DOI:
10.1039/C5RA16127D
(Paper)
RSC Adv., 2015,
5, 78061-78070
Synthesis of Pt doped Mg–Al layered double oxide/graphene oxide hybrid as novel NOx storage–reduction catalyst†
Received
11th August 2015
, Accepted 9th September 2015
First published on 9th September 2015
Abstract
We report the synthesis of Pt doped Mg–Al layered double oxide/graphene oxide (Pt–LDO/GO) hybrid as novel NOx storage and reduction (NSR) catalyst. For the preparation of layered double hydroxide/GO hybrids, LDHs and graphite oxide were first exfoliated into single-layers, followed by self-assembly. LDO/GO hybrids were obtained by thermal treatment of LDH/GO. The obtained LDH/GO and LDO/GO hybrids were thoroughly characterized using XRD, SEM, TEM, FT-IR, and BET analyses. Then the NOx storage capacity of neat LDO and LDO(10)/GO hybrids were compared by isothermal NOx adsorption tests. The influence of adsorption temperature, gas flow, calcination temperature, and LDH dispersion concentration were systematically studied. The results demonstrated that the NOx storage capacity of neat LDO was significantly improved from 0.175 to 0.314 mmol g−1 by introducing only 7 wt% of GO, which could be attributed to the enhanced particle dispersion and stabilization. Moreover, the NOx storage capacity of the hybrid could be further increased close to 0.335 mmol g−1 catalyst by doping with 2 wt% Pt. The Pt–LDO(1)/GO also exhibited excellent lean-rich cycling performance, with an overall 71.7% of NOx removal. This work provided a new scheme for the preparation of highly dispersed LDH/GO hybrid type NSR catalyst.
1. Introduction
Nitrogen oxides (NOx) from vehicle emissions contribute much to the depletion of tropospheric ozone, production of photochemical smog, acid rain and some human diseases.1 Conventional three-way catalysts (TWCs) are highly efficient in reducing NOx, CO, and unburned hydrocarbon (HC) emissions from gasoline engines, which work at stoichiometric air/fuel ratio (A/F = 14.7).2,3 However, the general demand for more fuel-efficient gasoline engines has led to the development of lean-burn engines that operate at a significantly higher air/fuel ratio (A/F > 14.7).4–6 For lean-burn engines, the concentration of O2 (percentage level) is so high that only very little reducing agents left in the exhaust gas and the reduction of NOx emissions on a TWC falls to very low levels. The reduction of NOx under lean operating conditions is perhaps the greatest challenge in this field.7
To achieve an efficient abatement of NOx from lean-burn engines, several technologies such as selective catalytic reduction (SCR), and NOx storage–reduction (NSR), etc. have been developed during the last few decades.8–10 There is a general consensus that NSR technology represents, at the moment, as one of the most promising solutions for the elimination of NOx from vehicle emissions. The NSR catalysts operate alternatively under lean and rich conditions. During lean operation, NOx in the exhaust gases is adsorbed onto the catalyst as nitrate species; while during rich operation, the stored NOx is converted to nitrogen by unburned hydrocarbons.11,12 Typical NSR catalysts consist of a high-surface-area support (e.g., γ-Al2O3, TiO2, ZrO2, TiO2–ZrO2, etc.), a NOx-storage component (an alkaline earth metal oxide, e.g., Ba, K, Ca, Mg, etc.), and a noble metal (e.g., Pt, Rh, etc.) that is active for both NO oxidation and stored NOx reduction. Presently, Pt/BaO/Al2O3 system is regarded as model NSR catalyst and has been extensively studied.13–18 However, such catalyst system also exhibited some drawbacks, e.g., inadequate NOx storage capability, limited operating temperature, thermal degradation, and sulfur poisoning, etc.19,20 For these reasons, new type of NSR catalysts are highly demanded.
LDHs are a class of ionic lamellar compounds that consist of positively charged brucite-like layers.21 Fornasari et al.22 reported that Pt and Pt–Cu dispersed on a LDH-derived mixed oxide (LDO) MgAlOx support showed greater NOx storage capacity at 200 °C and better sulfur tolerance than Pt/BaO/Al2O3. Lamb et al.23 reported a novel NOx NSR catalyst consisting of Pd dispersed on LDH derived MgAlOx, which showed four-fold greater storage capacity than neat MgAlOx. It is believed that reducing the particle size of LDH can increase its NOx storage capacity.24 However, it is difficult to further reduce the particle size lower than 20 nm owing to the layered feature of LDHs. In this contribution, we report that the delamination of LDHs into single layer may be the most effective solution to this problem.25 The delaminated nanosheets have an exceedingly high two-dimensionality (2D) with molecular thickness, higher specific surface area, and more degree of freedom, etc. However, the strong surface charge density of LDHs monolayer makes it easy to restack and difficult to be separated from solution. In order to tackle the restacking and separation issue, making LDHs based hybrid materials by mixing the positively charged LDHs suspension together with another negatively charged nanoparticles suspension using the electrostatic self-assembly has been reported as an efficient method to solve this problem.
Graphene oxide (GO), as one of the most important derivatives of graphene, contains several kinds of oxygen functional groups, such as hydroxyl, epoxide, carbonyl, and carboxyl groups, on its basal planes and edges.26–29 Taking these abundant oxygen functional groups into consideration, GO can be not only well dispersed in water to yield a stable colloidal suspension, but also potentially used as nanoscale 2D building blocks for the fabrication of GO based hybrid materials.30 Very recently, the investigation of GO and GO based hybrid materials for absorbents has become a hot topic. Garcia-Gallastegui et al.31 synthesized LDH/GO hybrid material by co-precipitation method for CO2 capture, and confirmed that both the CO2 sorption capacity and recyclability were increased when LDHs were supported onto GO, which could be attributed to the enhanced particle dispersion. On this basic, Wang et al.32 demonstrated a new approach for the preparation of LDH-based hybrid-type adsorbents for CO2 capture through electrostatically driven self-assembly between positively charged Mg–Al LDH single sheet and negatively charged GO monolayer and the absolute CO2 capture capacity of LDH was increased by more than twice by adding 6.54 wt% GO.
