DOI:
10.1039/C5RA18475D
(Paper)
RSC Adv., 2015,
5, 84465-84470
Preparation of monodispersed CuS nanocrystals in an oleic acid/paraffin system†
Received
9th September 2015
, Accepted 25th September 2015
First published on 28th September 2015
1. Introduction
Transition-metal chalcogenide nanocrystals, especially CuxS (1 ≤ x ≤ 2) NCs, have generated considerable interest because of unusual optical, magnetic, and solar electronic properties.1,2 Meanwhile, owing to surface effects and quantum confinement, the unique size-dependent physiochemical properties of nanosized CuxS are different from the corresponding bulk solids, displaying widespread potential applications in various fields, such as catalysis,3,4 photocatalysis,5 photovoltaic cells,6 electrochemical sensors,7 medicine,8 tribology,9 and so on. Normally, there are five stable CuxS (1 ≤ x ≤ 2) phases: covellite (CuS) in the copper-deficient region and anlilite (Cu1.75S or Cu7S4), digenite (Cu1.8S or Cu9S5), djurleite (Cu1.96S or Cu31S16), and chalcocite (Cu2S) in the copper-rich region.10,11 As is well known, the band gap of CuxS NCs can be tunable with varying its chemical stoichiometries, the average oxidation state of Cu, particle size and the defects.12–14 For example, Zhao et al.15 synthesized plasmonic Cu2−xS (x = 1, 0.2, 0.03) nanocrystals by three different chemical methods: sonoelectrochemical, hydrothermal, and solventless thermolysis methods. Their work showed that the optical and structural properties of copper-deficient copper(I) sulfides exhibited a blue shift in the band gap absorption compared to bulk Cu2−xS. Kriegel et al.16 demonstrated that copper chalcogenide nanocrystals might offer to hold excitons and highly tunable localized surface plasmon (LSPs) by changing the excitonic and plasmonic properties. Zou et al.17 prepared copper sulfide nanocrystals with different morphologies via a solvothermal method using copper acetate and sulfur chloride as precursors, which showed excellent electrocatalytic activity for methyl orange (MO) degradation. Lim et al.18 synthesized monodispersed different phase-pure copper sulfide nanocrystals via the decomposition of an air-stable precursor of copper(I) thiobenzoate (CuTB) in the presence of different stabilizing agents. However, some drawbacks are obvious for most synthesis methods of copper sulfide nanocrystals, such as high reaction temperatures, prolonged reaction times, high cost, and harmful/difficult work up. Recently, the cheap and safe methods to synthesis II-VI nanocrystals such as CdSe QDs from the non-toxic oleic acid and paraffin solvent system were reported,19 which are low energy cost, shorter processing time and less pollution with high yield. Here, we developed this method to prepare the high-quality CuS NCs belonging to IB-VIA group in an oleic acid/liquid paraffin system using low-cost cupric oxide and elemental sulfur as the precursors without the inert gas. The synthesis of uniform and monodisperse nanoparticles is of utmost importance to their many applications. The structural, morphological and optical properties of CuS nanocrystals were studied. The pure dispersed covellite CuS nanocrystals present a narrow band gap, and a broad absorption band in the visible-light and near-infrared (NIR) region, which might have wide applications.20
2. Experimental
2.1 Preparation of monodisperse CuS NCs
The typical synthesis procedure was as follows: (i) 2 mmol of CuO was added in the mixed solution containing 4 mL of oleic acid and 6 mL of liquid paraffin. The solution was stirred and heated to 180 °C in an oil bath until a blue homogeneous solution was obtained as precursor A, which digital photo is shown in Fig. 1a; (ii) 2 mmol of elemental S was dispersed in 10 mL of liquid paraffin. The solution was stirred and heated to 120 °C in an oil bath until a light yellow homogeneous solution was obtained as precursor B (Fig. 1b); (iii) the precursor B was swiftly injected into precursor B with vigorous stirring at 120 °C for different times. Then, the solution was quickly cooled to room temperature by cold cyclohexane; (iv) the black precipitate obtained was separated by centrifugation, washed with cyclohexane and toluene alternately for several times to remove the excess ions and ligands remaining in the final products. Finally, the product was redispersed in nonpolar solvents (e.g., cyclohexane, toluene, hexane, etc.). Thus, copper sulfide nanoparticles were readily synthesized. The oleic acid not only can react with CuO, but also can be as the stabilizer to modify the surface of the product. Fig. 1c presents the digital photograph of CuS NCs dispersed in cyclohexane with dark green color.
