DOI:
10.1039/C5RA19686H
(Paper)
RSC Adv., 2015,
5, 96918-96926
Electrochemical degradation of RB19 dye using low-frequency alternating current: effect of a square wave
Received
23rd September 2015
, Accepted 17th October 2015
First published on 20th October 2015
Abstract
This study mainly aims to investigate the effects of alternating current (AC) on Remazol Brilliant Blue R (RB19) dye removal from aqueous solutions by an electrochemical (EC) process. The effects of operating conditions on RB19 removal were investigated; the conditions include the AC frequency, the magnitude of a waveform in Vpp (AMPL) accompanied with a constant voltage that is added to an AC source (OFST), the supporting electrolyte (type and concentration), and the initial dye concentration. Moreover, the effects of variation in electrical conductivity, oxidation–reduction potential, and pH on the efficacy of the process were evaluated. Results showed that the highest RB19 removal efficiency with low electrode weight loss was obtained at AMPL and OFST of 8 Vpp and 0.2 V, respectively. Results of our kinetic study showed that the addition of NaCl as a supporting electrolyte has an enhancing effect on the rate constant, possibly because of an increase in the concentration of active oxidant species such as Cl2/OCl− in the electrolyte. A morphology study on the electrode surface showed that electrodes dissolved uniformly during the EC process. The loss on ignition (LOI) was determined to be 43.25% by X-ray fluorescence (XRF) analysis. The energy consumption and operating costs for RB19 removal using a square wave AC were evaluated. The results indicated that the use of a square wave AC is a promising wastewater treatment technique.
1. Introduction
Over the past 10 years, electrochemical (EC) processes have been most widely accepted for the removal of wastewater pollution.1,2 EC process subsets, which are used for removing dye from aqueous solutions, include electrocoagulation, EC reduction, EC oxidation, indirect electro-oxidation with powerful oxidants (electro-oxidation with active chlorine, electro-Fenton), and photo-supported EC methods (photoelectro-Fenton, photoelectrocatalysis).3,4 Because of the rather large capital investment and high cost of electricity associated with the development, practical application of EC techniques in water and wastewater treatment had been hindered worldwide. Drinking water and wastewater effluent standards’ promotion and establishment of strict environmental legislation resulted in renewed importance and development of EC techniques, especially for the past two decades.2,5 Today, because of extensive research, this technology has reached a level of development that is not only competitive with other technologies in terms of cost efficiency, but is also much more efficient and more competitive in terms of cost.2 In addition, sometimes in the case of inorganic or organic pollutants, the EC technique is an essential and crucial step in wastewater treatment.6 Frequently, direct current (DC) is used in an EC process for treating dye wastewater at relatively low voltages and relatively high currents.2,7 Financial inducements in performing EC processes with alternating current (AC) are numerous, one of them being the elimination of AC to DC conversion costs. Meanwhile, in a DC EC process, a passive film may form on the cathode leading to ineffective current transfer between electrodes,8 as a result of which the treatment efficiency decreases. This problem is resolved by using an AC EC process utilizing cyclic frequencies between the anode and the cathode. Many reports on the treatment of synthetic or real wastewater with DC EC processes are available,9–12 while only a small number of studies have reported low-frequency AC EC processes with different wave shapes and operating costs based on the required electrical energy and electrodes. On the other hand, chemical dyes or unnatural dyes that are used in different industries such as the textile industry, paper, tanning of leather, food processing, plastic, cosmetics, rubber, printing, and dye manufacturing industries are multipart organic molecules, which are used for painting different substances.13,14 Chemical dyes should have long-lasting properties, so they are resistant against degradation. Dye effluent in the environment, especially in water bodies, which leads to a decreased penetration of sunlight reducing its re-oxygenation ability, accounts for a considerable amount of pollutant.10,15,16 Although accurate data on the quantity of dye effluent from a variety of processes in the environment are not available, the discharge of synthetic dyes to the environment even in low quantities has created challenges to environmental scientists. According to available data, there are over 105 commercial dyes worldwide; more than 7 × 105 tons of dyes are produced per year, 5–10% of which is discharged into wastewater or water bodies.17 Among the dye-consuming industries, the textile dyeing industry is recognized to be one of the major environmental pollution contributors. The textile dyeing industry also consumes large volumes of clean water. Dye-containing aqueous solution treatment and water-reuse can play a noteworthy role in reducing the discharge of dye wastewater and providing reusable water for processing. Simply because of their water solubility, reactive azo dyes that have one or more azo groups (R1–N
N–R2) and aromatic rings typically replaced by sulfonate groups are one of the most widely used in the textile industry for dyeing cellulosic fibers, silk, wool, nylon, and leather.13 Reactive dyes form covalent bonds with hydroxyl or amino groups of the dyed material resulting in good fixation.6 Remazol Brilliant Blue R or Reactive Blue 19 dye is an anthraquinone-based vinyl sulphone dye, one of the most widely used reactive dyes. As RB19 is stable and steady, and has low biodegradability in aquatic environments for a long time,6 (with the half-life being 46 years at pH 7 and at 25 °C), it has been used as a model in dye removal studies. Methods with physical or chemical bases such as adsorption, chemical transformation, incineration, electrocoagulation, photocatalysis or ozonation, and biological or enzymatic treatment are the most reported methods for treating dye wastewater. The exact novelty of this work is the use of low voltage and low-frequency alternating current. Additionally, in the present work we used a function generator as a supply source. The usage of a function generator enabled us to study the AC EC process as a function of different waveforms and different current frequencies (commonly the frequency of a distribution network is 50 or 60 Hz), and using the magnitude of a waveform and an adjustable DC voltage added to the signal output (DC offset), simultaneously. Therefore, in this study, the removal of RB19 from aqueous solutions with stainless steel 304 electrodes in a batch using a very low frequency square wave AC was investigated in terms of technical aspects and operating costs. This study’s findings can introduce a new configuration for electrochemical systems, especially AC EC systems.