In this work, we present the first study on the synthesis of Pt doped LDO/GO hybrid as novel NSR catalyst. The hybrid was synthesized via an “exfoliation-self-assembly” method. In principle, such assembly is beneficial for maximizing the dispersion of LDH nanosheets on the surface of GO, which can consequently increase the utilization rate of LDO as active NOx adsorption materials. The LDH, LDO, GO, and hybrid materials were thoroughly characterized. The influence of adsorption temperature, gas flow, calcination temperature, and the concentration of LDH suspension were evaluated. Finally, the NOx storage and reduction performance of 2 wt% Pt doped LDO/GO hybrid catalyst was evaluated.
2. Experimental
2.1 Synthesis of samples
2.1.1 Synthesis of Mg–Al–NO3 LDH. Mg–Al–NO3 LDH was prepared using a standard co-precipitation procedure. A salt solution (100 mL) containing a mixture of 0.075 mol Mg(NO3)2·6H2O and 0.025 mol Al(NO3)3·9H2O was added drop-wise to a basic solution (100 mL) containing 0.05 mol Na2NO3. The pH of the mixture solution was kept constant at 10 by addition of a NaOH solution (4 M). The resulting slurry was stirred continuously for about 12 h at room temperature. After aging, the sample was filtered and washed with deionized water until pH = 7, then washed with acetone for several times and dried at 60 °C in an oven. The obtained sample is denoted as Mg–Al–NO3 LDH.
2.1.2 Synthesis of graphite oxide. The graphite oxide was obtained by the modified Hummers method.33 In brief, 3 g powdered flake graphite and 1.5 g sodium nitrate were added into 69 mL concentrated H2SO4 gradually. Then 9 g KMnO4 was added gradually with stirring while keeping the temperature of the mixture below 20 °C with ice-bath. The mixture was then stirred at 35 °C for 2 h, followed by the addition of 138 mL distilled water. After another 30 min stirring, another 420 mL distilled water was then added to terminate reaction. Subsequently, 3 mL 30% H2O2 was added and the colour of the mixture changed to bright yellow. The mixture was centrifuged and washed with 10% HCl solution to remove residual metal ions. The precipitate was then washed with Milli-Q water and centrifuged repeatedly until the pH value closed to 6. Then it was dried at 60 °C in an oven.
2.1.3 Delamination of LDHs. For the delamination of LDHs, 1 g Mg–Al–NO3 LDH was put into 100 mL formamide, followed by magnetic stirring until no sediment was observed upon standing. The concentration of delaminated Mg–Al–NO3 LDH dispersion can be controlled to be 1–10 g L−1, which is marked as LDH(1), LDH(2.5), LDH(5), LDH(7.5) and LDH(10).
2.1.4 Delamination of graphite oxide. To delaminate graphite oxide, the precipitate was treated by ultra-sonication at 700 W for 1 h and then filtered by centrifuging at 8000 rpm for 8 min. The delaminated graphite oxide was obtained in the supernatant. The precipitate was delaminated repeatedly. The concentration of delaminated graphite oxide dispersion, which was 1 g L−1, was determined by drying 100 mL of supernatant at 60 °C for 2 days, followed by measuring the mass using electronic balance. The obtained sample was denoted as GO.
2.1.5 Preparation of LDO/GO hybrid. The hybrid containing exfoliated Mg–Al–NO3 LDH and GO nanosheets was prepared by simply mixing the above obtained LDH and GO suspensions together by utilizing the electrostatic self-assembly principal. The concentration of GO suspension was 1 g L−1, and the concentration of LDH suspensions was controlled at 1, 2.5, 5, 7.5, and 10 g L−1, respectively. Five different LDH/GO hybrids were prepared by varying the LDH/GO volume ratios of 100/7, 100/17.5, 100/35, 100/52.6, 100/70 as shown in Table 1. The precipitation was centrifuged under 6000 rpm for 5 min, followed by washing with Milli-Q water and anhydrous ethanol repeatedly to remove water and formamide completely. After drying at 60 °C for 24 h, the LDH/GO hybrid was obtained. The obtained samples were denoted as LDH(1)/GO, LDH(2.5)/GO, LDH(5)/GO, LDH(7.5)/GO and LDH(10)/GO. The LDO(1)/GO, LDO(2.5)/GO, LDO(5)/GO, LDO(7.5)/GO, and LDO(10)/GO hybrids can be obtained by simply thermal treatment of the corresponding LDH/GO.
Table 1 The concentration and volume of LDH and GO suspensions used for the preparation of LDH/GO hybrids
Concentration of LDH suspension (g L−1) |
Volume of LDH suspension (mL) |
Concentration of GO suspension (g L−1) |
Volume of GO suspension (mL) |
wt% GO in hybrids |
1 |
100 |
1 |
7 |
7 |
2.5 |
100 |
1 |
17.5 |
7 |
5 |
100 |
1 |
35 |
7 |
7.5 |
100 |
1 |
52.6 |
7 |
10 |
100 |
1 |
70 |
7 |
2.1.6 Preparation of Pt doped Mg–Al LDO/GO hybrid catalyst. For the preparation of Pt doped LDO/GO hybrid type NSR catalyst, LDH/GO hybrid was first calcined at 400 °C for 5 h in air to get LDO/GO. Then 2 wt% Pt was doped on to LDO/GO hybrid using an impregnation method. In brief, 0.2 g LDO/GO hybrid, 0.106 mL H2PtCl6·6H2O ethanol solution (100 g L−1), and 20 mL ethanol were mixed together and stirred for 6 h at room temperature, followed by drying at 60 °C oven for 12 h. The obtained sample was further calcined at 400 °C for 5 h in air.