 |
| Fig. 1 The digital photos of (a) Cu precursor, (b) S precursor, (c) cyclohexane solutions of CuS NCs. | |
2.2 Characterization
X-ray diffraction (XRD) patterns obtained on an X-ray diffractometer (type D/Max2500pc) using Cu Kα irradiation at a scan rate of 0.02° 2θ s−1 were used to determine the phase structures of the prepared samples. The accelerating voltage and the applied current were 20 kV and 150 mA, respectively. The morphology of CuS NCs was studied by transmission electron microscopy (TEM) using a JEOL/Japan JSM-2100 transmission electron microscope operating at 200 kV. The electronic binding energy of the copper sulfide was examined by X-ray photoelectron spectroscopy (XPS) on a PHI-5000 VersaProbe instrument. Ultraviolet-visible and near-infrared spectrophotometer of CuS NCs was recorded on a U-4100 HITACHI UV-Vis-near infrared spectrophotometer with a 1.0 cm optical path length quartz cuvette in the wavelength range 300 nm to 1600 nm. Room-temperature photoluminescence (RT-PL) measurements were performed on ethanol suspension of samples with a pulsed Xe laser (RF-5301 PC) as the excitation wavelength of 200 nm.
3. Result and discussion
3.1 Structure and morphology
Fig. 2 shows the X-ray diffraction patterns of the as-prepared CuS NCs with different molar ratios of Cu2+
:
S2− reacted at 120 °C for 10 min. From Fig. 2, the main diffraction peaks of the as-prepared CuS NCs with 2
:
1 and 1
:
1 molar ratio of Cu2+
:
S2− are identified as the hexagonal covellite-phase CuS with lattice constants of a = b = 3.792 Å and c = 16.34 Å (JCPDS card no. 06-0464).21 The diffraction peaks of these two samples are sharp and intense, indicating a highly crystalline nature. But the typical diffractions of Cu9S5 phase can be observed in the diffractions peaks of CuS sample (Cu2+
:
S2− is 2
:
1), indicating that the sample contained the hexagonal covellite-phase CuS and digenite-phase Cu9S5. However, as the molar ratios of Cu2+
:
S2− is 1
:
1, the diffractions peaks present a pure hexagonal covellite-phase CuS. The mean grain size of nanocrystalline covellite CuS can be estimated to be ca. 8.7 nm by Scherrer formula as follows:
D = kλ/β cos θ |
where ‘D’ is crystallite size; ‘k’ is a parameter; ‘λ’ is the wavelength of the radiation, ‘β’ is the line broadening at half the maximum intensity (FWHM), ‘θ’ is half the diffraction angle.22 Moreover, as decreasing the molar ratio of Cu2+
:
S2− to 1
:
2, the yarrowite-phase Cu9S8 can be observed, and the diffraction peaks are broad, showing that excess S element might result in changing the phase of CuS, decreasing the crystalline nature, and reducing the particle size.23,24
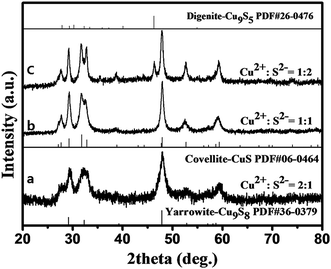 |
| Fig. 2 XRD pattern of CuS NCs with different molar ratio of Cu2+ : S2− reacted at 120 °C for 10 min, (a) 2 : 1, (b) 1 : 1, (c) 1 : 2. | |
TEM image of CuS NCs with 1
:
1 molar ratio of Cu2+
:
