DOI:
10.1039/C5SM00324E
(Paper)
Soft Matter, 2015,
11, 3794-3805
Simulation methods for solvent vapor annealing of block copolymer thin films†
Received
7th February 2015
, Accepted 27th March 2015
First published on 27th March 2015
Abstract
Recent progress in modelling the solvent vapor annealing of thin film block copolymers is examined in the context of a self-consistent field theory framework. Key control variables in determining the final microdomain morphologies include swelling ratio or swollen film solvent volume fraction, swollen film thickness, substrate and vapor atmosphere surface energies, effective volume fraction, and effective Flory–Huggins interaction parameter. The regime of solvent vapor annealing studied is where the block copolymer has a high enough Flory–Huggins parameter that ordered structures form during swelling and are then trapped in the system through quenching. Both implicit and explicit consideration of the solvent vapor is considered to distinguish the cases in which solvent vapor leads to a non-bulk morphology. Block-selective solvents are considered based on the experimental systems of polystyrene-b-polydimethylsiloxane annealed with toluene and heptane. The results of these simulations are compared with these experiments.
Introduction
Solvent vapor annealing (SVA) has become a leading processing method in producing long range ordered structures in thin film block copolymer (BCP) systems.1–18SVA is particularly important for BCPs with high Flory–Huggins interaction parameter χ,1–3,6–10,19–28 which are of interest for making microdomain patterns with small period but which have high order–disorder transition (ODT) temperatures requiring high annealing temperatures. SVA also enables access to non-bulk morphologies such as spheres or lamellae formed from a bulk-cylindrical BCP.29 The thin film morphology is governed primarily by χ, degree of polymerization N, BCP minority component volume fraction f,23,29,30 and surface/confinement effects,31 but SVA provides additional degrees of freedom based on the fraction of different solvents incorporated, their selectivity with respect to each block, and in thin films, solvent effects on the surface and interface energies.
Although there has been great success with SVA in producing ordered structures from BCPs with high χ,24,32 the detailed physics of how the ordering takes place is not fully understood and many studies have treated the annealing process as a “black box.” Real time monitoring of morphology is typically conducted by measuring film thickness using ellipsometry or spectral reflectometry methods,33–35 by using in situ scattering methods,25,26 or by atomic force microscopy when there is enough elastic contrast between blocks.36–38 The detailed final morphology is usually characterized through destructive methods such as scanning electron microscopy or transmission electron microscopy in which samples are etched or stained39 or nonintrusive scattering methods coupled with inverse data analysis methods.40,41
GISAXS (grazing incidence small-angle X-ray scattering) studies have characterized the average morphology as a function of annealing time for several BCP systems.25,42–46 These experiments showed that ordering began during the swelling stages of the thin film and that the final structures were independent of the casting method. If films are swollen too much or if the BCP has a low χ, the order is lost at a critical swelling thickness during the anneal as the system exceeds the ODT.45,46 In these cases ordered structures reappear during quenching and are highly dependent on the quench dynamics. However, if the system is quenched from an ordered state, little lateral (in-plane) shrinkage is observed and the film collapses in the out-of-plane direction.46 This implies that the ordered structures formed in the swelled state are essentially preserved apart from an out-of-plane contraction as the solvent escapes. Thus the morphologies formed during SVA are a function of solvent removal rate, swollen solvent concentration, and swollen film thickness, but not the original as cast film morphology.43
These experimental results set the stage for trying to model the systems in a realistic manner. Previous attempts at modelling solvent annealed systems have focused on trying to find the final state of the system assuming equilibrium conditions are reached.47–57 These models have considered solvent either implicitly by using effective χ and volume fraction f parameters that are a function of the solvent incorporated into the system, or explicitly by using a separate partition function for selective solvent species in addition to the polymer partition function. The models correspond to solvent annealed films where ordering occurs during swelling, thus the morphologies found represent structures “frozen” from the swollen state in the final quenched state. More recently, dynamic simulations have been attempted starting with a disordered mixture of neutral solvent and BCP with ordering arising from the assumed quench dynamics imposed on the system.58 There have also been attempts at modelling the full SVA process starting with a dry disordered film and including solvent in a particle based model.59 General approaches to dynamical methods have also been suggested.60
In this study, we present an overview of the current theoretical framework in understanding the physical process of SVA in light of the recent in situ experimental progress with GISAXS and advances in modelling techniques. This framework is then applied to self-consistent field theory (SCFT) simulations with solvent modeled both implicitly and explicitly.
Methods
A. Experimental basis
In SVA experiments, thin films of a BCP are placed in a chamber with a solvent atmosphere. This atmosphere can either be from a liquid reservoir near the sample61,62 or from a controlled flow of vapor and inert gas into the chamber.6–8,24,33,63–66 The solvents used can be neutral or selectively preferential to the different blocks in the BCP.12 The morphologies formed in these thin films can be varied by controlling the vapor pressures and ratio of selective solvents, and often differ qualitatively from the bulk morphology.24,33,61,67–69 The morphology can even be changed reversibly upon further annealing in solvents with different selectivity.24,32,70 The solvent plasticizes the film71–74 raising its diffusivity and allowing ordering to occur even at ambient temperature. During SVA, the film thickness can swell to several times the initial thickness depending upon the solvent and its vapor pressure. SVA is effective both for thick films (i.e. with thickness many times L0, the natural periodicity of microdomains in the BCP) and for films with thickness of ≈L0 which form a monolayer of microdomains. The greatest level of control over the solvent environment is obtained from a continuous flow SVA process where solvent vapor of known composition flows through the sample chamber.33,34 Terracing (formation of holes and islands on the film surface) can occur for morphologies with in-plane orientation,75–77 but this is minimized by ensuring that the swelled film thickness is commensurate with the domain spacing.
The model presented here is based on data obtained from thin films of two different molecular weight polystyrene-b-polydimethylsiloxane (PS-PDMS) BCPs as well as homopolymer PS and PDMS thin films solvent annealed in various ratios of toluene and heptane vapors. These experiments were performed both in a control flow setup as well as a vented open solvent reservoir. Details of these experiments can be found in the ESI† (S1) as well as previous work.33,35 However, the methodology can be applied to other polymer systems as well.
B. Theoretical framework
In order to apply simulation methodology to SVA in BCP thin film systems, a framework of the major stages during SVA needs to be defined, schematically shown in Fig. 1. The three stages are swelling, annealing, and quenching. An additional pre-stage, casting, describes how the film is deposited, usually by spin coating from a dilute solution. The pre-stage determines initial film thickness D0, but assuming a thermodynamic equilibrium is reached during annealing, the memory of the as-cast morphology is lost.46 Swelling refers to the ingress of solvent into the thin film and the resulting increase in film thickness, and quenching or deswelling refers to solvent egress and the resulting decrease in film thickness. The film is usually assumed to collapse in the out-of-plane direction, preserving in-plane microdomains.45,46 Annealing refers to the diffusion of polymer chains to form ordered structures in the presence of the solvent, and can occur during swelling and quenching.
