DOI:
10.1039/C5RA19575F
(Paper)
RSC Adv., 2015,
5, 95894-95902
Tailoring base catalyzed synthesis of palm oil based alkyd resin through CuO nanoparticles†
Received
22nd September 2015
, Accepted 14th October 2015
First published on 14th October 2015
Abstract
Palm oil based alkyd resin was synthesized by an alcoholysis–polyesterification process over a base catalyst tailored by copper oxide (CuO) nanoparticles. In the present paper we synthesized CuO sol in glycerol and subsequently used it in alkyd resin synthesis. The formation of the alkyd resin was confirmed by FTIR, Raman, 1H-NMR and 13C-NMR methods and its molecular weight was determined by gel permeation chromatography (GPC). The antimicrobial activity of the pseudo-homogeneous additive was determined via the Kirby–Bauer method and the stability of the CuO was determined by X-ray absorption near edge structure spectroscopy (XANES). The addition of CuO nano-sol to the conventional homogeneous base catalyzed system explored a new catalytic route for the preparation of bioresin from vegetable oil, reducing the reaction time as well as adding antimicrobial properties to the resin.
Introduction
The growing scarcity of fossil fuels as well as the threat to the environment associated with the application of petroleum-based monomers for the synthesis of alkyd resin can be resolved by the use of renewable resources and the availability of raw materials like vegetable oils of plant origin. Alkyd resin is mainly used in the formulation of paints, varnishes, lacquers, adhesives and composites.1–3 The main reactions for the synthesis of alkyd resins involve the alcoholysis of the oil by a part of the polyol used followed by esterification with a polyacid and the remainder of the polyol. The most common polyol and diacid components are glycerol and phthalic anhydride, respectively.4 Homogeneous base catalysts, such as Ca(OH)2, KOH, NaOH, LiOH or heterogeneous base catalysts, such as CaO, ZnO/alumina and calcium carbonate, are reported to conduct the reaction at ∼240 °C. After the first step of the reaction, the products contain 40–60% monoglyceride (MG),5,6 which is important to homogenise the reaction medium and allow the reaction to proceed to polyesterification,7 and the rest are diglyceride (DG) and triglyceride (TG). Monoglycerides, the glycerol monoesters of fatty acids, are important modifying agents in the manufacture of alkyd resins, polymers and lubricants, and need to be obtained in higher yields. The time required in the heterogeneous system to acquire maximum MG yield is longer compared to the homogeneous one. Lowering the activation energy as well as shortening the reaction time in alcoholysis is crucial to make the process effective. Ferretti et al.5 showed that MgO is a potential heterogeneous catalyst in MG preparation due to its high surface area. The process yields ∼77% of MG after 2 h of reaction; higher than the liquid-base-catalyzed homogeneous process (40–60%). The utility of the catalyst in the alcoholysis reaction has not been further explored for the polyesterification reaction. Nano-structured heterogeneous catalysts are promising nowadays due to their ultrafine size and high surface area. The inclusion of a nano-structured heterogeneous catalyst in a homogeneous catalysis system can provide a new catalytic environment for alkyd resin synthesis. Moreover, the catalyst remaining in the polymer matrix after polyesterification additionally acts as a property enhancer, for example, antimicrobial properties would be very interesting but have not yet been reported. A number of metal oxide nanoparticles such as zinc oxide (ZnO),8 titanium dioxide (TiO2),9 copper oxide (CuO)10 etc. which act as antimicrobial agents have drawn attention in recent years because they show strong activity against bacteria even at low concentration11 and are regarded as non-toxic materials.12 Of these, CuO nanoparticles have attracted more attention due to their high catalytic activity and low cost.13,14 The incorporation of nanoparticles into the polymer matrix is usually performed through mixing after formation of the polymer.8,10,15 Delgado et al.10 embedded copper (Cu) and CuO nanoparticles in polypropylene as antimicrobial agents and found that CuO are more effective than Cu. Besides, the antimicrobial activity of ZnO nanoparticles in a polypyrrole/chitosan blend was studied by Ebrahimiasl et al.,8 who reported that it is effective against bacteria, especially Pseudomonas aeruginosa. Our attempt is to promote catalytic activities of liquid bases with Cu nanoparticles in the chemical conversion of palm oil into alkyd resin. Palm is the most important agricultural crop in Malaysia, since Malaysia is one of the main palm oil producers and exporting countries in the world.16,17
In this context, a new catalytic environment containing NaOH and CuO nanoparticles was explored in alkyd resin synthesis. The CuO nanoparticles were prepared in glycerol medium and the antimicrobial activity of CuO incorporated alkyd resin was examined.