2.2 Characterizations of samples
Powder XRD analyses were conducted on a Shimadzu XRD-7000 X-ray diffractometer with Cu Kα radiation. Diffraction patterns were recorded within the range of 2θ = 5–70° with a scanning rate of 5° min−1 and a step size of 0.02°. The morphology of samples was characterized using field emission scanning electron microscope (FE-SEM, SU-8010). High resolution transmission electron microscopy (HR-TEM) images were obtained on a JEOL 2010, operating at 200 kV. Samples were prepared by dispersing the sample in isopropanol (10 mg L−1), and allowing a drop to dry onto a holey carbon copper grid (300 mesh, Agar Scientific). Fourier transform infrared spectrometer (FT-IR) experiments were performed using a FTS 3000 MX FT-IR spectrophotometer. Zeta potential of delaminated LDHs and GO suspensions were measured using a zeta potential analyzer (Nanosizer Nano ZS, Malvern Instruments). The BET specific surface areas (SSA) were measured from the N2 adsorption and desorption isotherms at 77 K collected from an ASAP 2020 physisorption analyzer (Micromeritics). Before each measurement, fresh samples were first degassed at 110 °C for overnight, while the calcined samples were degassed at 220 °C for overnight. The thermal stability of samples was evaluated using a thermo gravimetric analyzer (TGA, TA Q50) in the temperature range of 20–700 °C and in the presence of air.
2.3 NOx adsorption and reduction over catalysts
All these catalytic activity tests were performed in a fixed bed flow reactor (10 mm internal diameter). The NOx storage capacity of neat Mg–Al LDO, LDO/GO hybrid, and Pt doped LDO/GO hybrid catalyst were investigated by isothermal NOx storage at some certain temperatures. The NOx concentration of the inlet and outlet gases was monitored using an on-line NOx analyzer (Thermo Scientific 42i-HL). For each test, 0.2 g sample that was pre-calcined at 400 °C for 5 h in air was employed. The feed gas contains 700 ppm of NOx, 10% O2, and Ar as the balance gas, with a flow rate of 100 mL min−1. The NOx storage capacity (NSC) was calculated according to the following eqn (1). |
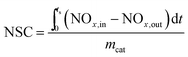 | (1) |
For the NOx lean and rich cycling tests, the duration of lean and rich period was controlled to be 12 min and 2 min, respectively. The lean condition is same to the isothermal NOx storage tests. The rich condition contains 700 ppm of NOx, 3.5% H2 in Ar balance and with a flow rate of 100 mL min−1. The NOx and produced N2 were monitored using an on-line quadrupole mass spectrometer (QGA, Hidden).
3. Results and discussion
3.1 XRD and zeta potential analysis
For the preparation of LDH suspension, Mg–Al–NO3 LDH powder was delaminated in formamide. By magnetically stirring for 24 h, a clear transparent colloidal LDH suspension could be obtained. The XRD data recorded without drying (Fig. 1(a)) exhibited a pronounced halo in a 2θ range of 20–30°, which was ascribed to the scattering of formamide. The absence of the characteristic basal peaks clearly suggested that the host sheets were not sufficiently stacked together to give coherent scattering of X-rays.24 Therefore, it could be concluded that the LDH had been delaminated into individual nanosheets. For the preparation of GO suspension, graphite oxide was delaminated in water by ultra-sonication at 700 W for 1 h. Fig. 1(b) shows the XRD patterns of graphite, graphite oxide and graphene oxide. As we expected, a strong and sharp peak (26.7°), corresponding to a layer space of 0.335 nm, was the typical diffraction peak (002) of graphite. After the graphite was oxidized, the peak (002) disappeared and a wide diffraction peak (11.2°) appeared. The interlayer space was increased to 0.794 nm, which due to the introducing of the oxygen-containing functional groups, the water molecules, and other molecules after the oxidation of graphite.
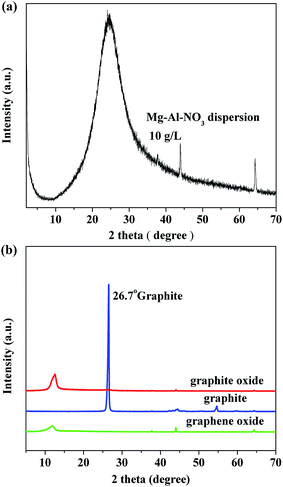 |
| Fig. 1 XRD patterns of (a) delaminated Mg–Al–NO3 LDH (10 g L−1), and (b) graphite oxide, graphite, and graphene oxide. | |
The zeta potential of positively exfoliated Mg–Al–NO3 LDH nanosheet colloidal suspension and the negatively charged GO suspension were measured (Table 2), which was +26.8 and −21.9 mV, respectively. This data suggested that both of these two dispersions were stable and well-dispersed. Due to the opposite charge of these two dispersions, LDH(10)/GO hybrid could be synthesized by electrostatic self-assembly of Mg–Al–NO3 LDH and GO nanosheets.
Table 2 Zeta potential analysis of the Mg–Al–NO3 LDH suspension in formamide and the GO suspension in water
Suspensions |
Zeta potential (mV) |
Zeta deviation (mV) |
Conductivity (mS cm−1) |
LDH suspension |
26.8 |
8.5 |
0.213 |
GO suspension |
−21.9 |
10.5 |
0.282 |
Fig. 2 shows the XRD patterns of neat Mg–Al–NO3 LDH and the as synthesized LDH(1)/GO, LDH(2.5)/GO, LDH(5)/GO, LDH(7.5)/GO and LDH(10)/GO. Neat LDH exhibited diffraction peaks at 2θ = 10.72°, 21.83° and 34.6°, which are the hydrotalcite-like characteristic reflections of (003), (006), and (009) peaks (JCPDS no. 22-0700), representing R3m symmetry and a hexagonal lattice.34 The well defined (110) and (113) diffraction peaks at 60.50° and 61.60° reveal a quite good dispersion of metal ions in the brucite-like layers.35 After calcination at 400 °C, the LDHs phases were completely destroyed and mixed oxide derivatives were formed (Fig. 2 LDO(10)/GO). For the calcined sample, three peaks with the 2θ angle centered at 35°, 43°, and 63° can be ascribed to the periclase-type MgO (JCPDS 45-0946). In the case of the LDH/GO hybrids prepared with different LDH dispersions, the diffraction peaks were almost identical to those of the pristine Mg–Al–NO3 LDH, and no characteristic peak of GO was observed.
