DOI:
10.1039/C5RA16079K
(Paper)
RSC Adv., 2015,
5, 99927-99934
Light irradiation induced aerobic oxidative deep-desulfurization of fuel in ionic liquid†
Received
10th August 2015
, Accepted 9th November 2015
First published on 11th November 2015
Abstract
An aerobic oxidative deep-desulfurization process for aromatic sulfides, such as dibenzothiophene (DBT), benzothiophene (BT), 4,6-dimethyldibenzothiophene (4,6-DMDBT), was carried out via ionic liquids (ILs) extractive coupled with photochemical oxidation. In this process, sulfur compounds in n-octane were firstly extracted into the IL phase and then oxidized to corresponding sulfones. The sulfur removal efficiency of DBT with air as the oxidizing agent could reach up to 99.1% under mild conditions. Then, a possible reaction mechanism of this metal-free photochemical oxidative desulfurization system was proposed. The sulfur removal efficiency decreased slightly, even though the original S-concentration of DBT increased from 500 to 1000 ppm. The oxidation reactivity of different sulfur compounds decreased in the order of: DBT > 4,6-DMDBT > BT. The influences of alkene and aromatic addition were also investigated. Gas Chromatograph-Mass Spectrometer (GC-MS) measurements demonstrated that the sulfur compounds were converted to their corresponding sulfones and separated out of the oil phase. Under optimal conditions, the IL could be recycled at least 5 times without a remarkable decrease in activity.
Introduction
Nowadays, air pollution, primarily caused by the exhaust from motor vehicle engines, has been one of the thorniest problems in the world, especially SOx produced by the sulfide in light oil or gasoline, which would cause acid rain, fog and haze.1 To minimize these pollutions, many regulations have been formulated to reduce sulfur concentration in diesel and light oil.2 Although a hydrodesulfurization (HDS) process is employed in modern industry and can remove many organic sulfides effectively, it is hard to remove thiophene, dibenzothiophene (DBT) and 4,6-dimethyldibenzothiophene (4,6-DMDBT) due to their strong steric-hindrance3,4 and aromaticity.5 In addition to these drawbacks, its operation environment is very harsh (e.g. high pressure, high temperature). From the point of sustainable development, moderate reaction environment is searched.
Many non-HDS methods, such as extractive desulfurization (EDS)6–10 and adsorptive desulfurization (ADS),11–14 have been developed to achieve deep desulfurization (<5 ppm). Among all of these methods, oxidative desulfurization (ODS) is considered to be a promising one.15–22 In which, hydrogen peroxide (H2O2), as a most common used oxidant, is activated to OH˙ by a variety of catalysts.23–29 Then the aromatic sulfide is oxidized to corresponding sulfone which can be easily transferred out of the system as its polarity has been changed.30 Though H2O2 is a green oxidant, its potential explosion in the industrial process limits its application.31 Many other oxidants, for instance: ozone,32,33 organic peracid34 and organic hydroperoxide,35,36 are also applied in ODS process. However, these oxidants suffer from either high volatilization or high costs. All these factors compelled researchers to find greener and lower cost oxidants.
Molecular oxygen (O2), as a greener and lower cost oxidant, is easily available. However, it is inactive at room temperature and atmosphere pressure due its triplet ground state.37 Therefore, many metal-based38–41 catalysts have been employed to activate O2. Though sulfur compounds can be successfully oxidized, the reactions always call for high temperature and high pressure.31,38–40 Photocatalytic oxidative desulfurization, as a novel and more moderate oxidative method, has been developed in recent years.30,42–48 In these reactions, O2 could be effectively activated by photocatalysts (e.g. Pt–RuO2/BiVO4,30 Pt–RuO2/TiO2,42 Ag/BiWO6,44 Ag–BiVO4
47) or photosensitizers (e.g. Rose Bengal,45 N-methylquinolinium tetrafluoborate46) at room temperature and atmosphere pressure. However, these photocatalysts or photosensitizers may pollute oil as they are hard to be separated from oil phase. In addition, the metal-based catalysts could also bring about environment pollutions. Development of metal-free oxidative desulfurization system is thus a promising technology. The use of metal-free oxidation system seems to be an appropriate proposal. More recently, aldehyde has been introduced to a metal-free oxidative desulfurization system.37 It could oxidize sulfur compounds effectively after reaction with O2 under the irradiation of light. Both the precursor and product of aldehyde show no pollution to oil. On contrary, the existence of these hydrogen compounds could contribute heat when they combust in engine. However, the sulfur removal efficiency in this system is still not high.