Results and discussion
Preparation of alkyd resin
The end point of alcoholysis was determined via methanol solubility test. The reaction mixtures were withdrawn at different time intervals to determine the solubility of the samples. Time required at the end point of each catalyzed reaction is presented in Fig. 1. It can be seen that the CuO–NaOH catalyzed reactions (A100, A200 and A300) showed significantly reduced reaction time. The A200 catalyzed system showed the shortest reaction time, while further addition of CuO did not influence the system significantly. Besides that, determination of the end point is useful in preventing a prolonged alcoholysis reaction time which can lead to aggravation of side reactions such as the formation of polyglycerols.18
 |
| Fig. 1 Effect of different catalytic systems on alcoholysis (reaction time). | |
In the alcoholysis reaction, the reaction occurred as fatty acid ligands of TG combined with the glycerol to produce MG and DG. The role of the OH− anion from NaOH was to extract hydrogen from glycerol for the formation of glyceroxide. The Na+ cation participates in the stabilization of negatively charged intermediates (glyceroxide). Besides that, it is also used to activate the TG molecule (polarization of C
O bond of TG) and facilitate the attack of the glyceroxide anion to the positively charged carbonyl carbon in TG.19 For the CuO–NaOH catalyzed reaction, a CuO nanoparticle can act as a catalyst providing the basic sites on its surface. Ferretti et al.19 reported the catalytic activity of MgO in the alcoholysis of fatty acid methyl ester (FAME), where the synthesis of monoglycerides was promoted mainly on strongly basic low coordination O2− surface sites. Moreover, for the CuO–NaOH system, CuO may assist Na+ cations with surface positive charges as well as possibly create higher electronegativity deviation resulting in higher catalytic activity. Further study will be required to elucidate the mechanism of the reaction in the CuO–NaOH catalysed system.
The second step is polyesterification, which is a condensation polymerization reaction. The progress of polyesterification was monitored by periodic determination of the acid value (AV) via the titration of unreacted carboxylic acid groups. The AV of different catalyzed reactions at different time intervals is shown in Fig. 2. The plot indicates that as the reaction progressed, the AVs decreased. The decrease in acid values was more rapid during the early stages of the reaction than that during the later stages of the reaction. Similar trends were also reported elsewhere.20–23 These changes in acid values during the polyesterification reaction have been explained on the basis of the different reactivity of the primary and secondary hydroxyl groups of MG.24 Since primary hydroxyl groups react faster than secondary groups, it is believed that the rapid decrease in acid values at the early stages is due to primary hydroxyl groups, while that at the later stages is due to secondary groups.20 In addition, a three-dimensional network of alkyd resin is probably formed in the later stages of polyesterification due to cross-linking of alkyd chains as the viscosity of the reaction medium is increased.25
 |
| Fig. 2 Plot of acid value and DP value against reaction time for different catalysis systems during the polyesterification process (■ A0, ● A100, ▲ A200 and ▼ A300). Table of initial reaction rates is shown inside the figure. | |
The influence of CuO addition is clearly evident in the early stages of the reaction as revealed in Fig. 2. The initial rates for each catalyzed system were determined by following a three-point method26 and the data are presented in Fig. 2 (table, inset). It can be observed from the figure that the initial reaction rates of the CuO catalyzed reactions (A100, A200 and A300) are significantly higher compared to A0. The initial reaction rates of A100, A200 and A300 were found to be 10.40, 12.79 and 13.07 mg KOH g−1 s−1 (Fig. 2, table inset). However, it is noticed that the initial reaction rates of A200 and A300 were almost similar. Apart from that, it can be seen that the A200 catalyzed reaction reached equilibrium earlier (60 min) than the others (Fig. 2). In addition, the DP (average degree of polymerization) of the reaction was calculated from the AV by using eqn (1) and (2). The effect of CuO content on DP is presented in Fig. 2. It can be seen that the DP value increased as the reaction progressed. The curve exhibits two distinct portions, where the initial linear portion corresponds to bond formation between primary hydroxyl groups of MG and PA. It is evident from Fig. 2 that the rates of this step for CuO–NaOH catalyzed systems were significantly higher than that of the conventional NaOH catalyzed reaction. The increase of CuO concentration demonstrated an increase in DP. The second curved portion corresponds to bond formation between secondary groups of MG and PA where the DP value of A200 was higher compared to others, up to 120 min of reaction time. In this context, A200 was selected as the optimum catalytic system.
The effect of temperature during A200 catalysed polyesterification is presented in Fig. 3. It can be seen that temperature influenced the reaction significantly, especially during the early stages of the reaction. The initial rate of the reaction for 220, 230, 240 and 250 °C was 1.8059, 8.3164, 12.7861 and 15.0289 mg KOH g−1 s−1, respectively (Fig. 3, table inset). However, in comparison to the A0 (at 240 °C) catalyzed reaction, the initial rate of reaction catalyzed by A200 at 230 °C was almost similar and reached equilibrium at 120 min. Besides that, the DP value of the sample at 230 °C for A200 was higher than A0 at 240 °C. This result suggests that the CuO–NaOH catalyst system requires lower temperature to achieve similar DP compared to the conventional NaOH catalyzed system. Furthermore, it was found the initial rate of the reaction was increased with the increase in temperature up to 240 °C for A200 and with further increase in temperature the AV and corresponding DP values were almost unchanged. In this context, 240 °C was chosen as the optimum condition considering the rapid early stage reaction and to shorten the reaction period.
