DOI:
10.1039/C5RA12562F
(Paper)
RSC Adv., 2015,
5, 60745-60753
Thermal, mechanical and optical transport properties of nanocomposite materials based on triethoxysilane-terminated polyimide and TiO2 nanoparticles
Received
29th June 2015
, Accepted 9th July 2015
First published on 9th July 2015
Abstract
In the preparation of polymer based nanocomposites (NCs), compatibility between the organic phase and inorganic nanoparticles as the filler can be improved by a variety of methods, such as functionalizing polymer chains at their ends, adding a coupling agent to bond the polymer chains and inorganic network etc. In this study, several novel polyimide/titanium dioxide nanocomposites (PI/TiO2 NCs) were prepared by the incorporation of TiO2 nanoparticles into silane terminated PI. To this point, 3-(bis(4-aminophenyl)amino)benzonitrile as a diamine monomer was first synthesized and then it was reacted with an excess amount of 4,4′-(hexafluoroisopropylidene) diphthalic anhydride. The triethoxysilane terminal groups were introduced by reacting the anhydride end-groups of the polymer with (3-aminopropyl)-triethoxysilane. Different hybrid materials based on the silane-terminated PI with inorganic TiO2 network were successfully fabricated by thermal imidization. The resulting materials were characterized by different techniques. According to the transmission electron microscopy images, the TiO2 nanoparticles were well dispersed into the PI matrix with a particle size around 20–40 nm. The resulting composite's mechanical, optical and thermal properties are effectively enhanced by the incorporation of 8 wt% TiO2 nanoparticles. According to the thermogravimetric analysis curves, the T5% of the NC was increased with the TiO2 loading and approximately a 63 °C improvement in T5% is found. The tensile strength of the hybrid films is significantly increased compared with the pure PI.
1. Introduction
Polymeric materials have many applications in multiple industries but improvements in their processability, durability and performance are required for their use in aerospace power and propulsion components.1–5 Forming hybrid polymer composites with a small amount of inorganic nanoparticles (NPs) is a promising approach to obtain balanced properties by exploiting the advantages of both organic polymer and inorganic NPs and the properties of the resulting nanocomposites (NCs) can be dramatically improved.6–8 In recent years, the synthesis of polymer NCs as new materials has attracted considerable attention since they possess novel optical, electronic, gas barrier, mechanical, and magnetic properties.9–11 Inorganic NPs exhibit excellent thermal stability and high modulus. A diversity of crystalline materials, i.e., three dimensional nano metal oxides, two-dimensional layered silicates, and one-dimensional carbon nanotubes, have been used for reinforcement of the polymer matrices.12,13 In addition to nanoclay and carbon nanotubes, oxide NPs are emerging fillers for many applications. Titanium dioxide (TiO2) are one of the most used inorganic NPs owing to its low cost, biocompatibility, low toxicity, UV shielding effect and photocatalytic properties.14 This NP offer favorable mechanical strength, thermal stability, and high surface area and as a result, it has been extensively studied in many polymeric materials.15–21
Aromatic polyimides (PIs) are a well-known class of high performance polymers that combine high thermal stability with chemical resistance, displaying excellent electrical and mechanical properties. Due to these characteristics, PIs have found extensive applications as fibers, films, coatings, photoresists, and composites.22–24 However, the synthesis and processing of these polymers are difficult because of their limited solubility and infusibility.25 To overcome these drawbacks, considerable efforts have been made to improve the processability of such polymers, while maintaining their remarkable properties.26 The most common strategy consists in the incorporation of flexible alkyl side chains, non-coplanar biphenylene moieties and bulky lateral substituent on the rigid polymer backbones.27–30 Among these, the introduction of bulky pendant units is a simple and convenient way to enhance the solubility and to incorporate new chemical functionalities.30 In order to induce certain features to the final PIs, while maintaining their intrinsic characteristics such as outstanding thermal stability and mechanical strength one way is designing new diamine or dianhydride monomers with novel molecular structures. According to the previous study by introducing of functional nitrile groups in the PI backbone, the thermooxidative resistance and the dielectric constant relative to the polymers may be increased in compression to those macromolecular without this substituent on to the chain.31,32 Also, the nitrile substituent may increase other physical properties of high performance materials, since it was shown that some amorphous polymers containing strong dipoles displayed piezoelectric response.31–33
In the preparation of PI NCs, compatibility between organic polymer and inorganic NPs can be enhanced by a variety of methods, such as functionalizing polymer chains at their ends, selecting appropriate groups of polymers within the repeat units, adding a coupling agent to bond PI chains and inorganic network.34–37 However, it is still a challenge to homogeneously disperse inorganic phase in polymer matrices in a highly efficient and controllable way. In continues to these researches, herein, we wish to report the preparation of new PI/TiO2 NCs using 3-aminopropyl triethoxysilane (APTEOS) functionalized PI. The Si–OEt end groups could condense with TiO2 NPs and provide organic–inorganic hybrids. For this purpose, a diamine monomer containing N-benzonitrile side chain was designed and synthesized. A novel silane terminated-PI film and related PI/TiO2 NCs were prepared via polycondensation reaction of the synthesized diamine and 4,4′-(hexafluoroisopropylidene) diphthalic anhydride (6FDA). The resulting materials were characterized by different techniques and it is hoped that the benzonitrile-containing PI will have enhanced processability as well as thermal stability.