2. Methods
2.1. Materials
The materials used were marketable-grade stainless steel (SS) 304 electrodes as shown in Table 1 (17 cm × 3 cm × 1 mm, total immersed surface area = 51 cm2), distilled water, RB19 (Alvan Sabet, Iran; refer to Table 2). Na2SO4 or NaCl (GR, Qualigens, Mumbai, India) was used as a supporting electrolyte.
Table 1 Chemical composition and physical and mechanical properties of stainless steel
Chemical composition |
Element |
% |
C |
0–0.07 |
Mn |
0–2.0 |
Si |
0–1 |
P |
0–0.05 |
S |
0–0.02 |
Cr |
17.5–19.5 |
Ni |
8–10.5 |
Fe |
Balance |
Mechanical properties |
Physical properties |
Tensile strength (MPa) |
520–720 |
Density |
8.00 g cm−3 |
Compression strength (MPa) |
210 |
Melting point |
1450 °C |
Modulus of elasticity |
193 GPa |
Proof stress 0.2% (MPa) |
210 |
Electrical resistivity |
0.072 × 10−6 Ù m |
Elongation A5 (%) |
45 min |
Thermal conductivity |
16.2 W m−1 K−1 |
Hardness Rockwell B |
92 |
Thermal expansion |
17.2 × 10−6 K |
Table 2 Main characteristics of RB19 dye
Chemical name |
Remazol Brilliant Blue R |
 |
C.l. Generic name |
C.l. Reactive Blue 19 |
Chemical class |
Anthraquinone |
Chemical name |
2-3-4-Amino-9,10-dihydro-3-sulpho-9,10-dioxoanthracen-4-yl aminobenzenesulphonyl vinyl disodiumsulphate |
Formula |
C22H10O11N2S3Na2 |
λmax (nm) |
594 |
Molecular weight (g mol−1) |
626.5 |
Biodegradability (%) |
<10 |
Toxicity to fish, CL50 (mg L−1) |
500–1000 |
Chemical structure |
2.2. Experimental setup
The experimental setup (Fig. 1) consists of a 500 mL capacity Plexiglas vessel 0.5 cm in thickness, SS 304 electrodes with a 2 cm distance between the two, an AFG-2000 function generator (GW INSTEK; 0–10 Vpp, 0.056 A, 50 Ω), and a magnetic stirrer (Shoimiazma, Iran). In the case of the function generator, the term peak-to-peak voltage (Vpp) refers to the maximum AC voltage.
 |
| Fig. 1 Electrochemical reactor used in the present study. | |
2.3. Experimental procedure
All the experiments were performed in a 500 mL capacity Plexiglas vessel in batch mode. Each batch contained 350 mL of RB19 aqueous solution. After each run, the samples were analyzed with an UV/vis spectrophotometer (Perkin-Elmer 550 SE, USA) at its maximum absorption wavelength (λmax = 592 nm). The oxidation–reduction potential of each sample was measured with an ORP meter (Eutech, Singapore), the temperature and electrical conductivity with HI 98129 (HANA), and the pH with HQ40d (Hach). The surface morphology of the electrodes was analyzed with a 13 MP, Samsung Galaxy Note 3 camera, and an elemental analysis of the electro-oxidation of RB19 sludge was performed with an X-ray fluorescence (XRF) and scanning electron microscopy (SEM) spectrometer: both instruments were located at the Faculty of Science, Tarbiat Modares University, Tehran, Iran.