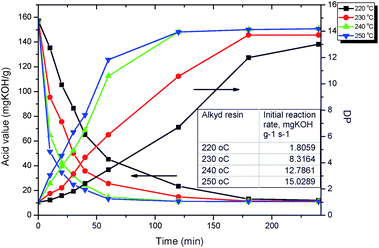 |
| Fig. 3 Plot of acid value and DP against reaction time for different temperatures during the A200 catalysed polyesterification process (■ 220 °C, ● 230 °C, ▲ 240 °C and ▼ 250 °C). Table of initial reaction rates is shown inside the figure. | |
Characterization of alkyd resin
FTIR analysis. The FTIR spectra of oil, alkyd and copper incorporated alkyd resin are shown in Fig. 4. The spectrum of oil was different compared to alkyd resin. In the FTIR spectrum of palm oil (Fig. 4, curve i), a broad band was observed at 3540–3200 cm−1 corresponding to O–H stretching vibration.23 The spectrum also showed a strong absorption in the region of 3030–2840 cm−1 due to C–H stretching.27,28 The absorption bands at 1740–1725 cm−1 were attributed to C
O and that at 1240–1100 cm−1 for C–O–C stretching vibration of the ester group in triglyceride molecules.29 Absorption at 1465–1445 cm−1 was assigned to C–H bending. In addition, the absorption peak at 722 cm−1 was due to the presence of unsaturation in fatty acids.30
 |
| Fig. 4 Infrared spectra of (i) oil, (ii) A0 and (iii) A200. | |
The FTIR spectra of alkyd resin (Fig. 4, curve ii and iii) indicated the presence of ester linkages and other characteristic peaks. It is important to note that a new characteristic peak of an ester group at 1280–1260 cm−1 (C–O–C stretching)22 appeared that was absent in the spectrum of oil. Besides that, palm oil showed a peak at 1748 cm−1 for C
O stretching, whereas, in the case of the synthesized resin that appeared at 1735 cm−1. Apart from that, the characteristic peak at 743 cm−1 corresponds to C–H bending of the aromatic ring contributed by phthalate units;28 confirming the formation of alkyd resin via a polyesterification process.23,27 Furthermore, the stretching frequencies of the spectra of A0 (Fig. 4, curve ii) and A200 (Fig. 4, curve iii) were almost the same. However, slight shifts of ester group (C–O–C stretching) and C–H bending of aromatic ring were noticed, from 1270 and 743 cm−1 for A0 to 1266 and 735 cm−1 for A200, respectively, suggesting interaction (electrostatic interaction/hydrogen bonding) between the polymer matrix and inorganic material (CuO).31
Raman analysis. Raman spectroscopy is one of the non-destructive analyses used to study the bonding interaction, crystallinity, defects, and dislocations of nanomaterials such as graphene, metal oxide, several polymers etc.32,33 In order to study the interaction which occurred between the CuO and alkyd resin, in addition to FTIR spectra; we also examined the Raman spectra of alkyd resin (A0) and CuO–alkyd (A200) (Fig. 5). Apart from that, CuO standard-alkyd was prepared by mixing 1 wt% of CuO standard powder with alkyd resin (A0) for investigation. The spectrum of CuO standard-alkyd is also presented in Fig. 5. The Raman spectra were recorded in the range 0–4000 cm−1. From the figure, it can be seen that the Raman frequencies of all samples were almost similar. The O–H stretching was observed in the region of 3750–3300 cm−1.34 The band at 3200–3050 cm−1 was attributed to
(C–H)35 and that at 3000–2800 cm−1 to C–H stretching.34 The band at 1820 cm−1 was assigned to C
O stretching.34 The peaks at 1635 cm−1 and 1400 cm−1 corresponded to C
C36–38 and CH2, CH3.36,38 The band for C–O–C was at 1250–1150 cm−1.36 The bands at 1050–950 cm−1 and 725–670 cm−1 were attributed to CH2, C–C36 and deformation of C–H.34,39 As seen from the figure, the peak of C–O–C at 1190 cm−1 (A0) was shifted to 1175 cm−1 (A200), which might be due to the influence of CuO. Apart from that, it is noticed that the band intensity of alkyd resin functional groups were reduced in the Raman spectra of A200 and CuO standard-alkyd. This is due to the fluorescence nature of the inorganic material (CuO) in the sample, which overwhelms the weaker scattering bands of alkyd. This is consistent with literature findings for using other materials like molybdenum oxide, graphene oxide and graphene.36,40,41 In addition, the appearance of CuO peaks in the Raman spectrum was not confirmed, as in the narrow scan at 200–800 cm−1. The CuO peaks (usually at 295, 340 and 630 cm−1) were not detected, which might be due to the low concentration of CuO in our samples.