S2− is displayed in Fig. 3. It can be seen that the most spherical particles of CuS NCs are uniformly and fairly monodispersed ranging from 2.2 to 15.8 nm in the diameter. The average diameter calculated in the TEM image of 100 CuS NCs is 9 ± 1.2 nm, agreement to the XRD result. From the HR-TEM image of CuS NCs as shown in the inset of Fig. 3, the lattice spacing of CuS is ca. 3.0 Å, which is a characteristic fringe spacing of the hexagonal CuS crystal phase in the (102) plane, consistent with previous reports.25,26 The TEM images of CuS NCs with different molar ratios of Cu2+
:
S2− (2
:
1, and 1
:
2) are presented in Fig. S1, (ESI†), which are both spherical and mono dispersed similar to Fig. 2, indicating that the different molar ratios of Cu/S had little effect on the final morphology of CuS nanoparticles in the oleic acid/liquid paraffin system. In the experiment, we found that the rinsing agent plays an important role for the final CuS NCs. Fig. S2a (ESI†) shows the TEM image of original CuS NCs without rinsing. Some aggregated black points connected with light-colored materials, showing that the CuS points were coated by excess oleic acid as stabilizer. However, after rinsing with polar ethyl alcohol for three times, we can see that CuS NCs were aggregated more heavily, showing that the polar agent might remove the stabilizer of oleic acid modified on the surface of CuS NCs (Fig. S2b (ESI†)). While, after rinsing with nonpolar cyclohexane, the CuS NCs present a well-dispersed and relatively uniform, as shown in Fig. S2c (ESI†), indicating that nonpolar rinsing agents might remove the excess of oleic acid on the surface of the CuS NCs and can maintain the modification layer on the surface of CuS NCs.
 |
| Fig. 3 TEM image and HRTEM image (the inset) of CuS NCs with 1 : 1 molar ratio of Cu2+ : S2−. | |
The elemental compositions and chemical speciation of CuS NCs with 1
:
1 molar ratio of Cu2+
:
S2− are further analyzed by XPS measurements (Fig. 4a). XPS spectra indicate the presence of signals of Cu and S elements as well as C and O elements. The peaks of O and C may come from H2O, O2 and CO2 adsorbed on the surface of the sample due to exposure to the air and adventitious hydrocarbon from the XPS instrument itself. The binding energies of Cu 2p and S 2p had been calibrated by referencing the C 1s peak (284.8 eV). As shown in Fig. 4a, the two typical peaks locating at the binding energies of 934.8 eV and 955.2 eV are attributed to Cu(II) 2p3/2 and Cu(II) 2p1/2, respectively, which are essentially identical binding energies for Cu 2p orbital in accordance with Cu2+ (Fig. 4b).27,28 In addition, a very weak peak corresponding to the satellite peak of Cu2+ at ca. 946 eV is observed, which is similar to the report by Yu et al.29 Furthermore, symmetrical shapes of the two Cu 2p XPS peaks also imply the presence of pure CuS. Similarly, the binding energy of S 2p centers at ca. 164 eV (Fig. 4c), exhibits a typical value for metal sulfides.26,30 Therefore, only Cu2+ and S2− exist in the CuS NCs.
