A novel carbon nanotubes reinforced superhydrophobic and superoleophilic polyurethane sponge for selective oil–water separation through a chemical fabrication
Received
31st July 2014
, Accepted 27th August 2014
First published on 27th August 2014
Abstract
Oil spillage and industrial oily wastewater have caused severe environmental concerns. A super absorbent material capable of separating oil–water mixtures, especially with a high absorption capacity and mechanical strength, is urgently desired. Here, a common and feasible approach to fabricate carbon nanotubes (CNTs) reinforced polyurethane (PU) sponge is presented that shows superhydrophobic and superoleophilic properties. The method involves the oxidative self-polymerization of dopamine and the reaction of hydrophilic polydopamine (PDA) with hydrophobic octadecylamine (ODA). The superhydrophobic stability of the as-prepared sponge with temperatures and in corrosive solutions of different pH is investigated. The as-prepared sponge could quickly and selectively absorb various kinds of oils up to 34.9 times of its own weight, and the absorbed oils can be collected by a simple squeezing process. More interestingly, the mechanical strength of the as-prepared sponge is improved due to the structural reinforcement of CNTs anchored on the sponge skeleton. Furthermore, the recovered sponge could be reused to separate oil–water mixture 150 times while maintaining its high absorption capacity. This promising multifunctional sponge exhibits significant potential as an efficient absorbent in large-scale oil–water separation applications.
Introduction
Along with the rapid development of petrochemical and marine industries, dealing with the increasing number of oil spills and industrial oily wastewater has become a worldwide challenge.1–3 Traditional absorbent materials for oil–water separation are almost microporous absorbers, such as wool,4 zeolites5 and activated carbon,6 which have the drawbacks of poor absorption capacity, non-selective water–oil absorption and they are difficult to reuse. Designing superhydrophobic surface with a water contact angle (WCA) greater than 150° has attracted great attention in recent years because these fascinating properties would be useful for extensive applications.7,8 Jiang et al.9 in 2004 first proposed the idea of taking the superhydrophobic surface into oil–water separation applications, and successfully prepared a superhydrophobic and superoleophilic stainless steel mesh. Subsequently, various materials, including carbon nanotubes (CNTs),10,11 graphene,12,13 copper mesh,14,15 polytetrafluoroethylene (PTFE)16,17 and trichloromethylsilane,18 have been used to prepare special wettable materials for the separation of oil from water. However, these materials suffer from limitations for practical applications due to their high cost or complicated manufacturing processes.
Commercially available polyurethane (PU) sponge is a porous and a hydrophilic polymer with the characteristics of low cost, high absorption ability, good elasticity and easy large-scale fabrication. Recently, it has become a favorable candidate for the fabrication of a superhydrophobic and superoleophilic sponge for oil–water separation.17,19–23 However, most fabrication processes are complicated and the superhydrophobic stability of the sponges over a range of temperatures and in corrosive solutions are rarely presented. In addition, the mechanical strength of the sponge used for oil–water separation is seldom reported, which is important parameter for the reuse of sponge. Therefore, a superhydrophobic and superoleophilic PU sponge with a high mechanical strength, excellent elasticity and long-term superhydrophobic stability is highly desirable for oil–water separation.
Mussel (Fig. 1a) can easily adhere to all kinds of inorganic and organic surfaces depending on its secreted proteins. The adhesive protein has been shown to contain abundant 3,4-dihydroxy-L-phenylalanine (DOPA) (Fig. 1b), which can form strong covalent and noncovalent bonds with substrates.24 Lee and co-workers found that dopamine (Fig. 1c), which is a molecular structural mimic of DOPA, could self-polymerize and deposit on numerous material surfaces under mild environment.25 The resultant polydopamine (PDA) (Fig. 1d) is an extremely versatile platform for a diverse range of secondary reactions.25,26 For example, Zhang et al.27 prepared a SiO2/PDA/Ag composite particle, and this core/shell/satellite particle exhibited extreme water repellency after 1H,1H,2H,2H-perfluorodecanethiol fluorination. Fei et al.28 modified the outer surface of CNTs by the oxidative polymerization of dopamine, and then successfully deposited gold nanoparticles on the PDA layer.