2.4. Determination of rate constant
In the performed experiments, the removal efficiency of RB19 was investigated in terms of the initial RB19 concentration, the type and amount of electrolyte, and the AC frequency, as well as with or without solution stirring; all experimental results obtained for RB19 removal as a function of electro-oxidation time were matched with pseudo-first order reaction kinetics:18 |
 | (1) |
where C is the concentration of RB19 (mg L−1) at an electro-oxidation time t, and C0 is the initial concentration of RB19 at time = 0 or prior to the EC process; k is the pseudo-first order RB19 removal constant obtained for the EC process (min−1). The constant k can be calculated from plotting ln(C/C0) vs. electro-oxidation time (min). The percentage of color removal was calculated using the following equation: |
 | (2) |
3. Results and discussion
3.1. Effects of applied voltage on RB19 removal
The RB19 removal efficiency was considerably affected by the applied voltage. Here, the applied voltage consists of an AC component and a DC offset. The peak-to-peak value of the AC signal is adjusted by AMPL (the magnitude of a waveform in Vpp) and the amplitude of the DC offset (a constant voltage that is added to an AC source) by OFST keys. The highest RB19 removal efficiency with low electrode weight loss or corrosion was observed when AMPL and OFST were set at 8 Vpp and 0.2 V, respectively (Fig. 2). The high RB19 removal efficiency may be due to the amount of OCl− produced under this condition.2,7 In the succeeding experiments, AMPL = 8 Vpp and OFST = 0.2 V was applied as the input voltage.
 |
| Fig. 2 Effects of applied AMPL and OFST: (a) effect of applied AMPL and OFST pairs on RB19 removal efficiency in the EC process; (b) effect of applied AMPL and OFST pairs on electrode weight loss in the EC process. | |
3.2. The role of the supporting electrolyte
Two different salts, namely NaCl and Na2SO4, were studied as a supporting electrolyte in order to select the one with the higher dye removal efficiency for the subsequent EC tests. With Vrms = 2.828 or V = 8 Vpp, OFST = 0.2 V, and the duty cycle = 95% kept constant, different amounts of the salts were added to the RB19 solution. The efficiency of RB19 removal was determined for various RB19 concentrations (mg L−1), AC frequencies (Hz), and electro-oxidation time (min) in two modes: one with and the other without solution stirring. Use of NaCl as an electrolyte resulted in considerable RB19 removal even without solution stirring. When stirred, both NaCl and Na2SO4 were useful in RB19 removal, but NaCl had a higher removal efficiency. The minimum amount of NaCl used for RB19 removal was lower than that of Na2SO4 in the case of the stirring solution mode. The RB19 removal percentage was 95.12% ± 1.4% at the maximum treatment time of 60 to 120 min in the case of NaCl, while the obtained mean removal percentage for Na2SO4 was 45.56% ± 20.7% at 180 to 210 min treatment time. The increased rate of RB19 removal observed with the use of NaCl instead of Na2SO4 may be due to the enhancement of chlorine/hypochlorite production under galvanostatic conditions.19 Concurrent creation of O2 and Cl2 occurs when the discharge potential of Cl2 is near to that of O2, in which case, the rate of Cl2 production is reduced. There is no dye removal in the case of Na2SO4 without stirring. In the non-stirring mode, a mean RB19 removal efficiency of 74.3% ± 20.04% (30.08% to 99.47%) was obtained for 0.5 to 5 g L−1 of NaCl used, and the minimum time to achieve dye removal was 78.9 ± 15.13 min. As the NaCl concentration increases, the discharge potential of Cl2 decreases according to the Nernst equation, resulting in more current being consumed. In this case, Cl2 and hypochlorite generation increases as well. Therefore, a higher RB19 removal efficiency is obtained. The presence of more NaCl enhances the generation rate of mononuclear and polynuclear Fe(OH)3 by the sequence of reactions shown in the following equations and improves the RB19 removal:
Cl2 + H2O → HOCl + H+ + Cl− |
Fe(OH)3 + HOCl + 2e− → Fe(OH)4− + Cl− |
The amount of NaCl does not show a significant relation to the RB19 concentration, AC frequency, and weight loss of the electrodes (P > 0.05) with their Pearson’s correlation being −0.075, 0.043, and −0.236, respectively. The correlation indicates a negative linear relationship between the NaCl amount in the solution and the RB19 concentration, and between the NaCl amount and the weight loss of the electrodes; however, there is a linear relationship between the NaCl amount in the solution and the AC frequency.
Stirring provides a homogeneous dye solution in the EC reactor resulting in efficient RB19 removal, but stirring at high speeds (greater than 400 rpm) diminishes the potential for flock creation, yielding a lower efficiency.20 In the non-stirring mode no homogeneous dye solution is obtained in the EC reactor, so the formed flocks sediment between the electrodes;21 therefore, cell resistance at a low stirring speed is desirable. Of course, the produced H2 bubbles and Cl2 on the electrode surface can improve the rate of mass transfer even without the use of a stirrer due to stirring by turbulence in the solution.
3.2.1. Kinetic investigations. The effects of the applied AC frequency, NaCl concentration, RB19 concentration, and solution stirring on the rate constant were investigated. The results presented in Table 3 show that NaCl has an enhancing effect on the rate constant because of the increased concentration of active oxidant species such as Cl2/OCl− in the solution.7 The determination coefficient (R2) of the plot for RB19 at two concentrations of 600 and 2000 mg L−1 was the highest, so the validity for the pseudo-first order model is confirmed for these concentrations.
