41–46 After 40 charge–discharge cycles as shown in Fig. 4c, the T24 maintains capacities of 225, 228 and 211 mA h g−1 at 1C, 2C and 5C, respectively. Such excellent rate properties are attributed to its hierarchical microsphere morphology and 3D Li+ diffusion channel provided by the original spinel structure. The rapid Li-ion exchange is dramatically enhanced by the synergic effect of layered and spinel components to relieve barriers and shorten the distance of Li+ diffusion. When compared to T24, the T36 presents inferior cyclability and rate capability. Electrochemical performance of the T36 is given in Fig. 4b, d and f, the maximal capacities are 269, 241, 205 and 168 mA h g−1 at 1C, 2C, 5C and 10C, respectively. As for a long cycle life (Fig. 4f), after 100 charge–discharge cycles at 10C, the T36 delivered obviously a smaller capacity of 154 mA h g−1 in comparison with T24 for a value of 181 mA h g−1. From what we have discussed above, the superior capacity at high rates and the high cycle retention of T24 should be ascribed to its higher original spinel contents and broader 3D Li+ diffusion channel.
With the aim to further understand the difference in electrochemical performances between T24 and T36, a PITT method has been applied to evaluate the Li-ion chemical diffusion coefficient (DLi+, cm2 s−1) in the initial discharge process. The procedure has been repeated for a voltage window of operation of 4.8–2 V. A computational formula for DLi+ is obtained by a specific hypothesis, considering that the diffusion process is based on the solution of a partial differential equation of Fick's second law with mathematical manipulation:47,48
| 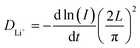 | (1) |
I (A) is the step current, L (μm) represents the diffusion distance, which is approximately the cathode thickness commonly, and t (s) refers to the step time. In order to minimize experimental error, we have picked electrode slices of T24 and T36 with the same load mass and thickness (L = 4.94 μm, Fig. S3, ESI†).
The chronoamperometry and ln(I)–t plots are displayed in Fig. S4, ESI.†DLi+ has been calculated from the slopes of d
ln(I)/dt and the plots of ln
DLi+ as a function of step potentials are shown in Fig. 5. The fluctuation of DLi+ coincides with dQ/dV curves as shown in Fig. S2.† From 4.7 V to 3.0 V, DLi+ decreases slowly owing to the gradual narrowing of the diffusion path along with the insertion of Li+ and reduction of Ni4+ → Ni2+.47 And then, after an increase from 3.0 V to 2.7 V, the value of DLi+ decreases obviously to about 2.6 V due to the process of Mn4+ → Mn3+ of the spinel phase. Comparatively, in spite of the variation of DLi+ along with the step potentials, the T24 always holds always a larger value of Li-ion chemical diffusion coefficient than that of T36. The results of PITT coincide with electrochemical tests, signifying that the higher spinel contents and broader 3D Li+ diffusion channel contribute to the easier insertion of Li-ions.
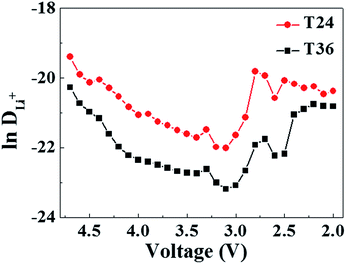 |
| Fig. 5 ln DLi+ as a function of the step potential at the first discharge process of T24 and T36. | |
Conclusions
In summary, by adopting a one-step solvothermal strategy, layered/spinel Li-rich materials have been successfully synthesized, and the experimental results suggest that the formation process of the heterostructure could be controlled along with the extension of the calcination time. Thanks to the higher spinel contents and faster Li-ion diffusion caused by wider Li+ diffusion channels, materials calcined at 650 °C for 24 hours present the optimal electrochemical performances, demonstrated by high initial efficiencies of 101% at 0.2C and even 92% at 2C, as well as high discharge capacities of 280, 256, 234 and 206 mA h g−1 at 1C, 2C, 5C and 10C, respectively. Such excellent electrochemical performances should be attributed to the hierarchical microsphere morphology and layered/spinel heterostructure. Besides, this is the first report about a one-step synthesis strategy for unmodified layered/spinel heterostructured Li-rich materials, which provides simultaneously remarkable initial coulombic efficiency and rate capability. The results reported herein offer novel insights into the design and preparation of high-performance Li-rich oxides.
Acknowledgements
This work is supported by NSFC (21321062, 21373008, 21273184).
Notes and references
- N. S. Choi, Z. Chen, S. A. Freunberger, X. Ji, Y. K. Sun, K. Amine, G. Yushin, L. F. Nazar, J. Cho and P. G. Bruce, Angew. Chem., 2012, 51, 9994–10024 CrossRef CAS PubMed.
