Synthesis of titanium cross-linked chitosan composite for efficient adsorption and detoxification of hexavalent chromium from water
Received
30th September 2014
, Accepted 22nd October 2014
First published on 22nd October 2014
Abstract
For the simultaneous adsorption and detoxification of hexavalent chromium from water, a new titanium–chitosan (Ti–CTS) composite was synthesized through a metal-binding reaction between titanium ions and the chitosan biopolymer followed by cross-linking with glutaraldehyde. The resultant composite was characterized by FT-IR, XRD, elemental mapping, SEM and XPS. The adsorption properties toward Cr(VI) were systematically investigated as a function of pH, dosage, initial concentration, contact time, temperature and co-existing ions. Experimental data were well described by the Langmuir isotherm and the pseudo-second order model with the maximum adsorption capacity of 171 mg g−1. More attractively, the Cr(VI) could be effectively adsorbed and reduced to the less toxic Cr(III) by the Ti–CTS composite. The experimental results, FT-IR and XPS indicated that the possible removal mechanism of Cr(VI) onto the Ti–CTS composite was summarized into three steps: (i) Cr(VI) adsorption by electrostatic attraction (Ti4+ and HCrO4−) and ligand exchange (Cl− and HCrO4−); (ii) Cr(VI) partly reduced to Cr(III); (iii) the re-adsorption of Cr(III) onto the Ti–CTS composite.
1. Introduction
Chromium is a common pollutant of the environment, which discharges from various industry processes such as leather tanning, electroplating and water cooling.1 Chromium exists as two species in natural waters: Cr(III) and Cr(VI). The former is essential for the proper functioning of living organisms and is less toxic than the latter species.2 However, Cr(VI) is a highly soluble, reactive and a mobile species in aquatic systems, thus exerting carcinogenicity and toxicity in biological systems due to its strong oxidizing properties.3 Due to its hazardous nature, Cr(VI) must be removed from wastewater prior to discharge into the environment.4 Traditionally, two types of treatment technologies are always used to remove Cr(VI) from wastewater: the first type reduces Cr(VI) to Cr(III) followed by chemical precipitation, and the second type directly removes Cr(VI).5 Currently, simultaneous adsorption and detoxification of Cr(VI) is considered as the most economical and effective method.6 Many adsorbents have been reported for the detoxification of Cr(VI) contaminated waters, such as polypyrrole/cellulose fiber composites,7,8 tannic acid immobilized powdered activated carbon with humic acid9 and based on zero-valent iron nanoparticles.2,10 However, the abovementioned adsorbents either have weak mechanical strength, low adsorption capacity or are easily susceptible to oxidation and agglomeration. These drawbacks have limited the applications for Cr(VI) removal from wastewater. It is necessary to develop new adsorbents with high adsorption capacity and stability for Cr(VI) removal, particularly for simultaneous Cr(VI) adsorption and reduction.
Chitosan (CTS) is one of the most important natural polymers composed of layers of crustaceans and cell walls of many fungi. It is a reproducible and environmentally friendly material and has been found to be capable of chemically or physically adsorbing various heavy metal ions.11 Recently, metal-based chitosan materials have been reported to be highly efficient in the removal of Cr(VI) from wastewater. For example, chitosan–Fe0 nanoparticles were prepared for the adsorption of hexavalent chromium from wastewater by some researchers.4,11–13 Zimmermann et al. reported a Fe-crosslinked chitosan complex that could effectively remove Cr(VI) from aqueous solutions.14 Furthermore, the chitosan–Fe(III) complex has also been applied to study the mechanism of detoxification of Cr(VI) by Shen.15 Moreover, titania-based adsorbents were also reported for adsorbing contaminants from wastewaters. It was reported that a titanium hydroxide-derived adsorbent16 and crystalline titanium dioxide17 were prepared for the adsorption of fluoride ions from aqueous solutions. TiO2-impregnated chitosan beads as a novel bio-based adsorbent have been prepared for arsenic removal by Miller.18 Moreover, the metal-binding ability of chitosan was also used to incorporate titanium metal for application as an adsorbent for fluoride adsorption.19 To the best of our knowledge, however, no reports have been published about titanium(VI) binding with chitosan for Cr(VI) adsorption and reduction.
The aim of this study was to synthesize a titanium–chitosan composite for the adsorption and reduction of Cr(VI) from water. The main objectives were as follows: (1) to synthesize and characterize the titanium–chitosan composite, (2) to evaluate the influence of different factors on the Cr(VI) adsorption by Ti–CTS composite, (3) to study the adsorption isotherms and kinetics of these reactions, (4) to test the role of chitosan in Cr(VI) reduction by the Ti–CTS composite, as well as chromium species in final products, and (5) to explore the reaction mechanism of this composite for Cr(VI) removal.
2. Materials and methods
2.1. Materials
Chitosan (food grade, 91% deacetylation degree, with an average molecular weight of 4.0 × 105 g mol−1) was supplied by Shanghai Weikang Biological Co. (China). Tetrabutyl titanate (analytical grade), acetate acid, and sodium hydroxide were purchased from Sinopharm Chemical Reagent Co., Ltd. (China). Glutaraldehyde was purchased from Merck (China). The standard solution (Cr(VI), 1000 mg L−1) was freshly prepared by dissolving the appropriate amount of potassium dichromate (K2Cr2O7) in distilled water. All other chemicals used were of analytical reagent grade, and all solutions were prepared with distilled water without further purification.
2.2. Preparation of the Ti–CTS composite
The Ti–CTS composite was synthesized according to the method previously reported, with some modifications.19,20 In detail, 3.22 g chitosan powder was added into 100 mL 2% (v/v) acetic acid aqueous solution and mixed until chitosan dissolved completely. Titanium solution was prepared by adding 5 mL concentrated HCl to 3.42 g of tetrabutyl titanate. This titanium solution was slowly added into the chitosan solution under stirring at 150 rpm for 2 h. Subsequently, the Ti–CTS composite was precipitated by the dropwise addition of 2.0 M sodium hydroxide solution with continuous stirring to obtain the composite. Then, 5 mL of 5% glutaraldehyde aqueous solution was added and stirred vigorously for cross-linked reaction for another 2 h more. After this reaction, the composite was separated from solution and washed with distilled water to obtain a neutral pH followed by drying at 40 °C for 2 days. The dried composite was used for chromium adsorption studies.