Table 3 Effects of the applied AC frequency, NaCl concentration, RB19 concentration, and solution stirring on the pseudo-first order RB19 removal constants
Without stirring |
With stirring |
Condition |
Kabs |
R2 |
Condition |
Kabs |
R2 |
C = 50 mg L−1, NaCl = 0.48 g L−1 |
Freq. = 500 Hz |
0.002 |
0.143 |
C = 100 mg L−1, NaCl = 0.05 g L−1, freq. = 500 Hz |
0.021 |
0.574 |
C = 200 mg L−1, NaCl = 2 g L−1 |
Freq. = 60 Hz |
0.018 |
0.785 |
Freq. = 300 Hz |
0.012 |
0.653 |
C = 100 mg L−1, Na2SO4 = 0.4 g L−1, freq. = 500 Hz |
0.002 |
0.87 |
C = 400 mg L−1, NaCl = 4 g L−1 |
Freq. = 2000 Hz |
0.03 |
0.731 |
Freq. = 500 Hz |
0.032 |
0.871 |
C = 500 mg L−1, NaCl = 5 g L−1 |
Freq. = 60 Hz |
0.058 |
0.83 |
C = 100 mg L−1, Na2SO4 = 3 g L−1, freq. = 500 Hz |
0.004 |
0.89 |
Freq. = 300 Hz |
0.032 |
0.734 |
C = 600 mg L−1, NaCl = 0.7 g L−1 |
Freq. = 1000 Hz |
0.005 |
0.966 |
C = 2000 mg L−1, NaCl = 2 g L−1 |
Freq. = 300 Hz |
0.026 |
0.95 |
Freq. = 500 Hz |
0.022 |
0.846 |
Frequent changes between acidification and alkalization can arise on the anode surface because of the cyclic nature of an AC signal.2,22,23 The consecutive acidification and alkalization at the electrode surface prevents oxide layer formation and activates the surface, probably contributing to the increase in the self-corrosion rate of the anode. As the AC frequency becomes higher, current reversal will be more rapid. Because of the cyclic alternating of AC, the RB19 molecules can either gather or adsorb at the SS 304 surface. Consequently, both oxidation of the adsorbed molecules and hydrogen production can take place by the cyclic change.24
3.3. Variation of solution pH, electrical conductivity, and ORP during the EC process
The pH values of the experimental solution at the end of the EC treatment period are given in Fig. 3a. The initial pH of RB19 is the pH of the RB19 solution without any pH adjustment. In all cases, a small increase in the pH values was obtained. It discloses that the rate of alkalization of the solutions increases. The rate of alkalization of the solutions near the SS 304 electrodes can play a major role in the electrode weight loss by corrosion. The alkalization happens from the changing cycles of the AC, which electrochemically reduces water into OH−.7,25 The ionization of RB19 occurs at pH 7.
or
In the presence of NaCl:
ClO− + H2O + 2e− → Cl− + 2OH− |
 |
| Fig. 3 (a) Variation of the pH value during the EC process; the small graph is related to the stirring mode. (b) Variation of the electrical conductivity value during the EC process. (c) Variation of the ORP value during the EC process; the small graph is related to the stirring mode. (d) Effect of initial RB19 concentration on the removal efficiency. | |
OH− accumulates and results in a pH change. Production of OH− ions would increase the conductivity of the solution near the SS 304 electrodes. Another scenario is that under alkaline conditions the main anions are OH−, which change into ˙OH radicals by losing an electron to the electrode (anode) surface. The transfer of OH− ions towards the anode is enhanced by the AC frequency.26 The increased production of these ˙OH radicals enhances the oxidation process of RB19.