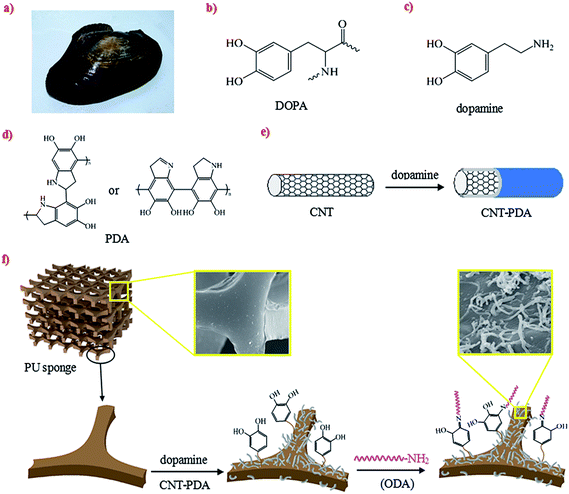 |
| Fig. 1 Photograph of mussel (a). Chemical structures of DOPA (b), dopamine (c) and PDA (d). Schematic drawings of the facile coating of CNTs with dopamine (e) and the fabrication process of superhydrophobic and superoleophilic PU–CNT–PDA–ODA sponge (f). | |
In this study, inspired by the remarkable adhesive ability of dopamine, we report a common and feasible approach to fabricate a superhydrophobic and superoleophilic polyurethane sponge reinforced by CNTs. The CNTs were first coated with a dopamine film, then the dopamine modified CNTs (CNT–PDA) were anchored on the skeleton of sponge through the self-polymerization of dopamine. Octadecylamine (ODA) was conjugated with a PDA film through a post chemical reaction afterward. The as-prepared sponge shows the outstanding properties of high absorption capacity, high mechanical strength, excellent elasticity and long-time superhydrophobic stability, which ensures that this promising sponge can be applied to handle oil spill accidents and oily wastewater.
Experimental
Materials
Polyurethane sponge (density: 0.03 g cm−3, average pore diameter: 200 μm) was supplied by Shenzhen Shiyuan Sponge Products Co., Ltd. Dopamine and tris(hydroxymethyl) aminomethane hydrochloride (Tris–HCl) were purchased from Suzhou Tianke Trade Co., Ltd. The CNTs (diameter: 20–40 nm) were purchased from Nanjing XF Nano Materials Tech Co., Ltd. ODA was provided by ShangHai Siyu Chemical Technology Co., Ltd. The anhydrous ethanol was provided by Huadong Reagent Factory of Shenyang in China. All the chemicals were used as received.
Sample preparation
The CNT–PDA was prepared as follows. Typically, 100 mg CNTs were added into freshly prepared dopamine solution with pH = 8.5. After ultrasonic dispersion for 20 min, the mixture was stirred for 24 h. Then, the CNT–PDA was filtered, washed with distilled water five times and dried at 50 °C.
A piece of PU sponge (15 mm × 10 mm × 10 mm) was first ultrasonically washed with distilled water and ethanol three times, and then etched in CrO3/H2SO4 solution for 1 min.19 The as-treated sponge and CNT–PDA (0.5 g L−1) were added into 20 mL dopamine solution (2 g L−1, pH = 8.5) followed by stirring for 24 h. After being washed with distilled water and dried in an oven, the resulting PU–CNT–PDA sponge was reacted with ODA (4–12 mM) in ethanol solution (pH = 8.5). Finally, the as-prepared PU–CNT–PDA–ODA sponge was washed with ethanol and dried in oven at 50 °C. In addition, we also prepared a PU–PDA–ODA sponge without adding CNT–PDA for comparison.
Characterization
Contact angles were measured by a contact-angle meter (JGW-360A, Chengdeshi Shipeng Detection Equipment Co., Ltd) using a droplet of water or lubricating oil (5 μL) at room temperature. Average values of contact angle were obtained from five measurements per sponge. The morphology of the sponges was evaluated by SEM (Quanta 200, SuZhou Bondray Electronics Technology Co., Ltd). FT-IR data were acquired using a Tensor27 infrared spectrometer (Shenyang Wanfang Zhongtong Trade Co., Ltd). TGA data were obtained using a thermogravimetric analyzers (STA73000, Beijing SaiSiMeng Instruments Co., Ltd) at a heating rate of 10 °C min−1 in an air atmosphere.