2.3. Characterization and measurement
The FTIR spectra of CTS, Ti–CTS and Ti–CTS loaded with Cr(VI) were recorded using a Nicolet 6700 FTIR spectrometer (Thermo Electron Corporation) in the range 4000–400 cm−1 with a resolution of 4 cm−1 in transmittance mode. X-ray diffraction (XRD) patterns of the Ti–CTS composite before and after adsorption of Cr(VI) were performed by a rotating anode X-ray powder diffractometer (D/MAX 2550 VB/PC, Rigaku corporation) with Cu Kα characteristic radiation. All samples were scanned from 5° to 80° (2θ) at a scanning rate of 3° (2θ) per minute. Elemental mapping images of the Ti–CTS composite before and after Cr(VI) adsorption were obtained by Transmission Electron Microscopy-Energy Dispersive X-ray Spectroscopy (TEM-EDXS, Genesis XM2 system, USA EDAX corporation). Scanning electronic microscopy (SEM) images were obtained using JSM-6360LV scanning electron microscope XPS spectra were obtained using a Thermo Scientific ESCALAB 250Xi X-ray photoelectron spectrometer (XPS) system (Al Kα X-ray source was used). The XPS spectra were fitted assuming a Gaussian–Lorentzian distribution for each peak in order to determine the binding energy of the element core levels, and all binding energies were referenced to the neutral carbon peak at 285.0 eV, and all of the XPS spectra were normalized.
The total concentration of Cr in solution was determined by an inductively coupled plasma optical emission spectrometer (ICP-OES 710 series, Agilent, USA). The residual Cr(VI) in solution was measured by the diphenylcarbohydrazide method. The absorbance of the purple Cr(VI)-diphenylcarbohydrazide product was observed after 10 min and measured by using a 722N UV-Vis spectrophotometer at a wavelength of 540 nm (Shanghai Precision & Scientific Instrument Co., Ltd.). The concentration of Cr(III) was calculated based on the difference between the total Cr and Cr(VI) concentrations.
2.4. Adsorption of chromium on the Ti–CTS composite
Batch adsorption experiments were carried out to evaluate the adsorption capacities of the Ti–CTS composite. A series of 250 mL reagent bottles containing 100 mL Cr(VI) solutions and 20 mg of Ti–CTS composite were shaken at 150 rpm for a certain time. The sample pH was adjusted to the desired value with 0.1 M HCl or 0.1 M NaOH. The concentration of chromium in the initial or equilibrium solutions was determined by ICP-OES or UV. The adsorption capacities were defined by the following equation: |  | (1) |
where qe is the amount of adsorbent in solid phase (mg g−1); Co and Ce are the initial and equilibrium concentrations of chromium in the liquid phase (mg L−1), respectively; V is the volume of the solution (L) and W is the mass of Ti–CTS composite (g).
3. Results and discussion
3.1. Characterization of the Ti–CTS composite
Fig. 1A shows the FT-IR spectra of CTS, Ti–CTS composite and Cr(VI) loaded Ti–CTS composite (Ti–CTS–Cr). The main characteristic peaks of CTS (a) are at 3443 cm−1 (–OH and –NH2 stretching vibrations), 2922 cm−1 (–CH stretching vibration), 1657 cm−1 (–NH2 bending vibration), 1382 cm−1 (–CH symmetric bending vibration), 1081 cm−1 (C–O stretching at C3) and 1034 cm−1 (C–O stretching at C6).21 For the FT-IR spectrum of Ti–CTS (b), the –NH2 bending at 1636 cm−1 underwent a shift of 21 cm−1 when compared with CTS, which confirmed that Ti4+ ions have interacted with the –NH2 group present in CTS. Moreover, the two bands at 1081 cm−1 and 1034 cm−1, corresponding to the C–OH stretching at C3 and C6, were merged into one band and moved to 1086 cm−1 (with a shift 5 cm−1). This might be due to the interaction of the –OH group in CTS with Ti4+.22 Furthermore, the band at around 3420 cm−1, attributed to –NH2 and –OH stretching vibrations in Ti–CTS, has shifted 23 cm−1 in Ti–CTS, which indicated Ti4+ ions bended onto amino and hydroxyl groups of CTS. In addition, the broad bands at 900–400 cm−1 were revealed for the Ti–O vibration and Ti Lewis sites, interacting with NH2 groups from the chitosan chain.23,24 After the adsorption of Cr(VI), the FT-IR spectrum of Ti–CTS–Cr (c) presented two new peaks at 901 cm−1 and 804 cm−1, which were due to the Cr–O stretching and asymmetric vibration, respectively.10,25 More importantly, a strong peak appeared at 1632 cm−1, which was attributed to the stretch vibration of C
O, and the decrease in C–O stretch band at 1034 cm−1 indicated that a carboxylated group had formed at the C6 position of CTS.26 Moreover, the band gaps (Eg) were also calculated via FT-IR spectra according to the Tauc–Davis–Mott Model.27 The values of Eg for Ti–CTS and Ti–CTS–Cr composites were 0.586 eV and 0.577 eV (n = 2), respectively. The Eg had a slight decrease after the adsorption of Cr(VI), which suggested that the presence of Cr(VI) would modify the electronic states and optical transitions of the composite and resulted in allowed transitions.