Some reports17,49–56 have shown that ILs extractive coupled with catalytic oxidative desulfurization (ECODS) could achieve deep sulfur removal efficiency. In this paper, we find that molecular oxygen in the air can be effectively activated by isobutyraldehyde (IBA) under the irradiation of UV light at room temperature and atmosphere pressure. ILs extractive coupled with photochemical oxidative desulfurization is thus developed in this paper. Thiophenic sulfur compounds in the oil are successfully extracted to ILs phase and then oxidized to sulfone by air under the irradiation of UV light, achieving deep desulfurization. Here, we propose novel features of this reaction system as follows: (1) oxygen in air could be used as oxidant instead of explosive H2O2. (2) Development of a metal-free photochemical oxidative desulfurization system. (3) IL used in this reaction system could be recycled repeatedly.
Experimental
Materials
All chemicals used in our experiments were analytical reagent grade (A. R.) without further purification. Octane (>98%), tetradecane (>99%), formaldehyde (99%), octylaldehyde (>98.5%), cyclohexene (>99%), 1-octene (>99%), paraxylene (>99%), and carbon tetrachloride (>99.5%) were purchased from Sinopharm Chemical Reagent Co., Ltd. DBT (>98%), benzothiophene (BT, >97%) and 4,6-DMDBT (>97%) were purchased from Sigma Aldrich. Isobutylaldehyde (>98%) was purchased from Aladdin. ILs (1-butyl-3-methylimidazolium tetrafluoroborate ([Bmim]BF4, >99%), 1-butyl-3-methyl-imidazolium hexafluorophosphate ([Bmim]PF6, >99%), 1-n-octyl-3-methylimidazolium tetrafluoroborate ([Omim]BF4, >99%) and 1-n-octyl-3-methylimidazolium hexafluorophosphate ([Omim]PF6, >99%)) were purchased from Shanghai Chengjie Chemical Co., Ltd.
Photochemical oxidative desulfurization
Here, we prepared six different model oils. First three model oils were prepared by dissolving three sulfur compounds, DBT, BT, 4,6-DMDBT, in n-octane with the same sulfur contents (500 ppm), respectively. Another three model oils were prepared by dissolving different amounts of DBT in n-octane. The sulfur contents of these three model oils was 600 ppm, 800 ppm and 1000 ppm, respectively. Tetradecane was used as an internal standard.
3 mL IL and 15 mL model oil were added into a 30 mL home-made two-necked quartz flask. Fresh air was introduced to the system by an air pump at the airflow velocity of 5 mL min−1. Here, a super thermostatic water bath was used to maintain the reaction temperature. Then, a certain amount of aldehyde was added into the reaction system after extraction for 20 min. The mixture was stirred for 4 h under UV irradiation (a 250 W high pressure Hg lamp). A digital image of reaction equipment was shown in Scheme S1.†
The reaction solution samples were collected every 30 min. In the experiment, upper clear oil was collected and injected into gas chromatography (GC) (Agilent 7890A, HP-5 column, 30 m long × 0.32 mm inner diameter (id) × 0.25 μm film thicknesses) with a flame ionization detector (FID) by micro-injector to evaluate the sulfur content. The conversion of DBT, BT and 4,6-DMDBT in the model oil was used to indicate the removal of sulfur compounds. The temperature of the GC process started at 100 °C and rose to 200 °C at 15 °C min−1. Injector temperature was 300 °C and detector temperature was 250 °C. The sulfur removal efficiency was calculated as shown in eqn (1), where C0 (ppm) was the initial sulfur concentration in the model oil and Ct (ppm) was the transient sulfur concentration at any time t (min). This calculated method was accepted by almost all groups. Combine the above two reasons, this conversion rate could instead the sulfur removal efficiency.
|
Sulfur removal (%) = (1 − Ct/C0) × 100
| (1) |
After reaction, the IL phase was separated and collected in a 10 mL centrifugal tube, then 2 mL CCl4 was added into the centrifugal tube to anti-extract oxidized sulfur compounds. After 2 min vibration, the tube was aged for 10 min. Then the CCl4 phase (lower phase) was collected and analyzed by GC-Mass Spectrometer (GC-MS) (Agilent 7890/5975C – GC/Mass Selective Detector (MSD); HP-5 MS column, 30 m long × 250 mm i.d. × 0.25 μm film thicknesses). The temperature program of the GC-MS process started at 100 °C and rose to 200 °C at 15 °C min−1. The injector temperature was 250 °C. The temperature of quadrupole, ion source and AUX interface was 150 °C, 230 °C and 280 °C, respectively.