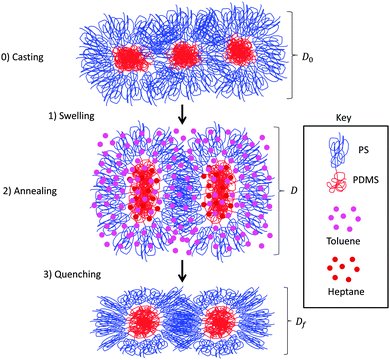 |
| Fig. 1 Schematic diagram showing overall ideal SVA process. Key of structures shown is on the right with blue coils being PS blocks, red coils being PDMS blocks, magenta dots being toluene solvent, and crimson dots being heptane solvent. (0) Casting of thin film of disordered micelles by spin coating or some other deposition method. (1) Swelling of the film occurs once the cast film is placed in solvent vapor atmosphere with film thickness increasing from D0 to D. (2) Annealing occurs during swelling while the equilibrium film thickness D is reached. (3) Quenching of the film occurs when the solvent atmosphere is removed and the film collapses to a final film thickness Df. Further annealing may occur during this step. | |
C. Modelling
Modelling the sequence of SVA stages is complex, especially if the film forms kinetically trapped structures. For films more than a few L0 thick, the concentration gradient of solvent in the film begins to play an important factor in the dynamics of quenching and can affect the final morphology when quench rates are slow.9 In the present work, swelled films less than 3L0 thick are considered and solvent gradients are neglected. To examine equilibrium morphologies, both an implicit model valid for low to moderate solvent incorporation by volume and a model where the solvent is modeled explicitly using a monoatomic fluid partition function are presented in the framework of SCFT.78–81 The details of the SCFT simulations used here are given in the ESI† (S2).
The film thickness and effective fraction of BCP in the implicit simulations and fraction of BCP and film thickness in the explicit simulations are determined from the experimental swelling ratio SR = D/D0, where D is the swollen film thickness before quenching and D0 is the initial film thickness. An effective χ (or range of χ) is selected to be proportional to the fraction of BCP in the implicit case42,58,82,83 though this is approximate due to uncertainties in measuring χ, and fluctuation effects.84 It should be noted the implicit model consists of just the standard BCP model but with effective f and χN parameters based on the incorporated solvents.
Since solvent annealed BCP systems can be thought of as multiple component and species systems, the number of degrees of freedom in the system can become intractable even with a small number of different solvents added to the system. To simplify the simulations, the solvents are treated as effective monomers of the two polymers such that each is completely selective to one of the blocks. This reduces the number of distinct chemical species in the system to two. A neutral solvent would then correspond to equal fractions of both monomers in this model. However, truly neutral solvents would promote a disordered structure, while highly preferential solvents in any ratio would likely promote microphase separation with micelle formation in the dilute polymer limit.
The alternative approach would treat each solvent as its own species, and each solvent added to the system would introduce additional χ parameters for interactions with each block and other solvents already in the system. In general this means for a p species system, there are
Flory–Huggins interaction parameters, i.e. 3, 6, 10… interaction parameters for a diBCP with 1, 2, 3… solvents, respectively. Additionally, each solvent has an independent volume fraction parameter. Such an approach quickly becomes intractable, thus we choose to assume the solvents behave analogous to the monomer of the corresponding polymer for which that solvent is selective.
For this assumption that a solvent behaves as a combination of two monomeric species for diBCP systems, an effective χ parameter denoted as χeff is applied to the system to account for the incorporation of solvent into the system without explicitly having χ parameters for each polymer and/or solvent pair. Previous studies85 have shown the relationship
| χeff ≅ χΦαBCP = χ(1 − Φsol)α | (1) |
to hold for neutral solvents where
Φsol is the volume fraction of solvent in the swollen film and
ΦBCP is the volume fraction of BCP in the swollen film (not to be confused with
f which refers to the minority component fraction of the BCP). Then
| 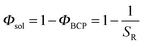 | (2) |
such that
χeff ≅
χS−αR. Here
α is a constant that is close to 1 in the dry film limit and increases to a value between 1.3 to 1.6 with increasing solvent incorporation.
42 Since most of our experiments have
SR in the range of 1.5 <
SR < 3.0,
χeff is in the range of

to

. If highly selective solvents are used (as is the case of heptane for PDMS
33), then
α can take on values less than 1 or even negative values in
eqn (1).
86 In these cases the solvents enhance phase separation between the blocks.
The model also includes an effective N. In the SCFT simulations, the chains are coarse-grained into Ns statistical monomers. Having more Ns segments leads to more accurate simulations, but at the cost of computational time which rises linearly with Ns. For the systems studied here, Ns = 125 which corresponds to 0.25N for a 45.5 kg mol−1f = 0.33 PS-PDMS and to 0.15N for a 75.5 kg mol−1 PS-PDMS with f = 0.41. Length scales in the simulations are determined from
which is then related to L0 of the BCP features. Here λ is the effective statistical monomer length which is ∼0.56 nm in real units as an average for PS and PDMS.78L0 is then given as
in the high χN limit.29 To facilitate comparisons, the dimensions of features are normalized to L0. In principle L0 itself depends on the solvent incorporation, but this dependence can be relegated into the effective χ and N parameters and how those parameters depend on the incorporated solvent fraction Φsol.
i. Implicit model.
The effective volume fraction feff is selected such that any incorporated solvent selective to the minority component adds to this effective fraction. This assumption is valid as long as the system remains microphase-separated upon adding solvent. Here we consider a model system with a BCP with minority component A, majority component B, and selective solvents Asol and Bsol, respectively. Using the convention that the volume fraction f refers to the minority component A in the BCP, the effective fraction of the A component in a swollen film is | feff = fΦBCP + ξA,solΦsol = fSR−1 + ξA,sol(1 − SR−1) | (3) |
where ξA,sol is the fraction of the total solvent in the film that is A-selective, and ξA,sol + ξB,sol = 1.
To describe solvents that are not fully selective to either block, such as toluene and heptane in PS-PDMS (heptane is highly preferential to PDMS whereas toluene is preferential to PS but also soluble in PDMS), a “selectivity fit” using β selectivity parameters is constructed which expresses ξA,sol as a linear combination of the fractions of toluene and heptane that swell only the A-block (PDMS), i.e.
| ξA,sol = βtolθtol + βheptθhept | (4) |
where
θtol +
θhept = 1 represents the respective fractions in the liquid solvent mixture from which the vapor is produced.
βtol and
βhept are the selectivity fit factors for a given solvent mixture, and allow the experiment, in which a solvent vapor consisting of two partially selective solvents is produced from a liquid solvent mixture, to be mapped onto the model, in which the solvent vapor is treated as a combination of fully-selective solvents.
Fit parameters were found from a previous study of the swelling behavior of PS, PDMS, and PS-PDMS thin films in mixed solvent vapors.33 The fit parameters were: βhept ≅ 1 for all values of θtol,βtol ≅ 0 for θtol < 0.7, and βtol increased linearly toward a value of 0.25 as θtol increased to 1. This represents the high selectivity of heptane to the PDMS block for any solvent mixture, whereas toluene is highly selective to the PS block, but starts to enter the PDMS as the solution becomes toluene-rich. Details of these fits are found in the ESI† (S3), but we point out that the data used to generate the fits was obtained from a continuous flow SVA system in which the solvent vapor was produced by bubbling nitrogen through liquid toluene and liquid heptane and mixing the resulting vapors in different proportions. The fits may differ for a system where the vapor is produced from a liquid solvent mixture due to the non-ideality of the toluene–heptane mixture.
Using these fit parameters, the range of feff accessible for a given PS-PDMS BCP can be calculated for different solvent fractions present and swelling ratios SR, and the microdomain morphologies then determined. Whether the BCP will still be microphase-separated in the swollen state can be estimated assuming χeffN ≥ 10.5 for microphase-separation to occur.29,30 Plots of the accessible range of feff for two PS-PDMS BCPs with molecular weights 45.5 kg mol−1 and 75.5 kg mol−1 and f = 0.33 and f = 0.41, respectively, at three swelling ratios are shown in Fig. 2. At these swelling ratios feff can theoretically cover a range of ∼0.2 to 0.7, i.e. the swollen BCP thin film could form spherical, cylindrical, gyroid or lamellar structures depending on the solvent mixture used. Moreover, the range of feff increases with swelling ratio.