2. Experimental
2.1. Materials
All materials and solvents were purchased from Merck Chemical Co and Aldrich Chemical CO. 3-Aminobenzonitrile, 1-fluoro-4-nitrobenzene, 6FDA, APTEOS, palladium on activated carbon (10 wt%) and hydrazine hydrates were used as received. N-Methyl-2-pyrrolidone (NMP), N,N-dimethylformamide (DMF) and N,N′-dimethylacetamide (DMAc) were dried over barium oxide, followed by fractional distillation. Nanosized TiO2 powder was purchased from Nanosabz Co. (Tehran, Iran) with average particle sizes of 30–50 nm.
2.2. Synthesis of diamine monomer
Diamine 2 was synthesis according to our previous article.33 In brief, at first, 3-(bis(4-nitrophenyl)amino)benzonitrile (1) was prepared by nucleophilic substitution reaction of 3-aminobenzonitrile with 1-fluoro-4-nitrobenzene in the present of cesium fluoride according to Scheme 1. This compound was purified by re-crystallization from acetic acid to dinitro intermediate 1 in 90% yield; mp: 218–220 °C. Than aromatic diamine 2 having a benzonitrile pendent group, 3-(bis(4-aminophenyl)amino)benzonitrile, was successfully synthesized by hydrazine Pd/C-catalytic reduction. The crude product was recrystallized from ethanol and dried in vacuum at 80 °C. The yield was 81%; mp 188–191 °C. The purity of monomer 2 was checked by thin layer chromatography, which showed one spot in an ethylacetate/cyclohexane mixture (50
:
50) with Rf = 0.42.
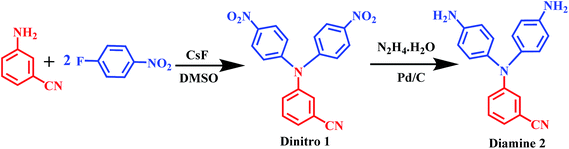 |
| Scheme 1 Synthesis of diamine with benzonitrile pendant group. | |
FTIR (KBr, cm−1) of diamine 2: 3448 (s), 3377 (s), 3113 (w), 3075 (w), 2225 (s), 1555 (m), 1535 (m) 1440 (w), 1323 (w), 1252 (w), 844 (m), 739 (w). 1H-NMR (400 MHz, DMSO-d6, ppm) of diamine 2: 4.49 (s, 4H, NH), 6.26–6.28 (d, 8H, Ar–H, J = 4.5 Hz), 6.49 (s, 1H, Ar–H), 6.76–6.78 (d, 1H, Ar–H), 7.19–7.20 (d, 1H, Ar–H, J = 4 Hz), 7.36–7.38 (dd, 1H, Ar–H, J = 4 Hz). 13C-NMR (100 MHz, DMSO-d6), of diamine 2, δ (ppm): 108.22 (Ar), 112.31 (CN), 118.82 (Ar), 121.18 (Ar), 123.32 (Ar), 124.12 (Ar), 125.17 (Ar), 137.25 (Ar), 138.45 (Ar), 141.35 (Ar), 148.33 (Ar). Elemental analysis calculated for C19H16N4 (300.36 g mol−1): calcd (%) C, 75.98%; N, 18.65%; H, 5.37%. Found (%) C, 75.86%; N, 18.79%; H, 5.39%.
2.3. Preparation of polyamic acid (PAA) and pristine PI
3-(Bis(4-aminophenyl)amino)benzonitrile (1.00 g, 3.32 mmol) as diamine monomer 2 was dissolved in NMP (20 wt%) and cooled with the ice water bath. After completely dissolved, 6FDA (1.47 g, 3.32 mmol) as the anhydride monomer 3 was added into the above solution under stirring with a mechanical stirrer, a condenser and a nitrogen inlet for 6 h at room temperature (R.T.) to obtain the polyamic acid (PAA) as shown in Scheme 2. The inherent viscosity of the PAA was 0.97 dL g−1, as measured in DMAc at a concentration of 0.5 g dL−1 at 30 °C. The PAA was converted into PI by thermal imidization method. In the method, about 2.00 g of the PAA solution was spread into a Petri culture dish 7 cm in diameter and baked at 90 °C overnight (ca. 12 h) for the removal of the casting solvent. The semidried PAA film was further dried and converted into the PI by sequential heating at 150 °C for 30 min, at 200 °C for 30 min, and at 250 °C for 1 h. The inherent viscosity of the PI was 1.13 dL g−1 at a concentration of 0.5 g dL−1.