Results and discussion
Effect of different desulfurization systems on removal of DBT
Firstly, sulfur removal efficiencies with different systems were investigated in Fig. 1. Sulfur removal efficiencies were first tested with only extraction (36.2%), UV light irradiation (2.2%) and IBA addition (3.4%) with air introduced as oxidant. Then, the sulfur removal efficiencies were tested in the absence of IBA addition (extractive combined with UV light irradiation), UV light irradiation (extractive combined with IBA addition) and IL addition (UV light irradiation combined with IBA addition), respectively. The sulfur removal efficiencies without IBA addition (38.3%) and UV light irradiation (37.8%) were similar to the IL extractive desulfurization efficiency (36.2%). The result indicated that the existence of IBA in model oil was critical, but it hardly functioned in the dark environment. Though the photochemical oxidation of DBT could reach up to 57.2% without IL extraction, it couldn't achieve deep desulfurization. However, when IL was added into the reaction system, forming ECODS, the sulfur removal efficiency increased dramatically and achieved ultra-deep desulfurization (99.1%). These results showed that the ECODS system was vastly superior to other desulfurization systems, which was consisted with other researcher's work.17,49–53,55 Blank experiment with N2 import instead of air was conducted to clarify the role of air in the photochemical reaction. The sulfur removal efficiency with N2 import was only 41.3%, indicating the air introduced also played indispensable role as IL extraction, UV light irradiation and IBA addition in this reaction process.
 |
| Fig. 1 Sulfur removal efficiency with different reaction system. Reaction conditions: T = 30 °C, t = 4 h, V(model oil) = 15 mL (500 ppm), V(Omim[BF4]) = 3 mL, V(IBA) = 150 μL, ν(air) = 5 mL min−1. | |
Possible mechanism of the DBT photochemical oxidation process
The proposed mechanism of photochemical oxidation of DBT in model oil was depicted in Scheme 1. Acyl radical (RCO˙) was firstly generated from the decomposition of IBA under UV light, which was the common characteristic of many aldehydes.57 Then, the peroxy radical (RCOOO˙) was produced by the reaction of RCO˙ and O2 in air. After that, peracid was generated through reactions by snatching a hydrogen atom from other IBA or hydrogen radicals (H˙) produced before.
 |
| Scheme 1 Peracid generated under UV light irradiation. | |
Peracid, as a strong oxidizer, could oxidize sulfur compounds to sulfoxide by the –OOH group in first stage. Then, sulfoxide was further oxidized to sulfone in the same way (Scheme 2). It seems that two stoichiometric RCOOOH could oxidize one sulfide to sulfone effectively. However, in real reaction, RCOOOH would react with IBA forming two corresponding acid molecules (RCOOH). More than stoichiomertric amount of IBA, therefore, was added to the reaction system to ensure deep desulfurization of model oil.
 |
| Scheme 2 Extractive and oxidization of DBT with peracid generated. | |
To prove the reaction mechanism proposed in Scheme 1, experiments with various types of aldehydes were carried out. The same molar amount of aldehyde was added into the reaction system, respectively. As can be seen from Fig. 2, the sulfur removal efficiency increased as: n-octylaldehyde < benzaldehyde < n-butyraldehyde < IBA. The highest sulfur removal efficiency was achieved with IBA addition. This might be caused by the higher stable acyl radical (with tertiary α-carbon) it generated.58 Besides, C–H bond energy in aldehyde group of IBA (364.5 kJ mol−1)59 was relatively lower than that of n-butyraldehyde (371.2 kJ mol−1),59 which made more (CH3)2CHCO˙ radicals produced in the same environment. Though C–H bond energy in aldehyde group of benzaldehyde (371.1 kJ mol−1)60 was close to that of n-butyraldehyde, the sulfur removal efficiency decreased when benzaldehyde was chosen. However, benzene ring in the molecular could absorb UV light which would reduce the generation acyl radical. This might be a plausible explanation that could be given for the decreased sulfur removal efficiency. When n-octylaldehyde was chosen, this eight carbon aldehyde would miscible be with oil and couldn't transfer to the IL phase to participate the oxidation reaction. Finally, the sulfur removal efficiency decreased as IBA > n-butyraldehyde > benzaldehyde > n-octylaldehyde.
 |
| Fig. 2 Effect of the types of aldehyde on sulfur removal efficiency. Reaction conditions: T = 30 °C, V(model oil) = 15 mL (500 ppm), V(Omim[BF4]) = 3 mL, ν(air) = 5 mL min−1. | |
Now, we can give the specific roles what UV, IBA, IL and air played on the desulfurization process. Without UV light irradiation, acyl radicals would not be generated. Then, peracid, as a strong oxidizer, would not be generated and sulfur compounds would not be oxidized. Without IBA added, acyl radicals would not generated at the same time. Sulfur compounds would also not be oxidized. Without IL added, ECODS system would not be formed and deep desulfurization would not be achieved. Without air introduced, the produced acyl radicals would not react with oxygen in air. Then peracid would not be generated and sulfur compounds would not be oxidized. In conclusion, UV, IBA, IL and air all play important roles on the desulfurization process.
Optimization of oxidative desulfurization parameters
Sulfur removal efficiency with four common ILs, [Bmim]BF4, [Bmim]PF6, [Omim]BF4 and [Omim]PF6, was investigated and listed in Table 1. Among the ILs studied, ILs with long carbon chain, as [Omim]BF4 and [Omim]PF6, showed better extractive capacity which directly led to a better sulfur removal efficiency. This was consistent with previous studies that ILs with larger size cation would have a better extractive ability.61,62 Though [Omim]PF6 also show well extractive ability, the following studies were carried out with the addition of [Omim]BF4.
