DOI:
10.1039/C5RA16446J
(Paper)
RSC Adv., 2015,
5, 81707-81712
High performance graphene embedded rubber composites†
Received
15th August 2015
, Accepted 8th September 2015
First published on 9th September 2015
Abstract
Nano-fillers have provided a big advantage for enhancing the performance of rubber composites through leading the synergy effects in the physical and chemical properties. However, despite various approaches having been explored, the process to make a homogenous and stable dispersion of nano-filler in the rubber matrix remains a major challenge in this field. Herein, we propose a simple and effective route for synthesizing nanocomposites of rubber with homogenous and stable dispersed low defect graphene flakes (l-GFs), which are prepared using l-GFs/SBR composites via aqueous-phase mixing of exfoliated l-GFs with SBR latex. The l-GFs embedded SBR matrix shows a remarkable improvement in the modulus and tensile strength even at the low loading rate, which is ascribed to the efficient dispersion of the l-GFs enhancing interfacial interaction with the rubber matrix. The integration of l-GFs into the SBR matrix significantly improves the thermal and electrical conductivities, as well as the gas barrier property of the rubber composites. This method is water-mediated, green and scalable, showing great potential for the production of various l-GFs-based rubber composites at an industrial level.
1. Introduction
Rubbers, regarded as strategic materials, have been tailored via the addition of different fillers to meet industrial demands in various applications.1 Currently, carbon black (CB), introduced over a century ago, is still the most widely used filler in the rubber industry.2 However, when filled with CB and subjected to dynamic stress, rubbers, such as natural rubber (NR) and styrene-butadiene rubber (SBR), tend to build up heat and generate hysteresis, which significantly accelerate the fatigue process of the materials.3 Moreover, because these filled rubbers possess intrinsically high gas permeability, butyl rubber has to be incorporated in some cases. Recently, it has been shown that nanoparticles embedded in rubber composites can offer remarkable reinforcement effects.4–7 Among these nanoparticles, graphene flake (GF), a monolayer of sp2-hybridized carbon atoms, has attracted tremendous attention in recent years owing to its exceptional thermal, mechanical, and electrical properties.8–10 In particular, the access to exfoliated graphene oxide (GO) and reduced graphene oxide (RGO) has accelerated the use of chemically modified graphene in scale-up productions. Adding GO and RGO to polymers has been reported for enhancing the mechanical, electrical, and thermal properties of polymer nanocomposites.11–13 Moreover, GFs-based polymer composites are highly desirable in many practical applications such as electronic devices, electromagnetic shielding, and thermal management.14,15 Prud'Homme et al.16 added RGO into several rubbers, including NR, styrene butadiene rubber (SBR) and poly(dimethyl siloxane). Zhan et al.17,18 developed RGO/NR composites by mixing NR latex with an aqueous GO suspension using ultrasonication, followed by an in situ reduction. However, few studies have been reported to date on using GO and RGO as multi-functional fillers for rubber composites.19–21 In addition, due to the high-level defects and disruption of the π-orbital structure of GO and RGO, the GO and RGO based rubber composites do not allow control over specific rubber matrices and tuning of their physical properties.22 Thus, the use of low defect GFs in rubber composites offers great promise for improving their performance.
The dispersibility of the GFs and their interfacial interactions with rubber matrixes are critical for improving performance, which can be achieved through surface functionalization of the GFs. However, in the case of GO, the functional groups unavoidably damage the structure of graphene sheets, thus compromising the properties of the composites. Functionalizing GFs while preserving their high dispersibility and intrinsic properties is a major challenge for various applications of the nanocomposites. Solution mixing23,24 has been considered in this study as an effective way to obtain the desired dispersion, because conventional mechanical blending methods cannot uniformly disperse the GFs sheets in the rubber matrix.