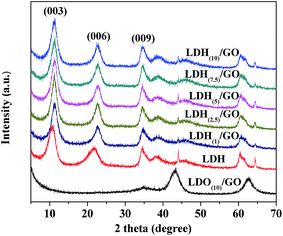 |
| Fig. 2 XRD patterns of LDH/GO hybrids prepared with different LDH suspensions (the concentration of LDH ranges from 1 to 10 g L−1) and the LDO(10)/GO hybrid. | |
3.2 FT-IR analysis
Fig. 3 shows the FT-IR spectra of GO, LDH, and different LDH/GO hybrids, ranging from 4000 to 400 cm−1. The spectrum of GO powder shows the O–H stretching mode at 3400 cm−1, C
O at 1677 cm−1, C
C at 1575 cm−1 originating from the skeletal vibrations of un-oxidized graphitic domains, C–O–C and C–O at 925–1445 cm−1 in epoxy or alkoxy.36–40 For Mg–Al LDH, the broad band centred at 3500 cm−1 corresponds to the O–H stretching vibration of the surface, the vibration of angular deformation of H2O molecules was seen at 1636 cm−1, the bands centred at 1382 cm−1 in the spectrum are attributed to a strong interaction of nitrate anions within the layer, the bands centred at 655–584 cm−1 are attributed to Al–O and Mg–O vibrations.41 The C
O and C
C peaks from GO were seen in the hybrids, indicating the successful hybridization of GO with LDH. In addition, with the decrease in the LDH concentration used for the preparation of the hybrids, the intensities of C
O and C
C peaks increased, which suggests a better dispersion of GO in the hybrids.
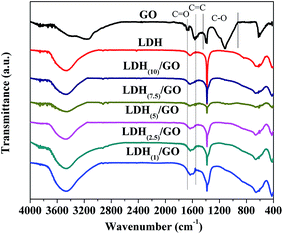 |
| Fig. 3 FT-IR spectra of graphite oxide, Mg–Al–NO3 LDH, and LDH/GO hybrids prepared with different LDH suspensions (the concentration of LDH ranges from 1 to 10 g L−1). | |
3.3 BET analysis
It is well known that textural properties, including the surface area and pore size distribution, play important roles for the performance of adsorption and catalysis. The N2 adsorption/desorption isotherms and the corresponding pore size distributions of LDH, LDO, LDH(10)/GO, and LDO(10)/GO are shown in Fig. 4. It could be seen that both the fresh and calcined samples exhibited Brunauer–Deming–Deming–Teller (BDDT)-type I and IV shape of isotherms with an H3-type hysteresis loop (P/P0 > 0.4) in the IUPAC classification, indicating the existence of mesopores in all samples. The specific surface area of LDO(10)/GO hybrid was 309.1 m2 g−1, which was much larger than that of neat LDO (220.1 m2 g−1). It has been proven that the addition of GO can decrease the aggregation of LDO, resulting in more exposed LDO nanosheets and enlarged specific surface area.42 From the pore size distribution curves of the four samples, we can see that both LDH(10)/GO and LDO(10)/GO hybrids showed narrow pore size distribution (3.73–3.98 nm) than that of pure LDH (33.72–33.83 nm), which was due to the introduction of GO. Such a unique mesoporous structure could provide efficient transport pathways to NOx storage and reduction process, which was beneficial to the adsorption properties of the material. Similarly, the specific surface area of other LDO/GO hybrids were also analyzed, which are 262.0, 264.3, 279.4, and 262.9 m2 g−1 for the LDO(1)/GO, LDO(2.5)/GO, LDO(5)/GO, and LDO(7.5)/GO hybrids, respectively. These data demonstrated that all the LDO/GO hybrids have much higher specific surface area than neat LDO.
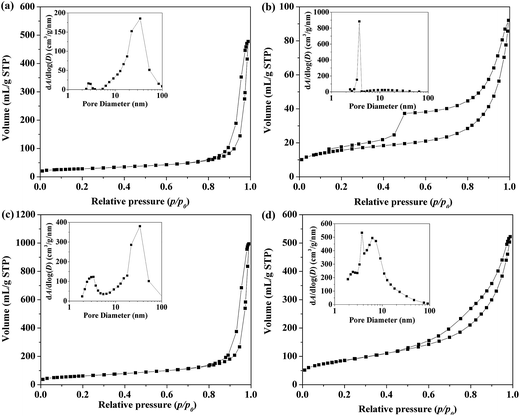 |
| Fig. 4 BET isotherm patterns of (a) fresh Mg–Al–NO3 LDH, (b) fresh Mg–Al–NO3 LDH(10)/GO hybrids, (c) Mg–Al LDO, (d) Mg–Al LDO(10)/GO hybrids, the inset shows the pore size distribution. | |
3.4 SEM and TEM analysis
The morphology of the LDH bulk, delaminated LDH and GO nanosheets, and the LDH(10)/GO hybrid catalyst were characterized by means of SEM and HR-TEM analysis, as shown in Fig. 5. Before delamination, the Mg–Al–NO3 LDH bulk showed a typical flower-like morphology, with a large number of nanosheets aggregated together (Fig. 5(a)). However, after delamination, very thin LDH nanosheets with translucent plate-like morphology could be clearly seen, as shown in Fig. 5(b). These typical two-dimensional nanoplates had a lateral size of ca. 0.5–1 μm. Due to the fracture or breakage of the sheets during delamination the nanoplatelets had a reduced size in comparison to the original LDHs. Fig. 5(c) shows the TEM image of delaminated GO nanosheets, which exhibited a typical wrinkled morphology of graphene oxide. The observed thin and curled nanosheets are consistent with previous reports.43–45 The TEM image of LDH(10)/GO hybrid was shown in Fig. 5(d), which indicates that the GO and LDH well mixed together.