Table 1 Effect of the types of ILs on sulfur removal efficiencya
Entry |
Types of ILs |
S-removal (%) |
Extraction |
Photochemical oxidation |
Reaction conditions: T = 30 °C, t = 2 h, V(model oil) = 15 mL (500 ppm), V(IL) = 3 mL, V(IBA) = 150 μL, v(air) = 5 mL min−1. S-removal without ILs. |
1 |
[Bmim]BF4 |
18.1 |
68.9 |
|
2 |
[Bmim]PF6 |
21.4 |
73.1 |
|
3 |
[Omim]BF4 |
36.1 |
91.7 |
|
4 |
[Omim]PF6 |
33.5 |
90.0 |
|
5 |
— |
|
|
35.5b |
To further study the influence of ILs in the process of desulfurization, the effect of the amount of IL was also studied and the results were presented in Fig. 3. When the amount of IL increased from 1 mL to 3 mL, the sulfur compounds remained in the oil decreased sharply from 134.2 ppm to 41.7 ppm after reaction for 2 h. These results indicated that the amount of ILs in the reaction played a vital role in DBT removal. Thus, reaction kinetics with different IL addition was given as shown in Fig. 4. The rate constant for the apparent consumption of sulfur compound was obtained from the pseudo-first-order eqn (2) and (3) as follows:
Here,
C0 and
Ct was the sulfur concentration at time 0 and the sulfur concentration at time
t, respectively. ln(
C0/
Ct) against the reaction time was plotted in
Fig. 4. The linear fit of ln(
Ct/
C0) against the reaction time demonstrated the pseudo-first-order kinetics characteristics. The rate constants
k increased rapidly from 0.2187 h
−1 to 1.0697 h
−1. The results indicated that reaction rate accelerated significantly when the IL added as ECODS system have been formed. Finally, 3 mL [Omin]BF
4 was chosen in the following investigation.
 |
| Fig. 3 Effect of ILs ([Omim]BF4) addition amount on sulfur removal efficiency. Reaction conditions: T = 30 °C, t = 2 h, V(model oil) = 15 mL (500 ppm), V(IBA) = 150 μL, ν(air) = 5 mL min−1. | |
 |
| Fig. 4 Pseudo-first-order kinetics for oxidation with different amount of IL addition. Reaction conditions: T = 30 °C, t = 2 h, V(model oil) = 15 mL (500 ppm), V(IBA) = 150 μL, ν(air) = 5 mL min−1. | |
The effect of IBA on desulfurization process was shown in Fig. 5. When IBA was absent, the conversion of DBT to sulfone (DBTO2) happened scarcely. When the amount of IBA increased, the sulfur removal efficiency increased accordingly. The final sulfur removal efficiency could reach up to 60.7%, 90.9% and 99.1% when 50, 100 and 150 μL IBA were added, respectively. This phenomenon indicated that IBA had a vital effect on DBT removal. Finally, 150 μL IBA was chosen in the following investigation.
 |
| Fig. 5 Effect of IBA addition amount on sulfur removal efficiency. Reaction conditions: T = 30 °C, V(model oil) = 15 mL (500 ppm), V(Omim[BF4]) = 3 mL, ν(air) = 5 mL min−1. | |
Sulfur removal efficiency with different S-concentration
Considering variable S-concentration in real oils, sulfur removal efficiency with different S-concentration was investigated. As can be seen from Fig. 6, sulfur removal efficiency decreased slightly even if S-concentration of model oil increased obviously. The sulfide in the oil could be removed totally after 5 h reaction, when the initial S-concentration was 500 ppm. When the initial S-concentration increased to 600 ppm and 800 ppm, the sulfur removal efficiency could still be higher than 99.0% and 97.0% after reaction for 6 h, respectively. Though the sulfur removal efficiency decreased when the S-concentration increased to 1000 ppm, it could still reach to 93.2% after reaction for 6 h. These data showed the powerful sulfur removal efficiency of this reaction system, which was scarcely reported before.