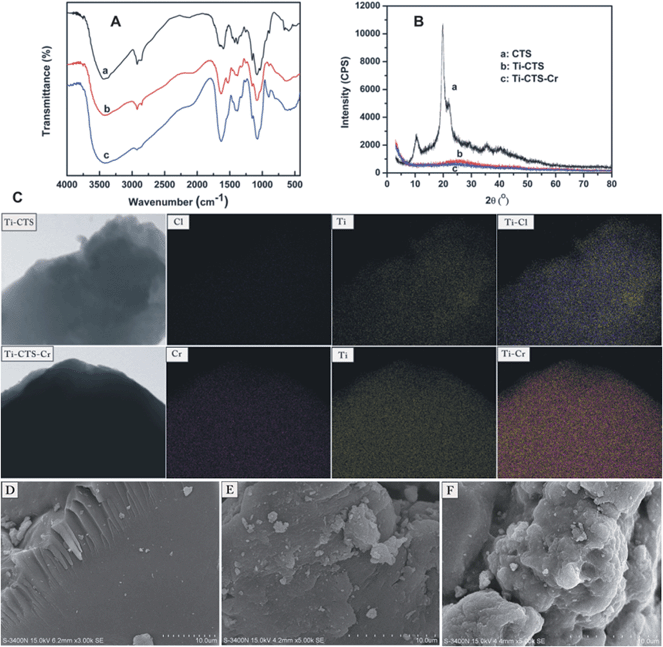 |
| Fig. 1 FT-IR (A) and XRD (B) spectra of the CTS (a), Ti–CTS (b), Ti–CTS–Cr (c); elemental mapping images (EMI, C) of Ti–CTS and Ti–CTS–Cr; SEM images of CTS (D), Ti–CTS (E) and Ti–CTS–Cr (F). | |
The XRD patterns of CTS, Ti–CTS and Ti–CTS–Cr composite in the range of 2θ = 3–80° are shown in Fig. 1B. CTS (a) showed characteristic peaks at 2θ = 10.5°, 19.7°, 35.5° and 40.3°, which were attributed to (001), (100), (101) and (002) planes, respectively.28 The XRD spectrum of the Ti–CTS composite is depicted in Fig. 1B-b. Only one extraordinary broad peak was observed and the position at 2θ = 19.7° was shifted to 25.6°. This was due to the conjugation of Ti4+ and chitosan, which decreased the crystalline nature to some extent. Therefore, the results confirmed the incorporation of Ti4+ ions into CTS. Fig. 1B-c demonstrates the XRD spectrum of the Ti–CTS–Cr composite, which shows the peak transferred to 26.2° after the adsorption of Cr(VI).
Elemental mapping image (EMI) was carried out to confirm the presence and distribution of elements in the composite. The EMI spectra of the Ti–CTS composite before and after Cr(VI) adsorption are shown in Fig. 1C. In order to improve the element resolution, C, O and N elements were omitted in the images. From the EMI images, the presence of Cl and Ti were clearly observed in the Ti–CTS composite and the elemental distribution was uniform. This clearly confirmed the incorporation of Ti4+ ions into chitosan matrix. After adsorption, Cr was presented in the EMI images, indicating that Cr(VI) adsorption occurred onto the composite. Moreover, Cr and Ti elements on the Ti–CTS–Cr composite were well-distributed, which further confirmed that the Cr(VI) ions were successfully adsorbed through the active sites on the surface of the Ti–CTS composite. Moreover, Cl disappeared after the adsorption of Cr(VI), suggesting that a ligand exchange reaction occurred between the coordinated chlorate and Cr(VI) ions. SEM images of CTS, Ti–CTS and Ti–CTS–Cr are shown in Fig. 1D, E and F. The surface of CTS (D) and the Ti–CTS composite (E) was non-porous and flat. However, a rough surface was formed for the Ti–CTS–Cr (F). This was due to the accumulation of Cr(VI) through the adsorption mechanism.
The XPS wide scan spectra of the Ti–CTS composite before and after Cr(VI) adsorption were also analyzed and are shown in Fig. 2A and B. In the figures, major peaks, such as C 1s, O 1s, N 1s, Ti 2p and Cl 2p3, were present. A new peak assigned to Cr 2p was clearly observed and the peak of Cl 2p3 simultaneously disappeared after Cr(VI) adsorption, which also confirmed the adsorption of Cr onto the Ti–CTS composite through ligand exchange. These results were consistent with the EMI analysis.
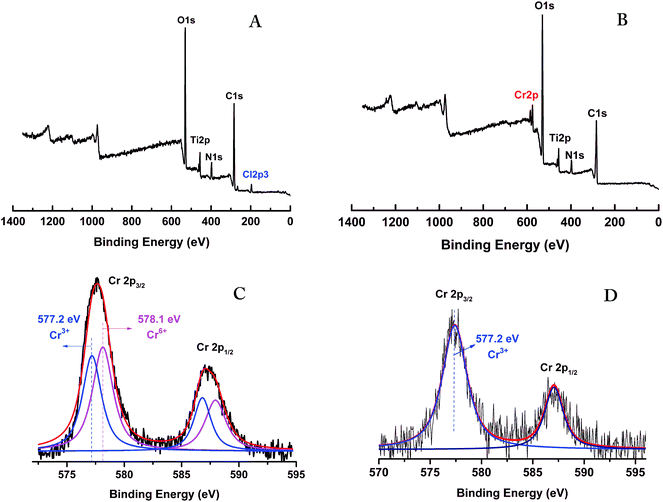 |
| Fig. 2 The wide scan XPS spectra of the Ti–CTS composite without (A) and with (B) Cr(VI) adsorbed; high resolution Cr 2p spectra of the Ti–CTS–Cr composite before (C) and after (D) desorption with NaOH. | |
3.2. Effect of pH
The removal of Cr(VI) from aqueous solutions was highly dependent on the pH of the solution because the pH affected not only the surface charges of the adsorbent but also the Cr species during the reaction. In this experiment, the initial pH of the solutions (30 mg L−1 Cr(VI)) was adjusted in the range of 2–9 using HCl or NaOH and its effects on Cr(VI) removal were explored. The results are shown in Fig. 3a. From Fig. 3a, the removal efficiency of Cr(VI) by the Ti–CTS composite was notably higher in an acidic medium rather than in an alkaline medium. The residual Cr concentration increased as the pH increased from 5.0 to 9.0. However, Cr(III) species accounted for a certain proportion of the total residual Cr concentration at 2 < pH < 4.0, which was due to the fact that protons participated in the reduction reaction in low pH solutions, as shown in eqn (2).29 Therefore, the optimal pH value for Cr(VI) removal was 5.0, corresponding to a Cr(VI) adsorption capacity of 123 mg g−1. | HCrO4− + 7H+ + 3e ⇄ Cr3+ + 4H2O E0 = +1.35 V | (2) |
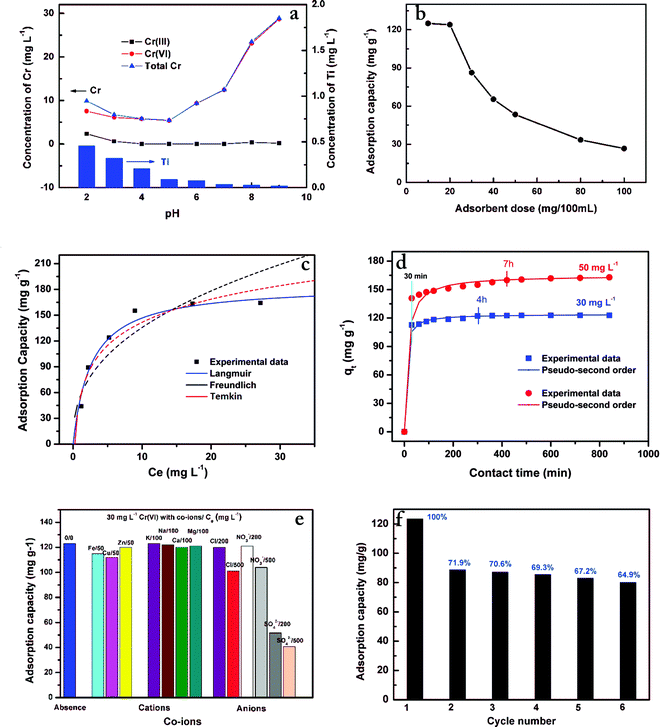 |
| Fig. 3 The effect of solution pH and concentration of Ti4+ leaching into solution (a); dosage of adsorbent (b); initial Cr(VI) concentration and isotherms (c); contact time and kinetics (d); co-existing cations and anions (e) and regeneration of the Ti–CTS composite (f). | |