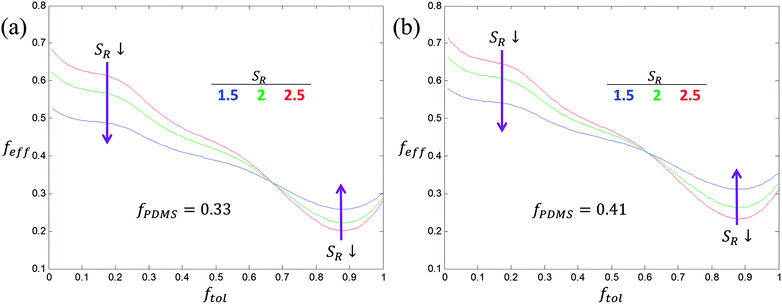 |
| Fig. 2 Plots of feff using fitted selectivity parameters for toluene and heptane solvents in PS-PDMS BCPs with (a) f = 0.33 and (b) f = 0.41 for three values of SR = 1.5, 2, and 2.5 shown in blue, green, and red, respectively. A larger range of effective fractions can be obtained at higher swelling ratios. There is a crossover point where feff = f at (a) θtol = 0.66 and (b) θtol = 0.6. | |
These calculations allow a solvent mixture to be determined which is effectively neutral to the two blocks such that feff = f. For f = 0.33 this occurs at θtol = 0.66 (2 to 1 volume ratio of toluene to heptane) and for f = 0.41 this occurs at θtol = 0.6 (3 to 2 toluene to heptane). Also, taking α= 1, χPS-PDMS = 0.14 at room temperature87 (other work gives χPS-PDMS as high as 0.27), and N = 495 and N = 847 for the two different BCPs, χeffN exceeds 10.5 for SR ≤ 6.6 and SR ≤ 11.3 for the two respective N. These rather large SR are many times greater than the experimental swelling ratios meaning these systems should not disorder upon swelling. Thus implicit simulations should be valid to model the PS-PDMS/toluene–heptane experiments.
ii. Explicit model.
In the case of explicit modelling, the SCFT framework used must be modified slightly to treat solvents as explicit species. The main alteration in the theory is the addition of a solvent partition function Qsol in addition to the single chain BCP partition function QBCP.80,81,88 Explicit modelling must be used if there is a large quantity of solvent in the system or when χN is so low that upon swelling the film could pass through the ODT. Qsol is given as | Qsol = ∫d eΩsol( ) | (5) |
where Qsol(
) is the position-dependent chemical potential field for the appropriate selective solvent. | 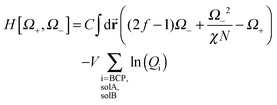 | (6) |
is the free energy Hamiltonian with the solvent partition function for a system with species A and B.
In this formalism, there are only A and B selective solvent species. In order to model the toluene and heptane system for PS-PDMS for high toluene fractions θtol > 0.7 where toluene behaves slightly selectively, the toluene fraction in the model needs to be adjusted to account for this selectivity. In other words, in comparing the explicit fractions of selective solvents in simulations with the experimental fractions of solvents, the region of pure Bsol is inaccessible experimentally in the PS-PDMS toluene and heptane system since pure toluene will swell both blocks (i.e. a solvent purely selective to PS would be needed experimentally to reach this model region). This limitation just means that some of the lower feff are inaccessible, but could be reached using a solvent with higher preference for PS. This also explains why feff increases for high θtol in Fig. 2 rather than continuing to decrease.
In order to calculate normalized densities of A and B, the following equations are evaluated. ϕA is the local minority BCP density, ϕB is the local majority BCP density, ϕsolA is the local density of Asol, ϕB is the density of Bsol, ΦBCP is the total fraction of BCP in the system, fsolA is the total fraction of Asol in the system, fsolB is the total fraction of Bsol in the system, Φsol = fsolA + fsolB, and q and q† are the forward and reverse propagators used to calculate the single chain partition function QBCP.
|  | (7) |
|  | (8) |
| 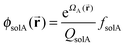 | (9) |
| 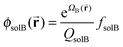 | (10) |
In these equations
ΩA and
ΩB are defined in terms of
Ω+ and
Ω− as
| 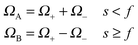 | (11) |
Upon adding these equations to the SCFT framework, explicit modelling can be performed.
Results and discussion
A. Experimental results
Experimental morphology results for a thin film of 75.5 kg mol−1f = 0.41 are shown in Fig. 3 under a variety of SVA conditions.35 Four morphologies were observed with SR ∼ 1.5–2.5, monolayer spheres, monolayer cylinders, monolayer perforated lamellae, and monolayer in-plane lamellae, for different solvent mixtures. A range of feff corresponding to the different experimental solvent ratios is given, calculated from the fitted parameters for βtol (which varies between 0 and 0.25 depending on the solvent mixture) and βhept ≅ 1. This range is given for the cases βtol = 0 and βtol = 0.25. In each of the four different samples in Fig. 3, and in additional cases presented in Table 1, there is a general agreement between the expected morphology for the calculated feff and the observed morphology.
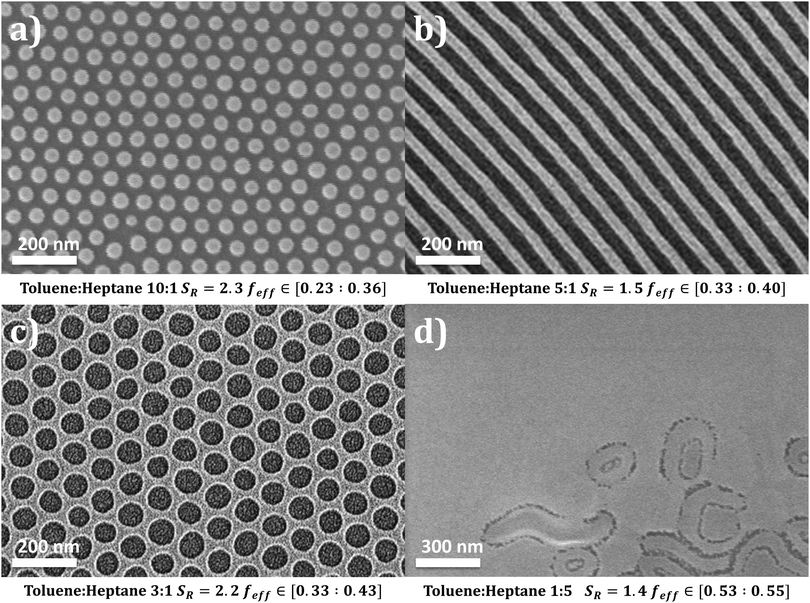 |
| Fig. 3 Scanning electron microscopy images from SVA thin films of a 75.5 kg mol−1 PS-PDMS BCP with bulk volume fraction f = 0.415 changing the ratio of toluene : heptane and SR. The feff ranges given are calculated based on the range of selectivity of toluene. Lighter regions are PDMS. (a) Spheres. (b) Cylinders. (c) Perforated lamellae. (d) In-plane lamellae. | |
Table 1 Theoretical feff ranges using different assumptions about preferentiality of toluene in swelling PDMS domains for different experimental SVA conditions with the corresponding experimentally observed morphologies
Toluene to heptane ratio |
θ
tol
|
θ
hept
|
S
R
|
f
eff range |
Observed morphology |
1 : 0 |
1.0 |
0.0 |
2.5 |
[0.16 : 0.31] |
Spheres |
10 : 1 |
0.91 |
0.09 |
2.3 |
[0.23 : 0.36] |
Spheres |
5 : 1 |
0.83 |
0.17 |
1.5 |
[0.33 : 0.40] |
Cylinders |
4 : 1 |
0.80 |
0.20 |
2.0 |
[0.31 : 0.41] |
Cylinders + perforated lamellae |
3 : 1 |
0.75 |
0.25 |
2.2 |
[0.33 : 0.43] |
Perforated lamellae |
2.5 : 1 |
0.71 |
0.29 |
1.5 |
[0.37 : 0.43] |
Cylinders + lamellae |
1.5 : 1 |
0.60 |
0.40 |
1.3 |
[0.41 : 0.41] |
Perforated lamellae + lamellae |
1 : 5 |
0.17 |
0.83 |
1.4 |
[0.53 : 0.55] |
Lamellae |
B. Simulation results
Here we detail the results from simulation studies of both implicit and explicit SVA conditions. Further considerations on how to compare these results with experiments are given in the ESI† (S4).