 |
| Scheme 2 Synthesis of PAA and PI. | |
FT-IR (KBr, cm−1) of the PI: 3086 (aromatic C–H stretching), 2225 (stretching C
N), 1777 (asymmetric imide C
O stretching), 1722 (symmetric imide C
O stretching), 1625 (aromatic C
C stretching), 1236, 1126 (C–F stretching), and 821 (C–N bending). 1H-NMR (400 MHz, DMSO-d6, ppm) of the PI: 6.26–6.27 (d, 2H, Ar–H, J = 3.5), 6.48–6.49 (s, 2H, Ar–H, J = 4.5 Hz), 6.68–7.69 (d, 2H, Ar–H, J = 4.5 Hz), 6.88 (s, 1H, Ar–H), 7.27–7.28 (d, 1H, Ar–H, J = 3.5), 7.36–7.37 (d, 1H, Ar–H, J = 3.5), 7.17–7.18 (d, 1H, Ar–H, J = 4.5 Hz), 7.66–7.68 (d, 1H, Ar–H, J = 3.5), 7.88–7.89 (d, 1H, Ar–H, J = 4.5 Hz), 8.17–8.18 (d, 1H, Ar–H, J = 4.5 Hz), 8.38–8.39 (d, 1H, Ar–H, J = 4.5 Hz). Anal. Calcd for C38H18F6N4 O4 (708.56 g mol−1): C, 64.42%; H, 2.56%; N, 7.91%; Found: C, 64.48%; H, 2.53%; N, 7.85%.
2.4. Preparation of the silane terminated-PI/TiO2 NC films
In the preparation of PI based NCs, compatibility between organic PI and inorganic NPs can be enhanced by a variety of methods, such as functionalizing polymer chains at their ends, selecting appropriate groups of polymers within the repeat units, adding a coupling agent to bond PI chains and inorganic network. Silane-terminated PI/TiO2 hybrid films were synthesized according to the synthesis pathway as shown in Scheme 3. In this way, 3-(bis(4-aminophenyl)amino)benzonitrile (1.00 g, 3.32 mmol) was dissolved in NMP (20 wt%) and cooled with the ice water bath. After completely dissolved, 6FDA (2.94 g, 6.64 mmol) was added into the above solution under stirring for 6 h at room temperature to formed the PAA solution. In the next step APTEOS (0.74 g, 3.32 mmol) was slowly dropped into the mixture. The reaction was stirred at room temperature for 6 h to obtain the PAA with triethoxysilane-terminated groups as shown in Scheme 3. Then different amount of TiO2 NPs (4, 8 and 12 wt%) were added to the PAA solution and thin films of PI with different percentages of TiO2 NPs were fabricated by casting onto dust-free glass plates. Resulted thin films were annealed using an electric air-circulating oven at 60, 120, 170, 220, and 270 °C for 1 h each and 300 °C for 6 h and then were cooled and removed from glass surface using a sharp edge blade. The obtained films were around 30–40 μm thick and were used for further characterization. The NCs are named as PI/TiO2 NC4%, PI/TiO2 NC8% and PI/TiO2 NC12%, where the percentage given in the genetic abbreviations is the weight percentage.
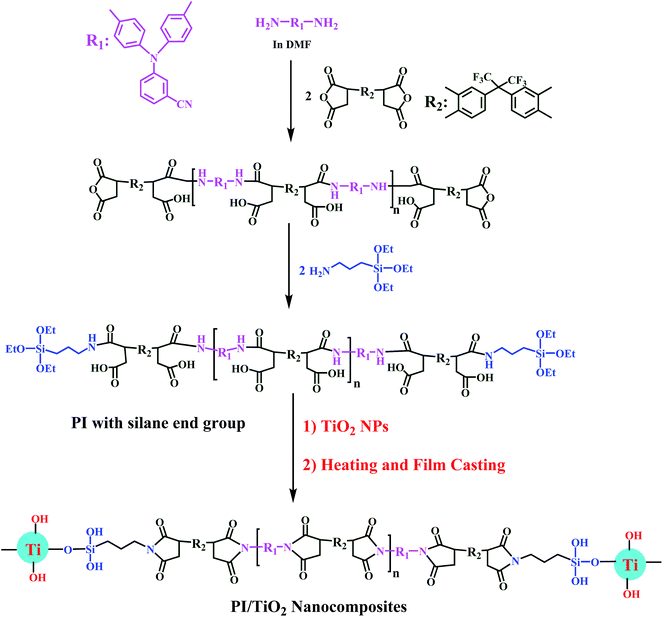 |
| Scheme 3 Synthesis of silane-terminated PI and PI/TiO2 NC materials. | |
2.5. Techniques
Fourier transform infrared (FT-IR) spectroscopic measurements were performed using a Magna-IR Nicolet 560 FTIR spectrophotometer by incorporating samples in KBr disks. The spectra were recorded in the range of 4000–400 cm−1 at a resolution of 4 cm−1. Carbon, hydrogen and nitrogen content of the compounds were determined by pyrolysis method by Vario EL elemental analyzer. NMR spectra were recorded on a Bruker Avance DRX 400 and 100 MHz, by using solutions in deuterated dimethylsulfoxide (DMSO-d6). Inherent viscosity (ηinh) of the polymer in DMAc was measured at about 0.5 g dL−1 concentration with an Ubbelohde viscometer at 30 ± 0.5 °C. The XRD patterns were collected by using a Philips Xpert MPD X-ray diffractometer. The diffractograms were measured for 2θ, in the range of 10–80°, using a voltage of 40 kV and Cu Kα incident beam (λ = 1.51418 Å). Thermal stability was measured with a TGA-2950 thermo gravimetric analyzer (TA instrument Co.) at a heating rate of 20 °C min−1 from room temperature to 800 °C under a continuous flow of nitrogen. Tensile strength and elongation at break of thin PI membranes were measured with the help of UTM-INSTRON, PLUS, Model no. 8800. Test samples with dimension of 10 × 25 mm2 and thickness in the range of 30–40 μm were used for the measurement of tensile strength and percentage of elongation at break. Ultra violet spectra of the polymer films were recorded at room temperature using Detector SD–2000 (Ocean Optics Inc.) and source lamp DH–2000.