 |
| Fig. 5 Raman spectra of A0, A200 and CuO standard-alkyd. | |
NMR analysis. Fig. 6 shows the 1H-NMR and 13C-NMR spectra of palm oil-based alkyd resins and the formation of alkyd resin is confirmed by the appearance of new peaks in comparison with the spectra of palm oil, which presented in Fig. S1.† The methylene (–CH2–) protons adjacent to hydroxyl groups in glycerol are seen at 3.50–3.80 ppm (Fig. 6a). Downfield shift of –CH2– groups in the glyceride unit (4.12–4.32 ppm) was observed which was probably due to the reaction of hydroxyls with PA, causing the more electron withdrawing from the ester to be presented.29 The peaks at 7.30–7.85 ppm are attributed to the resonance of –OOC–CH⋯CH–COO– protons from the PA moiety, confirming the incorporation of the PA. In the 13C-NMR spectra (Fig. 6b), a pronounced difference between the carbonyl ester of the pendent of oleate/palmitate and the phthalate ester can be observed at 173.00–175.00 ppm and 168.35–169.80 ppm, respectively. It is also observed that the appearance of smaller peaks at 61.00–74.00 ppm corresponds to the methylene groups (–CH2–) of the glyceride.21,29
 |
| Fig. 6 1H-NMR (a) and 13C-NMR (b) of palm oil-based alkyd resin. | |
Molecular weight characterization. Table 1 presents the weight average molecular weight (Mw) and molecular weight distributions (MWD) of the alkyd resin at various stages of the polymerization reaction. It can be seen that the Mw of the samples A0 and A200 increased as reaction progressed. A low molecular weight of alkyds was observed at the beginning of the reaction, which attributed to the low rate of polymerization. Increase in polymerization rate resulted in increased molecular weight in the later stage. This observation is in agreement with literature reported for various vegetable seed oil alkyds, where molecular weight increased as the reaction progressed.42,43 Similarly, the MWD values were increased as the reaction progressed as well as DP increased. This evidenced the formation of a linear polymer in early stages and a three-dimensional network of alkyd resins in later stages. The MWD values of A0 and A200 at 180 min were 2.83 and 2.81, respectively. The size distribution of the samples was almost the same, while their Mw were different. The Mw of A0 and A200 at 180 min were 2723 and 2403 g mol−1, respectively. A200 exhibits lower Mw than A0, indicating that it is more suitable to use as the chief ingredient in paints and surface coatings, where low Mw polymers show better performance in coating.44,45
Table 1 Molecular weights and molecular weight distributions of palm oil alkyd resin with CuO (A200) and without CuO nanoparticles (A0) at various stages of the reaction
Time (min) |
A0 |
A200 |
Mw (g mol−1) |
MWD |
Mw (g mol−1) |
MWD |
0 |
739 |
1.23 |
739 |
1.23 |
30 |
1418 |
1.74 |
1402 |
1.52 |
60 |
1739 |
1.85 |
1643 |
1.72 |
120 |
2191 |
2.24 |
2105 |
2.16 |
180 |
2723 |
2.83 |
2403 |
2.81 |
Stability of CuO nanoparticle. The XANES spectra can provide valuable information regarding the oxidation states of copper and the composition of the samples at different oxidation states. The spectra of Cu-based nanoparticles were investigated in order to understand the stability of CuO nanoparticles before and after the reaction, as shown in Fig. 7. As seen from the figure, the XANES spectra of the two CuO nanoparticle samples revealed similar features to the CuO standard. Furthermore, the relative compositions of the samples were elucidated and the XANES spectra were deconvoluted, considering the contributions of Cu, CuO and CuCl2·2H2O. A linear fitting of the composition of two samples (before and after reaction) was performed and the simulation results are summarized in Table 2. It can be seen that the phase of CuO nanoparticles prepared by the mentioned method was predominantly the CuO phase after the reaction, which may be due to the oxidation of pure Cu (17 wt%) during the polymerization reaction. The composition of CuO before and after the reaction consists of ∼83 and ∼100 wt% CuO, respectively.