i. Implicit simulation results.
3D implicit SCFT simulation were performed using parameters that correspond to a 75.5 kg mol−1f = 0.41 PS-PDMS BCP solvent annealed in various mixtures of toluene and heptane.35 Bulk simulations without solvent were performed initially to determine L0 for the BCP. L0 was defined as the spacing of a set of metastable hexagonally packed cylinders. This length scale was chosen since the polymer in the bulk is an equilibrium gyroid phase but gyroids do not form in thin film simulations. L0 would be related to the gyroid d211 spacing such that
.89 Details of the bulk simulations and the determination of L0 are discussed in the ESI† (S5).
To examine the effects of various solvent ratios on this system, four different effective fractions were chosen and simulations performed over a range of thicknesses. Based on the fitting factors β described above, the four effective volume fractions feff = 0.25, 0.35, 0.41 and 0.45 correspond to solvent ratios of toluene
:
heptane that produce morphologies spanning the range from spheres to cylinders to perforated lamellae to lamellae as shown in Table 1.
Periodic boundary conditions were applied in-plane with incommensurate unit cell dimensions of 1.85L0 by 1.62L0 to avoid biasing the in-plane morphologies. The use of larger simulation cells could also be performed but doing so is more computationally expensive. An effective (χN)eff = 18 was chosen as discussed in the ESI† (S5) to best model the approximate value of χ for the swelling conditions examined, though future studies should try to capture χeff as a function of feff and SR explicitly.
To reduce computation time the two surfaces were both chosen to be preferential to the majority block B such that monolayers of spheres, cylinders, perforated lamellae, or lamellae would form without a minority wetting layer, when the film thickness was commensurate with the monolayer thickness. The morphologies are equivalent to those formed for minority-preferential surfaces for films thicker by L0 (i.e. twice each wetting layer thickness of L0/2). The film thickness was varied from 0.5L0 up to 1.5L0.
Free energy curves with the monolayer morphology highlighted are shown in Fig. 4. The energy has a local minimum when a monolayer of microdomains formed. For the four feff cases studied, spheres were the monolayer equilibrium morphology for feff = 0.25, cylinders for feff = 0.35, perforated lamellae for feff = 0.41, and in-plane lamellae for feff = 0.45. Other transitional morphologies were observed at incommensurate thicknesses, and double layer morphologies formed at higher thicknesses. More details are presented in the ESI† (S6). The overall result is that in the implicit model, where a varying solvent ratio is modeled by changing the value of feff, we predict a range of morphologies which correspond well to those obtained experimentally (spheres, cylinders, perforated lamellae, lamellae at toluene
:
heptane = 10
:
1, 5
:
1, 3
:
1 and 1
:
5 respectively, Table 1). Additionally, these results are consistent with previous studies of confined thin film morphologies with similar conditions, and a direct comparison of the phase diagram is shown in the ESI† (S7).90
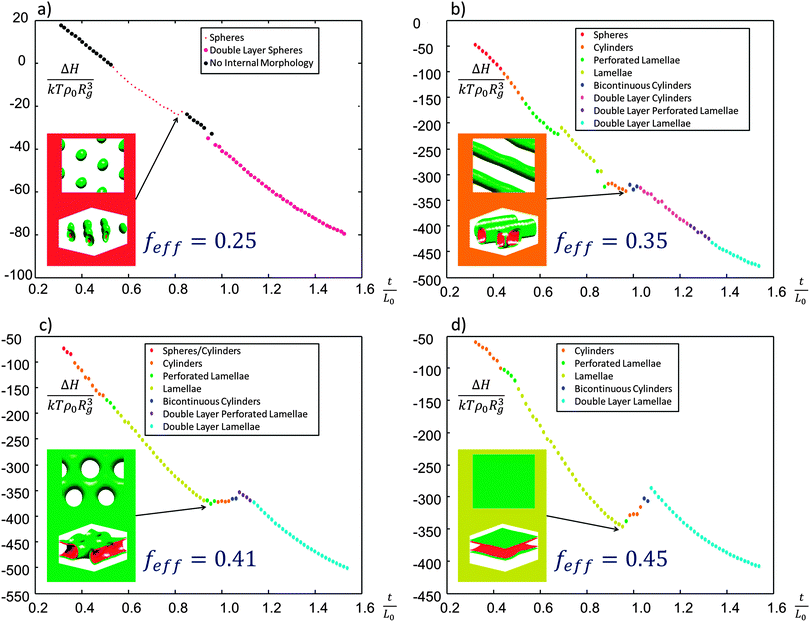 |
| Fig. 4 Plots of the normalized free energy difference ΔH compared to a disordered state for implicit SVA simulations with different feff as a function of normalized film thickness t/L0. Inset in each panel are top-down and side-angle views of the monolayer lowest energy structure with green ϕA = 0.5 isosurfaces showing the boundary layer between blocks and the red regions being A rich regions. (a) feff = 0.25, forming spheres as the lowest energy monolayer structure. (b) feff = 0.35, cylinders. (c) feff = 0.41, perforated lamellae. (d) feff = 0.45, in-plane lamellae. | |
ii. Explicit simulation results.
Explicit SVA simulations were performed in 2D with f = 0.4 and a fixed χN = 28 with different amounts of solvents with volume fractions fsolA, fsolB. Simulation cells of size 4L0 by 4L0 were chosen to be large enough to examine bulk behavior and the fraction of Asol and Bsol was varied from 0.00 to 0.60 such that fsolA + fsolB ≤ 0.60. The total fraction of BCP is evaluated using the incompressibility constraint that ΦBCP + fsolA + fsolB = 1. Additionally the effective fraction of A species is simply feff = fΦBCP + fsolA where fsolA = ξA,solΦsol and fsolB = ξB,solΦsol. Additional 2D simulations over a range of f, χN, fsolA, and fsolB were also performed to compare the relative phase behavior of the explicit model with the standard BCP phase space. These supplemental simulations and discussion of the results can be found in the ESI† (S8). The main conclusion from those simulations is that χeff(Φsol) depends on the ratio of fsolA to fsolB, total solvent fraction Φsol, and the original value of f. Quantifying this exact dependence is an immense task, so two extreme cases were examined in 1D by examining how the L0 of 1D density profiles varied with Φsol for an f = 0.5 copolymer for the cases of only A selective solvent and equal amounts of A and B selective solvents. These results and derived functional dependencies of χeff on Φsol are discussed in the ESI† (S9).