3. Results and discussion
3.1. FT-IR and NMR study
FT-IR, 1H-NMR and 13C-NMR spectra of the dinitro 1 and diamine 2 were reported in our previous article.33 In the FT-IR spectrum of the dinitro compound 1, the nitro group show two characteristic bands at around 1541 and 1338 cm−1 for NO2 asymmetric and symmetric stretching, respectively. After reduction, the characteristic absorptions of the nitro group disappeared and the amino group showed the typical N–H stretching absorption pair in the region of 3448–3377 cm−1. The characteristic absorptions of the nitrile group were observed at 2225 cm−1. In 1H-NMR spectrum of the diamine compound 2, a peak at 4.50 ppm was assigned to the amine protons group and all aromatic protons appeared at 6.25–7.38 ppm.
Conversion of the PAA to the fully cyclized PI was proved by means of by FT-IR, 1H NMR spectroscopy and elemental analysis techniques. The FT-IR spectra of the PAA and corresponding PI based on 6FDA are presented in Fig. 1. Neat PAA showed a broad absorption characteristic band of carboxylic O–H and amide N–H groups at about 2600–3700 cm−1 and a narrow characteristic band at 1685 cm−1 associated to C
O of amide linkages (Fig. 1a). In the spectra of PI, absorption bands of the imide groups appear at 1777 and 1722 cm−1 for the symmetric and anti-symmetric stretching vibrations of the carbonyl groups. Other characteristic absorption bands of the imide were appeared at 1353 and 702 cm−1 for the C–N stretching and C
O bending, respectively. Moreover, it is observed in Fig. 2c that the stretching vibration at about 1220∼1100 cm−1 and weak absorption band at 689 cm−1 were assigned to the C–F group and CF2 groups, respectively.38
 |
| Fig. 1 FT-IR spectra of the PAA (a) and PI (b). | |
 |
| Fig. 2 1H-NMR (400 MHz) spectra of PI in DMSO-d6 at R.T. | |
Fig. 2 exhibits a 1H-NMR spectra of the PI based on 6FDA, in which all the peaks have been readily assigned to the hydrogen atoms of the repeating unit and no amide or acid protons at 10–12 ppm were appeared. This indicates that complete imidization was really achieved. The assignments of each proton designated in the 1H-NMR spectrum are in complete agreement with the proposed polymer structures and PAA was converted into PI by chemical imidization. The sharp peaks at 4.50 ppm corresponding to the amine protons in 1H-NMR spectrum of diamine disappear completely here, and new peaks were appeared at 7.50–8.40 ppm correspond to the protons in the dianhydride units (Fig. 2).
The structures of the PI and hybrid composites were characterized by FT-IR spectra. Fig. 3 shows the FT-IR spectra of the pure TiO2 NP, PI and NC materials with different amount of TiO2 NPs. Neat TiO2 show the characteristic peak of hydroxyl group at 3423 cm−1 and the Ti–O–Ti bands are appeared in the range of 450–650 cm−1 (Fig. 3a).18,19 For the NCs containing triethoxysilane-terminated PI and inorganic TiO2 NPs, in addition to the PI peaks (Fig. 3d), the FT-IR spectra show new absorption bands at 1020–1100 cm−1 for Si–O–Ti symmetric stretching vibrations and at 890 cm−1 for Si–OH groups.19 The bands at 2880–2930 cm−1 can be ascribed to the C–H symmetrical and asymmetrical stretching absorptions of the CH2 group of the APTES, respectively. Also, the Ti–O–Si bands are appeared in the range of 450–650 cm−1 in the FT-IR spectra of the NC films (Fig. 3b and c). This result verifies that inorganic TiO2 NPs were successfully formed in the hybrid PI composites by the thermal imidization techniques.