At the optimum pH 5, the chromium species in solution were mainly HCrO4− (around 97%).14 The Ti4+ of the Ti–CTS composite could be also protonated and could increase the positive charge on the surface, which resulted in a stronger electrostatic attraction for chromium anions (HCrO4−). Therefore, chromium adsorption at pH 5.0 onto the Ti–CTS composite occurred via electrostatic attraction between Ti4+ and HCrO4− ions. Combined with the results of XPS spectra, Ti–CTS composite for the adsorption of the Cr(VI) could be considered as ligand-exchange reaction between the coordinated Cl− and HCrO4− and electrostatic attraction by Ti4+ as adsorption sites for HCrO4− ions. Above pH 5, the residual Cr(VI) concentration was increased as the pH increased. The reasons were given as follows: (1) the pHzpc of the Ti–CTS composite was 8.1, measured by a pH drafted method30 and the net surface charge became less positive with increase in the pH, which resulted in repulsive forces between the Ti–CTS composite and Cr(VI); (2) the higher concentration of OH− ions present in the high pH solution, competed with HCrO4− ions for the adsorption sites; (3) the chromium species were CrO42− and Cr2O72− in alkaline medium, which further decreased the Ti–CTS composite capacity for Cr(VI) adsorption. Furthermore, it is very interesting to note that at pH > 4, the Cr(III) concentration in the reaction solution was only negligible, indicating that once Cr(VI) was converted to Cr(III), Cr(III) was effectively adsorbed onto the composite. Thus, the subsequent experiments were conducted at the optimum condition of pH 5 and chromium species were only addressed as Cr(VI) in solutions.
In addition, in order to check the stability and chemical resistance in acidic media of Ti–CTS composite, Ti4+ ions released in Cr(VI) adsorption solution were analyzed by ICP-OES at pH 2–8 (Fig. 3a-Ti). The results showed that the concentration of Ti4+ ions leaching in solution was found to be 0.10–0.46 mg L−1 when the pH was from 2.0 to 4.0, but very low concentrations were found above pH 5, which confirmed that the Ti–CTS composite became more resistant to lower pH compared to its parent chitosan, which dissolved completely at pH 5.31
3.3. Effect of adsorbent dose
The adsorbent dose of the Ti–CTS composite was varied (10–100 mg/100 mL) while keeping a fixed concentration of Cr(VI) in solution. Fig. 3b illustrates the effect of adsorbent dose on the adsorption of Cr(VI). Higher adsorption capacities were observed for 10 mg and 20 mg of composite, which gradually decreased with increasing the weight of the Ti–CTS composite. The high adsorption observed for 10 mg and 20 mg of composite was attributed to easy accessibility of free active sites on the surface of the adsorbent. On increasing the weight of the Ti–CTS composite, the number of active sites increased but ratios of Cr(VI) to active sites decreased resulting in a gradual decrease of adsorption. Considering the ratios of Cr(VI) and the adsorption capacity, the optimum dose for Cr(VI) was chosen 20 mg/100 mL in the following adsorption study.
3.4. Effect of the initial concentration of Cr(VI) and adsorption isotherms
The effect of the initial Cr(VI) concentration on the adsorption capacity was tested in the range of 10–60 mg L−1 with a fixed contact time (10 h) and pH 5.0. The results in Fig. 3c show that the uptake of Cr(VI) on the Ti–CTS composite gradually increased as the initial concentration increased until the saturation point was attained at 50 mg L−1, thereafter a plateau was reached. This was due to the fact that available sites for adsorption remained constant for a fixed amount of Ti–CTS composite.
For the interpretation of the adsorption data, the equilibrium adsorption of this process was described by applying the Langmuir, Freundlich and Temkin isotherm models.
The linear forms of Langmuir, Freundlich and Temkin equations can be represented as follows:
| 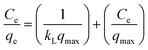 | (3) |
| 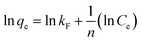 | (4) |
| 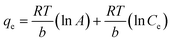 | (5) |
where
Ce is the equilibrium concentration of adsorbate in solution (mg L
−1);
qe and
qmax (mg g
−1) are the amounts adsorbed at equilibrium and the maximum adsorption capacity for monolayer formation on adsorbent, respectively.
kL (L mg
−1) is the Langmuir constant related to the maximum adsorption capacity and the energy of adsorption.
kF is the Freundlich constant and
n is the heterogeneity factor. The constant
B (RT/b) is related to the heat of adsorption.