Herein, we introduce a method for synthesizing multifunctional GFs-rubber composites using highly soluble, low defect GFs (l-GFs) fabricated by exfoliation from expanded graphite. To date, several methods have been reported on the fabrication of low-defect GFs, including solvent25 or surfactant-assisted exfoliation26,27 and the use of graphite intercalation compounds (GICs).28–30 Thus, the poor dispersibility and small flake sizes of the GFs in a rubber matrix should be improved to achieve better performance. In this study, the fabrication of micrometer-scale (over 1 μm) l-GFs and surface functionalization were simultaneously achieved by mild sonication of expanded graphite in n-methyl-2-pyrrolidone (NMP). The l-GFs were used as fillers for the first time in rubber composites, which offer improved mechanical, electrical and thermal properties. Furthermore, the l-GFs/rubber composites were prepared by aqueous-phase mixing of colloidal exfoliated l-GFs and SBR latex. This process not only plays a key role in preventing the aggregation of l-GFs during co-coagulation but also intimately bridges the l-GFs and rubber at the interfaces. The l-GFs embedded rubber matrix shows remarkable enhancement in electrical and thermal conductivity at low loadings, with unprecedentedly higher reinforcing efficiency. In addition, the preparation method is water-mediated, green, and scalable, and shows great potential in improving the performance of composite rubbers in various applications.
2. Experimental
Preparation of graphene oxide
Graphene oxide was obtained from SP-1 graphite (Bay Carbon) using the modified Hummers method. The oxidation product was purified by rinsing with a 10% HCl solution, repeatedly washing with copious amounts of de-ionized water, and filtering through an Anodisc aluminium oxide (AAO, 0.2 μm pores, Whatman) filter. The filtered material was dried under vacuum (80 °C, 12 h).
Preparation of l-GFs and dispersion
Worm-like expanded graphite (WEG) is a well-known material usually produced from various intercalation compounds submitted to a thermal shock. In this study, WEG was prepared by a conventional acid process combined with thermal exfoliation. First, GICs were synthesized from natural graphite (with a purity of 99 wt%). For the intercalation, pristine natural graphite flakes were mixed with a mixture (20
:
1 by volume) of concentrated sulfuric acid (98 wt%) and hydrogen peroxide (30 wt%). The obtained mixture was then stirred for about 1 h and then washed with de-ionized water until the pH level reached the neutral value of 7, which was confirmed with a pH tester. After drying at 100 °C for 24 h, the expandable graphite was obtained. When the GICs were heated at a certain temperature (200–1000 °C), the decomposition of the intercalating acid led to a sudden and dramatic increase in the dimension perpendicular to the graphene sheets. In this experiment, the expansion process was carried out at 900 °C by rapidly heating the GIC sample for 20 s. The obtained WEG was subjected to a final exfoliation to obtain a monolayer or a few layers of graphene sheets (l-GFs) by ultrasonication and centrifugation of a 1-methyl-2-pyrrolidinone (NMP) suspension (0.1 mg mL−1) of the sample. The l-GFs were filtered and washed with de-ionized (DI) water using a 0.1 micron Anodisc filter to remove the salts and residual solvent. The product was dried at 100 °C in a furnace. To measure the yield of l-GFs, the dispersed graphene flakes were filtered using an Anodisc aluminium oxide (AAO, 0.2 μm pores, Whatman) filter and washed with warm distilled water (pH 2). We carefully avoided sedimented graphene flakes during the filtrating process. After drying for 24 h, the yield of graphene flakes was discreetly measured on the basis of weight change. The yield of l-GFs was estimated to be 30 wt%. The l-GFs (10 mg) were dispersed in 30 ml of various solvents (acetone, DMF, THF, ethanol, pyridine, methanol, and water) with sonication for 3 hours. All the solvents were purchased from Sigma-Aldrich. After 2 weeks, absorbance (A) was measured for each suspension. After making a baseline with each pure solvent, a quartz cell was filled with the l-GF suspension and pure solvent with different concentrations such as 1
:
2, 2
:
1, and 3
:
0.