 |
| Fig. 3 FT-IR spectra of the TiO2 NPs (a), PI with 4% (b) and 12% (c) of TiO2 NPs and pure PI (d). | |
3.2. X-ray diffraction
Fig. 4 shows the XRD patterns of the pristine titania, PI matrix and NCs with different TiO2 percentage. For neat TiO2 (Fig. 4a), the peaks appeared at 101, 110, 004, 200, 105, 211, 204, 220, 301 were for the crystalline portion of this compound.28 The XRD analysis for the pure PI film exhibits a typical amorphous structure, which is associated with the broad peak of 2θ at 20° in the range from 15° to 25° (Fig. 4b). The PI/TiO2 films, on the other hand, show additional sharp diffraction peaks superimposed on top of the broad amorphous background. The XRD patterns of PI/TiO2 NCs with 4, 8 and 12 wt% of TiO2 NPs indicating that the morphology of TiO2 NPs has not been disturbed during the process. The intensity of peaks corresponding to TiO2 NPs increased with higher concentration of TiO2 in the obtained NCs. All these data indicated that TiO2 NPs were dispersed in the polymer matrix.
 |
| Fig. 4 XRD patterns of TiO2 NPs (a), the silane terminated PI (b) and PI with 4% (c), 8% (d) and 12% (e) of TiO2 NPs. | |
3.3. Morphology of PI and NCs
The morphology of the silane terminated PI with 4, 8 and 12 wt% of TiO2 NPs was monitored with FE-SEM technique as shown in Fig. 5. The silica loading and reinforcement binding with PI matrix are confirmed by the morphology. From FE-SEM images, any aggregation or phase separation has not been observed. This shows the method for the preparation of silane terminated PI/TiO2 NCs used in this study could make the inorganic part well dispersed into polymer matrix and gave uniform and homogeneous distribution of TiO2 NPs in these NCs as compared with PI without end group silane coupling agent.38 As discussed above, the triethoxysilane terminal groups of PI can inhibit strong phase separation tendency between organic PI and inorganic TiO2 NPs. Even for the high TiO2 concentration, PI/TiO2 NC12% still can prevent the significant phase separation of titania and lead to a homogenous distribution of TiO2 NPs (Fig. 5e and f).
 |
| Fig. 5 FE-SEM images of silane terminated PI with 4% (a and b), 8% (c and d) and 12% (e and f) of TiO2 NPs. | |
Fig. 6 shows the TEM micrographs of silane terminated PI NC with 4 and 12 wt% of TiO2 NPs. In these images, no aggregation is visible between the modified TiO2 NPs and relatively satisfactory dispersion of NPs can be observed in comparison with PI without using silane coupling agent by in situ polymerization.39 The above observation confirms that triethoxysilane terminal groups introduced by the reaction with APTEOS are important to counter-balance the phase separation tendency when the TiO2 content is too high. As shown in TEM images, it was estimated that the particle size of the TiO2 NPs in the NC materials PIs are around 20–40 nm with spherical shapes.
 |
| Fig. 6 TEM images of silane terminated PI with 4% (a and b) and 12% (c and d) of TiO2 NPs. | |
3.4. Mechanical properties of PI films
The effects of TiO2 NPs loading on the tensile properties of silane terminated PI/TiO2 NPs films were investigated and the results are presented in Fig. 7. Filler consisting entirely of TiO2 generally increases the ultimate strength, but decreases the maximum extensibility. The mechanical properties of NCs largely depend on the external load transfer between the reinforcing nanofiller phase and the matrix.40–42 According to the previous study,43 the strength should be reduced if there are no bonding sites between the organic polymer phase and the inorganic TiO2 phase due to the inert nature of the PIs and the weak interactions between these polymers and the TiO2. In this case, the TiO2 acts as nonreactive and non-reinforcing filler. It is generally believed that external stress on a polymer composite is transferred from the continuous phase (polymer matrix) to the discontinuous phase (filler). Therefore, the ultimate properties of the NCs are dependent on the extent of bonding between the two phases, the surface area of the TiO2, and the arrangements between the TiO2 particles. As can be seen in Fig. 7, the tensile strength of PI/TiO2 NPs films is significantly increased compared with the pure PI. The maximum stress at break (ultimate strength) was found to increase initially with increase in TiO2 content, and at 8 wt% TiO2 showed a maximum value of 112.41 MPa (relative to the 96.23 MPa of the neat PI) representing considerable improvement in tensile strength. As the TiO2 content increases (12 wt%), the tensile strength of PI/TiO2 films decreases, but still better than the pure PI film because of increasing brittleness. According to the Fig. 7, ultimate strength and initial modulus were increased with TiO2 contents, but ultimate elongation decreased with the increase of TiO2 contents, especially at higher TiO2 content. For elongation at break, the sample geometry (most importantly the film thickness) is an additional factor to consider and may be the determine factor why the 8 wt% TiO2 sample shows the best result.44 The above results showed that the interactions between the silane terminated PI and the TiO2 are very important.