- F. Fu, G. L. Xu, Q. Wang, Y. P. Deng, X. Li, J. T. Li, L. Huang and S. G. Sun, J. Mater. Chem. A, 2013, 1, 3860–3864 CAS.
- J. Hong, H.-D. Lim, M. Lee, S.-W. Kim, H. Kim, S.-T. Oh, G.-C. Chung and K. Kang, Chem. Mater., 2012, 24, 2692–2697 CrossRef CAS.
- G. Z. Wei, X. Lu, F. S. Ke, L. Huang, J. T. Li, Z. X. Wang, Z. Y. Zhou and S. G. Sun, Adv. Mater., 2010, 22, 4364–4367 CrossRef CAS PubMed.
- M. M. Thackeray, C. Wolverton and E. D. Isaacs, Energy Environ. Sci., 2012, 5, 7854–7863 CAS.
- M. M. Thackeray, C. S. Johnson, J. T. Vaughey, N. Li and S. A. Hackney, J. Mater. Chem., 2005, 15, 2257–2267 RSC.
- J. Gao, J. Kim and A. Manthiram, Electrochem. Commun., 2009, 11, 84–86 CrossRef CAS.
- F. Fu, Y.-P. Deng, C.-H. Shen, G.-L. Xu, X.-X. Peng, Q. Wang, Y.-F. Xu, J.-C. Fang, L. Huang and S.-G. Sun, Electrochem. Commun., 2014, 44, 54–58 CrossRef CAS.
- J. Liu, M. Hou, J. Yi, S. Guo, C. Wang and Y. Xia, Energy Environ. Sci., 2014, 7, 705–714 CAS.
- N. Yabuuchi, K. Yoshii, S. T. Myung, I. Nakai and S. Komaba, J. Am. Chem. Soc., 2011, 133, 4404–4419 CrossRef CAS PubMed.
- A. Bhaskar, S. Krueger, V. Siozios, J. Li, S. Nowak and M. Winter, Adv. Energy Mater., 2015, 5, 1401156 Search PubMed.
- D. Wang, R. Yu, X. Wang, L. Ge and X. Yang, Sci. Rep., 2015, 5, 8403 CrossRef CAS PubMed.
- J. Gao and A. Manthiram, J. Power Sources, 2009, 191, 644–647 CrossRef CAS.
- F. Wu, Z. Wang, Y. Su, N. Yan, L. Bao and S. Chen, J. Power Sources, 2014, 247, 20–25 CrossRef CAS.
- J.-S. Kim, C. S. Johnson, J. T. Vaughey and M. M. Thackeray, J. Power Sources, 2006, 153, 258–264 CrossRef CAS.
- G. Xu, J. Li, Q. Xue, X. Ren, G. Yan, X. Wang and F. Kang, J. Power Sources, 2014, 248, 894–899 CrossRef CAS.
- F. Fu, Q. Wang, Y.-P. Deng, C.-H. Shen, X.-X. Peng, L. Huang and S.-G. Sun, J. Mater. Chem. A, 2015, 3, 5197–5203 CAS.
- L. Chen, Y. Su, S. Chen, N. Li, L. Bao, W. Li, Z. Wang, M. Wang and F. Wu, Adv. Mater., 2014, 26, 6756–6760 CrossRef CAS PubMed.
- F. Wu, N. Li, Y. Su, H. Shou, L. Bao, W. Yang, L. Zhang, R. An and S. Chen, Adv. Mater., 2013, 25, 3722–3726 CrossRef CAS PubMed.
- D. Luo, G. Li, C. Fu, J. Zheng, J. Fan, Q. Li and L. Li, Adv. Energy Mater., 2014, 4, 1400062 Search PubMed.
- D. Wang, I. Belharouak, G. Zhou and K. Amine, Adv. Funct. Mater., 2013, 23, 1070–1075 CrossRef CAS.
- Y.-K. Sun, M.-J. Lee, C. S. Yoon, J. Hassoun, K. Amine and B. Scrosati, Adv. Mater., 2012, 24, 1192–1196 CrossRef CAS PubMed.
- F. Wu, N. Li, Y. Su, L. Zhang, L. Bao, J. Wang, L. Chen, Y. Zheng, L. Dai, J. Peng and S. Chen, Nano Lett., 2014, 14, 3550–3555 CrossRef CAS PubMed.
- B. Song, H. Liu, Z. Liu, P. Xiao, M. O. Lai and L. Lu, Sci. Rep., 2013, 3, 3094 Search PubMed.
- S. Wang, Y. Wu, Y. Li, J. Zheng, J. Yang and Y. Yang, Electrochim. Acta, 2014, 133, 100–106 CrossRef CAS.
- S. K. Jeong, J. S. Shin, K. S. Nahm, T. Prem Kumar and A. M. Stephan, Mater. Chem. Phys., 2008, 111, 213–217 CrossRef CAS.