The obtained result shows that the rate of RB19 removal increases slightly with the increasing EC treatment time and simultaneously increasing pH due to a reduced loss of active chlorine via gaseous chlorine leaving the cell or the formation of chlorate. On the other hand, with the increasing pH the oxidation potential of water decreases, leading to an increase in undesirable water oxidation (at the anode). In the presence of chloride, the oxidation of organic compounds is mediated by active chloro species.27,28 The main reactions at the electrodes are:
In the solution bulk, Cl2 hydrolysis takes place as follows:
Cl2 + H2O → HOCl + H+ + Cl− |
To study the effects of wastewater conductivity on RB19 removal (Fig. 3b), experiments were performed using various amounts of NaCl to change the electrical conductivity of the RB19 solution. With the NaCl concentration increasing, or equivalently, the electrical conductivity (ms cm−1) increasing, the ion concentration in the RB19 solution increases, and the resistance between the electrodes reduces. The solution conductivity variation causes ion content variation. Ions that contribute to the conductivity are H+ and OH−, among others. As Fig. 3b shows, there was a slight increase in the electrical conductivity (ms cm−1) during the EC treatment, which indicates that NaCl salt is the main contributing agent to the conductivity of the RB19 solution. However, EC treatment with NaCl can lead to RB19 removal by the following chloride reaction:
Cl2 + H2O → HOCl + H+ + Cl− |
6HClO + 3H2O → 3ClO− + 3Cl− + 12H+ + 3O2 + 6e− |
ClO− + H2O + 2e− → Cl− + 2OH− |
6ClO− + 3H2O → 2ClO3− + 4Cl− + 6H+ + 1.5O2 + 6e− |
RB19 + HOCl → product + Cl− |
Salt addition in the RB19 solution improves the solution conductivity, but leads to an increased amount of impurity in the wastewater as well, although for the electrical conductivity there are no effluent parameter limitations. The main ion released from the SS 304 electrodes during the EC process is iron, but the absolute value of the amount of released iron is very low. Iron is a biologically active element29 and can influence surrounding objects, i.e., the cells become subjected to electroporation. Furthermore, being an ion with a changeable valence, the ferrous ion generates free radicals, which can essentially affect the results.29
The ORP of the RB19 solution under EC treatment steadily dropped to −374.9 ± −103.4 mV (Fig. 3c), indicating a buildup of a reduced electrolyte condition. The reducing potential (negative ORP) is due to hydrogen gas production in the basic environment (pH = 11.6 ± 0.32).30
3.4. Initial RB19 concentration
The initial RB19 concentration was varied in order to check its influence on the rate of RB19 removal. The rate of removal was the highest when the initial RB19 concentration was moderate (200–500 mg L−1), while the removal rate decreased with the increasing and decreasing initial RB19 concentration, as shown in Fig. 3d. This may be explained by the fact that dye molecules with an increasing concentration tend to associate with clusters of low diffusivity; this lowers the rate of dye diffusion to the electrode surface with a consequent decrease in the rate of dye oxidation.31,32
3.5. Energy consumption
In any EC process, costs are incurred due to electrical energy demand, which affect the operating costs. In the following section, the electrical energy consumption was calculated using different approaches.
3.5.1. Energy consumption based on the power of the function generator. The total energy consumption expresses the AC power (25 W) used to cause the EC reactions. The electrical energy consumption was calculated using the following equation: |
 | (3) |
where P (kW) is the power, V is the volume (L) of treated RB19 solution, t is the EC treatment time (min), and C0 and Ct are the concentrations of the dye in mg L−1 at reaction time 0 and t, respectively.
3.5.2. Energy consumption for the removal of one kg of RB19. The energy consumption for the removal of one kg of RB19 is calculated using the following equation: |
 | (4) |
where t is the EC treatment time (h), V is the voltage in V, and I is the current in A; Sv is the treated volume (L), and ΔRB19 (g L−1) is the difference in RB19 concentration induced by the treatment. By using this equation, the energy consumption was calculated in kW h m−3.
3.5.3. Energy consumption based on specific electrical consumption. The specific electrical energy consumption (E) per kg RB19 removal in the EC process is a figure of merit, which is calculated using the following equation: |
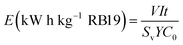 | (5) |
where C0 is the initial RB19 concentration (mg L−1), t is the EC treatment time (min), V is the voltage between the electrodes (Vpp), and Y is the RB19 removal efficiency (%)33 that is calculated using eqn (2).
3.5.4. Estimation of energy consumption and operating cost. For the EC process, the operating cost includes materials, mainly electrodes, and electrical energy costs. In this preliminary economic investigation, energy and electrode material costs were taken into account as major cost items in the calculation of the operating cost (Iranian Rial (IRR) and US$ per m3 of RB19 solution) as below:
3.5.4.1. Operating cost based on the required electrical energy and electrode material. |
Operation cost = aCenergy + bCelectrode
| (6) |
where Cenergy and Celectrode (kg m−3) are the consumption quantities for RB19 removal with SS 304 electrodes; they are obtained experimentally.34 The electrical energy price, a, and the electrode material price, b, are given as follows according to the Iranian market in May 2015: a = US$ 0.0129 per kW h, and b = US$ 3.344 per kg of SS 304. The cost for the electrical energy consumption was calculated by the following equation:
3.5.4.2. Electrical energy requirement. |
 | (7) |
where V is the cell voltage (V), I is the current (A), tEC is the EC process time (s), and Sv is the RB19 solution volume (m3).35 The electrode material cost was calculated using Faraday’s law in eqn (8):
3.5.4.3. SS 304 electrodes requirement. |
 | (8) |
where I is the current (A), t is the duration of the EC process (s), Mw is the molecular mass of SS 304 (55.845 g mol−1, the molar mass of Fe, was used in this study because the most abundant constituent of SS 304 is Fe), z is the number of electrons transferred (z = 2), F is Faraday’s constant (96
487 C mol−1), and V is the volume (m3) of the RB19 solution.Table 4 presents the results of electrical energy consumption estimated by all the methods described above. As can be seen, the use of Na2SO4 electrolyte leads to the highest electrical energy consumption, and based on the RB19 removal efficiency and the operating cost, it is not recommended for the EC dye removal process. In 2012, Iran reformed the energy price and electrical policy too.36 According to Iran’s Power Generation Transmission and Distribution Management Company (TAVANIR) reports, one kilowatt hour of electricity is sold for 430 Rials (about 0.017 cents) on average. Therefore, in comparison to the past, today’s electrical energy costs for dye (RB19) removal has a greater weight compared to the material cost for supplying SS 304 electrodes.