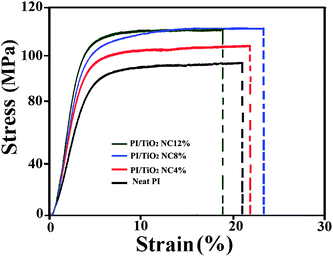 |
| Fig. 7 Tensile stress–strain curves of silane terminated PI with different amount of TiO2 NPs. | |
3.5. Thermal properties
The thermal stability of silane terminated PI/TiO2 NCs and pure PI as references was investigated at the heating rate of 20 °C min−1 from 20 to 800 °C. Fig. 8 shows TGA curves for the four samples pure PI, PI/TiO2 NC4%, PI/TiO2 NC8% and PI/TiO2 NC12%. The pure PI film, is quite stable up to 420 °C. The weight of the pure PI film remained around 98% under 450 °C, and then substantially decreased from 480 °C to 600 °C (Fig. 8). The PI/TiO2 NC film showed a similar pattern of weight loss but at higher temperature (over 500 °C) than the pure PI films and the decomposition was completed at around 600 °C. The decomposition temperature at 5% (T5%) weight loss for these composites increases with the TiO2 nanofillers loading. About 63 °C improvements in T5% is found in 10 wt% TiO2 nanofillers loading. Excellent thermal stability should be attributed to the contribution of the existed covalent bonding interaction between silane terminated PI and TiO2 nanofillers. The 10% weight loss temperatures (T10%) of the silane terminated PI is 513 °C and for NC materials with 4, 8 and 12 wt% of TiO2 nanofillers, it is 530, 564 and 576 °C, respectively (Table 1). The char yields at 800 °C of the NCs with different TiO2 content are higher than that of pure PI which provided more evidence of completely organic–inorganic bonding.45 The char yield of NCs was from 76 to 80% at 800 °C. By comparison of the thermal properties of these hybrid materials with different NCs with similar structures,28,30 the results show that these hybrids had higher thermal stability because of the good interaction between the silane terminated PI and TiO2 NPs. Hence, incorporation of the PI with reactive terminal groups showed ability to prevent the phase separation of TiO2 in PI matrices due to the strong covalent and partial hydrogen bonding networks formed during the process and the thermal properties was enhanced.
 |
| Fig. 8 TGA thermograms of silane terminated PI with different amount of TiO2 NP. | |
Table 1 Thermal properties of the pure PI and NC with different amount of TiO2 NPs
Samples |
Decomposition temperature (°C) |
Char yieldb (%) |
T5a |
T10a |
Temperature at which 5 and 10% weight loss was recorded by TGA at heating rate of 20 °C min−1 in a N2 atmosphere. Weight percent of the material left undecomposed after TGA at maximum temperature 800 °C in a N2 atmosphere. |
Pure PI |
493 |
513 |
73 |
PI/TiO2 NC4% |
515 |
530 |
76 |
PI/TiO2 NC8% |
556 |
564 |
78 |
PI/TiO2 NC12% |
563 |
576 |
80 |
3.6. Optical properties of the PI and composites
It is known that aromatic PI films, owing to their high glass-transition and decomposition temperature, low water absorption, good transmission and low optical loss, are excellent candidates for use as transparent flexible substrates in displays or other electronic applications.46 Thin films of PI and NC with different TiO2 NPs were used for optical transparency with UV-vis spectroscopy. Fig. 9 exhibits the UV-vis transmittance spectra of these hybrid films. UV-vis absorption spectra of PI/TiO2 hybrid films showed a maximum absorption at 390 nm. Silane terminated PI shows the highest transmittance of 97% at 480 nm, and the film is entirely colorless. After incorporating TiO2 NPs with weight percentage from 4% to 12% into silane terminated PI, the composite films kept transparent and uniform appearance, and their transmittance was only slightly decreased (Fig. 9). The light scattering and opacity caused by aggregated inorganic titania phases in the wavelength scale were effectively avoided for the films, which is attributed to the reaction between triethoxysilane terminal groups of polymer and TiO2 NPs as compared with other PI/TiO2 NC films.47 The UV shielding ability relates with the scattering and/or absorbance of TiO2 NPs. The scattering property plays a main role in shielding of UV irradiation. Thus, these PI/TiO2 hybrid films have potential to apply as coating to block the UV radiation, particularly between 370–400 nm. Most PI between the UV and visible area show strong absorption due to the highly conjugated aromatic structures and intermolecular charge-transfer complex formation of PI.48 According to the Fig. 9, the percentage of transmittance at 500 nm for neat PI is 98% and for NC with different amount of TiO2 NP, it is around 89–96%. All NCs showed highest optical transparency due to the presence of trifluoromethyl groups in anhydride part, because these groups are very much effective in decreasing charge transfer complex formation and improve the optical properties of the resulting hybrid materials.48–50
 |
| Fig. 9 UV-visible absorption spectra of silane terminated PI with different amount of TiO2 NPs. | |
4. Conclusion
In the preparation of polymer based NCs, compatibility between organic phase as a matrix and inorganic NPs as filler can be improved by a variety of methods, such as functionalizing polymer chains at their ends, adding a coupling agent to bond polymer chains and inorganic network and etc. In this study, first, new silane-terminated PI with benzonitrile pendant group was synthesized by the reacting of the anhydride end groups of the polymer with APTEOS. Then, a series of PI NC films based on the triethoxysilane-terminated PI and different amount of inorganic TiO2 NPs (4, 8 and 12 wt%) was successfully fabricated by thermal imidization techniques. The formation of the resulting NCs was confirmed by the FT-IR and XRD techniques. According to the FE-SEM and TEM images, the TiO2 NPs were well dispersed into the PI matrix and no aggregation was observed because the triethoxysilane terminal groups of PI can inhibit strong phase separation tendency between organic PI and inorganic TiO2 NPs. The size of the TiO2 NPs in the NC materials was around 20–40 nm with spherical shapes. The tensile strength of PI/TiO2 NPs films is significantly increased compared with the pure PI and the maximum stress at break was found to increase initially with increase in TiO2 content, and at 8 wt% TiO2 showed a maximum value of 112.41 MPa relative to the 96.23 MPa of the neat PI. According to the TGA curves, the T5% of the NC was increased with the TiO2 nanofillers loading and approximately 63 °C improvements in T5% is found in 8 wt% TiO2 nanofillers loading. Excellent thermal stability should be ascribed to the role of the existed covalent bonding interaction and or hydrogen bonding between silane terminated PI and TiO2 nanofillers. Neat PI and related NC films show good optical transparency due to the presence –CF3 groups in anhydride part. According to the obtained results, the resulting hybrid materials due to their good thermal, mechanical, optical and morphological properties, are amenable for use as high-performance materials and demonstrate a promising potential for future application.