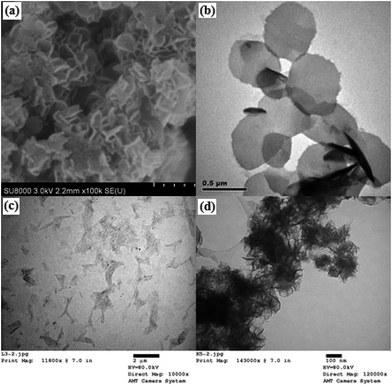 |
| Fig. 5 (a) FE-SEM of Mg–Al–NO3 LDH. HR-TEM image of (b) delaminated Mg–Al–NO3 LDH, (c) graphene oxide, (d) LDH(10)/GO hybrid. | |
Since it plays a key role in promoting the steps of NSR catalysis such as NO oxidation and adsorbed NOx reduction, XRD, FE-SEM, and HR-TEM analyses were conducted to study the size and state of doped Pt in the catalysts. Fig. 6(a) shows the XRD pattern of 2 wt% Pt doped LDO(10)/GO hybrid catalyst, in which only the LDO(10)/GO hybrid was detected. The absence of Pt diffraction peaks suggests that the Pt might be highly dispersed in the catalysts. In order to confirm the existence of Pt, SEM-EDS analysis was performed, as shown in Fig. 6(b) and (c). The Pt nanoparticles were so small that they could not be seen in the SEM images. However, the EDS analysis in three sites (as highlighted in Fig. 6(b)) confirmed the existence of Pt with an average Pt loading of 2.08 ± 0.42 wt%. This value is consistent with the theoretical amount used for the preparation. The existence of Pt and its average particle size on LDO(10)/GO hybrid was further investigated using HR-TEM, as shown in Fig. 7. Well dispersed Pt nanoparticles were clearly seen in Fig. 7(a). TEM image with higher resolution in Fig. 7(b) shows that the average particle size doped Pt was around 2.68–3.50 nm. These data confirmed that the dope Pt was highly dispersed in the hybrid catalyst, which is consistent with both the XRD and SEM analyses.
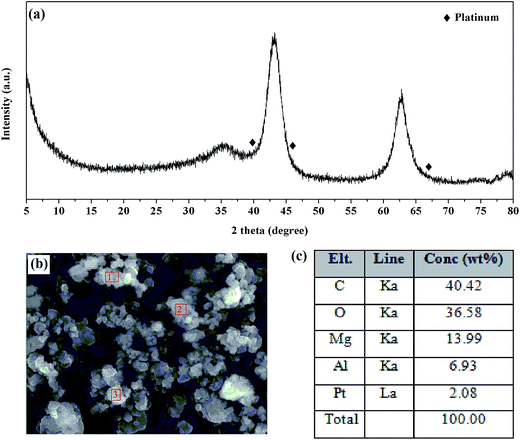 |
| Fig. 6 (a) XRD patterns of Pt–LDO(10)/GO hybrid, (b) SEM-EDS image of Pt–LDO(10)/GO hybrid, and (c) elemental mapping data of Pt–LDO(10)/GO hybrid. | |
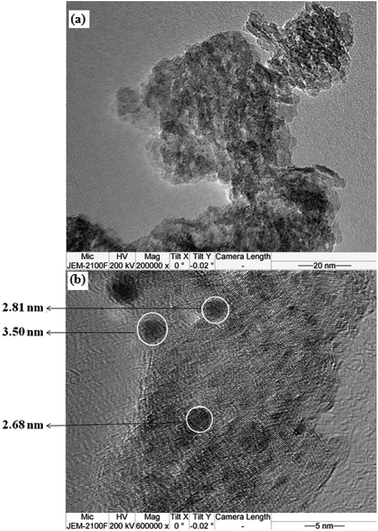 |
| Fig. 7 (a) TEM image of Pt–LDO(10)/GO hybrid catalyst, (b) TEM image with higher resolution. | |
3.5 NOx storage performance tests
For LDH itself, it does not have any basic sites. However, upon thermal treatment, the LDH gradually loses interlayer water, and then dehydroxylates and decarbonates to a large extent, leading to the formation of a mixed oxide with a 3D network. The active Mg–O species which induced either by the substitution of Mg2+ by Al3+ in the periclase MgO lattice, or by the diffusion of Al3+ out of the octahedral brucite layers are normally believed to be the adsorption sites.41 And the adsorbed NOx species were determined to be nitrates and nitrites.23 In order to determine the optimal NOx storage temperature of LDO(10)/GO hybrid, isothermal NOx storage in the temperature range of 250–400 °C were tested. Fig. 8(a) shows the isothermal NOx storage performance of neat Mg–Al LDO at 250, 300, 350 and 400 °C, respectively. At higher temperatures (350 and 400 °C), the adsorption rate was relatively low and it took around 20 min to reach saturation. While at lower temperatures (250 and 300 °C), the samples could quickly capture NOx within the first ca. 20 min. Meanwhile, the adsorption rates were relatively high and the saturated values were reached after about 60 min. The highest NOx storage amount, around 0.175 mmol g−1, was obtained at 300 °C. Fig. 8(b) exhibits the isothermal NOx storage performance of LDO(10)/GO hybrid. For this sample, it exhibited the quickest NOx uptake and saturation at 300 °C. The reachable lowest NOx concentration was about 430 ppm and the highest NOx storage amount was 0.226 mmol g−1. Therefore, these data suggest that the absolute NOx storage capacity of LDO can be significantly increased by adding 7 wt% GO as, from 0.175 to 0.226 mmol g−1.46,47
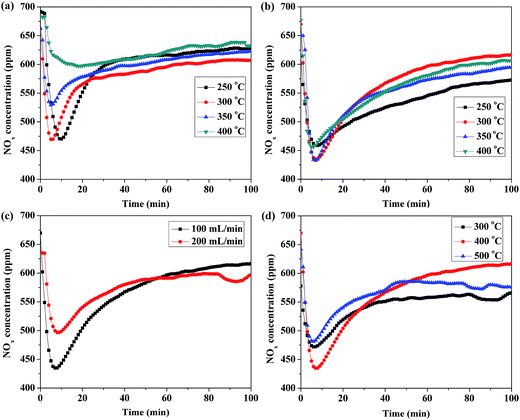 |
| Fig. 8 (a) Isothermal NOx storage over Mg–Al LDO at 250, 300, 350, and 400 °C, (b) isothermal NOx storage over Mg–Al LDO(10)/GO at 250, 300, 350, and 400 °C, (c) isothermal NOx storage over LDO(10)/GO hybrid with different SV, and (d) isothermal NOx storage over LDO(10)/GO hybrids calcined at 300, 400, and 500 °C. | |