As shown in Fig. 5, various phase regions were observed in the simulations depending on the values of fsolA and fsolB. The 2D bulk morphology with no solvent includes 2D circles (corresponding to through-plane cylinders) and line structures (lamellae) of A. As more fsolA is added to the system, the line structures become more dominant and eventually transitions to a perforated A network surrounding circles (or through-plane cylinders of B) and lines of B. As fsolB increases, the morphology transitions toward hexagonally close packed circular structures and eventually solvated A-rich micelles. As both A and B solvent fractions are increased, order is eventually lost.
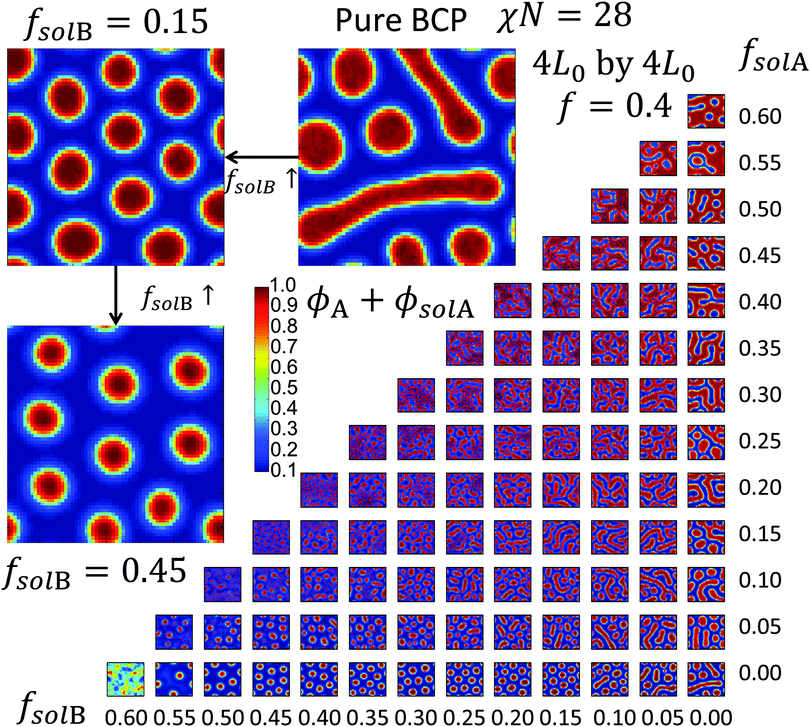 |
| Fig. 5 Minority A species density field maps for 2D simulations of a BCP with f = 0.4 and χN = 28 and various values of explicitly modelled A and B selective solvents. Total A species density is plotted. Inset: zoomed images of pure BCP, fsolB = 0.15, and fsolB = 0.45 density field maps show the effect of increasing solvent density. | |
From these results and those in the ESI,† there is a large range of fsolA and fsolB, up to around Φsol = 0.50 for ratios of fsolA to fsolB close to 1 where microphase-separated morphologies are retained without macrophase separation of the solvent from the BCP, with the maximum Φsol decreasing as the solvent quality approaches pure A or B depending on the exact value of f. The fact that the system can retain ordered structures at such high total solvent fractions gives credence to the ability of implicit simulations to model SVA up to SR values around 2. A comparison of the density profiles of the two models in 1D is shown in the ESI† (S10) for a case where macrophase segregation did not occur showing these density profiles are qualitatively the same when comparing the total A and B component densities of the explicit model with the A and B densities in the implicit model. However, there are several cases where disorder enters the system or macrophase separation occurs from simply adding more solvent, marking the limitation of implicit simulations. These 2D simulations provide a sense of how the morphology varies with solvent fraction; it is expected in 3D the phase boundaries would be shifted.
Quasi-static simulations were performed in 3D to examine the effect of quenching on the sample morphology. A BCP containing no explicit solvent was first equilibrated to a local saddle point solution. Next, the total unit cell thickness was increased incrementally to a larger swelling ratio by adding solvent, then collapsed back to the original film thickness by removing solvent. Finally the system was re-equilibrated. These simulations yield some information about the structural evolution during swelling and deswelling, but still the simulations only look at local equilibrium states and thus do not determine the kinetic pathway between states since steepest descent methods are still used to relax the fields.
Results using two separate surface wetting cases are shown in Fig. 6. In one case the top and bottom surface energy conditions are both preferential to PDMS (block A), and in the other case only the top surface is A-preferential while the bottom surface is B-preferential. In all these cases the morphologies that formed were in-plane morphologies. The solvent was incorporated such that fsolA = fsolB and the main variable changed was f reflecting the initial bulk BCP volume fraction. These conditions correspond roughly to neutral solvent, and probe the effect of rapid quenching, unlike the 2D simulations.
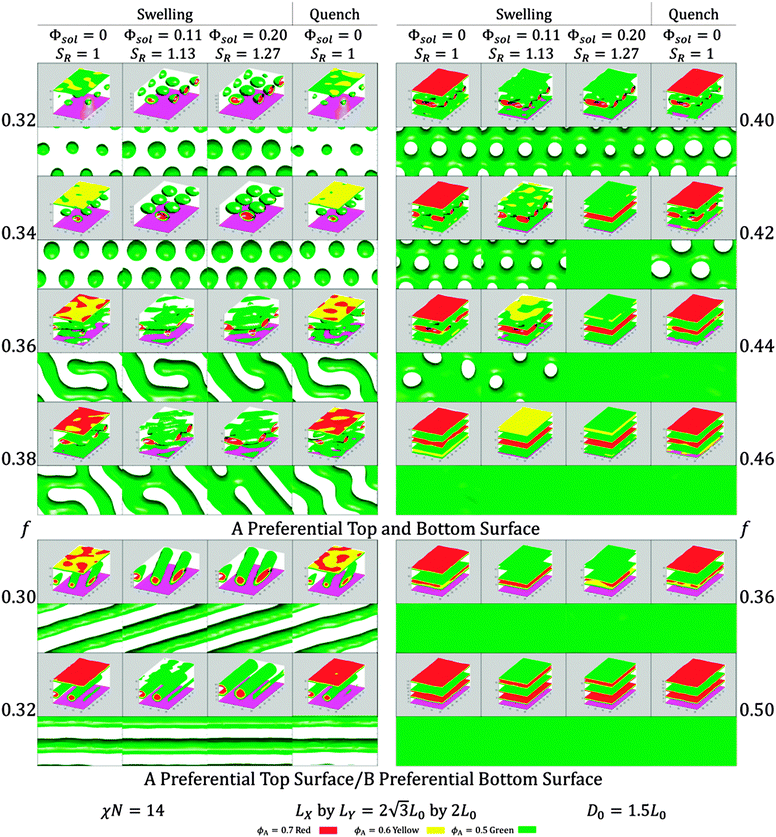 |
| Fig. 6 Quasi-static 3D explicit SVA simulations using different f values. χN = 14 and the unit cells were commensurate with close-packed features. The initial film thickness was 1.5L0. SR up to 1.27 are shown. Upper panels: top and bottom A-preferential conditions. As f increases hexagonally close packed spheres, cylinders, perforated lamellae, and in-plane lamellae are all observed. Only in the case of perforated lamellae does the morphology change appreciably upon quenching, likely because of metastability of the morphology at the simulated f. Alternatively, this observed behavior may simply be due to the first order phase transition between the equilibrium phases at different solvent fraction conditions. Bottom panels: top A and bottom B preferential conditions. Only cylinders and lamellae were observed for the f examined here, with perforated lamellae being suppressed. | |
As the BCP swelled the A domains increased in diameter but their morphology remained the same, and they shrank upon quenching. For the most part, quenching did not change the swollen morphology but in a few cases of perforated lamellae the swelling/quenching sequence led to a transition to a new morphology. These cases where a phase transition occurred represent either a metastable phase being encountered or a first order phase transition between phases due to the change in incorporated solvent fraction. A more comprehensive investigation would examine more thicknesses and solvent ratios, as well as changing χ and adjusting the surface preferentiality with increasing solvent fraction, but the results here indicate that explicit solvent incorporation is a good first step to model morphological changes. Additional quasi-static explicit SVA simulations are detailed in the ESI† (S11).