Preparation of rubber composites
The carbon materials/SBR composites were prepared by following standard procedures. First, SBR latex (20 phr) was mixed with 5 phr (parts per hundred rubber by weight) of carbon black, graphite, GO, and l-GFs by vigorous stirring for 24 h. During coagulation, a small amount of butadiene–styrene–vinyl–pyridine rubber (VPR) was added. The VPR plays a key role in the prevention of aggregation of l-GFs, and acts as an interface-bridge between l-GFs and SBR. The carbon nanomaterials/SBR emulsion was then coagulated by a 1.0 phr sulfuric acid solution. The coagulated composites were washed with water until the pH of the filtered water reached 6–7 and then they were dried in an oven at 50 °C for 24 h. Subsequently, 80 phr SBR and carbon materials (5 phr)/SBR emulsion (20 phr) were mixed with 50 phr carbon black in a Banbury mixer at a rotor speed of 60 rpm for master batches. The additives and vulcanization agents were added at the end so that the curing process of the mixture could be started. The compounds were placed in an aluminum mold and cured at 160 °C for T90, which is defined as the time to achieve 90% cure by rheometer under pressure. The formulations of the carbon materials/SBR composites are summarized in Table S1.†
Characterization
The morphology of the l-GFs was analysed using an atomic force microscope (AFM, SPA400, SII, Japan) in tapping mode under ambient conditions. X-ray photoelectron spectroscopy (XPS, Sigma Probe, AlKα) and transmission electron microscopy (TEM, Tecnai G2 F30) analyses were conducted. TEM samples were prepared by drying a droplet of the l-GFs suspensions on a carbon grid. A thermogravimetric analysis (TGA, NETZSCH TG 209 F3 Tarsus, Germany) was performed at a heating rate of 10 °C min−1 under Ar atmosphere. Raman spectra were obtained from 1200 to 3000 cm−1 using a Raman spectrometer (LabRAM HR UV/Vis/NIR, excitation at 514 nm). The FT-IR spectrum was measured using an FT-IR-4100 type-A FT-IR spectrometer with pure KBr as the background from 1000 and 3000 cm−1. Thermal conductivity was measured with a LFA 447. A thermal imaging camera (AX8, MDS Technology Co., Ltd) was used to obtain temperature curves of the SBR composites with GO and l-GFs according to time. Scanning electron microscopy (SEM, JEOL JSM-6490LV) was used to observe the morphology of the fractured surface of the rubber composites. The specimens were fractured in liquid nitrogen and the cross surfaces of samples were coated with gold using a sputtering process. Curing characteristics were measured over 30 min periods at 160 °C using a moving-die rheometer (DRM-100(LP-171)). Tensile tests were carried out in an Instron tensile machine (Instron Co., UK) at crosshead speed of 300 mm min−1. The dumbbell shape samples were 100 mm in thickness and 5 mm in width. At least four tests were carried out for each case.
3. Results and discussion
The overall process for fabricating the l-GFs/rubber composites is illustrated in Fig. 1. First, an established acid process combined with thermal exfoliation was used to develop the worm-like expanded-graphite (WEG) (Fig. 1b). The l-GFs dispersions were then prepared by sonicating the mixture of WEG and NMP for 1 h using a bath sonicator (Fig. 1c). The l-GF/rubber composite with SBR latex was synthesized through aqueous-phase mixing (Fig. 1d). The SBR (80 phr) with 5 phr (parts per hundred rubber by weight) CB, graphite, GO and l-GFs in the SBR latex (20 phr) were prepared, followed by the addition of additives and vulcanization agents for the curing process (see details in Experimental) (Fig. 1e).