In the meantime, the influence of other three important factors including gas flow, calcination temperature, and the concentration of LDH suspension had also been evaluated. Gas flow, in other words, space velocity (SV), is of great significance to evaluate catalysts. Motivation for examining SV is to see whether lowering SV might improve NOx removal for vehicle applications. As shown in Fig. 8(c), lower gas flow (100 mL min−1) led to better NOx storage capacity over LDO(10)/GO hybrid, owning to more contact time with catalyst in the mixture gas. Furthermore, it is clearly that calcination temperature affects the structure, surface composition, redox ability and the basicity of the catalyst, which consequently influence the NSR performance of the catalyst. Fig. 8(d) shows the isothermal storage of NOx with different calcination temperatures. Compared to the catalyst calcined at 400 °C, the ones calcined at 300 and 500 °C showed slightly lower NOx storage capacity. Consequently, it can be concluded that the optimal calcination temperature was 400 °C for LDO(10)/GO hybrid.
It has been reported that the exfoliation of LDHs is an interesting route for producing positively charged thin platelets with a thickness of a few atomic layers. Five LDH dispersions with different concentrations from 1 to 10 g L−1 were synthesized. Fig. 9 clearly shows that lower LDH dispersion concentration contributed much higher on NOx storage capacity for the reason that both LDH and GO dispersed uniformly in lower dispersion concentration and more specific surface areas and adsorption sites might be created. In conclusion, the highest adsorption amount reached to 0.314 mmol g−1 when the LDH dispersion was 1 g L−1, which was much higher than that of neat Mg–Al LDO (0.175 mmol g−1).
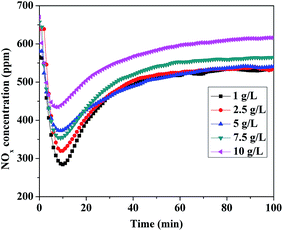 |
| Fig. 9 Isothermal NOx storage over LDO/GO hybrids that was prepared from the LDH dispersions ranging from 1 to 10 g L−1 at 300 °C. | |
For the NSR catalysts, noble metal such as Pt is necessary for both the NO oxidation to NO2 during lean condition and the adsorbed NOx reduction during rich condition. Thus, the influence of Pt doping on LDO and LDO(10)/GO hybrid was also studied, as shown in Fig. 10. Noticeably, after doping with Pt, the NOx storage capacity of LDO and LDO(10)/GO was increased from 0.175 and 0.226 mmol g−1 to 0.240 and 0.335 mmol g−1 at 300 °C, respectively. This improvement in NOx storage capacity can be attributed to promoted NO oxidation to NO2 by Pt, and NO2 is easier than NO to be adsorbed on the catalyst. This data suggests that the doping with Pt is favourable not only for NOx reduction but also for NOx adsorption.
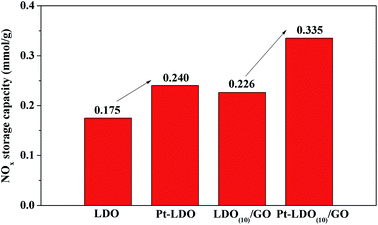 |
| Fig. 10 The NOx storage capacity of LDO, Pt–LDO, LDO(10)/GO, and Pt–LDO(10)/GO tested at 300 °C. | |
3.6 NOx storage–reduction cycles
Fig. 11(a) shows the NOx storage and reduction cycling tests over 2 wt% Pt–LDO(1)/GO hybrid at 300 °C. During lean periods (12 min), NO was first oxidized to NO2 by Pt and then adsorbed on LDO(1)/GO hybrid. The NOx profiles obtained during the lean periods showed almost the same shape. A sharp NOx removal peak appeared just once the Pt–LDO(1)/GO hybrid was put in contact with the gas mixture NO + O2, which was might due to the storage of NOx on the strongest adsorption sites created upon reduction. And the NOx level reached a more or less constant value afterwards. During rich periods (2 min), the adsorbed NOx reacted with reducing reagent (3.5% H2) in the presence of Pt. Because of the high reductive activity of Pt, the main product was N2 (Fig. 11(b)). Comparing to N2, the N2O peaks are much weaker and smaller, suggesting that the selectivity of the NOx conversion to N2 is relatively high. By integrating the difference between the input and output, we determined that 71.7% of NOx could be removed during the whole lean-rich cycling periods. The thermal stability of the catalyst is another important issue. Fig. S1† shows the TGA analyses of LDO/GO and calcined GO in the temperature range of 20–700 °C and in the presence of air. The data indicates that the calcined GO is thermally stable up to 400 °C, without any weight loss was observed. And once it was hybridized with LDO, its thermal stability seems to be significantly improved. By increasing the calcination temperature to 700 °C, there was only a slight decrease in weight. Since the operating temperature of this novel catalyst is ca. 300 °C, the thermal stability of the catalyst is not considered as a problem. Considering its thermal and cycling stability, it shows great potential to work as a NSR catalyst with improved NOx storage ability.