Conclusions
Both implicit and explicit SCFT simulations provide insight into the physics of SVA. By using effective parameters based on the amount of solvent incorporation, and treating the system as a two species system, predictions of the regimes where different thin film morphologies can be obtained becomes possible. The modelling was compared to results from PS-PDMS annealed in toluene and heptane vapors, in which the measured selectivity of the solvents to the blocks was used to derive a selectivity fit allowing the system to be mapped onto an idealized model with two fully-selective solvents. Both modelling and experiment show that spherical, cylindrical, perforated lamellar, and lamellar morphologies are obtained by varying the solvent ratio. The simulations and experiments compared here show the potential of SVA to access a wide array of morphologies simply by controlling selective solvent fractions. Future advances will allow the prediction of morphologies formed under a variety of SVA conditions, and the prediction of dynamic annealing paths to understand systems in which the ODT is reached upon swelling.
List of abbreviations, variables and symbols
Abbreviations
SVA | Solvent vapor annealing |
BCP | Block copolymer |
SCFT | Self-consistent field theory |
GISAXS | Grazing incidence small-angle X-ray scattering |
PS | Polystyrene |
PDMS | Polydimethylsiloxane |
ODT | Order–disorder transition |
Variables and symbols
χ
| Flory–Huggins interaction parameter “chi” |
f
| BCP minority component (PDMS in this study) volume fraction |
N
| Degree of polymerization |
D
0
| Initial film thickness |
D
| Swollen film thickness |
D
f
| Final film thickness after quenching |
L
0
| Natural BCP microdomain periodicity |
S
R
| Swelling ratio of swollen film thickness to initial film thickness |
p
| Number of species in a system |
i
| Species index |
χ
eff
| Effective χ parameter accounting for solvent incorporation |
R
g
| Radius of gyration of BCP |
Φ
BCP
| Fraction of swollen thin film that is BCP |
Φ
sol
| Volume fraction of solvent in swollen film |
α
| Exponent constant relating SR to χeff |
N
s
| Number of statistical chain segments in SCFT model |
λ
| Effective statistical monomer length (∼2 chemical repeat monomers) |
f
eff
| Volume fraction of minority component (PDMS) plus PDMS/minority component selective solvent present in a swollen film |
A | Minority component in implicit model (corresponds to PDMS and toluene & heptane in PDMS) |
B | Majority component in implicit model (corresponds to PS and toluene & heptane in PS) |
Asol | Solvent selective to A component |
Bsol | Solvent selective to B component |
ξ
A,sol
| Fraction of solvent in film that is Asol |
ξ
B,sol
| Fraction of solvent in film that is Bsol |
β
tol
| Selectivity fit parameter for toluene |
β
hept
| Selectivity fit parameter for toluene |
θ
tol
| Fraction of solvent in film that is toluene |
θ
hept
| Fraction of solvent in film that is heptane |
χ
PS-PDMS
| Bulk Flory–Huggins interaction parameter between PS & PDMS |
Q
sol
| Partition function of solvent in SCFT model (QsolA and QsolB) |
Q
BCP
| Single chain BCP partition function in SCFT model |
| Coordinate vector in SCFT model. Corresponds to real space grid point locations (x,y,z) |
H
| Hamiltonian in SCFT model that corresponds to the normalized free energy when evaluated with an SCFT chemical potential field solution |
Ω
sol
| Chemical potential field of solvent in SCFT model |
Ω
+
| Pressure-like chemical potential field in SCFT model |
Ω
−
| Exchange interaction chemical potential field in SCFT model |
Ω
A
| Chemical potential field for A component in SCFT model |
Ω
B
| Chemical potential field for B component in SCFT model |
C
| Proportionality constant for H in SCFT model that is a function of the polymer density, Rg, and N |
V
| Volume of unit cell in SCFT calculations |
ϕ
A
| Normalized density of A polymer in SCFT model |
ϕ
B
| Normalized density of B polymer in SCFT model |
s
| Chain coordinate position along the BCP chain (range of 0 to 1 where 0 is the chain head and 1 the chain tail) |
q & q† | Forward and reverse partition function propagators, respectively |
μ
| Total chemical potential field at a given spatial location |
ϕ
solA
| Normalized density of A selective solvent in explicit SCFT model |
ϕ
solB
| Normalized density of B selective solvent in explicit SCFT model |
f
solA
| Fraction of unit cell volume that is A selective solvent in explicit SCFT model |
f
solB
| Fraction of unit cell volume that is B selective solvent in explicit SCFT model |
t
| Film thickness in implicit SCFT simulations (corresponds to D in experiment) |
Acknowledgements
We thank Kevin W. Gotrik for his previous experimental contributions and insights that led to the development of many model details. We thank Professor Apostolos Avgeropoulos and his research group at the University of Ioannina, Greece for synthesizing the PS-PDMS polymers used in the experimental comparison of the simulations. We gratefully acknowledge financial support from the National Science Foundation award CMMI 1246740, Taiwan Semiconductor Manufacturing Company, Tokyo Electron Limited, and the Semiconductor Research Corporation.
References
- A. W. Harant and C. N. Bowman, J. Vac. Sci. Technol., B: Microelectron. Nanometer Struct., 2005, 23, 1615–1621 CrossRef CAS.
- Y. Xuan, J. Peng, L. Cui, H. Wang, B. Li and Y. Han, Macromolecules, 2004, 37, 7301–7307 CrossRef CAS.
- S. Kim, R. Briber and A. Karim, MRS Proc., 2006, 961, 0961 Search PubMed.
- M. Luo and T. H. Epps, Macromolecules, 2013, 46, 7567–7579 CrossRef CAS.
- C. Sinturel, M. Vayer, M. Morris and M. A. Hillmyer, Macromolecules, 2013, 46, 5399–5415 CrossRef CAS.
- K. A. Cavicchi and T. P. Russell, Macromolecules, 2007, 40, 1181–1186 CrossRef CAS.
- J. N. L. Albert, T. D. Bogart, R. L. Lewis, K. L. Beers, M. J. Fasolka, J. B. Hutchison, B. D. Vogt and T. H. Epps, Nano Lett., 2011, 11, 1351–1357 CrossRef CAS PubMed.
- Y. Tada, H. Yoshida, Y. Ishida, T. Hirai, J. K. Bosworth, E. Dobisz, R. Ruiz, M. Takenaka, T. Hayakawa and H. Hasegawa, Macromolecules, 2012, 45, 292–304 CrossRef CAS.
- S. H. Kim, M. J. Misner and T. P. Russell, Adv. Mater., 2004, 16, 2119–2123 CrossRef CAS PubMed.