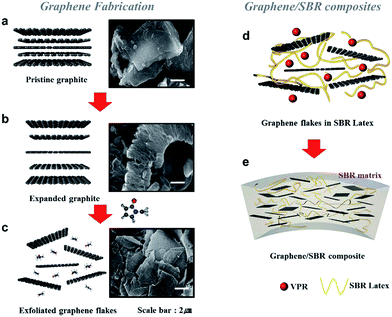 |
| Fig. 1 Schematic diagram showing the overall processing for preparing the l-GFs and l-GFs/SBR composites. (a) Schematic model and SEM images of graphite. (b) Schematic model and SEM images of expanded graphite prepared by a conventional acid process combined with a thermal shock method. (c) Schematic model and SEM images of the l-GFs prepared by solvent exfoliation in NMP. (d) Coagulation of the l-GFs aqueous solution and SBR latex. VPR: butadiene–styrene–vinyl–pyridine rubber. (e) Schematic model image of l-GFs/SBR composites. | |
Fig. 2a is a representative atomic force microscopy (AFM) image of the topography of the as-prepared l-GFs. The result shows the flakes are ∼2 μm in lateral size and 1–2 nm in height, which corresponds to a mono- or bi-layer graphene.12 A histogram plotted as a function of size and thickness (Fig. S2.1†) is obtained from the AFM image (20 μm × 20 μm). Additional AFM images are also shown in Fig. S2.2.† High-resolution transmission electron microscopy (HRTEM) images and the corresponding fast Fourier transform (FFT) pattern of the l-GFs in Fig. 2b and S2.3,† respectively, show a single layer l-GF as evidenced by the observation of the fringe pattern at the edge of the flake. The diffraction patterns indicate good crystallinity of the single layer l-GFs.31 This is also confirmed by the Raman spectra in Fig. 2c, where the D-band (∼1350 cm−1) for the l-GFs is extremely low compared to the ones for GO or RGO.32 The D to G (∼1580 cm−1) ratio is ∼0.25, suggesting a minor disorder in the sp2 carbon lattice and low defect of the flakes. The X-ray diffraction (XRD) patterns of different carbon materials are shown in Fig. 2d, in which the GO shows a peak at 11.4° corresponding to the (002) inter-planar spacing of 7.75 Å, while the graphite shows a peak at 28.6° corresponding to a d-spacing of 3.35 Å. In the case of the l-GFs, a broadened peak can be observed at 21.4° (d-spacing of 0.42 nm), suggesting that the loosely stacked exfoliated l-GFs are different from the Bernal stacking of graphite.
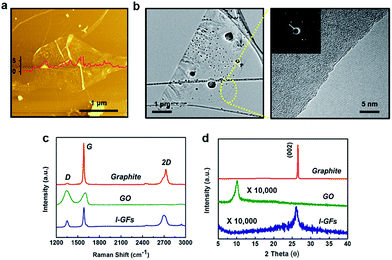 |
| Fig. 2 Characterization of the as-prepared l-GFs. (a) AFM images of the l-GFs on a mica substrate. (b) HRTEM image and fringe patterns of the monolayer l-GFs (inset). (c) Raman spectra of graphite, GO and l-GFs. The low ID/IG value of ∼0.25 indicates the high quality of the as-prepared l-GFs. (d) XRD patterns of graphite, GO and l-GFs. | |
The surface functionalization of l-GFs is confirmed by spectroscopic methods and thermogravimetric analysis (TGA). The carbon bonding state of the l-GFs was examined by X-ray photoelectron spectroscopy (XPS), and the results shown in Fig. 3a. All the C1s signals (I: GO and II: l-GFs) consist of C–C bond (284.5 eV) of sp2 carbon in the basal plane, C–O bond (286.4 eV) and C
O bond (288.2 eV) of carbonyl group, and OH–C
O bond (290.1 eV) of carboxylic group. However, the atomic ratio of oxygen in the l-GFs is 11.2%, which is significantly lower than that of the GO. The detailed values and fitting results of the individual peaks are given in the ESI Table S2 and Fig. S2.4.† FT-IR spectroscopy shows the presence of carboxylic moieties on the surface of the l-GFs (Fig. S2.5†). The TGA data in Fig. S2.6† show that the weight loss of the l-GFs is approximately 36.5 wt% in the region for the sublimation of functional groups in comparison with that of graphite. Fig. 3b presents the correlation between the absorbance (A) and concentration (c) measured by UV-Vis spectroscopy, indicating that the functionalized l-GFs can be readily re-dispersed in a range of organic solvents without aggregation. It is also shown in Fig. 3c that the l-GFs are not only stabilized in solutions with δp + δh of 13–29, in accordance with the findings reported by Ruoff et al.,33 but also are well dispersed in methanol and water with δp + δh > 29. Therefore, surface functionalization greatly improves the dispersibility of l-GFs, which facilitates the homogeneous incorporation of l-GFs into nanocomposites with SBR latex.