Results and discussion
Fabrication of superhydrophobic and superoleophilic PU sponge
The schematic drawings of the facile coating of CNTs with dopamine and the fabrication process of PU–CNT–PDA–ODA sponge are shown in Fig. 1e and f. CNTs were dispersed in an aqueous solution of dopamine to form a CNT–PDA composite with a large amount of phenolic hydroxy groups on their surface. The PU sponge was first etched in an oxidative CrO3/H2SO4 solution, with the aim of increasing the roughness of the sponge's skeleton and to produce hydrophilic groups such as –OH and –COOH.21 These functional groups on both the surfaces of sponge and CNT–PDA make them easily an reactive interface. Then, dopamine was deposited on the surfaces of the sponge and CNT–PDA through oxidative self-polymerization, resulting in the transformation of the sponge wettability from originally being hydrophilic and oleophilic (Fig. 2a) to superhydrophilic and superoleophilic (Fig. 2b). After adding ODA, the sponge became superhydrophobic and superoleophilic (Fig. 2c), indicating that the amino of ODA has reacted with PDA via Michael addition or Schiff base reactions.25 The WCA of the as-prepared sponge is 158° (Fig. 2d), and a drop of lubricating oil completely permeates through the surface with a contact angle of almost 0° (Fig. 2e).
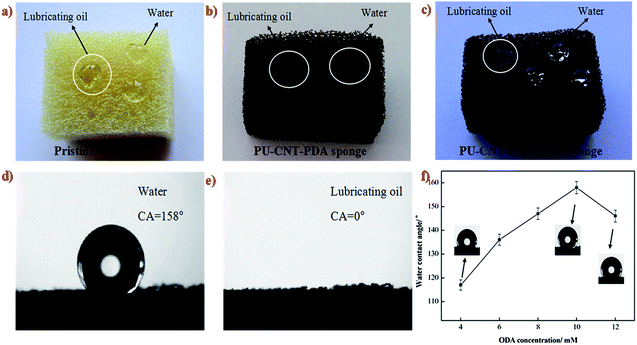 |
| Fig. 2 Digital photographs of water and lubricating oil droplets on the pristine PU sponge (a), PU–CNT–PDA sponge (b), and PU–CNT–PDA–ODA sponge (c). WCA of 158° (d) and lubricating oil contact angle of 0° (e) on the PU–CNT–PDA–ODA sponge. Effect of ODA concentration on the hydrophobic property of the PU–CNT–PDA–ODA sponge (f). | |
Hierarchical structure and low surface energy are the two key factors to construct special wettable surface.29,30 In the present work, the microscaled interconnected skeleton of the sponge and nanoscaled CNT–PDA both contribute to the micro–nano scale binary structure, and the low surface energy group is introduced by the hydrophobic long alkyl chain of ODA. We also investigated the effect of ODA concentration on the hydrophobic property of the PU–CNT–PDA–ODA sponge (Fig. 2f). It can be seen that the WCA increases gradually at first and then decreases with the increasing ODA concentration. The maximum WCA of the PU–CNT–PDA–ODA sponge reaches up to 158° at the concentration of 10 mM, which indicates a superhydrophobic property of the sponge. However, the WCA decreases to 146° when the concentration of ODA is 12 mM. The main reason of this phenomena is that high ODA concentration would lead the amino group of ODA as a core to be wrapped by the long alkyl chain, which could reduce the contact chance between the amino group and PDA, thus reducing the superhydrophobicity of sponge.
Surface morphological analysis
The surface morphological evolution of the PU sponge was investigated by SEM at different magnifications, as shown in Fig. 3. SEM images show that the pristine sponge exhibits a smooth surface and has a three dimensional hierarchical porous structure with pore sizes in the range of 70–300 μm (Fig. 3a). After being pretreated in oxidative CrO3/H2SO4 solution, the skeleton of the sponge becomes a little rougher than the pristine one (Fig. 3b). It is worth noting that the pretreatment of pristine sponge in the oxidative solution should not be too long (typically <1 min), to prevent the sponge from becoming brittle and losing elasticity. SEM images of the PU–PDA–ODA sponge are depicted in Fig. 3c. It can be seen that the skeletons of sponge are covered by countless micro–nano-scale protrusions, indicating that ODA has been successfully connected to the sponge through PDA. The PU–PDA–ODA sponge shows a WCA of 156° (inset of Fig. 3c1). Fig. 3d are the SEM images of the PU–CNT–PDA–ODA sponge. It is clear that numerous CNT–PDA were uniformly anchored on the skeleton surface of the sponge. The micro-porous structure of the sponge in combination with the nano-scale CNT–PDA created a dually rough structure, which is very similar to the structure as observed in a lotus leaf. This Cassie's mode-like structure of the PU–CNT–PDA–ODA sponge can effectively reduce the solid–liquid contact area, possessing a WCA of 158° (inset of Fig. 3d1).