The value of theoretical parameters and constants could be calculated from the intercept and slope of the linear equation, respectively. The results are summarized in Table 1. For the three studied isotherm models (Fig. 3c), the Langmuir isotherm (R2 = 0.993) correlated better than Freundlich and Temkin with the equilibrium data for the adsorption of Cr(VI) onto the Ti–CTS composite, suggesting a monolayer adsorption. The maximum adsorption value (171 mg g−1) was in good accordance with the experimentally obtained value (167 mg g−1). The proposed Ti–CTS composite was compared with other adsorbents recently reported in previous studies (listed in Table 2). It could be seen that the maximum adsorption capacity of Ti–CTS was higher than that of other reported adsorbents.28,32–39 Moreover, the value of n in the Freundlich isotherm was in the range of 1–10, representing a good adsorption.40 In this work, the exponent of n was 2.54 (1 < n < 10), indicating that the adsorption system was favorable.
Table 1 Langmuir, Freundlich and Temkin isotherm parameters and pseudo-second order kinetic parameters for Cr(VI) adsorption onto Ti–CTS composite
Adsorption isotherm parameters |
Kinetic pseudo-second-order |
Langmuir |
K
L (L mg−1) |
0.415 |
|
|
|
q
m (mg g−1) |
171 |
|
Initial Cr(VI) concentration |
R
2
|
0.993 |
Parameters |
30 mg L−1 |
50 mg L−1 |
Freundlich |
ln Kf |
4.0 |
q
exp (mg g−1) |
123 |
167 |
n
|
2.54 |
|
|
|
R
2
|
0.798 |
K
2 (g (mg min)−1) |
1.53 × 10−3 |
4.86 × 10−4 |
Temkin |
ln A |
1.35 |
q
e
2 (mg g−1) |
124 |
165 |
B
|
38.8 |
R
2
|
0.9997 |
0.9991 |
R
2
|
0.904 |
h (mg g−1 min−1) |
23.4 |
13.2 |
Table 2 Adsorption comparison of the Ti–CTS composite and recently reported studies on adsorbents for Cr(VI)
Adsorbents |
q
max (mg g−1) |
C
o (mg L−1) |
Time (min) |
pH/Temperature |
Reference |
Titanium cross-linked chitosan composite |
171 |
10–50 |
420 |
5/25 °C |
Present work |
Modified magnetic chitosan chelating resin |
58.5 |
10–300 |
120 |
2/28 °C |
28
|
Cross-linked chitosan resin |
86.8 |
20–160 |
120 |
3/25 °C |
32
|
Magnetic cyclodextrin – chitosan/graphene oxide (CCGO) |
67.66 |
5.0–50 |
300 |
3/30 °C |
33
|
Chitosan |
35.6 |
0.25–50 |
120 |
4/20 °C |
34
|
Ethylenediamine cross-linked magnetic chitosan resin |
51.8 |
20–200 |
10 |
2/30 °C |
35
|
Chitosan modified Fe0 nanowires in porous anodic alumina |
113.2 |
10–60 |
400 |
5/30 °C |
36
|
Poly (ethylene imine) grafted chitosan |
88.4 |
0–50 |
105 |
4/25 °C |
37
|
n-butylacrylate grafted chitosan |
17.15 |
0–300 |
60 |
3.5/30 °C |
38
|
Mesorhizobium amorphae strain CCNWGSo123 |
47.67 |
10–400 |
1000 |
2/30 °C |
39
|
3.5. Effect of contact time and adsorption kinetics
Batch experiments about the adsorption kinetics for the removal of Cr(VI) on the Ti–CTS composite were executed using the initial concentration of 30 and 50 mg L−1 at pH 5. As shown in Fig. 3d, the adsorption capacity of Cr(VI) onto the Ti–CTS composite increased with an increase in contact time. More than 80% of the Cr(VI) was absorbed by the Ti–CTS composite within the first 30 min. The rapid adsorption in the beginning could be attributed to the greater concentration gradient and more available sites for adsorption. Moreover, the initial Cr(VI) concentration had an evident effect on the adsorption process to reach the equilibrium. The time needed to reach the equilibrium for the initial Cr(VI) concentration of 30 mg L−1 was 4 h, whereas it took about 7 h for the initial Cr(VI) concentration of 50 mg L−1.
In order to investigate the rate-controlling mechanism of the adsorption process, the kinetic data were correlated to linear forms of the pseudo-first order rate model and the pseudo-second order rate model.
|  | (6) |
|  | (7) |
where
qt and
qe are the amounts of metal ions adsorbed at time
t (min) and equilibrium, respectively.
k1 (min
−1) and
k2 (g (mg min)
−1) are the pseudo-first-order and pseudo-second-order rate constants of adsorption, respectively. The values of the rate constants were also calculated from the intercept and slope of the curves. The initial adsorption rate (
h, mg g
−1 min
−1) could be calculated from
h =
k2qe2. After simulating the kinetic data, unfortunately, the pseudo-first order kinetic model was insufficient to describe the adsorption process of Cr(
VI) with low correlation coefficients (
R2 < 0.9, the results are not given here). However, the pseudo-second order rate model showed good linearity for the two different initial Cr(
VI) concentrations and the calculated correlation coefficients (
R2) were all higher than 0.999 (
Table 1). The theoretical
qe values were very close to the experimental values and the adsorption rate
h was found to decrease with an increase in the initial Cr(
VI) concentration, suggesting a more rapid adsorption of Cr(
VI) onto the Ti–CTS composite at a lower initial concentration. These results indicated that the adsorption of Cr(
VI) onto the Ti–CTS composite followed the pseudo-second order rate model, the overall process appeared to be controlled by chemisorption and there was no involvement of a mass transfer in solution.