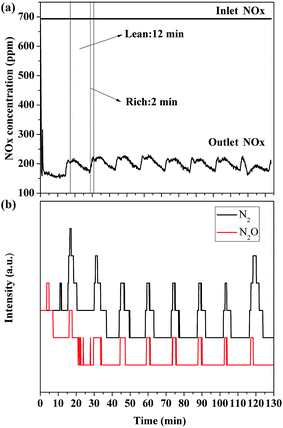 |
| Fig. 11 (a) Evolution of effluent NOx during lean-rich cycling test over 2 wt% Pt–LDO(1)/GO hybrid at 300 °C, and (b) evolution of effluent N2 and N2O during lean-rich cycling test over 2 wt% Pt–LDO(1)/GO hybrid at 300 °C. | |
4. Conclusions
A novel NSR catalyst Pt–LDO/GO consisting of exfoliated LDO and GO singles layers was prepared. The Mg–Al–NO3 LDH was delaminated into single nanosheets in formamide and the GO was obtained by exfoliation of graphite oxide in water through ultra-sonication. The obtained Pt–LDO/GO hybrid was thoroughly characterized. All LDH/GO hybrids possess much larger specific surface area of 262.0–309.1 m2 g−1 than that neat LDO (220.1 m2 g−1). The addition of GO decreased the aggregation of LDOs and resulted in more exposed LDO nanosheets and enlarged specific surface area. The Pt nanoparticles were well dispersed with an average particle size of ca. 2.68–3.50 nm. The results demonstrated that the optimal calcination temperature and operating temperature was 400 and 300 °C, respectively. The NOx storage capacity of neat LDO was significantly improved from 0.175 to 0.314 mmol g−1 by introducing only 7 wt% of GO, which could be attributed to the enhanced particle dispersion and stabilization. The LDO/GO hybrid prepared with lower LDH concentration showed higher NOx storage capacity, and the highest NOx storage capacity was obtained with LDO(1)/GO hybrid. Moreover, the NOx storage capacity of the hybrid could be further increased close to 0.335 mmol g−1 catalyst by doping with 2 wt% Pt. The Pt–LDO(1)/GO also exhibited excellent lean-rich cycling performance, with an overall 71.7% of NOx removal. This work provided a new scheme for the preparation of highly dispersed LDO/GO hybrid type NSR catalyst.
Acknowledgements
This work is supported by the National Natural Science Foundation of China (51308045), the Beijing Nova Programme (Z131109000413013), and the Program for New Century Excellent Talents in University (NCET-12-0787).
References
- S. Heylen, S. Smeekens, C. Kirschhock, T. Parac-Vogt and J. A. Martens, Energy Environ. Sci., 2010, 3, 910–916 CAS.
- B. H. Engler, D. Lindner, E. S. Lox, A. Schäfer-Sindlinger and K. Ostgathe, Stud. Surf. Sci. Catal., 1995, 96, 441 CrossRef CAS.
- J. G. Nunan, H. J. Robota, M. J. Cohn and S. A. Bradley, J. Catal., 1992, 133, 309 CrossRef CAS.
- R. D. Clayton, M. P. Harold and V. Balakotaiah, Appl. Catal., B, 2008, 84, 616 CrossRef CAS PubMed.
- L. I. Landong, C. Jixin, Z. Shujuan, Z. Fuxiang, G. Naijia, W. Tianyou and L. Shuliang, Environ. Sci. Technol., 2005, 39, 2841 CrossRef.
- H. Y. Huang, R. Q. Long and R. T. Yang, Energy Fuels, 2001, 15, 205 CrossRef CAS.
- F. Basile, G. Fornasari, A. Grimandi, M. Livi and A. Vaccari, Appl. Catal., B, 2006, 69, 58 CrossRef CAS PubMed.
- A. Baiker, P. Dollenmeier and M. Glinski, Appl. Catal., 1987, 35, 351 CrossRef CAS.
- M. Koebel, M. Elsener and M. Kleemann, Catal. Today, 2000, 59, 335 CrossRef CAS.
- Y. Li and J. N. Armor, Appl. Catal., B, 1993, 2, 239 CrossRef CAS.
- N. Takahashi, H. Shinjoh, T. Iijima, T. Suzuki, K. Yamazaki, K. Yokota, H. Suzukib, N. Miyoshib, S. Matsumotob, T. Tanizawab, T. Tanakab, S. Tateishic and K. Kasahara, Catal. Today, 1996, 27, 63 CrossRef CAS.
- N. Miyoshi, S. I. Matsumoto, K. Katoh, T. Tanaka, J. Harada, N. Takahashi, K. Yokota, M. Sugiura and K. Kasahara, SAE Tech. Pap., 1995, 950809 Search PubMed.
- W. S. Epling, L. E. Campbell, A. Yezerets, N. W. Currier and J. E. Parks, Catal. Rev., 2004, 46, 163 Search PubMed.
- S. Roy and A. Baiker, Chem. Rev., 2009, 109, 4054 CrossRef CAS PubMed.
- L. Lietti, P. Forzatti, I. Nova and E. Tronconi, J. Catal., 2001, 204, 175 CrossRef CAS.
- I. Nova, L. Castoldi, L. Lietti, E. Tronconi and P. Forzatti, Catal. Today, 2002, 75, 431 CrossRef CAS.