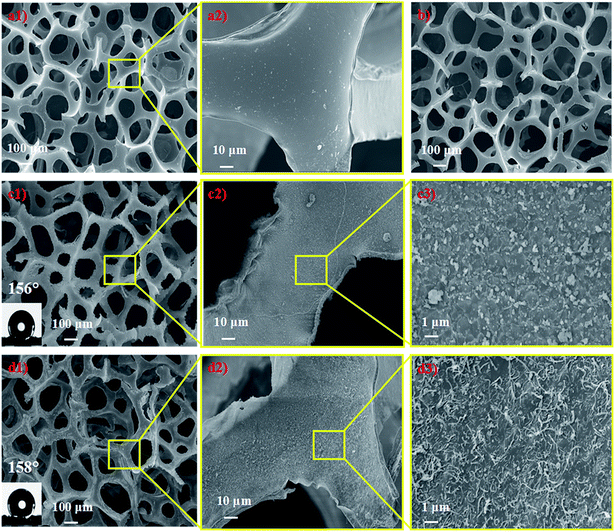 |
| Fig. 3 SEM images of pristine PU sponge (a1 and a2), PU sponge after oxidative CrO3/H2SO4 solution treatment (b), PU–PDA–ODA sponge (c1–c3), and PU–CNT–PDA–ODA sponge (d1–d3). | |
FT-IR and TG analysis
The FT-IR spectra of pristine PU sponge and PU–CNT–PDA–ODA sponge are shown in Fig. 4a. The band at 3622 cm−1 is associated with the stretching vibration of N–H, and the bands at 2982, 2887 and 678 cm−1 can be attributed to the stretching vibration and bending vibration of C–H. The band observed at 1702 cm−1 is the characteristic peak of C
O. The peaks at 1523 and 1365 cm−1 are from the stretching vibration of C
C in aromatic rings, and the band at 1116 cm−1 is attributed to the C–O stretching vibration. All above characteristic peaks confirm that the sponge is a kind of polyester–polyurethane.31 Compared with the FT-IR spectra of the pristine sample, the PU–CNT–PDA–ODA sponge displays several additional peaks at 3338, 1642, 1229 and 1098 cm−1, corresponding to the hydroxyl group of PDA, the aromatic ring of CNT–PDA, the C–N of ODA, and the C–O of PDA, respectively. In addition, the peak intensity for the N–H and saturated C–H become stronger, which is due to the introduction of ODA.
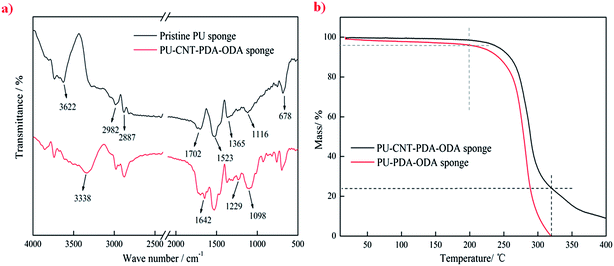 |
| Fig. 4 FT-IR spectra of pristine PU sponge and PU–CNT–PDA–ODA sponge (a), TGA curves of PU–PDA–ODA sponge and PU–CNT–PDA–ODA sponge (b). | |
The thermal stability of the PU–PDA–ODA and PU–CNT–PDA–ODA sponges was studied by thermogravimetric analysis. As shown in Fig. 4b, there is no clear weight loss at temperatures below 200 °C in the case of the PU–CNT–PDA–ODA sponge, and the weight loss is only 4% for the PU–PDA–ODA sponge. This proves that the addition of CNTs improved the thermal stability of the PU–CNT–PDA–ODA sponge. At 320 °C, the PU–PDA–ODA sponge completely loses its weight because of oxidative decomposition, while the weight of PU–CNT–PDA–ODA sponge is reduced to approximately 23%. This result indicates that the majority of modified CNTs have been anchored on the skeleton of the PU sponge, because the amount of total added CNTs is 25%.