 |
| Fig. 6 Sulfur removal efficiency of DBT with different S-concentration. Experiment condition: T = 30 °C, V(model oil) = 15 mL, V(IBA) = 150 μL, t = 6 h, V(Omim[BF4]) = 3 mL, ν(air) = 5 mL min−1. | |
Effect of different substrates on the sulfur removal efficiency
Other common thiophenic sulfides, like BT and 4,6-DMDBT, were also investigated. As shown in Fig. 7, the sulfur removal efficiency decreased in the order: DBT > BT > 4,6-DMDBT with extraction only. Here, 4,6-DMDBT showed the lowest extraction efficiency, which may be caused by the lower Nernst partition coefficient (KN) in comparison with DBT and BT.15 However, after reaction for 2 h, the sulfur removal efficiency decreased in the order: DBT > 4,6-DMDBT > BT. Obviously, BT possessed the lowest reactivity, which might be caused by the lowest electron density on the S atom.16 For DBT and 4,6-DMDBT, the electron density on the S atom was very close to each other (5.756 and 5.760 respectively).16 Thus, reactivity would mainly be affected by the steric hindrance of methyl groups existed in 4,6-DMDBT, which might become an obstacle for the approaching of active species to S atom. The sulfur removal efficiency of BT, DBT and 4,6-DMDBT was 48.6%, 91.7%, 57.9% after reaction for 2 h, respectively. For DBT, deep desulfurization (99.1%) was achieved after reaction for 4 h. However, for BT and 4,6-DMDBT, only 62.1% and 75.9% sulfur removal efficiency were achieved after reaction for 4 h. After reaction for another 4 h, sulfur removal efficiency increased little. In this experiment, the sulfur removal efficiency of BT and 4,6-DMDBT would reach to 75.5% and 86.9% after reaction for 8 h, respectively.
 |
| Fig. 7 Effect of substrate on sulfur removal efficiency. Reaction conditions: T = 30 °C, V(model oil) = 15 mL (500 ppm), V(Omim[BF4]) = 3 mL, V(IBA) = 150 μL, ν(air) = 5 mL min−1. | |
Oxidation products of three sulfur compounds were confirmed by GC-MS measurements. After reaction, CCl4 was used as an extraction agent to extract sulfur compounds from the separated IL phase. Experiments have been done to prove that he anti-extraction itself would not destroy the structure of DBT, BT and 4,6-DMDBT (Fig. S1†). The oil phase was also collected after reaction and detected. Total ion chromatogram (TIC) of model oil and the oxidized oil phase were both collected to prove that sulfur compounds were successfully removed out of the oil phase (Fig. S2†). Three different peaks were detected in the extracted CCl4 phase as can be seen from Fig. S3,† and the m/z value of each molecular ion peak was 216, 166 and 244, respectively. The above values show a difference of 32 to the mass charge ratio of DBT (m/z = 184), BT (m/z = 134) and 4,6-DMDBT (m/z = 212), which indicated that the sulfur compounds were oxidized to their corresponding sulfones.
Effect of the existence of olefin on sulfur removal efficiency
Olefin, as a component of oil, was coexisted with alkanes in diesel and light oil. The existence of olefin may reduce sulfur removal efficiency, as the double bonds in olefin may be oxidized in the strong oxidizing environment. Here, cyclohexene (cyclic olefin) and 1-octene (linear olefin) were selected as representative substances. The influence of the addition of cyclohexene and 1-octene was shown in Fig. 8 and 9, respectively. The sulfur removal efficiency decreased sharply when cyclohexene was added. The final sulfur removal efficiency decreased to 97.1%, 91.8%, 82.2% and 71.0% with 0.5 wt%, 1.5 wt%, 3 wt% and 5 wt% cyclohexene addition, respectively. While for 1-octene, the final sulfur removal efficiency remained 99.0% and 97.7% with 3 wt% and 5 wt% 1-octene addition, respectively. Here, we can conclude that the existence of cyclohexene has an obvious influence in this oxidative desulfurization system. Thus, some pretreatments need to be done to remove cyclic olefins before the oxidative desulfurization process.
 |
| Fig. 8 Effect of the existence of cyclohexene on sulfur removal efficiency. Experiment condition: T = 30 °C, V(model oil) = 15 mL (500 ppm), V(IBA) = 150 μL, V(Omim[BF4]) = 3 mL, ν(air) = 5 mL min−1. | |
 |
| Fig. 9 Effect of the existence of 1-octene on sulfur removal efficiency. Experiment condition: T = 30 °C, V(model oil) = 15 mL (500 ppm), V(IBA) = 150 μL, V(Omim[BF4]) = 3 mL, ν(air) = 5 mL min−1. | |
Effect of the existence of aromatics on sulfur removal efficiency
Aromatics, as another common component in diesel and light oil, would also have an impact of sulfur removal efficiency to some extent. Here, paraxylene was chosen as a representative substance. The influence of paraxylene addition was shown in Fig. 10. Though 10 wt% paraxylene was added, the sulfur removal efficiency didn't decreased much. After 4 h reaction, the sulfur removal efficiency decreased from 99.1% to 98.9%, 97.4% with 5 wt%, 10 wt% paraxylene addition, respectively. Though paraxylene was difficult to be oxidized in this environment, it could absorb UV light, which may have a slight negative influence on sulfur removal efficiency. Here, we can conclude that the existence of aromatics has a slight influence in this oxidative desulfurization system.
 |
| Fig. 10 Effect of the existence of paraxylene on sulfur removal efficiency. Experiment condition: T = 30 °C, V(model oil) = 15 mL (500 ppm), V(IBA) = 150 μL, V(Omim[BF4]) = 3 mL, ν(air) = 5 mL min−1. | |
Recycling of ILs
Recycling performance of IL was investigated, and the results were shown in Fig. 11. In each experiment, the oxidized oil phase was separated out, and then new model oil and isobutylaldehyde were added into the reaction flask. After 5 times recycling, sulfur removal efficiency decreased to 90.2%. The extraction ability of the recycled IL was also tested. As can be seen from Fig. 11, EDS ability decreased obviously from 36.1% to 19.7% after 5 times recycling. From the decreased EDS ability, we might conclude that the decreased sulfur removal efficiency after reaction for 4 h might be caused by the existence of saturated sulfone dissolved in IL phase. The remarkable recycling performance of the IL made this desulfurization method might be used in industrial application.