Table 4 Comparison of electrical energy consumption based on different methods at different NaCl concentrations in the EC process
Condition |
Method |
Energy consumption in kW h m−3, energy consumption in kW h L−1, or E in kW h kg−1 of RB19 |
NaCl = 0.5 g L−1. NaCl = 2 g L−1. NaCl = 4 g L−1. NaCl = 5 g L−1. |
No stirring |
3.5.1. |
421a |
111b |
117b |
90c |
39d |
76d |
94c |
201b |
284b |
3.5.2. |
20a |
310b |
410b |
1150c |
1190d |
1420d |
1880c |
4540b |
5900b |
3.5.3. |
14a |
8b |
8.3b |
4.6c |
5.7d |
7.1d |
6.7c |
8.3b |
6.4b |
3.5.4.2. |
418a |
685b |
533b |
342c |
571d |
685d |
609c |
533b |
533b |
3.5.4.3. |
0.04a |
0.07b |
0.05b |
0.03c |
0.06d |
0.07d |
0.06c |
0.05b |
0.05b |
3.5.4.1. (IRR) |
1.8 × 105a |
2.5 × 105b |
8.3 × 105b |
4.6 × 105c |
5.7 × 105d |
7.1 × 105d |
6.7 × 105c |
8.3 × 105b |
6.4 × 105b |
3.5.4.1. ($) |
5.42a |
8.9b |
6.9b |
4.44c |
7.4d |
8.9d |
7.9c |
6.9b |
6.9b |
R (%) |
30.1 |
86.33 |
64.17 |
74.58 |
99.57 |
96.1 |
90.24 |
66.8 |
58.01 |
Condition |
Method |
Electrolyte: NaCl = 50 mg L−1 |
Electrolyte: Na2SO4 = 3 g L−1 and 400 mg L−1 |
Stirring |
3.5.1. |
46.5 |
56 |
59.2 |
110.2 |
624 |
1336 |
3.5.2. |
4700 |
4820 |
4870 |
9620 |
26 530 |
44 360 |
3.5.3. |
4.7 |
4.87 |
4.82 |
9.62 |
26.5 |
44.4 |
3.5.4.2. |
457 |
457 |
457 |
914 |
1599.5 |
1371 |
3.5.4.3 |
0.047 |
0.047 |
0.047 |
0.093 |
0.047 |
0.047 |
3.5.4.1 (IRR) |
196 512 |
196 512 |
196 512 |
393 025 |
687 794 |
589 538 |
3.5.4.1. ($) |
5.9 |
5.9 |
5.9 |
11.8 |
20.7 |
17.8 |
R (%) |
97.1 |
94.67 |
93.78 |
94.94 |
60.33 |
30.57 |
3.6. UV-visible absorption spectral changes
The alteration in the absorption spectra (in both the UV and visible range) for various time intervals during treatment of RB19 through electro-oxidation is presented in Fig. 4. The peak observed in the visible region is caused by the blue color of the chromophore, while the peak observed in the ultraviolet region is a result of the anthraquinone structure of RB19. The decrease of the visible peak during the electro-oxidation period might be due to the destruction of the quinine links by the attack of ˙OH radicals or other oxidants (Cl2, OCl−, and OH−) produced during the oxidation process. The absorbance reduction in the UV region (about 256 nm) is considered as evidence of chromophore degradation. As Fig. 4 presents, the peaks of treated RB19 at different treatment times are in accordance with those of the non-treated RB19 indicating that the AC EC process can remove RB19 without producing intermediates.6
 |
| Fig. 4 UV-visible absorption spectral changes by the electrochemical process for various treatment times. | |
3.7. Characterization of the sludge obtained from the EC reactor
A dark bluish precipitate formed at the bottom of the EC reactor as well as on the surface of the RB19 solution at the end of the EC process due to floatation of RB19 flocculated out of the solution by hydrogen bubbles. However, because of the cyclic polarity change at the electrodes in AC mode, the sludge was raised around the electrodes, and its fouling phenomena were limited. The product was taken out of the solution and dried inside an oven for 3–4 h. It was then grinded to a fine powder and prepared for SEM and XRF analyses.37
It was shown that the by-products formed during the EC process consisted of elements like Ni, Pb, Cr, and Cl, as well as metal oxides such as Fe2O3. The major constituent, from loss on ignition (LOI), was measured to be 43.25% by weight of the EC sludge. The LOI is a measure of the quantity of organic matter in a sample that can be combusted at 550 °C. The loss in weight during combustion equates to the mass of organic matter in the sample. In other words, 43.25% of the EC sludge is organic matter or volatile solids content. It is thus related to the possible reduction of the sludge mass by incineration. The volatile solids content is usually quoted as a percentage of the total solids residue. The solids content remaining after ignition (ash) is termed the fixed residue (FR), which defines the mass of inorganic matter in the sludge, and thus, the mass of solids that would remain for ultimate disposal after incineration.