 |
| Fig. 3 Surface functionalization of the as-prepared l-GFs. (a) High-resolution XPS spectra of graphite, GO and l-GFs, with the C1s XPS spectra of the (I) GO and (II) l-GFs on silicon oxide substrates. The O/C atomic ratio of GO is higher than that of the l-GFs. The l-GFs spectra were deconvoluted into three peaks corresponding to sp2, COOH, and C O. (b) optical absorbance slopes at an excitation wavelength of ∼660 nm as a function of the l-GFs concentration in each solvent, showing Lambert–Beer behavior. Inset: l-GFs can form uniform dispersions but with different dispersing abilities in different solvents. Acetone shows the best dispersing ability according to the straight line fitting. (c) Dispersibility of the l-GFs in the solvents and their Hansen solubility parameter. | |
The physical properties of the rubber composites with l-GFs embedded SBR have been examined, along with those based on other integrated carbon materials, including CB, graphite, and GO.
Fig. 4a shows a comparison of the modulus and tensile strength among the SBR composites with different embedded carbon materials (5 phr loading ratio). The composites with l-GFs embedded SBR show an increase of the modulus by as much as 40%, without decrease in the tensile strength. The increased reinforcement can be attributed to the large contact area between l-GFs and rubber matrix in the SBR composite, as well as the coagulation of the l-GFs and SBR via the surface functional groups that enhance the interfacial adhesion and restrict the motion of rubber segmental chains. The insets of Fig. 4a and S2.7† show the scanning electron microscopy (SEM) images of the fracture rubber composites. The l-GFs/SBR exhibits roughened fractured surface, indicating the stronger interfacial adhesion between the l-GFs and SBR matrix. Furthermore, the fully exfoliated l-GFs and their good dispersion in the rubber composites also improve the gas barrier property. The formation of a tortuous path around the fillers in the rubber composite can result in low gas permeability by restraining the progression of gas molecules through the matrix. Fig. 4b shows a comparison of the gas-permeability and relative permeability of the l-GF/rubber composites with that of other carbon material embedded composites. The lowest oxygen transmission rate (OTR) value was obtained for the l-GFs/rubber composites as 6.87 × 10−14 m4 sec−1 N−1. The l-GFs/rubber composites show a 35% enhancement in barrier performance compared to the CB embedded composites, and a 22% enhancement compared to the GO/rubber composites. This result may be attributed to the lower defected l-GFs and their high dispersibility. The outstanding gas barrier property of the l-GFs/rubber composites is promising for applications as tire inner liners and rubber tubes. The dynamic mechanical properties, such as storage modulus and tan
δ (defined as the loss modulus to storage modulus ratio) of CB/SBR, GO/SBR, and l-GFs/SBR composites, versus temperature are depicted in Fig. 4c and d, respectively. The dynamic mechanical properties are important because many engineering rubbers are frequently subjected to dynamic loading. The storage modulus, reflecting the elastic response of a rubber, is a measure of the recoverable strain energy in the rubber. The storage modulus of the l-GFs embedded composites increases by as much as 100% relative to the CB embedded ones, and by 67% compared with that of the GO/SBR composites, indicating that the elastic response of the SBR towards deformation is strongly influenced by the presence of the l-GFs. Moreover, the addition of l-GFs to the SBR matrix decreases Tg (glass transition temperature) to −32.8 °C, while it is −26.1 °C for the control and −28.9 °C for the GO/SBR composites, respectively. The tan
δ of the l-GFs/SBR is also considerably lower than that of the control, implying an effective alleviation in the heat build-up and damping capability of the SBR systems.34
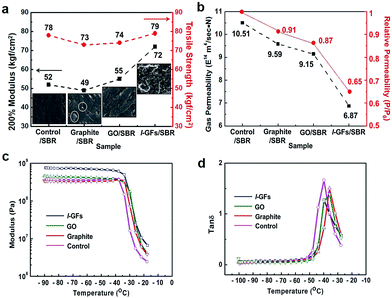 |
| Fig. 4 Mechanical property and gas permeability of the SBR composites. (a) Modulus and tensile strength of the SBR composites with graphite, GO and l-GFs. Inset: SEM images of the fracture surfaces of the SBR composites. (b) Gas permeability and relative permeability of the SBR composites at 5 phr loading of the carbon materials. (c) Storage modulus curves and (d) tan δ curves of the SBR composites with graphite, GO and l-GFs. | |