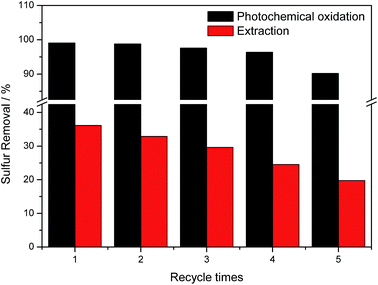 |
| Fig. 11 Investigation of recycling of ILs. Reaction conditions: T = 30 °C, t = 4 h, V(model oil) = 15 mL (500 ppm), V(Omim[BF4]) = 3 mL, V(IBA) = 150 μL, ν(air) = 5 mL min−1. | |
Conclusions
In summary, the photochemical oxidation method could effectively oxidize thiophenic sulfur compounds to their corresponding sulfones at room temperature and atmosphere pressure. Sulfur compounds in model oil were firstly extracted into ILs phase and then oxidized to corresponding sulfones, achieving deep desulfurization. The specific roles what UV irradiation, IBA addition, IL extraction and air played on the desulfurization process was confirmed according to the reaction mechanism we've proposed. Then, the experiment parameters were optimized (T = 30 °C, VIL = 3 mL, VIBA = 150 μL, v(air) = 5 mL min−1). Reaction reactivity of different substrates decreased in the order of: DBT > 4,6-DMDBT > BT, and the sulfur removal efficiency was 99.1%, 86.9% and 75.5% in the optimized environment, respectively. Cyclic olefins, such as cyclohexene, were found to have an obvious impact on sulfur removal efficiency, which indicated us that some pretreatment must to be done to reduce their content before the desulfurization process. Sulfur compounds were confirmed to be oxidized to their corresponding sulfones by GC-MS measurements. The superiority of this reaction system, such as deep sulfur removal efficiency, costless and easily available oxidant, moderate reaction environment and the well recyclability, made it more possible in practical application.
Acknowledgements
This work was financially supported by the National Nature Science Foundation of China (No. 21376111, 21376109, 21276117), Natural Science Foundation of Jiangsu Province (No. BK20131207, BK20150485), Postdoctoral Foundation of China (No. 2014M551516, 2015M570412).
References
- Y. S. Shen, P. W. Li, X. H. Xu and H. Liu, RSC Adv., 2012, 2, 1700–1711 RSC.
- T. Viveros-García, J. A. Ochoa-Tapia, R. Lobo-Oehmichen, J. A. de los Reyes-Heredia and E. S. Pérez-Cisneros, Chem. Eng. J., 2005, 106, 119–131 CrossRef.
- C. S. Song and X. L. Ma, Appl. Catal., B, 2003, 41, 207–238 CrossRef CAS.
- M. Carmen Capel-Sanchez, J. M. Campos-Martin and J. L. G. Fierro, Energy Environ. Sci., 2010, 3, 328–333 Search PubMed.
- E. Ito and J. A. R. van Veen, Catal. Today, 2006, 116, 446–460 CrossRef CAS.
- C. P. Li, D. Li, S. S. Zou, Z. Li, J. M. Yin, A. L. Wang, Y. N. Cui, Z. L. Yao and Q. Zhao, Green Chem., 2013, 15, 2793–2799 RSC.
- Q. L. Wang, L. C. Lei, J. K. Zhu, B. Yang and Z. J. Li, Energy Fuels, 2013, 27, 4617–4623 CrossRef CAS.
- N. H. Ko, J. S. Lee, E. S. Huh, H. Lee, K. D. Jung, H. S. Kim and M. Cheong, Energy Fuels, 2008, 22, 1687–1690 CrossRef CAS.
- H. S. Gao, M. F. Luo, J. M. Xing, Y. Wu, Y. G. Li, W. L. Li, Q. F. Liu and H. Z. Liu, Ind. Eng. Chem. Res., 2008, 47, 8384–8388 CrossRef CAS.
- H. P. Li, Y. H. Chang, W. S. Zhu, W. Jiang, M. Zhang, J. X. Xia, S. Yin and H. M. Li, J. Phys. Chem. B, 2015, 119, 5995–6009 CrossRef CAS PubMed.
- J. Xiao, X. X. Wang, M. Fujii, Q. J. Yang and C. S. Song, AIChE J., 2013, 59, 1441–1445 CrossRef CAS.