The sludge can be divided into parts, generally: (1) RB19 monomeric Fe and RB19 polymeric Fe that lead to a RB19 precipitate; (2) RB19 polymeric Fe + Fen(OH)n that create the EC sludge.
The morphology of the by-products obtained from the EC reactor is shown in Fig. 5a. The sludge generated by the SS 304 electrodes contains small particles that may be hydroxides, mainly Fe.
 |
| Fig. 5 (a) SEM and XRF results from the sludge produced after EC treatment of RB19 with SS 304 electrodes. (b) Photo of the SS 304 surface: (a) SS 304 without an EC process; (b1, b2, and b3) SS 304 in the EC process at various magnifications. | |
In order to gain more insight into the effects of AC, the morphology of the SS 304 electrode surface after several cycles of use was characterized by a camera as shown in Fig. 5b. It can be observed that the electrode surface is rough and disordered. Microstructure pores also formed around the nucleus of the active sites where electrode dissolution results in the production of Fe2O3. As a result, the electrodes dissolved uniformly during the EC process.38
SS 304 is non-magnetic (i.e., it has a low permeability) and has excellent ductility, formability, and toughness, even at cryogenic temperatures. In sections with temperatures above 60 °C, there is a risk of chloride-induced stress corrosion cracking, often from the outside, in the case when the insulation material gets wet.
4. Conclusions
It can be concluded that:
• higher removal efficiencies of dye could be acquired when AMPL = 8 Vpp and OFST = 0.2 V was applied as the input voltage;
• stirring of the solution led to a shorter required contact time;
• when used as a supporting electrolyte, NaCl provided a higher RB19 removal efficiency than Na2SO4;
• the ORP of the RB19 solution under EC treatment steadily dropped to −374.9 ± −103.4 mV, indicating a buildup of a reduced electrolyte condition i.e., hydrogen gas production in the basic environment;
• the UV-visible absorption spectral changes test showed that the peaks of treated RB19 at different treatment times are in accordance with those of the non-treated solution, demonstrating that the AC EC treatment can remove RB19 without producing intermediates;
• the sludge study showed that 43.25% of the EC sludge is organic matter or volatile solids content. It is thus related to the possible reduction of the sludge mass by incineration;
• the energy and electrode consumption was estimated by using different equations in our economic evaluation study. Results showed that the electrical energy costs for this process are greater than the cost for supplying the SS 304 electrodes. In general, the energy and electrode consumption of the suggested system is much lower than that of DC mode systems.
References
- R. Mao, X. Zhao, H. Lan, H. Liu and J. Qu, Water Res., 2015, 77, 1–12 CrossRef CAS PubMed.
- M. Eyvaz, M. Kirlaroglu, T. S. Aktas and E. Yuksel, Chem. Eng. J., 2009, 153, 16–22 CrossRef CAS.
- C. A. Martínez-Huitle and E. Brillas, Appl. Catal., B, 2009, 87, 105–145 CrossRef.
- S. Singh, V. C. Srivastava and I. D. Mall, RSC Adv., 2013, 3, 16426–16439 RSC.
- A. Ahmad, S. H. Mohd-Setapar, C. S. Chuong, A. Khatoon, W. A. Wani, R. Kumar and M. Rafatullah, RSC Adv., 2015, 5, 30801–30818 RSC.
- M. Siddique, R. Farooq, Z. M. Khan, Z. Khan and S. Shaukat, Ultrason. Sonochem., 2011, 18, 190–196 CrossRef CAS PubMed.
- J. B. Parsa, M. Rezaei and A. Soleymani, J. Hazard. Mater., 2009, 168, 997–1003 CrossRef CAS PubMed.
- Y.-F. Wu and C.-H. Chen, J. Alloys Compd., 2013, 550, 263–267 CrossRef CAS.
- E. Brillas and C. A. Martínez-Huitle, Appl. Catal., B, 2015, 166–167, 603–643 CrossRef CAS.
- A. Khatri, M. H. Peerzada, M. Mohsin and M. White, J. Cleaner Prod., 2015, 87, 50–57 CrossRef CAS.
- Y.-Z. Wang, A.-J. Wang, W.-Z. Liu, D.-Y. Kong, W.-B. Tan and C. Liu, Bioresour. Technol., 2013, 146, 740–743 CrossRef CAS PubMed.