- J. Peng, D. H. Kim, W. Knoll, Y. Xuan, B. Li and Y. Han, J. Chem. Phys., 2006, 125, 64702 CrossRef PubMed.
- A. Stenbock-Fermor and A. Knoll, Macromolecules, 2014, 47, 3059–3067 CrossRef CAS.
- J. D. Cushen, L. Wan, G. Pandav, I. Mitra, G. E. Stein, V. Ganesan, R. Ruiz, C. G. Willson and C. J. Ellison, J. Polym. Sci., Part B: Polym. Phys., 2014, 52, 36–45 CrossRef CAS PubMed.
- C.-J. Chu, P.-Y. Chung, M.-H. Chi, Y.-H. Kao and J.-T. Chen, Macromol. Rapid Commun., 2014, 35, 1598–1605 CrossRef CAS PubMed.
- S. W. Hong, D. L. Voronov, D. H. Lee, A. Hexemer, H. A. Padmore, T. Xu and T. P. Russell, Adv. Mater., 2012, 24, 4278–4283 CrossRef CAS PubMed.
- E. Kim, W. Kim, K. H. Lee, C. A. Ross and J. G. Son, Adv. Funct. Mater., 2014, 24, 6981–6988 CrossRef CAS PubMed.
- J. M. Kim, Y. Kim, W. I. Park, Y. H. Hur, J. W. Jeong, D. M. Sim, K. M. Baek, J. H. Lee, M.-J. Kim and Y. S. Jung, Adv. Funct. Mater., 2015, 25, 306–315 CrossRef CAS PubMed.
- P. Mokarian-Tabari, C. Cummins, S. Rasappa, C. Simao, C. M. Sotomayor Torres, J. D. Holmes and M. A. Morris, Langmuir, 2014, 30, 10728–10739 CrossRef CAS PubMed.
- J. Kao, K. Thorkelsson, P. Bai, Z. Zhang, C. Sun and T. Xu, Nat. Commun., 2014, 5, 4053 CAS.
- M. P. Stoykovich and P. F. Nealey, Mater. Today, 2006, 9, 20–29 CrossRef CAS.
- S. O. Kim, H. H. Solak, M. P. Stoykovich, N. J. Ferrier, J. J. de Pablo and P. F. Nealey, Nature, 2003, 424, 411–414 CrossRef CAS PubMed.
- R. Ruiz, H. Kang, F. A. Detcheverry, E. Dobisz, D. S. Kercher, T. R. Albrecht, J. J. de Pablo and P. F. Nealey, Science, 2008, 321, 936–939 CrossRef CAS PubMed.
- S. Park, D. H. Lee, J. Xu, B. Kim, S. W. Hong, U. Jeong, T. Xu and T. P. Russell, Science, 2009, 323, 1030–1033 CrossRef CAS PubMed.
- T. Lodge and M. Dalvi, Phys. Rev. Lett., 1995, 75, 657–660 CrossRef CAS.
- Y. S. Jung and C. A. Ross, Adv. Mater., 2009, 21, 2540–2545 CrossRef CAS PubMed.
- M. Y. Paik, J. K. Bosworth, D.-M. Smilges, E. L. Schwartz, X. Andre and C. K. Ober, Macromolecules, 2010, 43, 4253–4260 CrossRef CAS PubMed.
- Z. Di, D. Posselt, D.-M. Smilgies and C. M. Papadakis, Macromolecules, 2010, 43, 418–427 CrossRef CAS PubMed.
- J. Vogelsang, J. Brazard, T. Adachi, J. C. Bolinger and P. F. Barbara, Angew. Chem., Int. Ed., 2011, 50, 2257–2261 CrossRef CAS PubMed.
- W. A. Phillip, M. A. Hillmyer and E. L. Cussler, Macromolecules, 2010, 43, 7763–7770 CrossRef CAS.
- F. S. Bates and G. H. Fredrickson, Annu. Rev. Phys. Chem., 1990, 41, 525–557 CrossRef CAS PubMed.
- L. Leibler, Macromolecules, 1980, 13, 1602–1617 CrossRef CAS.
- A. Knoll, A. Horvat, K. S. Lyakhova, G. Krausch, G. J. A. Sevink, A. V Zvelindovsky and R. Magerle, Phys. Rev. Lett., 2002, 89, 035501 CrossRef CAS.
- Y. S. Jung and C. A. Ross, Nano Lett., 2007, 7, 2046–2050 CrossRef CAS PubMed.
- K. W. Gotrik, A. F. Hannon, J. G. Son, B. Keller, A. Alexander-Katz and C. A. Ross, ACS Nano, 2012, 6, 8052–8059 CrossRef CAS PubMed.
- K. W. Gotrik and C. A. Ross, Nano Lett., 2013, 13, 5117–5122 CrossRef CAS PubMed.
- W. Bai, A. F. Hannon, K. W. Gotrik, H. K. Choi, K. Aissou, G. Liontos, K. Ntetsikas, A. Alexander-Katz, A. Avgeropoulos and C. A. Ross, Macromolecules, 2014, 47, 6000–6008 CrossRef CAS.
- M. van Dijk and R. van den Berg, Macromolecules, 1995, 28, 6773–6778 CrossRef CAS.
- I. Hamley, S. Connell and S. Collins, Macromolecules, 2004, 37, 5337–5351 CrossRef CAS.
- S. Kim, M. Misner and T. Xu, Adv. Mater., 2004, 16, 226–231 CrossRef CAS PubMed.
- M. Park, Science, 1997, 276, 1401–1404 CrossRef CAS.
- D. F. Sunday, M. R. Hammond, W.-L. Wu, R. J. Kline and G. E. Stein, J. Micro/Nanolithogr., MEMS, MOEMS, 2013, 12, 031103 CrossRef PubMed.
- D. Sunday, M. Hammond, C. Wang, W.-L. Wu, D. M. Delongchamp, M. Tjio, J. Y. Cheng, J. W. Pitera and R. J. Kline, ACS Nano, 2014, 8, 8426–8437 CrossRef CAS PubMed.
- X. Gu, I. Gunkel, A. Hexemer, W. Gu and T. P. Russell, Adv. Mater., 2014, 26, 273–281 CrossRef CAS PubMed.
- X. Gu, I. Gunkel, A. Hexemer and T. P. Russell, Colloid Polym. Sci., 2014, 292, 1795–1802 CAS.
- J. Zhang, D. Posselt and D. Smilgies, Macromolecules, 2014, 47, 5711–5718 CrossRef CAS PubMed.
- A. Baruth, M. Seo, C. H. Lin, K. Walster, A. Shankar, M. A. Hillmyer and C. Leighton, ACS Appl. Mater. Interfaces, 2014, 6, 13770–13781 CAS.
- C. Sinturel and D. Grosso, ACS Appl. Mater. Interfaces, 2014, 6, 12146–12152 CAS.
- J. G. Son, J.-B. Chang, K. K. Berggren and C. A. Ross, Nano Lett., 2011, 11, 5079–5084 CrossRef CAS PubMed.
- J. G. Son, A. F. Hannon, K. W. Gotrik, A. Alexander-Katz and C. A. Ross, Adv. Mater., 2011, 23, 634–639 CrossRef CAS PubMed.
- J.-B. Chang, J. G. Son, A. F. Hannon, A. Alexander-Katz, C. A. Ross and K. K. Berggren, ACS Nano, 2012, 6, 2071–2077 CrossRef CAS PubMed.
- K. G. A. Tavakkoli, A. F. Hannon, K. W. Gotrik, A. Alexander-Katz, C. A. Ross and K. K. Berggren, Adv. Mater., 2012, 24, 4249–4254 CrossRef PubMed.