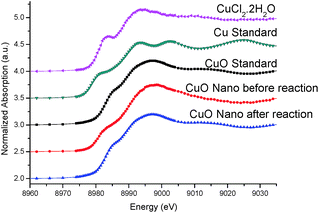 |
| Fig. 7 XANES spectra at the Cu K edge of Cu standard, CuO standard, CuCl2·2H2O, CuO nanoparticle before reaction and CuO nanoparticle after reaction. | |
Table 2 Composition of Cu/O obtained from the linear fitting with the sample CuO nanoparticles before and after the reaction
Nanoparticle |
CuO (wt%) |
Cu (wt%) |
Before reaction |
82.62 ± 0.15 |
17.38 ± 0.13 |
After reaction |
100 |
0 |
Antimicrobial study. The antimicrobial activity of A0 and A200 against microorganisms was tested based on zone of inhibition as presented in Table 3. Gram negative (Escherichia coli, Pseudomonas aeruginosa, Salmonella sp.) and Gram positive (Staphylococcus aureus) microorganisms were selected for the activity test. The zones of inhibition of A200 were tested after 24 h of incubation at 32.5 °C and found to be 23 mm for Escherichia coli, 25 mm for Pseudomonas aeruginosa, 15 mm for Staphylococcus aureus and 40 mm for Salmonella sp., whereas, the control and A0 samples did not show any zone of inhibition (Table 3). A200 showed good antimicrobial activity. However, the bactericidal mechanism is still not well known. It might be due to the strong binding of nanoparticles to cell membranes or electron donor groups such as sulphur and nitrogen in biological molecules, which results in the disruption of the bacterial cell wall and causes cell death.46–48 Apart from that, the formation of copper-peptide complexes may disturb the metabolism of bacterial cells and their power functions such as permeability and respiration which will also cause the death of bacterial cells.48,49 Overall comparison of the microbial reduction rates in the present study revealed Gram negative bacteria to be more susceptible to the antimicrobial effects of Cu ions than Gram positives, presumably due to their thinner wall, which may allow more rapid absorption of the ions into the cell.50,51
Table 3 Antimicrobial activity of A0 and A200
Challenge microorganism |
Diameter for zone of inhabitation |
Zone of inhibition (diameter, mm) |
Control |
Alkyd resin |
CuO incorporated alkyd resin |
Escherichia coli |
 |
 |
 |
23 |
Pseudomonas aeruginosa |
 |
 |
 |
25 |
Staphylococcus aureus |
 |
 |
 |
15 |
Salmonella sp. |
 |
 |
 |
40 |
Conclusions
Palm oil based alkyd resin was successfully synthesized by a homogeneous base catalysed system incorporated with CuO nanoparticles. The addition of a CuO nano-catalyst to the conventional NaOH catalytic system enhanced the catalytic behaviour of the alcoholysis–polyesterification process, reducing the reaction time for both alcoholysis and polyesterification reactions. The preparation of alkyd resin was confirmed by the formation of ester linkages as evidenced by FTIR, 1H-NMR and 13C-NMR. The antimicrobial activity of A0 and A200 were determined via the Kirby–Bauer method and A200 possessed better antimicrobial activity compared to A0. In addition, the molecular weight of alkyd demonstrated valuable information that the sample with lower Mw (A200) is more suitable for surface coating applications. The stability of CuO nanoparticles during the alkyd resin synthesis was examined and it was found that the state of CuO was unchanged throughout the whole experiment; indicating that CuO nanoparticles can be a potential co-catalyst as well as an antimicrobial agent for alkyd resin synthesis.
Experimental section
Materials
Copper(II) chloride salt (CuCl2·2H2O), hydrazine monohydrate (64%), ethanol (99.9%), anhydrous methanol, sodium hydroxide, glycerol, dimethyl sulfoxide (DMSO), copper(II) oxide (97%), copper(I) oxide (99.99%), Escherichia coli (ATCC 8739), Pseudomonas aeruginosa (ATCC 9027), Staphylococcus aureus (ATCC6538) and Salmonella sp. (ATCC 14028) were obtained from Sigma-Aldrich, Malaysia and used without further purification. Refined palm oil was provided by the Malaysian Palm Oil Board (MPOB), Malaysia.
Preparation of copper nanoparticles
The copper sol was synthesized by a sol–gel method at room temperature reported elsewhere.14,52,53 In brief, the required amount of CuCl2·2H2O was dissolved in 44 mL glycerol followed by 6 mL of hydrazine solution being injected into the mixture drop-wise, and the concentration of copper precursor in the sol was maintained in the range of 100–300 mg L−1. Prior to this, the hydrazine solution of 7.062 mM was prepared by diluting 64% hydrazine monohydrate in ethanol. The solution was stirred continuously for 10 h at room temperature. The formation and chemical state of copper nanoparticles was confirmed by using XANES.
Preparation of alkyd resin
Alkyd resin was synthesized by alcoholysis of palm oil with glycerol followed by polyesterification. During alcoholysis, 100 g of palm oil was heated at 240 °C and 22.2 g of glycerol (molar ratio of glycerol/oil = 2
:
1) was incorporated into the system under constant stirring. Thereafter, 0.3 g of NaOH was added and the reaction was conducted under nitrogen purging. MG formation was determined via the methanol solubility test:18 reaction mixture (1 mL) was withdrawn from the reactor and cooled at room temperature prior to the addition of 2 mL of anhydrous methanol. Complete solubility of the reaction mixture in methanol confirmed the ‘end point’ of alcoholysis and the reaction mixture was allowed to cool down at 140 °C. Thereafter, fine phthalic anhydride (PA) (38.7 g) was added into the reaction mixture to initiate the polyesterification process. The reaction temperature was maintained at 240 °C under nitrogen atmosphere. The samples were withdrawn at different time intervals to determine the acid value (AV) accordingly by ASTM D 1639-90 to monitor the progress of the reaction.23 The reaction mixture was quenched to room temperature when the AV reached ∼10. For the preparation of alkyd resin catalysed by the CuO–NaOH system, pure glycerol was substituted by the as-prepared copper sol in glycerol in various concentrations, i.e., 0, 100, 200 and 300 mg L−1 were labelled as A0, A100, A200 and A300, respectively. The synthetic pathway of alkyd resin is presented in Scheme 1.
 |
| Scheme 1 Synthetic pathway of palm oil-based alkyd resin (alcoholysis–polyesterification process). | |
Average degree of polymerization determination
The acid value of in-process samples withdrawn were determined by a titrating method. The extent of the reaction, P and average degree of polymerization, DP were calculated on the basis of acid value using the following equation:54,55where C0 is the initial acid value and Ct is the acid value at time, t of the reaction.