- C. Sentorun-Shalaby, S. K. Saha, X. Ma and C. Song, Appl. Catal., B, 2011, 101, 718–726 CrossRef CAS.
- J. J. Gao, X. Y. Chen, N. N. Ren, W. J. Wu, C. X. Li, H. Meng and Y. Z. Lu, AIChE J., 2013, 59, 2966–2976 CrossRef CAS.
- Y. S. Shen, X. H. Xu and P. W. Li, RSC Adv., 2012, 2, 6155–6160 RSC.
- J. T. Zhang, W. S. Zhu, H. M. Li, W. Jiang, Y. Q. Jiang, W. L. Huang and Y. S. Yan, Green Chem., 2009, 11, 1801–1807 RSC.
- C. Komintarachat and W. Trakarnpruk, Ind. Eng. Chem. Res., 2006, 45, 1853–1856 CrossRef CAS.
- W. Jiang, W. S. Zhu, Y. H. Chang, H. M. Li, Y. H. Chao, J. Xiong, H. Liu and S. Yin, Energy Fuels, 2014, 28, 2754–2760 CrossRef CAS.
- J. Xiong, W. S. Zhu, H. M. Li, Y. H. Xu, W. Jiang, S. H. Xun, H. Liu and Z. Zhao, AIChE J., 2013, 59, 4696–4704 CrossRef CAS.
- C. Wang, W. S. Zhu, Y. H. Xu, H. Xu, M. Zhang, Y. H. Chao, S. Yin, H. M. Li and J. G. Wang, Ceram. Int., 2014, 40, 11627–11635 CrossRef CAS.
- D. S. Zhao, Z. M. Sun, F. T. Li, R. Liu and H. D. Shan, Energy Fuels, 2008, 22, 3065–3069 CrossRef CAS.
- W. S. Zhu, B. L. Dai, P. W. Wu, Y. H. Chao, J. Xiong, S. H. Xun, H. P. Li and H. M. Li, ACS Sustainable Chem. Eng., 2015, 3, 186–194 CrossRef CAS.
- W. S. Zhu, P. W. Wu, L. Yang, Y. H. Chang, Y. H. Chao, H. M. Li, Y. Q. Jiang, W. Jiang and S. H. Xun, Chem. Eng. J., 2013, 229, 250–256 CrossRef CAS.
- Y. Q. Jiang, W. S. Zhu, H. M. Li, S. Yin, H. Liu and Q. J. Xie, ChemSusChem, 2011, 4, 399–403 CrossRef CAS PubMed.
- Y. Chen, S. Zhao and Y. F. Song, Appl. Catal., A, 2013, 466, 307–314 CrossRef CAS.
- J. M. Campos-Martin, M. C. Capel-Sanchez and J. L. G. Fierro, Green Chem., 2004, 6, 557 RSC.
- J. L. García-Gutiérrez, G. A. Fuentes, M. E. Hernández-Terán, F. Murrieta, J. Navarrete and F. Jiménez-Cruz, Appl. Catal., A, 2006, 305, 15–20 CrossRef.
- Y. H. Jia, G. Li and G. L. Ning, Fuel Process. Technol., 2011, 92, 106–111 CrossRef CAS.
- J. Zhang, A. J. Wang, X. Li and X. H. Ma, J. Catal., 2011, 279, 269–275 CrossRef CAS.
- P. W. Wu, W. S. Zhu, A. M. Wei, B. L. Dai, Y. H. Chao, C. F. Li, H. M. Li and S. Dai, Chem.–Eur. J., 2015, 21, 15421–15427 CrossRef CAS PubMed.
- F. Lin, D. E. Wang, Z. X. Jiang, Y. Ma, J. Li, R. G. Li and C. Li, Energy Environ. Sci., 2012, 5, 6400–6406 CAS.
- W. Zhang, H. Zhang, J. Xiao, Z. X. Zhao, M. X. Yu and Z. Li, Green Chem., 2014, 16, 211–220 RSC.
- C. H. Ma, B. Dai, P. Liu, N. Zhou, A. J. Shi, L. L. Ban and H. W. Chen, J. Ind. Eng. Chem., 2014, 20, 2769–2774 CrossRef CAS.
- J. L. Wang, D. S. Zhao and K. X. Li, Energy Fuels, 2010, 24, 2527–2529 CrossRef CAS.
- R. S. Drago, A. Mateus and D. Patton, J. Org. Chem., 1996, 61, 5693–5696 CrossRef CAS.
- W. Guo, C. Y. Wang, P. Lin and X. P. Lu, Appl. Energy, 2011, 88, 175–179 CrossRef CAS.
- X. R. Zhou, C. X. Zhao, J. Z. Yang and S. F. Zhang, Energy Fuels, 2007, 21, 7–10 CrossRef CAS.
- P. F. Zhang, Y. Wang, H. R. Li and M. Antonietti, Green Chem., 2012, 14, 1904–1908 RSC.