41
3.6. Thermodynamic study
To study the thermodynamics of the adsorption of Cr(VI) onto the Ti–CTS composite, the thermodynamic parameters, free energy change (ΔG0), enthalpy change (ΔH0) and entropy change (ΔS0) were estimated by using the following equations: | 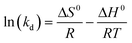 | (8) |
where kd is the adsorption distribution coefficient at different temperatures and the value was calculated by the ratio of qe to Ce (kd = qeCe−1). R is the universal gas constant (8.314 J (mol K)−1). ΔH0 and ΔS0 were calculated from the slope and intercept of the linear plot of ln(kd) vs. 1/T, respectively. The ΔG0 values were obtained from eqn (9) at different temperatures. The values of the thermodynamic parameters are listed in Table 3. The negative values of ΔG0 at all temperatures demonstrated that Cr(VI) adsorption onto the Ti–CTS composite was spontaneous and feasible. In addition, it was found that the absolute values of ΔG0 increased with adsorption temperature, suggesting that a high temperature was in favor of the increase of adsorption impetus and promoted Cr(VI) adsorption. Moreover, the positive value of ΔH0 indicated that the adsorption process was endothermic in nature, and the observed positive value of ΔS0 showed the increased randomness state at the solid–solution interface during the fixation of the adsorbate on the active sites of the adsorbent.
Table 3 Thermodynamic parameters for the adsorption of Cr(VI) by the Ti–CTS composite at different temperatures
T (K) |
ln kd |
ΔG0 (kJ mol−1) |
ΔH0 (kJ mol−1) |
ΔS0 (kJ mol−1 K−1) |
R
2
|
277.15 |
3.016 |
−6.87 |
3.38 |
0.037 |
0.987 |
293.15 |
3.083 |
−7.47 |
303.15 |
3.156 |
−7.84 |
308.15 |
3.161 |
−8.02 |
3.7. Interference of co-ions
By maintaining a 20 mg dosage of the Ti–CTS composite and 30 mg L−1 (100 mL) as initial Cr(VI) concentration at pH 5, the adsorption capacity was evaluated by different concentrations of co-existing cations (Fe3+, Cu2+, Zn2+, K+, Na+, Ca2+, Mg2+) and anions (Cl−, NO3− and SO42−). The results are depicted in Fig. 3e. From the figure, on one hand, the presence of 50 mg L−1 of Fe3+, Cu2+, Zn2+ and 100 mg L−1 of K+, Na+, Ca2+, Mg2+ showed no significant interferences with the adsorption of Cr(VI). On the other hand, the uptake of Cr(VI) was decreased with an increase in the concentration of co-anions. At 200 mg L−1 concentration of Cl− and NO3−, there was a slight effect on the adsorption capacity, whereas it decreased by 18% and 15%, respectively, as the concentration increased to 500 mg L−1. In addition, SO42− had a more significant effect on the adsorption capacities, the adsorption capacities being reduced to 43% and 33% when the concentrations were 200 and 500 mg L−1, respectively. This indicated a certain competition between Cl−, NO3− and SO42− with Cr(VI) anions for the interaction with active sites on the surface of the Ti–CTS composite.
3.8. Chromium species on the composite after adsorption
The high resolution XPS patterns of the Ti–CTS composite with and without Cr(VI) adsorption were conducted and shown in Fig. 2C and D. Interestingly, the Cr(VI) adsorbed onto the Ti–CTS composite was partially reduced to the relatively nontoxic Cr(III) based on the surface chemical compositions of the Ti–CTS composite during the removal process. From Fig. 2C, Cr 2p1/2 and Cr 2p3/2 line peaks were located around 587.2 eV and 577.7 eV. The broad peak of Cr 2p3/2 was deconvoluted into two peaks at binding energies of 577.2 eV and 578.1 eV, which were the characteristic peaks of Cr(III) and Cr(VI), respectively.1 These results suggested that both Cr(VI) and Cr(III) coexisted on the surface of the Cr(VI) adsorbed Ti–CTS composite. To further verify the existence of Cr(III) on the composite, the high resolution XPS spectrum of the Cr 2p region after the desorption process was also measured (shown in Fig. 2D). From the Fig. 2D, only one peak was observed with a binding energy of 577.2 eV at Cr 2p3/2, which belonged to the Cr(III), indicating that part of the Cr(VI) ions adsorbed onto the Ti–CTS composite has been reduced to Cr(III).
In order to qualify the Cr(III) and Cr(VI) on the Ti–CTS-Cr composite, further experiments were conducted. After adsorption, the composite was treated using two methods: (a) desorption and digestion: to remove chromium, 100 mL of 0.5 mol L−1 NaOH was used for 12 h under stirring at 150 rpm, and then the composite was re-collected and digested with mixed acids (HF/HCl/HClO4 = 1.0 mL/1.0 mL/0.5 mL); (b) direct digestion: the Ti–CTS–Cr composite was digested with the same abovementioned mixed acids. After treatment, the obtained solutions were analyzed for Cr(VI) and Cr(III) concentrations and the percentages of Cr(VI) and Cr(III) were calculated. The results are listed in Table 4. From Table 4, the percentage of Cr(VI) in the NaOH solution accounted for 99.3%, whereas the Cr(III) was 0.7%, suggesting that this part of chromium was only adsorbed onto the Ti–CTS. On the other hand, the content of Cr(III) was 98.7% in mixed acid digestion solution, which belonged to the reduction of chromium by the Ti–CTS composite. The same contents of Cr(VI) and Cr(III) were also obtained with the direct digestion method. Overall, 39.9% of Cr on the composite was reduced to Cr(III) and the percentage of 60.1% might only be adsorbed on the surface of the Ti–CTS composite through the electrostatic attraction between Ti4+ and HCrO4−.