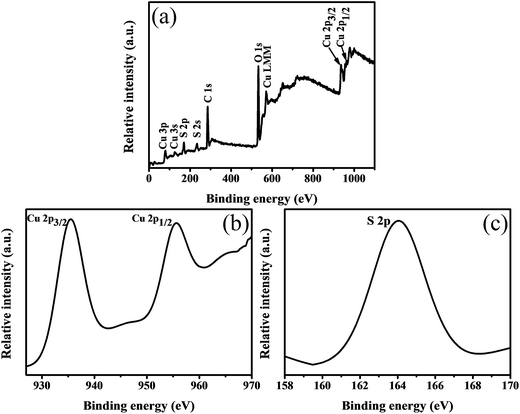 |
| Fig. 4 Typical XPS spectra of CuS NCs with 1 : 1 molar ratio of Cu2+ : S2− reacted at 120 °C for 10 min: (a) survey spectra (b) Cu 2p region spectrum, (c) S 2p region spectrum. | |
3.2 Optical properties
The optical properties of semiconductor nanocrystals can be studied using UV/Visible/NIR and photoluminescence spectra. The absorption spectrum of the obtained CuS (1
:
1) NCs presents a broad visible light absorption band between 400 and 800 nm as shown in Fig. 5a, indicating the CuS sample with a narrow band gap. Moreover, in the near-infrared region (around 800–1600 nm), the broad absorption bands can also be observed, similar to the typical cobellite CuS nano crystals, which might be due to the interband-transitions (absorptions) from valence states to unoccupied states.31–35 Normally, based on the UV-Vis absorption spectra, the optical bandgaps of the CuS crystals can be estimated using the following equation36
where α is the absorption coefficient, hν is the photon energy, A is a constant, h is the Plank constant, and n = 2 and 1/2 for direct and indirect transitions, respectively. The analysis of above equation shows that n = 1/2 fitted for the CuS crystals, indicating the indirect transitions, and the free carrier absorption appears at longer wavelengths.37 Thus, the energy band gap can be conveniently determined from the extrapolation of the linear portion of the (αhν)1/2 versus hν plots to α = 0. From Fig. 5b, the intercept of the straight line on the photon energy axis gives direct optical bandgap value as ca. Eg = 1.5 eV. In order to investigate the effect of the reaction time and the different Cu
:
S molar ratios for the band gap, the UV-Vis and near-IR absorption spectra of CuS NCs with different reaction times (5 min, 10 min, 15 min, 20 min) and different molar ratios of Cu2+
:
S2− (2
:
1, 1
:
1, 1
:
2) at 120 °C are shown in Fig. S3 (ESI†). We can see that all samples obtained can exhibit broad absorption in near-IR and visible-light regions, however, further increasing reaction time resulted in broading the width of the absorption peaks and decreasing the intensities of the absorption peaks, indicating that particle size and stoichiometric ratio of the sample had been changed (Fig. S3 (ESI†)). The result is similar to a previous report, in which they found that the band gap of CuS crystals could be changed with the change of the stoichiometric ratio of the CuS samples as well as with the reaction time.38
 |
| Fig. 5 (a) UV-Vis absorption spectra of as-prepared CuS NCs with 1 : 1 molar ratio of Cu2+ : S2− reacted at 120 °C for 10 min. (b) Plot of the indirect optical band gaps. | |
Photoluminescence (PL) based on the recombination of free carriers can be used to disclose and explain many phenomenons, such as the efficiency of charge carrier trapping, immigration, transfer, and the fate of photogenerated electrons and holes in semiconductor nanomaterials. Fig. S4 (ESI†) presents the PL excitation plots with different emission wavelength of 430 and 470 nm, we can see that suitable excitation wavelength is ranging from 200–250 nm. Fig. 6 shows the room-temperature (RT) PL spectra of the CuS crystals with different Cu
:
S molar ratios in an excitation wavelength of 200 nm, which exhibit six emission peaks. The emission peaks can be divided two parts: one part in green region comprises three peaks at 432, 453 and 471 nm, which can be correlated with the near band edge electronic transition (band to band transition); another part in blue region comprises three peaks at 484, 494 and 516 nm, which might be due to the defects presented in the CuS crystalline structure, consistentment with the previous report.39 Generally, the PL emissions in the blue region (longer wavelength) were considered to be the electronic transitions in the defect state of the CuS crystals, and PL emissions in the green region (short wavelength) were from the trap energy states in the band structure.10,40–42 Moreover, from Fig. 6, all CuS samples obtained present the similar PL peaks, but the peak intensities of CuS (1