- N. F. Tang, Y. N. Zhang, F. Lin, H. Y. Lu, Z. X. Jiang and C. Li, Chem. Commun., 2012, 48, 11647–11649 RSC.
- H. Y. Lü, Y. N. Zhang, Z. X. Jiang and C. Li, Green Chem., 2010, 12, 1954–1958 RSC.
- J. T. Sampanthar, H. Xiao, J. Dou, T. Y. Nah, X. Rong and W. P. Kwan, Appl. Catal., B, 2006, 63, 85–93 CrossRef CAS.
- X. R. Zhou, J. Li, X. N. Wang, K. Jin and W. Ma, Fuel Process. Technol., 2009, 90, 317–323 CrossRef CAS.
- F. Lin, Y. N. Zhang, L. Wang, Y. L. Zhang, D. G. Wang, M. Yang, J. H. Yang, B. Y. Zhang, Z. X. Jiang and C. Li, Appl. Catal., B, 2012, 127, 363–370 CrossRef CAS.
- W. S. Zhu, Y. H. Xu, H. M. Li, B. L. Dai, H. Xu, C. Wang, Y. H. Chao and H. Liu, Korean J. Chem. Eng., 2014, 31, 211–217 CrossRef CAS.
- D. J. Wang, G. L. Xue, Y. Z. Zhen, F. Fu and D. S. Li, J. Mater. Chem., 2012, 22, 4751–4758 RSC.
- X. Y. Gu, X. Li, Y. H. Chai, Q. Yang, P. X. Li and Y. M. Yao, Green Chem., 2013, 15, 357–361 RSC.
- Y. K. Che, W. H. Ma, Y. J. Ren, C. C. Chen, X. Z. Zhang and J. C. Zhao, J. Phys. Chem. B, 2005, 109, 8270–8276 CrossRef CAS PubMed.
- X. M. Gao, F. Fu, L. P. Zhang and W. H. Li, Phys. B, 2013, 419, 80–85 CrossRef CAS.
- A. Samokhvalov, E. C. Duin, S. Nair, M. Bowman, Z. Davis and B. J. Tatarchuk, J. Phys. Chem. C, 2010, 114, 4075–4085 CAS.
- F. T. Li, C. G. Kou, Z. M. Sun, Y. J. Hao, R. H. Liu and D. S. Zhao, J. Hazard. Mater., 2012, 205, 164–170 CrossRef PubMed.
- M. D. Zhou, W. Y. Meng, Y. Li, Q. Wang, X. B. Li and S. L. Zang, Energy Fuels, 2014, 28, 516–521 CrossRef CAS.
- B. Rodriguez-Cabo, H. Rodriguez, E. Rodil, A. Arce and A. Soto, Fuel, 2014, 117, 882–889 CrossRef CAS.
- W. S. Zhu, W. L. Huang, H. M. Li, M. Zhang, W. Jiang, G. Y. Chen and C. R. Han, Fuel Process. Technol., 2011, 92, 1842–1848 CrossRef CAS.
- J. L. Wang, Q. Q. Guo, C. M. Zhang and K. X. Li, RSC Adv., 2014, 4, 59885–59889 RSC.
- V. C. Srivastava, RSC Adv., 2012, 2, 759–783 RSC.
- X. C. Chen, Y. W. Guan, A. A. Abdeltawab, S. S. Al-Deyab, X. L. Yuan, C. Y. Wang and G. R. Yu, Fuel, 2015, 146, 6–12 CrossRef CAS.
- X. D. Tang, T. Hu, J. J. Li, F. Wang and D. Y. Qing, RSC Adv., 2015, 5, 53455–53461 RSC.
- W. Zhu, C. Wang, H. Li, P. Wu, S. Xun, W. Jiang, Z. Chen, Z. Zhao and H. Li, Green Chem., 2015, 17, 2464–2472 RSC.
- T. V. Rao, B. Sain, S. Kafola, Y. K. Sharma, S. M. Nanoti and M. O. Garg, Energy Fuels, 2007, 21, 3420–3424 CrossRef CAS.
- V. E. Tumanov, E. A. Kromkin and E. T. Denisov, Russ. Chem. Bull., 2002, 51, 1641–1650 CrossRef CAS.
- J. A. M. Simões, Chem. Phys. Lett., 1989, 158, 175–177 CrossRef.
- W. Jiang, W. S. Zhu, H. Li, X. Wang, S. Yin, Y. H. Chang and H. M. Li, Fuel, 2015, 140, 590–596 CrossRef CAS.
- A. Bösmann, L. Datsevich, A. Jess, A. Lauter, C. Schmitz and P. Wasserscheid, Chem. Commun., 2001, 2494–2495 RSC.
Footnote |
† Electronic supplementary information (ESI) available. See DOI: 10.1039/c5ra16079k |
|
This journal is © The Royal Society of Chemistry 2015 |
Click here to see how this site uses Cookies. View our privacy policy here.