Table 4 The amount of Cr(III), Cr(VI) and total Cr in Cr(VI)-loaded Ti–CTS composite (N = 3; desorption solution: 0.5 M NaOH; digestion acids: HF/HCl/HClO4 = 1.0 mL/1.0 mL/0.5 mL)
|
Desorption and digestion |
Direct digestion solution |
NaOH solution |
Mixed acid solution |
Cr(III) |
0.7% |
98.7% |
39.9% |
Cr(VI) |
99.3% |
1.3% |
60.1% |
3.9. Regeneration of the Ti–CTS composite
In order to investigate the reusability of the Ti–CTS composite, cyclic adsorption–regeneration tests were carried out for Cr(VI) adsorption. As shown in Fig. 3a, the adsorbed capacity was less (10 mg g−1) at high pH, indicating that the adsorbed Cr(VI) could be desorbed using alkaline solution. In this study, five concentrations of NaOH solutions, including 0.005, 0.01, 0.05, 0.10 and 0.20 mol L−1, were used to study the regeneration of the Ti–CTS composite. It was found that the desorption ratio increased until 0.05 mol L−1 NaOH was used and thereafter it maintained a constant value. Therefore, 0.05 mol L−1 NaOH solution was selected for Ti–CTS composite regeneration. Fig. 3f shows the adsorption abilities of the Ti–CTS composite for Cr(VI) during six adsorption–regeneration cycles. After the first cycle, the adsorption capacity had an evident decrease compared with the original composite. This was because some active sites were occupied by the Cr(III)-complex. Then, in the next five cycles, the adsorption capacities for Cr(VI) only had slight decreases and after six cycles the adsorption capacity still was 64.9%. This result suggested that the synthesized Ti–CTS composite could be used repeatedly for the treatment of Cr(VI) in wastewater.
3.10. Mechanism of Cr(VI) removal
From the results of the pH study, the functional groups on the surface of the Ti–CTS composite could be protonated and positively charged to form Ti4+ in an acidic medium. The protonated surface had a stronger electrostatic attraction for chromium anions (HCrO4−). On the other hand, the ligand of Cl on the surface Ti–CTS composite was also exchanged with HCrO4− and formed the Ti–HCrO4 complex, which was confirmed by the disappearance of Cl in XPS and EMI analyses. Thus, chemical adsorption occurred because of electrostatic attraction and ligand exchange between the hexavalent chromium anions and the surface active sites, which resulted in complex formation. After adsorption, the ligand exchange of Cr(VI) on the surface of the Ti–CTS composite was directly reduced to Cr(III) by the adjacent electron-donor of C-6 alcoholic groups, which were oxidized to carbonyl groups after the reaction. Then, these carbonyl groups, as dominant functional groups, would immediately re-adsorb the reduced Cr(III) by ion exchange. The following mechanism has been proposed for the Cr(III) adsorption on the surface of the Ti–CTS composite:42 | Cr3+ + H2O ⇄ [Cr(OH)]2+ + H+(pK1 = 3.85) | (10) |
| Ti–CTS–COOH + [Cr(OH)]2+ ⇄ (Ti–CTS–COO−-[Cr(OH)]2+) + H+ | (11) |
Therefore, the proposed possible adsorption coupled reduction mechanism for Cr(VI) removal by the Ti–CTS composite was presented in Scheme 1. The anionic Cr(VI) (HCrO4−) ions were firstly adsorbed onto the Ti–CTS composite by chelation of the Ti4+ center in the Ti–CTS complex and by the electrostatic attraction of protonated sites. Subsequently, the adsorbed Cr(VI) atoms were partially reduced by the adjacent primary alcoholic functions on C-6, which simultaneously oxidized to carbonyl groups. After that, the coordination bond between the reduced Cr(III) and the Ti4+ center in the Ti–CTS composite could be broken, and the free Cr(III) were re-absorbed by Cr-bonding onto the Ti–CTS complex. Finally, the Cr(VI) adsorbed onto the composite were desorbed by NaOH into solution. Thus, the Ti–CTS composite could adsorb the Cr(VI) and reduced it to the less toxic Cr(III) through a rapid and efficient process.
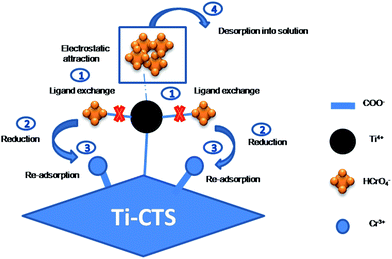 |
| Scheme 1 The proposed adsorption coupled reduction mechanism of Cr(VI) removal by the Ti–CTS composite. | |
4. Conclusion
The present study showed that the Ti–CTS composite was quite effective for the adsorption and detoxification of Cr(VI) from water. The process conditions were optimized by the adsorption capacity and leakage concentration of Ti4+. The adsorption data were well described by the Langmuir isotherm and kinetics following the pseudo-second order model, with the maximum adsorption capacity of 171 mg g−1 for Cr(VI). The possible removal mechanism for Cr(VI) detoxification was confirmed by the research findings, which consisted of adsorption, reduction and re-adsorption. It is expected that the Ti–CTS composite can be as a promising adsorbent for the treatment of Cr(VI)-contaminated water.
Acknowledgements
We are grateful for the financial support by the National Natural Science Foundation of China (Grant: 21407050).
References
- H. L. Ma, Y. Zhang, Q. H. Hu, D. Yan, Z. Z. Yu and M. Zhai, J. Mater. Chem., 2012, 22, 5914–5916 RSC.
- L. Alidokht, A. Khataee, A. Reyhanitabar and S. Oustan, Desalination, 2011, 270, 105–110 CrossRef CAS PubMed.
- X. Lv, J. Xu, G. Jiang, J. Tang and X. Xu, J. Colloid Interface Sci., 2012, 369, 460–469 CrossRef CAS PubMed.
- T. Liu, Z. L. Wang, L. Zhao and X. Yang, Chem. Eng. J., 2012, 189, 196–202 CrossRef PubMed.
- G. Arslan, S. Edebali and E. Pehlivan, Desalination, 2010, 255, 117–123 CrossRef CAS PubMed.
- B. Liu and Y. Huang, J. Mater. Chem., 2011, 21, 17413–17418 RSC.
- X. Liu, W. Zhou, X. Qian, J. Shen and X. An, Carbohydr. Polym., 2013, 92, 659–661 CrossRef CAS PubMed.
- X. Liu, X. Qian, J. Shen, W. Zhou and X. An, Bioresour. Technol., 2012, 124, 516–519 CrossRef CAS PubMed.