Superhydrophobic stability with temperature and in the presence of corrosive media
The superhydrophobic stability of the PU–CNT–PDA–ODA sponges with temperature and in the presence of corrosive media was investigated by heat treatment in a temperature ranging from 50 °C to 100 °C and immersion into aqueous solutions with pH in the range from 1 to 14 for 24 h. The sponges show stable superhydrophobicity in the temperature range of 50 to 100 °C, maintaining a constant WCA that is greater than 150° (Fig. 5a). The SEM observation shows that there is no change of the surface morphology of sponge after heat treatment (Fig. 5c). The WCA of the PU–CNT–PDA–ODA sponges decreases slightly after immersion into different pH solutions for 24 h, but that values all remained higher than 145° (Fig. 5b). This is because that corrosive solution erodes the surface of the sponge, resulting in the loss of CNTs anchored on the sponge, as supported by SEM imaging (Fig. 5d).
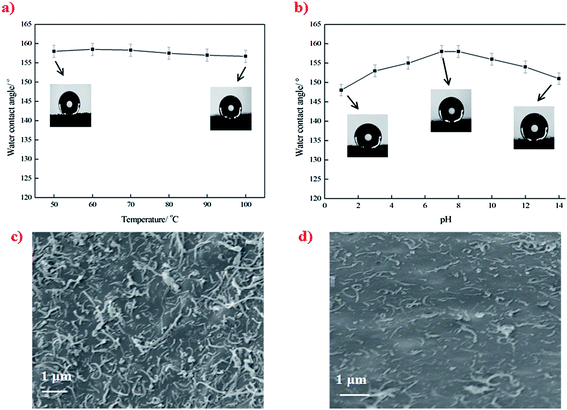 |
| Fig. 5 Effect of temperature on the WCA of the PU–CNT–PDA–ODA sponges (a). Relationship between pH values and WCA of the PU–CNT–PDA–ODA sponges after immersing them in solutions of different pH values for 24 h (b). SEM images of the sponges after heat treatment (c) for 24 h, immersing them in corrosive solution (d) for 24 h. | |
Enhancement of mechanical strength and elasticity
Unique mechanical strength and excellent elasticity are observed in the superhydrophobic PU–CNT–PDA–ODA sponge. A PU–CNT–PDA–ODA sponge of 6 cm2 could bear 3.3 kPa pressure without any deformation, while the pristine sponge with the same area is out of shape under the same loading (Fig. 6a). Based on Hooke's Law, the elasticity coefficient (EC) of the PU–CNT–PDA–ODA sponge is improved 4-fold over that of the pristine sponge (inset of Fig. 6a). The enhancement of mechanical strength and elasticity is mainly contributed by the mechanical reinforcing effect of CNTs anchored on the interconnected skeleton of the sponge (Fig. 3d3 and 5c). To the best of our knowledge, the performance enhancement of the PU sponge by CNTs in this work is reported for the first time.