- K. G. A. Tavakkoli, K. W. Gotrik, A. F. Hannon, A. Alexander-Katz, C. A. Ross and K. K. Berggren, Science, 2012, 336, 1294–1298 CrossRef CAS PubMed.
- K. G. A. Tavakkoli, S. M. Nicaise, A. F. Hannon, K. W. Gotrik, A. Alexander-Katz, C. A. Ross and K. K. Berggren, Small, 2013, 10, 493–499 CrossRef PubMed.
- P. Sun, Y. Yin, B. Li, T. Chen, Q. Jin, D. Ding and A.-C. Shi, J. Chem. Phys., 2005, 122, 204905 CrossRef PubMed.
- Y. Yin, P. Sun, B. Li, T. Chen, Q. Jin, D. Ding and A.-C. Shi, Macromolecules, 2007, 40, 5161–5170 CrossRef CAS.
- R. Jiang, B. Li, Z. Wang, Y. Yin and A.-C. Shi, Macromolecules, 2012, 45, 4920–4931 CrossRef CAS.
- J. Xu, Y. Yin, Z. Wang, R. Jiang, B. Li and A.-C. Shi, J. Chem. Phys., 2013, 138, 114905 CrossRef PubMed.
- F. Léonforte and M. Müller, Macromolecules, 2015, 48, 213–228 CrossRef.
- S. P. Paradiso, K. T. Delaney, C. J. García-Cervera, H. D. Ceniceros and G. H. Fredrickson, ACS Macro Lett., 2014, 3, 16–20 CrossRef CAS.
- S.-M. Hur, G. S. Khaira, A. Ram, M. Mu, P. F. Nealey and J. J. de Pablo, ACS Macro Lett., 2015, 4, 11–15 CrossRef CAS.
- M. Müller and J. J. de Pablo, Annu. Rev. Mater. Res., 2013, 43, 1–34 CrossRef PubMed.
- R. Guo, H. Huang, Y. Chen, Y. Gong, B. Du and T. He, Macromolecules, 2008, 41, 890–900 CrossRef CAS.
- J. W. Jeong, W. I. Park, M. Kim, C. A. Ross and Y. S. Jung, Nano Lett., 2011, 11, 4095–4101 CrossRef CAS PubMed.
- T. N. Zwietering, Chem. Eng. Sci., 1959, 11, 1–15 CrossRef CAS.
- A. Cholette and L. Cloutier, Can. J. Chem. Eng., 1959, 37, 105–112 CrossRef CAS PubMed.
- A. Horvat, K. S. Lyakhova, G. J. A. Sevink, A. V Zvelindovsky and R. Magerle, J. Chem. Phys., 2004, 120, 1117–1126 CrossRef CAS PubMed.
- J. N. L. Albert, W.-S. Young, R. L. Lewis, T. D. Bogart, J. R. Smith and T. H. Epps, ACS Nano, 2012, 6, 459–466 CrossRef CAS PubMed.
- J. Bang, B. J. Kim, G. E. Stein, T. P. Russell, X. Li, J. Wang, E. J. Kramer and C. J. Hawker, Macromolecules, 2007, 40, 7019–7025 CrossRef CAS.
- J. K. Bosworth, M. Y. Paik, R. Ruiz, E. L. Schwartz, J. Q. Huang, A. W. Ko, D.-M. Smilgies, C. T. Black and C. K. Ober, ACS Nano, 2008, 2, 1396–1402 CrossRef CAS PubMed.
- G. Cui, M. Fujikawa, S. Nagano, M. Sano, H. Takase, T. Miyazaki, S. Sakurai and K. Yamamoto, Polymer, 2014, 55, 1601–1608 CrossRef CAS PubMed.
- J. P. Singer, K. W. Gotrik, J.-H. Lee, S. E. Kooi, C. A. Ross and E. L. Thomas, Polymer, 2014, 55, 1875–1882 CrossRef CAS PubMed.
- K. Mori, H. Hasegawa and T. Hashimoto, Polymer, 1990, 31, 2368–2376 CrossRef CAS.
-
C. M. Hansen, Hansen Solubility Parameters, A User's Handbook, CRC Press, Boca Raton, FL, 2000 Search PubMed.
-
P. Bahadur and N. V. Sastry, Principles of Polymer Science, Alpha Science International, Ltd, Oxford, UK, 2005 Search PubMed.
- H. Elbs and G. Krausch, Polymer, 2004, 45, 7935–7942 CrossRef CAS PubMed.
- G. Coulon, B. Collin, D. Ausserre, D. Chatenay and T. P. Russell, J. Phys., 1990, 51, 2801–2811 CAS.
- J. N. L. Albert and T. H. Epps III, Mater. Today, 2010, 13, 24–33 CrossRef CAS.
- M. Fasolka and A. Mayes, Annu. Rev. Mater. Res., 2001, 31, 323–355 CrossRef CAS.
- R. A. Mickiewicz, J. K. W. Yang, A. F. Hannon, Y. Jung, A. Alexander-Katz, K. K. Berggren and C. A. Ross, Macromolecules, 2010, 43, 8290–8295 CrossRef CAS.
- A. Alexander-Katz, A. G. Moreira and G. H. Fredrickson, J. Chem. Phys., 2003, 118, 9030–9036 CrossRef CAS PubMed.
-
G. Fredrickson, The Equilibrium Theory of Inhomogeneous Polymers, Oxford University Press, Oxford, New York, 2005 Search PubMed.
- G. H. Fredrickson, V. Ganesan and F. Drolet, Macromolecules, 2002, 35, 16–39 CrossRef CAS.
- E. Helfand and Y. Tagami, J. Chem. Phys., 1972, 56, 3592–3601 CrossRef CAS PubMed.
- T. Hashimoto, M. Shibayama and K. Hiromichi, Macromolecules, 1983, 16, 1093–1101 CrossRef CAS.
- M. Müller and F. Schmid, Adv. Polym. Sci., 2005, 185, 1–58 CrossRef.
- T. P. Lodge, K. J. Hanley, B. Pudil and V. Alahapperuma, Macromolecules, 2003, 36, 816–822 CrossRef CAS.
- C. Lai, W. B. Russel and R. A. Register, Macromolecules, 2002, 35, 4044–4049 CrossRef CAS.
- J. Kennemur, L. Yao, F. Bates and M. Hillmyer, Macromolecules, 2014, 47, 1411–1418 CrossRef CAS.
- A. Alexander-Katz and G. H. Fredrickson, Macromolecules, 2007, 40, 4075–4087 CrossRef CAS.
- N. Politakos, E. Ntoukas, A. Avgeropoulos, V. Krikorian, B. D. Pate, E. L. Thomas and R. M. Hill, J. Polym. Sci., Part B: Polym. Phys., 2009, 47, 2419–2427 CrossRef CAS PubMed.
- W. Li, M. Liu, F. Qiu and A.-C. Shi, J. Phys. Chem. B, 2013, 117, 5280–5288 CrossRef CAS PubMed.
Footnotes |
† Electronic supplementary information (ESI) available: Experimental details, SCFT modelling details, effective fraction feff fit details, explicit and implicit model comparison, and additional simulation results. See DOI: 10.1039/c5sm00324e |
‡ Current address: Materials Science and Engineering Division, National Institute of Standards and Technology, 100 Bureau Drive, Gaithersburg, MD 20899, USA. |
|
This journal is © The Royal Society of Chemistry 2015 |
Click here to see how this site uses Cookies. View our privacy policy here.