:
1) are much higher than that ones of other two sample (2
:
1 and 1
:
2), indicating that the high crystallinity and pure covellite-phase of the CuS (1
:
1) nanocrystals resulted in enhanced intensity of PL emission. In the experiment, we also found that the excitation wavelength can also effect the PL spectra, the PL peak intensities decreases with increasing the excitation wavelength (200, 250, 300 and 350 nm) as shown in Fig. S5 (ESI†), indicating that the longer wavelength results in a lower electric transfer efficiency.43
 |
| Fig. 6 PL spectra of CuS NCs prepared at 120 °C for 10 min (a) 2 : 1, (b) 1 : 1, (c) 1 : 2. | |
3.3 Formation mechanism
The formation mechanism of CuS NCs is proposed as shown in Scheme 1. It is reasonably deduced that the formation mechanism of monodispersed CuS NCs was explained by the three main chemical reactions below. First, black CuO powder reacted with oleic acid at 180 °C in an oleic acid/liquid paraffin system to generate blue homogeneous copper complex solution (Cu precursor) (eqn (1)). Then, yellow elemental sulfur dissolved in liquid paraffin at 120 °C produced hydrogen sulfide to form a light yellow homogeneous solution due to a dehydrogenation reaction (eqn (2)). Finally, S precursor was added swiftly into Cu precursor with vigorously stirring at 120 °C. Thus, the CuS NCs could be readily obtained due to the reaction between the Cu-complex and H2S (eqn (3)). The overall reaction equation is listed in eqn (4). In summary, it should be noted that oleic acid plays an vital role on the preparation of CuS NCs due to preventing the aggregation as stabilizer, and reducing the nucleation rate to form smaller CuS NCs (owning to the slow release of Cu2+ from Cu-complex). Meanwhile, we considered the liquid paraffin not only acts as solvent (eqn (1)), but also as a reductant reagent (eqn (2)). The average yield of CuS NCs with 1
:
1 molar ratio of Cu2+
:
S2− can reach 59.2%.
 |
| Scheme 1 Proposed reaction sequence involved in the formation of CuS NCs. | |
4. Conclusions
The monodispersed CuS NCs with different structure phase have been successfully synthesized by a simple hot injection method using the cupric oxide and elemental sulfur as the precursors in an oleic acid/liquid paraffin system. To the best of our knowledge, it is the first time to synthesis CuS NCs using the cupric oxide and elemental sulfur as the precursors in an oleic acid/liquid paraffin system. The rinsing agents plays an important influence on the final morphology of the CuS NCs. The structure and morphology of the obtained CuS crystals have been confirmed by XRD, XPS, TEM and HRTEM. The optical properties of the CuS was characterized by UV-Vis and near-IR absorption and photolumninent spectra. The as-prepared CuS nanocrystals present the broad absorption bands in the visible-light and near-infrared (NIR) region, and its narrow band gap estimated from UV-Vis spectrum indicates that many potential applications in photovoltaic cells, electrochemical sensors and photocatalysis are anticipated. The facile and fast hot injection method using an oleic acid/liquid paraffin system is a promising processing route for preparation of CuS nanocrystals due to low environmental pollution, less toxicity, inexpensive cost, easy extraction for purification and simple reaction conditions.
Notes and references
- M. A. Yildirim, A. Ateş and A. Astam, Phys. E, 2009, 41, 1365–1372 CrossRef PubMed.
- M. Adelifard, H. Eshghi and M. M. B. Mohagheghi, Appl. Surf. Sci., 2012, 258, 5733–5738 CrossRef CAS PubMed.
- Q. Z. Wang, N. An, Y. Bai, H. H. Hang, J. J. Li, X. L. Lu, Y. H. Liu, F. P. Wang, Z. M. Li and Z. Q. Lei, Int. J. Hydrogen Energy, 2013, 38, 10739–10745 CrossRef CAS PubMed.