- X. Gong, W. Li, K. Wang and J. Hu, Bioresour. Technol., 2013, 141, 145–151 CrossRef CAS PubMed.
- L. N. Shi, Y. M. Lin, X. Zhang and Z. L. Chen, Chem. Eng. J., 2011, 171, 612–617 CrossRef CAS PubMed.
- T. Liu, L. Zhao, D. Sun and X. Tan, J. Hazard. Mater., 2010, 184, 724–730 CrossRef CAS PubMed.
- B. Geng, Z. Jin, T. Li and X. Qi, Chemosphere, 2009, 75, 825–830 CrossRef CAS PubMed.
- B. Geng, Z. Jin, T. Li and X. Qi, Sci. Total Environ., 2009, 407, 4994–5000 CrossRef CAS PubMed.
- A. C. Zimmermann, A. Mecabô, T. Fagundes and C. A. Rodrigues, J. Hazard. Mater., 2010, 179, 192–196 CrossRef CAS PubMed.
- C. Shen, H. Chen, S. Wu, Y. Wen, L. Li, Z. Jiang, M. Li and W. Liu, J. Hazard. Mater., 2013, 244, 689–697 CrossRef PubMed.
- T. Wajima, Y. Umeta, S. Narita and K. Sugawara, Desalination, 2009, 249, 323–330 CrossRef CAS PubMed.
- K. Babaeivelni and A. P. Khodadoust, J. Colloid Interface Sci., 2013, 394, 419–427 CrossRef CAS PubMed.
- S. M. Miller, M. L. Spaulding and J. B. Zimmerman, Water Res., 2011, 45, 5745–5754 CrossRef CAS PubMed.
- S. Jagtap, D. Thakre, S. Wanjari, S. Kamble, N. Labhsetwar and S. Rayalu, J. Colloid Interface Sci., 2009, 332, 280–290 CrossRef CAS PubMed.
- F. M. Hasmath and M. Sankaran, J. Chitin Chitosan Sci., 2013, 8, 42–49 Search PubMed.
- Z. Shi, K. Neoh, E. Kang, C. K. Poh and W. Wang, Biomacromolecules, 2009, 10, 1603–1611 CrossRef CAS PubMed.
- M. Rajiv Gandhi, G. Kousalya, N. Viswanathan and S. Meenakshi, Carbohydr. Polym., 2011, 83, 1082–1087 CrossRef PubMed.
- K. Kavitha, S. Sutha, M. Prabhu, V. Rajendran and T. Jayakumar, Carbohydr. Polym., 2013, 93, 731–739 CrossRef CAS PubMed.
- F. Al-Sagheer and S. Merchant, Carbohydr. Polym., 2011, 85, 356–362 CrossRef CAS PubMed.
- C. Y. Cao, J. Qu, W. S. Yan, J. F. Zhu, Z. Y. Wu and W. G. Song, Langmuir, 2012, 28, 4573–4579 CrossRef CAS PubMed.
- X. G. Chen and H. J. Park, Carbohydr. Polym., 2003, 53, 355–359 CrossRef CAS.
- X. Li, H. Zhu, J. Wei, K. Wang, E. Xu, Z. Li and D. Wu, Appl. Phys. A: Mater. Sci. Process., 2009, 97, 341–344 CrossRef CAS.
- Y. Abou El-Reash, M. Otto, I. Kenawy and A. Ouf, Int. J. Biol. Macromol., 2011, 49, 513–522 CrossRef CAS PubMed.
- D. Park, Y. S. Yun and J. M. Park, Environ. Sci. Technol., 2004, 38, 4860–4864 CrossRef CAS.
- M. Lopez-Ramon, F. Stoeckli, C. Moreno-Castilla and F. Carrasco-Marin, Carbon, 1999, 37, 1215–1221 CrossRef CAS.
- A. Sarhan, D. Ayad, D. Badawy and M. Monier, React. Funct. Polym., 2009, 69, 358–363 CrossRef CAS PubMed.
- Z. Wu, S. Li, J. Wan and Y. Wang, J. Mol. Liq., 2012, 170, 25–29 CrossRef CAS PubMed.
- L. Li, L. Fan, M. Sun, H. Qiu, X. Li, H. Duan and C. Luo, Colloids Surf., B, 2013, 107, 76–83 CrossRef CAS PubMed.
- C. Jung, J. Heo, J. Han, N. Her, S. J. Lee, J. Oh, J. Ryu and Y. Yoon, Sep. Purif. Technol., 2013, 106(0), 63–71 CrossRef CAS PubMed.
- X.-j. Hu, J.-s. Wang, Y.-g. Liu, X. Li, G.-m. Zeng, Z.-l. Bao, X.-x. Zeng, A.-w. Chen and F. Long, J. Hazard. Mater., 2011, 185, 306–314 CrossRef CAS PubMed.
- L. Sun, L. Zhang, C. Liang, Z. Yuan, Y. Zhang, W. Xu, J. Zhang and Y. Chen, J. Mater. Chem., 2011, 21, 5877–5880 RSC.
- G. Z. Kyzas, N. K. Lazaridis and M. Kostoglou, J. Colloid Interface Sci., 2013, 407, 432–441 CrossRef CAS PubMed.
- K. K. A. Santhana, C. U. Kumar, V. Rajesh and N. Rajesh, Int. J. Biol. Macromol., 2014, 66, 135–143 CrossRef PubMed.
- P. Xie, X. Hao, O. A. Mohamad, J. Liang and G. Wei, Appl. Biochem. Biotechnol., 2013, 169, 570–587 CrossRef CAS PubMed.
- Y. Bulut, N. Gözübenli and H. Aydın, J. Hazard. Mater., 2007, 144, 300–306 CrossRef CAS PubMed.
- Y.-S. Ho and G. McKay, Water Res., 2000, 34, 735–742 CrossRef CAS.
- D. Mohan and C. U. Pittman Jr, J. Hazard. Mater., 2006, 137, 762–811 CrossRef CAS PubMed.
|
This journal is © The Royal Society of Chemistry 2015 |
Click here to see how this site uses Cookies. View our privacy policy here.