The curing curves of the l-GF and other carbon material embedded rubber composites are shown in Fig. 5a. The parameters of the curing properties are listed in Table S2.† All the rubber composites show three different regions, which are (i) the scorch delay or induction period as the torque of compounds decreases, (ii) the vulcanizing when the curing reaction occurs, leading to a sharp increment of the torque with the formation of a network structure, and (iii) a plateau of curing curve when the network is stabilized through equilibrium. The MH − ML (Δ torque) value of the l-GFs/SBR (network crosslink density of vulcanization) increases compared to those of the other SBR composites. This supports the improved mechanical properties of the l-GFs/SBR composites in Fig. 4. Furthermore, the cure time of the l-GFs embedded composites is shorter than that of the GO/SBR composites, which is due to the enhanced thermal transition of the SBR through l-GFs. This indicates that the l-GFs with high thermal conductivity offer stronger crosslinking with the SBR during vulcanization. Fig. 5b shows the thermal and electrical conductivities of the rubber composites with different embedded carbon materials. The thermal conductivity of the l-GFs composites at 5 phr loading in SBR is 0.3445 W mK−1, which is considerably higher than those of the other composites. The l-GFs/rubber composites also show better filler performance than the GO/SBR composites due to their high quality and outstanding dispersibility. In addition, the increased phonon scattering at the defects in the GO may also affect the thermal conductivity of the composites.35,36 The electrical conductivity (31 kΩ) of the l-GFs/SBR composites is one order of magnitude higher than that (249 kΩ) of the GO/SBR composites due to the high quality l-GFs, as shown in Fig. 5b. The intimate interfacial bonding between l-GFs and the polymer matrix may be responsible for the superior thermal and electrical conductivities. Fig. 5c shows that the thermal absorption and the emission in the l-GFs composites are more efficient than in the GO/SBR composites. In addition, the thermal conductivity of the composites was characterized at temperatures (T) ranging from 100 to 300 K in Fig. 5d. The thermal conductivity of the l-GFs/SBR composites decreases nearly linearly as T decreases from 300 to 150 K, and the T-dependence weakens below 150 K. Similar trends can be observed for other carbon material embedded rubber composites. This linear temperature-dependent behavior is consistent with the Umklapp phonon scattering, which is characteristic for crystalline materials, including graphene.14 Pure SBR samples do not exhibit apparent temperature dependence over the temperature range.
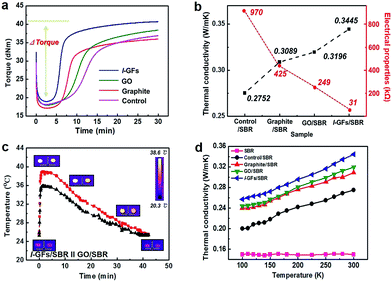 |
| Fig. 5 Thermal and electrical properties of the SBR composites. (a) Curing properties of the l-GFs/SBR composites. (b) Thermal and electrical conductivities of the SBR composites. (c) Temperature changes of the SBR composites with GO and l-GFs as a function of time captured by a thermal imaging camera. (d) Temperature dependence of the thermal conductivity for different SBR composites. | |
4. Conclusions
In conclusion, we have demonstrated that l-GFs can be facilely integrated into a rubber matrix by a novel, versatile, and simple approach, involving preparing functionalized low defect GFs (l-GFs) and producing rubber composites with SBR. The l-GFs embedded rubber composites, compared with composites based on other carbon materials, show improved mechanical, thermal, electrical, and gas barrier properties, which result from the high quality of the l-GFs, and their better dispersibility and interfacial bonding with the matrix. The functional groups lead to the good dispersibility of the l-GFs in aqueous or various organic solvents, facilitating their mixing, blending or dispersing processes. The results show that the l-GFs offer more advantages as fillers than CB and GO for producing rubber composites at low loading levels. This study may shed light on the scalable production of l-GFs-based rubber composites for different applications.