Conflict of interest
The authors declare no competing financial interest.
Acknowledgements
We wish to express our gratitude to the Research Affairs Division Isfahan University of Technology (IUT), Isfahan, for partial financial support. Further financial support from National Elite Foundation (NEF), and Iran Nanotechnology Initiative Council (INIC) is gratefully acknowledged.
References
- W. E. Moerner and S. M. Silence, Chem. Rev., 1994, 94, 127–155 CrossRef CAS
. - Z. M. Dang, Y. Q. Lin, H. P. Xu, C. Y. Shi, S. T. Li and J. Bai, Adv. Funct. Mater., 2008, 18, 1509–1517 CrossRef CAS PubMed
. - N. Awang, A. F. Ismail, J. Jaafar, T. Matsuura, H. Junoh, M. H. D. Othman and M. A. Rahman, React. Funct. Polym., 2015, 86, 248–258 CrossRef CAS PubMed
. - C. Constantinescu, A. Rotaru, A. Nedelcea and M. Dinescu, Mater. Sci. Semicond. Process., 2015, 30, 242–249 CrossRef CAS PubMed
. - M. Thelakkat, Macromol. Mater. Eng., 2002, 287, 442–461 CrossRef CAS
. - A. C. Balazs, T. Emrick and T. P. Russell, Science, 2006, 314, 1107–1110 CrossRef CAS PubMed
. - S. Gong, Z. H. Zhu and S. A. Meguid, Polymer, 2015, 56, 498–506 CrossRef CAS PubMed
. - R. Gines, R. Libanori, A. R. Studart, A. Bergamini, M. Motavalli and P. Ermanni, Composites, Part B, 2015, 72, 80–86 CrossRef CAS PubMed
. - S. Thomas, G. Zaikov and V. Meera, Recent advances in polymer nanocomposites: synthesis and characterizations, CRC Press, 2010 Search PubMed
. - E. Ruiz-Hitzky, M. Darder, A. C. S. Alcântara, B. Wicklein and P. Aranda, Adv. Polym. Sci., 2015, 267, 39–86 CrossRef
. - A. Kafy, K. K. Sadasivuni, H. C. Kim, A. Akther and J. Kim, Phys. Chem. Chem. Phys., 2015, 17, 5923–5931 RSC
. - F. Wypych and K. G. Satyanarayana, J. Colloid Interface Sci., 2005, 285, 532–543 CrossRef CAS PubMed
. - S. Khaled, R. Sui, P. A. Charpentier and A. S. Rizkalla, Langmuir, 2007, 23, 3988–3995 CrossRef CAS PubMed
. - R. J. Nussbaumer, W. R. Caseri, P. Smith and T. Tervoort, Macromol. Mater. Eng., 2003, 288, 44–49 CrossRef CAS PubMed
. - N. Nakayama and T. Hayashi, J. Appl. Polym. Sci., 2007, 105, 3662–3672 CrossRef CAS PubMed
. - P. C. Chiang and W. T. Whang, Polymer, 2015, 62, 1–10 CrossRef PubMed
. - H. Seyedjamali and A. Pirisedigh, Colloid Polym. Sci., 2011, 289, 15–20 CAS
. - S. Mallakpour and M. Dinari, Prog. Org. Coat., 2012, 75, 373–378 CrossRef CAS PubMed
. - S. Mallakpour and P. Asadi, Polym. Bull., 2012, 68, 53–67 CrossRef CAS
. - Q. F. Xu, Y. Liu, F. J. Lin, B. Mondal and A. M. Lyons, ACS Appl. Mater. Interfaces, 2013, 5, 8915–8924 CAS
. - H. Zhang, J. Huang, L. Yang, R. Chen, W. Zou, X. Lin and J. Qu, RSC Adv., 2015, 5, 4639–4647 RSC
. - D. Yu, A. Gharavi and L. Yu, J. Am. Chem. Soc., 1995, 117, 11680–11686 CrossRef CAS
. - M. K. Ghosh and K. L. Mittal, Polyimides: Fundamentals and Applications, Marcel Dekker Inc., New York, USA, 1996 Search PubMed
. - D. P. Erhard, F. Richter, C. B. A. Bartz and H. W. Schmidt, Macromol. Rapid Commun., 2015, 36, 520–527 CrossRef CAS PubMed