NMR spectroscopy
13C NMR. Spectra were recorded on high resolution spectrometers (AVANCE III; Bruker, Karlsruhe, Germany) located at the central laboratory (Universiti Malaysia Pahang, Malaysia) operating at a carbon-13 frequency of 500 MHz. Spectra were recorded at concentrations of 10–20% (w/v) (50–100 mg of sample in 0.5 mL of chloroform-d) using 5 mm NMR tubes at controlled temperatures of 30 ± 0.1 °C in the broadband proton decoupling mode. Full 13C NMR spectra were obtained with the following acquisition parameters: 16 K data points, spectral width 200 ppm, acquisition time 0.37 s, relaxation delay 5 s, pulse width 45° and 256–3000 scans. High resolution carbonyl spectra were recorded with 16 K data points, spectral width 10 ppm, acquisition time 12–20 s, relaxation delay 5 s and pulse width 45–90°. Free induction decays (FIDs) were transformed by zero filling up to 32 K data points to yield a digital resolution of 0.05–0.08 Hz per point. All FIDs, prior to Fourier transformation (FT), were filtered using an exponential multiplication (0.2–0.4 Hz line broadening) for sensitivity enhancement. The peak intensities of the high resolution 13C NMR carbonyl spectra were accurately quantified using the Linesim (Bruker) curve resolution program.
1H NMR. Samples (20 μL) were placed in 5 mm NMR tubes and dissolved in chloroform-d (0.7 mL) and DMSO-d6 (20 μL). The chemical shifts were referred indirectly to TMS signal (δ = 0.0 ppm) by assigning the residual signal from mono protonated CHD2Cl3 to 7.26 ppm. One-dimensional spectra were recorded on a Bruker AM400 instrument (Central Laboratory, Universiti Malaysia Pahang, Malaysia) operating at 400.13 MHz.
FTIR spectroscopy
Structural information on the samples (oil, A0 and A200) was attained using an FTIR Spectrometer (Spectrum 100 model, Perkin Elmer brand) equipped with an attenuated total reflectance (ATR) device in the wave number range 500–4500 cm−1 and resolution 4 cm−1. The liquid sample (oil, A0 and A200) of 0.2 mL was placed on the ATR sample holder before data recording. The FTIR spectra were taken in transmittance mode.
Raman spectroscopy
Raman spectra of samples were examined using a LabRam HR800 Raman spectroscope (Horiba Jobin-Yvon, France). The Raman system was operated at 10 mV laser power and an excitation wavelength of 514 nm with an Ar+ ion laser.
Gel permeation chromatography (GPC)
Molecular weights (Mw and Mn) and molecular weight distribution (Mw/Mn) of the resin were determined using a Waters gel permeation chromatograph equipped with a styragel column (HR series 3, 4E) and a 2410 differential refractometer detector. The analysis was performed at room temperature with purified high performance liquid chromatography grade tetrahydrofuran (THF) as eluent at 0.7 mL min−1. Low polydispersed linear polystyrene standards were used to construct the calibration curve based on universal GPC calibration. Data acquisition and processing were performed using the Waters Empower software package.
X-ray absorption near edge structure (XANES)
The Cu k-edge XANES measurements were conducted at Singapore Synchrotron Light Source (SSLS), Singapore. The electron storage ring was operated with an energy of 1.3 GeV (current = 100–200 mA). A Si (111) double-crystal monochromator was used for the selection of energy with an energy resolution (ΔE/E) of about 1.9 × 10−4 (eV eV−1). The incident photon energy was calibrated using a standard copper foil. The sample was placed inside a sample holder and the spectra were recorded from 8940 to 9160 eV at ambient temperature. The linear composition fitting was conducted using Athena, a program in the IFEFITT package. The states of CuO nanoparticles before and after the reaction were determined.
Antimicrobial test
The antimicrobial activity of the as-prepared alkyd resin samples prepared by A0 and A200 catalysts was determined by the Kirby–Bauer method.56 A number of microorganisms, such as Escherichia coli (ATCC 8739), Pseudomonas aeruginosa (ATCC 9027), Staphylococcus aureus (ATCC6538) and Salmonella sp. (ATCC 14028) were considered for the experiment. The cultures were maintained in a nutrient broth and subcultured at regular intervals. The samples were prepared (10 mg mL−1) using 0.5% DMSO. The microbial cultures in nutrient agar plates were inoculated using the spread plate technique and a cork borer was used to make a hole in the agar. The samples (10 mg mL−1) were loaded in the hole and incubated at 32.5 °C for 24 h. A blank sample was maintained separately as a control. The diameter of the zone of inhibition after 24 h incubation was measured.
Acknowledgements
This work was financially supported by a research grant from Universiti Malaysia Pahang, Malaysia (Project No. GRS 130350) and GSAS scholarship (Huei Ruey Ong) from the Malaysian Palm Oil Board for which the authors are very grateful.