Acknowledgements
We thank the NEXEN Tire for fabricating Rubber composites.
Notes and references
- J. L. Leblanc, Prog. Polym. Sci., 2002, 27, 627–687 CrossRef CAS.
- S. H. Song, H. K. Jeong and Y. G. Kang, J. Ind. Eng. Chem., 2010, 16, 1059–1065 CrossRef CAS PubMed.
- A. I. Medalia, Rubber Chem. Technol., 1991, 64, 481–492 CrossRef CAS.
- S.-H. Song, O. S. Kwon, H.-K. Jeong and Y.-G. Kang, Korean J. Mater. Res., 2010, 20, 104–110 CrossRef CAS PubMed.
- C. A. Rezende, F. C. Braganca, T. R. Doi, L. T. Lee, F. Galembeck and F. Boue, Polymer, 2010, 51, 3644–3652 CrossRef CAS PubMed.
- S. H. Song, H. K. Jeong, K. Y. Gu and C. T. Cho, Polymer, 2010, 34, 108–115 CAS.
- Z. Ali, H. H. Le, S. Ilisch, T. Thurn-Albrecht and H. J. Radusch, Polymer, 2010, 51, 4580–4588 CrossRef CAS PubMed.
- Y. W. Zhu, S. Murali, W. W. Cai, X. S. Li, J. W. Suk, J. R. Potts and R. S. Ruoff, Adv. Mater., 2010, 22, 5226 CrossRef CAS PubMed.
- A. K. Geim and K. S. Novoselov, Nat. Mater., 2007, 6, 183–191 CrossRef CAS PubMed.
- O. C. Compton and S. T. Nguyen, Small, 2010, 6, 711–723 CrossRef CAS PubMed.
- Y. Q. Li, T. Yu, T. Y. Yang, L. X. Zheng and K. Liao, Adv. Mater., 2012, 24, 3426–3431 CrossRef CAS PubMed.
- S. H. Song, K. H. Park, B. H. Kim, Y. W. Choi, G. H. Jun, D. J. Lee, B.-S. Kong, K.-W. Paik and S. Jeon, Adv. Mater., 2013, 25, 732–737 CrossRef CAS PubMed.
- Y. Q. Li, R. Umer, Y. A. Samad, L. X. Zheng and K. Liao, Carbon, 2013, 55, 321–327 CrossRef CAS PubMed.
- A. A. Balandin, Nat. Mater., 2011, 10, 569–581 CrossRef CAS PubMed.
- Z. P. Chen, C. Xu, C. Q. Ma, W. C. Ren and H. M. Cheng, Adv. Mater., 2013, 25, 1296–1300 CrossRef CAS PubMed.
- R. Prud'Homme, B. Ozbas, I. Aksay, R. Register and D. Adamo, US Pat., US7745528B2, 2010.
- Y. H. Zhan, J. K. Wu, H. S. Xia, N. Yan, G. X. Fei and G. P. Yuan, Macromol. Mater. Eng., 2011, 296, 590–602 CrossRef CAS PubMed.
- Y. H. Zhan, M. Lavorgna, G. Buonocore and H. S. Xia, J. Mater. Chem., 2012, 22, 10464–10468 RSC.
- X. Bai, C. Y. Wan, Y. Zhang and Y. H. Zhai, Carbon, 2011, 49, 1608–1613 CrossRef CAS PubMed.
- Z. H. Tang, X. H. Wu, B. C. Guo, L. Q. Zhang and D. M. Jia, J. Mater. Chem., 2012, 22, 7492–7501 RSC.
- B. Y. Chen, N. Ma, X. Bai, H. M. Zhang and Y. Zhang, RSC Adv., 2012, 2, 4683–4689 RSC.
- Z. Jia, M. B. Tucker and T. Li, Compos. Sci. Technol., 2011, 71, 365–372 CrossRef CAS PubMed.