. - H. S. Hsiao and Y. T. Chou, Polymer, 2014, 55, 2411–2421 CrossRef PubMed
. - Y. T. Chern and J. Y. Tsai, Macromolecules, 2008, 41, 9556–9564 CrossRef CAS
. - S. H. Hsiao, H. M. Wang, W. J. Chen, T. M. Lee and C. M. Leu, J. Polym. Sci., Part A: Polym. Chem., 2011, 49, 3109–3120 CrossRef CAS PubMed
. - M. Dinari and H. Ahmadizadegan, Polymer, 2014, 55, 6252–6260 CrossRef CAS PubMed
. - L. Yi, C. Li, W. Huang and D. Yan, J. Polym. Res., 2014, 12, 572–581 CrossRef
. - M. Dinari and H. Ahmadizadegan, RSC Adv., 2015, 5, 8630–8639 RSC
. - M. Bruma, F. Mercer, B. Schulz, R. Dietel, J. Fitch and P. Cassidy, High Perform. Polym., 1994, 6, 183–191 CAS
. - B. Lin and X. Xu, Polym. Bull., 2007, 59, 243–250 CrossRef CAS
. - M. Dinari and H. Ahmadizadegan, RSC Adv., 2015, 5, 26040–26050 RSC
. - C. F. Cheng, H. H. Cheng, P. W. Cheng and Y. J. Lee, Macromolecules, 2006, 39, 7583–7590 CrossRef CAS
. - J. Liu, Y. Nakamura, T. Ogura, Y. Shibasaki, S. Ando and M. Ueda, Chem. Mater., 2008, 20, 273–281 CrossRef CAS
. - S. K. Kim, X. Wang, S. Ando and X. Wang, Eur. Polym. J., 2015, 64, 206–214 CrossRef CAS PubMed
. - Z. Xiao, P. Guo and C. Wang, Colloid Polym. Sci., 2015, 293, 307–312 CAS
. - Y. Feng, J. Yin, M. Chen, M. Song, B. Su and Q. Lei, Mater. Lett., 2013, 96, 113–116 CrossRef CAS PubMed
. - X. Liu, J. Yin, Y. Kong, M. Chen, Y. Feng, K. Yan, X. Li, B. Su and Q. Lei, Thin Solid Films, 2013, 544, 352–356 CrossRef CAS PubMed
. - D. Qian, E. C. Dickey, R. Andrews and T. Rantell, Appl. Phys. Lett., 2000, 76, 2868–2870 CrossRef CAS PubMed
. - V. Antonucci, K. T. Hsiao and S. G. Advani, Review of polymer composites with carbon nanotubes, in Advanced Polymeric Materials Structure Property Relationships, ed. G. O. Shonaike and S. G. Advani, CRC Press, Boca Raton, 2003 Search PubMed
. - S. M. Khaled, R. Sui, P. A. Charpentier and A. S. Rizkalla, Langmuir, 2007, 23, 3988–3995 CrossRef CAS PubMed
. - S. Mallakpour and M. Dinari, Polymer, 2011, 52, 2514–2523 CrossRef CAS PubMed
. - M. Chen, J. Yin, R. Jin, L. Yao, B. Sua and Q. Lei, Thin Solid Films, 2015, 584, 233–237 Search PubMed
. - H. J. Yen, C. L. Tsai, P. H. Wang, J. J. Lin and G. S. Liou, RSC Adv., 2013, 3, 17048–17056 RSC
. - M. D. Damaceanu, C. P. Constantin, A. Nicolescu, M. Bruma, N. Belomoina and R. S. Begunov, Eur. Polym. J., 2014, 50, 200–213 CrossRef CAS PubMed
. - J. Liu, Y. Nakamura, T. Ogura, Y. Shibasaki, S. Ando and M. Ueda, Chem. Mater., 2008, 20, 273–281 CrossRef CAS
. - C. P. Yang, S. H. Hsiao and K. H. Chen, Polymer, 2002, 43, 5095–5104 CrossRef CAS
. - W. Jang, D. Shin, S. Choi, S. Park and H. Han, Polymer, 2007, 48, 2130–2143 CrossRef CAS PubMed
. - V. Kute and S. Banerjee, J. Appl. Polym. Sci., 2007, 103, 3025–3044 CrossRef CAS PubMed
.
|
This journal is © The Royal Society of Chemistry 2015 |
Click here to see how this site uses Cookies. View our privacy policy here.