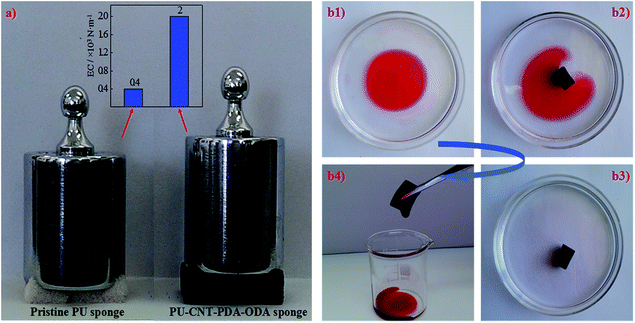 |
| Fig. 6 Digital photograph (a) of same weight on the pristine sponge (left) and PU–CNT–PDA–PDA sponge (right), elasticity coefficients (EC) of pristine sponge and PU–CNT–PDA–PDA sponge in the inset of (a). A series of photos for the process of absorption and collection of lubricating oil (dyed with Oil Red) from the surface of water (b1–b4). | |
Oil–water separation
The as-prepared PU–CNT–PDA–ODA sponge exhibits excellent selective absorption of oil from water. Once a piece of PU–CNT–PDA–ODA sponge touched the lubricating oil layer (dyed with Oil Red) on the water surface (the concentration ratio of oil to water is 0.5%, corresponding to the oil content of oilfield wastewater), it completely absorbed the oil within five seconds, resulting in a transparent water region without any contaminations (Fig. 6b). The absorbed oil could be collected just through a simple squeezing process, which is more time-saving and eco-friendly than other reported methods, such as heat treatment or11 burn off.32 The mechanism of the oil–water separation can be explained as follows. The sponge spontaneously absorbs the oil because of the similar surface energies between the oil (e.g. lubrication oil, 31 mN m−1) and ODA (31 mN m−1), but water is strongly repelled due to its much higher surface energy (72 mN m−1).21 Then, the oil is driven through the pores of the sponge into its bulk via capillary forces, while water stays exclusively at the exterior of the sponge, resulting in the highly efficient separation of oil from water.16,21 Further, the oleophilic ODA decorated on the interconnected skeleton facilitates the oil transportation from external into the inner pores and thus exhibits a large oil absorption capacity.
The absorption capacity (k) was calculated by the weight-gain ratio according to the following eqn (1):
where
M1 and
M2 represent the weight of the as-prepared sponge before and after absorption of oil or organic solvent, respectively. As shown in
Fig. 7a, the PU–CNT–PDA–ODA sponge could absorb a wide range of oils and organic solvents, and exhibits high absorption capacities ranging from 22 to 34.9 times of its own weight, depending on the viscosity and density of the oil or organic solvent. Moreover, the absorption capacity of our superhydrophobic sponge outshines the reported ones, as shown in
Table 1. After heating/corrosion treatment, the PU–CNT–PDA–ODA sponge still shows high oil absorption capacity (
Fig. 7b). From the slight changes of the water contact angle and the oil absorption capacity (
Fig. 5a, b and
7b), we can confirm that the PU–CNT–PDA–ODA sponge after heating/corrosion treatment still possesses excellent oil–water separating ability.
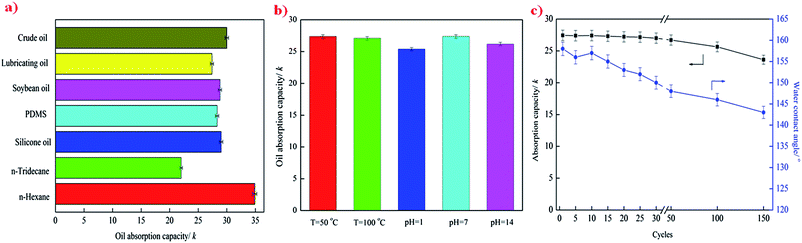 |
| Fig. 7 Absorption capacity of the superhydrophobic PU–CNT–PDA–ODA sponge for different oils and organic solvents (a). Lubricating oil absorption capacity of the PU–CNT–PDA–ODA sponge after heating/corrosion treatment (b). Effects of absorption/collection cycle on the absorption capacity of lubricating oil and WCA of the PU–CNT–PDA–ODA sponge (c). | |
Table 1 Oil absorption capacity of different absorbent materials
Absorbent materials |
Types of oil |
Oil absorption capacity |
Reference |
PU/PTFE/NPs sponge |
Mineral oil |
13 times |
16
|
PU/PTFE/SiO2/polysiloxane sponge |
Silicon oil |
9.9 times |
17
|
PU/AgNO3/dodecanoic acid sponge |
Lubricating oil |
19 times |
19
|
PU/CNT/PDMS sponge |
n-Hexane |
15 times |
20
|
Pristine sponge |
Lubricating oil |
8 times |
Our work |
PU–CNT–PDA–ODA sponge |
Silicon oil |
29 times |
Our work |
PU–CNT–PDA–ODA sponge |
Lubricating oil |
27.4 times |
Our work |
PU–CNT–PDA–ODA sponge |
n-Hexane |
34.9 times |
Our work |
The absorption capacity and WCA of the PU–CNT–PDA–ODA sponge as a function of absorption/collection cycle for lubricating oil is presented in Fig. 7c. For the earlier thirty absorption/collection cycles, there is no significant decrease in absorption capacity, and the WCA still remains greater than 150°, indicating that the sponge can withstand at least 30 cycles of mechanical squeezing without losing the superhydrophobicity. After 150 absorption/collection cycles, the absorption capacity of the PU–CNT–PDA–ODA sponge only decreases by 14%, and the WCA is still above 140°, showing outstanding reusability for oil/organics–water separation. The slight decrease in the absorption capacity is due to the residual oil inside the sponge, which cannot be fully removed just by a simple manual squeezing process. The excellent properties of high absorption capacity and good reusability of the superhydrophobic sponge will guarantee its promising application for oil–water separation purposes.