- C. X. Li, J. Adamcik and R. Mezzenga, Nat. Nanotechnol., 2012, 7, 421–427 CrossRef CAS PubMed.
- S. Stankovich, D. A. Dikin, G. H. B. Dommett, K. M. Kohlhaas, E. J. Zimney, E. A. Stach, R. D. Piner, S. T. Nguyen and R. S. Ruoff, Nature, 2006, 442, 282–286 CrossRef CAS PubMed.
- Y. Hernandez, V. Nicolosi, M. Lotya, F. M. Blighe, Z. Y. Sun, S. de, I. T. McGovern, B. Holland, M. Byrne, Y. K. Gun'ko, J. J. Boland, P. Niraj, G. Duesberg, S. Krishnamurthy, R. Goodhue, J. Hutchison, V. Scardaci, A. C. Ferrari and J. N. Coleman, Nat. Nanotechnol., 2008, 3, 563–568 CrossRef CAS PubMed.
- M. Lotya, Y. Hernandez, P. J. King, R. J. Smith, V. Nicolosi, L. S. Karlsson, F. M. Blighe, S. de, Z. M. Wang, I. T. McGovern, G. S. Duesberg and J. N. Coleman, J. Am. Chem. Soc., 2009, 131, 3611–3620 CrossRef CAS PubMed.
- M. Lotya, P. J. King, U. Khan, S. de and J. N. Coleman, ACS Nano, 2010, 4, 3155–3162 CrossRef CAS PubMed.
- L. M. Viculis, J. J. Mack and R. B. Kaner, Science, 2003, 299, 1361 CrossRef CAS PubMed.
- K. H. Park, D. Lee, J. Kim, J. Song, Y. M. Lee, H. T. Kim and J. K. Park, Nano Lett., 2014, 14, 4306–4313 CrossRef CAS PubMed.
- S. H. Song, M. H. Jang, J. Chung, S. H. Jin, B. H. Kim, S. H. Hur, S. Yoo, Y. H. Cho and S. Jeon, Adv. Opt. Mater., 2014, 2, 1016–1023 CrossRef CAS PubMed.
- W. T. Gu, W. Zhang, X. M. Li, H. W. Zhu, J. Q. Wei, Z. Li, Q. K. Shu, C. Wang, K. L. Wang, W. C. Shen, F. Y. Kang and D. H. Wu, J. Mater. Chem., 2009, 19, 3367–3369 RSC.
- M. Jin, H. K. Jeong, T. H. Kim, K. P. So, Y. Cui, W. J. Yu, E. J. Ra and Y. H. Lee, J. Phys. D: Appl. Phys., 2010, 43, 275402 CrossRef.
- S. Park, J. H. An, I. W. Jung, R. D. Piner, S. J. An, X. S. Li, A. Velamakanni and R. S. Ruoff, Nano Lett., 2009, 9, 1593–1597 CrossRef CAS PubMed.
- J. Liu, Y. L. Lu, M. Tian, F. Li, J. X. Shen, Y. Y. Gao and L. Q. Zhang, Adv. Funct. Mater., 2013, 23, 1156–1163 CrossRef CAS PubMed.
- S. Shenogin, A. Bodapati, L. Xue, R. Ozisik and P. Keblinski, Appl. Phys. Lett., 2004, 85, 2229–2231 CrossRef CAS PubMed.
- M. T. Hung, O. Choi, Y. S. Ju and H. T. Hahn, Appl. Phys. Lett., 2006, 89, 023117 CrossRef PubMed.
Footnote |
† Electronic supplementary information (ESI) available: Further details of AFM image of l-GFs according to the size and thickness, AFM image of l-GFs, HRTEM images of l-GFs, XPS analysis of GO and l-GFs, FT-IR analysis of graphite, GO and l-GFs, Thermal gravimetric analysis (TGA) of graphite, GO and l-GFs, SEM images of rubber composite, formation of rubber composites, and curing properties of rubber composites]. See DOI: 10.1039/c5ra16446j |
|
This journal is © The Royal Society of Chemistry 2015 |
Click here to see how this site uses Cookies. View our privacy policy here.