- L. Castoldi, I. Nova, L. Lietti and P. Forzatti, Catal. Today, 2004, 96, 43 CrossRef CAS PubMed.
- M. Piacentini, M. Maciejewski and A. Baiker, Appl. Catal., B, 2005, 59, 187 CrossRef CAS PubMed.
- D. Uy, K. A. Wiegand, A. E. O'Neill, M. A. Dearth and W. H. Weber, J. Phys. Chem. B, 2002, 106, 387 CrossRef CAS.
- C. Sedlmair, K. Seshan, A. Jentys and J. A. Lercher, Catal. Today, 2002, 75, 413 CrossRef CAS.
- J. S. Valente, M. Sánchez-Cantú, E. Lima and F. Figueras, Chem. Mater., 2009, 21, 5809 CrossRef CAS.
- G. Fornasari, F. Trifiro, A. Vaccari, F. Prinetto, G. Ghiotti and G. Centi, Catal. Today, 2002, 75, 421 CrossRef CAS.
- B. A. Silletti, R. T. Adams, S. M. Sigmon, A. Nikolopoulos, J. J. Spivey and H. H. Lamb, Catal. Today, 2006, 114, 64 CrossRef CAS PubMed.
- L. Li, R. Ma, Y. Ebina, N. Iyi and T. Sasaki, Chem. Mater., 2005, 17, 4386 CrossRef CAS.
- W. Hou, L. Kang, R. Sun and Z. H. Liu, Colloids Surf., A, 2008, 312, 92 CrossRef CAS PubMed.
- J. H. Seol, I. Jo, A. L. Moore, L. Lindsay, Z. H. Aitken, M. T. Pettes, X. S. Li, Z. Yao, R. Huang, D. Broido, N. Mingo, R. S. Ruoff and L. Shi, Science, 2010, 328, 213 CrossRef CAS PubMed.
- M. Acik, G. Lee, C. Mattevi, M. Chhowalla, K. Cho and Y. J. Chabal, Nat. Mater., 2010, 9, 840 CrossRef CAS PubMed.
- L. P. Biró, P. Nemes-Incze and P. Lambin, Nanoscale, 2012, 4, 1824 RSC.
- S. Mao, H. Pu and J. Chen, RSC Adv., 2012, 2, 2643 RSC.
- X. Huang, X. Qi, F. Boey and H. Zhang, Chem. Soc. Rev., 2012, 41, 666 RSC.
- A. Garcia-Gallastegui, D. Iruretagoyena, V. Gouvea, M. Mokhtar, A. M. Asiri, S. N. Basahel, S. A. Al-Thabaiti, A. O. Alyoubi, D. Chadwick and M. S. P. Shaffer, Chem. Mater., 2012, 24, 4531 CrossRef CAS.
- J. Y. Wang, X. Y. Mei, L. Huang, Q. W. Zheng and Y. Q. Qiao, J. Energy Chem., 2015, 24, 127 CrossRef.
- W. S. Hummers Jr and R. E. Offeman, J. Am. Chem. Soc., 1958, 80, 1339 CrossRef.
- F. Cavani, F. Trifirò and A. Vaccari, Catal. Today, 1991, 11, 173 CrossRef CAS.
- A. E. Palomares, A. Uzcátegui and A. Corma, Catal. Today, 2008, 137, 261 CrossRef CAS PubMed.
- I. Y. Kim, J. M. Lee, T. W. Kim, H. N. Kim, H. I. Kim, W. Choi and S. J. Hwang, Small, 2012, 8, 1038 CrossRef CAS PubMed.
- Y. R. Lee, I. Y. Kim, T. W. Kim, J. M. Lee and S. J. Hwang, Chem.–Eur. J., 2012, 18, 2263 CrossRef CAS PubMed.
- Z. Huang, P. Wu, B. Gong, Y. Fang and N. Zhu, J. Mater. Chem., 2014, 2, 5534 RSC.
- L. Li, R. Z. Ma, Y. Ebina, K. Fukuda, K. Takada and T. Sasaki, J. Am. Chem. Soc., 2007, 129, 8000 CrossRef CAS PubMed.
- J. L. Gunjakar, I. Y. Kim, J. M. Lee, N. S. Lee and S. J. Hwang, Energy Environ. Sci., 2013, 6, 1008 CAS.
- Q. Wang, X. Zhang, C. J. Wang, J. Zhu, Z. Guo and D. O'Hare, J. Mater. Chem., 2012, 22, 19113 RSC.
- J. Fang, M. Li, Q. Q. Li, W. Zhang, Q. L. Shou, F. Liu, X. B. Zhang and J. P. Cheng, Electrochim. Acta, 2012, 85, 248–255 CrossRef CAS PubMed.
- H. W. Wang, Z. A. Hu, Y. Q. Chang, Y. L. Chen, Z. Q. Lei, Z. Y. Zhang and Y. Y. Yang, Electrochim. Acta, 2010, 55, 8974 CrossRef CAS PubMed.
- H. Liang, X. Miao and J. Gong, Electrochem. Commun., 2012, 20, 149 CrossRef CAS PubMed.
- Z. Wang, X. Zhang, J. H. Wang, L. Zou, Z. T. Liu and Z. P. Hao, J. Colloid Interface Sci., 2013, 396, 251 CrossRef CAS PubMed.
- N. Takahashi, K. Yamazaki, H. Sobukawa and H. Shinjoh, Appl. Catal., B, 2007, 70, 198 CrossRef CAS PubMed.
- N. Takahashi, S. I. Matsunaga, T. Tanaka, H. Sobukawa and H. Shinjoh, Appl. Catal., B, 2007, 77, 73 CrossRef CAS PubMed.
Footnote |
† Electronic supplementary information (ESI) available. See DOI: 10.1039/c5ra16127d |
|
This journal is © The Royal Society of Chemistry 2015 |
Click here to see how this site uses Cookies. View our privacy policy here.