Conclusions
In conclusion, a novel superhydrophobic and superoleophilic PU sponge reinforced by CNTs was successfully fabricated. The CNTs were firmly anchored on the skeleton of sponge by the adhesive dopamine. The hydrophobic ODA was conjugated with the sponge through chemical bonding. The as-prepared PU–CNT–PDA–ODA sponge exhibited outstanding features: water repellency, superhydrophobic stability with temperature and in corrosive solutions, high mechanical strength, excellent elasticity and high selective absorption capacity up to 34.9 times of its own weight. Furthermore, the absorbed oils could be collected by a simple squeezing process, and the sponge could be reused for 150 times still with high absorption capacity and high hydrophobicity. Because of the inexpensive materials, feasible fabrication technique and excellent performance, this superhydrophobic PU–CNT–PDA–ODA sponge will be a promising candidate for the selective removal of oil from water.
Acknowledgements
The research is supported by the National Young Top Talents Plan of China (2012), National Science Foundation of China (Grant no. 50903010, 51175066), FANEDD (201164), New Century Excellent Talents in University (NCET-12-0704), Provincial New Century Excellent Talent (1251-NCET-007) and the Science Foundation for Distinguished Young Scholars of Heilongjiang Province (JC201403).
Notes and references
- C. H. Peterson, S. D. Rice, J. W. Short, D. Esler, J. L. Bodkin, B. E. Ballachey and D. B. Irons, Science, 2003, 302, 2082–2086 CrossRef CAS PubMed.
- J. Aurell and B. K. Gullett, Environ. Sci. Technol., 2010, 44, 9431–9437 CrossRef CAS PubMed.
- T. Daltona and D. Jinb, Mar. Pollut. Bull., 2010, 60, 1939–1945 CrossRef PubMed.
- M. M. Radetic, D. M. Jocic, P. M. Jovancic, Z. L. Petrovic and H. F. Thomas, Environ. Sci. Technol., 2003, 37, 1008–1012 CrossRef CAS.
- C. K. Tsai, C. Y. Liao, H. P. Wang, Y. C. Chien and C. J. G. Jou, Mar. Pollut. Bull., 2008, 57, 895–898 CrossRef CAS PubMed.
- A. Bayat, S. F. Aghamiri, A. Moheb and G. R Vakili-Nezhaad, Chem. Eng. Technol., 2005, 28, 1525–1528 CrossRef CAS.
- X. Yao, Y. L. Song and L. Jiang, Adv. Mater., 2011, 23, 719–734 CrossRef CAS PubMed.
- V. A. Ganesh, H. K. Raut, A. S. Nair and S. Ramakrishna, J. Mater. Chem., 2011, 21, 16304–16322 RSC.
- L. Feng, Z. Y. Zhang, Z. H. Mai, Y. M. Ma, B. Q. Liu, L. Jiang and D. B. Zhu, Angew. Chem., Int. Ed., 2004, 43, 2012–2014 CrossRef CAS PubMed.
- X. C. Gui, J. Q. Wei, K. L. Wang, A. Y Cao, H. W. Zhu, Y. Jia, Q. K. Shu and D. H. Wu, Adv. Mater., 2010, 22, 617–621 CrossRef CAS PubMed.
- X. C. Gui, Z. P. Zeng, Z. Q. Lin, Q. M. Gan, R. Xiang, Y. Zhu, A. Y. Cao and Z. K. Tang, ACS Appl. Mater. Interfaces, 2013, 5, 5845–5850 CAS.