- J. Zheng, M. Gu, J. Xiao, B. J. Polzin, P. Yan, X. Chen, C. Wang and J.-G. Zhang, Chem. Mater., 2014, 26, 6320–6327 CrossRef CAS.
- J. M. Zheng, Z. R. Zhang, X. B. Wu, Z. X. Dong, Z. Zhu and Y. Yang, J. Electrochem. Soc., 2008, 155, A775–A782 CrossRef CAS.
- Q. Xia, X. Zhao, M. Xu, Z. Ding, J. Liu, L. Chen, D. G. Ivey and W. Wei, J. Mater. Chem. A, 2015, 3, 3995–4003 CAS.
- X. Bian, Q. Fu, H. Qiu, F. Du, Y. Gao, L. Zhang, B. Zou, G. Chen and Y. Wei, Chem. Mater., 2015, 27, 5745–5754 CrossRef CAS.
- H. Liu, C. Du, G. Yin, B. Song, P. Zuo, X. Cheng, Y. Ma and Y. Gao, J. Mater. Chem. A, 2014, 2, 15640–15646 CAS.
- X. Huang, M. Wang and R. Che, J. Mater. Chem. A, 2014, 2, 9656–9665 CAS.
- H. Yu, Y. Qian, M. Otani, D. Tang, S. Guo, Y. Zhu and H. Zhou, Energy Environ. Sci., 2014, 7, 1068–1078 CAS.
- T. Zhang, J.-T. Li, J. Liu, Y.-P. Deng, Z.-G. Wu, Z.-W. Yin, J.-H. Wu, L. Huang and S.-G. Sun, ChemElectroChem, 2015 DOI:10.1002/celc.201500390.
- C. Venkateswara Rao, A. Leela Mohana Reddy, Y. Ishikawa and P. M. Ajayan, ACS Appl. Mater. Interfaces, 2011, 3, 2966–2972 Search PubMed.
- F. Amalraj, D. Kovacheva, M. Talianker, L. Zeiri, J. Grinblat, N. Leifer, G. Goobes, B. Markovsky and D. Aurbach, J. Electrochem. Soc., 2010, 157, A1121–A1130 CrossRef CAS.
- X. Miao, Y. Yan, C. Wang, L. Cui, J. Fang and G. Yang, J. Power Sources, 2014, 247, 219–227 CrossRef CAS.
- J. Liu, L. Chen, M. Hou, F. Wang, R. Che and Y. Xia, J. Mater. Chem., 2012, 22, 25380–25387 RSC.
- C. Liu, Z. Wang, C. Shi, E. Liu, C. He and N. Zhao, ACS Appl. Mater. Interfaces, 2014, 6, 8363–8368 CAS.
- A. Kraytsberg and Y. Ein-Eli, Adv. Energy Mater., 2012, 2, 922–939 CrossRef CAS.
- D. Ye, K. Ozawa, B. Wang, D. Hulicova-Jurcakova, J. Zou, C. Sun and L. Wang, Nano Energy, 2014, 6, 92–102 CrossRef CAS.
- S.-H. Yu, T. Yoon, J. Mun, S. Park, Y.-S. Kang, J.-H. Park, S. M. Oh and Y.-E. Sung, J. Mater. Chem. A, 2013, 1, 2833–2839 CAS.
- L. Zhang, N. Li, B. Wu, H. Xu, L. Wang, X. Q. Yang and F. Wu, Nano Lett., 2015, 15, 656–661 CrossRef CAS PubMed.
- Q. An, F. Lv, Q. Liu, C. Han, K. Zhao, J. Sheng, Q. Wei, M. Yan and L. Mai, Nano Lett., 2014, 14, 6250–6256 CrossRef CAS PubMed.
- G. He and A. Manthiram, Adv. Funct. Mater., 2014, 24, 5277–5283 CrossRef CAS.
- H. Jiang, Y. Hu, S. Guo, C. Yan, P. S. Lee and C. Li, ACS Nano, 2014, 8, 6038–6046 CrossRef CAS PubMed.
- C. H. Shen, L. Huang, Z. Lin, S. Y. Shen, Q. Wang, H. Su, F. Fu and X. M. Zheng, ACS Appl. Mater. Interfaces, 2014, 6, 13271–13279 CAS.
- D. Kovacheva, B. Markovsky, G. Salitra, Y. Talyosef, M. Gorova, E. Levi, M. Riboch, H.-J. Kim and D. Aurbach, Electrochim. Acta, 2005, 50, 5553–5560 CrossRef CAS.
Footnote |
† Electronic supplementary information (ESI) available. See DOI: 10.1039/c5ta06945a |
|
This journal is © The Royal Society of Chemistry 2016 |
Click here to see how this site uses Cookies. View our privacy policy here.