Notes and references
- M. R. Meneghetti and S. M. P. Meneghetti, Catal. Sci. Technol., 2015, 5, 765–771 CAS.
- C. Aulin and G. R. Ström, Ind. Eng. Chem. Res., 2013, 52, 2582–2589 CrossRef CAS.
- S. K. Dolui, ACS Sustainable Chem. Eng., 2015, 3, 261–268 CrossRef.
- H. Kalita, S. Selvakumar, A. Jayasooriyamu, S. Fernando, S. Samanta, J. Bahr, S. Alam, M. Sibi, J. Vold and C. Ulven, Green Chem., 2014, 16, 1974–1986 RSC.
- C. A. Ferretti, R. N. Olcese, C. R. Apesteguía and J. I. Di Cosimo, Ind. Eng. Chem. Res., 2009, 48, 10387–10394 CrossRef CAS.
- C. A. Ferretti, A. Soldano, C. R. Apesteguía and J. I. Di Cosimo, Chem. Eng. J., 2010, 161, 346–354 CrossRef CAS.
- D. Doulia, S. Rokotas and K. Georgopoulou, Surf. Coat. Int., Part B, 2006, 89, 215–219 CrossRef CAS.
- S. Ebrahimiasl, A. Zakaria, A. Kassim and S. N. Basri, Int. J. Nanomed., 2015, 10, 217 CAS.
- A. Kubacka, M. S. Diez, D. Rojo, R. Bargiela, S. Ciordia, I. Zapico, J. P. Albar, C. Barbas, V. A. M. dos Santos and M. Fernández-García, Sci. Rep., 2014, 4, 4134 Search PubMed.
- K. Delgado, R. Quijada, R. Palma and H. Palza, Lett. Appl. Microbiol., 2011, 53, 50–54 CrossRef CAS PubMed.
- R. Brayner, R. Ferrari-Iliou, N. Brivois, S. Djediat, M. F. Benedetti and F. Fiévet, Nano Lett., 2006, 6, 866–870 CrossRef CAS PubMed.
- T. Gordon, B. Perlstein, O. Houbara, I. Felner, E. Banin and S. Margel, Colloids Surf., A, 2011, 374, 1–8 CrossRef CAS.
- M. N. K. Chowdhury, M. D. H. Beg, M. R. Khan and M. F. Mina, Mater. Lett., 2013, 98, 26–29 CrossRef CAS.
- H. R. Ong, M. R. Khan, R. Ramli and R. M. Yunus, Appl. Mech. Mater., 2014, 481, 21–26 CrossRef CAS.
- E. Ozkan, F. T. Ozkan, E. Allan and I. P. Parkin, RSC Adv., 2015, 5, 8806–8813 RSC.
- F. L. Pua, S. Zakaria, C. H. Chia, S. P. Fan, T. Rosenau, A. Potthast and F. Liebner, Sains Malays., 2013, 42, 793–799 CAS.
- H. R. Ong, R. Prasad, M. M. R. Khan and M. N. K. Chowdhury, Appl. Mech. Mater., 2012, 121–126, 493–498 CAS.
- I. O. Igwe and O. Ogbobe, J. Appl. Polym. Sci., 2000, 78, 1826–1832 CrossRef CAS.
- C. A. Ferretti, S. Fuente, R. Ferullo, N. Castellani, C. R. Apesteguía and J. I. Di Cosimo, Appl. Catal., A, 2012, 413, 322–331 CrossRef.
- A. I. Aigbodion and F. E. Okieimen, Ind. Crops Prod., 2001, 13, 29–34 CrossRef CAS.
- T. E. Odetoye, D. S. Ogunniyi and G. A. Olatunji, Ind. Crops Prod., 2010, 32, 225–230 CrossRef CAS.
- T. E. Odetoye, D. S. Ogunniyi and G. A. Olatunji, Prog. Org. Coat., 2012, 73, 374–381 CrossRef CAS.
- I. E. Ezeh, S. A. Umoren, E. E. Essien and A. P. Udoh, Ind. Crops Prod., 2012, 36, 94–99 CrossRef CAS.
- H. A. Goldsmith, Ind. Eng. Chem., 1948, 40, 1205–1211 CrossRef CAS.
- A. I. Aigbodion and F. E. Okieimen, Eur. Polym. J., 1996, 32, 1105–1108 CrossRef CAS.
- H. S. Fogler, Elements of chemical reaction engineering, Prentice Hall Professional Technical Reference, USA, 4th edn, 2005 Search PubMed.
- V. C. Patel, J. Varughese, P. A. Krishnamoorthy, R. C. Jain, A. K. Singh and M. Ramamoorty, J. Appl. Polym. Sci., 2008, 107, 1724–1729 CrossRef CAS.
- S. M. Cakić, I. S. Ristić, V. M. Jašo, R. Ž. Radičević, O. Z. Ilić and J. K. B. Simendić, Prog. Org. Coat., 2012, 73, 415–424 CrossRef.