- H. C. Bi, X. Xie, K. B. Yin, Y. L. Zhou, S. Wan, L. B. He, F. Xu, F. Banhart, L. T. Sun and R. S. Ruoff, Adv. Funct. Mater., 2012, 22, 4421–4425 CrossRef CAS.
- D. D. Nguyen, N. H. Tai, S. B. Lee and W. S. Kuo, Energy Environ. Sci., 2012, 5, 7908–7912 CAS.
- Q. M. Pan, M. Wang and H. B. Wang, Appl. Surf. Sci., 2008, 254, 6002–6006 CrossRef CAS PubMed.
- C. R. Crick, J. A. Gibbins and I. P. Parkin, J. Mater. Chem. A, 2013, 1, 5943–5948 CAS.
- P. Calcagnile, D. Fragouli, I. S. Bayer, G. C. Anyfantis, L. Martiradonna, P. D. Cozzoli, R. Cingolani and A. Athanassiou, ACS Nano, 2012, 6, 5413–5419 CrossRef CAS PubMed.
- G. H. Jiang, R. B. Hu, X. G. Xi, X. H. Wang and R. J. Wang, J. Mater. Res., 2013, 28, 651–656 CrossRef CAS.
- J. P. Zhang and S. Seeger, Adv. Funct. Mater., 2011, 21, 4699–4704 CrossRef CAS.
- Q. Zhu, Q. M. Pan and F. T. Liu, J. Phys. Chem. C, 2011, 115, 17464–17470 CAS.
- C. F. Wang and S. J. Lin, ACS Appl. Mater. Interfaces, 2013, 5, 8861–8864 CAS.
- Q. Zhu, Y. Chu, Z. K. Wang, N. Chen, L. Lin, F. T. Liu and Q. M. Pan, J. Mater. Chem. A, 2013, 1, 5386–5393 CAS.
- H. X. Sun, A. Li, Z. Q. Zhu, W. D. Liang, X. H. Zhao, P. Q. La and W. Q. Deng, ChemSusChem, 2013, 6, 1057–1062 CrossRef CAS PubMed.
- X. Y. Zhang, Z. Li, K. S. Liu and L. Jiang, Adv. Funct. Mater., 2013, 23, 2881–2886 CrossRef CAS.
- L. A. Burzio and J. H. Waite, Biochemistry, 2000, 39, 11147–11153 CrossRef CAS PubMed.
- H. Lee, S. M. Dellatore, W. M. Miller and P. B. Messersmith, Science, 2007, 318, 426–430 CrossRef CAS PubMed.
- M. J. LaVoie, B. L. Ostaszewski, A. Weihofen, M. G. Schlossmacher and D. J. Selkoe, Nat. Med., 2005, 11, 1214–1221 CrossRef CAS PubMed.
- L. Zhang, J. J. Wu, Y. X. Wang, Y. H. Long, N. Zhao and J. Xu, J. Am. Chem. Soc., 2012, 134, 9879–9881 CrossRef CAS PubMed.
- B. Fei, B. T. Qian, Z. Y. Yang, R. H. Wang, W. C. Liu, C. L. Mak and J. H. Xin, Carbon, 2008, 46, 1795–1797 CrossRef CAS PubMed.
- D. Ebert and B. Bhushan, J. Colloid Interface Sci., 2012, 368, 584–591 CrossRef CAS PubMed.
- L. Feng, S. Li, Y. Li, H. Li, L. Zhang, J. Zhai, Y. Song, B. Liu, L. Jiang and D. Zhu, Adv. Mater., 2002, 14, 1857–1860 CrossRef CAS.
- D. W. Hatchett, G. Kodippili, J. M. Kinyanjui, F. Benincasa and L. Sapochak, Polym. Degrad. Stab., 2005, 87, 555–561 CrossRef CAS PubMed.
- X. T. Zhu, Z. Z. Zhang, G. N. Ren, J. Yang, K. Wang, X. H. Xu, X. H. Men and X. Y. Zhou, J. Mater. Chem., 2012, 22, 20146–20148 RSC.
|
This journal is © The Royal Society of Chemistry 2015 |
Click here to see how this site uses Cookies. View our privacy policy here.