- G. R. Chaudhary, P. Bansal and S. K. Mehta, Chem.–Eng. J., 2014, 243, 217–224 CrossRef CAS PubMed.
- U. T. D. Thuy, N. Q. Liem, C. M. A. Parlett, G. M. Lalev and K. Wilson, Catal. Commun., 2014, 44, 62–67 CrossRef CAS PubMed.
- A. D. Savariraj, K. K. Viswanathan and K. Prabakar, Electrochim. Acta, 2014, 149, 364–369 CrossRef CAS PubMed.
- L. Z. Pei, J. F. Wang, X. X. Tao, S. B. Wang, Y. P. Dong, C. G. Fan and Q. F. Zhang, Mater. Charact., 2011, 62, 354–359 CrossRef CAS PubMed.
- Y. B. Li, W. Lu, Q. Huang, M. Huang, C. Li and W. Chen, Nanomedicine, 2010, 5, 1161–1171 CrossRef CAS PubMed.
- Y. D. Zhang, B. J. Huang, P. J. Li, X. M. Wang and Y. G. Zhang, Tribol. Int., 2013, 58, 7–11 CrossRef CAS PubMed.
- N. Mukherjee, A. Sinha, G. G. Khan, D. Chandra, A. Bhaumik and A. Mondal, Mater. Res. Bull., 2010, 46, 6–11 CrossRef PubMed.
- S. H. Chaki, J. P. Tailor and M. P. Deshpande, Mater. Sci. Semicond. Process., 2014, 27, 577–585 CrossRef CAS PubMed.
- P. Kumar, M. Gusain and R. Nagarajan, Inorg. Chem., 2011, 50, 3065–3070 CrossRef CAS PubMed.
- M. T. S. Nair, L. Guerrero and P. K. Nair, Semicond. Sci. Technol., 1998, 13, 1164–1169 CrossRef CAS.
- C. Nascu, I. Pop, V. Ionescu, E. Indrea and I. Bratu, Mater. Lett., 1997, 32, 73–77 CrossRef CAS.
- Y. X. Zhao, H. C. Pan, Y. B. Lou, X. F. Qiu, J. J. Zhu and C. Burda, J. Am. Chem. Soc., 2009, 131, 4253–4261 CrossRef CAS PubMed.
- I. Kriegel, J. Rodriguez-Fernandez, A. Wisnet, H. Zhang, C. Waurisch, A. Eychmuller, A. Dubavik, A. O. Govorov and J. Feldmann, ACS Nano, 2013, 7, 4367–4377 CrossRef CAS PubMed.
- J. Zou, J. Z. Jiang, L. Huang, H. P. Jiang and K. X. Huang, Solid State Sci., 2011, 13, 1261–1267 CrossRef CAS PubMed.
- W. P. Lim, C. T. Wong, S. L. Ang, H. Y. Low and W. S. Chin, Chem. Mater., 2006, 18, 6170–6177 CrossRef CAS.
- Z. T. Deng, L. Cao, F. Q. Tang and B. S. Zou, J. Phys. Chem. B, 2005, 109, 166771 Search PubMed; Y. F. Liao, W. J. Li and S. L. He, Nanotechnology, 2007, 18, 375701 CrossRef.
- P. K. Nair and M. T. S. Nair, J. Phys. D: Appl. Phys., 1991, 24, 83 CrossRef CAS.
- K. Mageshwari, S. S. Mali, T. Hemalatha, R. Sathyamoorthy and P. S. Patil, Prog. Solid State Chem., 2011, 39, 108–113 CrossRef CAS PubMed.
- P. Scherrer, Göttinger Nachrichten Gesell., 1918, 2, 98 Search PubMed.
- M. R. Wang, F. Xie, W. J. Li, M. F. Chen and Y. Zhao, J. Mater. Chem. A, 2013, 1, 106–111 Search PubMed.