- E. F. Assanvo, P. Gogoi, S. K. Dolui and S. D. Baruah, Ind. Crops Prod., 2015, 65, 293–302 CrossRef CAS.
- J. Wu, T. Zhang, G. Ma, P. Li, L. Ling and B. Wang, J. Appl. Polym. Sci., 2013, 130, 4201–4208 CAS.
- Y. Xu, D. Chen, X. Jiao and K. Xue, J. Phys. Chem. C, 2007, 111, 16284–16289 CAS.
- G. Gouadec and P. Colomban, Prog. Cryst. Growth Charact. Mater., 2007, 53, 1–56 CrossRef CAS.
- J. Zięba-Palus, A. Michalska and A. Wesełucha-Birczyńska, J. Mol. Struct., 2011, 993, 134–141 CrossRef.
- J. L. Koenig and P. T. K. Shih, J. Polym. Sci., Part A-2, 1972, 10, 721–740 CrossRef CAS.
- M. A. Omri, A. Triki, M. Guicha, M. B. Hassen, M. Arous, H. A. El Hamzaoui and A. Bulou, Appl. Phys. A, 2015, 118, 1067–1078 CrossRef CAS.
- C. Liu, Z. Wang, Y. A. Huang, H. Xie, Z. Liu, Y. Chen, W. Lei, L. Hu, Y. Zhou and R. Cheng, RSC Adv., 2013, 3, 22380–22388 RSC.
- B. Marton, L. G. J. van der Ven, C. Otto, N. Uzunbajakava, M. A. Hempenius and G. J. Vancso, Polymer, 2005, 46, 11330–11339 CrossRef CAS.
- M. Skrifvars, P. Niemelä, R. Koskinen and O. Hormi, J. Appl. Polym. Sci., 2004, 93, 1285–1292 CrossRef CAS.
- J. A. F. Pierna, V. Baeten, O. Abbas and P. Dardenne, Biotechnol., Agron., Soc. Environ., 2011, 15, 75–84 CAS.
- K. Krishnamoorthy, M. Premanathan, M. Veerapandian and S. J. Kim, Nanotechnology, 2014, 25, 315101 CrossRef PubMed.
- K. Krishnamoorthy, K. Jeyasubramanian, M. Premanathan, G. Subbiah, H. S. Shin and S. J. Kim, Carbon, 2014, 72, 328–337 CrossRef CAS.
- A. I. Aigbodion and C. K. S. Pillai, J. Appl. Polym. Sci., 2001, 79, 2431–2438 CrossRef CAS.
- F. E. Okieimen and A. I. Aigbodion, Ind. Crops Prod., 1997, 6, 155–161 CrossRef CAS.
- M. Alam, D. Akram, E. Sharmin, F. Zafar and S. Ahmad, Arabian J. Chem., 2014, 7, 469–479 CrossRef CAS.
- S. K. Dhoke, T. J. M. Sinha, P. Dutta and A. S. Khanna, Prog. Org. Coat., 2008, 62, 183–192 CrossRef CAS.
- J. R. Morones, J. L. Elechiguerra, A. Camacho, K. Holt, J. B. Kouri, J. T. Ramírez and M. J. Yacaman, Nanotechnology, 2005, 16, 2346 CrossRef CAS PubMed.
- G. Applerot, J. Lellouche, A. Lipovsky, Y. Nitzan, R. Lubart, A. Gedanken and E. Banin, Small, 2012, 8, 3326–3337 CrossRef CAS PubMed.
- A. Y. Booshehri, R. Wang and R. Xu, Chem. Eng. J., 2015, 262, 999–1008 CrossRef.
- L. T. Benov and I. Fridovich, J. Biol. Chem., 1994, 269, 25310–25314 CAS.
- J.-W. Rhim, S.-I. Hong, H.-M. Park and P. K. Ng, J. Agric. Food Chem., 2006, 54, 5814–5822 CrossRef CAS PubMed.
- J. Singh and P. K. Dutta, J. Macromol. Sci., Part A: Pure Appl.Chem., 2011, 48, 246–253 CrossRef CAS.
- H. R. Ong, M. M. R. Khan, R. Ramli, Y. Du, S. Xi and R. M. Yunus, RSC Adv., 2015, 5, 24544–24549 RSC.
- H. R. Ong, M. R. Khan, M. N. K. Chowdhury, A. Yousuf and C. K. Cheng, Fuel, 2014, 120, 195–201 CrossRef CAS.
- E. G. Bobalek and M. T. Chiang, J. Appl. Polym. Sci., 1964, 8, 1147–1168 CrossRef CAS.
- E. G. Bobalek, E. R. Moore, S. S. Levy and C. C. Lee, J. Appl. Polym. Sci., 1964, 8, 625–657 CrossRef CAS.
- S. Ambika, S. Arunachalam, R. Arun and K. Premkumar, RSC Adv., 2013, 3, 16456–16468 RSC.
Footnote |
† Electronic supplementary information (ESI) available. See DOI: 10.1039/c5ra19575f |
|
This journal is © The Royal Society of Chemistry 2015 |
Click here to see how this site uses Cookies. View our privacy policy here.