- A. Pirkarami, M. E. Olya and S. Raeis Farshid, Water Resources and Industry, 2014, 5, 9–20 CrossRef.
- M. R. Samarghandy, E. Hoseinzadeh, M. Taghavi and A. Rahmani, BioResources, 2011, 6, 4840–4855 CAS.
- E. Hoseinzadeh, A. Reza Rahmanie, G. Asgari, G. McKay and A. Reza Dehghanian, Am. J. Sci. Ind. Res., 2012, 71, 682 CAS.
- K. Malachova, Z. Rybkova, H. Sezimova, J. Cerven and C. Novotny, Water Res., 2013, 47, 7143–7148 CrossRef CAS PubMed.
- X. Quan, X. Zhang and H. Xu, Water Res., 2015, 78, 74–83 CrossRef CAS PubMed.
- E. Hoseinzadeh, M.-R. Samarghandi, G. McKay, N. Rahimi and J. Jafari, Desalin. Water Treat., 2014, 52, 4999–5006 CrossRef CAS.
- L. Li and Y. Liu, J. Hazard. Mater., 2009, 161, 1010–1016 CrossRef CAS PubMed.
- D. Rajkumar and J. G. Kim, J. Hazard. Mater., 2006, 136, 203–212 CrossRef CAS PubMed.
- B. Z. Can, R. Boncukcuoglu, A. E. Yilmaz and B. A. Fil, J. Environ. Sci. Health, Part A: Environ. Sci. Eng., 2014, 12, 95 CrossRef PubMed.
- G. J. Millar, J. Lin, A. Arshad and S. J. Couperthwaite, J. Water Process Eng., 2014, 4, 166–178 CrossRef.
- M. Y. A. Mollah, R. Schennach, J. R. Parga and D. L. Cocke, J. Hazard. Mater., 2001, 84, 29–41 CrossRef CAS PubMed.
- X. Mao, S. Hong, H. Zhu, H. Lin, L. Wei and F. Gan, J. Wuhan Univ. Technol., Mater. Sci. Ed., 2008, 23, 239–241 CrossRef CAS.
- W. Cheng, N. Singh, J. A. Maci-Agullo, G. D. Stucky, E. W. McFarland and J. Baltrusaitis, Int. J. Hydrogen Energy, 2012, 37, 13304–13313 CrossRef CAS.
- I. Arslan-Alaton, I. Kabdaşlı, D. Hanbaba and E. Kuybu, J. Hazard. Mater., 2008, 150, 166–173 CrossRef CAS PubMed.
- Y. Xiong, M. S. Cha and S. H. Chung, Proc. Combust. Inst., 2015, 35, 3513–3520 CrossRef CAS.
- D. A. C. Coledam, J. M. Aquino, R. C. Rocha-Filho, N. Bocchi and S. R. Biaggio, Quim. Nova, 2014, 37, 1312–1317 CAS.
- R. Misra, N. N. Neti, D. D. Dionysiou, M. Tandekar and G. S. Kanade, RSC Adv., 2015, 5, 10799–10808 RSC.
- T. Tomov and I. Tsoneva, Bioelectrochemistry, 2000, 51, 207–209 CrossRef CAS PubMed.
- A. Ciblak, X. Mao, I. Padilla, D. Vesper, I. Alshawabkeh and A. N. Alshawabkeh, J. Environ. Sci. Health, Part A: Toxic/Hazard. Subst. Environ. Eng., 2012, 47, 718–726 CrossRef CAS PubMed.
- E. El-Ashtoukhy, N. Amin and M. Abdel-Aziz, Int. J. Electrochem. Sci., 2012, 7, 11137–11148 CAS.
- E. Nossol, A. B. S. Nossol, A. J. G. Zarbin and A. M. Bond, RSC Adv., 2013, 3, 5393–5400 RSC.
- C. K. Araújo, G. R. Oliveira, N. S. Fernandes, C. L. Zanta, S. S. L. Castro, D. R. da Silva and C. A. Martínez-Huitle, Environ. Sci. Pollut. Res., 2014, 21, 9777–9784 CrossRef PubMed.
- D. Ghosh, C. Medhi and M. Purkait, Chemosphere, 2008, 73, 1393–1400 CrossRef CAS PubMed.
- S. Vasudevan, B. S. Kannan, J. Lakshmi, S. Mohanraj and G. Sozhan, J. Chem. Technol. Biotechnol., 2011, 86, 428–436 CrossRef CAS.
- K. Amirnekooei, M. Ardehali and A. Sadri, Energy, 2012, 46, 374–385 CrossRef.
- S. Vasudevan, J. Lakshmi and G. Sozhan, J. Hazard. Mater., 2011, 192, 26–34 CAS.
- S. Vasudevan and J. Lakshmi, Water Sci. Technol., 2012, 65, 353–360 CrossRef CAS PubMed.
|
This journal is © The Royal Society of Chemistry 2015 |
Click here to see how this site uses Cookies. View our privacy policy here.