- C. F. Mu, Q. Z. Yao, X. F. Qu, G. T. Zhou, M. L Li and S. Q. Fu, Colloids Surf., A, 2010, 371, 14–21 CrossRef CAS PubMed.
- H. L. Xu, W. Z. Wang and W. Zhu, Mater. Lett., 2006, 60, 2203–2206 CrossRef CAS PubMed.
- C. Y. Wu, S. H. Yu, S. F. Chen, G. N. Liu and B. H. Liu, J. Mater. Chem., 2006, 16, 3326–3331 RSC.
- P. Roy, K. Mondal and S. K. Srivastava, Cryst. Growth Des., 2008, 8, 1530–1534 CAS.
- J. Qian, K. Wang, Q. M. Guan, H. N. Li, H. Xu, Q. Liu, W. Liu and B. J. Qiu, Appl. Surf. Sci., 2014, 288, 633–640 CrossRef CAS PubMed.
- J. G. Yu, J. Zhang and S. W. Liu, J. Phys. Chem. C, 2010, 114, 13642–13649 CAS.
- Y. C. Zhang, X. Y. Hu and T. Qiao, Solid State Commun., 2004, 132, 779–782 CrossRef CAS PubMed.
- P. Zhang and L. Gao, J. Mater. Chem., 2003, 13, 2007–2010 RSC.
- M. Saranya, C. Santhosh, R. Ramachandran, P. Kollu, P. Saravanan, M. Vinoba, S. K. Jeong and A. N. Grace, Powder Technol., 2014, 252, 25–32 CrossRef CAS PubMed.
- S. A. Zolotovskaya, V. G. Savitski, P. V. Prokoshin and K. V. Yumashev, J. Opt. Soc. Am. B, 2006, 23, 1268–1275 CrossRef CAS.
- M. C. Brelle, C. L. Torres-Martinez, J. C. McNulty, R. K. Mehra and J. Z. Zhang, Pure Appl. Chem., 2000, 72, 101–117 CrossRef CAS.
- Y. H. Li, J. W. Hu, G. J. Liu, G. W. Zhang, H. L. Zou and J. H. Shi, Carbohydr. Polym., 2013, 92, 555–563 CrossRef CAS PubMed.
- A. Saeid, M. Kavoos and N. Payman, Mater. Res. Bull., 2014, 51, 411–417 CrossRef PubMed.
- Q. L. Huang, H. Chen, Y. C. Zhang and C. L. Wu, J. Alloys Compd., 2011, 509, 6382–6387 CrossRef CAS PubMed.
- X. Yu and X. An, Mater. Lett., 2010, 64, 252 CrossRef CAS PubMed.
- S. Ou, Q. Xie, D. Ma, J. Liang, X. Hu, W. Yu and Y. Qian, Mater. Chem. Phys., 2005, 94, 460–466 CrossRef CAS PubMed.
- J. Z. Xu, S. Xu, J. Geng, G. X. Li and J. J. Zhu, Ultrason. Sonochem., 2006, 13, 451–454 CrossRef CAS PubMed.
- H. Z. Ke, W. Luo, G. E. Cheng, X. K. Tian and Z. B. Pi, J. Wuhan Univ. Sci. Technol., 2010, 25, 459–463 CrossRef CAS.
- H. T. Zhu, J. X. Wang and D. X. Wu, Inorg. Chem., 2009, 48, 7099–7104 CrossRef CAS PubMed.
- T. Thongtem, A. Phuruangrat and S. Thongtem, Curr. Appl. Phys., 2009, 9, 195–200 CrossRef CAS PubMed; B. Murali, J. Parui, K. G. Chandan, A. Mayoori and S. B. Krupanidhi, Adv. Sci., Eng. Med., 2013, 5, 105–111 CrossRef PubMed.
Footnote |
† Electronic supplementary information (ESI) available. See DOI: 10.1039/c5ra18475d |
|
This journal is © The Royal Society of Chemistry 2015 |
Click here to see how this site uses Cookies. View our privacy policy here.